板坯连铸机漏钢事故的原因分析及防止 精品
板坯连铸机粘结漏钢的原因分析及预防 刘雷锋

板坯连铸机粘结漏钢的原因分析及预防刘雷锋摘要:随着连铸技术的发展和广泛应用,连铸坯的质量和品质受到了人们的广泛关注,提高连铸坯的质量成为连铸生产中重点关注的问题之一。
连铸过程开始广泛运用于有色金属行业,尤其是铜和铝。
连铸技术迅速发展起来。
本文对此进行了分析研究。
关键词:坯;连铸;连铸工艺连铸漏钢是个常见现象。
钢水在结晶器内形成坯壳,连铸坯出结晶器后,薄弱的坯壳抵抗不住钢水静压力,出现断裂而漏钢。
对于薄板坯连铸来说更易发生漏钢事故。
漏钢对连铸生产危害很大。
即影响了连铸车间的产量,又影响了连铸坯的质量,更危及操作者的安全。
因此,降低薄板坯连铸漏钢率是提高生产效率,提高产量,提高产品质量,降低成本的重要途径。
现对某厂自2008~2013年薄板坯漏钢率进行统计。
2008年漏钢率达0.56%;2009年漏钢率达0.19%;2010年漏钢率达0.19%;2011年漏钢率达0.19%;2012年漏钢率达0.15%;2013年漏钢率达0.07。
1 工艺流程某厂第一钢轧厂工艺流程为:鱼雷罐供应铁水/混铁炉供应铁水→铁水预处理→转炉炼钢→氩站→精炼→薄板坯连铸2 薄板坯漏钢类型某厂薄板坯连铸漏钢主要有:粘结漏钢、裂纹漏钢、卷渣漏钢、开浇漏钢、鼓肚漏钢五个类型。
3 薄板坯漏钢特征、原因及预防措施3.1 粘结漏钢粘结漏钢是指钢水直接与结晶器铜板接触形成粘结点,粘结点处坯壳与结晶器壁之间发生粘结,此处在结晶器振动和拉坯的双重作用下被撕裂,并向下和两侧扩展,形成倒“V”形破裂线,钢水补充后又形成新的粘结点,这一过程反复进行,粘结点随坯壳运动不断下移,此处坯壳较薄,出结晶器后,坯壳不能承受上部钢水的静压力,便会发生漏钢事故。
据统计,粘结漏钢发生率最高,高达50%以上。
(1)铸坯粘结漏钢后特征。
粘结漏钢后铸坯特征。
坯壳呈“V”字型或“倒三角”状,粘结点明显。
(2)粘结漏钢的原因:1)保护渣性能不好。
保护渣在结晶器铜板与凝固坯壳之间起润滑的效果。
方坯连铸漏钢原因及控制措施

方坯连铸漏钢原因及控制措施随着铸造工艺的不断发展,连铸漏钢也越来越常见。
“漏钢”是指新铸件,尤其是连铸生产的铸件,在凝固过程中发生熔点介质损失,导致铸件质量严重损失的现象。
下面一起来介绍连铸漏钢原因及控制措施:一、连铸漏钢的原因1、擦模失效:擦模上不均匀的加热,擦模表面污染,接触夹头失效,都会导致擦模无法有效传热,从而出现漏钢现象。
2、溶解熔点低:金属的溶解能力不佳,无法对熔点介质起到有效的溶解,导致熔液中的金属析出或运动造成液强度减轻,漏出来。
3、连铸工艺失控:铸流过快,加熔温过高或低,注浆缺陷,铸件内部充满气体等操作失误,都会导致漏钢问题发生。
4、工艺板型失控:熔点介质密度不足或对外形尺寸不精确,以及外形板型尺寸分配不合理,都会导致漏钢。
二、连铸漏钢的控制措施1、精心选择工艺板型:要求板型尺寸分配合理,减轻内外形尺寸缺陷,保证熔点介质密度达到要求。
2、控制凝固温度:熔温要按要求降低,较低时保证金属密度,消除凝固时金属内部气体析出,提高液体凝固强度,从而避免漏钢。
3、控制连铸流条状:速度要求标准稳定,铸流周边无屑物,熔点介质体流均匀,防止凝固过程发生变形,防止熔点差异引起的漏钢。
