数控车工技师操作技能考核评分表
机械类—数控车工操作考试评分标准

机械类—数控车工操作考试评分标准数控车工操作考试评分标准由工件质量和职业素养(现场操作规范)两部分组成,总分为工件质量分与职业素养(现场操作规范)分之和。
一、工件质量评分标准1. 工件质量分的配分公布的工件质量评分标准(评分样表)中每一项评分项目(对应试题加工表面特征类型)为一个配分值区间;考试使用的工件质量评分标准中每一项评分项目(对应试题图样标注要素)为一个确定的配分数值。
2. 工件质量分的评定考试结束后由评定人员测量工件各评分项目的实际要素,填写检测结果,根据评定标准评定该项目的得分,各项得分之和即为工件质量分。
二、职业素养(现场操作规范)评分标准在考试过程中由评定人员按现场操作规范评定,单项分值按评分标准扣完为止。
若出现否决项则职业素养(现场操作规范)评分总分按零分计。
三、考试时间及考试停止操作考试时间150分钟包括工件加工与交卷、考试结束前的工位清理、卫生工作等。
以下情况考生必须立即停止考试:1.考评人员指出考生严重违反安全操作规程。
2.考试时间结束。
3.发生重大安全事故,终止考试。
四、考试说明1.考件材料和考试所使用的设备由考点统一准备。
2.考试所使用的工、量、刃、辅具等由考点统一准备。
3.公布的考场准备单样表为考生考前培训参考用,正式的考场准备通知单根据考点实际情况可能略有调整,不再公布。
4.考试过程中如发生因考生操作失误引起设备损坏情况,设备维修费用由参加考试的学校和学生共同承担,社会考生则由考生本人承担。
机械类—数控车工准备通知单(样表)一、材料准备:二、设备准备:四、工具准备:机械类—数控车工现场操作规范评分表准考证号考试场次工位号机械类—数控车工工件质量评分表(样表)。
数控车技能培训考核表格

数控车技能培训考核表格
考核项目评分标准评分(满分10分)
车刀更换正确操作步骤、时间和安全意识
加工精度加工零件尺寸与要求的偏差
加工效率完成零件加工所需时间及设备利用率
CNC程序编辑编写、修改和调试数控加工程序的能力
设备日常维护设备日常保养和维护的操作及记录
加工安全意识对设备操作安全规范和操作风险的认识
说明:
该表格用于对数控车技能培训学员进行综合考核,评估其在数控车操作和管理方面的能力。
考核项目包括车刀更换、加工精度、加工效率、CNC程序编辑、设备日常维护和加工安全意识等方面。
评分标准应当明确具体,以便能够客观、公正地评定学员的能力水平,评分满分为10分。
考核表格应当由专业的数控车技术培训机构或相关部门设计,并根据实际情况进行必要的调整和完善。
数控车工实操考核评分表

φ280-0.0
7
每超差0.01扣1分
9
φ330-0.03
10
不合要求不得分
10
长度600-0.05
4
每超差0.01扣1分
11
其他长度
2
不合要求不得分
12
螺纹退刀槽5×2
2
不合要求不得分
13
锥度45度
6
每超差2ˊ扣1分
14
整体外形
5
圆弧曲线连接圆滑、形状准确
15
粗糙度要求
10
大于1.6不得分
16
姓名
总分
考核工件名称
圆弧轴
图号
GB000203
序号
考核内容及要求
配分
评分标准
得分
1
手工编程
20
语法错误、数据错误2分/处
2
程序输入
3
手工输入
3
轨迹模拟
3
图形寻错
4
建立工件坐标系
4
建立合适零件坐标系
5
试切对刀
5
