实木家具的生产工艺流程PPT课件
实木家具生产工艺流程

实木家具生产工艺流程一:备料1.板材干燥,将木材的含水率控制在8%~10%,没有干燥过的木材一般含水率在50%以上,干燥过后的木材不容易出现爆裂变形等现象。
2.平衡,把干燥过的木头自然放置几天,让木材恢复平衡。
3.选料配料,木制品按其部位可分为外表用料、内部用料以及暗用料三种。
外表用料露在外面,如写字台的面、橱柜的可视部分等;内部用料指用在制品内部,如内档、底版等;暗用料指在正常使用情况下看不到的零部件,如抽屉导轨、包镶板、内衬条等。
选材时注意节疤、内裂、蓝变、朽木、端裂。
4.粗刨,给毛料板材定厚。
5.风剪,毛料板材修整长度。
下料按所需长度加长20mm。
6.修边,截去毛料板材上不能用的毛边。
7.配板,木料配板选材分直纹、山纹,颜色搭配一致,配板宽度按所需宽度合理放余量。
选料时要把内裂、端裂、节疤、蓝变、朽木部分取下。
8.布胶,在木料之间均匀布胶,胶的配比:固化剂(10—15克)、拼板胶(100克)的比,每次调胶500克左右。
9.拼板,使用拼板机将木材进行拼装,拼板注意高低差、长短差、色差、节疤。
10.XXX,布胶完成的木材放置2小时左右,让胶水凝固。
11.砂刨,刨去木料之间余外的胶水,使木料板面无余外胶水。
12.锯切定宽,用单片锯给木材定宽。
13.四面刨成型,根据需要的形状刨出木材。
14.养生,将木材自然放置24小时左右。
二:木工1.宽砂定厚,按要求砂止符合加工要求的尺寸,机加完成后进行抛光砂,,粗砂一次砂0.2mm,抛光砂一次砂0.1mm。
2.精切,给毛料定长,加工过程中做到无崩茬、发黑,长与宽加工误差不超过0.2mm,1米以下对角线≤0.5mm,1米以上板片对角线应≤1mm。
3.成型,根据图纸将木料加工成型。
加工时不允许有崩茬、毛刺、跳刀和发黑征象,加工的部件表面应光滑、平整、线型流畅一致,加工前检查设备部件螺丝有无松动,模板是否安装规范,刀具是否装紧,加工过程中禁止顺刀进料,部件尺寸误差不超过0.2mm。
实木家具生产工艺流程

实木家具生产工艺流程
一、原材料准备:
1.原木采购:选择具有质量保证的优质木材,如橡木、胡桃木等。
2.原木加工:对原木进行蒸煮、干燥、切割等处理,以确保木材的湿度和大小均匀。
二、设计与制作:
1.家具设计:根据客户需求进行家具的设计和定制,确保设计合理、功能完善。
2.雕刻与打磨:根据设计图纸进行雕刻和打磨工艺,提升家具的外观质量。
3.木材加工:对木材进行削成、镶嵌等加工工艺,制作出家具的各个部件。
4.组装与安装:将家具的各个部件进行组装,使用钉子、螺丝等连接件进行固定,最终形成完整的家具。
三、加工与组装:
1.平面加工:使用木工机械对家具板材进行切割、开槽等加工工艺。
2.圆弧加工:使用木工机械对家具的曲线部分进行加工和修整。
3.镶嵌加工:利用镶嵌工艺将不同种类、颜色或质地的木材拼接成花纹效果。
4.安装组装:将家具各螺丝、五金件进行安装固定,并测试结构强度和稳定性。
四、涂装与后处理:
1.打磨:对家具进行多次打磨,使表面平整、光滑。
2.刷漆:使用喷漆或刷涂的方式对家具进行上色,提升家具的外观质量。
3.上漆:根据客户要求,对家具进行多次涂漆、烘干,增加家具的亮度和保护层。
