典型数控铣床的设计
数控铣床设计说明书

1.1数控机床的产生和发展历程1.1.1数控机床的发展简史1946年世界上诞生了第一台电子计算机,同期美国北密执安的小型飞机承包商帕尔森斯公司(Parsosncoproraitno)为了制造飞机机翼轮廓的板状样板,提出了采用数字控制技术进行机械加工的思想,1949年由帕尔森斯公司与美国麻省理工学院伺服机构研究所合作开始从事数控机床的研制工作,1952年,研制出第一台实验性数控系统,并把它装在一台立式铣床上,成为世界上第一台数控机床,成功实现了同时控制三轴的运动。
1954年11月,在帕尔森斯专利基础上,第一台工业用的数控机床由美国本迪克斯公司(Bendixocproratjno)生产出来,从此,传统机床产生了质的变化。
50多年过去了,数控系统由当时的电子管起步,经历了两个阶段六代的发展,即:硬件逻辑数控,简称为数控(NC)阶段经历了三代,即1952年第一代—电子管;1995年第二代—晶体管和印刷电路板;1965年第三代—小规模集成电路,由于它体积小,功耗低,使数控系统的可靠性得以进一步提高,数控系统发展到第三代。
计算机数控(计算机数字的控制,简写为CNC)阶段也经历了三代,即1970年第四代—小型计算机,1974年第五代—微处理器(MNC)和1990年第六代—基于Pc的阶段。
数控系统发展到了第五代以后,从根本上解决了可靠性低、价格昂贵、应用不方便等极为关键的问题,并在上世纪七十年代末八十年代初以后首先在美国、日本、欧洲等工业发达国家得到大规模普及应用。
1.1.2 我国数控技术的发展1.1.2.1我国数控技术经过了研制开发、引进技术、消化吸收、科技攻关和产业攻关几个过程,并得到了飞速发展。
从1958年起,由一些科研院所、高等学校和少数机床厂起步进行数控系统的研制和开发,由于受到当时国产电子元器件水平低、部门经济等因素的制约,未能取得较大的进展。
在改革开放以后,经过“六五”(1981一1985年)的引进国外技术,“七五”(1986一1990年)的消化吸收和“八五”(1991一1995)国家组织的科技攻关和“九五”(1996一2000年)国家组织的产业化攻关,才使得我国数控技术逐步取得实质性的进展,一些较高档次的数控系统(五轴联动),分辨率为0.002 m的高精度数控系统、数字仿形数控系统、为柔性单元配套的数控系统都开发出来,并造出样机,开始了专业化生产和使用。
龙门式三坐标数控钻铣床设计

6 【 要】 摘 普通钻铣床主要应用于 机械修配车间, 适合于 单件小批量生产, 可加工零件范围较广,l l具有较全面的通用 铣床功能, 既可以用于钻削 加工, - ̄用于 也. j - 铣削 加工。 提高 为了 普通钻铣床的自 l 动 6化程度和加工范围, 提出了 机床的总体设计方案, 讨论了 机床的总体布局与传动方案, 研究了 机械传动 6 l系 统和数控系 统硬件的设计方法, 设计了 一台小型龙门式.坐 E 标数控钻铣床。 - 该小型龙门式三坐标数 l } 控钻铣床具有结构简单, 性好, 动化程度和加工精度高以 刚 自 及操作维 修方便等优点。 l
表 2经运动变换虚拟; -后 V RI T测量结果 jr  ̄ E CU
较为详细的论述 , 推导出该类机床后置处理转角计算公式和刀位 点坐标转换计算公式 。 通过对 比工件设计与求解结果的虚拟加工 的结果表明, 该方法正确 、 可行 。另外 , 该模型能适应不 同的机床 结构形式 , 而且考虑 了机床结构误差 的影响 , 为多坐标数控加工
平移运动副的运动量完全正确, 充分证明了所述机床运动变换建模 方法和求解方法的正确性 、 可行性, 同时具有较高的精确性。 表 3 比对 U G测量结果与 VE I T测量结果 RCU
