50万吨棒材方案
80万吨棒材工程给排水工艺概述
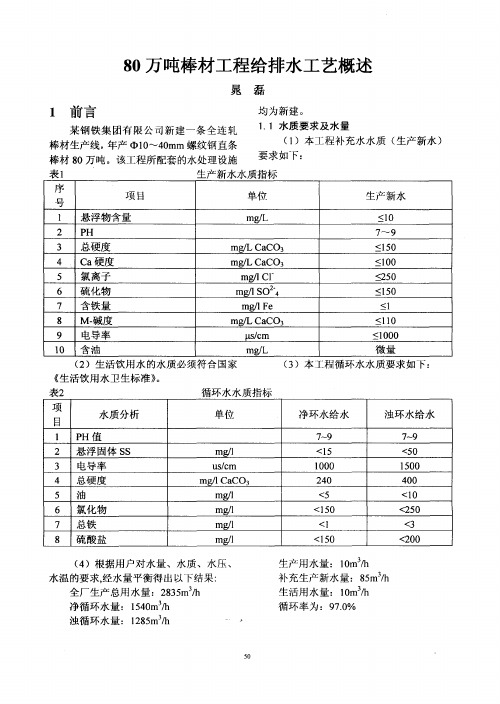
生产新 水 1 0
7 9 ~
3 4 5
6 7 8 9
总硬 度 C 硬 度 a 氯 离子
硫 化物 含铁 量 M. 碱度 电导率
l0 5 10 0 < 5 2O
l0 5 1 l0 1 10 00 微量
1 含 油 0
( )生活 饮用 水 的水质 必须 符合 国家 2 《 活饮 用水 卫生标 准 》 生 。 表2 项
表I
序
要求 如 下 :
生产新 水水质 指标 项目 悬 浮物含 量
PH
号 1
2
单位 mgL , m LC C a O3 mgLC C 3 / a O mgl 1 /C ’
mgl O 4 /S mgl e /F mgLC C 3 / a O  ̄/m s c mgL /
℃ <5 3 <5 3 <5 3 <5 3 常温
常温
制度 净环 水 净环 水 浊环 水 浊环 水 生活 水
生 产新 水
连续 连续 连续 连续 间断
问断
2 2电机 设备 间接 冷却循 环 水系统 . 该 系统 主要 供主 电机 、 压润 滑 、 液 空调 、 液 压站 等冷 却水 用户 。 使用 后 的水 , 质仅 水 有温 升 而未 受其 它污 染 , 可直 接 利用余 压上 冷 却塔 ,冷却 后 的水 同到吸 水井 ,经泵 加压 再 送 同各 用 户 循 环 使用 ,该 系 统 用水 量 为
<5 1 10 00 20 4
< 5
<0 5 l0 50 40 0
<0 1
电 导率
油
4 总硬 度
6 氯化 物
7 总铁 8 硫 酸 盐
mgl /
年产90万吨棒材车间设计设计说明

年产90万吨棒材车间设计设计说明年产90万吨棒材车间设计摘要本设计为年产90万吨棒材车间工艺设计。
品种为圆钢和螺纹钢的小型棒材厂,在此选择Φ16mm的圆钢作为典型产品进行该车间的设计。
本设计采用全连续轧制生产工艺,全线共有轧机18架,其中粗轧机6架,中轧机6架,精轧机6架,终轧最大轧制速度为16m/s。
采用主要工艺流程为选定坯料→加热→除鳞→轧制(粗、中、精轧)→冷却(水冷、风冷)→打捆→检查→入库。
棒材以定尺交货,横列式、半连续式、全连续式各种轧机都可以进行生产。
采用全连续式平立交替布置轧机,以保证产量减少事故。
此设计以设计任务书出发,首先论述了棒材的发展概况和市场需求,建厂的必要性和可能性,然后选择典型产品的产品大纲的制定、轧机的选择、孔型系统的选择及典型产品的孔型设计、力能参数的计算及校核、辅助设备的选取、车间布置等。
关键词:车间设计;孔型设计;棒材ABSTRACTThis is the technology design for producing 900,000 tons of hot rolled bar workshop per year.Round steel with diameter of 16 mm is chosen as typical product of the workshop to be designed. And we carry out national standard during the production.We use continuous rolling technology ,there is 18 mill in common ,6 for roughing mill ,6 for medium mill ,6 for finishing mill .The largest end mill speed is about 16m/s .This paper also analyzed the contemporary rod production in China. A series of problems to