合成氨工作原理工艺流程
合成氨生产工艺流程
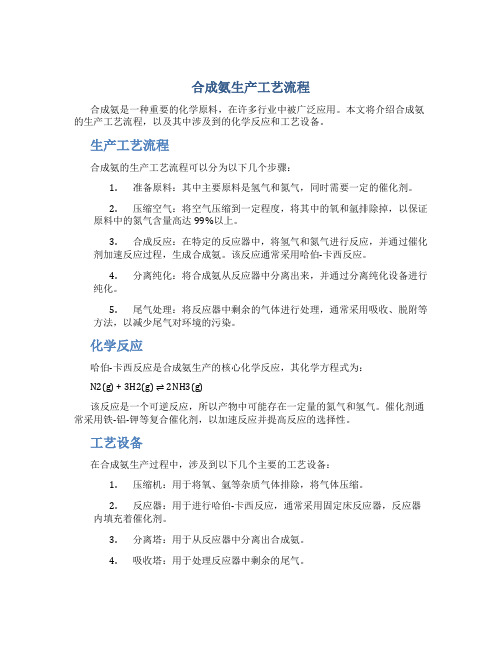
合成氨生产工艺流程合成氨是一种重要的化学原料,在许多行业中被广泛应用。
本文将介绍合成氨的生产工艺流程,以及其中涉及到的化学反应和工艺设备。
生产工艺流程合成氨的生产工艺流程可以分为以下几个步骤:1.准备原料:其中主要原料是氢气和氮气,同时需要一定的催化剂。
2.压缩空气:将空气压缩到一定程度,将其中的氧和氩排除掉,以保证原料中的氮气含量高达99%以上。
3.合成反应:在特定的反应器中,将氢气和氮气进行反应,并通过催化剂加速反应过程,生成合成氨。
该反应通常采用哈伯-卡西反应。
4.分离纯化:将合成氨从反应器中分离出来,并通过分离纯化设备进行纯化。
5.尾气处理:将反应器中剩余的气体进行处理,通常采用吸收、脱附等方法,以减少尾气对环境的污染。
化学反应哈伯-卡西反应是合成氨生产的核心化学反应,其化学方程式为:N2(g) + 3H2(g) ⇌ 2NH3(g)该反应是一个可逆反应,所以产物中可能存在一定量的氮气和氢气。
催化剂通常采用铁-铝-钾等复合催化剂,以加速反应并提高反应的选择性。
工艺设备在合成氨生产过程中,涉及到以下几个主要的工艺设备:1.压缩机:用于将氧、氩等杂质气体排除,将气体压缩。
2.反应器:用于进行哈伯-卡西反应,通常采用固定床反应器,反应器内填充着催化剂。
3.分离塔:用于从反应器中分离出合成氨。
4.吸收塔:用于处理反应器中剩余的尾气。
合成氨是一种十分重要的化学原料,其生产工艺流程麻烦且多种化学反应涉及其中,因此需要一系列的工艺设备来完成整个生产过程。
哈伯-卡西反应是该生产过程的核心反应,通过复合催化剂加速反应过程并提高反应的选择性。
通过合理的工艺流程设计和设备选型,能够实现高效、稳定的合成氨生产。
合成氨的工艺流程
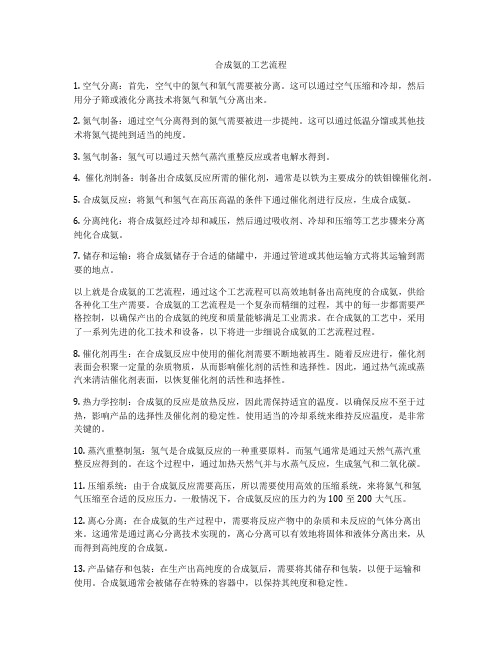
合成氨的工艺流程1. 空气分离:首先,空气中的氮气和氧气需要被分离。
这可以通过空气压缩和冷却,然后用分子筛或液化分离技术将氮气和氧气分离出来。
2. 氮气制备:通过空气分离得到的氮气需要被进一步提纯。
这可以通过低温分馏或其他技术将氮气提纯到适当的纯度。
3. 氢气制备:氢气可以通过天然气蒸汽重整反应或者电解水得到。
4. 催化剂制备:制备出合成氨反应所需的催化剂,通常是以铁为主要成分的铁钼镍催化剂。
5. 合成氨反应:将氮气和氢气在高压高温的条件下通过催化剂进行反应,生成合成氨。
6. 分离纯化:将合成氨经过冷却和减压,然后通过吸收剂、冷却和压缩等工艺步骤来分离纯化合成氨。
7. 储存和运输:将合成氨储存于合适的储罐中,并通过管道或其他运输方式将其运输到需要的地点。
以上就是合成氨的工艺流程,通过这个工艺流程可以高效地制备出高纯度的合成氨,供给各种化工生产需要。
