FMEA案例分析
fmea案例
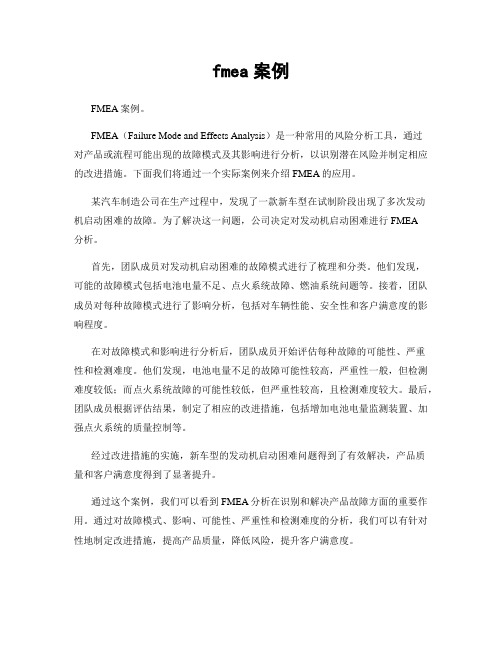
fmea案例FMEA案例。
FMEA(Failure Mode and Effects Analysis)是一种常用的风险分析工具,通过对产品或流程可能出现的故障模式及其影响进行分析,以识别潜在风险并制定相应的改进措施。
下面我们将通过一个实际案例来介绍FMEA的应用。
某汽车制造公司在生产过程中,发现了一款新车型在试制阶段出现了多次发动机启动困难的故障。
为了解决这一问题,公司决定对发动机启动困难进行FMEA分析。
首先,团队成员对发动机启动困难的故障模式进行了梳理和分类。
他们发现,可能的故障模式包括电池电量不足、点火系统故障、燃油系统问题等。
接着,团队成员对每种故障模式进行了影响分析,包括对车辆性能、安全性和客户满意度的影响程度。
在对故障模式和影响进行分析后,团队成员开始评估每种故障的可能性、严重性和检测难度。
他们发现,电池电量不足的故障可能性较高,严重性一般,但检测难度较低;而点火系统故障的可能性较低,但严重性较高,且检测难度较大。
最后,团队成员根据评估结果,制定了相应的改进措施,包括增加电池电量监测装置、加强点火系统的质量控制等。
经过改进措施的实施,新车型的发动机启动困难问题得到了有效解决,产品质量和客户满意度得到了显著提升。
通过这个案例,我们可以看到FMEA分析在识别和解决产品故障方面的重要作用。
通过对故障模式、影响、可能性、严重性和检测难度的分析,我们可以有针对性地制定改进措施,提高产品质量,降低风险,提升客户满意度。
总之,FMEA是一种简单而有效的风险分析工具,可以帮助我们识别和解决潜在风险,提高产品质量,降低成本,增强竞争力。
在实际工作中,我们应该充分发挥FMEA的作用,不断完善和改进产品和流程,为企业的可持续发展提供有力支持。
FMEA 案例分析
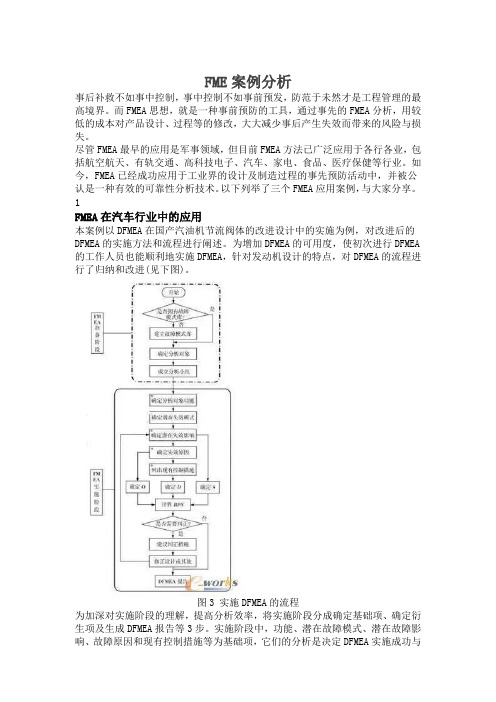
FME案例分析事后补救不如事中控制,事中控制不如事前预发,防范于未然才是工程管理的最高境界。
而FMEA思想,就是一种事前预防的工具,通过事先的FMEA分析,用较低的成本对产品设计、过程等的修改,大大减少事后产生失效而带来的风险与损失。
尽管FMEA最早的应用是军事领域,但目前FMEA方法已广泛应用于各行各业,包括航空航天、有轨交通、高科技电子、汽车、家电、食品、医疗保健等行业。
如今,FMEA已经成功应用于工业界的设计及制造过程的事先预防活动中,并被公认是一种有效的可靠性分析技术。
以下列举了三个FMEA应用案例,与大家分享。
1FMEA在汽车行业中的应用本案例以DFMEA在国产汽油机节流阀体的改进设计中的实施为例,对改进后的DFMEA的实施方法和流程进行阐述。
为增加DFMEA的可用度,使初次进行DFMEA 的工作人员也能顺利地实施DFMEA,针对发动机设计的特点,对DFMEA的流程进行了归纳和改进(见下图)。
图3 实施DFMEA的流程为加深对实施阶段的理解,提高分析效率,将实施阶段分成确定基础项、确定衍生项及生成DFMEA报告等3步。
