专业仿真训练(合成氨合成工段)报告
氨合成的实验报告

一、实验目的1. 了解氨合成的原理和方法;2. 掌握合成氨的基本操作;3. 通过实验,了解氨合成过程中的影响因素。
二、实验原理氨合成反应是一种可逆反应,其化学方程式为:N2(g) + 3H2(g) ⇌ 2NH3(g) + Q在一定温度、压力和催化剂的作用下,氮气和氢气反应生成氨气。
本实验采用铁基催化剂,在高温、高压条件下进行氨合成。
三、实验仪器与试剂1. 仪器:合成氨装置、氮气钢瓶、氢气钢瓶、温度计、压力计、流量计、加热器、冷凝器、接收瓶、试管、酒精灯等。
2. 试剂:氮气、氢气、铁基催化剂、无水氯化钙、硫酸、蒸馏水等。
四、实验步骤1. 检查合成氨装置,确保各部件连接牢固,无泄漏。
2. 将铁基催化剂放入反应器中,加入适量的无水氯化钙作为干燥剂。
3. 打开氮气钢瓶和氢气钢瓶,调节流量计,使氮气和氢气的流量比为1:3。
4. 将氮气和氢气分别通过无水氯化钙干燥剂,进入反应器。
5. 打开加热器,加热反应器至实验要求的温度(一般控制在400-500℃)。
6. 观察反应器内压力变化,当压力达到实验要求的压力(一般控制在10-20MPa)时,开始计时。
7. 在反应过程中,每隔一定时间,从接收瓶中取样,用硫酸酸化,观察氨气是否生成。
8. 实验结束后,关闭加热器,待反应器冷却至室温。
9. 收集剩余的氮气和氢气,测定其含量。
五、实验结果与分析1. 实验过程中,随着反应进行,反应器内压力逐渐升高,说明氨气生成。
2. 在实验过程中,观察到氨气生成,使溶液呈碱性,证明氨气已生成。
3. 实验结束后,剩余的氮气和氢气含量测定结果显示,氮气和氢气基本反应完全。
4. 实验结果与理论计算结果基本相符,说明实验操作正确,氨合成反应进行顺利。
六、实验讨论1. 实验过程中,反应器内压力变化对氨合成反应的影响较大。
压力越高,氨合成反应速率越快,氨气产量越高。
2. 温度对氨合成反应的影响也较大。
在一定温度范围内,温度越高,氨合成反应速率越快。
合成氨仿真实习报告
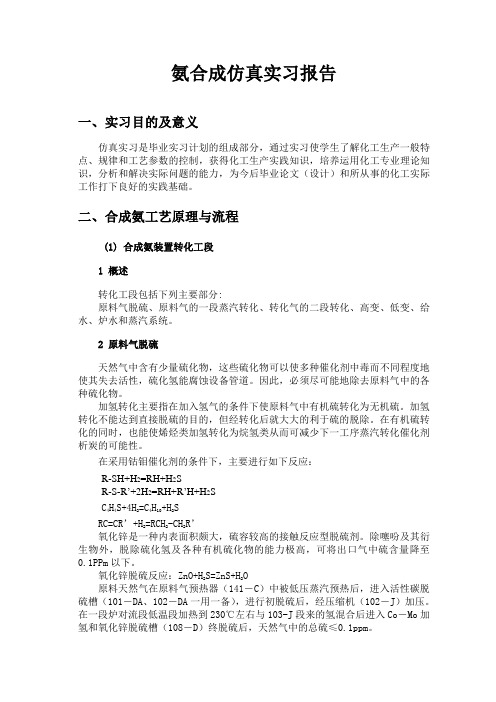
氨合成仿真实习报告一、实习目的及意义仿真实习是毕业实习计划的组成部分,通过实习使学生了解化工生产一般特点、规律和工艺参数的控制,获得化工生产实践知识,培养运用化工专业理论知识,分析和解决实际问题的能力,为今后毕业论文(设计)和所从事的化工实际工作打下良好的实践基础。
二、合成氨工艺原理与流程(1) 合成氨装置转化工段1 概述转化工段包括下列主要部分:原料气脱硫、原料气的一段蒸汽转化、转化气的二段转化、高变、低变、给水、炉水和蒸汽系统。
2 原料气脱硫天然气中含有少量硫化物,这些硫化物可以使多种催化剂中毒而不同程度地使其失去活性,硫化氢能腐蚀设备管道。
因此,必须尽可能地除去原料气中的各种硫化物。
加氢转化主要指在加入氢气的条件下使原料气中有机硫转化为无机硫。
加氢转化不能达到直接脱硫的目的,但经转化后就大大的利于硫的脱除。
在有机硫转化的同时,也能使烯烃类加氢转化为烷氢类从而可减少下一工序蒸汽转化催化剂析炭的可能性。
在采用钴钼催化剂的条件下,主要进行如下反应:R-SH+H2=RH+H2SR-S-R’+2H2=RH+R’H+H2SC 4H4S+4H2=C4H10+H2SRC=CR’+H2=RCH2-CH2R’氧化锌是一种内表面积颇大,硫容较高的接触反应型脱硫剂。