4.上蜡或抛光:对家具进行上蜡或抛光处理,提升家具的光泽度和质感。
5.检验与包装:对家具进行质量检验,清洁家具并进行包装,以确保产品质量和运输安全。
实木家具生产工艺流程

实木家俱生产工艺步骤一:备料1.板材干燥,将木材含水率控制在8%~10%,没有干燥过木材通常含水率在50%以上,干燥过后木材不轻易出现爆裂变形等现象。
2.平衡,把干燥过木头自然放置几天,让木材恢复平衡。
3.选料配料,木制品按其部位可分为外表用料、内部用料和暗用料三种。
外表用料露在外面,如写字台面、橱柜可视部分等;内部用料指用在制品内部,如内档、底版等;暗用料指在正常使用情况下看不到零部件,如抽屉导轨、包镶板、内衬条等。
选材时注意节疤、内裂、蓝变、朽木、端裂。
4.粗刨,给毛料板材定厚。
5.风剪,毛料板材修整长度。
下料按所需长度加长20mm。
6.修边,截去毛料板材上不能用毛边。
7.配板,木料配板选材分直纹、山纹,颜色搭配一致,配板宽度按所需宽度合理放余量。
选料时要把内裂、端裂、节疤、蓝变、朽木部分取下。
8.布胶,在木材之间均匀布胶,胶配比:固化剂(10—15克)、拼板胶(100克)比,每次调胶500克左右。
9.拼板,使用拼板机将木材进行拼装,拼板注意高低差、长短差、色差、节疤。
10.陈化,布胶完成木材放置2小时左右,让胶水凝固。
11.砂刨,刨去木材之间多出胶水,使木材板面无多出胶水。
12.锯切定宽,用单片锯给木材定宽。
13.四面刨成型,依据需要形状刨出木材。
14.养生,将木材自然放置二十四小时左右。
二:木工1.宽砂定厚,按要求砂止符合加工要求尺寸,机加完成后进行抛光砂,,粗砂一次砂0.2mm,抛光砂一次砂0.1mm。
2.精切,给毛料定长,加工过程中做到无崩茬、发黑,长和宽加工误差不超出0.2mm,1米以下对角线≤0.5mm,1米以上板片对角线应≤1mm。
3.成型,依据图纸将木材加工成型。
加工时不许可有崩茬、毛刺、跳刀和发黑现象,加工部件表面应光滑、平整、线型流畅一致,加工前检验设备部件螺丝有没有松动,模板是否安装规范,刀具是否装紧,加工过程中严禁顺刀进料,部件尺寸误差不超出0.2mm。
4.钻孔,按图纸工艺要求钻孔,加工过程中做到无崩口、无刺现象,孔位加工误差不得超出0.2mm,产品要做到配套钻孔,常试装、勤检验,确保产品品质。
实木家具工艺流程图

实木家具工艺流程图
实木家具是指产品的所有结构及可见部分,均以整块木料加工制作成,不使用任何贴面。
产品表里如一,即使刨去面层,内部也是完全相同的材质,换句话说,实木家具天然木材制成的家具,即所谓的纯实木家具,所有材料都是未经再次加工的天然材料,不使用任何人造板制成的家具。
家具表面一般都能看到木材真实的纹理。
如果想要真正展现出实木家具的自然原始之美,展现出自身的原木色,释放出自然与原始之美。
实木家具生产工艺就显得特别重要了。
实木家具工艺流程图
购进原木——开料——烘干——下料——拼板——下料——画线——开榫、打眼、开槽——组装——油漆——包装——出厂
其中施工工序分为三大类:
1:机械包括:
开料——烘干——下料——拼板——下料——画线——开榫、打眼、开槽;
2:组装:
这里就是组装组装这一工序看起来比较简单,一个家具的好坏都在这里了,所以这里是要求最细注意的地方最多的;
3:油漆包括:
打磨——刷底色——上腻子——喷漆——敲打----面漆。
