齿轮齿条传动设计计算
齿轮齿条传动计算和选型
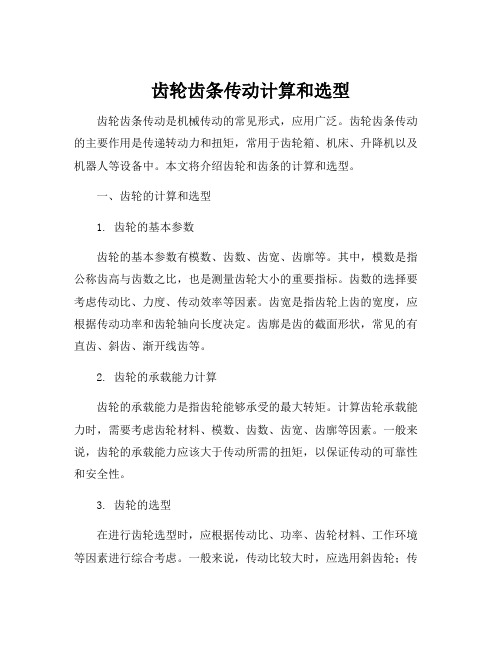
齿轮齿条传动计算和选型齿轮齿条传动是机械传动的常见形式,应用广泛。
齿轮齿条传动的主要作用是传递转动力和扭矩,常用于齿轮箱、机床、升降机以及机器人等设备中。
本文将介绍齿轮和齿条的计算和选型。
一、齿轮的计算和选型1. 齿轮的基本参数齿轮的基本参数有模数、齿数、齿宽、齿廓等。
其中,模数是指公称齿高与齿数之比,也是测量齿轮大小的重要指标。
齿数的选择要考虑传动比、力度、传动效率等因素。
齿宽是指齿轮上齿的宽度,应根据传动功率和齿轮轴向长度决定。
齿廓是齿的截面形状,常见的有直齿、斜齿、渐开线齿等。
2. 齿轮的承载能力计算齿轮的承载能力是指齿轮能够承受的最大转矩。
计算齿轮承载能力时,需要考虑齿轮材料、模数、齿数、齿宽、齿廓等因素。
一般来说,齿轮的承载能力应该大于传动所需的扭矩,以保证传动的可靠性和安全性。
3. 齿轮的选型在进行齿轮选型时,应根据传动比、功率、齿轮材料、工作环境等因素进行综合考虑。
一般来说,传动比较大时,应选用斜齿轮;传动功率较大时,应选用韧性好、强度高的材料制作齿轮;在高温、潮湿等恶劣环境下,应选用耐腐蚀的齿轮材料。
二、齿条的计算和选型1. 齿条的基本参数齿条的基本参数有模数、齿数、齿高、齿距等。
齿条的模数应与齿轮相配合,齿数应根据所传动的齿轮数确定。
齿高是指齿条齿与齿沟之间的垂直距离,齿距是指齿条两相邻齿的中心距离,齿高和齿距的大小比决定了齿条的传动精度。
2. 齿条的承载能力计算齿条的承载能力应考虑齿条材料、模数、齿数、齿高、齿距、传动功率等因素。
一般来说,齿条的承载能力应不小于传动所需的扭矩,以保证传动的可靠性和安全性。
3. 齿条的选型齿条的选型应根据传动比、齿条材料、功率、工作环境等因素进行综合考虑。
一般来说,选用韧性好、强度高、耐磨损、耐腐蚀的材料制作齿条,以保证齿条的使用寿命和可靠性。
同时,应根据传动功率和齿条长度确定齿条的截面形状和尺寸。
在选用齿条时,还应注意与传动齿轮的配合,确保传动精度。
齿轮齿条的传动计算[高效]
![齿轮齿条的传动计算[高效]](https://img.taocdn.com/s3/m/3f6e299382d049649b6648d7c1c708a1284a0ac7.png)
齿轮齿条的传动计算齿轮与齿条传动特点齿轮作回转运动,齿条作直线运动,齿条可以看作一个齿数无穷多的齿轮的一部分,这时齿轮的各圆均变为直线,作为齿廓曲线的渐开线也变为直线。
齿条直线的速度v 与齿轮分度圆直径d 、转速n 之间的关系为v=(/)60dn mm s π式中 d ——齿轮分度圆直径,mm ;n ——齿轮转速,min r 。
其啮合线12N N 与齿轮的基圆相切1N ,由于齿条的基圆为无穷大,所以啮合线与齿条基圆的切点2N 在无穷远处。
齿轮与齿条啮合时,不论是否标准安装(齿轮与齿条标准安装即为齿轮的分度圆与齿条的分度圆相切),其啮合角'α恒等于齿轮分度圆压力角α,也等于齿条的齿形角;齿轮的节圆也恒与分度圆重合。
只是在非标准安装时,齿条的节线与分度线不再重合。
齿轮与齿条正确啮合条件是基圆齿距相等,齿条的基圆齿距是其两相邻齿廓同侧直线的垂直距离,即cos cos b P P m απα==。
