铁路车辆防腐涂装技术方案
高速铁路钢轨的防腐与防锈技术

高速铁路钢轨的防腐与防锈技术近年来,随着交通运输的快速发展,高速铁路成为人们出行的重要选择之一。
而高速铁路的安全运行离不开稳固耐用的钢轨。
然而,钢轨在长时间的使用过程中,容易受到腐蚀和锈蚀的影响,影响铁路的运行安全。
因此,高速铁路钢轨的防腐与防锈技术成为一个重要的研究方向。
为了保证高速铁路钢轨的长期稳定使用,需要采取一系列的防腐与防锈措施。
首先,对于钢轨的表面防腐,可以使用喷涂防腐涂层的方法。
通过在钢轨表面喷涂防腐涂料,可以增加钢轨的耐腐蚀性能,延长其使用寿命。
防腐涂层应具备良好的附着力,不易剥落,能够抵抗酸碱侵蚀和大气腐蚀。
同时,还需要具备一定的耐磨性和耐热性,以适应钢轨在高速列车行驶过程中的各种挑战。
其次,高速铁路钢轨的防腐与防锈还需要考虑其内部结构的保护。
钢轨内部经常有水分的渗入,容易引发铁的生锈。
因此,可以采取防水、防潮的措施,例如在铁轨焊缝和连接处进行密封处理,防止水分渗入,从而延缓铁轨的锈蚀速度。
此外,对于已经出现锈蚀的钢轨,需要及时采取修复和保养措施。
可以使用机械磨削等方法去除铁轨表面的锈蚀层,然后进行喷涂防腐涂料,以恢复钢轨的光洁度和耐腐蚀性能。
同时,还需要定期对钢轨进行检测和维护,及时修复出现的损伤,避免损坏进一步扩大,保证高速铁路的安全运营。
除了上述的传统防腐防锈技术外,还有一些创新的技术在高速铁路钢轨的防腐与防锈方面得到了应用。
一种新型的防腐技术是利用纳米涂料技术。
纳米涂料具有优异的防腐蚀性能和抗氧化性能,可以在钢轨表面形成一层厚度非常薄的涂层,有效隔离空气和钢轨之间的接触,防止氧化反应的发生,从而延长钢轨的使用寿命。
另外,近年来也开始研究利用电化学防腐技术来保护高速铁路钢轨。
电化学防腐是通过在钢轨表面形成一层保护性的薄膜,以阻止腐蚀物质的进一步侵蚀。
电化学防腐技术具有无毒、无害、无污染的特点,克服了传统防腐方法中有害物质的缺点,是一种环保的防腐技术。
综上所述,高速铁路钢轨的防腐与防锈技术是保证铁路运行安全和提高钢轨使用寿命的重要措施。
城轨车辆用水性环氧底漆的涂装工艺及其技术要求

城轨车辆用水性环氧底漆的涂装工艺及其技术要求城轨车辆用水性环氧底漆的涂装工艺及其技术要求随着我国城市轨道交通建设的不断发展,预计在2016 年总建设里程会达到2500km,这就需要配备1万辆左右的车。
目前,国内的城轨车辆表面涂漆大多采用溶剂型涂料,而溶剂型涂料内含有重金属等有害物质,近年来,对溶剂型涂料的有害物质的掌控更加严格,具有较高的防腐性能且环保的水性涂料成为人们关注的重点。
水性涂料自身较强的防火、防腐和耐化学性能,也成为我国未来城轨车辆涂装施工的选择方向。
一、水性环氧涂料的性能(一)防腐性能城轨车辆的底材是由不锈钢、玻璃钢、铝合金等不相应的材料组合而成,水性环氧底漆使用在这种底材上需要有强大的附着力、防腐蚀性能。
水性环氧底漆要想获取与溶剂型相似的性能,在技术上有一定的困难,水性涂料与溶剂型涂料成膜机理有所不同导致两者涂抹性能有相应的偏差。
溶剂型环氧涂料的成膜机理是由环氧树脂同固化剂运用分子形式溶解于有机溶液内部,有很高的防腐性能。
