车架受力分析基础
混凝土搅拌运输车副车架的受力分析及结构优化
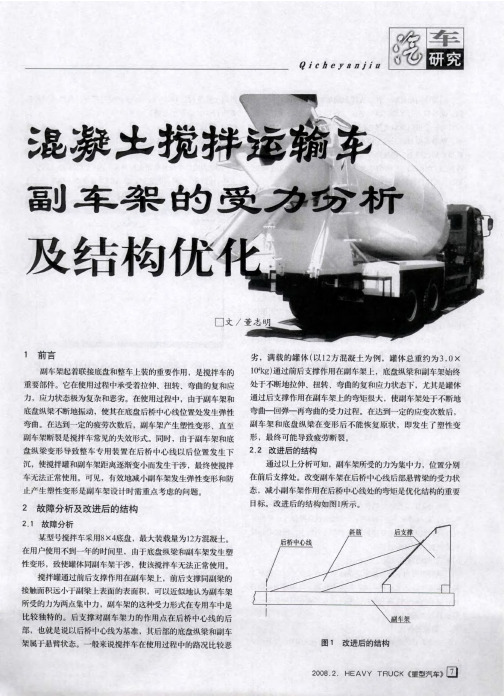
“ 蔷; 而 ’~ 一
Qi
n
i i
珏
暑 霸嗣 ◇
谢多
—
__l 卜
一
副 车 架 的
及结构优
1
前言
副 车架起 着联 接 底盘 和整 车 上 装 的重 要 作 用
,
劣
是搅 拌 车 的
1O
,
满 载 的罐 体 ( 以 1 2 方 混 凝 土 为 例
,
,
罐体 总重 约 为 3
.
0 X
。
l(g ) 通 过 前后支撑 作 用 在 副 车 架上
一 … .
为 l验证理论 计算的正确性以及优化 后的结 构在实际使 『 用过程 巾的效果 ,采用了贴片试验方法对优 化后的结构进行
r 际验证 。 实
…
t
骂
3 改进 后 的试 验过 程
3
.
1 试验所采 用的设备及 测点分布 本 次试 验采取的 测试仪 器是美国Z nc o k 6 8 o iB o / lE便携
由于 底盘纵 梁 和副 车架发 生 塑
,
致使罐 体 同副 车架 干 涉
使该搅拌 车 无 法 正 常使 用
,
。
搅拌罐 通过 前后 支 撑作 用 在副 车架上 接 触 面积 远 小 于 副 梁上 表 面 的表 面 积
,
前 后 支撑 同副 梁 的
’
可 以 近 似地 认 为副 车架
汽车车架的动力学分析--模态分析

图1-3 一阶弯曲
图1-4 二阶弯曲
图1-5 二阶扭转
图1-6 三阶弯曲
图1-7 前端局部模态
图1-8 弯扭组合
4.3汽车模态分析结果的评价指标
工程结构要具有与使用环境相适应的动力学特性。一辆汽车结构优劣的基本着眼点是在弯曲和扭转方面总的动态性能。如果汽车结构动力学特性不能与其使用环境相适应,即结构模态与激励频率藕合,或汽车子结构之间有模态藕合,都会使汽车产生共振,严重时会使整个汽车发生抖振,车内噪声过大,局部产生疲劳破坏等[5]。模态分析是计算结构的固有频率及其相应振型。结构的固有频率是评价结构动态性能的主要参数,当结构固有频率和工作频率一致时,就会发生共振现象,产生较大的振幅,大大降低寿命。固有振型是发生共振现象时结构的振动形式。
[6]黄华,茹丽妙.重型运输车车架的动力学分析[J].车辆与动力技术,2001.6
6参考文献
[1]余志生.汽车理论[M].北京:清华大学出版社, 1989
[2]丁丽娟.数值计算方法[M].北京:北京理工大学出版社, 1997
[3]王勖成,邵敏.有限元基本原理和数值方法[M].北京:清华大学出版社.1997
[4]傅志方,华宏星.模态分析理论与应用,上海交通大学出版社,2000
[5]《汽车工程设计》编辑委员会.汽车工程手册.试验篇.北京:人民交通出版社.2001.6
4车架模态计算与结果分析
4.1模态分析步骤
对车架进行模态分析主要有以下步骤:
(l)在Pro/E中建立车架的三维模型。
(2)施加边界条件和载荷(对于自由模态不施加约束条件),定义分析类型和求解方法并进行网格划分、提交求解器求解。
(3)提取结果,进行可视化处理,对结束进行分析。
