水泥粉磨工艺参数优化
风选磨半终粉磨工艺在水泥粉磨中的应用

风选磨半终粉磨工艺在水泥粉磨中的应用南京苏材重型机械有限公司刘永贵水泥粉磨工艺的优化设计直接影响到后期水泥生产成本,粉磨工艺选型除考虑系统产量,系统投资,系统电耗,还需考虑熟料利用率,水泥性能,水泥强度,设备的可靠性、系统的运转率、易损件磨耗等。
如何选取最优的粉磨工艺,最简洁的工艺配置,最可靠实用的生产设备,用最小的投资取得最大的经济效益,成为广大水泥企业所追求的目标。
现有粉磨工艺比较目前比较常见的粉磨工艺:预破碎设备(锤破、立轴破、对辊机等)+球磨机;预粉磨设备(辊压机、风选磨、CKP磨)+球磨机。
采用上述工艺设备都是尽量利用多破少磨粉磨原理,尽可能最大限度发挥预粉磨设备挤压破碎功能,后道球磨机起研磨修形作用,提高水泥粉磨能力。
目前半终粉磨系统在水泥粉磨中已经得到快速应用,半终粉磨系统即预粉磨产生的细粉通过分级生产的水泥成品直接采用高浓度布袋收尘器收集入成品库,避免了大量<45um细粉进入管磨机内部,导致细磨仓出现“过粉磨”所引起的研磨体及衬板表面严重粘附现象,使管磨机系统始终保持较高而稳定的粉磨效率。
扬中市大地水泥有限公司半终粉磨开路系统改造及运行情况扬中市大地水泥有限公司现有两条水泥粉磨生产线,主机配置两台φ3.5×13m水泥磨,其中一台采用辊压机半终粉磨工艺,另一台无预粉磨设备,本技术改造在无预粉磨的生产线上,采用南京苏材重型机械有限公司风选磨半终粉磨工艺。
图示11、粉磨系统改造前扬中市大地水泥有限公司水泥粉磨生产线φ3.5×13m磨机1台,采用开路磨工艺,配套收尘器PPC96-6。
磨机分为三仓,Ⅰ仓为阶梯衬板,仓长4.0m;Ⅱ仓位为中波纹衬板,仓长2.75m;Ⅲ仓位为小波纹衬板,仓长5.5m。
采用高铬研磨体,最大钢球为φ90mm,最小钢段为φ8×8mm;前隔仓采用双层隔仓,后隔仓为单层隔仓,台时产量65吨/时,粉磨电耗为36kWh/t。
工艺流程见图示1。
图示22、粉磨系统改造后扬中市大地水泥有限公司粉磨生产线φ3.5×13m磨机1台,采用前闭路后开路工艺见图示2;即FM40(有效长度5.0m)风选磨作为水泥预粉磨设备,熟料、明矾石、石膏等进入风选磨进行预粉磨(生产42.5级水泥时配比:熟料86%,磷石膏含煤渣12%,明矾石2%),配套O-sepa改进型选粉机S1500,合格成品直接通过收尘器入库,选粉机粗粉进入φ3.5×13m磨机,磨机分为三仓,采用带筛分的双层隔仓装置,增加通风面积,磨尾采用线切割热处理出料篦板;风选磨钢球采用φ60mm-φ100mm,高细磨机采用φ30mm-φ60mm钢球和φ10mm-φ25mm的钢锻。
水泥生产过程优化与控制

水泥生产过程优化与控制随着建筑工程的不断发展,水泥作为建筑材料之一,其生产也逐渐成为了一个重要的领域。
然而,由于水泥生产过程中存在着众多的问题,所以如何优化和控制这个过程就成为了一个值得深入探讨的话题。
在本文中,将重点讨论水泥生产过程中的问题及其优化和控制措施。
1. 水泥生产过程中存在的问题在水泥生产过程中,存在着许多问题,如物料热均衡不稳定、能源消耗高、排放物污染严重等。
