化工大学精馏实验报告
化工大学精馏实验报告汇总
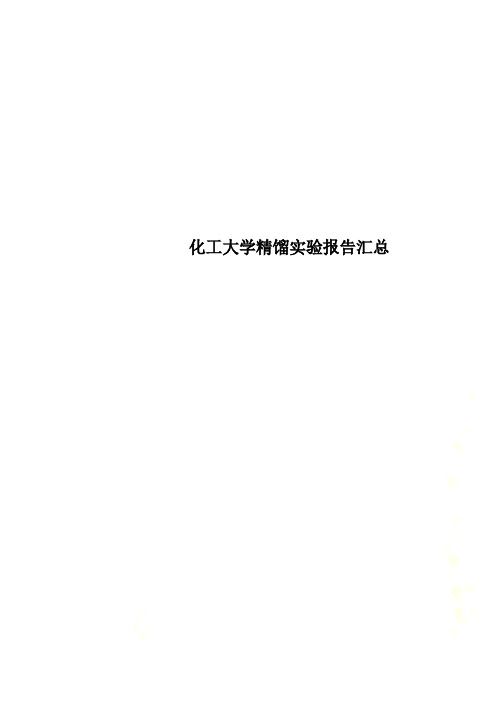
3
1.塔顶冷凝器 2.塔身 3.视盅 4.塔
釜 5.控温棒 6.支座
7.加热棒 8.塔釜液冷却器
9.转
子流量计 10.回流分配器
11.原料液罐 12.原料泵 13.缓
冲罐 14.加料口 15.液位计
2.回流分配装置 回流分配装置由回流分配器与控制器组成。控制器由控制仪表和电磁线圈 构成。回流分配器由玻璃制成,它由一个入口管、两个出口管及引流棒组成。 两个出口管分别用于回流和采出。引流棒为一根∮4mm 的玻璃棒,内部装有铁芯, 塔顶冷凝器中的冷凝液顺着引流棒流下,在控制器的控制下实现塔顶冷凝器的 回流或采出操作。即当控制器电路接通后,电磁圈将引流棒吸起,操作处于采 出状态;当控制器电路断开时,电磁线圈不工作,引流棒自然下垂,操作处于 回流状态。此回流分配器可通过控制器实现手动控制,也可通过计算机实现自 动控制。 3.测控系统 在本实验中,利用人工智能仪表分别测定塔顶温度、塔釜温度、塔身伴热 温度、塔釜加热温度、全塔压降、加热电压、进料温度及回流比等参数,该系 统的引入,不仅使实验跟更为简便、快捷,又可实现计算机在线数据采集与控 制。 4.物料浓度分析 本实验所用的体系为乙醇-正丙醇,由于这两种物质的折射率存在差异,且 其混合物的质量分数与折射率有良好的线性关系,故可通过阿贝折光仪分析料 液的折射率,从而得到浓度。这种测定方法的特点是方便快捷、操作简单,但 精度稍低;若要实现高精度的测量,可利用气相色谱进行浓度分析。 混合料液的折射率与质量分数(以乙醇计)的关系如下。
Q=U2/R
式中 U——电加热的加热电压,V;
R——电加热器的电阻,Ω。
2
三、装置和流程
本实验的流程如图 1 所示,主要有精馏塔、回流分配装置及测控系 统组成。
化工大学精馏实验报告
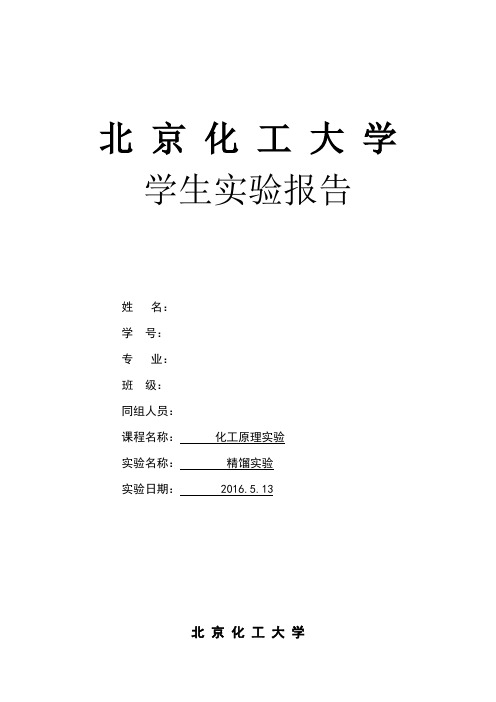
北京化工大学学生实验报告姓名:学号:专业:班级:同组人员:课程名称:化工原理实验实验名称:精馏实验实验日期: 2016.5.13北京化工大学实验五精馏实验摘要:本实验通过测定稳定工作状态下塔顶、塔釜及任意两块塔板的液相折光度,得到该处液相浓度,根据数据绘出x-y图并用图解法求出理论塔板数,从而得到全回流时的全塔效率及单板效率。
通过实验,了解精馏塔工作原理。
关键词:精馏,图解法,理论板数,全塔效率,单板效率。
一、目的及任务①熟悉精馏的工艺流程,掌握精馏实验的操作方法。
②了解板式塔的结构,观察塔板上汽-液接触状况。
③测定全回流时的全塔效率及单塔效率。
④测定部分回流时的全塔效率。
⑤测定全塔的浓度(或温度)分布。
⑥测定塔釜再沸器的沸腾给热系数。
二、基本原理在板式精馏塔中,由塔釜产生的蒸汽沿塔逐板上升与来自塔顶逐板下降的回流液,在塔板上实现多次接触,进行传热与传质,使混合液达到一定程度的分离。
回流是精馏操作得以实现的基础。
塔顶的回流量与采出量之比,称为回流比。
回流比是精馏操作的重要参数之一,其大小影响着精馏操作的分离效果和能耗。
回流比存在两种极限情况:最小回流比和全回流。
若塔在最小回流比下操作,要完成分离任务,则需要无穷多塔板的精馏塔。
当然,这不符合工业实际,所以最小回流比只是一个操作限度。
若操作处于全回流时,既无任何产品采出,也无原料加入,塔顶的冷凝液全部返回塔中,这在生产中午实际意义。
但是由于此时所需理论板数最少,又易于达到稳定,故常在工业装置的开停车、排除故障及科学研究时采用。
实际回流比常取最小回流比的1.2~2.0倍。
在精馏操作中,若回流系统出现故障,操作情况会急剧恶化,分离效果也将变坏。
板效率是体现塔板性能及操作状况的主要参数,有以下两种定义方法。