摩托车车架的载荷分析与合理设计

摩托车车架的载荷分析与合理设计摩托车车架作为摩托车的骨架,承担着承载引擎、悬挂系统以及车身负重的重要功能。
在设计和制造摩托车车架时,必须充分考虑各种载荷,以确保车架的稳定性、耐久性和安全性。
本文将重点探讨摩托车车架的载荷分析与合理设计。
首先,摩托车车架所承受的主要载荷包括动力载荷、重力载荷和操纵载荷。
动力载荷是指由引擎产生的力,通过车架传递到地面。
重力载荷是指车辆自身的重量以及乘员和物品的重量。
操纵载荷是指由车辆操纵部件(如转向柄和脚蹬)施加在车架上的力。
在设计车架时,必须充分考虑这些载荷的合力,以确保车架的强度和稳定性。
在进行载荷分析时,需要进行静态分析和动态分析。
静态分析是指在静止状态下对车架的载荷进行分析,可以通过有限元分析等计算方法来评估应力和变形。
动态分析则是对车架在不同车速、不同路况和不同操纵情况下的载荷进行分析,以确定其固有频率和振动模态。
这些分析有助于优化车架的设计,减少应力集中和振动问题。
在合理设计摩托车车架时,有几个关键因素需要注意。
首先,车架的主要结构材料应具备足够的强度和刚度,以抵抗各种载荷,并保持车架的稳定性。
常用的车架材料包括高强度钢、铝合金和碳纤维复合材料。
在选择材料时,需要平衡强度、刚度和重量等因素。
其次,车架的结构设计应合理分布载荷,避免应力集中和疲劳破坏。
通常采用一些结构加强措施,如加强筋、横梁和吊挂等,来增加车架的强度和刚度。
此外,应使用适当的连接件和焊接工艺,确保车架连接牢固、无松动,并能承受各种力的作用。
另外,车架的几何形状也对其载荷分析和设计起着重要作用。
车架的各个部位应能够合理分担载荷,并在发动机、悬挂系统和车轮之间提供充足的空间。
此外,优化车架的重心位置,使得重力载荷能够均匀分布,并有助于提高摩托车的稳定性和操控性。
最后,为了确保摩托车车架的可靠性和安全性,还需要进行严格的试验和验证。
例如,通过静载试验和动态载荷试验,可以验证车架在预定载荷下的性能和寿命。
自卸车卸载工况下副车架的受力分析

16 3
文章 编 号 :0 13 9 ( 00 0 — 16 0 10 — 9 7 2 1 )6 0 3— 2
Ma h n r De in c ie y sg
&
Ma u a t r n fc u e
第 6期 21 0 0年 6月
自卸车垂 载 『 工况下副车 7 架的受力分析
=r i M =P。 A・ O s 帆 =mw 。 g X
得到 : P
n g
, 、 J/ =
O 、 n+ A= /2 62 n 0= rtn ) 1 a a( c
个关键工况, 此时副车架的受力非常复杂 。本文 以某企业生产的 自 卸车为例 , 对此工况进行研究找 出此工况下 自卸车副车架易发 生应力集中的部位 , 自卸车的设计制造有一定的指导意义。 对
图 1举升机构受力图
22 .举升机构受力分析
油缸举升力应保证最大举升质量 时所需 的举升力矩。 考虑到
6
