钢筋混凝土中英文对照外文翻译文献
混凝土工艺中英文对照外文翻译文献
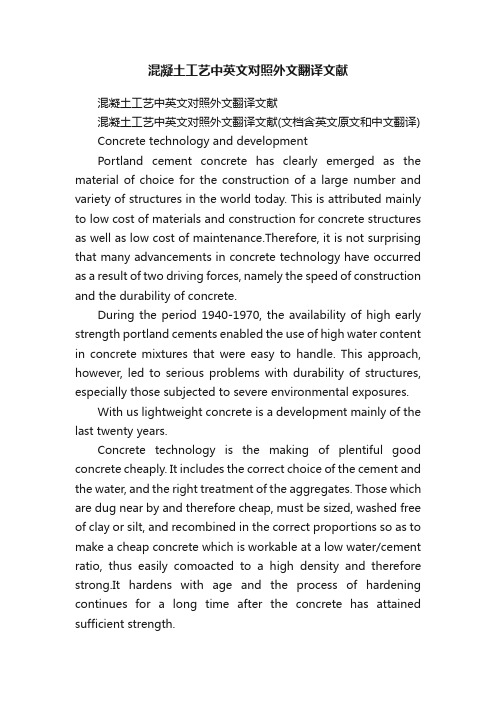
混凝土工艺中英文对照外文翻译文献混凝土工艺中英文对照外文翻译文献混凝土工艺中英文对照外文翻译文献(文档含英文原文和中文翻译) Concrete technology and developmentPortland cement concrete has clearly emerged as the material of choice for the construction of a large number and variety of structures in the world today. This is attributed mainly to low cost of materials and construction for concrete structures as well as low cost of maintenance.Therefore, it is not surprising that many advancements in concrete technology have occurred as a result of two driving forces, namely the speed of construction and the durability of concrete.During the period 1940-1970, the availability of high early strength portland cements enabled the use of high water content in concrete mixtures that were easy to handle. This approach, however, led to serious problems with durability of structures, especially those subjected to severe environmental exposures.With us lightweight concrete is a development mainly of the last twenty years.Concrete technology is the making of plentiful good concrete cheaply. It includes the correct choice of the cement and the water, and the right treatment of the aggregates. Those which are dug near by and therefore cheap, must be sized, washed free of clay or silt, and recombined in the correct proportions so as to make a cheap concrete which is workable at a low water/cement ratio, thus easily comoacted to a high density and therefore strong.It hardens with age and the process of hardening continues for a long time after the concrete has attained sufficient strength.Abrams’law, perhaps the oldest law of concrete technology, states that the strength of a concrete varies inversely with its water cement ratio. This means that the sand content (particularly the fine sand which needs much water) must be reduced so far as possible. The fact that the sand “drinks” large quantities of water can easily be established by mixing several batches of x kg of cement with y kg of stone and the same amount of water but increasing amounts of sand. However if there is no sand the concrete will be so stiff that it will be unworkable thereforw porous and weak. The same will be true if the sand is too coarse. Therefore for each set of aggregates, the correct mix must not be changed without good reason. This applied particularly to the water content.Any drinkable and many undrinkable waters can be used for making concrete, including most clear waters from the sea or rivers. It is important that clay should be kept out of the concrete. The cement if fresh can usually be chosen on the basis of the maker’s certificates of tensile or crushing tests, but these are always made with fresh cement. Where strength is important , and the cement at the site is old, it should be tested.This stress , causing breakage,will be a tension since concretes are from 9 to 11times as strong in compression as in tension, This stress, the modulus of rupture, will be roughly double the direct tensile breaking stress obtained in a tensile testing machine,so a very rough guess at the conpressive strength can be made by multiplying the modulus of rupture by 4.5. The method can be used in combination with the strength results of machine-crushed cubes or cylinders or tensile test pieces but cannot otherwise be regarded as reliable. With these comparisons,however, it is suitable for comparing concretes on the same site made from the same aggregates and cement, with beams cast and tested in the same way.Extreme care is necessary for preparation,transport,plating and finish of concrete in construction works.It is important to note that only a bit of care and supervision make a great difference between good and bad concrete.The following factors may be kept in mind in concreting works.MixingThe mixing of ingredients shall be done in a mixer as specified in the contract.Handling and ConveyingThe handling&conveying of concrete from the mixer to the place of final deposit shall be done as rapidly as practicable and without any objectionable separation or loss of ingredients.Whenever the length of haul from the mixing plant to the place of deposit is such that the concrete unduly compacts or segregates,suitable agitators shall be installed in the conveying system.Where concrete is being conveyed on chutes or on belts,the free fall or drop shall be limited to 5ft.(or 150cm.) unless otherwise permitted.The concrete shall be placed in position within 30 minutes of its removal from the mixer.Placing ConcreteNo concrete shall be placed until the place of deposit has been thoroughly inspected and approved,all reinforcement,inserts and embedded metal properly security in position and checked,and forms thoroughly wetted(expect in freezing weather)or oiled.Placing shall be continued without avoidable interruption while the section is completed or satisfactory construction joint made.Within FormsConcrete shall be systematically deposited in shallow layers and at such rate as to maintain,until the completion of the unit,a plastic surface approximately horizontal throughout.Each layer shall be thoroughly compacted before placing the succeeding layer.CompactingMethod. Concrete shall be thoroughly compacted by means of suitable tools during and immediately after depositing.The concrete shall be worked around all reinforcement,embedded fixtures,and into the comers of the forms.Every precaution shall be taken to keep the reinforcement and embedded metal in proper position and to prevent distortion.Vibrating. Wherever practicable,concrete shall be internally vibrated within the forms,or in the mass,in order to increase the plasticity as to compact effectively to improve the surface texture and appearance,and to facilitate placing of the concrete.Vibration shall be continued the entire batch melts to a uniform appearance and the surface just starts to glisten.A minute film of cement paste shall be discernible between the concrete and the form and around the reinforcement.Over vibration causing segregation,unnecessary bleeding or formation of laitance shall be avoided.The effect spent on careful grading, mixing and compaction of concrete will be largely wasted if the concrete is badly cured. Curing means keeping the concretethoroughly damp for some time, usually a week, until it has reached the desired strength. So long as concrete is kept wet it will continue to gain strength, though more slowly as it grows older.Admixtures or additives to concrete are materials arematerials which are added to it or to the cement so as to improve one or more of the properties of the concrete. The main types are:1. Accelerators of set or hardening,2. Retarders of set or hardening,3. Air-entraining agents, including frothing or foaming agents,4. Gassing agents,5. Pozzolanas, blast-furnace slag cement, pulverized coal ash,6. Inhibitors of the chemical reaction between cement and aggregate, which might cause the aggregate to expand7. Agents for damp-proofing a concrete or reducing its permeability to water,8. Workability agents, often called plasticizers,9. Grouting agents and expanding cements.Wherever possible, admixtures should be avouded, particularly those that are added on site. Small variations in the quantity added may greatly affect the concrete properties in an undesiraale way. An accelerator can often be avoided by using a rapid-hardening cement or a richer mix with ordinary cement, or for very rapid gain of strength, high-alumina cement, though this is very much more expensive, in Britain about three times as costly as ordinary Portland cement. But in twenty-four hours its strength is equal to that reached with ordinary Portland cement in thirty days.A retarder may have to be used in warm weather when a large quantity of concrete has to be cast in one piece of formwork, and it is important that the concrete cast early in the day does not set before the last concrete. This occurs with bridges when they are cast in place, and the formwork necessarily bends underthe heavy load of the wet concrete. Some retarders permanently weaken the concrete and should not be used without good technical advice.A somewhat similar effect,milder than that of retarders, is obtained with low-heat cement. These may be sold by the cement maker or mixed by the civil engineering contractor. They give out less heat on setting and hardening, partly because they harden more slowly, and they are used in large casts such as gravity dams, where the concrete may take years to cool down to the temperature of the surrounding air. In countries like Britain or France, where pulverized coal is burnt in the power stations, the ash, which is very fine, has been mixed with cement to reduce its production of heat and its cost without reducing its long-term strength. Up to about 20 per cent ash by weight of the cement has been successfully used, with considerable savings in cement costs.In countries where air-entraining cement cement can be bought from the cement maker, no air-entraining agent needs to be mixed in .When air-entraining agents draw into the wet cement and concrete some 3-8 percent of air in the form of very small bubbles, they plasticize the concrete, making it more easily workable and therefore enable the water |cement ratio to be reduced. They reduce the strength of the concrete slightly but so little that in the United States their use is now standard practice in road-building where heavy frost occur. They greatly improve the frost resistance of the concrete.Pozzolane is a volcanic ash found near the Italian town of Puzzuoli, which is a natural cement. The name has been given to all natural mineral cements, as well as to the ash from coal or the slag from blast furnaces, both of which may become cementswhen ground and mixed with water. Pozzolanas of either the industrial or the mineral type are important to civil engineers because they have been added to oridinary Portland cement in proportions up to