磨床
磨床操作基本知识

磨床操作基本知识磨床是一种用于加工金属零件的机床,通过在磨盘上旋转的磨具加工工件以得到精确的形状和尺寸。
磨床操作需要具备一定的基本知识和技能才能保证加工的质量和效率。
以下是磨床操作的基本知识。
1.磨床结构磨床主要由磨床床身、工作台、进给装置、磨头和切削液装置等部分组成。
操作者要熟悉磨床的主要结构和各部分的功能,以保证正确操作磨床。
2.磨具选择磨具的选择应根据工件材料和加工要求来确定,磨具的选用可以影响加工效率和加工质量。
一般来说,较硬的金属材料可以选择耐磨度较好的刚玉磨头,较软的金属材料可以选择炭化硅磨头,而钢和合金材料则可选择金刚石磨头。
3.工件夹紧工件夹紧要采用夹具,确保工件牢固固定在工作台上,以避免工件在加工过程中移动或变形,从而影响加工质量。
夹紧力应适当,夹紧部位应避免影响加工表面。
4.磨头安装安装磨头前应检查磨头的状况,磨头应安装正确,并保证磨头与工作台之间的距离适当。
如有必要,应磨出磨头的新边缘,以减少加工表面上的毛刺和瑕疵。
5.进给速度和深度进给速度和深度必须适当,以确保加工表面的质量和加工效率。
进给速度过快会导致表面粗糙,进给深度过大也会影响表面质量。
每次加工时应遵循逐渐加深和逐渐减小进给量的原则。
6.切削液的使用在磨削过程中,加工表面会产生大量的热量和磨屑,应用切削液既能冷却磨床和工件,又能防止磨屑粘附在工件上,从而起到清洗和润滑的作用。
在使用切削液时,应根据切削液的类型、浓度和量来调整切削液的流量、冷却效果和清洗效果。
以上是磨床操作的基本知识,操作者应严格按照操作规程和安全规范进行磨床操作,确保加工质量和操作安全。
平面磨床操作说明
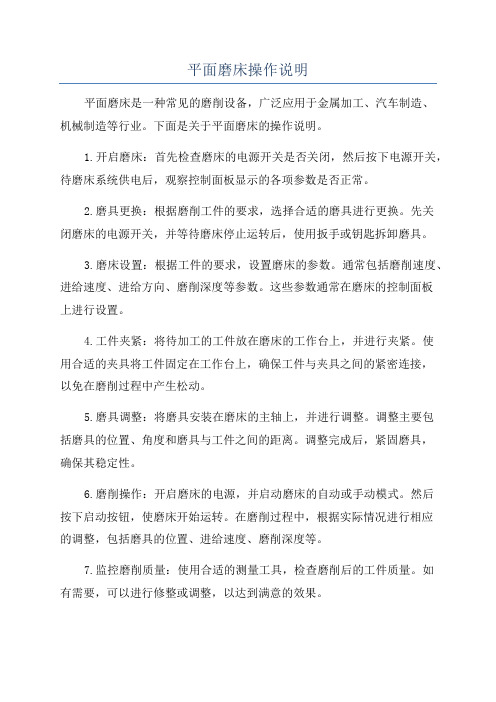
平面磨床操作说明平面磨床是一种常见的磨削设备,广泛应用于金属加工、汽车制造、机械制造等行业。
下面是关于平面磨床的操作说明。
1.开启磨床:首先检查磨床的电源开关是否关闭,然后按下电源开关,待磨床系统供电后,观察控制面板显示的各项参数是否正常。
2.磨具更换:根据磨削工件的要求,选择合适的磨具进行更换。
先关闭磨床的电源开关,并等待磨床停止运转后,使用扳手或钥匙拆卸磨具。
3.磨床设置:根据工件的要求,设置磨床的参数。
通常包括磨削速度、进给速度、进给方向、磨削深度等参数。
这些参数通常在磨床的控制面板上进行设置。
4.工件夹紧:将待加工的工件放在磨床的工作台上,并进行夹紧。
使用合适的夹具将工件固定在工作台上,确保工件与夹具之间的紧密连接,以免在磨削过程中产生松动。
5.磨具调整:将磨具安装在磨床的主轴上,并进行调整。
调整主要包括磨具的位置、角度和磨具与工件之间的距离。
调整完成后,紧固磨具,确保其稳定性。
6.磨削操作:开启磨床的电源,并启动磨床的自动或手动模式。
然后按下启动按钮,使磨床开始运转。
在磨削过程中,根据实际情况进行相应的调整,包括磨具的位置、进给速度、磨削深度等。
7.监控磨削质量:使用合适的测量工具,检查磨削后的工件质量。
如有需要,可以进行修整或调整,以达到满意的效果。
8.结束磨削:在磨削完成后,关闭磨床的电源开关,并等待磨床完全停止运转后,进行清理工作。
清理工作包括清除磨床上的碎屑、切削液等。