步骤错扣1分/处
6
加工调试
5
7
φ230-0.03
7
每超差0.01扣1分
7
19
安全操作、文明生产
视情节轻重扣分,扣分<10分
额定时间
90分钟
实际加工时间
考评人
综合评价
张数控车工技师操作评分
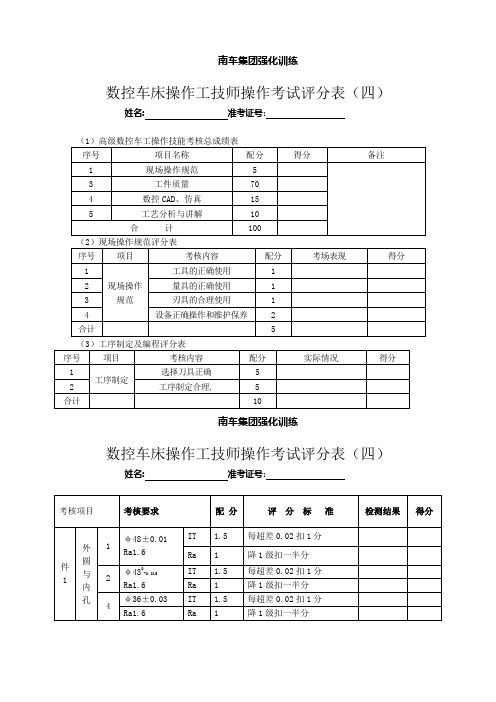
数控车床操作工技师操作考试评分表(四)
姓名:准考证号:
(1)高级数控车工操作技能考核总成绩表
序号
项目名称
配分
得分
备注
1
现场操作规范
5
3
工件质量
70
4
数控CAD、仿真
15
5
工艺分析与讲解
10
合计
100
(2)现场操作规范评分表
序号
项目
考核内容
配分
考场表现
得分
1
现场操作规范
工具的正确使用
1
12
椭圆轮廓度
2
达不到要求不得分
Ra1.6
1
降级不得分
13
内圆弧R3
1
达不到要求不得分
Ra1.6
1
降级不得分
14
28°内锥度,接触面≥70%
2
达不到要求不得分
Ra1.6
1
降级不得分
15
倒角(5处)
1
一处达不到要求不得分
16
内外沟槽各两处
2
超差不得分
Ra1.6
1
降级不得分
17
同轴度两处
2
达不到要求不得分
Ra
1
降级不得分
24
50-0.03两处
1
每超差0.02扣0.5分
25
98±0.02
1
每超差0.02扣0.5分
26
椭圆轮廓度/Ra1.6
1.5
/0.5
27
圆弧R2
1
达不到要求不得分
其它
29
M30X1.5左,旋向
1
每超差0.02扣1分
中级数控车床工的全面练习(图纸、评分表和完整程序)
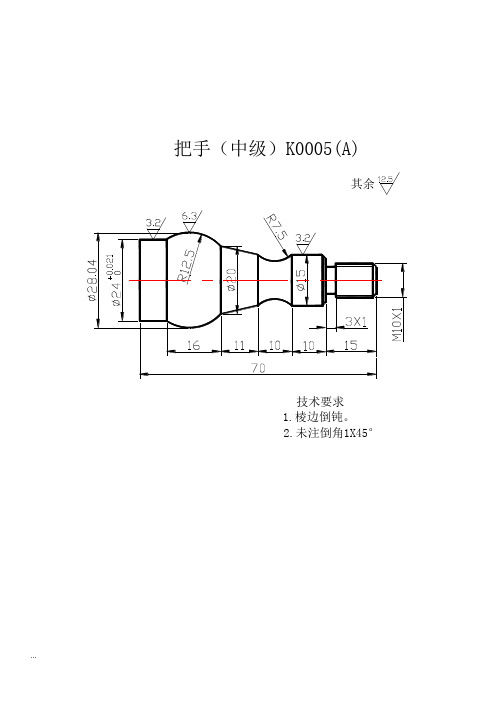
技术要求1.棱边倒钝。
2.未注倒角1X45°把手(中级)K0005(A)其余中级数控车床工技能评分表(A)专业工种号09216技术要求棱边倒钝。
未注倒角其余手柄(中级)K0003(B)中级数控车床工技能评分表(B)专业工种号09216技术要求棱边倒钝。
未注倒角其余旋钮(中级)K0002(C)中级数控车床工技能评分表(C)专业工种号09216技术要求棱边倒钝。
未注倒角旋钮(中级)K0006(D)中级数控车床工技能评分表(D)专业工种号09216技术要求棱边倒钝。
未注倒角端盖(中级)K0004(E)其余中级数控车床工技能评分表(E)专业工种号09216技术要求棱边倒钝。
未注倒角内锥体(中级)K0020(F)其余技术要求棱边倒钝。
未注倒角球头轴(中级)K0021(G)其余技术要求棱边倒钝。
未注倒角多阶套(中级)K0022(H)其余其余双锥螺套(中级)K0023(I)技术要求棱边倒钝。
未注倒角螺套(中级)K0024(J)其余技术要求棱边倒钝。
未注倒角K0005(A)把手01234G0 X100 Z100M3 S600T0101(外圆刀)G0 X30 Z2G73 U11 R11G73 P1 Q2 U0.8 F100N1 G0 X8 Z2G1 Z0X9.8 Z-1Z-15X13X15 W-1Z-25G2 X15 Z-35 R7.5G1 X20 Z-46G3 X24 Z-62 R12.5N2 G1 Z-75G0 X100 Z100M5M0M3 S2000T0101(外圆刀)G0 X30 Z2G70 P1 Q2 F80G0 X100 Z100M5M0M3 S500T0202(切槽/切断刀)G0 X17 Z-15G94 