精益生产系统培训
精益生产培训心得体会
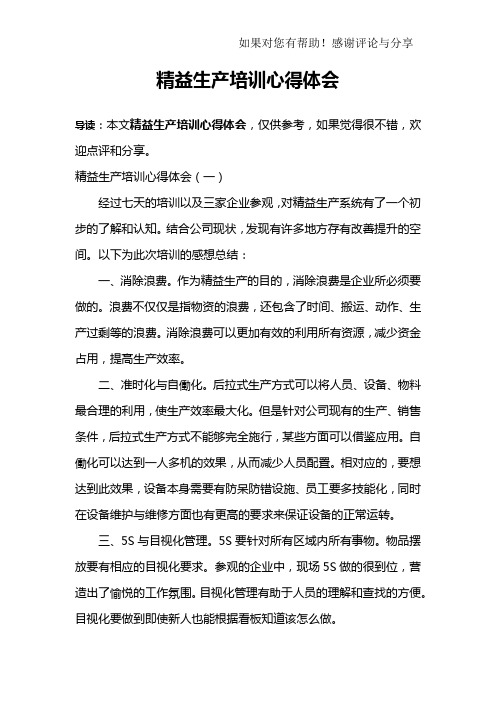
精益生产培训心得体会导读:本文精益生产培训心得体会,仅供参考,如果觉得很不错,欢迎点评和分享。
精益生产培训心得体会(一)经过七天的培训以及三家企业参观,对精益生产系统有了一个初步的了解和认知。
结合公司现状,发现有许多地方存有改善提升的空间。
以下为此次培训的感想总结:一、消除浪费。
作为精益生产的目的,消除浪费是企业所必须要做的。
浪费不仅仅是指物资的浪费,还包含了时间、搬运、动作、生产过剩等的浪费。
消除浪费可以更加有效的利用所有资源,减少资金占用,提高生产效率。
二、准时化与自働化。
后拉式生产方式可以将人员、设备、物料最合理的利用,使生产效率最大化。
但是针对公司现有的生产、销售条件,后拉式生产方式不能够完全施行,某些方面可以借鉴应用。
自働化可以达到一人多机的效果,从而减少人员配置。
相对应的,要想达到此效果,设备本身需要有防呆防错设施、员工要多技能化,同时在设备维护与维修方面也有更高的要求来保证设备的正常运转。
三、5S与目视化管理。
5S要针对所有区域内所有事物。
物品摆放要有相应的目视化要求。
参观的企业中,现场5S做的很到位,营造出了愉悦的工作氛围。
目视化管理有助于人员的理解和查找的方便。
目视化要做到即使新人也能根据看板知道该怎么做。
四、TPM.推行TPM要改变现有的管理方式,对设备点检及保养方面的要求要更加的细化,同时要有相应的目视化管理以便于操作者对设备进行维护。
此外,培训、教育不可缺少。
五、品质管理。
问题处理要现场、现地、现物,按照PDCA四阶段、八步骤进行,并持续改进,以零缺陷为最终目标。
解决问题时要找到问题的根本原因再解决。
六、标准作业。
标准作业包含生产节拍、作业顺序和标准手持量三个要素。
进行标准作业有相应的前提条件:设备稳定、品质稳定、人员多能工、动作可循环。
理想状态下的标准作业可以将人员效率、设备使用发挥到极致,最大限度的提高生产效率。
现有的工艺要求考虑到了单件产品的生产效率,但并没有将连续生产的效率最大化。
精益生产培训资料(好)

幻灯片1Lean Thinking and Lean Manufacturing System 精益思维和精益生产系统Starting with Toyota in the late 50’s and catching on in the mid – 80’s in the reminder of the industrial world, Lean Manufacturing has become a key strategy for manufacturers起源于20世纪50年代丰田汽车公司,而在80年代中期被欧美企业纷纷采用。
随着微利时代的来临,精益生产模式成为企业竞争的有力武器幻灯片2Marketing Competition and Globalization市场竞争及全球化●Shorter lead time and on time delivery●快速并准时交货●Grow the mix,special configurations●需求品种增加,特殊定制●Maintain / improve quality and reduce price●不断改进质量及降低销售价格●Total life cycle of product becoming shorter and shorter ●产品的生命周期越来越短●No boundary,business globalize village●无国界,业务“地球村”●幻灯片3Marketing Competition and Globalization市场竞争及全球化幻灯片4Lean Thinking and Lean Manufacturing System 精益思维和精益生产系统The are two ways to think about the relationship of Price, Cost and Profit在价格,成本和利润的关系中,有两种不同的思考方法:1。