实施阶段中,功能、潜在故障模式、潜在故障影响、故障原因和现有控制措施等为基础项,它们的分析是决定DFMEA实施成功与否的关键;S,O,D,RPN和建议的纠正措施为衍生项;基础项确定之后,衍生项可以随之确定。
1.分析基础项●功能:分析项目的功能,用尽可能简明的文字来说明被分析项目满足设计意图的功能;阀体的功能是与阀片配合保证最小流量;与怠速控制阀配合保证怠速流量;与节气门位置传感器配合保证主进气量。
●潜在故障模式:每项功能会对应一种或一种以上的故障模式,填写故障模式要遵循"破坏功能"的原则,即尽量列出破坏该功能的所有可能的模式;故障模式大部分来源于故障模式库,还有一部分是新出现的故障模式以及小组分析的结果,阀体的潜在故障模式为磨损、裂纹、断裂以及积碳等。
fmea失效模式分析案例
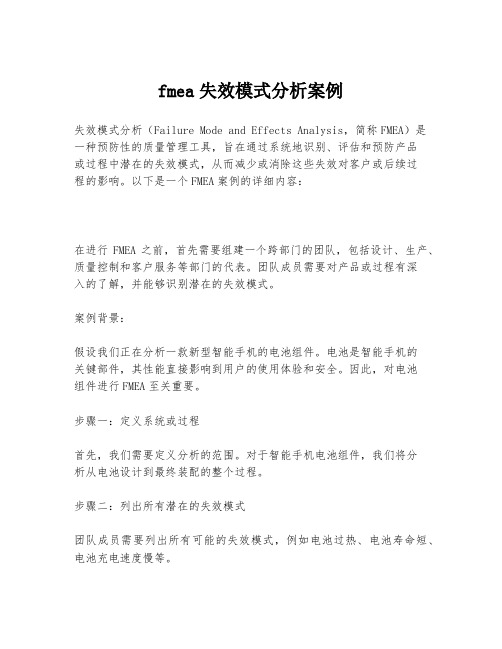
fmea失效模式分析案例失效模式分析(Failure Mode and Effects Analysis,简称FMEA)是一种预防性的质量管理工具,旨在通过系统地识别、评估和预防产品或过程中潜在的失效模式,从而减少或消除这些失效对客户或后续过程的影响。
以下是一个FMEA案例的详细内容:在进行FMEA之前,首先需要组建一个跨部门的团队,包括设计、生产、质量控制和客户服务等部门的代表。
团队成员需要对产品或过程有深入的了解,并能够识别潜在的失效模式。
案例背景:假设我们正在分析一款新型智能手机的电池组件。
电池是智能手机的关键部件,其性能直接影响到用户的使用体验和安全。
因此,对电池组件进行FMEA至关重要。
步骤一:定义系统或过程首先,我们需要定义分析的范围。
对于智能手机电池组件,我们将分析从电池设计到最终装配的整个过程。
步骤二:列出所有潜在的失效模式团队成员需要列出所有可能的失效模式,例如电池过热、电池寿命短、电池充电速度慢等。
步骤三:确定失效模式的潜在原因对于每个失效模式,团队需要确定可能导致该失效的原因。
例如,电池过热可能是由于电池设计不当、材料选择错误或制造过程中的缺陷。
步骤四:评估失效模式的严重性使用1到10的评分系统,团队需要评估每个失效模式的严重性。
评分越高,表示失效对客户或后续过程的影响越大。
步骤五:确定失效模式的潜在后果团队需要确定每个失效模式可能导致的后果。
例如,电池过热可能导致设备损坏或用户受伤。
步骤六:评估当前控制措施的有效性团队需要评估现有的控制措施是否能够有效预防或检测到潜在的失效模式。
例如,是否有严格的质量控制流程来检测电池的过热问题。
步骤七:计算风险优先数(RPN)风险优先数是通过将严重性(S)、发生概率(O)和检测难度(D)的评分相乘得到的。
RPN越高,表示该失效模式的风险越大。
步骤八:制定改进措施对于高RPN值的失效模式,团队需要制定改进措施。
这些措施可能包括重新设计电池、改进制造工艺或加强质量控制。
FMEA案例分析

点检
2
统
信号输 量
盒密封不良
目测
出异常
,或受潮氧
化
2 电气仪表系 传感器 传感器 无法计
统
信号输 量
出异常
9 零点输出过 大或电源性 能降低
3 仪表检测 3
3 电气仪表系 传感器 传感器 无法计 9
统
输出无 量
信号
桥路电压异 常
6 仪表检测 3
4 电气仪表系 传感器 传感器 无法计 9 传感器应变 6
该方法在 探测时有 多好
措施结果