about 20 percent without loss of strength in the cement and with great savings in cement cost. Their main interest is in large dams, where they may reduce the heat given out by the cement during hardening. Some pozzolanas have been known to prevent the action between cement and certain aggregates which causes the aggregate to expand, and weaken or burst the concrete.The best way of waterproof a concrete is to reduce its permeability by careful mix design and manufacture of the concrete, with correct placing and tighr compaction in strong formwork ar a low water|cement ratio. Even an air-entraining agent can be used because the minute pores are discontinuous. Slow, careful curing of the concrete improves the hydration of the cement, which helps to block the capillary passages through the concrete mass. An asphalt or other waterproofing means the waterproofing of concrete by any method concerned with the quality of the concrete but not by a waterproof skin.Workability agents, water-reducing agents and plasticizers are three names for the same thing, mentioned under air-entraining agents. Their use can sometimes be avoided by adding more cement or fine sand, or even water, but of course only with great care.The rapid growth from 1945 onwards in the prestressing of concrete shows that there was a real need for this high-quality structural material. The quality must be high because the worst conditions of loading normally occur at the beginning of the life of the member, at the transfer of stress from the steel to theconcrete. Failure is therefore more likely then than later, when the concrete has become stronger and the stress in the steel has decreased because of creep in the steel and concrete, and shrinkage of the concrete. Faulty members are therefore observed and thrown out early, before they enter the structure, or at least before it The main advantages of prestressed concrete in comparison with reinforced concrete are :①The whole concrete cross-section resists load. In reinforced concrete about half the section, the cracked area below the neutral axis, does no useful work. Working deflections are smaller.②High working stresses are possible. In reinforced concrete they are not usually possible because they result in severe cracking which is always ugly and may be dangerous if it causes rusting of the steel.③Cracking is almost completely avoided in prestressed concrete.The main disadvantage of prestressed concrete is that much more care is needed to make it than reinforced concrete and it is therefore more expensive, but because it is of higher quality less of it needs to be needs to be used. It can therefore happen that a solution of a structural problem may be cheaper in prestressed concrete than in reinforced concrete, and it does often happen that a solution is possible with prestressing but impossible without it.Prestressing of the concrete means that it is placed under compression before it carries any working load. This means that the section can be designed so that it takes no tension or very little under the full design load. It therefore has theoretically no cracks and in practice very few. The prestress is usually applied by tensioning the steel before the concrete in which it isembedded has hardened. After the concrete has hardened enough to take the stress from the steel to the concrete. In a bridge with abutments able to resist thrust, the prestress can be applied without steel in the concrete. It is applied by jacks forcing the bridge inwards from the abutments. This methods has the advantage that the jacking force, or prestress, can be varied during the life of the structure as required.In the ten years from 1950 to 1960 prestressed concrete ceased to be an experinmental material and engineers won confidence in its use. With this confidence came an increase in the use of precast prestressed concrete particularly for long-span floors or the decks of motorways. Whereever the quantity to be made was large enough, for example in a motorway bridge 500 m kong , provided that most of the spans could be made the same and not much longer than 18m, it became economical to usefactory-precast prestressed beams, at least in industrial areas near a precasting factory prestressed beams, at least in industrial areas near a precasting factory. Most of these beams are heat-cured so as to free the forms quickly for re-use.In this period also, in the United States, precast prestressed roof beams and floor beams were used in many school buildings, occasionally 32 m long or more. Such long beams over a single span could not possibly be successful in reinforced concrete unless they were cast on site because they would have to be much deeper and much heavier than prestressed concrete beams. They would certainlly be less pleasing to the eye and often more expensive than the prestressed concrete beams. These school buildings have a strong, simple architectural appeal and will be a pleasure to look at for many years.The most important parts of a precast prestressed concrete beam are the tendons and the concrete. The tendons, as the name implies, are the cables, rods or wires of steel which are under tension in the concrete.Before the concrete has hardened (before transfer of stress), the tendons are either unstressed (post-tensioned prestressing) or are stressed and held by abutments outside the concrete ( pre-tensioned prestressing). While the concrete is hardening it grips each tendon more and more tightly by bond along its full length. End anchorages consisting of plates or blocks are placed on the ends of the tendons of post-tensioned prestressed units, and such tendons are stressed up at the time of transfer, when the concrete has hardened sufficiently. In the other type of pretressing, with pre-tensioned tendons, the tendons are released from external abutments at the moment of transfer, and act on the concrete through bond or archorage or both, shortening it by compression, and themselves also shortening and losing some tension.Further shortening of the concrete (and therefore of the steel) takes place with time. The concrete is said to creep. This means that it shortens permanently under load and spreads the stresses more uniformly and thus more safely across its section. Steel also creeps, but rather less. The result of these two effects ( and of the concrete shrinking when it dries ) is that prestressed concrete beams are never more highly stressed than at the moment of transfer.The factory precasting of long prestressed concrete beams is likely to become more and more popular in the future, but one difficulty will be road transport. As the length of the beam increases, the lorry becomes less and less manoeuvrable untileventually the only suitable time for it to travel is in the middle of the night when traffic in the district and the route, whether the roads are straight or curved. Precasting at the site avoids these difficulties; it may be expensive, but it has often been used for large bridge beams.混凝土工艺及发展波特兰水泥混凝土在当今世界已成为建造数量繁多、种类复杂结构的首选材料。
土木工程钢筋混凝土结构中英文对照外文翻译文献
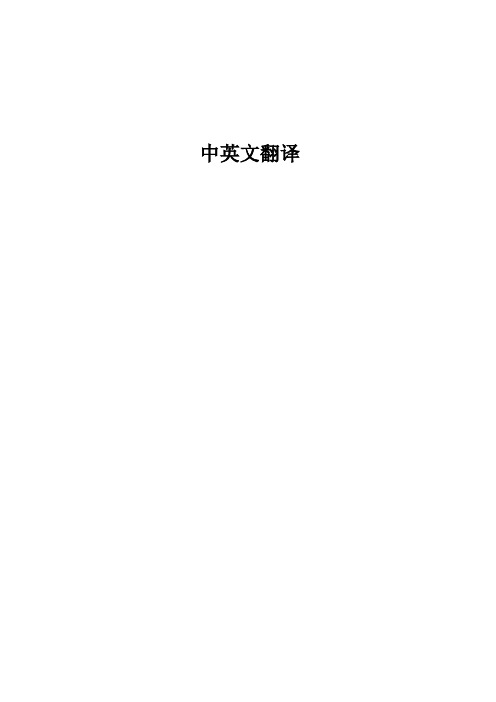
中英文翻译原文:DESIGN OF REINFORCED CONCRETESTRUCTURES1. BASIC CONCERPTS AND CHARACERACTERISTICS OF REINFORCED CONCRETEPlain concrete is formed from hardened mixture of cement, water , fine aggregate , coarse aggregate (crushed stone or gravel ) , air and often other admixtures . The plastic mix is placed and consolidated in the formwork, then cured to accelerate of the chemical hydration of hen cement mix and results in a hardened concrete. It is generally known that concrete has high compressive strength and low resistance to tension. Its tensile strength is approximatelyone-tenth of its compressive strength. Consequently, tensile reinforcement in the tension zone has to be provided to supplement the tensile strength of the reinforced concrete section.For example, a plain concrete beam under a uniformly distributed load q is shown in Fig .1.1(a), when the distributed load increases and reaches a value q=1.37KN/m , the tensile region at the mid-span will be cracked and the beam will fail suddenly . A reinforced concrete beam if the same size but has to steel reinforcing bars (2φ16) embedded at the bottom under a uniformly distributed load q is shown in Fig.1.1(b). The reinforcing bars take up the tension there after the concrete is cracked. When the load q is increased, the width of the cracks, the deflection and the stress of steel bars will increase . When the steel approaches the yielding stress ƒy , the deflection and the cracked width are so large offering some warning that the compression zone . The failure load q=9.31KN/m, is approximately 6.8 times that for the plain concrete beam.Concrete and reinforcement can work together because there is a sufficiently strong bond between the two materials, there are no relative movements of the bars and the surrounding concrete cracking. The thermal expansion coefficients of the two materials are 1.2×10-5K-1 for steel and 1.0×10-5~1.5×10-5K-1 for concrete .Generally speaking, reinforced structure possess following features :Durability .With the reinforcing steel protected by the concrete , reinforced concreteFig.1.1Plain concrete beam and reinforced concrete beamIs perhaps one of the most durable materials for construction .It does not rot rust , and is not vulnerable to efflorescence .(2)Fire resistance .Both concrete an steel are not inflammable materials .They would not be affected by fire below the temperature of 200℃ when there is a moderate amount of concrete cover giving sufficient thermal insulation to the embedded reinforcement bars.(3)High stiffness .Most reinforced concrete structures have comparatively large crosssections .As concrete has high modulus of elasticity, reinforced concrete structures are usually stiffer than structures of other materials, thus they are less prone to large deformations, This property also makes the reinforced concrete less adaptable to situations requiring certainflexibility, such as high-rise buildings under seismic load, and particular provisions have to be made if reinforced concrete is used.