立式加工中心机床的螺距误差补偿
华中8型数控系统的数控机床螺距误差补偿

测量光束 厂 ]
l 1
厂
一 .
I
,
绪 l
l
1
图 1 激光干涉仪误差测量系统 学 组件沿线 性轴移动 。通过 监测测量 光束 和参考光束 之 间的
光 路差异 的变化 , 产生定位 精度测量值 。 它是两个 光学组件 之
个两个补偿参 量设 置了专 门的参数 , 供坐标轴的误差补偿之用 。
件在工作时不能达 到预定 的位置而产生误差 。通常称此误差为 螺距误差。螺距误差 的补偿分为实时动态补偿 与静态补偿两种 方式。
通 常, 将反射镜设定为移动光学部件 , 将干涉镜设定为静止
部件 。 二者可以反过来 , 但是最大测量距离将缩短 。 因此 , 在长轴 测量 时 , 通常线性 干涉镜静止不动 , 而另一个反射镜移动。在短 轴测量 时, 为了方便 可以反置 。
相应 增加 。
8 1 8 B 数控 系统立式加工 中心 X轴为例 , 介绍螺距误差的测量与
补偿 。
静态均化补偿控制方法 ,是事先将螺距误差 的补偿值存 储
在数控 系统参数表 中, 待补偿值生效后 , 数控系统 自 动将 目 标 位 置的补偿值叠加到插补指令上 , 实现螺距误差的补偿 。
、
螺 距 误 差 与 补 偿
一
方面 ,由于滚珠丝杠螺母副受加工设备精度及加工条件
间的差异测 量值 , 与X L激光头 的位 置无关 。此测 量值 可以与 被 测机床坐 标轴定位 系统上 的读数 比较 ,获得坐标 轴 的精 度
误差。
变化的影响 , 滚 珠丝杠都存在螺距误差 ; 另一 方面 , 由于数控机 床安装时 , 丝杠和螺母未能预紧到理想状态 , 也会使机床运动部
立式加工中心机床的螺距误差补偿(精)

立式加工中心机床的螺距误差补偿随着我国制造业的飞速发展,数控机床制造技术也在不断地发展,同时对数控机床的各项性能提出了越来越高的要求。
机床的定位精度便成为了衡量机床性能的一项重要指标。
机械结构当中不可避免的摩擦、间隙,以及装配误差成为了制约机床定位精度的主要因素。
由此,数控系统的制造商开发出了螺距误差补偿功能,借此以消除或者削弱以上因素对机床定位精度的影响,从而达到更好的加工效果。
发那科与西门子两大公司在这个领域表现得尤为出色,以下将对这两种数控系统的螺距误差补偿方法进行详细介绍。
1.发那科数控系统机床的误差补偿(以FANUC 0i-MD为例)1.1基本概念1.1.1补偿点的指定各轴的补偿点的指定,可通过夹着参考点的补偿点编号指定(+)侧、(-)侧来进行。
机械的行程超过(+)侧、(-)侧所指定的范围时,有关超出的范围,不进行螺距误差补偿(补偿量全都成为0)。
1.1.2补偿点号补偿点数,在螺距误差设定画面上提供有共计1024 点,从0 到1023。
通过参数将该编号任意分配给各轴。
另外,螺距误差设定画面中,在最靠近负侧的补偿号前,显示该轴的名称。
1.1.3补偿点的间隔螺距误差补偿的补偿点为等间隔,在参数中为每个轴设定该间隔。
螺距误差补偿点的间隔有最小值限制,通过下式确定。
螺距误差补偿点间隔的最小值=最大进给速度(快速移动速度)÷75001.2相关参数(1)1851 每个轴的反向间隙补偿量。
(2)1852 每个轴的快速移动时的反向间隙补偿量。
(3)3620 每个轴的参考点的螺距误差补偿点号。
(4)3621 每个轴的最靠近负侧的螺距误差补偿点号。
(5)3622 每个轴的最靠近正侧的螺距误差补偿点号。
(6)3623 每个轴的螺距误差补偿倍率。
(7)3624 每个轴的螺距误差补偿点间隔。
注:以上参数中3620,3621,3622,3624修改后需要切断电源并重新上电才生效,其余参数修改后复位即可生效。
