堆取料机空间防碰撞系统设计与实现
圆形料场堆取料机刮板机防撞装置

图1 圆形料场堆取料机悬臂式刮板机是圆形料场堆取料机的取料机构,通常安装在取料回转平台下部铰座处。
刮板机主要由悬臂、导轨、驱动链轮、改向轮、链条和刮板组成,悬臂前部安装有悬挂,悬挂上安装动滑轮组。
刮板机在不同区域进行取料作业时,取料回转平台连同刮板机必须进行一Copyright©博看网. All Rights Reserved./ 2017年第9期图2 原防撞装置安装当防撞检测板与料堆相撞时,防撞检测板23旋转,接近开关检测板11与接近开关10远离,接近开关常闭触点闭合。
PLC 的DI4输入模块相对应的输入点变成高电平24 V ,PLC 的DI4输入模块相对应通道的指示灯亮,刮板机回转保护停机。
DI4输入模块接线图所示,PLC 程序如图4所示。
图3 DI4模块接线图图4 PLC 程序图5 防撞装置安装图4.1 主要零部件介绍1)底座防撞装置底座采用Q345B 材料制作,设计时底座的末端圆弧与刮板机悬臂外径一致,便于焊接安装,底Copyright ©博看网. All Rights Reserved.底座 2. 拨杆 3. 接近开关 4. 接近开关底座 5. 筒体6. 销轴7. 圆柱螺旋压缩弹簧8. 法兰9. 检测板图6 防撞装置装配图2)法兰防撞装置法兰采用Q345B材料制作,设计时考虑合理定位,法兰外侧加装挡板,限制销轴旋转,确保销轴和检测板准确动作和可靠复位,确保拨杆与接近开关准确靠近和远离。
3)筒体筒体采用Q345B材料制作,设计时仅需考虑长度合适、刚度足够即可。
4)销轴销轴采用SUS304材料制作,其首、末端需铣制平面,装配后能周向定位,以保证其连接的拨杆能准确、可靠地与接近开关靠近或远离。
销轴零件图如图7所示。
5)圆柱螺旋压缩弹簧圆柱螺旋压缩弹簧采用50CrV A材料制作,喷丸处理,设计时主要考虑有效圈数、总圈数、自由长度、弹簧直径和屈服系数。
图7 销轴零件图4.2 安装及调试防撞装置底座与刮板机悬臂和下导轨采用焊接连接,销轴与检测板采用焊接连接,其余零部件均采用螺栓或螺钉连接。
斗轮堆取料机防碰撞保护的研究

SAFETY ∙MONITORING 安全 · 检测堆取料机和取料机之间防碰撞的基本思路是将斗轮堆取料机和取料机投影到堆场水平面上,在水平面上对其投影进行防碰撞分析。
防碰撞模型主要包括相邻轨道梁上的两台设备和同一轨道梁上的两台设备。
设备在轨道梁上的位置,设备的回转角度用光电式绝对值编码器测定,堆取料机的俯仰角度用角度仪通过4~20 mA 的模拟量信号传到大机PLC中,取料机的俯仰角度通过光电式绝对值编码器测定然后传到大机PLC中。
大机PLC再通过工业以太网把行走、回转、俯仰等编码器数值传到中控PLC系统中。
中控与大机之间的通讯用光缆作为传输介质以工业以太网的方式进行通讯。
1 防碰撞数学模型建立1.1 相同轨道梁上两台单机碰撞分析图1为两台大机处于同一条轨道梁时的状况,为保障两台设备不发生碰撞,必须使A大机的尾车H1到B 大机悬臂或配重最近点小于程序设定的最短距离。
设大机悬臂长度L1,尾车部分长度L2,配重部分长度为L3,B大机的俯仰角度为α,以臂架向左平行轨道梁为回转零点,B大机的回转角度为β,两大机的位置差为d。
B大机回转角度的绝对值≤90°时三维算法为d =L2+ L1sin α cos | β | (1)B大机回转角度的绝对值>90°时的三维算法为d =L2+ L3sin α cos(180°-| β | ) (2)1.2 相邻轨道梁上大机碰撞分析相邻轨道梁上两台大机碰撞情况分为A、B两种模式,见图2。
