汽车液压盘式制动器结构优化项目设计方案
紧凑型轿车盘式制动器设计优化方案探究
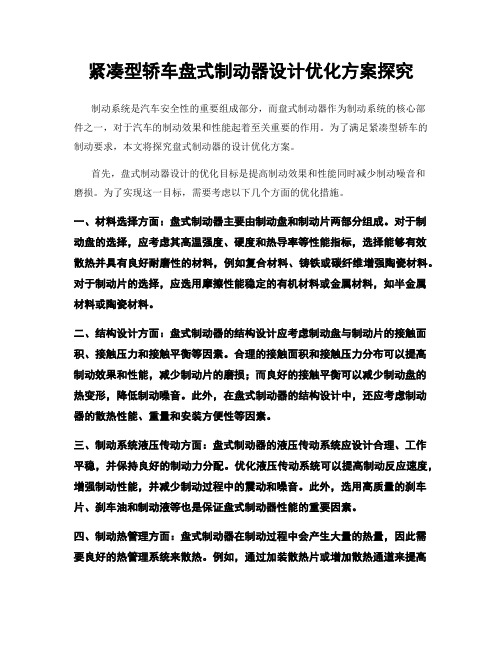
紧凑型轿车盘式制动器设计优化方案探究制动系统是汽车安全性的重要组成部分,而盘式制动器作为制动系统的核心部件之一,对于汽车的制动效果和性能起着至关重要的作用。
为了满足紧凑型轿车的制动要求,本文将探究盘式制动器的设计优化方案。
首先,盘式制动器设计的优化目标是提高制动效果和性能同时减少制动噪音和磨损。
为了实现这一目标,需要考虑以下几个方面的优化措施。
一、材料选择方面:盘式制动器主要由制动盘和制动片两部分组成。
对于制动盘的选择,应考虑其高温强度、硬度和热导率等性能指标,选择能够有效散热并具有良好耐磨性的材料,例如复合材料、铸铁或碳纤维增强陶瓷材料。
对于制动片的选择,应选用摩擦性能稳定的有机材料或金属材料,如半金属材料或陶瓷材料。
二、结构设计方面:盘式制动器的结构设计应考虑制动盘与制动片的接触面积、接触压力和接触平衡等因素。
合理的接触面积和接触压力分布可以提高制动效果和性能,减少制动片的磨损;而良好的接触平衡可以减少制动盘的热变形,降低制动噪音。
此外,在盘式制动器的结构设计中,还应考虑制动器的散热性能、重量和安装方便性等因素。
三、制动系统液压传动方面:盘式制动器的液压传动系统应设计合理、工作平稳,并保持良好的制动力分配。
优化液压传动系统可以提高制动反应速度,增强制动性能,并减少制动过程中的震动和噪音。
此外,选用高质量的刹车片、刹车油和制动液等也是保证盘式制动器性能的重要因素。
四、制动热管理方面:盘式制动器在制动过程中会产生大量的热量,因此需要良好的热管理系统来散热。
例如,通过加装散热片或增加散热通道来提高散热效果;同时,合理选择制动盘和制动片的材料,以提高其耐热性能,减少热膨胀和热衰减对制动性能的影响。
综上所述,紧凑型轿车盘式制动器的设计优化方案涉及材料选择、结构设计、液压传动和热管理等多个方面。
通过合理选择材料、改善结构设计、优化液压传动系统和加强热管理,可以提高制动效果和性能,减少制动噪音和磨损,进而提高紧凑型轿车的整体安全性和驾驶体验。
紧凑型轿车盘式制动器设计的结构优化与性能提升
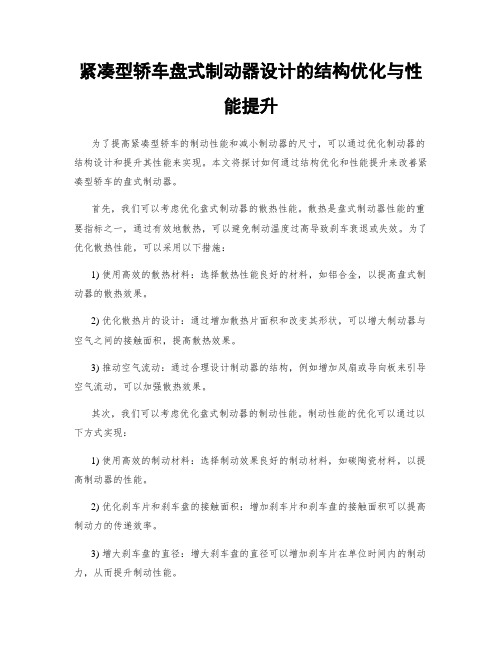
紧凑型轿车盘式制动器设计的结构优化与性能提升为了提高紧凑型轿车的制动性能和减小制动器的尺寸,可以通过优化制动器的结构设计和提升其性能来实现。
本文将探讨如何通过结构优化和性能提升来改善紧凑型轿车的盘式制动器。
首先,我们可以考虑优化盘式制动器的散热性能。
散热是盘式制动器性能的重要指标之一,通过有效地散热,可以避免制动温度过高导致刹车衰退或失效。
为了优化散热性能,可以采用以下措施:1) 使用高效的散热材料:选择散热性能良好的材料,如铝合金,以提高盘式制动器的散热效果。
2) 优化散热片的设计:通过增加散热片面积和改变其形状,可以增大制动器与空气之间的接触面积,提高散热效果。
3) 推动空气流动:通过合理设计制动器的结构,例如增加风扇或导向板来引导空气流动,可以加强散热效果。
其次,我们可以考虑优化盘式制动器的制动性能。
制动性能的优化可以通过以下方式实现:1) 使用高效的制动材料:选择制动效果良好的制动材料,如碳陶瓷材料,以提高制动器的性能。
2) 优化刹车片和刹车盘的接触面积:增加刹车片和刹车盘的接触面积可以提高制动力的传递效率。
