铸造学07讲铸件凝固温度场.
课件 金属成型理论基础 第五章 铸件的凝固 第一节 铸件的温度场(2)
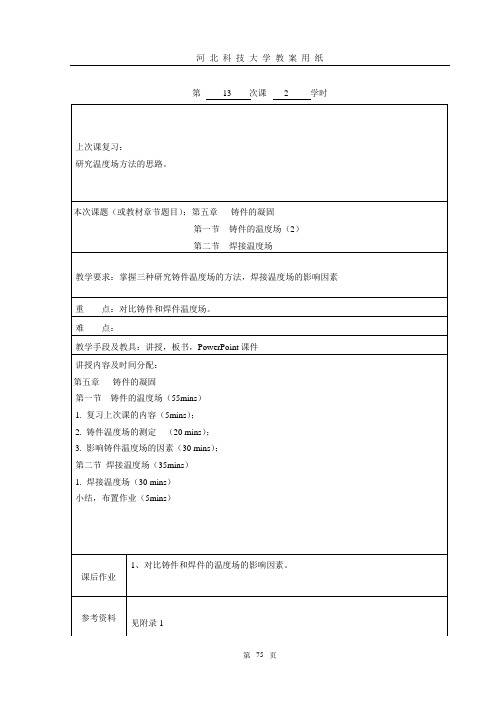
第13 次课 2 学时第五章 铸件的凝固第一节 铸件的温度场(2)三、铸件的温度场的测定测定方法见图3-11 铸件及铸型各部分安放热电偶,然后分别利用多点自动记录装置给出温度与时间的曲线 如图3-12a 其中1、2、3、、、、为铸件中不同位置(距界面间距)每一条曲线代表铸件某一特定位置的温度随时间变化的曲线。
根据图3-12a 可给出铸件断面上不同时刻的温度场图3-12b (叙述曲线的做法)和铸件凝固动态曲线(下一节讲)从温度场曲线看出:○1温度场随时间变化 --- -不稳定温度场; ○2温度场的变化速率---- 温度梯度; 两个例子:—— 图3-13是纯铝圆柱形铸件的温度场a .铸型中的液态金属几乎同时从t 浇 降到t sb .接近铸件表面的合金结晶时释放,阻止了内部合金的温度下降,在曲线上表现出平台;c .拐点出现的时刻说明结晶(凝固前沿)到达的时刻;d .凝固初期,温度梯度大,以后逐渐减慢;e .固溶体合金的温度场与此相似t L 有拐点 t s 没有明显拐点——图3-14共晶型合金的温度场a .铸型内合金很快降至液相线温度b .两个拐点:t L 液相线温度 t s 共晶温度两个概念:等温面(等温线):某一瞬间温度场中温度相同点组成的面(或线)有时温度场用等温面(或线)表示。
用途:不规则的铸件通过测定或通过数值模拟来确定等温面,直观判断铸件的凝固顺序,找出缩孔的位置。
——所以对铸造工艺设计很有意义。
四、影响铸件温度场的因素以上已指出:某一瞬间的温度场可以用等温面表示,即是由不同温度的等温面组成。
温度场任何点的温度沿等温面法线方向上的增加率称为该点的温度梯度:gradt=xt x t lim x ∂∂=∆∆∆(℃/m ) 所以,温度梯度是表示温度场沿单位长度上的温度变化速率,也是时间空间的函数。
gradt 增大 ,铸件的温度场越陡,铸件的凝固速度越大。
下面讨论温度场的影响因素,实际上是温度梯度的影响因素。
铸造学07讲铸件凝固温度场ppt课件

Tw f (t)
Tqx,y,z,t
n
T = n
TwTf
温度场计算的解析法
➢ 解析方法是直接应用现有的数学理论和定律去推导和演绎 数学方程(或模型),得到用函数形式表示的解,也就是 解析解。
➢ 优点:是物理概念及逻辑推理清楚,解的函数表达式能够清楚地表
达温度场的各种影响因素,有利于直观分析各参数变化对温度高低的 影响。
所以得(铸件侧温度分布):
同理可得铸型侧温度场方程式为:
对于公式中的界面温度Ti,可以通过在界面处热流的
连续性条件求出,
• 即:上式中, b1 = λ1 c1 ρ1 ,为铸件的蓄热系 数; b 2 = λ2 c 2 ρ2 ,为铸型的蓄热系数。最后
可得铸件、铸型内温度分布的解析解为:
半无限大平板铸件凝固过程的 一维不稳定温度场(温度分布)
并令:
R V1 A1
➢ 可得一般铸件凝固时间的近似计算公式:
R
K
➢ R为铸件的折算厚度,称为“模数”。“模数法”
也称为“折算厚度法则”。
➢ 从传热学角度来说,模数代表着铸件热容量与散热表 面积之间的比值关系,凝固时间随模数增大而延长。 ——对于形状复杂的铸件,其体积与表面积的计算都 是比较麻烦的,这时可将复杂铸件的各部分看作是形 状简单的平板、圆柱体、球、长方体等单元体的组合, 分别计算出各单元体的模数,但各单元体的结合面不 计入散热面积中。一般情况下: 模数最大的单元体的凝固时间即为铸件的凝固时间。
1)解析法(理论法):
➢ 因铸型温度分布为:T 2b 1 T 1 b 10 b b 2 2 T 20 b 1 T b 110 b b 1 2 T 20 er 2 fx a2t