大机的回转角度范围为-120°~120°,以臂架向上平行轨道梁为回转零点。
A模式中C大机臂架最前端和D大机臂架最前端距离不能小于设定值;B 模式中C大机臂架最前端和D大机配重最后端距离不能小于设定值。
图2中的A模式设C大机回转角度大于等于0°,小于等于120°,D大机回转角度大于等于-120°,小于等于0°,设C大机俯仰角度为α1,回转角度为β1;D大机俯仰角度为α2,回转角度为β2,两大机的臂架长度为L1,两大机位置差值为d,算法为d = | L1sin α1 cos β1-L1sin α2 cos β2 | (3)图2中B模式设C大机俯仰角度为α1,回转角度为β1,β1为0°~120°;D大机俯仰角度为α2,回转斗轮堆取料机防碰撞保护的研究杨敏康神华粤电珠海港煤炭码头有限责任公司 珠海 519050摘 要:神华粤电珠海港煤炭码头公司现有8台斗轮堆取料机和2台取料机,由于堆场范围广,斗轮堆取料机和取料机行走距离长,大车行走编码器易出现偏差,同一轨道梁之间以及相邻的轨道梁之间容易发生斗轮堆取料机相撞事故,对司机人身安全和设备稳定运行造成很大的威胁。
XX钢铁集团原料场堆取料机防碰撞技术方案

XX钢铁集团有限公司原料场堆取料机防碰撞及定位检测技术方案目录1.项目概述 (3)2.防碰撞定位控制系统实现功能 (3)2.1绝对位置检测 (4)2.2空间防碰撞 (4)2.3安全联锁控制 (5)2.4防混料检测 (5)2.5动态显示 (5)3.防碰撞控制系统构成 (5)3.1 系统构成 (5)3.2系统信号流程 (6)4.格雷母线技术简介 (7)4.1 格雷母线检测原理 (7)4.2 检测方式 (9)4.3 格雷母线的结构 (10)4.4位置检测特点 (10)5.实现方案 (11)5.1 机车走行位置检测方案 (11)5.2 悬臂旋转位置检测方案 (11)6.基本配置清单 (13)7.项目承担企业简介与成功案例.............................................. 错误!未定义书签。
7.1企业简介...................................................................................... 错误!未定义书签。
XX钢铁集团原料场堆取料机走行及回转位置检测技术方案1.项目概述XX钢铁有限公司拟建设高炉、烧结、球团和燃煤发电厂,需提供原燃料供应系统、成套设备、配套设施提供及相关服务,先期建设综合原料场一步工程,配套有5台大型堆取料机设备,其中贮料场有堆取料机4台、混均堆场有堆料机1台和取料机1台,为实现料场机械自动运行、位置跟踪、安全防碰撞保护系统功能,要求料场同轨道的两台堆取料机必须设置可靠的防碰撞控制系统置,确保关键设备生产安全和实现设备精细化管理,提高原料场运行效益。
原料场与混均料场的堆取料机、双轮取料机是煤场重要作业设备,跨间内有两台及两台以上的大型设备工作时必须设置防碰撞装置,碰撞距离在5~20m可调、设置减速与停止功能与进行声光报警、安全运行,另外布料小车要求实现精确位置对正下料。
港口堆、取料机防碰撞问题的数学模型

—16 6 .2 一12 6 .5
— .4 552
342 .O 818 . 4
—1 .7 19
69 .7 一1 86 . 0
268 . 8
2 . O 39 6 1. 2 99 2