3) 增大刹车盘的直径:增大刹车盘的直径可以增加刹车片在单位时间内的制动力,从而提升制动性能。
最后,还可以考虑优化盘式制动器的结构设计。
通过合理设计制动器的结构,可以减小制动器的尺寸,并提升其性能。
1) 采用轻量化设计:通过使用轻量化材料和减少不必要的结构部件,可以减小制动器的重量,提高轮毂的悬挂性能。
2) 优化制动器的结构强度:通过合理设计制动器的结构,提高制动器的结构强度,减小制动器的变形和振动,从而提高制动器的性能和寿命。
总之,通过结构优化和性能提升,可以改善紧凑型轿车的盘式制动器。
通过优化散热性能、提升制动性能和优化结构设计,可以提高制动器的性能和安全性,满足紧凑型轿车的制动需求。
基于紧凑型轿车需求的盘式制动器优化设计
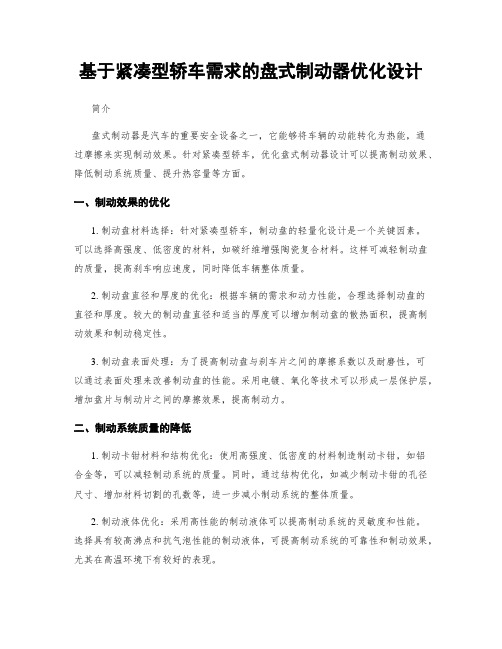
基于紧凑型轿车需求的盘式制动器优化设计简介盘式制动器是汽车的重要安全设备之一,它能够将车辆的动能转化为热能,通过摩擦来实现制动效果。
针对紧凑型轿车,优化盘式制动器设计可以提高制动效果、降低制动系统质量、提升热容量等方面。
一、制动效果的优化1. 制动盘材料选择:针对紧凑型轿车,制动盘的轻量化设计是一个关键因素。
可以选择高强度、低密度的材料,如碳纤维增强陶瓷复合材料。
这样可减轻制动盘的质量,提高刹车响应速度,同时降低车辆整体质量。
2. 制动盘直径和厚度的优化:根据车辆的需求和动力性能,合理选择制动盘的直径和厚度。
较大的制动盘直径和适当的厚度可以增加制动盘的散热面积,提高制动效果和制动稳定性。
3. 制动盘表面处理:为了提高制动盘与刹车片之间的摩擦系数以及耐磨性,可以通过表面处理来改善制动盘的性能。
采用电镀、氧化等技术可以形成一层保护层,增加盘片与制动片之间的摩擦效果,提高制动力。
二、制动系统质量的降低1. 制动卡钳材料和结构优化:使用高强度、低密度的材料制造制动卡钳,如铝合金等,可以减轻制动系统的质量。
同时,通过结构优化,如减少制动卡钳的孔径尺寸、增加材料切割的孔数等,进一步减小制动系统的整体质量。
2. 制动液体优化:采用高性能的制动液体可以提高制动系统的灵敏度和性能。
选择具有较高沸点和抗气泡性能的制动液体,可提高制动系统的可靠性和制动效果,尤其在高温环境下有较好的表现。
三、热容量的提升1. 制动系统散热设计:为了提高制动系统的热容量,可以在设计中合理设置散热片和通风孔,加强制动系统的散热效果。
通过增加散热片的面积和适当设置通风孔,能够快速散热,降低制动系统的温度,提高制动性能。
2. 制动盘内部通风片设计:在制动盘内部加入通风片,可以提高制动盘的内部空气流通性,增加散热效果。
通过通风片的设计,能够使热量更加迅速地从制动盘中散发出来,提高制动能力和稳定性。
结论基于紧凑型轿车需求的盘式制动器优化设计是为了提高制动效果、降低制动系统质量、提升热容量等方面。
基于力学原理的紧凑型轿车盘式制动器设计与优化

基于力学原理的紧凑型轿车盘式制动器设计与优化轿车盘式制动器是现代汽车制动系统中的重要组成部分,它通过摩擦阻力将动能转化为热能,实现汽车的制动功能。
本文将基于力学原理,针对紧凑型轿车盘式制动器进行设计与优化。
首先,我们来了解一下盘式制动器的工作原理。
盘式制动器由制动盘、制动片和制动钳等部件组成。
当驾驶员踩下制动踏板时,制动钳内的活塞向制动片施加力,使制动片与制动盘产生摩擦,从而减速或停止车辆。
基于这一工作原理,我们可以通过以下几个方面对紧凑型轿车盘式制动器进行设计与优化。
