电镀铜实验报告
彩色电镀铜实验报告(3篇)

第1篇一、实验目的1. 掌握彩色电镀铜的基本原理和工艺流程。
2. 了解彩色电镀铜在金属表面装饰中的应用。
3. 探究不同添加剂对彩色电镀铜效果的影响。
4. 提高电镀操作技能,培养实际操作能力。
二、实验原理彩色电镀铜是一种在金属表面形成彩色镀层的电镀工艺。
其基本原理是在电镀液中添加一定量的彩色添加剂,通过电解作用,使金属表面沉积出具有特定颜色的铜镀层。
彩色添加剂的种类和用量对镀层的颜色和性能有重要影响。
三、实验材料与仪器1. 金属基材:铁板、铜板、铝板等。
2. 电镀液:硫酸铜、硫酸、硼酸、彩色添加剂等。
3. 仪器:直流稳压电源、电解槽、电流表、电压表、计时器、搅拌器等。
四、实验步骤1. 准备电镀液:根据实验要求,配制一定浓度的硫酸铜、硫酸、硼酸溶液,并加入适量的彩色添加剂。
2. 搅拌均匀:将电镀液倒入电解槽中,用搅拌器搅拌均匀。
3. 预处理:将金属基材表面进行打磨、清洗、活化等预处理,以提高镀层的附着力。
4. 电镀:将预处理后的金属基材放入电解槽中,接通电源,调整电流和电压,进行电镀。
5. 洗涤:电镀完成后,取出金属基材,用去离子水冲洗干净。
6. 干燥:将金属基材放入干燥箱中,干燥至室温。
五、实验结果与分析1. 镀层颜色:通过改变彩色添加剂的种类和用量,可以得到不同颜色的镀层。
例如,加入适量的红色添加剂可以得到红色镀层,加入适量的蓝色添加剂可以得到蓝色镀层。
2. 镀层性能:彩色电镀铜镀层具有良好的耐腐蚀性、耐磨性和附着力。
通过调整电镀参数,可以提高镀层的性能。
3. 彩色添加剂的影响:彩色添加剂的种类和用量对镀层的颜色和性能有重要影响。
实验结果表明,适量的彩色添加剂可以提高镀层的颜色鲜艳度和耐腐蚀性。
六、实验结论1. 彩色电镀铜是一种简单、高效、经济的金属表面装饰工艺。
2. 通过调整电镀参数和彩色添加剂的种类和用量,可以得到不同颜色和性能的镀层。
3. 彩色电镀铜镀层具有良好的耐腐蚀性、耐磨性和附着力,适用于各种金属表面装饰。
电镀铜实验报告

电镀铜实验报告篇一:电镀铜--原理(参考)电镀铜原理篇电镀是指利用电解的方法从一定的电解质溶液(水溶液、非水溶液或熔盐)中,在经过处理的基体金属表面沉积各种所需性能或尺寸的连续、均匀而附着沉积的一种电化学过程的总称。
电镀所获得沉积层叫电沉积层或电镀层。
镀层的分类方法:按使用目的:防护性镀层、防护装饰性镀层和功能性镀层按电化学性质分类:阳极性镀层和阴极性镀层。
阳极性镀层:凡镀层相对于基体金属的电位为负时,镀层是阳极,称阳极性镀层,如钢上的镀锌层。
阴极性镀层:镀层相对于基体金属的电位为正时,镀层呈阴极,称阴极镀层,为阻隔型镀层,如钢上的镀镍层、镀锡层等,尽可能致密。
一、电镀的基本原理及工艺1电镀的基本原理(1)电化学发应以酸性溶液镀铜为例简述电镀过程大的的电化学反应阴极反应:Cu2++ 2e = Cu2H+ + 2e = H2阳极反应:Cu - 2e = Cu2+4OH- - 4e = 2H2O+O22、电镀液组成电镀溶液有固定的成分和含量要求,使之达到一定的化学平衡,具有所要求的电化学性能。
镀液构成:电镀液由主盐,导电盐,活化剂,缓冲剂,添加剂等组成。
电解溶液按主要放电离子存在的形式,一般可分为主要以简单(单盐)形式存在和主要以络离子(复盐)形式存在的电解液两大类。
主盐在阴极上沉淀出所要求的镀层金属的盐称为主盐。
镀液主盐的含量多少,直接影响镀层的质量。
主盐的浓度过高,则镀层粗糙;主盐浓度过低,则允许的电流密度小,电流效率明显下降,影响沉积速度,还将导致其它问题。
导电盐提高溶液导电性的盐类,增强溶液导电性,提高分散能力。
缓冲剂能使溶液pH值在一定范围内维持基本恒定的物质。
