经蚀刻腐蚀
蚀刻的原理

蚀刻的原理蚀刻是一种常见的加工方法,它通过化学腐蚀或电化学腐蚀的方式,在材料表面形成微小的凹槽或图案。
蚀刻技术被广泛应用于半导体制造、微电子器件制造、光刻制程等领域。
蚀刻的原理是通过控制腐蚀剂的浓度、温度、时间和腐蚀速率等参数,使得材料表面的特定部分被腐蚀,从而实现对材料的加工和改性。
蚀刻的原理可以分为化学蚀刻和电化学蚀刻两种方式。
化学蚀刻是指利用化学腐蚀剂对材料表面进行腐蚀,常用的蚀刻剂有酸、碱、氧化剂等。
在化学蚀刻中,腐蚀剂与材料表面发生化学反应,使得材料表面被腐蚀,形成所需的结构或图案。
而电化学蚀刻则是利用电化学腐蚀的原理,通过在腐蚀过程中加入电场或电流,控制腐蚀速率和腐蚀位置,实现对材料的加工和改性。
蚀刻的原理基于材料的化学性质和电化学性质。
不同的材料对不同的腐蚀剂表现出不同的腐蚀性能,这取决于材料的晶体结构、晶界、晶格缺陷等因素。
在蚀刻过程中,腐蚀剂与材料表面发生化学反应,使得材料表面被腐蚀,形成所需的结构或图案。
同时,电化学蚀刻还涉及到电化学反应和电极过程,通过控制电场或电流的作用,可以实现对材料表面的精确加工和改性。
蚀刻的原理还与腐蚀剂的选择、浓度、温度、腐蚀时间等参数密切相关。
不同的腐蚀剂对材料的腐蚀速率和腐蚀位置有不同的影响,因此在蚀刻过程中需要精确控制腐蚀剂的浓度和温度,以及腐蚀时间,从而实现对材料的精确加工和改性。
总的来说,蚀刻的原理是通过化学腐蚀或电化学腐蚀的方式,在材料表面形成微小的凹槽或图案,实现对材料的加工和改性。
蚀刻技术在微纳加工、半导体制造、光刻制程等领域有着重要的应用,对于制备微小结构和器件具有重要意义。
深入理解蚀刻的原理,对于提高蚀刻技术的精度和效率,具有重要的理论和实际意义。
Metal Corrosion
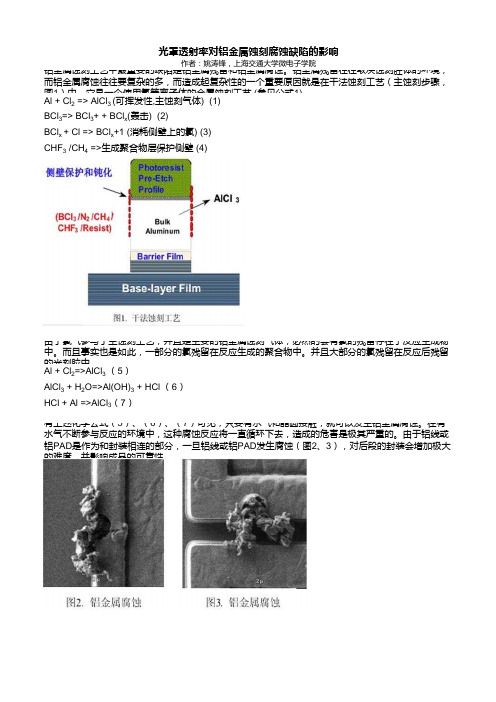
所以不同的透射率的产品在铝金属蚀刻时,同样的铝金属腐蚀,但是引起腐蚀的原因是不同的。我们 要针分对析低出透正射确率的的成产因品,,并主采要取防相止应的得是措过施量。 侧壁聚合物的生成,可采取的措施有: 1)降低偏置射频功率,从而减少侧壁聚合物的生成。 2) 减少光刻胶的厚度,保证刻蚀后光刻胶残留的条件下,减少侧壁聚合物的生成。 3) 减少CHF3 /CH4等气体的流量,从而减少侧壁聚合物的生成。 4) 减少过蚀刻(Over Etch)时间,从而减少侧壁聚合物的生成,但要保证足够的氧化层损耗。 针对高透射率的产品,主要防止的是侧壁钝化的不足,即增加聚合物的生成,可采取的措施有: 1) 增加光刻胶的厚度,增加侧壁聚合物的生成。 2) 增加CHF3 /CH4等气体的流量,从而增加侧壁聚合物的生成。 3) 增加过蚀刻(Over Etch)时间,增加侧壁聚合物的生成。 结论
蚀刻用腐蚀液与配方比例

蚀刻用腐蚀液与配方比例Document number:WTWYT-WYWY-BTGTT-YTTYU-2018GT刻蚀基础(转载)湿式蚀刻技术最早的蚀刻技术是利用特定的溶液与薄膜间所进行的化学反应来去除薄膜未被光阻覆盖的部分,而达到蚀刻的目的,这种蚀刻方式也就是所谓的湿式蚀刻。
因为湿式蚀刻是利用化学反应来进行薄膜的去除,而化学反应本身不具方向性,因此湿式蚀刻过程为等向性,一般而言此方式不足以定义3微米以下的线宽,但对于3微米以上的线宽定义湿式蚀刻仍然为一可选择采用的技术。
湿式蚀刻之所以在微电子制作过程中被广泛的采用乃由于其具有低成本、高可靠性、高产能及优越的蚀刻选择比等优点。