首先,制动盘的选材和结构设计对制动性能有着重要影响。
在选材方面,盘式制动器的制动盘通常采用铸铁或钢材料,它们具有良好的导热性和抗热膨胀性能。
而轻量化和耐热性更高的复合材料也在近年来得到了广泛应用。
在结构设计方面,可以通过增加制动盘的通风孔或凹槽等形式提高散热效果,进一步提升制动性能。
其次,制动片的材料选择和形状设计对制动效果有着重要影响。
常见的制动片材料包括有机材料、半金属材料和陶瓷材料等。
有机材料具有制动平稳、噪音低的特点,而半金属材料则具有耐高温、制动力强的特点。
陶瓷材料则具有重量轻、耐磨损、制动效果稳定的特点,但成本较高。
通过合理选择制动片材料,并对其形状进行优化,可以提高制动性能和寿命,降低噪音和磨损。
此外,制动钳的设计也是影响制动器性能的关键因素之一。
制动钳需要具备足够的刚性、力量和稳定性,以确保制动片与制动盘之间的良好接触和压力均匀分布。
同时,合理设计制动钳的传力结构和减震装置,可以提高制动效果,并降低制动时产生的噪音和震动。
最后,制动系统的液压传动系统也需要进行设计与优化。
液压传动系统包括制动油管、制动泵和制动主缸等部件,它们的设计和配置需要保证制动力的稳定输出和灵敏度。
在设计时,应充分考虑制动盘和制动片的特性,以及车辆的重量和速度等因素,合理选择液压系统的参数,并确保制动效果稳定和可靠。
综上所述,基于力学原理的紧凑型轿车盘式制动器的设计与优化,需要从制动盘、制动片、制动钳和液压传动系统等各个方面进行综合考虑。
基于性能和结构的紧凑型轿车盘式制动器优化设计

基于性能和结构的紧凑型轿车盘式制动器优化设计紧凑型轿车盘式制动器是现代汽车制动系统中的重要组成部分,对于车辆的制动性能和安全性起着关键作用。
优化设计可以提高制动器的性能和结构,从而提升整车的制动效果和驾驶体验。
本文将基于性能和结构的角度,对紧凑型轿车盘式制动器进行优化设计,并提出相应的方案。
一、性能优化1. 制动力的提升:通过优化摩擦材料和制动液的性能,可以改善制动器的刹车效果。
选用高性能摩擦片,提高摩擦系数和耐磨性,确保制动力的稳定输出;选用高质量制动液,提高油压传递效率,减少制动系统的延迟。
2. 散热性能的提升:制动器在制动过程中会产生大量的热量,如果散热不良会导致制动力下降甚至制动衰竭。
通过设计散热通道和增加散热片等方式,增强制动器的散热性能,降低温升,增加制动器的工作稳定性。
3. 制动系统的调校:制动器的性能与整车的悬挂、电子控制系统等因素密切相关。
通过对制动系统进行调校和优化,使其与整车的其他系统协调工作,提高制动器的响应速度和制动效果。
二、结构优化1. 材料的优化:选择高强度、低密度的材料,可以降低制动器的质量,提高整车的燃油经济性和操控性能。
同时,合理的材料选择还能够提高制动器的耐磨性和抗热性能。
2. 结构的优化:通过优化制动器的结构设计,如减小主缸和制动钳的尺寸,减少滑动阻力和摩擦损失,降低制动器的磨损和能量损失。
合理设计制动器的凸轮和制动片间隙,提高制动片的刹车效果。
3. 制动器的轻量化设计:通过减小制动器的质量,可以降低整车的非悬挂质量,提高悬挂系统的工作效率和车辆的燃油经济性。
轻量化设计还能够减小制动器的惯性质量,提高制动器的响应速度。
三、优化设计方案1. 采用高性能摩擦材料,如陶瓷复合材料,提高摩擦系数和耐磨性。
2. 优化制动液的性能,选用高质量制动液,提高油压传递效率。
3. 设计散热通道,增加散热片,提高制动器的散热性能。