精益生产系统培训课件04-拉动原则

4. 看板卡片在车间按照不同的零件种类 挂在装满的箱子上
看板零件的堆放空间
5. 托盘/小车满载着箱子和看板卡被运到 下一道工序
Legende
Material KANBAN-Karte
YT-ZRPS Organisation
ZRPS 深入培训-拉动原则
13 / 17 页
看板的游戏规则
遵守看板规则是发挥看板系统功能的前提。
Baut ei l :
fertiges Gelenk 030.160.007.515
Produktionsort:
Bereich:
Endmont age
Z I E L:
Lager or t :
Fertigw .-Lager
Pr odukt i onsmi t t el :
Hochrainer 107337
YT-ZRPS Organisation
低库存 – 高灵活性
ZRPS 深入培训-拉动原则
5 / 17 页
生产是自我调控的
之前:
不同的领域 控制流程
之后:
生产自我调控
PPS 生产品种计划
数量计划
PPS 程序计划
数量计划
生产链中只有最后一道工序 是被计划和控制的.
时间 和操作步骤计划 在物理层次上的细节控制
9 / 17 页
看板* 作为 信息载体
*日文: Karte卡片
联系超级市场及工人的信息载体 看板 看板几种可能的表现形式,例如:
看板箱 看板箱空了之后又回到上一道工序装满
看板卡 看板卡在看板箱被取出第一个零件后被送回
电子看板 例如扫描器在看板箱被取走后,信息被传递到前一道工序。
…
YT-ZRPS Organisation
精益生产培训TPM

精益生产培训TPM概述精益生产,全称为精益生产管理,是一种基于实践的、持续改进的生产管理方法,旨在提高生产效率、降低成本、提高质量、减少浪费。
它结合了精益生产和卓越制造的理念和工具,采用系统化、综合性的方法,通过改进生产流程、提高设备效率、优化原材料利用率等手段,从而实现生产线的优化和整体效能的提升。
TPM,即全面生产管理(Total Productive Maintenance),是精益生产领域的一个关键概念和工具。
它强调通过系统化的设备维护和保养,提高设备可靠性和稳定性,减少停机时间,提高生产效率。
TPM包括预防性维护、设备维护、设备管理和设备改善等方面的内容,它通过全员参与、团队合作和持续改进的方式,实现生产设备的最大化利用率和生产线的优化。
精益生产培训TPM的目标精益生产培训TPM旨在通过培养员工的精益思维和技能,提升生产线的效率、质量和可靠性。
具体目标包括:1.培养员工的精益生产意识:使员工了解精益生产的核心理念和原则,培养他们对浪费的敏感性和改进的意识。
2.提高员工的技能和能力:通过培训和学习,提高员工在设备维护、设备管理和设备改善等方面的技能和能力,让他们能够主动参与到生产线的优化中。
3.优化生产流程:通过培训和实践,帮助员工识别和消除生产过程中的浪费和瓶颈,优化生产流程,提高生产效率。
4.改进设备可靠性和稳定性:通过培训和实践,帮助员工了解设备维护和保养的重要性,掌握设备故障分析和预防措施,提高设备可靠性和稳定性。
5.培养团队合作和沟通能力:通过培训和团队活动,培养员工的团队合作和沟通能力,使他们能够有效地与他人合作,推动改进的实施。