这些问题一方面会影响到水泥生产的质量和效率,另一方面也会对环境产生负面的影响。
具体而言,水泥生产过程中存在以下几个主要问题:1.1 减少磨矿能耗磨矿是水泥生产过程中最耗能的环节之一,其占总能耗的30%左右。
目前,磨矿的能耗已经成为了比较严重的问题。
为了解决这个问题,可以从以下几个方面入手:(1)提高设备的效率,例如使用高效的磨煤机等。
(2)节约能源,例如采用低能耗的磨料和燃料等。
(3)改变磨矿的工艺流程,例如采用新型的磨煤机等。
1.2 降低炉排排放物的含量在水泥生产过程中,炉排排放物是一个比较严重的问题。
炉排排放物不仅对环境造成影响,还会对生产质量和健康产生负面的影响。
因此,为了降低炉排排放物的含量,可以从以下几个方面入手:(1)改进燃烧工艺,例如采用高效的烧结技术等。
(2)优化炉排结构,例如设置高温旋流器等。
(3)提高粉尘回收效率,例如采用新型的过滤设备等。
1.3 加强能源利用水泥生产过程中需要耗费大量的能源,因此,在节约能源方面也很重要。
为了加强能源利用,可以从以下几个方面入手:(1)回收余热,例如采用余热回收技术等。
(2)采用新型燃料,例如采用生物质等。
(3)优化工艺流程,例如采用高效的干燥设备等。
2. 水泥生产过程的优化与控制为了解决上述问题,需要采取一系列的优化和控制措施。
在下面,将具体介绍一些具体的措施:2.1 控制原材料的品质和含量对于水泥生产过程中的原材料,其品质和含量很大程度上会影响到生产的质量和效率。
因此,需要对原材料进行严格的控制。
提高水泥磨能力的途径

提高水泥磨能力的途径水泥粉磨过程的高效率、低能耗运行,一直是生产企业追求的目标。
“提高磨机能力”,也是一个永恒的话题。
不断提高球磨机的粉磨效率,降低粉磨电耗和生产成本,最大幅度地达到高细、高产,是我们不懈追求的目标。
尤其是水泥新标准的实施,对水泥细度、比表面积和颗粒组成都提出了更高的要求,水泥企业往往以降低混合材掺加量或提高水泥比表面积来提高水泥强度,而要获得较高比表面积最简单的办法是降低磨机的产量和增加研磨时间,但带来的结果是出现“过粉磨现象”,使<3um的微粉增多且颗粒组成状况不佳,强度提高不多,而粉磨电耗却大幅度上升。
这种采用降低产量和增加研磨时间提高水泥成品细度或增加熟料含量来提高水泥强度的作法,势必会造成生产成本的上升。
因此,必须从磨机内部改造、物料预破碎、研磨体的合理级配等入手来提高水泥3-30um颗粒的含量,从而提高水泥的强度。
一、提高水泥磨能力的一般途径1、降低入磨物料粒度降低入磨物料(熟料)粒度,可降低单位产品电耗,提高水泥粉磨能力。
入磨物料粒度大小是影响磨机产量的主要因素,粒度小可减小钢球的平均球径,在装载量相同的情况下,钢球个数增加,钢球的总面积增加,可增加钢球与物料的接触面积,提高粉磨效率,因此采用“多碎少磨”即磨前预粉碎工艺可降低粉磨系统电耗和提高磨机能力。
2、调整磨机内部结构采取了磨前预破碎工艺,入磨物料粒度减小了,但粉磨能力并未提高,现象是出磨提升和O-Sepa选粉机电流高、负荷重,循环负荷率高、达到了240%,选粉效率很低、才25%左右,通过作筛析曲线也得到了印证,在第一仓曲线很陡,第二仓曲线接近水平线。
