多孔介质设置及建模实例
FLUENT多孔介质数值模拟设置
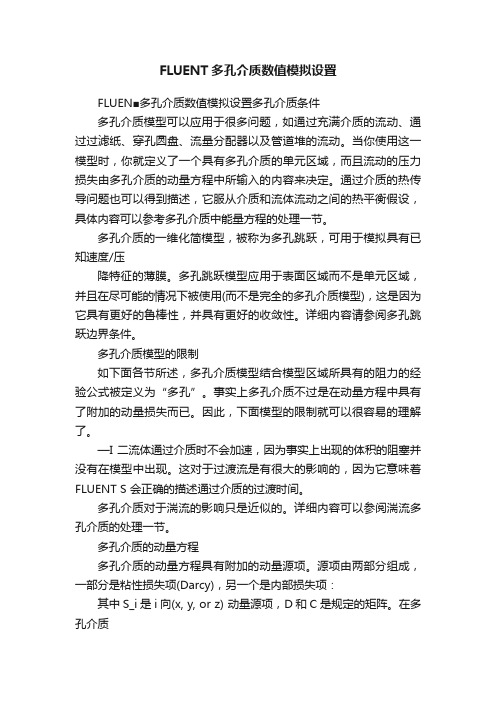
FLUENT多孔介质数值模拟设置FLUEN■多孔介质数值模拟设置多孔介质条件多孔介质模型可以应用于很多问题,如通过充满介质的流动、通过过滤纸、穿孔圆盘、流量分配器以及管道堆的流动。
当你使用这一模型时,你就定义了一个具有多孔介质的单元区域,而且流动的压力损失由多孔介质的动量方程中所输入的内容来决定。
通过介质的热传导问题也可以得到描述,它服从介质和流体流动之间的热平衡假设,具体内容可以参考多孔介质中能量方程的处理一节。
多孔介质的一维化简模型,被称为多孔跳跃,可用于模拟具有已知速度/压降特征的薄膜。
多孔跳跃模型应用于表面区域而不是单元区域,并且在尽可能的情况下被使用(而不是完全的多孔介质模型),这是因为它具有更好的鲁棒性,并具有更好的收敛性。
详细内容请参阅多孔跳跃边界条件。
多孔介质模型的限制如下面各节所述,多孔介质模型结合模型区域所具有的阻力的经验公式被定义为“多孔”。
事实上多孔介质不过是在动量方程中具有了附加的动量损失而已。
因此,下面模型的限制就可以很容易的理解了。
—I 二流体通过介质时不会加速,因为事实上出现的体积的阻塞并没有在模型中出现。
这对于过渡流是有很大的影响的,因为它意味着FLUENT S 会正确的描述通过介质的过渡时间。
多孔介质对于湍流的影响只是近似的。
详细内容可以参阅湍流多孔介质的处理一节。
多孔介质的动量方程多孔介质的动量方程具有附加的动量源项。
源项由两部分组成,一部分是粘性损失项(Darcy),另一个是内部损失项:其中S_i是i向(x, y, or z) 动量源项,D和C是规定的矩阵。
在多孔介质单元中,动量损失对于压力梯度有贡献,压降和流体速度(或速度方阵)成比例。
对于简单的均匀多孔介质:其中a是渗透性,C_2时内部阻力因子,简单的指定D和C分别为对角阵1/a 和C_2其它项为零。
FLUENT?允许模拟的源项为速度的幕率:其中C_0和C_1为自定义经验系数。
注意:在幕律模型中,压降是各向同性的,C_0的单位为国际标准单位。
多孔介质介绍

Fluent自带了一个多孔介质的例子,catalytic_converter.cas,是一个汽车尾气催化还原装置,其中绿色部分为催化剂部分其他设置就不说了,只说说与多孔介质有关的设置。
在建立模型时,必须将多孔介质单独划分为一个区域,然后才可以在设置边界条件时将这个区域设置为多孔介质。
1、在zone中选中该区域,在type中选中fluid,点set来到设置面板。
2、在Fluid面板中,选中Porous zone选项,如果忽略多孔区域对湍流的影响,选中Laminar zone。
3、首先是速度方向的设置,在2d中,在direction-1 vector中填入速度方向,在3d中,在direction-1 vector和direction-2 vector中填入速度方向,余下的未填方向,可以根据principal axis得到。
另外也可以用Update From Plane Tool来得到这两个量。
4、填入粘性阻力系数和惯性阻力系数,这两个系数可以通过经验公式得到。
在catalytic_converter.cas中可以看到x方向的阻力系数都比其他两个方向的阻力系数小1000倍,说明x方向是主要的压力降方向,其他两个方向不流通,压力降无限大。
(经验公式可以看帮助文件,其中有详细的介绍)。
随后的Power Law Model 中两个系数是另一种描述压力降的经验模型,一般不使用,可以保留缺省值0。
5、最后是Fluid Porosity,这个值只在模型选择了Physical Velocity 时才起作用,一般对计算没有影响,这个值要小于1。
补充:这个值在计算热传导时也起作用。
下面是改变一些参数后的比较。
1、速度方向的改变:原case:1、0、0 和0、1、0 y=0截面的速度矢量图修正case:-0.7366537、0.06852359、0.6727893 和0.6694272、-0.06727878、0.7398248 y=0速度矢量图2、修改Porosity值为0.5 原case,y=0截面修正case,y=0截面:修正case,且打开solver面板中的Physical Velocity选项:最后比较一下有多孔介质和无多孔介质对流场的影响。
fluent中多孔介质模型的设置
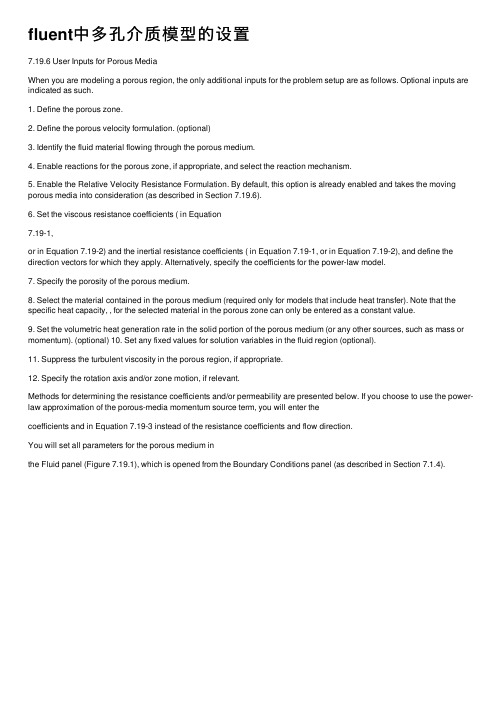
fluent中多孔介质模型的设置7.19.6 User Inputs for Porous MediaWhen you are modeling a porous region, the only additional inputs for the problem setup are as follows. Optional inputs are indicated as such.1. Define the porous zone.2. Define the porous velocity formulation. (optional)3. Identify the fluid material flowing through the porous medium.4. Enable reactions for the porous zone, if appropriate, and select the reaction mechanism.5. Enable the Relative Velocity Resistance Formulation. By default, this option is already enabled and takes the moving porous media into consideration (as described in Section 7.19.6).6. Set the viscous resistance coefficients ( in Equation7.19-1,or in Equation 7.19-2) and the inertial resistance coefficients ( in Equation 7.19-1, or in Equation 7.19-2), and define the direction vectors for which they apply. Alternatively, specify the coefficients for the power-law model.7. Specify the porosity of the porous medium.8. Select the material contained in the porous medium (required only for models that include heat transfer). Note that the specific heat capacity, , for the selected material in the porous zone can only be entered as a constant value.9. Set the volumetric heat generation rate in the solid portion of the porous medium (or any other sources, such as mass or momentum). (optional) 10. Set any fixed values for solution variables in the fluid region (optional).11. Suppress the turbulent viscosity in the porous region, if appropriate.12. Specify the rotation axis and/or zone motion, if relevant.Methods for determining the resistance coefficients and/or permeability are presented below. If you choose to use the power-law approximation of the porous-media momentum source term, you will enter thecoefficients and in Equation 7.19-3 instead of the resistance coefficients and flow direction.You will set all parameters for the porous medium inthe Fluid panel (Figure 7.19.1), which is opened from the Boundary Conditions panel (as described in Section 7.1.4).Figure 7.19.1: The Fluid Panel for a Porous Zone Defining the Porous ZoneAs mentioned in Section 7.1, a porous zone is modeled as a special type of fluid zone. To indicate that the fluid zone is a porous region, enablethe Porous Zone option in the Fluid panel. The panel will expand to show the porous media inputs (as shown in Figure7.19.1).Defining the Porous Velocity FormulationThe Solver panel contains a Porous Formulation region where you can instruct FLUENT to use either a superficial or physical velocity in the porous medium simulation. By default, the velocity is set to SuperficialVelocity. For details about using the Physical Velocity formulation, see Section 7.19.7.Defining the Fluid Passing Through the Porous MediumTo define the fluid that passes through the porous medium, select the appropriate fluid in the Material Name drop-down list in the Fluid panel. If you want to check or modify the properties of the selected material, you can click Edit... to open the Material panel; this panel contains just the properties of the selected material, not the full contents of thestandard Materials panel.If you are modeling species transport or multiphase flow,the Material Name list will not appear in the Fluid panel. Forspecies calculations, the mixture material for all fluid/porous zones will be the material you specified in the SpeciesModel panel. For multiphase flows, the materials are specified when you define the phases, as described in Section 23.10.3. Enabling Reactions in a Porous ZoneIf you are modeling species transport with reactions, you can enable reactions in a porous zone by turning on the Reaction option inthe Fluid panel and selecting a mechanism in the ReactionMechanism drop-down list.If your mechanism contains wall surface reactions, you will also need to specify a value for the Surface-to-Volume Ratio. Thisvalue is the surface area of the pore walls per unit volume ( ), and can be thought of as a measure of catalyst loading. With this