C8T3 水泥的生产工艺
水泥生产流程
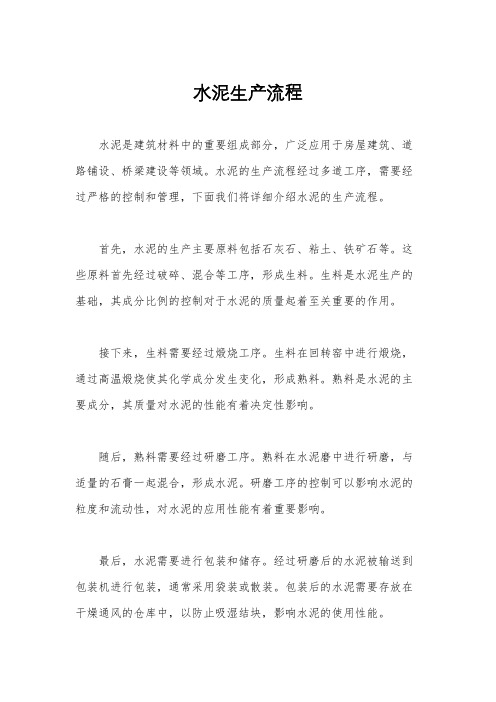
水泥生产流程
水泥是建筑材料中的重要组成部分,广泛应用于房屋建筑、道路铺设、桥梁建设等领域。
水泥的生产流程经过多道工序,需要经过严格的控制和管理,下面我们将详细介绍水泥的生产流程。
首先,水泥的生产主要原料包括石灰石、粘土、铁矿石等。
这些原料首先经过破碎、混合等工序,形成生料。
生料是水泥生产的基础,其成分比例的控制对于水泥的质量起着至关重要的作用。
接下来,生料需要经过煅烧工序。
生料在回转窑中进行煅烧,通过高温煅烧使其化学成分发生变化,形成熟料。
熟料是水泥的主要成分,其质量对水泥的性能有着决定性影响。
随后,熟料需要经过研磨工序。
熟料在水泥磨中进行研磨,与适量的石膏一起混合,形成水泥。
研磨工序的控制可以影响水泥的粒度和流动性,对水泥的应用性能有着重要影响。
最后,水泥需要进行包装和储存。
经过研磨后的水泥被输送到包装机进行包装,通常采用袋装或散装。
包装后的水泥需要存放在干燥通风的仓库中,以防止吸湿结块,影响水泥的使用性能。
在整个生产流程中,需要对原料、生料、熟料和水泥的各道工序进行严格的控制和管理,以确保水泥的质量稳定。
此外,环保和安全也是水泥生产过程中需要重点关注的问题,需要严格遵守相关的环保和安全法规,确保生产过程安全、清洁。
总的来说,水泥的生产流程经过原料准备、煅烧、研磨和包装等多道工序,需要严格控制和管理,以确保水泥的质量和生产过程的安全、环保。
希望通过本文的介绍,读者能对水泥的生产流程有更加深入的了解。
水泥制造流程
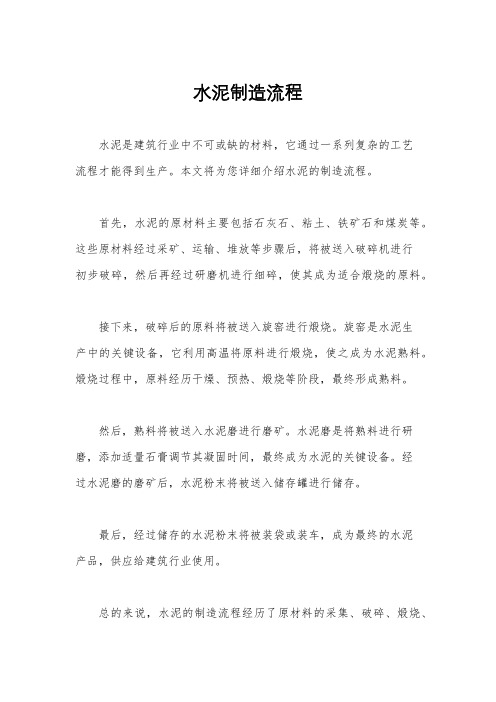
水泥制造流程
水泥是建筑行业中不可或缺的材料,它通过一系列复杂的工艺
流程才能得到生产。
本文将为您详细介绍水泥的制造流程。
首先,水泥的原材料主要包括石灰石、粘土、铁矿石和煤炭等。
这些原材料经过采矿、运输、堆放等步骤后,将被送入破碎机进行
初步破碎,然后再经过研磨机进行细碎,使其成为适合煅烧的原料。
接下来,破碎后的原料将被送入旋窑进行煅烧。
旋窑是水泥生
产中的关键设备,它利用高温将原料进行煅烧,使之成为水泥熟料。
煅烧过程中,原料经历干燥、预热、煅烧等阶段,最终形成熟料。
然后,熟料将被送入水泥磨进行磨矿。
水泥磨是将熟料进行研磨,添加适量石膏调节其凝固时间,最终成为水泥的关键设备。
经
过水泥磨的磨矿后,水泥粉末将被送入储存罐进行储存。
最后,经过储存的水泥粉末将被装袋或装车,成为最终的水泥
产品,供应给建筑行业使用。
总的来说,水泥的制造流程经历了原材料的采集、破碎、煅烧、