9.日常维护:定期对磨床进行维护保养工作。
包括清洁磨床表面、润滑磨床的移动部件、检查电器设备的正常工作等。
值得注意的是,操作平面磨床时需要遵循以下安全规范:1.佩戴适当的个人防护装备,如工作服、手套、眼镜等。
以防止磨削过程中产生的碎片对身体造成伤害。
2.严格遵守操作规程,避免在磨床运转时进行操作或接近磨床。
3.在磨削过程中,及时将磨削液集中在磨床指定的位置,避免磨削液溅在地面上。
4.在操作磨床时,不得将手部或其他物体靠近磨具或磨床的活动部件。
磨床工作原理

磨床工作原理磨床是一种用于对工件进行加工的机床,其工作原理主要是通过磨削工具对工件表面进行切削,从而达到加工的目的。
磨床工作原理的核心是磨削过程,下面将详细介绍磨床的工作原理及其相关知识。
首先,磨床的工作原理是利用磨削工具对工件进行精密的切削。
磨削工具通常是一种硬度很高的材料制成的砂轮,通过高速旋转产生的离心力和摩擦力来对工件进行磨削。
在磨削过程中,砂轮与工件表面产生相对运动,磨削掉工件表面的金属材料,从而使工件表面得到精密的加工。
其次,磨床工作原理的关键是磨削过程中的切削力和热量控制。
磨削过程中,砂轮对工件表面施加切削力,使工件表面的金属材料被切削下来。
同时,由于磨削过程中会产生大量的摩擦热,因此需要通过冷却液或者冷却系统来控制磨削区域的温度,防止工件表面因热量过大而产生变形或者损坏。
再次,磨床工作原理还涉及到磨削工具的选择和磨削参数的确定。
不同的工件材料和加工要求需要选择不同的砂轮材料和磨削参数,如磨削速度、进给速度、磨削深度等。
通过合理选择磨削工具和确定磨削参数,可以实现对工件表面的精密加工,提高加工质量和效率。
最后,磨床工作原理还包括磨床的结构和控制系统。
磨床通常由机床主体、磨削主轴、进给系统、冷却系统、磨削工具和控制系统等部件组成。
其中,控制系统是磨床的关键部件,通过对磨削参数和磨削过程的控制,实现对工件加工的精密控制。
总的来说,磨床工作原理是通过磨削工具对工件表面进行精密切削,控制切削力和热量,选择合适的磨削工具和确定磨削参数,以及通过磨床的结构和控制系统实现对工件加工的精密控制。
只有深入理解磨床的工作原理,才能更好地应用磨床进行加工,提高工件加工的精度和效率。
磨床工作原理
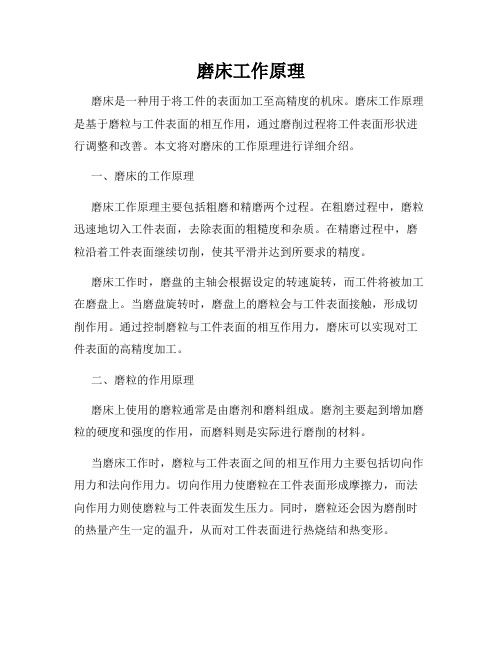
磨床工作原理磨床是一种用于将工件的表面加工至高精度的机床。
磨床工作原理是基于磨粒与工件表面的相互作用,通过磨削过程将工件表面形状进行调整和改善。
本文将对磨床的工作原理进行详细介绍。
一、磨床的工作原理磨床工作原理主要包括粗磨和精磨两个过程。
在粗磨过程中,磨粒迅速地切入工件表面,去除表面的粗糙度和杂质。
在精磨过程中,磨粒沿着工件表面继续切削,使其平滑并达到所要求的精度。
磨床工作时,磨盘的主轴会根据设定的转速旋转,而工件将被加工在磨盘上。
当磨盘旋转时,磨盘上的磨粒会与工件表面接触,形成切削作用。
通过控制磨粒与工件表面的相互作用力,磨床可以实现对工件表面的高精度加工。
二、磨粒的作用原理磨床上使用的磨粒通常是由磨剂和磨料组成。
磨剂主要起到增加磨粒的硬度和强度的作用,而磨料则是实际进行磨削的材料。
