约克 YORK 彩屏YK离心操作说明书
约克YK离心冷水机组

培训内容1.常用的计量单位换算2.系统结构3.工作原理4.润滑系统4.常见故障5维护与保养计量单位换算长度1英寸=25.4mm 1米=100cm=3.94英寸(in) 容积1加仑(gallon)=4.55升(L)英制1加仑(gallon)=3.79升(L)美制质量1磅(Ib)=454克(g)1kg=2.2Ib流量1每加/仑每分(gpm)=3.786升/每分(L/m) 压力1磅(PSI)=6.89千帕(Kpa) 1Kpa=0.145PSI 温度℃=5(℉-32)/9 ℉=9/5+32热能1冷吨=3024Kcal=3.516KW功率1马力(Hp)=0.746千瓦特(Kw) 1kW=1.34HP常用术语:表压=绝对压力-大气压力真空度=大气压力-绝对压力蒸发器小温差=冷冻水出水温度-蒸发温度冷却器小温差=冷凝温度-冷却水出水温度小温差取决于换热器性能好坏过冷度=对应的饱和温度-离开冷凝器的制冷剂温度过热度=排气温度传-对应的冷凝饱和度油压差=油泵出口压力-压缩机的入口压力离心式冷水机组工作原理机组前视图机组后视图2010/4/14蒸发器冷凝器截流元件压缩机电机冷却塔制冷机组的整体布局机组代码YK机组结构离心机组的组成部件机组构造蒸发器冷凝器电动机齿轮叶轮预旋转导叶关键部件制冷设备的四个主要组成部分: 压缩机冷凝器节流(膨胀)装置蒸发器各部件的作用压缩机提升压力低压(低温)气体被吸入压缩机并被压缩成高压(高温)气体活塞式、双/ 单螺杆、回转式离心冷凝器从压缩机出来的高温制冷剂气体进入冷凝器,在一定压力下释放热量变成液体。
高温制冷剂在冷凝器中冷凝。
各部件的作用节流装置(膨胀阀) :液体经过节流装置使压力下降。
孔板、热力膨胀阀、电子膨胀阀、毛细管等蒸发器液体制冷剂进入蒸发器蒸发为气体。
制冷剂在蒸发器中吸收热量。
预旋转导流冷凝器过冷器均流板满液式蒸发器截流孔板叶片叶轮汽液分离板离心式冷水机组满液式蒸发器干式蒸发器满液式蒸发器压缩机吸气管均气板支撑板固定棒视镜支撑板液位控制油收集器回油管均液板液态冷媒供液管PEH蒸发器吸气口出水进水供液口离心式冷水机组汽液分离板离心式冷水机组预旋转导流叶片预旋转导叶部分开启关闭预旋转导流叶片全开预旋转导流叶片全关预旋转导流叶片预旋转导流叶片部分关闭离心式冷水机组叶轮叶轮离心式冷水机组均流板离心式冷水机组冷凝器高效换热铜管铜管规格加强部分常规部分230.025"0.050 - 0.053"220.028"0.053 - 0.056"200.035"0.059 - 0.063"实际铜管厚度水流管板铜管支撑板高效换热铜管高效换热铜管换热器采用新型高效换热型面(内螺纹/外肋片)提高机组效率,降低结垢率,节省维护费用水流方向筒体端板中间支撑板TubeSheetTube Support WATERFLOW离心式冷水机组过冷器离心式冷水机组截流孔板截流元件固定截流孔板可变截流孔板强化非设计工况性能液体管线调节阀制冷剂液位探头维持冷凝器最佳液位 通过MicroPanel控制叶轮预旋转导叶高速齿轮轴封止推轴承轴颈轴承轴颈轴承轴颈轴承连轴器低速齿轮高速齿轮低速齿轮特点及优势最优化的叶轮设计适应于各类特定的运行工况可靠相同部件在军事工业上使用单螺旋设计与VSD 完美配合轴与轴封剖面图YK系列轴封双层密封泰福龙C型密封环约克双层轴封的优点约克机组采用双层密封以保证轴承的润滑及密封; 冷媒进入压缩机前,已与润滑油彻底分离;冷媒在轴封处的泄漏微乎其微;喘振发生离心式压缩机旋转失速和喘振的差别旋转失速旋转失速是所有离心式压缩机在流量减小(负荷减小)和/或者压头增加(温度头增加)时发生的一种空气动力学中的扰动现象。
约克离心式冷水机组说明书

, 了解每个, 包括日常设备检3YK 离心式冷水机组设计特点约克OptiView TM YK 离心式冷水机组能提供各种形式的配置,以满足不同用户的需要。
配置约克变频驱动装置(VSD)的YK 机组彩色图象显示控制中心约克OptiView TM 彩色图象显示控制中心,同时显示机组每个部件的运行参数与插图,控制简单形象。
变频配置,高效节能(选项)配置变频驱动器,独特的自适应容量控制将电机变频和导流叶片调节完美地结合在一起,大大提高机组的效率,令部分负荷耗电指标低达0.2kW/ton ,机组的年节能可达15%-25%。
单级压缩机,先进可靠约克单级压缩机的运动部件较少、设计简洁高效,它的长工作寿命已在许多应用中得到了证明。
轻质、高强度的铝制叶轮采用后弯叶片,效率很高。
翼形导流叶片减少了气流的扰动,使部分负荷能保持最高效的性能。
压缩机可平稳地从100% 卸载到最低负荷。
开式电机,安全可靠闭式电机烧毁后会对冷水机组造成灾难性的破坏,整台机组必须彻底清洁,并要更换制冷剂后方可使用。
约克YK 离心式冷水机组采用风冷式电机,从而避免了这种危险。
制冷剂根本不会与电机接触,避免了对冷水机组其它部分的污染。
保险公司在对大型空调设备保险时,通常风冷式电机的保险费要比制冷剂冷却的闭式电机低得多。
充分利用低温冷却水,显著节能符合实际工况下的节能要求,机组能充分利用低达12.8℃的冷却水,获得明显的节能效果,而不像有些机组那样需要人为地将水温控制在21~24℃。
高效热交换器,表现卓越热交换器采用了最新的高效换热铜管,使传热效率最佳、结构紧凑。
水侧和制冷剂侧强化传热,减少机组能耗和管道结垢。
结构紧凑,安装方便机组设计精密紧凑,大大减少机房占地面积。
安装时只需少量的接管和布线,帮助用户节约安装费用。
环保冷媒,造福人类- 约克YK 冷水机组的性能经美国空调制冷供暖协会(AHRI)认证。
- 符合最新的AHRI550/590标准。
- 采用HFC-134a 环保制冷剂,对臭氧层没有损害。
约克YK机组维修保养技术手册

绿色环保
HCFC-22 ( CHClF2 ) = 0.055 HCFC-123( CHCl2CF3 ) = 0.02 HFC-134a ( CF3CH2F )= 0.0
2013/9/17 32
综上所述,约克YK离心式机组具有以下五大优点:
高效节能
控制先进
可靠性高, 灵活性好 维修简单, 费用低廉 绿色环保
降低冷却水进水温度 = 节能 压力 高效节能
降低冷凝器进水温度
降低压头
冷凝器
压头 蒸发器 减少能耗 压缩机 减少压缩机功耗
焓
2013/9/17
15
产品特点 - 低冷却水温正常运行
能耗指标kW/Ton冷却水进水温度℉曲线图
0.55 0.50 0.45 0.40
高效节能
对手
60% Load 100% Load
重庆
重庆 重庆 重庆 重庆 重庆 重庆 重庆 重庆 重庆
YK900
YK1000 YK800\YK550\YK600 YK1100 YK700 YK620 YK550 YK900 YK650 YK700
2013/9/17
3
3 8 2 2 2 2 1 4 2
35
问 题?