与液压 ,0 93 ( ) 7 1. 2 0 ,7 1 : — 9 11
[] 2 陈涛 , 彭芳瑜 , 周云飞. 基于结构误差补偿 的多坐标 机床后置变换 [] J. 中国制造业信息化 , 0 ,22 :8 9 . 2 33 ( )8 — 0 0
’ 中 图分类 号 :H1 ,G 文 献标 识码 : T 3T 5 A
;
9
精度 、 效率、 品种等的要求越来 越大 , 传统 的通用机床 、 专用机床
XKA5750数控铣床主传动系统设计

XKA5750数控铣床主传动系统设计数控铣床是一种利用数控技术实现自动加工的机床。
在数控铣床中,主轴传动系统是非常重要的部分,它的设计和性能直接影响到加工的质量和效率。
本文将重点讨论XKA5750数控铣床主传动系统的设计。
主轴传动系统是数控铣床的核心部分,它负责提供主轴的旋转运动。
在设计主轴传动系统时,需要考虑以下几个关键因素:1.主轴驱动方式:主轴传动系统可以采用直接驱动或间接驱动方式。
直接驱动方式将电机直接连接到主轴上,可以提高传动效率和刚性,但也增加了设备成本。
间接驱动方式则采用中间驱动装置,可以提供更高的扭矩输出,适合加工大型和重型工件。
2.主轴转速范围:主轴转速范围决定了数控铣床的加工能力。
一般来说,数控铣床的主轴转速要能够满足不同加工要求的需求,包括高速切削和低速高力矩加工。
3.主轴传动方式:主轴传动系统可以采用带或齿轮传动。
带传动方式结构简单,运行平稳,但传输效率较低,适用于低功率和低转速的场合。
齿轮传动方式转矩传递效率高,适用于高功率和高转速的场合,但噪声和振动较大。
在设计主轴传动系统时,需要根据实际需求综合考虑。
4.主轴刚性和精度:主轴传动系统的刚性和精度直接影响到加工的精度和表面质量。
刚性主要取决于电机选型、传动装置的稳定性和主轴轴承的刚度。
精度则受到主轴轴承精度、传动装置的误差和传感器的精度等影响。
为了确保主轴的刚性和精度,我们可以选择高性能的电机和精密的轴承,并采用优质的传动装置。
同时,还可以配备传感器和控制系统,实时监测主轴的运行状态,确保其稳定性和精度。
总之,XKA5750数控铣床主传动系统的设计需要综合考虑驱动方式、转速范围、传动方式、刚性和精度等因素,以满足不同加工要求。
在设计过程中,需要选择合适的设备和配件,进行系统优化和调试,以达到最佳的加工效果。
简易数控铣床的系统设计
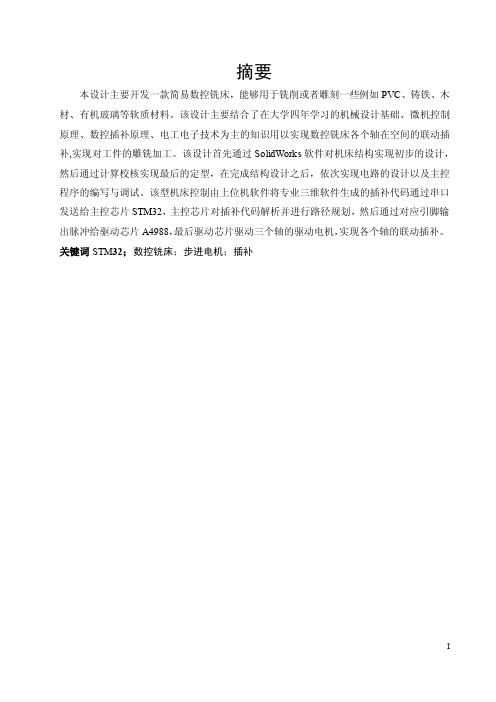
摘要本设计主要开发一款简易数控铣床,能够用于铣削或者雕刻一些例如PVC、铸铁、木材、有机玻璃等软质材料。
该设计主要结合了在大学四年学习的机械设计基础、微机控制原理、数控插补原理、电工电子技术为主的知识用以实现数控铣床各个轴在空间的联动插补,实现对工件的雕铣加工。
该设计首先通过SolidWorks软件对机床结构实现初步的设计,然后通过计算校核实现最后的定型,在完成结构设计之后,依次实现电路的设计以及主控程序的编写与调试。
该型机床控制由上位机软件将专业三维软件生成的插补代码通过串口发送给主控芯片STM32,主控芯片对插补代码解析并进行路径规划,然后通过对应引脚输出脉冲给驱动芯片A4988,最后驱动芯片驱动三个轴的驱动电机,实现各个轴的联动插补。