le u d n nai ni n y nyn d au i e uptc’mcai oeo t i n r ld g odi az g n cl n t m uks e n amdlnh d e o u o n c t b al i a c  ̄ gh d o l r h c l e
【 要】 摘 通过对某 厂生产的自 卸车卸载工况力学 模型的分 析计算, 得出了自  ̄ 卸-副车架 载工 i - 在卸
;况下所受的各个关键力的数值; 利用有限元软件对该自 卸车副车架的模型进行了静i分析, 态 - 找出了 在卸 {
l载工 况下, 卸车副 该自 车架易 应力集中 发生 的部位, 该车的 为 进一步改 进提供了 依据。
汽车车架的静态强度分析

汽车车架的静态强度分析汽车车架静态强度分析的目的是确定车架在不同负载下的应力和变形情况,从而判断车架是否能够承受正常工作条件下所受到的力和压力,并且保持结构的稳定性。
这需要进行力学计算和数值模拟,通过建立数学模型和采用适当的分析方法,来模拟和预测车架在不同工况下的受力情况。
在汽车车架的静态强度分析中,一般需要考虑以下几个方面:1.车架材料的选取:合理选择车架材料对保证车架的强度和轻量化具有重要影响。
常用的车架材料包括高强度钢、铝合金和碳纤维等。
根据车架的设计要求和使用环境的特点,选择合适的材料进行分析和计算。
2.车架的边界条件:在进行车架强度分析时,需要确定车架的边界条件,包括支撑结构、连接方式和外部负载等。
这些边界条件将直接影响到车架的受力情况和变形情况。
3.车架的结构设计:车架的结构设计是保证车架强度和刚度的关键。
合理的结构设计可以减小车架的重量,提高其强度和刚度。
在设计过程中需要考虑各个部件的布局、横截面形状和连接方式等因素,以满足设计要求。
4.车架的强度计算和模拟分析:在进行车架强度计算时,需要采用适当的力学理论和分析方法,例如有限元分析等。
通过对车架进行力学计算和数值模拟,可以得到车架的应力和变形情况,从而评估车架的强度和稳定性。
在进行汽车车架的静态强度分析时,还需要考虑不同工况下的负载情况。
例如,正常行驶时车辆的自重负载、车辆悬挂系统的负载和车轮悬挂加载等。
通过综合考虑这些因素,可以得到车架在不同工况下的强度和稳定性,并对设计进行优化。
总之,汽车车架的静态强度分析是保证车辆运行安全的重要环节。
通过对车架材料、边界条件、结构设计和负载情况等方面的分析和计算,可以评估车架的强度、刚度和稳定性,并为车架的优化设计提供指导。
汽车车架的静态强度分析
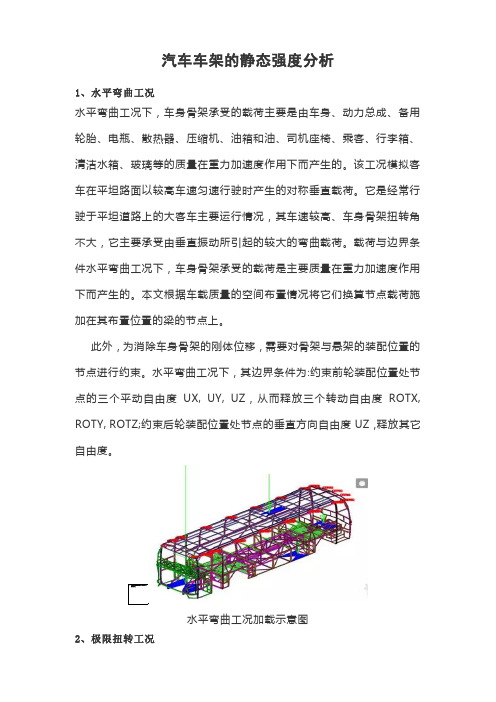
汽车车架的静态强度分析1、水平弯曲工况水平弯曲工况下,车身骨架承受的载荷主要是由车身、动力总成、备用轮胎、电瓶、散热器、压缩机、油箱和油、司机座椅、乘客、行李箱、清洁水箱、玻璃等的质量在重力加速度作用下而产生的。
该工况模拟客车在平坦路面以较高车速匀速行驶时产生的对称垂直载荷。
它是经常行驶于平坦道路上的大客车主要运行情况,其车速较高、车身骨架扭转角不大,它主要承受由垂直振动所引起的较大的弯曲载荷。
