CA1041轻型车制动系统设计解析
EQ1041汽车制动系统的设计-任务书

并通过设计,锻炼了理论联系实际的能力和工程应用的能力,同时培养了学生开拓创新的能力和与人交往的能力。
二、设计(论文)内容、技术要求(研究方法)
1.主要研究内容
(9)毕业设计答辩准备及答辩第17周(6月20日~6月24日)
五、主要参考资料
[1]刘惟信 . 汽车设计 . 清华大学出版社
[2]制动系统的发展现状及趋势 .汽车研究与开发2005.1
[3]周志立 . 汽车ABS原理与结构 ,机械工业出版社
[4]陈家瑞 . 汽车构造 ,机械工业出版社
[5]王国林 . 汽车底盘构造及维修 ,高等教育出版社
[6]齐晓杰 . 汽车液压、液力与气压传动技术,化学工业出版社
[7]王世刚 . 机械设计实践 . 哈尔滨工程大学出版社
[8]戴枝荣 . 工程材料 . 高等教育出版社
[9]王宝玺 . 汽车拖拉机制造工艺学,机械工业出版社
[10]王望予 . 汽车设计,机械工业出版社
六、备注
指导教师签字:
年 月 日
教研室主任签字:
在调查研究的基础上,分析轻型汽车的结构特点和使用条件,设计一套完整的汽车制动系统,包括制动系统的类型的选择、制动系统的总体布置形式,制动器的类型选择和结构设计,及ABS结构型式及工作原理设计。
2.研究方法
1)在调研和搜集资料的基础上,认真分析制动系统的结构特点,确定合理的设计参数;
2)确定制动系统的结构类型和工作原理,完成制动系统的总布置设计;
2)设计有一定创新性。
三、设计(论文)完成后应提交的成果
车辆工程毕业设计(论文)ca1041轻型商用车制动系统设计【全套图纸】
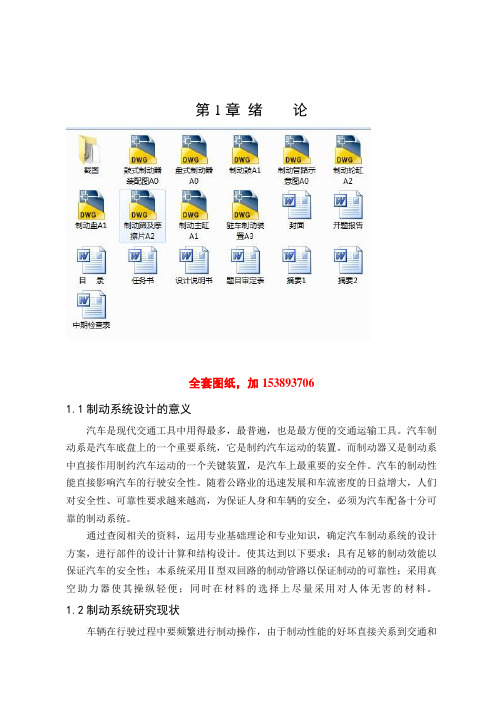
第1章绪论全套图纸,加1538937061.1制动系统设计的意义汽车是现代交通工具中用得最多,最普遍,也是最方便的交通运输工具。
汽车制动系是汽车底盘上的一个重要系统,它是制约汽车运动的装置。
而制动器又是制动系中直接作用制约汽车运动的一个关键装置,是汽车上最重要的安全件。
汽车的制动性能直接影响汽车的行驶安全性。
随着公路业的迅速发展和车流密度的日益增大,人们对安全性、可靠性要求越来越高,为保证人身和车辆的安全,必须为汽车配备十分可靠的制动系统。
通过查阅相关的资料,运用专业基础理论和专业知识,确定汽车制动系统的设计方案,进行部件的设计计算和结构设计。
使其达到以下要求:具有足够的制动效能以保证汽车的安全性;本系统采用Ⅱ型双回路的制动管路以保证制动的可靠性;采用真空助力器使其操纵轻便;同时在材料的选择上尽量采用对人体无害的材料。
1.2制动系统研究现状车辆在行驶过程中要频繁进行制动操作,由于制动性能的好坏直接关系到交通和人身安全,因此制动性能是车辆非常重要的性能之一,改善汽车的制动性能始终是汽车设计制造和使用部门的重要任务。
当车辆制动时,由于车辆受到与行驶方向相反的外力,所以才导致汽车的速度逐渐减小至零,对这一过程中车辆受力情况的分析有助于制动系统的分析和设计,因此制动过程受力情况分析是车辆试验和设计的基础,由于这一过程较为复杂,因此一般在实际中只能建立简化模型分析,通常人们主要从三个方面来对制动过程进行分析和评价:(1)制动效能:即制动距离与制动减速度;(2)制动效能的恒定性:即抗热衰退性;(3)制动时汽车的方向稳定性;目前,对于整车制动系统的研究主要通过路试或台架进行,由于在汽车道路试验中车轮扭矩不易测量,因此,多数有关传动系!制动系的试验均通过间接测量来进行汽车在道路上行驶,其车轮与地面的作用力是汽车运动变化的根据,在汽车道路试验中,如果能够方便地测量出车轮上扭矩的变化,则可为汽车整车制动系统性能研究提供更全面的试验数据和性能评价。