有关加工中心螺距补偿的方法
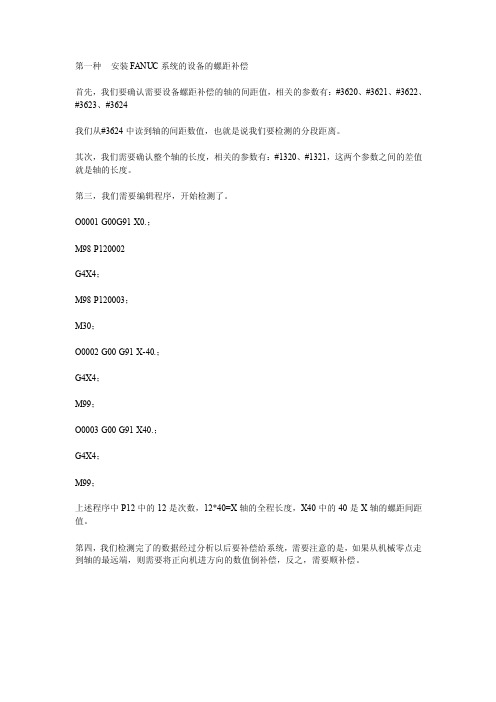
第一种安装FANUC系统的设备的螺距补偿首先,我们要确认需要设备螺距补偿的轴的间距值,相关的参数有:#3620、#3621、#3622、#3623、#3624我们从#3624中读到轴的间距数值,也就是说我们要检测的分段距离。
其次,我们需要确认整个轴的长度,相关的参数有:#1320、#1321,这两个参数之间的差值就是轴的长度。
第三,我们需要编辑程序,开始检测了。
O0001 G00G91 X0.;M98 P120002G4X4;M98 P120003;M30;O0002 G00 G91 X-40.;G4X4;M99;O0003 G00 G91 X40.;G4X4;M99;上述程序中P12中的12是次数,12*40=X轴的全程长度,X40中的40是X轴的螺距间距值。
第四,我们检测完了的数据经过分析以后要补偿给系统,需要注意的是,如果从机械零点走到轴的最远端,则需要将正向机进方向的数值倒补偿,反之,需要顺补偿。
第二种安装三菱系统的设备的螺距补偿开始的两个步骤都一致,我们只要确认了轴的全长和间距值就可以了。
第三,编辑程序O0000 G91G28X0.;G90G0X0.5;G4X1;G00X0.;G4X6;M98 P11L20;G90G0X-800.5;G4X1;G00X-800.;G4X6;M98 P12L20;M99;O0011 G91G0X0.;X-40.;G4X4;M99;O0022 G91G0X0.;X40.;G4X4;M99;第四,我们选择从机械0到-800处的检测顺序。
检测出来的数据分为两页,正向20点,负向20点,第一页中补偿负向的数值,并且从#127开始倒序补入,补偿的数值需要乘2。
第二页中补偿正向的数值,并且从#256开始倒序补入,补偿的数值需要乘2。
轮回式双向螺距误差补偿方法_游华云

补偿表中查找相匹配的位置。在绝大多数情况下 , 反 馈位置应当在补偿表中相邻两个补偿点之间 。 数控 系统在这两个补偿点之间进行线性插值 , 得到当前 伺服周期的补偿值: C ( x ) = - Em X
m + 1
Xm ( Em+ - Xm
1
- Em ) . ( 5)
其中 : X m < x < X m+ 1 , 0 < m < m+ 1 < n。 然后利用这个补偿值对坐标位置进行修正 , 使 之与指令位置保持一致。 参见图 1 。
对于半闭环数控机床 , 机床的定位误差占整个 加工误差的 50 % ~ 60 % [1 ]。 而影响机床定位精度的 主要因素有机床几何精度、 伺服控制精度、 测量系统 的精度以及环境温度波动等 。 对机床零部件经过设
游华云 , 等 : 轮回式双向螺距误差补偿方法
1457
行轨迹控制 , 但滚珠丝杠的螺距不可能绝对准确 , 加 上热、 摩擦以及扭矩等的作用 , 势必存在误差 , 直接 导致机床定位误差 。 在目前的数控系统中 , 通常在丝杠的整个行程 上 , 预先测得平均反向间隙值。 当坐标轴改变方向 时 , 将反向间隙值加到反馈位置增量中 ,以补偿因反 向间隙引起的空走行程 , 从而使坐标轴在正反方向 的定位精度保持一致。 然后对正向螺距误差进行补 偿 , 使坐标轴正向行程的实际位置与指令位置的偏 差尽可能小。由于正反向定位精度的一致性 , 因此反 向定位精度得到保证。 这种方法假定丝杠反向间隙处处相等 , 偏离实 际情况 , 补偿效果差 , 而 且需要反复多次测量和计 算 , 补偿工作量较大。 