采取的 措施
不
严 重 度 数
频 度 数
易 探 测 度
R .P . N
数
跟踪
?评审 ?确认 ?控制计划
13
潜在的失效模式及后果分析(设计 FMEA )
第 页,共 页
(2)项目名称
(5)车型年/类型
(8)核心小组
(9)功能 要求
左前车门 H8HX-A . -上、下车 -保护乘员免 受天气/噪音/ 侧碰撞的影响 a.车门附件 (如后视镜/门 锁/门铰链/及 门窗升降器的 支撑 b.为外观装饰 项目提供适当 的表面 c.喷漆和软内 饰
PFMEA 开始于基本的操作方法讨论完成时,完成时间早于生产 计划制定和生产批准之前
5
开发三部曲
6
控制计划 /过程流程 结合
产品质量计划顺序
过程流程清单 (包括所有的过程)
APQP程序 将启动这个过程
DFMEA
过程流程清单 转化为
过程控制计划
过程流程/ 控制计划 (所有的“”主要“过程)
PFMEA (所有的“”主要“过程)
带入杂质
对下道 工序
无法紧固 不能配合 不能连接 无法安装 损坏设备 危害操作者
最新FMEA分析经典案例

潜在失效模式及后果分析FMEA编号: PFMEA-S02-76项目名称:富元电子组装线过程责任:装配车间编制人:赵立领车型年/车辆类型:____ 关键日期: FMEA日期(原始):19/4/13 修订:_______主要参加人:1潜在失效模式及后果分析FMEA编号: PFMEA-S02-76项目名称:富元电子组装线过程责任:装配车间编制人:赵立领车型年/车辆类型:____ 关键日期: FMEA日期(原始):19/4/13 修订:_______主要参加人:2潜在失效模式及后果分析FMEA编号: PFMEA-S02-76项目名称:富元电子组装线过程责任:装配车间编制人:赵立领车型年/车辆类型:____ 关键日期: FMEA日期(原始):19/4/13 修订:_______主要参加人:3潜在失效模式及后果分析FMEA编号: PFMEA-S02-76项目名称:富元电子组装线过程责任:装配车间编制人:赵立领车型年/车辆类型:____ 关键日期: FMEA日期(原始):19/4/13 修订:_______主要参加人:4潜在失效模式及后果分析FMEA编号: PFMEA-S02-76项目名称:富元电子组装线过程责任:装配车间编制人:赵立领车型年/车辆类型:____ 关键日期: FMEA日期(原始):19/4/13 修订:_______主要参加人:5潜在失效模式及后果分析FMEA编号: PFMEA-S02-76项目名称:富元电子组装线过程责任:装配车间编制人:赵立领车型年/车辆类型:____ 关键日期: FMEA日期(原始):19/4/13 修订:_______主要参加人:61718191101111121131111611711811912012112212311-规定丸粒流量并锁定-丸粒添加程序1次/80min,每次添加25Kg1.2mm丸粒。
25-设1127128129130113213313411361371139140141142143144145146147148149150。
新版fmea七步法案例