汽车设计课程设计说明书
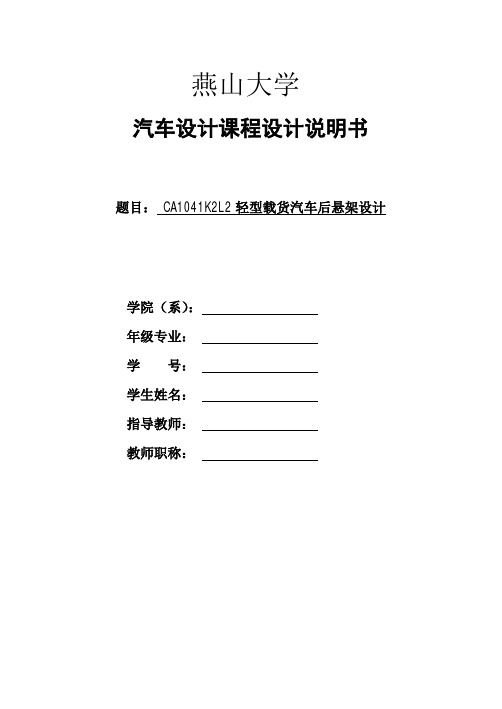
燕山大学汽车设计课程设计说明书题目: CA1041K2L2轻型载货汽车后悬架设计学院(系):年级专业:学号:学生姓名:指导教师:教师职称:目录一、悬架静载荷的计算 (1)二、参数选择及计算方法 (1)1.选择悬架主要参数:n c、f c、c s、.n0、f0 (1)2.确定板簧总长L,满载静止弧高Ha,动挠度f d上、f d下 (2)3.板簧片数及断面参数选择 (3)4.板簧的应力校核 (5)5.各片长度的确定 (6)6.板簧的刚度验算 (6)7. 各片应力计算 (9)8.预应力及其选择 (10)9. 板簧总成自由状态下的弧高及曲率半径计算 (12)10. 各片在自由状态下的曲率半径及弧高计算 (13)11. 板簧的动应力和最大应力 (15)12. 最大加速度驱动时的最大应力 (16)13. 卷耳及弹簧销的强度核算 (16)三、附件的选择 (17)1.减震器 (17)2.U形螺栓 (19)3.U型螺栓上的螺母 (19)4.中心螺栓 (19)5.弹簧卡处的铆钉和螺栓 (19)6.卷耳处的销及油杯 (20)7.滑动轴承 (20)四、总结 (20)b)板簧长度增加能降低弹簧刚度,改善汽车行驶的平顺性;c)在垂直刚度给定的条件下,板簧长度增加又能明显增加钢板弹簧的纵向角刚度。
在总布置可能的条件下,应尽可能将钢板弹簧取长些。
原因如下:1 增加钢板弹簧长度L能显著降低弹簧应力,提高使用寿命降低弹簧刚度,改善汽车平顺性。
2 在垂直刚度c给定的条件下,又能明显增加钢板弹簧的纵向角刚度。
3 刚板弹簧的纵向角刚度系指钢板弹簧产生单位纵向转角时,作用到钢板弹簧上的纵向力矩值。
4 增大钢板弹簧纵向角刚度的同时,能减少车轮扭转力矩所引起的弹簧变形。
对于卡车的后悬架推荐在如下的范围内选择:L=(0.35-0.45)轴距代入数据,可得:mm.L1240310040=×=⑵满载静止弧高Ha满载静止弧高Ha是装配到汽车上之后的板簧弧高,一般后悬架为Ha r = 20~30 mm,考虑到钢板弹簧安装好后有足够的上跳动挠度,将满载静止弧高Ha取为25mm。
汽车底盘系统介绍第十一节制动系统设计要求

汽车底盘系统介绍第十一节制动系统设计要求制动系统设计要求:满足法规:GB21670-2008,GB7258-2012,ECER13及销售对象所在国法规和要求。
GB 21670GB7258GB 21670及ECE R13H1、制动系统性能目标设定(1)设计计算:在项目设计之初,根据以往数据库定义初版设计目标,在竞品车测试后根据测试数据再进行设计目标修订,通过设计计算量化零部件设计参数。
目标设定测试数据(2)制动距离:根据目前市场同类车型制动性能测试结果分析,制动距离主要集中在41~47m,为了提高产品竞争力,某平台下的车型制动性能目标设定时应突出性能优势,故制动性能目标设定如下:a.制动距离目标设定为:空载≤42m,满载≤44m;b.设定制动噪音、踏板感、整车制动性能等细节目标,规范试验方法及验收标准;c.全系标配ABS,同时有EBD、ESC、BA、轮胎压力监控系统等选配功能。