水性环氧树脂涂料成膜机理是因为多数水分不断蒸发,环氧树脂粒子实施接触,进而形成紧密堆积的结构状态,剩下的水分及固化分子都处于分散粒子内部,水分经过蒸发,进而分散相粒子产生凝结,形成较为紧密的六边形结构。
与此同时,固化剂分子导致分子相粒子的界面及内部出现固化反应,树脂的玻璃的温度不断上升,扩散变慢粒子不容易进行凝结。
固化反应无法完全展开,无法形成计较均匀的涂抹,致使防腐性能与溶剂型涂料出现较大差异。
(二)施工性能现阶段,城轨车辆涂装工艺要求水性环氧底漆应该具有下列功能。
根据现今溶剂型施工工艺,底漆施工的不同工序一般间隔24 小时,水性环氧底漆无法改变其生产效率。
进行底漆施工采用高压无气展开喷涂,通常给予两次喷涂直至达到要求的厚度。
湿碰湿施工环节每次的间隔时间为20―30mi n。
底漆完工之后开始烘烤,烘烤的温度设置在70oC,要求良好的涂膜外观。
之后采用砂纸进行打磨。
铁路货车用水性涂料及涂装技术研究
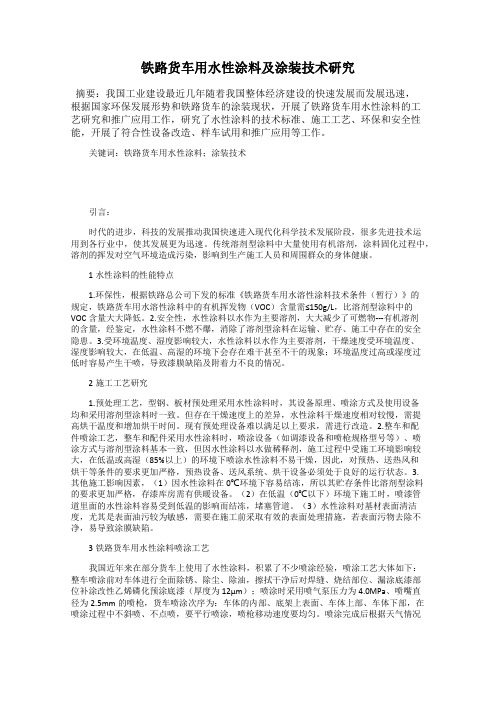
铁路货车用水性涂料及涂装技术研究摘要:我国工业建设最近几年随着我国整体经济建设的快速发展而发展迅速,根据国家环保发展形势和铁路货车的涂装现状,开展了铁路货车用水性涂料的工艺研究和推广应用工作,研究了水性涂料的技术标准、施工工艺、环保和安全性能,开展了符合性设备改造、样车试用和推广应用等工作。
关键词:铁路货车用水性涂料;涂装技术引言:时代的进步,科技的发展推动我国快速进入现代化科学技术发展阶段,很多先进技术运用到各行业中,使其发展更为迅速。
传统溶剂型涂料中大量使用有机溶剂,涂料固化过程中,溶剂的挥发对空气环境造成污染,影响到生产施工人员和周围群众的身体健康。
1水性涂料的性能特点1.环保性,根据铁路总公司下发的标准《铁路货车用水溶性涂料技术条件(暂行)》的规定,铁路货车用水溶性涂料中的有机挥发物(VOC)含量需≤150g/L,比溶剂型涂料中的VOC含量大大降低。
2.安全性,水性涂料以水作为主要溶剂,大大减少了可燃物---有机溶剂的含量,经鉴定,水性涂料不燃不爆,消除了溶剂型涂料在运输、贮存、施工中存在的安全隐患。
3.受环境温度、湿度影响较大,水性涂料以水作为主要溶剂,干燥速度受环境温度、湿度影响较大,在低温、高湿的环境下会存在难干甚至不干的现象;环境温度过高或湿度过低时容易产生干喷,导致漆膜缺陷及附着力不良的情况。
2施工工艺研究1.预处理工艺,型钢、板材预处理采用水性涂料时,其设备原理、喷涂方式及使用设备均和采用溶剂型涂料时一致。
但存在干燥速度上的差异,水性涂料干燥速度相对较慢,需提高烘干温度和增加烘干时间。
现有预处理设备难以满足以上要求,需进行改造。
2.整车和配件喷涂工艺,整车和配件采用水性涂料时,喷涂设备(如调漆设备和喷枪规格型号等)、喷涂方式与溶剂型涂料基本一致,但因水性涂料以水做稀释剂,施工过程中受施工环境影响较大,在低温或高湿(85%以上)的环境下喷涂水性涂料不易干燥,因此,对预热、送热风和烘干等条件的要求更加严格,预热设备、送风系统、烘干设备必须处于良好的运行状态。
厂修铁路货车油漆涂装质量的工艺控制

操作者掉接技能培训.
