汽车实用英语教材讲义讲稿 汽车基础英语 第3讲 Automotive components(汽车的组成部分)
汽车实用英语教材讲义讲稿 汽车基础英语 第1讲 Car log(车标)
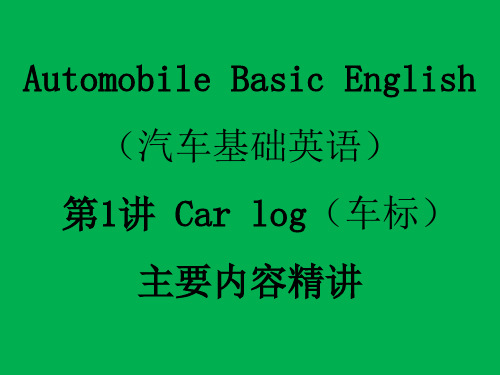
– China
– USA
– Japan
– British – French – Germany – Italy
1.1.3 Logo meaning (车标的含义)
– 车标的含义:“椭圆”:象征地球,表示面向世界、走向国际 化;椭圆在动态中是最稳定的,喻示及祝愿吉利的事业稳如磐 石,在风雨中屹立不倒;“六个六”:象征太阳的光芒,只有 走进太阳,才能吸取无穷的热量,只有经过竞争的洗礼,才能 百炼成钢;六个六,“六六大顺”,祝愿如意、吉祥;六个六 ,吉利一步一个台阶,不断超越,发展无止境;六个六,中华 优秀传统文化的底蕴,是吉利不断发展超越的精神源泉;六个 六,发展民族工业,走向世界,是吉利不舍不弃的追求;“内 圈蔚蓝”:象征广阔的天空,超越无止境,发展无止境;“外 圈深蓝”象征无垠的宇宙,超越无限,空间无限。
从汽车产量来说,汽车联盟是当时德国第二大汽车制造公
司,商品标志为四个连接的圆环,代表参与合并的四家汽 车公司。世界上也就首次出现了四环标志。
– 丰田车标设计的重点是椭圆形组成的左右对称的构成。椭 圆是具有两个中心的曲线,表示汽车制造者与顾客心心相 印。并且,横竖两椭圆组合在一起,表示丰田(Toyota)的 第一个字母T。背后的空间表示Toyota的先进技术在世界 范围内拓展延伸,面向未来,面向宇宙不断飞翔,代表了 公司日益进步的技术水平及无穷的创新机会。
1.1.3 Logo meaning (车标的含义)
1.1.4 Do you know the manufacturers of these cars? (你知道下面几款汽车是属于哪个汽车公司?)
1.1.1 Do you know these car logos? (你知道这些汽车标志吗?)
汽车专业英语unit3
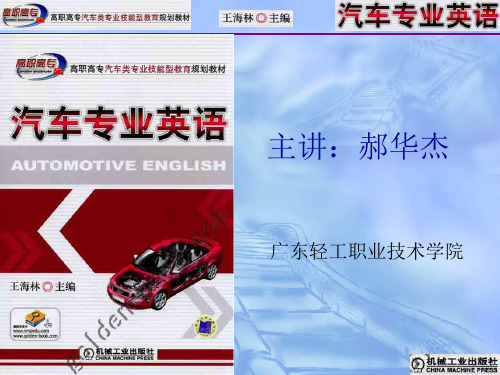
Brake System(制动系)
3.4.1 Brake(制动器)
3.4.2 Parking Brake(驻车制动)
End of Unit3
xxxxxx学校unitchassis底盘31powertrainsystemappliescomponentsneededdrivefromroadwheelsincludingclutchtransmissiondriveshaftuniversaljointdriveaxleaxleshaftgearbox变速器manualtransmissionmt手动变速器automatictransmissiondriveaxle驱动桥finaldrive主减速器universalgearing万向传动装置universaljoint万向节suspension汽车悬架steeringsystem转向系331steeringgear转向器332powersteeringgear动力转向系brakesystem制动系341brake制动器342parkingbrake驻车制
Part 1 Automotive Basics 第1部分 汽车基础
Unit 3 Chassis (底盘)
3.1Power Train System(传动系统)
The power train system applies to the components needed to transfer the drive from the engine to the road wheels, including clutch, transmission, drive shaft, universal joint, drive axle, axle shaft and so on.