— .8 528
—1. 2 038 —86 .9
— .4 526
~ . 6 8 82 —24 6 . l
起重 机 结 构有 限 元 分 析 [ ] J .起 重 运 输 机 械 ,20 06
( 3):1 O一1 . 2
与前臂 主 梁 连 接 处 会 出现 较 大应 力 ,故 前 拉 杆 及 其连接 处 的 日常 检测 十分 必要 。
s mma ie n n lz s c l so r b e ewe n sa k r/ e l i r n t e ve f me h n s u r sa d a a y e ol in p o lms b t e t e e s rc ame s i h iw o c a im,t u t a q ie h z i h si c urste
T i a i nf a trf r n e v u o e s l t n t h ol in p o l ms t a y o c rd r g t e c o d n t g o e a h sh s sg i c n ee e c a ef rt o ui o t e c l so r b e h tma c u u i h o r ia i p r — i l h o i n n t n flr e ma h n r . i s o ag c ie y o
纳 和 分 析 ,得 到 其 空 问 相 对 位 置 的数 学 关 系 ,推 导 出 适 于其 防 碰 撞 的 数 学 表 达 式 ,对 于 解 决 大 型 机 械 协 同 作 业 过 程 中可 能 发 生 的 碰 撞 问题 有 重 要 的参 考 价 值 。
浅析煤炭码头堆场堆、取料机防碰撞设计理论

2 S e h aT a j o l e mia o't. in i 0 4 6 C ia . h n u ini C a r n l . d, a jn3 0 5 , hn ) n T C L T
Ab t a t A a g —c l o m-l w n n r v l g e u p n , et i e g h o tc e n e l i r S sr c : s l r e s ae b o s i g a d ta ei q i me t a c ran l n t f sa k ra d r came ’ e n
as cu es ae Wi eatrl rjc ep r n e it d c da ni ol i rga migpa , hc l Oc rnt p c . t t c a poet x e ec ,nr u e na tcls nporm n l w ih o i h hh u i o - io n
mi g p o e s a e i to u e . n r c s r n r d c d
Ke r s s c y r a t c l so sa k r r c ame y wo d :t k a d; ni ol in;t c e ;e l i r o — i
天 津 港 南 疆 港 区神 华 煤 炭 码 头 ,堆 场 面 积 约
料场堆取料机的防碰撞控制研究
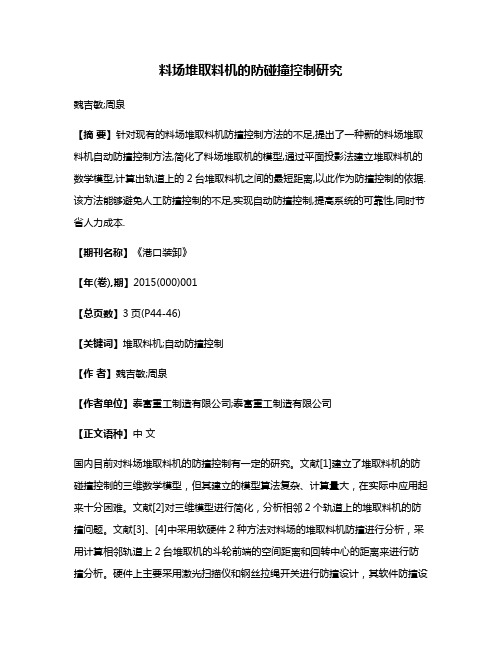