(4)Locally available resources. It is always possible to make use of the local resources of labour and materials such as fine and coarse aggregates. Only cement and reinforcement need to be brought in from outside provinces.(5)Cost effective. Comparing with steel structures, reinforced concrete structures arecheaper. 1.37kn/m6m 200 400(a)plain concrete beam 9.31kn/m6m 200 400(b)Reinfoced concrete beam2φ16(6)Large dead mass, The density of reinforced concrete may reach2400~2500kg/pare with structures of other materials, reinforced concrete structures generally have a heavy dead mass. However, this may be not always disadvantageous, particularly for those structures which rely on heavy dead weight to maintain stability, such as gravity dam and other retaining structure. The development and use of light weight aggregate have to a certain extent make concrete structure lighter.(7)Long curing period.. It normally takes a curing period of 28 day under specified conditions for concrete to acquire its full nominal strength. This makes the progress of reinforced concrete structure construction subject to seasonal climate. The development of factory prefabricated members and investment in metal formwork also reduce the consumption of timber formwork materials.(8)Easily cracked. Concrete is weak in tension and is easily cracked in the tension zone. Reinforcing bars are provided not to prevent the concrete from cracking but to take up the tensile force. So most of the reinforced concrete structure in service is behaving in a cracked state. This is an inherent is subjected to a compressive force before working load is applied. Thus the compressed concrete can take up some tension from the load.2. HISTOEICAL DEVELPPMENT OF CONCRETE STRUCTUREAlthough concrete and its cementitious(volcanic) constituents, such as pozzolanic ash, have been used since the days of Greek, the Romans, and possibly earlier ancient civilization, the use of reinforced concrete for construction purpose is a relatively recent event, In 1801, F. Concrete published his statement of principles of construction, recognizing the weakness if concrete in tension, The beginning of reinforced concrete is generally attributed to Frenchman J. L. Lambot, who in 1850 constructed, for the first time, a small boat with concrete for exhibition in the 1855 World’s Fair in Paris. In England, W. B. Wilkinson registered a patent for reinforced concrete l=floor slab in 1854.J.Monier, a French gardener used metal frames as reinforcement to make garden plant containers in 1867. Before 1870, Monier had taken a series of patents to make reinforced concrete pipes, slabs, and arches. But Monier had no knowledge of the working principle of this new material, he placed the reinforcement at the mid-depth of his wares. Then little construction was done in reinforced concrete. It is until 1887, when the German engineers Wayss and Bauschinger proposed to place the reinforcement in the tension zone, the use of reinforced concrete as a material of construction began to spread rapidly. In1906, C. A. P. Turner developed the first flat slab without beams.Before the early twenties of 20th century, reinforced concrete went through the initial stage of its development, Considerable progress occurred in the field such that by 1910 the German Committee for Reinforced Concrete, the Austrian Concrete Committee, the American Concrete Institute, and the British Concrete Institute were established. Various structural elements, such as beams, slabs, columns, frames, arches, footings, etc. were developed using this material. However, the strength of concrete and that of reinforcing bars were still very low. The common strength of concrete at the beginning of 20th century was about 15MPa in compression, and the tensile strength of steel bars was about 200MPa. The elements were designed along the allowable stresses which was an extension of the principles in strength of materials.By the late twenties, reinforced concrete entered a new stage of development. Many buildings, bridges, liquid containers, thin shells and prefabricated members of reinforced concrete were concrete were constructed by 1920. The era of linear and circular prestressing began.. Reinforced concrete, because of its low cost and easy availability, has become the staple material of construction all over the world. Up to now, the quality of concrete has been greatly improved and the range of its utility has been expanded. The design approach has also been innovative to giving the new role for reinforced concrete is to play in the world of construction.The concrete commonly used today has a compressive strength of 20~40MPa. For concrete used in pre-stressed concrete the compressive strength may be as high as 60~80MPa. The reinforcing bars commonly used today has a tensile strength of 400MPa, and the ultimate tensile strength of prestressing wire may reach 1570~1860Pa. The development of high strength concrete makes it possible for reinforced concrete to be used in high-rise buildings, off-shore structures, pressure vessels, etc. In order to reduce the dead weight of concrete structures, various kinds of light concrete have been developed with a density of 1400~1800kg/m3. With a compressive strength of 50MPa, light weight concrete may be used in load bearing structures. One of the best examples is the gymnasium of the University of Illinois which has a span of 122m and is constructed of concrete with a density of 1700kg/m3. Another example is the two 20-story apartment houses at the Xi-Bian-Men in Beijing. The walls of these two buildings are light weight concrete with a density of 1800kg/m3.The tallest reinforced concrete building in the world today is the 76-story Water Tower Building in Chicago with a height of 262m. The tallest reinforced concrete building in China today is the 63-story International Trade Center in GuangZhou with a height a height of 200m. The tallest reinforced concrete construction in the world is the 549m high International Television Tower in Toronto, Canada. He prestressedconcrete T-section simply supported beam bridge over the Yellow River in Luoyang has 67 spans and the standard span length is 50m.In the design of reinforced concrete structures, limit state design concept has replaced the old allowable stresses principle. Reliability analysis based on the probability theory has very recently been introduced putting the limit state design on a sound theoretical foundation. Elastic-plastic analysis of continuous beams is established and is accepted in most of the design codes. Finite element analysis is extensively used in the design of reinforced concrete structures and non-linear behavior of concrete is taken into consideration. Recent earthquake disasters prompted the research in the seismic resistant reinforced of concrete structures. Significant results have been accumulated.3. SPECIAL FEATURES OF THE COURSEReinforced concrete is a widely used material for construction. Hence, graduates of every civil engineering program must have, as a minimum requirement, a basic understanding of the fundamentals of reinforced concrete.The course of Reinforced Concrete Design requires the prerequisite of Engineering Mechanics, Strength of Materials, and some if not all, of Theory of Structures, In all these courses, with the exception of Strength of Materials to some extent, a structure is treated of in the abstract. For instance, in the theory of rigid frame analysis, all members have an abstract EI/l value, regardless of what the act value may be. But the theory of reinforced concrete is different, it deals with specific materials, concrete and steel. The values of most parameters must be determined by experiments and can no more be regarded as some abstract. Additionally, due to the low tensile strength of concrete, the reinforced concrete members usually work with cracks, some of the parameters such as the elastic modulus I of concrete and the inertia I of section are variable with the loads.The theory of reinforced concrete is relatively young. Although great progress has been made, the theory is still empirical in nature in stead of rational. Many formulas can not be derived from a few propositions, and may cause some difficulties for students. Besides, due to the difference in practice in different countries, most countries base their design methods on their own experience and experimental results. Consequently, what one learns in one country may be different in another country. Besides, the theory is still in a stage of rapid development and is subjected to revision according to new findings from research. In China, the design code undergoes major revision in about every fifteen years and with minor revision in between. This book is based on the latest current code in China “Code for Design of Concrete Structures”(GB50010-2002). The studentsmust keep in mind that this course can not give them the knowledge which is universally valid regardless of time and place, but the basic principles on which the current design method in the country is established.The desk calculator has made calculations to a high degree of precision possible and easy. Students must not forget that concrete is a man-made material and a 10% consistency in quality is remarkably good. Reinforcing bad=rs are rolled in factory, yet variation is=n strength may be as high as 5%. Besides, the position of bars in the formwork may deviate from their design positions. In fact two figure accuracy is adequate for almost all the cases, rather than carrying the calculations to meaningless precision. The time and effort of the designer are better spent to find out where the tension may occur to resist it by placing reinforcement there.中文译文:钢筋混凝土结构设计一、钢筋混凝土基本概念和特点混凝土是指由水泥胶凝的水、细致聚合体、粗聚合物(碎石或沙砾)、空气、以及其他混合物的坚硬混合物。