4、做好擦模的质量检查:对于熔温比较低,可以把擦模上的温度控制在10℃以上,采用精度高的擦模,并定期更换夹头,保证擦模的有效性。
5、控制注浆:注浆量要求恒定,注浆温度要按规定进行维护,保持良好的注浆状态。
总之,要想有效抑制连铸漏钢发生,需要严格按照铸造工艺流程,控制铸流和熔温,擦模要按要求维护,并定期检测,保持传热媒介熔点一致,严格控制工艺板型尺寸,保证良好的注浆状态,体现对材料及加工质量的关注。
只有严格控制好上述各个环节,才能解决连铸漏钢问题,保证铸件质量更好的实现。
板坯连铸机漏钢原因分析及控制措施

板坯连铸机漏钢原因分析及控制措施1.操作不当:操作人员操作不规范或经验不足,如操作时间过长、操作不准确等,容易导致板坯连铸机漏钢。
为了避免操作不当导致漏钢,应加强操作人员培训,提高他们的技术水平和操作经验,严格遵循操作规程,并进行必要的考核和监督。
2.连铸结晶器破损:连铸结晶器是冷却板坯的关键部件,如果结晶器破损,冷却水可能会直接进入铸坯中,导致漏钢。
为了避免这种情况,应定期对结晶器进行检查和维修,及时发现并更换破损的部件。
3.气孔:气孔是指铸坯内部存在的空隙,通常由于钢水中的氢气无法完全逸出而形成。
气孔会影响铸坯的质量,导致漏钢。
为了减少气孔,可以采取以下措施:(1)控制钢水的合金成分,控制钢水中的氢含量。
(2)在铸造过程中加入除氧剂,提高钢水中的溶解氧含量,减少气体生成。
(3)合理设计结晶器,使气泡易于从铸坯中升出。
4.结晶器堵塞:连铸结晶器内部可能会堵塞,导致冷却水无法均匀地冷却铸坯,造成漏钢。
为了避免结晶器堵塞,应定期对结晶器进行清洗和维修,保证结晶器内部的冷却水流通畅。
5.铸坯温度过高:铸坯温度过高会导致铸坯内部产生过多的气体,增加气孔的形成,从而引起漏钢。
为了控制铸坯温度,可以在连铸过程中控制冷却水的流量和温度,以达到合理的冷却效果;同时,在连铸过程中加强温度监控,及时调整连铸速度和冷却水的冷却效果。
6.铸模破损:铸模破损会导致铸坯内部形成孔洞和裂缝,导致漏钢。
为了避免铸模破损,应定期进行铸模的检查和维修,及时更换破损的部件。
7.其他原因:除了以上几点外,板坯连铸机漏钢还可能受到其他因素的影响,如连铸设备的老化、设备维护不当等。
为了确保连铸机的正常运行和减少漏钢,应加强设备的维护保养,定期进行设备的检修和更换关键部件。
综上所述,要控制板坯连铸机漏钢,需要从操作规范、设备维护、冷却控制等多个方面着手,以保证连铸过程的正常进行和铸坯质量的提高。
只有在整个生产过程中严格按照操作规程进行操作,定期维护检修设备,并加强钢水质量控制,才能有效控制和减少板坯连铸机漏钢的发生。
厚板坯连铸机漏钢原因分析及预防措施
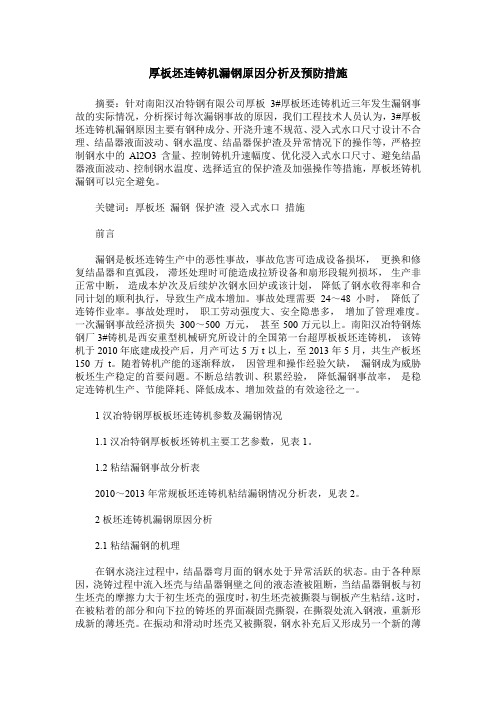
厚板坯连铸机漏钢原因分析及预防措施摘要:针对南阳汉冶特钢有限公司厚板3#厚板坯连铸机近三年发生漏钢事故的实际情况,分析探讨每次漏钢事故的原因,我们工程技术人员认为,3#厚板坯连铸机漏钢原因主要有钢种成分、开浇升速不规范、浸入式水口尺寸设计不合理、结晶器液面波动、钢水温度、结晶器保护渣及异常情况下的操作等,严格控制钢水中的Al2O3含量、控制铸机升速幅度、优化浸入式水口尺寸、避免结晶器液面波动、控制钢水温度、选择适宜的保护渣及加强操作等措施,厚板坯铸机漏钢可以完全避免。
