机械加工的切削参数
机械加工 刀具切削参数表
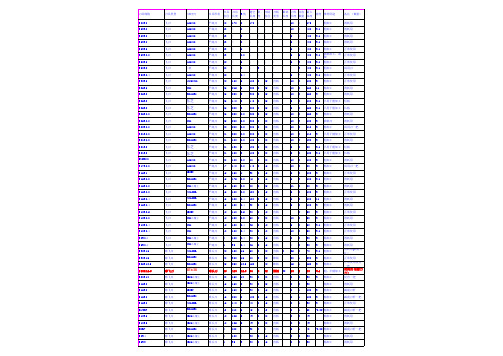
刀具类型 飞刀 飞刀 飞刀 飞刀 飞刀 飞刀 飞刀 飞刀 飞刀 飞刀 飞刀 飞刀 飞刀 飞刀 飞刀 飞刀 飞刀 飞刀 飞刀 飞刀 飞刀 飞刀 飞刀 飞刀 飞刀 飞刀 飞刀 飞刀 飞刀 飞刀 飞刀 飞刀 飞刀 飞刀 飞刀 球飞刀 球飞刀 球飞刀 球飞刀 球飞刀 球飞刀 球飞刀 球飞刀 球飞刀 球飞刀 球飞刀 球飞刀 球飞刀 球飞刀 球飞刀
刀具 长度 170 \ \ \ \ \ \ \ \ 180 215 220 140 200 220 200 200 200 180 130 180 180 140 160 175 160 180 180 120 110 120 120 100 100 95 120 300 250 120 160 160 160 200 140 110 105 105 100 100 95
R角 8 8 8 8 6 0.8 6 2 0.4 6 6 2 2 2 0.8 0.8 0.8 0.8 0.8 2 2 0.8 0.8 1 0.8 0.8 0.8 0.4 0.4 2.5 0.8 0.4 0.4 0.4 0.4 16 15 12.5 12.5 10 8 8 8 8 6 6 5 4 4 3
精度 推荐用途 粗加工 -0.1 -0.1 -0.1 -0.1 -0.1 -0.1 -0.1 -0.1 -0 0.1 -0 -0.1 -0.1 -0 -0 -0 -0 -0 -0.1 -0.1 -0 -0 -0 -0.1 -0 -0 0.1 -0 -0 -0 -0.1 -0.1 -0 -0 -0.1 -0 -0 -0.1 -0 粗加工 粗加工 精加工 粗加工 插铣加工,清 根 粗加工 粗加工 精加工 粗加工 精加工 粗加工 只用于粗加工 只用于粗加工 精加工 插铣刀 精加工 只用于精加工 粗加工 只用于粗加工 只用于粗加工 粗加工 精加工 精加工 粗加工 精加工 粗加工 粗加工 粗加工 粗加工 精加工 粗加工 粗加工 精加工 精加工 粗加工 精加工 精加工 粗,半精加工 精加工 精加工 -0 -0 -0 -0 精加工 精加工 精加工 精加工 精加工 精加工 -0 精加工 精加工 精加工
机械制造技术:确定切削参数三要素

n
=
1000vc
d
≈
318vc d
508
查机床手册,选主轴转速为500r/min
12
THANKS FOR LOOKING
TECHNOLOGY OF MECHANICAL MANUFACTURE
确定切削参数三要素
主要内容:
1 . 切削三要素的定义 2 . 切削用量的选择
2
确定切削参数三要素
任务要求
某轴(锻件)直径尺寸为
50
0 0.016
mm(精度IT6),粗糙
度为Ra0.8μm。若采用加工方法为:粗车--半精车--粗
加工方法为:粗车--半精车--粗磨--精磨。试确定车削加工工序的切削用量
粗车:
10
确定切削参数三要素
粗车
背吃刀量:加工余量4.5mm,可一次车削完成, αp=4.5mm。 查机械加工工艺手册,选进给量f=0.5mm/r。 查机械加工工艺手册,选切削速度Vc=60m/min 。
计算主轴转速:
n
=
1000vc ≈ 318vc 381.6
进给量 a)纵向进给量 b)横向进给量
6
确定切削参数三要素
(3)背吃刀量 ap
对于车削和刨削加工来说,背吃刀量ap为工件上 已加工表面和待加工表面间的垂直距离,单位为mm。
对于外圆车削的深度可用下式计算:
ap=(dw-dm)/ 2 mm
dw—— 待加工表面直径(mm) dm——已加工表面直径(mm)
7
确定切削参数三要素
车削加工如何确定切削用量?
