铝合金锻件的缺陷与对策
铝合金压铸件表面铸造缺陷11类问题分析及解决办法

铝合⾦压铸件表⾯铸造缺陷11类问题分析及解决办法⼀、表⾯铸造缺陷1.1拉伤(1)特征:①沿开模⽅向铸件表⾯呈线条状的拉伤痕迹,有⼀定深度,严重时为整⾯拉伤;②⾦属液与模具表⾯粘黏,导致铸件表⾯缺料。
(2)产⽣原因:①模具型腔表⾯有损伤;②出模⽅向⽆斜度或斜度过⼩;③顶出不平衡;④模具松动:⑤浇铸温度过⾼或过低,模具温度过⾼导致合⾦液粘附;⑥脱模剂使⽤效果不好:⑦铝合⾦成分含铁量低于O.8%;⽬冷却时间过长或过短。
(3)处理⽅法:①修理模具表⾯损伤;②修正斜度,提⾼模具表⾯光洁度;③调整顶杆,使顶出⼒平衡;④紧固模具;⑤控制合理的浇铸温度和模具温度180-250 ;⑥更换脱模剂:⑦调整铝合⾦含铁量; @调整冷却时间;⑨修改内浇⼝,改变铝液⽅向。
1.2⽓泡(1 )特征:铸件表⾯有⽶粒⼤⼩的隆起表⽪下形成的空洞.(2)产⽣原因①合⾦液在压室充满度过低,易产⽣卷⽓,压射速度过⾼;②模具排⽓不良;③熔液未除⽓,熔炼温度过⾼;④模温过⾼,⾦属凝固时间不够,强度不够,⽽过早开模顶出铸件,受压⽓体膨胀起来;⑤脱模剂太多;⑥内浇⼝开设不良,充填⽅向交接。
(3)处理⽅法①改⼩压室直径,提⾼⾦属液充满度;②延长压射时间,降低第⼀阶段压射速度,改变低速与⾼速压射切换点;③降低模温,保持热平衡;④增设排⽓槽、溢流槽,充分排⽓,及时清除排⽓槽_上的油污、废料;⑤调整熔炼⼯艺,进⾏除⽓处理;⑥留模时间适当延长:⑦减少脱模剂⽤量。
1.3裂纹(1)特征:①铸件表⾯有呈直线状或波浪形的纹路,狭⼩⽽长,在外⼒作⽤下有发展趋势;②冷裂隙开裂处⾦属没被氧化;③热裂-开裂处⾦属已被氧化。
(2)产⽣原因:①合⾦中铁含量过⾼或硅含量过⾼;②何孚有害杂质的含量过⾼,降低了合⾦的塑性;③铝硅铜合⾦含锌量过⾼或含铜量过低;④模具,特别是模腔整体温度太低;⑤铸件壁厚、薄存有剧烈变化之处收缩受阻,尖⾓位形成应⼒;⑥留模时间过长,应⼒⼤;⑦顶出时受⼒不均匀。
铝合金压铸件所有缺陷及对策大全

铝合金压铸件所有缺陷及对策大全一、化学成份不合格主要合金元素或杂质含量与技术要求不符,在对试样作化学分析或光谱分析时发现。
1、配料计算不正确,元素烧损量考虑太少,配料计算有误等;2、原材料、回炉料的成分不准确或未作分析就投入使用;3、配料时称量不准;4、加料中出现问题,少加或多加及遗漏料等;5、材料保管混乱,产生混料;6、熔炼操作未按工艺操作,温度过高或熔炼时间过长,幸免于难烧损严重;7、化学分析不准确。
对策:1)、对氧化烧损严重的金属,在配料中应按技术标准的上限或经验烧损值上限配料计算;配料后并经过较核;2)、检查称重和化学分析、光谱分析是否正确;3)、定期校准衡器,不准确的禁用;4)、配料所需原料分开标注存放,按顺序排列使用;5)、加强原材料保管,标识清晰,存放有序;6)、合金液禁止过热或熔炼时间过长;7)、使用前经炉前分析,分析不合格应立即调整成分,补加炉料或冲淡;8)、熔炼沉渣及二级以上废料经重新精炼后掺加使用,比例不宜过高;9)、注意废料或使用过程中,有砂粒、石灰、油漆混入。
二、气孔铸件表面或内部出现的大或小的孔洞,形状比较规则;有分散的和比较集中的两类;在对铸件作X光透视或机械加工后可发现。
1、炉料带水气,使熔炉内水蒸气浓度增加;2、熔炉大、中修后未烘干或烘干不透;3、合金液过热,氧化吸气严重;4、熔炉、浇包工具氧等未烘干;5、脱模剂中喷涂过重或含发气量大;6、模具排气能力差;7、煤、煤气及油中的含水量超标。