当磨床工作时,磨粒与工件表面之间的相互作用力主要包括切向作用力和法向作用力。
切向作用力使磨粒在工件表面形成摩擦力,而法向作用力则使磨粒与工件表面发生压力。
同时,磨粒还会因为磨削时的热量产生一定的温升,从而对工件表面进行热烧结和热变形。
通过控制磨粒与工件表面的相互作用力和温度,磨床能够对工件表面进行精确的修整和加工,以达到预期的加工效果。
三、影响磨床工作的因素磨床的工作效果受到多个因素的影响,以下是一些关键因素的介绍:1. 磨粒尺寸和硬度:磨粒的尺寸和硬度直接影响到磨床的加工效果。
较大尺寸的磨粒往往能够更快地去除工件表面的杂质和粗糙度,但其加工精度会相对较低;而较小尺寸的磨粒则能够获得更高的加工精度。
2. 加工速度:磨床加工速度对于加工效果至关重要。
过高的加工速度会导致工件表面过度热烧结和热变形,影响加工精度;而过低的加工速度则会使加工效率低下。
3. 磨剂与冷却液的使用:磨剂和冷却液的使用可以降低加工时产生的热量,减少磨粒与工件表面的热烧结。
同时,冷却液还能起到冷却磨床部件的作用,延长其使用寿命。
四、磨床的应用领域磨床广泛应用于航空航天、汽车制造、模具加工等行业。
磨床的特点及应用

磨床的特点及应用磨床是一种用来加工金属和非金属材料的机床。
它是利用磨粒高速旋转时对工件进行切削的加工工具。
磨床主要包括工作台、主轴、磨粒盘和运动机构等组成部分。
下面将详细介绍磨床的特点及应用。
磨床的特点:1.高精度:磨床可以实现很高的加工精度。
由于磨粒的切削方式是类似于磨削的原理,因此可以在工件表面实现非常小的加工误差,从而得到更高的精度。
2.高表面质量:磨床可以在工件表面得到很好的光洁度和平整度,可以达到亚毫米的表面粗糙度。
这对于某些对表面质量要求较高的产品非常重要。
3.加工硬材料:磨床可以加工硬度较高的材料,如高速钢、合金钢、刚石、碳化硼等。
这些材料通常难以用传统的切削机床进行加工,而磨床可以通过磨削的方式有效地加工。
4.适用性广:磨床可以加工各种不同形状和尺寸的工件,如圆柱形、圆锥形、球面形、平面形等,具有很好的灵活性和适应性。
5.适合大批量生产:磨床具有稳定的加工性能和高的加工效率,尤其适合大批量生产。
可以通过自动化设备和自动编程实现磨床的连续工作和高效率加工。
6.提高工件寿命:磨床可以通过磨削的方式修复工件表面的损伤和疲劳,提高工件的寿命和使用性能。
磨床的应用:1.模具加工:磨床在模具制造中起着重要的作用。
模具加工要求高精度和高表面质量,磨床可以满足这些要求。
模具加工通常包括精密曲面磨削、球面磨削、锥面磨削等工艺。
2.航空航天工业:磨床在航空航天工业中广泛应用。
航空航天工业对零部件的精度要求非常高,而且往往需要加工复杂的曲面和形状。
磨床可以满足这些要求,可以加工出高精度的飞机零部件和航天器零部件。
3.汽车工业:磨床是汽车工业中常用的加工设备。
汽车发动机零部件、变速器零部件、传动轴等需要高精度加工的零部件都可以通过磨床进行加工。
磨床可以提供高精度和高效率的加工,提高汽车的质量和性能。
4.机械制造工业:磨床在机械制造工业中具有广泛的应用。
例如加工轴承、滚子、齿轮等传动件,以及获得高精度的导轨、导丝杆等机械构件。
磨床的原理

磨床的原理