本文提出的双向螺距误差补偿 方法可以通过一次性测量 , 实现对正 、反方向的螺距 误差补偿 , 有效地解决了丝杠反向间隙处处不等的 问题 ,获得了更高的补偿精度。 1. 2 双向螺距误差补偿 该方法的基本原理如下 : 1) 测量实际位置 。根据数控系统负载情况确定 每个坐标轴的补偿点数 n , 从而确定各坐标轴的补 偿间隔 S。 以坐标轴的参考点为测量基准点 , 分别 以 S 为间隔测量各补偿点的实际位置 , 正反两个方 向分别测量若干组数据 。 最后计算得到正反方向两 组实际位置的平均值 X mea、 X mea: X m ea = { X i | i = 0, 1,… , n } , X m ea = { X i | i = 0, 1,… , n }.
螺距误差补偿

一、螺距误差产生原因
①滚珠丝杆副处在进给系统传动链的末级,丝杆和螺母存在各种误差,如螺距累积误差、螺纹滚道型面误差、直径尺寸误差等,其中丝杆的螺距累积误差会造成机床目标值偏差。
②滚珠丝杆在装配过程中,由于采用了双支承结构,使丝杆轴向拉长,造成丝杆螺距误差增加,产生机床目标值偏差。
③在机床装配过程中,丝杆轴线与机床导轨平行度的误差会引起机床目标值偏差。
二、螺距误差补偿的作用
螺距误差补偿通过调整数控系统的参数增减指令值的脉冲数,实现机床实际距离与指令移动距离相接近,以提高机床的定位精度。
螺距误差补偿只对机床补偿段起作用,在数控系统允许的范围内起到补偿作用。
9.1 螺距误差补偿[共2页]
![9.1 螺距误差补偿[共2页]](https://img.taocdn.com/s3/m/9edc6295a8956bec0975e3f8.png)
第9章系统补偿功能与SIMODRIVE611D驱动优化
机床在对工件进行加工的过程中,由于测量系统、力的传递过程中产生的误差、机床自身磨损或装配工艺问题的影响,加工工件的轮廓会偏离理想的几何曲线,导致加工工件产品质量的下降。
特别是在加工大型的工件时,由于温度和机械力的影响,加工精度损失更为严重。
因而在机床出厂前,需要进行一定的误差补偿。
螺距误差补偿和反向间隙补偿是两种最常见的补偿方式,还有温度补偿、垂直度补偿、跟随误差补偿以及摩擦补偿也比较常见。
另外,在机械传动结构良好的情况下,要使机械系统与电气系统达到更加良好的匹配,需要通过驱动优化来实现。
9.1 螺距误差补偿
螺距误差的补偿是按坐标轴来进行的,轴的补偿曲线如图9-1所示。
图9-1 轴的补偿曲线
激活误差补偿需设定以下相关机床参数。
① MD 38000 轴最大误差补偿点数。
根据该机床的特点,X轴螺距误差参数补偿点数为50,即MD 38000 [0 AX1] =50;Z轴螺距误差补偿点数为100,即MD 38000 [0 AX2] =100。
参数设定好后,系统自动产生相应轴的补偿文件,补偿文件存放在目录/NC-ACTIVE-DATA/Meas-System-err-comp下。
可以修改每轴的补偿点数。
如果改变MD38000,系统会在下一次上电时重新对内存进行分配。
建议在修改该参数之前,备份已存在的零件加工程序、R 参数和刀具参数的驱动数据。
② MD32700螺距误差补偿使能。
MD32700=0 螺距补偿不生效,允许修改补偿文件。
【豆丁-免费】-》数控机床螺距误差补偿与分析

文章编号:1001-2265(2010)02-0098-04收稿日期:2009-09-29;修回日期:2009-10-26作者简介:李继中(1963—),男,湖南人,深圳职业技术学院高级工程师,副处长,从事数控技术研究,(E -mail )ljizhong@szp t .edu .cn 。