2013/9/17 36
工厂完成配装、连线及 测试 单点接线 与门连锁断路器 UL认证的地线故障保护 不需要额外的占地 所有信息可在控制屏上 显示
可靠性高
控制先进
2013/9/17
31
产品特点 - HFC-134a环保冷媒
CFC: 氯氟烃(碳氢化合物的氟、氯完全衍生 物)ODP较高 HCFC: 氢氯氟烃 (不完全卤代烃)ODP较低 HFC: 氢氟烃(不完全卤代烃)ODP为零 ODP (臭氧消耗潜能值)
约克YK离心冷水机组资料
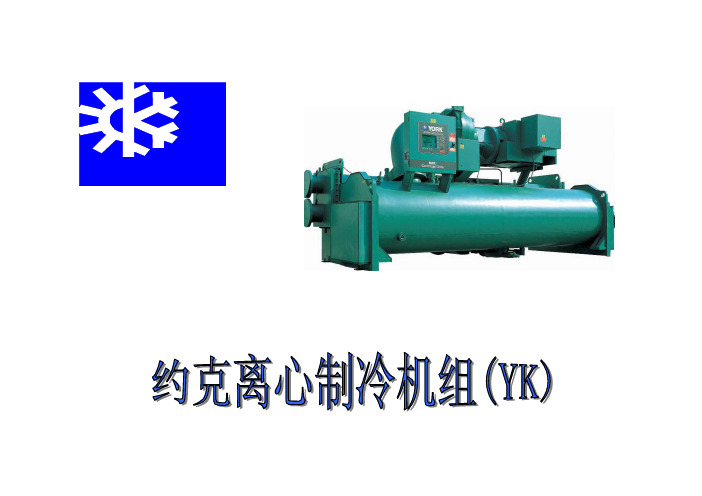
CODE
START RUN
无钥匙
STOP / RESET
“免钥匙” 微电脑控制中心外观
微电脑控制中心的组成部件
电源板 微处理板 数字输入板 继电输出板 输入/输出扩充板 键盘 显示面板
控制柜
工作流程图
电源板
电源板
电源板
从变压器接收24V电压 把稳定的和不稳定的电压输送给控制盘
• 导叶马达开关
• 远程启动/停机
• 远程设定
数
• 水流开关
字
• 油循环
输
• 高压安全
入
• 开机/停机 开关
板
系统温度/压力 (模拟输入)
键盘
关闭马达
多路马达电流 地址
CM-2 电流模块
马达电流
启动 信号
微 处 理 板
继电 输出板
• 抽气电磁阀 • 油泵启动器 • 排气电磁阀 • 启动继电器 • 停机继电器 • 导叶马达 • 冷冻水泵
喘振发生
离心式压缩机旋转失速和喘振的差别
旋转失速 旋转失速是所有离心式压缩机在流量减小(负荷减
小)和/或者压头增加(温度头增加)时发生的一种空气 动力学中的扰动现象。
在所有类型的旋转失速中,只有总流量中的一小部 分在叶轮或扩散器内部再循环。绝大多数的流体被从蒸 发器连续不断地泵入冷凝器。在失速发生时,蒸发器和 冷凝器的压力表是稳定的。
STATUS
DISPLAY
CHILLED LIQUID TEMPS
REFRIGERANT PRESSURES
OIL PRESSURE
OPTIONS
SSS MOTOR CURRENT / VOLTS
CONDENSER LIQUID TEMPS
约克YK水冷离心式冷水机组介绍PPT

Constant Speed
Load
变速离心式冷水机组
1.2 1.1 1.0 0.9
kW / ton
0.8 0.7 0.6 0.5 0.4 0.3 0.2
10 0% 80 % 60 % 40 % 20 %
Constant Speed Variable Speed
Load
变速离心式冷水机组
1.2 1.1 1.0 0.9
0
5
10 时间 (sec)
20
40
起动电流
电机满负荷电流 FLA (%)
500%
400% 300%
星三角起动器
200% 100%
Millennium 变频驱动器
0
5
10 时间 (se0.50
kW / ton
0.45 0.40 0.35 0.30 0.25 85 F
80 F
75 F
70 F
65 F
60 F
Entering Condenser Water Temperature
0.65 0.60 0.55 0.50
kW / ton
Traditional 60% Load 100% Load 80% Load
0.45 0.40 0.35 0.30 0.25 85 F
YORK (lecwt) 60% Load 100% Load 80% Load
80 F
75 F
70 F
65 F
60 F
Entering Condenser Water Temperature
0.65 0.60 0.55 0.50
kW / ton
喘振区
Speed + PRV Open Speed+PRV Control PRV Control +
约克YK机组维修保养技术手册

可靠性高
控制先进
2019/2/20
31
产品特点 - HFC-134a环保冷媒
CFC: 氯氟烃(碳氢化合物的氟、氯完全衍生 物)ODP较高 HCFC: 氢氯氟烃 (不完全卤代烃)ODP较低 HFC: 氢氟烃(不完全卤代烃)ODP为零 ODP (臭氧消耗潜能值)
2019/2/20
16
产品特点 - 高效换热器设计
高效强化换热管
采用最新高效换热铜管,传热效率最佳 水侧和制冷剂侧强化传热,减少机组能耗和管道结垢
蒸发器壳体底部装有分液槽
制冷剂在整个壳体长度方向均匀分布,传热效果最佳
冷凝器内置过冷器
过冷液体,改善循环效率
冷凝器内置排气挡板
可靠性高, 灵活性好
能够全自动监控机组运行,记录运行状态 参数,简化运行管理工作
具有自诊断功能,可以记录故障状况,进 行机组运行趋势分析,以实现预防性保养 ,将故障率将至最低 提供多种安全保护及报警功能,保证机组 安全运行,故障率低 数据记录安全先进
维修简 单,费 用低廉
控制先进
2019/2/20 24
2019/2/20 4
产品介绍 – 系统介绍
制冷剂循环
完全由工厂组装,包括蒸发器、冷凝器、压缩机、电机 、润滑系统、控制中心和所有跟机组有关的接管和敷线
2019/2/20 5
产品特点
可靠性高, 灵活性好
开式电机,电机空气冷却 单级压缩,配预旋转导流叶片
高效节能
专利轴封设计
低冷却水温工况下正常运行 高效换热器设计
YORK螺约克杆机离心机YS,YK,YT主板故障常见

YORK螺约克杆机离⼼机YS,YK,YT主板故障常见判断YORK约克螺杆机离⼼机YS、YK、YT主板常见故障私⼈⽇志2010-03-17 19:57:48| 分类:约克机|字号⼤中⼩订阅YSYKYT主板常见故障判断⼀、元件功能介绍Control Panel 由主板、I/O板、电源、显⽰器、键盘及CM-2板(机电式启动⽤)或ACCB(⾃适应容量控制板,VSD⽤)组成。
1. 主板主板包括操作软件,微处理器及模拟量输⼊。
其中EPROM包括启动⾃检程序,BRAM 为保存数据的电池,FLASH贮存整个操作程序。
启动失败时,可检查EPROM、BRAM和FLASH CARD。
FLASH版本描述,C.MLM.nn —(01=YK、02=YT、03=YS、04=YK(P)、05=YR)跳线设定JP2、JP3、JP4、JP5、JP7、JP8根据不同显⽰器品牌,按照显⽰器标签描述设定JP34 冷媒型式设定。
YS、YK机组IN:选择R22,OUT:选择R134aYT机组IN:选择R11,OUT:选择R123JP35 冷⽔/盐⽔程序设定,IN:冷⽔⼯况OUT:盐⽔⼯况JP37 压缩机电机启动器类型IN:机电式或固态启动器OUT:VSD,同时JP39必须为IN。
JP39 固态启动器类型IN:A型OUT:B型JP41、JP42—⾼速⽌推轴承近程式传感探头型号IN:+12DCOUT:+24DCSW1设定SW1-2 油泵型式ON:变频油泵OFF:定速油泵SW1-3预润滑时间ON:增强型预润滑,时间180S OFF:标准预润滑,时间150SSW1-4软件⾃检SW1-5重启动设定ON:⾃动启动OFF:⼿动启动SW1-6反重复启动计时ON:反重复启动计时,OFF:反重复启动计时失效SW1-7VSD电源频率ON:50Hz OFF:60Hz主板J19连接I/O板J1J19-1 ⾼压开关J19-2 马达控制器安全关机J19-3 停⽌开关J19-4 启动开关J19-5 ⾼浮球开关(YT)J19-6 VSD油泵运⾏状态(YK),低浮球开关(YT)J19-7 PRV限位(YT, YK)油位开关(YS)J19-14 冷冻⽔流开关J19-17 辅助安全关机J19-18 冷却⽔流开关J19-21 +5VJ19-22~J9 -25 接地J19-26, 27 +12VJ19-28 OVA关J19-29 OVA 开J19-32 PRV或滑阀关J19-33 PRV或滑阀开J19-46 循环关机J19-47 安全关机电源J1-1 +5V 接稳压电源311AJ1-2 地接稳压电源309AJ1-3 +12V 接稳压电源307AJ1-4 -12V 接稳压电源303A2.I/O板包括数字量的输⼊输出。
约克离心制冷机组(YK )培训资
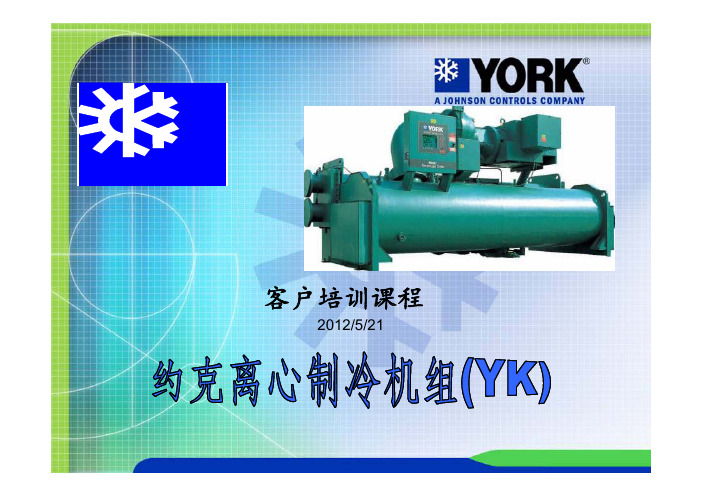
2012/5/21客户培训课程培训内容1.常用的计量单位换算2.系统结构3.工作原理4.润滑系统系4.常见故障5维护与保养2012/5/212计量单位换算长度1英寸=25.4mm 1米=100cm=39.4英寸(in)容积1加仑(gallon)=4.55升(L)英制ll3791加仑(gallon)=3.79升(L)美制质量1磅(Ib)=454克(g)1kg=2.2Ib流量1每加仑/每分钟(gp/m)=3.786升/每分钟(L/m)=3786压力1磅(PSI)=6.89千帕(Kpa) 1Kpa=0.145PSI 温度℃5(32)/9 ℃9/532=5(℉-32/9℉=9/5+32热能1冷吨=3024Kcal=3.516KW功率1马力(Hp)=0.746千瓦特(Kw) 1kW=1.34HP2012/5/213离心式冷水机组工作原理2012/5/214制冷机组的整体布局冷却塔冷凝器蒸发器截流元件压缩机电机2012/5/21机组代码2012/5/216YK机组结构离心机组的组成部件2012/5/217机组构造2012/5/218关键部件齿轮叶轮预旋转导叶电动机冷凝器2012/5/219蒸发器制冷设备的四个主要组成部分:压缩机冷凝器节流(膨胀)装置蒸发器2012/5/2110各部件的作用压缩机提升压力低压(低温)气体被吸入压缩机并被压缩成高压(高温)气体活塞式、双/ 单螺杆、回转式离心冷凝冷凝器从压缩机出来的高温制冷剂气体进入冷凝器,在一定压力下释放热量变成液体。
高温制冷剂在冷凝器中冷凝。
2012/5/2111各部件的作用节流装置(膨胀阀) :液体经过节流装置使压力下降。
液体经过节流装置使压力下降孔板、热力膨胀阀、电子膨胀阀、毛细管等蒸发器液体制冷剂进入蒸发器蒸发为气体。
液体制冷剂进入蒸发器蒸发为气体制冷剂在蒸发器中吸收热量。
