史上最全的反应器结构及工作原理图解!
反应器(化工设备操作维护课件)
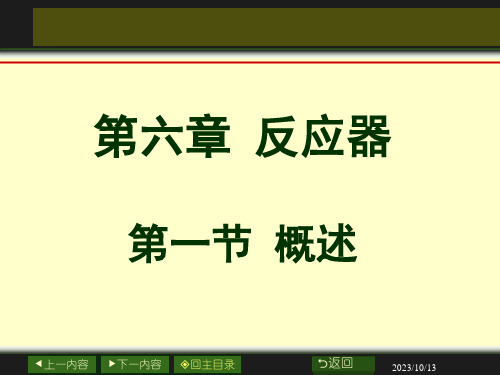
上一内容 下一内容 回主目录
2023/10/13
表 釜式反应器常见故障与处理方法
故障 搅拌轴转数降 低或停止转动
搪瓷搅拌器脱 落 出料不畅
产生原因 皮带打滑 皮带损坏 电机故障 被介质腐蚀
出料管堵塞 压料管损坏
处理方法
调整皮带 更换皮带 修理或更换电机 更换搪瓷轴或修 补 清理出料管 修理或更换配管
2、特点:反应过程伴有传热、传质和反应物的流动过程。 物理与化学过程相互渗透影响,反应过程复杂化。
上一内容 下一内容 回主目录
2023/10/13
§1-2 反应器的类型
• 反应器的类型: 釜式反应器 管式反应器
操作方式 材料 操作压力 绝热管式
换热管式
上一内容 下一内容 回主目录
2023/10/13
2023/10/13
b. 机械密封
机械密封 结构较复 杂,但密 封效果甚 佳。
上一内容 下一内容 回主目录
2023/10/13
4、换热装置
换热装置是用来加热或冷却反应物料,使之符合工艺 要求的温度条件的设备。
其结构型式主要有夹套式、蛇管式、列管式、外部循 环式等,也可用回流冷凝式、直接火焰或电感加热。
上一内容 下一内容 回主目录
2023/10/13
第六章 反应器
第二节 釜式反应器
上一内容 下一内容 回主目录
2023/10/13
§2-1 反应釜基本结构
(一)基本结构:
壳体 密封装置 换热装置 传动装置
上一内容 下一内容 回主目录
2023/10/13
1、搅拌釜式反应器的壳体结构
壳体结构:一般为碳钢材 料,筒体皆为圆筒型。釜 式反应器壳体部分的结构 包括筒体、底、盖(或称 封头)、手孔或人孔、视 镜、安全装置及各种工艺 接管口等。
管式反应器的结构及其应运演示幻灯片

图3.9 带接管的T形透镜环
2020/4/13
14
管式反应器的结构
四,管件 反应器的连接必须按规定的紧固力矩进行。所以对
法兰、螺柱和螺母都有一定要求。
五,机架 反应器机架用桥梁钢焊接成整体。地脚螺栓安放在
基础桩的柱头上,安装管子支架部位装有托架。管子用抱 箍与托架固定。
2020/4/13
15
管式法生产高压聚乙烯
管式反应器长径此为10000-100000。乙烯在管中流速为8-30m/s, 停留时间为0.5至数分钟。以空气、氧气或有机过氧化物为引发剂 (催化剂)。聚合反应产生的热量可使最高温度达到330'C,经反应器 冷却段冷后再添加引发剂聚合。在反复放热一冷却后,抽出反应产 物在高压分离器中分离出聚合物和未反应的乙烯。聚合物经后处理 即成产品。目前,乙烯单程转化率已从初期的8-15%提高到24-30%。 当采用25.4mm反应管径时,生产能力可以达到10-20kt/a。
管式反应器的结构及其应运
2
1
管式反应器
管式反应器是一种呈管状、长径比很 大可连续操作的由多根细管串联或并 联而构成的一种反应器。是一种适用 于气体和液体、液体和液体的反应的 设备,还可用于腐蚀性物料的稀释。2020/4/13源自2管式反应器的特点
1 由于反应物的分子在反应器内停留时间相等,所以在反应器内任 何一点上的反应物浓度和化学反应速度都不随时间而变化,只随 管长变化。
2020/4/13
18
管式法生产高压聚乙烯
至今为止,各种管式法工艺的基本流程大体上与上述 工艺相同。然而,由于采用了不同的聚合反应器的进料点, 分子量调节剂、引发剂及其不同的注入部泣,以及由于助 剂注入方法、产品的处理、返回乙烯的量和送出部位的不 同,也就形成了各种不同特点的工艺。
【最强汇总】13种厌氧反应器原理与结构