X8 R0 F20G0 X100Z100M5M0M3 S600T0303(螺纹刀)G0 X12 Z5G92 X9.5 Z-13 F1X9.2X8.9 X8.8X8.8G1 F100G0 X100 Z100M5M0M3 S500T0202(切槽/切断刀)G0 X30 Z-(70+刀宽)G94 X2 R0 F20G0 X100Z100M5M30K0002(C)旋钮O1234G0 X100 Z100M3 S500T0101(外圆刀)G0 X35 Z2G71 U1 R1G71 P1 Q2 U0.8 F100 N1 G0 X0G1 Z0G3 X23.75 Z-2.05 R35 G3 X25.23 Z-3.005 R1 G1 X28 Z-21.7X33 W-1.3N2 Z-38G0 X100 Z100M5M0M3 S2000T0101(外圆刀)G0 X35 Z2G70 P1 Q2 F80G0 X100 Z100M5M0M3 S500T0202(切槽/切断刀)G0 X35 Z-(33+刀宽)G94 X2 R0 F20G0 X100Z100M5M0调头M3 S500T0303(镗孔刀)G0 X18 Z2G71 U0.5 R0.5G71 P3 Q4 U-0.8 F80 N3 G0 X27G1 Z0X25 Z-1Z-4 X21.5X18.7 W-1.5Z-17N4 X18G0 Z150M5M0M3 S1000T0303(镗孔刀)G0 X18 Z2G70 P3 Q4 F60G0 Z150M5M0M3 S500T0404(螺纹刀)G0 X18 Z5G92 X19 Z-14 F1.5 X19.2X19.4X19.6X19.8X20X20G1 F100G0 Z150M5M30;K0004(E)端盖O1234(镗孔刀)G0 X100 Z100M3 S500T0202G0 X13 Z2G71 U0.5 R0.5G71 P1 Q2 U-0.8 F80N1 G0 X25G1 Z0X22.3 Z-1.5Z-10X20Z-15G3 X14 Z-20 R10N2 Z-30G0 X100 Z100M5M0M3 S1000T0202(镗孔刀)G0 X13 Z2G70 P1 Q2 F60G0 X100 Z100M5M0M3 S600T0303(螺纹刀)G0 X21 Z5G92 X22.5 Z-8 F1.5X22.7X22.9X23.1X23.3X23.5X23.7X24X24G1 F100G0 Z100X100M5M0 M3 S500T0101(外圆刀)G0 X30 Z2G71 U1 R1G71 P3 Q4 U0.8 F100 N3 G0 X28N4 G1 Z-35G0 X100 Z100M5M0M3 S20000T0101(外圆刀)G0 X30 Z2G70 P3 Q4 F80G0 X100 Z100M5M0M3 S500T0404(切槽/切断刀)G0 X30 Z-(30+刀宽)G94 X13 R0 F20G0 X100Z100M5M30K0020(F)内锥体O1234G0 X100 Z100M3 S500T0202(镗孔刀)G0 X14 Z2G71 U0.5 R0.5G71 P1 Q2 U-0.8 F100N1 G0 X26G1 Z0X24 Z-1Z-15X22X19 Z-45N2 X15G0 Z150M5M0M3 S1200T0202(镗孔刀)G0 X14 