➢ 所以其温度梯度有:
铸造过程中热场分析

铸造过程中热场分析及其应用在金属液全部浇入型腔后至金属液凝固的这段时间里,型腔内金属液(包括铸件和浇冒系统)以温度为表症的比内能(单位质点含有的能量J/kg)分布即为热场。
在传统的铸造工艺理论中,将铸件几何结构中材料富集部位,也就是几何断面较大的部位确定为热节,并将热节纳入工艺控制重点。
这些都是建立在金属液浇注完这一时刻,型腔内金属液温度都一样的基础上的,然后根据均匀散热的条件,单位比表面积最小的部位即比内能下降最慢的部位,就是最后凝固部位,也即是一般热节所在部位。
但是利用铸件热节分布来安排铸造工艺,在生产实践中往往会出现工艺缺陷,也就是说,铸件局部过热和过热引起的缺陷不一定出现在几何热节处。
为此引入热场概念。
通过对铸型浇注完毕后,金属液总体的温度分布以及随冷却条件的差异导致温度分布变化的研究,确定热场的分布,用比内能的概念取代热节,从而决定铸造工艺的布置,以弥补单纯依靠热节来安排铸造工艺的不足。
一、热场的分类根据铸造工艺的不同,所形成热场对铸件顺序凝固是否有利,热场可分为良性热场和不良热场两种。
以最简单的平板铸件为例,说明铸造工艺布置对热场和铸件缺陷的影响。
图1为不良热场,图2为良性热场。
图1中的铸造工艺布置按几何热节法找不出任何不妥当的地方,但是按此工艺生产的铸件会在A处的位置出现缩松缺陷。
这是由于图1中金属液的温度分布是按图中顺序数的增大而递减的。
导致这一现象的产生原因是铸型的吸热作用和明冒口的辐射散热作用,图中死角部分(序号6)附近的金属液一旦充入就不再流动,在未浇注完毕时就已开始冷却结晶,而中间区域是充型通道,温度始终接近于浇注温度,这个区域附近的型砂温度也比较高,至使在补缩通道中不能形成温度递减的顺序凝固现象,而补缩通道的上游却先与下游凝固,使A处产生缩松缺陷。
因此可以看出,对于几何断面均匀的铸件,在各部位散热条件基本一致时,由于温度分布的不均匀使铸件备部位的比内能不均匀,所以在均匀的质量场中形成了不均匀的热场,即不良热场,对铸件的顺序凝固不利,易产生铸造缺陷。
铸件凝固过程温度场分析计算

毕业设计铸件凝固过程温度场分析计算姓名: XX学号: XX班级: 10自动化(数控)2专业:自动化(数控)所在系:自动化工程系指导教师: XXX铸件凝固过程温度场分析计算摘要铸造是国民经济的重要产业部门之一,一个国家制造工业的规模和水平就靠它来反映。
航空、航天、汽车、机械等各行业的迅速发展,对铸件的需求量越来大,对铸造金属的性能及铸件本身的可靠性等要求也越来越高。
先进制造技术的发展要求铸件的生产向轻型化、精确化、强韧化、复合化及无环境污染方向发展。
铸造温度场是铸件在生产、加工及使用过程中产生缩孔缩松的主要原因,缩孔缩松不仅降低铸件的尺寸精度和使用性能,甚至直接导致铸件报废。
对铸造过程温度场进行数值模拟,可以预测铸件的缩孔缩松,为优化铸造工艺、减少应力、应变导致的铸件缺陷,提高铸件尺寸精度和使用寿命提供科学的参考依据[1]。
此毕业设计就是通过计算机模拟铸件的形成过程,并对其进行相应的温度场分析,根据判据找到缺陷发生的位置,旨在为实际生产提供理论基础,为改进工艺设计作贡献。