在实际生产中,往往是已知工件直径,并根据工件材料、刀具材
料和加工要求等因素选定切削速度,再由切削速度确定(换算)车床
机械加工切削参数汇总

例外的切削速度
工件重量为300公斤时,n
带 <300转/分;公斤300<工
中 件重量<1000公斤时,n<
心 架
200转/分;公斤1000<工 件重量<3000公斤时,n< 100转/分;工件体积较大
切 或偏心量大时,切削时必须
削 再适当降低转速,务必结合
实际情况做好维稳加工。
带
车削细长轴类时,需用尾 顶,切削转速须根据实际情
800
30 560~670 730~909 1000 1100
677~812 1000 1200
410 820 1000
640~840 1000
630
40 530~630 632~790 870 988
514~610 760 1000
356 712 870
480~630 760
585
采用钻 削方式
50 425~510 495~618 680 770
直径
10
20
30
40
50
60
涂
70
层 80
硬 90
质 合
A3 100
金 200
刀
300
具
400
500
600
700
800
900
1000
型材
锻件毛坯车 调质件转速 加工
削转速77 120
转速
150
1200
1300
1300
1000
1200
1200
818
1200
1200
610
1000
1100
470
750
950
1200
1300
960
机械加工切削参数表

0.03~0.07
250
0.3
0.08~0.1
350
100
0.1
0.05~0.08
300
0.2
0.1~0.15
500
0.2
0.05~0.08
250
0.3
0.1~0.15
350
2A12-T4固溶处理并时效状态(硬度:105HB)内圆车削
类别
Ra
dw
高速钢车刀(W18Cr4V等)
硬质合金车刀(YG8等)
ap(mm)
f(mm/r)
v(m/min)
ap(mm)
f(mm/r)
v(m/min)
粗车
6.3
20
0.6
0.2
250
0.8
0.2
400
1
0.1
200
1.2
0.1
300
100
1
0.2
250
1
0.2
400
2
0.1
200
2
0.1
300
精车
1.6
20
0.1
0.03~0.07
300
0.2
0.08~0.1
500
15~20
0.3
0.1~0.15
60~80
100
0.1
0.05~0.08
15~20
0.3
0.2~0.3
90~110
0.2
0.05~0.08
15~20
0.4
0.15~0.2
90~110
40Cr钢热轧状态钢车刀(W18Cr4V等)
硬质合金车刀(YT15等)
ap(mm)
加工参数计算公式

加工参数计算公式
加工参数计算公式是指在机械加工中,根据工件的特性和加工要求,计算出加工参数的公式。
主要包括以下内容:
1. 切削速度计算公式:切削速度=π×直径×转速÷60,其中π取3.14。
2. 进给速度计算公式:进给速度=每齿进给×齿数×转速,其中每齿进给指每个齿槽切削时的进给量,齿数指刀具上的齿数。
3. 切削深度计算公式:切削深度=每齿进给×齿数,其中每齿进给和齿数同上。
4. 切削力计算公式:切削力=切削力系数×主轴转矩÷刀具半径,其中切削力系数是由材料、切削参数等因素确定的常数。