齿轮与齿条的实际啮合线为12B B ,即齿条顶线及齿轮齿顶圆与啮合线12N N 的交点2B 及1B 之间的长度。
齿轮齿条传动的几何尺寸计算 齿轮与齿条传动的尺寸计算见表齿条的主要特点:(1)由于齿条齿廓为直线,所以齿廓上各点具有相同的压力角,且等于齿廓的倾斜角,此角称为齿形角,标准值为20°。
(2)与齿顶线平行的任一条直线上具有相同的齿距和模数。
(3)与齿顶线平行且齿厚等于齿槽宽的直线称为分度线(中线),它是计算齿条尺寸的基准线。
齿轮的模数为1,齿数为11则,分度圆直径 d=m*z=11mm 周长:34.54mm齿条的速度:20*34.54*0.001/60=0.69m/s扭矩45kgf.cm转换单位为 45*9.8*0.01=4.41Nm齿条推力4.41/(11*0.001)=400.9N 齿条受到的力=T/r(齿轮半径)不知道是否对?。
齿轮齿条传动计算
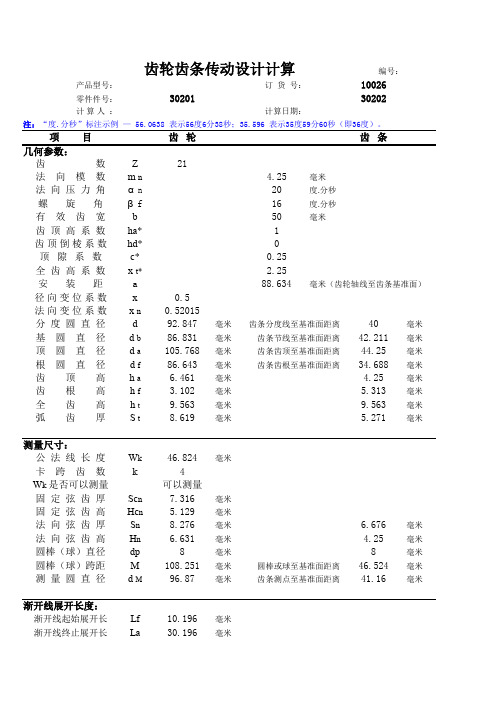
齿轮齿条传动设计计算 编号:产品型号:订货号:10026零件件号:3020130202计算人 :计算日期:注:“度.分秒”标注示例 — 56.0638 表示56度6分38秒;35.596 表示35度59分60秒(即36度)。
项目齿轮齿条几何参数:齿数Z21法向模数m n 4.25毫米法向压力角αn20度.分秒螺旋角βf16度.分秒有效齿宽b50毫米齿顶高系数ha*1齿顶倒棱系数hd*0顶隙系数c*0.25全齿高系数x t* 2.25安装距a88.634毫米(齿轮轴线至齿条基准面)径向变位系数x0.5法向变位系数x n0.52015分度圆直径d92.847毫米齿条分度线至基准面距离40毫米基圆直径 d b86.831毫米齿条节线至基准面距离42.211毫米顶圆直径 d a105.768毫米齿条齿顶至基准面距离44.25毫米根圆直径 d f86.643毫米齿条齿根至基准面距离34.688毫米齿顶高h a 6.461毫米 4.25毫米齿根高h f 3.102毫米 5.313毫米全齿高h t9.563毫米9.563毫米弧齿厚S t8.619毫米 5.271毫米测量尺寸:公法线长度W k46.824毫米卡跨齿数k4W k 是否可以测量可以测量固定弦齿厚Sc n7.316毫米固定弦齿高Hc n 5.129毫米法向弦齿厚S n8.276毫米 6.676毫米法向弦齿高H n 6.631毫米 4.25毫米圆棒(球)直径dp8毫米8毫米圆棒(球)跨距M108.251毫米圆棒或球至基准面距离46.524毫米测量圆直径 d M96.87毫米齿条测点至基准面距离41.16毫米渐开线展开长度:渐开线起始展开长Lf10.196毫米渐开线终止展开长La30.196毫米起始点(齿根)θf13.2721度.分秒终止点(齿顶)θa39.5102度.分秒中凸点范围θmin22.1514度.分秒θmax31.0308度.