PCBA工艺可制造性规范THT培训
PCBA可制造设计规范
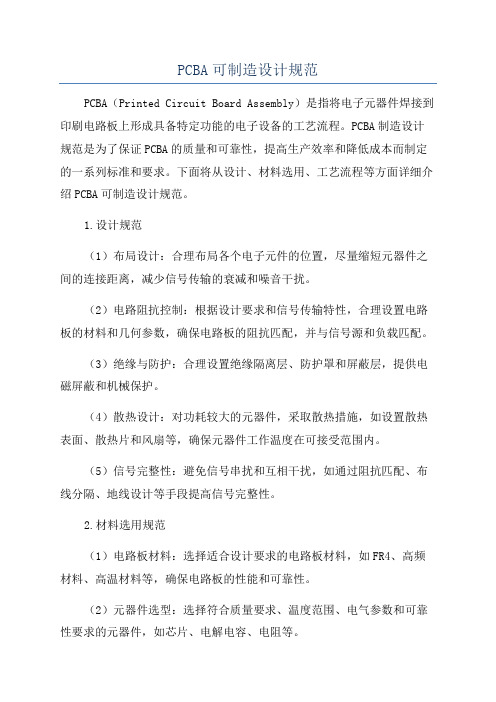
PCBA可制造设计规范PCBA(Printed Circuit Board Assembly)是指将电子元器件焊接到印刷电路板上形成具备特定功能的电子设备的工艺流程。
PCBA制造设计规范是为了保证PCBA的质量和可靠性,提高生产效率和降低成本而制定的一系列标准和要求。
下面将从设计、材料选用、工艺流程等方面详细介绍PCBA可制造设计规范。
1.设计规范(1)布局设计:合理布局各个电子元件的位置,尽量缩短元器件之间的连接距离,减少信号传输的衰减和噪音干扰。
(2)电路阻抗控制:根据设计要求和信号传输特性,合理设置电路板的材料和几何参数,确保电路板的阻抗匹配,并与信号源和负载匹配。
(3)绝缘与防护:合理设置绝缘隔离层、防护罩和屏蔽层,提供电磁屏蔽和机械保护。
(4)散热设计:对功耗较大的元器件,采取散热措施,如设置散热表面、散热片和风扇等,确保元器件工作温度在可接受范围内。
(5)信号完整性:避免信号串扰和互相干扰,如通过阻抗匹配、布线分隔、地线设计等手段提高信号完整性。
2.材料选用规范(1)电路板材料:选择适合设计要求的电路板材料,如FR4、高频材料、高温材料等,确保电路板的性能和可靠性。
(2)元器件选型:选择符合质量要求、温度范围、电气参数和可靠性要求的元器件,如芯片、电解电容、电阻等。
(3)焊接材料:选用适合工艺流程的焊接材料,如无铅焊料、焊膏等,确保焊接质量和可靠性。
3.工艺流程规范(1)印刷:确保PCB板材表面光洁、均匀,印刷厚度均匀一致,避免短路和偏厚现象。
(2)贴片:确保元器件与PCB板材精准对位,减少误差和偏离,避免虚焊、漏焊和偏焊。
(3)回流焊接:控制焊接温度和时间,确保焊点可靠性和焊接质量,避免过热和虚焊。
(4)清洗:清除焊接过程中产生的残留物,如焊膏、金属颗粒等,保证PCBA表面的干净和可靠性。
(5)测试与检验:进行全面的功能测试和质量检验,确保PCBA的功能和质量达到设计要求。
4.环境标准(1)温度和湿度:控制生产环境的温度和湿度,以确保PCBA的稳定性和可靠性。
PCBA性培训资料

PCBA性培训资料一、PCBA 简介PCBA 是 Printed Circuit Board Assembly 的缩写,即印刷电路板组装。
它是将电子元器件安装在印刷电路板上,并通过焊接等工艺使其成为一个具有特定功能的电子组件。
PCBA 广泛应用于各种电子设备中,如计算机、手机、家电、汽车电子等。
二、PCBA 生产流程PCBA 的生产流程大致可以分为以下几个主要步骤:1、设计原理图设计:确定电路的连接和功能。
PCB 布局设计:安排电子元器件在电路板上的位置。
2、制板制作 PCB 裸板:通过蚀刻、钻孔等工艺将电路图印制在基板上。
3、元器件采购根据 BOM(物料清单)采购所需的电子元器件。
4、贴片使用贴片机将表面贴装元器件(SMD)精确地安装在 PCB 板上。
5、插件手工或机器将插件元器件插入 PCB 板的相应孔位。
6、焊接采用回流焊或波峰焊等工艺将元器件焊接在 PCB 板上。