2012/5/2112冷凝器满液式蒸发器过冷器截流孔板2012/5/2113预旋转导叶部分开启关闭2012/5/2114PRV2012/5/2115压缩机的吸气口及导流叶片(机组根据实际负荷,自动际负荷自动调节导流叶片,使制冷量可自15%~100%无级变化)2012/5/2116导流叶片总成2012/5/2117预旋转导流叶片全开2012/5/2118预旋转导流叶片全关预旋转导流叶片2012/5/2119预旋转导流叶片部分关闭2012/5/2120离心式冷水机组叶轮2012/5/2121叶轮2012/5/2122离心式冷水机组2012/5/2123离心式冷水机组冷凝器2012/5/2124冷凝器均流板强化换热管过冷器2012/5/2125高效换热铜管水流230.0250.050 0.0530.025"0.050-0.053"220.028"0.053 - 0.056"200.035"0.059 - 0.063"2012/5/2126高效换热铜管水流方向WATERTube SheetTube SupportFLOW换热器采用新型高效换热型面筒体端板中间支撑板(内螺纹/外肋片)提高机组效率,降低结垢率,节省维护费用2012/5/2127截流元件固定截流孔板可变截流孔板强化非设计工况性能液体管线调节阀制冷剂液位探头维持冷凝器最佳液位通过MicroPanel控制2012/5/2128叶轮预旋转导叶轴颈轴承高速齿轮止推轴承连轴器轴颈轴承2012/5/2129轴封低速齿轮轴颈轴承低速/高速齿轮2012/5/2130高速齿轮2012/5/2131低速齿轮2012/5/2132特点及优势最优化的叶轮设计适应于各类特定的运行工况可靠相同部件在军事工业上使用单螺旋设计与VSD 完美配合2012/5/2133约克双层轴封的优点约克机组采用双层密封以保证轴承的润滑及密封; 冷媒进入压缩机前,已与润滑油彻底分离; 冷媒在轴封处的泄漏微乎其微;2012/5/2134连轴器工厂定位柔性连轴器 D--法兰电动机2012/5/21352012/5/2136电机与压缩机的复式联轴器(冷媒系统与电气系统完全分开)开式电机彻底消除了冷媒冷却闭式电机的能耗(电机由空气冷却,散热量不带入制冷系统,效率可提高约3%~5%)2012/5/2137York压缩机的电机轴承电机两侧都有轴承支撑内置的一对斜齿轮两侧都有轴承支撑(共2对齿轮)非常传统的设计方法开式电机靠周围的空气冷却不需电机线圈温度保护探头2012/5/2138开式马达设计避免闭式马达被烧毁的惨剧减少维修工作量可靠性更强多种冷媒兼容性开式马达技术电动机蒸汽透平燃气发动机2012/5/2139•如因电压不正常或安装不善•开式电机只需重新绕组,制只需重新绕组制维护费用。
- 1、下载文档前请自行甄别文档内容的完整性,平台不提供额外的编辑、内容补充、找答案等附加服务。
- 2、"仅部分预览"的文档,不可在线预览部分如存在完整性等问题,可反馈申请退款(可完整预览的文档不适用该条件!)。
- 3、如文档侵犯您的权益,请联系客服反馈,我们会尽快为您处理(人工客服工作时间:9:00-18:30)。
OPERATING & MAINTENANCEM AX E TMCENTRIFUGAL LIQUID CHILLERS Supersedes: NOTHING Form 160.73-O2 (1202)MODEL YK (STYLE F)R-134a COOLING ONLYWITH OPTIVIEW TM CONTROL CENTERFOR ELECTRO-MECHANICAL STARTER, SOLID STATE STARTER & VARIABLE SPEED DRIVE00611VIPLDO5842YORK INTERNATIONALFORM 160.73-O2(1202)2This equipment is a relatively complicated apparatus. During installation, operation, maintenance or service, individuals may be exposed to certain components or conditions including, but not limited to: refrigerants, oils, materials under pressure, rotating components, and both high and low voltage. Each of these items has the potential, if misused or handled improperly, to cause bodily injury or death. It is the obligation and respon-sibility of operating/service personnel to identify and recognize these inherent hazards, protect themselves, and proceed safely in completing their tasks. Failure to comply with any of these requirements could result in serious damage to the equipment and the propertyIMPORTANT!READ BEFORE PROCEEDING!GENERAL SAFETY GUIDELINESin which it is situated, as well as severe personal in-jury or death to themselves and people at the site.This document is intended for use by owner-authorized operating/service personnel. It is expected that this in-dividual possesses independent training that will enable them to perform their assigned tasks properly and safely. It is essential that, prior to performing any task on this equipment, this individual shall have read and under-stood this document and any referenced materials. This individual shall also be familiar with and comply with all applicable governmental standards and regulations pertaining to the task in question.SAFETY SYMBOLSThe following symbols are used in this document to alert the reader to areas of potential hazard:WARNING indicates a potentially hazardous situation which, if not avoided, could result in death or se-rious injury.DANGER indicates an imminently hazardous situation which, if not avoided, will result in death or serious injury.CAUTION identifies a hazard which could lead to damage to the machine, damage to other equipment and/or environmental pollution. Usually an instruction will be given, together with a brief explanation.External wiring, unless specified as an optional connection in the manufacturer’s product line, is NOT to be connected inside the micro panel cabinet. Devices such as relays, switches, transducers and controls may NOT be installed inside the micro panel. NO external wiring is allowed to be run through the micro panel. All wiring must be in accordance with YORK’s published specifications and must be performed ONLY by qualified YORK personnel. YORK will not be responsible for damages/problems resulting from improper connections to the controls or application of improper control signals. Failure to follow this will void the manufacturer’s warranty and cause serious damage to property or injury to persons.NOTE is used to highlight additional information which may be helpful to you.FORM 160.73-O2(1202)YORK INTERNATIONAL3CHANGEABILITY OF THIS DOCUMENTIt is the responsibility of operating/service personnel as to the applicability of these documents to the equip-ment in question. If there is any question in the mind of operating/service personnel as to the applicability of these documents, then, prior to working on the equipment, they should verify with the owner whether the equipment has been modified and if current literature is available.DESIGN LEVEL (F)POWER SUPPLY – for 60 Hz 5 for 50 Hz COMPRESSOR CODE H4, H5, H6, H7, H8, J1, J2, J3, J4, P1, P2, P3, P4, P5, P6, P7 CONDENSER CODEAB, AC, AD, BB, BC, BD, CF, CG, CH, DF, DG, DH, EB, EC, ED, FA, FB, FC, FD, GB, GC, GD, HB, HC, HD, JB, JC, JD, TB, TC, TD, VB, VC, VD EVAPORATOR CODEAB, AC, AD, BB, BC, BD, CF, CG, CH, DF, DG, DH