竞品车型100km/h初速时的制动距离(空载)最后成绩最新汽车之家制动距离评价:≤39m优秀,39<合格≤44m,>44m差。
(3)踏板感空满载制动强度下的踏板力和位移曲线(4)制动噪声主观评价结果雷达图保证制动性能,同时突出舒适性,半金属(Semi Met): 北美和亚洲市场;寿命长,负荷高,成本低,舒适性好,但是摩擦系数低,噪音和对盘磨损大;低金属(Low Steel) : 欧洲市场;高性能,速度敏感,但是噪音大,寿命短,制动粉尘严重;非石棉有机物(NAO): 亚洲,欧洲和北美市场;噪音低,制动粉尘少,Creep Groan小,高温和高负荷特性差。
(5)制动性能试验和主观评价根据法规以及企业标准进行验收,完成目标设定的验证;2、制动系统主要参数的选择(1)根据整车配置输入与制动系统有关的整车参数及要求。
整车空/满载质量;轴距;空载/满载质心高;空载/满载各轴到质心水平距离;前/后轮胎滚动半径;制动器、操纵系统相关参数选择及计算。
长城客货车制动系统结构分析

长城客货车制动系统结构分析
长城客货车的制动系统是保证车辆安全行驶的关键部分,它主要由以下几个部分组成:
1. 制动踏板:位于驾驶座旁边的地板上,用于由驾驶员踩下以施加制动力。
2. 主缸:位于汽车发动机舱内,与制动踏板相连,主要功能是将驾驶员施加在制动踏板上的力量转化为液压能量,并传递给制动系统的其他部分。
3. 制动管路:主缸通过制动管路将液压能量传递给车轮上的制动器,制动管路一般由一根或多根金属管路组成,负责将液压压力传输到制动器。
4. 制动鼓/制动盘:分别位于车轮上的制动系统部分,通过制动鼓/制动盘的摩擦作用,将车轮减速或停止。
5. 制动皮碗/制动片:是制动盘和制动鼓内部与之接触的部分,通过与制动盘/制动鼓接触并产生摩擦力,实现制动效果。
6. 制动助力器:用于增加制动力的辅助设备,一般为真空助力器或液压助力器,通过依靠引擎真空或液压力量来提供辅助制动力。
以上是长城客货车制动系统的基本结构组成部分,不同车型的制动系统可能会有些差异,但整体原理是类似的。
在行驶过程中,当驾驶员踩下制动踏板时,主缸将液压能量传递给制动器,实现车辆制动的目的。
制动系统的稳定性和可靠性对于行车安全至关重要,因此定期检查和维护制动系统是非常重要的。
解放牌CA1041K26系列轻型载货汽车线束图解

文 献 标 识 码 :B
文 章 编 号 : 10 — 6 9 2 0 0 — 0 0 0 0 3 8 3 ( 0 7)4 0 2 - 9
解放牌 C o 1 6 列 轻型 载货 汽车线 束布 局如 图1 示 ,电路原 理如 图2 示 ,线束剖 析如 表1 示 。 A1 4 K2 系 所 所 所
一 一 匝 刚 隧 暑 脚 料 趣 替 副 辩 苦
2 《 车 器》O7 第4 2 汽 电 2O 年 期
博 耐 特 我 信 赖 我 选 择 详见彩 1 广告 3
维普资讯
裹 1 解 放 牌 CA1 4 K2 o 1 6系 列 轻 型 载 货 汽 车 线 束 表 名 称 前雾 灯 开 关 内
磐 .H 0 幽雾 . H 唧 嘲 卅 . ∞
帽 . 墨 锄 抛 辎 L ∞ J.H 唧嘲卅 . 稚 世
. ∞ 』f : 雾 .