料场堆取料机的防碰撞控制研究魏吉敏;周泉【摘要】针对现有的料场堆取料机防撞控制方法的不足,提出了一种新的料场堆取料机自动防撞控制方法,简化了料场堆取机的模型,通过平面投影法建立堆取料机的数学模型,计算出轨道上的2台堆取料机之间的最短距离,以此作为防撞控制的依据.该方法能够避免人工防撞控制的不足,实现自动防撞控制,提高系统的可靠性,同时节省人力成本.【期刊名称】《港口装卸》【年(卷),期】2015(000)001【总页数】3页(P44-46)【关键词】堆取料机;自动防撞控制【作者】魏吉敏;周泉【作者单位】泰富重工制造有限公司;泰富重工制造有限公司【正文语种】中文国内目前对料场堆取料机的防撞控制有一定的研究。
文献[1]建立了堆取料机的防碰撞控制的三维数学模型,但其建立的模型算法复杂、计算量大,在实际中应用起来十分困难。
文献[2]对三维模型进行简化,分析相邻2个轨道上的堆取料机的防撞问题。
文献[3]、[4]中采用软硬件2种方法对料场的堆取料机防撞进行分析,采用计算相邻轨道上2台堆取机的斗轮前端的空间距离和回转中心的距离来进行防撞分析。
硬件上主要采用激光扫描仪和钢丝拉绳开关进行防撞设计,其软件防撞设计中将2台堆取料机斗轮之间的距离作为2台堆取料机之间的最短距离,而实际中2台堆取料机的最短距离并不是2台堆取料机斗轮与斗轮之间的距离,故该方法存在一定的缺陷。
本文对堆取料机的模型进行简化,将堆取料机投影到料场水平面,在水平面上对堆取料机的投影进行防撞分析。
本文不仅分析了相邻2个轨道上2台堆取料机的防撞,而且还对同一条轨道上相邻的2台堆取料机进行防撞分析。
对堆取料机的数学建模方法主要有三维立体模型法、平面投影法等。
下面以一个简化的料场为例,分析用平面投影法如何推导出斗轮堆取料机防撞问题的数学模型。
简化的料场中总共4条行走轨道,其示意图见图1。
以堆取料机的臂架与轨道重合方向为0度方向。
顺时针旋转的方向为正方向,逆时针旋转的方向为负方向。
网络发布版---堆取料机GNSS精确位置检测及智能防碰撞系统

1.4 本系统采用的GNSS定位技术
本系统采用在堆场合适位置建立基准站,在堆取料机的回转中心和悬臂中部或者头部中心点安装GPS流动站。通过GPS的位置信息和空间几何算法,得出两台堆取料机之间的最小距离,从而可以判断出堆取料机发生碰撞的可能性,使得作业人员进行相应处理。本系统可以实时计算出堆取料机悬臂的相对位置和距离,实现多台堆取料机在同一个场垛中安全作业。该系统包括:大机及悬臂位置反馈系统、空间数据算法系统、空间防碰撞预警控制系统。
(三) 在功能二的基础上,管理人员可以在料场的任意位置,以任意大小的面积来标注堆料状况,可以标注出堆料种类,堆料重量,堆料面积,并且可以根据需要和个人习惯,标注备注内容,设置料堆为任意颜色,方便自身的统计和监控。
(四) 可以对堆取料机之间的碰撞报警进行设置。报警分为3个档,分别为:预警,报警,急停。每个档都可以设置一个具体的报警距离(例如20米)和一个报警颜色。
1.2 目前大机采用的定位方式
目前堆取料机位置检测大多采用的是人眼定位、光电编码器装置(光码盘)、激光位移传感器、行走限位开关、RFID方式。光电编码器装置,整套装置安装在驱动电机前部的一个金属壳体内,由盘状齿轮与定位车齿条啮合,通过驱动轴驱动编码器。盘状齿轮的圆周与定位车驱动小齿轮的圆周相同。编码器由传动齿轮自下而上通过减速机、联轴节驱动,实现定位车的位置检测。这几种检测位置的方式均存在一定缺陷,具体表现如下:
2.3 GNSS定位原理