be solved are put forward. The design bases on the design paper, which firstly states the development. The necessity and possibility of setting up a plant are also discussed.Then the design is set out in certain procedures, mainly including the making of product outline, choosing mills, choosing pass system, designing of pass in typical products force and energy parameters calculating and checking, auxiliary equipment, choosing workshop arrangement.Keywords: workshop design,pass design,bar目录摘要 (I)ABSTRACT................................................................................................................. I I 目录. (III)引言 (1)第1章文献综述 (2)1.1我国线棒材发展现状 (2)1.1.1 产能高 (2)1.1.2 生产装备参差不齐 (2)1.1.3 管理水平逐年提高 (3)1.1.4 高质量、高附加值的经济线材少 (3)1.2棒材的种类和用途 (3)1.3市场对棒材的质量要求 (4)1.4棒材的生产特点 (4)1.5棒材的生产工艺 (4)1.5.1 坯料 (4)1.5.2 加热和轧制 (5)1.5.3 棒材的冷却和精整 (6)1.6棒材轧制的发展方向 (6)1.6.1 连铸坯热装热送或连铸直接轧制 (6)1.6.2 柔性轧制技术 (6)1.6.3 高精度轧 (7)1.6.4 继续提高轧制速度 (7)1.6.5 低温轧制 (7)1.7棒材生产的目的和意义 (8)第2章建厂依据和产品大纲 (9)2.1建厂依据 (9)2.2厂址的选择 (9)2.2.1建厂地区选择应考虑的要求 (10)2.3产品大纲的确定 (11)2.3.1 产品的标准 (11)2.3.2 产品大纲编制时应注意的问题 (11)2.3.3 产品方案的主要内容 (12)2.4产品质量 (12)2.5产品大纲 (13)2.6坯料选择 (14)2.7坯料选用所考虑因素 (15)2.7.1 坯料形状尺寸 (15)2.7.2 钢坯的重量 (15)2.7.3 坯规格及允许偏差 (15)2.7.4 坯料的检查与清理 (16)第3章轧机选择及工艺流程 (17)3.1轧机型式对比与选择 (17)3.1.1开式机架 (17)3.1.2闭式机架 (17)3.1.3半闭口机架 (17)3.1.4无牌坊轧机 (17)3.1.5悬臂式机架 (18)3.1.6平立可转换轧机 (19)3.2轧机布置选择比较 (21)3.2.1横列式轧机 (21)3.2.2顺列式布置的轧机 (22)3.2.3连续式布置的轧机 (22)3.2.4轧机机架数确定 (23)3.3棒材轧制生产工艺的制定 (24)3.3.1 制定生产工艺的原则 (24)3.3.2 生产工艺流程图 (25)3.3.3 生产工艺特点 (27)3.3.4 轧制方案制定 (27)3.4.1 坯料表面预处理 (27)3.4.2 坯料加热 (28)3.4.3 钢材的轧制 (29)3.4.4 钢材的冷却与精整 (31)3.5轧辊的各个参数 (31)3.5.1轧辊的材质选择 (32)3.5.2轧辊直径 (33)3.5.3辊身长度 (34)3.5.4轧辊轴承 (35)3.5.5轧辊辊颈直径和辊颈长度的确定 (36)3.5.6轧辊的调整机构 (37)3.6轧机主传动 (38)3.6.1 减速机和齿轮机座 (38)3.6.2 电机 (38)3.6.3 连接轴 (39)第4章孔型系统选择与设计 (41)4.1孔型设计理论 (41)4.1.1孔型设计的内容 (41)4.1.2孔型设计的基本原则 (41)4.1.3孔型设计考虑的几点因素: (41)4.2孔型系统的选择 (42)4.2.1棒材的连轧 (42)4.2.2连轧孔型设计原则 (42)4.2.3棒材孔型系统 (43)4.3孔型的设计计算 (45)4.3.1典型产品 (45)4.3.2 轧制各道次面积的确定 (48)4.4成品孔型的设计 (48)4.4.1箱型孔的设计 (50)4.4.2圆孔和椭圆孔的设计 (51)第5章轧制节奏图表与产量计算 (55)5.1咬入角的计算 (55)5.2前滑值的计算 (55)5.2.1摩擦系数f的选择 (55)5.2.2中性角的计算 (55)5.2.3前滑值h S的计算 (55)5.3轧辊转速及电机速度的确定 (56)5.4轧制节奏图表 (56)5.4.1 轧制间隙时间 (56)5.4.2 各道次轧制间隙时间 (57)5.4.3 总间隙时间 (58)5.5轧钢机产量的计算 (59)5.5.1 轧钢机产量概述 (59)5.5.2 车间年产量的计算 (61)5.6提高轧钢机产量的主要途径 (62)第6章力能参数的校核 (63)6.1轧制温度的计算 (63)6.1.1 轧制道次中的温度变化的影响因素 (63)6.1.2 各道次轧制温度的确定 (64)6.2轧制力能计算及电机校核 (66)6.2.1 平均单位压力的计算 (66)6.2.2 总轧制压力模型 (66)6.3轧制力矩的计算 (67)6.4附加摩擦力矩的计算 (68)6.4.1 轧辊轴承中的附加摩擦力矩 (68)6.4.2 传动机构中的摩擦力矩 (68)6.4.3附加摩擦力矩 (68)6.4.4 辐射热所引起的温降计算 (69)6.5空转力矩的计算 (69) (69)6.8电机功率的计算 (70)6.9对辊身计算弯曲强度 (70)6.10对辊颈计算弯曲和扭转强度 (71)6.11对辊头验算扭转强度 (72)第7章辅助设备的选择 (73)7.1选择原则 (73)7.2加热设备 (73)7.2.1入炉设备 (73)7.2.2 出炉设备 (74)7.2.3 炉型的选择 (74)7.2.4 加热炉产量计算 (76)7.2.5 炉子尺寸的计算 (76)7.3导位、活套设备 (78)7.3.1 导卫装置 (78)7.3.2 活套活套的设计 (78)7.4剪切设备的选择 (79)7.4.1 1#飞剪机 (79)7.4.2 2#飞剪机 (81)7.4.3 3#倍尺剪 (82)7.4.4 4#定尺剪 (83)7.5冷床的选择 (85)7.5.1冷床的结构与形式 (85)7.5.2冷床的参数确定 (86)7.6起重设备的选择 (88)7.6.1 起重机 (88)7.6.2 辊道的选用 (90)7.7堆垛机 (91)7.8打捆机 (91)第8章棒材厂工艺平面布置 (92) (92)8.3设备间距的确定 (93)8.3.1 热炉到第一架轧机距离的确定 (93)8.3.2 轧机间距的确定 (94)8.3.3 水冷区域的确定 (94)8.4制动裙板 (95)8.5厂房布置 (95)8.6仓库面积计算 (96)8.6.1原料仓库面积的计算 (96)8.6.2 成品仓库面积的计算 (96)8.7车间其他设施面积的确定 (97)8.7.1 操纵台位置的选择 (97)8.7.2 主电室位置的选择 (97)8.7.3 柱距尺寸 (98)8.7.4 吊车轨面标高 (98)第9章车间技术经济指标 (99)9.1各类材料消耗指标 (99)9.2各类材料消耗指标 (99)9.3金属消耗概述 (100)9.3.2 燃料消耗 (101)9.3.3其余的材料消耗 (102)9.4综合技术经济指标 (102)9.4.1日历作业率 (102)9.4.2成材率 (102)9.5车间劳动组织 (103)9.5.1 劳动定额 (103)9.5.2 车间劳动人员 (103)第10章环境保护及综合利用 (104)10.1轧钢厂的环境保护 (104)10.2节能和综合利用 (105)10.2.1轧钢厂的节能 (105)10.2.2轧钢厂的综合利用 (106)结论 (107)参考文献 (108)致谢 (110)附录 (111)引言钢铁材料以其所具有的特性——较高的强度、韧性、易加工成型性、绿色可循环性在未来很长一段时期内仍将是重要的结构材料。
棒材工程监理规划

棒材工程监理规划精品棒、线材生产线及配套项目工程监理规划总监理工程师:总工程师:2010年06月目录第一章总则1.工程项目概况及特点2.监理工作的要紧依据3.监理工作范畴4.监理工作内容5.本工程项目监理工作目标6.本工程监理质量操纵要点及措施7.项目监理组织机构第二章质量操纵1、质量操纵的任务2、质量操纵的依据3、质量操纵的原则4、质量操纵的方法5、监理质量保证体系6、质量预控措施7、施工过程中的质量操纵8、各要紧工程分部施工时期的质量操纵点和操纵手段9、试运转10、工程竣工验收11、保修期的监理工作第三章进度操纵1、工程进度操纵的方法2、工程进度操纵的措施第四章投资操纵1、投资操纵的任务和目标2、投资操纵风险分析3、投资操纵的方法4、规避风险操纵投资的防范措施5、工程投资操纵的监理工作第五章合同治理1、合同治理的任务2、合同分析的要点3、合同治理的内容4、索赔和反索赔的操纵措施5、减少工期延期的预控措施及治理方法第六章信息治理1、信息治理的任务和监理手段2、信息治理的内容3.信息编目分类4、完工移交建设单位监理档案名目第七章组织和谐1.配合建设单位办理相关手续,同意建设主管部门治理2.现场组织和谐3.现场组织和谐的方法4.监理月报第八章安全生产和文明施工1.安全生产的任务2.安全监理方法3.要紧安全监理防范措施4.文明施工治理的任务一、项目概况及特点1.项目概况精品高速线材生产线、精品棒材生产线及相关配套工程位于厂区东北侧,现有高线和二棒车间西侧,现有二炼钢西北侧。
工程合同项下的工程总价款为人民币X万元(其中建安费X万元)。
1.1 建设内容主厂房、水处理、1.3工程规模:年产量为100万吨棒材和50万吨线材两条生产线1.4建设工期: 本工程合同绝对工期(热负荷试车成功):精品棒材生产线及公辅设施配套项目工程:绝对工期为XXX天;精品线材生产线及配套方坯连铸项目工程:绝对工期为XXX天;1.5工程投资:本1.6工程质量标准:严格按现行冶金行业、国家相关标准进行工程监理,工程质量达到合格标准,争创贵州省优质工程。
棒材生产工艺简述
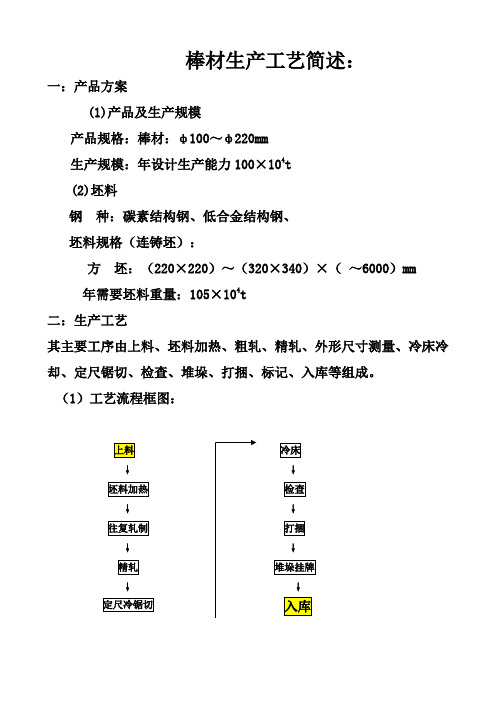
棒材生产工艺简述:一:产品方案(1)产品及生产规模产品规格:棒材:ф100~ф220mm生产规模:年设计生产能力100×104t(2)坯料钢种:碳素结构钢、低合金结构钢、坯料规格(连铸坯):方坯:(220×220)~(320×340)×(~6000)mm年需要坯料重量:105×104t二:生产工艺其主要工序由上料、坯料加热、粗轧、精轧、外形尺寸测量、冷床冷却、定尺锯切、检查、堆垛、打捆、标记、入库等组成。
(1)工艺流程框图:↓↓↓↓↓↓↓(2)工艺流程简介所有轧线设备均布置在+0.00m平台上,轧线标高为+1.40m。
当生产时,合格的连铸钢坯以单根方式从连铸热坯出坯台架送入输送辊道,输送辊道将坯料向前输送。
(坯料在输送辊道运输过程中经设在辊道中的坯料秤称重,自动显示纪录每根坯料的重量。