新版FMEA七步法案例分析1. 背景介绍FMEA(Failure Mode and Effects Analysis)是一种常用的风险分析方法,旨在识别并评估系统或过程中的潜在故障模式、其对系统性能的影响以及采取的措施。
新版FMEA七步法是对传统FMEA方法的改进和完善,强调了风险预防和控制的重要性。
本文将以汽车制造业中的零部件生产过程为例,详细介绍新版FMEA七步法的应用过程和结果。
2. 案例背景假设某汽车制造公司生产某型号车辆的发动机零部件,该零部件在汽车性能中起到至关重要的作用。
公司决定采用新版FMEA七步法对该零部件生产过程进行风险分析,以提高产品质量和生产效率。
3. 案例过程步骤一:明确目标在这一步骤中,团队明确了目标:提高零部件生产过程的质量和效率。
同时,制定了详细的项目计划,明确每个步骤的时间和责任人。
步骤二:制定团队为了保证分析的全面性和准确性,公司组建了一个跨职能的团队,包括设计工程师、生产工程师、质量控制人员、供应商等。
每个团队成员都具备相关领域的专业知识和经验。
步骤三:定义过程在这一步骤中,团队对零部件生产过程进行了详细的定义和描述。
包括输入物料、工艺流程、设备使用等方面的信息。
同时,团队还明确了每个步骤的控制点和关键参数。
步骤四:风险分析团队根据零部件生产过程的定义,开始进行风险分析。
通过采用常用的风险评估工具,如故障模式与影响分析(FMEA)和故障树分析(FTA),对每个步骤的潜在故障模式和影响进行了评估和排名。
例如,在零部件生产过程中,一个潜在的故障模式是工艺参数设置错误,导致产品尺寸不合格。
该故障模式的影响包括:影响产品装配质量、增加产品退货率、增加维修成本等。
步骤五:制定改进措施在风险分析的基础上,团队制定了一系列改进措施,以减少潜在故障的发生概率和减轻故障影响。
这些改进措施包括:•设立更严格的工艺参数控制标准,确保每个步骤的参数设置正确;•引入自动化设备,减少人为操作错误的可能性;•加强员工培训,提高操作技能;•建立更严格的质量检查流程,确保产品质量符合要求。
fmea案例

fmea案例FMEA案例。
FMEA(Failure Mode and Effects Analysis)是一种系统性的、前瞻性的方法,用于识别和消除产品或过程中的潜在故障和问题。
通过对可能的故障模式、故障影响和故障原因进行分析,可以预防和减少故障的发生,提高产品的质量和可靠性。
下面我们将通过一个实际案例来介绍FMEA的应用。
案例背景:某汽车制造公司在生产过程中发现,部分车型的发动机在高速行驶时出现了持续性的抖动现象,经过初步调查发现,这一问题导致了不少车辆的质量问题,严重影响了客户的使用体验,因此迫切需要找到问题的根源并解决。
FMEA分析过程:1. 确定分析范围,首先确定分析的范围,包括发动机的设计、生产、装配、使用和维护等环节。
2. 识别故障模式,对发动机可能出现的故障模式进行识别和描述,例如发动机抖动、发动机熄火、发动机失去动力等。
3. 评估故障影响,针对每个故障模式,评估其对产品性能、安全性、可靠性等方面的影响程度,以及对客户的影响。
4. 确定故障原因,分析每个故障模式可能的原因,例如设计缺陷、零部件质量问题、生产工艺不当等。
5. 制定改进措施,针对识别出的故障模式和原因,制定相应的改进措施,包括设计优化、工艺改进、零部件更换等。