关键词STM32;数控铣床;步进电机;插补AbstractThis design mainly developed a simple CNC milling machine, can be used for milling or sculpture such as PVC, soft material such as cast iron, wood, organic glass.This design is mainly combined the study in the university four years of mechanical design basis, principle of microcomputer control, numerical control interpolation principle, electrical and electronic technology as the main knowledge to achieve the linkage of the CNC milling machine each axis in space interpolation, realize the artifact carved milling processing.This design first by SolidWorks software structure to realize the preliminary design of nc machine tools, and then by calculating and checking the final shape, after complete the structural design, the realization of circuit design as well as the master control program written in turn and debugging.The type of machine tool control by the PC software to professional 3d interpolation code generated by the software via a serial port sent to the main control chip STM32, master control chip for interpolation code parsing and path planning, and then through the output pulse of the corresponding pin to drive chip A4988, finally the drive motor driver chip driver three axis, realize the interaction of each axis interpolation.Keywords STM32; CNC milling machine; stepper motor ; interpolation辽宁工程技术大学毕业设计(论文)引言近些年,随着互联网的发展,以美国为代表的发达国家的“再工业化”概念,以及以中国为首的新兴国家的崛起使得以德国为首的制造业强国的工业产品销售受到不同程度的影响。
数控铣床毕业设计方案
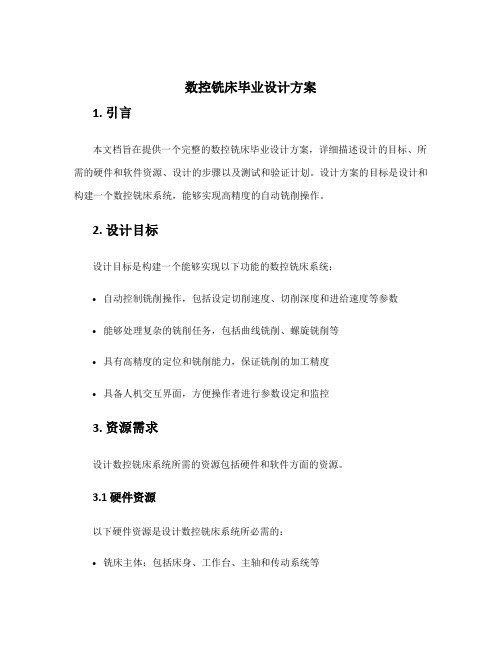
数控铣床毕业设计方案1. 引言本文档旨在提供一个完整的数控铣床毕业设计方案,详细描述设计的目标、所需的硬件和软件资源、设计的步骤以及测试和验证计划。
设计方案的目标是设计和构建一个数控铣床系统,能够实现高精度的自动铣削操作。
2. 设计目标设计目标是构建一个能够实现以下功能的数控铣床系统:•自动控制铣削操作,包括设定切削速度、切削深度和进给速度等参数•能够处理复杂的铣削任务,包括曲线铣削、螺旋铣削等•具有高精度的定位和铣削能力,保证铣削的加工精度•具备人机交互界面,方便操作者进行参数设定和监控3. 资源需求设计数控铣床系统所需的资源包括硬件和软件方面的资源。