载荷与边界条件水平弯曲工况下,车身骨架承受的载荷是主要质量在重力加速度作用下而产生的。
本文根据车载质量的空间布置情况将它们换算节点载荷施加在其布置位置的梁的节点上。
此外,为消除车身骨架的刚体位移,需要对骨架与悬架的装配位置的节点进行约束。
水平弯曲工况下,其边界条件为:约束前轮装配位置处节点的三个平动自由度UX, UY, UZ,从而释放三个转动自由度ROTX, ROTY, ROTZ;约束后轮装配位置处节点的垂直方向自由度UZ,释放其它自由度。
水平弯曲工况加载示意图2、极限扭转工况整车满载水平放置,后两轮固定,前轴间加一极限扭矩(前轴负荷的一半乘以轮距),相当于客车单轮悬空的极限受力情况,模拟客车在崎岖不平的道路上低速行驶时产生的斜对称垂直载荷。
极限扭矩计算公式:T =P x L/2,其中T表示计算扭矩、p表示前桥悬挂负荷、L表示前轮轮距。
扭转工况下的动载,在时间上变化得很缓慢,所以惯性载荷也很小,因此,车身的扭转特性也可以近似地看作是静态的,而试验结果也证实了这一点,静态扭转试验和动载试验所测得的骨架的薄弱部位一致。
即静态扭转时骨架上的大应力点,就可以用来判定动载时的大应力点。
载荷与边界条件由于路面不平度的作用,汽车需要模拟两前轮之一悬空时,车身骨架静态极限扭转时承受的应力分布情况,这种情况下车身骨架的载荷同满载水平弯曲工况一样。
边界条件为:约束左(右)前轮装配位置处节点的三个平动自由度UX, UY, UZ,释放三个转动自由度ROTX, ROTY, ROTZ;释放右(左)前轮装配位置处节点的所有自由度;约束后轮装配位置处节点的垂直方向自由度UZ,释放其它所有自由度。
汽车底盘车架受力分析与优化设计

汽车底盘车架受力分析与优化设计汽车底盘车架是汽车的支撑结构,承担着整个车辆的重量以及各种动力和悬挂装置的载荷。
在日常使用过程中,车架需要承受来自道路不平整、悬挂系统振动以及车辆加速、制动等多方面的受力。
因此,对于汽车底盘车架的受力分析和优化设计至关重要。
汽车底盘车架主要承载车身和发动机,同时还需要提供稳定的悬挂点和安全的乘坐环境。
为了确保车架能够承受各种受力情况下的安全运行,需要对车架进行受力分析。
受力分析的目的是确定各个关键部位的受力情况,以及评估车架是否具备足够的强度和刚度来应对这些受力。
在受力分析过程中,常用的方法包括有限元分析和应力分析。
有限元分析是一种数值计算方法,通过将复杂的结构划分成许多小的单元来近似求解结构的受力情况。
应力分析则是通过应力公式计算各个部位的受力情况。
这些分析方法可以帮助工程师确定车架的强度、刚度和耐久性,并根据分析结果进行优化设计。
在现代汽车设计中,轻量化和刚度是主要的设计目标之一。
轻量化可以减少车辆的自重,提高燃油经济性和动力性能,而刚度则可以提高悬挂系统的稳定性和操控性能。
因此,在进行车架优化设计时,需要平衡车架的强度和重量,并确保刚度满足要求。
为了实现优化设计,可以采用多种方法。
一种常用的方法是结构拓扑优化,通过重构车架的材料分布和连接方式来减少重量并增加刚度。
另一种方法是材料优化,选择优质的车架材料来提高强度和刚度。
