21世纪初电解加工的发展和应用
电解加工的理论及应用

详细描述
电极应具备足够的导电性、耐腐蚀性和加工稳定性。电极的设计需根据加工需求,如工件形状、材料 特性、加工精度等,进行优化。此外,电极的形状和尺寸也会影响加工效果,如电流密度分布、加工 区域等。
加工参数的确定与控制
总结词
加工参数的合理选择和控制对电解加工效果至关重要。
快速原型制造
电解加工可用于快速原型制造,缩短产品开发周期,降低开 发成本。
能源领域
核能设备制造
电解加工在核能设备制造中用于加工特殊材料和复杂结构,提高设备的可靠性 和安全性。
太阳能光伏板制造
电解加工在太阳能光伏板制造中用于高效硅片的切割和表面处理,提高光电转 换效率。
03 电解加工的关键技术
电解液的选择与优化
电解加工的未来展望
随着新材料、新工艺、智能制造等领 域的快速发展,电解加工技术将不断 革新,加工范围和加工精度将得到进 一步拓展和提高。
电解加工技术与其他先进制造技术的 结合将为复杂构件的精密制造提供更 多可能性,为高端装备制造和智能制 造提供有力支撑。
未来电解加工技术将更加注重环保、 节能和可持续发展,推动绿色制造和 智能制造的深度融合。
高加工精度
加工范围广
加工效率高
环境友好
由于电解加工是依靠电化学反 应进行加工的,因此加工过程 中没有机械切削力,可以减少 工具磨损和热变形等误差,实 现高精度的加工。
电解加工可以加工各种硬、脆 、软等难加工材料,如不锈钢 、硬质合金、金刚石等。同时 ,通过调整电解液的成分和加 工参数,可以实现对不同材料 的加工。
微细电解加工
利用微细电极和微细电解液,实现微小尺寸和复杂结构的加工,满足微电子、生物医学 等领域的需求。
电解加工的原理和应用教案
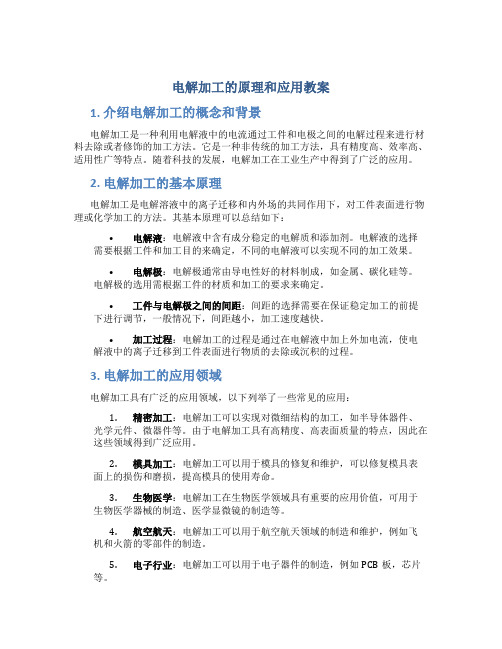
电解加工的原理和应用教案1. 介绍电解加工的概念和背景电解加工是一种利用电解液中的电流通过工件和电极之间的电解过程来进行材料去除或者修饰的加工方法。
它是一种非传统的加工方法,具有精度高、效率高、适用性广等特点。
随着科技的发展,电解加工在工业生产中得到了广泛的应用。
2. 电解加工的基本原理电解加工是电解溶液中的离子迁移和内外场的共同作用下,对工件表面进行物理或化学加工的方法。
其基本原理可以总结如下:•电解液:电解液中含有成分稳定的电解质和添加剂。
电解液的选择需要根据工件和加工目的来确定,不同的电解液可以实现不同的加工效果。
•电解极:电解极通常由导电性好的材料制成,如金属、碳化硅等。
电解极的选用需根据工件的材质和加工的要求来确定。
•工件与电解极之间的间距:间距的选择需要在保证稳定加工的前提下进行调节,一般情况下,间距越小,加工速度越快。
•加工过程:电解加工的过程是通过在电解液中加上外加电流,使电解液中的离子迁移到工件表面进行物质的去除或沉积的过程。