6. 实施改进措施,将改进措施落实到实际生产中,并进行跟踪和验证,确保问题得到有效解决。
案例分析结果:经过FMEA分析,发现该汽车发动机抖动的主要原因是由于某零部件的设计不当导致的,该零部件在高速行驶时容易产生共振现象,从而引起发动机抖动。
针对这一问题,制定了更换设计合理的零部件、优化发动机控制系统等改进措施,并在生产中逐步实施。
经过一段时间的跟踪和验证,发现抖动现象得到了明显改善,客户投诉情况也大幅减少。
结论:通过FMEA分析,该汽车制造公司成功地找到了发动机抖动问题的根源,并采取了有效的改进措施,提高了产品质量和客户满意度。
FMEA方法不仅帮助企业预防和解决了具体的质量问题,更重要的是建立了一套系统性的质量管理方法,为企业持续改进提供了有力的工具和支持。
FMEA案例范文
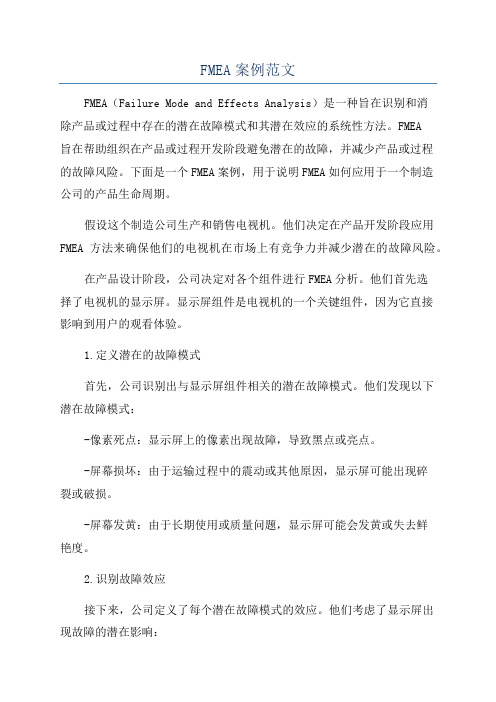
FMEA案例范文FMEA(Failure Mode and Effects Analysis)是一种旨在识别和消除产品或过程中存在的潜在故障模式和其潜在效应的系统性方法。
FMEA旨在帮助组织在产品或过程开发阶段避免潜在的故障,并减少产品或过程的故障风险。
下面是一个FMEA案例,用于说明FMEA如何应用于一个制造公司的产品生命周期。
假设这个制造公司生产和销售电视机。
他们决定在产品开发阶段应用FMEA方法来确保他们的电视机在市场上有竞争力并减少潜在的故障风险。
在产品设计阶段,公司决定对各个组件进行FMEA分析。
他们首先选择了电视机的显示屏。
显示屏组件是电视机的一个关键组件,因为它直接影响到用户的观看体验。
1.定义潜在的故障模式首先,公司识别出与显示屏组件相关的潜在故障模式。
他们发现以下潜在故障模式:-像素死点:显示屏上的像素出现故障,导致黑点或亮点。
-屏幕损坏:由于运输过程中的震动或其他原因,显示屏可能出现碎裂或破损。
-屏幕发黄:由于长期使用或质量问题,显示屏可能会发黄或失去鲜艳度。
2.识别故障效应接下来,公司定义了每个潜在故障模式的效应。
他们考虑了显示屏出现故障的潜在影响:-像素死点:用户在观看电视节目或电影时会被黑点或亮点分散注意力,影响观看体验。
-屏幕损坏:显示屏碎裂或破损可能导致显示效果变差,甚至无法使用。
-屏幕发黄:显示屏发黄或失去鲜艳度会影响图像质量,用户无法获得高质量的观看体验。
3.评估潜在原因和控制措施公司评估了每个潜在故障模式的可能原因,并制定相应的控制措施以减少潜在故障模式的出现概率:-像素死点的可能原因:制造过程中的材料问题,控制措施是选择高质量的材料,进行严格的质量控制。
-屏幕损坏的可能原因:运输过程中的震动,控制措施是加强包装和运输过程中的保护。
-屏幕发黄的可能原因:长期使用,控制措施是使用高品质的材料和组件,以及进行适当的维护和保养。
4.评估风险严重性和优先级公司为每个潜在故障模式评估了风险严重性和优先级,以指导其在产品设计过程中的决策:-像素死点的风险严重性:中等,由于像素死点会影响观看体验,但不会导致电视机无法使用。
- 1、下载文档前请自行甄别文档内容的完整性,平台不提供额外的编辑、内容补充、找答案等附加服务。
- 2、"仅部分预览"的文档,不可在线预览部分如存在完整性等问题,可反馈申请退款(可完整预览的文档不适用该条件!)。