【最强汇总】13种厌氧反应器原理与结构厌氧微生物处理是目前高浓度有机废水处理工艺中不可或缺的处理工段,它较好氧微生物处理不仅能耗低,同时还可以产生沼气作为能源二次利用。
厌氧反应容积负荷高较好氧反应高出很多,对于处理同等量的COD厌氧反应投资更低。
最强汇总!13种厌氧生物反应器原理与结构图!目前常用的厌氧处理工艺有:UASB、EGSB、CSTR、IC、ABR、UBF等。
其他厌氧处理工艺有:AF、AFBR、USSB、AAFEB、USR、FPR、两相厌氧反应器等。
升流式厌氧污泥床反应器(Up-flow Anaerobic Sludge Bed/Blanket,简称UASB),是一种处理污水的厌氧生物方法,又叫升流式厌氧污泥床。
UASB由污泥反应区、气液固三相分离器(包括沉淀区)和气室三部分组成。
在底部反应区内存留大量厌氧污泥,具有良好的沉淀性能和凝聚性能的污泥在下部形成污泥层。
要处理的污水从厌氧污泥床底部流入与污泥层中污泥进行混合接触,污泥中的微生物分解污水中的有机物,把它转化为沼气。
沼气以微小气泡形式不断放出,微小气泡在上升过程中,不断合并,逐渐形成较大的气泡,在污泥床上部由于沼气的搅动形成一个污泥浓度较稀薄的污泥和水一起上升进入三相分离器,沼气碰到分离器下部的反射板时,折向反射板的四周,然后穿过水层进入气室,集中在气室沼气,用导管导出,固液混合液经过反射进入三相分离器的沉淀区,污水中的污泥发生絮凝,颗粒逐渐增大,并在重力作用下沉降。
沉淀至斜壁上的污泥沿着斜壁滑回厌氧反应区内,使反应区内积累大量的污泥,与污泥分离后的处理出水从沉淀区溢流堰上部溢出,然后排出污泥床。
结构形式见图1:最强汇总!13种厌氧生物反应器原理与结构图!膨胀颗粒污泥床(Expanded Granular Sludge Blanket Reactor,简称EGSB),是第三代厌氧反应器。
其构造与UASB反应器有相似之处,可以分为进水配水系统、反应区、三相分离区和出水渠系统。
反应釜知识大全

对于高粘度液体,就选用大直径、低转速搅拌器,如锚式、框式和桨式。
2、按搅拌目的选型
对低粘度均相液体混合,主要考虑循环流量,各种搅拌器的循环流量按从大到小顺序排列:推进式、涡轮式、桨式。
对于非均相液-液分散过程,首先考虑剪切作用,同时要求有较大的循环流量,各种搅拌器的剪切作用按从大到小的顺序排列:涡轮式、推进式、桨式。
5碳钢反应釜
适用于不含腐蚀性液体的环境,比如某些油品的加工。
6不锈钢反应釜
具有优良的机械性能,可承受较高的工作压力,也可承受块状固体物料中料时的冲击。
耐热性能好,工作温度范围广(-196—600℃),在较高温度下不会氧气起皮,可用于直接明火加热。
具有较高的耐磨腐蚀性能。
传热效果好,升温和降温速度快。
4电加热反应釜
将电阻丝缠绕在反应釜筒体的绝缘层上,或安装在离反应釜若干距离的特设绝缘体上,便可用电来加热反应。前三种方法获得高温均需在釜体上增设夹套,由于温度变化的幅度大,使釜的夹套及壳体承受温度变化而产生温差压力。
采用电加热时,设备较轻便简单,温度较易调节,而且不用泵、炉子、烟囱等设施,开动也非常简单,危险性不高,成本费用较低,但操作费用较其它加热方法高,热效率在85%以下,因此适用于加热温度在400℃以下和电能价格较低的地方。
2蒸汽加热反应釜
加热温度在100℃以下时,可用一个大气压以下的蒸汽来加热;当加热范围是100-180℃时,用饱和蒸汽;当温度更高时,可采用高压过热蒸汽。
3其他介质加热的反应釜
若工艺要求必须在高温下操作,或欲避免采用高压的加热系统时,可用其它介质来代替水和蒸汽,如矿物油(275-300℃)、联苯醚混合剂(沸点258℃)、熔盐(140-540℃)、液态铅(熔点327℃)等。
反应器结构及工作原理现用图解

反响器构造及工作原理图解小7:这里给大家介绍一下常用的反响器设备,主要有以下类型:①管式反响器。