除噻吩及其衍生物外,脱除硫化氢及各种有机硫化物的能力极高,可将出口气中硫含量降至0.1PPm以下。
氧化锌脱硫反应:ZnO+H2S=ZnS+H2O原料天然气在原料气预热器(141-C)中被低压蒸汽预热后,进入活性碳脱硫槽(101-DA、102-DA一用一备),进行初脱硫后,经压缩机(102-J)加压。
在一段炉对流段低温段加热到230℃左右与103-J段来的氢混合后进入Co-Mo加氢和氧化锌脱硫槽(108-D)终脱硫后,天然气中的总硫≤0.1ppm。
3 原料气的一段蒸汽转化经脱硫后的原料气的总硫含量降至0.1PPm以下,与水蒸汽混合后进行转化反应:CH4 + H2O =CO + 3H2C n H2n+2 + nH2O =nCO + (2n+1)H2由于转化反应是吸热反应,在高温条件下有利于反应平衡及反应速度。
合成氨工艺的实训报告
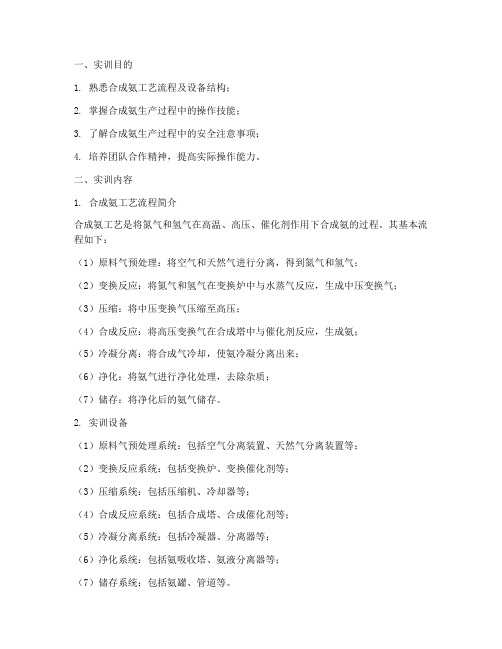
一、实训目的1. 熟悉合成氨工艺流程及设备结构;2. 掌握合成氨生产过程中的操作技能;3. 了解合成氨生产过程中的安全注意事项;4. 培养团队合作精神,提高实际操作能力。
二、实训内容1. 合成氨工艺流程简介合成氨工艺是将氮气和氢气在高温、高压、催化剂作用下合成氨的过程。
其基本流程如下:(1)原料气预处理:将空气和天然气进行分离,得到氮气和氢气;(2)变换反应:将氮气和氢气在变换炉中与水蒸气反应,生成中压变换气;(3)压缩:将中压变换气压缩至高压;(4)合成反应:将高压变换气在合成塔中与催化剂反应,生成氨;(5)冷凝分离:将合成气冷却,使氨冷凝分离出来;(6)净化:将氨气进行净化处理,去除杂质;(7)储存:将净化后的氨气储存。
2. 实训设备(1)原料气预处理系统:包括空气分离装置、天然气分离装置等;(2)变换反应系统:包括变换炉、变换催化剂等;(3)压缩系统:包括压缩机、冷却器等;(4)合成反应系统:包括合成塔、合成催化剂等;(5)冷凝分离系统:包括冷凝器、分离器等;(6)净化系统:包括氨吸收塔、氨液分离器等;(7)储存系统:包括氨罐、管道等。
3. 实训操作(1)原料气预处理:观察空气分离装置、天然气分离装置的工作状态,了解其工作原理;(2)变换反应:观察变换炉、变换催化剂的工作状态,了解变换反应过程;(3)压缩:观察压缩机、冷却器的工作状态,了解压缩过程;(4)合成反应:观察合成塔、合成催化剂的工作状态,了解合成反应过程;(5)冷凝分离:观察冷凝器、分离器的工作状态,了解冷凝分离过程;(6)净化:观察氨吸收塔、氨液分离器的工作状态,了解净化过程;(7)储存:观察氨罐、管道的工作状态,了解储存过程。
4. 实训安全注意事项(1)严格遵守操作规程,确保操作安全;(2)佩戴好劳动保护用品,如安全帽、防尘口罩、防护眼镜等;(3)注意设备运行状态,发现问题及时上报;(4)保持现场清洁,防止事故发生;(5)注意个人卫生,防止职业病。
合成氨仿真实习心得
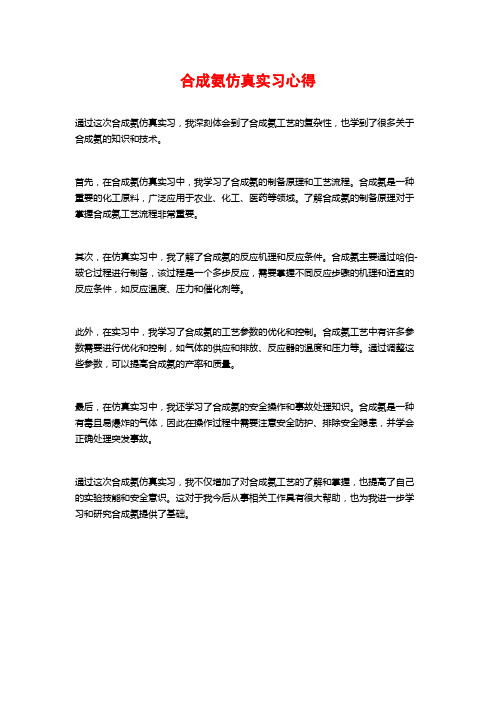
合成氨仿真实习心得
通过这次合成氨仿真实习,我深刻体会到了合成氨工艺的复杂性,也学到了很多关于合成氨的知识和技术。
首先,在合成氨仿真实习中,我学习了合成氨的制备原理和工艺流程。
合成氨是一种重要的化工原料,广泛应用于农业、化工、医药等领域。
了解合成氨的制备原理对于掌握合成氨工艺流程非常重要。