对策:1)、严禁把带有水气的炉料装入炉中,装炉前要在炉边烘干;2)、炉子、坩埚及工具未烘干禁止使用;3)、注意铝液过热问题,停机时间要把炉调至保温状态;4)、精炼剂、除渣剂等未烘干禁止使用,使用时禁止对合金液激烈搅拌;5)、严格控制钙的含量;6)、选用挥发性气体量小的脱模剂,并注意配比和喷涂量要低;7)、未经干燥的氯气等气体和未经烘干的氯盐等固体不得使用。
三、涡流孔铸件内部的细小孔洞或合金液流汇处的大孔洞。
铸造铝合金热处理质量缺陷及其消除与预防
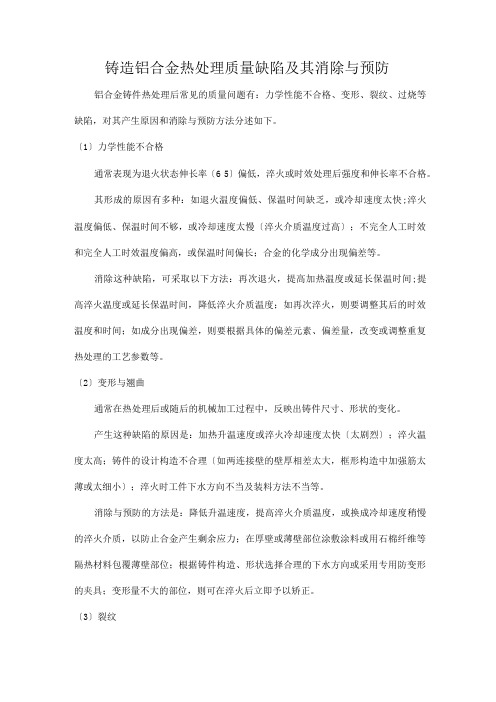
铸造铝合金热处理质量缺陷及其消除与预防铝合金铸件热处理后常见的质量问题有:力学性能不合格、变形、裂纹、过烧等缺陷,对其产生原因和消除与预防方法分述如下。
〔1〕力学性能不合格通常表现为退火状态伸长率〔6 5〕偏低,淬火或时效处理后强度和伸长率不合格。
其形成的原因有多种:如退火温度偏低、保温时间缺乏,或冷却速度太快;淬火温度偏低、保温时间不够,或冷却速度太慢〔淬火介质温度过高〕;不完全人工时效和完全人工时效温度偏高,或保温时间偏长;合金的化学成分出现偏差等。
消除这种缺陷,可采取以下方法:再次退火,提高加热温度或延长保温时间;提高淬火温度或延长保温时间,降低淬火介质温度;如再次淬火,则要调整其后的时效温度和时间;如成分出现偏差,则要根据具体的偏差元素、偏差量,改变或调整重复热处理的工艺参数等。
〔2〕变形与翘曲通常在热处理后或随后的机械加工过程中,反映出铸件尺寸、形状的变化。
产生这种缺陷的原因是:加热升温速度或淬火冷却速度太快〔太剧烈〕;淬火温度太高;铸件的设计构造不合理〔如两连接壁的壁厚相差太大,框形构造中加强筋太薄或太细小〕;淬火时工件下水方向不当及装料方法不当等。
消除与预防的方法是:降低升温速度,提高淬火介质温度,或换成冷却速度稍慢的淬火介质,以防止合金产生剩余应力;在厚壁或薄壁部位涂敷涂料或用石棉纤维等隔热材料包覆薄壁部位;根据铸件构造、形状选择合理的下水方向或采用专用防变形的夹具;变形量不大的部位,则可在淬火后立即予以矫正。
〔3〕裂纹表现为淬火后的铸件外表用肉眼可以看到明显的裂纹,或通过荧光检查肉眼看不见的微细裂纹。
裂纹多曲折不直并呈暗灰色。
产生裂纹的原因是:加热速度太快,淬火时冷却太快〔淬火温度过高或淬火介质温度过低,或淬火介质冷却速度太快〕;铸件构造设计不合理〔两连接壁壁厚差太大,框形件中间的加强筋太薄或太细小〕;装炉方法不当或下水方向不对;炉温不均匀,使铸件温度不均匀等。
消除与预防的方法是:减慢升温速度或采取等温淬火工艺;提高淬火介质温度或换成冷却速度慢的淬火介质;在壁厚或薄壁部位涂敷涂料或在薄壁部位包覆石棉等隔热材料;采用专用防开裂的淬火夹具,并选择正确的下水方向。
铝合金压铸件常见缺陷及改进方案范文

铝合金压铸件常见缺陷及改进方案铝合金压铸件作为一种高强度、高韧性的材料,被广泛应用于工业制造和家用电器等领域。
然而,由于不同生产厂家的生产工艺和技术水平不同,压铸件在生产中容易出现一些常见的缺陷。
本文将介绍铝合金压铸件常见的缺陷,并提出相应的改进方案。
一、铝合金压铸件常见缺陷1.气孔在铝合金压铸件的制造过程中,容易在铸件内部形成气孔,这是由于铸造中熔铸金属与模具表面接触时产生的气体无法完全排除而形成的。
气孔会降低铸件的强度和韧性,甚至会在使用过程中产生裂纹。