但相对于干式蚀刻,除了无法定义较细的线宽外,湿式蚀刻仍有以下的缺点:1)需花费较高成本的反应溶液及去离子水;2)化学药品处理时人员所遭遇的安全问题;3)光阻附着性问题;4)气泡形成及化学蚀刻液无法完全与晶圆表面接触所造成的不完全及不均匀的蚀刻;5)废气及潜在的爆炸性。
湿式蚀刻过程可分为三个步骤:1)化学蚀刻液扩散至待蚀刻材料之表面;2)蚀刻液与待蚀刻材料发生化学反应;3)反应后之产物从蚀刻材料之表面扩散至溶液中,并随溶液排出(3)。
三个步骤中进行最慢者为速率控制步骤,也就是说该步骤的反应速率即为整个反应之速率。
大部份的蚀刻过程包含了一个或多个化学反应步骤,各种形态的反应都有可能发生,但常遇到的反应是将待蚀刻层表面先予以氧化,再将此氧化层溶解,并随溶液排出,如此反复进行以达到蚀刻的效果。
如蚀刻硅、铝时即是利用此种化学反应方式。
湿式蚀刻的速率通常可藉由改变溶液浓度及温度予以控制。
溶液浓度可改变反应物质到达及离开待蚀刻物表面的速率,一般而言,当溶液浓度增加时,蚀刻速率将会提高。
而提高溶液温度可加速化学反应速率,进而加速蚀刻速率。
除了溶液的选用外,选择适用的屏蔽物质亦是十分重要的,它必须与待蚀刻材料表面有很好的附着性、并能承受蚀刻溶液的侵蚀且稳定而不变质。
蚀刻工艺(酸性、碱性、微蚀)

PCB外层电路的蚀刻工艺在印制电路加工中﹐氨性蚀刻是一个较为精细和覆杂的化学反应过程, 却又是一项易于进行的工作。
只要工艺上达至调通﹐就可以进行连续性的生产, 但关键是开机以后就必需保持连续的工作状态﹐不适宜断断续续地生产。
蚀刻工艺对设备状态的依赖性极大, 故必需时刻使设备保持在良好的状态。
目前﹐无论使用何种蚀刻液﹐都必须使用高压喷淋﹐而为了获得较整齐的侧边线条和高质量的蚀刻效果﹐对喷嘴的结构和喷淋方式的选择都必须更为严格。
对于优良侧面效果的制造方式﹐外界均有不同的理论、设计方式和设备结构的研究, 而这些理论却往往是人相径庭的。
但是, 有一条最基本的原则已被公认并经化学机理分析证实﹐就是尽速让金属表面不断地接触新鲜的蚀刻液。
在氨性蚀刻中﹐假定所有参数不变﹐那么蚀刻的速率将主要由蚀刻液中的氨(NH3)来决定。
因此, 使用新鲜溶液与蚀刻表面相互作用﹐其主要目的有两个﹕冲掉刚产生的铜离子及不断为进行反应供应所需要的氨(NH3)。
在印制电路工业的传统知识里﹐特别是印制电路原料的供货商们皆认同﹐并得经验证实﹐氨性蚀刻液中的一价铜离子含量越低﹐反应速度就越快。
事实上﹐许多的氨性蚀刻液产品都含有价铜离子的特殊配位基(一些复杂的溶剂)﹐其作用是降低一价铜离子(产品具有高反应能力的技术秘诀)﹐可见一价铜离子的影响是不小的。
将一价铜由5000ppm降至50ppm, 蚀刻速率即提高一倍以上。
由于在蚀刻反应的过程中会生成大量的一价铜离子, 而一价铜离子又总是与氨的络合基紧紧的结合在一起﹐所以要保持其含量近于零是十分困难的。
而采用喷淋的方式却可以达到通过大气中氧的作用将一价铜转换成二价铜, 并去除一价铜, 这就是需要将空气通入蚀刻箱的一个功能性的原因。
但是如果空气太多﹐又会加速溶液中的氨的损失而使PH值下降﹐使蚀刻速率降低。
氨在溶液中的变化量也是需要加以控制的, 有一些用户采用将纯氨通入蚀刻储液槽的做法, 但这样做必须加一套PH计控制系统, 当自动监测的PH结果低于默认值时﹐便会自动进行溶液添加。
金属蚀刻工艺流程

金属蚀刻工艺流程