汽车专业英语教程多媒体教学课件Unit 3

德国是汽车的发源 地。1886年,卡 尔·本茨和哥德利 普·戴姆勒共享了 发明汽车带来的荣 耀。他们各自建立 了自己的汽车公司, 并于1926年合并组 建为戴姆勒—奔驰 汽车公司。如今, 梅塞德斯一奔驰这 个品牌已经蜚声国 际。而其无可争议 的德国竞争对手是 宝马公司,其公司 起源与其他公司不 同。宝马公司成立 于1916年,以生产 航空发动机开始创 业;1928年,宝马 公司转向生产汽车。
an enviable reputation as the maker of Mercedes-Benz cars . Its undisputed
German competitor is BMW (Bavarian Motor Works),a firm with very different origins . BMW , formed in 1916 , began by producing aero engines.and switched to motor cars in 1928.
investments in auto design and production.Each auto manufacturer has tried
to win the competition on the world
markets and therefore never stopped
making research for new models . Consequently , the world auto industry has been developed very fast.
1956年,第一 汽车制造厂在长 春建成,并生产 出我国第一批解 放牌汽车。在这 之后,其他几个 汽车制造厂相继 在南京、北京、 济南和四川建立。 20世纪80年代初 期,我国自行设 计和装备的第二 汽车制造厂投入 大规模生产。
汽车专业英语全套课件完整版ppt教学教程最新最全

throughout the cylinder area to keep the
水套
engine cool. There is also a drilled
internally
passageway within some blocks for the
内部地
camshaft. Many oil holes are drilled
built within the block. These passageways, coolant 冷却液
also known as water sockets, surround the
oil pan 机油盘
cylinders. They allow coolant to circulate water socket
(气缸体) 2- cylinder
(气缸) 3- crankcase area
(曲轴箱部分)
2. Cylinder Liners
The purpose of using a liner is that, if the cylinder is damaged, the liner can be removed and replaced rather easily. There
liner(发动机)气 缸套
remove 拆下 replace 取代 seal 密封,封条 leak 使渗漏 valve 气门;阀 port 孔管道 exhaust 排气 in addition 另外 intake 进气,吸入 manifold 歧管 spark 火花 plug 塞子 injector 喷油器 install 安装
consists of piston, compression rings, oil control rings, piston pin and connecting rod.(1)piston: Piston fits
汽车英文文献讲课讲稿
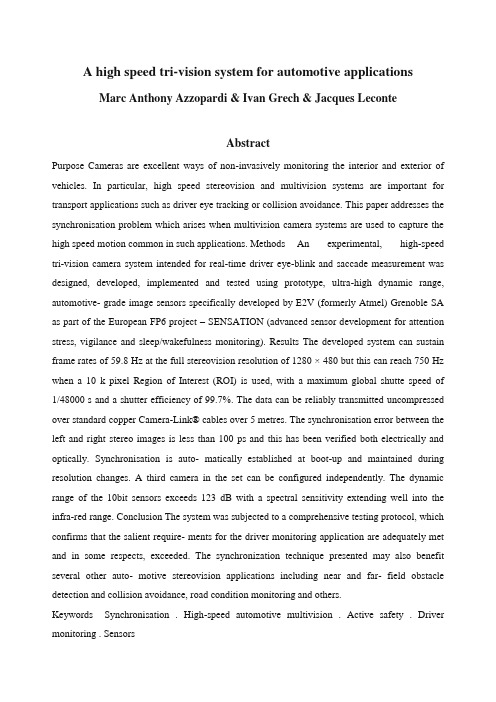
A high speed tri-vision system for automotive applicationsMarc Anthony Azzopardi & Ivan Grech & Jacques LeconteAbstractPurpose Cameras are excellent ways of non-invasively monitoring the interior and exterior of vehicles. In particular, high speed stereovision and multivision systems are important for transport applications such as driver eye tracking or collision avoidance. This paper addresses the synchronisation problem which arises when multivision camera systems are used to capture the high speed motion common in such applications. Methods An experimental, high-speed tri-vision camera system intended for real-time driver eye-blink and saccade measurement was designed, developed, implemented and tested using prototype, ultra-high dynamic range, automotive- grade image sensors specifically developed by E2V (formerly Atmel) Grenoble SA as part of the European FP6 project – SENSATION (advanced sensor development for attention stress, vigilance and sleep/wakefulness monitoring). Results The developed system can sustain frame rates of 59.8 Hz at the full stereovision resolution of 1280 × 480 but this can reach 750 Hz when a 10 k pixel Region of Interest (ROI) is used, with a maximum global shutte speed of 1/48000 s and a shutter efficiency of 99.7%. The data can be reliably transmitted uncompressed over standard copper Camera-Link® cables over 5 metres. The synchronisation error between the left and right stereo images is less than 100 ps and this has been verified both electrically and optically. Synchronisation is auto- matically established at boot-up and maintained during resolution changes. A third camera in the set can be configured independently. The dynamic range of the 10bit sensors exceeds 123 dB with a spectral sensitivity extending well into the infra-red range. Conclusion The system was subjected to a comprehensive testing protocol, which confirms that the salient require- ments for the driver monitoring application are adequately met and in some respects, exceeded. The synchronization technique presented may also benefit several other auto- motive stereovision applications including near and far- field obstacle detection and collision avoidance, road condition monitoring and others.Keywords Synchronisation . High-speed automotive multivision . Active safety . Driver monitoring . Sensors1 IntroductionOver the coming years, one of the areas of greatest research and development potential will be that of automotive sensor systems and telematics [1, 2]. In particular, there is a steeply growing interest in the utilisation of multiple cameras within vehicles to augment vehicle Human-Machine Interfacing (HMI) for safety, comfort and security.For external monitoring applications, cameras are emerging as viable alternatives to systems such Radio, Sound and Light/Laser Detection and Ranging (RADAR, SODAR, LADAR/LIDAR). The latter are typically rather costly and either have poor lateral resolution or require mechanical moving parts.For vehicle cabin applications, cameras outshine other techniques with their ability to collect large amounts of information in a highly unobtrusive way. Moreover, cameras can be used to satisfy several applications at once by re-processing the same vision data in multiple ways, thereby reducing the total number of sensors required to achieve equivalent functionality. However, automotive