关键词:ANSYS;有限元分析;温度场;铸件凝固Casting Solidification Temperature Field Analysis andCalculationABSTRACTCasting is one of the important sectors of national economy, manufacturing industrial scale and level of a country depends on it to reflect. Aviation, aerospace, automotive, machinery and other industries, the rapid development of the to the greater demand for the castings, casting the metal on the performance and reliability requirements of the casting itself more and more is also high. The development of advanced manufacturing technology for casting production to light-duty composite, high-precision, strong, and no environmental pollution.Casting temperature field is castings produced in the process of production, processing and use the main cause of porosity shrinkage, porosity shrinkage not only reduce the size of the casting precision and operational performance, even as a direct result of the casting scrap. A numerical simulation of the temperature field of casting process can predict the shrinkage of the shrinkage, in order to optimize the casting process, reduce the stress and strain caused by the casting defects, improve the casting dimension accuracy and provide scientific reference for service life. The formation of this graduation design is through the computer simulation of casting process, and carries on the corresponding temperature field analysis, according to the criterion of finding defects location and aims to provide theoretical basis for actual production, make contributions to improve process design.Key Words:ANSYS;The finite element analysis;Temperature field;Casting solidification目录第一章绪论 (1)1.1本课题的背景和意义 (1)1.1.1铸件凝固过程温度场分析计算的意义 (1)1.1.2国内外发展状况 (1)1.1.3本课题的研究内容 (1)1.2本课题研究的方法和手段 (1)第二章理论及软件 (3)2.1本论文的理论基础 (3)2.1.1热传递的基本方式 (3)2.1.2导热过程的基本概念 (5)2.1.4ANSYS简介 (9)2.1.5软件功能介绍 (9)第三章软件模拟 (11)3.1建模和ANSYS前处理 (11)3.1.1PRO/E建立铸件模型 (11)3.1.2铸件砂型的建立 (12)3.1.3铸件在ANSYS的前处理过程 (15)3.2温度场求解过程 (22)3.2.1定义对流条件 (22)3.2.2求解设置 (25)3.3基于温度场的分析 (26)3.3.1温度场模拟结果 (26)结论 (31)参考文献 (32)致谢 (33)第一章绪论1.1 本课题的背景和意义1.1.1铸件凝固过程温度场分析计算的意义铸造温度场是铸件在生产、加工及使用过程中产生缩孔缩松的主要原因;铸造应力是铸件在生产、加工及使用过程中产生变形和裂纹的主要原因,缩孔缩松和裂纹不仅降低铸件的尺寸精度和使用性能,甚至直接导致铸件报废。
【材料成型原理--铸造】第4章 液态金属凝固过程中的传热与传质
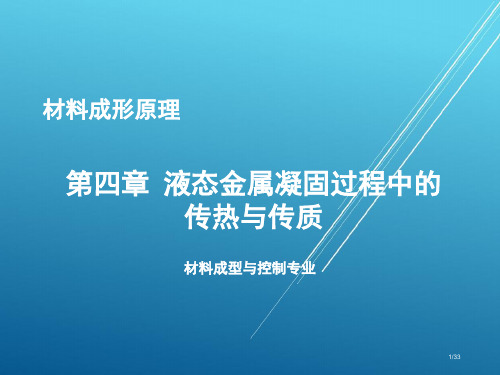
• 2、模型建立
• 温度TL时,开始凝固: • 固 度k相0C:0。百分数dfS;溶质浓
• 液相:溶质浓度几乎不变, 为C0。 • 温度降到T*时,
• 固 数f相S;:溶质浓度C*S;百分
•
液相:溶质浓 数fL。
度
C*L;百
分
28/33
• 当dfSf)S界,溶面这质处些浓固溶度相质增增将加加均d百C匀*L分扩,量散则为到:d整fS个时液,相排中出,溶使质剩量余为液(相C*(L-C1*S-) • (C*L-C*S)dfS=(1-fS)dC*L
30/33
31/33
32/33
33/33
34/33
35/33
• (二)固相无扩散,液相只有有限扩散(无对流或搅拌) 的溶质再分配
• 1、假设: • (1)合金单相凝固; • (2)固相无扩散(接近实际情况); • (3)液相有限扩散(无对流、搅拌); • (4)固液相线为直线,k0为常数; • (5)试样很长,单向放热,平面推进。
• 该两式为平衡凝固时溶质再分配的数学模型。
19/33
CS
1
C0k0 f S (1 k0 )
CL
k0
C0 f L (1 k0 )
• 3、验证 (1)开始凝固时 • 初始条件:fS0,fL1 • 则:CS=k0C0;CL=C0 (2)凝固结束时 • 初始条件:fS1,fL0 • 则:CS=C0;CL=C0/k0
凝固时间与凝固层厚度的平方成正比。
计算结果与实际接近。
适合大平板和结晶间隔小的铸件。
14/33
• 3、“折算厚度”法则
R2 t
K2
R V1 为铸件折算厚度或铸件模数。
A1
铸件凝固过程温度场的数值模拟
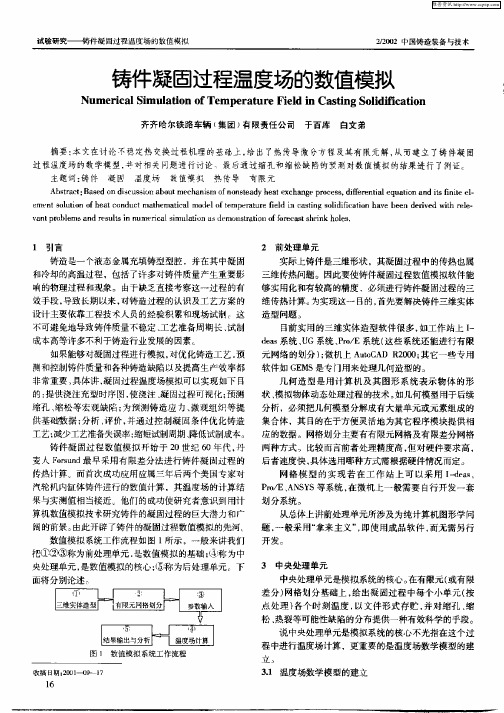
3 中央处 理 单元
从总体上讲前处理单拿来 主义” 即使用成品软件 , , 而无需另行
开 发。
中央处理单元是模拟系统 的核心。 在有限元 ( 或有限 差分) 网格划分基础上 , 给出凝 固过程 中每个小单元 ( 按
点处理 ) 各个时刻温度 , 以文件形式存贮 , 并对缩孔 、 缩
实际上铸件是三维形状 ,其凝固过程中的传热也属
三维传热问题 。因此要使铸件凝固过程数值模拟软件能
够实用化和有较高的精度 ,必须进行铸件凝固过程 的三 维传热计算 。 为实现这一 目的, 首先要解决铸件三维实体
造 型问题 。
目 前实用的三维实体造型软件很多 , 如工作站上 I — da 系统 、G系统、r E系统 ( es U Po / 这些系统还能进行有限
状、 模拟物体动态处理过程 的技术。 如几何模型用于后续