培训内容和方法精益生产培训TPM的内容包括但不限于以下几个方面:1.精益生产理念和原则:通过讲座和案例分析,介绍精益生产的核心理念和原则,让员工理解精益生产的价值和意义。
2.浪费识别和改进:通过实践活动,帮助员工识别生产过程中的各种浪费,如等待、过程瑕疵、运输、过度加工等,提出改进措施。
精益生产管理培训资料

KINSNA
精益生产的两大支柱
准时化:在必要的时候,生产必要数量的必要产品, 英文全称 “JUST IN TIME”, 简称“JIT”。
----均衡生产 ----单个流生产 ----标准化作业 ----拉动式 ----看板应用
KINSNA
精益生产的两大支柱
自动化:动字带人字旁的自动化,即是“机器被赋予 了人的智慧”,起到杜绝过量制造和生产不合格品这种
KINSNA
为何要实施精益生产
3.增加现金的周转 -原材料 -在制品 -成品
KINSNA
为何要实施精益生产
4.增加库存周转率 -测定库存轮流频率的财务数据 -对现有资金周转有直接影响 -对制造交货期有影响 库存周转率=销售标准成本/平均现有库存 原来周转率=35000/9000=3.8 精益生产后周转率=35000/3000=11.6
KINSNA
在越来越多的其他行业的企业中,精益管理的 生产组织方法、人员管理方法以及企业协作方法 都被广泛地吸收与推广 丰田公司开创精益生产的同时,日本独特的 文化氛围也促进精益生产的产生。强调集体与协 作的东方文化,为精益管理的人力管理提供了一 个全新的思维角度。符合这种追求集体与协调意 识的我国企业文化,更应用精益思想管理企业。 目前全球众多的发达国家都在采用精益生产 和六个西格玛的管理思想来降低成本,提高竞争能 力,满足顾客的要求.
KINSNA
中国现将成为世界制造业的重心。面对资金雄厚、生 产条件先进且早已形成了自己一套管理体系的世界跨
国集团和国内同行业的佼佼者,我们如何应对?面对
竞争日益激烈的市场,困扰企业的种种不良现象,已 成为阻碍企业生存和发展的致命因素。但同样这些现 象也是使我们企业痛下决心,进行生产管理的过程控 制、提高制造系统的柔性、提升企业市场反应速度。
生产车间精益培训计划方案
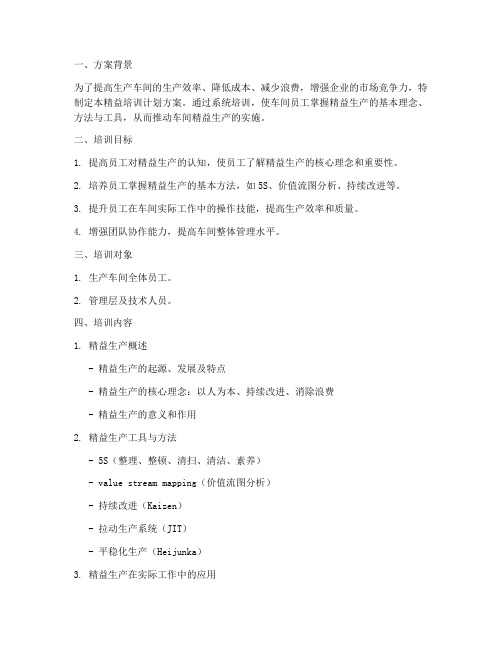
一、方案背景为了提高生产车间的生产效率、降低成本、减少浪费,增强企业的市场竞争力,特制定本精益培训计划方案。
通过系统培训,使车间员工掌握精益生产的基本理念、方法与工具,从而推动车间精益生产的实施。
二、培训目标1. 提高员工对精益生产的认知,使员工了解精益生产的核心理念和重要性。
2. 培养员工掌握精益生产的基本方法,如5S、价值流图分析、持续改进等。
3. 提升员工在车间实际工作中的操作技能,提高生产效率和质量。
4. 增强团队协作能力,提高车间整体管理水平。
三、培训对象1. 生产车间全体员工。
2. 管理层及技术人员。
四、培训内容1. 精益生产概述- 精益生产的起源、发展及特点- 精益生产的核心理念:以人为本、持续改进、消除浪费- 精益生产的意义和作用2. 精益生产工具与方法- 5S(整理、整顿、清扫、清洁、素养)- value stream mapping(价值流图分析)- 持续改进(Kaizen)- 拉动生产系统(JIT)- 平稳化生产(Heijunka)3. 精益生产在实际工作中的应用- 车间布局优化- 生产流程优化- 设备维护与保养- 员工培训与激励4. 精益生产案例分享- 国内外优秀企业精益生产案例- 企业内部成功实施精益生产的案例五、培训方式1. 理论讲解:邀请精益生产专家进行授课,使员工对精益生产有全面了解。
2. 案例分析:通过实际案例,让员工学会运用精益生产工具与方法解决实际问题。