Z2G70 P1 Q2 F60G0 Z150M5M0M3 S500T0101(外圆刀)G0 X35 Z2G71 U1 R1G71 P3 Q4 U0.8 F100N3 G0 X28G1 Z0X30 Z-1Z-20X34N4 Z-70G0 X100 Z100M5M0M3 S2000T0101(外圆刀)G0 X35 Z2G70 P3 Q4 F80 G0 X100 Z100M5M0T0303(螺纹刀)S450 M3G0 X32 Z5G92 X29.7 Z-22 F1.5 X29.4X29.1X28.8X28.5X28.4X28.3G0 X100 Z100 M5M0M3 S500T0404(切槽/切断刀)G0 X35 Z-20G94 X27 F20G0 Z-50G94 X31 F20G0 Z-69G94 X30 F20X32 R2.5X14 R0G0 X100Z100M5M30K0022(H)多阶套O0001G0 X100 Z100 S500 M3 T0303(内孔刀)G0 X18.6 Z0G71 U0.8 R0.5G71 P1 Q2 U-0.6 F60 N1 G0 X26G1 Z0X24 Z-1Z-5X21N2 X19 W-1G0 X100 Z100 M5M0S800 M3T0303(内孔刀)G0 X18.6 Z2G70 P1 Q2 F60G0 X100 Z100 M5M0T0404(螺纹刀)S450 M3G0 X17.6 Z5G92 X19 Z-22 F1.5X19.3X19.5X19.7X19.8X19.9X20G0 X100 Z100 M5M0M3 S500T0101(外圆刀)G0 X35 Z2G71 U1 R1G71 P3 Q4 U1 F100N3 G0 X28G1 Z0X30 Z-1Z-10X33 X34 W-0.5N4 Z-69G0 X100 Z100 M5M0M3 S500T0202(切槽/切断刀)G0 X36 Z-(24+刀宽) G94 X28.4 F15W-2W-4W-6.5W-9X28.2 W-(14-刀宽) X33 R1.5G0 W-(14-刀宽)G94 X33 R1.5 F15G0 X36 Z-(51+刀宽) G94 X28.4F15W-2W-4W-6.5W-9X28.2 W-(14-刀宽) X33 R1.5G0 X100 Z100 M5M0M3 S500T0202(切槽/切断刀)G0 X36 Z-(64+刀宽) G1 X26 F15X28W1X26 W-1X14X36 F100G0 X100 Z100 M5M30。
数控车工技师操作技能考核评分表

超差0.01扣1分
3
Ra1.6
降级不得分
2
30
φ410 -0.039
IT
超差0.01扣1分
3
Ra1.6
降级不得分
2
M30×1.5-6H
IT
一项不符扣1分
1
Ra1.6
降级不得分
1
锥面(30°、
8.5、42.02)
IT
一项不符扣1分
1
Ra1.6
降级不得分
1
椭圆
轮廓
与检测样板一致得分
2
Ra1.6
降级不得分
序号
考核内容及要求
评分标准
配分
检测结果
扣分
得分
备注
26
Tr36×6
IT
大径
超差0.02扣1分
1
中径
超差0.02扣1分
2
Ra3.2
降级不得分
2
27
φ580 -0.03
IT超差0.01扣1分2源自Ra1.6降级不得分
1
28
φ55-0.01-0.04
IT