MODEL EB, FB, FC, FD, GB, GC, GD, GF, GH, HB, HC, HF, HH, JF, JG, JH, TF, TG, TH, VF, VH, WF, WHNOMENCLATUREYK CB CB P6 – CM FMOTOR CODE 60 Hz 50 Hz CH CX 5CE 5CT CJ CY 5CF 5CU CK CZ 5CG 5CV CL CA 5CH 5CW CM CB 5CI 5CX CN DA 5CJ 5DA CP DB 5CK 5DB CR DC 5CL 5DC CS DD 5CM 5DD CT DE 5CN 5DE CU DF 5CO 5DF CV DH 5CP 5DG CW DJ 5CQ 5DH CF CG 5CR 5OJ 5CSIn complying with YORK’s policy for continuous prod-uct improvement, the information contained in this doc-ument is subject to change without notice. While YORK makes no commitment to update or provide current information automatically to the manual owner, that in-formation, if applicable, can be obtained by contacting the nearest YORK Applied Systems Service office.REFERENCE INSTRUCTIONSDESCRIPTION FORM NO. SOLID STATE STARTER (MOD “B”) – OPERATION & MAINTENANCE 160.00-O2 VARIABLE SPEED DRIVE – OPERATION 160.00-O1 VARIABLE SPEED DRIVE – SERVICE INSTRUCTIONS 160.00-M1 INSTALLATION 160.73-N1 OPTIVIEW CONTROL CENTER - SERVICE INSTRUCTIONS 160-54-M1 WIRING DIAGRAM – UNIT WITH ELECTRO-MECHANICAL STARTER 160.73-PW1 WIRING DIAGRAM – UNIT WITH MOD “A” SOLID STATE STARTER 160.73-PW2 WIRING DIAGRAM – UNIT WITH VARIABLE SPEED DRIVE 160.73-PW3 RENEWAL PARTS – UNIT 160.73-RP4 RENEWAL PARTS – OPTIVIEW CONTROL CENTER 160.54-RP1 OPTIVIEW™ PANEL - OPERATION & MAINTENANCE 160.54.O1FORM 160.73-O2(1202)4SECTION 1 Description of System and Fundamentals of Operation (6)System Operating Procedures......................................................................9System Components Description (1)5Operational Maintenance (21)Troubleshooting (23)SECTION 6Maintenance (25)SECTION 7Preventive Maintenance (34)TABLE OF CONTENTSYORK INTERNATIONALFORM 160.73-O2(1202)LIST OF FIGURESFIG. 1 – MODEL YK MAXE TM CHILLER (6)DETAIL A – COMPRESSOR PREROTATIONVANES (7)FIG. 2 – REFRIGERANT FLOW-THROUGH CHILLER (8)FIG. 3 – OIL LEVEL INDICATOR LABEL (9)FIG. 4 – CHILLER STARTING SEQUENCE &SHUTDOWN SEQUENCE(EM STARTER & SOLID STATE STARTER) (10)FIG. 5 – CHILLER STARTING SEQUENCE &SHUTDOWN SEQUENCE(VARIABLE SPEED DRIVE) (11)FIG. 6 – LIQUID CHILLER LOG SHEETS (12)FIG. 7 – SYSTEM COMPONENTS (15)FIG. 8 – SCHEMATIC DRAWING (YK) COMPRESSORLUBRICATION SYSTEM (16)FIG. 9 – OIL RETURN SYSTEM (21)FIG. 10 – CHARGING OIL RESERVOIR WITH OIL (22)FIG. 11– EVACUATION OF CHILLER (25)FIG. 12 – SATURATION CURVE (27)FIG. 13 – DIAGRAM - MEGGING MOTOR WINDINGS (29)FIG. 14 – MOTOR STATOR TEMPERATURE &INSULATION RESISTANCE (30)YORK INTERNATIONAL5FORM 160.73-O2(1202)6electro-mechanical starter, YORK Solid State Starter(optional), or Variable Speed Drive (optional).In operation, a liquid (water or brine to be chilled)flows through the evaporator, where boiling refrigerantabsorbs heat from the liquid. The chilled liquid is thenpiped to fan coil units or other air conditioning terminalunits, where it flows through finned coils, absorbing heatfrom the air. The warmed liquid is then returned to thechiller to complete the chilled liquid circuit.The refrigerant vapor, which is produced by the boil-ing action in the evaporator, flows to the compressorwhere the rotating impeller increases its pressure andtemperature and discharges it into the condenser. Waterflowing through the condenser tubes absorbs heat fromthe refrigerant vapor, causing it to condense. The con-denser water is supplied to the chiller from an externalSECTION 1DESCRIPTION OF SYSTEM AND FUNDAMENTALS OF OPERATION00116vip CONDENSERCONTROLCENTERCOMPRESSORMOTOREVAPORATORFIG. 1 – MODEL YK MAXE TM CHILLERSYSTEM OPERATION DESCRIPTION (SEE FIG. 2)The YORK Model YK MaxE TM Chiller is commonly ap-plied to large air conditioning systems, but may be used onother applications. The chiller consists of an open motormounted to a compressor (with integral speed increasinggears), condenser, evaporator and variable flow control.The chiller is controlled by a modern state of the art Mi-crocomputer Control Center that monitors its operation.The Control Center is programmed by the operator to suitjob specifications. Automatic timed start-ups and shut-downs are also programmable to suit nighttime, week-ends, and holidays. The operating status, temperatures,pressures, and other information pertinent to operationof the chiller are automatically displayed and read on agraphic display. Other displays can be observed by press-ing the keys as labeled on the Control Center. The chillerwith the OptiView Control Center is compatible with anYORK INTERNATIONALFORM 160.73-O2(1202)YORK INTERNATIONAL71source, usually a cooling tower. The condensed refrig-erant drains from the condenser into the liquid return line, where the variable orifice meters the flow of liquid refrigerant to the evaporator