value, FLUENT can calculate the total surface area on which the reaction takes place in each cell bymultiplying by the volume of the cell. See Section 14.1.4 for detailsabout defining reaction mechanisms. See Section 14.2for details about wall surface reactions.Including the Relative Velocity Resistance FormulationPrior to FLUENT 6.3, cases with moving reference frames used the absolute velocities in the source calculations for inertial and viscous resistance. This approach has been enhanced so that relative velocities are used for the porous source calculations (Section 7.19.2). Using the Relative Velocity Resistance Formulation option (turned on by default) allows you to better predict the source terms for cases involving moving meshes or moving reference frames (MRF). This option works well in cases withnon-moving and moving porous media. Note that FLUENT will use the appropriate velocities (relative or absolute), depending on your case setup. Defining the Viscous and Inertial Resistance CoefficientsThe viscous and inertial resistance coefficients are both defined in the same manner. The basic approach for defining the coefficients using a Cartesian coordinate system is to define one direction vector in 2D or two direction vectors in 3D, and then specify the viscous and/or inertial resistance coefficients in each direction. In 2D, the second direction, which is not explicitly defined, is normal to the plane defined by the specified direction vector and the direction vector. In 3D, the third direction is normal to the plane defined by the two specified direction vectors. For a 3D problem, the second direction must be normal to the first. If you fail to specify two normal directions, the solver will ensure that they are normal by ignoring any component of the second direction that is in the first direction. You should therefore be certain that the first direction is correctly specified. You can also define the viscous and/or inertial resistance coefficients in each direction using a user-defined function (UDF). The user-defined options become available in the corresponding drop-down list when the UDF has been created and loaded into FLUENT. Note that the coefficients defined in the UDF must utilize the DEFINE_PROFILE macro. For moreinformation on creating and using user-defined function, see the separate UDF Manual.If you are modeling axisymmetric swirling flows, you can specify an additional direction component for the viscous and/or inertial resistance coefficients. This direction component is always tangential to the other two specified directions. This option is available for both density-based and pressure-based solvers.In 3D, it is also possible to define the coefficients using a conical (or cylindrical) coordinate system, as described below.Note that the viscous and inertial resistance coefficients aregenerally based on the superficial velocity of the fluid in the porous media.The procedure for defining resistance coefficients is as follows:1. Define the direction vectors.To use a Cartesian coordinate system, simply specify the Direction-1 Vector and, for 3D, the Direction-2 Vector. The unspecifieddirection will be determined as described above. These directionvectors correspond to the principle axes of the porous media.For some problems in which the principal axes of the porous mediumare not aligned with the coordinate axes of the domain, you may notknow a priori the direction vectors of the porous medium. In suchcases, the plane tool in 3D (or the line tool in 2D) can help you todetermine these direction vectors.(a) "Snap'' the plane tool (or the line tool) onto the boundary of theporous region. (Follow the instructions inSection 27.6.1 or 27.5.1 for initializing the tool to a position on anexisting surface.)(b) Rotate the axes of the tool appropriately until they are alignedwith the porous medium.(c) Once the axes are aligned, click on the Update From PlaneTool or Update From Line Tool button inthe Fluid panel. FLUENT will automatically set the Direction-1Vector to the direction of the red arrow of the tool, and (in 3D)the Direction-2 Vector to the direction of the green arrow.To use a conical coordinate system (e.g., for an annular, conical filter element), follow the steps below. This option is available only in 3D cases.(a) Turn on the Conical option.(b) Specify the Cone Axis Vector and Point on Cone Axis. Thecone axis is specified as being in the direction of the Cone AxisVector (unit vector), and passing through the Point on Cone Axis.The cone axis may or may not pass through the origin of thecoordinate system.(c) Set the Cone Half Angle (the angle between the cone's axis andits surface, shown in Figure 7.19.2). To use a cylindrical coordinate system, set the Cone Half Angle to 0.Figure 7.19.2: Cone Half AngleFor some problems in which the axis of the conical filter element is not aligned with the coordinate axes of the domain, you may notknow a priori the direction vector of the cone axis and coordinates ofa point on the cone axis. In such cases, the plane tool can help you todetermine the cone axis vector and point coordinates. One method is as follows:(a) Select a boundary zone of the conical filter element that isnormal to the cone axis vector in the drop-down list next to the Snap to Zone button.(b) Click on the Snap to Zone button. FLUENT will automatically"snap'' the plane tool onto the boundary. It will also set the Cone Axis Vector and the Point on Cone Axis. (Note that you will still have to set the Cone Half Angle yourself.)An alternate method is as follows:(a) "Snap'' the plane tool onto the boundary of the porous region.(Follow the instructions in Section 27.6.1 for initializing the tool to a position on an existing surface.)(b) Rotate and translate the axes of the tool appropriately until thered arrow of the tool is pointing in the direction of the cone axisvector and the origin of the tool is on the cone axis.