3.1 硬件资源以下硬件资源是设计数控铣床系统所必需的:•铣床主体:包括床身、工作台、主轴和传动系统等•伺服电机:用于驱动主轴和进给轴•传感器:如位置传感器、力传感器等,用于实时监控和反馈•控制器:用于控制伺服电机和传感器,实现自动化控制3.2 软件资源以下软件资源是设计数控铣床系统所必需的:•CAD软件:用于绘制和编辑零件的几何形状•CAM软件:用于生成数控铣削的刀具路径和切削参数•控制软件:用于编写和加载数控程序,控制铣床系统的运行4. 设计步骤设计数控铣床系统的步骤如下:1.确定设计需求和目标,明确所需的功能和性能指标2.设计铣床主体,包括床身、工作台、主轴和传动系统等部分3.选择并配置合适的伺服电机和传感器4.设计控制系统,包括控制器和相应的控制软件5.开发人机交互界面,实现参数设定和监控功能6.软件开发,包括CAD软件和CAM软件的使用以及控制软件的编写7.进行系统集成和调试8.进行性能测试和验证5. 测试和验证计划为确保数控铣床系统的正常运行和满足设计需求,需要进行全面的测试和验证。
测试和验证计划如下:1.功能测试:验证系统是否能够实现设计的功能,包括自动控制铣削操作、复杂铣削任务的处理等2.精度测试:测试系统的定位精度和加工精度,与设计要求进行比较3.可靠性测试:进行长时间运行测试,检测系统的稳定性和可靠性4.用户界面测试:测试人机交互界面的易用性和功能完善性5.性能测试:测试系统在不同工况下的性能表现,如切削速度、进给速度和切削深度等6. 总结本文档详细描述了一个数控铣床毕业设计方案,包括设计目标、所需的硬件和软件资源、设计的步骤以及测试和验证计划。
定梁式数控龙门铣床整体结构设计
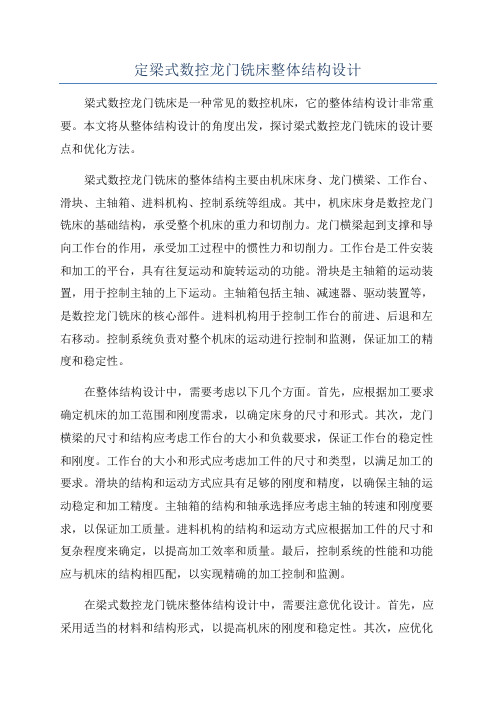
定梁式数控龙门铣床整体结构设计梁式数控龙门铣床是一种常见的数控机床,它的整体结构设计非常重要。
本文将从整体结构设计的角度出发,探讨梁式数控龙门铣床的设计要点和优化方法。
梁式数控龙门铣床的整体结构主要由机床床身、龙门横梁、工作台、滑块、主轴箱、进料机构、控制系统等组成。
其中,机床床身是数控龙门铣床的基础结构,承受整个机床的重力和切削力。
龙门横梁起到支撑和导向工作台的作用,承受加工过程中的惯性力和切削力。
工作台是工件安装和加工的平台,具有往复运动和旋转运动的功能。
滑块是主轴箱的运动装置,用于控制主轴的上下运动。
主轴箱包括主轴、减速器、驱动装置等,是数控龙门铣床的核心部件。
进料机构用于控制工作台的前进、后退和左右移动。
控制系统负责对整个机床的运动进行控制和监测,保证加工的精度和稳定性。
在整体结构设计中,需要考虑以下几个方面。
首先,应根据加工要求确定机床的加工范围和刚度需求,以确定床身的尺寸和形式。
其次,龙门横梁的尺寸和结构应考虑工作台的大小和负载要求,保证工作台的稳定性和刚度。
工作台的大小和形式应考虑加工件的尺寸和类型,以满足加工的要求。
滑块的结构和运动方式应具有足够的刚度和精度,以确保主轴的运动稳定和加工精度。
主轴箱的结构和轴承选择应考虑主轴的转速和刚度要求,以保证加工质量。
进料机构的结构和运动方式应根据加工件的尺寸和复杂程度来确定,以提高加工效率和质量。
最后,控制系统的性能和功能应与机床的结构相匹配,以实现精确的加工控制和监测。
在梁式数控龙门铣床整体结构设计中,需要注意优化设计。
首先,应采用适当的材料和结构形式,以提高机床的刚度和稳定性。
其次,应优化各组件的尺寸和位置,以减少功耗和噪声,并提高加工精度和效率。
此外,应选择合适的传动方式和轴承结构,以提高机床的工作精度和可靠性。