其次,在仿真实习中,我了解了合成氨的反应机理和反应条件。
合成氨主要通过哈伯-玻仑过程进行制备,该过程是一个多步反应,需要掌握不同反应步骤的机理和适宜的反应条件,如反应温度、压力和催化剂等。
此外,在实习中,我学习了合成氨的工艺参数的优化和控制。
合成氨工艺中有许多参数需要进行优化和控制,如气体的供应和排放、反应器的温度和压力等。
通过调整这些参数,可以提高合成氨的产率和质量。
最后,在仿真实习中,我还学习了合成氨的安全操作和事故处理知识。
合成氨是一种有毒且易爆炸的气体,因此在操作过程中需要注意安全防护、排除安全隐患,并学会正确处理突发事故。
通过这次合成氨仿真实习,我不仅增加了对合成氨工艺的了解和掌握,也提高了自己的实验技能和安全意识。
这对于我今后从事相关工作具有很大帮助,也为我进一步学习和研究合成氨提供了基础。
煤制合成氨仿真实验报告
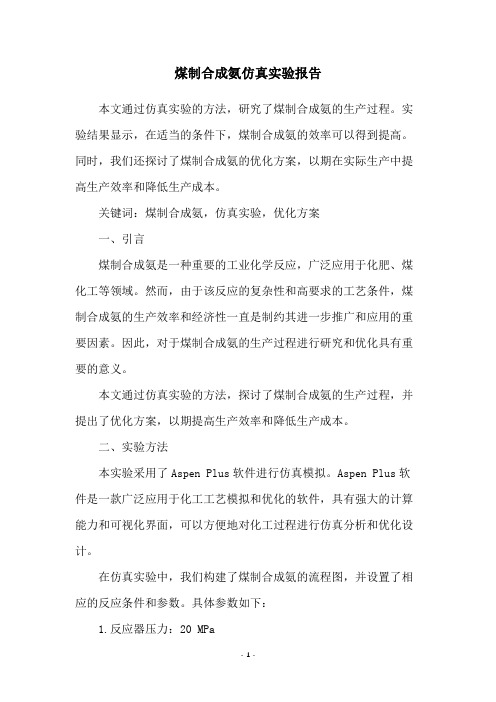
煤制合成氨仿真实验报告本文通过仿真实验的方法,研究了煤制合成氨的生产过程。
实验结果显示,在适当的条件下,煤制合成氨的效率可以得到提高。
同时,我们还探讨了煤制合成氨的优化方案,以期在实际生产中提高生产效率和降低生产成本。
关键词:煤制合成氨,仿真实验,优化方案一、引言煤制合成氨是一种重要的工业化学反应,广泛应用于化肥、煤化工等领域。
然而,由于该反应的复杂性和高要求的工艺条件,煤制合成氨的生产效率和经济性一直是制约其进一步推广和应用的重要因素。
因此,对于煤制合成氨的生产过程进行研究和优化具有重要的意义。
本文通过仿真实验的方法,探讨了煤制合成氨的生产过程,并提出了优化方案,以期提高生产效率和降低生产成本。
二、实验方法本实验采用了Aspen Plus软件进行仿真模拟。
Aspen Plus软件是一款广泛应用于化工工艺模拟和优化的软件,具有强大的计算能力和可视化界面,可以方便地对化工过程进行仿真分析和优化设计。
在仿真实验中,我们构建了煤制合成氨的流程图,并设置了相应的反应条件和参数。
具体参数如下:1.反应器压力:20 MPa2.反应器温度:500℃3.反应器进料比:H2:N2=3:14.氮气流量:1000 kmol/h5.氢气流量:3000 kmol/h6.催化剂种类:铁钼催化剂7.催化剂负荷量:100 kg/m3通过对上述参数的设置和调整,我们得到了煤制合成氨的仿真模拟结果。
三、实验结果与分析1.催化剂种类和负荷量的影响为了探讨催化剂种类和负荷量对煤制合成氨的影响,我们进行了不同催化剂种类和负荷量的仿真实验。
实验结果表明,铁钼催化剂比其他催化剂更适合煤制合成氨的反应条件。
此外,在催化剂负荷量为100 kg/m3时,反应效率最高,可以达到85%以上。
2.反应器压力和温度的影响为了探讨反应器压力和温度对煤制合成氨的影响,我们进行了不同反应器压力和温度的仿真实验。
实验结果表明,在反应器压力为20 MPa,温度为500℃时,煤制合成氨的效率最高,可以达到90%以上。
合成氨工艺实训总结与体会

合成氨工艺实训总结与体会实训地点:XXXXX大学化学工程实验中心实训时间:2021年9月1日~2021年9月10日实训人员:XX同学(XXX学院,XXX专业)实训内容:通过实验,了解合成氨的基本原理、反应机理、工艺流程,掌握合成氨的实验操作技能,了解合成氨的工艺控制方法和安全生产知识。
