注塑车间筹备计划
注塑车间整体规划一车间

注塑车间整体规划一车间一、背景介绍注塑车间是创造业中常见的生产车间之一,主要用于生产塑料制品。
为了提高生产效率和质量,以及优化车间布局,整体规划注塑车间成为必要的任务。
本文将详细介绍注塑车间整体规划的步骤和要点。
二、车间布局设计1. 车间面积注塑车间的面积应根据生产需求和设备数量合理确定。
普通来说,每台注塑机需要约10-15平方米的空间。
根据车间面积,确定注塑机的数量,并为其留出合适的操作空间。
2. 原材料存储区在车间中设置原材料存储区,用于存放塑料颗粒和其他所需的原材料。
存储区应设立合适的货架和标识,以便工人能够快速找到所需的原材料。
3. 注塑机布局注塑机应根据生产流程和操作人员的工作需求进行布局。
注塑机之间应保留足够的间距,以便操作人员进行操作和维护。
同时,应考虑到注塑机的进出料方便性和安全性。
4. 辅助设备安排除了注塑机,注塑车间还需要配备一些辅助设备,如干燥机、冷却塔、冷却水系统等。
这些设备应根据生产需求和工艺要求进行合理的布局和安排。
5. 成品存储区在车间中设置成品存储区,用于存放已经注塑成型的产品。
存储区应设立合适的货架和标识,以便工人能够快速找到所需的成品。
三、设备选型和配置1. 注塑机选型根据生产需求和产品要求,选择合适的注塑机型号。
考虑到生产效率、产品质量和能耗等因素,选用具有先进技术和稳定性能的注塑机。
2. 辅助设备选型根据生产需求和工艺要求,选择合适的辅助设备。
例如,根据原材料的湿度,选择合适的干燥机;根据产品的冷却要求,选择合适的冷却塔和冷却水系统。
3. 设备配置根据车间布局和生产需求,合理配置注塑机和辅助设备的位置。
确保设备之间的连接和运输通道畅通,并考虑到设备的维护和保养便利性。
四、人员组织和培训1. 人员组织根据生产规模和生产流程,合理组织车间人员。
设立车间主管和班组长,明确各个岗位的职责和权限,并确保人员配备合理,以保证生产的顺利进行。
2. 培训计划为新员工和现有员工制定培训计划,培养他们的技能和知识。
企业注塑车间策划书3篇

企业注塑车间策划书3篇篇一企业注塑车间策划书一、项目背景随着市场需求的不断增加,企业的注塑业务也在不断扩大。
为了提高生产效率、保证产品质量,企业计划对注塑车间进行升级改造。
二、项目目标1. 提高生产效率:优化生产流程,减少生产周期,提高设备利用率。
2. 保证产品质量:引入先进的质量管理体系,加强过程控制,降低废品率。
3. 改善工作环境:优化车间布局,提高安全性,降低噪音和粉尘污染。
4. 提升企业形象:打造现代化的注塑车间,提升企业的品牌形象和市场竞争力。
三、项目内容1. 设备更新与升级:淘汰老旧设备,引进具有国际先进水平的注塑机、模具及周边设备。
2. 自动化改造:采用先进的自动化技术,实现上下料、检测、包装等工序的自动化操作。
3. 车间布局优化:根据生产流程和设备布局要求,重新规划车间布局,减少物流距离和搬运时间。
4. 通风与空调系统升级:安装高效的通风和空调设备,改善车间工作环境。
5. 能源管理系统建设:引入智能能源管理系统,实现能耗监测和优化控制。
6. 质量控制系统建立:建立完善的质量管理体系,配备先进的检测设备和仪器。
7. 人员培训与素质提升:组织员工参加技术培训和安全培训,提高员工技能水平和安全意识。
四、项目实施计划1. 项目启动阶段:成立项目组,明确项目目标、任务分工和时间节点。
进行需求调研和方案设计。
2. 设备采购与安装阶段:根据设计方案,采购所需设备和材料。
组织设备安装和调试。
3. 自动化改造与系统集成阶段:实施自动化改造,实现设备之间的互联互通。