数控机床螺距误差补偿与分析李继中(深圳职业技术学院,深圳 518055)摘要:文章通过实例介绍数控机床滚珠丝杆传动机构的螺距误差的测量、补偿依据、补偿方法与操作要点,以及补偿效果的验证与分析。
通过利用英国REN I SHAW 公司的ML10激光干涉仪对F ANUC 0i 系统数控铣床X 轴的螺距误差进行测量、补偿及验证,结果说明,对滚珠丝杆传动机构的反向偏差与螺距误差进行补偿是提高机床精度的一种重要手段。
关键词:滚珠丝杆;螺距误差;反向偏差;补偿;定位精度;激光干涉仪中图分类号:TH16;TG65 文献标识码:AThe Com pen s a ti on and Ana lysis of P itch Error for NC M ach i n i n g ToolsL I J i 2zhong(Shenzhen Polytechnic,Shenzhen 518055,China )Abstract:22、’2Key words:0 引言目前,机床的传动机构一般均为滚珠丝杆副。
当机床几何精度得到保证后,机床轴线的反向偏差与滚珠丝杆的螺距误差是影响机床定位精度与重复定位精度的主要因素,对机床轴线的反向偏差、滚珠丝杆的螺距误差进行补偿能极大地提高机床精度,机床控制系统也对这个两个补偿参量设置了专门的参数,供轴线误差补偿之用,并将其补偿功能作为控制系统的基本控制功能。
1 螺距误差的补偿方式由于加工设备的精度及加工条件的变化影响,滚珠丝杆都存在螺距误差。
螺距误差补偿对开环控制系统和半闭环控制系统具有显著的效果,可明显提高系统的定位精度和重复定位精度;对于全闭环控制系统,由于其控制精度高,螺距误差补偿效果不突出,但也可以进行螺距误差补偿,以便提高控制系统的动态特性,缩短机床的调试时间。
13、螺距误差补偿及反向间隙补偿

螺距误差补偿及反向间隙补偿根据下表设置螺距误差补偿相关参数:参数号参数位设定值设置说明3620 XZ 100200每个轴的参考点的螺距误差补偿点号3621 XZ 负方向最远的补偿位置号根据下面的公式进行计算:参考点的补偿位置号—(负方向的机床行程/补偿位置间隔)+ 1 100-(1000/50)+1=81 所以负方向补偿位置号设置为813622 XZ 正方向的最远补偿位置号根据下面的公式进行计算:参考点的补偿位置号+(正方向的机床行程/补偿位置间隔)+ 1 100+(0/50)+1=101 所以参考点正方向补偿位置号为101.3624 补偿点间隔输入格式为无小数点输入格式,由于X轴为直径值编程,所以X轴补偿点间隔应为实际补偿点间隔的2倍,应设置为100000,为100mm.参数号参数位设定值设置说明1800 #4(RBK) 是否分别进行切削进给/快速移动反向间隙补偿0: 不进行。
1: 进行。
1851 XZ 每个轴的反向间隙补偿量,设置后,回零生效1852 XZ 每个轴的快速移动时的反向间隙补偿量,回零生效由于FANUC系统螺距误差补偿采用增量式的补偿方式,所以在进行螺距误差补偿时,需根据补偿数据进行补偿数据的设定个。
下表为螺距误差补偿表由于每个补偿点的最大补偿值只能到7,在上表中可以看到,在-400mm测量位置处出现了一次22的值,此点是所有补偿点误差的最大值,所以补偿倍率按此点进行计算,而且考虑其它点的误差值,将补偿倍率设置为3倍。
补偿倍率设置为3倍,所有的补偿值都放大了三倍,所以在补偿数据处看到的是计算值的1/3,如果测量人员给出的是补偿值,那么补偿数据就按上图中的数据进行输入,如果给出的是误差值,则需将上图中的补偿数据取反。
螺距误差补偿在回零后即可生效。
- 1、下载文档前请自行甄别文档内容的完整性,平台不提供额外的编辑、内容补充、找答案等附加服务。