(c) Once the axes and origin of the tool are aligned, click onthe Update From Plane Tool button inthe Fluid panel. FLUENT will automatically set the Cone AxisVector and the Point on Cone Axis. (Note that you will still have toset the Cone Half Angle yourself.)2. Under Viscous Resistance, specify the viscous resistancecoefficient in each direction.Under Inertial Resistance, specify the inertial resistance coefficient in each direction. (You will need to scroll down with the scroll bar to view these inputs.)For porous media cases containing highly anisotropic inertial resistances, enable Alternative Formulation under Inertial Resistance.The Alternative Formulation option provides better stability to the calculation when your porous medium is anisotropic. The pressure loss through the medium depends on the magnitude of the velocity vector ofthe i th component in the medium. Using the formulation ofEquation 7.19-6 yields the expression below:(7.19-10) Whether or not you use the Alternative Formulation option depends on how well you can fit your experimentally determined pressure drop data to the FLUENT model. For example, if the flow through the medium is aligned with the grid in your FLUENT model, then it will not make a difference whether or not you use the formulation.For more infomation about simulations involving highly anisotropic porous media, see Section 7.19.8.Note that the alternative formulation is compatible only with the pressure-based solver.If you are using the Conical specification method, Direction-1 is the cone axis direction, Direction-2 is the normal to the cone surface (radial ( )direction for a cylinder), and Direction-3 is the circumferential ( ) direction.In 3D there are three possible categories of coefficients, and in 2D there are two:In the isotropic case, the resistance coefficients in all directions are the same (e.g., a sponge). For an isotropic case, you must explicitlyset the resistance coefficients in each direction to the same value.When (in 3D) the coefficients in two directions are the same and those in the third direction are different or (in 2D) the coefficients inthe two directions are different, you must be careful to specify thecoefficients properly for each direction. For example, if you had aporous region consisting of cylindrical straws with small holes inthem positioned parallel to the flow direction, the flow would passeasily through the straws, but the flow in the other two directions(through the small holes) would be very little. If you had a plane offlat plates perpendicular to the flow direction, the flow would notpass through them at all; it would instead move in the other twodirections.In 3D the third possible case is one in which all three coefficients are different. For example, if the porous region consisted of a plane ofirregularly-spaced objects (e.g., pins), the movement of flow between the blockages would be different in each direction. You wouldtherefore need to specify different coefficients in each direction. Methods for deriving viscous and inertial loss coefficients are described in the sections that follow.Deriving Porous Media Inputs Based on Superficial Velocity, Using a Known Pressure LossWhen you use the porous media model, you must keep in mind that the porous cells in FLUENT are 100% open, and that the values that you specify for and/or must be based on this assumption. Suppose, however, that you know how the pressure drop varies with the velocity through the actual device, which is only partially open to flow. The following exercise is designed to show you how to compute a valuefor which is appropriate for the FLUENT model.Consider a perforated plate which has 25% area open to flow. The pressure drop through the plate is known to be 0.5 times the dynamic head in the plate. The loss factor, , defined as(7.19-11)is therefore 0.5, based on the actual fluid velocity in the plate, i.e., the velocity through the 25% open area. To compute an appropriate valuefor , note that in the FLUENT model:1. The velocity through the perforated plate assumes that the plate is 100% open.2. The loss coefficient must be converted into dynamic head loss per unit length of the porous region.Noting item 1, the first step is to compute an adjusted loss factor, , which would be based on the velocity of a 100% open area:(7.19-12) or, noting that for the same flow rate, ,(7.19-13)The adjusted loss factor has a value of 8. Noting item 2, you must now convert this into a loss coefficient per unit thickness of the perforated plate. Assume that the plate has a thickness of 1.0 mm (10 m). The inertial loss factor would then be(7.19-14)Note that, for anisotropic media, this information must be computed for each of the 2 (or 3) coordinate directions.Using the Ergun Equation to Derive Porous Media Inputs for a Packed BedAs a second example, consider the modeling of a packed bed. In turbulent flows, packed beds are modeled using both a permeability and an inertial loss coefficient. One technique for deriving the appropriate constants involves the use of the Ergun equation [ 98], a semi-empirical correlation applicable over a wide range of Reynolds numbers and for many types of packing:(7.19-15)When modeling laminar flow through a packed bed, the second term in the above equation may be dropped, resulting in the Blake-Kozenyequation [ 98]:(7.19-16) In these equations, is the viscosity, is the mean particlediameter, is the bed depth, and is the void fraction, defined as the volume of voids divided by the volume of the packed bed region. Comparing Equations 7.19-4 and 7.19-6 with 7.19-15, the permeability and inertial loss coefficient in each component direction may be identified as(7.19-17) and(7.19-18) Using an Empirical Equation to Derive Porous Media Inputs for Turbulent Flow Through a Perforated PlateAs a third example we will take the equation of Van Winkle et al. [ 