看似简单,实则每个细节都要好好把握,以保证实木家具产品的质量。
(ppt版)家具生产工艺
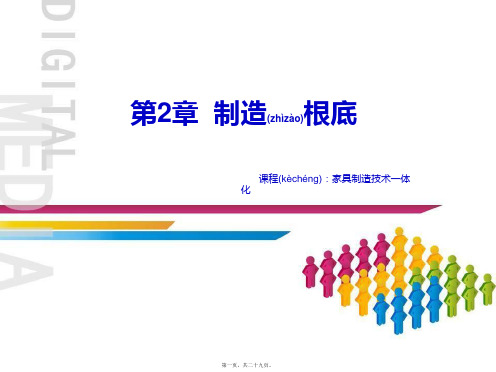
课程(kèchéng):家具制造技术一体 化
第一页,共二十九页。
本章节 内容: (zhāngjié)
• 第一局部:材料根底(gēndǐ) • 第二局部:结构根底 • 第三局部:加工根底 • 第四局部:典型设备 • 第五局部:典型工具 • 第六局部:木材枯燥
第二页,共二十九页。
• (3)零部件位置(wèi zhi)
•
的三种可能
被加工(jiā gōng)的零部件不动〔定位式加工 (jiā gōng)〕
被加工的零件固定在可移动的工作台上,能随
工作台一起移动〔定位通过式加工〕
被加工的零件按着需要移动〔通过式加工〕
加工度与自由度的关系见表2.3-1
第五页,共二十九页。
• 镂铣机
时; • 〔2〕粗刨后应采用不同的锯截方案。
第二十页,共二十九页。
• 5.集成材和实木拼板材(bǎn cái)的配料 • 〔1〕集成材曲线形毛料的配制 • 〔2〕实木拼板曲线形毛料的配制
第二十一页,共二十九页。
• 常用的配料设备(shèbèi)
• 1.细木工带锯机
• 2.横截锯〔横截圆锯机〕
第二十二页,共二十九页。
单面压刨床的刀轴安装 在工作台的上面,工件 沿着工作台面向前进给 时,通过刀轴上的刀片 将工件刨成一定的厚度。 工作台可以(kěyǐ)根据工件 的厚度要求,沿床身垂 直导、方材毛料的四个外表(wàibiǎo)进行平面刨光或型面铣 型。
第十二页,共二十九页。
• 1、定义〔见书本(shūběn)〕
•
工艺基准:定位基准、装配基准和测量基准
• 2、基准
设计基准:指在图纸上用于确定零件位置及标注(biāo zhù)尺
木制品生产的工艺过程与加工(ppt 64页)
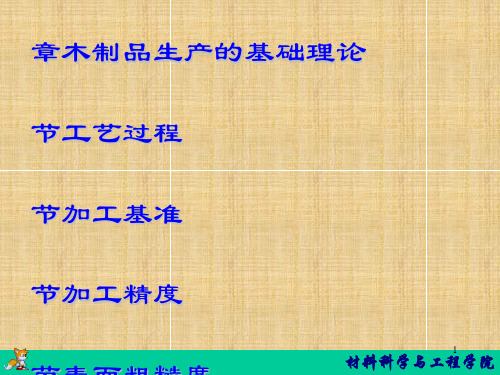
35
材料科学与工程学院
(三)夹具、模具的精度及零部件在夹具、模具上 的安装误差
1.组成夹具、模具各零部件的制造精度;
2.模具、夹具的安装方法及安装的精度;
3.夹具、模具受力变形而引起的加工误差。
采用刚度好的材料制造,使其具有足够的刚度, 减少在夹紧力和切削刀作用下产生的变形。
36
材料科学与工程学院
① 将原材料通过各种生产设备制成零部件
— 各自的工段、不同的工序
② 零部件的胶合、装配和装饰
— 零部件生产的后期加工处理
③ 零部件和产品的质量检验
— 生产车间全程监控
6
材料科学与工程学院
(4)生产服务包括(厂内生产管理)
① 生产车间、车间班组的生产组织和管理 — 车间负责人、工艺员、工段长、主机手、辅
动和绕Z轴转动,又约束了两个自有度。 4. 当把工件靠在Y-Z组成的平面上,工件便不能沿X轴移动。
至此,工件的六个自由度就全被约束了。从而使工件能在 设备上准确地定位和夹紧,这就是工件定位的“六点”规 则。
24
材料科学与工程学院
三.基准的基本概念
(一)基准
为了使零部件在设备上相对于刃具或在产品 中相对其它零部件具有正确的位置,需利用一些 点、线、面来定位,这些点、线、面就叫基准。
11
材料科学与工程学院
12
材料科学与工程学院
4.工艺过程路线图 制品中所有零部件工艺过程流程图的汇总或简称