合成氨的工艺流程是一个复杂而精细的过程,其中的每一步都需要严格控制,以确保产出的合成氨的纯度和质量能够满足工业需求。
在合成氨的工艺中,采用了一系列先进的化工技术和设备,以下将进一步细说合成氨的工艺流程过程。
8. 催化剂再生:在合成氨反应中使用的催化剂需要不断地被再生。
随着反应进行,催化剂表面会积聚一定量的杂质物质,从而影响催化剂的活性和选择性。
因此,通过热气流或蒸汽来清洁催化剂表面,以恢复催化剂的活性和选择性。
9. 热力学控制:合成氨的反应是放热反应,因此需保持适宜的温度。
以确保反应不至于过热,影响产品的选择性及催化剂的稳定性。
使用适当的冷却系统来维持反应温度,是非常关键的。
10. 蒸汽重整制氢:氢气是合成氨反应的一种重要原料。
而氢气通常是通过天然气蒸汽重整反应得到的。
在这个过程中,通过加热天然气并与水蒸气反应,生成氢气和二氧化碳。
11. 压缩系统:由于合成氨反应需要高压,所以需要使用高效的压缩系统,来将氮气和氢气压缩至合适的反应压力。
一般情况下,合成氨反应的压力约为100至200大气压。
合成氨工艺及反应原理简介

合成氨工艺及反应原理简介合成氨工艺采用烃类蒸汽转化法。
天然气经加压至4.05MPa,经预热升温在脱硫工序脱硫后,与水蒸汽混合,进入一段转化炉进行转化制H2,随后进入二段转化炉,在此引入空气,转化气在炉内燃烧放出热量,供进一步转化,同时获得N2。
工艺气经余热回收后,进入变换系统,将CO变为CO2,随后经脱碳、甲烷化反应除去CO和CO2,分离出的CO2送往尿素工艺。
工艺气进入分子筛系统除去少量水份,为合成氨提供纯净的氢氮混合气。
氢氮混合气经压缩至14MPa,送入合成塔进行合成氨的循环反应,少量惰性气体经过普里森系统分离进行回收利用。
产品氨送往尿素工艺和氨罐保存。
合成氨工艺的5个过程:1、天然气脱硫:R-SH+H2=RH+H2S H2S+ZnO=H2O(汽)+ZnS2、转化CH4+H20(汽)=CO+3H2 CH4+2H2O(汽)=CO2+4H2 (H2+ 1/2 O2=H2O)3、变换:CO+H2O(汽)=CO2+H24、脱碳:1)K2CO3+CO2+H2O⇔2KHCO32KHCO3⇔K2CO3+CO2+H2O2)甲烷化:CO+3H2=CH4+H2O CO2+4H2=CH4+2H2O5、N2+3H2=2NH31 脱硫系统工艺流程及原理1.1流程天然气进入界区后分为两路:一路作原料气,另一路作燃料气。
原料天然气进入原料气压缩机吸入罐116-F,除去携带的液体,经过原料气压缩机102-J被压缩到4.05MPa(G),经过原料气预热盘管预热到399℃,接着原料气与来自合成气压缩机103-J一段的富氢气混合。
经过Co-Mo加氢器101-D把有机硫转换成H2S,将3 ml/m3的有机硫转化为无机硫,原料气中总硫为30~90ml/m3左右,经氧化锌脱硫槽脱硫至总硫小于0.5mg/m3。
随后进入氧化锌脱硫槽,天然气中的硫化物被ZnO所吸附,制得合格原料气。