磨矿等多个环节,每个环节都至关重要,缺一不可。
只有严格控制每个环节的工艺参数,才能保证水泥产品的质量稳定。
希望本文能为您对水泥制造流程有所了解,谢谢阅读!。
水泥生产工艺技术操作规程
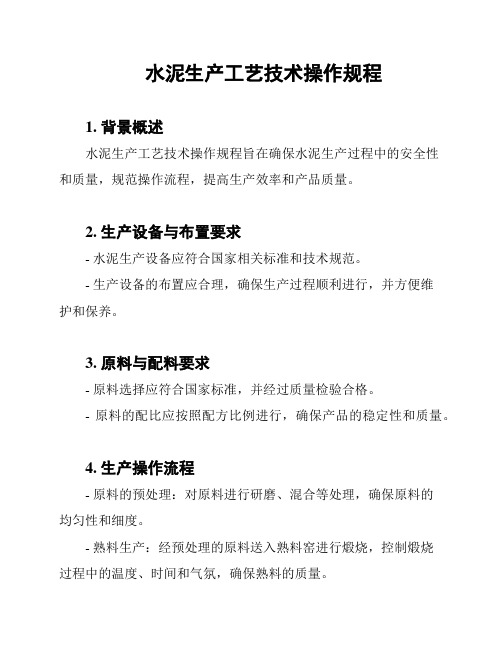
水泥生产工艺技术操作规程1. 背景概述水泥生产工艺技术操作规程旨在确保水泥生产过程中的安全性和质量,规范操作流程,提高生产效率和产品质量。
2. 生产设备与布置要求- 水泥生产设备应符合国家相关标准和技术规范。
- 生产设备的布置应合理,确保生产过程顺利进行,并方便维护和保养。
3. 原料与配料要求- 原料选择应符合国家标准,并经过质量检验合格。
- 原料的配比应按照配方比例进行,确保产品的稳定性和质量。
4. 生产操作流程- 原料的预处理:对原料进行研磨、混合等处理,确保原料的均匀性和细度。
- 熟料生产:经预处理的原料送入熟料窑进行煅烧,控制煅烧过程中的温度、时间和气氛,确保熟料的质量。
- 水泥生产:将熟料经磨机磨细成水泥,控制磨细过程的温度、时间和磨体比表面积,确保水泥的品质。
- 成品包装:将生产好的水泥包装成袋装或散装,按照规定的包装标准进行封装。
5. 质量控制要求- 设置严格的质量控制点,对每个生产环节进行抽样检测,确保产品符合国家相关标准。
- 定期进行设备检查和维护,保证设备的正常运行和产品质量的稳定性。
- 建立质量档案,记录各个批次的生产数据和质量检测结果,对质量进行跟踪和分析。
6. 安全生产要求- 制定安全操作规程,员工必须按照规程操作,防止事故和职业伤害的发生。
- 定期进行安全教育和培训,提高员工的安全意识和应急处理能力。
- 配备必要的安全设施和个人防护用品,确保员工的人身安全。
7. 环境保护要求- 水泥生产过程中,要合理利用资源,降低能耗和物料消耗。
- 控制生产过程中的废气、废水和固体废物的排放,符合国家环保要求。
8. 文件管理与责任追究- 制定文件管理制度,对各类操作规程、记录和报告进行管理和归档。
- 对违反操作规程和质量要求的人员,按照公司相关规定进行责任追究。
以上为《水泥生产工艺技术操作规程》的内容要点,旨在指导水泥生产过程中的操作,并确保生产的安全性、质量和环境保护。
水泥制作流程
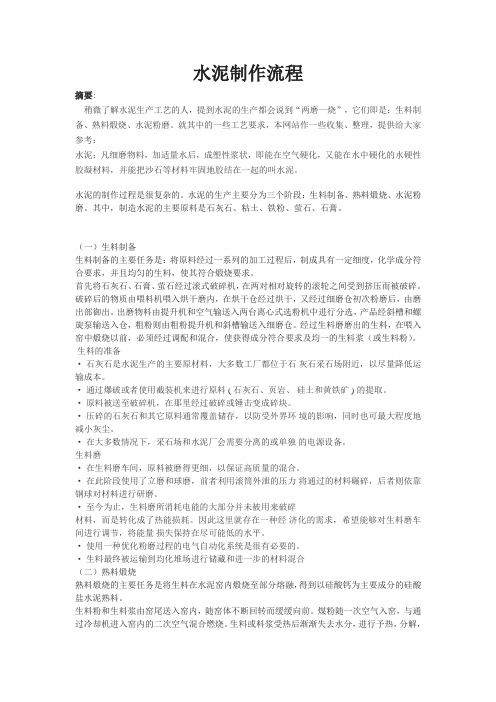
水泥制作流程摘要:稍微了解水泥生产工艺的人,提到水泥的生产都会说到“两磨一烧”,它们即是:生料制备、熟料煅烧、水泥粉磨。
就其中的一些工艺要求,本网站作一些收集、整理,提供给大家参考:水泥:凡细磨物料,加适量水后,成塑性浆状,即能在空气硬化,又能在水中硬化的水硬性胶凝材料,并能把沙石等材料牢固地胶结在一起的叫水泥。