7、检测进行外观检查,确保元器件安装正确、无短路等缺陷。
功能测试,检测 PCBA 是否能正常工作。
8、清洗去除焊接过程中产生的助焊剂等残留物。
9、包装对合格的 PCBA 进行包装,以保护其在运输和存储过程中不受损坏。
三、PCBA 中的电子元器件1、电阻作用:限制电流、分压等。
常见类型:固定电阻、可变电阻。
2、电容作用:存储电荷、滤波、耦合等。
常见类型:电解电容、陶瓷电容、钽电容等。
3、电感作用:储存能量、滤波等。
常见类型:空心电感、磁芯电感。
4、二极管作用:单向导电、整流等。
常见类型:整流二极管、稳压二极管、发光二极管等。
5、三极管作用:放大信号、开关等。
常见类型:NPN 型三极管、PNP 型三极管。
6、集成电路(IC)作用:实现复杂的功能,如运算、控制等。
常见类型:微处理器、存储器、逻辑芯片等。
四、PCBA 焊接工艺1、回流焊原理:通过加热使焊膏熔化,实现元器件与 PCB 板的焊接。
优点:焊接质量高、效率高、适合表面贴装元器件。
PCBA工艺可制造性的基本概念介绍ppt

《PCBA设计及可靠性》
THANK YOU.
静电防护
在PCBA制造过程中,静电是一个潜在的危害因素,可能导致元器件损坏或性能下降。
洁净度要求
PCBA制造过程中,对环境中的尘埃、颗粒物等污染物有严格的要求,以确保焊接质量和 可靠性。
05
总结
总结本次介绍的要点
01
PCBA工艺可制造性是指在不同环境和条件下,通过选择合适的材料、设计合理 的电路板结构、制定规范的制板流程和严格的质量控制体系,实现高效率、低 成本、高质量的PCBA制作。
背景
近年来,随着电子产品的不断升级换代和技术进步, 电子制造企业面临着日益激烈的市场竞争。为了提高 生产效率和产品质量,降低制造成本,电子制造企业 需要关注PCBA工艺的可制造性问题。通过对PCBA工 艺可制造性的研究和改进,可以有效地解决生产过程 中的瓶颈问题,提高生产效率和产品质量,增强企业 的市场竞争力。
采用专业的EDA(电子设计自动化)软件,如Cadence、 Synopsys等。
设计优化
通过软件工具进行布局优化、布线优化、信号完整性仿真等,提 高PCBA的可制造性。
数据分析
利用软件工具进行数据分析,识别出可能的制造问题和风险,提 前进行规避和优化。
案例三:环境因素对可制造性的影响
温度和湿度
对于PCBA制造来说,温度和湿度是两个重要的环境因素,对制造过程中的元器件性能和 焊接质量产生影响。
率。
软件模块化
02
将软件程序划分为多个模块,以提高代码的可读性和可维护性
。
软件测试和验证
03
对软件进行全面、细致的测试和验证,以确保其正确性和可靠
性。
环境优化
生产环境设置
smt培训资料(全)

SMT培训手册上册SMT基础知识目录一、SMT简介二、SMT工艺介绍三、元器件知识四、SMT辅助材料五、SMT质量标准六、安全及防静电常识第一章SMT简介SMT 是Surface mount technology的简写,意为表面贴装技术。
亦即是无需对PCB钻插装孔而直接将元器件贴焊到PCB表面规定位置上的装联技术。
SMT的特点从上面的定义上,我们知道SMT是从传统的穿孔插装技术(THT)发展起来的,但又区别于传统的THT。