4. 车间布局调整与装修阶段:根据新的布局方案,进行车间调整和装修。
5. 设备调试与试生产阶段:对设备进行全面调试,确保设备运行稳定。
进行试生产,验证生产工艺和产品质量。
五、项目预算与资金筹措1. 预算:项目总投资预计为[X]万元,其中设备购置及安装费用[X]万元,自动化改造费用[X]万元,车间布局调整及装修费用[X]万元,其他费用[X]万元。
注塑车间整体规划一车间

注塑车间整体规划一车间一、背景介绍注塑车间是制造业中重要的生产车间之一,主要用于注塑成型工艺,生产各种塑料制品。
为了提高生产效率和产品质量,需要对注塑车间进行整体规划和优化。
本文将详细介绍注塑车间整体规划的内容和要求。
二、规划目标1. 提高生产效率:通过合理布局和优化工艺流程,减少生产环节的浪费,提高注塑车间的生产效率。
2. 优化工作环境:改善注塑车间的工作环境,提高员工的工作舒适度和安全性。
3. 提高产品质量:通过规范化的生产流程和严格的质量控制,提高注塑产品的质量,减少次品率。
三、规划内容1. 车间布局:根据生产工艺和设备要求,合理规划注塑车间的布局。
将设备、原材料存放区、成品存放区、工作区域等合理划分,确保生产流程的顺畅和物料的流动性。
2. 设备选型:根据生产需求和产品特性,选择适合的注塑设备。
考虑设备的生产能力、稳定性、能耗等因素,选用高效、节能的注塑设备。
3. 工艺流程优化:分析注塑生产的工艺流程,找出瓶颈和不必要的环节,进行优化。
合理安排生产顺序,减少换模时间和停机时间,提高生产效率。
4. 环境改善:改善注塑车间的通风、照明和噪音控制等条件,提供良好的工作环境。
安装通风设备、照明设备和噪音隔离设备,确保员工的健康和安全。
5. 质量控制:建立完善的质量控制体系,包括原材料的检验、生产过程的监控和成品的检测。
制定质量标准和操作规程,确保产品符合质量要求。
四、规划步骤1. 调研分析:对注塑车间的现状进行调研和分析,了解生产流程、设备状况、工作环境等情况。
2. 制定规划方案:根据调研结果和规划目标,制定注塑车间整体规划方案。
包括车间布局、设备选型、工艺流程优化、环境改善和质量控制等内容。
3. 实施规划方案:按照规划方案,逐步实施注塑车间的整体规划。
包括设备采购、车间改造、工艺优化和环境改善等工作。
4. 监督检查:在实施过程中,进行监督和检查,确保规划方案的顺利实施。
及时解决问题和调整方案,确保规划目标的实现。
注塑车间筹备计划

注塑车间筹备计划一.可行性研究的依据随着科学技术的高速发展,生产力水平的提高,生产结构日趋复杂、精密,产品价值日趋提升,用户对产品的质量要求高的精密产品需求多,精密产品的附加值也就越高。
二、原材料主要原材料:工程塑胶。
水:生产用水量为10到20吨/小时,消防给水量为20吨/小时。
电:增置一台200KV A节能变压器。
(按装机多少来配)三、需求预测、产品方案和拟建规模年生产量300万套。
共需要注塑机器4台.四、厂情与厂址介绍五、生产设计方案1、主要工艺流程2、设备一.注塑方面设备1.注塑机4台2.冷却水塔(可以用井水) 1套3.粉碎机2台4.拌料机1台5.工作台4张6.模具架7.行车(如果模具小一般可以不配)1套8.模温机(如果是只做PP料不需要)数台9.机械手(不一定需要)4台10.无尘车间中央空调(不一定需要)1套二.检验设备1.游标卡尺数套2.千分尺数套3.投影仪(根据产品的精密度选用)1台4.3次元测量仪(根据产品的精密度选用)1台六、生产组织与员工培训计划本项目采用类比法,拟定人员X人。