最后,应合理布置各部件和管线,以提高机床的维护便利性和使用寿命。
总之,梁式数控龙门铣床的整体结构设计是决定其加工质量和效率的关键因素。
数控机床设计实例
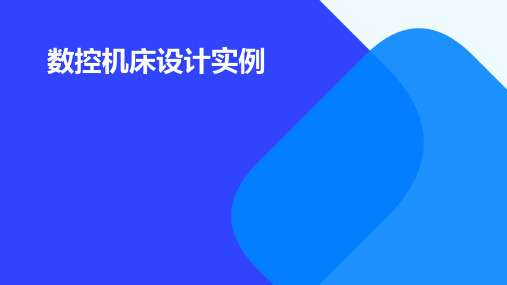
实现复杂曲面的加工,提高加工效率和表面质量。
智能控制技术
利用人工智能、机器学习等技术,实现自适应加工和智能故障诊断。
智能制造与数字化转型的机遇与挑战
数字化工厂
通过物联网、大数据等技 术,实现生产过程的实时 监控和优化。
定制化生产
满足个性化需求,提高生 产效率和灵活性。
工业互联网
实现设备间的互联互通, 提升生产协同效率。
数控机床适用于大规模生产、加工复杂零件等领域,是现代制造业的核心设备之一。
数控机床的分类与用途
01
02
03
按加工工艺分类
数控车床、数控铣床、数 控磨床等。
按控制轴数分类
三轴、四轴、五轴等数控 机床。
按运动方式分类
点位控制、直线控制、轮 廓控制等数控机床。
数控机床的发展历程与趋势
数控机床的发展经历了多个阶段,从 早期的NC机床到现代的CNC机床, 再到智能数控机床。
数控车床设计实例二
该数控车床主要应用于汽车零部件的加工,具有高刚度、高 稳定性的特点。其设计注重了热对称性,避免了热变形对加 工精度的影响。同时,该数控车床采用了大功率主轴和大容 量冷却系统,满足了高效加工的需求。
数控铣床设计实例
数控铣床设计实例一
该数控铣床主要用于加工模具和复杂零件,具有高精度、高效率的特点。其设计采用了五轴联动技术,实现了复 杂零件的加工。同时,该数控铣床采用了模块化设计,方便了生产和维修。
数控机床设计实例
contents
目录
• 数控机床概述 • 数控机床设计实例介绍 • 数控机床设计流程 • 数控机床关键技术解析 • 数控机床应用案例分析 • 数控机床的未来发展与挑战
01
定梁式数控龙门铣床整体结构设计

定梁式数控龙门铣床整体结构设计摘要:根据国内与国外對于龙门铣床的研究情况来看,此次设计一种可以用于加工各种复杂的零件的龙门数控铣床,符合实际的生产需要。
其结构主要包括了横向进给机构、纵向仅给机构、工作台以及立柱等的组成部分。
其运行是采用伺服电机然后是滚珠丝杠进行传动。
总体上讲述了其所包含的结构、特点以及其工作原理。
并且具体的阐述了此铣床的整体结构以及校核的方法对其进行了分析。
龙门铣床;数控;伺服电机;滚珠丝杠1 机床的设计要求数控龙门铣床的总体方案设计主要包括了:(1)总体布局设计:各个部件的位置、各个部件的运动进行分析、还有其整体的外观。
(2)技术参数设计:各个部件的尺寸、刀具的转速和进给量、电机的功率和所能承载的力。
(3)结构优化设计:整个机床的刚度、运动特性、受热性能等。
此机床符合国家的标准,其参数为:工作台的整体尺寸为:3000×1200mm,工作台所能承受的最大载荷为2吨,能够具有高的速度和效率,结构简单稳定,精度高且用于铣削较为复杂的零件。
2 设计方案我所设计的铣床主要是工作台能够做纵向移动的数控龙门铣床。
这种工作台移动的数控龙门铣床主要的特点包括了(1)成本低,生产较为简单。
这种龙门铣床的整体的长度必须比工作台行程的长度多两倍。
而移动式的龙门铣床的整体的长度就得是龙门架的侧面宽度与纵向行程之和。
(2)这种机床的动态响应好。
这种机床的龙门架是固定在立柱上的,所以当工作台移动时其所切屑的稳定性好,这样便保证了机床所加工零件的精度和动态响应性。
我所采用的为西门子 4-05的数控系统,因为这个数控系统具有龙门轴的同步功能。
这一项功能能够让龙门框架的进给轴(X1,X2)达到无机械偏差的位移的目的。
可以对运动的值进行比对,能够检测出很小的偏差并且及时的更正,增大了其精度。