显然该磨机第一仓冲击力太强,第二仓研磨能力严重不足,针对这种状况,在第二仓加了3吨小钢球后,台时产量可提到70t/h左右,为进一步发挥该磨机能力,又对磨机内部结构作了适当调整,将一仓长度由原来的5.35m缩短为4.85m,即把隔仓板向前移动一块衬板长度,二仓长度由原来的7.25m增加到7.75m,增加细磨仓的研磨能力,提高粉磨效率。
沙特SCC万吨生产线水泥粉磨系统分析及改造
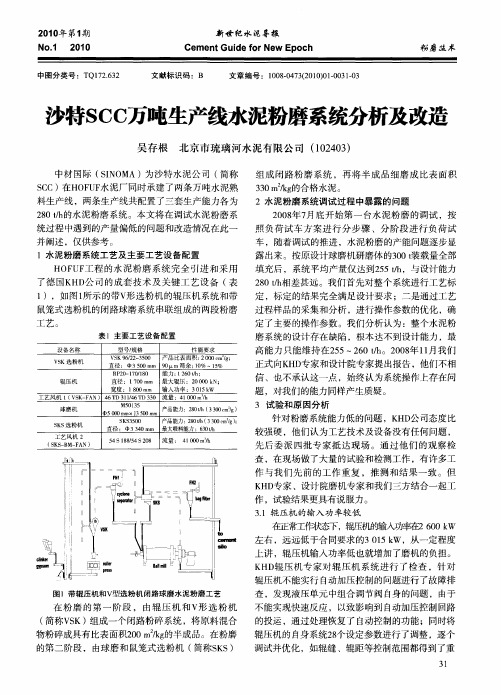
定了主要的操作参数。我们分析认为 :整个水泥粉 磨 系统 的设 计存 在 缺陷 ,根本 达不 到设 计能力 ,最 高能力只能维持在2 5 2 0t 。20 年 1月我们 5 ~ 6 h 0 8 1 / 正式向K D H 专家和设计院专家提出报告 ,他们不相 信 、也 不 承认这 一点 ,始 终认 为系 统操作 上存 在 问 题 ,对我们的能力同样产生质疑。
产品能力
:20/ 3 0 m/ 8t h( 0c : 3 g)
( K S S
S¥50 K 3o 产品 能力: 8 t ( 0 m/) 20/ 3 0 c ; h 3 g 直径 : 中33 0mm 最大 喂料 能力 :60t 4 3P a 5 8,4S2 8 流 量 4S185 0
2 1 年 第1 00 期
No 1 . 2 1 0 0
新 世 纪水 泥导报 C me t ief r e E o h e n d w p c Gu o N
文献标识码 :B 文章 编号 :10 .4 32 1) 1 0 1 3 0 80 7 (0 00 — 3 - 0 0
3 试 验和原 因分析 源自辊 压 机 工艺 风 机 1( S — A 4 D3 14 D30 流 量 :4l 0 V K F N) 6T 1/6T 3 0m/ 0 h
球磨机 SS K 选粉机
工艺 风 机 2
—
中500 0
M 0 3 5 15
mm ̄】 0 35 0mm
彩蘑丝 木
中图分类号 :T 7 .3 Q1 2 2 6
沙特S C C 万吨生产线水泥粉磨系统分析及改造
吴存根 北京市琉璃 河水 泥有限公 司 (0 4 3 12 0 )
中材国际 ( I O SN MA)为沙特水泥公 司 ( 简称 组成 闭路粉磨 系统 ,再将半成 品细磨成 比表面积 S C)在 H F F 泥厂 同时 承建 了两 条万 吨水 泥熟 30m/g3 格水 泥 。 C OU水 3  ̄合 k 料生产线,两条生产线共配置了三套生产能力各为 20t 的水泥粉磨系统 。本文将在调试水泥粉磨系 8 h / 统过程中遇到的产量偏低的问题和改造情况在此一 并 阐述 ,仅供 参考 。 1水 泥粉磨 系统工 艺及主 要工 艺设 备配置
水泥粉磨工艺参数优化

水泥粉磨工艺参数优化摘要:随着我国现代化建设的不断深入,水泥的用量不断增大,迫使我国水泥生产技术不断改进,加之国内外水泥生产技术的引进和交流,我国水泥工艺有了明显的进步和发展。