电解液中活化剂阳极活化剂,能促进阳极溶解,使镀液中镍离子得到正常补充,氯化物含量过低,阳极易钝化,过高,阳极溶解过快,镀层结晶粗糙。
络合剂能与络合主盐中的金属离子形成络合物的物质称为络合剂。
添加剂为了改善镀层的性质,可在电解液中添加少量的添加剂。
金属电镀实验报告

金属电镀实验报告摘要本实验以金属电镀为主题,通过对铜制品的电镀实验,探究了金属电镀的原理与过程。
实验结果表明,金属电镀能够有效地使金属制品表面镀上一层金属,并且能够提高金属制品的耐腐蚀性和美观度。
本实验通过详细的步骤描述和实验结果分析,为金属电镀技术的应用提供了理论和实践基础。
1. 引言金属电镀是一种将金属离子沉积到导电体表面的技术,常用于增加金属制品的耐腐蚀性和美观度。
其原理是利用电解质溶液中的金属离子在电极表面还原为金属原子,并沉积在导电体表面,形成一层金属镀层。
本实验以铜制品为例,探究铜的电镀过程。
2. 实验步骤2.1 准备实验材料和设备在实验开始前,需要准备以下材料和设备: - 铜制品 - 铜盐溶液 - 电源 - 电解槽 - 导电线 - 铜电极2.2 清洗铜制品首先,将铜制品以及铜电极清洗干净,确保其表面没有任何杂质和污垢。
可以使用溶剂或者清洁剂进行清洗,并用纯水彻底冲洗干净。
2.3 准备电解槽将电解槽中注满铜盐溶液,并确保溶液中铜离子的浓度适当。
将铜电极分别连接到电源的正负极,将铜制品通过导电线连接到电源的负极。
2.4 进行电镀将连接好的铜制品在铜盐溶液中悬浮,确保其与铜电极不接触。
打开电源,调节合适的电流和电压,开始进行电镀。
电流和电压的大小可以根据实际需要进行调整。
2.5 观察和记录在电镀过程中,观察铜制品表面的变化。
记录电镀时间、电流、电压等关键参数,并观察电镀层的厚度和均匀性。
2.6 结束电镀根据实验的要求,确定电镀的时间。
当达到预定时间后,关闭电源,取出电镀完成的铜制品。
3. 实验结果与分析根据实验步骤所描述的方法,我们进行了金属电镀实验,并观察到以下结果:•铜制品经过电镀后,表面出现明显的铜色镀层。
•铜电极上的铜离子逐渐减少,镀层逐渐增厚。
•铜制品表面的铜离子逐渐减少,与铜离子的浓度逐渐增大,使得铜原子开始沉积在铜制品表面。
实验结果表明,金属电镀实验成功地将铜离子沉积在铜制品表面,形成了一层均匀的铜镀层。
简易镀铜实验报告
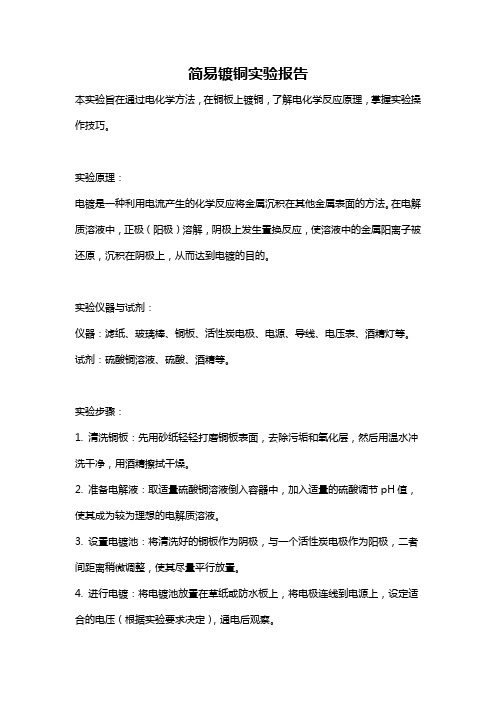
简易镀铜实验报告本实验旨在通过电化学方法,在铜板上镀铜,了解电化学反应原理,掌握实验操作技巧。
实验原理:电镀是一种利用电流产生的化学反应将金属沉积在其他金属表面的方法。
在电解质溶液中,正极(阳极)溶解,阴极上发生置换反应,使溶液中的金属阳离子被还原,沉积在阴极上,从而达到电镀的目的。
实验仪器与试剂:仪器:滤纸、玻璃棒、铜板、活性炭电极、电源、导线、电压表、酒精灯等。
试剂:硫酸铜溶液、硫酸、酒精等。
实验步骤:1. 清洗铜板:先用砂纸轻轻打磨铜板表面,去除污垢和氧化层,然后用温水冲洗干净,用酒精擦拭干燥。
2. 准备电解液:取适量硫酸铜溶液倒入容器中,加入适量的硫酸调节pH值,使其成为较为理想的电解质溶液。
3. 设置电镀池:将清洗好的铜板作为阴极,与一个活性炭电极作为阳极,二者间距离稍微调整,使其尽量平行放置。
4. 进行电镀:将电镀池放置在草纸或防水板上,将电极连线到电源上,设定适合的电压(根据实验要求决定),通电后观察。
5. 观察与分析:观察电镀过程中,铜板表面的变化,如溶解、电流大小等。
实验结果与分析:在进行电镀过程中,我们能够观察到以下现象:铜板表面开始产生气泡,并逐渐溶解,同时,电流表指针开始转动。
随着电流的注入,气泡不断释放,铜板表面的溶解速度也逐渐加快。