to complete the refrigerant circuit.7619A(D)DETAIL A –COMPRESSOR PREROTATION VANESThe major components of a chiller are selected to handle the refrigerant, which would be evaporated at full load design conditions. However, most systems will be called upon to deliver full load capacity for only a relatively small part of the time the unit is in operation.CAPACITY CONTROLThe major components of a chiller are selected for full load capacities, therefore capacity must be controlled to maintain a constant chilled liquid temperature leaving the evaporator. Prerotation vanes (PRV), located at the entrance to the compressor impeller, compensate for variation in load (See Detail A).The position of these vanes is automatically controlled through a lever arm attached to an electric motor located outside the compressor housing. The automatic adjust-ment of the vane position in effect provides the perfor-mance of many different compressors to match various load conditions from full load with vanes wide open to minimum load with vanes completely closed.YORK INTERNATIONALFORM 160.73-O2(1202)8FIG. 2 – REFRIGERANT FLOW-THRU CHILLER PREROTATION VANES (See Detail A)SUCTIONEVAPORATORELIMINATOROIL COOLERLD00924FLOW CONTROL ORIFICESUB-COOLERCONDENSERDISCHARGE BAFFLEDISCHARGECOMPRESSORFORM 160.73-O2(1202)YORK INTERNATIONAL9START-UP PROCEDUREPre-StartingPrior to starting the chiller, observe the OptiView Control Center. Make sure the display reads SYSTEM READY TO START .To pre-start the chiller, use the following procedure: 1.Oil Heater – The oil heater must be energized for 12 hours prior to starting the chiller.2.Prior to start, the clock must be programmed for the proper day and time. Any setpoints which are desired to be changed may be programmed. All Control Cen-ter setpoints should be programmed before the chiller is started. (Refer to Form 160.54-O1).Vent any air from the chiller water boxes prior to starting the water pumps. Failure to do so will result in pass baffle damage.START-UP1.If the chilled water pump is manually operated, start the pump. The Control Center will not allow the chiller to start unless chilled liquid flow is established through the unit. (A field supplied chilled water flow switch is required.) If the chilled liquid pump is wired to the Microcomputer Control Center the pump will automatically start, therefore, this step is not neces-sary.SECTION 2SYSTEM OPERATING PROCEDURESOIL HEATERSIf the oil heater is de-energized during a shutdown period, it must be energized for 12 hours prior to starting com-pressor, or remove all oil and recharge compressor with new oil. (See “Oil Charging Procedure”, page 22.)OIL HEATER OPERATIONThe oil heater operation is controlled by the OptiView™ Control Center. The heater is turned on and off to main-tain the oil temperature to a value 50°F (10°C) above the condenser saturation temperature. This is the target value and if the oil temperature falls to 4°F (-15.5°C) or more below the target, the heater is turned on. It is turned off when the oil temperature increases to 3°F (-16°C) above the target value.If the target value is greater than 160°F (71°C), the target defaults to 160°F (71°C). If the target value is less than 110°F (43.3°C), it defaults to 110°F (43.3°C). To prevent overheating of the oil in the event of a con-trol center component failure, the oil heater thermostat (1HTR) is set to open at 180°F (82°C).CHECKING THE OIL LEVEL IN THE OIL RESERVOIRProper operating oil level – During operation, the oil level should fall to the “Operating Range” identified on the vertical oil level indicator label. See Figure 3.• If the oil level during operation is in the “OverFull” region of the oil level indicator, oil should be removed from the oil reservoir, This reduces the oil level to the “Operating Range”.• If the oil level during operation is in the “Low Oil”region of the oil level indicator, oil should be added to the oil reservoir. (See “Oil Charging Procedure”, page 22)Comply with EPA and Local regu-lations when removing or disposingof Refrigeration System oil!FIG. 3 – OIL LEVEL INDICATOR LABELLD08647YORK INTERNATIONALFORM 160.73-O2(1202)102.To start the chiller, press the COMPRESSOR START switch. This switch will automatically spring return to the RUN position. (If the unit was previously started, press the STOP/RESET side of the COMPRESSOR switch and then press the START side of the switch to start the chiller.) When the start switch is energized, the Control Center is placed in an operating mode and any malfunction will be noted by messages on a graphic display.Any malfunctions which occur during STOP/RESET are also displayed.When the chiller is shut down, the