工艺路线图。
13
材料科学与工程学院
(二)工序的分化和集中 1.工序的分化 (1)概念:使每个工序中所包含的工作量尽量减
少,把较大的、复杂的工序分成一系列小的、简 单的工序。
《家具生产工艺培训》课件
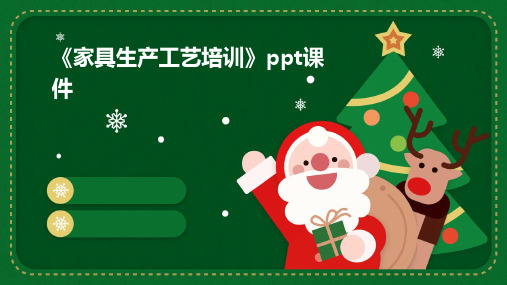
常用的有松木、橡木、胡桃木等,根据不同家具类型和用途选择合适的木材。
木材
如中密度纤维板、刨花板等,具有成本低、易于加工的特点。
人造板
如螺丝、合页、拉手等,用于连接和固定家具各个部分。
五金件
用于涂装和粘合家具各个部分,需选择环保、无害的产品。
涂料与胶水
金属连接的方法有多种,如焊接、螺丝连接、铆钉连接等。应根据实际情况选择合适的连接方式,以保证家具的稳定性和美观度。
总结词
金属表面处理可以提升家具的耐久性和美观度。
详细描述
常见的金属表面处理方法包括喷涂、电镀、烤漆等。应根据需求选择合适的表面处理方式,以达到防腐蚀、防刮擦、美观的效果。
软体家具工艺
加强员工安全生产培训和教育,提高员工的安全意识和安全操作技能。
01
02
03
04
了解国家环保法规和标准,确保企业生产活动符合环保要求。
加强环保设施建设和运行管理,确保污染物稳定达标排放。
建立环保管理体系,制定环保规章制度和操作规程。
开展环境监测和环保统计工作,及时掌握企业环保状况。
选择符合环保要求的原材料和零部件,优先选用可再生、可回收利用的材料。
指接
将两块或更多块木材拼接在一起,形成较大的平板,常用于制作桌面或地板等大面积的部件。
拼板
将一块木材嵌入另一块木材中,将木材粘合在一起,以提高其强度和稳定性。
胶合
上漆
在家具表面涂上油漆,以达到美观和保护的效果。
打蜡
在家具表面涂抹蜡,以提高其光泽度和防水性。
烫金
将金属箔或金箔烫印在家具表面,以达到装饰效果。
详细描述
展示高效、低成本的家具生产流程,分析其生产效率和成本控制。
木制家具生产流程
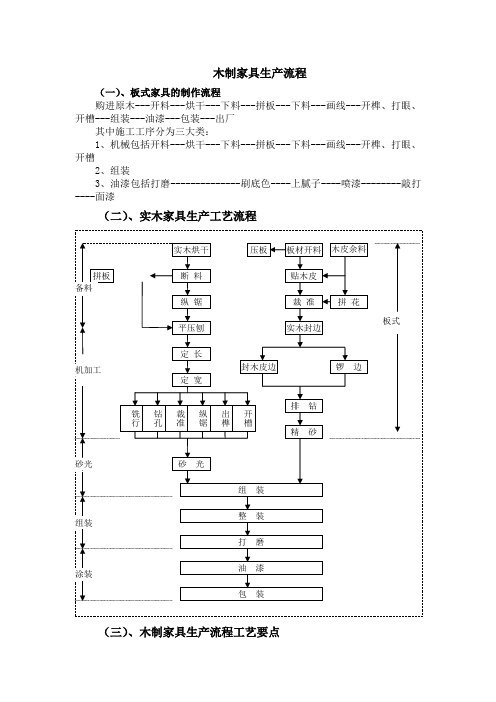
木制家具生产流程(一)、板式家具的制作流程购进原木---开料---烘干---下料---拼板---下料---画线---开榫、打眼、开槽---组装---油漆---包装---出厂其中施工工序分为三大类:1、机械包括开料---烘干---下料---拼板---下料---画线---开榫、打眼、开槽2、组装3、油漆包括打磨--------------刷底色----上腻子----喷漆--------敲打----面漆(二)、实木家具生产工艺流程(三)、木制家具生产流程工艺要点断 料纵 锯平压刨定 长定 宽实木烘干板材开料 贴木皮 裁 准 实木封边 压板 拼板木皮余料 拼 花 封木皮边 锣 边 排 钻精 砂 铣行 钻孔 裁准 纵锯 出榫 开槽砂 光组 装整 装打 磨油 漆包 装 机加工备料 砂光 组装 涂装板式木制家具生产工艺主要有五个过程:1、配料;2、白胚加工;3、组装;4、涂装;5、包装。
1、配料家具传统的配料方法通常由以下几道工序组成:选料、切长、压刨、纵剖、平刨、拼板、套材、压刨、四面刨等。
随着新型加工设备的出现,以上的流程已得到相应的简化,但基本原理是不会改变的。
配料一般需用到下列机器:切床、压刨、开料锯、平刨、铣床、拼板机、带锯、四面刨等。