水泥的制作过程是很复杂的。
水泥的生产主要分为三个阶段:生料制备、熟料煅烧、水泥粉磨。
其中,制造水泥的主要原料是石灰石、粘土、铁粉、萤石、石膏。
(一)生料制备生料制备的主要任务是:将原料经过一系列的加工过程后,制成具有一定细度,化学成分符合要求,并且均匀的生料,使其符合煅烧要求。
首先将石灰石、石膏、萤石经过滚式破碎机,在两对相对旋转的滚轮之间受到挤压而被破碎。
破碎后的物质由喂料机喂入烘干磨内,在烘干仓经过烘干,又经过细磨仓初次粉磨后,由磨出部御出。
出磨物料由提升机和空气输送入两台离心式选粉机中进行分选,产品经斜槽和螺旋泵输送入仓,粗粉则由粗粉提升机和斜槽输送入细磨仓。
经过生料磨磨出的生料,在喂入窑中煅烧以前,必须经过调配和混合,使获得成分符合要求及均一的生料浆(或生料粉)。
生料的准备·石灰石是水泥生产的主要原材料,大多数工厂都位于石灰石采石场附近,以尽量降低运输成本。
·通过爆破或者使用截装机来进行原料 ( 石灰石、页岩、硅土和黄铁矿 ) 的提取。
·原料被送至破碎机,在那里经过破碎或锤击变成碎块。
·压碎的石灰石和其它原料通常覆盖储存,以防受外界环境的影响,同时也可最大程度地减小灰尘。
·在大多数情况下,采石场和水泥厂会需要分离的或单独的电源设备。
生料磨·在生料磨车间,原料被磨得更细,以保证高质量的混合。
·在此阶段使用了立磨和球磨,前者利用滚筒外泄的压力将通过的材料碾碎,后者则依靠钢球对材料进行研磨。
·至今为止,生料磨所消耗电能的大部分并未被用来破碎材料,而是转化成了热能损耗。
水泥生产工艺

水泥生产工艺
生产工艺主要是原料加工、配料搅拌、成型、养护等过程,其中配料搅拌包括石灰石和水的重量比例、外加剂用量、矿物掺合料、水泥用量及熟料烧成时间、水泥品种与标号选择等。
水泥生产流程:原材料—磨粉—配料—混合—制粒—熟化(或煅烧)—成品;熟料在成品仓经过一定时间的静置后,需进行破碎以利于下道工序使用,将破碎后的物料进入粉磨系统进行粉磨。
成品经出料口输送至卸车装置。
水泥生产流程中各个环节中主要设备有回转窑、立式辊压机、卧式螺旋预热器、球磨机、制粒机、包装机等。
其中回转窑为整个生产线提供热源。
水泥生产工艺与流程

水泥生产工艺与流程水泥生产工艺与流程通常包括以下几个步骤:原材料采购,砂石破碎,石灰石破碎,粉磨,混合,煅烧,磨煤机,热风炉,烟气处理,包装和存储等。
首先,原材料的采购是水泥生产的第一步。
主要原材料包括石灰石、粘土和矿渣等。
这些原材料通过供应商采购进入水泥厂。
其次,砂石破碎和石灰石破碎是为了将原材料中的大块石料破碎成适合入磨机的小颗粒。
这一步通常使用颚式破碎机和磨辊机进行。