5. 主轴转矩计算公式:主轴转矩=刀具力×刀具半径,其中刀具力由切削力计算公式得出。
6. 切削功率计算公式:切削功率=切削力×切削速度,其中切削力由切削力计算公式得出,切削速度同上。
通过以上公式计算出加工参数,可以保证机械加工过程中的效率和质量,提高生产效益。
- 1 -。
机械加工工时定额(车、铣、镗)切削用量参考表
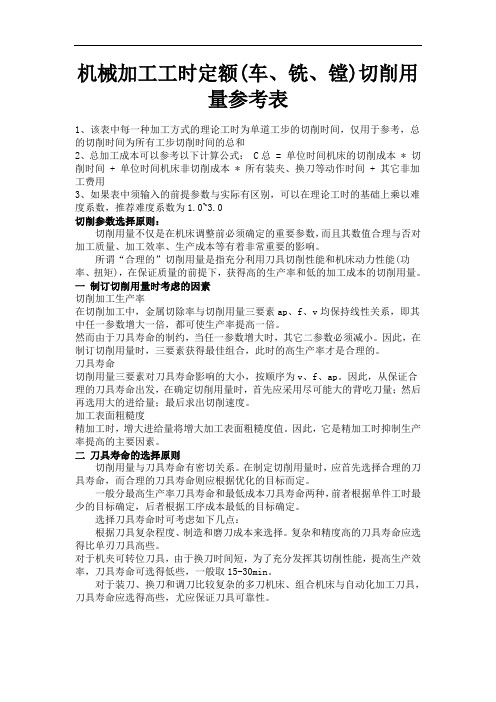
机械加工工时定额(车、铣、镗)切削用量参考表1、该表中每一种加工方式的理论工时为单道工步的切削时间,仅用于参考,总的切削时间为所有工步切削时间的总和2、总加工成本可以参考以下计算公式: C总 = 单位时间机床的切削成本 * 切削时间 + 单位时间机床非切削成本 * 所有装夹、换刀等动作时间 + 其它非加工费用3、如果表中须输入的前提参数与实际有区别,可以在理论工时的基础上乘以难度系数,推荐难度系数为1.0~3.0切削参数选择原则:切削用量不仅是在机床调整前必须确定的重要参数,而且其数值合理与否对加工质量、加工效率、生产成本等有着非常重要的影响。
所谓“合理的”切削用量是指充分利用刀具切削性能和机床动力性能(功率、扭矩),在保证质量的前提下,获得高的生产率和低的加工成本的切削用量。
一制订切削用量时考虑的因素切削加工生产率在切削加工中,金属切除率与切削用量三要素ap、f、v均保持线性关系,即其中任一参数增大一倍,都可使生产率提高一倍。
然而由于刀具寿命的制约,当任一参数增大时,其它二参数必须减小。
因此,在制订切削用量时,三要素获得最佳组合,此时的高生产率才是合理的。
刀具寿命切削用量三要素对刀具寿命影响的大小,按顺序为v、f、ap。
因此,从保证合理的刀具寿命出发,在确定切削用量时,首先应采用尽可能大的背吃刀量;然后再选用大的进给量;最后求出切削速度。
加工表面粗糙度精加工时,增大进给量将增大加工表面粗糙度值。
因此,它是精加工时抑制生产率提高的主要因素。
二刀具寿命的选择原则切削用量与刀具寿命有密切关系。
在制定切削用量时,应首先选择合理的刀具寿命,而合理的刀具寿命则应根据优化的目标而定。
一般分最高生产率刀具寿命和最低成本刀具寿命两种,前者根据单件工时最少的目标确定,后者根据工序成本最低的目标确定。
选择刀具寿命时可考虑如下几点:根据刀具复杂程度、制造和磨刀成本来选择。
复杂和精度高的刀具寿命应选得比单刃刀具高些。
对于机夹可转位刀具,由于换刀时间短,为了充分发挥其切削性能,提高生产效率,刀具寿命可选得低些,一般取15-30min。
切削参数计算公式
切削参数计算公式切削参数计算是机械加工中非常重要的一环,它决定了整个加工过程的效率和质量。
在进行切削参数计算时,需要考虑多个因素,如切削速度、进给速度、切削深度等。
下面我们将介绍一些常用的切削参数计算公式,帮助加工人员更好地确定合适的切削参数。
1.切削速度的计算公式:切削速度是指工件表面上单位时间内被切削刀具切削的长度,通常用m/min 来表示。
切削速度的计算公式为:Vc=π×D×n其中,Vc 为切削速度,单位为m/min;D 为刀具的直径,单位为mm;n 为主轴转速,单位为r/min。
2.进给速度的计算公式:进给速度是指切削刀具在工件上运动的速度,通常用mm/r 来表示。
进给速度的计算公式为:F=f×n其中,F 为进给速度,单位为mm/r;f 为每齿进给量,单位为mm,通常由刀具制造商提供;n 为主轴转速,单位为r/min。