那么,SMT与THT比较它有什么优点呢?下面就是其最为突出的优点:1.组装密度高、电子产品体积小、重量轻,贴片元件的体积和重量只有传统插装元件的1/10左右,一般采用SMT之后,电子产品体积缩小40%~60%,重量减轻60%~80%。
2.可靠性高、抗振能力强。
焊点缺陷率低。
3.高频特性好。
减少了电磁和射频干扰。
4.易于实现自动化,提高生产效率。
5.降低成本达30%~50%。
节省材料、能源、设备、人力、时间等。
采用表面贴装技术(SMT)是电子产品业的趋势我们知道了SMT的优点,就要利用这些优点来为我们服务,而且随着电子产品的微型化使得THT无法适应产品的工艺要求。
因此,SMT是电子装联技术的发展趋势。
其表现在:1.电子产品追求小型化,使得以前使用的穿孔插件元件已无法适应其要求。
2.电子产品功能更完整,所采用的集成电路(IC)因功能强大使引脚众多,已无法做成传统的穿孔元件,特别是大规模、高集成IC,不得不采用表面贴片元件的封装。
3.产品批量化,生产自动化,厂方要以低成本高产量,出产优质产品以迎合顾客需求及加强市场竞争力。
4.电子元件的发展,集成电路(IC)的开发,半导体材料的多元应用。
5.电子产品的高性能及更高装联精度要求。
6.电子科技革命势在必行,追逐国际潮流。
SMT有关的技术组成SMT从70年代发展起来,到90年代广泛应用的电子装联技术。
由于其涉及多学科领域,使其在发展初其较为缓慢,随着各学科领域的协调发展,SMT在90年代得到讯速发展和普及,预计在21世纪SMT将成为电子装联技术的主流。
PCBA目检 ( SMT) 规范ppt课件
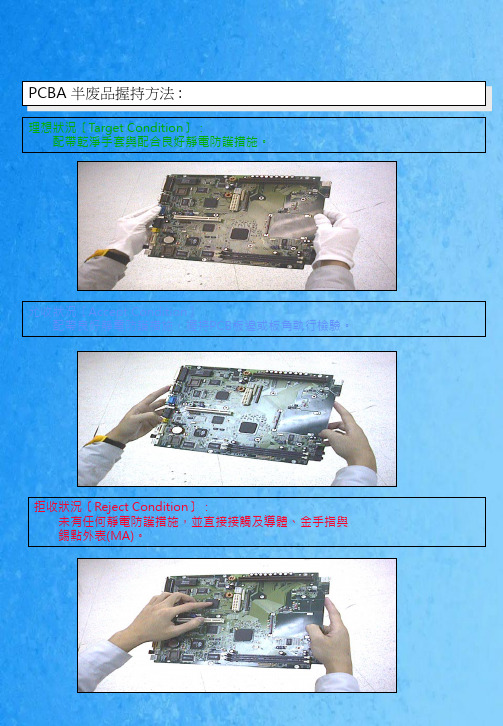
允收狀況(Accept Condition)
1.腳跟的焊錫帶已延伸到引線 上彎曲處的底部(B)。
拒收狀況(Reject Condition) 過90度
1.腳跟的焊錫帶延伸到引線上 彎曲處的底部(B)上方,延伸 過高,且沾錫角超過90度,才 拒收(MI)。
SMT焊點性工藝標準--J型接腳零件之焊點最小量
1.各接腳側端外緣,已 超過焊墊外端外緣(MI)。
已超過焊墊側端外緣
SMT零件組裝工藝標準--QFP零件腳跟之對準度
理想狀況(Target Condition)
1.各接腳都能座落在各焊 墊的中央,而未發生偏 滑。
X
W
允收狀況(Accept Condition)
1.各接腳已發生偏滑,腳跟
剩餘焊墊的寬度,最少保 有一個接腳寬度(X≧W)。
1.錫已超越到晶片頂部的上方 (MI) 。
2.錫延伸出焊墊端(MI)。 3.看不到晶片頂部的輪廓(MI)
。
SMT焊錫性工藝標準--焊錫性問題 (錫珠、錫渣)
理想狀況(Target Condition)
1.無任何錫珠、錫渣殘留於 PCB。
允收狀況(Accept Condition)
D≦ 0.15mm 拒收狀況(Reject Condition)
1.錫珠、錫渣直徑D或長度 L≦0.15mm。
(D,L≦0.15mm)
1.錫珠、錫渣直徑D或長度L> 0.15mm(MI)。 2.单面超越5个拒收.(MI)
.