2.缩孔与气孔相似,缩孔是由于熔铸金属冷却收缩后引起的。
缩孔也会降低铸件的强度和韧性。
缩孔缺陷通常存在于压铸件的壁厚和角部。
3.毛刺毛刺是由于铸模不当或模具磨损所引起的,通常发生在铝合金压铸件的壁薄处或边缘。
毛刺会影响铸件的外观和功能,甚至会划伤使用者的手部。
4.裂纹裂纹是由于铝合金压铸件在制造和使用过程中所受到的应力超过了材料的耐受能力所引起的。
这种缺陷通常在压铸件的角部和连接处发生,会导致铸件失去强度和稳定性。
二、铝合金压铸件改进方案1.优化材料制备为了避免铸件在制造和使用过程中的开裂、气孔等缺陷,可以通过优化材料制备的过程来提高铸件的质量。
当前,用于铝合金压铸件制造的材料通常采用钙处理、收尾处理和特殊合金添加等改进技术,这些改进技术可以大幅减少气孔、缩孔和裂纹等缺陷的出现。
2.改进模具设计压铸模具的设计是影响压铸件质量的关键因素之一。
为了避免铸件的毛刺和纹路等缺陷,可以采用最新的3D打印技术设计模具,并优化模具的表面质量和耐磨性,从而确保铝合金压铸件的成形质量。
3.控制铸造过程铝合金压铸件的铸造工艺也是影响铸件质量的关键因素之一。
为了达到较好的铸造效果,可以优化铸造过程参数,例如控制铸造温度、在压铸件内部加压、运用真空铝合金熔铸等技术,以减少缺陷的出现。
4.采用热处理技术热处理可改变铝合金压铸件的微观组织和物理性能,从而使之具有更好的耐热性、耐蚀性和机械性能。
铝合金压铸产品铸造缺陷、产生原因及处理办法

铝合金压铸产品铸造缺陷、产生原因及处理办法一、表面铸造缺陷1. 拉伤a特征:①沿开模方向铸件表面呈线条状的拉伤痕迹,有一定深度,严重时为整面拉伤;②金属液与模具表面粘和,导致铸件表面缺料。
b产生原因:①顶出不平衡;②模具型腔表面有损伤;③出模方向无斜度或斜度过小;④模具松动:⑤浇铸温度过高或过低,模具温度过高导致合金液粘附;⑥铝合金成分含铁量低于0.8%;⑦脱模剂使用效果不好;⑧冷却时间过长或过短。
c处理方法:①修理模具表面损伤;②控制合理的浇铸温度和模具温度1 80-250;③调整顶杆,使顶出力平衡;④紧固模具;⑤更换脱模剂;⑥修正斜度,提高模具表面光洁度;⑦调整铝合金含铁量;⑧调整冷却时间;⑨修改内浇口,改变铝液方向。
2. 裂纹a特征:①铸件表面有呈直线状或波浪形的纹路,狭小而长,在外力作用下有发展趋势;②冷裂隙开裂处金属没被氧化;③热裂一开裂处金属已被氧化。
b产生原因:①铸件壁厚、薄存有剧烈变化之处收缩受阻,尖角位形成应力;②合金中铁含量过高或硅含量过高;③铝硅铜合金含锌量过高或含铜量过低;④模具,特别是模腔整体温度太低;⑤合金有害杂质的含量过高,降低了合金的塑性;⑥留模时间过长,应力大;⑦顶出时受力不均匀。
c处理方法:①正确控制合金成分,在某些情况下可在合金中加纯铝锭以降低合金中含镁量或铝合金中加铝硅中间合金以提高硅含量;②缩短开模及抽芯时间提高模温,保持模具热平衡;③变更或增加顶出位置,使顶出受力均匀;④改变铸件结构,加角,改变出模斜度,减少壁厚差。
3. 气泡a特征:铸件表面有米粒大小的隆起表皮下形成的空洞.b产生原因:①合金液在压室充满度过低,易产生卷气,压射速度过高;②熔液未除气,熔炼温度过高;③模具排气不良;④脱模剂太多;⑤模温过高,金属凝固时间不够,强度不够,而过早开模顶出铸件,受压气体膨胀起来;⑥内浇口开设不良,充填方向交接。