好水泥是“磨”出来的,目前,由于粉磨主机设备及预产处理设备选型等因素,不同规模的粉磨站的工艺流程也相应各具特色,总体产量与粉磨的耗能也有所不同。
关键词:联合粉磨;水泥粉磨工艺;参数优化;很长一段时期,我国的水泥粉磨都是纯球磨机系统,磨机产量一直处于比较低的水平,以最具代表性的?3.2m球磨机为例,纯球磨机系统生产水泥在35~45t/h,出磨水泥细度0.08 mm 筛余较高;同时,磨内过粉磨现象较严重,致使水泥颗粒级配不理想,且磨内温度高,既影响磨机产量,而且研磨体粘糊现象也时有发生。
传统的水泥粉磨生产模式,有很多缺点,比如:效率低、污染大、成本贵等,这与建立高效绿色的新型企业和社会不能吻合。
水泥生产过程中,粉磨生产的耗能大约占水泥生产能耗的70%,所以它对整个水泥生产的节能减排,起着非常重要的作用。
一、水泥粉磨工艺的现状1.管磨机粉磨系统。
对水泥的生产工艺进行调查不难发现,现阶段绝大部分的工艺都是通过管磨机作为主要的粉磨设备进行生产的。
目前我国国内的水泥管磨机直径已经达到了5m 左右,产量可以保持在150t/h 以上。
磨机内的研磨体一般是柱状或者圆球状的,圆球形的研磨体主要通过和物料进行点接触来完成冲击和破碎,因为接触面积较小,所以粉磨的效率也比较低。
在进行抛落的时候可以采用助磨剂等手段,在一定程度上提升生产效率。
通过对管磨机的粉磨工作方式进行分析得知,这种粉磨工艺对研磨工作能力有余,但是对物料的破碎能力不足,大粒径的物料通过管磨机粗磨仓进行破碎是不合理的。
因此,可以在入磨前对物料进行处理,缩小入磨物料粒径,这是实现磨机增产降耗的有效途径。
2.联合粉磨系统。
联合粉磨系统,就是使用一套辊压机预粉磨系统加一套纯球磨机系统,辊压机的粉碎原理为料床粉碎, 作业时, 压力作用在由大量颗粒组成的密实料层上, 颗粒间互相施力, 能以最低能量获得最佳粉碎功, 能量利用率高。
辊压机水泥联合粉磨系统的试产与调整

喂 料皮 带 至V 选粉 机 之 间为垂 直 下料 溜 管 , 型
料饼 未经打散直 接进入V 型选粉 机 ,选粉 效果较
() 1 磨头存在溢料现象 。由于磨机磨头进料 口采用 嵌入 式 喂料装 置 ( 5 ),当加大 喂料 量时 4。
差 ,同时因下料点相对集 中,V 型选粉机打散板磨 因物料 的冲力致部分细粉从磨头缝隙溢出,现场灰 损严重 。为了提高打散效果 ,在V 型选粉机入料溜 尘大 、环境差 ,被迫人为减少喂料量或加大磨尾拉
中图分类号 :T 7 .3 Q126 2
辊压机水泥联合粉磨系统的试产与调整
胡宏 刚 邹伟斌 王 中鸽。
1安徽省 淮南舜岳水泥有限责任公 司,227 ; 2 中国建材 工业经济研 究会 水泥专业委 员会 ,103 ; . 302 . 081
3 成都建 筑材料 工业设计研 究院有限公 司,60 5 . 10 1
O sp 高效选粉机 —ea
系统风机 系统袋 收尘 器
型号 N 40 , 一 50 最大喂料量 80/, 1 h 产量 10 20/, t 6 ~ 7 h 选粉风量 20 0 , t 7 0 / 功率 20 W 0 mh 5 k