3. 电解加工的应用领域电解加工具有广泛的应用领域,以下列举了一些常见的应用:1.精密加工:电解加工可以实现对微细结构的加工,如半导体器件、光学元件、微器件等。
由于电解加工具有高精度、高表面质量的特点,因此在这些领域得到广泛应用。
2.模具加工:电解加工可以用于模具的修复和维护,可以修复模具表面上的损伤和磨损,提高模具的使用寿命。
3.生物医学:电解加工在生物医学领域具有重要的应用价值,可用于生物医学器械的制造、医学显微镜的制造等。
4.航空航天:电解加工可以用于航空航天领域的制造和维护,例如飞机和火箭的零部件的制造。
5.电子行业:电解加工可以用于电子器件的制造,例如PCB板,芯片等。
6.汽车工业:电解加工可以用于汽车工业中的各种金属部件的制造和维护,如汽车轮毂、节流阀等。
4. 电解加工的教学内容和方法为了有效教授电解加工的原理和应用,我们可以采用以下教学内容和方法:•理论讲解:首先通过理论讲解,介绍电解加工的基本原理和应用领域。
电解加工技术的现状与展望
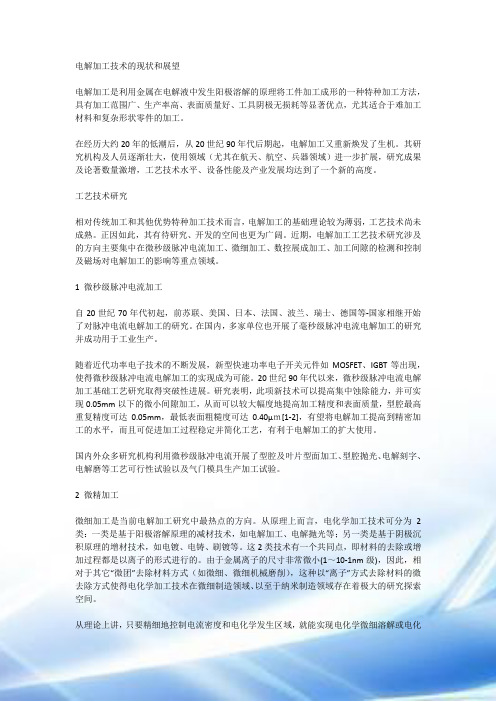
电解加工技术的现状和展望电解加工是利用金属在电解液中发生阳极溶解的原理将工件加工成形的一种特种加工方法,具有加工范围广、生产率高、表面质量好、工具阴极无损耗等显著优点,尤其适合于难加工材料和复杂形状零件的加工。
在经历大约20年的低潮后,从20世纪90年代后期起,电解加工又重新焕发了生机。
其研究机构及人员逐渐壮大,使用领域(尤其在航天、航空、兵器领域)进一步扩展,研究成果及论著数量激增,工艺技术水平、设备性能及产业发展均达到了一个新的高度。
工艺技术研究相对传统加工和其他优势特种加工技术而言,电解加工的基础理论较为薄弱,工艺技术尚未成熟。
正因如此,其有待研究、开发的空间也更为广阔。
近期,电解加工工艺技术研究涉及的方向主要集中在微秒级脉冲电流加工、微细加工、数控展成加工、加工间隙的检测和控制及磁场对电解加工的影响等重点领域。
1 微秒级脉冲电流加工自20世纪70年代初起,前苏联、美国、日本、法国、波兰、瑞士、德国等-国家相继开始了对脉冲电流电解加工的研究。
在国内,多家单位也开展了毫秒级脉冲电流电解加工的研究并成功用于工业生产。
随着近代功率电子技术的不断发展,新型快速功率电子开关元件如MOSFET、IGBT等出现,使得微秒级脉冲电流电解加工的实现成为可能。
20世纪90年代以来,微秒级脉冲电流电解加工基础工艺研究取得突破性进展。
研究表明,此项新技术可以提高集中蚀除能力,并可实现0.05mm以下的微小间隙加工,从而可以较大幅度地提高加工精度和表面质量,型腔最高重复精度可达0.05mm,最低表面粗糙度可达0.40μm[1-2],有望将电解加工提高到精密加工的水平,而且可促进加工过程稳定并简化工艺,有利于电解加工的扩大使用。