最大应 力计算值 : ( 5 m , x = P/ + A = 7 9 7 . 5 3 4 / 1 1 3 . 1 = 7 . 0 5 N / mm ̄ , 满 足要 求。 ( 3 ) 配 1 2 全牙丝杆 使用中1 2 x 5 0 的 内膨胀 螺栓。 所受的最 大拉 力P …= 7 9 7 . 5 3 4 N, 小于允许抗 拉静荷 载1 4 6 8 0 N, 满 足要 求。
目 擅童
起 抠 , 处 理 不 净 舍 髟 响 津 曩 附 着 力 .
: l i E,蔓采无可见的鼻孔. 日 检查
器 中 和
焊孔的存在舍群t庸蚀 .使潦奠t 焊乳较小. 若焊接检查员两意,可 裂、起泡,使盒一衰面早蚀. 在衰面处理后用环氯填料封填;若 面积丈或太多.孵重埠. 预防t改进婢接工艺方法.
寰酉.
检查方法
向麓及危害 形成流撞后使车体外观整. 海荆 特濠膜干
改正 /预防措麓 打磨.
抛丸后钢丸清理不净.残留于心盘座 用高压风进行反复吹扫。 直至精理 辞■tI 啦 : 干净, 设计制作防护罩在抽丸前对 影响油潦附着. 并且在车件落成时暑 心盘座等姓进行防护。以防蛔丸进 碚伤心盘磨托盘,謦响行车安全. A其中。 处理不净套导藏漳膜附着力差、 珊落 预防,不可避免. 轴 泡. 改正t刮铲或打磨清豫. 遗常为t牲、油膳性.吸湿 , 薯蔗墨 预防,不可避免.
四线制
计算点均 检查
垢. 并且 氯化皮、 铁 ■和油 漳 衄 8 3 濠屡嶂附 着 曲已基 奉清瞎 . 萁 囊蕾材附着牢固.
帽丸残余t 蔓求抛丸后车体 鲁齄无帼丸殪曹. 目 控蠢 t V  ̄ l h 要求清除干净. 目 测检查
攘 卺
铁路货车涂装工艺2007
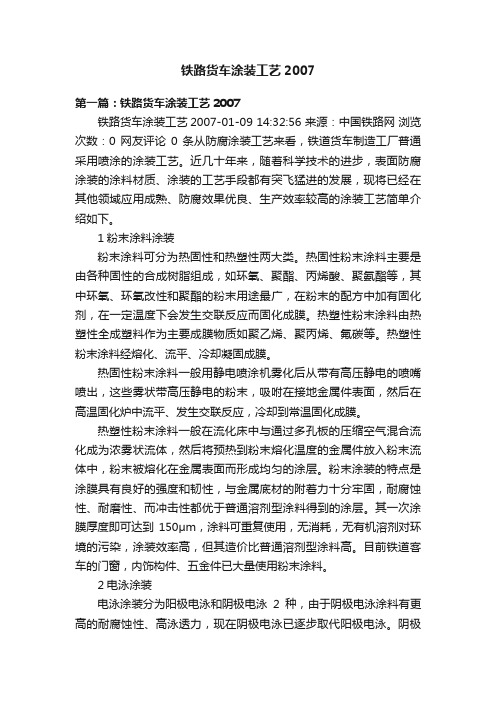
铁路货车涂装工艺2007第一篇:铁路货车涂装工艺2007铁路货车涂装工艺2007-01-09 14:32:56 来源:中国铁路网浏览次数:0 网友评论0 条从防腐涂装工艺来看,铁道货车制造工厂普通采用喷涂的涂装工艺。
近几十年来,随着科学技术的进步,表面防腐涂装的涂料材质、涂装的工艺手段都有突飞猛进的发展,现将已经在其他领域应用成熟、防腐效果优良、生产效率较高的涂装工艺简单介绍如下。
1粉末涂料涂装粉末涂料可分为热固性和热塑性两大类。
热固性粉末涂料主要是由各种固性的合成树脂组成,如环氧、聚酯、丙烯酸、聚氨酯等,其中环氧、环氧改性和聚酯的粉末用途最广,在粉末的配方中加有固化剂,在一定温度下会发生交联反应而固化成膜。
热塑性粉末涂料由热塑性全成塑料作为主要成膜物质如聚乙烯、聚丙烯、氟碳等。
热塑性粉末涂料经熔化、流平、冷却凝固成膜。
热固性粉末涂料一般用静电喷涂机雾化后从带有高压静电的喷嘴喷出,这些雾状带高压静电的粉末,吸咐在接地金属件表面,然后在高温固化炉中流平、发生交联反应,冷却到常温固化成膜。
热塑性粉末涂料一般在流化床中与通过多孔板的压缩空气混合流化成为浓雾状流体,然后将预热到粉末熔化温度的金属件放入粉末流体中,粉末被熔化在金属表面而形成均匀的涂层。
粉末涂装的特点是涂膜具有良好的强度和韧性,与金属底材的附着力十分牢固,耐腐蚀性、耐磨性、而冲击性都优于普通溶剂型涂料得到的涂层。
其一次涂膜厚度即可达到150μm,涂料可重复使用,无消耗,无有机溶剂对环境的污染,涂装效率高,但其造价比普通溶剂型涂料高。
目前铁道客车的门窗,内饰构件、五金件已大量使用粉末涂料。
2电泳涂装电泳涂装分为阳极电泳和阴极电泳2种,由于阴极电泳涂料有更高的耐腐蚀性、高泳透力,现在阴极电泳已逐步取代阳极电泳。