外文翻译---混凝土,钢筋混凝土和预应力混凝土
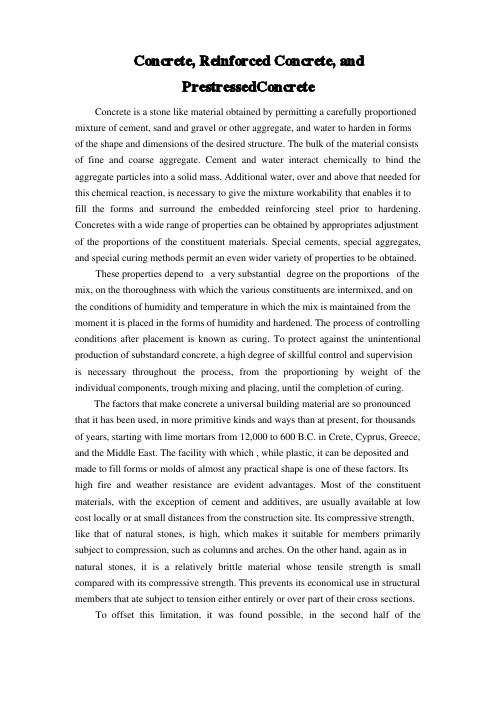
Concrete, Reinforced Concrete, andPrestressedConcreteConcrete is a stone like material obtained by permitting a carefully proportioned mixture of cement, sand and gravel or other aggregate, and water to harden in forms of the shape and dimensions of the desired structure. The bulk of the material consists of fine and coarse aggregate.Cement and water interact chemically to bind the aggregate particles into a solid mass. Additional water, over and above that needed for this chemical reaction, is necessary to give the mixture workability that enables it to fill the forms and surround the embedded reinforcing steel prior to hardening. Concretes with a wide range of properties can be obtained by appropriates adjustment of the proportions of the constituent materials.Special cements,special aggregates, and special curing methods permit an even wider variety of properties to be obtained.These properties depend to a very substantial degree on the proportions of the mix, on the thoroughness with which the various constituents are intermixed, and on the conditions of humidity and temperature in which the mix is maintained from the moment it is placed in the forms of humidity and hardened. The process of controlling conditions after placement is known as curing.To protect against the unintentional production of substandard concrete, a high degree of skillful control and supervision is necessary throughout the process,from the proportioning by weight of the individual components, trough mixing and placing, until the completion of curing.The factors that make concrete a universal building material are so pronounced that it has been used, in more primitive kinds and ways than at present, for thousands of years, starting with lime mortars from 12,000 to 600 B.C. in Crete, Cyprus, Greece, and the Middle East. The facility with which , while plastic, it can be deposited and made to fill forms or molds of almost any practical shape is one of these factors. Its high fire and weather resistance are evident advantages.Most of the constituent materials,with the exception of cement and additives,are usually available at low cost locally or at small distances from the construction site. Its compressive strength, like that of natural stones,is high,which makes it suitable for members primarily subject to compression, such as columns and arches. On the other hand, again as in natural stones,it is a relatively brittle material whose tensile strength is small compared with its compressive strength. This prevents its economical use in structural members that ate subject to tension either entirely or over part of their cross sections.To offset this limitation,it was found possible,in the second half of thenineteenth century,to use steel with its high tensile strength to reinforce concrete, chiefly in those places where its low tensile strength would limit the carrying capacity of the member. The reinforcement, usually round steel rods with appropriate surface deformations to provide interlocking, is places in the forms in advance of the concrete. When completely surrounded by the hardened concrete mass, it forms an integral part of the member.The resulting combination of two materials,known as reinforced concrete,combines many of the advantages of each:the relatively low cost,good weather and fire resistance, good compressive strength, and excellent formability of concrete and the high tensile strength and much greater ductility and toughness of steel.It is this combination that allows the almost unlimited range of uses and possibilities of reinforced concrete in the construction of buildings,bridges,dams, tanks, reservoirs, and a host of other structures.In more recent times, it has been found possible to produce steels, at relatively low cost, whose yield strength is 3 to 4 times and more that of ordinary reinforcing steels.Likewise,it is possible to produce concrete4to5times as strong in compression as the more ordinary concrete. These high-strength materials offer many advantages, including smaller member cross sections, reduced dead load, and longer spans. However, there are limits to the strengths of the constituent materials beyond which certain problems arise.To be sure,the strength of such a member would increase roughly in proportion to those of the materials. However, the high strains that result from the high stresses that would otherwise be permissible would lead to large deformations and consequently large deflections of such member under ordinary loading conditions.Equally important,the large strains in such high-strength reinforcing steel would induce large cracks in the surrounding low tensile strength concrete, cracks that would not only be unsightly but that could significantly reduce the durability of the structure.This limits the useful yield strength of high-strength reinforcing steel to 80 ksi according to many codes and specifications; 60 ksi steel is most commonly used.A special way has been found, however, to use steels and concrete of very high strength in combination. This type of construction is known as prestressed concrete. The steel,in the form of wires,strands,or bars, is embedded in the concrete under high tension that is held in equilibrium by compressive stresses in the concrete after hardening,Because of this precompression,the concrete in a flexural member will crack on the tension side at a much larger load than when not so precompressed. Prestressing greatly reduces both the deflections and the tensile cracks at ordinaryloads in such structures, and thereby enables these high-strength materials to be used effectively. Prestressed concrete has extended, to a very significant extent, the range of spans of structural concrete and the types of structures for which it is suited.混凝土,钢筋混凝土和预应力混凝土混凝土是一种经过水泥,沙子和砂砾或其他材料聚合得到经过细致配比的混合物,在液体变硬使材料石化后可以得到理想的形状和结构尺寸。
钢筋混凝土中英文对照外文翻译文献

中英文资料对照外文翻译目录1 中文翻译 (1)1.1钢筋混凝土 (1)1.2土方工程 (2)1.3结构的安全度 (3)2 外文翻译 (6)2.1 Reinforced Concrete (6)2.2 Earthwork (7)2.3 Safety of Structures (9)1 中文翻译1.1钢筋混凝土素混凝土是由水泥、水、细骨料、粗骨料(碎石或;卵石)、空气,通常还有其他外加剂等经过凝固硬化而成。
将可塑的混凝土拌合物注入到模板内,并将其捣实,然后进行养护,以加速水泥与水的水化反应,最后获得硬化的混凝土。
其最终制成品具有较高的抗压强度和较低的抗拉强度。
其抗拉强度约为抗压强度的十分之一。
因此,截面的受拉区必须配置抗拉钢筋和抗剪钢筋以增加钢筋混凝土构件中较弱的受拉区的强度。
由于钢筋混凝土截面在均质性上与标准的木材或钢的截面存在着差异,因此,需要对结构设计的基本原理进行修改。
将钢筋混凝土这种非均质截面的两种组成部分按一定比例适当布置,可以最好的利用这两种材料。
这一要求是可以达到的。
因混凝土由配料搅拌成湿拌合物,经过振捣并凝固硬化,可以做成任何一种需要的形状。
如果拌制混凝土的各种材料配合比恰当,则混凝土制成品的强度较高,经久耐用,配置钢筋后,可以作为任何结构体系的主要构件。
浇筑混凝土所需要的技术取决于即将浇筑的构件类型,诸如:柱、梁、墙、板、基础,大体积混凝土水坝或者继续延长已浇筑完毕并且已经凝固的混凝土等。
对于梁、柱、墙等构件,当模板清理干净后应该在其上涂油,钢筋表面的锈及其他有害物质也应该被清除干净。
浇筑基础前,应将坑底土夯实并用水浸湿6英寸,以免土壤从新浇的混凝土中吸收水分。
一般情况下,除使用混凝土泵浇筑外,混凝土都应在水平方向分层浇筑,并使用插入式或表面式高频电动振捣器捣实。
必须记住,过分的振捣将导致骨料离析和混凝土泌浆等现象,因而是有害的。
水泥的水化作用发生在有水分存在,而且气温在50°F以上的条件下。
混凝土工艺中英文对照外文翻译文献

混凝土工艺中英文对照外文翻译文献混凝土工艺中英文对照外文翻译文献(文档含英文原文和中文翻译)Concrete technology and developmentPortland cement concrete has clearly emerged as the material of choice for the construction of a large number and variety of structures in the world today. This is attributed mainly to low cost of materials and construction for concrete structures as well as low cost of maintenance.Therefore, it is not surprising that many advancements in concrete technology have occurred as a result of two driving forces, namely the speed of construction and the durability of concrete.During the period 1940-1970, the availability of high early strength portland cements enabled the use of high water content in concrete mixtures that were easy to handle. This approach, however, led to serious problems with durability of structures, especially those subjected to severe environmental exposures.With us lightweight concrete is a development mainly of the last twenty years.Concrete technology is the making of plentiful good concrete cheaply. It includes the correct choice of the cement and the water, and the right treatment of the aggregates. Those which are dug near by and therefore cheap, must be sized, washed free of clay or silt, and recombined in the correct proportions so as to make a cheap concrete which is workable at a low water/cement ratio, thus easily comoacted to a high density and therefore strong.It hardens with age and the process of hardening continues for a long time after the concrete has attained sufficient strength.Abrams’law, perhaps the oldest law of concrete technology, states that the strength of a concrete varies inversely with its water cement ratio. This means that the sand content (particularly the fine sand which needs much water) must be reduced so far as possible. The fact that the sand “drinks” large quantities of water can easily be established by mixing several batches of x kg of cement with y kg of stone and the same amount of water but increasing amounts of sand. However if there is no sand the concrete will be so stiff that it will be unworkable thereforw porous and weak. The same will be true if the sand is too coarse. Therefore for each set of aggregates, the correct mix must not be changed without good reason. This applied particularly to the water content.Any drinkable and many undrinkable waters can be used for making concrete, including most clear waters from the sea or rivers. It is important that clay should be kept out of the concrete. The cement if fresh can usually be chosen on the basis of the maker’s certificates of tensile or crushing tests, but these are always made with fresh cement. Where strength is important , and the cement at the site is old, it should be tested.This stress , causing breakage,will be a tension since concretes are from 9 to 11times as strong in compression as in tension, This stress, the modulus of rupture, will be roughly double the direct tensile breaking stress obtained in a tensile testing machine,so a very rough guess at the conpressive strength can be made by multiplying the modulus of rupture by 4.5. The method can be used in combination with the strength results of machine-crushed cubes or cylinders or tensile test pieces but cannot otherwise be regarded as reliable. With these comparisons, however, it is suitable for comparing concretes on the same site made from the same aggregates and cement, with beams cast and tested in the same way.Extreme care is necessary for preparation,transport,plating and finish of concrete in construction works.It is important to note that only a bit of care and supervision make a great difference between good and bad concrete.The following factors may be kept in mind in concreting works.MixingThe mixing of ingredients shall be done in a mixer as specified in the contract.Handling and ConveyingThe handling&conveying of concrete from the mixer to the place of final deposit shall be done as rapidly as practicable and without any objectionable separation or loss of ingredients.Whenever the length of haul from the mixing plant to the place of deposit is such that the concrete unduly compacts or segregates,suitable agitators shall be installed in the conveying system.Where concrete is being conveyed on chutes or on belts,the free fall or drop shall be limited to 5ft.