3. 实地参观:组织员工参观精益生产优秀企业,直观感受精益生产的魅力。
4. 实操演练:设置模拟车间,让员工在实际操作中掌握精益生产技能。
5. 小组讨论:分组讨论,激发员工思维,共同解决实际问题。
六、培训时间与周期1. 培训时间:分为两个阶段,第一阶段为理论培训,第二阶段为实操培训。
2. 培训周期:第一阶段为2周,第二阶段为4周。
七、培训效果评估1. 培训结束后,对员工进行考核,检验培训效果。
2. 对培训过程中存在的问题进行总结,及时调整培训方案。
CL精益生产培训上

111.7
12.1
自动化(组装)
1.7
1.2
3.1
项目
地区
观念比较
构筑精益企业之屋
以斯密的劳动分工理论、福特的流水线和斯隆的管理创新为代表的第一次工业革命,效率的极大提高改变了工业文明的进程以丰田生产系统发展而来的精益生产方式冲击了传统的、依赖大批量生产提高效率及劳动分工的观念,代表了第二次工业革命的开始
Life Cycle Cost In Different System
不同系统中的成本
精益生产系统之产品生命周期成本
大规模生产模式下的产品生命周期成本
Lean Manufacturing And Automation精益生产与自动化
投资
直接员工
自动化程度
精益思想:关注流程
企业的生产流程包括:订单处理、物料计划、采购下单、供应商备料、运输、来料检验、存储、搬运、加工、检验和返工、过程等待、成品库存、发运、货款回收等环节
Focused on total elimination of wasteOngoing efforts to improve Quality, Productivity, and ResponsivenessRecognition of employee abilities消除浪费不断改进员工参与
2
生产管理的任务
Safety 安全、士气
Quality 质量
Delivery 交货
Cost 成本
SQDC
生产管理者的职责
组长:质量及不合格品的注意;生产线 停线的责任领班:生产力改进;成本降低主管:生产控制,作业标准,质量控制, 培 训,安全,经理:目标方针,资源配备,系统优化
Lean Thinking and Lean Manufacturing System 精益思维和精益生产系统
精益生产培训心得体会(精选9篇)
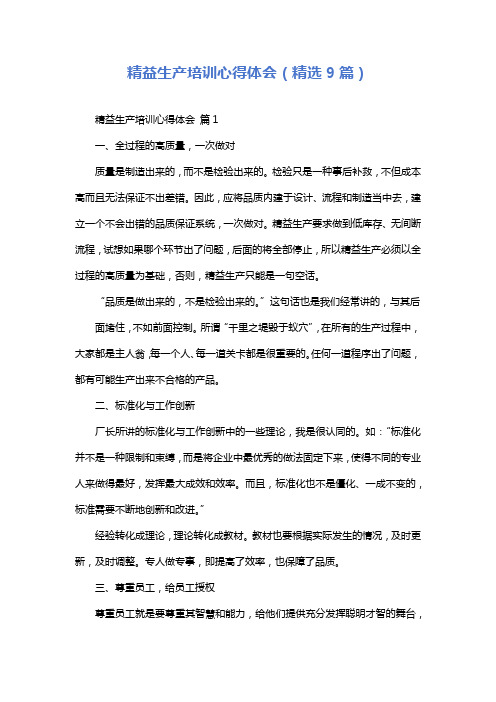
精益生产培训心得体会(精选9篇)精益生产培训心得体会篇1一、全过程的高质量,一次做对质量是制造出来的,而不是检验出来的。
检验只是一种事后补救,不但成本高而且无法保证不出差错。
因此,应将品质内建于设计、流程和制造当中去,建立一个不会出错的品质保证系统,一次做对。
精益生产要求做到低库存、无间断流程,试想如果哪个环节出了问题,后面的将全部停止,所以精益生产必须以全过程的高质量为基础,否则,精益生产只能是一句空话。
“品质是做出来的,不是检验出来的。
”这句话也是我们经常讲的,与其后面堵住,不如前面控制。
所谓“千里之堤毁于蚁穴”,在所有的生产过程中,大家都是主人翁,每一个人、每一道关卡都是很重要的。
任何一道程序出了问题,都有可能生产出来不合格的产品。
二、标准化与工作创新厂长所讲的标准化与工作创新中的一些理论,我是很认同的。
如:“标准化并不是一种限制和束缚,而是将企业中最优秀的做法固定下来,使得不同的专业人来做得最好,发挥最大成效和效率。
而且,标准化也不是僵化、一成不变的,标准需要不断地创新和改进。
”经验转化成理论,理论转化成教材。
教材也要根据实际发生的情况,及时更新,及时调整。
专人做专事,即提高了效率,也保障了品质。