3.切削深度的计算公式:切削深度是指刀具切入工件内部的深度,通常用mm 来表示。
切削深度的计算公式为:ae = ft×n其中,ae 为切削深度,单位为mm;ft 为切削时每齿的切削厚度,单位为mm;n 为主轴转速,单位为r/min。
4.主轴转速的计算公式:主轴转速是指主轴每分钟旋转的圈数,通常用r/min 来表示。
主轴转速的计算公式可以根据切削速度和刀具直径来确定,公式为:n=Vc/(π×D)其中,n 为主轴转速,单位为r/min;Vc 为切削速度,单位为m/min;D 为刀具的直径,单位为mm。
5.铣削切削力的计算公式:铣削切削力是在铣削过程中刀具对工件作用的力,通常用N(牛顿)来表示。
铣削切削力的计算公式为:Ft = Kc×ae×ap×fr其中,Ft 为铣削切削力,单位为N;Kc 为切削力系数;ae 为切削深度,单位为mm;ap 为轴向进给深度,单位为mm;fr 为切削速度,单位为mm/min。
切削参数s和f
切削参数s和f引言概述:切削参数s和f是在机械加工中非常重要的参数,它们对于加工质量和效率有着直接的影响。
s代表切削速度,即工件表面单位时间切削长度;f代表进给速度,即刀具单位时间切削的深度。
本文将从五个大点来详细阐述切削参数s和f的意义和影响。
正文内容:1. 切削参数s和f的定义和关系1.1 切削速度s的定义和计算方法1.2 进给速度f的定义和计算方法1.3 切削速度s和进给速度f的关系及其对加工质量的影响2. 切削参数s和f对加工表面质量的影响2.1 切削速度s对加工表面粗糙度的影响2.2 进给速度f对加工表面粗糙度的影响2.3 切削速度s和进给速度f的综合影响3. 切削参数s和f对切削力的影响3.1 切削速度s对切削力的影响3.2 进给速度f对切削力的影响3.3 切削速度s和进给速度f的综合影响4. 切削参数s和f对切削温度的影响4.1 切削速度s对切削温度的影响4.2 进给速度f对切削温度的影响4.3 切削速度s和进给速度f的综合影响5. 切削参数s和f对切削寿命的影响5.1 切削速度s对切削寿命的影响5.2 进给速度f对切削寿命的影响5.3 切削速度s和进给速度f的综合影响总结:综上所述,切削参数s和f在机械加工中具有重要的意义。
切削速度s和进给速度f的选择对于加工质量、表面质量、切削力、切削温度和切削寿命等方面都有着直接的影响。
合理选择切削参数s和f,能够提高加工效率,保证加工质量,延长刀具寿命,提高机械加工的整体效益。
因此,在实际加工中,我们应该根据具体情况合理选择切削参数s和f,以达到最佳的加工效果。
机械加工的切削参数
机械加工的切削参数机械加工是通过切削工具对工件进行削除材料的加工过程。
切削参数是指在机械加工过程中,用于控制切削过程的一些重要参数。
在机械加工中,选择合适的切削参数可以有效提高加工质量和生产效率。
本文将详细介绍机械加工的切削参数。
1. 加工速度(Cutting Speed)加工速度是指工件表面的任意点在切削过程中所接受到的线速度。
它与切削刀具转速和切削刀具直径有关。
加工速度的选择应根据工件材料、刀具材料和刀具类型来确定。
通常,应选择适当的加工速度,以保证加工表面质量的要求,同时避免刀具磨损过快。
2. 进给速度(Feed Rate)进给速度是指刀具相对于工件的线速度。
它与切削刃数、切削深度和加工速度有关。
进给速度的选择应根据工件材料、刀具材料和切削刃数来确定。