分秒传动质量指标算:重合度ε总 3.052根切不根切齿顶变尖齿顶未变尖齿顶未变尖公差值:(按 GB10095—88 渐开线圆柱齿轮 精度,GB10096—88 齿条精度)精度等级Ⅰ:8Ⅱ:7Ⅲ:7齿厚极限偏差代码上偏差下偏差齿厚上偏差Ess-0.1毫米-0.15毫米齿厚下偏差Esi-0.2毫米-0.25毫米齿厚公差Ts0.1毫米0.1毫米最小法向侧隙jn min0.25毫米最大法向侧隙jn max0.45毫米公法线平均长度上下偏差及公差:GB 10095—88Ews-0.106毫米Ewi-0.176毫米Ew0.07毫米圆棒(球)跨距上下偏差及公差:GB 10095—88Ems-0.217毫米-0.206毫米Emi-0.361毫米-0.343毫米Em0.144毫米0毫米切向综合公差F'i0.077毫米0.139毫米一齿切向综合公差f'i0.019毫米0.063毫米齿距累积公差F P0.063毫米0.105毫米齿距极限偏差±f pt0.018毫米0.028毫米基节极限偏差±f pb0.016毫米齿形 公差 f f0.014毫米0.034毫米齿向 公差Fβ0.016毫米齿面接触斑点按高度45%按长度60%X方向轴线平行度公差 f x0.016毫米Y方向轴线平行度公差 f y0.008毫米安装距极限偏差±f a0.027毫米齿坯公差:孔径尺寸公差IT7GB 1800—79孔径形状公差IT6GB 1800—79顶圆尺寸公差(用作基准)IT8GB 1800—79(不用作基准)IT11, 但不大于0.425毫米图样标注: 齿轮18-7-7-0.1GB 10096—88-0.2齿轮28-7-7-0.15GB 10096—88-0.25注:齿厚上、下偏差两边加括号。
齿轮齿条的设计计算与校核
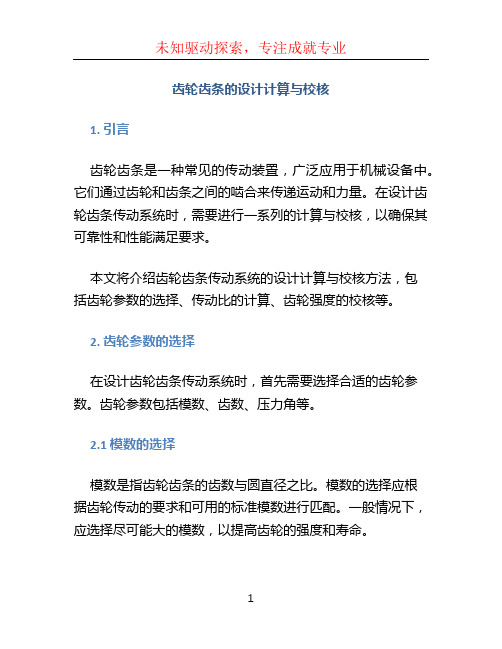
齿轮齿条的设计计算与校核1. 引言齿轮齿条是一种常见的传动装置,广泛应用于机械设备中。
它们通过齿轮和齿条之间的啮合来传递运动和力量。
在设计齿轮齿条传动系统时,需要进行一系列的计算与校核,以确保其可靠性和性能满足要求。
本文将介绍齿轮齿条传动系统的设计计算与校核方法,包括齿轮参数的选择、传动比的计算、齿轮强度的校核等。
2. 齿轮参数的选择在设计齿轮齿条传动系统时,首先需要选择合适的齿轮参数。
齿轮参数包括模数、齿数、压力角等。
2.1 模数的选择模数是指齿轮齿条的齿数与圆直径之比。
模数的选择应根据齿轮传动的要求和可用的标准模数进行匹配。
一般情况下,应选择尽可能大的模数,以提高齿轮的强度和寿命。
2.2 齿数的选择齿数的选择主要考虑齿轮传动的传动比和齿轮的工作条件。
传动比是指齿轮输入轴的转速与输出轴的转速之比。
2.3 压力角的选择压力角是指齿轮齿条啮合面上法线与齿轮轴线之间的夹角。
压力角的选择应根据齿轮传动的要求和可用的标准压力角进行匹配。
一般情况下,应选择尽可能小的压力角,以减小齿轮齿条的侧向力和噪声。
3. 传动比的计算传动比是齿轮齿条传动系统中重要的性能指标之一,它影响着输出轴的转速和扭矩。
传动比的计算可以根据齿轮齿数的比值来确定。
4. 齿轮强度的校核齿轮强度是齿轮齿条传动系统设计中关键的校核指标之一,它决定了齿轮的承载能力和寿命。
齿轮强度的校核可以通过齿轮的材料强度和几何参数来确定。
4.1 齿轮模数的校核齿轮模数的校核可以通过计算齿轮的接触应力和弯曲应力来进行。
应保证齿轮的接触应力和弯曲应力不超过齿轮材料的强度极限。
4.2 齿轮齿数的校核齿轮齿数的校核可以通过计算齿轮的接触比和模数来进行。
应保证齿轮的接触比和模数满足设计要求。
4.3 齿轮强度的校核齿轮强度的校核可以通过计算齿轮的接触疲劳寿命来进行。
