铸铁熔炼
铸造合金及其熔炼(铸铁熔炼)
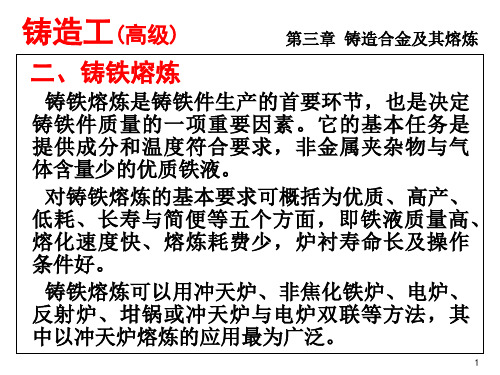
第三章 铸造合金及其熔炼
二、铸铁熔炼
铸铁熔炼是铸铁件生产的首要环节,也是决定 铸铁件质量的一项重要因素。它的基本任务是 提供成分和温度符合要求,非金属夹杂物与气 体含量少的优质铁液。
对铸铁熔炼的基本要求可概括为优质、高产、 低耗、长寿与简便等五个方面,即铁液质量高、 熔化速度快、熔炼耗费少,炉衬寿命长及操作 条件好。
9
铸造工(高级)
第三章 铸造合金及其熔炼
(5)熔化与出渣 在正常熔化过程中,
应严格控制风量、风压、不得随意停风。按 规定及时取样,测量铁液温度、风量、风压、 风温等。经常观察风口、出渣口、出铁口、 加料口,注意铁液、炉渣质量,风量、风压、 三角试块白口变化。及时发现和排除故障, 保证熔化正常。应按时打开出渣口出渣,一 般每隔30~45min出一次渣。
2
铸造工(高级)
第三章 铸造合金及其熔炼
图3-12 冲天炉结构简图
1—炉脚 2—炉底板 3—炉底门 4—风口窥视孔 5—风箱 6—耐火砖
7—加料口 8—烟囱 9—除尘器 10—风口 11—过桥 12—前炉盖 13—前炉窥视孔 14—出渣口及出渣槽
15—出铁口及出铁槽
3
铸造工(高级)
第三章 铸造合金及其熔炼
10
铸造工(高级)
第三章 铸造合金及其熔炼
从炉渣的颜色、状态可以判断冲天炉的 熔化质量。观察酸性冲天炉炉渣时,一般 用铁棒蘸些炉渣,抽拉成丝,在亮处观察。 炉况正常的炉渣为黄绿色玻璃状。炉渣呈 深咖啡色,说明铁液含硫偏高;炉渣上带 白道或白点,说明石灰石加入量过多;炉 渣呈黑色玻璃状,致密、密度大,说明铁 液已严重氧化。
打炉前,应在炉底铺上干砂不能有积水或潮湿。 打开炉底门,用铁棒将底焦和未熔炉料捅下, 用水浇灭。
简述球墨铸铁的熔炼过程及铁水质量控制的方法。

球墨铸铁熔炼过程及铁水质量控制方法本文简述了球墨铸铁的熔炼过程以及铁水质量控制的方法,旨在帮助读者了解球墨铸铁的生产过程及其质量控制要点。
球墨铸铁是一种高强度、高韧性的铸铁材料,其生产过程中铁水质量控制至关重要。
下面将分别介绍球墨铸铁的熔炼过程和铁水质量控制方法。
一、熔炼过程球墨铸铁的熔炼过程主要包括原材料准备、熔炼、调整和浇注四个步骤。
1.原材料准备:球墨铸铁的原材料主要包括铁水、废钢、回炉料等。
铁水要求含碳量在2.5% 以下,硅、锰、硫、磷等元素的含量也要控制在一定范围内。
废钢和回炉料要求干净、无油污、无杂物。
2.熔炼:球墨铸铁的熔炼一般在电炉中进行。
熔炼过程中要加入适量的废钢和回炉料,并控制好熔炼温度和时间。
熔炼结束后要进行精炼,以去除杂质和气体。
3.调整:调整是指在熔炼结束后,对铁水进行成分和温度的调整。
调整的目的是使铁水的成分符合要求,并使其温度达到浇注所需要的范围内。
4.浇注:浇注是球墨铸铁生产的最后一步。
在浇注前,需要对铁水进行净化处理,并控制好浇注温度和速度。