缩孔 、 缩松等宏观缺陷 ; 为预测铸造应力 、 微观组织等提 分析,必须把几何模型分解成有大量单元或元素组成的 供基础数据 ; 分析 、 评价 , 并通过控制凝固条件优化铸造 集合体 ,其 目的在于方便灵活地为其它程序模块提供相 工艺; 减少工艺准备失误率; 缩短试制周期 、 降低试制成本。 应的数据 。网格划分主要有有 限元网格及有限差分网格 铸件凝 固过程数值模拟 开始于 2 0世纪 6 年代 , o 丹 两种方式 比较而言前者处理精度高 , 但对硬件要求高, 麦人 Fr n 最早采用有 限差分法进行铸件凝 固过程 的 os d u 后者速度快 , 具体选用哪种方式需根据硬件情况而定 。 传热计算。而首次成功应用应属 三年后两个美国专家对 网格 模型 的实现 若在 工作 站上可 以采用 Ida 、 - es 汽轮机内缸体铸件进行的数值计算 ,其温度场的计算结 PoE A S S等系统 , r 、N Y / 在微机上一般需要 白行开发一套 果与实测值相当接近。他们 的成功使研究者意识到用计 划 分系统 。 算机数值模拟技术研究铸件的凝固过程的巨大潜力和广 阔的前景。 由此开辟了铸件的凝固过程数值模拟的先河。 数值模拟系统工作流程如图 1 所示 ,一般来讲我们 把①②⑧称为前处理单元 , 是数值模 拟的基础 ; ④称 为中 央处理单元 , 是数值模拟的核心 ; ⑤称为后处理单元 下 面将 分别论 述 ÷
第二章 凝固的温度场
20
三、界面热阻与实际凝固温度场
上述关于铸造过程凝固温度场的分布以及凝固时间的讨 论均将铸件与铸型的接触当作是理想状态下的紧密接触, 实际界面存在热阻。
界面局部接触,有间隙
热阻来源 铸型型腔内表面常存在涂料
实际界面接触状况与涂料状况对界面热阻大小有重要影响。
第二章 凝固温度场
21
第二章 凝固温度场
10
第二节 铸件凝固温度场的解析解法
一、半无限大平板铸件凝固过程的
一维不稳定温度场
二、铸件凝固时间计算 三、界面热阻与实际凝固温度场
四、铸件凝固方式及其影响因素
第二章 凝固温度场
11
一、半无限大平板铸件凝固过程的 一维不稳定温度场
T T10
铸型 λ2 c2 ρ2
x T1 Ti T10 Ti erf 2 a t 1
得:
K
或:
2
K2
18
第二章 凝固温度场
将式(2-24)中的V1与A1推广理解为一般形 状铸件的体积与表面积,并令:
V1 R A1
可得一般铸件凝固时间的近似计算公式:
R K
R为铸件的折算厚度,称为“模数”。“模数法” 也称为“折算厚度法则”。
第二章 凝固温度场
19
从传热学角度来说,模数代表着铸件热容量与散
x erf 2 at 2
x
2 at 0
e
2
d
第二章 凝固温度场
14
代入铸件(型)的边界条件得:
x T1 Ti T10 Ti erf 2 a t 1
T T10
铸件凝固过程中热应力场及热裂的数值模拟研究分析.
铸件凝固过程中热应力场及热裂的数值模拟研究分析1 铸件凝固过程数值模拟的意义及概况自1962年丹麦Fround第1个采用电子计算机模拟铸件凝固过程以来,计算机在铸造工艺研究中得到了广泛的应用,如凝固过程温度场、热应力场的数值模拟,充型过程流速场的数值模拟;组织形态及力学性能的数值模拟等。
通过这些单1或复合过程的数值模拟,可以分析铸件中存在的各种缺陷的产生原因,进而采取相应工艺措施来消除缺陷,实现工艺优化,同时可以节省大量的人力、物力和财力,缩短产品从设计到应用的周期,增强产品的市场竞争能力。
如今,在芬兰,90%以上的铸造厂在日常中应用铸造模拟软件辅助铸造工艺设计;世界上一些大型的汽车公司的铸造厂,如美国的通用、福特,德国的奔驰等,都把数值模拟软件作为1种日常工具来使用。
近10年来,涌现出了许多优秀的铸造过程数值模拟软件,如美国的ProCast、德国的MAGMASoft、芬兰的CastCAE、西班牙的ForCast、日本的CASTEM、法国的SIMULOR软件等。