应保证齿轮的接触疲劳寿命不低于设计要求。
5. 结论齿轮齿条的设计计算与校核是确保齿轮齿条传动系统可靠性和性能的重要环节。
齿轮齿条传动计算公式

齿轮齿条传动计算公式
齿轮齿条传动是机械变速箱中常用的传动方式,它可以实现机械拖拉机的传动功率变化,以满足不同转速和功率需求。
齿轮齿条传动的计算公式是求解机械传动系统的一种基本方法。
齿轮齿条传动计算公式一般由四个参数组成:齿轮直径d、齿轮压力角α、齿条节距p和齿条压力角β。
其中,齿轮直径d表示齿轮的外径,齿轮压力角α表示齿轮的压力角,齿条节距p表示齿条的节距,齿条压力角β表示齿条的压力角。
齿轮齿条传动计算公式的基本形式是:
传动比=齿轮直径d×cosα÷(齿条节距p×cosβ)
其中,传动比是指齿轮齿条传动中齿轮转速与齿条转速的比值,也就是传递功率的比值。
为了得到更精确的传动比,还需要考虑一些其他因素,比如:齿轮和齿条的齿数、齿轮和齿条材料的强度和硬度等。
此外,还需要考虑齿轮齿条传动中齿轮和齿条的装配精度,以及齿轮齿条传动系统的摩擦损失、噪声等。
在设计齿轮齿条传动时,除了使用计算公式外,还需要考虑传动特性、动力学分析、摩擦学分析等。
以上内容是关于齿轮齿条传动计
算公式的基本介绍,希望能够帮助大家了解齿轮齿条传动的计算方法。
齿轮齿条设计计算公式

齿轮齿条设计计算公式齿轮和齿条是机械传动中常见的元件,用于传递动力和转速。
齿轮齿条的设计计算是设计师在进行齿轮齿条设计时所必须掌握的知识。
本文将介绍齿轮齿条设计计算的一些基本公式和原理。
一、齿轮设计计算公式1. 齿数计算公式齿数是齿轮设计中最基本的参数之一,可以通过以下公式计算:N = (π * D) / m其中,N为齿数,D为齿轮直径,m为模数。
2. 齿轮间距计算公式齿轮间距是指两个相邻齿轮之间的中心距离,可以通过以下公式计算:P = (N1 + N2) / 2 * m其中,P为齿轮间距,N1和N2分别为两个相邻齿轮的齿数,m为模数。
3. 齿轮传动比计算公式齿轮传动比是指两个相邻齿轮的转速之比,可以通过以下公式计算:i = N2 / N1其中,i为传动比,N1和N2分别为两个相邻齿轮的齿数。
4. 齿轮模数计算公式齿轮模数是指齿轮齿数和齿轮直径之间的比值,可以通过以下公式计算:m = D / N其中,m为模数,D为齿轮直径,N为齿数。
二、齿条设计计算公式1. 齿条模数计算公式齿条模数是指齿条齿数和齿条长度之间的比值,可以通过以下公式计算:m = L / N其中,m为模数,L为齿条长度,N为齿数。
2. 齿条传动比计算公式齿条传动比是指齿条的移动距离与齿轮转动角度之间的比值,可以通过以下公式计算:i = L / (π * D)其中,i为传动比,L为齿条的移动距离,D为齿轮的直径。
3. 齿条齿数计算公式齿条齿数是指齿条上的齿数,可以通过以下公式计算:N = L / m其中,N为齿数,L为齿条长度,m为模数。
三、齿轮齿条设计计算实例假设有一对齿轮,其中一个齿轮的齿数为20,直径为40mm,另一个齿轮的齿数为40,直径为80mm,模数为2mm。
我们可以通过上述公式进行计算。
根据齿数计算公式,可得第一个齿轮的齿数为20,第二个齿轮的齿数为40。
根据齿轮间距计算公式,可得齿轮间距为(20+40)/2*2=60mm。