超差0.01扣1分
2
Ra1.6
降级不得分
1
29
φ25+0.03 0
超差不得分
1
18
12±0.05
超差不得分
1
19
4.50.05 0
超差不得分
1
20
R5、R2
超差不得分
2
21
4×2
超差不得分
1
22
118±0.04
超差不得分
2
23
形位公差1处
错误不得分
2
数控车工评分表
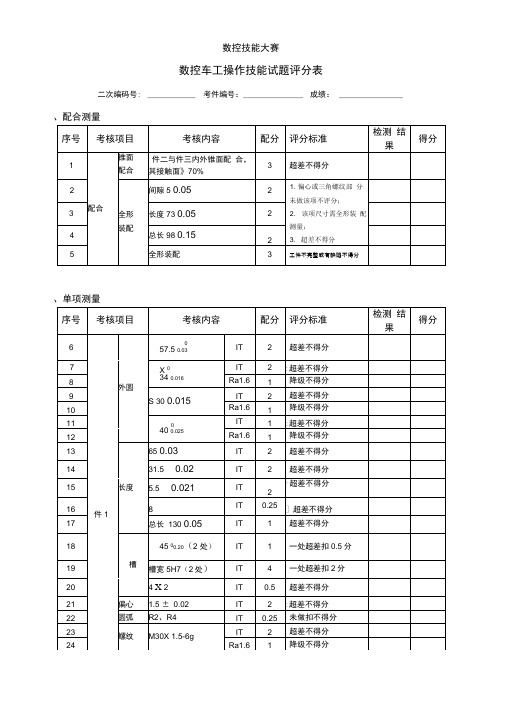
"0.04
280
IT
2
超差不得分
43
件2
260.02
IT
2
超差不得分
44
长度
50.015
IT
2
超差不得分
45
8
IT
0.25
超差不得分
46
480.02
IT
2
超差不得分
47
总长52
IT
0.25
超差不得分
48
内沟槽4X2
IT
0.5
:超差不得分
49
外沟槽59X4
IT
0.5
超差不得分
50
沟槽
70
IT
0.5
34
Ra1.6
1
:降级不得分
35
内孔
0.039
400.010
IT
2
:超差不得分
36
Ra1.6
1
:降级不得分
37
0.035
57.50.010
IT
2
:超差不得分
38
Ra1.6
1
降级不得分
39
41.67、37.67
IT
1
一处超差扣0.5分
40
内锥
内锥表面
Ra1.6
1
降级不得分
41
0.04
120
IT
2
超差不得分
IT
4
一处超差扣2分
20
4X2
IT
0.5
超差不得分
21
偏心
1.5±0.02
IT
2
:超差不得分
22
圆弧
R2、R4
车工中级操作技能考核评分记录表
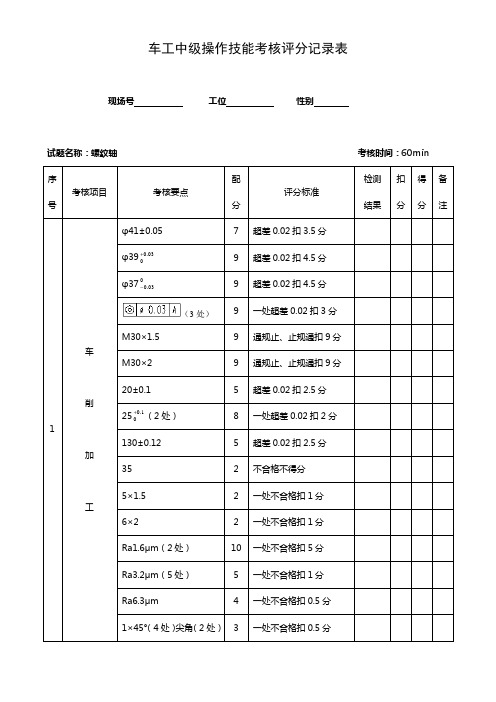
车工中级操作技能考核评分记录表现场号工位性别试题名称:螺纹轴考核时间:60min 序号考核项目考核要点配分评分标准检测结果扣分得分备注1 车削加工φ41±0.05 7 超差0.02扣3.5分φ3903.0+9 超差0.02扣4.5分φ37003.0-9 超差0.02扣4.5分(3处)9 一处超差0.02扣3分M30×1.5 9 通规止、止规通扣9分M30×2 9 通规止、止规通扣9分20±0.1 5 超差0.02扣2.5分251.0+(2处)8 一处超差0.02扣2分130±0.12 5 超差0.02扣2.5分35 2 不合格不得分5×1.5 2 一处不合格扣1分6×2 2 一处不合格扣1分Ra1.6μm(2处)10 一处不合格扣5分Ra3.2μm(5处) 5 一处不合格扣1分Ra6.3μm 4 一处不合格扣0.5分1×45°(4处)尖角(2处) 3 一处不合格扣0.5分考评员: 核分员: 年月日车工中级操作技能考核评分记录表现场号工位性别试题名称:圆锥螺纹轴考核时间:60min 序号考核项目考核要点配分评分标准检测结果扣分得分备注1 车削加工φ410025.0-7 每超差0.02扣3.5分φ39±0.02 7 每超差0.02扣3.5分φ350025.0-7 每超差0.02扣3.5分1:10(5°42′18″)10 每超差10′扣5分(3处)9 一处每超差0.02扣3分M24×2 12 通规止、止规通扣12分130±0.1 4 每超差0.02扣2分30015.0-5 每超差0.02扣2.5分2505.0-4 每超差0.02扣2分25 2 不合格不得分20 2 不合格不得分8×1.5 2 