浇注过程中要保证铁水充满模具,并防止出现冷缩、缩孔等缺陷。
二、铁水质量控制方法球墨铸铁的铁水质量控制方法主要包括以下几个方面:1.控制原材料的质量:要求铁水、废钢和回炉料的质量符合要求,避免使用劣质原材料。
2.控制熔炼工艺:要求熔炼过程中加入适量的废钢和回炉料,并控制好熔炼温度和时间,避免过热和过冷。
3.控制调整工艺:要求对铁水进行成分和温度的调整,使其符合要求。
4.控制浇注工艺:要求浇注前对铁水进行净化处理,并控制好浇注温度和速度,避免出现冷缩、缩孔等缺陷。
浅谈3种铸铁熔炼法

浅谈3种铸铁熔炼法含碳量在2%以上的铁碳合金,铸铁可分为:①灰口铸铁。
②白口铸铁。
③可锻铸铁。
④球墨铸铁。
⑤蠕墨铸铁。
⑥合金铸铁,本文国际铸业网就为大家介绍铸铁熔炼方法1.冲天炉熔炼法(1)冲天炉构造冲天炉的基本构造示如图1。
炉身、风箱及烟道等用钢板焊成。
炉身内部通常砌以耐火砖层,以便抵御焦碳燃烧产生的高温作用。
为了储存铁液,多数冲天炉都配有前炉。
(2)冲天炉熔炼原理在熔炼过程中,炉身的下部装满焦碳,称为底焦。
在底焦的上面交替装有一批批的铁料(生铁、废钢、回炉料、铁合金等)、焦碳及熔剂(石灰石、萤石等)。
通过鼓风,使底焦强烈燃烧,产生的高温炉气沿炉身高度方向上升,使其上面一层铁料熔化。
(3)冲天炉熔炼的优缺点及其应用冲天炉是最普遍应用的铸铁熔炼设备。
它的优点是:1、用焦炭作燃料,焦炭燃烧产生的热量直接用来熔化炉料和提高铁液温度,在能量消耗方面比电孤炉和其它熔炉节省。
2、设备比较简单,大小工厂皆可采用。
缺点:但冲天炉也存在一定的缺点,主要是由于铁液直接与焦炭接触,故在熔炼过程中会发生铁液增碳和增硫的过程。
采用了冲天炉一电孤炉双联熔炼法或冲天炉一感应电炉双联熔炼法,以充分利用冲天炉熔化效率较高、电孤炉和感应电炉对铁液过热能力强及化学成分控制容易的优点。
2.感应电炉熔炼(1)感应电炉构造及工作原理感应电炉是利用电流感应产生热量来加热和熔化铁料的熔炉。
炉子的构造分为有芯式和无芯式两种,在无芯式感应电炉中,坩埚内的铁料在交变磁场的作用下产生感应电流,并因此产生热量,而将其自身熔化和使铁液过程热。
在有芯式感应电炉中,需要加入用其它熔炉(如冲天炉)熔化的铁液,在环形铁芯内产生的交变磁场使沟槽内的铁液过程,并利用沟槽中铁液与其上面熔池中的铁液循环作用而加热全部铁液。
无芯式感应电炉具有熔化固体炉料的能力,而有芯感应电炉只能过热已熔化的铁液,但在过热铁液的电能消耗方面,则以有芯感应电炉更为节省。
(2)感应电炉熔炼的优缺点及其应用与冲天炉熔炼相比,感应电炉熔炼的优点是1、熔炼过程中不会有增碳和增硫现象,2、熔炼过程可以造渣覆盖铁液,在一定程度上能防止铁液中硅、锰及合金元素的氧化,3、减少铁液从炉气中吸收气体,从而使铁液比较纯净。
铸铁的熔炼技术与规范PPT课件