ZnO脱硫槽共二个,可以串联或并联操作,一般串联操作。
阀门及管线的配置可以使任何一个脱硫槽停止使用而另一个继续运转。
合成氨的工艺流程

合成氨的工艺流程
合成氨是一种重要的化工原料,广泛应用于化肥、医药、塑料等多个领域。
其工艺流程主要包括氮气和氢气的催化反应,下面将详细介绍合成氨的工艺流程。
首先,合成氨的工艺流程是通过哈伯-玻斯曼过程实现的。
在工业上,通常采用铁-铝催化剂进行合成氨的催化反应。
反应的化学方程式为N2 + 3H2 → 2NH3。
在反应过程中,氮气和氢气在催化剂的作用下发生反应,生成氨气。
其次,合成氨的工艺流程需要高温高压条件。
反应温度通常在400-500摄氏度,压力在100-200大气压。
高温高压条件有利于提高反应速率和转化率,从而提高合成氨的产率。
然后,合成氨的工艺流程需要进行氮气和氢气的预处理。
氮气通常来自空分设备,需要进行脱氧、脱水等处理,以保证氮气的纯度和干燥度;而氢气通常来自重整装置,也需要进行脱氧、脱硫等处理,以保证氢气的纯度和干燥度。
此外,合成氨的工艺流程还需要进行氨气的分离和净化。
合成
氨反应产生的氨气中通常伴随着少量的氮气、氢气、水蒸气和杂质气体,需要进行分离和净化,以得到高纯度的合成氨产品。
最后,合成氨的工艺流程还需要进行废气处理。
合成氨反应产生的废气中含有一定量的氮气、氢气和氨气,以及少量的催化剂粉尘和有机物,需要进行处理,以达到环保排放标准。
综上所述,合成氨的工艺流程是一个复杂的化学过程,需要高温高压条件下进行氮气和氢气的催化反应,同时进行氮气和氢气的预处理,以及氨气的分离和净化,最终进行废气处理。
这一工艺流程的稳定运行对设备的稳定性和操作技术都有较高要求,但合成氨作为重要的化工原料,其生产工艺的不断改进和优化将对化工行业的发展起到积极作用。
合成氨的工艺流程
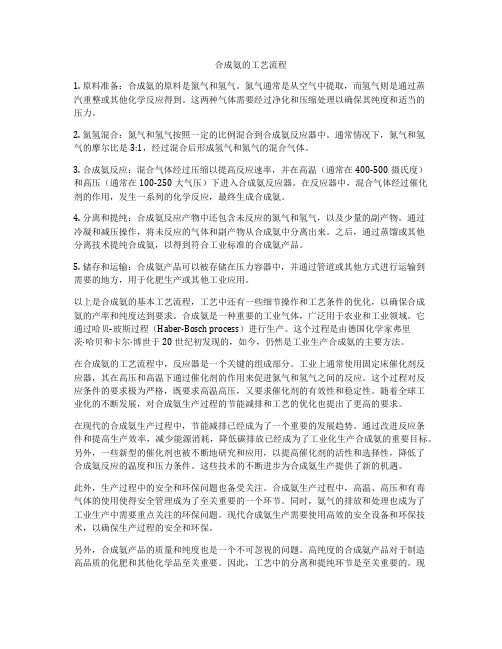
合成氨的工艺流程1. 原料准备:合成氨的原料是氮气和氢气。
氮气通常是从空气中提取,而氢气则是通过蒸汽重整或其他化学反应得到。
这两种气体需要经过净化和压缩处理以确保其纯度和适当的压力。
2. 氮氢混合:氮气和氢气按照一定的比例混合到合成氨反应器中。
通常情况下,氮气和氢气的摩尔比是3:1,经过混合后形成氢气和氮气的混合气体。
3. 合成氨反应:混合气体经过压缩以提高反应速率,并在高温(通常在400-500摄氏度)和高压(通常在100-250大气压)下进入合成氨反应器。
在反应器中,混合气体经过催化剂的作用,发生一系列的化学反应,最终生成合成氨。
4. 分离和提纯:合成氨反应产物中还包含未反应的氮气和氢气,以及少量的副产物。
通过冷凝和减压操作,将未反应的气体和副产物从合成氨中分离出来。
之后,通过蒸馏或其他分离技术提纯合成氨,以得到符合工业标准的合成氨产品。
5. 储存和运输:合成氨产品可以被存储在压力容器中,并通过管道或其他方式进行运输到需要的地方,用于化肥生产或其他工业应用。