D> 0.15mm
DIP零件組裝工藝標準--零件腳長度標準
理想狀況(Target Condition)
1.插件之零件假设於焊錫後有浮 高 或傾斜,須符合零件腳長度標 準。 2.零件腳長度以 L 計算方式 : 需從PCB沾錫面為衡量基準, 可目視零件腳出錫面為基準。
PCBA制程培训材料
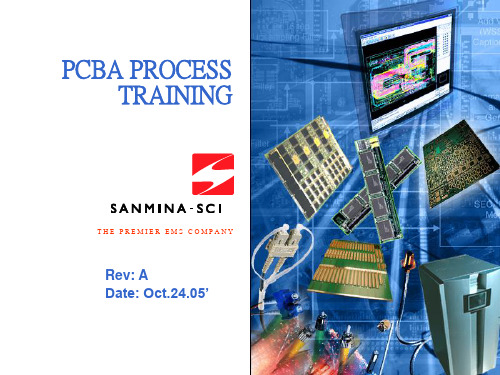
(二)波峰焊的工艺流程:
1. 手插件(Hand Insertion) 2. 松香系统(Flux) 3. 波峰焊 (W/S) 4. 整饰(Touch up) 5. 目检(VMI)
(一)波峰焊工艺组成
生产工艺过程 1. 线路板通过传送带进入波峰焊机以后,会经过某个形式的 助焊剂涂敷装置,在这里助焊剂利用波峰、发泡或喷射的方 法涂敷到线路板上。由于大多数助焊剂在焊接时必须要达到 并保持一个活化温度来保证焊点的完全浸润,因此线路板在 进入波峰槽前要先经过一个预热区。
• 粘力 • 塌落性 • 可焊性 • 助焊剂导电性 • 酸度(mgKOH/g) • 卤化物含量
粘度及金属含量
以下因素影响粘度: 粘度
焊膏中的金属含量 助焊剂的粘度 温度 焊膏寿命、储存情况 预搅拌
金属含量
识别LOT# 和 PART#
LOT# - 50802943
5 = 2005 08 = 8月 02 = 2号 943 = 设备、操作人员编号
Function Test
FVMI
OBA
Packing
Final QA
二、表面贴装技术(SMT)
表面贴装技术, 简称SMT, 作为新一代电子装联技术已经渗 透到各个领域,SMT产品具有结构紧凑、体积小、耐振动、 抗冲击,高频特性好、生产效率高等优点。SMT在电路板装 联工艺中已占据了领先地位。
● SMT 的特点:
1. 组装密度高、电子产品体积小、重量轻, 贴片元件的体积和 重量只有传统插装元件的1/10左右, 一般采用SMT之后, 电子 产品体积缩小40%~60%, 重量减轻60%~80%。 2. 可靠性高、抗振能力强。焊点缺陷率低。 3. 高频特性好。减少了电磁和射频干扰。 4. 易于实现自动化, 提高生产效率。降低成本达30%~50%。 5. 节省材料,能源,设备, 人力,时间等。
PCBA工艺可制造性的基本概念介绍

pcba工艺可制造性的基本概念介绍汇报人:日期:•pcba工艺可制造性概述•pcba设计对工艺可制造性的影响•pcba材料对工艺可制造性的影响•制造过程中可能遇到的问题及解决方案•提高pcba工艺可制造性的建议和策略目录01pcba工艺可制造性概述定义PCBA(Printed Circuit Board Assembly)工艺可制造性是指在设计阶段,评估PCB板及其组件在制造过程中实现可靠、高效及低成本的制造工艺的能力。
重要性工艺可制造性评估对于PCB板及组件的批量生产至关重要,可确保制造过程中的质量和成本控制,提高生产效率和降低废品率。
定义与重要性包括布局、走线、过孔等设计因素,影响信号完整性、生产效率及成本。
PCB板设计组件的类型、大小及布局影响生产流程和成本。
组件选型与布局原材料、人工成本及供应链管理等影响总成本和交货期。
制造成本与供应链管理制造过程中使用的流程和工艺技术对生产效率和产品质量有直接影响。
制造流程与工艺技术工艺可制造性的影响因素工艺可制造性的评估方法评估PCB板和组件的设计是否符合制造要求,检查布局、走线等设计因素。
设计审查仿真与建模试制与验证数据分析与持续改进利用仿真软件和建模工具预测制造过程中可能出现的问题。
在小批量生产中测试和验证PCB板和组件的制造工艺及质量。
收集生产过程中的数据,分析瓶颈和问题,持续改进制造工艺和流程。
02pcba设计对工艺可制造性的影响PCB板的尺寸和形状应符合制造工艺的要求,例如最大和最小板尺寸、板厚度等。
电路板尺寸和形状元件间距和布局层数和材料元件的间距和布局应考虑制造过程中焊点的质量和可靠性,以及布线的能力。
PCB板的层数和材料应考虑制造过程的复杂性和成本,以及电路板的功能需求。
03设计规则与限制0201元件选择元件的选择应考虑其规格、性能、可靠性以及制造能力,例如封装类型、引脚间距等。
元件布局元件的布局应考虑电路板的整体结构、散热性能以及信号质量,同时也要符合制造工艺的要求。
PCBA板生产工艺培训 ppt课件

2.将标识的不良品转至修理工位修理 3.作业时必须戴防静电带/衣服/帽子.