三、尊重员工,给员工授权尊重员工就是要尊重其智慧和能力,给他们提供充分发挥聪明才智的舞台,为企业也为自己做得更好。
出错一定有其内在的原因,只要找到原因施以对策,下次就不会出现了。
精益的企业雇佣的是“一整个人“,不精益的企业只雇佣了员工的“一双手“。
让员工也把自己的经验,自己的看法讲出来。
也许领导的所作出的决定可能是错的,领导只看到了事情的一面,而未能看到事情的全部。
在碰到问题的时精益生产培训心得体会篇2经过七天的培训以及三家企业参观,对精益生产系统有了一个初步的了解和认知。
结合公司现状,发现有许多地方存有改善提升的空间。
以下为此次培训的感想总结:一、消除浪费作为精益生产的目的,消除浪费是企业所必须要做的。
- 1、下载文档前请自行甄别文档内容的完整性,平台不提供额外的编辑、内容补充、找答案等附加服务。
- 2、"仅部分预览"的文档,不可在线预览部分如存在完整性等问题,可反馈申请退款(可完整预览的文档不适用该条件!)。
- 3、如文档侵犯您的权益,请联系客服反馈,我们会尽快为您处理(人工客服工作时间:9:00-18:30)。
6S
a. 整理(Sort): 去掉不需要的东西 b. 整顿(Set in order): 需要品定点定位放置 c. 清扫(Shine): 创造一个安全、舒适的工作环境 d. 清洁(Standardize): 创造标准的作业程序 e. 素养(Sustain): 自我约束 f. 安全(Safety): 遵守SOE准则
➢ 一种以客户为导向,后拉式派工生产系统
何谓浪费
➢ 工厂内部存在的浪費有
不良品 搬运
动作
不必要之加工
认知断层
等待
制造过早/过剩
库存
为何推行精益生产(1)
A. 高品质 B. 低成本 C. 缩短生产周期 D. 提高生产弹性 E. 互信与尊重
为何要推行精益生产(2)
1. 减少WIP(在制品库存)﹔ 2. 缩短MLT(生产前置时间)﹐目前工厂内讲的MLT是指从裁断开
3. Cycle Time(CT)周期时间﹕一人或一组人在某道工序平均完成一件 产品所花的时间,假如在整个流程中每个作业的周期时间等於TAKT TIME(间隔时间)的话,则生产线不平衡损失为零。
4. Work-in-process(WIP)在制品库存:在制程中拥有附加价值的 原料或半成品的数量。
5. Right First Time(RFT)首次品质通过率﹕产品经过一道或一连串 作业程序后不再需要额外加工手续的比率
精益生产的背景(5)-丰田精实屋意义
1. 稳定:一致且可以预期的生产 2. 安全:无公伤事故,一切以安全为重 3. 平准:平衡的、平准的以及依序的生产 4. 标准化作业:大家同意的现有最佳制造或组装的运作模式 5. 改善:持续的进步 6. 稳定:一致且可以预期的生产 7. 刚好即时:在适当的时间收到正确数量的正确的产品 8. 自动化:人字旁的自动化,意指「有大脑的机器」。 当故障或不良产
生时,机器会自动停止
精益生产背景(6)
➢ 鞋业界又以adidas与Nike开始要求生产工厂推行精益生产
➢ Adidas命名为:Lean ➢ Nike命名(Lean Production)就是消除工厂内部一切不必要的浪费, 以愈少的资源投入而获取更多的利益产出的生产模式。
精益生产衡量指标(2)
1. TAKT TIME(TT)生产时间间隔时间﹕能满足客户需求的每双制造速度 2. Build Customer Schedule(BCS)依客户生产实际达成率﹕满足客
户需求的交货准确率﹐生产线中是指依计划达成率。 3. Value Adding(VA)附加价值﹕任何能转换原料成为顾客愿意花钱支
➢ 一个创造包含更多有价值动作的生产流程 之系统 ➢ 一个更能充分运用人力资源的系统 ➢ 一个能持续改善的系统
精益生产衡量指标(1)