(1)总板效率EE=N/Ne式中 E——总板效率;N——理论板数(不包括塔釜);Ne——实际板数。
(2)单板效率EmlEml =(xn-1-xn)/(xn-1-xn*)式中 Eml——以液相浓度表示的单板效率;xn ,xn-1——第n块板和第n-1块板的液相浓度;xn*——与第n块板气相浓度相平衡的液相浓度。
精馏实验实验报告3篇
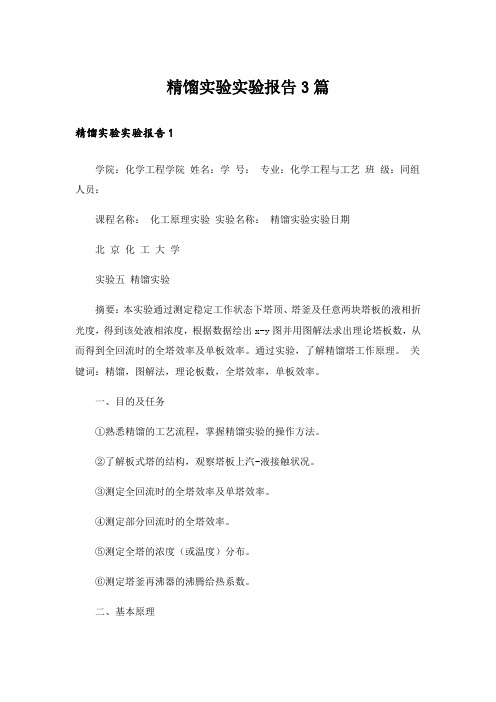
精馏实验实验报告3篇精馏实验实验报告1学院:化学工程学院姓名:学号:专业:化学工程与工艺班级:同组人员:课程名称:化工原理实验实验名称:精馏实验实验日期北京化工大学实验五精馏实验摘要:本实验通过测定稳定工作状态下塔顶、塔釜及任意两块塔板的液相折光度,得到该处液相浓度,根据数据绘出x-y图并用图解法求出理论塔板数,从而得到全回流时的全塔效率及单板效率。
通过实验,了解精馏塔工作原理。
关键词:精馏,图解法,理论板数,全塔效率,单板效率。
一、目的及任务①熟悉精馏的工艺流程,掌握精馏实验的操作方法。
②了解板式塔的结构,观察塔板上汽-液接触状况。
③测定全回流时的全塔效率及单塔效率。
④测定部分回流时的全塔效率。
⑤测定全塔的浓度(或温度)分布。
⑥测定塔釜再沸器的沸腾给热系数。
二、基本原理在板式精馏塔中,由塔釜产生的蒸汽沿塔逐板上升与来自塔顶逐板下降的回流液,在塔板上实现多次接触,进行传热与传质,使混合液达到一定程度的分离。
回流是精馏操作得以实现的基础。
塔顶的回流量与采出量之比,称为回流比。
回流比是精馏操作的重要参数之一,其大小影响着精馏操作的分离效果和能耗。
回流比存在两种极限情况:最小回流比和全回流。
若塔在最小回流比下操作,要完成分离任务,则需要无穷多塔板的精馏塔。
当然,这不符合工业实际,所以最小回流比只是一个操作限度。
若操作处于全回流时,既无任何产品采出,也无原料加入,塔顶的冷凝液全部返回塔中,这在生产中午实际意义。
但是由于此时所需理论板数最少,又易于达到稳定,故常在工业装置的开停车、排除故障及科学研究时采用。
实际回流比常取最小回流比的1.2~2.0倍。
在精馏操作中,若回流系统出现故障,操作情况会急剧恶化,分离效果也将变坏。
板效率是体现塔板性能及操作状况的主要参数,有以下两种定义方法。
(1)总板效率EE=N/Ne式中E——总板效率;N——理论板数(不包括塔釜);Ne——实际板数。
(2)单板效率EmlEml=(xn-1-xn)/(xn-1-xn__)式中 Eml——以液相浓度表示的单板效率;xn ,xn-1——第n块板和第n-1块板的液相浓度;xn__——与第n块板气相浓度相平衡的液相浓度。
化工原理精馏实验报告
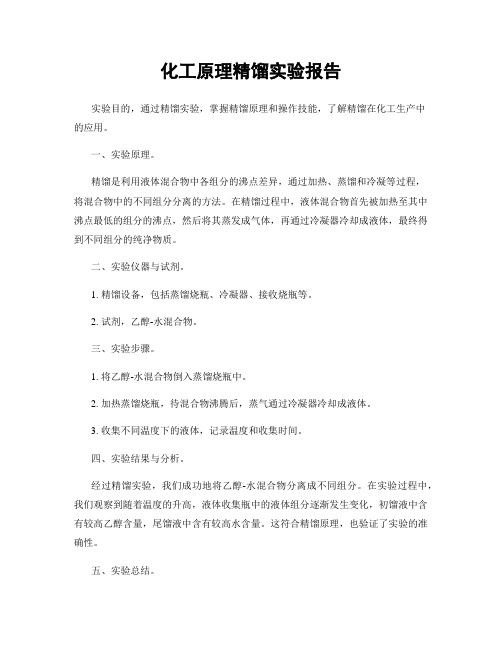
化工原理精馏实验报告实验目的,通过精馏实验,掌握精馏原理和操作技能,了解精馏在化工生产中的应用。
一、实验原理。
精馏是利用液体混合物中各组分的沸点差异,通过加热、蒸馏和冷凝等过程,将混合物中的不同组分分离的方法。
在精馏过程中,液体混合物首先被加热至其中沸点最低的组分的沸点,然后将其蒸发成气体,再通过冷凝器冷却成液体,最终得到不同组分的纯净物质。
二、实验仪器与试剂。
1. 精馏设备,包括蒸馏烧瓶、冷凝器、接收烧瓶等。
2. 试剂,乙醇-水混合物。
三、实验步骤。
1. 将乙醇-水混合物倒入蒸馏烧瓶中。
2. 加热蒸馏烧瓶,待混合物沸腾后,蒸气通过冷凝器冷却成液体。
3. 收集不同温度下的液体,记录温度和收集时间。
四、实验结果与分析。
经过精馏实验,我们成功地将乙醇-水混合物分离成不同组分。
在实验过程中,我们观察到随着温度的升高,液体收集瓶中的液体组分逐渐发生变化,初馏液中含有较高乙醇含量,尾馏液中含有较高水含量。