①改小压室直径,提高金属液充满度;②延长压射时间,降低第一阶段压射速度,改变低速与高速压射切换点;③增设排气槽、溢流槽,充分排气,及时清除排气槽上的油污、废料;④降低模温,保持热平衡;⑤调整熔炼工艺,进行除气处理;⑥留模时间适当延长;⑦减少脱模剂用量。
铝合金的铸造缺陷及其解决方案

铝合金的铸造缺陷及其解决方案关键信息项:1、铝合金铸造缺陷的类型名称:____________________________描述:____________________________2、造成铸造缺陷的原因因素:____________________________详细解释:____________________________3、解决方案的具体措施方法:____________________________实施步骤:____________________________4、预防铸造缺陷的策略策略:____________________________执行要点:____________________________11 铝合金铸造缺陷的类型111 气孔气孔是铝合金铸造中常见的缺陷之一。
气孔通常呈圆形或椭圆形,其尺寸大小不一。
112 缩孔和缩松缩孔是由于铸件在凝固过程中,金属液补缩不足而形成的较大孔洞。
缩松则是分散的细小缩孔。
113 夹渣夹渣指在铸件内部或表面存在的非金属夹杂物。
114 裂纹裂纹分为热裂纹和冷裂纹。
热裂纹在凝固末期高温下形成,冷裂纹则在较低温度下产生。
12 造成铸造缺陷的原因121 熔炼工艺不当熔炼过程中,如果温度控制不合理、熔炼时间过长或过短、搅拌不均匀等,都可能导致合金成分不均匀,气体和夹杂物含量增加。
122 浇注系统设计不合理浇注系统的结构和尺寸如果设计不当,可能导致金属液的流动不畅,产生卷气、冲砂等问题,从而形成气孔、夹渣等缺陷。
123 模具问题模具的温度不均匀、模具的排气不畅、模具的表面粗糙度不合适等,都可能影响铸件的质量,导致缺陷的产生。
124 铸造工艺参数不合理包括浇注温度、浇注速度、冷却速度等参数,如果选择不当,会直接影响铸件的凝固过程,从而引发各种缺陷。
13 解决方案的具体措施131 优化熔炼工艺严格控制熔炼温度和时间,采用合适的搅拌方式,确保合金成分均匀,减少气体和夹杂物的含量。
铝合金铸件缺陷产生原因及防止措施

春兴铸造(苏州工业园区)有限公司
铝合金铸件缺陷产生原因及防止措施
名称 特征 产生原因 防止措施
文件编号:CX/TD-ED02 生效日期:
版本号: A0
页码:2/15 缺陷写真
1 两股金属硫相互对接, 1 适当提高浇注温度和压铸型温度, 但未完全融合,而又夹杂 对局部型温过低处应加热,少用涂料 存在期间,两股金属结合 。 力极弱。
卡尺
变形拱起
6、有的变形铸件可经整形消弭
春兴铸造(苏州工业园区)有限公司
铝合金铸件缺陷产生原因及防止措施
名称 特征 产生原因 一、合金流动不良导 致:(1)、金属液含气量 高,氧化严重,以致流动 性下降。(2)、合金浇注 温度及模具温度过低。 (3)、内浇口速度过低。 (4)、蓄能器内氮气压力 不足。(5)、压室充满度 低。(6)、铸件壁太薄或 厚薄悬殊等设计不当。 防止措施
文件编号:CX/TD-ED02
生效日期: 页码:14/15
版本号: A0
缺陷写真
金属 液未充满 型腔,铸 欠铸 件上出现 填充不完 整的部位 。
1 改善合金的流动性:(1) 、模具温度。 (3)、提高压射速度。(4)、 补充氮气,提高有效压力。(5) 、采用定量浇注。(6)、革新铸 件结构,适当调整壁厚