关键词:厚板坯漏钢保护渣浸入式水口措施前言漏钢是板坯连铸生产中的恶性事故,事故危害可造成设备损坏,更换和修复结晶器和直弧段,滞坯处理时可能造成拉矫设备和扇形段辊列损坏,生产非正常中断,造成本炉次及后续炉次钢水回炉或该计划,降低了钢水收得率和合同计划的顺利执行,导致生产成本增加。
事故处理需要24~48小时,降低了连铸作业率。
事故处理时,职工劳动强度大、安全隐患多,增加了管理难度。
一次漏钢事故经济损失300~500 万元,甚至500万元以上。
南阳汉冶特钢炼钢厂3#铸机是西安重型机械研究所设计的全国第一台超厚板板坯连铸机,该铸机于2010年底建成投产后,月产可达5万t以上,至2013年5月,共生产板坯150万t。
随着铸机产能的逐渐释放,因管理和操作经验欠缺,漏钢成为威胁板坯生产稳定的首要问题。
不断总结教训、积累经验,降低漏钢事故率,是稳定连铸机生产、节能降耗、降低成本、增加效益的有效途径之一。
1汉冶特钢厚板板坯连铸机参数及漏钢情况1.1汉冶特钢厚板板坯铸机主要工艺参数,见表1。
1.2粘结漏钢事故分析表2010~2013年常规板坯连铸机粘结漏钢情况分析表,见表2。
2板坯连铸机漏钢原因分析2.1粘结漏钢的机理在钢水浇注过程中,结晶器弯月面的钢水处于异常活跃的状态。
由于各种原因,浇铸过程中流入坯壳与结晶器铜壁之间的液态渣被阻断,当结晶器铜板与初生坯壳的摩擦力大于初生坯壳的强度时,初生坯壳被撕裂与铜板产生粘结。
板坯连铸机粘接漏钢的原因与预防措施
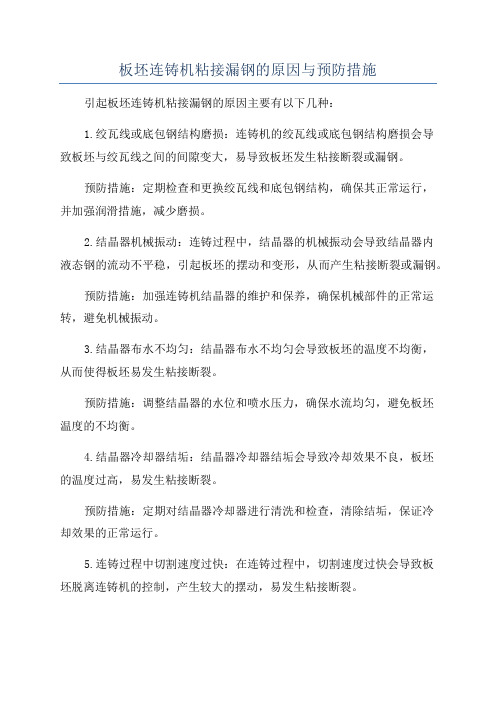
板坯连铸机粘接漏钢的原因与预防措施引起板坯连铸机粘接漏钢的原因主要有以下几种:1.绞瓦线或底包钢结构磨损:连铸机的绞瓦线或底包钢结构磨损会导致板坯与绞瓦线之间的间隙变大,易导致板坯发生粘接断裂或漏钢。
预防措施:定期检查和更换绞瓦线和底包钢结构,确保其正常运行,并加强润滑措施,减少磨损。
2.结晶器机械振动:连铸过程中,结晶器的机械振动会导致结晶器内液态钢的流动不平稳,引起板坯的摆动和变形,从而产生粘接断裂或漏钢。
预防措施:加强连铸机结晶器的维护和保养,确保机械部件的正常运转,避免机械振动。
3.结晶器布水不均匀:结晶器布水不均匀会导致板坯的温度不均衡,从而使得板坯易发生粘接断裂。
预防措施:调整结晶器的水位和喷水压力,确保水流均匀,避免板坯温度的不均衡。
4.结晶器冷却器结垢:结晶器冷却器结垢会导致冷却效果不良,板坯的温度过高,易发生粘接断裂。
预防措施:定期对结晶器冷却器进行清洗和检查,清除结垢,保证冷却效果的正常运行。
5.连铸过程中切割速度过快:在连铸过程中,切割速度过快会导致板坯脱离连铸机的控制,产生较大的摆动,易发生粘接断裂。
预防措施:调整切割速度,使其适应板坯的尺寸和形状,减少切割过程中的摆动。
6.进料辊道制动控制不当:进料辊道制动控制不当会导致板坯的速度不稳定,易产生粘接断裂。
预防措施:加强对进料辊道的制动控制,确保板坯的进料速度平稳,减少速度变化造成的影响。
为了预防板坯连铸机粘接漏钢问题1.定期检查和更换关键部件,确保设备的正常运行。
2.加强润滑措施,减少设备磨损。
3.定期对连铸机进行维护和保养,避免机械振动。
4.调整结晶器的水位和喷水压力,保证水流均匀。
5.定期清洗结晶器冷却器,确保冷却效果的正常运行。
6.调整切割速度,使其适应板坯的尺寸和形状。
7.加强对进料辊道的制动控制,保证板坯的进料速度平稳。