国内外众多研究机构利用微秒级脉冲电流开展了型腔及叶片型面加工、型腔抛光、电解刻字、电解磨等工艺可行性试验以及气门模具生产加工试验。
2 微精加工微细加工是当前电解加工研究中最热点的方向。
从原理上而言,电化学加工技术可分为2类:一类是基于阳极溶解原理的减材技术,如电解加工、电解抛光等;另一类是基于阴极沉积原理的增材技术,如电镀、电铸、刷镀等。
电解加工技术的应用和发展

电解加工技术的应用和发展*
范植坚1,杨 森1,唐 霖2
(1.西安工业大学 机电工程学院,西安 710032;2.哈尔滨工业大学 机电工程学院,哈尔滨 150001)
摘 要: 结合电解加工技 术 应 用 发 展 的 关 键,综 述 了 促 进 电 解 加 工 技 术 进 步 的 重 要 研 究 工 作,列举了计算机技术在电解加工工艺、阴极设计、控 制 和 设 备 方 面 的 部 分 应 用 实 例 以 及 微 细 电化学加工的研究进展,阐述了复合、组合集成是拓 宽 电 解 加 工 应 用 范 围 的 有 效 途 径 的 理 念. 分 析 了 目 前 航 空 、航 天 、兵 器 工 业 对 电 解 加 工 需 求 增 长 以 及 石 油 采 掘 对 电 解 加 工 的 需 求 异 军 突 起 的 情 况 ,电 解 加 工 技 术 的 日 臻 完 善 和 新 的 发 展 机 遇 预 示 着 电 解 加 工 的 春 天 到 了 . 关 键 词 : 电 解 加 工 ;计 算 机 技 术 ;复 合 和 组 合 ;微 细 电 化 学 加 工 中 图 号 : TG662 文 献 标 志 码 : A
* 收稿日期:2012-04-25 作 者 简 介 :范 植 坚 (1943-),女 ,西 安 工 业 大 学 教 授 ,主 要 研 究 方 向 为 特 种 加 工 .E-mail:zhijianfan@xatu.edu.cn.
776
西 安 工 业 大 学 学 报 第 32 卷
工的研究始于80年代中 期,1986 年 波 兰 华 沙 工 业 大学的 J.Kozak 提 出 以 棒 状 阴 极 作 旋 转 运 动, Kozak等开发了可 实 现 对 电 解 加 工 过 程 模 拟 的 计 算机辅助工程软件 CAE-ECM,根据阴极运动轨迹 求解工件形状或由给定工件形状反求阴极运动轨 迹,利用工艺试验 进 行 验 证,这 种 方 法 已 为 多 国 学 者 接 受 [45-48].南 京 航 空 航 天 大 学 采 用 直 线 刃 阴 极 数 控展成电解加工整体叶轮已在航空发动机上得到 应用,针对 闭 式 整 体 构 件 受 刀 具 可 达 性 限 制 的 问 题,提出采用近成 形 阴 极 数 控 电 解.开 发 的 数 控 展 成电解加工软件 包,具 有 叶 片 型 面 的 数 据 处 理、数 控加工的展成运动轨迹运 算 及 仿 真 等 功 能 , [27,49-51] 如图1所示.