电动助力转向系统中齿轮齿条传动设计与计算_刘庚寅

收稿日期:2012-09-14作者简介:刘庚寅(1970—),男,汉,湖南邵东人,硕士研究生,研究方向:汽车电动助力转向系统。
E-mail :lgy960@ 。
电动助力转向系统中齿轮齿条传动设计与计算刘庚寅,刘晟昱,彭微君,葛阳清,康永升(株洲易力达机电有限公司,湖南株洲412002)摘要:介绍了P-EPS 电动助力转向系统的传动原理及其主要零部件。
特别是就某一车型的P-EPS 齿轮齿条的设计计算进行了详细的分析。
对不同载荷车型的齿轮齿条模数和齿数的匹配分别进行了计算,为新产品的开发提供了参考和指导。
关键词:电动助力转向系统;P-EPS ;齿轮轴;齿条轴Design and Calculation on Transmission between Pinion andRack in Electric Power Steering SystemLIU Gengyin ,LIU Shengyu ,PENG Weijun ,GE Yangqing ,KANG Yongsheng (Zhuzhou Elite Electro Mechanical Co.,Ltd.,Zhuzhu Hunan 412002,China )Abstract :The theory and main components of P-EPS electric power steering system were introduced here.Especially ,the design and calculation for rack and pinion of P-EPS about one car were analyzed in detail.Also ,matching relation between modulus and teeth number of rack and pinion were separately calculated for different car types with different weight ,so the reference and guides were provided for the devel-opment of new products.Keywords :Electric power steering system ;P-EPS ;Pinion ;Rack0前言国产电动助力转向系统(EPS )经过十几年的探索与研究,技术日趋成熟,并以其相对传统液压转向系统的突出优点而得到众多汽车厂家的认可,并在中小排量汽车上得到了广泛应用。
齿轮齿条的传动计算

齿轮齿条的传动计算齿轮齿条传动是一种常见的传动方式,广泛应用于机械设备中。
它具有传动效率高、传动精度高、传动比稳定等特点,适用于输送大扭矩和远距离运动的场合。
下面,我将详细介绍齿轮齿条传动的计算方法。
齿轮齿条传动的计算步骤大致可以分为以下几个方面:齿轮参数的选择、齿轮齿条的传动比计算、齿轮齿条传动的力学计算。
第一步,齿轮参数的选择。
在进行齿轮齿条传动计算之前,需要确定齿轮和齿条的参数。
齿轮一般由模数、齿数、齿轮轴的直径等参数组成,而齿条则由模数、齿数和长度等参数组成。
根据实际应用情况,可以根据传动的扭矩和速度要求选择合适的齿轮和齿条参数。