阴极电泳涂料是由用有机酸中具有叔胺基的合成树脂形成的水溶性或胶体分散型树脂、添加剂、有机溶剂和纯水配制而成,树脂在水中离解,带正电荷,被涂金属件作阴极,另一不锈钢板作阳极,浸在阴极电泳涂液中通直流电压,在电场的作用下伴随着复杂的物理化学、胶体化学、电化学过程,合成树脂沉积在金属件表面,然后在高温固化炉中固化成膜。
轨道工程防腐漆施工方案

轨道工程防腐漆施工方案一、项目概况随着城市建设的不断发展,轨道交通工程已成为城市交通的重要组成部分。
轨道工程的建设对于城市交通的发展起着至关重要的作用,然而长期以来,轨道工程在使用中经常会受到海洋腐蚀、酸雨侵蚀、车辆碰撞等多方面的影响,导致建设后出现腐蚀、老化等问题。
为了保证轨道设施的使用寿命和安全性,轨道工程防腐漆的施工变得尤为重要。
二、施工目的本次轨道工程防腐漆施工的目的是对原有轨道设施进行防腐处理,延长其使用寿命和保障使用安全。
三、施工对象本次施工对象为某城市地铁1号线全线轨道设施。
四、施工内容1. 对轨道设施进行表面处理,包括清理、除锈、打磨等工序;2. 涂刷防腐漆,对轨道设施进行保护处理;3. 检验、验收。
五、施工工艺1. 清理工序:a)采用机械清理和化学清洗相结合的方法,将轨道设施表面的锈蚀物和杂物去除干净;b) 清洗完毕后,以清水冲洗干净。
2. 除锈工序:a) 采用除锈机械对轨道设施进行除锈处理,确保表面光洁;b) 除锈完毕,再次清洗干净。
3. 打磨工序:a) 使用砂轮对轨道设施进行打磨,确保表面光滑;b) 打磨完毕后,进行清洗。
4. 防腐漆施工:a) 选用符合要求的防腐漆进行施工,确保涂刷均匀;b) 根据防腐漆的特性和要求进行施工,确保达到防腐效果;c) 确保涂刷完毕后,进行检查,确认无漏刷。
5. 检验验收:a) 对施工完毕的轨道设施进行检验,确认质量达标;b) 验收合格后,进行签字确认。
六、施工人员1. 负责人一名,负责施工方案的制定和工程的管理;2. 施工技术人员若干名,负责施工工艺的实施和现场管理;3. 施工工人若干名,负责具体施工工序。
七、施工材料1. 除锈机械和清洗设备;2. 防腐漆;3. 涂刷工具和施工辅料;4. 安全防护用品。
八、施工设备1. 除锈机械;2. 清洗设备;3. 涂刷设备。
九、施工安全1. 施工前,对施工区域进行安全检查,确保无隐患;2. 施工人员必须佩戴安全防护用品,并按照规定进行作业;3. 施工现场必须设置明显的安全警示标识,确保施工现场安全;4. 施工现场必须配备急救设备,确保施工人员的安全;5. 施工过程中,禁止使用明火,确保施工安全。
工程车辆防腐施工方案

工程车辆防腐施工方案背景介绍工程车辆在施工和运输过程中,面临着各种外界影响,包括酸雨、盐雾、高温、高湿等环境因素,容易导致车辆表面出现腐蚀、褪色、锈蚀等问题,甚至影响车辆性能和寿命。
因此,工程车辆防腐施工方案的制定十分重要。
防腐施工方案表面处理首先,要对车辆表面进行适当的处理,包括去除锈蚀、清洗和除油等。
具体方法包括:•磨光:利用砂纸、钢丝刷等工具将表面锈蚀处磨光,以达到达到平滑的效果。
•喷砂:将金属表面进行喷砂处理,利用高压气流冲击表面,去除腐蚀、锈斑和老底漆,达到表面清洁度的要求。
•化学处理:利用化学剂(如磷化剂、酸洗剂等)对金属表面进行溶解、萃取和转化处理,以去除氧化膜和表面污染物。
防腐涂层在表面处理完成后,需要对工程车辆涂上防腐涂层,以保护车身不被腐蚀和锈蚀。