电解加工的原理及应用范围

电解加工的原理及应用范围1. 电解加工的原理电解加工是一种利用电化学原理进行金属加工的方法。
它基于电解液中的离子导电性和金属表面的化学反应来实现加工过程。
电解加工利用电流通过工作电极和工件之间的电解液,通过电极的阳极氧化或阴极解除来去除金属材料。
该过程在金属零件表面形成微小的坑洞或凹陷,从而实现加工效果。
电解加工的原理基于两个关键因素:电解液和电流。
1.1 电解液电解液是电解加工过程中一个重要的组成部分。
它通常由溶剂和电解质组成。
溶剂是一种导电的液体,如水或有机溶剂。
电解质是在溶剂中溶解的化学物质,如盐或酸。
电解质通过提供离子来使电流在电解液中传导。
1.2 电流电流是电解加工的推动力。
通过施加电压,电解液中的离子会导致金属表面的氧化或还原反应。
阳极氧化是一种将阳极材料转化为氧化物的反应,而阴极解除是一种将阴极表面的氧化物还原为金属的反应。
2. 电解加工的应用范围电解加工具有广泛的应用范围,特别是在微细加工和特殊材料加工方面。
以下列举了电解加工的主要应用领域:2.1 微加工电解加工在微加工领域有着广泛的应用。
由于其高精度和低表面粗糙度的特点,电解加工被广泛用于制造微细结构和微型零件。
微细加工领域的应用包括:•微机械系统(MEMS)制造•显微加工•微切削加工•精密钻孔2.2 金属腐蚀电解加工可以用于金属腐蚀过程中的精确控制。
通过调整电解液的成分和电流密度,可以实现对金属表面的特定区域进行腐蚀。
金属腐蚀的应用包括:•金属模具制造•电路板制造•金属艺术品制作2.3 超合金加工电解加工在超合金加工中发挥着重要作用。
超合金通常是高强度和高温材料,难以通过传统的切削或加热加工方法进行加工。
电解加工提供了一种有效的方式来加工超合金,同时提供良好的表面质量。
超合金加工的应用领域包括:•航空航天工业•汽车制造业•能源领域2.4 生物医学应用电解加工在生物医学领域也有一定的应用。
它用于制作生物医学器械和植入物,如人工关节、心脏支架和人工骨骼。
电解加工技术及其应用

电解加工技术及其应用
1什么是电解加工技术
电解加工技术是一种利用电解原理来切削、刻蚀等加工材料的方法。
它是利用电极与工件之间通入电解液或氧化物熔体,在一定的电场作用下,使工件上的物质在界面运动的过程中发生化学变化,从而达到切削、刻蚀等目的。
2电解加工技术的优势
相比传统机械加工,电解加工技术具有以下优势:
1.可以切削复杂形状的工件;
2.可以切削高硬度、高脆性、难以加工的材料;
3.可以切削高精度和高表面质量的零件;
4.没有机械切削过程中产生的热变形、毛刺等问题;
5.可以节约原材料、降低生产成本。
3电解加工技术的应用
电解加工技术广泛应用于模具、航空航天、汽车制造、仪表、医疗设备等领域。
具体应用包括:
1.制造高精度模具和模板;
2.加工超硬合金、陶瓷、钨钢等材料的零件;
3.制造微细孔、花纹、图案等细节部分;
4.制造超平面、3D曲面、球面等各种形状的零件;
5.制造高质量的电极、电介质等器件。
总之,电解加工技术是一项高效、高精度、高表面质量的加工技术,将会越来越多地应用于各个领域中。
电解加工发展趋势
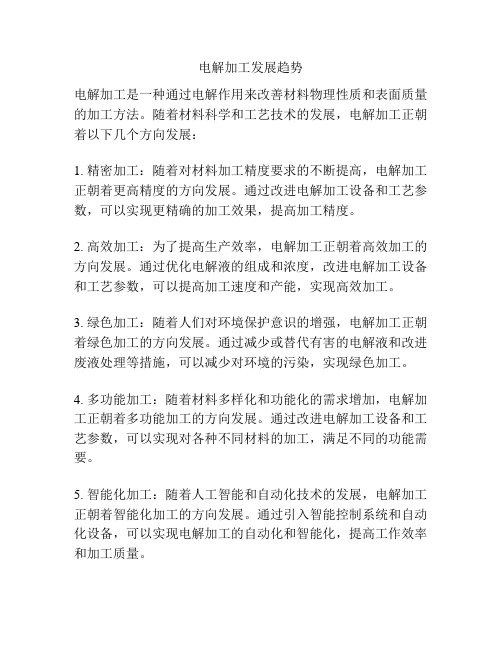
电解加工发展趋势
电解加工是一种通过电解作用来改善材料物理性质和表面质量的加工方法。
随着材料科学和工艺技术的发展,电解加工正朝着以下几个方向发展:
1. 精密加工:随着对材料加工精度要求的不断提高,电解加工正朝着更高精度的方向发展。