一般来说,进给速度应选取适当的值,以保证加工精度的要求,同时提高生产效率。
3. 切削深度(Cutting Depth)切削深度是指刀具进入工件的深度。
切削深度的选择应根据工件材料、刀具材料和加工要求来确定。
一般来说,切削深度不宜过大,以避免切削力过大引起刀具破损或加工表面质量下降。
4. 切削量(Cutting Amount)切削量是指单位时间内切削掉的工件材料体积。
切削量的选择应根据工件材料、刀具材料和加工要求来确定。
通常,切削量应合理选择,以提高生产效率,同时避免刀具磨损过快或加工表面质量下降。
5. 主轴速度(Spindle Speed)主轴速度是指切削刀具的转速。
主轴速度的选择应根据刀具材料、切削深度和切削量来确定。
合理选择主轴速度可以保证刀具的使用寿命和加工表面质量。
6. 切削角度(Cutting Angle)切削角度是指刀具刃口与切削方向之间的夹角。
切削角度的选择应根据工件材料、刀具材料和加工要求来确定。
合理选择切削角度可以提高切削效率和加工表面质量。
7. 切削液(Cutting Fluid)切削液是指在切削过程中加入的润滑冷却剂。
切削液的选择应根据工件材料、刀具材料和切削条件来确定。
机械加工切削全参数表
机械加工切削全参数表 Document serial number【UU89WT-UU98YT-UU8CB-UUUT-UUT108】常用材料机械加工切削参数推荐表共 26 页2015年9月目录1 切削用量选定原则选择机械加工切削用量就是指具体确定切削工序的切削深度、进给量、切削速度及刀具耐用度。
选择切削用量时,要综合考虑生产率、加工质量和加工成本。
从切削加工生产率考虑:切削深度、进给量、切削速度中任何一个参数增加一倍,都可提高生产率一倍。
从刀具耐用度考虑:应首先采用最大的切削深度,再选用大的进给量,然后根据确定的刀具耐用度选择切削速度。
从加工质量考虑:精加工时,采用较小的切削深度和进给量,采用较高的切削速度。
2 车削加工切削参数推荐表车削要素切削速度v:工件旋转的线速度,单位为m/min。
进给量f:工件每旋转一周,工件与刀具相对位移量,单位为mm/r。
切削深度a:垂直于进给运动方向测量的切削层横截面尺寸,单位为pmm。
Ra :以轮廓算术平均偏差评定的表面粗糙度参数,单位为μm。
d:工件直径,单位为mm。
w外圆车削示意图内圆车削示意图切削速度与转速关系:3.3181000nddnv ==π m/mindvd v n 3.3181000==π r/min v :切削速度,工件旋转的线速度,单位为m/min 。
n :工件的转速,单位为r/min 。
d :工件观察点直径,单位为mm 。
车削参数45钢热轧状态(硬度:187HB )外圆车削45钢热轧状态(硬度:187HB )内圆车削45钢调质状态(硬度:28~32HRC)外圆车削32HRC)内圆车削45钢调质状态(硬度:28~40Cr钢热轧状态(硬度:212HB)外圆车削40Cr钢热轧状态(硬度:212HB)内圆车削40Cr钢调质状态(硬度:28~32HRC)外圆车削28~32HRC)内圆车削40Cr钢调质状态(硬度:H62硬化状态(硬度:164HB)外圆车削H62硬化状态(硬度:164HB)内圆车削2A12-T4固溶处理并时效状态(硬度:105HB)外圆车削2A12-T4固溶处理并时效状态(硬度:105HB)内圆车削TC4固溶处理并时效状态(硬度:320~380HB)外圆车削380HB)内圆车削TC4固溶处理并时效状态(硬度:320~3 铣削加工切削参数推荐表 铣削要素铣削速度v :铣刀旋转运动的线速度,单位为m/min 。