以上是合成氨的基本工艺流程,工艺中还有一些细节操作和工艺条件的优化,以确保合成氨的产率和纯度达到要求。
合成氨是一种重要的工业气体,广泛用于农业和工业领域。
它通过哈贝-玻斯过程(Haber-Bosch process)进行生产。
这个过程是由德国化学家弗里茨·哈贝和卡尔·博世于20世纪初发现的,如今,仍然是工业生产合成氨的主要方法。
在合成氨的工艺流程中,反应器是一个关键的组成部分。
工业上通常使用固定床催化剂反应器,其在高压和高温下通过催化剂的作用来促进氮气和氢气之间的反应。
这个过程对反应条件的要求极为严格,既要求高温高压,又要求催化剂的有效性和稳定性。
随着全球工业化的不断发展,对合成氨生产过程的节能减排和工艺的优化也提出了更高的要求。
在现代的合成氨生产过程中,节能减排已经成为了一个重要的发展趋势。
通过改进反应条件和提高生产效率,减少能源消耗,降低碳排放已经成为了工业化生产合成氨的重要目标。
合成氨各工序工艺详细流程

合成氨各工序工艺详细流程合成氨是一种重要的化工原料,广泛用于合成各类农药、肥料、化学品等。
下面将详细介绍合成氨的工序和流程。
合成氨的工艺主要分为三个步骤:气体净化、气体压缩和反应制氨。
1.气体净化:合成氨的原料气体主要有空气和甲烷。
在进入反应装置之前,需要进行气体净化处理。
空气首先经过过滤装置去除微小杂质、灰尘和固体颗粒物。
然后通过制冷装置降低气体温度,使其中的水蒸气凝结成液体,然后被排放。
甲烷通过碳分子筛吸附去除杂质。
这样可以保证反应装置中气体的纯度和稳定性。
2.气体压缩:经过气体净化后的空气和甲烷被分别压缩到一定压力,以满足反应器中的需求。
通常使用压缩机进行压缩,然后将压缩后的气体分别输送到反应器中。
3.反应制氨:反应制氨是整个过程的关键步骤。
通常采用哈柏法(Haber-Bosch)来实现反应制氨。
反应器中,高温高压的空气与甲烷的混合气体通过催化剂床进行催化反应。
常用的催化剂是铁与铁-铝的混合物,也可以加入少量的钾、镁等元素。
反应是一个放热反应,反应温度一般在380-550°C 之间,压力一般在1.7-3.5 MPa之间。
催化剂的存在可以提高反应速率,但也会增加反应的等离子体强度,导致了碳催化剂和蒸汽的选择性降低,产生非氮气杂质。
反应过程中,氮气与氢气进行反应生成氨气。
原料气体经过催化剂床后,反应转化率不高,需要多次通过催化剂床进行反应。
一般采用多级反应器和中间冷却装置,提高氨气的产率和纯度。
经过多级反应后,氨气还需要进行冷却和净化处理,以达到合成氨的纯度要求。
以上是合成氨的工序和流程的详细介绍。
合成氨的过程需要进行气体净化、气体压缩和催化反应制氨。
这个过程需要确保原料气体的纯度和稳定性,通过压缩提高原料气体的压力,催化剂的存在可以提高反应速率和转化率。
经过多级反应,最终得到高纯度的合成氨。
合成氨工艺的不断优化和改进,可以提高合成氨的生产效率和氨气的纯度,降低生产成本。