1. Manufacture Lead Time(MLT)生产前置时间:由原物料转换成 最终产品所需的时间,以小时/分钟计算。
2. Process Time(PT)加工时间:制程中一特定流程所花费的时间 (完成一个作业程序所需花的时间),它包括机器作业时(MT)﹐人工 作业时间(HT)与重合时间(OT).
使我们不断生产出更好与之更便宜的产品;标准是必需的,但除非它意 指提升标准化的水准,不然标准化就是句空话!
精益生产的背景(4)-丰田精实屋
目标: 高品质、低成本、最短生产周期
即时 连续流 节拍时间 拉式系统
人字旁的自动化 对不正常状况 给予停机与警示
区分人的工作 现机器的工作
平准化 标准化作业 改善 稳定与安全
精益生产系统
主讲:
主要内容
1. 精益生产的背景 2. 何谓精益生产 3. 为何要推行精益生产 4. 推行精益生产要达到的标准 5. 精益生产衡量指标 6. 推行精益生产之相关工具 7. 推行精益生产技法之阶段
精益生产的背景(1)
福特生产系统
精益生产的背景(2)
➢ 1920年代福特Ford Rouge Complex是拥有全球最佳生产技术的标竿
视觉控制(1)
➢ 视觉控制 1 : 运用工具或图表让现场每一个员工都能清楚地了解整个 生产情形。
➢ Eg. 三色牌看板 --挂在现场每一条生产线上并显示每小时的品质﹑产量 及在制品库存。
品质
产量
在制品库存 绿色:达到或超过目标产能 黄色:略低于目标能;
红色 ﹕大大低于目标产能,需 采取紧急措施﹔
始至成型完成的总时间﹔ 3. 提高生产效率﹔ 4. 在正确时间点上制造出正确产品﹔ 5. 由原来的『推式』改成『拉式』系统﹔ 6. 供应商即时送达和首次来货品质的重要性提升﹔ 7. 对员工授权并从变革成长﹔ 8. 适应市场需求的变化趋势﹐提高企业自身的应变能力。
推行精益生产要达到的标准
A. 连续不断的物流 – 不会因为没有价值的步骤而中断 B. 低库存 – 降低被冻结的资金并减少空间的使用 C. 被授权的员工 – 员工参与决策与进行改善 D. 频繁地补充所需 – 小批量 E. 有弹性的设备 – 适当的机器规模与能符合每日需求的快速转换技术 F. 对问题快速反应 – 系统化解决问题的方法 G. 精实系统是:
➢ 这些技术包含了及时运输和生产
➢ 这些方法被复制到福特在欧洲的其他工厂,稍后,也被用到日本的丰 田车市作为模范。
精益生产的背景(3)-福特的生产哲学
A. 消除浪费:关键在於节省劳动力,以期得到更多的效用和创造更多的价 值。」
B. 运用边连续流的生产模式:主、副流程的同步化 C. 力行品质来自於源头:零不良生产;消除成型线最 后面的品检需求 D. 标准化&持续改善:我们视“取之於公众,用之於公众”为己任,并促
付的活动或作业称称之附加价值,像是高周波、 排版印刷等。 4. Non -value-adding(非附加价值): 任何花费时间和资源但却不增加
产品的价值的作业或活动,例如搬运、等待。 5. Productivity 生产力﹕每人每小时生产双数﹐它可以真实反映生产效
率之高低
推行精益生产相关工具
A. 6S B. 视觉控制 C. Takt Time D. 小组平衡 E. 错误防范 F. 标准作业 G. 看板 H. 一双流 I. 改善 J. 小组管理