prerotation vanes will close automatically to prevent loading the compressor on start-up.When the chiller starts to operate, the following au-tomatic sequences are initiated: (Refer to Fig. 4 & 5, “Chiller Starting & Shutdown Sequence Chart”.)1.The OptiView Control Center display message willread SYSTEM PRELUBE for the first 50 seconds of the starting sequence.2.The oil pump will start to circulate oil for a 50 second pre-run to establish oil flow and adequate lubrication to all bearings, gears, and rotating surfaces within the compressor.The high and low oil pressure transducers (OP) and the oil temperature sensor (RT3) will sense any mal-function in the lubrication system.3.The anti-recycle timer software function will operate after the 50 seconds of pre-run time. At this time, the timer will be initiated and will run for 30 minutes after the compressor starts. If the chiller shuts down during this period of time, it cannot be started until the timer completes the 30 minute cycle.4.The chilled liquid pump contacts will close, start-ing the chilled liquid pump, to allow liquid flow through the evaporator when the COMPRESSOR start switch is energized.5.After the first 50 seconds of operation, the com-pressor will start.6.For display messages and information pertaining to the operation of the OptiView™ Control Center, refer to Form 160.54-O1.FIG. 4 – CHILLER STARTING SEQUENCE & SHUTDOWN SEQUENCE (EM STARTER & SOLID STATE STARTER)LD04040** NOT FOR ALL SHUTDOWNS. REFER TO “DISPLAY MES-SAGES” SECTION OF THIS MANUAL.FORM 160.73-O2(1202)2FIG. 5 – CHILLER STARTING SEQUENCE & SHUTDOWN SEQUENCE (VARIABLE SPEED DRIVE)LD04130CHILLER OPERATIONAfter the compressor reaches its operating speed, the Prerotation Vanes will begin to open under the control of the Microprocessor Board which senses the leaving chilled liquid temperature. The unit capacity will vary to maintain the leaving CHILLED LIQUID TEMPERA-TURE setpoint. The Prerotation Vanes are modulated by an actuator under the control of the Microprocessor Board. The vane control routine employs proportional plus derivative (rate) control action. A drop in chilled liquid temperature will cause the actuator to close the Prerotation Vanes to decrease chiller capacity. When the chilled liquid temperature rises, the actuator will open the Prerotation Vanes to increase the capacity of the chiller.However, the current draw (amperes) by the compressor motor cannot exceed the setting of the % CURRENT LIMIT at any time during the unit operation, since the Microcomputer Control Center 40 to 100% three-phase peak current limit software function, plus the 3-phase 100% solid state overload current limiter (CM-2), on Electro-Mechanical Starter applications, or the Solid State Starter current Limit function will override the temperature control function and prevent the Prerotation Vanes from opening beyond the % CURRENT LIMIT setting.** NOT FOR ALL SHUTDOWNS. REFER TO “DISPLAY MES-SAGES” SECTION OF THIS MANUAL.If the load continues to decrease, after the Prerotation Vanes are entirely closed, the chiller will be shut down by the Leaving Chilled Liquid – Low Temperature Control.CONDENSER WATER TEMPERATURE CONTROLThe YORK MaxE TM chiller is designed to use less power by taking advantage of lower than design temperatures that are naturally produced by cooling towers throughout the operating year. Exact control of condenser water such as a cooling tower bypass, is not necessary for most installations. The chiller requires only that the minimum condenser water temperature be no lower than the valuedetermined by referring to the formula below:where:ECWT = Entering Condensing Water Temperature LCWT = Leaving Chilled Water TemperatureC Range = Condensing water temperature range at the given load condition.Min. ECWT = LCWT – C RANGE + 17ºF Min. ECWT = LCWT – C RANGE + 9.4ºCFORM 160.73-O2(1202)OPERATING INSPECTIONS – See Section 2By following a regular inspection using the display readings of the Microcomputer Control Center, and maintenance procedure, the operator will avoid serious operating difficulty. The following list of inspections and procedures should be used as a guide.Daily1.Check OptiView™ Control Center displays.2.If the compressor is in operation, check the bearing oil pressure on the SYSTEM Screen. Also check the oil level in the oil reservoir. Operating oil level should be between the upper and lower sight glasses. Drain or add oil if necessary.3.Check entering and leaving condenser water pressure and temperatures for comparison with job design conditions. Condenser water temperatures can be checked on the SYSTEM Screen.4.Check the entering and leaving chilled liquid