综上所述,板坯连铸机粘接漏钢问题的原因多种多样,但通过采取相应的预防措施,可以有效减少粘接漏钢问题的发生,提高连铸工艺的稳定性和良品率。
板坯粘结漏钢分析

5 结束语
1)降低保护渣熔化温度、粘度,提高熔速, 对减少粘结漏钢有利; 2)采用非正弦振动,对减少粘结漏钢有利; 3)提高钢水纯净度,对避免粘结漏钢有利; 4)稳定拉速和液面,“黑渣”操作,可减少粘 结漏钢; 5)温度过低,拉速不宜过高。
3.1 保护渣性能及耗量的影响 3.2 钢水纯净度的影响 3.3 结晶器液面波动的影响 当结晶器内钢液面上升到与渣圈相接触时,液 渣向下的通道将被堵住,当钢液面继续上升时, 会把渣圈向上推,将渣圈与固态渣膜分开,使钢 液直接和结晶器壁接触,并粘结在一起;正滑脱 时,坯壳强度大于粘结力,坯壳被拉走,如果坯 壳强度小于粘结力时,坯壳被拉断,在结晶器出 口产生漏钢。 3.4 拉速变化的影响 拉速发生变化后,温度变化滞后,液渣层厚度 变化、固态渣膜变化和恢复到最佳状态所需时间 推迟,在高拉速时,更易出现这种漏钢。
Nhomakorabea保护渣熔化速度低,单位时间内熔化的保护渣量小,进入铸坯与铜板缝隙的 液渣量就少。 保护渣熔化温度对钢液面上溶渣层厚度的影响如图1。 保护渣熔化温度h、钢液面温度t,、保护渣表面温度h。在钢液面上的熔渣层 与粉渣层间形成一个温度为t:的等温面,在稳定态传热的条件下,通过双层 平板的传热,在粉渣层内带走的热量应等于熔渣层所传导的热量。 即 通过粉渣层传热 q1= 1(t 2 t1); (1) S1 通过熔渣层传热 q2= 2(t 3 t 2 ) ; (2) S2 按稳定态传热条件,则ql=q2由此得出:
板坯粘结漏钢分析
1 2 3 4 5
前言 生产条件 影响粘结漏钢的因素及原因 粘结漏钢的预防措施 结束语
1 前言
漏钢是连铸生产中严重的生产事故, 影响铸机作业率,降低钢水收得率并 使设备严重损坏。 粘结漏钢在板坯连铸漏钢原因中所 占比例大,2000年我厂板坯连铸漏钢 25次,其中粘结漏钢13次,占漏钢次 数的52%。
连铸漏钢的事故类型及原因、预防措施

连铸漏钢的事故类型及原因、预防措施所谓漏钢是指连铸初期或浇注过程中,铸坯坯壳凝固情况不好或因其他外力作用引起坯壳断裂或破漏使内部钢水流出的现象。
漏钢是连铸生产中恶性事故之一,严重的漏钢事故不仅影响连铸机的正常生产,降低作业率,而且还会破坏铸机设备,造成设备损坏。
漏钢事故因发生的时间不同及发生在铸机上的位置不同分为多种形式,其产生的原因也各不相同,主要分为以下几点:⑴开浇漏钢:开浇起步不好而造成漏钢。
⑵悬挂漏钢:结晶器角缝大,角垫板凹陷或铜板划伤,致使在结晶器中拉坯阻力增大,极易发生起步悬挂漏钢。
⑶裂纹漏钢:在结晶器坯壳产生严重纵裂、角裂或脱方,出结晶器后造成漏钢。
⑷夹渣漏钢:由于结晶器渣块或异物裹入凝固壳局部区域,使坯壳厚度太薄而造成漏钢。
⑸切断漏钢:当拉速过快,二次冷却水太弱,使液相穴过长,铸坯切割后,中心液体流出。
⑹粘结漏钢:铸坯粘结在结晶器壁而拉断造成的漏钢。
开浇漏钢(1)中包塞棒头部及上水口碗部烘烤不良。
因碗部较低,传统烘烤方法烘烤火焰达不到碗部,致使碗部温度比其他部位温度低100~200℃。
钢水温度低易造成冷钢垫棒、钢流失控,被迫提高拉速,导致坯头未充分凝固,造成开浇漏钢。
(2)纸绳松动,钢水从其缝隙中渗漏;纸绳受潮,遇钢水后爆炸产生缝隙,钢水从缝隙中渗漏。