一般来说,在平面上要确定某点的位置,需要两个要素。而在空间上,要确定某点的位置,就需要三个要素。GNSS定位空间上的某一点,首先我们可以得到GPS卫星的位置;其次,我们又能准确测定我们所在地点A至卫星之间的距离,那么A点一定是位于以卫星为中心、所测得距离为半径的圆球上。进一步,我们又测得点A至另一卫星的距离,则A点一定处在前后两个圆球相交的圆环上。我们还可测与第三个卫星的距离,就可以确定A点只能是在三个圆球相交的两个点上。根据一些地理知识,可以很容易排除其中一个不合理的位置。但是由于GPS的干扰因素较多,所以定位空间上的某一点,至少需要五颗以上的卫星。
堆取料机空间防碰撞系统设计与实现

系统包括 : 大臂位置反馈 系统 、 空 间数据计 算系统 、 空间防碰撞控制系统。现在分别介绍其详细设计。 2 . 1 大臂位置反馈 系统
通常的大臂空间位置反馈都是采用行走 、 回转 、 俯仰 3 个编码器的数值计算得 出的 ,本设计采用 当
系统 一直是 个难 题 。本 文设 计 了一种 堆取 料机 空 间 防碰 撞控 制 系统 , 其原 理是 在堆 取 料机 上 的大臂
和回转中心安装 G P S 流动站。通过 G P S 的位置信息和空间几何算法, 得 出2台堆取料机之间的最小 距离, 从 而可 以判 断 出堆 取 料机发 生碰 撞 的可 能性 , 使得 工 作人 员进 行相 应处 理 , 解决 了行 走编 码器
今世界 上最 先进 的定 位手段——R T K G P S测 量系
统。R T K是能够在野外实时得到厘米级定位精度的 测量方法 , 它采用 了载波相位动态实时差分 ( R e a l —
第 1期
李长安 : 堆 取 料 机 空 间防 碰 撞 系统 设 计 与 实现
・8 l-
t i m e k i n e m a t i c ) 方法 , 是G P S应用 的重大里程碑 。高 精度的 G P S 测量 , 必须采用载波相位观测值 , R T K定 位技术就是基于载波相位观测值的实 时动态定位技 术 ,它能够实时地提供测站点在指定坐标系中的三 维定位结果 ,并达到厘米级精度 。在 R T K作业模式 下, 基准站通过数据链 , 将其观测值和测站坐标信息
1 背 景 技 术
堆 取 料作 业 过程 中 ,在 一 个 堆场 中经 常需 要使
正, 但不准确 因素仍无法彻底解决 。 ( 2 ) 对 大臂 的空 间位 置计 算 过 程非 常 复 杂 , 该计 算过程需要结合行走 、 俯仰 、 回转 3 个编码器 的数值
- 1、下载文档前请自行甄别文档内容的完整性,平台不提供额外的编辑、内容补充、找答案等附加服务。
- 2、"仅部分预览"的文档,不可在线预览部分如存在完整性等问题,可反馈申请退款(可完整预览的文档不适用该条件!)。
- 3、如文档侵犯您的权益,请联系客服反馈,我们会尽快为您处理(人工客服工作时间:9:00-18:30)。
堆取料机空间防碰撞系统设计与实现李长安(神华黄骅港务有限责任公司 河北 沧州 061113)摘 要: 在国内外煤炭码头中,堆料机、取料机是散货堆场作业的核心设备,堆取料机空间防碰撞系统一直是个难题。
设计一种堆取料机空间防碰撞控制系统,其原理是在堆取料机上的大臂和回转中心安装gps流动站,通过gps的位置信息和空间几何算法,得出两个堆取料机之间的最小距离从而可以判断出堆取料机发生碰撞的可能性,使得工作人员进行相应处理,解决行走编码器不准确、误差累积的问题。
本系统可以实时计算出堆取料机大臂的相对位置和距离,可实现两台甚至多台堆取料机在同一个场垛中安全作业。
关键词: 堆取料机;RTK系统;基准站;流动站;处理单元中图分类号:TF31 文献标识码:A 文章编号:1671-7597(2012)1110067-03全作业,严重影响效率。