最终,我们可以观察到铜板表面出现了一层均匀的铜层,电流表指针停止转动。
这是因为在电解液中,硫酸铜溶液逐渐分解为铜离子和硫酸根离子,铜离子被电流带往阴极(铜板),并在阴极上发生还原反应,沉积成金属铜。
在电解液中,硫酸根离子起到稳定电解液的作用,控制电解过程。
电流的大小取决于电源电压和电解液中的离子浓度。
实验结论:通过本实验,我们成功地在铜板上进行了简易的镀铜实验。
在电解液中,电流通过铜板时,铜离子被带往阴极,发生还原反应,并沉积在铜板上,最终形成一层光滑均匀的铜层。
需要注意的是,在进行电镀实验时,应注意安全问题,避免触电和化学品溅出。
实验过程中,应正确连接电源,调节合适的电压和电流。
电镀铜实验报告
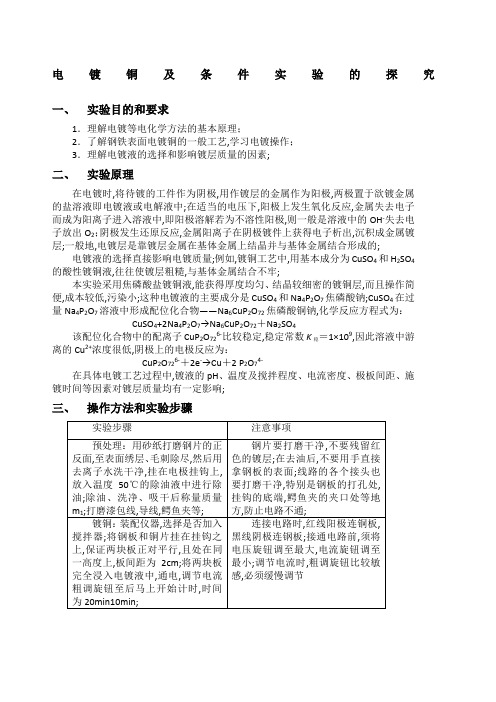
电镀铜及条件实验的探究一、实验目的和要求1.理解电镀等电化学方法的基本原理;2.了解钢铁表面电镀铜的一般工艺,学习电镀操作;3.理解电镀液的选择和影响镀层质量的因素;二、实验原理在电镀时,将待镀的工件作为阴极,用作镀层的金属作为阳极,两极置于欲镀金属的盐溶液即电镀液或电解液中;在适当的电压下,阳极上发生氧化反应,金属失去电子而成为阳离子进入溶液中,即阳极溶解若为不溶性阳极,则一般是溶液中的OH-失去电子放出O2;阴极发生还原反应,金属阳离子在阴极镀件上获得电子析出,沉积成金属镀层;一般地,电镀层是靠镀层金属在基体金属上结晶并与基体金属结合形成的;电镀液的选择直接影响电镀质量;例如,镀铜工艺中,用基本成分为CuSO4和H2SO4的酸性镀铜液,往往使镀层粗糙,与基体金属结合不牢;本实验采用焦磷酸盐镀铜液,能获得厚度均匀、结晶较细密的镀铜层,而且操作简便,成本较低,污染小;这种电镀液的主要成分是CuSO4和Na4P2O7焦磷酸钠;CuSO4在过量Na4P2O7溶液中形成配位化合物——Na6CuP2O72焦磷酸铜钠,化学反应方程式为:CuSO4+2Na4P2O7→Na6CuP2O72+Na2SO4该配位化合物中的配离子CuP2O726-比较稳定,稳定常数K稳=1×109,因此溶液中游离的Cu2+浓度很低,阴极上的电极反应为:CuP2O726-+2e-→Cu+2 P2O74-在具体电镀工艺过程中,镀液的pH、温度及搅拌程度、电流密度、极板间距、施镀时间等因素对镀层质量均有一定影响;三、操作方法和实验步骤四、数据记录与处理五、实验结果分析先分析是否搅拌这个自变量,在20min情况下,是否搅拌对镀层厚度的影响不大;估计是长时间电镀后,镀层覆盖到一定程度,不再覆盖,从镀层均匀度来看,搅拌的镀层更均匀;10min 的情况下,不搅拌的镀层厚度搅拌的镀层更厚,估计是4号钢片表面积更大,易于镀铜的关系;4组数据也说明了搅拌对镀层厚度影响不大,但是从镀层观察结果来看,搅拌后的镀层更均匀光亮;再来看时间这个自变量,4组实验总库伦量相等,20min的镀层厚度明显比10min的大,而且镀层也更均匀;六、心得顾佳辉:通过这次试验,我理解了电镀等电化学方法的基本原理,了解了钢铁表面电镀铜的一般工艺,学习电镀操作,明白了电镀液的选择和影响镀层质量的因素;准备阶段方面,对碳钢片的预处理很重要,用砂纸打磨钢片的正反面,至表面绣层、毛刺除尽,然后用去离子水洗干净,这几步我们做的很仔细;在板间距的控制上,我们在搅拌过程中很难保持每个部位都是相距2cm,只能保证中线相距2cm;另外镀层结束后对镀层观察方面,对于均匀度这样的特性,我们只能通过肉眼观察,难免有较大误差,最好可以用专门的仪器来判定;此实验通过控制变量的方法,研究单一变量对电镀效果的影响;在实验过程中,我认为有两点需要改进的地方;其一是该实验作为分析实验,需要数据的精确性,但是因为本实验中质量差最大为,只精确到的数据不足以