一、实训总结本次实训内容丰富、操作简单易行,让我在增长知识的同时也掌握了实验技能。
以下是我的实训总结:1. 掌握了合成氨的基本原理和反应机理。
在实验室老师的详细讲解和现场操作的指导下,我对合成氨的反应原理和机理有了更深刻的理解。
通过实验,我明白了合成氨的反应主要包括气态氢和气态氮逐渐转变成液态氨,并且掌握了如何调整反应速率和控制反应温度以达到最佳合成效果的方法。
2. 掌握了合成氨的实验操作技能。
合成氨实验是一项敏感难度高的工作,操作失误很容易造成实验失败。
经过老师的指导和多次实验的反复操作后,我成功完成了合成氨实验,并且获得了理想结果。
我也发现,在实验中细节决定成败,及时注意每一项反应细节可以预防事故,确保实验操作的安全性和稳定性。
3. 了解了合成氨工艺的控制和安全知识。
在实验中,我们学习了合成氨工厂的结构、合成氨工艺中常用的反应器类型和在合成氨生产中所需的安全控制措施。
尤其是我们探讨了如何合理调配反应用气的流量、温度以及压力,如何控制火灾危险的发生,如何从突发事件中迅速应对等安全问题,有了一定的实践经验和认识。
二、体会与收获通过合成氨实训,我不仅从理论上了解了合成氨工艺,更重要的是收获了实验操作经验和安全生产意识。
具体体会如下:1. 调试心理的重要性。
操作合成氨实验时,需要不断进行实验调节和反应条件的控制,听从导师的指导,冷静分析问题,调试各项参数等等。
这个过程让我很有收获,在实验的过程中不断探索,不断试验,对自己的思考能力和实际操作的能力都有了一定的提升。
2. 安全与专业技能同等重要。
合成氨实验必须真正做到安全第一,专业技能、实验经验次之。
合成氨的实习报告

一、实习目的本次实习旨在通过在合成氨生产企业的实际操作中,深入了解合成氨的生产过程、工艺原理及设备运行,提高自己的动手能力和实际操作技能,为今后从事相关工作奠定基础。
二、实习单位及时间实习单位:XX合成氨厂实习时间:2020年7月1日至2020年7月31日三、实习内容1. 合成氨生产原理及工艺流程合成氨是通过将氮气和氢气在高温、高压及催化剂的作用下,合成氨气。
具体工艺流程如下:(1)原料气制备:将空气中的氮气和氢气分离,得到高纯度的氮气和氢气。
(2)净化:对氮气和氢气进行净化,去除其中的杂质。
(3)合成:将净化后的氮气和氢气在合成塔中,在催化剂的作用下,在高温、高压下合成氨气。
(4)分离:将合成塔中生成的氨气与未反应的氢气和氮气分离。
(5)液化:将分离出的氨气液化,得到液氨产品。
2. 实际操作在实习期间,我跟随师傅学习了合成氨生产过程中的各个环节。
具体如下:(1)原料气制备:参观了原料气制备车间,了解了原料气的分离、净化等工艺流程。
(2)净化:学习了氮气和氢气的净化方法,包括低温甲醇洗、活性炭吸附等。
(3)合成:参观了合成塔,了解了合成塔的结构、催化剂的使用及合成条件。
(4)分离:学习了氨气与氢气和氮气的分离方法,如冷凝、冷剂循环等。
(5)液化:了解了液氨的生产过程,包括液化、储存、运输等。
3. 安全生产在实习期间,我学习了合成氨生产过程中的安全知识,包括火灾、爆炸、中毒等事故的预防和处理方法。
同时,还学习了企业的安全生产规章制度,提高了自己的安全意识。
四、实习收获1. 理论与实践相结合:通过实习,将所学的理论知识与实际操作相结合,加深了对合成氨生产过程的理解。