从功能上看,许多软件可以对砂型铸造、金属型铸造、精密铸造、压力铸造等多种工艺进行温度场、流场、应力场的数值模拟,可以预测铸件的缩孔、缩松、裂纹等缺陷和铸件各部位的组织。
国内在经历了10多年的基础研究和发展后,也出现了一些技术水平接近国外商品化的应用软件,可以进行铸钢、铸铁件砂型铸造时的三维温度场模拟及收缩缺陷的预测,以及对铸钢、铝合金件的热应力场进行模拟。
总的来说,国外软件的通用性强,能进行铸造全过程的数值模拟,并具有较强的后置处理功能及友好的用户界面。
建模方便,易于模型设计和修改,便于用户掌握和使用。
其计算精度与运算速度等方面也能满足需要。
正因为如此,国外模拟软件已经成为实际生产中的有力工具.国内不少用户趋向于采用大型通用工程软件如:COSMOS、ANSYS、ADINA等进行模拟计算。
2 数值模拟的基础性研究2.1 铸件凝固过程温度场数值模拟经过几十年的发展,铸件凝固过程温度场数值模拟技术已日臻成熟。
2.凝固温度场的测定
凝固温度场的测定一、意义和目的铸件温度场是指浇注后,某一时刻铸件内部的温度分布规律。
在温度场中,向着铸件中心的方向上单位长度的温度变化率称为温度梯度。
本实验主要是测定凝固时期各个时刻的铸件温度场。
铸件凝固时期的温度场越陡,即温度梯度越大,则铸件冷却得越快,它的凝固速度就越大。
某一时刻铸件温度场中温度相同点所组成的面称为等温面。
对于在一个温度范围(结晶间隔)内凝固的合金而言,铸件断面中由达到液相线温度的点所组成的面,称为液相线等温面,或称为液相边界。
同样,由达到固相线温度的点组成的面,称为固相线等温面,或称为固相边界。
凝固过程中,铸件断面上液相边界和固相边界之间的区域谓之凝固区域,也就是铸件凝固过程中凝固并存区域。
阐明凝固时期各个时刻的凝固区域大小和它从铸件表面向铸件中心移动规律的曲线,称为凝固动态曲线。
测定凝固动态曲线能够比较全面地描绘铸件凝固过程和研究这种过程。
凝固区域的大小即宽度决定了铸件的凝固方式,即逐层凝固方式、糊状凝固方式和中间凝固方式。
凝固区域于狭窄,铸件越是倾向于逐层凝固方式。
这种凝固方式的铸件容易形成集中缩孔,便于采取措施(例如用冒口)去除铸件中的集中缩孔;铸件的热裂倾向性小和金属液充型能力较好。
凝固区域越宽,铸件越是倾向于糊状凝固方式。
这种凝固方式的铸件容易形成分散性的缩孔即缩松,即使采用冒口亦难以消除这种缩松;铸件的热裂倾向性大和金属液充型能力差。
金属和铸型两方面的各种因素决定了凝固区域的宽窄,也就是决定了铸件的凝固方式。
例如合金的结晶间隔(液相线到固相线之间的温度间隔)越大,铸件的凝固区域就越宽,糊状凝固方式的倾向性就越大。
反之,结晶间隔越小,则铸件的凝固区域越窄,逐层凝固方式的倾向越大。
当合金的化学成分一定时,也就是结晶间隔大小一定时,铸型冷却能力越大,铸件温度场就越陡,温度梯度就越大,凝固区域就越窄,强化了逐渐逐层凝固的倾向,可以削弱铸件糊状凝固的倾向。
将液态金属在同一浇注温度下同时注入几个同样的铸型,经过不同的时间间隔,分别使铸型中尚未凝固的残余液体流失,获得固态金属硬壳,这种研究凝固的方法称为倾出法。
铝合金铸件凝固温度测量及分析_敬必成
铝合金铸件凝固温度测量及分析敬必成代习彬罗定荣刘志先周麟升重庆新红旗缸盖制造有限公司,重庆 402560摘要:通过实验在线测量铸件凝固过程温度变化,绘制凝固过程温度曲线图。
计算出凝固过程中温度梯度、冷却速度、凝固方式。
根据计算结果分析及预测可能产生的缺陷。
关键词:凝固过程;温度梯度;凝固方式;冷却速度铸件是熔融金属注入铸型,凝固后得到的具有一定形状、尺寸和性能的金属零件或零件毛坯[1]。
金属的凝固是铸件形成过程中的重要环节,在很大程度上决定铸件的内部质量。
铸件出现的缩孔、缩松、针孔、浇不足、偏析、冷裂、热裂、变形等缺陷都是在凝固过程中产生的。