4. 与整车的悬挂和电子控制系统协调工作,提高制动器的响应速度和制动效果。
优化紧凑型轿车盘式制动器性能的工程设计方法
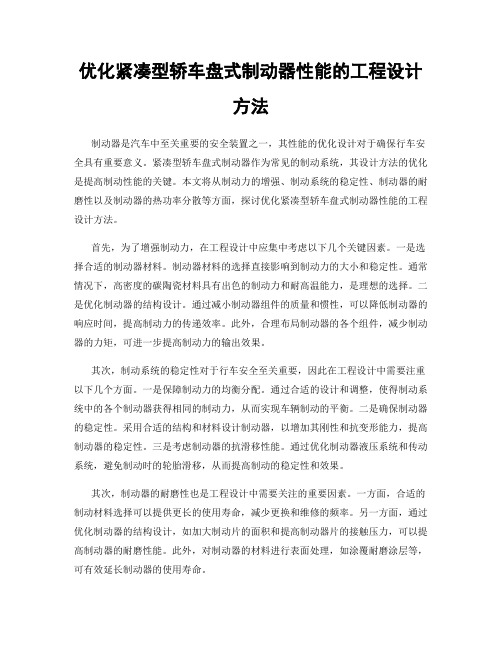
优化紧凑型轿车盘式制动器性能的工程设计方法制动器是汽车中至关重要的安全装置之一,其性能的优化设计对于确保行车安全具有重要意义。
紧凑型轿车盘式制动器作为常见的制动系统,其设计方法的优化是提高制动性能的关键。
本文将从制动力的增强、制动系统的稳定性、制动器的耐磨性以及制动器的热功率分散等方面,探讨优化紧凑型轿车盘式制动器性能的工程设计方法。
首先,为了增强制动力,在工程设计中应集中考虑以下几个关键因素。
一是选择合适的制动器材料。
制动器材料的选择直接影响到制动力的大小和稳定性。
通常情况下,高密度的碳陶瓷材料具有出色的制动力和耐高温能力,是理想的选择。
二是优化制动器的结构设计。
通过减小制动器组件的质量和惯性,可以降低制动器的响应时间,提高制动力的传递效率。
此外,合理布局制动器的各个组件,减少制动器的力矩,可进一步提高制动力的输出效果。
其次,制动系统的稳定性对于行车安全至关重要,因此在工程设计中需要注重以下几个方面。
一是保障制动力的均衡分配。
通过合适的设计和调整,使得制动系统中的各个制动器获得相同的制动力,从而实现车辆制动的平衡。
二是确保制动器的稳定性。
采用合适的结构和材料设计制动器,以增加其刚性和抗变形能力,提高制动器的稳定性。
三是考虑制动器的抗滑移性能。
通过优化制动器液压系统和传动系统,避免制动时的轮胎滑移,从而提高制动的稳定性和效果。
其次,制动器的耐磨性也是工程设计中需要关注的重要因素。
一方面,合适的制动材料选择可以提供更长的使用寿命,减少更换和维修的频率。
另一方面,通过优化制动器的结构设计,如加大制动片的面积和提高制动器片的接触压力,可以提高制动器的耐磨性能。
此外,对制动器的材料进行表面处理,如涂覆耐磨涂层等,可有效延长制动器的使用寿命。
最后,工程设计中需要考虑制动器的热功率分散问题,以保障制动系统的稳定性和持久性。
紧凑型轿车盘式制动器在制动时会产生大量的热量,如果不能有效分散这部分热量,会导致制动器系统的过热,进而影响制动性能。
紧凑型轿车盘式制动器优化设计方案研究

紧凑型轿车盘式制动器优化设计方案研究引言:随着汽车工业的发展,紧凑型轿车在市场上的需求与日俱增。
为了满足消费者对安全性能和驾驶舒适性的要求,盘式制动器的设计方案变得尤为重要。
本文将研究紧凑型轿车盘式制动器优化设计方案,通过对设计参数的优化和材料的选择,提高制动器的性能和可靠性。
一、制动器的工作原理和发展趋势1. 制动器的工作原理:盘式制动器通过制动盘和制动片的摩擦力来减速车辆。
2. 制动器的发展趋势:随着车辆速度的提高和制动性能要求的增加,制动器的发展趋势主要包括以下几个方面:a. 提高制动器的制动力和散热性能;b. 减小制动器的尺寸和重量;c. 降低制动噪音和振动。
二、紧凑型轿车盘式制动器设计参数的优化紧凑型轿车盘式制动器的设计参数优化可以从以下几个方面进行研究:1. 制动片材料的选择:a. 优化制动片材料的摩擦系数和稳定性,以提高制动效果;b. 选择具有良好散热性和耐磨性的制动片材料,延长制动器的使用寿命。
2. 制动盘的设计和优化:a. 选择适当的制动盘材料,提高制动盘的强度和刚度;b. 优化制动盘的散热效果,降低制动盘的温度;c. 通过减少制动盘的质量和减小制动盘直径,降低制动器的重量。