另外,近几年出现的新型的设备有:全自动电脑优选锯、高周波拼板机、全自动高精度四面刨等等。
品质控制在配料过程中亦是相当重要的,配料的品质控制重点有:材料的质量(毛边、撕裂、凹陷、压痕、虫孔、腐朽、变形、节疤等)、含水率、尺寸、刀痕、拼板胶的配比及质量、拼板压力、加压时间、布胶的方法及用量、木纹的大小及方向、板材的握钉力及平整度。
另外,热压也可归纳入配料的工序里,它是板材前期加工中的重要一环。
热压包括拼花、贴皮、曲压等等。
热压所使用的机器归纳机来有以下几种:切皮机、车缝机、布胶机、热压机、冷压机、封边机、曲压机等,近几年用于热压工序的新型机器不断的推陈出新,也使得许多传统工艺无法加工的产品现在可以加工了。
- 1、下载文档前请自行甄别文档内容的完整性,平台不提供额外的编辑、内容补充、找答案等附加服务。
- 2、"仅部分预览"的文档,不可在线预览部分如存在完整性等问题,可反馈申请退款(可完整预览的文档不适用该条件!)。
- 3、如文档侵犯您的权益,请联系客服反馈,我们会尽快为您处理(人工客服工作时间:9:00-18:30)。
3.质量要求:门方厚度符合图纸要求,公差范围+0.3MM。 柜内角接90°角,柜内尺寸误差可达+5MM。 实木门生 产流程三、开子口(门柜) 1. 基本工艺及操作要求:锯 切前,检查锯
片无裂纹,锯齿有无松动与脱落,如有应更换锯片。锯 切中,如锯片变钝也应更换;批量加工前应先试车,检查 子口规格是否符合图纸要求。 2. 使用材料:不同规格尺 寸的净料。 3. 质量要求:
用PH值试纸测试。 工艺过程如下: 先加水至规定分量- -按比例加入胶粉――加入适量催干剂――充分搅拌―― 出胶。该调配过程应严格按比例投料。 2.使用材料: “AEROLITE”胶粉或
同性能胶粉:水、催化剂。 3.质量要求:目测胶液中是
否有悬浮的颗粒状胶粉,如有则应继续搅拌,直至胶液 均匀一致。调致好后,胶液应陈放10分钟才能涂胶。 实 木门生产流程四、涂胶、配坯、
少于7小时。 2. 使用材料:各种规格的净材、胶液、冷压 机、涂胶滚筒。 3.质量要求: 3.1. 涂胶时胶液应均匀一 致,保证无漏涂,气泡等现象。 3.2. 排芯时检查枋有无 腐朽、死
节、厚度不一,缺棱等缺陷,有则应将其剔除、更换。
3.3. 检查芯条与边方间的间隙,实芯门芯枋间的间隙不得 超过2MM,芯枋端与门枋之间的间隙不得超过3MM。 3.4. 板件经胶压后
有崩边、缺口。 实木门生产流程六、封边、铣边与修整
1.基本工艺及操作要求: 1.1.封边条的截切要长料长用, 短料短用。斜口切成45°角,内侧长与门的规格一致。 1.2.手工涂胶时
,胶水要涂匀,封边后流出的胶水要及时擦干净。 1.3.封 边后要用螺机将高出面板的不平整部份螺平。 1.4.边部铣
平后要刨光,手刨修整时要注意不可将表层夹板或胶板 刨破 2.使用材料:
具有准确规格尺寸的净材。 质量要求:榫肩要与工件长 度方向呈45°或90°角,或符合装配要求,榫头尺寸要 符合图纸规定或装配要求。 实木门生产流程一、钻榫眼 1.其本工艺和操作要求:开
机前,按照图纸要求,调好定位装置,装好刀具,打眼
前要求先划线或定位,操作时,工件要对正,压紧压实, 进料速度因材质软硬、工件厚度而不同。 2.使用材料: 具有准确规格尺寸的净材。 3.