2 浇注温度不宜过高,特别是高熔 点合金
网状毛刺
3 压铸型在压铸前要充分预热,达 到工作温度范围要求。
4 压铸型要定期或压铸一定次数后 退火、打磨成型部分表面
网状毛刺
春兴铸造(苏州工业园区)有限公司
铝合金铸件缺陷产生原因及防止措施
名称 特征 产生原因 因液态和凝固时期体 收缩的体积亏损引起缩馅 1 压铸件壁厚相差太大。 2 合金液态和凝固时期体 收缩过大 3 浇注位置不当 4 压射比压低 5 压铸型局部温度过高。 防止措施 1 压铸件壁厚应均匀,厚薄过度要缓 2 选用液态和凝固时期体收缩小的合 金 3 正确设计内浇口位置和数量、大小 。 4 增加压射压力 5 适当降低浇注温度和压铸型温度; 对压铸型局部温度高处进行冷却。
铝合金锻件的常见缺陷及对策

铝合金锻件的常见缺陷及对策铝合金材料因其密度较小,强度适宜,因而得到广泛的应用。
根据成分和工艺性能不同,铝合金分为变形铝合金和铸造铝合金两大类。
变形铝合金按其热处理强化能力又可分为热处理不强化铝合金和热处理强化铝合金。
变形铝合金按其使用性能及工艺性能可分为防锈铝合金(用LF表示)、硬铝合金(用LY表示),超硬铝合金(用LC 表示)和锻铝合金(用LD表示)。
影响铝合金再结晶温度的主要因素有:合金成分、压力加工前的均匀化规范、压力加工方式(应力状态)、变形温度、变形速度、变形程度和最终热处理制度等。
铝合金的晶粒尺寸对力学性能有较大影响,铝合金锻件中的粗晶显著降低强度极限和屈服极限,降低零件的使用性能和寿命。
因此,锻造铝合金时需注意控制晶粒度。
铝合金锻件的晶粒大小与变形温度、变形程度、受剪切变形的情况以及固溶处理前的组织状态等有关。
详见几种主要缺陷形成的机理和对策中的备料不当产生的缺陷及其对锻件的影响。
供锻造和模锻的铝合金原坯料,一般采用铸锭和挤庄坯料,个别情况下亦采用轧制坯料。
铸锭坯料往往具有疏松、气孔、缩孔、裂纹、成层、夹渣、氧化膜和树枝状偏析等缺陷。
挤压坯料一般具有粗晶环、成层、缩尾、夹渣、氧化膜和表皮气泡等缺陷。
铝合金坯料的上述缺陷,不仅锻造时容易开裂,而且直接影响到锻件质量,所以锻前需要按标准对坯料进行检查,合格后方能投产。
铝合金的锻造特点如下:1.塑性较低铝合金的塑性受合金成分和锻造温度的影响较大。
大多数铝合金对变形速度不十分敏感,但是随着合金中合金元素含量的增加,合金的塑性不断下降。
2.流动性差铝合金质地很软,外摩擦系数较大,所以流动性较差,模锻时难于成形。
3.锻造温度范围窄铝合金的锻造温度范围一般都在150℃以内,少数高强度铝合金的锻造温度范围甚至不到100℃,由于铝合金的锻造温度范围很窄,所以一般都采用能精确控制加热温度的带强制循环空气的箱式电阻炉或普通箱式电阻炉进行加热,温差控制在上±10℃以内。
- 1、下载文档前请自行甄别文档内容的完整性,平台不提供额外的编辑、内容补充、找答案等附加服务。
- 2、"仅部分预览"的文档,不可在线预览部分如存在完整性等问题,可反馈申请退款(可完整预览的文档不适用该条件!)。
- 3、如文档侵犯您的权益,请联系客服反馈,我们会尽快为您处理(人工客服工作时间:9:00-18:30)。
铝合金锻件常见的缺陷与对策来源:中国铝材信息网,更新时间:2007-4-28 16:57:52,阅读:1861次(一)概述铝合金是以铝为基,加入了锰、镁、铜、硅、铁、镍、锌等各种元素而形成的。
它密度较小,强度适宜,因而得到了愈来愈广泛的应用。