2)回炉料 它包括浇、冒口,废铸件及废铁等,要按不同牌号、成分分类堆放, 要清除表面黏砂及内部砂芯,破碎成一定块度,加入废钢的目的是降低铸 铁的含碳量,改善力学性能。 3)废钢 它是指废钢件冲压或切割钢材剩下的边角料等。 4)铁合金 铁合金主要用于调整铸铁化学成分和孕育处理,常用的硅铁、锰铁牌 号见表8-4和表8-5。
(3)碱性耐火材料 碱性耐火材料为镁砖及镁砂,MgO的质量分数在85%以上, 能抵抗碱性炉渣的侵蚀,耐火度在2000℃以上。
2. 炉料
冲天炉用炉料由燃料、金属料及熔剂三部分构成。 (1)燃料 冲天炉熔炼的燃料主要用焦炭。我国铸造用焦的成分和性能见表8-1, 焦炭块度大小可按表8-2。
(2)金属料 冲天炉熔炼的金属料包括生铁、回炉料、废钢及铁合金四种。 1)铸造生铁(包括球墨铸铁用生铁) 铸造生铁已有国家标准(见表8-3)。
4. 送风熔化 5. 出铁与放渣
(1)出铁 (2)出渣
6. 停风打炉 五、冲天炉熔炼过程的炉前检验和炉况判断 1. 炉前检验
(1)测量铁液温度 (2)判断铸铁中碳、硅含量
2. 冲天炉的炉况判断
冲天炉的熔化过程是一个复杂的物理、化学变化的过程。 根据冲天炉熔化过程的各种现象所总结整理的判断炉况的资料见表8-6。
4. 冲天炉的熔化率和熔化强度
(1)熔化率 熔化率即冲天炉每小时能熔化铁料的吨数。 (2)熔化强度 熔化强度是反映冲天炉炉膛单位面积熔化铁料能力大小的物理量。
Байду номын сангаас
四、冲天炉的熔炼操作工艺 1. 熔化前的准备工作
熔化前的准备工作包括炉料准备和对修炉后的质量进行 检查。
2. 点火 3. 加料
金属料加料次序为: 生铁→铁合金→回炉料→废钢 (1)层焦的加入 (2)金属料的加入 (3)熔剂的加入
铸铁的熔炼安全方法及其特点

铸铁的熔炼安全方法及其特点铸铁是一种常见的铁炭合金,因其具有良好的铸造性能、机械性能和使用寿命而广泛应用于各种工业领域。
但是,铸铁熔炼工序过程中存在着一定的危险性,需要特殊的安全措施来保护工作人员的生命财产安全。
本文将介绍铸铁的熔炼安全方法及其特点。
铸铁熔炼的安全方法1. 安全防护措施在铸铁熔炼的过程中,需要使用高温、高压、易燃、易爆等物质,因此必须采取一系列的安全防护措施来确保工作人员的安全。
主要包括以下几项:•人员防护:熔炉周围应设置警示标志、安全栏杆、安全带等,保证人员不会接触到高温、高压等危险物质;•器材防护:加入铁炭等物料要使用防护手套、口罩、护目镜等防护器具,以确保物料不会伤及人员;•灭火设备:熔炉周围应该设有灭火器材,以防出现意外火情;•通风设备:铸铁熔炼过程中产生的烟雾等有害气体需要得到及时排出,因此应该设置通风设备,保证空气质量。
2. 操作规范铸铁熔炼操作规范应该得到严格遵守,以确保工作人员的安全。
主要的注意事项包括以下几点:•严禁使用带有铁钉、螺钉等金属杂质的铁炭;•熔炉温度过高时应该适当放缓投料速度,以免熔炉爆炸;•严禁在熔炉周围堆放易燃易爆的物品;•禁止在熔炉口或熔炉周围工作人员接近熔炉,以免烫伤或灼伤。