(or 150cm.) unless otherwise permitted.The concrete shall be placed in position within 30 minutes of its removal from the mixer.Placing ConcreteNo concrete shall be placed until the place of deposit has been thoroughly inspected and approved,all reinforcement,inserts and embedded metal properly security in position and checked,and forms thoroughly wetted(expect in freezing weather)or oiled.Placing shall be continued without avoidable interruption while the section is completed or satisfactory construction joint made.Within FormsConcrete shall be systematically deposited in shallow layers and at such rate as to maintain,until the completion of the unit,a plastic surface approximately horizontal throughout.Each layer shall be thoroughly compacted before placing the succeeding layer.CompactingMethod. Concrete shall be thoroughly compacted by means of suitable tools during and immediately after depositing.The concrete shall be worked around all reinforcement,embedded fixtures,and into the comers of the forms.Every precaution shall be taken to keep the reinforcement and embedded metal in proper position and to prevent distortion.Vibrating. Wherever practicable,concrete shall be internally vibrated within the forms,or in the mass,in order to increase the plasticity as to compact effectively to improve the surface texture and appearance,and to facilitate placing of the concrete.Vibration shall be continued the entire batch melts to a uniform appearance and the surface just starts to glisten.A minute film of cement paste shall be discernible between the concrete and the form and around the reinforcement.Over vibration causing segregation,unnecessary bleeding or formation of laitance shall be avoided.The effect spent on careful grading, mixing and compaction of concrete will be largely wasted if the concrete is badly cured. Curing means keeping the concretethoroughly damp for some time, usually a week, until it has reached the desired strength. So long as concrete is kept wet it will continue to gain strength, though more slowly as it grows older.Admixtures or additives to concrete are materials are materials which are added to it or to the cement so as to improve one or more of the properties of the concrete. The main types are:1. Accelerators of set or hardening,2. Retarders of set or hardening,3. Air-entraining agents, including frothing or foaming agents,4. Gassing agents,5. Pozzolanas, blast-furnace slag cement, pulverized coal ash,6. Inhibitors of the chemical reaction between cement and aggregate, which might cause the aggregate to expand7. Agents for damp-proofing a concrete or reducing its permeability to water,8. Workability agents, often called plasticizers,9. Grouting agents and expanding cements.Wherever possible, admixtures should be avouded, particularly those that are added on site. Small variations in the quantity added may greatly affect the concrete properties in an undesiraale way. An accelerator can often be avoided by using a rapid-hardening cement or a richer mix with ordinary cement, or for very rapid gain of strength, high-alumina cement, though this is very much more expensive, in Britain about three times as costly as ordinary Portland cement. But in twenty-four hours its strength is equal to that reached with ordinary Portland cement in thirty days.A retarder may have to be used in warm weather when a large quantity of concrete has to be cast in one piece of formwork, and it is important that the concrete cast early in the day does not set before the last concrete. This occurs with bridges when they are cast in place, and the formwork necessarily bends under the heavy load of the wet concrete. Some retarders permanently weaken the concrete and should not be used without good technical advice.A somewhat similar effect,milder than that of retarders, is obtained with low-heat cement. These may be sold by the cement maker or mixed by the civil engineering contractor. They give out less heat on setting and hardening, partly because they harden more slowly, and they are used in large casts such as gravity dams, where the concrete may take years to cool down to the temperature of the surrounding air. In countries like Britain or France, where pulverized coal is burnt in the power stations, the ash, which is very fine, has been mixed with cement to reduce its production of heat and its cost without reducing its long-term strength. Up to about 20 per cent ash by weight of the cement has been successfully used, with considerable savings in cement costs.In countries where air-entraining cement cement can be bought from the cement maker, no air-entraining agent needs to be mixed in .When air-entraining agents draw into the wet cement and concrete some 3-8 percent of air in the form of very small bubbles, they plasticize the concrete, making it more easily workable and therefore enable the water |cement ratio to be reduced. They reduce the strength of the concrete slightly but so little that in the United States their use is now standard practice in road-building where heavy frost occur. They greatly improve the frost resistance of the concrete.Pozzolane is a volcanic ash found near the Italian town of Puzzuoli, which is a natural cement. The name has been given to all natural mineral cements, as well as to the ash from coal or the slag from blast furnaces, both of which may become cements when ground and mixed with water. Pozzolanas of either the industrial or the mineral type are important to civil engineers because they have been added to oridinary Portland cement in proportions up to about 20 percent without loss of strength in the cement and with great savings in cement cost. Their main interest is in large dams, where they may reduce the heat given out by the cement during hardening. Some pozzolanas have been known to prevent the action between cement and certain aggregates which causes the aggregate to expand, and weaken or burst the concrete.The best way of waterproof a concrete is to reduce its permeability by careful mix design and manufacture of the concrete, with correct placing and tighr compaction in strong formwork ar a low water|cement ratio. Even an air-entraining agent can be used because the minute pores are discontinuous. Slow, careful curing of the concrete improves the hydration of the cement, which helps to block the capillary passages through the concrete mass. An asphalt or other waterproofing means the waterproofing of concrete by any method concerned with the quality of the concrete but not by a waterproof skin.Workability agents, water-reducing agents and plasticizers are three names for the same thing, mentioned under air-entraining agents. Their use can sometimes be avoided by adding more cement or fine sand, or even water, but of course only with great care.The rapid growth from 1945 onwards in the prestressing of concrete shows that there was a real need for this high-quality structural material. The quality must be high because the worst conditions of loading normally occur at the beginning of the life of the member, at the transfer of stress from the steel to the concrete. Failure is therefore more likely then than later, when the concrete has become stronger and the stress in the steel has decreased because of creep in the steel and concrete, and shrinkage of the concrete. Faulty members are therefore observed and thrown out early, before they enter the structure, or at least before it The main advantages of prestressed concrete in comparison with reinforced concrete are :①The whole concrete cross-section resists load. In reinforced concrete about half the section, the cracked area below the neutral axis, does no useful work. Working deflections are smaller.②High working stresses are possible. In reinforced concrete they are not usually possible because they result in severe cracking which is always ugly and may be dangerous if it causes rusting of the steel.