磨床是一种用来对工件进行精密加工的机床,它通过磨削工具对工件进行切削,以达到加工精度和表面质量要求。
磨床的原理主要包括磨削工具、工件和磨削过程三个方面。
首先,磨床的磨削工具是实现加工的关键。
磨削工具通常采用砂轮,其主要成
分是磨料和结合剂。
磨料是砂轮的主要切削部分,其硬度和尺寸决定了磨削的加工精度和表面质量。
结合剂则起到固定和支撑磨料的作用,同时也能影响砂轮的切削性能。
选择合适的磨料和结合剂,可以有效提高砂轮的加工效率和加工质量。
其次,磨床的工件是需要进行加工的对象。
工件通常是金属或非金属材料,其
形状和尺寸各异。
在磨削过程中,工件通过夹持装置固定在磨床上,然后与磨削工具接触,进行精密的切削。
磨床可以对工件进行外圆、内圆、平面、曲面等形式的加工,满足不同工件的加工需求。
最后,磨床的磨削过程是实现加工的关键环节。
在磨削过程中,磨削工具以高
速旋转,同时对工件施加一定的切削压力,使磨料与工件之间产生相对运动,从而实现切削加工。
磨削过程中,磨料不断磨损,需要及时修整或更换磨削工具,以保证加工质量和效率。
同时,磨削过程中还需要考虑冷却润滑、排屑清除等工艺措施,以保证加工的稳定性和安全性。
总的来说,磨床的原理是通过磨削工具对工件进行精密切削,实现加工精度和
表面质量的要求。
磨削工具、工件和磨削过程是磨床实现加工的三个基本要素,它们相互作用,共同完成加工任务。
通过合理选择磨削工具、合理夹持工件和合理控制磨削过程,可以实现高效、高质的磨削加工。
磨床的概念
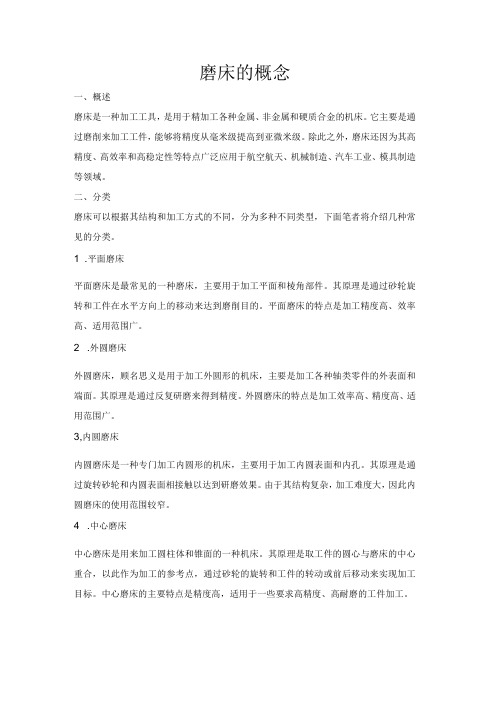
磨床的概念一、概述磨床是一种加工工具,是用于精加工各种金属、非金属和硬质合金的机床。
它主要是通过磨削来加工工件,能够将精度从毫米级提高到亚微米级。
除此之外,磨床还因为其高精度、高效率和高稳定性等特点广泛应用于航空航天、机械制造、汽车工业、模具制造等领域。
二、分类磨床可以根据其结构和加工方式的不同,分为多种不同类型,下面笔者将介绍几种常见的分类。
1 .平面磨床平面磨床是最常见的一种磨床,主要用于加工平面和棱角部件。
其原理是通过砂轮旋转和工件在水平方向上的移动来达到磨削目的。
平面磨床的特点是加工精度高、效率高、适用范围广。
2 .外圆磨床外圆磨床,顾名思义是用于加工外圆形的机床,主要是加工各种轴类零件的外表面和端面。
其原理是通过反复研磨来得到精度。
外圆磨床的特点是加工效率高、精度高、适用范围广。
3,内圆磨床内圆磨床是一种专门加工内圆形的机床,主要用于加工内圆表面和内孔。
其原理是通过旋转砂轮和内圆表面相接触以达到研磨效果。
由于其结构复杂,加工难度大,因此内圆磨床的使用范围较窄。
4 .中心磨床中心磨床是用来加工圆柱体和锥面的一种机床。
其原理是取工件的圆心与磨床的中心重合,以此作为加工的参考点,通过砂轮的旋转和工件的转动或前后移动来实现加工目标。
中心磨床的主要特点是精度高,适用于一些要求高精度、高耐磨的工件加工。
5 .齿轮磨床齿轮磨床是一种专门用来磨削齿轮及相应齿形的机床,主要用于高精度齿轮的制造。
齿轮磨床具有磨削效果好、完成度高、加工效率高等特点。
三、技术指标磨床的精度和稳定性是其最重要的两个技术指标。