金属蚀刻是一种通过化学物质作用于金属材料表面实现图案刻写的工艺,它主要应用于电子元器件、工艺品、装饰品等领域。
下面将详细介绍金属蚀刻的工艺流程。
首先,准备好所需的工具和材料。
这包括腐蚀液、金属材料、蚀刻底板等。
腐蚀液是金属蚀刻的重要物质,常用的有硫酸、盐酸等。
金属材料可以选择铜、铝、钢等。
接下来,将金属材料固定在蚀刻底板上。
这可以使用夹具或胶水等方法,确保金属材料牢固地固定在底板上,以免在蚀刻过程中出现移动或变形。
然后,将腐蚀液倒入浅盘中。
根据不同的材料和蚀刻要求选择合适的腐蚀液,并注意腐蚀液的浓度和温度。
接着,将蚀刻底板放入浅盘中的腐蚀液中,使金属材料完全浸没其中。
蚀刻的时间根据蚀刻要求的深度和速度来决定,一般需要几分钟至几小时不等。
在蚀刻过程中,需要定期检查金属材料的蚀刻情况。
可以使用显微镜等工具观察并判断是否达到了要求的蚀刻深度或图案效果。
当达到预期的蚀刻效果后,将蚀刻底板从腐蚀液中取出,并立即用水冲洗干净,以停止蚀刻过程。
这也有助于防止腐蚀液对金属材料的进一步腐蚀。
最后,用溶剂或清洁剂将蚀刻底板上的残留物清洗干净。
这样可以确保金属表面整洁,同时也有助于后续的涂装、上光或其他处理工艺。
总结起来,金属蚀刻工艺流程包括准备材料、固定金属材料、倒入腐蚀液、浸泡蚀刻、检查蚀刻效果、冲洗蚀刻底板和清洗残留物等步骤。
这个流程需要严格控制每个环节的条件和操作,以确保蚀刻效果符合要求。
金属蚀刻文档

金属蚀刻1. 引言金属蚀刻是一种常见的金属加工技术,通过在金属表面制造出一系列图案、文字或设计来达到装饰、标识或防腐的目的。
金属蚀刻技术具有精确性高、持久耐用、易于维护等特点,在许多领域得到广泛应用。
本文将介绍金属蚀刻的原理、过程和应用,并对常见的蚀刻材料、设备和注意事项进行探讨。
2. 原理金属蚀刻的基本原理是利用化学反应将金属表面一定部分区域上的金属材料溶解或氧化,从而形成所需的图案或文字。
一般来说,金属蚀刻主要通过以下两种方法来实现:2.1. 酸蚀刻酸蚀刻是最常见的金属蚀刻方法之一,常用的酸液有盐酸、硝酸等。
酸蚀刻的原理是将金属放入蚀刻液中,酸液将与金属表面发生化学反应,使得金属表面上的部分金属被蚀刻掉。
通过控制蚀刻液中的酸液浓度、腐蚀时间等参数,可以实现对金属表面的精细刻画。
2.2. 电化学蚀刻电化学蚀刻利用电解液和电源的作用,通过在金属表面施加一定电压,在阳极和阴极之间引起电流流动,从而腐蚀金属表面。
与酸蚀刻相比,电化学蚀刻可以更精确地控制金属的蚀刻深度和速度。
电化学蚀刻常用于对微细线路、电路板等进行蚀刻,具有较高的精度和可重复性。
3. 蚀刻过程金属蚀刻的过程一般包括以下几个步骤:3.1. 表面处理在蚀刻之前,需要对金属表面进行一些必要的处理,以保证蚀刻效果的良好和稳定。
常见的表面处理方法包括清洗、去油、打磨和抛光等。
清洗可使用碱性溶液或有机溶剂,去除金属表面的尘土和杂质。
去油可以使用酸洗或有机溶剂去除金属表面的油脂。
打磨和抛光可以提高金属表面的光洁度和平整度。
3.2. 蚀刻材料准备金属蚀刻需要用到适当的蚀刻液或电解液。
根据所需的蚀刻效果和金属材料的不同,选择合适的蚀刻液很重要。
常见的金属蚀刻液有硝酸、盐酸、硫酸、氟化液等。
蚀刻液的配比和浓度应根据具体情况进行调整。
3.3. 蚀刻操作蚀刻操作的具体步骤包括将金属样品放入蚀刻液中,控制蚀刻时间和温度,定时搅拌蚀刻液等。
对于大型或复杂的金属蚀刻任务,可能需要使用自动蚀刻设备或特殊的操作技术。