通过改进电解加工设备和工艺参数,可以实现更精确的加工效果,提高加工精度。
2. 高效加工:为了提高生产效率,电解加工正朝着高效加工的方向发展。
通过优化电解液的组成和浓度,改进电解加工设备和工艺参数,可以提高加工速度和产能,实现高效加工。
3. 绿色加工:随着人们对环境保护意识的增强,电解加工正朝着绿色加工的方向发展。
通过减少或替代有害的电解液和改进废液处理等措施,可以减少对环境的污染,实现绿色加工。
4. 多功能加工:随着材料多样化和功能化的需求增加,电解加工正朝着多功能加工的方向发展。
通过改进电解加工设备和工艺参数,可以实现对各种不同材料的加工,满足不同的功能需要。
5. 智能化加工:随着人工智能和自动化技术的发展,电解加工正朝着智能化加工的方向发展。
通过引入智能控制系统和自动化设备,可以实现电解加工的自动化和智能化,提高工作效率和加工质量。
总的来说,电解加工正朝着精密、高效、绿色、多功能和智能化的方向发展,以满足不断变化的市场需求和工业发展的要求。
电解加工技术在新材料制备中的应用研究进展

电解加工技术在新材料制备中的应用研究进展概述电解加工技术是一种利用电解液中的电解质活动和金属离子在导电介质中迁移的原理,对工件表面进行加工和处理的技术。
随着新材料技术的发展和应用需求的提高,电解加工技术在新材料制备中得到了广泛的应用。
本文将从三个方面来探讨电解加工技术在新材料制备中的应用研究进展:电解加工技术在金属材料制备中的应用、电解加工技术在非金属材料制备中的应用以及电解加工技术在复合材料制备中的应用。
一、电解加工技术在金属材料制备中的应用1.1 电解铸造技术电解铸造技术是利用电解液中的金属离子在电场作用下,在模具中沉积和固化成型的一种制备金属材料的方法。
相比传统的炉冶炼铸造技术,电解铸造技术具有成本低、无污染、成型精度高等优点,适用于制备微小、复杂形状的金属材料,如微电子器件中的金属导线和导电片等。
1.2 电解沉积技术电解沉积技术是将金属离子通过外加电流在导电基体上沉积成薄膜或者纳米颗粒的方法。
通过调节电解液中的电流密度、温度、pH值等参数,可以制备出具有特定形貌和物理化学性质的金属薄膜,如金属合金膜、氧化膜、镀金工艺等。
电解沉积技术在金属材料的表面改性、功能化和金属纳米颗粒的制备等方面有着广泛的应用。
1.3 电解制备金属陶瓷复合材料电解制备金属陶瓷复合材料是将金属离子和陶瓷颗粒通过电解沉积的方法制备成具有金属基体和陶瓷颗粒分布的复合材料。
该技术可以根据需要选择不同的金属离子和陶瓷颗粒进行复合,具有调节材料性能、提高材料强度和硬度的优势。
电解制备金属陶瓷复合材料在航空航天、军事和汽车行业等领域有着广泛的应用前景。
二、电解加工技术在非金属材料制备中的应用2.1 电解精加工技术电解精加工技术是利用电解液中的离子和材料表面的电化学反应,在微观尺度上对非金属材料进行精细加工和表面改性的方法。
该技术具有加工精度高、表面质量好等优点,在半导体、光电子和生物医学等领域中有广泛的应用,例如光栅结构的制备、石墨烯的氧化和还原等。
- 1、下载文档前请自行甄别文档内容的完整性,平台不提供额外的编辑、内容补充、找答案等附加服务。
- 2、"仅部分预览"的文档,不可在线预览部分如存在完整性等问题,可反馈申请退款(可完整预览的文档不适用该条件!)。
- 3、如文档侵犯您的权益,请联系客服反馈,我们会尽快为您处理(人工客服工作时间:9:00-18:30)。