3. 制动器液压系统的设计:a. 优化制动系统的液压传动比和制动启动压力,提高制动力的实时可调性;b. 选择高效的液压制动泵和制动器液压油,提高制动系统的快速响应性能。
4. 制动片和制动盘的接触过程模拟:a. 借助计算机仿真软件,对制动片和制动盘的接触过程进行模拟和分析;b. 通过优化制动片和制动盘的表面形状和接触压力分布,提高制动器的摩擦效果和制动性能。
三、制动器的性能测试和评估为了验证优化设计方案的效果,需要进行制动器的性能测试和评估。
测试项目包括:1. 制动力和制动距离的测试;2. 制动噪音和振动的测试;3. 制动器的散热性能测试。
测试结果将用于评估设计方案的有效性,并指导后续的改进和优化。
结论:通过对紧凑型轿车盘式制动器的优化设计方案的研究,可以提高制动器的性能和可靠性。
紧凑型轿车盘式制动器设计优化方案研究

紧凑型轿车盘式制动器设计优化方案研究1. 紧凑型轿车盘式制动器介绍紧凑型轿车盘式制动器是一种常见的汽车制动系统,用于将车轮的动能转化为热能,从而实现汽车的减速和停车功能。
它由制动盘、制动钳和制动片等主要部件组成,具有结构简单、制动效果好、制动力平稳等特点。
2. 目前存在的问题然而,在使用过程中,紧凑型轿车盘式制动器也存在一些问题。
首先,制动盘和制动片之间的磨损会导致制动效果下降和噪音增加,需要定期更换制动片和研磨制动盘。
其次,制动片与制动盘之间的接触面积有限,对制动力的传递效率有一定的限制。
此外,制动器的散热性能也较差,长时间高速行驶时易出现制动力下降现象。
3. 设计优化方案为了解决上述问题并进一步提高紧凑型轿车盘式制动器的性能,设计优化方案如下:3.1 制动片材料优化首先,可以通过优化制动片材料来提高制动效果和耐磨性。
选择耐高温、低磨损的复合材料作为制动片的制造材料,可以延长制动片的使用寿命,降低更换频率,提高制动性能。
此外,还可以进行材料表面处理,如使用专门的涂层或纳米材料,以减少与制动盘的磨损和摩擦。
3.2 制动盘结构优化同时,可以对制动盘的结构进行优化设计。
采用更加均匀的通风孔设计,增强制动盘的散热性能,减少长时间高速行驶时的制动力下降情况。
此外,通过优化制动盘的形状和尺寸,可以增加制动盘与制动片之间的接触面积,提高制动力的传递效率。
3.3 制动钳结构优化制动钳作为制动器的核心部件之一,其结构也可以进行优化。
采用更轻量化的材料制造制动钳,可以减轻整个制动系统的重量,提高车辆的燃油经济性。
此外,通过优化制动钳的刚度和几何形状,可以提高制动器的响应速度,使制动效果更加平稳和可控。
3.4 制动系统控制策略优化最后,对于紧凑型轿车盘式制动器来说,制动系统的控制策略也是非常重要的。
采用先进的传感器和电子控制单元,实现对制动器工作状态的实时监测和控制,可以根据不同的行驶条件调整制动力和制动盘温度,以提供更加精确和可靠的制动效果,同时减少制动器的磨损和能量损失。
- 1、下载文档前请自行甄别文档内容的完整性,平台不提供额外的编辑、内容补充、找答案等附加服务。
- 2、"仅部分预览"的文档,不可在线预览部分如存在完整性等问题,可反馈申请退款(可完整预览的文档不适用该条件!)。
- 3、如文档侵犯您的权益,请联系客服反馈,我们会尽快为您处理(人工客服工作时间:9:00-18:30)。
汽车液压盘式制动器结构优化项目设计方案1.1制动系统设计的意义汽车是现代交通工具中用得最多、最普遍、也是运用得最方便的交通工具。