vision still faces several open challenges in terms of optoelectronic-performance, size, reliability, power con- sumption, sensitivity, multi-camera synchronisation, inter- facing and cost.In this paper, several of these problems are addressed. As an example, driver head localisation, point of gaze detection and eye blink rate measurement is considered for which the design of a dash-board-mountable automotive stereovision camera system is presented. This was developed as part of a large FP6 Integrated Project - SENSATION (Advanced Sensor Development for Attention, Stress, Vigilance and Sleep/Wakefulness Monitoring). The overarching goal of extendable to multivision systems [5–8].The camera system is built around a matched set of prototype, ultra-high dynamic range, automotive-grade, image sensors specifically developed and fabricated by E2V Grenoble SA for this application. The sensor which is a novelty in its own right, is the AT76C410ABA CMOS monochrome automotive image sensor. This sensor imple- ments a global shutter to allow distortion-free capture of fast motion. It also incorporates an on- chip Multi-ROI feature with up to eight Regions Of Interest (ROI) with pre- programming facility and allows fast switching from one image to another. In this way, several real-time parallel imaging processing tasks can be carried out with one sensor. Each ROI is independently programmable on-the-fly withrespect to integration time, gain, sub-sampling/binning, position, width and height.A fairly comprehensive series of “bench tests”were conducted in order to test the validity of the new concepts and to initially verify the reliability of the system across various typical automotive operating conditions. Additional rigorous testing would of course be needed to guarantee a mean time before failure (MTBF) and to demonstrate the efficacy of the proposed design techniques over statistically significant production quantities.2 Application backgroundThe set of conceivable automotive camera applications is an ever-growing list with some market research reports claiming over 10 cameras will be required per vehicle [9]. The incomplete list includes occupant detection, occupant classification, driver recognition, driver vigilance and drowsiness monitoring [10], road surface condition moni- toring, intersection assistance [11], lane-departure warning [12], blind spot warning, surround view, collision warning, mitigation or avoidance, headlamp control, accident record-ing, vehicle security, parking assistance, traffic sign detection [13], adaptive cruise control and night/synthetic vision (Fig. 1).2.1 Cost considerationsThe automotive sector is a very cost-sensitive one and the monetary cost per subsystem remains an outstanding issue which could very well be the biggest hurdle in the way of full deployment of automotive vision. The supply-chain industry has been actively addressing the cost dilemma by introducing Field Programmable Gate Array (FPGA) vision processing and by moving towards inexpensive image sensors based on Complementary Metal Oxide Semiconductor (CMOS) technology [14]. Much has been borrowed from other very large embedded vision markets which are also highly cost-sensitive: These are mobile telephony and portable computing. However, automotive vision pushes the bar substantially higher in terms of performance requirements. The much wider dynamic range, higher speed, global shuttering, and excellent infra-red sensitivity are just a few of the characteristics that set most automotive vision applications apart. This added complex- ity increases cost. However, as the production volume picks up, unit cost is expected to drop quite dramatically by leveraging on the excellent economies of scale afforded by the CMOS manufacturing process.Some groups have been actively developing and pro- moting ways of reducing the number of cameras required per vehicle. Some of these methods try to combine disparate applications tore-use the same cameras. Other techniques (and products) have emerged that trade-off some accuracy and reliability to enable the use of monocular vision in scenarios which traditionally required two or more cameras [10, 15, 16]. Distance estimation for 3D obstacle localisation is one such example. Such tactics will serve well to contain cost in the interim. However, it is expected that the cost of the imaging devices will eventually drop to a level where it will no longer be the determining factor in the overall cost of automotive vision systems. At this point, we argue thatFig. 