2. 1 叶片型面加工 据综合统计 ,由于叶片难加工且数量多 ,用传统
3 第九届全国特种加工学术年会优秀论文 收稿日期 : 2001 - 11 - 24
切削方法加工约占整台发动机加工劳动量的 30 % 以上 。而相对于叶片的几何结构及采用的材料 ,电 解加工却能充分发挥其技术特长 。前苏联 、中国 、英 国早从 20 世纪 50 年代末 、60 年代初就开始采用电 解加工叶片 ,至今仍然保持着其不可替代的重要地 位。尽管由于精密锻造 、精密铸造 、精密辊轧技术的 提高而有更多的叶片采用精密成形 ,使电解加工叶 片的数量有一些减少 ,但随着 叶片材料向 高强 、高 硬、高韧性方向发展 ,钛合金、钴镍超级耐热合金的 采用 ,以及叶片几何结构的变化 ,超精密、超薄 、大扭 角、低展弦比等特殊结构叶片的出现 ,对加工又提出 了新的、更高的要求 ,电解加工依然是优选工艺方法 之一 。英国 R. R. 公司已经建立了专门的叶片自动 生产线 ,以计算机进行控制能稳定保证加工精度 ,同 时还使生产准备周期缩短到原来的 1/ 10 。在俄罗 斯 ,航空发动机工厂仍大量采用电解加工叶片 。在 我国 ,主要航空发动机工厂都有较大规模的专用电 解加工厂房。而在美国 、加拿大 ,也有电解加工叶片 的专业工厂 ,如加 拿大 Walbar 公司 的电解 加工分 厂 ,有 30 台以上的叶片电解机床 ,专门加工超薄 、精 密压气机叶片 。由此可见 ,电解加工已成为航空发 动机叶片制造中主要的 、不可缺少的优选工艺技术 。 随着电解加工技术水平的提高和现代航空发动机发 展的需求 ,在一些新结构 、新材料的叶片加工中 ,电 解加工在继续发挥其重要作用的同时 ,还会得到新
整体机匣对于减轻航空发动机重量、提高压气 机和涡轮部件的工作效率、进而增大推力和推重比 、 提高安全可靠性都有着积极作用 。从 70 年代开始 , 在新型高推重比航空发动机中逐渐采用整体机匣 。 其结构为薄壁筒(或锥筒) 形 、或薄壁环形 ;材料为钛 合金 (压气机机匣) 、不锈钢 、高温耐热合金 (涡轮导 向器和后承力机匣) 等 ; 在机匣内外壁上均布有多组 尺寸 、形状都相同 、但构型复杂的减重型槽和安装突 台。机匣毛坯多为铸造或锻造的圆筒或圆环 ,从毛 坯加工至复杂结构的机匣成品 ,去除量将近 2/ 3 或 更多 。如奥林普斯发动机分气机匣 ,毛坯 450kg 加 工到机匣成品为 67. 5kg 。如此大的去除量 (又是难 切削材料) 、如此复杂的薄壁机匣加工 ,采用数控切 削加工很困难 ; 而采用若干个不同形状的阴极在均 布的不同工位上重复电解加工 ,则充分发挥了电解
电解加工模具型腔、型面的研究与应用开始于 20 世纪 60 年代 ,1970 年前后达到了高峰 。但是 ,随 着模具生产逐渐转向多品种、小批量 ,甚至是几件或 单件需求 ,而且要求生产周期短 。传统的用成形阴 极进行拷贝式电解加工很难满足这些要求。再加上 数控切削机床、电火花加工机床的出现与发展 ,大量 的模具加工变为由数控切削和电火花加工所承担 , 使模具电解加工数量逐渐减少 。1980 年以后 ,在一 些先进工业国家 ,如日本 ,除了上述原因外 ,还考虑 到电解加工所引起的环境保护问题 ,已经不采用电 解加工模具 。在我国 ,有的工厂考虑到生产的继承 性 ,而且模具也有一定的批量 ,经济核算依然适合采 用电解加工 。因此 ,模具电解加工在我国少量工厂 仍然在生产线上应用 。近些年来 ,由于直流脉冲电 源 、特别是输出电流较大的高频窄脉冲直流电源的 研制以及相应电解工艺方面的重大进展 ,使得其加 工精度 、速度 、表面质量比较电火花成形加工 、数控 切削加工都有着明显的竞争优势 ,使得它可能在精 密模具加工中发挥作用。 2. 4 特殊孔类加工