所以,认识铸件的凝固规律,对防止产生铸造缺陷、改善铸件组织、提高铸件的性能,有十分重要的意义。
而测定铸件凝固温度场是了解铸件凝固过程的一个非常重要的途径。
铸件的凝固方式主要分为逐层凝固、糊状凝固(体积凝固)及中间凝固。
铝合金铸件几乎都是逐层凝固成型。
逐层凝固的凝固前沿与熔液直接接触,金属由液体转变为固态时发生的体积收缩,直接得到熔液的补充。
因此,凝固过程中产生缩松的倾向小,而在最后凝固部位形成缩松。
在凝固过程中,由于收缩受阻而产生晶间裂纹,容易得到溶液的补充,使裂纹愈合,所以热裂倾向小[2]。
冷却速度对铸件质量也有显著的影响。
冷却速度越大,枝晶间距越小,A356铝合金变质效果越好[3]。
冷却速度对针孔的形成也有影响[4~6]。
冷却速度越快形成的气孔较少,分布比较集中并呈规则的小圆形。
冷却速度慢时形成的气孔不仅数量多分布离散,而且大小形状各不相同[7]。
1 实验条件及方法选取公司正常生产的A356铝合金缸盖A和缸盖B,在火花塞孔(未预铸)中部选取三个点进行温度测量,具体测量点位置如图1、图2所示。
将热电偶固定在测量点后,在线测量凝固过程温度变化,做出凝固过程温度曲线图。
位置“上”为冒口,位置“中”为火花塞孔上部,位置“下”为火花塞孔下部。
图1 缸盖A温度测量点示意图图2 缸盖B温度测量点示意图2 实验结果缸盖A凝固过程温度曲线图如图3所示,缸盖B凝固过程温度曲线图如图4所示。
- 1、下载文档前请自行甄别文档内容的完整性,平台不提供额外的编辑、内容补充、找答案等附加服务。
- 2、"仅部分预览"的文档,不可在线预览部分如存在完整性等问题,可反馈申请退款(可完整预览的文档不适用该条件!)。
- 3、如文档侵犯您的权益,请联系客服反馈,我们会尽快为您处理(人工客服工作时间:9:00-18:30)。
时(即 t = 0 时)的瞬时温度分布。(充填
铸型后铸件冷却凝固开始时刻)
• 边界条件: 边界条件是指计算区域的表
面与周围介质间的热交换情况。
常见的边界条件有以下三类
第一类边界条件: 给定物体表 面温度随时间的变化关系 第二类边界条件: 给出通过物 体表面的比热流随时间的变化 关系(包括对称、绝热面) 第三类边界条件: 给出物体周 围介质温度以及物体表面与周 围介质的换热系数
式中:
a
c
2
—— 导温系数, —— 拉普拉斯运算符号。
2T 2T a 2 2 t x y
T 2T a 2 t x
• 二维传热: T
• 一维传热:
• 上述微分方程式是传热学理论中的最基本 公式,适合于包括铸造、焊接过程在内的 所有热传导问题的数学描述,但在对具体 热场进行求解时,除了上述微分方程外, 还要根据具体问题给出导热体的初始条件 与边界条件。 • 此外思考,凝固潜热在控制方程中是如何 体现?(温度回升法、折算比热法等)
Tw f (t )
T q x, y , z , t n
T = n
Tw T f
• 上述三类边界条件中,以第三 类边界条件最为常见。
温度场计算的解析法
解析方法是直接应用现有的数学理论和定律去推导和演绎 数学方程(或模型),得到用函数形式表示的解,也就是 解析解。 优点:是物理概念及逻辑推理清楚,解的函数表达式能够清楚地表
若实际三维铸件或其局部可以近似地认为是沿着界面的法 线方向一维热传导,这样就构成了半无限大平板铸件凝固 过程的一维不稳定温度场的求解问题。为简化问题、有利 解析法实现 假设: (1)凝固过程的初始状态为:铸件与铸型内部分别为均温, 铸件的起始温度为浇铸温度T 10 ,铸型的起始温度为环境 温度或铸型预热温度T20 ; (2)铸件金属的凝固温度区间很小,可忽略不计; (3)不考虑凝固过程中结晶潜热的释放; (4)铸件的热物理参数 λ1 、c1 、ρ1与铸型的热物理参数 λ2 、c2 、ρ2 不随温度变化;