tem-peratures and evaporator pressure for comparison with job design conditions on the SYSTEM Screen.5.Check the condenser saturation temperature (based upon condenser pressure sensed by the condenser transducer) on the SYSTEM Screen.6.Check the compressor discharge temperature on the SYSTEM Screen. During normal operation discharge temperature should not exceed 220°F (104°C).At start-up, the entering condenser water temperature may be as much as 25°F (14°C) colder than the standby return chilled water temperature. Cooling tower fan cycling will normally provide adequate control of the entering condenser water temperature on most instal-lations.OPERATING LOG SHEETA permanent daily record of system operating conditions (temperatures and pressures) recorded at regular inter-vals throughout each 24 hour operating period should be kept.An optional status printer is available for this purpose or Fig. 6 shows a log sheet used by YORK Personnel for recording test data on chiller systems. It is available from the factory in pads of 50 sheets each under Form 160.44-F7 and may be obtained through the nearest YORK office. Automatic data logging is possible by connecting the optional printer and programming the DATA LOGGER function.An accurate record of readings serves as a valuable reference for operating the system. Readings taken when a system is newly installed will establish normal conditions with which to compare later readings.For example, an increase in condenser approach temperature (condenser temperature minus leaving condenser water temperature) may be an indication of dirty condenser tubes.FIG. 6 – LIQUID CHILLER LOG SHEETS *NOTE: These items can be printed by an electronic printer connected to the Microboard and pressing the PRINTkey on the Keypad, or automatically using the Data Logger feature.LD0046723889AFORM 160.73-O2(1202)27.Check the compressor motor current on the SYSTEM Screen.8.Check for any signs of dirty or fouled condenser tubes. (The temperature difference between water leaving condenser and saturated condensing tem-perature should not exceed the difference recorded for a new unit by more than 4°F, 2.2°C).Weekly1.Check the refrigerant charge. (See “Checking The Refrigerant Charge”, page 28.)2.Leak check the entire chiller.Quarterly1.Perform chemical analysis of oil.Semi-Annually (or more often as required) 1.Change and inspect compressor oil filter element.2.Oil return system. a.Change dehydrator.b.Check nozzle of eductor for foreign particles. 3.Check controls and safety cutouts.Annually (more often if necessary)If quarterly inspection indicates oil is fine, replacing the oil is not necessary.1.Drain and replace the oil in the compressor oil sump. (See “Oil Charging Procedure” page 22.) 2.Evaporator and Condenser. a.Inspect and clean water strainers. b.Inspect and clean tubes as required. c.Inspect end sheets.pressor Drive Motor (See motor manufacturers maintenance and service instruction supplied with unit) a.Clean air passages and windings per manufac-turers instructions.b.Meg motor windings – See Fig. 13 for details.c.Lubricate per motor manufacturer recommenda-tions.4.Inspect and service electrical components as necessary.5.Perform refrigerant analysis.NEED FOR MAINTENANCE OR SERVICEIf the system is malfunctioning in any manner or the unit is stopped by one of the safety controls, consult the “Operation Analysis Chart”, (Table 1), pages 23 and 24 of this instruction. After consulting this chart, if you are unable to make the proper repairs or adjust-ments to start the compressor or the particular trouble continues to hinder the performance of the unit, please call the nearest YORK District Office. Failure to report constant troubles could damage the unit and increase the cost of repairs.STOPPING THE SYSTEMThe Optiview™ Control Center can be programmed to start and stop automatically (maximum, once each day) whenever desired. Refer to Form 160.54-O1. To stop the chiller, proceed as follows:1.Push the COMPRESSOR STOP/RESET switch. The compressor will stop automatically. The oil pump will continue to run for coastdown period. The oil pump will then stop automatically.2.Stop the chilled water pump (if not wired into the Microcomputer Control Center, in which case it will shut off automatically simultaneously with the oil pump.) (The actual water pump contact operation is dependent upon the position of Microboard jumper J54.)3.Open the switch to the cooling tower fan motors, if used.4.The compressor sump oil heater is energized when the unit is stopped.PROLONGED SHUTDOWNIf the chiller is to be shut down for an extended period of time (for example, over the winter season), the following