合成氨工艺流程
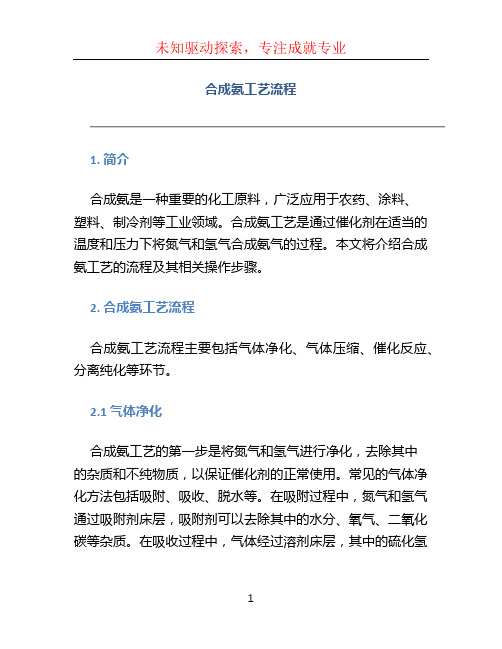
合成氨工艺流程1. 简介合成氨是一种重要的化工原料,广泛应用于农药、涂料、塑料、制冷剂等工业领域。
合成氨工艺是通过催化剂在适当的温度和压力下将氮气和氢气合成氨气的过程。
本文将介绍合成氨工艺的流程及其相关操作步骤。
2. 合成氨工艺流程合成氨工艺流程主要包括气体净化、气体压缩、催化反应、分离纯化等环节。
2.1 气体净化合成氨工艺的第一步是将氮气和氢气进行净化,去除其中的杂质和不纯物质,以保证催化剂的正常使用。
常见的气体净化方法包括吸附、吸收、脱水等。
在吸附过程中,氮气和氢气通过吸附剂床层,吸附剂可以去除其中的水分、氧气、二氧化碳等杂质。
在吸收过程中,气体经过溶剂床层,其中的硫化氢等有毒气体被吸收掉。
同时,还可以使用脱水剂去除气体中的水分。
2.2 气体压缩在气体净化后,将净化后的氮气和氢气进行压缩,提高其压力,以便后续的催化反应。
氮气和氢气分别进入压缩机进行压缩,压缩机通常采用多级压缩,保证气体压力的稳定和可控。
2.3 催化反应经过气体压缩后的氮气和氢气进入催化剂床层,进行合成氨的催化反应。
催化剂通常采用铁、钼或镍等金属催化剂,催化剂在适当的温度和压力下,使氮气和氢气发生反应,生成合成氨气。
催化反应是一个放热反应,需要控制温度以避免过高的温度导致副反应的发生。
2.4 分离纯化经过催化反应生成的合成氨气含有大量的副产物和未反应的氮气、氢气等杂质。
在分离纯化环节中,需要进行吸附、压缩、蒸馏等操作,将合成氨气中的杂质去除,提高纯度。
常见的分离纯化方法包括低温吸附法、压缩法和蒸馏法。
3. 工艺条件和参数合成氨工艺的实施需要满足一定的工艺条件和参数,以确保反应的进行和产出的质量。
常见的工艺条件和参数包括温度、压力、催化剂种类和配比、气体流速等。
3.1 温度催化反应的温度是合成氨工艺中的关键参数之一。
温度过高会导致副反应的发生,影响合成氨气的产量和纯度;温度过低则会降低反应速率。
一般情况下,催化反应的温度在300-500°C之间控制。
室温合成氨 高压氮气流 石墨 催化剂
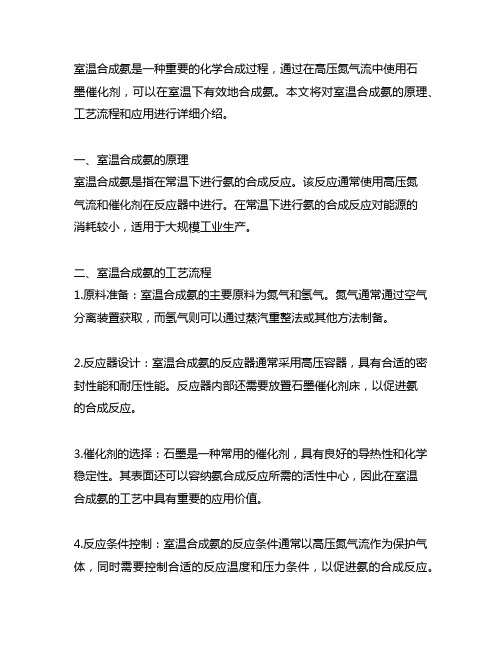
室温合成氨是一种重要的化学合成过程,通过在高压氮气流中使用石墨催化剂,可以在室温下有效地合成氨。
本文将对室温合成氨的原理、工艺流程和应用进行详细介绍。
一、室温合成氨的原理室温合成氨是指在常温下进行氨的合成反应。
该反应通常使用高压氮气流和催化剂在反应器中进行。
在常温下进行氨的合成反应对能源的消耗较小,适用于大规模工业生产。
二、室温合成氨的工艺流程1.原料准备:室温合成氨的主要原料为氮气和氢气。
氮气通常通过空气分离装置获取,而氢气则可以通过蒸汽重整法或其他方法制备。
2.反应器设计:室温合成氨的反应器通常采用高压容器,具有合适的密封性能和耐压性能。
反应器内部还需要放置石墨催化剂床,以促进氨的合成反应。