1 Some automotive vision applicationsreliability, performance and accuracy consid- erations will again reach the forefront.In this paper the cost issue is addressed, but in a different way. Rather than discarding stereo- and multi-vision altogether, a low-cost (but still high-performance) technique for synchronously combining multiple cameras is pre- sented. Cabling requirements are likewise shared, resulting ina reduction in the corresponding cost and cable harness weight savings.2.2 The role of high speed visionA number of automotive vision applications require high frame-rate video capture. External applications involving high relative motion such as traffic sign, oncoming traffic or obstacle detection are obvious candidates. The need for high speed vision is perhaps less obvious in the interior of a vehicle. However, some driver monitoring applications can get quite demanding in this respect. Eye-blink and saccade measurement, for instance, is one of the techniques that may be employed to measure a driver’s state of vigilance and to detect the onset of sleep [10, 16]. It so happens that these are also some of the fastest of all human motion and accurate rate of change measurements may require frame rates running up to several hundred hertz. Other applica- tions such as occupant detection and classification can be accommodated with much lower frame rates but then the same cameras may occasionally be required to capture high speed motion forvisual-servoing such as when modulating airbag release or seatbelt tensioning during a crash situation.2.3 A continued case for stereovision/multivisionSeveral of the applications mentioned, stand to benefit from the use of stereovision or multivision sets of cameras operating in tandem. This may be necessary to extend the field of view or to increase diversity and ruggedness and also to allow accurate stereoscopic depth estimation [11]. Then, of course, multivision is indeed one of the most effective ways of counteracting optical occlusions.Monocular methods have established a clear role (alongside stereoscopy) but they rely on assumptions that may not always be true or consistently valid. Assumptions such as uniform parallel road marking, continuity of road texture, and operational vehicle head or tail lights are somewhat utopian and real world variability serves to diminish reliability. Often, what is easily achievable with stereoscopy can prove to be substantially complex with monocular approaches [17]. The converse may also be true, because stereovision depends on the ability to unambigu- ously find corresponding features in multiple views. Stereovision additionally brings a few challenges of its own, such as the need for a large baseline camera separation, sensitivity to relative camera positioning and sensitivity to inter-camera synchronisation.Not surprisingly, it has indeed been shown that better performance (than any single method) can be obtained by combining the strengths of both techniques [18, 19]. As the cost issue fades away, monovision and multivision should therefore be viewed as complimentary rather than competing techniques. This is nothing but yet another example of how vision data can be processed and interpreted in multiple ways to improve reliability and obtain additional information.In this paper, the benefit of combining stereo and monocular methods is demonstrated at the hardware level. A tri-vision camera is presented that utilises a synchronized stereovision pair of cameras for 3D head localisation and orientation measurement. Using this information, a third monocular high-speed camera can then be accurately controlled to rapidly track both eyes of the driver using the multi-ROI feature. Such a system greatly economises on bandwidth by limiting the high speed capture to very small and specific regions of interest. This compares favourably to the alternative method of running a stereovision system at high frame rate and at full resolution.2.4 The importance for high synchronisationOne of the basic tenets of multivision systems is the accurate temporal correspondence between frames captured by the different cameras in the set. Even a slight frequency or phase difference between the image sampling processes of the cameras would lead to difficulties during transmis- sion and post processing. Proper operation usually rests on the ability to achieve synchronised, low latency video capture between cameras in the same multivision set. Moreover, this requirement extends to the video transport mechanism which must also ensure synchronous delivery to the central processing hubs. The need for synchronization depends on the speed of the motion to be captured rather than the actual frame rate employed, but in general, applications which require high speed vision will often also require high synchronisation.Interestingly, even preliminary road testing of automo- tive vision systems reveals another sticky problem – camera vibration. This is a problem that has already been faced many years ago by the first optical systems to enter mainstream vehicle use [20]–The optical tracking mechanisms used in car-entertainment CDROM/DVD drives are severely affected by automotive vibration and fairly complex (and fairly expensive) schemes are required to mitigate these effects [21]. The inevitable vibration essentially converts nearly all mobile application scenarios into high speed vision problems because even low amplitude camera motion translates into significant image motion. The problem gets worse as the subject distance and/or optical focal