这符合精馏原理,也验证了实验的准确性。
五、实验总结。
通过本次实验,我们深入了解了精馏原理和操作技能,掌握了精馏在化工生产中的应用。
精馏作为一种重要的分离方法,在化工领域有着广泛的应用,可以有效地提取纯净物质,满足不同生产需求。
六、实验注意事项。
1. 在实验过程中,要注意控制加热温度,避免混合物过热。
2. 实验结束后,要及时清洗和保养实验仪器,确保下次实验的顺利进行。
七、参考文献。
1. 《化工原理与实践》,XXX,XXX出版社,XXXX年。
2. 《化工实验指导》,XXX,XXX出版社,XXXX年。
以上就是本次化工原理精馏实验的实验报告,希望能对大家有所帮助。
精馏实训实验报告

精馏实训实验报告
实验名称:精馏实训实验报告
实验目的:
通过对精馏实训实验的操作和分析,掌握精馏原理和工艺流程,加深对化工分离技术的理解和掌握,提高实验操作技能和实验报告撰写能力。
实验原理:
精馏是一种化学分离技术,基于液体的不同沸点而进行分离。
在精馏过程中,液体混合物被加热,使其产生汽化并进入冷凝器,被冷却成液态,进一步分离成纯液体。
实验步骤:
1. 将实验设备准备妥当,包括精馏塔、加热装置、冷却器等。
2. 准备洗涤瓶和试管,清洗干净后装入待分离的混合物样品。
3. 开始加热,通过不同气化温度和液态沸点,产生不同的沸点温度,使混合物中的组分分离。
4. 将冷却器中的液体收集起来,观察其纯度和色泽等特征。
实验结果:
通过实验,我们得到了两个不同混合物的分离产物。
通过实验后,我们发现其纯度较高、色泽明亮。
实验分析:
精馏是一种高效的化学分离技术,能够实现高纯度物质的分离,广泛应用于制药、化工、精细化工等领域。
实验结果表明,掌握精馏技术和流程对于提高化工实验能力和实践经验有重要作用。
实验结论:
精馏实训实验结果表明,通过掌握精馏技术和流程对于精细化工的研发和生产具有重要意义。
在实验操作和实验报告撰写方面,也有助于提高实验技能和综合能力。
精馏实训的实验报告处理

一、实验目的1. 理解精馏的原理和操作方法。
2. 掌握精馏塔的结构和汽液接触状况。
3. 测定全回流时的全塔效率及单板效率。
4. 测定部分回流时的全塔效率。
5. 测定全塔的浓度分布。
6. 测定塔釜再沸器的沸腾给热系数。
二、实验原理精馏是一种利用不同组分在气液两相间分配系数差异进行分离的单元操作。
在精馏过程中,混合物在塔内通过多次汽液两相间的传质和传热,达到分离的目的。
精馏塔是进行精馏操作的主要设备,主要包括塔体、塔板、再沸器、冷凝器等部分。
三、实验数据1. 塔顶、塔釜及任意两块塔板的液相折光度。
2. 稳定工作状态下塔顶、塔釜及任意两块塔板的液相浓度。
3. 理论塔板数。
4. 全回流时的全塔效率及单板效率。
5. 部分回流时的全塔效率。
6. 全塔的浓度分布。
7. 塔釜再沸器的沸腾给热系数。
四、数据处理1. 根据液相折光度,利用比尔定律计算液相浓度。
比尔定律:A = εlc其中,A为吸光度,ε为摩尔吸光系数,l为光程,c为液相浓度。
2. 利用图解法求出理论塔板数。
将液相浓度与理论塔板数绘制成x-y图,通过拟合直线,得到理论塔板数。
3. 计算全回流时的全塔效率及单板效率。
全塔效率:η_total = (L - D) / L单板效率:η_plate = (L - D) / (L + D)其中,L为回流液量,D为采出液量。
4. 计算部分回流时的全塔效率。
部分回流时的全塔效率:η_part = (L - D) / L5. 测定全塔的浓度分布。
根据实验数据,绘制全塔的浓度分布图。
6. 测定塔釜再沸器的沸腾给热系数。
根据实验数据,计算塔釜再沸器的沸腾给热系数。