霰
岛 霰 . 稚 锄 霰 . 卜
稃 器 卅 .
稃 器 卅 . H 雾 .
囱 囱
稚 锄 需 . n 赠 繁 . n
后
1 橙 .+ 前 雾 灯 开关 5 . 0 三 上 05 .黑 搭 铁 仪 表 台束 间 b 6 l 10 / 旦. 仪 表 c 2, 表 台 束 间 a 3 .橙 蓝 1 仪 l 05 /白 — 仪 表 台 束 间 4 0 小 灯 继 电 .绿 1(
器 3)
2 03 棕 0 _5
2 0 < 汽车电器》 o 7 20 年第 4 期
维普资讯
:
o ¨ ∞ o
一∞ ∞
∞N一
ll £尸
N 卜1 . r6 .
∞
幂 』I = : 稚 馋
一 一 匝 剧 隧 暑 脚 卅 趣 搽 副 t 看 礁 菖 《U嬖 摄 鞋 匝
轻型载货汽车制动器设计

本科学生毕业设计轻型载货汽车制动器设计院系名称:汽车与交通工程学院专业班级:学生姓名:指导教师:职称:黑龙江工程学院二○一一年六月The Graduation Design for Bachelor's Degree Design of Light Bill’s AutomobileBrakeCandidate:Specialty:Class:Supervisor:Title:Heilongjiang Institute of Technology2011-06·Harbin摘要从汽车诞生时起,车辆制动器在车辆的安全方面就起着决定性作用。
目前,汽车所用制动器几乎都是摩擦式的,可分为鼓式和盘式两大类。
盘式制动器的主要优点是在高速刹车时能迅速制动,散热效果优于鼓式刹车,制动效能的恒定性好。
鼓式制动器的主要优点是刹车蹄片磨损较少,成本较低,便于维修、由于鼓式制动器的绝对制动力远远高于盘式制动器,所以普遍用于后轮驱动的卡车上,故本次轻型载货汽车采用前盘后鼓式制动器。
本设计前轴采用浮动钳盘式制动器,后轴采用制动器为领从蹄式鼓式制动器。
设计的主要内容包括:制动器的研究现状及意义、制动器方案的选择与分析、盘式制动器结构的设计、鼓式制动器结构的设计。
关键词:轻型载货汽车,盘式制动器,鼓式制动器,制动蹄,设计ABSTRACTThe brake has played a significant role in vehicular security since the car was born. In current, most of the brake is frictional, which concludes disc brake and drum brake. The chief advantages of disc brake are that it can apply the brake quickly in high-speed trig, that it has a better cooling function than drum trig, and that the application of the brake can have a long affection. While the chief advantages of drum brake are that trig hoof can have less abrasion and cost, and that it can be easily mended .As the drum brake has a higher drag force than disc brake, it use in rear wheel drive truck widely, due to these factions, We use before the disc brakes followed by the drum brake in this light shipment car.The front axle of this design use before the floating disc brakes, and the rear axle use brought from the hoof type drum brake.The first chapter of the design instruction chiefly introduces the current state and the purport of brake, the second chapter tells the choice and the analysis of the brake project mostly, the following chapter describes the calculation and check of the disc brake structural design, and the last chapter introduces the calculation and check of the drum brake structural design.Keywords: Light bills car,Disc brake ,drum brakes, Brake shoes, design.