根据不同需要,可以选择以下几种涂层。
•有机涂料:例如丙烯酸树脂、聚氨酯涂料、烤漆等,具有良好的防水性能和耐大气腐蚀性能,但其使用寿命较短。
•无机涂料:例如锌粉涂料、磷化涂料等,具有较好的防腐性能和耐用性,但是涂层产生的废气和废液对环境和工人健康有一定影响。
•防腐膜:将聚乙烯、聚丙烯等高分子材料,制成薄膜,缠绕在钢铁表面,从而隔绝氧气和水分,限制钢铁的腐蚀和锈蚀。
补漆及保养在施工车辆经过一段时间后,涂层可能会出现局部的氧化、脱落和褪色现象。
因此需要做好定期的保养和补漆工作。
•定期清洗:对车辆表面进行清洗,清除表面的污垢和尘土,以保证涂层的外观光泽。
•定期检查:定期对车辆表面进行检查,发现损伤或涂层表层破损的情况立刻进行补漆,防止腐蚀进一步发展。
结论工程车辆是建筑施工和运输中必不可少的设备,因此加强其防腐施工保护对于延长其使用寿命和减少维修成本都具有非常重要的意义。
在实际的施工过程中,应该根据车辆特点和实际需求进行定制施工方案,遵循规范,提高施工质量。
铁道车辆涂装质量问题工艺研究与解决方案

铁道车辆涂装质量问题工艺研究与解决方案摘要:随着《挥发性有机物(VOCs)污染防治技术政策》、《大气污染防治行动计划》等相继出台,我国对重点地区和重点行业VOCs进行管控,我国对VOCs 的排放标准越来越高,对其排放标准也越来越高。
在《“十三五”挥发性有机物污染防治工作方案》中,我国环保部门明确指出,要加大对工业企业的综合整治力度,同时要加强对工业生产和生活活动的监管。
山东省颁布的《挥发性有机物排放标准第5部分:表面涂装行业》中,对其进行了较高的要求,并对其进行了相应的规范。
针对我国目前的环境形势和当地的管控要求,迫切需要对有轨电车漆膜设备进行污染防治。
针对目前铁路运输中普遍使用的涂料设备及涂料工艺中的有机尾气特征,对涂料设备进行了改进。
关键词:轨道车辆涂装;VOC;环保改造1轨道车辆涂装装备轨道交通车辆的涂装系统以环氧底漆、不饱和聚醋腻子、聚氨醋中间涂漆及面漆为主体,在2018之前,以溶剂性涂料为主,近年来,由于其技术及性能的不断提高,在市政铁路及部分高铁列车上得到了广泛的应用。
在这些油漆中,以环氧和聚氨醋漆为主要的溶剂型油漆,在喷射的过程中会形成漆雾、甲苯、二甲苯、乙酸乙醋、非甲烷总碳氢化合物等有机废气,所占比例约为40-60%。
当前,铁路交通工具的油漆施工还是以人工操作为主,其中最常用的是高压无气喷雾和空气喷雾,近年来,在施工中逐渐采用了喷射机器人和静电喷雾技术。
为确保产品的品质,施工工作将在油漆车间进行,每个油漆工序都需要在油漆车间进行,油漆表面烘干后,再将油漆送到烘干车间或天然烘干工作台。
为了便于工艺的实现,喷漆房的主体部分使用了干式喷烘一体结构,它具备了空气过滤、加热、循环、过喷涂料吸附及有机溶剂处理等多种功能。
在进行喷漆的时候,利用吹风系统的加热、去湿和过滤,可以获得洁净的空气,从而确保室内有合适的温度和湿度。
与此同时,在汽车周围,会产生一种层流空气,呈现包裹状,将过喷漆雾向下压。
- 1、下载文档前请自行甄别文档内容的完整性,平台不提供额外的编辑、内容补充、找答案等附加服务。
- 2、"仅部分预览"的文档,不可在线预览部分如存在完整性等问题,可反馈申请退款(可完整预览的文档不适用该条件!)。
- 3、如文档侵犯您的权益,请联系客服反馈,我们会尽快为您处理(人工客服工作时间:9:00-18:30)。