五、结果与分析1. 全回流时的全塔效率及单板效率较高,说明精馏塔的分离效果较好。
2. 部分回流时的全塔效率较全回流时有所降低,但仍在可接受范围内。
3. 全塔的浓度分布均匀,说明精馏过程稳定。
4. 塔釜再沸器的沸腾给热系数较大,说明再沸器传热效率较高。
六、结论通过本次精馏实训,我们掌握了精馏的原理和操作方法,了解了精馏塔的结构和汽液接触状况。
实训报告总结化学精馏
#### 一、实训背景化学精馏作为化工生产中的一种重要单元操作,在石油、化工、医药等领域具有广泛的应用。
为了深入了解化学精馏的原理、过程及操作方法,我们进行了化学精馏实训。
通过本次实训,我们掌握了化学精馏的基本操作技能,加深了对化工生产过程的认知。
#### 二、实训目的1. 理解化学精馏的原理和过程;2. 掌握化学精馏设备的基本操作方法;3. 培养实际操作能力,提高安全意识;4. 增强团队协作能力,提高沟通协调能力。
#### 三、实训内容本次实训主要包括以下内容:1. 化学精馏原理及过程;2. 化学精馏设备介绍;3. 化学精馏操作步骤;4. 化学精馏异常处理及安全注意事项。
#### 四、实训过程1. 理论学习:首先,我们对化学精馏的原理、过程及设备进行了系统学习,了解了精馏的基本概念、操作原理、设备结构及操作方法。
2. 设备参观:随后,我们参观了实训现场,实地了解了精馏塔、冷凝器、再沸器等设备的结构及工作原理。
3. 操作实践:在理论学习和设备参观的基础上,我们开始进行化学精馏操作实践。
具体步骤如下:a. 检查设备状态,确保设备完好;b. 启动设备,进行冷态开车;c. 进料,调整塔内温度、压力等参数;d. 调整回流比,控制塔顶、塔底产品纯度;e. 观察设备运行情况,发现异常及时处理。
4. 异常处理:在实训过程中,我们遇到了一些异常情况,如塔内温度、压力波动等。
通过查阅资料和请教老师,我们学会了如何处理这些异常情况。
5. 总结与反思:实训结束后,我们对本次实训进行了总结和反思,分析了操作过程中存在的问题,并提出了改进措施。
#### 五、实训收获1. 理论知识的巩固:通过本次实训,我们对化学精馏的原理、过程及设备有了更深入的了解,为今后从事相关工作打下了坚实基础。
2. 实际操作能力的提高:在实训过程中,我们掌握了化学精馏的基本操作方法,提高了实际操作能力。
3. 安全意识的增强:通过实训,我们认识到化工生产过程中的安全重要性,增强了安全意识。
化工原理精馏实验 北京化工大学
化工原理实验精馏实验报告实验日期:2014.5.5一、实验目的1、了解筛板式精馏塔的结构,学习数字显示仪表的原理及使用。
2、学习筛板式精馏塔的操作方法,观察汽液两相接触状况的变化。
3、测定在全回流时精馏塔总板效率,分析汽液接触状况对总板效率的影响。
4*、测定在全回流时精馏塔的单板效率。
分析汽液接触状况对单板效率的影响。
5*、测定部分回流时的总板效率,分析气液接触状况对总板效率的影响。
6*、测定精馏塔在全回流下塔体浓度(温度)分布。
带*项为教学大纲要求之外项目。
二、实验原理:在精馏过程中,由塔釜产生的蒸汽沿塔逐板上升与来自塔顶逐板下降的回流液在塔板上多次部分汽化部分冷凝,进行传热与传质,使混合液达到一定程度的分离。
回流是精馏操作的必要条件,塔顶的回流量与采出量之比称为回流比。
回流比是精馏操作的主要参数,它的大小直接影响精馏操作的分离效果和能耗。
若塔在最小回流比下操作,要完成分离任务,则需要无穷多块塔板,在工业上是不可行的。
若在全回流下操作,既无任何产品的采出,也无任何原料的加入,塔顶的冷凝液全部返回到塔中,这在生产中无任何意义。
但是,由于此时所需理论板数最少,易于达到稳定,故常在科学研究及工业装置的开停车及排除故障时采用。
通常回流比取最小回流比的1.2~2.0倍。