根据成分和工艺性能不同,铝合金分为变形铝合金和铸造铝合金两大类。
变形铝合金按其热处理强化能力可分为热处理不强化铝合金和热处理强化铝合金(见图5-11)。
图5-11 铝合金分类图变形铝合金按其使用性能及工艺性能分为防锈铝合金(用LF表示)、硬铝合金(用LY表示),超硬铝合金(用LC表示)和锻铝合金(用LD表示)。
它们的主要牌号和成分见表5-10。
表5-10 变形铝合金主要牌号的化学成分及挤压棒材的力学性能类别牌号化学成分(质量分数)(%)力学Cu Mg Mn Fe Si 其它直径尺寸/mm材料状态σb/MPaδ5(%)≥防锈铝合金LF22.0~2.8或Cr0.15~0.40所有尺寸M或R≤22610 LF54.0~5.00.3~0.6V0.02~0.10厚0.5~4.5M27015 LF11LF 124.8~5.58.3~9.60.30~0.600.40~0.80Ti或V0.02~0.15Ti0.05~0.15≤200>200Sb0.004~0.05M>200直径≤150270M,RM或R152503731015 LF21 1.0~1.6所有尺寸M或R≤16720注:状态符号表示意义:M—退火,CZ—淬火(自然时效),CS—淬火(人工时效),R—热挤。
Cu、Mg、Zn等是铝合金中的主要强化元素。
它们一方面溶解在铝中使固溶体强化;另一方面,它们在铝合金中形成大量的化合物,成为铝合金中的强化相和过剩相(见表5-11)。
表5-11 铝合金中的过剩相和强化相类型向性。
镍在铝合金中可以改善合金的抗腐蚀性能和提高热强性。
Fe、Si、Na、K等都属于铝合金中的杂质元素,其中主要是Fe和St。
Fe在铝中的溶解度很小,在655℃时为0.5%,在室温时仅为0.002%。
Fe主要形成金属化合物FeAl3,是硬脆的针状化合物。
Si在铝中的溶解度略大一些,在577℃时可溶入1.65%,在室温时为0.05%。
Si除溶入铝中外,多余的则单独存在于铝中,通常称为“游离硅”。
铝合金中由于存在大量的强化相和过剩相,因此,其铸态组织中呈现多相混杂的状态。
另外,在某些铝合金(例如LY12)铸态组织中还常常存在共晶混合物。
这些物质通常又硬又脆,且呈网状分布于晶界。
而且,由于铸造时的冷却条件,使这些化合物相在铸锭中形成了区域偏析,枝晶偏析和晶间偏析,此外,还有气孔、缩孔等缺陷,严重降低了铝合金铸锭的塑性。
通过热塑性变形可以使铝合金铸态组织得到较大改善,性能得到较大提高。
以LY11为例,经挤压变形后,形成纤维状组织,在挤压变形程度小于70%之前,随着变形程度的增加,材料纵向及横向的强度指标都不断提高。
当变形程度继续增加时,纵向性能继续提高,而横向性能急剧下降,即引起了性能的异向性。
流线的分布情况对铝合金的性能有很大影响,流线不顺、涡流和穿流都使铝合金的塑性指标、疲劳强度和抗腐蚀性能有明显降低。
因此,编制成形工艺时,应当使流线方向与零件最大受力方向一致。
某些热处理可以强化的变形铝合金,按照一定的规范热变形之后,可以使变形强化的效果保存下来,使合金的强度提高,即所谓热形变强化效应,这是因为,按照一定的规范热变形之后,某些合金的再结晶温度高于淬火加热温度,所以热处理后的制品具有未再结晶组织。
这种组织的晶粒细小,并且晶粒中形成许多亚晶块,故强度性能远远高于再结晶组织的制品。
影响铝合金再结晶温度的主要因素有:合金成分、压力加工前的均匀化规范、压力加工方式(应力状态)、变形温度、变形速度、变形程度和最终热处理制度等。