279, 339] and show how porous media inputs can be calculated for pressure loss through a perforated plate with square-edged holes.The expression, which is claimed by the authors to apply for turbulent flow through square-edged holes on an equilateral triangular spacing, is(7.19-19) where= mass flow rate through the plate= the free area or total area of the holes= the area of the plate (solid and holes)= a coefficient that has been tabulated for various Reynolds-numberrangesand for various= the ratio of hole diameter to plate thicknessfor and for the coefficient takes a value of approximately 0.98, where the Reynolds number is based on hole diameter and velocity in the holes.Rearranging Equation 7.19-19, making use of the relationship(7.19-20)and dividing by the plate thickness, , we obtain(7.19-21)where is the superficial velocity (not the velocity in the holes). Comparing with Equation 7.19-6 it is seen that, for the direction normal to the plate, the constant can be calculated from(7.19-22)Using Tabulated Data to Derive Porous Media Inputs for Laminar Flow Through a Fibrous MatConsider the problem of laminar flow through a mat or filter pad which is made up of randomly-oriented fibers of glass wool. As an alternative to the Blake-Kozeny equation (Equation 7.19-16) we might choose to employ tabulated experimental data. Such data is available for many types offiber [ 158].fraction of dimensionless permeability of glass woolwhere and is the fiber diameter. , for use inEquation 7.19-4, is easily computed for a given fiber diameter and volume fraction.Deriving the Porous Coefficients Based on Experimental Pressure and Velocity DataExperimental data that is available in the form of pressure drop against velocity through the porous component, can be extrapolated to determine the coefficients for the porous media. To effect a pressure drop across a porous medium of thickness, , the coefficients of the porous media are determined in the manner described below.If the experimental data is:then an curve can be plotted to create a trendline through these points yielding the following equationwhere is the pressure drop and is the velocity.Note that a simplified version of the momentum equation, relating the pressure drop to the source term, can be expressed as (7.19-24)or(7.19-25)Hence, comparing Equation 7.19-23 to Equation 7.19-2, yields the following curve coefficients:(7.19-26)with kg/m , and a porous media thickness, , assumed to be 1m in this example, the inertial resistance factor, .Likewise,with , the viscous inertial resistancefactor,. Note that this same technique can be applied to the porous jump boundary condition. Similar to the case of the porous media, you have to take into account the thickness of the medium . Yourexperimental data can be plotted in ancurve, yielding an equation that is equivalent to Equation 7.22-1. From there, you can determine the permeability and the pressure jumpcoefficient .Using the Power-Law ModelIf you choose to use the power-law approximation of the porous-media momentum source term (Equation 7.19-3), the only inputs required are the coefficients and . Under Power Law Model in the Fluid panel, enter the values for C0 and C1. Note that the power-law model can be used in conjunction with the Darcy and inertia models.C0 must be in SI units, consistent with the value of C1.Defining PorosityTo define the porosity, scroll down below the resistance inputs inthe Fluid panel, and set the Porosity under Fluid Porosity .You can also define the porosity using a user-defined function (UDF). The user-defined option becomes available in the corresponding drop-down list when the UDF has been created and loaded into FLUENT. Note that the porosity defined in the UDF must utilize the DEFINE_PROFILE macro. For more information on creating and using user-defined function, see the separate UDF Manual.The porosity, , is the volume fraction of fluid within the porous region (i.e., the open volume fraction of the medium). The porosity is used in the prediction of heat transfer in the medium, as described in Section 7.19.3, and in the time-derivative term in the scalar transport equations for unsteady flow, as described in Section 7.19.5. It also impacts the calculation of reaction source terms and body forces in the medium. These sources will be proportional to the fluid volume in the medium. If you want to represent the medium as completely open (no effect of the solid medium), you should set the porosity equal to 1.0 (the default). When the porosity is equal to 1.0, the solid portion of the medium will have no impact on heat transfer or thermal/reaction source terms in the medium.Defining the Porous MaterialIf you choose to model heat transfer in the porous medium, you must specify the material contained in the porous medium.To define the material contained in the porous medium, scroll down below the resistance inputs in the Fluid panel, and select the appropriate solid in the Solid Material Name drop-down list under Fluid Porosity. If you want to check or modify the properties of the selected material, you canclick Edit... to open the Material panel; this panel contains just the properties of the selected material, not the full contents of thestandard Materials panel. In the Material panel, you can define thenon-isotropic thermal conductivity of the porous material using auser-defined function (UDF). The user-defined option becomes available in the corresponding drop-down list when the UDF has been created and loaded into FLUENT. Note that the non-isotropic thermal conductivity defined in the UDF must utilize the DEFINE_PROPERTY macro. For more information on creating and using user-defined function, see the separate UDF Manual.Defining SourcesIf you want to include effects of the heat generated by the porous medium in the energy equation, enable the Source Terms option and set anon-zero Energy source. The