其中厂长室、产、供、销、财务、人事、技术、质管、设备、工会等各类行政管理人员5人,检验3人,注塑车间8人,喷涂车间装配车间待定人,,后勤及其他待定人.技术人员专业配套,在生产准备的同时,对职工进行经营管理、技术培训及安全生产、质量管理全面教育。
新增工人按高中水平招考,择优录取,培训合格后上岗。
七、项目实施进度预测1.咨询、商务谈判、签约把订单缺确定下来,估计产品的大小克重,模具的大小,年计划订单量。
2.初步设计设备的大小数量、做出购买设备计划,订购设备。
通常影响射出机选择的重要因素包括模具、产品、塑料、成型要求等,因此,在进行选择前必须先收集或具备下列资讯:◆模具尺寸(宽度、高度、厚度)、重量、特殊设计等;◆使用塑料的种类及数量(单一原料或多种塑料);◆注塑成品的外观尺寸(长、宽、高、厚度)、重量等;◆成型要求,如品质条件、生产速度等。
注塑车间整体规划一车间

注塑车间整体规划一车间引言概述:注塑车间作为制造业中重要的生产环节,其整体规划对于提高生产效率和产品质量至关重要。
本文将从四个方面详细阐述注塑车间整体规划的重要性及其具体内容。
一、车间布局规划1.1 优化工作流程:通过合理规划车间内各个工作区域的位置和布局,使得物料的流动路径更加合理,减少物料运输时间和人力资源浪费。
1.2 安全与环保考虑:在车间布局规划中,需要考虑到安全通道、防火设施、紧急出口等因素,同时注重环保要求,合理设置废料处理区域。
1.3 空间利用率优化:通过合理规划车间内设备和工作区域的位置,最大限度地利用有限的空间资源,提高车间的生产能力。
二、设备选型和布置2.1 设备选型:根据生产需求和产品特性,选择适合的注塑设备,包括注塑机、模具、辅助设备等,确保设备的稳定性和生产效率。
2.2 设备布置:根据车间布局规划,合理安排设备的位置,考虑到设备之间的空间和操作人员的工作流程,提高设备的利用率和生产效率。
2.3 自动化设备应用:在设备选型和布置中,可以考虑引入自动化设备,如自动送料机器人、自动取料机械手等,提高生产效率和产品质量。
三、人员培训和管理3.1 培训计划制定:针对注塑车间的工作特点和要求,制定详细的培训计划,包括操作技能培训、安全培训、质量控制培训等,确保员工具备必要的技能和知识。
3.2 岗位职责明确:明确注塑车间内各个岗位的职责和工作流程,确保每个员工在工作中清楚自己的职责,提高工作效率和生产质量。
3.3 绩效考核机制建立:建立科学的绩效考核机制,根据员工的工作表现和贡献,进行绩效评估和激励,激发员工的积极性和创造力。
四、质量管理和持续改进4.1 质量控制标准制定:制定详细的质量控制标准和流程,包括原材料检验、生产过程控制、产品检测等,确保产品质量符合要求。
4.2 引入质量管理工具:引入质量管理工具如SPC(统计过程控制)和6σ(六西格玛)等,进行数据分析和问题解决,持续改进产品质量。
注塑车间整体规划一车间
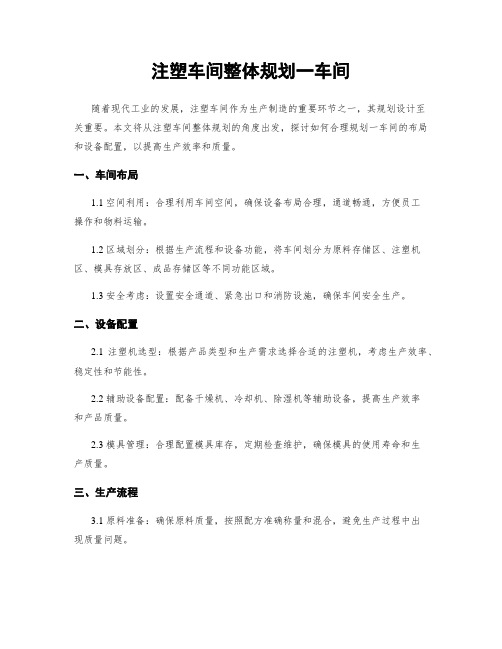
注塑车间整体规划一车间随着现代工业的发展,注塑车间作为生产制造的重要环节之一,其规划设计至关重要。
本文将从注塑车间整体规划的角度出发,探讨如何合理规划一车间的布局和设备配置,以提高生产效率和质量。
一、车间布局1.1 空间利用:合理利用车间空间,确保设备布局合理,通道畅通,方便员工操作和物料运输。
1.2 区域划分:根据生产流程和设备功能,将车间划分为原料存储区、注塑机区、模具存放区、成品存储区等不同功能区域。
1.3 安全考虑:设置安全通道、紧急出口和消防设施,确保车间安全生产。
二、设备配置2.1 注塑机选型:根据产品类型和生产需求选择合适的注塑机,考虑生产效率、稳定性和节能性。