(3)铁屑层过薄,造成钢水将纸绳燃烧后从缝隙渗出;铁屑层过厚,将导致坯头强度不足,坯壳被拉断;铁屑受潮、有油污或有杂物,遇钢水后爆炸或燃烧,钢水将纸绳燃烧后从缝隙渗出或坯头强度不足,坯壳被拉断。
(4)传统的封堵引锭方式是用纸绳将引锭头与结晶器间四周的缝隙塞紧、塞实。
钢水到站测温时,先在引锭头上均匀铺撒20~30mm厚的铁钉屑,然后在铁钉屑上按规定交叉摆放好钢板条。
如果钢板条摆放不好,会使钢水直接冲刷铁屑和纸绳;若钢板条熔化不充分,则初生坯壳过薄,拉坯时将导致坯壳撕破。
(5)操作中存在以下问题:开浇钢流过大,将铁屑冲散或将钢水溅到结晶壁上、角缝上形成夹钢;起步提速过快,每次超过0.1m/min,初生坯壳承受不了其拉力;有异物进入结晶器,并咬入初生坯壳中。
连铸机漏钢的原因及防范措施
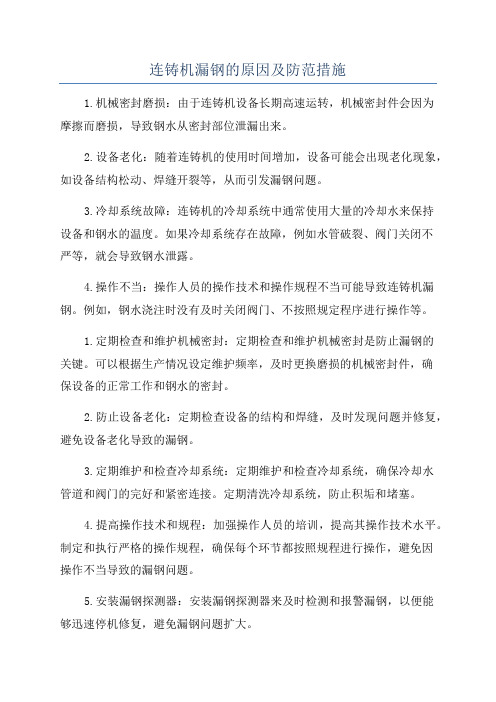
连铸机漏钢的原因及防范措施1.机械密封磨损:由于连铸机设备长期高速运转,机械密封件会因为摩擦而磨损,导致钢水从密封部位泄漏出来。
2.设备老化:随着连铸机的使用时间增加,设备可能会出现老化现象,如设备结构松动、焊缝开裂等,从而引发漏钢问题。
3.冷却系统故障:连铸机的冷却系统中通常使用大量的冷却水来保持设备和钢水的温度。
如果冷却系统存在故障,例如水管破裂、阀门关闭不严等,就会导致钢水泄露。
4.操作不当:操作人员的操作技术和操作规程不当可能导致连铸机漏钢。
例如,钢水浇注时没有及时关闭阀门、不按照规定程序进行操作等。
1.定期检查和维护机械密封:定期检查和维护机械密封是防止漏钢的关键。
可以根据生产情况设定维护频率,及时更换磨损的机械密封件,确保设备的正常工作和钢水的密封。
2.防止设备老化:定期检查设备的结构和焊缝,及时发现问题并修复,避免设备老化导致的漏钢。
3.定期维护和检查冷却系统:定期维护和检查冷却系统,确保冷却水管道和阀门的完好和紧密连接。
定期清洗冷却系统,防止积垢和堵塞。
4.提高操作技术和规程:加强操作人员的培训,提高其操作技术水平。
制定和执行严格的操作规程,确保每个环节都按照规程进行操作,避免因操作不当导致的漏钢问题。
5.安装漏钢探测器:安装漏钢探测器来及时检测和报警漏钢,以便能够迅速停机修复,避免漏钢问题扩大。
6.提高设备的自动化程度:通过提高设备的自动化程度,减少人为的操作,从而降低操作失误导致的漏钢风险。
总之,连铸机漏钢的原因多种多样,需要通过定期检查和维护设备,提高操作技术和规程,安装漏钢探测器等方式来加强防范措施,确保连铸机的正常运行和钢水的安全。
- 1、下载文档前请自行甄别文档内容的完整性,平台不提供额外的编辑、内容补充、找答案等附加服务。
- 2、"仅部分预览"的文档,不可在线预览部分如存在完整性等问题,可反馈申请退款(可完整预览的文档不适用该条件!)。
- 3、如文档侵犯您的权益,请联系客服反馈,我们会尽快为您处理(人工客服工作时间:9:00-18:30)。
板坯连铸机漏钢事故的原因分析及防止摘要:本文分析了某某钢二炼钢厂板坯连铸机漏钢事故产生产的原因及防止板坯连铸机漏钢的措施。
采取相应控制措施之后,目前某某钢二炼钢厂常规板坯连铸机频繁漏钢的势头得到了明显的控制。