paragraphs outline the procedure to be followed.1.Test all system joints for refrigerant leaks with aFORM 160.73-O2(1202)leak detector. If any leaks are found, they should be repaired before allowing the system to stand for a long period of time.During long idle periods, the tightness of the system should be checked periodically.2.If freezing temperatures are encountered while thesystem is idle, carefully drain the cooling water from the cooling tower, condenser, condenser pump, and the chilled water system-chilled water pump and coils.Open the drains on the evaporator and condenser liquid heads to assure complete drainage. (If a Vari-able Speed Drive, drain its water cooling system. If Solid State Starter. drain water from starter cooling loop.)3.On the SETUP Screen, disable the clock. This con-serves the battery.4.Open the main disconnect switches to the compressormotor, condenser water pump and the chilled water pump. Open the 115 volt circuit to the Control Cen-ter.FORM 160.73-O2(1202)SECTION 3SYSTEM COMPONENTS DESCRIPTIONMOTOREVAPORATORCOMPRESSORSUCTIONDUAL RELIEF VALVESSIGHT GLASSVARIABLE SPEEDOIL PUMP CONTROLBOX REFRIGERANT CHARGING VALVE00611vipFRONT VIEWFIG. 7 – SYSTEM COMPONENTSOPTIVIEW CONTROLCENTER3FORM 160.73-O2(1202)FIG. 7 – SYSTEM COMPONENTS (CONT’D)28778ADISCHARGE LINEOIL COOLEROIL RESERVOIRPUMPREAR VIEWFORM 160.73-O2(1202)GENERALThe YORK Model YK MaxE TM Centrifugal Liquid Chiller is completely factory-packaged including evapo-rator, condenser, compressor, motor, lubrication system, OptiView Control Center, and all interconnecting unit piping and wiring.COMPRESSORThe compressor is a single-stage centrifugal type pow-ered by an open-drive electric motor.The rotor assembly consists of a heat-treated alloy steel drive shaft and impeller shaft with a cast aluminum, fully shrouded impeller. The impeller is designed for bal-anced thrust and is dynamically balanced and over-speed tested. The inserted type journal and thrust bearings are fabricated of aluminum alloy. Single helical gears with crowned teeth are designed so that more than one tooth is in contact at all times. Gears are integrally assembled in the compressor rotor support and are film lubricated. Each gear is individually mounted in its own journal and thrust bearings.The open-drive compressor shaft seal is a double bellows cartridge style with ceramic internal and atmospheric seal faces. The seal is oil-flooded at all times and is pressure-lubricated during operation.CAPACITY CONTROLPrerotation vanes (PRV) modulate chiller capac-ity from 100% to as low as 15% of design for normal air conditioning applications. Operation is by an external, electric PRV actuator which automatically controls the vane position to main-tain a constant leaving chilled liquid temperature.COMPRESSOR LUBRICATION SYSTEM(See Fig. 8)The chiller lubrication system consists of the oil pump, oil filter, oil cooler and all interconnecting oil piping and passages. There are main points within the motor-compressor which must be supplied with forced lubri-cation as follows: pressor Drive Shaft (Low Speed)a.Shaft seal.b.Front and rear journal bearings – one on eachside of driving gear.c.Low speed thrust bearing (forward and reverse).pressor Driven Shaft (High Speed)a.Forward and reverse high speed thrustbearing.b.Two journal bearings.3.Speed Increasing Gearsa.Meshing surfaces of drive and pinion gear teeth.To provide the required amount of oil under the nec-essary pressure to properly lubricate these parts, a motor driven submersible oil pump is located in a remote oil sump.Upon pressing of the COMPRESSOR START switchon the Control Center, the oil pump is immediately energized. After a 50 second pre-lube period, the com-pressor motor will start. The oil pump will continue torun during the entire operation of the compressor, andfor 150 seconds during compressor coastdown.The submerged oil pump takes suction from the sur-rounding oil and discharges it to the oil cooler where heatis rejected. The oil flows from the oil cooler to the oil filter. The oil leaves the filter and flows to the emergencyoil reservoir where it is distributed to the compressor bearings. The oil lubricates the compressor rotating components and is returned to the oil sump.There is an emergency oil reservoir located at the highest point in the lubrication system internally inthe compressor. It provides an oil supply to the various bearings and gears in the event of a system shutdown due to power failure. The reservoir, located on the top ofthe compressor, allows the oil to be distributed throughthe passages by gravity flow, thus providing necessary lubrication during the compressor coastdown.3。