solver will compute the heat generated by the porous region by multiplying this value by the total volume of the cells comprising the porous zone. You may also define sources of mass, momentum, turbulence, species, or other scalar quantities, as described in Section 7.28.Defining Fixed ValuesIf you want to fix the value of one or more variables in the fluid region of the zone, rather than computing them during the calculation, you can do so by enabling the Fixed Values option. See Section 7.27 for details. Suppressing the Turbulent Viscosity in the Porous RegionAs discussed in Section 7.19.4, turbulence will be computed in the porous region just as in the bulk fluid flow. If you are using one of the turbulence models (with the exception of the Large Eddy Simulation (LES) Model), and you want the turbulence generation to be zero in the porous zone, turn on the Laminar Zone option in the Fluid panel. Refer to Section 7.17.1 for more information about suppressing turbulence generation.Specifying the Rotation Axis and Defining Zone MotionInputs for the rotation axis and zone motion are the same as for a standard fluid zone. See Section 7.17.1 for details.。
多孔介质设置及建模实例

我做的多孔介质的简单例子(均为k-e RNG所做))模型仿真结果多孔介质定义的方法(2008-12-14 20:28:12)不知道怎的,这些日子都跟多孔介质干上了1. Define the porous zone.2. Define the porous velocity formulation. (optional)3. Identify the fluid material flowing through the porous medium.4. Enable reactions for the porous zone, if appropriate, and select the reaction mechanism.5. Set the viscous resistance coefficients and the inertial resistance coefficients , and define the direction vectors for which they apply. Alternatively, specify the coefficients for the power-law model.6. Specify the porosity of the porous medium.7. Select the material contained in the porous medium (required only for models that include heat transfer). Note that the specific heat capacity, , for the selected material in the porous zone can only be entered as a constant value.8. Set the volumetric heat generation rate in the solid portion of the porous medium (or any other sources, such as mass or momentum). (optional)9. Set any fixed values for solution variables in the fluid region (optional).10.Suppress the turbulent viscosity in the porous region, if appropriate.11. Specify the rotation axis and/or zone motion, if relevant.fluent中多孔介质porous media设置问题(2008-12-13 20:08:07)标签:杂谈分类:CFD计算流体力学经过痛苦的一段经历,终于将局部问题真相大白,为了使保位同仁不再经过我之痛苦,现在将本人多孔介质经验公布如下,希望各位能加精:1。
Fluent计算多孔介质模型资料
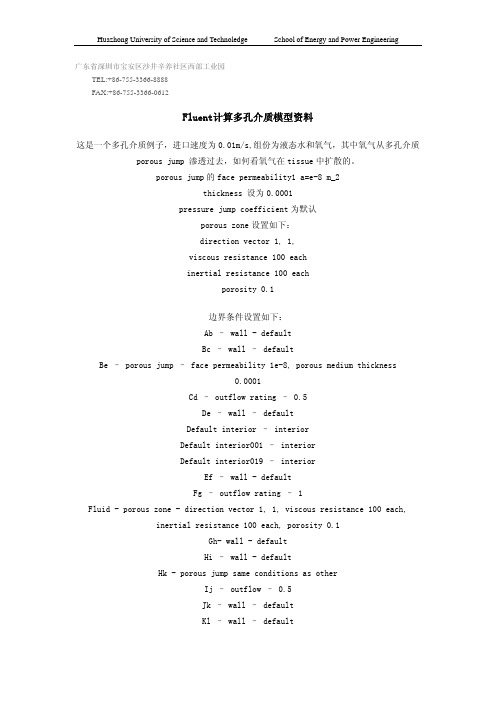
广东省深圳市宝安区沙井辛养社区西部工业园 TEL:+86-755-3366-8888 FAX:+86-755-3366-0612Fluent计算多孔介质模型资料这是一个多孔介质例子,进口速度为0.01m/s,组份为液态水和氧气,其中氧气从多孔介质porous jump 渗透过去,如何看氧气在tissue中扩散的。
porous jump的face permeability1 a=e-8 m_2thickness 设为0.0001pressure jump coefficient为默认porous zone设置如下:direction vector 1, 1,viscous resistance 100 eachinertial resistance 100 eachporosity 0.1边界条件设置如下:Ab – wall - defaultBc – wall – defaultBe – porous jump – face permeability 1e-8, porous medium thickness0.0001Cd – outflow rating – 0.5De – wall – defaultDefault interior – interiorDefault interior001 – interiorDefault interior019 – interiorEf – wall - defaultFg – outflow rating – 1Fluid - porous zone - direction vector 1, 1, viscous resistance 100 each,inertial resistance 100 each, porosity 0.1Gh- wall - defaultHi – wall - defaultHk - porous jump same conditions as otherIj – outflow – 0.5Jk – wall – defaultKl – wall – defaultLa – velocity inlet – 0.01 m/s, temperature 300K, 0.5 mass fraction O2 Lfluid – porous zone - direction vector 1, 1, viscous resistance 100 each,inertial resistance 100 each, porosity 0.1Pipefluid – fluid – default (no porous zone)Models – species transport – water and oxygen mixtureVariations – different boundary conditions at top and bottom (outflow, wall ect)注意,其中porous zone在gambit中设置为fluid,在fluent中设置为porous zone边界条件设置如下:Ab – wall - defaultBc – wall – defaultBe – porous jump – face permeability 1e-8, porous medium thickness0.0001Cd – outflow rating – 0.5De – wall – defaultDefault interior – interiorDefault interior001 – interiorDefault interior019 – interiorEf – wall - defaultFg – outflow rating – 1Fluid - porous zone - direction vector 1, 1, viscous resistance 100 each,inertial resistance 100 each, porosity 0.1Gh- wall - defaultHi – wall - defaultHk - porous jump same conditions as otherIj – outflow – 0.5Jk – wall – defaultKl – wall – defaultLa – velocity inlet – 0.01 m/s, temperature 300K, 0.5 mass fraction O2 Lfluid – porous zone - direction vector 1, 1, viscous resistance 100 each,inertial resistance 100 each, porosity 0.1Pipefluid – fluid – default (no porous zone)Models – species transport – water and oxygen mixtureVariations – different boundary conditions at top and bottom (outflow, wall ect) 注意,其中porous zone在gambit中设置为fluid,在fluent中设置为porous zone。
fluent中多孔介质设置问题和算例
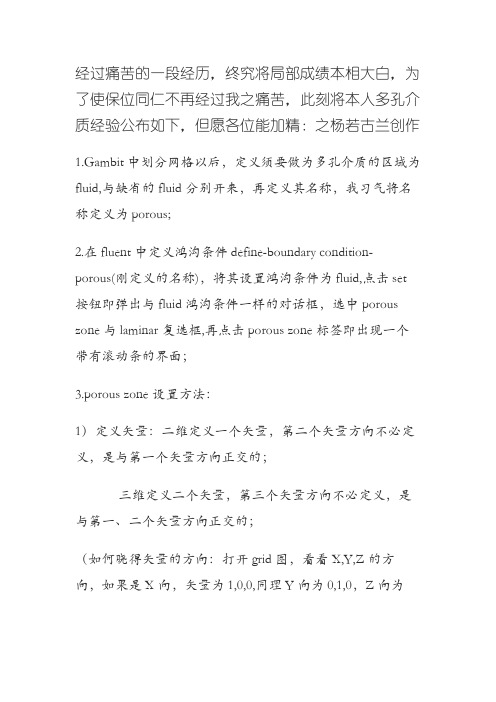
经过痛苦的一段经历,终究将局部成绩本相大白,为了使保位同仁不再经过我之痛苦,此刻将本人多孔介质经验公布如下,但愿各位能加精:之杨若古兰创作1.Gambit中划分网格以后,定义须要做为多孔介质的区域为fluid,与缺省的fluid分别开来,再定义其名称,我习气将名称定义为porous;2.在fluent中定义鸿沟条件define-boundary condition-porous(刚定义的名称),将其设置鸿沟条件为fluid,点击set 按钮即弹出与fluid鸿沟条件一样的对话框,选中porous zone与laminar复选框,再点击porous zone标签即出现一个带有滚动条的界面;3.porous zone设置方法:1)定义矢量:二维定义一个矢量,第二个矢量方向不必定义,是与第一个矢量方向正交的;三维定义二个矢量,第三个矢量方向不必定义,是与第一、二个矢量方向正交的;(如何晓得矢量的方向:打开grid图,看看X,Y,Z的方向,如果是X向,矢量为1,0,0,同理Y向为0,1,0,Z向为0,0,1,如果所须要的方向与坐标轴正向相反,则定义矢量为负)圆锥坐标与球坐标请参考fluent帮忙.2)定义粘性阻力1/a与内部阻力C2:请参看本人上一篇博文“终究搞清fluent中多孔粘性阻力与内部阻力的计算方法”,此处不赘述;3)如果了定义粘性阻力1/a与内部阻力C2,就不必定义C1与C0,由于这是两种分歧的定义方法,C1与C0只在幂率模型中出现,该处坚持默认就行了;4)定义孔隙率porousity,默认值1暗示全开放,此值按实验测值填写即可.完了,其他设置与普通k-e或RSM不异.