关键词:板坯粘结漏钢保护渣水口浸入深度1 前言某某钢第二炼钢厂常规板坯连铸机自2005年4月18日投产以来,铸机漏钢问题始终困绕着二炼钢厂的正常生产,对二炼钢厂的正常生产造成了重大的冲击,连铸机的漏钢问题成为制约二炼钢厂生产的瓶颈环节。
频繁的漏钢事故使连铸机设备的劣化趋势明显加剧,铸机检修质量无法保证。
为降低连铸机漏钢事故,二炼钢厂成立了攻关组,经过对漏钢事故的原因进行分析,采取了相应的措施,板坯连铸机结晶器漏钢事故得到了明显的控制。
2 某某钢第二炼钢厂常规板坯连铸机参数及漏钢相关情况简介2.1某某钢第二炼钢厂常规板坯连铸机的主要工艺参数表1 主要工艺参数铸机产量万吨/年2 生产钢种四大类二十多个品种3 连铸坯厚度mm 160,2204 连铸坯宽度mm 850~16005 铸机半径m 9.56 连铸机型式立弯式(连续弯曲,连续矫直)7 连铸机冶金长度m 31.98 铸机正常拉速m/min 1.0~1.49 结晶器长度mm 95010 振动方式液压(正弦,非正弦)11 二冷方式气水冷却(十四个控制回路)2.2漏钢统计情况从某某钢二炼钢厂常规板坯连铸机从2004年4月18日正式投产以来,共发生各种漏钢事故17次。
其中粘结漏钢14次,占到所有漏钢的82%。
其它三次漏钢为卷渣漏钢,裂纹漏钢,尾坯漏钢。
板坯连铸机漏钢事故成为制约全厂正常生产的瓶颈环节。
3 某某钢二炼钢厂常规板坯连铸机漏钢原因分析3.1粘结漏钢结晶器粘结漏钢形成的过程如图1所示。
在钢水浇注过程中,结晶器弯月面的钢水处于异常活跃的状态。
如图1所示,由于各种原因,浇铸过程中流入坯壳与结晶器铜壁之间的液态渣被阻断,当结晶器铜板与初生坯壳的摩擦力大于初生坯壳的强度时,初生坯壳被拉断,与铜板产生粘结。
这时,在被粘着的部分(1)和向下拉的铸坯(2)的界面凝固壳破断;在破断处流入钢液,重新形成新的薄坯壳(3);在振动和滑动时坯壳又被拉断,钢水补充后又形成另一个新的薄坯壳。
这一过程反复进行,直到新坯壳到达结晶器出口就产生漏钢。
3.2某某钢二炼钢厂板坯连铸机产生粘结漏钢的原因3.2.1工艺方面的原因(1)浇注过程中异常情况下结晶器液面波动大,使弯月面处的结晶器保护渣的注入时断时续,使铜板直接与钢液相接触,造成粘结漏钢。
图2 保护渣在结晶器中结构如图2所示,在浇注过程中结晶器液渣从弯月面处沿着铸坯坯壳与附着在结晶器铜上的固态渣膜之间的间隙,在铜板与坯壳之间起到润滑作用和改善传热。
当结晶器液面波动过大时,尤其在结晶器液面在大幅上涨,而振动台在下振的瞬间,结晶器铜板四周的固态渣圈对结晶器弯月面形成挤压,导致结晶器液渣层断流的机率大大增加。
另外,由于我厂的中包车升降液压系统设计原因,中包车在升降过程中不平稳,并且升降速度达到了30~40mm/s,无法调整,导致在升降中包过程中结晶器液面波动大。
根据我厂对粘结漏钢的统计,在所有粘结漏钢事故中,有五次发生在升完中包后约1分钟之内。
(2)水口插入深度与粘结漏钢的关系。
中包水口的插入深度是连铸所控制的重要工艺参数。
水口插入深度对液面波动影响较大,当插入深度深时,液面波动减少,熔渣表面的波动幅度减弱,降低保护渣卷入的可能性,但是钢水表面温度降低,这就不利于保护渣熔化,结晶器液渣层可能变薄。
同时,插入深度过深时高温区下移,对开成的坯壳造成冲击,若钢水过热度过高,可能导致形成的坯壳二次重熔,坯壳减薄,出结晶器易漏钢。
插入深度小时,结晶器液面波动大,对液渣层形成冲击,并且液渣层不均匀,易产生卷渣和粘结。