③Cracking is almost completely avoided in prestressed concrete.The main disadvantage of prestressed concrete is that much more care is needed to make it than reinforced concrete and it is therefore more expensive, but because it is of higher quality less of it needs to be needs to be used. It can therefore happen that a solution of a structural problem may be cheaper in prestressed concrete than in reinforced concrete, and it does often happen that a solution is possible with prestressing but impossible without it.Prestressing of the concrete means that it is placed under compression before it carries any working load. This means that the section can be designed so that it takes no tension or very little under the full design load. It therefore has theoretically no cracks and in practice very few. The prestress is usually applied by tensioning the steel before the concrete in which it is embedded has hardened. After the concrete has hardened enough to take the stress from the steel to the concrete. In a bridge with abutments able to resist thrust, the prestress can be applied without steel in the concrete. It is applied by jacks forcing the bridge inwards from the abutments. This methods has the advantage that the jacking force, or prestress, can be varied during the life of the structure as required.In the ten years from 1950 to 1960 prestressed concrete ceased to be an experinmental material and engineers won confidence in its use. With this confidence came an increase in the use of precast prestressed concrete particularly for long-span floors or the decks of motorways. Whereever the quantity to be made was large enough, for example in a motorway bridge 500 m kong , provided that most of the spans could be made the same and not much longer than 18m, it became economical to usefactory-precast prestressed beams, at least in industrial areas near a precasting factory prestressed beams, at least in industrial areas near a precasting factory. Most of these beams are heat-cured so as to free the forms quickly for re-use.In this period also, in the United States, precast prestressed roof beams and floor beams were used in many school buildings, occasionally 32 m long or more. Such long beams over a single span could not possibly be successful in reinforced concrete unless they were cast on site because they would have to be much deeper and much heavier than prestressed concrete beams. They would certainlly be less pleasing to the eye and often more expensive than the prestressed concrete beams. These school buildings have a strong, simple architectural appeal and will be a pleasure to look at for many years.The most important parts of a precast prestressed concrete beam are the tendons and the concrete. The tendons, as the name implies, are the cables, rods or wires of steel which are under tension in the concrete.Before the concrete has hardened (before transfer of stress), the tendons are either unstressed (post-tensioned prestressing) or are stressed and held by abutments outside the concrete ( pre-tensioned prestressing). While the concrete is hardening it grips each tendon more and more tightly by bond along its full length. End anchorages consisting of plates or blocks are placed on the ends of the tendons of post-tensioned prestressed units, and such tendons are stressed up at the time of transfer, when the concrete has hardened sufficiently. In the other type of pretressing, with pre-tensioned tendons, the tendons are released from external abutments at the moment of transfer, and act on the concrete through bond or archorage or both, shortening it by compression, and themselves also shortening and losing some tension.Further shortening of the concrete (and therefore of the steel) takes place with time. The concrete is said to creep. This means that it shortens permanently under load and spreads the stresses more uniformly and thus more safely across its section. Steel also creeps, but rather less. The result of these two effects ( and of the concrete shrinking when it dries ) is that prestressed concrete beams are never more highly stressed than at the moment of transfer.The factory precasting of long prestressed concrete beams is likely to become more and more popular in the future, but one difficulty will be road transport. As the length of the beam increases, the lorry becomes less and less manoeuvrable until eventually the only suitable time for it to travel is in the middle of the night when traffic in the district and the route, whether the roads are straight or curved. Precasting at the site avoids these difficulties; it may be expensive, but it has often been used for large bridge beams.混凝土工艺及发展波特兰水泥混凝土在当今世界已成为建造数量繁多、种类复杂结构的首选材料。
钢筋混凝土结构中英文对照外文翻译文献

中英文对照外文翻译(文档含英文原文和中文翻译)Reinforced ConcreteConcrete and reinforced concrete are used as building materials in every country. In many, including the United States and Canada, reinforced concrete is a dominant structural material in engineered construction. The universal nature of reinforced concrete construction stems from the wide availability of reinforcing bars and the constituents of concrete, gravel, sand, and cement, the relatively simple skills required in concrete construction, and the economy of reinforced concrete compared to other forms of construction. Concrete and reinforced concrete are used in bridges, buildings of all sorts underground structures, water tanks, television towers, offshore oil exploration and production structures, dams, and even in ships.Reinforced concrete structures may be cast-in-place concrete, constructed in their final location, or they may be precast concreteproduced in a factory and erected at the construction site. Concrete structures may be severe and functional in design, or the shape and layout and be whimsical and artistic. Few other building materials off the architect and engineer such versatility and scope.Concrete is strong in compression but weak in tension. As a result, cracks develop whenever loads, or restrained shrinkage of temperature changes, give rise to tensile stresses in excess of the tensile strength of the concrete. In a plain concrete beam, the moments about the neutral axis due to applied loads are resisted by an internal tension-compression couple involving tension in the concrete. Such a beam fails very suddenly and completely when the first crack forms. In a reinforced concrete beam, steel bars are embedded in the concrete in such a way that the tension forces needed for moment equilibrium after the concrete cracks can be developed in the bars.The construction of a reinforced concrete member involves building a from of mold in the shape of the member being built. The form must be strong enough to support both the weight and hydrostatic pressure of the wet concrete, and any forces applied to it by workers, concrete buggies, wind, and so on. The reinforcement is placed in this form and held in place during the concreting operation. After the concrete has hardened, the forms are removed. As the forms are removed, props of shores are installed to support the weight of the concrete until it has reached sufficient strength to support the loads by itself.The designer must proportion a concrete member for adequate strength to resist the loads and adequate stiffness to prevent excessive deflections. In beam must be proportioned so that it can be constructed. For example, the reinforcement must be detailed so that it can be assembled in the field, and since the concrete is placed in the form after the reinforcement is in place, the concrete must be able to flow around, between, and past the reinforcement to fill all parts of the form completely.The choice of whether a structure should be built of concrete, steel, masonry, or timber depends on the availability of materials and on a number of value decisions. The choice of structural system is made by the architect of engineer early in the design, based on the following considerations:1. Economy. Frequently, the foremost consideration is the overall const of the structure. This is, of course, a function of the costs of the materials and the labor necessary to erect them. Frequently, however, the overall cost is affected as much or more by the overall construction time since the contractor and owner must borrow or otherwise allocate money to carry out the construction and will not receive a return on this investment until the building is ready for occupancy. In a typical large apartment of commercial project, the cost of construction financing will be a significant fraction of the total cost. As a result, financial savings due to rapid construction may more than offset increased material costs. For this reason, any measures the designer can take to standardize the design and forming will generally pay off in reduced overall costs.In many cases the long-term economy of the structure may be more important than the first cost. As a result, maintenance and durability are important consideration.2. Suitability of material for architectural and structural function.A reinforced concrete system frequently allows the designer to combine the architectural and structural functions. Concrete has the advantage that it is placed in a plastic condition and is given the desired shape and texture by means of the forms and the finishing techniques. This allows such elements ad flat plates or other types of slabs to serve as load-bearing elements while providing the finished floor and / or ceiling surfaces. Similarly, reinforced concrete walls can provide architecturally attractive surfaces in addition to having the ability to resist gravity, wind, or seismic loads. Finally, the choice of size of shape is governed by the designer and not by the availability of standard manufactured members.3. Fire resistance. The structure in a building must withstand the effects of a fire and remain standing while the building is evacuated and the fire is extinguished. A concrete building inherently has a 1- to 3-hour fire rating without special fireproofing or other details. Structural steel or timber buildings must be fireproofed to attain similar fire ratings.4. Low maintenance.Concrete members inherently require less maintenance than do structural steel or timber members. This is particularly true if dense, air-entrained concrete has been used forsurfaces exposed to the atmosphere, and if care has been taken in the design to provide adequate drainage off and away from the structure. Special precautions must be taken for concrete exposed to salts such as deicing chemicals.5. Availability of materials. Sand, gravel, cement, and concrete mixing facilities are very widely available, and reinforcing steel can be transported to most job sites more easily than can structural steel. As a result, reinforced concrete is frequently used in remote areas.On the other hand, there are