由长径比较大的空管或填充管构成,可用于实现气相反响和液相反响。
②釜式反响器。
由长径比较小的圆筒形容器构成,常装有机械搅拌或气流搅拌装置,可用于液相单相反响过程和液液相、气液相、气液固相等多相反响过程。
用于气液相反响过程的称为鼓泡搅拌釜〔见鼓泡反响器〕;用于气液固相反响过程的称为搅拌釜式浆态反响器。
③有固体颗粒床层的反响器。
气体或(和)液体通过固定的或运动的固体颗粒床层以实现多相反响过程,包括固定床反响器、流化床反响器、移动床反响器、涓流床反响器等。
④塔式反响器。
用于实现气液相或液液相反响过程的塔式设备,包括填充塔、板式塔、鼓泡塔等〔见彩图〕。
一、管式反响器一种呈管状、长径比很大的连续操作反响器。
这种反响器可以很长,如丙烯二聚的反响器管长以公里计。
反响器的构造可以是单管,也可以是多管并联;可以是空管,如管式裂解炉,也可以是在管内填充颗粒状催化剂的填充管,以进展多相催化反响,如列管式固定床反响器。
通常,反响物流处于湍流状态时,空管的长径比大于50;填充段长与粒径之比大于100(气体)或 200〔液体〕,物料的流淌可近似地视为平推流。
分类:1、水平管式反响器由无缝钢管与U 形管连接而成。
这种构造易于加工制造和检修。
高压反响管道的连接承受标准槽对焊钢法兰,可承受1600-10000kPa 压力。
如用透镜面钢法兰,承受压力可达 10000-20230kPa。
2、立管式反响器立管式反响器被应用于液相氨化反响、液相加氢反响、液相氧化反响等工艺中。
3、盘管式反响器将管式反响器做成盘管的形式,设备紧凑,节约空间。
但检修和清刷管道比较困难。
4、U 形管式反响器U 形管式反响器的管内设有多孔挡板或搅拌装置,以强化传热与传质过程。
U 形管的直径大,物料停留时间增长,可应用于反响速率较慢的反响。
5、多管并联管式反响器多管并联构造的管式反响器一般用于气固相反响,例如气相氯化氢和乙炔在多管并联装有固相催化剂的反响器中反响制氯乙烯,气相氮和氢混合物在多管并联装有固相铁催化剂的反响器中合成氨。
13种厌氧生物反应器结构及原理

13种厌氧生物反应器结构及原理厌氧生物反应器是一种用于处理含有机物污染物的废水、垃圾和有机废料的设备。
与常规的好氧生物反应器相比,厌氧生物反应器能够在无氧环境下降解有机废物,产生可再生的能源,如甲烷气体。
下面将介绍13种常见的厌氧生物反应器结构及原理。
1.家庭型生物反应器(家庭式厌氧发酵箱)家庭型生物反应器是一种小型厌氧生物反应器,常用于处理家庭废弃物。
它由一个密封的容器组成,内部含有厌氧微生物,废物在容器内分解产生甲烷气体。
2.填料式反应器(填料式厌氧反应器)填料式反应器是一种常见的厌氧生物反应器。
它由一个圆筒形容器组成,内部填充有一种特殊填料,如陶粒或聚合物。
填料提供了更大的表面积,用于附着厌氧微生物,促进废物的降解。
3.流化床反应器(流化床堆式厌氧反应器)流化床反应器利用流化床的原理进行废物处理。
废物被喷入反应器中,与床层内流动的气体混合并流化,从而实现废物降解和产气。
4.固定床反应器(固定床式厌氧反应器)固定床反应器是一种常见的厌氧生物反应器。
废物通过固定床内的孔隙流动,废物在固定床内降解,产生甲烷气体。
5.上升式床反应器(上升式床式厌氧反应器)上升式床反应器将废物从底部喷入反应器中,废物上升流动与厌氧微生物接触,实现废物的降解。
6.下降式膜池反应器(下降式膜池式厌氧反应器)下降式膜池反应器利用膜池和厌氧微生物来处理废物,膜池可以将固体和液体分离,同时提供厌氧微生物所需的无氧环境。
7.膜生物反应器(膜式厌氧反应器)膜生物反应器使用微孔膜将厌氧微生物和废物分离开。
厌氧微生物在反应器中降解废物,并通过膜分离器收集产生的甲烷气体。