汽车制动系统是汽车底盘上的一个重要系统,它是制约汽车运动的装置,而制动器又是制动系中直接作用制约汽车运动的一个关键装置,是汽车上最重要的安全件。
汽车的制动性能直接影响汽车的行驶安全性。
随着公路业的迅速发展和车流密度的日益增大,人们对安全性、可靠性的要求越来越高,为保证人身和车辆安全,必须为汽车配备十分可靠的制动系统。
本次毕业设计题目为大学生方程式赛车制动系统设计。
1.2制动系统研究现状车辆在形式过程中要频繁进行制动操作,由于制动性能的好坏直接关系到交通和人身安全,因此制动性能是车辆非常重要的性能之一,改善汽车的制动性能始终是汽车设计制造和使用部门的重要任务。
当车辆制动时,由于车辆受到与行驶方向相反的外力,所以才导致汽车的速度逐步减小到0,对这一过程中车辆受力情况的分析有助于制动系统的分析和设计,因此制动过程受力情况分析是车辆试验和设计的基础,由于这一过程较为复杂,因此一般在实际中只能建立简化模型分析,通常人们从三个方面来对制动系统进行分析和评价:1)制动效能:即制动距离与制动减速度;2)制动效能的恒定性:即热衰退性;3)制动时汽车方向的稳定性;目前,对于整车制动系统的研究主要通过路试或台架进行,由于在汽车道路试验中车轮扭矩不易测量,因此,多数有关制动系的试验均通过间接测量来进行汽车在道路上的行驶,其车轮与地面的作用力是汽车运动变化的根据,在汽车道路试验中,如果能够方便地测量出车轮上扭矩的变化,则可为汽车整车制动性能研究提供更全面的试验数据和性能评价。
1.3本次制动系统应达到的目标1)具有良好的制动效能;2)具有良好的制动效能稳定性;3)制动时汽车操纵稳定性好;4)制动效能的热稳定性好;2制动系统方案论证分析与选择2.1制动器形式方案分析汽车制动器几乎均为机械摩擦式,即利用旋转元件和固定元件两工作表面间的摩擦产生的制动力矩使汽车减速或停车。
一般摩擦式制动器按旋转元件的形状分为鼓式和盘式两大类。
2.1.1鼓式制动器鼓式制动器是最早形式汽车制动器,当盘式制动器还没有出现前,它已经广泛应用于各类汽车上。
鼓式制动器又分为内张型鼓式制动器和外束型鼓式制动器两种结构型式。
内张型鼓式制动器的摩擦元件是一对带有圆弧形摩擦蹄片的制动蹄,后者则安装在制动底板上,而制动底板则紧固在前桥的前梁或后桥桥壳半轴套管的凸缘上,其旋转的摩擦元件作为制动鼓。
车轮制动器的制动鼓均固定在轮毂上。
制动时,利用制动鼓的圆柱内表面与制动蹄摩擦蹄片的外表面作为一对摩擦表面在制动鼓上产生摩擦力矩,故又称为蹄式制动器。
外束型鼓式制动器的固定摩擦元件是带有摩擦片且刚度较小的制动带,其旋转摩擦元件为制动鼓,并利用制动鼓的外圆柱表面与制动带摩擦片的内圆弧作为一对摩擦表面,产生摩擦力矩作用于制动鼓,故又称为带式制动器。
在汽车制动系中,带式制动器曾仅用作一些汽车的中央制动器,通常所说的鼓式制动器就是指这种内张型鼓式结构,鼓式制动器按蹄的类型分为:1)领从蹄式制动器如图2-1所示,若图上方的旋向箭头代表汽车前进时制动鼓的旋转方向(制动鼓正向旋转),则蹄1为领蹄,蹄2为从蹄。
汽车倒车时制动鼓的旋转方向变为反向旋转,则相应得使领蹄与从蹄也就相互对调了。
这种当制动鼓正、反反向旋转时总具有一个领蹄和一个从蹄的内张型鼓式制动器称为领从蹄使制动器。
领蹄所受的摩擦力使蹄压得更紧,即摩擦力矩具有增势作用,故又称为增势蹄;而从蹄所受的摩擦力使蹄有离开制动鼓的趋势,即摩擦力矩具有减势作用,故又称为减势蹄。
增势作用使领蹄所受的法向反力增大,而减势作用使从蹄所受的法向反力减小。