故当前一般都采用人工监控的方法来1 背景技术避免空间碰撞事故。
堆取料作业过程中,在一个堆场中经常需要使用多个堆取2 具体设计方案料机进行作业。
图1为堆取料机在堆场作业的示意图,10为堆场,20为堆取料机,30为行走轨道。
在一个堆场中可能有多个笔者设计了一种堆取料机空间防碰撞系统,该系统包括:堆取料机,沿着行走轨道进行行走作业,在行走过程中,多个大臂位置反馈系统、空间数据计算系统、空间防碰撞控制系堆取料机的大臂之间有可能会发生碰撞。
统。
现在分别介绍其详细设计。
2.1 大臂位置反馈系统通常的大臂空间位置反馈都是采用行走、回转、俯仰三个编码器的数值计算得出的,本设计采用当今世界上最先进的定位手段-RTK GPS测量系统。
RTK是能够在野外实时得到厘米级定位精度的测量方法,它采用了载波相位动态实时差分(Real-time kinematic)方法,是GPS应用的重大里程碑。
高精度的GPS测量必须采用载波相位观测值,RTK定位技术就是基于载波相位观测值的实时动态定位技术,它能够实时地提供测站点在指定坐标系中的三维定位结果,并达到厘米级精度。
在RTK作业模式下,基准站通过数据链将其观测值和测站坐标信息一起传送给流动站。
流动站不仅通过数据链接收来自基准站的数据,还要采集GPS观测数据,并在系统内组成差分观测值进行实时处理,同时给出厘米级定位结果,历时不到一秒钟。
基准站的位置可以根据具体需要设置在任意位置,在本系图1 堆取料机在堆场作业的示意图统中,选取中控室安装一台基准站,每台堆取料机上安装两台目前国内包括黄骅港在内的煤炭码头中,没有有效地方法流动站,分别安装在大机回转中心点和大臂头部中心点处,流来提前预知堆取料机20之间是否将要发生碰撞,堆取料机空间防碰撞是堆取料作业过程中的难题。
具体来说,现有的防碰撞方法中需要结合堆取料机的行走数据,而现有的方法获取的堆取料机的行走数据经常不准,由于堆取料机的行走距离很长,都在1500m以上,而用于获取堆取料机的行走数据的行走编码器都安装在行走轮上,堆取料机的行走轨道与堆取料机的行走轮之间的摩擦力不均,一旦堆取料机的行走轮出现打滑现象,行走数据就会出现不准确的情况,长时间累积会造成误差越来越大,即使通过行走定点校正对编码器进行修正,但不准确因素仍无法彻底克服。
其次,对大臂的空间位置计算过程非常复杂,该计算过程需要结合行走、俯仰、回转3个编码器的数值进行空间建模,而图2 流动站在堆取料机上的安装位置示意图这3个编码器都有不同程度的误差,这就造成累积误差,故大臂在图2中,1为1号流动站,2为2号流动站。
两个流动站实时空间坐标的准确性不高。
另一种现有的防碰撞方法是根据2个堆检测空间的三维坐标信息,并通过以太网传输给中控室的取料机是否处于一个场垛进行判断,如果2个堆取料机不在同一plc主机,这样根据“两点确定一条直线”原理,中控plc就可个场垛就可以正常作业。
2个堆取料机进入一个场垛进行作业以实时的知道堆取料机的大机回转中心和堆取料机的大臂头部时,就对两个堆取料机都进行锁定,使其不能工作,由此避免中心所在轴线的位置了。
堆取料机之间发生碰撞,这严重影响了堆取料机的同场作业。
通过使用流动站和基准站来检测的大臂位置信息可以精确由于以上原因,现有的防碰撞方法无法有效避免堆取料机到厘米级,并且不受堆取料机自身行走轮打滑和其他编码器累空间防碰撞问题,使得2个堆取料机无法同时在同一个堆场中安积误差的影响,因此比现有的防碰撞方法更加准确高效。
