SAE J1455-1994 汽车电器试验标准
SAEJ(标准参考)翻译

SAEJ(标准参考)翻译1 范围该SAE标准涵盖了应⽤于汽车球墨铸铁铸件和相关的⾏业的铸铁试件的⾦相组织和最低机械性能要求。
铸件需详细说明是铸态或热处理状态。
如果铸件需热处理,需获得客户的批准。
本附录提供了在化学成分,显微组织和⼒学性能,铸造性能等⽅⾯⾯信息以及为特定条件服务的其他信息。
在此标准的SI单位是磅2.2参考⽂献2.1 相关出版物The following publications form a part of the specification to the extent specified herein. Unless otherwise indicated, the latest revision of SAE publications shall apply2.1.1 ASTM 国际出版物Available from ASTM INTERNA TIONAL, 100 Barr Harbor Drive, West Conshohocken, PA 19428-2959ASTM E10 –-Standard Test Method for Brinell Hardness of Metallic MaterialsASTM E23—Standard Test Methods for Notched Bar Impact Testing of Metallic Materials ASTM E111—Standard Test Method for Young's Modulus, Tangent Modulus and Chord Modulus ASTM A247—Standard Test Method for Evaluation the Microstructure of Graphite in Iron CastingsASTM A536—Standard Specification for Ductile Iron CastingsSTP-455—Gray, Ductile, and Malleable Iron Castings Current Capabilities (out-of-print)2.1.2其他出版物Metals Handbook, V ol. 1, 2, and 5, 8th Edition, American Society for Metals, Metals Park, OH Gray and Ductile Iron Castings Handbook, Gray and Ductile Iron Founder Society, Cleveland, OH H. D. Angus, Physical Engineering Properties of Cast Iron, British Cast Iron Research Association, Birmingham, England3.3 牌号机械性能和冶⾦描述如表1所⽰。
汽车电器盒标准内容

汽车用电器盒企业标准1、范围本规范规定了汽车用电器盒的技术要求、试验方法、检验规则及标志、包装、运输、储存。
本规范适用于xxx公司各种车型。
2、规范性引用文件下列文件中的条款通过本标准的引用而成为本标准的条款。
凡是注日期的引用文件,其随后所有的修改单(不包括勘误的内容)或修订版均不适用于本标准,然而,鼓励根据本标准达成协议的各方研究是否可使用这些文件的最新版本。
凡是不注日期的引用文件,其最新版本适用于本标准。
GB 2423.1-1989 电工电子产品基本环境试验规程试验A:低温试验方法GB2423.2-1989 电工电子产品基本环境试验规程试验B:高温试验方法GB2423.10-1995 电工电子产品基本环境试验规程试验FC:振动(正弦)试验方法GB2423.22-1987 电工电子产品基本环境试验规程试验N:温度变化试验方法QC/T 413-1999 《汽车电气设备基本技术条件》QC/T 420-1999 《汽车用熔断器》QC/T 417.1~417.5-2001《车用电线束插接件》3、术语3.1 连接插头:用来与外部电路进行电连接的电器的导电部分。
3.2 连接插座:用于与继电器插头或保险片连接的具有一定卡紧力的插座。
3.3 插接力:将继电器端子或标准插片插入接线盒所需的力。
3.4 拔出力:将继电器插头或标准插片从接线盒中拔出所需的力。
3.5 桥接片在测量电压降时,连接继电器或保险丝拆下后需要导通部位具有不同形状的一种接线片3.6 连续定额:连续定额是制造厂对产品所规定的可以长期运行的负载和条件。
4、技术要求4.1 接线盒应符合本标准的规定,并按照经规定程序批准的图样及设计文件制造。
接线盒为连续定额。
规定采用的熔断器应符合QC/T 420-1999《汽车用熔断器》的规定,插接件应符合QC/T 417.1~417.5-2001《车用电线束插接器》的规定4.2 接线盒的外形及安装尺寸应符合产品图样的规定。
汽车零部件环境可靠性试验项目及标准解析
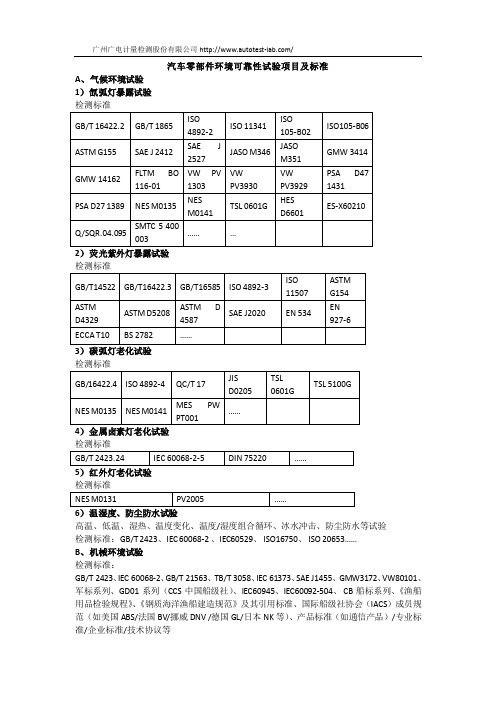
ISO 3231:1993 ASTM G 87-02 ISO 6957:1988 GB/T 2423.51-2000
EIA-364-65A IEC 60068-2-60:1995 l 霉菌试验 可执行标准
GB/T 2423.16-2008 GJB 150.10A-2009 GB 11606.12-89 GB12085.11-89
广州广电计量检测股份有限公司通过卓越的质量保证服务,协助通用、福特、大众、法 雷奥等知名整车企业和零部件企业质量技术不断进步。
广州广电计量检测股份有限公司(GRGT)定位行业高端,引领行业先锋,历经近 50 年 的发展,目前成为一家技术精湛、服务精心、管理精细的一流的计量检测专业机构。 GRGT 是原国家信息产业部军工电子 602 计量测试站,通过国家实验室(CNAS)、国防实验 室(DILAC)和总装实验室认可,并通过中国计量认证(CMA),是中国 CB 实验室,建立企 业计量最高标准 80 多项,通过 CNAS、DILAC 认可项目 591 项。
C、化学环境试验 l 中性盐雾腐蚀试验(NSS) 可执行标准
GB/T 10125-1997 GB/T 2423.17-2008 GB/T 1771-2007 ISO 9227:2006
ASTM B 117-07 JIS Z 2371:2000 l 醋酸盐雾腐蚀试验(ASS) 可执行标准
GB/T 10125-1997 ISO 9227:2006 JIS Z 2371:2000 l 铜加速醋酸盐雾腐蚀试验(CASS) 可执行标准
检测项目: * 正弦振动(定频/扫频/共振搜索/共振保持) * 随机振动(窄带/宽带/正弦+随机/随机+随机) * 三综合振动(温度+湿度+振动) * 加速度冲击和碰撞 * 跌落冲击(垂直跌落/滚筒跌落) * 钢球冲击(球径和球重及高度的能量冲击) * 包装力学试验(振动、跌落、冲击、堆码、搬运夹持堆码) * 能源试验(瞬态波动/稳态波动/能源异常/能源故障) * 倾斜与摇摆(定方位、定角度、定周期) * 可以根据客户要求或者特种条件进行测试(如动态疲劳测试/瞬态测试)
汽车电子可靠性测试及相关标准

二、电子设备可靠性测试标准1、ISO国际标准化组织中,ISO/TC22/SC3?负责汽车电气和电子技术领域的标准化工作。
汽车电子产品的应用环境包括电磁环境、电气环境、气候环境、机械环境、化学环境等。
目前ISO?制订的汽车电子标准环境条件和试验标准主要包含如下方面:ISO16750-1:道路车辆-电子电气产品的环境条件和试验:总则ISO16750-2:道路车辆-电子电气产品的环境条件和试验:供电环境ISO16750-3:道路车辆-电子电气产品的环境条件和试验:机械环境ISO16750-4:道路车辆-电子电气产品的环境条件和试验:气候环境ISO16750-5:道路车辆-电子电气产品的环境条件和试验:化学环境ISO20653?汽车电子设备防护外物、水、接触的等级ISO21848?道路车辆-供电电压42V?的电气和电子装备电源环境国内目前汽车电子产品的环境试验标准主要还是按照产品的技术条件来规定。
全国汽车标准化技术委员会(SAC/TC114)正在参照ISO?标准制订相应的国家和行业标准。
ISO?的标准在欧美车系的车厂中得到了广泛采用,而日系车厂的要求相对ISO?标准来说偏离较大。
为了确保达到标准的限值,各汽车车厂的内控的环境条件标准一般比ISO?的要求要苛刻。
2、AEC?系列标准上个世纪九十年代,克莱斯勒、福特和通用汽车为建立一套通用的零件资质及质量系统标准而设立了汽车电子委员会(AEC),AEC?建立了质量控制的标准。
AEC-Q-100?芯片应力测试的认证规范是AEC?的第一个标准。
AEC-Q-100?于1994?年首次发表,由于符合AEC?规范的零部件均可被上述三家车厂同时采用,促进了零部件制造商交换其产品特性数据的意愿,并推动了汽车零件通用性的实施,使得AEC?标准逐渐成为汽车电子零部件的通用测试规范。
经过10?多年的发展,AEC-Q-100?已经成为汽车电子系统的通用标准。
在AEC-Q-100?之后又陆续制定了针对离散组件的AEC-Q-101?和针对被动组件的AEC-Q-200?等规范,以及AEC-Q001/Q002/Q003/Q004?等指导性原则。
电子电气设备外壳防护体系解读IP等级外壳防护解析

一、概述对于户外用的便携式电子电气设备、汽车电子设备、通讯设备等均有外壳防护测试要求,针对某些使用环境条件还可能会有特殊要求,如风沙大,热带潮湿,海岸边多盐雾,多雨淋、喷雾等比较严酷的使用环境条件。
电子电气零部件的外壳必须具备相应的防护能力,主要包括防接触、防水、防爆、防机械碰撞等防护要求,以确保元器件使用的安全性和可靠性。
下面就目前比较流行的外壳防护体系做全面的总结和梳理,介绍各防护体系的标准要求和测试方法,并分析其异同点。
二、IP防护体系IP防护体系来源于国际电工委员会(IEC),也就是国际上和国内普遍采用的IP代码,该代码体系以EN/IEC 60529-2001 Degrees of protection provided by enclosures(IP code)标准为基础,我国标准GB 4208就等同采用了该标准。