铣床的整体装配图如下图所示:3 主轴箱的设计要求(1)使其所调节的速度范围能够达到其最大值而且能够进行无极变速。
(2)提高主轴箱的刚性与稳定性,以及它的精度。
- 1、下载文档前请自行甄别文档内容的完整性,平台不提供额外的编辑、内容补充、找答案等附加服务。
- 2、"仅部分预览"的文档,不可在线预览部分如存在完整性等问题,可反馈申请退款(可完整预览的文档不适用该条件!)。
- 3、如文档侵犯您的权益,请联系客服反馈,我们会尽快为您处理(人工客服工作时间:9:00-18:30)。
数控铣床的主传动系统设计1. 主传动系统变速方式交流变频无级调速主轴电机使数控机床主传动实现了无级调速,解决了直流电机长期运转产生整流火花和电刷磨损的难题。
数控机床的主运动要求有较大的调速范围,以保证加工时能选用合理的切削用量,从而获得最佳的生产率、加工精度和表面质量。
为了适应各种工件和各种工件材料的要求,数控铣床调速范围应进一步扩大。
为了确保低速时的扭矩,有的数控机床在交流电机无级变速的基础上配以齿轮变速。
对于通用型数控铣床,要求主轴变速范围200~100≥np R ,恒功率区的变速范围尽量大,当主轴最低转速拟定后,主轴的计算转速应较低,以满足低速大转矩的切削加工要求。
实现这些功能应在交流无级调速主轴电机后串联分级变速机构,以扩大电机的恒功率区变速范围。
如果分级变速机构设计得不合适,则须选用较大功率的电机。
原因是电机在恒转矩区运行时,应保证主轴在最低转速切削时有足够大的功率;主轴在恒功率区工作时,有些系统会出现功率缺口,为了在缺口低谷处功率能保证传递全部功率,只有选择额定功率较大的电机给予补偿。
2. 串联分级变速机构的主传动系统设计 (1)分级变速机构设计分级变速机构级数Z 主要取决于主轴要求的恒功率变速范围np R 、电机的恒功率变速范围dp R 和分级变速机构的变速范围f R ,同时还和机构的复杂程度和主轴是否允许有功率缺口有关,常用的级数Z =2、3、4。
① 假设Z =2,传动比为1i 、2i ,且21i i >,则级数比f R i i ==21/ϕ,要使主轴转速连续,功率无缺口的条件是dp R ≤ϕ (即dp f R R <),这与要求主轴的恒功率区变速范围np R 尽量大,相矛盾,使得主轴转速不连续,功率有缺口,如图8-15(a )所示。
由图8-15(a )可以看出,采用一个Z =2的变速机构(即Ⅱ轴为主轴)时,只有级数比dp R ≤ϕ时,主轴的恒功率区转速连续,但主轴np R 很小,不能满足机床要求。
若再增加一个Z =2的传动组,(如图8-15(a )中Ⅱ—Ⅲ轴),主轴为第Ⅲ轴,则 np R 扩大范围很宽,但要经常换档且操纵机构复杂,主轴转速不连续,功率有缺口,因此不可取。
② 假设Z =4,如图8-15( b )所示,四联滑移齿轮或两个双联滑移齿轮,使变速机构轴向尺寸增大,也不可取。
① 假设Z =3,传动比为1i 、2i 、3i ,且321i i i >>,则级数比211/i i =ϕ,f i i 322/=ϕ,21ϕϕ⋅=f R ,令21ϕϕϕ⋅=,则ϕ=f R 。
如图8-16所示。
当dp R =3,ϕ≤3时,主轴无功率缺口,采用一级带轮(或齿轮)和一个三联滑移齿轮传动,较为理想。
由图8-16看出,采用图中所示的变速组来实现分级变速机构较为理想,主轴的恒功率区范围较宽,功率无缺口,转速连续。
上述理论分析及其设计计算步骤方法,举例说明如下:(2)实例计算假设本例数控铣床,其主轴变速范围,最高转速min /2500max r n =,最低转速min /25min r n =,最大切削功率kW P n 10m ax =,在最低转速工作时的功率kW P n 3m in =,主传动机械总效率系数η=0.9。