此外,还可以通过优化悬挂系统和车轮布局来减小车架的受力情况。
在进行优化设计之前,需要对车架的受力情况进行详细的分析。
首先,需要确定车辆的使用环境和工况,包括道路状况、车辆负载、行驶速度等。
然后,在这些工况下,进行静态和动态的受力分析,确定各个关键部位的受力情况。
最后,根据分析结果进行优化设计,改善车架的受力分布和刚度。
总之,汽车底盘车架的受力分析与优化设计是保证车辆安全、稳定和可靠运行的重要环节。
通过采用先进的受力分析方法和优化设计策略,可以最大限度地提高车架的强度和刚度,并实现轻量化的目标。
车架受力分析
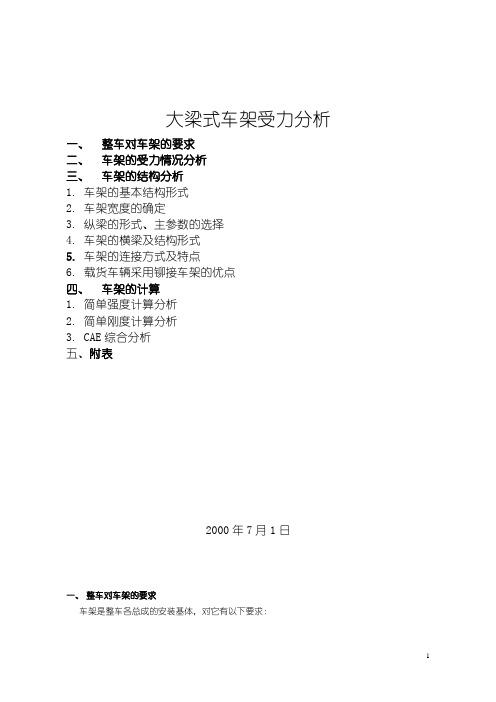
大梁式车架受力分析一、整车对车架的要求二、车架的受力情况分析三、车架的结构分析1.车架的基本结构形式2.车架宽度的确定3.纵梁的形式、主参数的选择4.车架的横梁及结构形式5.车架的连接方式及特点6.载货车辆采用铆接车架的优点四、车架的计算1.简单强度计算分析2.简单刚度计算分析3.CAE综合分析五、附表2000年7月1日一、整车对车架的要求车架是整车各总成的安装基体,对它有以下要求:1.有足够的强度。
要求受复杂的各种载荷而不破坏。
要有足够的疲劳强度,在大修里程内不发生疲劳破坏。
2.要有足够的弯曲刚度。
保证整车在复杂的受力条件下,固定在车架上的各总成不会因车架的变形而早期损坏或失去正常工作能力。
3.要有足够的扭转刚度。
当汽车行使在不平的路面上时,为了保证汽车对路面不平度的适应性,提高汽车的平顺性和通过能力,要求车架具有合适的扭转刚度。
对载货汽车,具体要求如下:3.1车架前端到驾驶室后围这一段车架的扭转刚度较高,因为这一段装有前悬架和方向机,如刚度弱而使车架产生扭转变形,势必会影响转向几何特性而导致操纵稳定性变坏。
对独立悬架的车型这一点很重要。
3.2包括后悬架在内的车架后部一段的扭转刚度也应较高,防止由于车架产生变形而影响轴转向,侧倾稳定性等。
3.3驾驶室后围到驾驶室前吊耳以前部分车架的刚度应低一些,前后的刚度较高,而大部分的变形都集中在车架中部,还可防止因应力集中而造成局部损坏现象。
4.尽量减轻质量,按等强度要求设计。
二、车架的受力情况分析1.垂直静载荷:车身、车架的自重、装在车架上个总成的载重和有效载荷(乘员和货物),该载荷使车架产生弯曲变形。
2.对称垂直动载荷:车辆在水平道路上高速行使时产生,其值取决于垂直静载荷和加速度,使车架产生弯曲变形。
3.斜对称动载荷在不平道路上行使时产生的。
前后车轮不在同一平面上,车架和车身一起歪斜,使车架发生扭转变形。
其大小与道路情况,车身、车架及车架的刚度有关。
4.其它载荷4.1汽车加速和减速时,轴荷重新分配引起垂直载荷。
- 1、下载文档前请自行甄别文档内容的完整性,平台不提供额外的编辑、内容补充、找答案等附加服务。
- 2、"仅部分预览"的文档,不可在线预览部分如存在完整性等问题,可反馈申请退款(可完整预览的文档不适用该条件!)。
- 3、如文档侵犯您的权益,请联系客服反馈,我们会尽快为您处理(人工客服工作时间:9:00-18:30)。