3.催化剂的选择:石墨是一种常用的催化剂,具有良好的导热性和化学稳定性。
其表面还可以容纳氨合成反应所需的活性中心,因此在室温合成氨的工艺中具有重要的应用价值。
4.反应条件控制:室温合成氨的反应条件通常以高压氮气流作为保护气体,同时需要控制合适的反应温度和压力条件,以促进氨的合成反应。
5.产品分离纯化:室温合成氨反应结束后,需要对产物进行分离和纯化处理,以获得高纯度的氨气。
三、室温合成氨的应用室温合成氨具有广泛的应用价值,主要用于化工行业的氨合成及相关领域的制氢反应。
具体包括:- 合成氨肥料的生产:氨是植物生长过程中必需的氮源,因此被广泛用于合成氨肥料的生产。
- 化学工业中的氨制备:氨用于生产硝酸、尿素等化工产品。
- 氨的储运和制冷:由于氨易液化,因此还用于工业领域的制冷和储运等方面。
室温合成氨的工艺具有能源消耗小、成本低等优点,因此在工业生产中具有重要的应用前景,尤其对于一些无法进行高温高压氨合成的场合具有特殊意义。
室温合成氨是一种重要的化学合成过程,利用高压氮气流和石墨催化剂可以在室温下高效地合成氨。
该工艺的原理、工艺流程和应用具有重要的工业应用意义,对于促进氨合成技术的发展和工业化生产具有重要的推动作用。
- 1、下载文档前请自行甄别文档内容的完整性,平台不提供额外的编辑、内容补充、找答案等附加服务。
- 2、"仅部分预览"的文档,不可在线预览部分如存在完整性等问题,可反馈申请退款(可完整预览的文档不适用该条件!)。
- 3、如文档侵犯您的权益,请联系客服反馈,我们会尽快为您处理(人工客服工作时间:9:00-18:30)。
合成氨工作原理与工艺流程
摘要:本文通过介绍氨合成的基本原理,研究了温度,压力、空速以及氢氮比对氨合成反应的影响,阐述了往复循环机,透平循环机,合成塔工艺流程
关键词:氨工作;原理;工艺流程
abstract: this paper introduces the basic principle of ammonia synthesis, analyzes the effects of temperature, pressure, space velocity and ratio of hydrogen to nitrogen of ammonia synthesis reaction, elaborated the reciprocating cycle engine, turbine circulation machine, synthetic tower process
key words: ammonia; principle; technical process
中图分类号:tu74文献标识码:a文章编号:2095-2104(2012)05-0020-02
一、氨合成的基本原理