2.2 辅助设备配置:配备干燥机、冷却机、除湿机等辅助设备,提高生产效率和产品质量。
2.3 模具管理:合理配置模具库存,定期检查维护,确保模具的使用寿命和生产质量。
三、生产流程3.1 原料准备:确保原料质量,按照配方准确称量和混合,避免生产过程中出现质量问题。
3.2 生产操作:严格按照操作规程操作注塑机,保持设备清洁,定期检查维护,确保生产过程稳定。
3.3 质量控制:建立完善的质量检测体系,对生产过程进行监控和检验,及时发现和解决质量问题。
四、人员管理4.1 培训教育:对车间员工进行岗位培训和安全教育,提高员工技能和意识,保障生产安全和质量。
4.2 岗位设置:合理设置岗位职责和工作流程,明确各岗位职责,提高生产效率。
4.3 绩效考核:建立科学的绩效考核机制,激励员工积极性,提高生产效率和质量。
五、环境管理5.1 清洁卫生:定期清洁车间环境,保持车间整洁,防止污染影响生产质量。
5.2 环保措施:遵守环保法规,采取节能减排措施,减少对环境的影响。
5.3 废料处理:建立废料处理制度,分类处理废料,减少资源浪费,保护环境。
综上所述,注塑车间整体规划一车间需要综合考虑布局、设备、生产流程、人员管理和环境管理等方面,确保生产过程高效、安全、环保,提高生产效率和产品质量。
注塑车间整体规划二车间

注塑车间整体规划二车间引言概述:注塑车间是生产注塑制品的重要场所,对车间的整体规划直接影响到生产效率和产品质量。
本文将从注塑车间整体规划二车间的角度出发,详细介绍注塑车间规划的重要性和具体内容。
一、车间布局设计1.1 合理利用空间:注塑车间的布局设计应充分考虑生产设备和物料的摆放位置,确保生产流程顺畅,减少生产过程中的交叉干扰。
1.2 安全考虑:在车间布局设计中应考虑到安全通道、应急出口等安全设施的设置,确保员工在生产过程中的安全。
1.3 环保要求:在车间布局设计中应考虑到废料处理区域、通风设备等环保设施的设置,确保车间生产环境符合环保标准。
二、生产设备配置2.1 设备选型:在注塑车间整体规划中,应根据产品种类和生产需求选择适合的注塑设备,确保生产效率和产品质量。
2.2 设备布局:在车间内部设备布局设计中,应考虑设备之间的间距和通道的设置,确保设备之间的协调运作。
2.3 设备维护:在规划注塑车间时,应考虑到设备的维护保养问题,设置设备维护区域,确保设备的正常运转。
三、物料存储管理3.1 物料分类:在注塑车间整体规划中,应根据物料的种类和使用频率进行分类存储,确保物料的易取易放。
3.2 物料储存方式:在车间内部物料存储管理中,应考虑到物料的储存方式,如货架、仓库等,确保物料的安全和整洁。
3.3 物料进出管理:在规划注塑车间时,应考虑到物料的进出管理,设置物料进出口,确保物料的准确使用。
四、人员管理4.1 培训计划:在注塑车间整体规划中,应制定员工培训计划,提高员工的技能和意识,确保生产过程的顺利进行。
4.2 岗位分工:在车间内部人员管理中,应明确各个岗位的职责和权限,确保生产过程的协调运作。
4.3 安全教育:在规划注塑车间时,应加强安全教育,提高员工的安全意识,确保生产过程中的安全。
五、生产流程优化5.1 工艺改进:在注塑车间整体规划中,应不断优化生产工艺,提高生产效率和产品质量。
5.2 质量控制:在车间内部生产流程优化中,应加强质量控制,确保产品符合标准。
注塑车间整体规划二车间
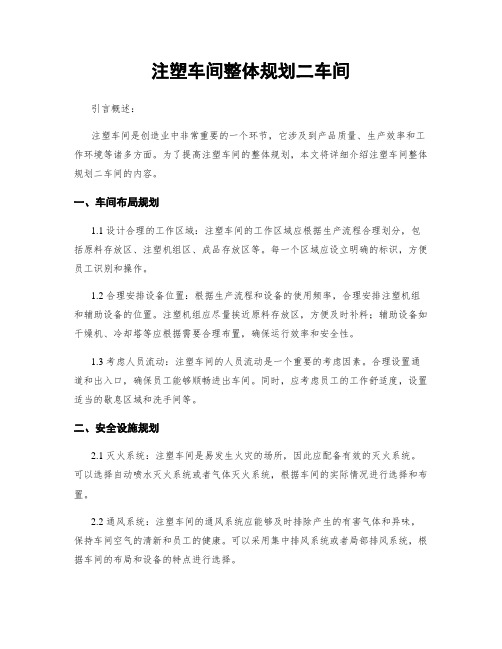
注塑车间整体规划二车间引言概述:注塑车间是创造业中非常重要的一个环节,它涉及到产品质量、生产效率和工作环境等诸多方面。