蚀刻用腐蚀液与配方比例

蚀刻用腐蚀液与配方比例刻蚀基础(转载)湿式蚀刻技术最早的蚀刻技术是利用特定的溶液与薄膜间所进行的化学反应来去除薄膜未被光阻覆盖的部分,而达到蚀刻的目的,这种蚀刻方式也就是所谓的湿式蚀刻。
因为湿式蚀刻是利用化学反应来进行薄膜的去除,而化学反应本身不具方向性,因此湿式蚀刻过程为等向性,一般而言此方式不足以定义3微米以下的线宽,但对于3微米以上的线宽定义湿式蚀刻仍然为一可选择采用的技术。
湿式蚀刻之所以在微电子制作过程中被广泛的采用乃由于其具有低成本、高可靠性、高产能及优越的蚀刻选择比等优点。
但相对于干式蚀刻,除了无法定义较细的线宽外,湿式蚀刻仍有以下的缺点:1) 需花费较高成本的反应溶液及去离子水;2) 化学药品处理时人员所遭遇的安全问题;3) 光阻附着性问题;4) 气泡形成及化学蚀刻液无法完全与晶圆表面接触所造成的不完全及不均匀的蚀刻;5) 废气及潜在的爆炸性。
湿式蚀刻过程可分为三个步骤:1) 化学蚀刻液扩散至待蚀刻材料之表面;2) 蚀刻液与待蚀刻材料发生化学反应;3) 反应后之产物从蚀刻材料之表面扩散至溶液中,并随溶液排出(3)。
三个步骤中进行最慢者为速率控制步骤,也就是说该步骤的反应速率即为整个反应之速率。
大部份的蚀刻过程包含了一个或多个化学反应步骤,各种形态的反应都有可能发生,但常遇到的反应是将待蚀刻层表面先予以氧化,再将此氧化层溶解,并随溶液排出,如此反复进行以达到蚀刻的效果。
如蚀刻硅、铝时即是利用此种化学反应方式。
湿式蚀刻的速率通常可藉由改变溶液浓度及温度予以控制。
溶液浓度可改变反应物质到达及离开待蚀刻物表面的速率,一般而言,当溶液浓度增加时,蚀刻速率将会提高。
而提高溶液温度可加速化学反应速率,进而加速蚀刻速率。
除了溶液的选用外,选择适用的屏蔽物质亦是十分重要的,它必须与待蚀刻材料表面有很好的附着性、并能承受蚀刻溶液的侵蚀且稳定而不变质。
而光阻通常是一个很好的屏蔽材料,且由于其图案转印步骤简单,因此常被使用。
金属蚀刻工艺流程

金属蚀刻工艺流程金属蚀刻是一种利用化学反应将金属表面部分或全部腐蚀掉,制造出一定形状或花纹的工艺。
它广泛应用于美术工艺品、标牌、金属雕刻等领域。
下面是金属蚀刻工艺的一个典型流程:1.设计:首先,根据客户需求,设计师会进行图纸的设计。
图纸包括所需雕刻的形状、大小、样式等。
2.材料准备:选择合适的金属材料进行蚀刻。
常见的金属材料有铜、不锈钢、铝等。
根据材料的不同,蚀刻的效果也会有所差异。
3.清洗:将金属材料进行清洗,去除表面的油污、灰尘等杂质。
这一步很重要,因为杂质会影响后续的蚀刻效果。
4.涂覆保护剂:使用保护剂(如防蚀剂、胶水等)在金属表面形成一层保护层,以防止整个金属材料被腐蚀。
5.印刷:如果需要在金属表面打印图案或文字,可以使用丝网印刷技术进行印刷。
印刷时,根据图纸要求,将图案或文字印在金属材料上。
6.曝光:将设计的图案印在感光胶上,然后再将感光胶放在金属材料上,使用UV曝光机进行曝光。
通过曝光,感光胶上的图案会固化。
7.蚀刻:将金属材料置于蚀刻液中。
蚀刻液通常是一种有刻蚀性的溶液,能够与金属表面发生化学反应,将金属表面腐蚀掉。
蚀刻液的选择取决于金属材料和所需的蚀刻效果。
8.清洗:蚀刻完成后,需要将蚀刻液从金属表面洗去,以停止蚀刻的过程。
一般会使用清水或者中性化学品进行清洗。
9.去除保护剂:蚀刻完成后,需要将之前涂覆的保护剂从金属表面清除。
可以使用化学清洗剂或者机械方法进行清洗。