a number of factors that may cause one to select a material other than reinforced concrete. These include:1. Low tensile strength.The tensile strength concrete is much lower than its compressive strength ( about 1/10 ), and hence concrete is subject to cracking. In structural uses this is overcome by using reinforcement to carry tensile forces and limit crack widths to within acceptable values. Unless care is taken in design and construction, however, these cracks may be unsightly or may allow penetration of water. When this occurs, water or chemicals such as road deicing salts may cause deterioration or staining of the concrete. Special design details are required in such cases. In the case of water-retaining structures, special details and / of prestressing are required to prevent leakage.2. Forms and shoring. The construction of a cast-in-place structure involves three steps not encountered in the construction of steel or timber structures. These are ( a ) the construction of the forms, ( b ) the removal of these forms, and (c) propping or shoring the new concrete to support its weight until its strength is adequate. Each of these steps involves labor and / or materials, which are not necessary with other forms of construction.3. Relatively low strength per unit of weight for volume.The compressive strength of concrete is roughly 5 to 10% that of steel, while its unit density is roughly 30% that of steel. As a result, a concrete structure requires a larger volume and a greater weight of material than does a comparable steel structure. As a result, long-span structures are often built from steel.4. Time-dependent volume changes. Both concrete and steel undergo-approximately the same amount of thermal expansion and contraction. Because there is less mass of steel to be heated or cooled,and because steel is a better concrete, a steel structure is generally affected by temperature changes to a greater extent than is a concrete structure. On the other hand, concrete undergoes frying shrinkage, which, if restrained, may cause deflections or cracking. Furthermore, deflections will tend to increase with time, possibly doubling, due to creep of the concrete under sustained loads.In almost every branch of civil engineering and architecture extensive use is made of reinforced concrete for structures and foundations. Engineers and architects requires basic knowledge of reinforced concrete design throughout their professional careers. Much of this text is directly concerned with the behavior and proportioning of components that make up typical reinforced concrete structures-beams, columns, and slabs. Once the behavior of these individual elements is understood, the designer will have the background to analyze and design a wide range of complex structures, such as foundations, buildings, and bridges, composed of these elements.Since reinforced concrete is a no homogeneous material that creeps, shrinks, and cracks, its stresses cannot be accurately predicted by the traditional equations derived in a course in strength of materials for homogeneous elastic materials. Much of reinforced concrete design in therefore empirical, i.e., design equations and design methods are based on experimental and time-proved results instead of being derived exclusively from theoretical formulations.A thorough understanding of the behavior of reinforced concrete will allow the designer to convert an otherwise brittle material into tough ductile structural elements and thereby take advantage of concrete’s desirable characteristics, its high compressive strength, its fire resistance, and its durability.Concrete, a stone like material, is made by mixing cement, water, fine aggregate ( often sand ), coarse aggregate, and frequently other additives ( that modify properties ) into a workable mixture. In its unhardened or plastic state, concrete can be placed in forms to produce a large variety of structural elements. Although the hardened concrete by itself, i.e., without any reinforcement, is strong in compression, it lacks tensile strength and therefore cracks easily. Because unreinforced concrete is brittle, it cannot undergo large deformations under load and failssuddenly-without warning. The addition fo steel reinforcement to the concrete reduces the negative effects of its two principal inherent weaknesses, its susceptibility to cracking and its brittleness. When the reinforcement is strongly bonded to the concrete, a strong, stiff, and ductile construction material is produced. This material, called reinforced concrete, is used extensively to construct foundations, structural frames, storage takes, shell roofs, highways, walls, dams, canals, and innumerable other structures and building products. Two other characteristics of concrete that are present even when concrete is reinforced are shrinkage and creep, but the negative effects of these properties can be mitigated by careful design.A code is a set technical specifications and standards that control important details of design and construction. The purpose of codes it produce structures so that the public will be protected from poor of inadequate and construction.Two types f coeds exist. One type, called a structural code, is originated and controlled by specialists who are concerned with the proper use of a specific material or who are involved with the safe design of a particular class of structures.The second type of code, called a building code, is established to cover construction in a given region, often a city or a state. The objective of a building code is also to protect the public by accounting for the influence of the local environmental conditions on construction. For example, local authorities may specify additional provisions to account for such regional conditions as earthquake, heavy snow, or tornados. National structural codes genrally are incorporated into local building codes.The American Concrete Institute ( ACI ) Building Code covering the design of reinforced concrete buildings. It contains provisions covering all aspects of reinforced concrete manufacture, design, and construction. It includes specifications on quality of materials, details on mixing and placing concrete, design assumptions for the analysis of continuous structures, and equations for proportioning members for design forces.All structures must be proportioned so they will not fail or deform excessively under any possible condition of service. Therefore it is important that an engineer use great care in anticipating all the probableloads to which a structure will be subjected during its lifetime.Although the design of most members is controlled typically by dead and live load acting simultaneously, consideration must also be given to the forces produced by wind, impact, shrinkage, temperature change, creep and support settlements, earthquake, and so forth.The load associated with the weight of the structure itself and its permanent components is called the dead load. The dead load of concrete members, which is substantial, should never be neglected in design computations. The exact magnitude of the dead load is not known accurately until members have been sized. Since some figure for the dead load must be used in computations to size the members, its magnitude must be estimated at first. After a structure has been analyzed, the members sized, and architectural details completed, the dead load can be computed more accurately. If the computed dead load is approximately equal to the initial estimate of its value ( or slightly less ), the design is complete, but if a significant difference exists between the computed and estimated values of dead weight, the computations should be revised using an improved value of dead load. An accurate estimate of dead load is particularly important when spans are long, say over 75 ft ( 22.9 m ), because dead load constitutes a major portion of the design load.Live loads associated with building use are specific items of equipment and occupants in a certain area of a building, building codes specify values of uniform live for which members are to be designed.After the structure has been sized for vertical load, it is checked for wind in combination with dead and live load as specified in the code. Wind loads do not usually control the size of members in building less than 16 to 18 stories, but for tall buildings wind loads become significant and cause large forces to develop in the structures. Under these conditions economy can be achieved only by selecting a structural system that is able to transfer horizontal loads into the ground efficiently.钢筋混凝土在每一个国家,混凝土及钢筋混凝土都被用来作为建筑材料。
建筑土木工程外文翻译外文文献英文文献混凝土桥梁
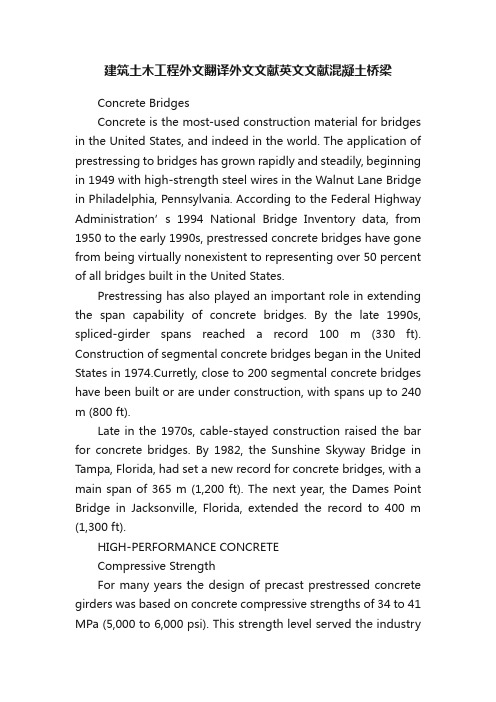