显示出其变量改变后对镀层厚度的影响,应该使用更高精度的测重仪器;同时镀铜过程实际镀层覆盖六个表面积,但是计算过程只考虑了两个,也会造成误差;其二是四次实验分两组由不同的操作者在不同的仪器上完成,尽管电镀液混合过,但是仪器本身有所差别,操作者也有差别,会导致实验数据不准;综上,本次试验结论有待考究,结合以上两点改进后实验数据会更加精确;万舜:这次“电镀铜及条件实验的探究”实验;实验的原理我们在化学课程中早已学习过,但是在实际的电镀工业中,考虑到镀层的光滑程度以及牢固度,所以我们选用的不是基本成分为CuSO4和H2SO4的酸性镀铜液,而是焦磷酸盐镀铜液,这样能获得厚度均匀、结晶较细密的镀铜层;在实验操作方面,预处理阶段非常关键,直接关乎到整个实验的成功与否;所以打磨,清洗,去油等处理都需要很细心的去做;由于我们是要探讨不同条件下电镀的效果差异,所以我们需要与另一个小组保持其余条件的一致,所以电镀液需要实现进行混合平分;在电镀过程中,由于需要将钢板和铜片完全浸没在电镀液中,所以我们无法观察到电镀过程中的每一个变化;而且我们的比较的变量中有一个是是否搅拌,所以为了让数据更我说服力,我们最好是和另一个组同步搅拌速率;最后称重,计算镀层厚度时,我们所做的两个数据结果非常接近,而另一组的结果相差则比较大;我觉的最终的原因应该是空气天平的灵敏度不够,达不到实验的精度要求,这一点在我们称量镀铜后的钢板质量时就可以发现了,两次质量差仅有或,质量产生的误差可能就达到了50%;再就是我们计算钢板表面积时,只计算了上下两个表面,没有加上侧面积,也没有减去打孔的面积,但是表面积引起的相对误差较小;最后观察镀层时,虽然正反两面差距都不大,但是仍可以观察到,搅拌过的那组两面的镀层均匀程度更接近;这个实验不但让我直接了解并操作了电镀铜的工序,也让我重温了电路的连接,更重要的是可以探究不同条件下对镀层质量的影响;。
铁上镀铜实验报告(3篇)

第1篇一、实验目的1. 了解铁上镀铜的原理和方法。
2. 掌握电镀工艺的基本步骤和注意事项。
3. 掌握电镀设备的操作方法。
4. 通过实验,提高动手能力和实验技能。
二、实验原理铁上镀铜是一种电镀工艺,利用电解质溶液中的铜离子在铁表面还原沉积,形成一层铜膜。
电镀过程中,铁作为阴极,铜作为阳极,电解质溶液通常为硫酸铜溶液。
三、实验材料与仪器1. 实验材料:铁片、硫酸铜溶液、电流表、电源、烧杯、玻璃棒、砂纸、胶布等。
2. 实验仪器:电镀槽、直流电源、电镀电源、电镀夹具、量筒、pH试纸等。
四、实验步骤1. 准备工作:将铁片用砂纸打磨干净,去除表面油污和氧化层,并用胶布固定在电镀夹具上。
2. 配制硫酸铜溶液:按照实验要求,准确量取一定量的硫酸铜固体,加入适量的去离子水,搅拌均匀,配制成一定浓度的硫酸铜溶液。
3. 调节pH值:使用pH试纸检测硫酸铜溶液的pH值,根据需要加入适量的稀硫酸或稀氢氧化钠溶液,调节pH值至适当范围。
4. 电镀:将铁片放入电镀槽中,将铜片作为阳极,插入硫酸铜溶液中,连接好电源,调节电流至实验要求。
5. 镀层形成:保持电流稳定,电镀一段时间后,观察铁片表面是否形成均匀的铜膜。
6. 清洗与干燥:电镀完成后,关闭电源,取出铁片,用去离子水冲洗干净,晾干。
五、实验结果与分析1. 实验结果:通过电镀实验,铁片表面成功形成了均匀的铜膜,镀层厚度适中,表面光滑。
2. 结果分析:电镀过程中,硫酸铜溶液中的铜离子在铁表面还原沉积,形成铜膜。
电流密度、温度、时间等因素对镀层质量有较大影响。
在本实验中,通过合理控制电流密度、温度和时间等参数,成功实现了铁上镀铜。
六、实验结论1. 铁上镀铜实验成功,证明了电镀工艺在金属表面处理中的应用价值。
2. 通过实验,掌握了电镀工艺的基本步骤和注意事项,提高了动手能力和实验技能。