IP防护体系中,对外壳提出了防接触和防水的防护要求,一般有两位数字组成,例如IP56,第一位特征数字表示防接触的等级,第二位特征数字则表示防水的等级。
除了IEC 60529/GB 4208标准之外,标准DIN 40050、ISO 20653等标准也采用了IP防护体系,并针对具体应用补充了三个防水等级,分别是IPX4K、IPX6K和IPX9K,防接触等级则完全一致。
IP防护体系中,各防护等级具体防护含义和相应的测试方法见表1[1]和表2[2].表1 IP防护体系-第一位特征数字参考文献:[1] GB 4208-2008/IEC 60529-2001外壳防护等级(IP代码)[2] ISO 20653-2006 Road vehicles – Degrees of protection (IP-Code) – Protection of electrical equipment against foreign objects. Water and access[3] GB/T 20138-2006/IEC 62262;2002电器设备外壳对外界机械碰撞的防护等级< IK代码>[4] NEMA Standards Publication 250-2003 Enclosures for Electrical Equipment(1000 Volts Maximum)[5] JIS D0203-1994 Method of moisture, rain and spray test for automobile[6] JIS D0207-1977 General rules of dust test for automobile parts。
sae 标准
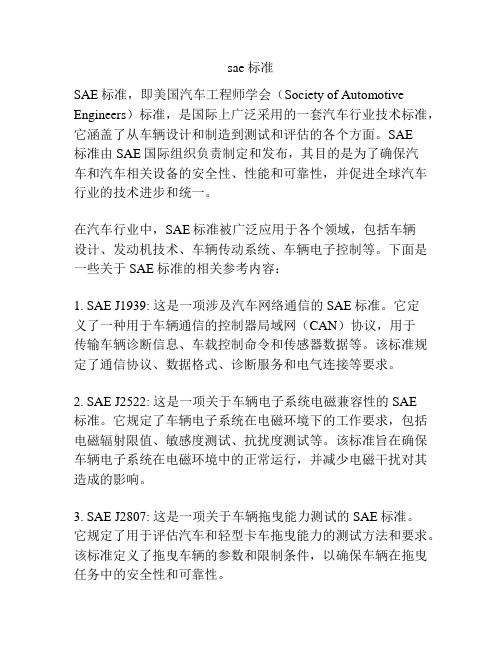
sae 标准SAE标准,即美国汽车工程师学会(Society of Automotive Engineers)标准,是国际上广泛采用的一套汽车行业技术标准,它涵盖了从车辆设计和制造到测试和评估的各个方面。
SAE标准由SAE国际组织负责制定和发布,其目的是为了确保汽车和汽车相关设备的安全性、性能和可靠性,并促进全球汽车行业的技术进步和统一。
在汽车行业中,SAE标准被广泛应用于各个领域,包括车辆设计、发动机技术、车辆传动系统、车辆电子控制等。
下面是一些关于SAE标准的相关参考内容:1. SAE J1939: 这是一项涉及汽车网络通信的SAE标准。
它定义了一种用于车辆通信的控制器局域网(CAN)协议,用于传输车辆诊断信息、车载控制命令和传感器数据等。
该标准规定了通信协议、数据格式、诊断服务和电气连接等要求。
2. SAE J2522: 这是一项关于车辆电子系统电磁兼容性的SAE标准。
它规定了车辆电子系统在电磁环境下的工作要求,包括电磁辐射限值、敏感度测试、抗扰度测试等。
该标准旨在确保车辆电子系统在电磁环境中的正常运行,并减少电磁干扰对其造成的影响。
3. SAE J2807: 这是一项关于车辆拖曳能力测试的SAE标准。
它规定了用于评估汽车和轻型卡车拖曳能力的测试方法和要求。
该标准定义了拖曳车辆的参数和限制条件,以确保车辆在拖曳任务中的安全性和可靠性。
4. SAE J826: 这是一项关于汽车人体工程学设计的SAE标准。
它规定了在设计车辆驾驶舱和座椅时应考虑的人体工程学要求,包括驾驶员身体尺寸、姿势和动作等方面。
该标准旨在提高驾驶员的舒适性、安全性和操作便捷性。
5. SAE J3061: 这是一项关于车辆网络安全的SAE标准。
它提供了一种用于评估和管理汽车网络安全风险的方法,包括威胁建模、安全需求分析和安全验证等。
该标准旨在确保车辆网络系统的安全性和防护能力,防止恶意攻击和非法访问。
总之,SAE标准在汽车行业中具有重要的地位和作用。
汽车继电器标准内容
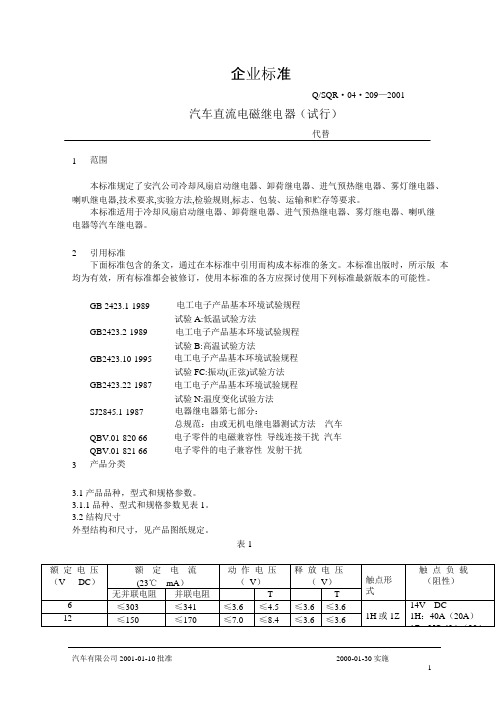
1企业标准Q/SQR·04·209—2001汽车直流电磁继电器(试行)代替范围本标准规定了安汽公司冷却风扇启动继电器、卸荷继电器、进气预热继电器、雾灯继电器、喇叭继电器,技术要求,实验方法,检验规则,标志、包装、运输和贮存等要求。
本标准适用于冷却风扇启动继电器、卸荷继电器、进气预热继电器、雾灯继电器、喇叭继电器等汽车继电器。
2 引用标准下面标准包含的条文,通过在本标准中引用而构成本标准的条文。
本标准出版时,所示版本均为有效,所有标准都会被修订,使用本标准的各方应探讨使用下列标准最新版本的可能性。
GB2423.1-1989GB2423.2-1989 GB2423.10-1995 GB2423.22-1987 SJ2845.1-1987QBV.01-82066 QBV.01-82166电工电子产品基本环境试验规程试验A:低温试验方法电工电子产品基本环境试验规程试验B:高温试验方法电工电子产品基本环境试验规程试验FC:振动(正弦)试验方法电工电子产品基本环境试验规程试验N:温度变化试验方法电器继电器第七部分:总规范:由或无机电继电器测试方法汽车电子零件的电磁兼容性导线连接干扰汽车电子零件的电子兼容性发射干扰3产品分类3.1 产品品种,型式和规格参数。
3.1.1 品种、型式和规格参数见表1。
3.2 结构尺寸外型结构和尺寸,见产品图纸规定。
表124≤80.8≤91≤14.2≤16.0≤3.6≤3.6)NC.30A(20A)4 技术要求4 技术要求4.1 环境条件4.1.1 温度贮存(无载):按5.2 条规定进行试验。
试验后,继电器的动作电压和释放电压应符合4.2.2条规定,接触压降应符合4.2.3条规定。
4.1.2 温度贮存(带载):按5.3 条规定进行试验。
试验后,继电器的动作电压和释放电压应符合4.2.2条规定,接触压降应符合4.2.3条规定。
4.1.3 温度变化:按5.4条规定进行试验。
汽车零部件可靠性常用测试标准

8、防尘测试、防水测试
防尘防水测试主要考察零部件在防尘防水的功能以及进水进尘后对零部件功能的影响 情况。
参考的测试标准: 测试标准: GB/T 4208-2008
DIN 40050.9-1993 IEC 60529-2001
ISO 20653-2006 SMTC 3 800 001-9.3.11 28401NDS01
6. 温度冲击目的:
温度循环/冲击试验是评估产品在高底温和温度交变的效应。效应:膨胀、减弱结构强度、 化学腐蚀电解所用、增加绝缘体导电作用、可动零件变形、表面涂料鬼裂等。
参考的测试标准: BMW GS95003-4,GMW3172 5.5.5, GMW3431 4.4.2, GM9123P 10.2.1, VW801015.2.2, Etl_82517 8.2.8 , FORD Ds00005 10.9.4 , FORD_WDS00.00EA_D114.5.6/4.5.7 , MGRES6221001 9.3.6, SES E 001-04 6.7, PSAB21 7090 6.6.3, IEC60068-2-14(air to air), MIL-STD-883E 1011.9,MIL-STD-202G/107G,MIL-STD-810F 503.4,GB2324.22,GJB150.5 0)
FORD_WDS 00.00EA_D114.5.1/4.5.2/4.5.3/4.5.4/4.5.5/4.5.8/4.8.1/4.8.4, MGRES6221001 9.3,MGRES6221001 11, SES E 001-04 6.1/6.2/6.3/6.4/6.5/6.8/6.9/6.11, IEC60068-2-30 , SAEJ1455 , JESD22-A103C , JESD22-A100B , EIA-364 , GB2324.1/2/3/4/9/34/4, GJB 150.3/4/9,MIL-STD-810F507.4,MIL-STD-202G 103B/106G,MIL-STD-1004.1
- 1、下载文档前请自行甄别文档内容的完整性,平台不提供额外的编辑、内容补充、找答案等附加服务。
- 2、"仅部分预览"的文档,不可在线预览部分如存在完整性等问题,可反馈申请退款(可完整预览的文档不适用该条件!)。
- 3、如文档侵犯您的权益,请联系客服反馈,我们会尽快为您处理(人工客服工作时间:9:00-18:30)。
SAE Technical Standards Board Rules provide that: “This report is published by SAE to advance the state of technical and engineering sciences. The use of this report is entirely voluntary, and its applicability and suitability for any particular use, including any patent infringement arising therefrom, is the sole responsibility of the user.”SAE reviews each technical report at least every five years at which time it may be reaffirmed, revised, or cancelled. SAE invites your written comments and suggestions.QUESTIONS REGARDING THIS DOCUMENT: (412) 772-8512 FAX: (412) 776-0243TO PLACE A DOCUMENT ORDER; (412) 776-4970 FAX: (412) 776-0790SAE WEB ADDRESS 2.1.4R ELATED P UBLICATIONS—The following publications are provided for information purposes only and are not arequired part of this document.TAPPI T801-83TAPPI T802-813.Application3.1Environmental