8.微型反应器(微型厌氧生物反应器)微型反应器是一种小型的厌氧生物反应器,用于处理小量的废物。
反应器通常是由微型流道和反应池组成,利用微湍流和微流动加速废物的降解过程。
9.连续流式反应器(连续流式厌氧反应器)连续流式反应器是一种将废物连续供应到反应器中的反应器。
废物通过反应器流动,与厌氧微生物接触,实现废物的降解。
《多相反应及反应器》PPT课件

(4)生成的反应产物R向其浓 度梯度下降的方向扩散。
由于B组分不挥发,所以反 应仅在液相中进行。
精选PPT
14
气液反应宏观速率
气固催化反应时,反应速率以单位体积催化剂定义,因 此定态时对于一级不可逆反应有:
NA=kGam(cAG-cAS) =rA=kcAs
MkL2 kL
DAL kL
kkD L2AL
气液反应用于气体净化时,主要考虑是传质速率,用增
大因子来标志由于化学反应的存在而使传质速率增大的
倍数是合适的。
精选PPT
26
气液反应有效因子(液相利用率)
当气液反应的目的是为了制取产品时,所关心的则是 液相中化学反应进行的速率和反应物的转化率,以及 相间传质对液相化学反应速率的影响。为了说明这种 影响,和处理气固相催化反应时所用的方法一样,也 引用有效因子的概念。
化学反应速率大的气液反应,反应在液膜已基本进行完毕,其宏观 反应速率由 kDAl cAi 式决定,此时的速率只与k、DAL和cAi有关。 因此,欲提高宏观反应速率,需从提高反应温度(可使k及DAL增大)、 减小气膜阻力(可使cAi增大)等着手,而增加液相湍动,减小液膜厚 度等,效果是不大的。
化学反应速率慢的气液反应,反应主要在液相主体中进行,此时采 用存液量大的反应器比较有利。如果液相主体中的反应速率己能适 应传递过程的要求(即αM>>1),则一切有利于强化传质的措施, 都会提高整个过程的速率。反之;如果液相主体的反应速率远较传 质速率低(即αM<<1),则应设法改善液相反应条件,方可使整个 过程的速率加快。
如果和M都小,致使M《1时,则β→αM,η→l。
27种反应器的结构及原理(图文并茂),你想了解的都在这里了

27种反应器的结构及原理(图文并茂),你想了解的都在这里了导语化学反应器是化工生产的核心设备,其技术的先进程度对化工生产有着重要的影响,直接影响装置的投资规模和生产成本。
也是化工生产过程的心脏,从原料经过反应器到我们想要的产品。
反应器的类型反应器的类型很多,如果按反应器的工作原理来分,可以概括为以下几种类型:一、管式反应器在化工生产中,连续操作的长径比较大的管式反应器可以近似看成是理想置换流动反应器(平推流反应器,Plug flow reactor,简称PFR)。
它既适用于液相反应,又适用于气相反应。
由于PFR能承受较高的压力,用于加压反应尤为合适。
具有容积小、比表面大、返混少、反应参数连续变化、易于控制的优点,但对于慢速反应,则有需要管子长,压降大的不足。
管式反应器类型1水平管式反应器由无缝钢管与U形管连接而成。
这种结构易于加工制造和检修。
高压反应管道的连接采用标准槽对焊钢法兰,可承受1600-10000kPa 压力。
如用透镜面钢法兰,承受压力可达10000-20000kPa。
2立管式反应器立管式反应器被应用于液相氨化反应、液相加氢反应、液相氧化反应等工艺中。
3盘管式反应器将管式反应器做成盘管的形式,设备紧凑,节省空间。
但检修和清刷管道比较困难。
4U形管式反应器U形管式反应器的管内设有多孔挡板或搅拌装置,以强化传热与传质过程。
U形管的直径大,物料停留时间增长,可应用于反应速率较慢的反应。
5多管并联管式反应器多管并联结构的管式反应器一般用于气固相反应,例如气相氯化氢和乙炔在多管并联装有固相催化剂的反应器中反应制氯乙烯,气相氮和氢混合物在多管并联装有固相铁催化剂的反应器中合成氨。