10.抛光:为了使金属表面更光滑细腻,常常需要进行抛光处理。
抛光可以使用机械方法进行,也可以使用化学方法。
11.烘干:抛光完成后,需要将金属材料进行烘干,以便后续加工和保护。
12.确认质量:最后,需要对蚀刻效果进行检查,确保符合客户的要求。
如有需要,可以进行进一步的修复和加工。
- 1、下载文档前请自行甄别文档内容的完整性,平台不提供额外的编辑、内容补充、找答案等附加服务。
- 2、"仅部分预览"的文档,不可在线预览部分如存在完整性等问题,可反馈申请退款(可完整预览的文档不适用该条件!)。
- 3、如文档侵犯您的权益,请联系客服反馈,我们会尽快为您处理(人工客服工作时间:9:00-18:30)。
包装封存
电子产品构思 线路板设计
线路板制作
成品检验
元件安装调试
快速制板方法分类
四种快速制板方法: 1、物理雕刻制板; 2、热转印制板; 3、曝光制板; 4、小型工业制板。
其中小型工业制板又分为湿膜和干膜两种 工艺
快速制板简要知识
1、PCB板线宽和线隙单位:mil,1mm=40mil 一般的制作要求有3个档次:8mil、6mil、4mil。 2、线路板分为:单面板、双面板、多层板 3、线路板按硬度分为:刚性板和软板 4、样板类型:覆铜板、镀锡板、阻焊板、丝印
4、调节速度调节旋钮,使传送轮速 度合适,以达到最好的表面处理效果;
5、将待处理的覆铜板置于传送滚轮上, 抛光机将自动完成板材去氧化物层、油污 等全过程。
自动抛光机
4.4a 双面贯孔
化学沉铜分为五个步骤: 1、碱性除油:55℃-65℃(最佳温度60℃),时间5分钟 目的:除去铜箔和孔内的油污、油脂及毛刺铜粉,调整孔壁电荷。 2、活化 :最佳温度为30℃,时间2分钟 目的:让整块板和孔壁活化后布满导电介质。 3、热固化:100 ℃, 时间5分钟 目的:将活化过的PCB板置于烘干箱内进行热固化。 4、微蚀:30-35℃,时间2分钟 目的:只留下孔壁的导电介质,为后续的镀铜提供一个微粗糙的活性
3 化学蚀刻制板工艺
1. 热转印制板 2. 曝光制板 3. 小型工业制板
3.1 热转印制板工艺
裁板下料
Pcb文件 编辑
钻孔 及检修
激光打印 转印底片
单面转 印敷铜板
线路蚀刻
自动钻孔
3.1a 简易单面热转印流程图
3.1b 单面自动热转印
• 特点:1、能自动钻孔,板件面积可达350×250mm,可3块覆铜板叠加钻孔,最小孔径达 0.35mm;2、能同时蚀刻6块350×250mm线路板,智能化温度和对流装置加快蚀刻速度和保 证蚀刻精度
1
2
3
4
手动精密裁板机
4.2 数控钻孔
• 钻孔通常有手工钻孔和数控自动钻孔两种方法,本节将介绍数控 钻孔的方法。
• 数控钻床能根据PROTEL、POWERPCB、ORCAD、PANDS生 成的PCB文件自动识别钻孔数据,并快速、精确地完成定位、钻 孔等任务。用户只需将设计好的PCB文件直接导入数控钻后台软 件即可自动完成批量钻孔。
3.3 热转印和曝光制板区别
区别如下:
3.4 小型工业制板工艺
裁板下料
数控钻孔
抛光
双面贯孔
显影
曝光
丝印图形
镀铜
镀锡
蚀刻
丝印阻焊
丝印文字
3.5a 小型工业制板工序
4.1 裁板
板材准备又称下料,在PCB板制做前,应根据设计好的 PCB图大小来确定所需PCB板基的尺寸规格,我们可根据具 体需要进行裁板。
3.1c 热转印制板适用范围
热转印制板特点及适用范围:
1、制板成本低,主要制板材料为:敷铜板、热转印纸、蚀刻剂、钻头;