length increases. Mounting the cameras more rigidly helps by reducing the vibration amplitude, but it also automatically increases the vibration frequency which negates some of the gain. Active cancellation of vibration is no new topic [22]; however, this usually comes at a disproportionate cost. Thus, while high frame rates may not be important in all situations, short aperture times and high synchronization remain critically important to circumvent the vibration problem.A small numerical example quickly puts the problem into perspective. Consider a forward looking camera for in- lane obstacle monitoring based on a ¼ inch, 1024×512 image sensor array with an active area of 5.7×2.9 mm behind a 28 mm (focal length) lens. If such a system is subjected to a modest 10 mrad amplitude, sinusoidal, angular vibration at 100 Hz, simple geometric optics implies a peak pixel shift rate of around 32,000 pixels/sec.Thus, if the error in correspondence between left and right stereo frames is to be limited to a vertical shift comparable to one pixel, a stereovision system would require a frame synchronisation accuracy which is better than 30 microseconds. Then on the road, the levels ofvibration can get significantly worse and this does not yet take into account the additional high speed motion that may be present in the field of view. In summary, synchronization is a problem that has been largely overlooked and will become more important as the industry and consumer performance expectations increase. In this paper, a synchronisation technique based on matched cameras sharing a single clock is presented. The system affords a very high degree of synchronisation –in fact, much higher than is actually demanded by the driver monitoring application. Synchronisation difficulties arising during initialisation and camera mode changes are also addressed in this paper using a novel frozen-clock programming technique.2.5 High bandwidth interconnect and processingAutomotive vision faces another formidable challenge –bandwidth. Having several cameras running at high frame rates and at high resolutions quickly pushes such applica- tions into the multi GBit/s domain. This poses new pressures on a sector that is still barely warming up to multi-MBit/s interface speeds. New automotive video interface standards will be required, and while it makes sense to base these on existing and proven interconnects, it may be argued that a completely new standard is needed to properly address the requirements of this peculiar market. The stage is set for a standards-war and in fact, one is currently brewing which should eventually see the evolu- tion of a veritable Automotive Video Bus. Such a bus faces a tall order which includes: low cable cost, low interface cost, low specific weight, multi-GBit/s sustained throughput, multiplex-ability, preservation of synchronisation, high integrity, excellent electromagnetic compatibility (EMC) characteristics, low latency, low jitter, and a minimum 5 m cable span without repeaters [23].There is of course a second repercussion of such high bandwidths. Impressive data rates necessitate equally impressive computational power in order to perform all the associated video processing in real-time. This is fairly problematic considering the limited capabilities of most automotive embedded processors, but this is changing with the entry of FPGAs into the automotive market [23–25]. Aside from offering substantial (and sufficient) in-line processing power, FPGAs also serve to reduce cost by combining most of the interface glue-logic into a single chip. Then, FPGAs have the added appeal of re- configurability which allows aftermarket updates through simple firmware changes –though this raises several security concerns [25].3 Video interfacesA survey of currently available interface standards reveals that none of the present offerings are ideally suited to faithfully transport high speed, high resolution, synchron- ised stereovideo over appreciable distances. The following is a comparative discussion of the merits and shortcomings of the various interfaces.3.1 Bandwidth considerationsThe Interface throughput is the major concern since high resolutions are desirable and the required frame rates can reach into the high hundreds per second. At a moderate 200 frames per second, a 10 bit per pixel, greyscale, 640×480× 2, stereovision system generates video at 1.229 GBit/s. Even 1536×768×2 at 12 bit is not at all farfetched for certain applications and this touches 5.662 GBit/s which is impossible to accommodate on most current interfaces. Evidently, the interface is a bottleneck that needs to be addressed.For our driver monitoring application, 60 Hz is sufficient for accurate head localisation. However 200 Hz or more is desirable for fast eye-saccade and eye-blink capture. Running the entire system at 200 Hz at full resolution is therefore wasteful. By using a trinocular system, the frame rate of the stereovision pair can be set to 60 Hz, while a third monocular camera tracks the eyes alone at 200 Hz using a pair