特 辑 《电加工与模具》2001 年第 6 期
3
21 世 纪 初 电 解 加 工 的 发 展 和 应 用
南京航空航天大学 徐家文 华南理工大学 王建业 首都航天机械公司 田继安
摘 要 在总结近 20 年来电解加工研究与应用的基础上 ,对 21 世纪初叶电解加工的发展及应用方 向进行了论述。特别指出 :随着加工机理的深入研究和计算机控制技术应用水平的提高 ,电解加工在微精加 工 、难切削材料的复杂型面和复杂整体结构件的加工领域 ,将发挥其独特作用 ,具有重要的应用前景 。
特 辑 《电加工与模具》2001 年第 6 期
加工的特点 ,比机械切削提高工效 5~10 倍 。由此 , 在英 、美 、俄等国 ,电解加工机匣又成了电解加工的 又一成功应用领域 。为了提高加工效率 ,经常选用 大电流加工 ,其电源以万安培计 ;机床则为多工位数 控电解加工机床 。我国在这一领域的研究和应用几 年前才开始 。 2. 7 电解去毛刺
电解去毛刺已在航空、航天 、汽车的液压件 、叶 片榫齿 、齿轮等产品的制造中得到大量应用 ,不仅延 长了生产效率 ,同时更保证了产品质量 ,提高了产品 使用寿命。如德国在民用工业中大量应用电解去毛 刺技术 ,对齿轮 、液压件中的各种交叉孔壁去毛刺采 用专门设计 的电解去毛刺 机床 ,自 动化程度较 高。 在当前国际市场竞争环境下 “, 去毛刺”是保证产品 质量的需要 。如某些外国汽车制造厂 ,对每个齿轮 都要在线运转检测“去毛刺”的质量 ,以确保质量可 靠 ,延长产品使用寿命 。 2. 8 电解研磨复合抛光
—1 —
《电加工与模具》2001 年第 6 期 特 辑
Hale Waihona Puke 的应用 。 2. 2 炮管膛线加工
炮管膛线电解加工是世界上 ,也是我国最早就 开展研究并获得成功应用的实例。由于膛线电解加 工具有质量好、无表面缺陷 ,矩形膛线能加工成小圆 角过渡 ,有利于提高使用寿命和可靠性等突出优点 , 在实际生产中获得稳定应用并得到不断改进 、完善 , 已经成为生产中的定型工艺。随着计算机控制技术 的发展 ,近些年来我国又研究成功了以计算机控制 的锥体阴极移动式膛线电解工艺 ,可实现变缠度膛 线的加工 ,对于提高新型火炮的性能具有重要意义 。 可以说 ,炮管膛线电解加工将仍然会得到稳定的发 展与应用。 2. 3 模具加工
于 80 年代中期开始 ,人们致力于研究电解研磨 复合抛光三 维型面 ,但 离实际应用 还有一定差 距。 作为一项提高表面质量、提高生产效率 、减轻劳动强 度的新型复合抛光技术 ,在某些领域 ,还有值得研究 的必要并具有应用前景。 2. 9 在线电解修整超细金刚石 、C BN 磨轮
这是电解加工扩大应用领域的一个成功范例。 电解修整金属接合剂金刚石磨轮始于 70 年代前苏 联 ,80 年代日本也开始进行研究。当时由于修整工 艺上没有突 破 ,并 没有得 到实际 应用 。90 年代 以 后 ,日本研究人员巧妙地运用磨削液作为修整工作 液 ,进行很弱的电解修整作用 ,而产生的“电解泥”却 起着研磨剂的作用 ,使得在线电解修整超细金刚石 、 CBN 磨轮在精密 、超精密 磨削工程陶瓷 、半 导体硅 片 、硬化玻璃 、超硬合金材料中发挥了重要作用。其 尺寸 精度达到 0 . 1μm ,加工表面 Rma x10 nm 。研究 成果在一些高精产品的零件制造中得到应用 。