①初选电机功率根据机床要求来初选电机功率,并要考虑主传动的机械总效率系数,电机功率选得适当,则主轴的恒功率区无缺口或有微小缺口;当电机功率选得较大时,主轴的恒功率区允许有略大的缺口。
在本例中,初选电机功率D P >10kW ,根据电机规格,可选用11kW 或15kW 的电机。
② 确定最小输出功率计算主轴在最低转速(min /25min r n =)达到最小功率(kW P n 3m in =)时,电机应输出的功率min D P :min D P =kW P n 3.39.0/3/m in ==η③计算电机实用的最低转速min D n若D P 选为11kW ,则:min /4501500113.3min min r n P P n d D D D =⨯=⨯=若D P 选为15kW ,则:min /3301500153.3min min r n P P n d D D D =⨯=⨯=式中:d n —电机的基本转速,取d n =1500r/min 。
④计算电机额定转矩D T :)(9550m N n P T dDD ⋅= 当D P 分别取11kW 、15kW 时,D T 约为m N ⋅70和m N ⋅5.95。
⑤计算电机的最小转矩min D T)(9550maxmin m N n PT d D D ⋅=式中:max d n —电机的最高转速,取min /4500max r n d =。
当D P 分别取11kW 、15kW 时,min D T 分别为m N ⋅3.23和m N ⋅8.31。
⑥计算电机实用的恒转矩变速范围DT RminD d DT n n R =当D P 分别取11 kW 、15 kW 时,DT R 分别为3.3和4.5。
电机实用的恒转矩区的变速范围DT R 也是主轴的恒转矩区变速范围的对应值nT R ,即:DT nT R R =。
⑦根据上述计算画出电机实用转速范围的功率转矩特性图,如图8-17(a )、(b )所示。
⑧主轴变速系统其它参数的计算 主轴计算转速j n :min)/(min r R n n nT j ⨯=主轴恒动功率变速范围np R :j np n n R /max =分级变速机构的变速范围f R :dp np f R R R /=式中:dp R —电机的恒功率区变速范围。
min max /d d dp n n R =其中: max d n 、min d n 分别为电机的最高和最低转速。
主传动系统总降速比∑i :d j n n i /=∑以上各参数计算结果如表8-5所示,由表可知:如果选用不同电机功率,而要求主轴在最低转速(min /25min r n =)达到最小功率(kW P n 3m in =)相同 ,则会导致两种方案的主要技术参数有较大差别。
表8-5 主传动两种方案有关数据对照表⑨串联分级变速机构的转速图和功率转矩特性曲线图根据表8-5中的各个参数,可画出两种方案的转速图和对应的功率转矩特性曲线图,如图8-18(a)、(b)为11 kW的电机串联分级变速机构的转速图和功率转矩特性曲线图。
图8 -19 (a)、(b)为15 kW的电机串联分级变速机构的转速图和功率特性曲线图。
从图8-18(b)中可以看出:主轴的恒功率区对应有小缺口,在换档时降低功率约0.5 kW,影响不大,能满足要求。
从图8-19(b)中可以看出:主轴的恒功率区无缺口,但电机功率大,有些浪费,因此,选用11kW的交流调频电机较理想。
⑩结论(a )带有分级变速机构的变速范围f R 取决于交流调速电机恒功率调速范围dp R 和级数Z 。
当电机确定后,要使主轴转速连续的条件是级数比dp R ≤ϕ,否则,主轴转速不连续,产生功率缺口。