七、实验注意事项1. 实验过程中,注意安全,防止触电和烫伤。
2. 配制硫酸铜溶液时,要准确量取硫酸铜固体,避免溶液浓度过高或过低。
电镀铜粒及铜丝模拟报告

试验结论(一)
5. 不导电物质(火山灰,手套毛,污垢)出现凹 痕,导电物质阳极泥出现严重铜粒,显影液出 现剥离现象。出现铜粒只有阳极泥,但从PP线 倒缸的状态来看,抽走药水后铜缸缸底极少阳 极泥,倒缸后仍然出现厚背板铜粒问题,说明 PP线的阳极泥造成铜粒的可能性较小
试验结论(二)
1. 存板放中的尘粒在板中的结合力较差,经过PP前处理后 基本去除,不会造成铜粒问题
PPTH试验
1. 跟进DR用砂纸打磨板做PTH及PPTH后出 现铜粒问题
问题
1. 钻孔后出披锋,DR工序用砂纸打磨造成 PTH产生铜粒
2. PTH有铜粒用砂纸打磨造成PP产生铜粒
砂纸打磨是造成铜粒及铜丝的罪该祸首 如何才能不用砂纸打磨,请大家献策!
不同电流密度的影响(10ASF )
不同电流密度的影响(15ASF )
不同电流密度的影响(20ASF )
BACK
不同光亮剂含量的影响( 0.5 ml/L )
不同光亮剂含量的影响( 1.0 ml/L )
不同光亮剂含量的影响( 1.5 ml/L )
不同光亮剂含量的影响( 2.0 ml/L )
2. ODF 1#磨板用2.4mm板厚的板不同磨板参数磨板不会 造成板面铜粒问题
3. 目前我司两次PTH过程不会造成板面铜粒问题 4. 经过砂纸磨板后用不同磨板机磨板在PP后出现严重的铜
粒及铜丝现象,从PTH反映来看厚背板多数有砂纸打磨 流程。说明造成板面铜粒及铜丝的为砂纸打磨造成的 5. 经砂纸打磨后的板在3#PP及5#PP都出现铜粒及铜丝 问题
BACK
PPTH后用砂纸打磨后用不同磨板机处理 对镀铜的影响(IS机)63X
PPTH后用砂纸打磨后用不同磨板机处理对镀 铜的影响(IS机+1#磨板机)63X
电镀铜 化学实验报告
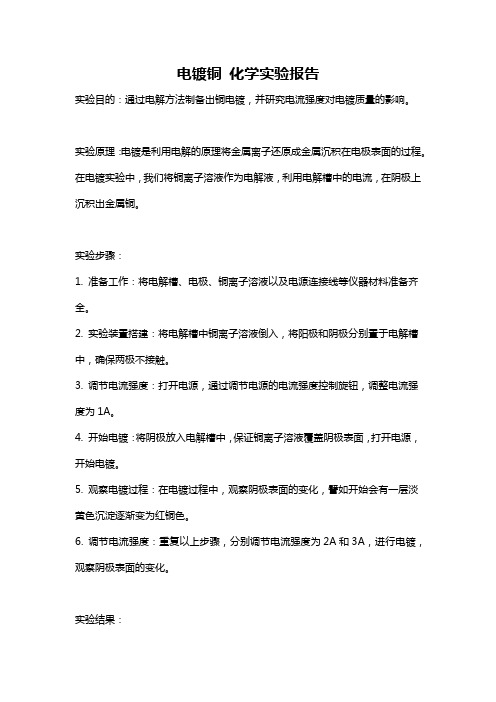
电镀铜化学实验报告实验目的:通过电解方法制备出铜电镀,并研究电流强度对电镀质量的影响。
实验原理:电镀是利用电解的原理将金属离子还原成金属沉积在电极表面的过程。
在电镀实验中,我们将铜离子溶液作为电解液,利用电解槽中的电流,在阴极上沉积出金属铜。
实验步骤:1. 准备工作:将电解槽、电极、铜离子溶液以及电源连接线等仪器材料准备齐全。
2. 实验装置搭建:将电解槽中铜离子溶液倒入,将阳极和阴极分别置于电解槽中,确保两极不接触。
3. 调节电流强度:打开电源,通过调节电源的电流强度控制旋钮,调整电流强度为1A。
4. 开始电镀:将阴极放入电解槽中,保证铜离子溶液覆盖阴极表面,打开电源,开始电镀。
5. 观察电镀过程:在电镀过程中,观察阴极表面的变化,譬如开始会有一层淡黄色沉淀逐渐变为红铜色。
6. 调节电流强度:重复以上步骤,分别调节电流强度为2A和3A,进行电镀,观察阴极表面的变化。
实验结果:在1A电流强度下电镀,电镀时间为30分钟,阴极表面形成了一层均匀的红铜沉淀。
电镀质量较好。
在2A电流强度下电镀,电镀时间为30分钟,阴极表面形成了一层红铜沉淀,但表面不均匀,有一些凸起和凹陷。
在3A电流强度下电镀,电镀时间为30分钟,阴极表面形成了一层厚厚的红铜沉淀,但表面非常不均匀,有较多的凹陷和坑洞。
实验分析:通过上述实验结果可以看出,电流强度对电镀质量有影响。
在1A电流强度下,电镀质量较好,铜沉淀均匀。
随着电流强度的增加,电镀质量变差,表面变得不均匀,出现凸起和凹陷。
这是因为较低的电流强度有利于离子的均匀分布和沉积,而较高的电流强度则促进了不均匀的沉积。
此外,较高的电流强度会导致阴极温度升高,使电镀质量更加不稳定。