克服了现有技术中由于大臂空间位置反馈都是采用行走、回转、俯仰三个编2.2.2 异面情况分析码器的数值计算得出的,而造成的误差累积问题。
如图4所示,在异面的情况下,求两个大臂的最小距离可2.2 空间数据计算系统以采用两条直线间计算公垂线的办法来实现,但是由于两条大空间数据计算系统的主要任务是根据采集到的各堆取料机臂的长度有限,有可能不存在公垂线,这时则需要将两条大机大臂位置信息来计算任意两台堆取料机大臂的空间最小距离。
回转中心和大臂头部中心所构成的线段延长为两条直线,求出可以通过多种方法来根据位置信息确定多个堆取料机中任意两直线的公垂线和两条大臂的交点p1、p2,首先检查交点p1有没个堆取料机的大臂之间的最小距离,由于堆取料机的大臂较有在第一堆取料机的大臂上,如果在则选定p1为第一个点,如长,两个堆取料机之间的距离可以近似看作是两个堆取料机的果不在则选择第一堆取料机的大臂头部的点A作为第一点;然后大臂之间的距离。
所以两个堆取料机之间的最小距离为:一堆检查p2点有没有在第二堆取料机的大臂上,同理如果在,则作取料机的大机回转中心和堆取料机的大臂头部中心所构成的线为第二个点,如果不在,则选中第二堆取料机的大臂头部的点段、与另一堆取料机的大机回转中心和堆取料机的大臂头部中心所构成的线段之间的最小距离。
其中当两个堆取料机的大臂共面时,最小距离为一堆取料机的大臂头部中心到另一个大机回转中心和大臂头部中心所构成的线段的垂直距离或两个堆取料机的大臂头部中心之间的最小距离;当两个堆取料机的大臂异面时,最小距离为一堆取料机的大机回转中心和堆取料机的大臂头部中心所构成的线段、与另一堆取料机的大机回转中心和堆取料机的大臂头部中心所构成的线段的公垂线段的距离或两个堆取料机的大臂头部中心之间的最小距离。
采集到各台堆取料机的位置信息后,可以通过以下过程来建立堆取料机大机回转中心和大臂头部中心所构成的线段的空间直线方程,现在以两个堆取料机为例具体介绍,两个堆取料图4 两个大机异面时的状态示意图机可以称为第一堆取料机和第二堆取料机。
2.2.3 具体算法实现设第一堆取料机的大机回转中心A和大臂头部中心B处的三根据以上原理,可以按照如下过程来确定最小距离。
维坐标分别为A(x1,y1,z1)、B(x2,y2,z2),第二堆取首先需要判断A、B、C、D四个点是否在同一个平面即共面料机的大机回转中心C和大臂头部中心D处的三维坐标分别为C还是异面,具体过程如下:(x3,y3,z3)、D(x4,y4,z4)。
也就是说通过RTK采集了计算A(x1,y1,z1)、B(x2,y2,z2)、C(x3,y3,四个点的坐标,每两个点可以确定一条线段。
根据空间立体几z3)、D(x4,y4,z4)四个点构成的四个向量AB(a1,b1,何,两条直线线段的关系有两种情况,共面和异面。
所谓共面c1)、AC(a2,b2,c2)、AD(a3,b3,c3)、CD(a4,b4,是指两条直线在一个平面内,而异面则指两条直线不在一个平c4)分别为:面内,现在分别介绍两种情况下如何两个堆取料机之间的最小公式1:AB:a1=x1-x2;b1=y1-y2;c1=z1-z2 距离。
公式2:AC:a2=x1-x3;b2=y1-y3;c2=z1-z32.2.1 共面情况分析公式3:AD:a3=x1-x4;b3=y1-y4;c3=z1-z4如图3所示,两条直线共面存在两种情况,一种是两条直公式4:CD:a4=x4-x3;b4=y4-y3;c4=z4-z3线平行,一种是两条直线相交。