达温度场的各种影响因素,有利于直观分析各参数变化对温度高低的 影响。
缺点:通常需要采用多种简化假设,而这些假设往往并不适合实际
情况,这就使解的精确程度受到不同程度的影响。目前,只有简单的 一维温度场(“半无限大”平板、圆柱体、球体)才可能获得解析解。
温度场计算的数值求解法 (凝固数值模拟)
• 数值方法又叫数值分析法,是通过对 传热控制微分方程的简化、然后利用 计算机编程,利用计算机求解简化后 的代数模型。得到的近似解也称数值 解。故又称为数值模拟或计算机模拟。 • 常用数值化求解方法有:
• 等温面:空间具有相同温度点的组合面。 • 等温线:某个特殊平面与等温面相截的交线。 • 温度梯度( gradT ):对于一定温度场,沿等温面或等温 线某法线方向的温度变化率。温度梯度越大,图形上反映 为等温面(或等温线)越密集。
热传导过程的偏微分方程
• 三维傅里叶热传导微分方程为:
T 2T 2T 2T 2 a T 2 2 2 t c x y z
(5)铸件与铸型紧密接触,无界面热阻,即 铸件与铸型在界面处等温(Ti)。显然,凝 固过程中,铸件与铸型中的温度分布符合:
该一维非稳态传热微分方程通解为:
式中,C 、D为不定积分常数, erf (x)为高斯误差 函数,其计算式为:
其值可通过查表求得。误差函数的性质为: x=0, erf(x)=0,erf(-x)=-erf(x), erf(∞)=1, erf(-∞)=-1. • 对于铸件侧,有边界条件:x =0( t >0)时, T1 = T2 = Ti ,初始条件:t=0 时,T1 = T10 , 所以得(铸件侧温度分布):
• 差分法:是把原来求解物体内随空间、时 间连续分布的温度问题,转化为求在时间 领域和空间领域内有限个离散点的温度值 问题,再用这些离散点上的温度值去逼近 连续的温度分布。差分法的解题基础是用 差商来代替微商,这样就将热传导微分方 程转换为以节点温度为未知量的线性代数 方程组,得到各节点的数值解。
T
T10 铸型 λ2 c2 ρ2 铸件 λ1 c1 ρ1
半无限大平板铸件凝固过程的 一维不稳定温度场(温度分布)
Ti
T20
0 图2-3无限大平板铸件凝固温度场分布
x
铸件凝固时间
• 铸件的凝固时间:是指从液态金属充满型 腔后至全部凝固完毕所需要的时间。铸件 凝固时间是制订生产工艺、获得稳定铸件 质量的重要依据。
同理可得铸型侧温度场方程式为:
对于公式中的界面温度Ti,可以通过在界面处热流的 连续性条件求出,
• 即:上式中, b1 = λ1 c1 ρ1 ,为铸件的蓄热系 数; b 2 = λ2 c 2 ρ2 ,为铸型的蓄热系数。最后 可得铸件、铸型内温度分布的解析解为:
——其中忽略了可能很重要的界面热阻的影响!
铸件凝固温度场及其 凝固数值模拟概论
北京科技大学钢铁冶金系 张家泉
提纲
凝固传热基本原理 热传导过程的偏微分方程 凝固温度场的求解方法 1)数学解析法 2)数值模拟法 2)铸件凝固时间 3)凝固数值模拟应用举例
凝固传热基本原理
一)温度场基本概念 • 稳定温度场: 不随时间而变的温度场(即温度只是坐标的 函数),其表达式为: T = f(x, y, z) • 不稳定温度场:温度场不仅在空间上变化,并且也随时间 变化的温度场——铸件凝固多属于带相变热释放与冷却传 热的非稳态温度场问题。 T = f (x, y, z, t)
• 有限元法:是根据变分原理来求解热传导 问题微分方程的一种数值计算方法。有限 元法的解题步骤是先将连续求解域分割为 有限个单元组成的离散化模型,再用变分 原理将各单元内的热传导方程转化为等价 的线性方程组,最后求解全域内的总体合 成矩阵。
铸件凝固温度场的解析解法
• 例:半无限大平板铸件凝固过程的一维不 稳定温度场