其中,精度又主要包括加工精度、加工平面的平行度和垂直度、加工表面粗糙度以及精度稳定性等。
在使用磨床时,还需对其负载能力、磨削能力、磨轮直径、磨轮转速和工件旋转速度等技术指标进行了解。
四、总结磨床是一种高效、高精度、高稳定性的加工工具,可广泛应用于各个领域的制造业中。
本文主要介绍了磨床的概念、分类、特点及常见技术指标等内容,希望能对读者在了解和选择磨床时有所帮助。
磨床的用途

磨床的用途磨床是一种用于对工件进行精密磨削加工的机械设备。
它广泛应用于各个制造行业,例如机械制造、汽车制造、航空航天、电子设备等。
磨床通过磨削方法,能够对工件进行高精度的加工,使其达到预定的尺寸、形状、表面粗糙度和轮廓度要求。
磨床的主要用途有以下几个方面:1. 精密磨削磨床具有高精度、高稳定性的特点,能够对工件进行精密磨削。
它可以对各种材料的工件进行磨削加工,包括金属、非金属、硬质合金等。
通过磨床的磨削加工,可以使工件达到较高的精度要求,提高产品的质量和精度。
2. 平面磨削磨床可用于对各种平面进行磨削加工,例如平面磨床可以对平面进行加工、面磨床可用于对工件的面进行磨削加工。
这种加工方式可以使工件表面达到较高的平整度和光洁度要求,提高产品的外观质量和表面质量。
3. 内外圆磨削磨床还可用于对工件的内外圆进行磨削加工。
例如,内圆磨床可以对工件的内圆进行加工,外圆磨床可以对工件的外圆进行加工。
这种加工方式可以使工件的圆度、圆柱度和表面质量达到要求,提高产品的精度和几何形状。
4. 锥面磨削磨床还可用于对工件的锥面进行磨削加工。
例如,锥面磨床可以对工件的锥面进行加工。
这种加工方式可以使工件的锥度、圆度和表面质量达到要求,提高产品的几何形状和精度。
5. 线形磨削磨床还可用于对工件进行线形磨削加工。
例如,专用的线切割磨床可以对工件进行线形磨削,从而实现工件的线性加工。
这种加工方式可以使工件的线形精度达到要求,提高产品的线性度和几何形状。
磨床的用途非常广泛,能够对各种工件进行精密磨削加工。
它可以提高产品的精度、表面质量和几何形状,达到设计要求。
在现代制造业中,磨床已经成为不可或缺的重要设备之一。
随着科技的发展,磨床将不断提高其加工精度和效率,满足不断提高的制造要求。
- 1、下载文档前请自行甄别文档内容的完整性,平台不提供额外的编辑、内容补充、找答案等附加服务。
- 2、"仅部分预览"的文档,不可在线预览部分如存在完整性等问题,可反馈申请退款(可完整预览的文档不适用该条件!)。
- 3、如文档侵犯您的权益,请联系客服反馈,我们会尽快为您处理(人工客服工作时间:9:00-18:30)。
磨床总体布局
3.1 磨床总体设计
1.加工零件的工艺分析(表面形状,尺寸,材料,技术条件,批量,加工余量等);
2.调查研究比较国内,外同类机床,经验总结,进行改革创新;
3.图纸设计(总图,部件装配图,零件图,工艺卡,目录,标准件,外购件目录,铸件,锻件目录,说明书,装箱单,合格证);
4.制造,装配,调试;
5.小批量生产,设计改进;
3.2、总体设计注意事项
1.保证机床满足加工精度要求,刚性,稳定性好;
2.传动系统力求简短;
3.操作调整方便;
4.安全保护,冷却液供给,回收,废渣的排除。
3.3 磨床总体布局设计
3.3.1 加工零件