不合格扣2分3×1 2 不合格扣2分Ra1.6μm(2处)8 一处不合格扣4分Ra3.2μm(5处)10 一处不合格扣2分Ra6.3μm(8处) 4 一处不合格扣0.5分考评员: 核分员: 年月日车工高级操作技能考核评分记录表现场号工位性别试题名称:圆锥梯形螺纹轴操作时间:70min序号考核项目评分要素配分评分标准检测结果扣分得分备注1 车削加工φ360025.0-7 超差0.02扣3.5分φ34±0.02 6 超差0.02扣3分φ2302.001.0+-7 超差0.04扣3.5分1:10(5°42′18″±5″) 6 超差5′扣3分(3处)6 一处超差0.02扣2分Tr30×6φ300375.0-3 超差0.02扣1.5分Tr30×6牙型角30°±16′6 超差2′扣3分Tr30×6中径8 超差0.02扣4分Tr30×6底径 4 超差0.02扣2分130±0.1 3 超差0.02扣1.5分2504.0-3 超差0.02扣1.5分2002.0-3 超差0.02扣1.5分10×3.5 4 一处不合格扣2分25 2 不合格不得分20 2 不合格不得分Ra1.6μm(2处)8 一处不合格扣4分Ra3.2μm(7处)14 一处不合格扣2分Ra6.3μm 3 一处不合格扣0.5分尖角与30°倒角(6处) 3 一处不合格扣0.5分两端A3中心孔 2 一处不合格扣1分2 现场考核工具、量具使用,清理现场,安全文明操作工具、量具使用错一件从总分中扣1分,未清理现场扣5分,每违反一项规定从总分中扣5分,严重违规停止操作。
- 1、下载文档前请自行甄别文档内容的完整性,平台不提供额外的编辑、内容补充、找答案等附加服务。
- 2、"仅部分预览"的文档,不可在线预览部分如存在完整性等问题,可反馈申请退款(可完整预览的文档不适用该条件!)。
- 3、如文档侵犯您的权益,请联系客服反馈,我们会尽快为您处理(人工客服工作时间:9:00-18:30)。
江苏省职业技能鉴定
数控车工技师操作技能考核评分表
考件编号:姓名:准考证号:总分:①件1和件2配合分:15分;
②件1检测精度配分表(合计:50分)
③零件二检测精度配分表(合计:35分)
26 Tr36×6 IT
大径超差0.02扣1分 1
中径超差0.02扣1分 2 Ra3.2 降级不得分 2
27 φ58 0 -0.03
IT 超差0.01扣1分 2
Ra1.6 降级不得分 1
28 φ55-0.01
-0.04
IT 超差0.01扣1分 2
Ra1.6 降级不得分 1
29 φ25 +0.03
IT 超差0.01扣1分 3
Ra1.6 降级不得分 2 30 φ41 0 -0.039
IT 超差0.01扣1分 3
Ra1.6 降级不得分 2
M30×1.5-6H IT 一项不符扣1分 1 Ra1.6 降级不得分 1
锥面(30°、8.5、42.02)IT 一项不符扣1分 1 Ra1.6 降级不得分 1
椭圆
轮廓与检测样板一致得分 2
Ra1.6 降级不得分 1
26 4×2、8×4 超差不得分 1
27 27±0.05 超差不得分 1
28 20±0.03 超差不得分
29 36 0
-0.05
超差不得分 1
30 13.5 0
-0.06
超差不得分 1
31 88±0.05 超差不得分 1
32 倒角未注公差错误不得分 1
33 零件整个轮廓全部完成未全部完成轮廓加工
不得分
2
考评员复核统分。