铁路车辆防腐涂装工程施工方案编制单位:西京建设有限公司法定代表人或授权委托人:日期:2019年03月06日铁路车辆防腐涂装技术方案一、项目概述铁路车辆的防护主要采用油漆(涂料)进行防护,其间经历了几次大的变化。
客车用涂料中底漆由酚醛、醇酸铁红或磁化铁防锈漆改为环氧、环氧酌磷酸锌或铬酸锌底漆,腻子由酩胶、石青腻子逐步改为环氧酷或不饱和聚酷腻子,面漆则由丙烯酸改性醇酸、丙烯酸聚氨酷替代了大部分普通醇酸漆;2001年底铁道部运输局装备部己要求从2002年下半年开始,新造客车全部采用双组份涂料。
货车用厚浆型醇酸漆在20世纪90年代初全面推广,取代原用的酚醛、醇酸漆。
目前新造车辆己广泛使用钢材喷砂(抛丸)预处理技术和磷化的方法,使用预涂底漆作工序间防锈,并有部分工厂引进了涂漆机械手和双组份高压无气喷涂机,建立了喷漆房和烘房、涂装流水线以及大量工艺装备,大大提高了作业效率。
在涂装工艺方面,1998年有关单位参照国际铁路联盟UIC842标准制订了第一个关于涂装技术的全面、综合性的铁道行业标准——TB/T2879.1-6-1998《铁路机车车辆涂料及涂装》系列标准。
整个标准包括了6个部分:(1)涂料供货技术条件;(2)涂料检验方法;(3)金属和非金属材料表面处理技术条件;(4)货车防护和涂装技术条件;(5)客车和牵引动力车的防护和涂装技术条件;(6)涂装质量检查和验收规程。
标准涉及了铁路机车车辆防护用涂料及涂装工作的各个方面,其特点是将涂装工作做为一个整体进行考虑,主要内容包括:(1)根据涂料产品的特点,将产品质量检验工作分为三种阶段分别进行,即进货涂料、待涂装涂料和涂装后涂膜的检验。
二、实施工艺方案工艺流程:车厢表面高压水喷射清理、砂轮机机械打磨除锈、高压水喷射清洗、刮涂腻子、环氧防腐底漆、环氧中间漆、耐候可复涂聚氨酯面漆。
铁路客车和货车车体结构采用了不同的涂装系。
一般客车(包括机车)为:表面处理加预涂底漆,底漆2道,腻子5~7道,中间涂层1道,面漆2道:内侧则在底漆之上加涂1道阻尼(防腐)涂料。
货车为:表面处理加预涂底漆,厚浆型底漆2道、厚浆型面漆2道(或底面合一厚浆漆2道):转向架部分通常为防锈底漆1道加面漆1道。
2.1预涂底漆目前铁道部大部分车辆厂都采用钢材喷(抛)丸的方法对钢材表面进行预处理,对薄板(≤4mm)则多采用磷化方法,之后涂覆预涂底漆(车间底漆)。
主要使用品种有丙烯酸类、环氧类、聚乙烯醇缩丁醛类(乙烯磷化底漆类)和无机富锌类涂料。
为适应钢材预处理线的要求,这类底漆的主要特点是干燥快,规定指标为表干时间≤5min,同时具有可焊性。
[1992]334号铁道部文件中,规定了预涂底漆及部分车辆用涂料的技术要求,表3中即为其各项要求指标。
表3 预涂底漆技术要求预涂底漆的主要问题是:由于车辆制造过程中多采用电焊加工,客车墙体还需火工校平,对大部分涂料来说,有机成膜物烧损严重,味道大,如果涂膜过厚还会影响到焊接质量,过薄则防锈性能下降。
无机富锌底漆虽然烧损小,防锈性能好,但表面处理要求高,采用醇酸或环氧酷类等油性防锈底漆时存在配套性问题,再加上锌蒸汽的负面影响,用户较少。
从理论上说,使用预涂底漆的主要目的是工序间防锈,在涂防锈底漆前应全部清除,但实际上车辆制造厂通常均直接在其上涂覆底漆。
由于预涂底漆防锈质量较差,导致防锈底漆不能充分发挥作用,会使整个涂装系的防护质量下降。
近年笔者曾多次提出修订预涂底漆技术条件,制订铁道行业标准。
由于上述几种原因,南车集团近期考虑对薄板以磷化替代预涂底漆,目前正在试验考查过程中。