Y — 3 2 .F 4 7 — 3 ,风量 3 0 0 ,全压 5 0 a 5 1 0m/ 0 h 20P ,功 率 7 0k 1 W XP L M2X1 D,处理风量 2 0 0m/ ,总过滤面积 460m 4 7O h 6
象。
风量 ,从而影响产质量。为此 ,在磨内进料落料点 护板部位加焊螺旋进料板 ,以将细粉导人磨 内。 ( 2)磨 内物料 流 速 快 ,出磨 细度 偏粗 。为 了 适当减缓磨内物料流速、增加物料的磨细时间 ,在 磨机第二仓内挡料圈 ( 活化环 ) 靠磨筒体 ( 外圆 ) 部位用耐磨钢板封焊一圈 ,焊堵挡料圈部分空挡 , 封堵 高度 在 10mm左 右 ,这 样 既不 影 响 原 来 挡料 5 圈 ( 活化环 ) 微 段 的活化 功能 ,又 能起 到部 分挡 对
水泥磨提产改造方案
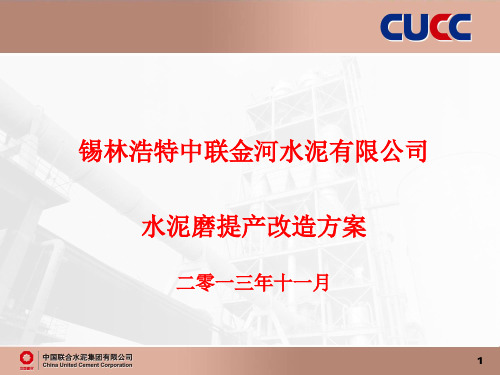
极低,有效地延长了其使用寿命。
⑹ 主轴下轴承密封采用新的设计方案,采用了干油站强制润滑轴承, 有效地解决了轴承进灰和漏油两项重大难题,切实有效地延长了轴承使用 寿命。 ⑺ 高效率的集尘系统可将30μm以下颗粒及时并大量地收集进入成品
,有效地提高了产品的比表面积。
四、高效涡流选粉机性能参数:
4.3 Sepax高效涡流选粉机特点
四、高效涡流选粉机性能参数:
85%以上,但其系统装机容量却要降低30%,且可在正压下工作,细粉 收集仅采用高效旋风筒即可,无需再配置庞大的气箱脉冲袋式除尘器, 这样不但降低了粉磨电耗,而且也降低了投资费用(省去了气箱脉冲袋 式除尘器)和维护保养费用。与转子式选粉机相比其分级效率高出15% ,而装机容量却差不多,因而产量要高出20~30%。
1.3.2产、质量指标
时间
辊压机 辊压机 出磨提 入磨提 80um 比 表 项目名 选粉机 磨机电 筛 余 m2/kg 台时t/h 动辊电 定辊电 升机电 升机电 称 电流 流 ≦1.2% >370 流 流 流 流
345 125 35 32 99 130 180 160
14:00 PO42.5 0.4
3 、布袋收尘器JMPL128-2X8D,处理风量150000m3/h,过滤风 速1.07m/min,系统阻力≦1500Pa,风机GY75T-VN021F,风 量180000m3/h,压力7500Pa,电机YJTGKK5003-6/560kw 4、球磨机Ǿ3.8X13m,二仓,其中一仓长2.75m,二仓9.75m。电
⑶ 与O-Sepa涡流选粉机相比, Sepax涡流选粉机增加了分散、预分
级装置。采用航空空气动力学分析方法对整个流场进行了优化设计;采用 悬浮分散技术使物料充分分散;采用预分级技术,有效地减小了大小颗粒 间的干扰,为精确分级创造了条件。 ⑷ Sepax涡流选粉机与尺寸相近的离心式、旋风式、单(双)转子
用正交试验法优化水泥粉磨工艺参数

萼 - 一 惫 嫠 警 - 噻 一 一 ≯
1 9 . 4 7 o 7 4 82 4 2 8 .2 4 0 5 41 2 6 20 5 o 5 o 25 1 8 26 1 、 6 2 . . 0 20 5 2 1 0 3 8 14 29 1 0 . 9 . . 8 0