可不选)在输送辊道上不合格的坯料(人工右眼检查、表面缺陷、弯曲度过大和目测测长不符合要求的坯料),可由设在输送辊道侧面的剔除装置剔出。
合格的坯料输送到+2.00m 平台的辊道上,通过炉前顶钢机送入加热炉。
热送坯料进入加热炉的温度约为≈600°C左右。
当采用冷坯生产时,坯料以4~5根成组方式经输送辊道向前输送,(在输送过程中进行称重,)在辊道的另一侧设有不合格钢坯剔除装置,经人工检查表面缺陷和弯曲度达不到要求的坯料在此剔出。
坯料后经提升机构将坯料提升到+2.00m平台的辊道上,通过入炉辊道送入加热炉加热。
蓄热推钢式加热炉按不同钢种的加热制度,将坯料加热到980~1150°C。
加热好的钢坯在推钢机的推动下从炉前滑道滑出,出炉后的钢坯由输送辊道运送到粗轧机组第一架轧机中。
不合格的钢坯由钢坯剔除装置在此剔出。
钢坯首先进入粗轧机组(ф750x2)中轧制,最后送往一架两辊成品精轧机(ф650)轧制。
粗轧和中轧为往返式轧制。
合格钢坯经机前运输辊道送至第一架开坯ф750轧钢机,经机后升降台抬送与机前翻钢板翻钢,轧制4道次后,由机前移钢机送往ф750二架轧机,轧件经机后升降台抬送与机前翻钢板翻钢,轧制3道次后经二架轧机机后输送辊道,送至ф650二辊式成品精轧机,在经轧机前设有气动翻钢装置,当成品进入合金扭转导槽时,由设在机前的红外线检测仪检测到信号并发出指令,使气缸动作,完成精轧机前的翻钢,使平椭圆转为立椭圆,精轧机经过一道次轧制形成所需成品。
棒材生产线二级过程控制系统的设计和应用
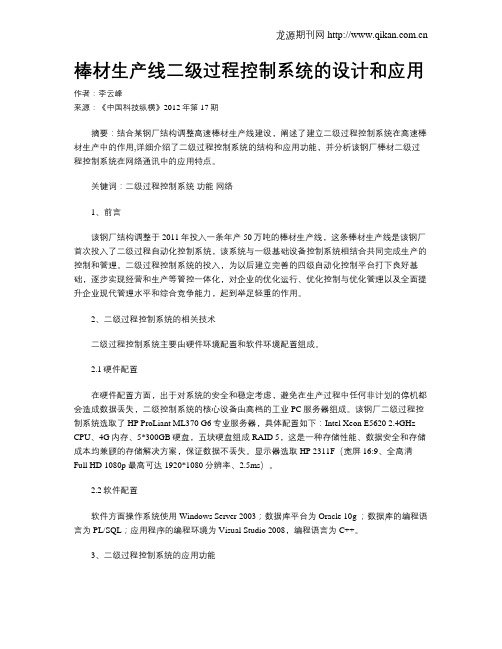
棒材生产线二级过程控制系统的设计和应用作者:李云峰来源:《中国科技纵横》2012年第17期摘要:结合某钢厂结构调整高速棒材生产线建设,阐述了建立二级过程控制系统在高速棒材生产中的作用,详细介绍了二级过程控制系统的结构和应用功能,并分析该钢厂棒材二级过程控制系统在网络通讯中的应用特点。
关键词:二级过程控制系统功能网络1、前言该钢厂结构调整于2011年投入一条年产50万吨的棒材生产线,这条棒材生产线是该钢厂首次投入了二级过程自动化控制系统,该系统与一级基础设备控制系统相结合共同完成生产的控制和管理。
二级过程控制系统的投入,为以后建立完善的四级自动化控制平台打下良好基础,逐步实现经营和生产等管控一体化,对企业的优化运行、优化控制与优化管理以及全面提升企业现代管理水平和综合竞争能力,起到举足轻重的作用。
2、二级过程控制系统的相关技术二级过程控制系统主要由硬件环境配置和软件环境配置组成。
2.1硬件配置在硬件配置方面,出于对系统的安全和稳定考虑,避免在生产过程中任何非计划的停机都会造成数据丢失,二级控制系统的核心设备由高档的工业PC服务器组成。
该钢厂二级过程控制系统选取了HP ProLiant ML370 G6专业服务器,具体配置如下:Intel Xeon E5620 2.4GHz CPU、4G内存、5*300GB硬盘,五块硬盘组成RAID 5,这是一种存储性能、数据安全和存储成本均兼顾的存储解决方案,保证数据不丢失。
显示器选取HP 2311F(宽屏16:9、全高清Full HD 1080p 最高可达1920*1080分辨率、2.5ms)。
2.2软件配置软件方面操作系统使用Windows Server 2003;数据库平台为Oracle 10g ;数据库的编程语言为PL/SQL;应用程序的编程环境为Visual Studio 2008,编程语言为C++。
3、二级过程控制系统的应用功能结合该钢厂棒材生产线的需求和现场的实际情况,棒材生产线的二级过程控制系统具备了生产计划、物料跟踪、设定值下发、轧制参数查询、报表等功能,同时实现了轧机状态监控、HMD和CMD信号监控、飞剪的剪切长度和状态信号等有效数据的记录和处理。
新版50吨电炉炼钢产能(60立方小型炼铁高炉)