目录摘要 (I)ABSTRACT ...................................................... I I 第1章绪论. (1)1.1制动器的目的意义 (1)1.2制动器的研究现状 (1)1.3制动器的研究内容及方法 (3)1.4本章小结 (4)第2章制动器方案论证分析与选择 (5)2.1 制动器结构方案的确定 (5)2.1.1鼓式制动器结构方案的确定 (5)2.1.2盘式制动器结构方案的确定 (8)2.2制动器主要参数及其选择 (9)2.2.1制动器设计相关主要技术参数 (9)2.2.2同步附着系数 (10)2.2.3前后轴制动力矩分配系数b (10)2.2.4制动器最大制动力矩 (11)2.3本章小结 (11)第3章盘式制动器结构设计 (12)3.1盘式制动器的主要参数确定 (12)3.1.1 制动盘直径D (12)3.1.2 制动盘厚度h (12)3.1.3 摩擦衬片内半径R1与外半径R2 (12)3.1.4 摩擦衬片工作面积A..................... 错误!未定义书签。
毕业设计阁瑞斯轻型客车制动系统设计说明书

摘要随着高速公路的不断发展,汽车车速的不断提高,车流密度也不断增大。
现代汽车对制动系的工作可靠性要求日益提高。
因为只有制动性能良好,制动系工作可靠的汽车才能充分发挥出其高速行驶的动力性能并保证行驶的安全性。
由此可见,本次制动系统设计具有实际意义。
对于福田风景轻型客车的制动系统设计,首先制定出制动系统的结构方案,本设计确定采用前盘后鼓式制动器,串联双腔制动主缸,HH型交叉管路布置。
其次计算制动系统的主要设计参数(确定同步附着系数,制动力分配系数,制动器最大制动力矩),制动器主要参数设计和液压驱动系统的参数计算。
再次利用计算机辅助设计绘制装配图,布置图和零件图。
最终进行制动力分配编程,对设计出的制动系统的各项指标进行评价分析。
通过本次设计的计算结果表明设计出的制动系统是合理的、符合标准的。
其满足结构简单、成本低、工作可靠等要求。
关键词:福田风景轻型客车;制动系统设计;前盘后鼓式制动器;制动主缸AbstractWith the continuous development of highways, the continuous improvement of vehicle speed, traffic density has increased continuously. Hyundai Motor brake on the work of the increasing reliability requirements. Only good braking performance, the braking system of reliable car to give full play to its high-speed driving performance and to ensure that the momentum on security. Evidently, this braking system design of practical significance.For the design of Foton View Light Bus,First developed structure of the braking system, the design determined by pre-and post-drum brakes, dual-chamber tandem brake master cylinders, HH-cross-line layout. This was followed by calculation of the main braking system design parameters (attachment coefficient determined simultaneously, the braking force distribution coefficient, the biggest brake brake torque), the