Data and Test Method Validity—The information included in the following sections is basedupon test results achieved by major North American truck manufacturers and component equipment suppliers.Operating extremes were measured at test installations normally used by manufacturers to simulate environmental extremes for vehicles and original equipment components. They are offered as a design starting point. Generally, they cannot be used directly as a set of operating specifications because some environmental conditions may change significantly with relatively minor physical location changes. This is particularly true of vibration, engine compartment temperature, and electromagnetic compatibility. Actual measurements should be made as early as practicable to verify these preliminary design baselines.The proposed test methods are currently being used for laboratory simulation or are considered to be a realistic approach to environmental design validation. They are not intended to replace actual operational tests under adverse conditions. The recommended methods describe standard cycles for each type of test. The designer must specify the number of cycles over which the vehicle electronic components should be tested.The number of cycles will vary depending upon equipment, location, and function. While the standard test cycle is representative of an actual short term environmental cycle, no attempt is made to equate this cycle to an acceleration factor for reliability or durability. These considerations are beyond the scope of this document.3.2Organization of Test Methods and Environmental Extremes Information3.2.1The data presented in this document are contained in Sections 4 and 5. Section 4, Environmental Factorsand Test Methods, describes the thirteen characteristics of the expected environment that have an impact on the performance and reliability of truck and bus electronic systems. These descriptions are titled:a.Temperatureb.Humidityc.Salt Spray Atmosphered.Immersion and Splash (Water, Chemicals, and Oils)e.Steam Cleaning and Pressure Washingf.Fungusg.Dust, Sand, and Gravel Bombardmenth.Altitudei.Mechanical Vibrationj.Mechanical Shockk.General Heavy-Duty Truck Electrical Environmentl.Steady State Electrical Characteristicsm.Transient, Noise, and Electrostatic Characteristicsn.Electromagnetic Compatibility/Electromagnetic InterferenceThey are organized to cover three facets of each factor:1.Definition of the factor2.Description of its effect on control, performance, and long-term reliability3. A review of proposed test methods for simulating environmental stress3.2.2I N S ECTION 5a.Underhood1.Engine (Lower Portion)2.Engine (Upper Portion)3.Bulkheadb.Interior (cab)1.Floor2.Instrument Panel3.Head Liner4.Inside Doorsc.Interior (aft of cab)1.Bunk Area2.Storage Compartmentd.Chassis1.Forward2.Reare.Exterior of Cab1.Under Floor2.Rear3.Top4.Doors3.3Combined Environments—The vehicle environment consists of many natural and induced factors.Combinations of these factors are present simultaneously. In some cases, the effect of a combination of these factors is more serious than the effect of exposing samples to each environmental factor in series. For example, the suggested test method for humidity includes high- and low-temperature exposure. This combined environmental test is important to vehicle electronic components when proper operation is dependent on seal integrity. Temperature and vibration is a second combined environmental test method that can be significant to components. During design analysis a careful study should be made to determine the possibility of design susceptibility to a combination of environmental factors that could occur at the planned mounting location. If the possibility of susceptibility exists, a combined environmental test should be considered.3.4Test Sequence—The optimum test sequence is a compromise between two considerations:3.4.1The order in which the environmental exposures will occur in operational use.3.4.2 A sequence that will create a total stress on the sample that is representative of operation stress.The first consideration is impossible to implement in vehicle testing since exposures occur in a random order.The second consideration prompts the test designer to place the most severe environments last. Many sequences that have been successful follow this general philosophy, except that the