- 3、如文档侵犯您的权益,请联系客服反馈,我们会尽快为您处理(人工客服工作时间:9:00-18:30)。
失效模式
频度
严重度
探测度
FMEA的顺序
现行设 计控制 风 险 顺 序 数 R P N
过程 功能 要求
潜在 失效 模式
潜在 失效 的后 果
严 重 级 度 数 别 S
潜在 失效 的 起因/ 机理
频 度
预 数 防
不 易 探 测 探 度 测 数 D
措施结果
建议 措施
责任 和目 标完 成日 期
采取的 措施
不 易 R 严 频 重 探 .P 度 测 . 度 数 数 度 N 数
第一阶段 计划和 确定项目
第二阶段 产品设计 和开发 样件制作
第三阶段 过程设计 和开发
第四阶段 产品和 过程确定 试生产
第五阶段 反馈、评定 和纠正措施 批量生产
FMEA 的时间顺序
DFMEA PFMEA
概念
初始设计
设计完成
样件制造
设计/过程 确认
生产开始
DFMEA 开始早于过程,完成时间在早期的图样完成但任何工 具的制造开始之前 PFMEA 开始于基本的操作方法讨论完成时,完成时间早于生产 计划制定和生产批准之前
目标:最大化的 产品质量、可靠性 、成本和可维护性
机器
工具 工作站 生产线 操作者培训 过程 测量
注意:将全过程的 失效模式降为最小 目标:最大化的 全过程质量、 可靠性、成本 和可维护性
FMEAs的关联
失效模式
后 果
原 因
SFMEA
DFMEA
问题的分支
问题
问题产生的原因
问题产生的原因来自 SFMEA
准确的后果定义 设计失效模式产 来自SFMEA 生的原因
PFMEA
问题产生的原因来自 DFMEA
和DFMEA相同 的后果
详细的过程失效 模式产生的原因
PPAP 与APQP、CP、FMEA、MSA,SPC关系
DFMEA
PFMEA
样件CP
试生产CP
PPAP MSA SPC SPC (Ppk≧1.67) (Cpk≧1.33) 生产CP
开发三部曲
控制计划/过程流程结合
产品质量计划顺序
过程流程清单 (包括所有的过程) APQP程序 将启动这个过程 过程流程清单 转化为 过程控制计划 PFMEA (所有的“”主要“过程) 利用RPN值来评定特性 DFMEA 过程流程/ 控制计划 (所有的“”主要“过程)
DFMEA介绍
1.7设计目标→ 产 1.8可靠性和质量目标→ 1.9初始材料清单→ 品 1.10初始过程流程图→ 1.11初始产品和过程特殊 设 特性清单→ 1.12产品保证计划→ 计 1.13管理者支持→ 与 开 发 2.1DFMEA 2.2可靠性和装配性 2.3设计验证 2.4设计评审 2.5样件制造——控制计划 产品设计 2.6工程图(包括数学数据) 部门输出 2.7工程规范 2.8 材料规范 2.9 图样和规范更改 2.10新设备、工装和设施要求 2.11产品/过程特殊特性 策划 2.12量具和有关试验设备要求 小组输出 2.13 小组可行性承诺和管理者 支持
潜在的失效模式及后果分析(设计 FMEA )
第
( 2 ) 项目名称 ( 5 ) 车型年/ 类型 ( 8 ) 核心小组 ( 9 ) 功能 要求 0 1 , 0 3 车身密封 1 9 9 狮牌 4 门/ 旅行车 ( 3 ) 设计责任 ( 6 ) 关键日期 车身工程部 2012/9/18