试 熟一 … 料 …~望 一 —鱼 一 一 , 互 一L E A 一枕 一 一
2
7
3
8
4
8
n
素试 验方 法确 定该 组 工艺 参数 , 如 ,0 的控 制 值 例 S
一
∞ 鹋
勰
般 是做 纯熟 料 水泥 的 S 水 泥强 度试 验 . 0 以强 度
勰 ∞ 虬
5 2 吨 。  ̄ 0e L/
关 键字 : 交试验 水 泥粉 磨参数 工 艺参数优 化 正
水泥 粉 磨细 度 ( .8 m 孔 筛 筛余 %) 水 泥 S 00 m , 0
含 量 . 种混 合 材 的掺量 是 水泥 粉 磨工 艺 的一 组重 各 要 工 艺参数 水 泥细度 与强 度呈 非线性 正 比关 系 ,
∞
最 高 值 所 对 应 的 S 作 为 水 泥 生 产 S 制 指 O值 O控 标 实际 上 , 种方 法得 出 的 S 并非 最佳 控 制 这 0值
指标 , 际生产 中 , 实 细度 、 合 材掺 量 均对 水 泥强 度 混 产 生影 响 . 这种 协 同作 用 很难 用数 学 模 式表 达 正 交 设 计 方法 通 过 多 因素 分 析试 验 【. ” 对水 泥 配方 进 行 优化 【 本文 对水 泥粉 磨工 艺参数 进 行优 化时 , , 选
因素 A B C D E
l 75 5 0 25 l O O 50 0 5 O 20 5
- 1、下载文档前请自行甄别文档内容的完整性,平台不提供额外的编辑、内容补充、找答案等附加服务。
- 2、"仅部分预览"的文档,不可在线预览部分如存在完整性等问题,可反馈申请退款(可完整预览的文档不适用该条件!)。
- 3、如文档侵犯您的权益,请联系客服反馈,我们会尽快为您处理(人工客服工作时间:9:00-18:30)。
水泥粉磨工艺参数优化
发表时间:2019-01-16T15:23:02.627Z 来源:《防护工程》2018年第31期作者:朱飞
[导读] 很长一段时期,我国的水泥粉磨都是纯球磨机系统,磨机产量一直处于比较低的水平。
中建材(合肥)粉体科技装备有限公司安徽合肥 230051
摘要:随着我国现代化建设的不断深入,水泥的用量不断增大,迫使我国水泥生产技术不断改进,加之国内外水泥生产技术的引进和交流,我国水泥工艺有了明显的进步和发展。
好水泥是“磨”出来的,目前,由于粉磨主机设备及预产处理设备选型等因素,不同规模的粉磨站的工艺流程也相应各具特色,总体产量与粉磨的耗能也有所不同。
关键词:联合粉磨;水泥粉磨工艺;参数优化;
很长一段时期,我国的水泥粉磨都是纯球磨机系统,磨机产量一直处于比较低的水平,以最具代表性的?3.2m球磨机为例,纯球磨机系统生产水泥在35~45 t/h,出磨水泥细度0.08 mm 筛余较高;同时,磨内过粉磨现象较严重,致使水泥颗粒级配不理想,且磨内温度高,既影响磨机产量,而且研磨体粘糊现象也时有发生。
传统的水泥粉磨生产模式,有很多缺点,比如:效率低、污染大、成本贵等,这与建立高效绿色的新型企业和社会不能吻合。
水泥生产过程中,粉磨生产的耗能大约占水泥生产能耗的70%,所以它对整个水泥生产的节能减排,起着非常重要的作用。