1.塔板效率板式精馏塔中汽液两相在各塔板上相互接触而发生传质作用,由于接触时间短暂和不够充分,并且汽相上升也有一些雾沫夹带,因此其传质效率总不会达到理论板效果。
通常用塔板效率来表示塔板上传质的完善程度。
塔板效率是体现塔板性能及操作状况的主要参数。
影响塔板效率的因素很多,大致归纳为:流体的物理性质(如粘度、密度、相对挥发度和表面张力等)塔板结构以及操作条件等,由于影响塔板效率的因素相当复杂,目前仍以实验的方法测定。
a. 总板效率(或全塔的效率):反映全塔中各层塔板的平均分离效果,常用于板式塔的设计。
(2-44)式中: ET ——总板效率 NT ——理论板数 NP ——实际板数全回流操作时理论板数可通过逐板计算或利用汽液平衡数据通过图解法求出。
精馏实验报告范文
精馏实验报告范文一、实验目的1.理解精馏原理及应用;2.熟悉精馏实验操作;3.掌握精馏实验装置的搭建和使用;4.学习通过精馏分离混合液。
二、实验原理精馏是一种用于分离液体混合物的方法,通过利用混合物中各组分的沸点差异,将其中的单一组分分离出来。
其中关键的装置是精馏柱,其作用是提供充足的接触面积和良好的乘流,从而实现物质的分离。
在精馏柱中,液体混合物被加热,其中的易挥发组分首先蒸发,进入精馏柱上部,经过冷凝器后再次变成液体,流入收集容器。
随着加热的继续,液体混合物逐渐蒸发,但易挥发组分的分馏效果更好,因而净水汽的组分逐渐富集。
三、实验步骤1.连接实验装置:将冷凝器与精馏柱相连接,再将精馏柱连接到加热装置上;2.添加混合液:在烧杯中加入适量混合液,将其倒入精馏柱中;3.初次加热:打开加热装置,缓慢增加温度直到混合液开始沸腾;4.收集馏分:在冷凝器冷却液的作用下,挥发的易挥发组分冷凝成液体,流入收集容器;5.蒸馏过程:随着温度的继续升高,不同组分挥发并冷凝的次序不同,不同组分的纯度也不同,根据纯度要求及实验目的,可以适时更换收集容器。
四、实验装置与材料1.实验烧杯:用于装载混合液;2.精馏装置:包括精馏柱、冷凝器等,用于实现物质的分馏;3.加热装置:控制温度的提高;4.收集容器:用于收集不同组分的馏分。
五、实验结果及分析我们在实验中选择了乙醇和水的混合液进行精馏实验。
在初次加热时,温度逐渐升高,混合液开始沸腾。
随着温度的继续升高,混合液蒸发并冷凝,乙醇的馏分率逐渐增加。
最后收集到的乙醇纯度较高,符合预期结果。
通过实验,我们可以得出以下结论:1.精馏可以有效地将混合物中的组分分离出来,利用沸点差异实现纯度的提高;2.精馏柱和冷凝器的设计对分馏效果有重要影响,良好的接触面积和乘流可以提高分馏效率;3.实验的操作技巧和对温度的控制也会影响分馏效果。
六、实验总结通过本次精馏实验,我们深入了解了精馏技术的原理和应用,并且通过实际操作掌握了精馏实验的步骤和技巧。
化工原理精馏实验报告
化工原理精馏实验报告
实验目的:掌握化工原理中的精馏操作,并通过实验验证理论知识的正确性。
实验原理:
精馏是一种分离液体混合物组成的常用方法。
精馏通过不同组成的液体在加热的条件下产生蒸汽,然后再在冷凝管中冷凝成液体,最后通过收集液体可以得到不同组成的馏分。
实验仪器:
1. 精馏塔:用于分离混合物。
2. 加热器:提供加热源。
3. 冷凝器:用于冷凝产生的蒸汽。
4. 温度计:用于测量温度。
实验步骤:
1. 将需要进行精馏的混合物加入精馏塔中。
2. 打开加热器,通过加热产生蒸汽。
3. 在冷凝器中冷凝产生的蒸汽,并收集液体。
4. 使用温度计测量液体的沸点。
5. 根据液体的沸点,确定得到的馏分的组成。
实验结果:
在实验过程中,我们成功地通过精馏操作将待分离的混合物分解为不同组成的馏分。
通过温度计测量得到的沸点数据,我们可以精确地确定馏分的组成。
实验结论:
通过这次实验,我们掌握了化工原理中的精馏操作,并验证了理论知识的正确性。
精馏是一种常用的分离液体混合物的方法,在工业生产中有着广泛的应用。
掌握了精馏操作,有助于我们理解和解决化工过程中的实际问题。
- 1、下载文档前请自行甄别文档内容的完整性,平台不提供额外的编辑、内容补充、找答案等附加服务。
- 2、"仅部分预览"的文档,不可在线预览部分如存在完整性等问题,可反馈申请退款(可完整预览的文档不适用该条件!)。
- 3、如文档侵犯您的权益,请联系客服反馈,我们会尽快为您处理(人工客服工作时间:9:00-18:30)。
化工大学精馏实验报告 Company number:【0089WT-8898YT-W8CCB-BUUT-202108】北 京 化 工 大 学 化 工 原 理 实 验 告: : : :: :实验名称 班级 姓名 学号 同组成员 实验日期 精馏实验实验日期精馏实验一、实验目的1、熟悉填料塔的构造与操作;2、熟悉精馏的工艺流程,掌握精馏实验的操作方法;3、了解板式精馏塔的结构,观察塔板上汽液接触状况;4、掌握液相体积总传质系数Ka的测定方法并分析影响因素x5、测定全回流时的全塔效率及单板效率;6、测量部分回流时的全塔效率和单板效率二、实验原理在板式精馏塔中,混合液的蒸汽逐板上升,回流液逐板下降,气液两相在塔板上接触,实现传质、传热过程而达到分离的目的。
如果在每层塔板上,上升的蒸汽与下降的液体处于平衡状态,则该塔板称之为理论塔板。
然而在实际操做过程中由于接触时间有限,气液两相不可能达到平衡,即实际塔板的分离效果达不到一块理论塔板的作用。
因此,完成一定的分离任务,精馏塔所需的实际塔板数总是比理论塔板数多。
回流是精馏操作得以实现的基础。
塔顶的回流量与采出量之比,称为回流比。
回流比是精馏操作的重要参数之一,其大小影响着精馏操作的分离效果和能耗。
回流比存在两种极限情况:最小回流比和全回流。
若塔在最小回流比下操作,要完成分离任务,则需要有无穷多块板的精馏塔。
这在工业上是不可行的,所以最小回流比只是一个操作限度。
若在全回流下操作,既无任何产品采出,也无原料加入,塔顶的冷凝液全部返回塔中,这在生产中无实验意义。
实际回流比常取最小回流比的~倍。
本实验处于全回流情况下,既无任何产品采出,又无原料加入,此时所需理论板最少,又易于达到稳定,可以很好的分析精馏塔的性能。
影响塔板效率的因素很多,大致可归结为:流体的物理性质(如粘度、密度、相对挥发度和表面张力等)、塔板结构以及塔的操作条件等。
由于影响塔板效率的因素相当复杂,目前塔板效率仍以实验测定给出。
板效率是体现塔板性能及操作状况的主要参数,有两种定义方法。
(1)总板效率E式中:E——总板效率;N——理论板数(不包括塔釜);N——实际板数e(2)单板效率Eml式中:E——以液相浓度表示的单板效率;mlx,1n x ——第n块板和第n-1块板的液相浓度;n*x——与第n块板气相浓度相平衡的液相浓度。
n总板效率与单板效率的数值通常由实验测定。
单板效率是评价塔板性能优劣的重要数据。
物系性质、板型及操作负荷是影响单板效率的重要参数。
当物系与板型确定后,可通过改变气液负荷达到最高的板效率;对于不同的板型,可以在保持相同的物系及操作条件下,测定其单板效率,以评价其性能的优劣。
总板效率反映全塔各塔板的平均分离效果,常用于板式塔设计中。
实验所选用的体系是乙醇—正丙醇,这两种物质的折射率存在差异,且其混合物的质量分数与折射率有良好的线性关系,通过使用阿贝折光仪来分析料液的折射率,从而得到浓度。
若改变塔釜再沸器中电加热器的电压,塔内上升蒸汽量将会改变,同时,塔釜再沸器电热器表面得温度将发生改变,其沸腾给热系数也将发生变化,从而可以得到沸腾给热系数与加热量的关系。