铸铁熔炼的特点铸铁熔炼的特点主要包括技术要点、生产流程、工艺装备和优点等。
1. 技术要点铸铁熔炼的技术要点主要有以下几点:•在铸铁熔炼过程中,需要严格控制温度,以确保所得产品的性能和品质;•熔炼材料的质量对产品的品质也有很大影响,因此需要使用高质量的铁炭、石油焦等;•铸铁熔炼过程中还需要选择适当的熔炉型号和操作方法,以确保生产效率和产品品质。
2. 生产流程铸铁熔炼的生产流程主要包括以下几个步骤:•预处理:采购符合要求的原料,进行物料配送、过筛和除杂;•熔炼:将铁炭、石油焦等原材料加入熔炉中,采取熔炼技术进行上料、温度控制、熔化等过程;•化验:对所得产品进行化学成分分析、显微组织分析等检测;•出炉:铸造、清理操作后,将所得产品取出炉子;•包装:按照规定,清洗、打码、贴标识等操作后,将成品包装。
铸铁的熔炼方法及其特点
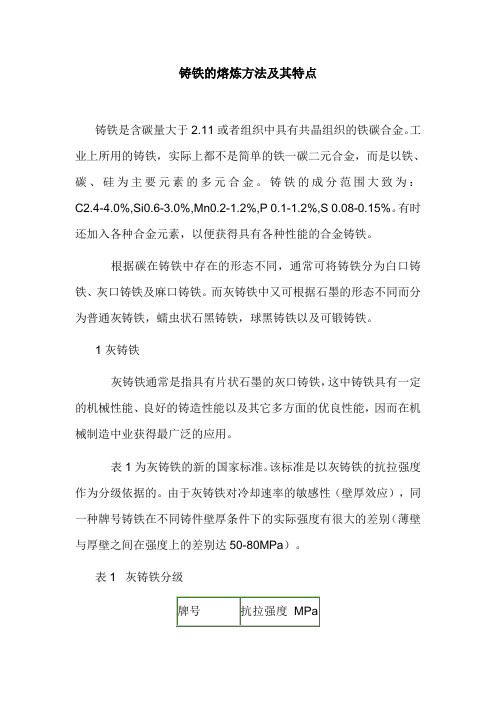
铸铁的熔炼方法及其特点铸铁是含碳量大于2.11或者组织中具有共晶组织的铁碳合金。
工业上所用的铸铁,实际上都不是简单的铁一碳二元合金,而是以铁、碳、硅为主要元素的多元合金。
铸铁的成分范围大致为:C2.4-4.0%,Si0.6-3.0%,Mn0.2-1.2%,P 0.1-1.2%,S 0.08-0.15%。
有时还加入各种合金元素,以便获得具有各种性能的合金铸铁。
根据碳在铸铁中存在的形态不同,通常可将铸铁分为白口铸铁、灰口铸铁及麻口铸铁。
而灰铸铁中又可根据石墨的形态不同而分为普通灰铸铁,蠕虫状石黑铸铁,球黑铸铁以及可锻铸铁。
1 灰铸铁灰铸铁通常是指具有片状石墨的灰口铸铁,这中铸铁具有一定的机械性能、良好的铸造性能以及其它多方面的优良性能,因而在机械制造中业获得最广泛的应用。
表1为灰铸铁的新的国家标准。
该标准是以灰铸铁的抗拉强度作为分级依据的。
由于灰铸铁对冷却速率的敏感性(壁厚效应),同一种牌号铸铁在不同铸件壁厚条件下的实际强度有很大的差别(薄壁与厚壁之间在强度上的差别达50-80MPa)。
表1 灰铸铁分级2 球墨铸铁及蠕墨铸铁球墨铸铁和蠕墨铸铁一般是用稀土镁合金对铁液进行处理,以改善石墨形态,从而得到比灰铸铁有更高机械性能的铸铁。
球墨铸铁依照其基体和性能特点而分为六种:即铁素体(高韧性)球墨铸铁,珠光体(高强度)球墨铸铁,贝氏体(耐磨)球墨铸铁,奥氏体一贝氏体(耐磨)球墨铸铁,马氏体一奥氏体(抗磨)球墨铸铁及奥氏体(耐热、耐蚀)球墨铸铁。
蠕墨铸铁具有不同比例的珠光体—铁素体基体组织。
铸铁性能与其石墨的蠕化程度(蠕化率)及基体有关。
在石墨蠕化良好条件下,珠光体蠕墨铸铁的强度和硬度较高,耐磨性强。
适于制造耐磨零件,如汽车的刹车鼓等。
而铁素体蠕墨铸铁的导热性较好,在高温作用下,不存在珠光体分解问题,组织较稳定,适用于制造在高温下工作、需要有良好的抗热疲劳能力、导热性的零件,如内燃机汽缸盖、进排气岐管等。
3 可锻铸铁可锻铸铁是将白口铸铁通过固态石墨化热处理(包括有或无脱碳过程)得到的具有团絮状石墨的铁碳合金。