领从蹄式制动器的效能及稳定性均处于中等水平,但由于其在汽车前进与倒车时的制动性能不变,且结构简单,造价较低,也便于服装驻车制动机构,故这种结构仍广泛用于中、重型载货汽车的前、后轮制动器及轿车的后轮制动器。
图2-1 领从蹄式制动器2)双领蹄式制动器若在汽车前进时两制动蹄均为领蹄的制动器,则称为双领蹄使制动器(如图2-2所示)。
显然,当汽车倒车时这种制动器的两制动蹄又都变为从蹄故它又可称为双向领蹄式制动器。
如图所示,两制动蹄各用一个单活塞制动轮缸推动,两套制动蹄、制动轮缸等机件在制动底板上是以制动底板中心作对称布置的,因此,两蹄对制动鼓的作用的合力恰好相互平衡,故属于平面式制动器。
双领蹄式制动器有高的正向制动效能,但倒车时则变为双从蹄式使制动效能大降,这种结构经常用于中级轿车的前轮制动器,这是因为这类汽车前进制动时,前轴的动轴荷及附着力大于后轴,而倒车时则相反。
图2-2双领从蹄式制动器3)双向双领蹄式制动器当制动鼓正向和反向旋转时,两制动助均为领蹄的制动器则称为双向双领蹄式制动器(如图2-3所示)。
它也属于平衡式制动器。
由于双向双领蹄式制动器在汽车前进及倒车时的制动性能不变,因此广泛应用于中、轻型载货汽车和部分轿车的前后轮,但用作后轮制动器时,则需另设中央制动用于驻车制动。
刮动跨制动埜回位弹簧调母可调支座或向双领JS式制动器图2-3 双向双领蹄式制动器4)单向增力式制动器单向增力式制动器如图2-4所示两蹄下端以顶杆相连接,第二制动蹄支承在其上端制动地板上的支承销上,由于制动时两蹄的法向反力不能相互平衡,因此它居于一种非平衡式的制动器。
单向增力式制动器在汽车前进制动时的制动效能很高,且高于前述的各种制动器,但在倒车制动时,其制动效能却是最低的。
因此,它用于少数轻、中型货车和轿车上作为前轮制动器。
4图2-4 单向增力式制动器5)双向增力式制动器将单向增力式制动器的单活塞式制动轮缸换用双活塞式制动轮缸,其上端的支承销也作为两蹄共用的,则称为双向增力式制动器(如图2-5所示)。
对双向增力式制动器来说不论汽车前进制动或倒退制动,该制动器均为增力式制动器。
双向增力式制动器在大型高速轿车上用的较多,而且常常将其作为行车制动与驻车制动功用的制动器,但行车制动是由液压经制动轮缸产生制动蹄的张开力进行制动,而驻车制动则是用制动操纵手柄通过钢索拉绳及杠杆等机械操纵系统进行操纵。
双向增力式制动器也广泛用于汽车的中央制动器,因为驻车制动要求制动器正向、反向的制动效能都很咼,而且驻车制动若不用于应急制动时也不会产生咼温,故其热衰退冋题并不突出。
但由于结构问题使它在制动过程中散热和排水性能差,容易导致制动效率下降。
因此,在轿车领域上已经逐步退出让位给盘式制动器。
但由于成本低,仍然在一些经济型车中使用,主要用于制动负荷比较小的后轮和驻车制动。
图2-5双向增力式制动器2.1.2盘式制动器盘式制动器按摩擦副中定位原件的结构不同可分为钳盘式和全盘式两大类。
1)钳盘式钳盘式制动器按制动钳的结构形式不同可分为定钳盘式制动器、浮钳盘式制动器等。
a定钳盘式制动器:这种制动器中的制动钳固定不动,制动盘与车轮相连并在制动钳体开口槽中旋转。
具有以下优点:除活塞和制动块外无其他滑动件,易于保证制动钳的刚度;结构及制造工艺与一般鼓式制动器相差不多,容易实现鼓式制动器到盘式制动器的改革,能很好地适应多回路制动系的要求。
b浮钳盘式制动器:这种制动器具有以下优点:仅在盘得内侧具有液压缸,故轴向尺寸小,制动器能进一步靠近轮毂;没有跨越制动盘的油道或油管,液压缸冷却条件好,所以制动液汽化的可能性小;成本低;浮动盘的制动块可兼用驻车制动。