原则上在水口结构一定条件下,水口插入深度随拉速增加而增加。
根据现场的实际使用情况,二炼钢厂常规板坯连铸机的拉速控制在1.0~1.3m/min,水口插入深度控制在110~140mm,基本满足生产需要。
(3)铸机拉速调整幅度过大导致漏钢。
在大幅度提拉速过程中,容易导致结晶器液面波动大,增加了粘结的机率。
同时,在大幅度提拉速的过程中,短时间内结晶器液面层会迅速减少,根据现的实际测量,在正常浇注过程中提拉速幅度达到0.2m/min时,浇注20秒后,结晶器内的渣液层厚度由11mm减少到约7mm。
在我厂的粘结漏钢中由两次与引原因直接相关。
(4)换水口操作不当。
在换水口过程中,由于新旧水口在结晶器中大范围的搅动,造成结晶器液渣层迅速减少。
同时由于换水结晶器液面波动大,导致粘结的机率会大大增加。
(5)结晶器中结冷钢导致漏钢。
在浇注过程中,如果结晶器中结冷钢,则会使结晶器液层厚度不均匀,并且液渣的流动性变差。
同时在结冷钢处结晶器液渣层流动性变差,初生坯壳与结晶器铜板之间液渣层断流,导致粘结漏钢。
导致结晶器结冷钢的主要因素有:保护渣保温性能差、中包浸入式水口侧孔侵蚀异常、结晶器流场偏流、水口不对中。
另外由于我厂的结晶器设计是按照1.6m/min以上的工作拉速设计的,而由于种种原因,目前连铸机的正常拉速无法达到设计拉速。
对于所结晶器铜板厚度与水缝设计是否能够满足目前的拉速,目前正在核算。
(6)保护渣的适用性及选型。
连铸结晶器保护渣最主要的两项冶金功能是“润滑”和“控制传热”。
这两项功能的良好发挥是借助于熔融保护渣充填在结晶器壁和坯壳之间的缝隙内形成渣膜得以实现。
良好的保护渣对减少粘结漏钢起决定性的做用。
我厂在2005年10月份连续出现漏钢,分析原因发现保护渣在浇注过程中出现结晶器液渣层不稳定的现象,液渣层最厚达到了15mm,最薄只有不到5mm,说明此保护渣在浇注过程中出现了分熔现象,导致结晶器液渣层不稳定,在结晶器液渣层厚度降到7mm以下时,粘结漏钢的机率大大增加。
3.2.2设备方面的原因(1)结晶器振动台的精度。
我厂振动台的设计精度要求为:横向±0.1mm,纵向±0.1mm,相位差<±0.4°。
但于没有按照设备安装规范及时进行机整系统检修及精度调整,导致振动台失修,振动台的导轮与导向板之的间隙由设备安装时的0.02mm增大到了0.3mm,振动台报警频繁,结晶器振动的偏摆量明显加大。
结晶器振动偏摆加大,会使坯壳与结晶器铜板之间的间距不稳定,时大时小,从而使坯壳所受的摩擦力不均匀。
另外,振动偏摆,也会使结晶器与坏壳间缝隙大小产生差异,导致结晶器保护渣流人不均匀。
坯壳的薄弱处被拉破而导致漏钢。
(2)结晶器锥度。
由于我厂的结晶器液压自动调宽装置没有投入使用,所采取的措施对结晶器窄面使用顶杆进行固定,保证在浇注过程中结晶器锥的变化在标准范围之内。
目前结晶器窄面的锥度基本能够得到保证,但是宽面锥度经常出现严重超标的现象。
我厂某次漏钢事故后对最近两天的结晶器锥度变化情况统计情况见表2。