铸铁熔炼工艺流程

铸铁熔炼工艺流程
铸铁熔炼工艺流程是指将铁矿石经过一系列的加工和处理,最终转化为铸铁的过程。
铸铁是一种常见的铁合金,具有良好的铸造性能和机械性能,广泛应用于机械制造、建筑、交通等领域。
铸铁熔炼工艺流程主要包括以下几个步骤:
1. 矿石选矿:首先需要从矿山中采集铁矿石,经过破碎、筛分等工艺处理,将矿石中的杂质和非铁金属去除,得到纯净的铁矿石。
2. 炼铁:将铁矿石放入高炉中进行炼铁,炉内温度高达1500℃以上,铁矿石在高温下与焦炭反应,产生还原气体,将铁矿石中的氧化铁还原为铁,同时将矿石中的杂质和非铁金属还原出来,形成炉渣和生铁。
3. 调质:将生铁放入调质炉中进行调质,调整铁中的碳含量和其他合金元素的含量,使其达到铸造要求。
4. 熔炼:将调质后的铁放入熔炉中进行熔炼,加入适量的废钢、废铁等回收材料,控制炉温和炉内气氛,使铁液中的杂质和气体得以排除,形成纯净的铸铁液。
5. 浇铸:将铸铁液倒入铸型中进行浇铸,待铸铁冷却凝固后,取出铸件,进行后续的加工和处理。
以上就是铸铁熔炼工艺流程的主要步骤。
在实际生产中,还需要根
据不同的铸造要求和工艺特点,进行相应的调整和改进。
铸铁熔炼工艺的优化和改进,可以提高铸铁的质量和产量,降低生产成本,促进工业的发展。
铸铁熔炼温度

铸铁熔炼温度
铸铁熔炼温度是指将铸铁炉料加热至足够高的温度,使其完全熔化并具有一定的流动性,以便铸造成型。
一般而言,铸铁熔炼温度受到多种因素的影响,包括铸铁材料的类型、成分、加热方式、炉型和铸造要求等。
不同类型的铸铁其熔炼温度也不尽相同。
例如,灰铸铁的熔点通常在1100℃左右,而球墨铸铁的熔点则要高一些,一般在1200℃以上。
铸铁的熔炼温度还会受到其成分的影响,如含碳量和合金元素的添加等。
一般来说,含碳量越高的铸铁,其熔点也就越高。
在炉型和加热方式方面,铸铁的熔炼温度也有所不同。
传统的铁皮炉、高炉等炉型通常采用燃煤、燃油等传统燃料进行加热,熔炼温度相对较低,且易产生污染物。
而现代的电弧炉、感应炉等炉型则采用电能进行加热,熔炼温度较高且能耗低。
最后,铸造要求也是影响铸铁熔炼温度的重要因素。
不同的铸造要求需要不同的熔炼温度来满足。
例如,需要铸造大型零件时,熔炼温度需要更高,以确保炉料能够充分流动,并填满模具中的空隙。
综上所述,铸铁熔炼温度是一个相对复杂的问题,需要考虑多种因素来确定。
在生产实践中,需要根据具体情况进行优化,以达到最佳的铸造效果。
- 1 -。
- 1、下载文档前请自行甄别文档内容的完整性,平台不提供额外的编辑、内容补充、找答案等附加服务。
- 2、"仅部分预览"的文档,不可在线预览部分如存在完整性等问题,可反馈申请退款(可完整预览的文档不适用该条件!)。
- 3、如文档侵犯您的权益,请联系客服反馈,我们会尽快为您处理(人工客服工作时间:9:00-18:30)。
三、金属炉料对冲天炉铁液温度的影响
金属炉料块度