(b )分级变速机构的级数Z 的选择应根据设计数控机床的具体要求确定。
通常Z =3时,若dp R =3 时,分级变速机构的恒功率区变速范围可扩大到9左右,主轴转速连续。
(c )选择电机功率时,在满足机床要求的前提下,若无特殊要求,就不必选择较大功率的电机,以免造成浪费。
数控铣床的伺服进给系统设计下面以数控铣床工作台的纵向(X轴)进给系统为例,来说明其特点和结构设计方法。
数控铣床对进给系统的要求集中在精度、稳定性和快速响应三个方面。
1. 传动系统设计伺服电机一般最高转速为1500r/min 或2000r/min。
如果伺服电机通过联轴器与丝杠直接连接,即=1。
假设工作台快速进给的最高速度要求达到=15,取电机的最高转速=1500r/min,则丝杠的最高转速也为1500r/min。
基本丝杠导程为假设定位精度要求为±0.012/300,重复定位精度为±0.006。
则根据精度要求,数控铣床的脉冲当量可定为脉冲。
伺服电机每转应发出的脉冲数达到伺服系统中常用的位置反馈器有旋转变压器和脉冲编码器。
旋转变压器的分解精度为每转2000个脉冲,如果采用旋转变压器方案,则在伺服电机和旋转变压器之间安装5:1的升速齿轮。
采用编码器方案时,因脉冲编码器有每转2000个、2500个、5000个脉冲等数种产品,故编码器后面应加倍频器。
速度反馈装置中,与旋转变压器配套的,可采用测速发电机。
其性能为电机按1000r/mi n输出一定的电压量。
如采用脉冲编码器方案,则可在倍频器后加频率/电压转换器(F/ V)。
其转换比例为每分钟个脉冲,输出电压为(如6V)。
本例中,通过上面的计算知:伺服电机每转发出的脉冲个数为个,故其转换比例仍为6(V)/1000(r/min)。
图8-20为上述两种方案的传动系统图。
这两种方案都可采用,各配不同的数控系统即可。
2. 滚珠丝杠的选择(1)滚珠丝杠精度假设本系统要达到±0.012/300的定位精度,根据要求查阅滚珠丝杠样本,对于1级()精度丝杠,任意300内导程允许误差为0.006,2级()精度丝杠的导程允许误差为0.008。
初步设丝杠的任意300行程内的行程变动量为定位精度的1/3~1/2,即0.004~0.006,因此,可取滚珠丝杠精度为级,即1级精度丝杠。
(2)滚珠丝杠选择滚珠丝杠的名义直径、滚珠的列数和工作圈数,应按当量动载荷选择。
丝杠的最大载荷为切削时的最大进给力加上摩擦力;而最小载荷为摩擦力。
假设最大纵向进给力=5000N,工作台质量300,工件与夹具的最大质量为500,采用贴塑导轨,则:工作台加上工件与夹具的质量为:300+500=800因为贴塑导轨的摩擦因数为0.04,故丝杠的最小载荷(即摩擦力)(N)丝杠最大工作载荷(N)轴向工作载荷(平均载荷)为:(N)其中,、分别为丝杠最大、最小轴向载荷;当载荷按照单调连续或周期性单调连续变化时,则:(2+)/3。
从(1)的计算分析中知:丝杠最高转速为1500r/min,假定工作台最小进给速度为1/min,则丝杠的最低速度为:0.1(r/min)可取为0,则丝杠的平均转速为:(1500+0)/2=750(r/min)故丝杠工作寿命为:式中L—工作寿命,以为一个单位;—丝杠平均转速,r/min;T—丝杠使用寿命,对数控铣床可取T=15000。
当量动载荷为:式中—载荷性质系数,无冲击取1~1.2,一般情况取1.2~1.5,有较大冲击振动时取1.5~2.5,本例中取=1.5;—精度影响系数,对于1、2、3级精度的滚珠丝杠取=1,对于4、5级滚珠丝杠取=0.9,本例中取=1。
根据以上计算,查滚珠丝杠样本中与相近的额定动载荷,使得﹤,然后由此确定滚珠丝杠副的型号和尺寸。