车架受力分析基础一、对车架整车的受力要求二、车架的受力情况具体分析三、车架的结构分析1.车架的基本结构形式2.车架宽度的确定3.纵梁的形式、主参数的选择4.车架的横梁及结构形式5.车架的连接方式及特点6.载货车辆采用铆接车架的优点四、车架的计算1.简单强度计算分析2.简单刚度计算分析3.CAE综合分析五、附表2000年7月1日一、整车对车架的要求车架是整车各总成的安装基体,对它有以下要求:1.有足够的强度。
要求受复杂的各种载荷而不破坏。
要有足够的疲劳强度,在大修里程内不发生疲劳破坏。
2.要有足够的弯曲刚度。
保证整车在复杂的受力条件下,固定在车架上的各总成不会因车架的变形而早期损坏或失去正常工作能力。
3.要有足够的扭转刚度。
当汽车行使在不平的路面上时,为了保证汽车对路面不平度的适应性,提高汽车的平顺性和通过能力,要求车架具有合适的扭转刚度。
对载货汽车,具体要求如下:3.1车架前端到驾驶室后围这一段车架的扭转刚度较高,因为这一段装有前悬架和方向机,如刚度弱而使车架产生扭转变形,势必会影响转向几何特性而导致操纵稳定性变坏。
对独立悬架的车型这一点很重要。
3.2包括后悬架在内的车架后部一段的扭转刚度也应较高,防止由于车架产生变形而影响轴转向,侧倾稳定性等。
3.3驾驶室后围到驾驶室前吊耳以前部分车架的刚度应低一些,前后的刚度较高,而大部分的变形都集中在车架中部,还可防止因应力集中而造成局部损坏现象。
4.尽量减轻质量,按等强度要求设计。
二、车架的受力情况分析1.垂直静载荷:车身、车架的自重、装在车架上个总成的载重和有效载荷(乘员和货物),该载荷使车架产生弯曲变形。
2.对称垂直动载荷:车辆在水平道路上高速行使时产生,其值取决于垂直静载荷和加速度,使车架产生弯曲变形。
3.斜对称动载荷在不平道路上行使时产生的。
前后车轮不在同一平面上,车架和车身一起歪斜,使车架发生扭转变形。
其大小与道路情况,车身、车架及车架的刚度有关。
4.其它载荷4.1汽车加速和减速时,轴荷重新分配引起垂直载荷。
4.2汽车转弯时产生的侧向力。
4.3一前轮撞在凸包上,车架水平方向上产生箭切变形。
4.4装在车架上总成(方向机、发动机、减振器)产生的作用反力。
4.5载荷作用线不通过纵梁的弯曲中心(油箱、悬架)而使纵梁产生局部受扭。
因此车架的受力是一复杂的空间力系,纵梁和横梁截面形状和连接的多变多样,使车架的受载更复杂化。
车架CAE分析时一轮悬空这种极限工况,即解除一个车轮的约束,分析车架弯扭组合情况下的最大应力。
普通载货汽车车架的弯矩图如下:三、车架的结构分析1.车架的基本结构形式边梁式(载货车、大客车常用结构)框式周边式(复杂的边梁式,越野车、轿车常用)车架 X型式(X型横梁,抗扭性能强)脊梁式(抗扭性能好)综合式(前后框式、中间脊梁式)目前公司各种车架基本都是边梁式车架。
2.车架宽度的确定车架的宽度主要由前后轮距确定的,确定车架的宽度按以下原则进行:①车架前部宽度主要考虑前轮的最大转角,选用成型的方向机要考虑方向机的安装,有时结合驾驶室的安装统一考虑。