of 10,000 pixel ROIs. This way, assuming 10bit, the bandwidth requirements are reduced to a more manageable (369+40) MBit/s. The information collected using the stereovision system guides the ROI placement for the third camera.Hence, for this application, the strict requirement is for an interface that can sustain 409 MBit/s of throughput. However, in view of the possibility of other vision applications and future resolution improvements, the design should aim for an interface which should be able to handle a significantly higher bandwidth.3.2 Latency and jitter considerationsThroughput alone does not fully describe the problem. Low system latency is another aspect that cannot be neglected. Practically all of the automotive vision applications mentioned, depend on real-time low latency access to the processed output from the vision information. The driver vigilance application is no exception but other even more demanding applications come to mind. At 90 km/h a vehicle covers 25 m every second. A single second of lag in a high speed obstacle detection situation can make the difference between avoiding an accident and reacting too late. The problem with latency is that it all adds up. There is latency at the sensor, transmission latency, processing latency and actuator (or human) latency. If this totals up to anything more than a fewtens (or hundreds) of milliseconds, the effectiveness of most of these safety systems would be seriously compromised. Of course, establishing an exact value for the desired latency is no precise science because it depends on the situation.Video processing is perhaps the most important contributor to the overall latency and this usually needs dedicated hardware to keep up with the demands. FPGAs were already mentioned in this respect. Transmission is next in line in terms of latency severity. Delays due to buffering should be minimised or eliminated. Moreover, the latency should be fixed and uniform. Many signal processing techniques and control systems do not react too well to random variations in their sampling interval. Hence, there is a strong requirement for deterministic system behaviour with negligible transmission and processing time jitter.3.3 Video interface selectionAnalogue interfaces were once the only practical way of transmitting video information. The analogue bandwidth of coaxial copper cables is fairly good, latency is minimal and such interfaces offer excellent temporal determinism. Multi- camera support is also readily possible using radio frequency (RF) modulation/multiplexing and is a mature and reliable technique. However, guaranteeing signal integrity of analogue video becomes prohibitively difficult at high resolutions and frame rates. Moreover, with the prevalent use of intrinsically digital CMOS image sensors, it would be highly inconvenient and expensive to convert digital video data to analogue and back just for transmis- sion. The future lies entirely with digital. Table 1 provides a comparative summary of the various interfaces that were considered in this project.The initial obvious choice for digital video transmission technology is to look at established standards in the consumer electronics market. This could exploit the associated economies of scale and high maturity. However, a closer look reveals several shortcomings. While serial packet-transport protocols such as the Ethernet-derived GigE-Vision standard can sustain up to 750 Mbit/s [26], they have poor temporal characteristics, including high latency, poor determinism and substantial timing jitter making them rather unsuitable for high performance vision applications [27]. Even so, such throughput is only possible by using Jumbo Framing (a non-standard proprietary technology) [28]. Central processor (CPU) utilisation can also be unacceptably high. Multimedia-oriented protocols such as the Universal Serial Bus (USB2) and Firewire (IEEE1394b) only partially address these problems through the inclusion of specialisochronous modes of operation. The raw bandwidth is fairly high at 480 MBit/s and 3.2 Gbit/s respectively. However, their timing accuracy is limited to no better than ±125 µs, [29, 30]. Moreover, synchronous transport of multimedia streams over intrinsically asyn- chronous protocols poses complexities that outweigh the benefits [31].On the other hand, parallel video bus standards such as RS-422 and RS-644 which are based on parallel Low- Voltage Differential Signalling (LVDS), exhibit low latency, are highly deterministic, are synchronous and are relatively jitter-free by design. They also offer good throughput. Of course, the downside of any parallel bus is a severe limitation in length due to cable delay skew as well as the need for thick expensive cables.。
Unit 03 Automobile Engines 汽车专业英语教学课件
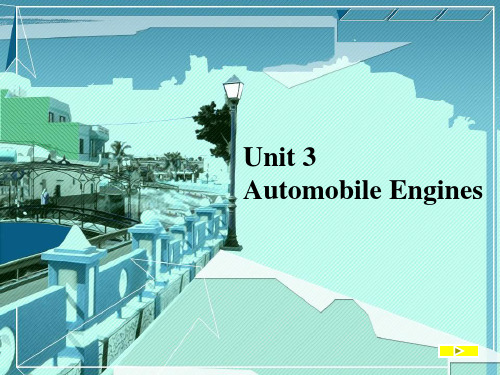
Unit 3 Automobile Engines
Engines have at least two valves per cylinder, one intake valve and one exhaust valve. Many newer engines are using multiple intake and exhaust valves per cylinder for increased engine power and efficiency[4].