氨是由气态氢和氮在氨触媒的作用下反应生成的,其反应式为:3h2+n2=2nh3+热量这是一个可逆、放热、体积缩小的反应,对其反应机理存在着不同的观点,一般认为:氮在铁催化剂上被活性吸附,离解为氮原子,然后逐步加氢,连续生成nh、nh2和nh3。
即:n2(扩散)→2n(吸附)→2nh(吸附)→2nh2(吸附)→ 2nh 3(脱附)→2nh3(扩散到气相)由质量作用定律和平衡移动原理可知:1.温度升高,不利于反应平衡而有利于反应速度。
2.压
力愈高愈有利于反应平衡和速度。
3.氢氮气(比例3:1)含量越高越有利于反应和速度。
4.触媒不影响反应平衡,但可以加快反应速度。
二、温度对氨合成反应的影响
1、氨合成反应是一个可逆放热反应。
当反应温度升高时,平衡向着氨的分解方向移动;温度降低反应向着氨的生成方向移动。
因此,从平衡观点来看,要使氨的平衡产率高,应该采取较低的反应温度。
2、但是从化学反应速度的观点来看,提高温度总能使反应的速度加快,这是因为温度升高分子的运动加快,分子间碰撞的机率增加,同时又使化合时分子克服阻力的能力加大,从而增加分子有效结合的机率。
3、总之,温度低时,反应有利于向合成氨的方向进行,但是氨合成的反应速度较低;提高温度不利于向氨的合成方向移动,但反应速度可以增加。
在实际生产中反应温度的选择主要决定于氨合成催化剂的性能。
三、压力对氨合成反应的影响
1、氨的合成反应是一个分子的氮与三个分子的氢结合生成两个分子的氨,即氨合成反应是分子数目减少、体积缩小的反应,提高压力,可使反应向着生成氨的方向进行。
对于氨合成反应来说,提高压力就是提高反应气体的浓度,从而增加反应分子间碰撞的机会,加快了反应的速率。
2、总之,增加压力对氨的合成反应是有利的,既能增大平衡转化率,又能加快反应速率。
但压力也不宜过高,否则,不仅增加动力的消耗,而且对设备和材料的要求也较高。
根据我国具体情况,目前在小型合成氨厂,设计压力一般为31.4mpa。
四、空速对氨合成反应的影响
1、气体与催化剂接触时间的长短,通常用空速来表示。
它的物理意义是:在标准状况下,单位时间内在1m3的催化剂上所通过的气体体积。
其单位为m3(标)气体/(m3催化剂h),或简写为h-1。
2、在一定的合成条件下,空速增加,气体与催化剂接触时间减少,出合成塔气体氨含量降低。
增加空间速度可以提高氨的产量。
但由于空间速度的增加,每生产一吨氨所需的循环气量,输送气体所需克服的阻力等都要增大,因而消耗的能量也随之加大。
尤其是空间速度过大,从合成塔出来的气体带出的热量增多,会使催化剂床层的温度难以控制,并使循环气中氨不易冷凝。
五、氢氮比对氨合成反应的影响
根据平衡移动原理,如果改变平衡体系的浓度,平衡就向减弱这个改变的方向移动。
氨合成反应的进行,是按h2/n2=3:1的比例消耗的,因此提高氢气、氮气的分压,维持h2/n2=3:可以提高平衡氨含量。
从氨合成反应速度可知,在非平衡的状态下,适当增加氮的分压对催化剂吸附氮的速度有利,因为氮的活性吸附是氨合成反应过程的控制步骤。