②车架中部的宽度要考虑发动机及发动机附件(排气管、变速操纵杆)的安装。
③为考虑高速车的稳定性,希望增加车架后部宽度,以便能加大后簧托距。
如BJ1027A和CA1026的托距都很大。
④对双胎车,车架后部宽度取决于轮胎、板簧、车架三者的间隙。
⑤从简化工艺的角度看,最好做成前后等宽,对低价位的产品,这一点很重要。
⑥考虑标准的要求,我国汽车专业标准规定中型载货车边梁式车架的宽度为864±5mm。
典型结构:①轿车、微型车和单胎轻型车车架做成窄后宽结构,前部窄是为了增大前轮转角。
从发动机安装处开始加宽。
②双胎载货车,做成前宽后窄结构。
如1028非独立悬架的都市小卡和NPR。
1049(NKR55LL)是以上两种车架的综合,前部宽度630、中部740、后部700。
NHR单胎车型前部宽度630,中部中部740、后部800。
3.纵梁的型式、主参数的选择3.1纵梁的型式纵梁主要有以下五种形式:槽型薄壁断面、闭口薄闭断面、Z字型断面、工字型断面等。
其中重型载货汽车和超重型载货汽车采用工字型结构截面的型材,Z字型断面不常用。
在此主要讨论前面两种结构形式的纵梁断面。
两种结构(相同的断面面积)的优缺点如下:3.2纵梁主参数的选择3.2.1要满足强度和刚度需要,具体从以下三个方面考虑:①根据轴距对车架刚度的初步验算;②同类车型的类比分析,具体见附表(一)。
③初步的强度计算。
3.2.2要考虑规划中产品对车架断面的要求,满足产品系列化对车架纵梁强度和刚度的要求。
3.2.3车架纵梁要尽量简单,减少断面急剧过度及弯曲,减少应力集中。
3.2.4通过CAE分析,最终确定车架强度和加强板的形状和结构形式。
对槽型梁结构,要注意纵梁高宽比的确定,通常范围为 2.8—3.5之间,例如1029车架为170/55=3.09比较合适。
1046E6为195/55=3.54,宽度偏小。
4.车架的横梁及结构形式车架横梁将左、右纵梁连接起来,构成一个框架,使车架有足够的扭转刚度。
汽车的主要总成也靠横梁支撑。
具体的确定的原则如下:4.1要确保车架前部的扭转刚度。
对独立悬架车型,更要注意。
4.2板簧支架和吊耳处尽量设置横梁,以降低纵梁的应力和变形。
后板簧前后支架处力和转距很大,一般设置一根抗扭刚度大,连接宽度的横梁。
4.3发动机部位,尽量设计简易的横梁,减少纵梁变形。
4.4合理设计横梁与纵梁的连接方式及结构,4.4.1横梁和纵梁的腹板连接,工艺简单,连接刚性差,但不会使纵梁出现大的应力,车架中部采用这种连接。
4.4.2横梁与纵梁腹板及翼面(上或下)相连接。
工艺并不复杂,应用广泛。
但后板簧托架的力会通过纵梁传递给横梁,因此要减少板簧托架的悬伸长度,使载荷点尽量靠近纵梁弯曲中心。
当偏心载荷较大时,可将纵梁做成局部封口,或将横梁穿过纵梁,将载荷直接传递给横梁。
4.4.3横梁与纵梁上下翼面相连接。
由于有刚性很好的角支撑,可产生良好的斜支撑作用,使整个车架刚度增加,翼面外边不会因受压而产生翘曲。
车架两端的横梁采用这种方式和纵梁连接。