ppt课件
16
SMT工艺流程——ICT测试
方法: 1.取ICT治具置于ICT测试机台上,将排线按序号对应插在ICT治具之插座上; 2.取ICT天板固定于ICT治具上模上,固定前必须用平衡玻璃板检查ICT天板上
丝印机的参数设置
注意事项:
1. PCB投入前必须100%检查焊盘,确认无异物、脏污、氧化等不良 2.拿取PCB时不可直接接触到PCB,必须使用手指套.
ppt课件
5
SMT工艺流程—印刷机
3.锡膏按少量多次添加,锡膏在钢网上滚动的直径最好保持1.0-1.5cm。 4.钢网清洁,一小时手动清洁,包括网框内的锡膏清洁 5.每2小时由IPQC测试一次锡膏厚度
Over
D區
180ºC
30~5
0sec
TIME(sec)
15
SMT工艺流程——炉后检验
方法:
1.按"SMT 缺陷检验标准"和PI 对PCBA 进行目检 2.首先检查所有CHIP 料有无缺件、错料、反面、破损等不良,并记录和用箭头 纸标识。
3. 用放大镜目检所有IC 有无反向,移位、少锡、连焊等不良,将不良点标识, 并填写SPC检查记录表,将有规律性的,集中的特殊的不良问题点及时反馈当班负责 人及IPQC/PE。 注意事项:
用蜡笔在PCB板面上做标记,传下一站;如果屏幕上出现“FAIL”,并显示FAIL位 置,则用不良标签贴于不良处,放入不良品胶盒中。 注意事项:
1、ICT的气压值为:4.5±0.5kg/cm²。 2、不良状况如实记录,不良品作不良标记后送维修站维修。 3、作业员必须戴静电环作业。
- 1、下载文档前请自行甄别文档内容的完整性,平台不提供额外的编辑、内容补充、找答案等附加服务。
- 2、"仅部分预览"的文档,不可在线预览部分如存在完整性等问题,可反馈申请退款(可完整预览的文档不适用该条件!)。
- 3、如文档侵犯您的权益,请联系客服反馈,我们会尽快为您处理(人工客服工作时间:9:00-18:30)。
THD元件的选择、设计
• 6.元件引脚直径大于(长或宽取较大值) 1.2mm,或引脚为钢针等较硬的材质,元件 的引脚高度应设计为标准高度 3.5mm+/0.5mm(仅仅适合厚度为1.6mm,2.2mm的 PCB).以避免剪脚作业。例如:变压器, 电感…
3.5mm+/-0.5mm
THD元件的选择、设计
制造工艺:印刷--贴片--回流焊接--下一工序
PCBA装联的工艺选择
2.单面纯THD插装-PCB仅一面分部插装类器件。
制造工艺:插件--波峰焊接--下一工序
PCBA装联的工艺选择
3.双面SMD贴装-PCB两面均为SMD贴装器件。
制造工艺:印刷--贴片--回流焊接--印刷-贴片-回流焊接--下一工序
PCBA装联的工艺选择
4.单面SMD与THD元件混装-SMT与THD元件分 部在PCB板的同一面
制造工艺:印刷-贴片--回流焊接--插件--波峰 焊接--下一工序
PCBA装联的工艺选择
5.双面THD 与SMD元件混装-PCB一面为THD插装 元件,另一面为SMD贴装元件。
制造工艺:印刷-贴片--回流焊接--插件--波峰焊 接--下一工序
详细排序
第二节 THD元件的选择、设计
返回大纲
THD元件的选择、设计
• 1.同功能元件,除经常使用的插座、插头, 如有SMD类型封装,不应使用THD插装类元 件。
• 2.原则上跳线不可用于PCB表面电器、线 路连接导通作用。如必须使用,跳线本体 须做绝缘处理.