为了提高注塑车间的整体规划,本文将详细介绍注塑车间整体规划二车间的内容。
一、车间布局规划1.1 设计合理的工作区域:注塑车间的工作区域应根据生产流程合理划分,包括原料存放区、注塑机组区、成品存放区等。
每一个区域应设立明确的标识,方便员工识别和操作。
1.2 合理安排设备位置:根据生产流程和设备的使用频率,合理安排注塑机组和辅助设备的位置。
注塑机组应尽量挨近原料存放区,方便及时补料;辅助设备如干燥机、冷却塔等应根据需要合理布置,确保运行效率和安全性。
1.3 考虑人员流动:注塑车间的人员流动是一个重要的考虑因素。
合理设置通道和出入口,确保员工能够顺畅进出车间。
同时,应考虑员工的工作舒适度,设置适当的歇息区域和洗手间等。
二、安全设施规划2.1 灭火系统:注塑车间是易发生火灾的场所,因此应配备有效的灭火系统。
可以选择自动喷水灭火系统或者气体灭火系统,根据车间的实际情况进行选择和布置。
2.2 通风系统:注塑车间的通风系统应能够及时排除产生的有害气体和异味,保持车间空气的清新和员工的健康。
可以采用集中排风系统或者局部排风系统,根据车间的布局和设备的特点进行选择。
2.3 安全警示标识:在注塑车间的关键位置设置安全警示标识,包括禁止吸烟、禁止乱堆放物品、禁止未经许可进入等。
这些标识应清晰可见,提醒员工注意安全。
三、能源利用规划3.1 节能设备选用:在注塑车间的设备选用上,应优先选择节能型设备。
例如,采用节能型注塑机组和辅助设备,减少能源的消耗,降低生产成本。
3.2 能源监测系统:建立注塑车间的能源监测系统,实时监测能源的使用情况和消耗量。
通过对数据的分析,及时发现能源浪费的问题,并采取相应的措施进行改进。
3.3 能源管理培训:为注塑车间的员工提供能源管理培训,增强他们的节能意识和能源管理能力。
通过培训,员工能够更好地利用能源,减少浪费,提高车间的能源利用效率。
- 1、下载文档前请自行甄别文档内容的完整性,平台不提供额外的编辑、内容补充、找答案等附加服务。
- 2、"仅部分预览"的文档,不可在线预览部分如存在完整性等问题,可反馈申请退款(可完整预览的文档不适用该条件!)。
- 3、如文档侵犯您的权益,请联系客服反馈,我们会尽快为您处理(人工客服工作时间:9:00-18:30)。
注塑车间筹备计划
一.可行性研究的依据
随着科学技术的高速发展,生产力水平的提高,生产结构日趋复杂、精密,产品价值日趋提升,用户对产品的质量要求高的精密产品需求多,精密产品的附加值也就越高。
二、原材料
主要原材料:工程塑胶。
水:生产用水量为10到20吨/小时,消防给水量为20吨/小时。
电:增置一台200KV A节能变压器。
(按装机多少来配)
三、需求预测、产品方案和拟建规模
年生产量300万套。
共需要注塑机器4台。
四、厂情与厂址介绍
五、生产设计方案
1、主要工艺流程
2、设备
一.注塑方面设备
1.注塑机4台
2.冷却水塔(可以用井水)1套
3.粉碎机2台
4.拌料机1台
5.工作台4张
6.模具架
7.行车(如果模具小一般可以不配)1套
8.模温机(如果是只做PP料不需要)数台
9.机械手(不一定需要)4台
10.无尘车间中央空调(不一定需要)1套
二.检验设备
1.游标卡尺数套
2.千分尺数套
3.投影仪(根据产品的精密度选用)1台
4.3次元测量仪(根据产品的精密度选用)1台
六、生产组织与员工培训计划
本项目采用类比法,拟定人员X人。
其中厂长室、产、供、销、财务、人事、技术、质管、设备、工会等各类行政管理人员5人,检验3人,注塑车间8人,喷涂车间装配车间待定人,,后勤及其他待定人。
技术人员专业配套,在生产准备的同时,对职工进行经营管理、技术培训及安全生产、质量管理全面教育。