- 2、"仅部分预览"的文档,不可在线预览部分如存在完整性等问题,可反馈申请退款(可完整预览的文档不适用该条件!)。
- 3、如文档侵犯您的权益,请联系客服反馈,我们会尽快为您处理(人工客服工作时间:9:00-18:30)。
立式加工中心机床的螺距误差补偿
随着我国制造业的飞速发展,数控机床制造技术也在不断地发展,同时对数控机床的各项性能提出了越来越高的要求。
机床的定位精度便成为了衡量机床性能的一项重要指标。
机械结构当中不可避免的摩擦、间隙,以及装配误差成为了制约机床定位精度的主要因素。
由此,数控系统的制造商开发出了螺距误差补偿功能,借此以消除或者削弱以上因素对机床定位精度的影响,从而达到更好的加工效果。
发那科与西门子两大公司在这个领域表现得尤为出色,以下将对这两种数控系统的螺距误差补偿方法进行详细介绍。
1.发那科数控系统机床的误差补偿(以FANUC 0i-MD为例)
1.1基本概念
1.1.1补偿点的指定
各轴的补偿点的指定,可通过夹着参考点的补偿点编号指定(+)侧、(-)侧来进行。
机械的行程超过(+)侧、(-)侧所指定的范围时,有关超出的范围,不进行螺距误差补偿(补偿量全都成为0)。
1.1.2补偿点号
补偿点数,在螺距误差设定画面上提供有共计1024 点,从0 到1023。
通过参数将该编号任意分配给各轴。
另外,螺距误差设定画面中,在最靠近负侧的补偿号前,显示该轴的名称。
1.1.3补偿点的间隔
螺距误差补偿的补偿点为等间隔,在参数中为每个轴设定该间隔。
螺距误差补偿点的间隔有最小值限制,通过下式确定。
螺距误差补偿点间隔的最小值=最大进给速度(快速移动速度)÷7500
1.2相关参数
(1)1851 每个轴的反向间隙补偿量。
(2)1852 每个轴的快速移动时的反向间隙补偿量。
(3)3620 每个轴的参考点的螺距误差补偿点号。
(4)3621 每个轴的最靠近负侧的螺距误差补偿点号。
(5)3622 每个轴的最靠近正侧的螺距误差补偿点号。
(6)3623 每个轴的螺距误差补偿倍率。
(7)3624 每个轴的螺距误差补偿点间隔。
注:以上参数中3620,3621,3622,3624修改后需要切断电源并重新上电才生效,其余参数修改后复位即可生效。
1.3操作方法(以X轴行程为850mm的丝杠为例,全长采集20个数据)
1.3.1连接激光干涉仪
1.3.2设置参数
(1)1851,1852都设置为0,确保第一次数据采集时反向间隙为0。
(2)3620设置为1,表示X轴的补偿值以补偿数据表中的第1号为参考点。
(3)3621设置为1,表示X轴的补偿值从补偿数据表的第1号开始。
(4)3622设置为21,由于全长一共补偿20个数据,且从螺补数据表中的第1号开始,所以此参数设置为21。
(5)3623设置为1,表示补偿值的倍率为1倍,实际补偿值=补偿值*补偿倍率。
(6)3624设置为42.500,全长为850mm,共补偿20个数据,850/20=42.5。
(7)将螺距误差设定画面(进入方法:system键→扩展键→螺补)所有值都设置为0。
1.3.3运行螺距补偿程序并通过激光干涉仪采集数据,程序如下:
#3=0
N3 G0 G90 G54 X0
#1=0
#2=0
G4X4
N1 G0 G91 X85
#1=#1+1
G4 X6
IF [#1 LT 10] GOTO 1
N2 G0 G91 X-85
#2=#2+1
G4 X4
IF [#2 LT 10] GOTO 2
#3=#3+1
IF [#3 LT 5] GOTO 3
M30
1.3.4调试人员对激光干涉仪采集的数据进行分析得出补偿数据,并将补偿数据输入数控系统。