Unit 3 Automobile Engines
The crankshaft is located below the cylinders on an inline engine, at the base of the V on a V-type engine and between the cylinder banks on a flat engine[3]. As the pistons move up and down, they turn the crankshaft just like your legs pump up and down to turn the crank that is connected to the pedals of a bicycle.
Unit 3 Automobile Engines
A common configuration is to have one camshaft located in the engine block with the lifters connecting to the valves through a series of linkages. The camshaft must be synchronized with the crankshaft so that the camshaft makes one revolution for every two revolutions of the crankshaft. In most engines, this is done by a "Timing Chain" (similar to a bicycle chain) that connects the camshaft with the crankshaft.
(3)unit 3(automobile basic structure)
产生大量热使缸内压力迅速上升,并通过曲轴将动力传到
传动系统而产生动力的。
• The chassis includes the power train, steering,
suspension, and braking systems.
• 底盘包括传动系统、转向系统、悬架系统、制动系统。
cylinder n.汽缸 gasoline n.汽油机 spark n.火花 ignition n.点燃,点火 diesel n.柴油机 compression n. 压缩 assembly n.总成,装备 chassis n.底盘 suspension n.悬架
• • • • • • • • •
or indicator light.
• 充电系统主要部件包括:蓄电池,交流发电机,集成在发
电机中的电压调节器,充电警告或指示灯。
四、课堂练习 发动机罩 金属板 底盘 悬架 启动机 动力装置 传动系统
• Chassis • Suspension • Starter • Power unit • Power train • Sheet metal • Hood
electrical system
braking system power train electrical system (generator) suspension
• A car contains more than 15000 parts, these parts
can be divided into four major categories: engine, chassis, body and electrical system.
汽车专业英语Unit 3
菲亚特 世界十大汽车公司之一,菲亚 特汽车公司始建于1899年7月 意大利都灵市,创始人是乔瓦 尼· 阿涅利。它是世界上第一个 生产微型车的汽车生产厂家。 这家公司的全称是意大利都灵 汽车制造厂,菲亚特(FIAT)是 该公司缩写的译音,FIAT也是 该公司产品的商标。菲亚特集 团总部设在意大利都灵市。工 程车辆公司有伊维柯公司。主 要品牌法拉利 菲亚特 阿尔法和 兰西亚。
兰博基尼汽车标志 这是一头浑身充满力气, 正准备冲击的公牛,寓意 由意大利兰博基尼公司生 产的赛车马力大、速度快、 战无不胜。汽车标志中这 只具有意大利血统的公牛 所代表的豪华跑车,在欧 美的名气绝不逊色于法拉 利的那匹骏马
法拉利汽车标识设计 1920年,法拉利效力于阿 尔法车厂当试车员,同时 参与赛车。1923年他在沙 维奥的赛车胜出之后,意 大利空军王牌飞行员巴拉 加的母亲,把儿子获得的 “腾跃骏马”的徽章赠给 了他。法拉利在那个标志 里加上意大利国旗。
萨博汽车logo设计 原先造军用飞机的 Saab想用头戴王冠半 鹰、半狮的怪兽图案 传达一种对于战争的 警觉,和一种捍卫权 力的态度。二次世界 大战后,Saab将其制 造飞机的技术和经验 搬到地面,开始生产 汽车。
道奇汽车品牌标志 虽然挂的是羊头,卖的可 是汽车。这只神气的羊头, 既表示“道奇”车强壮彪 悍,善于决斗,又表示道 奇车朴实无华的平民倾向。 不过现在注重内在豪华、 舒适但外表朴实憨厚的它 已经成为了各地富商名流 的当然选择。
福特 福特汽车公司由亨利· 福特先生创立于1903年, 是世界上最大的汽车企业之一。1908年,福特汽 车公司生产出世界上第一辆属于普通百姓的汽 车—T型车,世界汽车工业革命就此开始。福特 先生为此被尊为“为世界装上轮子”的人。亨 利· 福特先生成功的秘诀只有一个:尽力了解人们 内心的需求,用最好的材料,由最好的员工,为 大众制造人人都买得起的好车。主要品牌阿斯 顿· 马丁、福特、捷豹、路虎、林肯、马自达、水 星和Volvo。