(1)FMEA编号
验收准则 输 出 计算书
图样
• • • •
放行前需得到批准
RPN 流程
来自经验和数据 DFMEA 探 严 频 潜在 潜在 重 级 潜在失效 现行 测 项目/功能 度 失效模式 失效后果 度 别 的起因/机理 设计控制 度 O D S S PFMEA 探 严 潜在 潜在 重 级 潜在失效 频 现行 测 项目/功能 度 失效模式 失效后果 度 别 的起因/机理 设计控制 度 O D 设计 过程 起 因 后 果 RPN 控 制 RPN 来自预测
页,共
1234
页
( 4 ) 编制人
泰特- 车身工程师
( 7 ) F M E A 编制日期 2 0 1 2 / 6 / 1 1 ( 7 ) 修订日期 2 0 1 2 / 7 / 2 ( 2 2 ) 措施结果 1 (16)现 (16)现 (11)潜 严 13 探 风险 ( 2 0 ) 责任及 ( 1 0 ) 潜在 ( 1 4 ) 潜在失效 5 行设计 行设计 ( 1 9 ) 建议措 在失效后 重 级 测 顺序 目标完成日 ( 2 1 ) 采取的 失效模式 起因/ 机理 频 控制预 控制探 施 S O D RPN 果 度 别 度 数 期 措施 度 防 测
SGS管理学院
企业真诚的服务伙伴
Your Partner in Achieving Excellence 失效模式及后果分析
(案例)
李剑波
典型的FMEAs
系统
部件 子系统 主系统
注意:将系统的 失效模式降为最小
设计
部件 子系统 主系统 注意:将设计的 失效模式降为最小
过程
人 机 料 法 环 测
目标:最大化的 产品质量、可靠性 和成本
设计开发输入和输出
法律法规要求 标准 特别是强制性 功 保安使能 密全用要 性性性 求 输 入
• • •
确保 •充分与适宜性 •要求完整、明确 •不矛盾
产品规范
服务规范
化电机物性 学气械理能 性性性性要 能能能能求 以往类似 设计信息
设计规范
记 录 或 文 件
•方案确认 •初步设计 •详细设计 •规范设计 •资料设计(验证) •服务定型(确认) •实施服务 •设计任务书 •设计规范 •产品说明书
质量功能展开(QFD)
产品技 术需求 顾 客 需 求 关键零 件特性 产品规 划矩阵
产 品 技 术 需 求 关 键 零 件 特 性
关键 工序
关 键 工 艺 步 骤
零件规 划矩阵
关键 参数 工艺/质 量控制矩 阵
工艺规 划矩阵
典型的QFD瀑布式分解模型示意图
需求质量展开表
一级 1.明亮且看得清楚 二级 11 看远处清楚 三级 111 灯明亮 112 光线的方向正 113 明亮度的扩展 114 没有散光 12 即 使 在 特 殊 条 件 121 即使天气不好也 下也看得清楚 看得见 122 与手柄连动 13 看近处清楚 123 跳跃时也看得见
ቤተ መጻሕፍቲ ባይዱ
功能 、特 征或 要求
后果 是什 么
有多 糟糕
会有什么问题 •无功能 •部分功能 •功能过强 •功能降级 •功能间歇 •非预期功能 起因 是什 么
发生 频率 如何 怎样 预防 和探 测
能做些什么 •设计更改 •过程更改 •特殊控制 •采用新程序 或指南的更 改 该方法在 探测时有 多好
跟踪 •评审 •确认 •控制计划