2. 提高动手能力:在实习过程中,动手操作了合成氨生产的各个环节,提高了自己的动手能力。
3. 安全意识:通过学习安全生产知识,提高了自己的安全意识,为今后的工作打下了基础。
4. 团队协作:在实习过程中,与同事相互学习、相互帮助,培养了团队协作精神。
化工仿真实习报告书(doc 8页)

化工仿真实习报告书(doc 8页)仿真实习实习报告姓名:专业:学号:实习成绩:课程名称:仿真实习报告实习形式:上机指导教师:2010 -2011 学年第 1 学期实习时间:实习地点:(二)合成氨仿真练习1、合成系统开车(1)投用LSH109(104-F液位高联锁),LSH111(105-F液位高联锁)(辅助控制盘画面)(2)打开SP71(合成工段现场),把工艺气引入104-F,PIC-182(合成工段DCS)设置在2.6Mpa投自动(3)显示合成塔压力的仪表换为低量程表○L(合成工段现场合成塔旁)(4)投用124-C(图1合成工段现场开阀VX0015进冷却水),123-C(图1合成工段现场开阀VX0016进锅炉水预热合成塔塔壁) ,116-C(合成工段现场开阀VX0014),打开阀VV077,VV078投用SP35(在图1合成工段现场合成塔底右部进口处)。
(5)按103-J复位(辅助控制盘画面),然后启动103-J(合成工段现场启动按钮),开泵117-J注液氨(在冷冻系统图的现场画面)(6)开MIC23,HCV11,把工艺气引入合成塔105-D,合成塔充压(合成工段现场图)(7)逐渐关小防喘振阀FIC7,FIC8,FIC14(8)开SP1付线阀VX0036均压后(一小段时间),开SP1,开SP72(在合成塔现场图画面上)及SP72前旋塞阀VX0035(合成塔现场图)(9)当合成塔压力达到1.4Mpa时换高量程压力表○H(现场图合成塔旁)(10)关SP1付线阀VX0036,关SP72及前旋塞阀VX0035,关HCV-11(11)开PIC-194设定在10.5MPa,投自动(108-F出口调节阀)(12)开入102-B旋塞阀VV048,开SP70。
(13)开SP70前旋塞阀VX0034,使工艺气循环起来。
(14)打开108-F顶MIC18阀(开度为100(合成现场图)(15)投用102-B联锁FSL85(辅助控制盘画面)(16)打开MIC17(合成塔系统图)进燃料气,102-B点火(合成现场图),合成塔开始升温(17)开阀MIC14调节合成塔中层温度,开阀MIC15,MIC16,控制合成塔下层温度,(合成塔现场图)(18)停泵117-J,停止向合成塔注液氨(19)PICA8设定在1.68MPa投自动。
- 1、下载文档前请自行甄别文档内容的完整性,平台不提供额外的编辑、内容补充、找答案等附加服务。
- 2、"仅部分预览"的文档,不可在线预览部分如存在完整性等问题,可反馈申请退款(可完整预览的文档不适用该条件!)。
- 3、如文档侵犯您的权益,请联系客服反馈,我们会尽快为您处理(人工客服工作时间:9:00-18:30)。
(2013 年 12 月专业基础仿真训练论文 题 目:论述合成氨合成工段的安全措施 学生姓名: 学 院:化工学院 系 别:化学工程系 专 业: 班 级:指导教师:前言在经历过合成氨合成工段的仿真实训以后,使得自己明白了合成氨合成的工艺流程,了解了所涉及到的一些设备和管道,其中有些高压高温设备或者高压低温的设备。