50万吨电炉炼钢、连铸连轧生产线建设草案目录1 总论1.1项目提出1.2建设规模1.3产品初步方案2 炼钢2.1工艺及设备选择2.2生产方法2.3炼钢工艺流程2.3.1流程2.3.2工艺流程简述2.4炼钢主体设备及主要参数2.4.1电弧炉2.4.2钢包精炼炉2.4.3连铸系统2.5炼钢、精炼及连铸各项主要指标2.5.1电炉指标2.5.2 LF炉指标2.5.3 连铸机指标2.6主要原材料2.6.1废钢、生铁2.6.2其它材料2.6.3电极3 棒材轧钢生产线3.1工艺及设备选择3.2生产方法选择3.3工艺流程3.4工艺流程简述3.5棒材轧机主设备及参数3.6棒材规格品种4 小型型钢轧钢生产线4.1工艺及设备选择4.2工艺流程4.3工艺流程简述4.4型材轧机设备及参数4.5型材轧制规格品种5 动力能源5.1热力5.2供电6 环境保护7 设备费用(预估)8 其它1.总论1.1 项目提出炼钢能力55万吨,配公司现有螺纹钢连轧生产线及另外一条小型型钢生产线,共计50万吨轧钢能力,形成完整的钢铁生产线,以适应市场需求。
1.2 建设规模按公司现有的螺纹钢连轧生产线为基础,并另配一条小型型钢生产线,上游配套相应的炼钢连铸生产线,建成炼钢厂、轧钢厂,形成一条完整的生产链。
炼钢厂主要装备50吨交流偏心底出钢(50tAC/EBT)电弧炉2座,50吨钢包精炼炉一座,三机三流多功能方圆坯连铸机一台(R8m或R9m)。
在目前条件下以全废钢为原料,形成短流程炼钢生产线,年产钢水55万吨、连铸坯53万吨(150~220方坯或Φ150~220圆坯)。
轧钢厂分两部分,其一以我公司现有棒材连轧生产线为基本模式,由20架全水平式机组组成棒材连轧生产线,除生产螺纹钢外,考虑生产圆钢管坯钢等产品,年生产能力30万吨;同时另建一条半连轧小型型钢生产线,年生产能力每年20万吨。
1.3 产品初步方案棒材产品方案为大、小规格比较齐全的Ⅱ级Ⅲ级螺纹钢,低合金结构钢种圆钢及碳素管坯圆钢。
年产量100万吨棒材车间设计

(5)轧机结构形式先进合理,制造容易,操作简单,维修方便。
(6) 备品备件更换容易,并利于实现备品备件的标准化。
(7)有良好的综合技术经济指标。
而对于钢板轧机、钢管轧机、小型及线材轧机,除了要求一定的强度外,还要求有足够的刚度,以保证这些轧制产品的几何形状的正确和尺寸的精度,因此选择轧钢机时除遵循上述原则之外,要从工艺要求出发,根据不同产品的生产特点和具体要求来确定轧机的结构形式,主要的技术参数和它们的布置方式。
1.3.1
1#切头飞剪(一台)
位于粗轧与中轧之间
其主要参数有:
形式:开口曲柄式,带夹送辊装置;
剪切最大截面积:3500㎡;
剪切温度:900℃;
轧件抗拉强度:110MP~120MP;
轧件运行速度:0.5m/s~2.5m/s
剪切头尾公差:±20mm
碎断长度:600mm
夹送辊装置为焊接钢结构,并带有悬臂辊,辊子直径为330mm,宽度为100mm,由马达通过齿轮传动下辊,上辊为气动压下。
金属收得率可提高6-12%; 2、 每吨钢大约节约热能14万大卡;
1.1.2 炉型选择
炉型的选择取决于坯料的断面大小,钢材品种和加热质量等要求。线棒材轧机加热炉大都采用步进梁式加热炉。梁底组合式步进加热炉比推钢式加热炉有较多的优点,也优于步进底式加热炉,它能使钢坯的加热温度均匀,没有或很少有水管墨印,坯料不与滑轨摩擦,不会划伤坯料,加热质量好。
小结:
炉宽: B=10.6m
有效炉长:L=18m
有效炉底面积:S=190.8㎡
炉底过钢面积:S`=180㎡
四、其它参数
空气预热温度:450℃-550℃
攀钢110万吨棒线材生产线建设与发展