图5-12是LD10合金的组织状态与变形温度和变形速度的关系。
图5-12 淬火后的LD10合金的组织状态和变形温度和变形速度的关系Ⅰ—不存在再结晶Ⅱ—完全再结晶Ⅲ—变形后就开始了再结晶其余为混合组合铝合金的晶粒尺寸对力学性能有较大影响,铝合金锻件中的粗晶显著降低强度极限和屈服极限,降低零件的使用性能和寿命。
因此,锻造铝合金时需注意控制晶粒度。
铝合金锻件的晶粒大小与变形温度、变形程度、受剪切变形的情况以及固溶处理前的组织状态等有关。
详见几种主要缺陷形成的机理和对策中的备料不当产生的缺陷及其对锻件的影响。
供锻造和模锻的铝合金原坯料,一般采用铸锭和挤庄坯料,个别情况下亦采用轧制坯料。
铸锭坯料往往具有疏松、气孔、缩孔、裂纹、成层、夹渣、氧化膜和树枝状偏析等缺陷。
挤压坯料一般具有粗晶环、成层、缩尾、夹渣、氧化膜和表皮气泡等缺陷。
铝合金坯料的上述缺陷,不仅锻造时容易开裂,而且直接影响到锻件质量,所以锻前需要按标准对坯料进行检查,合格后方能投产。
铝合金的锻造特点如下:1.塑性较低铝合金的塑性受合金成分和锻造温度的影响较大。
大多数铝合金对变形速度不十分敏感,但是随着合金中合金元素含量的增加,合金的塑性不断下降,对变形速度的敏感性逐渐增加(图5-13),由图还可以看出,当变形温度较低时,铝合金的塑性急剧下降,特别是高强度铝合金(LC4等)表现最为突出。
图5-13 不同变形温度和速度对铝合金塑性的影响—静载变形 ---动载变形2.流动性差铝合金质地很软,外摩擦系数较大(表5-12),所以流动性较差,模锻时难于成形。
表5-12 铁碳合金与铝合金变形时的外摩擦系数合金铁碳合金(%)铝合金(%)变形速度/(m/s)<1 >1①<1 >1变形温度/℃(0.8~0.95)T熔②0.40 0.35 0.50 0.48 (0.5~0.8)T熔0.45 0.40 0.48 0.45注:若采用润滑剂摩擦系数可降低15%~25%。
①锤击作用也适用。
②T熔是指绝对熔化温度。
3.锻造温度范围窄铝合金的锻造温度范围一般都在150℃以内,少数高强度铝合金的锻造温度范围甚至不到100℃,由于铝合金的锻造温度范围很窄,所以一般都采用能精确控制加热温度的带强制循环空气的箱式电阻炉或普通箱式电阻炉进行加热,温差控制在上±10℃以内。
同时,为了保证适当的终锻温度,提高合金的塑性和流动性,改善合金的成形条件,用于锻造和模锻的工具或模具需要预热。
4.导热性良好铝合金由于导热性好,加热时内应力小,且易于均匀热透,所以坯料可以直接装人接近始锻温度的高温炉膛内进行快速加热。
挤压坯料在不产生锻造裂纹的条件下,不必进行保温,但铸造坯料加热时需要保温。
5.始锻温度和终锻温度要严加控制始锻温度一般取上限,这样有利于提高合金的塑性和流动性,使金属易于成形。
但有些合金始锻温度太高,将引起强度下降。
例如,LD10合金始锻温度高于470℃时,强度约下降24MPa;LF6合金始锻温度从360℃提高到420℃,强度约下降15MPa。
终锻温度高有利于保持挤压坯料的挤压效应,能得到具有未再结晶组织和力学性能高的锻件。
终锻温度过低,容易产生大晶粒,使锻件的力学性能大大降低。
同时,终锻温度过低,使合金的塑性和流动性急剧下降,容易产生表面和内部裂纹。
(二)锻造过程中常见的缺陷与对策1.过烧由于铝合金的温度范围窄,其锻造加热温度,尤其是淬火加热温度很接近合金的共晶熔化温度,容易发生过烧。