THD元件的选择、设计
3.有高震动要求,或者重量超过15g的轴向 元件,应有专用的支架,支撑固定。(例 如:保险管)
PCBA装联的工艺选择
8.双面THD与SMD混装—PCB两面均分部THD类 插装元件,其中一面同时分部SMD贴装元件。
制造工艺:印刷-贴片--回流焊接--插件--波峰 焊接--插件--手工焊接--下一工序
PCBA装联的工艺选择
9.双面THD与SMD混装2—PCB两面均分部THD类 插装元件,两面面同时分部SMD贴装元件。
大纲
PCBA制造工艺选择
PCB表面处理方法
THD元件的选择、设计
PCB表面丝印、标识
PTH/NPTH通孔与焊盘设计
PCBA布局设计
PCBA拼板、工艺边设计
第一节 PCBA装联的工艺选择
返回大纲
PCBA装联的工艺选择
常见的PCBA装联工艺常见的PCBA 装联方式有以 下几种:
1.单面纯SMD贴装—PCB仅一面贴装SMD元件。
THD元件的选择、设计
4.工作频率较高或工作稳定较高的有浮高要 求的元件,应选择元件本身有支撑装置或 元件引脚有定位设计。(例如:压敏电阻, 三极管…)
THD元件的选择、设计
5.通孔插装的元件应选用底部(与PCB结合 部位)有有透气设计的元件,以免造成 “瓶塞效应”,造成焊接不良。
瓶塞效应:指由于元件与PCB结合过紧,导 致焊接时,PCB内部受热产生气体无法排 出(焊接面与焊锡完全结合),导致焊点 产生针孔,炸锡或焊接高度不够等不良现 象。
• 例如:散热器
THD元件的选择、设计
• 13.散热器设计 • a.散热器上组装的元件,必须保证组装后,
组件的引脚在同一水平线上,以利于插装 作业。
同一水平
THD元件的选择、设计
• b.散热器上的元件的类别应尽量为1种,如 有特殊原因,也应保证同一散热器本体上 组件的类别在3种以下,且从外观上容易区 分,以防止装配性错误。
制造工艺:印刷-贴片--回流焊接--印刷-贴片--回 流焊接--插件--波峰焊接--插件--手工焊接--下一 工序
PCBA装联的工艺选择
以上9种PCBA装联方式依照制造工艺特点, 其装联难度不一,设计时应优先考虑较为 简单的制造工艺(顺序1.2.3…9),尽量使 用自动化装联程度高的工艺,避免手工作 业程序。
PCBA的可制造性设计规范 --THT培训
Through Hole Technology 通孔插装技术/工艺
工艺部 PCBA-冯涛
破冰
注意
• 1.本规范所涉及的内容不能保证其完整性, 但是对产品设计有一定的约束力。
• 2.本规范内容不一定是标准的,但是对于我 们的产品相对适用。
• 3.本规范内容不是最终的,因为产品不断更 新,电子行业不断进步,规范内容也会 ” 与时俱进“。
• c.同一散热器上的元件最多应保持在4~5个, 以防止组装中的公差叠加,导致插装作业 难度增加,影响产品整体制造速度以及造 成质量隐患。
THD元件的选择、设计
• 11.如板面有连接器、插座、插针类得元件, 其顶端应做倒角设计,以方便插装。且元 件与PCB结合部位必须做透气设计。
• 倒角的大小视元件插孔或引脚大小决定, 这里不做规定
THD元件的选择、设计
• 12.PCB组件与PCB装联的方式尽量避免使用 螺钉连接,可设计为定位柱,利用波峰焊 接进行机械连接,可有效提高装配效率, 同时减低材料使用。
PCBA装联的工艺选择
6.双面SMD与THD混装—PCB两面均分布SMD 贴装元件,其中一面同时分部THD插装元件。
制造工艺:印刷-贴片--回流焊接--印刷-贴片-回流焊接--插件--波峰焊接--下一工序
PCBA装联的工艺选择
7.双面纯THD插装-PCB两面均分布THD插装类元 件。
制造工艺:插件--波峰焊接--插件--手工焊接--下 一工序
THD元件的选择、设计
• 9.SOJ,PLCC,BGA和引脚间距小于0.8mm 等贴 片类元件不可以采用波峰焊接方式。
BAG
PLCC
SOJ
THD元件的选择、设计
• 10.导线尽量不要直接与PCB连接,进行焊接 作业。以确保其可操作性,同时避免导线绝 缘层损害。应使用连接器或插座,利用其焊 接机理,进行机械连接。
• 7.使用双面混装工艺的PCBA,PCB底面SMD 元件的高度不可超过3mm。
3 mm
THD元件的选择、设计
• 8.SMD类元件的耐温必须达到260摄氏度以上, 且包装方式必须满足防潮,防震,放挤压, 防静电的要求以满足产品制造过程。
• THD类元件的耐温必须达到120摄氏度以上及 260度,6s/3次以上的要求,其包装方式必须 满足防潮,防震,放挤压,防静电的要求, 以满足产品制造过程。同时应首先选择编带 式的封装方式,以提高元件的加工效率。