- 1、下载文档前请自行甄别文档内容的完整性,平台不提供额外的编辑、内容补充、找答案等附加服务。
- 2、"仅部分预览"的文档,不可在线预览部分如存在完整性等问题,可反馈申请退款(可完整预览的文档不适用该条件!)。
- 3、如文档侵犯您的权益,请联系客服反馈,我们会尽快为您处理(人工客服工作时间:9:00-18:30)。
教师姓名授课形式讲授授课时数1授课日期年月日授课班级
授课项目及任务名称
第四章切削加工基础
第二节机械加工的切削参数
教学目标知识目
标
掌握切削用量的三要素。
掌握切削用量的选择原则。
技能目
标
学会正确的选用切削用量。
教学重点切削运动三要素、切削用量的选择原则教学难点三要素的含义、选择原则
教学方法教学手段
借助于多媒体课件和相关动画及视频,详细教授切削运动三要素、切削用量的选择原则等基础知识。
教师先通过PPT课件进行理论知识讲解,再利用相关动画和视频进行演示,让学生能够将理论知识转化成实践经验。
同时学生根据所学内容,完成知识的积累,为以后的实践实训打下基础。
学时安排1.切削三要素约30分钟;
2.切削用量选择约15分钟;
教学条件多媒体设备、多媒体课件。
课外作业查阅、收集切削用量的相关资料。
检查方法随堂提问,按效果计平时成绩。
教学后记
授课主要内容
第二节机械加工的切削参数
机械加工的切削是切削进程中不可缺少的因素。
主要是指切削用量要素。
切削用量要素主要包括:切削速度vc、进给量f 和切削深度ap.
一、切削用量要素
切削用量要素一般是指切削用量三要素:切削速度vc、进给量f 和切削深度ap.
在切削加工时,首先选取尽可能大的切削深度,其次是尽可能大的进给量,最后确定切削速度。
1.切削速度vc
含义:是切削加工时刀具切削刃上的某一点相对于待加工表面在主运动方向上的瞬时速度。
计算:
vc=πdn/1000
Vc:切削速度(m/min)
d:工件待加工表面的直径(最大直径,mm)
n:工件的转速(r/min)
主运动为直线时,则为直线运动速度(如刨削)
2.进给量 f
在工件或刀具的每一转或每一往复行程的时间内,刀具与工件之间沿进给运动方向的相对位移。
通常用表示,单位为mm/r或mm/行程
3.背吃刀量(切削深度)ap
含义:工件待加工表面与已加工表面的垂直距离
计算
ap=(dw-dm)/2
ap:背吃刀量(mm)
dw:工件待加工表面直径(mm)
dm:工件已加工表面直径(mm)
二、切削用量的选择
切削三要素中影响刀具耐用度最大的是切削速度,其次是进给量,最小的是切削深度,所在,在选择切削用量时,首先选择最大的切削深度,其次是选用较大的进给量,最后是选定合理的切削速度。
另外,在选择切削用量时,应注意考虑以下因素:
(1)根据零件直径、加工余量和机床、刀具精度等来选择切削用量。
(2)根据刀具材料、焊接质量和机床、刀具的刃磨条件来选择切削用量。
(3)根据各类毛坯的硬度。
任务小结
回顾本次任务所学知识,强调本节课的重点与难点,本课主要讲解切削运动三要素、切削用量的选择原则等基础知识。
学习评价
以学习过程当中学生的现场任务完成情况为基础,结合学生的课堂学习接收能力,作为计入平时成绩依据。
课后作业
简述切削用量的三要素?。