所以在锻件和模具加热以及锻件淬火加热时,必须十分注意温度上限,严格遵守工艺操作规程,否则会引起锻件过烧。
锻件过烧后,表面发暗、起泡,一锻就裂。
在热处理时产生的过烧,也可能形成裂纹。
过烧锻件的高倍组织特点是:晶界发毛、加粗,出现低熔点化合物的共晶复熔球,形成三角晶界。
轻微过烧的锻件,强度稍有提高,但疲劳性能较差。
严重过烧后各项性能急剧下降,使锻件成为废品。
2.裂纹由于铝合金的塑性和流动性较差,很容易产生表面和内部裂纹。
产生表面裂纹的原因与坯料种类有关。
用铸锭做坯料,往往由于铸锭含氢量高、有严重的疏松、氧化夹渣、粗大的柱状晶、存在有严重的内部偏析、高温均匀化处理不充分以及铸锭表面缺陷(凹坑、划痕、棱角等)都会在锻造时产生表面裂纹。
另外,坯料加热不充分,保温时间不够、锻造温度过高或过低,变形程度太大,变形速度太高、锻造过程中产生的弯曲、折叠没有及时消除,再次进行锻造,都可能产生表面裂纹。
挤压坯料表面的粗晶环、表皮气泡等,也容易在锻造时产生开裂。
铝合金锻件的内部裂纹,主要是由于坯料内部存在有粗大的氧化物夹渣和低熔点脆性化合物,变形时在拉应力或切应力的作用下产生开裂,并不断扩大。
此外,锻造时多次滚圆,当每次变形量较小(小于15%~20%)时,也会产生内部中心裂纹。
由于铝合金的锻造温度范围很窄,如果锻造工具和模具没有预热,或预热温度不够也会引起锻件产生裂纹。
因此,要防止产生表面和内部裂纹,必须采取如下对策:1)选择高质量的原坯料,坯料表面的各种缺陷要彻底清除干净。
例如,挤压坯料常常需要车皮。
在锤上锻造不便于车皮的小棒料时,开始要轻击,打碎粗晶环,然后逐渐加重打击;2)铸锭坯料要进行充分的高温均匀化处理,消除残余内应力和品内偏析,以提高金属塑性。
锻造加热时,要保证在规定的加热温度进行加热并充分保温;3)根据不同合金,选择最佳锻造温度范围。
例如,LC4合金铸锭的最佳锻造温度范围为:在440℃左右加热保温,然后缓冷至410~390℃左右锻造,塑性最好;4)铝合金由于流动性差,不宜采用变形激烈的锻造工序(如滚压),并且变形程度要适当,变形速度要越低越好;5)锻造操作时要注意防止弯曲、压折,并要及时矫正或消除所产生的缺陷。
滚圆时,压下量不能小于20%,并且滚圆的次数不能太多。
6)用于锻造和模般的工具,要充分预热,加热温度最好接近锻造温度,一般为200~420℃,以便提高金属的塑性和流动性。
3.大晶粒锻铝(LD2、LD5、LD7、LD10、2024、2068)和硬铝(LYll、LY12等)很容易产生大晶粒,它们主要分布在锻件变形程度小而尺寸较厚的部位,变形程度大和变形激烈的区域以及飞边区附近。
另外,在锻件的表面也常常有一层粗晶。
产生大晶粒的原因除了由于变形程度过小(落入临界变形区)或变形程度过大和变形激烈不均匀所引起之外,加热和模锻次数过多,加热温度过高(例如LD2合金淬火温度过高,保温时间过长,常常出现大晶粒),终锻温度太低也会产生大晶粒。
锻件表面层的粗晶,其产生原因有两种情况:其一,是挤压坯料表层粗晶环被带人锻件;其二,是模锻时模膛表面太粗糙,模具温度较低,润滑不良,使表面接触层激烈剪切变形,因而产生粗晶。
所以,为避免铝合金锻件产生大晶粒:1)必须改进模具设计,合理选择坯料,保证锻件均匀变形;2)避免在高温下长时间加热,对LD2等容易晶粒长大的合金,淬火加热温度取下限;3)减少模锻次数,力求一火锻成;4)保证终锻温度;5)提高模膛表面粗糙度达Rα0.4μm以上,采用良好的工艺润滑剂。