《汽车专业英语(第3版)》教学讲义 Task2 信息化教学教案
Task2 Basic Structure of Automobile汽车基本结构
建议教学时数:4-6学时
教材中课堂活动2的游戏操作方法及截屏说明:
1.双击游戏课件,出现“欢迎使用软件”界面,关掉后的界面见截图2-1;
2.点击左上角的Edit,见截图2-2;
3.点OK后,用鼠标将英文词汇拖入与图片对应的框内,见截图2-3;
4.待完成所有图片与词汇的匹配后,点击check键,见截图2-4。
在训练中,难免会出错,重新拖入即可。
达到了用游戏的方法来训练英文词汇的目的,引导学生在游戏中学习,营造愉悦学习气氛,使学生保持学习兴趣,提高学习效果。
任课教师借助于课堂活动这个环节,也可以获得学生更真实的平时成绩。
截图2-1 截图2-2
截图2-3 截图2-4。
汽车专业英语Unit 3 PPT
PART FIVE-NOTES TO THE TEXT (难点解析)
1.The chassis of the automobile is the basic foundation of the vehicle.It includes the transmission system,driving system, steering system,and braking systems.
system. ➢ Learn about the key components of the chassis and can
translate them into English. ➢ Grasp the special term and useful expressions about the
chassis.
transmission system
传动系统
driving system
行驶系统
steering system
转向系统
braking system
制动系统
PART THREE-TEXT(阅读资料)
The Structure of the Chassis The chassis is a very important part of the automobile.All
UNIT 3 AUTOMOBILE CHASSIS汽车底盘
授课教师:
LESSON1 THE CHASSIS STRUCTURE底盘构造
Learning Objectives(学习目标)
➢ Learn about the main systems of the chassis. ➢ Learn about the name and the function of the four main
- 1、下载文档前请自行甄别文档内容的完整性,平台不提供额外的编辑、内容补充、找答案等附加服务。
- 2、"仅部分预览"的文档,不可在线预览部分如存在完整性等问题,可反馈申请退款(可完整预览的文档不适用该条件!)。
- 3、如文档侵犯您的权益,请联系客服反馈,我们会尽快为您处理(人工客服工作时间:9:00-18:30)。
第3讲 Automotive components (汽车的组成部分)
主要内容精讲
1.3 Automotive components (汽车的组成部分)
1.3.1 The appearance of a car(汽车外观图) 1.3.2 The center console(汽车内部图) 1.3.3 Dashboard+Warning light(仪表盘+警示灯) 1.3.4 Tools (随车工具) 1.3.5 Car diagram(汽车图)
1.3.3 Dashboard+Warning light(仪 表盘+警示灯)
– Passat Dashboard (大众帕萨特仪表盘)
1.3.4 Tools(随车工具)
– Jack(千斤顶)
– Tire pressure (胎压计)
– Fire extinguisher(灭火器)
– Tire(轮胎)
– Wire rope(钢丝绳)
– Battery line(蓄电池线)
1.3.5 Car diagram(汽车图)
– 整车尺寸 ( Measurements )
• Example of a Vehicle Specification Chart (车辆规 格参数表示例)
END
• 1.Look at the picture and fill in the blanks. (看图填 空)
Hale Waihona Puke • 2.Chinese translation into English. (中文翻译成英文)
– 加速踏板 – 发动机舱 – 制动踏板 – 门锁 – 前照灯 – 座椅 – 行李舱 – 空调 – 刮水器 – 喇叭
1.3.1 The appearance of a car(汽 车外观图)
1.3.2 The center console(汽 车内部图)
» The center console of Shanghai Volkswagen Passat ( 上海大众帕萨特领驭驾驶台)
– Exercise: Practice makes perfect.(熟能生巧)