temperature cycle is placed or performed first in order to condition the sample mechanically.4.Environmental Factors and Test Methods4.1Temperature4.1.1D EFINITION—Thermal factors are probably the most pervasive environmental hazard to vehicle electroniccomponents. Sources for temperature extremes and variations include:4.1.1.1The vehicle's climatic environment, including the diumal and seasonal cycles—Variations in climate bygeographical location must be considered. In the most adverse case, the vehicle that spends the winter in Canada may be driven in the summer in the Arizona desert. T emperature variations due to this source range from −54 to +85 °C (−65 to +185 °F).4.1.1.2Heat sources and sinks generated by the vehicle's operation—The major sources are the engine anddrivetrain components, including the brake system. Wide variations are found during operation. For instance, temperatures on the surface of the engine can range from the cooling system 88 °C (190 °F) to the surface at the exhaust system at 816 °C (1500 °F). This category also includes conduction, convection, and radiation of heat because of the various modes of the vehicle's operation.4.1.1.3Self-heating of the equipment due to its internal dissipation—A design review of the worst casecombination of peak ambient temperature (see 4.1.1.1 and 4.1.1.2), minimized heat flow away from the equipment, and peak-applied steady-state voltage should be conducted.4.1.1.4Vehicle operational mode and actual mounting location—Measurements should be made at the actualmounting site during the following vehicular conditions while they are subjected to the maximum heat generated by adjacent equipment, and while they are at the maximum ambient environment:a.Engine startb.Engine idlec.Engine high speedd.Engine turn off (Prior history important.)e.Various engine/road conditions4.1.1.5Ambient conditions before installation due to storage and transportation extremes—Shipment in unheatedaircraft cargo compartments may lower the minimum storage (nonoperating) temperature to −50 °C (−58°F).The thermal environmental conditions that are a result of these conditions can be divided into three categories:a.Extremes - The ultimate upper and lower temperatures the equipment is expected to experience.b.Cycling - The cumulative effects of temperature cycling within the limits of the extremes.c.Shock - Rapid change of temperature. Figure 1 illustrates one form of vehicle operation that inducesthermal shock and is derived from an actual road test of two vehicles. Thermal shock is also inducedwhen vehicle electronic componentry at elevated temperature is exposed to sudden rain or roadsplash, or when it is moved from a heated shelter into a low (−40 °C/−40 °F) ambient temperatureenvironment.FIGURE 1—TIME INTO RUN-MINUTES VEHICLE WARM-UP CHARACTERISTICS The vehicle electronic component designer is urged to develop a systematic, analytic method for dealing with steady-state and transient thermal analysis. The application of many devices containing semiconductors is temperature limited. For this reason, the potential extreme operating conditions for each application must be scrutinized to avoid failure in the field.4.1.2E FFECT O N P ERFORMANCE—The damaging effects of thermal stock and thermal cycling include:4.1.2.1Cracking of printed circuit board or ceramic substrates.4.1.2.2Thermal stress of fatigue failures of solder joints.4.1.2.3Delamination of printed circuit boards and other interconnect system substrates.4.1.2.4Seal failures, including the breathing action of some assemblies, due to temperature-induced dimensionalvariation that permits intrusion of liquid or vapor borne contaminants.4.1.2.5Failure of circuit components due to direct mechanical stress caused by differential thermal expansion. 