总结一下,与君共享!Tutorial 7. Modeling Flow Through Porous Media IntroductionMany industrial applications involve the modeling of flow through porous media, suchas filters, catalyst beds, and packing. This tutorial illustrates how to set up and solve aproblem involving gas flow through porous media.The industrial problem solved here involves gas flow through acatalytic converter. Catalyticconverters are commonly used to purify emissions from gasoline and diesel enginesby converting environmentally hazardous exhaust emissions to acceptable substances.Examples of such emissions include carbon monoxide (CO), nitrogen oxides (NOx), andunburned hydrocarbon fuels. These exhaust gas emissions are forced through a substrate,which is a ceramic structure coated with a metal catalyst such as platinum or palladium.The nature of the exhaust gas flow is a very important factor in determining the performanceof the catalytic converter. Of particular importance is the pressure gradientand velocity distribution through the substrate. Hence CFD analysis is used to designefficient catalytic converters: by modeling the exhaust gas flow, the pressure drop andthe uniformity of flow through the substrate can be determined. In this tutorial, FLUENTis used to model the flow of nitrogen gas through a catalytic converter geometry, so thatthe flow field structure may be analyzed.This tutorial demonstrates how to do the following:_ Set up a porous zone for the substrate with appropriate resistances._ Calculate a solution for gas flow through the catalytic converterusing the pressurebasedsolver._ Plot pressure and velocity distribution on specified planes of the geometry._ Determine the pressure drop through the substrate and the degree of non-uniformityof flow through cross sections of the geometry using X-Y plots and numerical reports.Problem DescriptionThe catalytic converter modeled here is shown in Figure 7.1. The nitrogen flows inthrough the inlet with a uniform velocity of 22.6 m/s, passes through a ceramic monolithsubstrate with square shaped channels, and then exits through the outlet.While the flow in the inlet and outlet sections is turbulent, the flow through the substrateis laminar and is characterized by inertial and viscous loss coefficients in the flow (X)direction. The substrate is impermeable in other directions, which is modeled using losscoefficients whose values are three orders of magnitude higher than in the X direction.Setup and SolutionStep 1: Grid1. Read the mesh file (catalytic converter.msh).File /Read /Case...2. Check the grid.Grid /CheckFLUENT will perform various checks on the mesh and report the progress in theconsole. Make sure that the minimum volume reported is a positive number.3. Scale the grid.Grid!Scale...(a) Select mm from the Grid Was Created In drop-down list.(b) Click the Change Length Units button.All dimensions will now be shown in millimeters.(c) Click Scale and close the Scale Grid panel.4. Display the mesh.Display /Grid...(a) Make sure that inlet, outlet, substrate-wall, and wall are selected in the Surfacesselection list.(b) Click Display.(c) Rotate the view and zoom in to get the display shown in Figure7.2.(d) Close the Grid Display panel.The hex mesh on the geometry contains a total of 34,580 cells.Step 2: Modelsfine /Models /Solver...2. Select the standard k-εfine/ Models /Viscous...Step 3: Materials1. Add nitrogen to the list of flfine /Materials...(a) Click the Fluent Database... button to open the Fluent Database Materialspanel.i. Select nitrogen (n2) from the list of Fluent Fluid Materials.ii. Click Copy to copy the information for nitrogen to your list of fluid materials.iii. Close the Fluent Database Materials panel.(b) Close the Materials panel.Step 4: Boundary Conditions.Define /Boundary Conditions...1. Set the boundary conditions for the fluid (fluid).(a) Select nitrogen from the Material Name drop-down list.(b) Click OK to close the Fluid panel.2. Set the boundary conditions for the substrate (substrate).(a) Select nitrogen from the Material Name drop-down list.(b) Enable the Porous Zone option to activate the porous zone model.(c) Enable the Laminar Zone option to solve the flow in the porous zone withoutturbulence.(d) Click the Porous Zone tab.i. Make sure that the principal direction vectors are set as shown in e the scroll bar to access the fields that are not initially visible in thepanel.ii. Enter the values in Table 7.2 for the Viscous Resistance and Inertial Resistance.Scroll down to access the fields that are not initially visible in the panel.(e) Click OK to close the Fluid panel.3. Set the velocity and turbulence boundary conditions at the inlet (inlet).(a) Enter 22.6 m/s for the Velocity Magnitude.(b) Select Intensity and Hydraulic Diameter from the Specification Method dropdownlist in the Turbulence group box.(c) Retain the default value of 10% for the Turbulent Intensity.(d) Enter 42 mm for the Hydraulic Diameter.(e) Click OK to close the Velocity Inlet panel.4. Set the boundary conditions at the outlet (outlet).(a) Retain the default setting of 0 for Gauge Pressure.(b) Select Intensity and Hydraulic Diameter from the Specification Method dropdownlist in the Turbulence group box.(c) Enter 5% for the Backflow Turbulent Intensity.(d) Enter 42 mm for the Backflow Hydraulic Diameter.(e) Click OK to close the Pressure Outlet panel.5. Retain the default boundary conditions for the walls (substrate-wall and wall) andclose the Boundary Conditions panel.Step 5: Solution1. Set the solution parameters.Solve /Controls /Solution...(a) Retain the default settings for Under-Relaxation Factors.(b) Select Second Order Upwind from the Momentum drop-down list in the Discretizationgroup box.(c) Click OK to close the Solution Controls panel./Monitors /Residual...(a) Enable Plot in the Options group box.(b) Click OK to close the Residual Monitors panel.3. Enable the plotting of the mass flow rate at the outlet.Solve / Monitors /Surface...(a) Set the Surface Monitors to 1.(b) Enable the Plot and Write options for monitor-1, and click the Define... buttonto open the Define Surface Monitor panel.i. Select Mass Flow Rate from the Report Type drop-down list. ii. Select outlet from the Surfaces selection list.iii. Click OK to close the Define Surface Monitors panel.