main parameters of design and brake hydraulic drive system parameters. Drawing once again use computer-aided design assembly drawing, layout plans and parts. Final braking force distribution of programming, the design of the braking system of indicators to evaluate the analysis.Through this design calculations designed to show that the braking system is reasonable, in line with standards. To meet its structure is simple, low cost, reliability requirements.Keywords:Foton View Light Bus;Brake System Design;Qianpanhougu brake;Brake master cylinders目录第1章绪论 (1)1.1制动系统工作原理 (1)1.2汽车制动系统的组成 (2)1.3汽车制动系统的类型 (2)1.4 汽车制动系统的功用和要求 (3)1.4.1 汽车制动系统的功用 (3)1.4.2 汽车制动系统的设计要求 (3)第2章制动系统设计方案 (4)2.1 制动器结构形式方案 (4)2.2液压制动管路布置方案 (6)2.3制动主缸的设计方案 (7)2.4制动驱动机构形式方案 (8)2.4.1简单制动系 (9)2.4.2动力制动系 (9)2.4.3伺服制动系 (9)第3章制动系统主要参数确定 (10)3.1 轻型货车主要设计参数 (10)3.2 同步附着系数的确定 (10)3.3 制动器制动力分配系数β的确定 (11)3.4 前后制动器最大制动力矩的确定 (12)3.5 制动器主要参数的确定 (12)3.5.1 制动鼓直径D的确定 (12)3.5.2 制动器主要参数的确定b和包角θ的确定 (13)θ的确定 (13)3.5.3 摩擦衬片起始角3.5.4 制动器中心到张开力作用线距离e的确定 (13)3.5.5 制动蹄支销连线至制动器中心值a的确定 (13)3.5.6 支销中心距c2的确定 (13)3.5.7 摩擦片摩擦系数μ的确定 (13)第4章制动器的设计与计算 (14)4.1 前、后鼓式制动器制动转矩计算 (14)4.1.1 制动蹄的压力中心 (14)4.1.2 制动蹄的效能因数 (14)4.1.3 每一制动器的制动转矩 (15)4.2 制动性能计算 (15)4.2.1 制动减速度j (15)4.2.2 制动距离 (15)第5章制动驱动机构设计 (17)5.1 制动轮缸直径d的确定 (17)d的确定 (17)5.2 制动主缸直径F的确定 (17)5.3 制动踏板力P5.4 制动踏板工作行程的确定 (18)第6章评价分析 (19)6.1 汽车制动性能评价指标 (19)6.2 制动效能 (19)6.3 制动效能的恒定性 (19)6.4 制动时汽车的方向稳定性 (19)6.5 前、后制动器制动力分配 (20)6.5.1 地面对前、后车轮的法向作用力 (20)6.5.2 理想的前、后制动器制动力分配曲线 (21)6.6 制动系统的发展趋势 (22)第7章结论 (26)参考文献 (27)致谢 (28)附录一外文翻译 (29)附录二相关程序 (38)第1章绪论汽车制动系是用于使行驶中的汽车减速或停车,使下坡行驶的汽车的车速保持稳定以及使已停驶的汽车在原地(包括在斜坡上)驻留不动的机构。
- 1、下载文档前请自行甄别文档内容的完整性,平台不提供额外的编辑、内容补充、找答案等附加服务。
- 2、"仅部分预览"的文档,不可在线预览部分如存在完整性等问题,可反馈申请退款(可完整预览的文档不适用该条件!)。
- 3、如文档侵犯您的权益,请联系客服反馈,我们会尽快为您处理(人工客服工作时间:9:00-18:30)。
参数1.制动系统的主要参数及其选择同步附着系数对于前后制动器制动力为固定比值的汽车,只有在附着系数ϕ等于同步附着系数0ϕ的路面上,前、后车轮制动器才会同时抱死,当汽车在不同ϕ值的路面上制动时,可能有以下三种情况[4]。
1、当0ϕϕ<时2、当0ϕϕ>时3、当0ϕϕ=时附着条件的利用情况可以用附着系数利用率ε(或称附着力利用率)来表示,ε可定义为ϕϕεqG F B ==制动强度和附着系数利用率根据选定的同步附着系数0ϕ,已知:Lh L g02ϕβ+=制动器最大的制动力矩为保证汽车有良好的制动效能和稳定性,应合理地确定前、后轮制动器的制动力矩。