Abstract Based on t he review of t he research and application of electrochemical machining ( ECM) dur2 ing t he near 20 years , t he tendency of ECM development and application is di scussed in t his paper. It i s especial2 ly pointed out t hat , t he ECM will pay an i mport ant and particular role and show us t he brilliant f uture in some applicat ion fiel ds , includi ng t he micro2precision machi ni ng , t he machini ng of complex surface of hard2to2cut ma2
terials and complex int egrated structure. 关键词 电解加工 发展 应用
1 概述
电解加工以其加工速度快 、表面质量好 、凡金属 都能加工而且不怕材料硬、韧 、无宏观机械切削力 、 工具阴极无损耗 、可用同一个成形阴极作单方向送 进而成批加工复杂型腔、型面 、型孔等优点 ,在 20 世 纪 60 年代初 ,首先在炮管膛线和航空发动机涡轮叶 片的加工中得到应用 ,其后又逐渐扩大应用于锻模 型腔、深孔 、小孔 、长键槽 、等截面叶片整体叶轮的加 工以及去毛刺等 领域 ,取 得了显著的 技术 、经 济效 果 。但是 ,在 70 年代以后 ,随着国际市场经济竞争 形式的变化 ,产品更新换代快 ,生产批量减小 ,使得 电解加工的适用范围也发生变化。总体看应用范围 有所减小 ,但应用要求却越来越高 ;由于电解加工的 技术特点 ,在某些领域又得到新的应用。基于这种 变化 ,本文将从分析 、总结 80 年代以来电解加工的 研究与应用出发 ,探讨 、预测 21 世纪初的 10~20 年 内电解加工的发展及应用趋势。文中内容 ,期望得 到同行专家的建议和批评指正 。
—2 —
发动机镍基合金涡轮导流叶片上呈空间不同角度分 布的 25 个深小孔 、Inco718 镍基合金制造的涡轮后 轴 12 个润滑油孔 (孔径 �1. 45mm ,孔深 70. 1mm) 、 进口导流叶片上的深 扁防冰孔 (扁孔截面 : 5mm × 14mm , 长边两端 R2. 5mm ,孔深 260m m) 以及钛合 金机匣上的多种型孔、型槽 、凸台都是直到今天仍在 生产线上成功应用的实例 ,它们充分发挥了电解加 工的特点和优势。 2. 5 整体叶盘加工
该项技术的研究始于 70 年代 ,80 年代成功地 应用于不锈钢 、碳钢零件的平面和内外圆旋转面抛 光 。可以将表 面粗 糙度 从 Rma x几微米抛光到准镜 面的程度 ,达到 Rmax0 . 2 ~0. 3μm ,最佳效果可以达 到镜面 ,即 Rmax < 0 . 1μm 。从 90 年代初开始 ,我国 也逐步进行研究 ,在实验室中得到较满意的抛光效 果并得到部分应用 。但总的看 ,扩大工业应用还存 在不少问题 。