6活塞流反应器性能特点:① 反应器的长径比较大。
②假设不同时刻进入反应器的物料之间不发生逆向混合(返混)。
③反应物沿管长方向流动,反应时间是管长的函数,其浓度随流动方向从一个截面到另一个截面而变化。
二、釜式反应器釜式反应器也称槽式、锅式反应器,它是各类反应器中结构较为简单且应用较广的一种反应器。
- 1、下载文档前请自行甄别文档内容的完整性,平台不提供额外的编辑、内容补充、找答案等附加服务。
- 2、"仅部分预览"的文档,不可在线预览部分如存在完整性等问题,可反馈申请退款(可完整预览的文档不适用该条件!)。
- 3、如文档侵犯您的权益,请联系客服反馈,我们会尽快为您处理(人工客服工作时间:9:00-18:30)。
史上最全的反应器结构及工作原理图解!这里给大家介绍一下常用的反应器设备,主要有以下类型:①管式反应器。
由长径比较大的空管或填充管构成,可用于实现气相反应和液相反应。
②釜式反应器。
由长径比较小的圆筒形容器构成,常装有机械搅拌或气流搅拌装置,可用于液相单相反应过程和液液相、气液相、气液固相等多相反应过程。
用于气液相反应过程的称为鼓泡搅拌釜(见鼓泡反应器);用于气液固相反应过程的称为搅拌釜式浆态反应器。
③有固体颗粒床层的反应器。
气体或(和)液体通过固定的或运动的固体颗粒床层以实现多相反应过程,包括固定床反应器、流化床反应器、移动床反应器、涓流床反应器等。
④塔式反应器。
用于实现气液相或液液相反应过程的塔式设备,包括填充塔、板式塔、鼓泡塔等(见彩图)。
一、管式反应器一种呈管状、长径比很大的连续操作反应器。
这种反应器可以很长,如丙烯二聚的反应器管长以公里计。
反应器的结构可以是单管,也可以是多管并联;可以是空管,如管式裂解炉,也可以是在管内填充颗粒状催化剂的填充管,以进行多相催化反应,如列管式固定床反应器。
通常,反应物流处于湍流状态时,空管的长径比大于50;填充段长与粒径之比大于100(气体)或200(液体),物料的流动可近似地视为平推流。
分类:1、水平管式反应器由无缝钢管与U形管连接而成。
这种结构易于加工制造和检修。
高压反应管道的连接采用标准槽对焊钢法兰,可承受1600-10000kPa 压力。
如用透镜面钢法兰,承受压力可达10000-20000kPa。
2、立管式反应器立管式反应器被应用于液相氨化反应、液相加氢反应、液相氧化反应等工艺中。
3、盘管式反应器将管式反应器做成盘管的形式,设备紧凑,节省空间。
但检修和清刷管道比较困难。
4、U形管式反应器U形管式反应器的管内设有多孔挡板或搅拌装置,以强化传热与传质过程。
U形管的直径大,物料停留时间增长,可应用于反应速率较慢的反应。
5、多管并联管式反应器多管并联结构的管式反应器一般用于气固相反应,例如气相氯化氢和乙炔在多管并联装有固相催化剂的反应器中反应制氯乙烯,气相氮和氢混合物在多管并联装有固相铁催化剂的反应器中合成氨。
性能特点:1、由于反应物的分子在反应器内停留时间相等,所以在反应器内任何一点上的反应物浓度和化学反应速度都不随时间而变化,只随管长变化。
2、管式反应器具有容积小、比表面大、单位容积的传热面积大,特别适用于热效应较大的反应。
3、由于反应物在管式反应器中反应速度快、流速快,所以它的生产能力高。
4、管式反应器适用于大型化和连续化的化工生产。
5、和釜式反应器相比较,其返混较小,在流速较低的情况下,其管内流体流型接近与理想流体。
6、管式反应器既适用于液相反应,又适用于气相反应。
用于加压反应尤为合适。
此外,管式反应器可实现分段温度控制。
其主要缺点是,反应速率很低时所需管道过长,工业上不易实现。
二、釜式反应器釜式反应器也称槽式、锅式反应器,它是各类反应器中结构较为简单且应用较广的一种。
主要应用于液—液均相反应过程,在气—液、液—液非均相反应过程中也有应用。