结论:通过本次实验,我们成功制备了铜电镀,并发现电流强度对电镀质量有明显的影响。
较低的电流强度有利于获得均匀的电镀层,而较高的电流强度会使电镀质量变差。
因此,在实际应用中,需要根据所需电镀质量的要求来选择适当的电流强度。
- 1、下载文档前请自行甄别文档内容的完整性,平台不提供额外的编辑、内容补充、找答案等附加服务。
- 2、"仅部分预览"的文档,不可在线预览部分如存在完整性等问题,可反馈申请退款(可完整预览的文档不适用该条件!)。
- 3、如文档侵犯您的权益,请联系客服反馈,我们会尽快为您处理(人工客服工作时间:9:00-18:30)。
电镀铜实验报告篇一:电镀铜--原理(参考)电镀铜原理篇电镀是指利用电解的方法从一定的电解质溶液(水溶液、非水溶液或熔盐)中,在经过处理的基体金属表面沉积各种所需性能或尺寸的连续、均匀而附着沉积的一种电化学过程的总称。
电镀所获得沉积层叫电沉积层或电镀层。
镀层的分类方法:按使用目的:防护性镀层、防护装饰性镀层和功能性镀层按电化学性质分类:阳极性镀层和阴极性镀层。
阳极性镀层:凡镀层相对于基体金属的电位为负时,镀层是阳极,称阳极性镀层,如钢上的镀锌层。
阴极性镀层:镀层相对于基体金属的电位为正时,镀层呈阴极,称阴极镀层,为阻隔型镀层,如钢上的镀镍层、镀锡层等,尽可能致密。
一、电镀的基本原理及工艺1电镀的基本原理(1)电化学发应以酸性溶液镀铜为例简述电镀过程大的的电化学反应阴极反应:Cu2++ 2e = Cu2H+ + 2e = H2阳极反应:Cu - 2e = Cu2+4OH- - 4e = 2H2O+O22、电镀液组成电镀溶液有固定的成分和含量要求,使之达到一定的化学平衡,具有所要求的电化学性能。
镀液构成:电镀液由主盐,导电盐,活化剂,缓冲剂,添加剂等组成。
电解溶液按主要放电离子存在的形式,一般可分为主要以简单(单盐)形式存在和主要以络离子(复盐)形式存在的电解液两大类。
主盐在阴极上沉淀出所要求的镀层金属的盐称为主盐。
镀液主盐的含量多少,直接影响镀层的质量。
主盐的浓度过高,则镀层粗糙;主盐浓度过低,则允许的电流密度小,电流效率明显下降,影响沉积速度,还将导致其它问题。
导电盐提高溶液导电性的盐类,增强溶液导电性,提高分散能力。
缓冲剂能使溶液pH值在一定范围内维持基本恒定的物质。
电解液中活化剂阳极活化剂,能促进阳极溶解,使镀液中镍离子得到正常补充,氯化物含量过低,阳极易钝化,过高,阳极溶解过快,镀层结晶粗糙。
络合剂能与络合主盐中的金属离子形成络合物的物质称为络合剂。
添加剂为了改善镀层的性质,可在电解液中添加少量的添加剂。
添加剂在电解液中不能改变电解液的性质,单能显著改善镀层的性质。
光亮剂:使镀层光亮。
整平剂:能使镀件微观谷处获得微观峰处更厚的镀层。
湿润剂:能降低电极溶液间的界面张力,使溶液易于在电极表面铺展。
镀层细化剂:能使镀层结晶细致篇二:电镀铜粒跟进报告铜粒不良专项改善立项及阶段性完成时间表表Step 1介定问题(A)目的:改善铜粒不良,搜集产品不良图片及现场不良现象,根据不良图片及现场现象层别查找不良产生真因并制定相对改善措施,提升产品合格率。
(B)小组人员介定:组长:ME:(主任/将旭锋)主要负责人:ME:(工程师/郭海涵)、PROD:(主管/李东)成员:ME:(工程师/曹新建)、建鹏供应商:(刘柳)、贝加尔供应商:(吴新忠)(C)背景及主要不良体现:铜粒不良主要体现在XX年02月-04月近3个月,因铜粒不良产生频率较高,导致成本偏高,影响产能效率及人员效率,以及直接导致产生报废不良。