表2 结晶器锥度变化统计浇次宽面外弧宽面内弧窄左窄右上口下口标准0.5±0.2 0.5±0.2 6.9±0.2 1550.82 1532.61142浇次开浇0.83 0.74 0.72 0.91 0.92 0.8 6.95 7.04 1549.18 1532.2 停浇 1.59 1.18 1.02 0.21 0.62 0.39 6.45 6.75 1550.93 1532.66143浇次开浇0.56 0.75 0.69 0.67 0.86 0.64 7.11 6.87 1550.31 1532.5 停浇0.92 1.01 0.87 0.31 0.01 0.09 7.11 7.6 1550.88 1532.68144浇次开浇0.72 0.7 0.78 0.71 1.05 0.88 6.81 7 1550.46 1532.8 停浇0.41 0.05 0.04 1.16 1.33 1.08 6.87 7.07结晶器宽面锥度超标,对于保护渣的液渣流入通道产生影响,使粘结的机率大大增加。
3.3边裂漏钢这种漏钢主要是由于结晶器窄面铜板倒锥度在浇铸过程中变小或结晶器窄面铜的矩形度严重超标所致。
当窄面铜板锥度小时,坯壳与窄面铜板产生较大的气隙,使板坯窄面冷却强度降低、坯壳减薄,板坯窄面出现鼓肚现象,板坯内弧宽面距角部10~30 mm处坯壳薄弱处凹陷,并形成裂纹,进而导致漏钢。
2004年9月我厂发生大量的边部裂纹,并且导致一次边裂漏钢,主要原因为结晶器矩形度超标,结晶器内腔内弧长度比外弧长度大了1.7mm,铸坯断面尺寸内弧比外弧大10mm。
对结晶器窄面铜板进行调整之后,再没有出现铸坯边裂。
3.4开浇漏钢开浇漏钢产生的主要原因有:(1)开浇钢水热度过高,拉速起步后,使形成的坯壳二次重熔,导致出结晶器时的坯壳过薄,出结晶器后无法承受钢水的静压力。
(2)开浇前中包没有烘烤好,开浇后塞棒控制流失常,出苗时间不够强行起步并提拉速。
(3)结晶器中的冷料的冷却强度不够。
(4)开浇操作不规范,试棒时机控制不当,使钢水没有在引锭头上一次性形成完整的坯壳,导致引锭头上坯壳的强度不够。
4 减少二炼钢厂板坯连铸机漏钢的工艺优化及设备管理措施通过以上对某某钢二炼钢厂常规板坯连铸机投产以产生漏钢原因分析,主要从以下几个方面对工艺进行优化,并且加强设备的管理。
(1)要求上台钢水的[S]控制在0.020%以下,保证在凝固晶界处无FeS生成,提高初生坯壳强度,可减少粘结漏钢。
(2)坚持“恒温恒拉速”的原则,保持浇注工艺稳定,实现恒温浇注,保护渣熔化均匀,坯壳生长均匀。
(3)采用液面自动控制,使液面波动控制在±3mm。
同时在浇注过程中升降中包车时,先将拉速降到0.9m/min以下,然后点动操作,之后采用水平调整操作,使结晶器液面波动控制在最小的范围内。
(4)在结晶器漏钢预报出现报警时,及时降拉速。
由于我厂的结晶器漏钢预报系统目前运行并不正常,在浇注过程中由中控工监控漏钢预报系统监画面,当出现报警或监控画面异常时要立即通知机长采取相应的措施。
(5)将塞棒吹氩的氩气流量控制在5~15l/min,保证结晶器化渣良好。
(6)在提拉速过程中严格按照0.05m/min的幅度操作,并且在提拉速之前要测量结晶器液渣层厚度。
在换水口前后20分钟之内严格换渣操作,防止液渣层断流。
同时中包钢水过热度小于10℃时,严禁提拉速。
(7)浇注过程中,保证水口对中。
同时将水口的浸入深度严格的控制在110~140mm的范围之内,并且根拉速和中包温度进行微度的调整。
(8)使用合适的保护渣,浇注过程中操作者密切关注保护渣的熔化情况,每一炉都要测量液渣层厚度,同每炉钢估算一次保护渣的消耗量,保护渣的消耗量控制在0.6~0.65kg/t钢,对于结晶器四周的大渣条要及时挑出。