2)全盘式在全盘制动器中,摩擦副的旋转元件及固定元件均为圆盘形,制动时各盘摩擦表面全部接触,其作用原理与摩擦式离合器相同。
由于这种制动器散热条件较差,其应用远远没有钳盘式制动器广泛。
盘式制动器与鼓式制动器相比,有以下优点:1)制动效能稳定性好;2)制动力矩与汽车运动方向无关;3)易于构成双回路,有较高的可靠性和安全性;4)尺寸小、质量小、散热好;5)制动衬块上压力均匀,衬块磨损均匀;6)更换衬块工作简单容易。
7)衬块与制动盘间的间隙小,缩短了制动协调时间。
8)易于实现间隙自动调整。
综合以上优缺点最终确定本次设计采用前后盘式制动器,且均为浮钳盘式制动器。
2.2制动驱动机构的机构形式选择根据动力源的不同,制动驱动机构可分为简单制动、动力制动及伺服制动三大类型。
而力的传递方式又有机械式、液压式、气压式、气压液压式的区别。
221简单制动系简单制动系即人力制动系,是靠四级作用于制动踏板上或手柄上的力作为制动力源。
而传力方式有机械式和液压式两种。
机械式的靠杆系或钢丝绳传力,其结构简单,造假低廉,工作可靠,但机械效率低,因此仅用于中、小型汽车的驻车制动装置中。
液压式的简单制动系统通常称为液压制动系,用于行车制动装置。
其优点是作用滞后时间短(0.1-0.3S),工作压力大(可达10MPa-12MPa),缸径尺寸小,可布置在制动器内部作为制动蹄的张开机构或制动块的压紧机构,使之结构简单、紧凑、质量小、造价低。
但其有限的力传动比限制了它在汽车上的适用范围。
另外,液压管路在过渡受热时会形成气泡而影响传输,即产生所谓“气阻”使制动效能降低甚至失效;而当气温过低时(-25摄氏度和更低时),由于制动液的粘度增大,使工作的可靠性降低,以及当有局部损坏时,使整个系统都不能继续工作,液压式简单制动系曾广泛用于轿车、轻型及以下的货车和部分中型货车上。
但由于操作较沉重,不能适应现代汽车提高操作轻便性的要求,故当前仅多用于微型汽车上,在轿车和轻型汽车已经极少采用。
2.2.2动力制动系动力制动系是以发动机动力形成的气压或液压势能作为汽车制动的全部力源进行制动,而司机作用于制动踏板或手柄上的力仅用于对制动回路中控制元件的操纵。
在简单制动系中的踏板力与其行程间的发比例关系在动力制动系中便不复存在。
动力制动系有气压制动系、气顶液式制动系和全液压动力制动系 3 种。
1)气压制动系气压制动系是动力制动系最常见的型式,由于可获得较大的制动驱动力,且主车与被拖的挂车以及汽车列车之间制动驱动系统的连接装置结构简单、连接和断开均很方便,因此被广用于总质量为8t以上尤其是15t以上的载货汽车、越野汽车和客车上,但气压制动系必须采用空气压缩机、储气筒、制动阀等装置,使其结构复杂、笨重、轮廓尺寸大、造价高;管路中气压的产生和撤除均较慢,作用滞后时间较长(0.3s-0.9s),因此,当制动阀到制动气室和储气罐的距离较远时,有必要加设启动的第二控制元件--继动阀(即加速阀)以及快放阀;管路工作压力较低(一半为0.5MPa-0.9MPa)。
因而制动器室的直径达,只能置于制动器之外,在通过杆件及凸轮或锲块驱动制动蹄,使非簧载质量增大;另外制动气室排气时也有较大噪声。
2)气顶液式制动系气顶液式制动系是动力制动系的另一种型式,即利用气压系统作为普通的液压制动系统主缸的驱动力源的一种制动驱动机构,它兼有液压制动和气压制动的主要优点。