Step 2目前状况与目标值地址:江苏省常熟市东南经济开发区黄浦江路72号电话:8 传真:8Step 3现场排查及制定改善措施:收集现场不良现象并对现场不良现象制定相对的改善措施逐步改善,并统计各种改善措施执行后的不良数据,分析此改善措施执行后对产品良率的提升比率% ,验证改善措施的有效性。
Step 4实施改善后(1个月)的数据收集地址:江苏省常熟市东南经济开发区黄浦江路72号电话:8 传真:8 Step 5实施改善后的效果确定及再次原因分析:针对以上排查中的6项怀疑点逐步改善后,至4月25日铜粒不良基本已消失,但在每个周末的1-2天,不固定的偶尔会出现个别铜缸产生轻微铜粒不良, 按改善要求要求针对该铜缸进行拖缸电解后,铜粒会立即随应消失。
以此现象分析确定前期铜粒不良的主要原因为:4月份以前因电镀工序产量压力较大 ,没有足够的时间对电镀工序进行周保养及月保养所导致每次添加铜球后拖缸电解保养不足及时间不足,铜缸内有机物及铜球本身携带的磷杂质未能在电解过程中有效处理, 残留于电镀槽液内,生产正常电镀过程中附著与板面而产生铜粒不良。
Step 6预防措施将以上改善中的6项改善措施经再次细化后,作为长期的改善预防措施并程序化,加入受控程序文件《WI》保养要求内。
Step 7改善措施标准文件化更改修订受控程序文件《WI》修订内容如下:①、自来水洗过滤芯更换频率由原来未介定更换频率现介定为:3天更换一次;以便保证水洗的清洁度②、新铜球补加前处理时,取消双氧水的使用,改为用3~5%的稀硫酸溶液浸泡30~90分钟③、补加铜球后和保养后要求用10ASF电流密度拖缸2小时、20ASF 电流密度拖缸2小时后方可生产。
④、后续尾数板要求用其它型号±1〃范围内铜厚要求相同的用其它型号板子补充为满缸再进行生产,以及边条竖上并不可重复使用,且不可空夹子(备注:其它两项改善动作:在前期的文件中已有相应的规定无须再做更改)Step 8最终数据总结4月至5月最近10W铜粒不良报废数据及报废趋势:(13-17周为改善前18-22周为改善后)地址:江苏省常熟市东南经济开发区黄浦江路72号电话:8 传真:8②、专案改善前1个月与改善后1个月的报废数据对比:(报废率由每W的实际报废%计算,数据来源与MRB的报废数据)Step 10结论:自5月份改善专项实施后,铜粒专项合格率在4月份基础上提升39.47%,铜粒不良报废趋势同步处于直线下降趋势,由此数据证明铜粒改善专案在推行和实施过程中确定有效并可达到前期的预期效果,但对铜粒不良仍不能完全杜绝。
如须杜绝此类不良,就目前工艺条件而言还有很大差距,必须对现有设备和工艺条件进行相对调整。
地址:江苏省常熟市东南经济开发区黄浦江路72号电话:8 传真:8篇三:电镀铜的性能分析和影响因素电镀铜的性能分析及影响因素(作者)摘要:关键词:英文摘要:0 绪论? 电镀概述电镀是金属的化学和电化学防护方法的发展。
它是一种电化学过程,也是一种氧化还原过程。
通过这种电化学过程,使金属或非金属工件的表面上再沉积一层金属的方法就叫做电镀。
采用适当的工艺可以在金属或非金属工件的表面上获得所需要的不同种类的镀层,在国民经济的各个生产和科学发展领域里,如机械、无线电、仪表、交通、航空及船舶工业中,在日用品的生产和医疗器械等设备的制造中,金属镀层都有极为广泛而应用。
世界各国由于钢铁所造成的损失数据是相当惊人的,几乎每年钢铁产量的,三分之一由于腐蚀而报废,当然电镀层不可能完全解决这个问题,但是良好的金属镀层还是能在这方面做出较大贡献的。
电镀则是获得金属防护层的有效方法。
电镀方法所得到的金属镀层,结晶细致紧密,结合力良好,它不但具有良好的防腐性能,而且满足工业某些特殊用途。
? 电镀的优缺点电镀具有其不能为化学镀代替的优点:(1)可以沉积的金属及合金品种远多于化学镀。
(2)价格比化学镀低得多。
(3)工艺成熟,镀液简单、易于控制。