(c) Click OK to close the Surface Monitors panel.4. Initialize the solution from the inlet.Solve /Initialize /Initialize...(a) Select inlet from the Compute From drop-down list.(b) Click Init and close the Solution Initialization panel.5. Save the case file (catalytic converter.cas).File /Write /Case...6. Run the calculation by requesting 100 iterations.Solve /Iterate...(a) Enter 100 for the Number of Iterations.(b) Click Iterate.The FLUENT calculation will converge in approximately 70 iterations. By thispoint the mass flow rate monitor has attended out, as seen in Figure 7.3.(c) Close the Iterate panel.7. Save the case and data files (catalytic converter.cas and catalytic converter.dat).File /Write /Case & Data...Note: If you choose a file name that already exists in the current folder, FLUENTwill prompt you for confirmation to overwrite the file.Step 6: Post-processing1. Create a surface passing through the centerline for post-processing purposes.Surface/Iso-Surface...(a) Select Grid... and Y-Coordinate from the Surface of Constant drop-down lists.(b) Click Compute to calculate the Min and Max values.(c) Retain the default value of 0 for the Iso-Values.(d) Enter y=0 for the New Surface Name.(e) Click Create.2. Create cross-sectional surfaces at locations on either side of the substrate, as wellas at its center.Surface /Iso-Surface...(a) Select Grid... and X-Coordinate from the Surface of Constant drop-down lists.(b) Click Compute to calculate the Min and Max values.(c) Enter 95 for Iso-Values.(d) Enter x=95 for the New Surface Name.(e) Click Create.(f) In a similar manner, create surfaces named x=130 and x=165 with Iso-Valuesof 130 and 165, respectively. Close the Iso-Surface panel after all the surfaceshave been created.3. Create a line surface for the centerline of the porous media. Surface /Line/Rake...(a) Enter the coordinates of the line under End Points, using the starting coordinateof (95, 0, 0) and an ending coordinate of (165, 0,0), as shown.(b) Enter porous-cl for the New Surface Name.(c) Click Create to create the surface.(d) Close the Line/Rake Surface panel.4. Display the two wall zones (substrate-wall and wall).Display/Grid...(a) Disable the Edges option.(b) Enable the Faces option.(c) Deselect inlet and outlet in the list under Surfaces, and make sure that onlysubstrate-wall and wall are selected.(d) Click Display and close the Grid Display panel.(e) Rotate the view and zoom so that the display is similar to Figure 7.2.5. Set the lighting for the display.Display /Options...(a) Enable the Lights On option in the Lighting Attributes group box.(b) Retain the default selection of Gourand in the Lighting drop-down list.(c) Click Apply and close the Display Options panel.6. Set the transparency parameter for the wall zones (substrate-wall and wall).Display/Scene...(a) Select substrate-wall and wall in the Names selection list.(b) Click the Display... button under Geometry Attributes to openthe DisplayProperties panel.i. Set the Transparency slider to 70.ii. Click Apply and close the Display Properties panel.(c) Click Apply and then close the Scene Description panel.7. Display velocity vectors on the y=0 surface.Display /Vectors...(a) Enable the Draw Grid option.The Grid Display panel will open.i. Make sure that substrate-wall and wall are selected in the list under Surfaces.ii. Click Display and close the Display Grid panel.(b) Enter 5 for the Scale.(c) Set Skip to 1.(d) Select y=0 from the Surfaces selection list.(e) Click Display and close the Vectors panel.The flow pattern shows that the flow enters the catalytic converter as a jet, withrecirculation on either side of the jet. As it passes through the porous substrate, itdecelerates and straightens out, and exhibits a more uniform velocity distribution.This allows the metal catalyst present in the substrate to be more effective.Figure 7.4: Velocity Vectors on the y=0 Plane8. Display filled contours of static pressure on the y=0 plane. Display /Contours...(a) Enable the Filled option.(b) Enable the Draw Grid option to open the Display Grid panel.i. Make sure that substrate-wall and wall are selected in the list under Surfaces.ii. Click Display and close the Display Grid panel.(c) Make sure that Pressure... and Static Pressure are selected from the Contoursof drop-down lists.(d) Select y=0 from the Surfaces selection list.(e) Click Display and close the Contours panel.Figure 7.5: Contours of the Static Pressure on the y=0 planeThe pressure changes rapidly in the middle section, where the fluid velocity changesas it passes through the porous substrate. The pressure drop can be high, due to theinertial and viscous resistance of the porous media. Determining this pressure dropis a goal of CFD analysis. In the next step, you will learn how to plot the pressuredrop along the centerline of the substrate.9. Plot the static pressure across the line surface porous-cl.Plot /XY Plot...(a) Make sure that the Pressure... and Static Pressure are selectedfrom the Y AxisFunction drop-down lists.(b) Select porous-cl from the Surfaces selection list.(c) Click Plot and close the Solution XY Plot panel.Figure 7.6: Plot of the Static Pressure on the porous-cl Line SurfaceIn Figure 7.6, the pressure drop across the porous substrate can be seen to beroughly 300 Pa.10. Display filled contours of the velocity in the X direction on the x=95, x=130 andx=165 surfaces.Display /Contours...(a) Disable the Global Range option.(b) Select Velocity... and X Velocity from the Contours of drop-down lists.(c) Select x=130, x=165, and x=95 from the Surfaces selection list, and deselecty=0.(d) Click Display and close the Contours panel.The velocity profile becomes more uniform as the fluid passes through the porousmedia. The velocity is very high at the center (the area in red) just before thenitrogen enters the substrate and then decreases as it passes through and exits thesubstrate. The area in green, which corresponds to a moderate velocity, increasesin extent.Figure 7.7: Contours of the X Velocity on the x=95,x=130, and x=165 Surfaces11. Use numerical reports to determine the average, minimum, and maximum of thevelocity distribution before and after the porous substrate.Report /Surface Integrals...