带轴肩的多台阶轴,精度IT7以下,Ra1.6---Ra0.4,材料45#,40cr,球墨铸铁等;
3.3.2 初步估计组成部分
a.床身;
b.工作台面;c头架;d尾架;e砂轮架;f 修整器;g 测量装置;h 砂轮进给电机;I 修整器进给电机;j 电器框;k工作台进给电机;l 工件旋转电机;m 润滑冷却装置;n数控装置;
3.3.3 总体布局初步设计
1.T型床身;
2.工作台移动;
3.工作台型面采用倾斜10°的型面;
4.砂轮架主轴与床身导轨倾斜30°角;
5.头尾架中心线平行;
6.采用成型砂轮修整器(金刚石滚轮),采用MARPPOS公司轴向,径向测量仪,配用该公司E5数控框(如图3-1所示)来控制轴向尺寸,径向尺寸,测量仪布置在横梁上;
图3-1 E5数控框
7.数控系统的四坐标轴
X轴:砂轮架进给 Y轴:修整器进给
Z轴:工作台移动 W轴:工件旋转
各轴采用交流伺服电机,通过精密无间隙弹性连轴器直接与滚珠丝杆相连;
8.液压油箱单独(减小热变形,简化机床结构,易实现标准化,通用化,便于维修);
9.电器框与机床采用空中走线;
10.机床前防护罩采用全封闭结构;
3.3.4 纵向与横向尺寸的确定
1.纵向尺寸
①工件最大长度;
②头架长度;
③尾架长度;
④上台面长度;
⑤下台面长度;
⑥床身长度;
⑦后床身长度(考虑砂轮架和修整器大小按经验给定);
⑧整个床身宽度(视觉效果);
⑨砂轮架中心与机床床身对称线相距
图3-2 磨床纵向尺寸
2.横向尺寸
1)画出横向尺寸床身的V型导轨作为横向尺寸的基准,画出床身的平面导轨作为高度尺寸的基准线,根据确定的工作台参数,导轨参数B1’,B2’中心画出左视图
2)确定上,下工作台厚度和宽度
(1)厚度:用类比法
上工作台中心(3-1)
下工作台中心(3-2)
为工作台导轨的中心距,工作台导轨选用80 75 250
>>
MKS1632A数控高速端面外圆磨床及其砂轮架设计
取 =0.3 250=75mm
=0.38 250=95mm
(2)宽度
3)确定头,尾架顶尖中心位置
顶尖中心安排在V型导轨的中心线上,这样有利于磨削最小直径工件的,砂轮架趋近于工作台不致相碰。
缺点是使导轨的承载压力较大,故常适当加宽V型导轨的宽度。
4)确定头尾架顶尖中心至床身底面的高度H1
左右
根据工人身高,经验。
类比取
5)工作台回转中心位置B9
6)确定机床总高H
所以H取2000mm。
3.3.5 砂轮架相关尺寸设计
(1)砂轮架导轨(V—平导轨)100 90 400
考虑到砂轮的大小及重量与砂轮架的稳定性,取L`中心=500mm,从而可定出砂轮架的宽度约为600mm,导轨为0.15MPa 的卸荷导轨。
图3-3 砂轮架的导轨
(2)砂轮架横向行程长度(3-4)
式中为砂轮架快速进退的行程,一般取。
此处取。
(3-5)
安全系数取0.1足够
(取373)
(3)砂轮架高度和长度
砂轮架箱体导轨的高度h3,砂轮底板滑台高度h4,砂轮中心距砂轮底面高度h5,与后床身顶面至平导轨的高度h0,为避免上,下工作台运动时与箱体相碰,安装在后床身上的垫板顶面需低于上下工作台的顶面,同时考虑横向进给机构穿过床身的位置等,根据经验
①取
②砂轮架中心距后床身顶面