在化工生产中,既适用于间歇操作过程,又可单釜或多釜串联用于连续操作过程,但在间歇生产过程应用最多。
1、间歇釜间歇釜式反应器,或称间歇釜。
操作灵活,易于适应不同操作条件和产品品种,适用于小批量、多品种、反应时间较长的产品生产。
间歇釜的缺点是:需有装料和卸料等辅助操作,产品质量也不易稳定。
但有些反应过程,如一些发酵反应和聚合反应,实现连续生产尚有困难,至今还采用间歇釜。
2、连续釜连续釜式反应器,或称连续釜3、釜式搅拌反应器釜式搅拌反应器有立式容器中心搅拌、偏心搅拌、倾斜搅拌,卧式容器搅拌等类型。
其中以立式容器中心搅拌反应器是最典型的一种常用搅拌器及流型示意性能特点:釜式反应器具有适用的温度和压力范围宽、适应性强、操作弹性大、连续操作时温度浓度容易控制、产品质量均一等特点。
但用在较高转化率工艺要求时,需要较大容积。
通常在操作条件比较缓和的情况下操作,如常压、温度较低且低于物料沸点时,应用此类反应器最为普遍。
三、固定床反应器又称填充床反应器,装填有固体催化剂或固体反应物用以实现多相反应过程的一种反应器。
固体物通常呈颗粒状,粒径2~15mm左右,堆积成一定高度(或厚度)的床层。
床层静止不动,流体通过床层进行反应。
它与流化床反应器及移动床反应器的区别在于固体颗粒处于静止状态。
固定床反应器主要用于实现气固相催化反应,如氨合成塔、二氧化硫接触氧化器、烃类蒸汽转化炉等。
用于气固相或液固相非催化反应时,床层则填装固体反应物。
涓流床反应器也可归属于固定床反应器,气、液相并流向下通过床层,呈气液固相接触。
固定床反应器有三种基本形式:1、轴向绝热式固定床反应器流体沿轴向自上而下流经床层,床层同外界无热交换。
2、径向绝热式固定床反应器流体沿径向流过床层,可采用离心流动或向心流动,床层同外界无热交换。
径向反应器与轴向反应器相比,流体流动的距离较短,流道截面积较大,流体的压力降较小。
但径向反应器的结构较轴向反应器复杂。
以上两种形式都属绝热反应器,适用于反应热效应不大,或反应系统能承受绝热条件下由反应热效应引起的温度变化的场合。
3、列管式固定床反应器由多根反应管并联构成。
管内或管间置催化剂,载热体流经管间或管内进行加热或冷却,管径通常在25~50mm之间,管数可多达上万根。
列管式固定床反应器适用于反应热效应较大的反应。
此外,尚有由上述基本形式串联组合而成的反应器,称为多级固定床反应器。
例如:当反应热效应大或需分段控制温度时,可将多个绝热反应器串联成多级绝热式固定床反应器,反应器之间设换热器或补充物料以调节温度,以便在接近于最佳温度条件下操作。
性能特点:优点:1、返混小,流体同催化剂可进行有效接触,当反应伴有串联副反应时可得较高选择性。
2、催化剂机械损耗小。
3、结构简单。
缺点:1、传热差,反应放热量很大时,即使是列管式反应器也可能出现飞温(反应温度失去控制,急剧上升,超过允许范围)。
2、操作过程中催化剂不能更换,催化剂需要频繁再生的反应一般不宜使用,常代之以流化床反应器或移动床反应器。
固定床反应器中的催化剂不限于颗粒状,网状催化剂早已应用于工业上。
目前,蜂窝状、纤维状催化剂也已被广泛使用。
四、流化床反应器流化床反应器是一种利用气体或液体通过颗粒状固体层而使固体颗粒处于悬浮运动状态,并进行气固相反应过程或液固相反应过程的反应器。
在用于气固系统时,又称沸腾床反应器。
流化床反应器在现代工业中的早期应用为20世纪20年代出现的粉煤气化的温克勒炉(见煤气化炉);但现代流化反应技术的开拓,是以40年代石油催化裂化为代表的。
目前,流化床反应器已在化工、石油、冶金、核工业等部门得到广泛应用。