质量要求:加工出的榫眼表面要光滑、无毛刺,其规格 与定位尺寸必须符合图纸要求或装配要求。 实木门生产
流程二、门枋组柜 1.基本工艺和操作要求:根据图纸规 格尺寸要求检查门选用合格进行装
配,门枋与门枋间采用榫接合时,定位后应在接后处双
面钻圆孔,打入圆棒固定。若有特殊要求门枋间不采用 榫接合,则应双面打“V”形钉固定。 2.使用材料、设备: 门枋各组成件、手工、锤、钉。
,应检查有无脱胶现象。 实木门生产流程五、截门边 1. 基本工艺及操作要求:开机前先检查机件是否正常,锯 片有无裂纹,松动、脱落现象,滑道是否顺畅。并且根 据部件规格调好设备才锯片,操作
时要均速进料,不可猛撞据片,半成品加工应轻放,以 免损坏产品。 2.使用材料 3.质量要求:门的长、宽尺寸 要符合图纸要求,公差范围+1MM,门的两相邻边成90° 角,锯边要光滑,不允许
胶压 1.其本工艺及操作要求: 1.1 涂胶前将基材表面清理 干净,然后用滚筒手工均匀滚涂,涂胶时不得有缺陷、 气泡现象发生,并不能将胶水沾污产品的表面。通常涂 量为120-150g/m
2 1.2. 排芯:实芯板排芯时,芯条要紧密排列,不能有松 动;格子空芯板排芯时,按图先排横条,划线后再排直条。 1.3. 胶压:胶压时上下板坯要对齐避免不正常状态加压, 胶压时间不得
我国古代人为自己家添加保护“屏障”用的门都是木制 而成的,这也就是我们常说的原木门也属于实木门中的 一种。那么,沿用至今的实木门生产流程是怎么样的, 您了解吗? 实木门生产基本工艺和操
作要求:开机前,须将刀头按图纸调整到加工规定的位
置。然后先试车,试出的榫头尺寸符合要求后才批量生 产。加工时的进料速度V进均匀适当,不可猛拉硬撞,以 免损坏刀具,影响精度。 使用材料:
各规格的封边条。 3.质量标准 3.1.封边条不能有不符合选
材标准的缺陷,某些含允许小缺陷的面放在内侧,好面 朝外。各边封边条应完整,无接口。边与边的45°角接表面无胶水流挂痕迹,门高度和宽度尺寸 允许误差+1.5MM,门厚度允许误差+1MM。 实木门生产 流程七、开锁眼 1.基本工艺及操作要求:根据图纸尺寸 要求,调好木门定位装置
角 1.基本工艺及操作要求: 1.1.开机前,先检查机器运转
是否正常,铣刀有无损坏,并根据图纸规定圆位。开机 时,要按图纸调节好刀具。 1.2.手工进料时要紧靠导向滚 匀速推进,保证所
,待刀头运转正常方可进刀钻孔。钻孔前,需检查钻头 是否锋利,有无破损操作中搬运要小心,以免产品受损 2. 使用材料:各种净料尺寸的板材。 3.质量要求:钻头直 径要符合尺寸要求,锁眼要符
合图纸规定或配合锁样板要求,允许误差范围+0.5MM。 各规格的锁眼必须与板面垂直,孔边不得崩烂和发焦、 发黑,边工后部件表面不得有刮伤、擦痕等。 实木门生 产流程八、开铰位 1.基本工
子口要求符合图纸要求,误差范围+1MM,对于有选材标 准中允许小缺陷的工件。进锯时应尽量将小缺陷在开子 口时切除或将允许的缺陷留在背面。 实木门生产流程四、 调胶 1.基本工艺及操作要求
:采用“AEROAITE”胶粉或其他同性能的胶粉,按胶粉: 水=100:94调配,用量一般为胶液的1-2%,气温低高, 催干剂用量可小;气温低则用量多,调好的胶液PH值约 为4-5间,可
艺及操作要求:铣槽前先在工件上划线,根据图纸尺寸
和工件划线调好定位挡块,然后开机。操作中,铣刀要 对正靠紧,铣出槽后要用木斧手工加工出直角。 2.使用 材料:各种净材尺寸的零部件。 3
.质量要求:加工出的铰位表面要光洁平整,无毛茬木刺。
铰位的深浅和尺寸必须与要用门铰位样品量吻合,铰位 偏差允许+0.3MM,深浅尺寸公差允许+0.5MM。 实木 门生产流程九、门框螺圆