新增工人按高中水平招考,择优录取,培训合格后上岗。
七、项目实施进度预测
1.咨询、商务谈判、签约
把订单缺确定下来,估计产品的大小克重,模具的大小,年计划订单量。
2.初步设计设备的大小数量、做出购买设备计划,订购设备。
通常影响射出机选择的重要因素包括模具、产品、塑料、成型要求等,因此,在进行选择前必须先收集或具备下列资讯:
◆模具尺寸(宽度、高度、厚度)、重量、特殊设计等;
◆使用塑料的种类及数量(单一原料或多种塑料);
◆注塑成品的外观尺寸(长、宽、高、厚度)、重量等;
◆成型要求,如品质条件、生产速度等。
、选对型: 由产品及塑料决定机种及系列。
由于射出机有非常多的种类,因此一开始要先正确判断此产品应由哪一种注塑机,或是哪一个系列来生产,例如是一般热塑性塑胶或电木原料或PET原料等,是单色、双色、多色、夹层或混色等。
此外,某些产品需要高稳定(闭回路)、高精密、超高射速、高射压或快速生产(多回路)等条件,也必须选择合适的系列来生产。
2、放得下:由模具尺寸判定机台的“大柱内距”、“模厚”、“模具最小尺寸”及“模盘尺寸”是否适当,以确认模具是否放得下。
◆模具的宽度及高度需小于或至少有一边小于大柱内距;
◆模具的宽度及高度最好在模盘尺寸范围内;
◆模具的厚度需介于注塑机的模厚之间;
◆模具的宽度及高度需符合该注塑机建议的最小模具尺寸,太小也不行。
3、拿得出:由模具及成品判定“开模行程”及“托模行程”是否足以让成品取出。
◆开模行程至少需大于成品在开关模方向的高度的两倍以上,且需含竖浇道(sprue)的长度;
◆托模行程需足够将成品顶出。
4、锁得住:由产品及塑料决定“锁模力”吨数。
当原料以高压注入模穴内时会产生一个撑模的力量,因此注塑机的锁模单元必须提供足够的“锁模力”使模具不至于被撑开。
锁模力需求的计算如下:
◆由成品外观尺寸求出成品在开关模方向的投影面积;
◆撑模力量=成品在开关模方向的投影面积(cm2)×模穴数×模内压力(kg/cm2);
◆模内压力随原料而不同, 一般原料取350~400kg/cm2;
◆机器锁模力需大于撑模力量,且为了保险起见,机器锁模力通常需大于撑模力量的1.17倍以上。
至此已初步决定夹模单元的规格,并大致确定机种吨数,接着必须再进行下列步骤,以确认哪一个射出单元的螺杆直径比较符合所需。
5、射得饱: 由成品重量及模穴数判定所需“射出量”并选择合适的“螺杆直径”。
◆计算成品重量需考虑模穴数(一模几穴);
◆为了稳定性起见,射出量需为成品重量的1.35倍以上,亦即成品重量需为射出量的75%以内。
6、射得好:由塑料判定“螺杆压缩比”及“射出压力”等条件。
有些工程塑料需要较高的射出压力及合适的螺杆压缩比设计,才有较好的成型效果,因此为了使成品射得更好,在选择螺杆时亦需考虑射压的需求及压缩比的问题。
一般而言,直径较小的螺杆可提供较高的射出压力。
7、射得快:及“射出速度”的确认。
有些成品需要高射出率速射出才能稳定成型,如超薄类成品,在此情况下,可能需要确认机器的射出率及射速是否足够,是否需搭配蓄压器、闭回路控制等装置。
一般而言,在相同条件下,可提供较高射压的螺杆通常射速较低,相反的,可提供较低射压的螺杆通常射速较高。
因此,选择螺杆直径时,射出量、射出压力及射出率(射出速度),需交叉考量及取舍。
此外,也可以采用多回路设计,以同步复合动作缩短成型时间。
3.土建施工或租厂房
要求电力和水方便够用。
规划好设备的放置位置
4.生产准备
招聘管理人员,做生产的前期准备,
5.设备、模具交货、安装调适
6.人员培训
7.试制、鉴定,计算成本。