第二步,齿轮齿条的传动比计算。
传动比是指齿轮齿条传动时输入轴的转速与输出轴的转速之比。
传动比的计算公式如下:传动比=齿轮的齿数/齿条的齿数根据传动比的计算公式可以得到齿轮齿条传动的传动比。
第三步,齿轮齿条传动的力学计算。
齿轮齿条传动的力学计算主要包括齿轮的扭矩、齿轮的受力分析等。
首先,根据输入轴的扭矩和传动比可以计算出输出轴的扭矩。
其次,根据齿轮的齿数、模数和齿轮材料的弹性模量可以计算出齿轮的受力情况,包括齿面接触应力、齿面接触疲劳寿命等。
齿轮齿条传动的计算需要注意以下几点:1.在选择齿轮和齿条的参数时,需要根据传动的实际应用情况来确定。
例如,如果传动的扭矩较大,则需要选择齿数较多的齿轮和较宽的齿条,以提高传动的承载能力。
2.在计算齿轮齿条的传动比时,需要确保齿轮和齿条的齿数之间存在整数关系,以保证传动的稳定性。
3.在进行齿轮齿条传动的力学计算时,需要考虑材料的强度和齿轮的受力情况,以确保传动的可靠性。
综上所述,齿轮齿条传动的计算是一项复杂的工作,需要考虑多个因素。
只有正确选择齿轮和齿条的参数,并进行合理的力学计算,才能确保齿轮齿条传动的正常工作。
通过对齿轮齿条传动的计算和分析,可以提高传动效率和传动精度,实现机械设备的稳定运行。
- 1、下载文档前请自行甄别文档内容的完整性,平台不提供额外的编辑、内容补充、找答案等附加服务。
- 2、"仅部分预览"的文档,不可在线预览部分如存在完整性等问题,可反馈申请退款(可完整预览的文档不适用该条件!)。
- 3、如文档侵犯您的权益,请联系客服反馈,我们会尽快为您处理(人工客服工作时间:9:00-18:30)。
1.选定齿轮类型、精度等级、材料级齿数
1)选用直齿圆柱齿轮齿条传动。
2)速度不高,故选用7级精度(GB10095-88)。
3)材料选择。
由表10-1选择小齿轮材料为40Cr(调质),硬度为280HBS,齿条材料为45钢(调质)硬度为240HBS。
4)选小齿轮齿数Z1=24,大齿轮齿数Z2=∞。
2.按齿面接触强度设计
由设计计算公式进行计算,即
d1t ≥2.32√K t T1
φd
∙
u+1
u
(
Z E
[σH]
)2
3
(1)确定公式内的各计算数值
1)试选载荷系数K t =1.3。
2)计算小齿轮传递的转矩。
(预设齿轮模数m=8mm,直径d=160mm)
T1=95.5×105P1
n1
=
95.5×105×0.2424
7.96
=2.908×105N∙mm
3) 由表10-7选齿宽系数φd=0.5。
4)由表10-6查得材料的弹性影响系数Z E=189.8MPa 1 2。
5)由图10-21d按齿面硬度查得小齿轮的接触疲劳强度极限σHlim1=600MPa;齿条的接触疲劳强度极限σHlim2=550MPa。
6)由式10-13计算应力循环次数。
N1=60n1jL h=60×7.96×1×(2×0.08×200×4)=6.113×104
7)由图10-19取接触疲劳寿命系数K HN1=1.7。
8)计算接触疲劳许用应力。
取失效概率为1%,安全系数S=1,由式(10-12)得
[σH]1=K HN1σHlim1
S
=1.7×600MPa=1020MPa
(2)计算
1)试算小齿轮分度圆直径d t1,代入[σH]1。