③砂轮架底座安装修整器,内有传动丝杆
取
④后床身进给导轨内装丝杆
取
图3-4 砂轮架的高度和宽度
⑤砂轮架底板长度:
∴ 取 =900mm
⑥砂轮架导轨长度
∴取
(4)砂轮架主轴电机的选择
①用类比法,砂轮架主轴电机的功率取15kw;
②计算法(3-6)
取 3.3.6 头架相关尺寸的确定
①长,宽,高:440 400 411mm
②主轴锥孔:莫氏5#锥孔
③中心高:(3-7)
通过以上计算头架中心高取180mm
④主轴转速(3-8)
取
⑤交流伺服电机选择
用类比法,交流伺服电机选择IFT5076-DA(D1 18N-M)电机
>>
MKS1632A数控高速端面外圆磨床及其砂轮架设计
砂轮磨削工件需要的功率
(3-9)
交流伺服电机通过20/38的双楔齿轮带传递给工件,即
∴合格
⑥主轴不旋转,主轴靠拨盘带动旋转
3.3.7 尾架相关尺寸的确定
①5#莫氏锥孔
②中心高180mm,台面倾斜10°
③直线滚动导轨
④液压油缸,顶紧力
3.3.8 工作台
要求上,下台面便于调整头尾架,便于安装滚珠螺母。
倾斜10°以便于头尾架定位,冷却液回流;及使头尾架不等高时修刮侧面
3.3.9 横向进给机构
交流伺服电机----联轴器----滚珠丝杆----砂轮架
压力卸荷导轨压力油0.15Mpa 卸去压力
V—平导轨
砂轮架行程
3.3.10 砂轮修整器
伺服电机---丝杆---修整器
直线滚动导轨
主轴直径D=50mm,采用液体动压轴承(16r/min 6.3Mpa)
修整速度=
修整器直径故
修整器行程为160mm
3.3.11 液压系统
①修整器;②尾架;③量仪(两个);④润滑油;⑤床身导轨;⑥砂轮架卸荷导轨;⑦丝杆;⑧直线滚动导轨;⑨间歇
3.3.12 电气部分
SIMENS 810G 控制五坐标轴砂轮架主轴
3.3.13 机床保护系统
①静压供油系统压力继电器压差发讯器
液压控制器电路延时
②尾架伸缩油缸静压供油系统:设置自动循环电路,可手动,也可用于脚踏。
当工件旋转时,由于互锁装置,使起无效。
③油箱液压控制
④数控系统(在各坐标轴)自诊断与保护功能
如:电池电压低程序错误
⑤各坐标轴由行程开关控制最大位移量
⑥安全防护罩(砂轮罩,机床前罩)全封闭式
⑦导轨面保护
Ⅰ 工作台导轨:不锈钢可伸缩防护罩
Ⅱ 砂轮架导轨:㈠前部:翻板式护罩+橡皮(防水);㈡后罩:钢罩。
Ⅲ 修整器导轨:折叠式
第4章部件设计(砂轮架)
4.1 砂轮架设计的基本要求
砂轮架是磨床上用来带动砂轮作高速旋转的关键部件,主要由传动部件和主轴轴承部分组成,主轴与轴承是砂轮架的主要组成部分,因此对砂轮架设计提出的基本要求也是针对主轴轴承部分的。
砂轮架设计应满足以下几点基本要求:
1.主轴旋转精度高,旋转稳定;
2.主轴轴承系统刚性好;
3.振动小,发热低,不漏油;
4.装配制造简单,调整维修方便。
4.2 主轴旋转精度及其提高措施
1.砂轮架旋转精度是指主轴前端的径向跳动和轴向蹿动大小,它直接影响工件的表面粗糙度和表面缺陷。
一般端面外圆磨床砂轮架允许的径向和轴向跳动允许误差取5µm~~10µm。
2.提高主轴旋转精度的措施
(1)选择合适的主轴轴承:动静压轴承;
(2)提高主轴的加工精度;
(3)正确选择主轴轴向止推方式:液体静压。