4.1.2.6The acceleration of chemical attack on interconnects, due to temperature rise, can result in progressivedegradation of circuit components, printed circuit board conductors, and solder joints.In addition to these phenomena, high temperature extremes can cause a malfunction by:4.1.2.7Exceeding the dissociation temperature of surrounding polymer or other packaging components.4.1.2.8Carbonizing of the packaging materials resulting in the eventual progressive failure of the associatedpassive or active components. This is possible in cases of excessively high temperature. In addition, noncatastrophic failure is possible because of electrical leakage in the resultant carbon paths.4.1.2.9Changing the active device characteristics with increased heat, including changes in gain, impedance,collector-base leakage, peak blocking voltage, collector-base junction second breakdown voltage, etc.4.1.2.10Changing the passive device characteristics, such as permanent or temporary drift in resistor value andcapacitor dielectric constants, with increased temperature.4.1.2.11Changing the interconnect and relay coil performance due to the conductivity temperature coefficient ofcopper.4.1.2.12Changing the properties of magnetic materials with increasing temperature, including Curie point effectsand loss of permanent magnetism.4.1.2.13Changing the dimensions of packages and components leading to the separation of subassemblies.4.1.2.14Changing the strength of soldered joints because of changes in the mechanical characteristics of thesolder.4.1.2.15The severe mechanical stress caused by ice formation in moisture bearing voids or cracks.4.1.2.16The very rapid and extreme internal thermal stress caused by applying maximum power to semiconductoror other components after extended cold soak under aberrant operating conditions such as 36 V battery jumper starts.4.1.3R ECOMMENDED T EST M ETHODS4.1.3.1Temperature Cycle Test—Recommended thermal cycle profiles are shown in Figures 2a, b, and c andrecommended extreme temperatures in T ables 1A and 1B. If temperature characterization has been performed according to 4.1.1.4 the measured temperature may be substituted for the values in Tables 1a and 1b for the purpose of this document. The test method of Figure 2a, a 24 h cycle, offers longer stabilization time and permits a convenient room ambient test period. Figure 2b, an 8 h cycle, provides more temperature cycles for a given test duration. It is applicable only to vehicle electronic components whose temperatures will reach stabilization in a shorter cycle time. Stabilization should be verified by actual measurements; thermocouples, etc. It is important that all parts of the test specimen be held at the specified maximum and minimum temperatures for at least 15 min, after reaching stability at that temperature. This is to maintain thermal or pressure stresses generated in the test specimen for a reasonable period of time. Figure 2c illustrates a test method for thermal shock.FIGURE 2A—24 HOUR THERMAL CYCLEFIGURE 2B—SHORT (8 HOUR) THERMAL CYCLEFIGURE 2C—THERMAL SHOCKTABLE 1A—ENVIRONMENTAL EXTREME SUMMARY HEAVY-DUTY CAB OVER ENGINE TRUCK/TRACTORLocation (1)1.Figure 3 - Pictorial Description of LocationsTemperaturesMinTemperatures OperatingTemperaturesMax (2)2.If temperature characterization has been performed according to 4.1.1.4, the measured temper-ature may be substituted for the values in Tables 1a and 1b for the purpose of this document.ENGINE1a Underhood - Lower −40 °C 56 °C over ambient −40 °F 100 °F over ambient 1b Underhood - Upper (3)3.Exhaust Manifold 816 °C 1500 °F−40 °C 222 °C over ambient −40 °F 400 °F over ambient 1c Underhood Bulkhead−40 °C 56 °C over ambient −40 °F 100 °F over ambientINTERIOR:2a Floor−40 °C 27 °C 66 °C −40 °F 80 °F 150 °F 2b Instrument Panel (4)4.Windshield (Daylight opening on top of instrument panel) Direct sunlight surface temperature 115 °C maximum 240 °F maximum−40 °C 24 °C 85 °C −40 °F 75 °F 185 °F 2c Headliner −40 °C 24 °C 79 °C −40 °F75 °F 175 °F2d Inside Door 3a Bunk Area−40 °C 24 °C 93 °C −40 °F 75 °F 200 °F 3b Storage Compartment−40 °C 24 °C 74 °C −40 °F 75 °F165 °F CHASSIS:4a Forward −40 °C 120 °C −40 °F 248 °F 4b Rear−40 °C 95 °C −40 °F 203 °FEXTERIOR:5a Under No Data 5b Back No Data 5c Door −40 °C 56 °C over ambient −40 °F 100 °F over ambient5d TopNo DataMaximum ambient temperature may reach 85 °C (185 °F)TABLE 1B—ENVIRONMENTAL EXTREME SUMMARY HEAVY-DUTYCONVENTIONAL ENGINE TRUCK/TRACTORLocation (1)1.Figure 3 - Pictorial Description of LocationsTemperaturesMinTemperatures OperatingTemperaturesMax (2)2.If temperature characterization has been performed according to 4.1.1.4, the measured temper-ature may be substituted for the values in Tables 1a and 1b for the purpose of this document.ENGINE1a Underhood - Lower −40 °C56 °C over ambient −40 °F100 °F over ambient 1b Underhood - Upper (3)3.Exhaust Manifold 816 °C 1500 °F−40 °C222 °C over ambient −40 °F400 °F over ambient 1c Underhood Bulkhead−40 °C56 °C over ambient −40 °F100 °F over ambientINTERIOR:2a Floor−40 °C 27 °C 75 °C −40 °F 80 °F 165 °F 2b Instrument Panel (4)4.Windshield (Daylight opening on top of instrument panel) Direct sunlight surface temperature 115 °C maximum 240 °F maximum−40 °C 24 °C 85 °C −40 °F 75 °F 185 °F 2c Headliner −40 °C 24 °C 79 °C −40 °F75 °F 175 °F2d Inside Door 3a Bunk Area−40 °C 24 °C 93 °C −40 °F 75 °F 200 °F 3b Storage Compartment−40 °C 24 °C 74 °C −40 °F 75 °F165 °F CHASSIS:4a Forward −40 °C 121 °C −40 °F 250 °F 4b Rear−40 °C 93 °C −40 °F 200 °FEXTERIOR:5a Under No Data 5b Back No Data 5c Door −40 °C 56 °C over ambient −40 °F 100 °F over ambient5d TopNo DataMaximum ambient temperature may reach 85 °C (185 °F)FIGURE 3—VEHICLE ENVIRONMENTAL ZONESSeparate or single test chambers may be used to generate the temperature environment described by the thermal cycles. By means of circulation, the air temperature should be held to within ±3 °C (±5 °F) at each of the extreme temperatures. The test specimens should be placed in a position, with respect to the airstream, where there is substantially no obstruction to the flow of air across the specimen. If two test specimens are used, care must be exercised to assure that the test samples are not subject to temperature transition rates greater than that defined in Figures 2a and 2b. Direct heat conduction from the temperature chamber heating element to the specimen should be minimized.NOTE—Airflow is a function of actual equipment location. Simulation of actual airflow and thermal transfer operation conditions should be considered in test design.Electrical performance should be measured under the expected operational minimum and maximum extremes of excitation, input and output voltage, and load at both the cold and hot temperature extremes.These measurements provide insight into electrical variations with temperature.4.1.3.2Thermal Shock Test—Thermal shock that can be expected in the vehicle environment is simulated by themaximum rates of change shown on the recommended thermal cycle profile portrayed in Figure 2c. The thermal shock test should begin with a 2 h presoak (−40 °C/−40 °F). The test item should be transferred to the hot chamber (85 °C/185 °F) where it should remain for 2 h, then transferred to the cold chamber (−40 °C/−40 °F) for 2 h. This cycle should be repeated at least five times. Each transfer should be accomplished in1 min or less.4.1.3.3Thermal Stress—Thermal stress is caused by repeat cycling through the thermal profiles of Figures 2a, b,and c. Many failures are due to fatigue. Slow cycles not repeated often will not demonstrate this. The number of cycles is a function of the vehicle electronic component application. Functional electrical testing during temperature transitions or immediately after temperature transitions, is a means of detecting poor electrical connections. The effect of thermal stress is similar to thermal shock but is caused by fatigue.NOTE—Although uniform oven temperatures are desirable, the only means of heat removal in some vehicle environments may be by special heat sinks or by free convection to surrounding air. Itmay be necessary to use conductive heat sinks with independent temperature controls in theformer case and baffles or slow speed air stirring devices in the latter to simulate such conditionsin the laboratory (see Section 3).4.1.4R ELATED S PECIFICATIONS—A generally accepted method for small part testing is defined in MIL-STD-202F,Method 107F, Thermal Shock, Method A or B, alternately MIL-STD-810D, Method 503.2. The short dwell periods at high temperature are satisfactory where temperature stabilization is verified by actual measurements.4.2Humidity4.2.1D EFINITIONS—(Contained in 4.2.2)4.2.2E FFECTS O N P ERFORMANCE—Both primary and secondary humidity sources exist in the vehicle. In additionto the primary source externally applied ambient humidity, the cyclic thermal-mechanical stresses caused by operational heat sources introduce a variable vapor pressure on the seals. Temperature gradients set up by these cycles can cause the dew point to travel from locations inside the equipment to the outside and back, resulting in additional stress on the seals.The actual relative humidity in the vehicle depends on factors such as operational heat sources, trapped vapors, air-conditioning, and cool-down effects. Recorded data indicates an extreme condition of 98% relative humidity at 38 °C (100 °F).Primary failure modes include corrosion of metal parts because of galvanic and electrolytic action, as well as corrosion caused by interaction with contaminated water and oxygen. Other failure modes include changes in electrical properties, surface bridging corrosion products and condensation between circuits, decomposition of organic matter because of attacking organisms (for example, mildew), and swelling of elastomers.4.2.3R ECOMMENDED T EST M ETHODS—The most common way to determine the effect of humidity on vehicleelectronic components is to over test and examine any failure for relevance to the more moderate actual operating conditions. The most common test is an 8 h active temperature humidity cycling under accelerated conditions (Figure 4a). A second test is an 8 to 24 h exposure at 103.4 kPa gage pressure (15 lbf/in2 gage) in a pressure vessel (Figure 4b). This is a quick and effective method for uncovering defects in plastic encapsulated semiconductors.FIGURE 4—RECOMMENDED HUMIDITY CYCLESAn optional frost condition may be incorporated during one of these humidity cycles. Electrical performance should be continuously monitored during these frost cycles to note erratic operation. Heat-producing and moving parts may require altering the frost condition portions of the cycle to allow a period of nonoperation induced frosting.4.2.4R ELATED S PECIFICATIONS—Many related humidity specifications are recommended for review and reference.The first: MIL-STD-810D, Method 507.2, Procedures I through III, Humidity, is a system-oriented test method. The second, a modified version of MIL-STD-202F, Method 103B, Humidity (Steady State), is intended to evaluate materials. The third, MIL-STD-202F, Method 106E, Moisture Resistance, is a procedure for testing small parts.4.3Salt Spray Atmosphere4.3.1D EFINITION—(Contained in 4.3.2)4.3.2E FFECT O N P ERFORMANCE—Vehicle electronic components mounted on the chassis, exterior, and underhoodare often exposed to a salt spray environment. In coastal regions, the salt is derived from sea breezes, and in colder climates, from road salt. Although salt spray is generally not found in the interior of the vehicle, it is advisable to evaluate the floor area for potential effects of saline solutions that were transferred from the outside environment by vehicle operators, passengers, and transported equipment.Failure modes due to salt spray are generally the same as those associated with water and water vapor.However, corrosion effects and alteration of conductivity are accelerated by the presence of saline solutions and adverse changes in pH.4.3.3R ECOMMENDED T EST M ETHODS—The recommended test method for measuring susceptibility of vehicleelectronic component to salt spray is the American Society for Testing and Materials (ASTM) Standard Method of Salt Spray (Fog) Testing Number B 117-73. Similar test methods are found in MIL-STD-202, Method 101D, and MIL-STD-810D, Method 509.2.The test consists of exposing the vehicle electronic component to a solution of five parts salt to 95 parts water, atomized at a temperature of 35 °C (95 °F). The component being tested should be exposed to the salt spray for a period of 24 to 96 h. The actual exposure time must be determined by analysis of the specific mounting location. When the tests are concluded, the test specimens should be gently rinsed in clean running water, about 38 °C (100 °F), to remove salt deposits from the surface, and then immediately dried.Drying should be done with a stream of clean, compressed dry air at about 175.8 to 241.3 kPa gage pressure (35 to 40 lbf/in2 gage). The vehicle electronic component should be tested under nominal conditions of voltage and load throughout the test.NOTE—The Pascal (Pa) is the designated SI (metric) unit for pressure and stress. It is equivalent to 1 N/m2.Where leakage resistance values are critical, appropriate measurements under wet and dry conditions may be necessary.4.3.4R ELATED S PECIFICATIONS—ASTM B 117-73 is the recommended test method.4.4Immersion and Splash (Water, Chemicals, and Oils)4.4.1D EFINITION—Vehicle electronic component mounted on or in the vehicle are exposed to varying amounts ofwater, chemicals, and oil. A list of potential environmental chemicals and oils includes:Engine Oils and AdditivesTransmission OilRear Axle OilPower Steering FluidBrake FluidAxle GreaseWasher SolventGasolineDiesel