2、制板速度快,10分钟内可完成一块单面线路板制作;60分钟内可 完成双面板制作;
3、最小线宽、线隙精度到达10mil;
4、主要适用于创新实验室、小型实训室的建设,可满足学生电子竞赛、 课题设计、毕业设计、研发创新和实训等设计制作任务。
全自动数控钻床
数控钻软件操作界面
4.3 板材抛光
作用:
去除覆铜板金属表面氧化物、保护膜及油污,进行表面抛 光处理。
操作步骤:
1、 旋转刷轮调节手轮,使上、 下刷轮与不锈钢辊轴间隙调整合理;
2、开启水阀,使抛光时能喷水冲 洗,以使覆铜板表面处理更干净;
3、开启风机开关,使线路板经过 风机装置时,能烤干覆铜板表面的水 份;
摆动
5’
4
30~35℃ 碱性体系 摆动
2’
4.5 图形转移
在双面线路板制作中,图形转移主要有两种方式:一种是热转印转移法,一 种是曝光转移法。本章主要介绍工厂上通用的曝光转移法。
曝光转移法
底片制作
丝网制作
电镀锡
双面图形转移
油墨固化
油墨印刷
4.5a 热转印法
• 热转印转移法 热转印机主要利用静电成像设备代替专用印制板制板照相设备,利用含 树脂的静电墨粉代替光化学显影定影材料,通过静电印制电路制板机在 敷铜板上生成电路板图的防蚀图层,经蚀刻(腐蚀) 成印制电路板。
裁板下料
2 雕刻制板工艺
Pcb文件 编辑输出
数控钻孔
金属化孔
铣边成型
雕刻线路
2.1雕刻流程图
2.2 雕刻制板适用范围
主要适用范围:
1、对线径要求不高的样板制作(大部分线路制作精度在10mil以上); 2、样板制作量极少(只能串行单块制作,不能小批量); 3、对打样时间无严格要求(雕刻我司小型工业样板需要6小时); 4、耗材损耗大:1把雕刀只能雕3块150cm2双面板 5、无工艺学习(只有雕刻流程,标准制板工艺极不完整)。
和波峰焊接困难; 6、工艺简单,不适合实训基地建设。
1.2 化学蚀刻制板的特点
1、工艺流程全面,工业级流程; 2、制板成功率非常高; 3、制板速度快,制作1块10×15cm镀锡双面板
75分钟; 4、制作精度高,可达4mil; 5、含镀锡及阻焊工艺,焊盘附着力强,方便回流
波峰设备焊接; 6、工艺完整,适合创新电子和实训基地建设。
面结构,增强铜层和基材铜之间的结合力。 5、镀铜:
利用电解的方法使金属铜沉积在工件表面,以形成均匀、致密 、结合力良好的金属铜层。
4.4b操作温度及操作时间表
碱性除油 活化 热固化 微蚀
序号 最佳温度 主要成分 搅拌方式 控制时间
1
碱性体系 摆动
5’
60℃
2
若酸体系 摆动
2’
30℃
3
100 ℃
--
裁板下料
3.2 曝光制板工艺
Pcb文件 编辑输出
激光打印 菲林底片
感光板曝光
蚀刻成型
显影
3. 2a 简易曝光单面制板
• 特点:1、制作精度高达6mil;2、制板幅面为210× 300mm;3、制作材料为感光 板
3.2b 单面小批量曝光制板
• 特点:1、自动批量钻孔;2、制作线隙、线径达4mil;3、批量蚀刻
板
1 快速制板分类
线
路
化学蚀刻制板
板
制
作
方
物理雕刻制板
法
1.1 物理雕刻制板的特点
1、工艺流程简单、具有一定自动化程度; 2、制板速度慢,雕刻1块我司双面小型工业样板
需6小时,成功率较低。 3、制作精度较低,精度10mil; 4、耗材贵:雕刻10×15 cm双面样板1块需要耗
费1把雕刀。(刀尖:0.13、0.18mm) 5、因无镀锡及阻焊工艺,焊盘附着力差,回流焊