所用的物料有氢气以及中间产物等都是易燃易爆的高危物料,在生产和运输的过程中如果生产操作不当或者设备出现故障,造成大量的这些有毒、有害、易燃、易爆气体泄漏,极易引起发生重大火灾、爆炸和员工的中毒等后果。
所以在此基础上,我将对合成氨的合成工段所能设计到的安全方面进行论述,一方面是为了使得人们充分的认识到合成工段的危险方面,从而在发生异常情况时候能够从容应对,另一方面也是为了减少事故所给厂子所带来的巨大损失。
第1章简述合成氨合成工段的工艺流程从甲烷化来的新鲜气(40℃、2.6Mpa、H2/N2=3:1)先经压缩前分离罐(104-F)进合成气压缩机(103-J)低压段,在压缩机的低压缸将新鲜气体压缩到合成所需要的最终压力的二分之一左右,出低压段的新鲜气先经136-C用甲烷化进料气冷却至93.3℃,再经水冷器(116-C)冷却至38℃,最后经氨冷器(129-C)冷却至7℃,后与氢回收来的氢气混合进入中间分离罐(105-F),从中间分离罐出来的氢氮气再进合成气压缩机高压段。
合成回路来的循环气与经高压段压缩后的氢氮气混合进压缩机循环段,从循环段出来的合成气进(124-C)。
高压合成气自124-C出来后,分两路继续冷却,第一路串联通过原料气和循环气一级和二级氨冷器117-C和118-C的管侧,冷却介质都是冷冻用液氨,另一路通过就地的MIC-23节流后,在合成塔进气和循环气换热器120-C的壳侧冷却,两路会合后,又在新鲜气和循环气三级氨冷器119-C 中用三级液氨闪蒸槽112-F来的冷冻用液氨进行冷却,冷却至-23.3℃。
冷却后的气体经过水平分布管进入高压氨分离器(106-F),在前几个氨冷器中冷凝下来的循环气中的氨就在106-F中分出,分离出来的液氨送往冷冻中间闪蒸槽。
从氨分离器出来后,循环气进入合成塔进气-新鲜气和循环气换热器120-C的管侧,从壳侧的工艺气体中取得热量,然后又进入合成塔进气--出气换热器(121-C)的管侧,再由HCV-11控制进入(105-D),在121-C管侧的出口处分析气体成分。
合成气进气由合成塔105-D的塔底进入,自下而上地进入合成塔,经由MIC-13直接到第一层触媒的入口,用以控制该处的温度,这一近路有一个冷激管线,和两个进层间换热器付线可控制第二、第三层的入口温度必要时可以分别用MIC-14、15和16进行调节。
气体经最底下一层触媒床后,又自下而上地把气体导入内部换热器的管侧,把热量传给进来的气体,再由105-D的顶部出口引出。
合成塔出口气进入合成塔--锅炉给水换热器123-C的管侧,把热量传给锅炉给水,接着又在121-C的壳侧与进塔气换热而进一步被冷却,最后回到103-J 高压缸循环段(最后一个叶轮)而完成了整个合成回路。
合成塔出来的气体有一部分是从高压吹出气分离缸108-F经MIC-18调节并用Fl-63指示流量后,送往氢回收装置或送往一段转化炉燃料气系统。
从合成回路中排出气是为了控制气体中的甲烷化和氩的浓度,甲烷和氩在系统中积累多了会使氨的合成率降低。
吹出气在进入分离罐108-F以前先在氨冷器125-C冷却,由108-F分出的液氨送低压氨分离器107-F回收。
合成塔备有一台开工加热炉(102-B),它是用于开工时把合成塔引温至反应温度,开工加热炉的原料气流量由FI-62指示,另外,它还设有一低流量报警器FAL-85与FI-62配合使用,MIC-17调节102-B燃料气量。