最大制动力是在汽车附着质量被完全利用的条件下获得的,这时制动力与地面作用于车轮的法向力21Z Z 、 成正比。
所以,双轴汽车前、后车轮附着力同时被充分利用或前、后轮同时抱死的制动力之比为:ggf f h L h L Z Z F F 01022121ϕϕ-+== 制动器所能产生的制动力矩,受车轮的计算力矩所制约,即e f f r F T 11=e f f r F T 22=对于选取较大0ϕ值的各类汽车,应从保证汽车制动时的稳定性出发,来确定各轴的最大制动力矩。
当0ϕϕ>时,相应的极限制动强度ϕ<q ,故所需的后轴和前轴制动力矩为e gf r qh L LGT ϕ)(1max 2-=max 2max 11f f T T ββ-=制动器因数和制动蹄因数制动器因数又称为制动器效能因数。
其实质是制动器在单位输入压力或力的作用下所能输出的力或力矩,用于评比不同结构型式的制动器的效能。
制动器因数可定义为在制动鼓或制动盘的作用半径上所产生的摩擦力与输入力之比,即PR T BF f=对于鼓式制动器,设作用于两蹄的张开力分别为1P 、2P ,制动鼓内圆柱面半径即 制动鼓工作半径为R ,两蹄给予制动鼓的摩擦力矩分别为1Tf T 和2Tf T ,则两蹄的效能因 数即制动蹄因数分别为:R P T BF Tf T 111=RP T BF Tf T 222=整个鼓式制动器的制动因数则为RP P T T RP P T T PRT BF Tf Tf Tf Tf f )()(2)(5.021212121++=++==当P P P ==21时,则2121T T Tf Tf BF BF PRT T BF +=+=蹄与鼓间作用力的分布,其合力的大小、方向及作用点,需要较精确地分析、计算才能确定。
今假设在张力P 的作用下制动蹄摩擦衬片与鼓之间作用力的合力N 如图3.2所示作用于衬片的B 点上。
这一法向力引起作用于制动蹄衬片上的摩擦力为f N f ,为摩擦系数。
a ,b ,c ,h ,R 及α为结构尺寸,如图3.2所示。
图3.2 鼓式制动器的简化受力图对领蹄取绕支点A 的力矩平衡方程,即0=-+Nb nFC Ph由上式得领蹄的制动蹄因数为⎪⎪⎪⎪⎭⎫⎝⎛-==b c f f b h P Nf BF T 11 当制动鼓逆转时,上述制动蹄便又成为从蹄,这时摩擦力f N 的方向与图3.2所 示相反,用上述分析方法,同样可得到从蹄绕支点A 的力矩平衡方程,即0=--Nb nFC Ph⎪⎪⎪⎪⎭⎫ ⎝⎛+==b c f f b h P Nf BF T 122.鼓式车轮制动器的结构参数与摩擦系数制动鼓直径D当输入力P 一定时,制动鼓的直径越大,则制动力矩越大,且使制动器的散热性能越好。
但直径D 的尺寸受到轮辋内径的限制,而且D 的增大也使制动鼓的质量增加,使汽车的非悬挂质量增加,不利于汽车的行驶的平顺性。
制动鼓与轮辋之间应有一定的间隙,以利于散热通风,也可避免由于轮辋过热而损坏轮胎。
由此间隙要求及轮辋的尺寸即可求得制动鼓直径D 的尺寸。
由于CA1041采用16in 的轮辋所以取76.0/=r D D ,制动鼓直径D 与轮辋直径Dr 之比的一般范围为:货车 83.0~64.0/=r D D 。
制动蹄摩擦片宽度b 、制动蹄摩擦片的包角β和单个制动器摩擦面积∑A 综上所述选取领蹄 1101=β,从蹄 1001=β 单个制动器摩擦面积∑A :360/)(21ββπ+=∑Db A摩擦衬片起始角0β摩擦衬片起始角0β如图3.4所示。
通常是将摩擦衬片布置在制动蹄外缘的中央,并令2900ββ-= 。
领蹄包角:2900ββ-= 从蹄包角:2900ββ-=图3.4鼓式制动器的主要几何参数张开力P的作用线至制动器中心的距离a制动蹄支销中心的坐标位置k与c摩擦片摩擦系数选择摩擦片时,不仅希望起摩擦系数要高些,而且还要求其热稳定性好,受温度和压力的影响小。
不宜单纯的追求摩擦材料的高摩擦系数,应提高对摩擦系数的稳定性和降低制动器对摩擦系数偏离正常值的敏感性的要求。
后者对蹄式制动器是非常重要的各种制动器用摩擦材料的摩擦系数的稳定值约为5.03.0,少数可达0.7。
一般说~来,摩擦系数越高的材料,其耐磨性能越差。
所以在制动器设计时,并非一定要追求最高摩擦系数的材料。
当前国产的制动摩擦片材料在温度低于250℃时,保持摩擦系数f=0.35~0.4已不成问题。
因此,在假设的理想条件下计算制动器的制动力矩,取f=0.3可使计算结果接近实际值。
另外,在选择摩擦材料时,应尽量采用减少污染和对人体无害的材料。