(1)将反向间隙输入参数1851与1852中,数值单位为1/1000mm。
(2)在螺距误差设定画面(进入方法:system键→扩展键→螺补)输入补偿值,每一点的补偿值为该点的实际偏差与前一点实际偏差的差值,注意:实际补偿值=输入补偿值*补偿倍率。
(3)将机床复位。
1.3.5再次运行螺补程序验证补偿结果是否合乎要求。
2.西门子数控系统机床的误差补偿(以SIMENS 828D为例)
2.1相关参数
(1)32450 反向间隙补偿值。
(2)32700 螺距误差补偿生效。
注:以上参数修改后需要复位才可以生效。
2.2操作方法(以X轴行程为850mm的丝杠为例,全长采集10个数据)
2.2.1连接激光干涉仪
2.2.2正确设置参数
(1)将32450设置为0,确保第一次数据采集时反向间隙为0。
(2)将32700设置为0,并按下复位键。
(3)编辑补偿文件,补偿文件的存储位置为:菜单选择→调试→系统数据→NC数据→NC 生效数据→测量系统误差补偿。
编辑后补偿文件内容如下:
$AA_ENC_COMP[0,0,AX1]=0.00
$AA_ENC_COMP[0,1,AX1]=0.00
$AA_ENC_COMP[0,2,AX1]=0.00
…………
$AA_ENC_COMP[0,29,AX1]=0.00
$AA_ENC_COMP[0,30,AX1]=0.00
$AA_ENC_COMP_STEP[0,AX1]=85
$AA_ENC_COMP_MIN[0,AX1]=0
$AA_ENC_COMP_MAX[0,AX1]=850
$AA_ENC_COMP_IS_MODULO[0,AX1]=0
M17
其中,$AA_ENC_COMP_STEP[0,AX1]=85表示补偿间隔为85mm。
$AA_ENC_COMP_MIN[0,AX1]=0表述补偿数据的起始位置为X=0。
$AA_ENC_COMP_MAX[0,AX1]=850表示补偿数据的终止位置为X=850。
$AA_ENC_COMP_IS_MODULO[0,AX1]=0表示补(下转第70页)(上接第38页)偿轴为直线轴。
(4)将补偿文件复制到零件程序目录下,并在自动方式下运行AX1_EEC.MPF 程序。
(5)将将32700设置为1,然后重启系统,返回参考点后补偿值生效。
2.2.3运行螺距补偿程序并通过激光干涉仪采集数据,程序如下:
AA:R1=0
R2=0
R3=0
G54 G90 G0 X0
G4 F5
BB:G0 G91 X85
G4 F5
R1=R1+1
IF R1<10 GOTOB BB
G4F5
CC:G0 G91 X-85
G4 F5
R2=R2+1
IF R2<10 GOTOB CC
R3=R3+1
G4 F5
IF R3<5 GOTOB AA
M02
2.2.4调试人员对激光干涉仪采集的数据进行分析得出补偿数据,并将补偿数据输入数控系统。
(1)将反向间隙输入参数32450中,数值单位为1/1000mm。
(2)将32700设置为0,并按下复位键。
(3)编辑补偿文件,将激光干涉仪采集的数据输入到相对应的补偿文件中。
(4)在自动方式下运行AX1_EEC.MPF 程序。
(5)将将32700设置为1,然后重启系统,返回参考点后补偿值生效。
2.2.5再次运行螺补程序验证补偿结果是否合乎要求。
3.总结
虽然数控系统的螺距误差补偿功能可以在一定程度下削弱装配误差对机床定位精度的影响,但先进的机械设计与合理的装配工艺才是影响机床加工精度的决定因素。
因此,当螺距误差较大的时候,还是首先要进行机械维修,将螺距误差控制在一个比较小的范围后在进行螺距误差补偿,以达到精益求精的效果。