攀钢110万吨棒线材生产线建设与发展宋建国;陈文灶【摘要】攀钢抓住市场机遇,在攀枝花本部搬迁建设一条110万吨的棒线材生产线,本文对该生产线的工艺布局、主要装备特点、产品定位及后期发展等进行了介绍.【期刊名称】《四川冶金》【年(卷),期】2018(040)005【总页数】3页(P38-40)【关键词】棒材;高线;生产工艺;技术改造【作者】宋建国;陈文灶【作者单位】攀钢集团攀枝花金属制品有限公司,四川攀枝花617023;攀钢集团攀枝花金属制品有限公司,四川攀枝花617023【正文语种】中文【中图分类】TG33根据攀钢产线结构调整需求,攀钢集团利旧搬迁攀成钢闲置设备,在攀枝化本部建设一条年产50万吨高速线材生产线和60万吨的棒材生产线。
棒材于2017年3月1日热负荷试车,高线于2017年5月9 日热负荷试车。
在一年的时间内,完成项目的搬迁建设与达产达效,实现当年投资、当年建成、当年赢利的任务,成为攀钢新的利润增长点。
截止2017年12月底,全年累计生产建筑用钢40.8万吨,棒材实现了Φ14~40mm规格、高线实现了Φ6.5~12 mm规格的螺纹钢、圆钢生产。
现今,高速线材生产线正致力于高端金属制品用线材的开发,逐步打造西南地区最具竞争力的建材生产基地和金属制品材生产基地。
1 平面布置根据地理位置条件,为有效节约占地和工程投资,尽可能利旧闲置设备及设施,高速线材与棒材车间平行相邻布置,依次布置线材主轧跨(231.0 m×24.0 m+135.0 m×21.0 m)、棒材主轧跨(428.5 m×24.5 m)、原料跨(440.5 m×33.0 m)、成品跨(256.5 m×18.5 m,预留184.0 m×18.5 m)。
车间最大长度440.5 m,最大宽度100 m,线材主轧线设备布置在+5.0 m平台上。
工艺平面布置示意图如图1所示。
2 主要装备2.1 棒材生产线主要由1台蓄热推钢式加热炉、18架轧机、3台飞剪、1台冷剪机、1台步进齿式冷床、检查收集设备等组成。
- 1、下载文档前请自行甄别文档内容的完整性,平台不提供额外的编辑、内容补充、找答案等附加服务。
- 2、"仅部分预览"的文档,不可在线预览部分如存在完整性等问题,可反馈申请退款(可完整预览的文档不适用该条件!)。
- 3、如文档侵犯您的权益,请联系客服反馈,我们会尽快为您处理(人工客服工作时间:9:00-18:30)。
50万吨全连轧棒材工程
设计方案
2017.10.18
1. 概述
1.1设计依据
本方案是根据甲方的基本要求设计的。
甲方技术要求细化后方案将做进一步调整和完善。
1.2主要设计决定
(1)车间设计生产能力为50万t/年。
(2)主要产品为螺纹钢筋和圆钢棒材,其中螺纹钢筋生产规格为Φ10~Φ28mm,圆钢生产规格为Φ16~Φ60.0mm,钢种为普碳钢、优质钢和低合金钢\铝及铝合金1xxx~7xxx系列等。
(3)采用150×150×9000mm连铸坯作为原料。
(4)精轧机采用短应力线高刚度轧机,轧制速度18m/s。
(5)棒材生产线生产工艺分为原料准备、加热、轧制、控制冷却及成品精整等工序,整个轧制工艺采用连续化自动控制。
1.3 主要设计特点及装备水平
(1)坯料全部为连铸坯,一火成材。
(2)全线轧机采用平立交替布置,实现了连续无扭轧制,避免了轧件在轧制过程中的扭转,可有效地减少成品轧件的表面缺陷。
(3)轧线采用微张力和无张力活套轧制,保证产品尺寸精度。
(4)采用控制冷却工艺,可节约能源,改善产品的金相组织,提高产品质量。
(5)采用切分轧制工艺,平衡小规格产品产量。
(6)孔型系统设计采用椭圆-圆孔型系统,轧机导卫系统采用了滚动导卫,可确保轧件的稳定轧制,并可减少轧件的划伤。
(7)轧机主传动采用直流传动系统,技术成熟,运行稳定。
(8)车间采用基础自动化及过程控制两级自动化控制系统。
轧机主要性能参数见表2-5。
各组轧机选型:
(1)粗中轧机组
粗中轧机选用二辊闭口式轧机。
机列设备组成主要包括:轧机工作机座、轧机底座、压下装置、横移装置(立式轧机为提升装置)、传动接轴、接轴托架、联合减速箱、主电机、联轴器、电机底座等。