防锈底漆铁道车辆近年主要使用的防锈底漆品种有:无机富锌底漆,环氧富锌底漆,醇酸底漆,酚醛防锈底漆,环氧醋防锈底漆,双组份环氧底漆,环氧聚氨酷底漆等。
各工厂根据车辆的要求及涂装工艺情况,选用不同品种和牌号的涂料。
富锌底漆主要用于出口车,醇酸、酚醛防锈底漆主要用于旧车修理,而新造车则多采用环氧酷防锈底漆、双组份环氧或环氧聚氨酯底漆等。
施工时通常采用高压无气喷涂,一般为1-2道,干膜厚度60μm。
表4为TB/T260-2001《铁道机车车辆防锈底漆》规定的技术条件。
为了使车体外表平整美观,铁路客车和机车制造过程中大量使用了腻子进行找平,目前主要使用环氧脂和不饱和聚脂(原子灰)腻子。
表5为TB/T2393-2001《铁路机车车辆面漆》标准的附录B(腻子产品的技术要求》中的技术指标。
表5 腻子的技2.4中间涂层中间涂层的作用是增加底漆(或腻子膜)与面漆之间的附着力,并改善面漆的外观丰满度。
与面漆相比,通常中间涂层的颜料份相对较高,这样可填补微小的缺陷,用在对外观要求较高的场合效果显著。
目前大部分新造客车和机车上均己采用中间涂层。
表6为TB/T2393-2001附录A中对中间涂层的技术要求。
表6 中间涂层的2.5面漆新造铁路客车和机车用面漆以丙烯酸改性醇酸磁漆、及丙烯酸改性聚氨酷磁漆为主,其中25B型客车仍为绿色为主,25G和25K型车则多用红(桔红)白相间和蓝(酞普蓝)白相间的颜色构图。
由于车体表面平整度的问题,前一段新造车多采用亚光(或半光)面漆,600镜面光泽值为40%~70%,但运输局己要求今后以高光漆(光泽值80%以上)为主。
修理车原则上仍沿用原车涂装系。
三、施工技术措施1、砂轮机除锈工艺1.1针对铁路车厢防腐涂装,金属表面预处理严格按照技术要求及相关规范进行。
1.2 动力工具除锈后表面应干燥、无油污、无氧化皮、无锈迹、无灰尘,达到国家标准《涂装前钢材表面锈蚀等级和除锈等级》规定。
1.3对腐蚀严重部位用电动角磨机、电动网刷对金属表面上的污物、焊渣、铁锈、氧化皮彻底清除干净,特别是(夹角、死角)等部位,使基层表面露出明显的金属光泽。
除锈专用旋转丝刷不同于常规的砂轮机动力工具,可针对锅炉钢梁节点、角落狭小的部位除锈处理,除锈彻底不留死角。
1.4 不易打磨的部位,用合金钢铲、刮刀、手锤、钢丝刷和砂布等除去浮锈、漆皮,打磨至显露金属光泽。
1.5 钢材表面如局部有油脂和污垢,一般可采用局部处理措施;大面积或全部有,则可采用棉纱蘸有机溶剂进行清洗。
1.6表面预处理采用动力工具除锈时,首先试运好砂轮机,看其是否偏转、偏轮,接电源线有无漏电处。
清理掉基面的油污、积垢,然后进行砂轮机除锈。
除锈时要用力均匀。
1.7除锈时,正确握住砂轮机,让砂轮机从基面的某一部位开始,沿这一固定点向固定方向进行磨光除锈。
1.8针对重锈,死角处要选择合适方式,重点进行除锈。
操作时必须戴防护眼镜,避免飞溅的钢丝伤害眼睛。
1.9砂轮机除锈时,在接触锈面时要轻重适中,严禁用力过猛,以免损坏机械或机械脱手伤人。
2、喷砂除锈工艺(特殊情况业主单位要求时)2.1脱脂净化。
金属基体进行表面除锈之前,必须仔细地清理焊渣、飞溅物等附属物,并清洗基体表面可见的油脂及其它污物。
2.2环境要求。
在喷砂过程中,空气相对湿度要小于85%,被处理结构表面的温度至少要高于露点3℃以上。
在不利的气候条件下,要采取有效措施(如遮盖、加热或输入净化干燥的空气等),以满足工作环境的要求。
2.3操作要点a.设备要尽量靠近被处理的工件表面,以减少管路长度和压力损失,避免过多的管道磨损,也便于施工人员相互联系和掌握。