性能特点:与固定床反应器相比,流化床反应器的优点是:1、可以实现固体物料的连续输入和输出;2、流体和颗粒的运动使床层具有良好的传热性能,床层内部温度均匀,而且易于控制,特别适用于强放热反应;3、便于进行催化剂的连续再生和循环操作,适于催化剂失活速率高的过程的进行,石油馏分催化流化床裂化的迅速发展就是这一方面的典型例子。
然而,由于流态化技术的固有特性以及流化过程影响因素的多样性,对于反应器来说,流化床又存在很明显的局限性:1、由于固体颗粒和气泡在连续流动过程中的剧烈循环和搅动,无论气相或固相都存在着相当广的停留时间分布,导致不适当的产品分布,降低了目的产物的收率;2、反应物以气泡形式通过床层,减少了气-固相之间的接触机会,降低了反应转化率;3、由于固体催化剂在流动过程中的剧烈撞击和摩擦,使催化剂加速粉化,加上床层顶部气泡的爆裂和高速运动、大量细粒催化剂的带出,造成明显的催化剂流失;4、床层内的复杂流体力学、传递现象,使过程处于非定常条件下,难以揭示其统一的规律,也难以脱离经验放大、经验操作。
五、移动床反应器一种用以实现气固相反应过程或液固相反应过程的反应器。
在反应器顶部连续加入颗粒状或块状固体反应物或催化剂,随着反应的进行,固体物料逐渐下移,最后自底部连续卸出。
流体则自下而上(或自上而下)通过固体床层,以进行反应。
由于固体颗粒之间基本上没有相对运动,但却有固体颗粒层的下移运动,因此,也可将其看成是一种移动的固定床反应器。
鲁奇炉钢铁工业和城市煤气工业发展之初,移动床反应器就曾被用于煤的气化。
1934年研制成功的移动床加压气化器(鲁奇炉),至今仍是规模最大的煤气化装置,其单台日生产能力已达到1Mm以上。
石油催化裂化发展初期,曾采用移动床反应器,但现已被流化床反应器和提升管反应器所取代。
目前,应用移动床反应器的重要化工生产过程有连续重整、二甲苯异构化等催化反应过程和连续法离子交换水处理过程。
三塔式移动床工艺流程图移动床反应工艺流程性能特点:与固定床反应器及流化床反应器相比,移动床反应器的主要优点是固体和流体的停留时间可以在较大范围内改变,返混较小(与固定床反应器相近),对固体物料性状以中等速度(以小时计)变化的反应过程也能适用。
与此相比,固定床反应器和流化床反应器分别仅适用于固体物料性状变化很慢(以月计)和很快(以分、秒计)的反应过程。
移动床反应器的缺点是控制固体颗粒的均匀下移比较困难。
工业生产中有时采用模拟移动床以避免上述缺点(见固定床传质设备)。
六、涓流床反应器又称滴流床反应器,是气体和液体并流通过颗粒状固体催化剂床层,以进行气液固相反应过程的一种反应器(见图)。
涓流床反应器中催化剂以固定床的形式存在,故这种反应器也可视为固定床反应器的一种。
为了有利于气体在液体中的溶解,涓流床反应器常在加压下操作。
石油炼制中的加氢裂化和加氢脱硫,是应用大型涓流床反应器的工业过程。
涓流床反应器在化工生产中也有应用,但规模较小,例如用于以三氧化钨为催化剂,由丙烯水合制取异丙醇等。
涓流床反应器内的流体流动状况,与填充塔略有不同,气液两相并流向下,不会发生液泛;催化剂微孔内贮存一定量近于静止的液体。
涓流床反应器通常采用多段绝热式,在段间换热或补充物料以调节温度;每段顶部设置分布器使液流均布,以保证催化剂颗粒的充分润湿。
性能特点:与气液固相反应过程常用的浆态反应器相比,涓流床反应器的主要优点是:1、返混小,便于达到较高的转化率;2、液固比低,液相副反应少;3、避免了催比剂细粉的回收问题。
缺点是:温度控制比较困难;催化剂颗粒内表面往往未能充分利用;反应过程中催化剂不能连续排出再生。
七、塔式反应器塔式反应器主要分为以下几种:1、鼓泡塔反应器鼓泡塔反应器广泛应用于液体相也参与反应的中速、慢速反应和放热量大的反应。
例如,各种有机化合物的氧化反应、各种石蜡和芳烃的氯化反应、各种生物化学反应、污水处理曝气氧化和氨水碳化生成固体碳酸氢铵等反应,都采用这种鼓泡塔反应器。