大:预热、熔化时间长,熔化区下移,过热区缩短。
卡料,炉料不能均匀下移,恶化热交换条件。 小:阻塞气流通道,造成严重氧化。 一般最大料块尺寸应小于1/3炉内径 炉料的纯洁度 表面的泥沙和铁锈,阻碍料块受热,熔融成渣消耗 热量
四、熔炼操作参数对冲天炉铁液温度的影响
送风位置 侧部送风 侧部插入式 中央送风
中央送风冲天炉
整体结构
直筒型,整块式炉底门 盅罩保护
中央风嘴
钢管,耐火泥和石英砂
主要特点
1 供风均匀,炉衬侵蚀小
削弱炉壁效应,减少炉壁冲刷,降低鼓风消耗,充分利用小 块焦炭
2 结构简单,炉况较稳定
炉体结构和送风系统简单而严密,漏风少,风口尺寸稳定, 炉衬侵蚀小,炉膛尺寸稳定,炉况稳定
程度增大,CO比CO2具有更大
的稳定性
炉气燃烧比
概念 意义:
v
CO2 100 % CO2 CO
10200 23800 v 100 % 34000
燃料利用率: A
炉气性质:判断氧化性或还原性 燃烧温度:ηv增加,温度上升 燃烧产物量:燃烧产物脱离焦炭层时的气相成分
四 冲天炉内焦炭燃烧
扩大过热区,铁液温度提高
批料层过薄:铁焦混杂串料 成分与温度波动大
五、冲天炉结构参数对铁液温度的影响
1、炉型的影响(气温分布)
缩小送风区直径:
送风强度提高、有利穿透 炉气均匀、强化燃烧。 扩大溶化区直径: 溶化强度提高、溶化区域 小,提高平均熔化区高度。 缩小加料口直径: 下料均匀、减少炉壁效应
2、风口布置的影响
二、送风对冲天炉铁液温度的影响
1、风量的影响
风量提高 进风速度、炉内气体流动速度
空气量提高,强化燃烧、扩大
氧化带、提高高温区温度。 提高燃烧速度、料层下降快、 过热区高度缩短, 过热不足。 最佳送风量(最惠风量)
2、风速的影响
提高风速:风口处平均流速 (风量不变,截面改变)
穿透能力提高 清除焦碳表面灰渣 减少炉衬侵蚀 对焦碳吹冷 加大元素烧损 增加送风动能 国内小风口40-60m/s 国外10m/s
双层送风冲天炉
炉型与风口布置 曲线炉膛 两排倒置风口
主要特点
双层燃烧 热量上移
风口角度:5-20,30-75 改善炉气分布 克服炉壁效应
卡腰三节炉
结构概况
上节,中节炉身 下入炉缸
斜度大,深入炉缸,强 化燃烧,利于过热
炉气分布均匀
削弱了炉壁效应,炉壁 冲刷轻
六、冲天炉的网形图
2、焦碳的性质、块度、强度和气孔率
焦碳的性质:
发热量Q;单位重量焦碳完全燃烧所放出的热量 Q=34000(1-A)千焦/公斤
反应性R:焦碳还原CO2的能力 CO R= %
2CO2+CO
焦碳的块度:
影响冲天炉氧化带高度,块度提高空隙加大有利于 径确定。
焦碳强度:
燃
烧。块度过大,反应面积减少不利于燃烧,根据炉堂直
tT 2243
三、焦碳层状燃烧
固体块状燃料呈层状堆积时所进行的燃烧(冲天炉底焦)
1焦碳燃烧的反应过程
加热着火
放热大于散热
动力燃烧
化学反应控制
扩散燃烧
氧扩散控制
2、焦碳的层状燃烧过程
氧化带 氧基本消失,CO2达到最 大值