一、水泥粉磨工艺的现状
1.管磨机粉磨系统。
对水泥的生产工艺进行调查不难发现,现阶段绝大部分的工艺都是通过管磨机作为主要的粉磨设备进行生产的。
目前我国国内的水泥管磨机直径已经达到了5m 左右,产量可以保持在150t/h 以上。
磨机内的研磨体一般是柱状或者圆球状的,圆球形的研磨体主要通过和物料进行点接触来完成冲击和破碎,因为接触面积较小,所以粉磨的效率也比较低。
在进行抛落的时候可以采用助磨剂等手段,在一定程度上提升生产效率。
通过对管磨机的粉磨工作方式进行分析得知,这种粉磨工艺对研磨工作能力有余,但是对物料的破碎能力不足,大粒径的物料通过管磨机粗磨仓进行破碎是不合理的。
因此,可以在入磨前对物料进行处理,缩小入磨物料粒径,这是实现磨机增产降耗的有效途径。
2.联合粉磨系统。
联合粉磨系统,就是使用一套辊压机预粉磨系统加一套纯球磨机系统,辊压机的粉碎原理为料床粉碎, 作业时, 压力作用在由大量颗粒组成的密实料层上, 颗粒间互相施力, 能以最低能量获得最佳粉碎功, 能量利用率高。
联合粉磨工艺采用辊压机粉磨时, 不仅挤压力大, 粉碎效果好, 而且物料在机器内停留时间短, 有利于提高产量。
经辊压机粉磨后的产品为扁平状, 这种料饼用手一捻即碎, 其中大部分是细粉, 少数粗颗粒也充满了裂纹, 改善了易磨性, 为进一步粉磨创造了条件。
经过辊压机粉磨系统之后的半成品物料,已经达到一定细度,而且物料的易磨性也大大改善,这样也可以提高球磨机的粉磨效率,联合粉磨系统的水泥不仅产量高,而且水泥的品质是最佳的也是最可控的,此种水泥更适应市场的需求,目前市场的水泥也主要是联合粉磨系统生产的水泥。
联合粉磨的产量可以大幅度提高,且粉磨的工序电耗比纯球磨机粉磨系统的水泥单位电耗约可降低约10~15kWh/t。
3.立磨粉磨系统。
目前国外也有一定的厂家使用立磨粉磨系统粉磨水泥,立磨系统自身的产量高,系统简单,能耗量较低,但是立磨系统的水泥标准稠度需水量高,颗粒形貌是扁平状,水泥品质难以满足国内市场的需求,在国内使用立磨系统粉磨水泥的还很少见。
立磨粉磨和辊压机粉磨有相似的地方,两者都是料床粉碎,立磨磨辊和物料的接触面是柱面和平面,而辊压机接触面是柱面和柱面,产品的颗粒形貌也很相似。
联合粉磨系统因为是辊压机预粉磨系统加球磨机系统,成品水泥颗粒形貌因为经过球磨机整形,所以成品水泥的品质能够保证,但是辊压机联合粉磨系统比比立磨系统要复杂,生产操作要比立磨要麻烦。
目前为止,世界上最大的立磨机产量可以达到600t/h 左右,且立磨粉磨系统比管磨机粉磨系统的水泥单位电耗约可降低15kWh/t。
二、水泥粉磨工艺参数优化
1.细度对水泥强度的影响
细度状态是水泥的细度控制值、水泥的颗粒分布(颗粒组成、颗粒级配)、水泥颗粒形状三者的统称,他们对水泥的强度及性能有很大的影响。
一是水泥细度控制值,国内表示水泥细度的方法一般有4种:平均粒径、筛余、比表面积和颗粒分布,我国水泥工业生产中常用筛余和比表面积来控制水泥成品的细度。
然而,当筛余值相同时,比表面积也各不相同,以至于水泥的强度值也相差很多。