然后,原材料的粉磨是将破碎后的石料经过磨机进行进一步的细磨。
磨机采用的是水泥垂直磨机和水泥球磨机。
磨机通过高速旋转的钢球和辊压力将石料研磨成细粉。
之后,将粉磨后的原材料与适量的矿渣和混合材料进行混合。
混合过程主要是通过给定比例,将原材料进行搅拌混合,以保证水泥的特定化学成分。
接下来,混合后的原材料被送入煅烧炉,进行高温煅烧。
煅烧温度通常在1400-1500℃之间,以确保水泥成分的反应和矿物相转化。
在煅烧过程中,通过磨煤机将煤粉喷入煅烧炉中,以提供煅烧所需的热量。
同时,需要使用热风炉提供的高温风,以维持煅烧过程的恒温。
在煅烧过程中,产生的烟气通过烟气处理设备进行处理,以减少对环境的污染。
烟气处理设备通常包括除尘器、脱硫器和脱氮器等,以去除烟气中的颗粒物、二氧化硫和氮氧化物等有害物质。
最后,经过煅烧和处理后的水泥被送入包装工段,进行包装和存储。
包装通常采用袋装或散装形式,然后将包装好的水泥存储在仓库中,待发运。
综上所述,水泥生产工艺与流程包括原材料采购、砂石破碎、石灰石破碎、粉磨、混合、煅烧、磨煤机、热风炉、烟气处理、包装和存储等多个步骤。
每个步骤都需要严格控制参数,以确保水泥的质量和成分达到标准要求。
水泥生产工艺流程图

水泥生产工艺流程水泥的生产工艺可以简述为两磨一烧,即原料要经过采掘、破碎、磨细和混匀制成生料,生料经1450℃的高温烧成熟料,熟料再经破碎,与石膏或其他混合材一起磨细成为水泥。
一、水泥生产的生料制备1 破碎工艺水泥生产过程中,很大一部分原料要进行破碎,如石灰石、黏土、铁矿石及煤等。
2生料的预均化工艺原料预均化,实现原料的初步均化,。
3 生料的烘干工艺烘干工艺是将生料通过烘干机加热干燥。
烘干设备有回转式和悬浮式烘干机、烘干塔等,回转式烘干机内温度约700℃,排放废气量约1300m3/t料。
4 生料的粉磨工艺二、水泥生产的煅烧目前大中型水泥厂多使用回转窑,小型水泥厂多使用立窑,我国还有50﹪以上的水泥仍使用立窑生产。
1 立窑煅烧立窑工艺的设备是静止的竖窑,分为普通立窑和机械化立窑,属于半干法生产。
立窑的日产量已达250~300t/d。
立窑又分普通立窑和机立窑,普通立窑采用间歇式生产,能耗热耗较高,产生的废气量约3900立米/吨熟料,粉尘浓度15g/m3。
2 新型干法旋窑煅烧它是在旋窑煅烧增加预分解窑与悬浮预热工艺。
生料在预热器以内悬浮状态或沸腾状态下与热气流进行热交换,又在分解炉中加入占总燃料用量50~60%的燃料,使生料在入窑前的碳酸钙分解率达80%以上。
预热分解把生料的预热和部分分解由预热器来完成,代替回转窑部分功能。
(1)物料分散换热80%在入口管道内进行的。
喂入预热器管道中的生料,在与高速上升气流的冲击下,物料折转向上随气流运动,同时被分散。