还原带
氧化带顶面至恒定区 干燥带
氧化带
燃烧反应
C+O2=CO2
二、冲天炉熔炼原理及工艺过程 1、工艺过程:
修炉烘炉 点火加底焦 加料
送风熔化
连续加料
停风打炉
2、工作过程
焦碳燃烧:热量的来源,形成高温炉气和炽热的 焦碳表面。
热交换: 向上运动的高温炉气和炽热的焦碳表 面与向下运动的炉料间进行,使炉料 预热、熔化、过热。
冶金反应:由于高温、炉气、炉渣与元素间反应 而使金属液成分变化。
获得高温铁水的关键
炉气最高温度和
过热区的高度
Δt=αh(tmax—tm)
(四)炉缸区的热交换 冷却区----没有空气供给焦碳不燃烧。 开渣口操作----可以利于铁液过热。
第三节 影响铁液温度的主要因素 一、焦碳对冲天炉铁液温度的影响
固定碳含量高 大于85% 块度适当大、强度高 低的反应能力 小于30 %
3 氧化烧损大
焦炭运行失常造成的风口区内焦炭层中较大的空隙时氧化烧 损的主要原因(焦炭块度过大,风量风速过大,结渣,风渣帽)
风口排数
单排风口:燃烧集中
多排风口:气流均匀 主副倒置:意见不统一
多排小风口冲天炉
整体结构
曲线炉膛,炉体五节:活动炉缸, 1-5排风口区,6-7排风口区 热风炉胆,钢板圈
主风口
缺点:
铁水温度、成分不易控制,增碳、增硫。
铁水中非金属夹杂物和含气量较多。
铁及合金元素有一定烧损。
对炉料和焦炭有一定要求。
过热能力较差。
必须有高效的除尘装置。
2、电炉
电弧炉
电弧炉熔炼的优缺点: 温度高
可以脱硫磷
可以减少合金元素氧化烧损
对炉料要求不严格
耗电量大 易使钢液含气量增加 炉中钢液温度不均匀
2C+O2=2CO
ΔQ=34070kj/kg
ΔQ=10270kj/kg ΔQ=23800kj/kg
2CO+O2=2CO2
还原带
CO2+C=2CO ΔQ=-162500kj/kg
燃烧热力学特性
1.氧化反应能自发进行,还原反应 978K以上具有自发进行可能性。
2. 978K时碳氧化燃烧具有相同的
反应趋势。 3.温度低于978K 2CO+O2=2CO2 反应进行的完全程度最大。 4.温度高于978K放热反应进行不 利 ,生成CO比CO2具有更大的 稳定性。 5.温度高于978K,还原反应进行
1、底焦高度 理论底焦高度H1,实际底焦高度Ho Ho>H1 空烧、
焦耗大、溶化率低
预热充分、溶化区窄位置 高、有利过热。 H0<H1 溶化带下移、落生, 铁液温度低、氧化严重
溶化速度快
2.焦碳消耗量
每批层焦量=溶化每批金属料的底焦烧失量
每批层焦的底焦烧失时间=每批金属料的溶化
时间
3、批料量
减少批料量:溶化时间缩短 溶化区缩小、平均位置提高
基本控制因素:焦耗、风量 重要指标:温度、生产率 焦耗一定:风量 风量一定:焦耗
生产率 温度 生产率温度
要求生产率一定:
低焦耗低风量——温度低 高焦耗高风量——温度高 要求一定铁水温度: 最佳配合是最佳送风量与
所需温度和焦耗线的交点
金属炉料不接触燃料和炉气.