d 1t ≥2.32√K t T 1φd ∙u +1u (Z E [σH ])23
=2.32√1.3×2.908×1050.5∙∞+1∞ (189.81020)23=68.89mm
2)计算圆周速度v 。
v =πd 1t n 160×1000=π×68.89×7.9660×1000
=0.029m s ⁄ 3)计算齿宽b 。
b =φd ∙d 1t =0.5×68.89=34.445mm
4)计算齿宽与齿高之比b h 。
模数
m t =d 1t z 1=68.8924
=2.87 齿高
h =2.25m t =2.25×2.87=6.46mm
b h =34.4456.46
=5.33 5)计算载荷系数。
根据v =0.029m/s ,7级精度,由图10-8查得动载荷系数K V =1;
直齿轮,K Hα=K Fα=1;
由表10-2查得使用系数K A =1.5;
由表10-4用插值法查得7级精度、小齿轮为悬臂布置时K Hβ=1.250。
由b h =5.33,K Hβ=1.250查图10-13得K Fβ=1.185;故载荷系数
K =K A K V K HαK Hβ=1.5×1×1×1.250=1.875
6)按实际的载荷系数校正所算得的分度圆直径,由式(10-10a )得
d 1=d 1t √K K t 3=68.89×√1.8751.33=77.84mm 7)计算模数m 。
m =
d 1z 1=77.8424
=3.24mm 3. 按齿根弯曲强度设计
由式(10-5)得弯曲强度设计公式为
m≥√2KT1
φd z12(
Y Fa Y Sa [σF]
)
3
(1)确定公式内各计算数值
1)由图10-20c查得小齿轮的弯曲疲劳强度极限σFE1=500MPa;齿条的弯曲强度极限σFE2=380MPa;
2)由图10-18取弯曲疲劳寿命系数K FN1=1.1,K FN2=1.2;
3)计算弯曲疲劳许用应力。
取弯曲疲劳安全系数S=1.4,由式(10-12)得
[σF]1=K FN1σFE1
S
=
1.1×500
1.4
=392.86MPa
[σF]2=K FN2σFE2
S
=
1.2×380
1.4
=325.71MPa
4)计算载荷系数K。
K=K A K V K FαK Fβ=1.5×1×1×1.185=1.78 5)查取齿形系数。
由表10-5查得Y Fa1=2.65, Y Fa2=2.06。
6)查取应力校正系数。
由表10-5查得Y Sa1=1.58,Y Sa2=1.97。
7)计算齿轮齿条的Y Fa Y Sa
[σF]
并加以比较。
Y Fa1Y Sa1 [σF]1=
2.65×1.58
392.86
=0.01066
Y Fa2Y Sa2 [σF]2=
2.06×1.97
325.71
=0.01246
齿条的数值大。
(2)设计计算
m≥√2×1.78×2.908×105
0.5×242
×0.01246
3
=3.55mm
由于齿轮模数m的大小主要决定弯曲强度,而齿面接触疲劳强度主要取决于齿轮直径。
可由弯曲强度算得的模数3.55并就近圆整为标准值m=4mm,按接触强度算得的分度圆直径d1=77.84mm,算出齿轮齿数
z1=d1
m
=
77.84
4
≈20
以上计算过程验证了模数m=8,直径d=160的齿轮是符合强度要求的。