由牛顿冷却定律,可知式中Q——加热量,kW;α——沸腾给热系数,kW/(m2·K)A——传热面积,m2t∆——加热器表面与温度主体温度之差,℃。
m若加热器的壁面温度为t s,塔釜内液体的主体温度为t w,则上式可改写为由于塔釜再沸器为直接电加热,则其加热量Q为式中:U——电加热器的加热电压,V;R——电加热器的电阻,Ω(3)根据进料热状态参数作q线,q线方程:——进料液组成(摩尔分数);式中:xfq——进料热状态参数。
式中:C——定性温度下进料液的平均比热,(kJkmol-1℃-1)p——进料温度,℃;TfT——进料泡点,℃;s——进料的千摩尔气化潜热,(kJ/kmol);rc(4)由塔底残液浓度X W垂线与平衡线的交点,精馏段操作线与q线交点的连线作提馏段操作线。
(5)图解法求出理论塔板数。
三、实验流程1、实验装置本实验的流程如图所示,主要由精馏塔、回流分配装置及测控系统组成。
1、配料罐2、配料罐放空阀3、循环泵4、进料罐5、进料罐放空阀6、进料泵7、进料旁路阀8、进料流量计9、快速进料阀10、进料口位置阀11、玻璃塔节12、塔釜加热器13、塔釜液位计14、塔釜出料阀15、塔釜冷却器16、出料泵17、快速出料阀18、π型液位控制管19、回流比分配器20、塔顶冷凝器21、塔顶放空阀22、冷却水流量计2、设备参数(1)精馏塔精馏塔为筛板塔,全塔共8块塔板,塔身的结构尺寸为:塔径φ(57×)mm,塔板间距80mm:溢流管截面积,溢流堰高12mm,底隙高度6mm;每块塔板开有43个直径为的小孔,正三角形排列,孔间距为6mm。
为了便于观察塔板上的汽—液接触情况,塔身设有一节玻璃视盅,在第1~6块塔板上均有液相取样口。
蒸馏釜尺寸为φ108mm×4mm×400mm。
塔釜装有液位计、电加热器()、控温电加热器(200W)、温度计接口、测压口和取样口,分别用于观察釜内液面高度,加热料液,控制电加热量,测量塔釜温度,测量塔顶与塔釜的压差和塔釜液取样。
由于本实验所取试样为塔釜液相物料,故塔釜可视为一块理论板。
塔顶冷凝器为一蛇管式换热器,换热面积,管外走蒸汽,管内走冷却水。
(2)回流分配装置分配装置由回流分配器与控制器组成。
控制器由控制仪表和电磁线圈构成。
回流分配器由玻璃制成,它由一个入口管、两个出口管及引流棒组成。
两个出口管分别用于回流和采出。
引流棒为一根φ4mm的玻璃棒,内部装有铁芯,塔顶冷凝器中的冷凝液顺着引流棒流下,在控制器的控制下实现塔顶冷凝器的回流或采出操作。
即当控制器电路接通后,电磁线圈将引流棒吸起,操作处于采出状态;当控制器电路断路时,电磁线圈不工作,引流棒自然下垂,操作处于回流状态。
此回流分配器既可通过控制器实现手动控制,也可通过计算机实现自动控制。
(3)测控系统在本试验中,利用人工智能仪表分别测定塔顶温度、塔釜温度、塔身伴热温度、塔釜加热温度、全塔压降、加热电压、进料温度及回流比等参数,该系统的引入,不仅使实验更为简便、快捷,又可实现计算机在线数据采集与控制。
(4)物料浓度分析本实验所选用的体系为乙醇-正丙醇,由于这两种物质的折色率存在差异,且其混合物的质量分数与折色率有良好的线性关系,故可通过阿贝折光仪分析液料的折色率,从而得到浓度。
这种测定方法的特点是方便快捷、操作简单,但精度稍低;若要实现高精度的测量,可利用气相色谱进行浓度分析。
四、实验操作1、配制原料。
将乙醇、正丙醇按体积比1:3放入1罐中,开3泵混匀,送入4罐。
2、塔釜进来斗。
开6泵和5、9、10阀门,进料占液位计高度4/5左右,关闭6泵和上述阀门。