3.制动蹄的分析计算制动蹄摩擦面的压力分布规律从前面的分析可知,制动器摩擦材料的摩擦系数及所产生的摩擦力对制动器因数有很大影响。
掌握制动蹄摩擦面上的压力分布规律,有助于正确分析制动器因数。
在理论上对制动蹄摩擦面的压力分布规律作研究时,通常作如下一些假定:(1)制动鼓、蹄为绝对刚性;(2)在外力作用下,变形仅发生在摩擦衬片上;(3)压力与变形符合虎克定律由于本次设计采用的是领从蹄式的制动鼓,现就领从蹄式的制动鼓制动蹄摩擦面的压力分布规律进行分析。
如图3.5所示,制动蹄在张开力P作用下绕支承销O'点转动张开,设其转角为θ∆,则蹄片上某任意点A 的位移AB 为AB =A O '·θ∆ 从图3.5中的几何关系可看到ϕβsin cos '''O O D O A O == AC =sin O O 'ϕθ∆⋅因为θ∆⋅'O O 为常量,单位压力和变形成正比,所以蹄片上任意一点压力可写成ϕsin 0q q =根据国外资料,对于摩擦片磨损具有如下关系式fqv K W 11=如果摩擦衬片磨损有如下关系:2222v fq K W =则其磨损后的压力分布规律为αsin C q =(C 也为一常数)。
制动器因数及摩擦力矩分析计算如前所述,通常先通过对制动器摩擦力矩计算的分析,再根据其计算式由定义得出制动器因数BF 的表达式。
假设鼓式制动器中制动蹄只具有一个自由度运动,由此可得:(1)定出制动器基本结构尺寸、摩擦片包角及其位置布置参数,并规定制动鼓旋转方向;(2)参见3.4.1节确定制动蹄摩擦片压力分布规律,令ϕsin 0q q =;(3)在张开力P 作用下,确定最大压力0q 值。
参见图3.7,δϕ所对应的圆弧,圆弧面上的半径方向作用的正压力为ϕqRd ,摩擦力为ϕfqRd 。
把所有的作用力对O '点取矩,可得ph =⎰210ϕϕq RMsin 2ϕd ϕ-⎰210ϕϕfq R(R-Mcos ϕ)sin ϕd ϕ据此方程式可求出0q 的值。
图3.7 制动蹄摩擦力矩分析计算计算沿摩擦片全长总的摩擦力矩T f =⎰210ϕϕfq R 2 sin ϕd ϕ=0fq R 2(cos 1ϕ-cos 2ϕ)单个领蹄的制动蹄因数BF Tl⎪⎭⎫ ⎝⎛-'=fB r a A r fhBF T 1单个从蹄的制动蹄因数BF T2⎪⎭⎫ ⎝⎛+'=fB r a A r fhBF T 2图3.8 支承销式制动蹄制动蹄片上的制动力矩鼓式制动蹄片上的制动力矩在计算鼓式制动器时,必须建立制动蹄对制动鼓的压紧力与所产生的制动力矩之间的关系。
由制动鼓作用在摩擦衬片单元面积的法向力为:αααd bR q qbRd dN sin max ==而摩擦力fdN 产生的制动力矩为ααd f bR q dNfR dT T f sin 2max ==在由α'至α''区段上积分上式,得)cos (cos 2max αα''-'=f bR q T Tf当法向压力均匀分布时,αbRd q dN p =)(2αα'-''=f bR q T p Tf 增势蹄产生的制动力矩1Tf T 可表达如下:111ρfN T Tf =写出制动蹄上力的平衡方程式:0)sin (coscos 111101=+-+δδαf N S P x 01111=+'-N f C S a P x ρ对于增势蹄可用下式表示为11111111])s i n (c o s /[B P f f c fh P T Tf =-+'=ρδδρ 对于减势蹄可类似地表示为22222222])s i n(c o s /[B P f f c fh P T Tf =+-'=ρδδρ图3.10 制动力矩计算用图为了确定1ρ,2ρ及1δ,2δ,必须求出法向力N 及其分量。
如果将N d 看作是它投影在1x 轴和1y 轴上分量x dN 和x dN 的合力,则根据式(3.23)有:)2cos 2(cos sin 41cos max 2max αααααααααα''-''===⎰⎰''''''bR q d bR q dN N y因此对于领蹄: []''''''12sin 2sin 2/()2cos 2(cos arctan arctan(ααβααδ+--==xyN N根据式(3.24)和式(3.26),并考虑到221y x N N N +=则有[]2'"2"'"'1)2sin 2sin 2()2cos 2(cos )cos (cos 4ααβααααρ+-+--=a R对于从蹄:[]''''''22sin 2sin 2/()2cos 2(cos arctan arctan(ααβααδ+--==xyN N则有:[]2'"2"'"'2)2sin 2sin 2()2cos 2(cos )cos (cos 4ααβααααρ+-+--=a R由于设计α'和α''相同,因此δ和ρ值也近似取相同的。