轧机主要结构为:机架采用钢板焊接式牌坊;上辊采用液压马达快速压下、手动微调弹性阻尼体平衡;轧辊轴承采用四列圆柱轴承及四点角接触轴承;由螺杆机构进行轧辊轴向调整和固定;液压小车换辊及更换轧槽;机架固定型式为液压锁紧;采用大伸缩量十字万向接轴;平辊轧机接轴托架为气动调节;轧机主传动为联合减速机型式。
立式轧机为上传动。
(2)精轧机组
精轧机选用高刚度短应力线轧机。
机列设备组成主要包括:轧机工作机座、轧机底座、横移装置(立式轧机为提升装置)、轧机锁紧装置、传动接轴、接轴托架、联合减速箱、主电机、联轴器、电机底座等。
轧机工作机座结构特点:短应力线轧机,刚度高,精度好,承载能力大,调整换辊方便,设备结构紧凑,设备重量轻。
轧机主要结构为:轧辊轴承采用四列短圆柱轴承及推力轴承;轧辊平衡采用液压缸;轴向调整采用螺旋丝杠,轴向游隙小;轧辊压下调整采用低速液压马达驱动一手动复合调整方式;轧辊开口度对称调整,轧机调整时轧制中心线始终不变;整机换辊,当轧机移出轧线后,采用专用换辊车。
立式轧机为上传动。
轧机横移装置采用液压缸进行轧机工作机座的横移更换孔槽及换辊。
当需要进行换辊操作时,先将轧机横移至传动侧极限位置,将接轴托架与轧机脱开,然后再将轧机横移至操作侧极限位置,用天车将整架轧机工作机座吊走。
轧机工作机座锁紧采用弹簧锁紧、液压回松方式。
平立转换轧机平立转换机构的结构特点:采用液压缸驱动方式,轧机由水平位置和垂直位置分别进行转换时,由两个液压缸驱动轧机的转换机构,以保证轧机进行位置的转换,位置由接近开关控制。
轧机其它部分主要结构型式同平辊精轧机列。
2.6 主要辅助设备
(1)炉区设备
包括上料台架、入炉辊道、推入机、推钢机、加热炉、出钢机、拉出机、出炉辊道等。
上料台架为液压推钢式,规格8×6.5m,可预留;推钢机为液压推钢式,推力185t;推入机、出钢机和拉出机均为电动,入炉辊道和出炉辊道均为交流电机单独传动。
(2)轧区辅助设备
包括卡断剪、1#飞剪、2#飞剪、立式活套、精轧后辊道、3#飞剪等。
卡断剪为气动,附在1#轧机牌坊上;1#飞剪为曲柄式,直流电机传动;2#飞剪为回转式,直流电机传动;3#飞剪为曲柄-回转组合式,直流电机传动;精轧后辊道为交流变频电机单独传动。
(3)冷床区设备
包括冷床上料辊道、制动裙板、冷床、齐头辊、冷床下料辊道、冷床下料装置等。
冷床上料辊道规格为Φ190×200mm,长度186m,交流变频电机单独传动;制动裙板为液压升降;冷床规格为96×10m,两台直流电机传动;齐头辊道为交流变频电机单独传动;冷床下料装置为电动升降,液压行走;冷床下料辊道规格为Φ230×1000mm,长度100m,交流电机单独传动。
(4)精整区设备
包括定尺冷剪、剪后辊道、定尺挡板、横移台架、打捆收集辊道、人工打捆装置、称重装置、成品收集装置、短尺剔除装置等。
其中定尺冷剪为固定式剪,剪切力650t,交流电机驱动;定尺挡板为气动推拉挡板,共3套,分别用于剪切6m、9m、12m定尺;剪后辊道规格为Φ230×1000mm,长度28m,为交流电机单独传动;横移台架为三段链,交流电机传动,上钢装置为电动,集料钩为液压驱动;打捆收集辊道规格为Φ230×500mm,长度66m,交流电机单独传动,带有气动抱紧装置;人工打捆装置为人工气动打捆;成品收集装置为U型收集槽;短尺剔除装置为磁力拉钢机。
(5)液压润滑设备
液压设备包括炉区液压站、轧区液压站、冷床液压站和精整液压站;
润滑设备包括粗中轧稀油润滑站、精轧稀油润滑站、冷床干油润滑站(两套)、油气润滑站等。
2.7 车间平面布置
车间主厂房由原料跨、主轧跨及成品跨组成;辅助间由主电室、轧辊机修间及水处理设施等组成。
主电室、轧辊机修间与主轧跨靠近布置。
2.8 车间主要技术经济指标
车间主要技术经济指标见表2-6。