第2章合成氨合成工段安全技术措施1.设备安全从第一章的工艺流程简介中可以看出在整个合成工段所用到的设备有合成氨反应器、炉子、换热器、分离罐和压缩机和大量的运送管线阀门。
其中大部分属于压力容器,所以对其压力的监控一定要严格。
1.1 对氨合成反应器的检查由于合成氨反应是有催化剂的放热反应。
所以一定要控制反应的温度,应该在反应器中安装一些测温自控装置,以便在温度发生异常的时候自动控制温度的上升,在反应器上可以安装一些诸如安全阀、爆破片、排气孔等泄压装置。
对反应器应该定时进行内部和外部的检查,发现问题及时解决。
1.2 对炉子的检查炉子主要是用来给反应器初期供热的设备,主要所用的燃料是天然气。
所以炉子一定要选用防爆型的,并设置列管故障保护设施。
设置一定数量的温度和压力检测装置,以便控制输出温度,使得炉子控制在最佳燃烧范围内。
定期对炉子的内部和外部进行检查。
1.3 对换热器的检查换热器是两种温度不同的物质交换温度的场所,所以考虑换热器中所走的物料,选择合适材料和类型的换热器。
考虑是否超过换热器的设计温度,设备的冲洗是否适当,维修工作能否安全的进行,两种物料能否在换热器内充分的交换热量等等。
1.4对分离罐的检查定期对分离罐进行压力测试,所使用的分离罐是否符合相应的标准。
检查压力的释放是否适当,紧急情况下能将容器中的物料隔离吗?分离罐的放空和排污是否有详细的说明。
对一些重要的液位进行及时监控,发现异常能够及时处理。
1.5 对压缩机的检查在选用压缩机的时候,考虑出口压力是否会超过壳体本身的设计压力,出口压力会不会超过下游设备或者管道的设计压力,进压缩机的物料的温度会不会超过壳体的设计温度,对压缩机的机械部件进行定期的维护加润滑油,保证其正常运行。
在压缩机周围应设置防护罩,避免意外的发生。
1.6 对管线阀门的检查管线是链接设备之间的主要通道,在对管道的检查中,应考虑内部物料的类型、温度以及压力,是否符合工艺条件。
检查管线和阀门是否发生泄漏和破损,设置应有的放空和排污系统。
是否需要安装切断阀,止逆阀等等。
对管线阀门进行定期的清理,保证管线阀门的正常运行。
2.工艺操作的安全技术2.1催化反应的安全技术氨合成是氢气和氮气按照一定比例,在催化剂的作用在进行的可逆放热的化学反应。
在氨合成操作过程中,若是催化剂的选择不正确或者加入不适量,易造成局部反应的剧烈。
催化剂需要在一定的温度条件下,若是反应温度控制不当,可能会发生超温爆炸或者着火事故,还有可能使得催化剂失活,以至于反应目标产物无法产生。
原料气中某种能与催化剂反应的杂志含量增加,可能成为爆炸危险物。
(1)合成氨是在高压高温下有固相的催化剂存在下进行的,主要危险性有:由于原料及成品存在易燃、易爆、有毒,在反应中设备和管道容易受到腐蚀,因此要特别防止压缩工段的氢气在高压下发生泄漏,产生爆炸。
应备有充分蒸汽或者惰性气体,以便应急。
在开车或者检修设备、管线之前,必须用氮气进行吹扫。
(2)在装卸催化剂的时候,要防止破碎和污染,防止催化剂自然超温烧坏。
加热炉是热量的来源,在催化剂重整过程中,加热炉的安全和稳定非常重要,应采用温度自动调节系统。
对于重要工艺参数,相如温度压力、流量、液位等均采用安全报警,必要时采用联锁保护装置。
2.2 加热操作的安全在氨合成工段中,炉子是最主要的供热工具,在开车的时候供给反应器热量。
是的反应能够正常的运行。
当反应器的温度达到380度的时候,就停止给反应器供热,在操作过程中应严格控制温度范围和升温的速度。