尽管如此,电镀也有其自身的缺点:电镀只能在导体表面上进行,其结合力一般不及化学镀? 电镀铜的应用领域铜具有良好的导电、导热性能,质软而韧,有良好的压延性和抛光性能。
为了提高表面镀层和基体金属的结合力,铜镀层常用作防护、装饰性镀层的底层,对局部渗碳工件,常用镀铜来保护不需要渗碳的部位。
1)铜箔粗化处理铜箔是制造印制板的关键导电材料,但是印制板外层铜箔毛面在与绝缘基板压合制造覆铜板之前必须经过电镀铜粗化处理,使之具有一定的表面粗糙度,才能保证与基板有足够的粘合力。
铜箔的粗化处理通常分 2 步:一是在较低铜离子浓度高电流密度下的粗化处理,二是在高铜离子浓度低电流密度下的固化处理。
粗化处理过程中必须使用特殊的添加剂,否则铜箔在高温层压制造覆铜板时会出现“铜粉转移”现象,影响与基板的结合力,严重时会使线路从基板上脱落。
在制造多层线路板时,内层铜箔也需要进行强化处理。
传统的内层铜箔使用黑化处理方法,但是黑化方法产生的氧化铜会在后续过程中产生空洞,造成层间互连可靠性降低。
有日本研究人员采用在酸性硫酸盐电镀铜溶液中添加苯并喹啉系列有机物作为添加剂,并改变溶液中的酸铜比和操作条件对内层铜箔进行处理,避免了“空洞”现象的发生。
2) PCB 制作PCB 微孔制作印制板上的小孔具有至关重要的作用,通过它不仅可以实现印制板各层之间的电气互连,还可以实现高密度布线。
一张印制板上常常具有成千上万个小孔,有的多达数万个甚至十万个。
在这些孔中不仅有贯通于各层之间的导通孔,还有位于印制板表层的盲孔和位于内部的埋孔,而且孔径大小不一,位置各异。
因此,孔内铜金属化的质量就成为决定印制板层间电气互连的关键。
传统的印制板孔金属化工艺主要分2步:一是通过化学镀铜工艺在钻孔上形成一层导电薄层(厚度一般为 0.5 μm),二是在已经形成的化学镀铜层上再电镀一层较厚的铜层(20 μm 左右)。
但是化学镀铜层存在以下问题:(1)镀速比较慢,生产效率低,镀液不稳定,维护严格;(2)使用甲醛为还原剂,是潜在的致癌物质且操作条件差;(3)使用的 EDTA 等螯合剂给废水处理带来困难;(4)化学镀铜层和电镀层的致密性和延展性不同,热膨胀系数不同,在特定条件下受到热冲击时容易分层、起泡,对孔的可靠性造成威胁。
基于以上几点,人们开发出了不使用化学镀铜而直接进行电镀铜的工艺。
该方法是在经过特殊的前处理后直接进行电镀铜,简化了操作程序。
随着人们环保意识的增强,又由于化学镀铜工艺存在种种问题,化学镀铜必将会被直接电镀铜工艺所取代。
PCB 电路图形制作除了印制板的孔金属化工艺用到电镀铜技术外,在印制板形成线路工艺中也用到电镀铜。
一种是整板电镀,另外一种是图形电镀。
整板电镀是在孔金属化后,把整块印制板作为阴极,通过电镀铜层加厚,然后通过蚀刻的方法形成电路图形,防止因化学镀铜层太薄被后续工艺蚀刻掉而造成产品报废。
图形电镀则是采取把线路图形之外部分掩蔽,而对线路图形进行电镀铜层加厚。
制造比较复杂的电路常常把整板电镀与图形电镀结合起来使用。
3) IC 封装技术的应用电镀铜在电子封装上应用的也比较多。
例如 BGA,μBGA 等封装体的封装基板布线及层间的互连(通过电镀铜填充盲孔)都要用到电镀铜技术[3]。
又如,IC封装载板越来越多地采用 COF (Chip On Flexible printedboard) 的形式,也称为覆晶薄膜载板。
该载板是高密度多层挠性印制板,也是通过电镀铜来实现布线及互连。
因为铜镀层具有良好的导电、导热性,倒装芯片FC (Flip Chip) 载板上的电极凸点先经电镀铜形成凸点后接着电镀金膜,最后再与芯片上的铝电极相连接。
4)超大规模集成电路芯片(ULSI 芯片)中铜互连目前,ULSI 中电子器件的特征线宽已由微米级降低到亚微米级,并且有不断降低的趋势。