在一般的生产条件下,氨产率只能达到平衡值的50%~70%,因此,在生产中应适当提高氮的比例,一般控制
循环气中氢氮比在2.2~2.8之间较为适宜。
六、往复循环机工艺流程
经合成反应,水冷器冷却、氨分离器分离后的混合气体,进入循环机气缸压缩提高压力,再送入系统与新鲜气混合进入合成塔。
七、透平循环机工艺流程
1、主气体工艺流程从高压机来的新鲜气少部分进入保护气系统,大部分经过滤油器滤油后与从氨分出来的气体混合,经冷凝塔、氨冷器、再进入冷凝塔分离氨后,从冷凝塔二次出口出来,分两路从机身两侧对称进入高压筒体内,气体从电机与高压筒体的环隙纵向流过,带走电机散发的热量,然后再经中间接筒的气孔与保护气汇合进入叶轮,经压缩后送至合成塔。
从合成塔出来的气体经水冷器冷却(ⅱ系统先经中锅),再经氨分离器分离氨后与高压机来的新鲜气混合进入冷凝塔,依此循环。
2.、保护气工艺流程从高压机岗位来的少量新鲜气经小氨冷器冷却后进入气水分离器分离掉其中的水和油,再经硅胶干燥器吸收气体中残存的水份,干燥后的气体进入透平机电机的定子与转子间的环隙,直接带走电机的热量,与循环气在中间接筒汇合后再进入透平机的叶轮压缩。
3.、硅胶再生工艺流程由高压机送来的少量新鲜气或事故氮气(500-700nm3/h)经氨冷器冷却、气水分离器分离水和油后,进入电加热器提高温度(≤180℃)后进入需再生的硅胶干燥器,依靠气体的热量将硅胶吸附的水份蒸发并进行干燥,出干燥器的气体由
放空管放空或回收,同时将水份带走。
当干燥器气体出口温度达100-120℃后表明再生合格。
八、合成塔工艺流程
1、自压缩机来的新鲜气分离油水后,进入ⅰ、ⅱ、ⅲ系统与循环机来的循环气同时进入滤油器分离油污,经ⅰ、ⅱ、ⅲ系统冷凝塔上部予冷后,入氨冷器进行二次冷却,入冷凝塔下部进行二次分离,气体上升至冷凝塔上部予热后,经ⅰ、ⅱ、ⅲ系统主、副阀进入合成塔,在触媒的作用下合成为氨。
ⅰ、ⅲ系统合成塔出口气体、ⅱ系统合成塔二次出口气体(ⅱ系统合成塔一次出口气体入中锅,再进合成塔)经水冷器,氨分离器进行一次冷却分离后,进入循环机补充压力送往滤油器,连续循环。
2、从压缩出来的氢氮气经滤油器分离掉油、水等杂质后与循环气混合进入冷凝塔底部分离器,分离掉的液氨去球罐,循环气到上部换热器换热,出冷凝塔后进入透平循环机加压后,进入合成塔环隙与内件换热,从底部出合成塔后进入热交(管外)换热,换热后的气体再次进入合成塔底部换热器(管外)换热,而后由中心管到触媒层,触媒层内循环气由上至下开始合成反应,出触媒层后进入合成塔底部换热器(管内)换热,而后出合成塔进锅炉换热产蒸汽,出锅炉后循环气再次进入热交(管内)换热,进入水冷进行冷却,冷却后进入氨分离器分离液氨,分离掉的液氨去球罐,循环气进冷凝塔上部换热器(管内)冷却,而后进氨冷器进一步冷却,出氨冷器后与补气油分来的新鲜气混合进入冷凝塔底部分离器,如此往复
循环。
一次、二次分离之液氨送往氨库-吹除气送往氨回收-氨冷器液氨来自氨库,气氨送往联碱或氨水站。