FuelFuel AdditivesAlcoholAnti-Freeze Water MixtureDegreasersSoap and DetergentsSteamBattery AcidWater and SnowSalt WaterWaxesKeroseneFreonSpray PaintPaint StrippersEtherDust Control Agents (magnesium chloride)Moisture Control Agents (calcium chloride)Vinyl PlasticizersUndercoating MaterialMuriatic AcidAmmoniaThe modified chemical characteristics of these materials when degraded or contaminated should also be considered.4.4.2E FFECT O N P ERFORMANCE—Loss of the integrity of the container can result in corrosion or contamination ofvulnerable internal components. The chemical compatibility can be determined by laboratory chemical analysis. Devices such as sensors, that may be immersed in fluids for a long period, should be subjected to laboratory life tests in these fluids.4.4.3R ECOMMENDED T EST M ETHODS—The vehicle electronic component designer should first determine whetherthe parts must withstand complete immersion or splash, and which fluids are likely to be present in the application. Immersion and splash tests are generally performed following other environmental tests because this sequence tends to aggravate incipient defects in seals, seams, and bushings that might otherwise escape notice.Splash testing should be performed with the equipment mounted in a normal operating position with any drain holes open. Any integral parts, such as electrical connectors, shall be in place. Areas of the equipment not subject to splash testing may be sealed or otherwise isolated. The test apparatus should be designed to provide 100% coverage of the test surface using 80 degrees flat fan nozzles located 20 to 25 cm(10 to 12 in) from the test surface. The apparatus should provide a source pressure of approximately200kPa gauge (29 psig) with a flow rate of 2650 cm3/min (0.7 gal/min). The equipment should be exposed to the spray for 5 min of a 10 min period for a total of two cycles.During immersion testing, utilizing water as the fluid, the component ordinarily is not operated due to setup logistics and techniques of this test. In this test, the vehicle electronic component in its normal exterior package is immersed in tap water at about 18 °C (65 °F). The test sample should be completely covered by the water. The sample is first positioned in its normal mounting orientation. It remains in this position for 5min and then rotated 180 degrees. It should remain in this position for 5 min and then rotated 90 degrees about the other axis where it remains for 5 min. Immediately after removal, the sample should be exposed toa temperature below freezing until the entire mass is below freezing. The sample is then returned to roomtemperature, air dried, functionally tested, and inspected for damage.More severe tests such as combined temperature, pressure, and continuous fluid contact must be considered for equipment subjected to extreme environments; for example, exposure to coolant water, brake fluid, and transmission oil. Caution must be used in specifying combined tests because they may be unrealistically severe for many applications.4.4.4R ELATED S PECIFICATIONS—None4.5Steam Cleaning and Pressure Washing4.5.1D EFINITION—(Contained in 4.5.2)4.5.2E FFECTS O N P ERFORMANCE—The intense heat from cleaning sprays and the caustic nature of chemicalagents used in washing solutions create a severe environment for devices and associated wiring and connectors mounted in the engine, chassis, and exterior areas. This exposure can cause a degradation of insulation and seals as well as cracking of vinyl connectors and component packaging. High pressure wash-down may produce results similar to salt spray in many truck interior.4.5.3R ECOMMENDED T EST M ETHOD—The electronic component under test shall be mounted in its normaloperating position with drain holes, if used, open. If an integral connector is used, it shall be mated. The test apparatus should be designed to provide 100% coverage of the exposed surface of the electronic component using flat fan spray nozzles located 20 to 30 cm (7.9 to 11.8 in) away. This apparatus should provide a source pressure of approximately 1400 kPa gage (203 lbf/in2 gage) with a flow rate of 9460 cm3/min (150gal/h). For the steam cleaning, the water temperature should be at 93 °C (200 °F). The test item should be exposed to the spray for 3 s of a 6 s period for a total of 375 cycles.A sample test device is illustrated in Figure 5.。