b.喷射管应力求顺直,减少弯折处的集中磨损,要经常调换弯折处的磨损方向,延长管道使用寿命。
c.严格控制工艺参数。
料桶的工作压力在0.5~0.6MPa之间,空气压缩机的出口压力不得低于0.6MPa,喷嘴与工件表面的距离根据试喷结果,一般应控制在80~200mm,喷射角30~75°为宜。
2.4料气比例的调节:在喷砂过程中,控制适当的料气比例是提高工效、保证质量、降低磨料损耗和节省材料的关键。
磨料过少,不能充分利用压缩空气的能量,工效低。
磨料过多,管道被大量砂料占据,每个砂粒分配的动力能量就有限,喷射无力,砂耗高工效低。
因此,必须根据空气压力、喷嘴直径、结构表面锈蚀状态、处理的质量、效率等情况,经常而及时的加以调整,既要避免砂阀开启度过小、空气量大,引起磨料供应太少而影响工效,又要防止砂阀开启过大,空气量过小,引起喷砂无力,灰尘弥漫,影响视线而盲目乱喷、漏喷和复喷。
2.5合理利用喷嘴孔径大小的变化,新喷嘴孔径小,先喷小断面;孔径大时,再喷平面。
2.6喷射完毕后,及时清理工件表面灰尘,检查除锈质量。
3. 涂装施工环境要求3.1控制钢材表面温度与露点温度国家相关标准规定钢材表面的温度必须高于空气露点温度3℃以上,方能进行施工;露点温度可根据空气温度和相对温度从下表查得。
例如,测得空气温度为30℃,空气湿度为70%,从上表可以查出露点温度为23.9℃,则钢材表面的温度应在23.9+3 =26.9℃以上时,才能进行涂装施工。
涂装的适宜温度为0~60℃度,相对湿度=85%,被涂钢构件表面温度应高于露点3度以上。
当相对湿度=85%时,钢板表面湿度接近露点时,容易在底材表面结露,从而影响涂膜与底材的结合。
对于环氧类型的涂料,当低于10度时,其固化反应很慢。
3.2底材处理和涂装应有良好的光线条件,如果自然光线照亮不够,应采用其它补充的照明方式,以便于对底材处理情况和涂膜状况的检查。
3.3所有降水的天气,如下雨、下雾等天气不能进行涂装和底材的处理作业。
3.4应注意风力不得超过五级,否则涂料损失过大,表面粘附杂质增多,影响涂层质量和耐久性。
4..涂料防腐层施工4.1涂装前的准备4.1.1涂装前应检查所用涂料的品种、型号、规格是否符合施工技术条件的规定。
质量不合格或变质的涂料绝不能使用。
4.1.2涂装前应对涂料的基本组成和性能以及施工方法进行了解,根据涂料的施工要求选择和确定适当的涂装工艺。
4.1.3由于涂料中各种成分的比重不同,一般涂料经过储存后,会出现程度不同的沉淀。
因此在涂装前必须将涂料搅拌至完全均匀,如有漆皮和颗粒,则应使用80~120目的筛网过滤后再使用。
4.1.4 双组份的涂料,一定要现配现用,双组份混合后应在两小时内使用完毕,超时的涂料不能涂装使用。
4.2涂料涂装技术要求4.2.1涂装前应检查所用漆的品种、型号、规格是否符合施工技术条件的规定,质量不合格或变质的油漆不能使用。
4.2.2涂装前对油漆的基本组成和性能以及施工方法进行了解,根据油漆的施工要求选择和确定适当的涂装工艺。
4.2.3由于油漆中各种成份的比重不同,因此在涂装前必须将油漆搅拌至完全均匀,如有漆皮和颗粒,则应使用80~120目的筛网过滤后再使用。
4.2.4甲乙两组份的涂料,一定要现配现用,双组份混合后应在两小时内使用完毕,剩余的涂料不能涂装使用。
4.2.5为确保工程质量,钢构件涂装需严格按设计要求办理。
施工时,当天使用的涂料在当天配置,不得随意添加稀释剂;并要求必须等下一层漆干透后,方可涂次一层漆。