在反应器有物料进行反应的时候,由于反应是放热反应,所以应控制反应热量的产生,当温度超过额定值的时候,应该及时移热量。
避免发生冲料和爆炸。
加热炉的安全要点有:(1)将炉子门同反应器用砖墙完全隔离,炉膛构造应采用烟道气辐射方式加热,避免火焰之间接触设备,以防止因高温烧穿管道。
(2)炉子内部应该经常清理,防止局部过热引起锅底破裂。
(3)使用天然气燃烧的炉子,点火前应该吹扫炉膛,排除能积存的爆炸性混合气体。
(4)当炉子发生漏料的时候,能够第一时间转移物料并阻止燃料继续进入。
3.电气及静电安全技术3.1防电气事故安全技术在合成氨合成工段,存在有压缩机、照明系统、报警系统、以及检测监控系统等都需要电。
因为在合成阶段,物料大都是易燃易爆物质,所以要严格控制电器的使用,严格按照操作规程进行,防止触电事故的发生和漏电现象的产生。
在每个电器上都应该设置良好的接地保护装置,正确的运行电器,避免过载使用,防止火灾,短路、接触不良、铁芯发热等现象产生。
在电器设备、线路、报警系统监控检测系统中,安装、调试与运行维护、检修中,不严格遵守相应的电气设备及系统运行操作中,所以会导致电气事故的发生。
由于电气设备或者电气线路安装不符合要求,会直接造成触电事故,由于电气设备运行管理不当,会使绝缘损坏而漏电,又没有切实有效的安全措施。
主要表现在以下几个方面;(1)缺乏电气安全知识(2)违反操作规程(3)使用不合格的设备(4)维修、管理不善防止触电事故的发生主要措施有采用安全的电压,在任何情况下都不会对人身造成伤害;采用绝缘的方式来隔离人员和线路的接触;采用屏护和间距,就是用护罩,箱盒、围栏把带电体与外界隔离。
间距就是使带电体与人保持一定的距离。
采用电工的安全用具是防止触电、坠落、灼伤等工伤事故。
3.2 防静电安全技术在合成氨合成阶段,静电现象也是很常见的,由于物料和设备的摩擦、接触分离、液体换热,受热撞击,都会产生静电。
静电危害的防治措施有:(1)控制静电产生(2)防止静电积累(3)防止爆炸性混合物的产生具体控制措施有采用合适的材料、增加静止时间、静电屏蔽、接地、增湿、加抗静电剂、静电消除器。
3.3防雷电安全技术在现在的合成氨工厂大都趋向于大型化,所以设备一般都设置在室外,而且设备都是金属,当然就避免不了夏天雷电的袭击。
雷电会产生数万伏的冲击电压,课毁坏任何设备,在有可燃物质存在的情况下还会发生爆炸的现象。
所以在工厂防雷电袭击也是很重要的一项。
防雷电装置包括接闪器、引下线、接地装置、电涌保护器。
其中设备本身的制造应该符合相关标准。
第3章现场操作管理及消防设施布置3.1 人员操作规范管理美国工程师海因里希提出事故致因理论,其中提到事故的发生是由于认得不安全行为和物的不全状态导致的。
所以由于人为的事故占绝大多数,因此对于人员操作的规范显得尤为重要。
造成人员行为性危险因素主要有:1.心理、生理性危险有害因素:(1)负荷超限(2)健康状况异常(3)从事禁忌作业(4)心理异常(5)辨识功能缺陷2.行为性危险有害因素(1)指挥错误(2)操作错误(3)监护失误从上述因素可知人员的操作规程对于安全生产的重要性,所以企业在管理方面应该尽可能完善安全管理条例,完善相应的制度。
认真学习《安全生产法》等法律、法规及各项安全制度,在员工中牢固树立安全第一、预防为主的思想,加强对站长、安全员的岗位培训并在工作中严格执行各项规章制度。