由于翼面不能自由翘曲,但转距过大时,纵梁翼面会出现应力过大现象。
4.4.4对受力较大的结构附件,要注意其与车架纵梁的连接方式,避免因纵梁局部应力过大造成纵梁开裂。
注意减振器支架、驾驶室支架、板簧支架、发动机支架的设计。
5.车架的连接方式和特点车架的连接方式有铆接、焊接和螺栓连接三种:5.1铆接车架:铆接成本低,适合于大批量生产,其刚度与铆钉的数量极其分布有关,因此铆钉布置设计很重要。
5.2焊接车架:焊接车架能使其连接牢固,不致产生松动,能保证有大的刚度。
但焊接容易产生较大的变形和内应力,因此对焊接的质量要求很高。
适用于小批量生产和修理。
5.3螺栓连接:特殊使用条件和特殊用途的车架采用。
但长期使用,容易产生松动,易发生严重的质量事故。
一般汽车的纵梁和横梁的连接不采用这种方式。
无论是焊接车架,还是铆接车架,紧固件的数量和尺寸应和横梁的大小相适应,铆钉分布不要太近。
当利用连接板的翻边紧固时,应加大连接板的宽度和厚度,紧固孔应靠近翻边处,防止连接损坏。
6.载货车辆采用铆接车架的优点对于车速较高(≥100km/h)和总质量大于3500kg的轻型汽车,建议采用铆接车架,优点如下:6.1车速高,为确保高速行驶的稳定性,必须提高车架精度,因此优先采用铆接车架。
皮卡、部分越野车、微型货车车架一般采用焊接工艺(纵梁是薄壁闭口断面)。
是受以下几个特殊因素影响而决定的:①这部分车型使用中超载不多。
②断面较小,最大断面高在130毫米以下,采用铆接时铆钳空间不够充裕。
③前两类产品的批量不大,如采用铆接投入较大。
6.2矩管焊接车架的缺点虽部分小型货车和越野车采用矩管车架,有以下缺点:6.2.1矩形管弯曲后回弹大,影响了整车高度方向的基准。
焊接后车架本身的尺寸精度不高。
6.2.2矩形管纵梁,同样抗弯模量前提下,成本高。
原2310-II车架(100X50X5)170.6公斤重,成本1100元,改成1022EZC2A冲压车架(150X50X4),总成131公斤,成本830元,成本降低,抗弯模量大幅度增加。
6.2.3不利于总布置。
线路、管路、附件的固定不好处理。
6.3 焊接车架焊接变形大1022EZC2A车架为冲压焊接车架,焊接变形大,长期以来达不到设计要求,只好办理偏差许可,具体数据见附表(二)。
6.4焊接车架不可避免有焊接缺陷对焊接工艺,容易出现过烧、假焊、咬边等焊接缺陷,由于焊接缺陷的存在,车架出现质量问题的机会增多。
6.5 对卡车行业,铆接车架是主流国内轻型车行业中,除了北轻汽受工艺条件的限制以外,基本都是铆接车架。
北轻汽的主导产品BJ1041和BJ1061为焊接车架,BJ1041严格说来是一种“轻抛车型”,后悬架为渐变刚度簧,无副簧,整车承载能力弱,销售区域也基本在北方。
焊接车架不是轻卡车架的主流。
6.6公司即将有铆接工艺为生产BJ1049轻卡的车架,公司正在上是铆接线,为进一步分摊铆接线的投入,新设计的车架应优先考虑采用铆接工艺。
四、车架计算1.简单强度计算附表附表(一)怀柔车辆厂1022EZC2A车架尺寸实际精度。