(a) Select Mass-Weighted Average from the Report Type drop-down list.(b) Select Velocity and X Velocity from the Field Variable drop-down lists.(c) Select x=165 and x=95 from the Surfaces selection list.(d) Click Compute.(e) Select Facet Minimum from the Report Type drop-down list and click Computeagain.(f) Select Facet Maximum from the Report Type drop-down list and click Computeagain.(g) Close the Surface Integrals panel.The numerical report of average, maximum and minimum velocity can be seen inthe main FLUENT console, as shown in the following example:The spread between the average, maximum, and minimum values for X velocitygives the degree to which the velocity distribution isnon-uniform. You can also usethese numbers to calculate the velocity ratio (i.e., the maximum velocity divided bythe mean velocity) and the space velocity (i.e., the product of the mean velocity andthe substrate length).Custom field functions and UDFs can be also used to calculate more complex measuresof non-uniformity, such as the standard deviation and the gamma uniformityindex.SummaryIn this tutorial, you learned how to set up and solve a problem involving gas flow throughporous media in FLUENT. You also learned how to perform appropriate post-processingto investigate the flow field, determine the pressure drop across the porous media andnon-uniformity of the velocity distribution as the fluid goes through the porous media.Further ImprovementsThis tutorial guides you through the steps to reach an initial solution. You may be ableto obtain a more accurate solution by using an appropriate higher-order discretizationscheme and by adapting the grid. Grid adaption can also ensure that the solution isindependent of the grid. These steps are demonstrated in Tutorial 1.。
多孔介质模型的参数设置

多孔介质模型的参数设置
多孔介质模型中包含的参数有很多,具体参数设置需要根据具体情况而定。
下面列举一些可能需要设置的参数:
1. 孔隙率:表示多孔介质中孔隙体积与总体积的比值,通常用百分数表示。
2. 孔径分布:表示多孔介质中孔隙大小的分布情况,在不同尺度上都有可能存在不同的孔径分布。
3. 渗透率:表示多孔介质对于流体的流动性能,通常用流量、压差等指标来描述。
4. 孔隙形状:表示多孔介质中各个孔隙的形状,包括球形、椭圆形、不规则形等。
5. 渗流方向:表示多孔介质中流体的主要流动方向,有可能是单向、双向或多向的。
6. 孔隙壁面性质:表示多孔介质中孔隙壁面的材料性质,包括表面形状、分子亲和力等。
7. 多相流参数:如果多孔介质中存在多种不同的流体,则需要考虑流体之间的相互作用。
8. 温度与压力:多孔介质中的温度与压力将会对流体的流动性能产生影响。
这些参数的设置将直接影响多孔介质模型的精度与可靠性,因此需要仔细选择并进行有效的设置。
fluent多孔介质模型课件

多孔介质是由多相物质所占据的共同空间,也是多相物质共存 的一种组合体,没有固体骨架的那部分空间叫做孔隙,由液体或气 体或气液两相共同占有,相对于其中一相来说,其他相都弥散在其 中,并以固相为固体骨架,构成空隙空间的某些空洞相互连通。
多孔介质模型可以应用于很多问题,如通过充满介质的流动、 通过过滤纸、穿孔圆盘、流量分配器以及管道堆的流动。
多孔介质的Darcy定律:通过多孔介质的层流流动中,压降和 速度成比例,常数C2 可以考虑为零。忽略对流加速以及扩散。
△Px, △Py, △Pz分别是x,y,z三个方向的压力降。△nx, △ny, △nz分 别是多孔介质在x,y,z三个方向的真实厚度。
多孔介质的源项
多孔中的惯性损失:在高速流动中,多孔介质动量源项中的常 数C2 可以对惯性损失作出修正。 C2可以看成沿着流动方向每一单 位长度的损失系数,因此允许压降指定为动压头的函数。
表中
,a为纤维直径。α的含义与darcy定律的方程中相同,
对于给定纤维直径和体积比的多孔介质是容易求出的。
用压强和速度的实验数据计算多孔介质系数
在已知多孔介质上的速度与压强降的试验数据时,可以通过插值求 出多孔介质上系数。
速度(m/s) 20.0 50.0 80.0 110.0
压强降(Pa) 78.0 487.0
1432.0 2964.0
采用上表的数据可以拟合出一条“速度-压强降”曲线,其方程 为:
对比上述两式便可求出粘性阻力系数和惯性阻力系数。
实例计算
WALL
进
出
口
口
symmetry
Porous one
Porous three Porous two
上图中的计算区域尺寸如下: 总的计算域:长1m,宽0.1m; Porous two:长0.57m,宽0.02m; (处于正中间) Porous one:宽0.03m,高0.06m; Porous three:宽0.03m,高0.06m;
- 1、下载文档前请自行甄别文档内容的完整性,平台不提供额外的编辑、内容补充、找答案等附加服务。
- 2、"仅部分预览"的文档,不可在线预览部分如存在完整性等问题,可反馈申请退款(可完整预览的文档不适用该条件!)。
- 3、如文档侵犯您的权益,请联系客服反馈,我们会尽快为您处理(人工客服工作时间:9:00-18:30)。
我做的多孔介质的简单例子(均为k-e RNG所做))模型
仿真结果
多孔介质定义的方法(2008-12-14 20:28:12)
不知道怎的,这些日子都跟多孔介质干上了
1. Define the porous zone.
2. Define the porous velocity formulation. (optional)
3. Identify the fluid material flowing through the porous medium.
4. Enable reactions for the porous zone, if appropriate, and select the reaction mechanism.
5. Set the viscous resistance coefficients and the inertial resistance coefficients , and define the direction vectors for which they apply. Alternatively, specify the coefficients for the power-law model.
6. Specify the porosity of the porous medium.
7. Select the material contained in the porous medium (required only for models that include heat transfer). Note that the specific heat capacity, , for the selected material in the porous zone can only be entered as a constant value.
8. Set the volumetric heat generation rate in the solid portion of the porous medium (or any other sources, such as mass or momentum). (optional)
9. Set any fixed values for solution variables in the fluid region (optional).
10.Suppress the turbulent viscosity in the porous region, if appropriate.
11. Specify the rotation axis and/or zone motion, if relevant.
fluent中多孔介质porous media设置问题(2008-12-13 20:08:07)
标签:杂谈分类:CFD计算流体力学
经过痛苦的一段经历,终于将局部问题真相大白,为了使保位同仁不再经过我之痛苦,现在将本人多孔介质经验公布如下,希望各位能加精:
1。
Gambit中划分网格之后,定义需要做为多孔介质的区域为fluid,与缺省的fluid分别开来,再定义其名称,我习惯将名称定义为porous;
2。
在fluent中定义边界条件define-boundary condition-porous(刚定义的名称),将其设置边界条件为fluid,点击set按钮即弹出与fluid边界条件一样的对话框,选中porous zone与laminar复选框,再点击porous zone标签即出现一个带有滚动条的界面;
3。
porous zone设置方法:
1)定义矢量:二维定义一个矢量,第二个矢量方向不用定义,是与第一个矢量方向正交的;
三维定义二个矢量,第三个矢量方向不用定义,是与第一、二个矢量方向正交的;
(如何知道矢量的方向:打开grid图,看看X,Y,Z的方向,如果是X向,矢量为1,0,0,同理Y向为0,1,0,Z向为0,0,1,如果所需要的方向与坐标轴正向相反,则定义矢量为负)
圆锥坐标与球坐标请参考fluent帮助。
2)定义粘性阻力1/a与内部阻力C2:请参看本人上一篇博文“终于搞清fluent中多孔粘性阻力与内部阻力的计算方法”,此处不赘述;
3)如果了定义粘性阻力1/a与内部阻力C2,就不用定义C1与C0,因为这是两种不同的定义方法,C1与C0只在幂率模型中出现,该处保持默认就行了;
4)定义孔隙率porousity,默认值1表示全开放,此值按实验测值填写即可。
完了,其他设置与普通k-e或RSM相同。
总结一下,与君共享!
终于搞清fluent中多孔粘性阻力与内部阻力的计算方法
Experimental data that is available in the form of pressure drop against velocity through
the porous component, can be extrapolated to determine the coecients for the porous media. To e ect a pressure drop across a porous medium of thickness, n, the coecients of the porous media are determined in the manner described below.If the experimental data is:
Velocity Pressure Drop
(m/s) (Pa)
20.0 78.0
50.0 487.0
80.0 1432.0
110.0 2964.0。