二是水泥颗粒分布,水泥颗粒大小与水化过程有着直接的影响,不同粒径的水泥水化速度及水化程度差异很大。
三是水泥颗粒形状,水泥颗粒形状对水泥性能的影响较为复杂,由于粉磨水泥的设备及研磨介质不同,其生产的水泥粉体颗粒形状也完全不同。
球形度不同的水泥颗粒,在水化过程中的变化是不同的,也就表现出水泥的早期强度和后期强度不一样。
立磨系统生产的水泥颗粒中长条形、圆柱形颗粒多,水泥颗粒之间的相互连生、搭接有助于早期强度的提高,但颗粒间的摩擦系数大,要达到一定的流动度就需要多加水,即标准稠度用水量增加,使后期强度增长率及后期强度均较球形度高的水泥颗粒低。
水泥粉磨使用球磨机比使用立式磨得到的产品中颗粒球形度要高,如果球磨机的细磨仓用小钢球代替钢段,对提高水泥颗粒的球形度更为有利。
2.开流粉磨工艺的影响
开流粉磨工艺是利用管式磨机,将不同硬度、不同大小的混合物料同时送入磨内粉磨,出磨的水泥不经过选粉直接作为成品水泥直接入库。
开流粉磨对比圈流粉磨颗粒级配较好一些,强度也较高。
但粉磨后的成品水泥中30~80μm 的颗粒中混合材的含量约有30%以下,5~3μm 的颗粒中混合材的含量约有60%以下,0~5μm 的颗粒中混合材的含量约有80%左右。
这种粉磨工艺比表面积虽然高但都是由混合材的过粉磨产生的,因此称为假性比表面积。
混合材在水泥中主要起物理性能的载体作用,活性度较低,水泥的颗粒形状过细会导致产生静电、包球、吸水性大、石膏脱水等现象,在粉磨过程中过粉磨会耗费大量的电耗和时间。
3.预粉磨工艺的影响。
目前我国在2000t/d 以上的新型干法水泥生产线中已经普遍采用辊压机与球磨机组成的粉磨系统(包括循环预粉磨、联合粉磨、半终粉磨等),这是因为辊压机在粉磨效率上几乎是球磨机的2倍左右,有很大幅度的节电效果。
辊压机与球磨机组成的联合粉磨系统的节电水平因其消耗功率的大小而变化,辊压机每消耗1(kW·h)/t,可使球磨机电耗下降1.8~2(kW·h)/t 左右,从而使辊压机和球磨机组成的预粉磨系统的总电耗降低0.8~1(kW·h)/t,节电效果显著。
在实际运行中通过调整辊压机的液压压力、磨辊转速等
操作参数,完全掌握了辊压机在挤压不同粒径、不同物料的运行规律。
在水泥成品比表面积>300m2/kg时,可以保证辊压机在安全、平稳的运行状态下,使辊压机的性能得到充分发挥。
联合粉磨必须关注入料的粒度均一性问题,如果入料粒度的均一性较差,特别是易碎性差时,就应该考虑对大粒度物料的预破碎或者预辊压。
预粉磨工艺降低了入磨物料的粒度,它是磨机产量提高的主要原因。
同时为降低研磨体平均尺寸及调整填充率,从而改善出磨水泥的细度状态提供了保证。
只有不断对粉磨系统进行改造和创新,才能保证水泥粉磨工作长期优质地进行,降低单位能耗,减少生产成本,为粉磨技术的发展提供经验和参考。
参考文献:
[1]赵永林,张利敏. 我国水泥粉磨技术的现状及改进措施简述[J]. 内蒙古石油化工,2016(08)
[2]李纯茂,刘骁. 浅谈水泥粉磨工艺[J]. 建材发展导向,2015(03)
[3]乔龄山. 水泥的最佳颗粒分布及其评价方法[J]. 水泥,2016(8):1-5.。