3、全回流操作1)开塔顶放空阀门21,塔釜抽取样品,用阿贝折光仪测原始组成n d;2)按塔釜加热“手动控制”绿色按钮,调加热电压120V,开冷却水min;3)使用新针筒取样纯乙醇、正丙醇,测40°C时折光率,确定方程参数a、b;4)发现回流比分配器中有液体回流后,调整到最佳电压(70~110V),稳定10分钟;5)反复推、拉取样器,抽取热样品,注意全针筒替换,正确使用折光仪测折光率;4、部分回流操作(全回流稳定10分钟后进行)1)设定回流比为2、3或4并运行,根据泡沫高度等调节至合适的加热电压;2)开塔釜出料阀14,设定塔釜液位控制高度(修改SV值=刻度线时的PV值);3)开进来斗阀10,再开进料泵6,结合旁路阀7调整进料量约40ml/min;4)开进料罐底部阀门,用瓶盖取样测量进料组成n d;5)检查阀门5打开,稳定15分钟,顶、釜及塔板取样分析同上;5、实验结束先关进料泵6,再关进来斗阀10、釜出来斗阀14,然后停塔釜加热、回流比仪表。
10分钟后关阀门21,停冷却水,关闭阀门2和5等。
注意事项:1)塔釜加热启动后,冷却水一定要接通,约min;2)取样后针头不拔出,只拿走针筒,同时放上一个全针筒;3)使用同一台折光仪,样品稳定10s再读数,镜头纸用完要展开,干后继续用;4)取样后多余物料打入配料罐1内,检查阀门2打开;5)部分回流操作时检查关闭快速进料阀门9;6)塔釜液位不要低于液位计高度1/3,以免烧坏加热器;7)实验过程等待系统稳定时,可观察冷模板式塔的各种现象。
五、数据处理1.W乙醇=a+b×n d中参数a、b的确定表1、40℃下W乙醇与n d关系表求解方程式{1=a+b×0=a+b×1.3794,可得{b=−41.8410。
2. 全回流实验1) 精馏塔中各板上的流液的折光率和易挥发组分的含量表2、全回流实验原始数据塔顶平均温度 t 顶=79.1+79.12=79.1℃塔釜平均温度 t 釜=91.0+91.02=91.0℃全塔压降 ?P =1.12+1.122=1.12kPa以第四块板数据为例进行计算: 平均折光率 n d,顶=n d,顶,1+n d,顶,22=1.3661+1.36582=1.3660乙醇质量分数 W =a +b ×n d,顶=57.7155−41.8410×1.3660=0.5607乙醇摩尔分数 X =WM 乙醇WM乙醇+1−WM正丙醇=0.5607460.560746+1−0.560760=0.6247⁄⁄则可得下表表3、各板上液体的折光率和摩尔分率2) 乙醇—正丙醇平衡关系表4、 乙醇—正丙醇平衡数据表(P=)由上表数据可得下图3) 图解法求理论板数根据表3和表4的数据可得下图4) 全塔效率和单板效率计算由图解法可知,理论塔板数为5块板(包括塔釜),故理论板数N== 因此全塔效率为E =N ×100%=3.4×100%=42.5% 由相平衡关系可得 1(1)x y x αα=-- ,故 1111y x ααα-=⨯+根据表4的数据做1/y 与1/x 关系图如下 由图可知斜率K =1α=0.5063,因此α= 全回流操作线方程为 1y n n x +=X 5∗=X 4α−(α−1)X 4=0.62471.9751−(1.9751−1)×0.6247=0.45第5块板的单板效率E ml,5=X 4−X 545∗=0.6247−0.5825=24% 故,总板效率 E =NNe ×100%=3.48×100%=42.5%单板效率 E ml,5=X 4−X 5X 4−X 5∗=0.6247−0.58250.6274−0.45=24%由以上可得下表表6、 全回流操作实验结果六、 操作流程七、误差分析1、全回流操作时单板效率偏低,可能是以下原因造成的:1)塔板面积有限;2)气液在塔板上的接触时间不够充分,使得气液两相在达到平衡前就相互分离;3)气速偏高,液沫夹带量大,或液量偏大,气泡夹带量大,都对传质不利;2、全塔效率偏低,可能是以下原因造成的:全塔效率是板式塔分离性能的综合量度,不单与板效率、点效率有关而且与板效率随组成的变化有关。