两条直线平行的情况是指两个首先,需要判断A、B、C、D四个点是否处于一个平面内。
堆取料机的大臂在空间坐标中平行时的状态;而两条直线相交根据四点共面定理,若三个向量的混合积(AB,AC,AD)=0,在实际中则不能发生,因为大臂是实体,不可能出现相交的情即如果况,由于大臂的长度有限,所以在共面的情况下,除了平行,公式5:a1хb2хc3+a2хb3хc1+a3хb1хc2-a3хb2х另一个状态则是不平行,有相交的趋势。
在这两种情况下,出c1-a1хb3хc2-a2хb1хc3=0现两个堆取料机的大臂相碰撞的可能情形有以下三种:一是第则四点共面,否则,说明不共面即异面。
一堆取料机的大臂的头部碰到第二堆取料机的大臂的头部,二在判断出共面的情况下:是第一堆取料机的大臂的头部碰到第二堆取料机的大臂的上下如果左右侧部,三是第二堆取料机的大臂的头部碰到第一堆取料机公式6:(a2хa4+b2хb4+c2хc4)/(sqrt(a2х的大臂的上下左右侧部。
在共面的情况下,不可能出现两个大a2+b2хb2+c2хc2)хsqrt(a4хa4+b4хb4+c4хc4)>=0说明两个向量之间的夹角为0-90°,则第一堆取料机的大臂头部中心到第二堆取料机的大机回转中心和大臂头部中心所构成的线段有垂线。
其中sqrt()代表平方根运算。
根据两点确定一条直线原则,第二堆取料机的大臂的直线方程可以设为:公式7:(x-x3)/a4=(y-y3)/b4=(z-z3)/c4则过已知点A(x1,y1,z1)且与已知直线CD相垂直的平面的方程为:图3 两个大机共面时的状态示意图公式8:a4(x-x1)+b4(y-y1)+c4(z-z1)=0所以共面情况下算法的原理是求出一个大臂的头部中心到可以通过以上两个方程求出第二堆取料机的直线与垂直平另一个大机回转中心和大臂头部中心所构成的线段的垂直距面的交点(x5,y5,z5),所以,可以通过两点之间的距离计离,当每个大臂头部中心到另一个堆取料机的大机回转中心和算出第一堆取料机的大臂头部中心与第二堆取料机的大机回转大臂头部中心所构成的线段都没有垂线时,可直接求出两个大中心和大臂头部中心所构成的线段的距离为:臂头部中心之间的最小距离。
公式9:Dist1=sqrt((x1-x5)х(x1-x5)+(y1-y5)XCZх(y1-y5)+(z1-z5)х(z1-z5))中心与另一个公垂点的距离为两个堆取料机之间的最小距离。
否则其中,如果仅满足x1<x7<x2或x2<x7<x1,表明点p1在线段AB中计算第一堆取料机的大臂头部中心与第二堆取料机的大臂而p2不在线段CD中,则头部中心距离,即点A、C之间的距离:公式22:Mindist2= sqrt((x3-x7)х(x3-x7+(y3-公式10:Dist3= sqrt(a2хa2+b2хb2+c2хc2)y7)х(y3-y7)+(z3-z7)х(z3-z7))同理,如果如果仅满足x3<x8<x4或x4<x8<x3,表明点p1不在线段AB中公式11:(a1хa2+b1хb2+c1хc2)/(sqrt(a1х而p2在线段CD中,则a1+b1хb1+c1хc1)хsqrt(a2хa2+b2хb2+c2хc2))>=0公式23:Mindist2= sqrt((x8-x1)х(x8-x1+(y8-说明两个向量之间的夹角为0-90°,则第二堆取料机的大y1)х(y8-y1)+(z8-z1)х(z8-z1))臂头部中心到第一堆取料机的大机回转中心和大臂头部中心所如果都不在,则求出两个大臂头部中心的距离构成的线段有垂线。