金属液成分稳定,烧损少.
热效率低5-8%.
4 煤粉化铁炉
煤粉化铁炉熔炼特点
煤粉与空气充分混合,燃烧充分,燃料利 用率高 高温炉气和炉壁热作用,过热效果差。 (过桥,火道,竖炉底) 空气过剩,硅,锰烧损大,脱碳明显,利 于低碳铁水
5、反射炉
是借助于高温炉气和炉顶热幅射加热和熔化的, 可以熔化大量金属液,可以把巨型废件整体重熔, 对炉料和燃料要求不严格. 有周期式和连续式熔化的不同形式. 热效率低12-15%. 占地面积大,熔化速度慢. 金属元素烧损多.
第三排,2+3=66%
热风装置:密筋片式
主要特点
1 多排倒置式小风口
提高风速,强化高灰份小粒度焦炭燃烧,改善气流分布, 鼓风能耗高
2 曲线炉膛--扩大了熔化区
(1)强化底焦燃烧,削弱炉壁效应(风口区小) (2) 改善下料均匀性,充分利用炉膛容积
(3) 提高熔化区位置,改善熔化区形状
3 热风炉胆
提高理论燃烧温度200度
承受炉料的冲击和挤压,防止破碎。强度高反应性下降。
焦碳的气孔率:
焦碳内气孔的体积占包括气孔在内的焦碳体积的百分数。
气孔率提高反应面积加大,反应性提高35-45%
二、焦炭发热量计算与燃烧计算
发热量:单位重量的固体燃料或液体燃料,或标态下
单位体积的气体燃料,经完全燃烧,且燃烧产物冷却 到反应物质的温度时所放出的热量。 焦炭发热量:
燃烧过程存在固态炉料和溶剂 的作用 燃烧比与焦炭消耗 熔化率与风量和焦耗 低焦耗,弱送风,精控制 风量与炉气成分 影响不大:还原强,氧化带 高,还原区短,两方面作用 抵消 炉气成分可计算出风量
焦炭燃烧主要影响因素
焦炭:粒度,成份,发热量,反应性,强度 送风:送风位置,风口结构,风量,风速,风温,
含氧量,适度
铸铁的熔炼
第一章 概论
第一节 熔炼的基本要求
1
、铁水质量高---成分、温度、纯净。
2、融化速度快---予热、熔化、过热。 3、熔耗少---元素、电力、燃料、炉衬。 4、操作方便
5、符合环保要求
优质、高产、低耗、无污染
第二节 熔炼设备
1、冲天炉
优点:
结构简单 热效率高
占地面积小
生产成本低 操作方便 生产效率高 连续生产
3、风温的影响
提高进入空气的温度
增加氧化带的热量
强化燃烧速度 提高炉气最高温度
缩短氧化区域 加剧co2的还原 降低炉气燃烧比
4、风中氧的浓度的影响 富氧送风
加速底焦的燃烧速度,与热风效果相似
增加CO2的浓度.
风中含氧量增加3%,提高炉气最高温度
相当400º C热风的熔炼效果.
氧化带缩短、还原带扩大
第二章 冲天炉内焦碳燃烧的基本规律
一、焦碳的基本组成与性质
1、焦碳的基本组成
碳C(固定碳含量):热量来源 80-87% 挥发分Л:可燃气体CO、H2、CH4、小于1.5% 硫S:有害元素小于1.2% 灰份A:不可燃部分CaO、MgO、SiO2、Al2O3、