(2)气固分离当气流携带料粉进入旋风筒后,被迫在旋风筒筒体与内筒(排气管)之间的环状空间内做旋转流动,并且一边旋转一边向下运动,由筒体到锥体,一直可以延伸到锥体的端部,然后转而向上旋转上升,由排气管排出。
(3)预分解预分解技术是在预热器和回转窑之间增设分解炉和利用窑尾上升烟道,设燃料喷入装置,使燃料燃烧的放热过程与生料的碳酸盐分解的吸热过程,在分解炉内以悬浮态或流化态下迅速进行,使入窑生料的分解率提高到90%以上。
水泥生产工艺流程
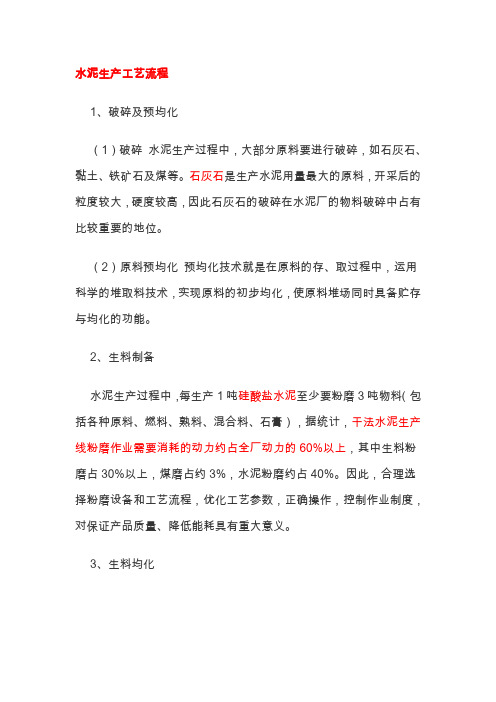
水泥生产工艺流程1、破碎及预均化(1)破碎水泥生产过程中,大部分原料要进行破碎,如石灰石、黏土、铁矿石及煤等。
石灰石是生产水泥用量最大的原料,开采后的粒度较大,硬度较高,因此石灰石的破碎在水泥厂的物料破碎中占有比较重要的地位。
(2)原料预均化预均化技术就是在原料的存、取过程中,运用科学的堆取料技术,实现原料的初步均化,使原料堆场同时具备贮存与均化的功能。
2、生料制备水泥生产过程中,每生产1吨硅酸盐水泥至少要粉磨3吨物料(包括各种原料、燃料、熟料、混合料、石膏),据统计,干法水泥生产线粉磨作业需要消耗的动力约占全厂动力的60%以上,其中生料粉磨占30%以上,煤磨占约3%,水泥粉磨约占40%。
因此,合理选择粉磨设备和工艺流程,优化工艺参数,正确操作,控制作业制度,对保证产品质量、降低能耗具有重大意义。
3、生料均化新型干法水泥生产过程中,稳定入窖生料成分是稳定熟料烧成热工制度的前提,生料均化系统起着稳定入窖生料成分的最后一道把关作用。
4、预热分解把生料的预热和部分分解由预热器来完成,代替回转窑部分功能,达到缩短回窑长度,同时使窑内以堆积状态进行气料换热过程,移到预热器内在悬浮状态下进行,使生料能够同窑内排出的炽热气体充分混合,增大了气料接触面积,传热速度快,热交换效率高,达到提高窑系统生产效率、降低熟料烧成热耗的目的。
(1)物料分散换热80%在入口管道内进行的。
喂入预热器管道中的生料,在与高速上升气流的冲击下,物料折转向上随气流运动,同时被分散。
(2)气固分离当气流携带料粉进入旋风筒后,被迫在旋风筒筒体与内筒(排气管)之间的环状空间内做旋转流动,并且一边旋转一边向下运动,由筒体到锥体,一直可以延伸到锥体的端部,然后转而向上旋转上升,由排气管排出。
(3)预分解预分解技术的出现是水泥煅烧工艺的一次技术飞跃。
它是在预热器和回转窑之间增设分解炉和利用窑尾上升烟道,设燃料喷入装置,使燃料燃烧的放热过程与生料的碳酸盐分解的吸热过程,在分解炉内以悬浮态或流化态下迅速进行,使入窑生料的分解率提高到90%以上。