建筑土木工程外文翻译外文文献英文文献混凝土桥梁Concrete BridgesConcrete is the most-used construction material for bridges in the United States, and indeed in the world. The application of prestressing to bridges has grown rapidly and steadily, beginning in 1949 with high-strength steel wires in the Walnut Lane Bridge in Philadelphia, Pennsylvania. According to the Federal Highway Administration’s 1994 National Bridge Inventory data, from 1950 to the early 1990s, prestressed concrete bridges have gone from being virtually nonexistent to representing over 50 percent of all bridges built in the United States.Prestressing has also played an important role in extending the span capability of concrete bridges. By the late 1990s, spliced-girder spans reached a record 100 m (330 ft). Construction of segmental concrete bridges began in the United States in 1974.Curretly, close to 200 segmental concrete bridges have been built or are under construction, with spans up to 240 m (800 ft).Late in the 1970s, cable-stayed construction raised the bar for concrete bridges. By 1982, the Sunshine Skyway Bridge in Tampa, Florida, had set a new record for concrete bridges, with a main span of 365 m (1,200 ft). The next year, the Dames Point Bridge in Jacksonville, Florida, extended the record to 400 m (1,300 ft).HIGH-PERFORMANCE CONCRETECompressive StrengthFor many years the design of precast prestressed concrete girders was based on concrete compressive strengths of 34 to 41 MPa (5,000 to 6,000 psi). This strength level served the industrywell and provided the basis for establishing the prestressed concrete bridge industry in the United States. In the 1990s the industry began to utilize higher concrete compressive strengths in design, and at the start of the new millennium the industry is poised to accept the use of concrete compressive strengths up to 70 MPa (10,000 psi).For the future, the industry needs to seek ways to effectively utilize even higher concrete compressive strengths. The ready-mixed concrete industry has been producing concretes with compressive strengths in excess of 70 MPa for over 20 years. Several demonstration projects have illustrated that strengths above 70 MPa can be achieved for prestressed concrete girders. Barriers need to be removed to allow the greater use of these materials. At the same time, owners, designers, contractors, and fabricators need to be more receptive to the use of higher-compressive-strength concretes.DurabilityHigh-performance concrete (HPC) can be specified as high compressive strength (e.g., in prestressed girders) or as conventional compressive strength with improved durability (e.g., in cast-in-place bridge decks and substructures). There is a need to develop a better understanding of all the parameters that affect durability, such asresistance to chemical, electrochemical, and environmental mechanisms that attack the integrity of the material. Significant differences might occur in the long-term durability of adjacent twin structures constructed at the same time using identical materials. This reveals our lack of understanding and control of the parameters that affect durability. NEW MATERIALS Concrete design specifications have in the past focusedprimarily on the compressive strength. Concrete is slowly moving toward an engineered material whose direct performance can be altered by the designer. Material properties such as permeability, ductility, freeze-thaw resistance, durability, abrasion resistance, reactivity, and strength will be specified. The HPC initiative has gone a long way in promoting these specifications, but much more can be done. Additives, such a fibers or chemicals, can significantly alter the basic properties of concrete. Other new materials, such as fiber-reinforced polymer composites, nonmetallic reinforcement (glass fiber-reinforced and carbon fiber-reinforced plastic, etc.), new metallic reinforcements, or high-strength steel reinforcement can also be used to enhance the performance of what is considered to be a traditional material. Higher-strength reinforcement could be particularly useful when coupled with high-strength concrete. As our natural resources diminish, alternative aggregate sources (e.g., recycled aggregate) and further replacement of cementitious materials with recycled products are being examined. Highly reactive cements and reactive aggregates will be concerns of the past as new materials with long-term durability become commonplace.New materials will also find increasing demand in repair and retrofitting. As the bridge inventory continues to get older, increasing the usable life of structures will become critical. Some innovative materials, although not economical for complete bridges, will find their niche in retrofit and repair.OPTIMIZED SECTIONSIn early applications of prestressed concrete to bridges, designers developed their own ideas of the best girder sections. The result is that each contractor used slightly different girder shapes. It was too expensive to design custom girders for eachproject.As a result, representatives for the Bureau of Public Roads (now FHWA), the American Association of State Highway Officials (AASHO) (now AASHTO), and the Prestressed Concrete Institute (PCI) began work to standardize bridge girder sections. The AASHTO-PCI standard girder sections Types I through IV were developed in the late 1950s and Types V and VI in the early 1960s. There is no doubt that standardization of girders has simplified design, has led to wider utilization of prestressed concrete for bridges, and, more importantly, has led to reduction in cost.With advancements in the technology of prestressed concrete design and construction, numerous states started to refine their designs and to develop their own standard sections. As a result, in the late 1970s, FHWA sponsored a study to evaluate existing standard girder sections and determine the most efficient girders. This study concluded that bulb-tees were the most efficient sections. These sections could lead to reduction in girder weights of up to 35 percent compared with the AASHTO Type VI and cost savings up to 17 percent compared with the AASHTO-PCI girders, for equal spancapability. On the basis of the FHWA study, PCI developed the PCI bulb-tee standard, which was endorsed by bridge engineers at the 1987 AASHTO annual meeting. Subsequently, the PCI bulb-tee cross section was adopted in several states. In addition, similar cross sections were developed and adopted in Florida, Nebraska, and the New England states. These cross sections are also cost-effective with high-strength concretes for span lengths up to about 60 m (200 ft).SPLICED GIRDERSSpliced concrete I-girder bridges are cost-effective for a spanrange of 35 to 90 m (120 to 300 ft). Other shapes besides I-girders include U, T, and rectangular girders, although the dominant shape in applications to date has been the I-girder, primarily because of its relatively low cost. A feature of spliced bridges is the flexibility they provide in selection of span length, number and locations of piers, segment lengths, and splice locations. Spliced girders have the ability to adapt to curved superstructure alignments by utilizing short segment lengths and accommodating the change in direction in the cast-in-place joints. Continuity in spliced girder bridges can be achieved through full-length posttensioning, conventional reinforcement in the deck, high-strength threaded bar splicing, or pretensioned strand splicing, although the great majority of applications utilize full-length posttensioning. The availability of concrete compressive strengths higher than the traditional 34 MPa (5,000 psi) significantly improves the economy of spliced girder designs, in which high flexural and shear stresses are concentrated near the piers. Development of standardized haunched girder pier segments is needed for efficiency in negative-moment zones. Currently, the segment shapes vary from a gradually thickening bottom flange to a curved haunch with constant-sized bottom flange and variable web depth.SEGMENTAL BRIDGESSegmental concrete bridges have become an established type of construction for highway and transit projects on constrained sites. Typical applications include transit systems over existing urban streets and highways, reconstruction of existing interchanges and bridges under traffic, or projects that cross environmentally sensitive sites. In addition, segmental construction has been proved to be appropriate for large-scale,repetitive bridges such as long waterway crossings or urban freeway viaducts or where the aesthetics of the project are particularly important.Current developments suggest that segmental construction will be used on a larger number of projects in the future. Standard cross sections have been developed to allow for wider application of this construction method to smaller-scale projects. Surveys of existing segmental bridges have demonstrated the durability of this structure type and suggest that additional increases in design life are possible with the use of HPC. Segmental bridges with concrete strengths of 55 MPa (8,000 psi) or more have been constructed over the past 5 years. Erection with overhead equipment has extended applications to more congested urban areas. Use of prestressed composite steel and concrete in bridges reduces the dead weight of the superstructure and offers increased span lengths.LOAD RATING OF EXISTING BRIDGESExisting bridges are currently evaluated by maintaining agencies using working stress, load factor, or load testing methods. Each method gives different results, for several reasons. In order to get national consistency, FHWA requests that all states report bridge ratings using the load factor method. However, the new AASHTO Load and Resistance Factor Design (LRFD) bridge design specifications are different from load factor method. A discrepancy exists, therefore, between bridge design and bridge rating.A draft of a manual on condition evaluation of bridges, currently under development for AASHTO, has specifications for load and resistance factor rating of bridges. These specifications represent a significant change from existing ones. States will beasked to compare current load ratings with the LRFD load ratings using a sampling of bridges over the next year, and adjustments will be proposed. The revised specifications and corresponding evaluation guidelines should complete the LRFD cycle of design, construction, and evaluation for the nation's bridges.LIFE-CYCLE COST ANALYSISThe goal of design and management of highway bridges is to determine and implement the best possible strategy that ensures an adequate level of reliability at the lowest possible life-cycle cost. Several recent regulatory requirements call for consideration of life-cycle cost analysis for bridge infrastructure investments. Thus far, however, the integration of life-cycle cost analysis with structural reliability analysis has been limited. There is no accepted methodology for developing criteria for life-cycle cost design and analysis of new and existing bridges. Issues such as target reliability level, whole-life performance assessment rules, and optimum inspection-repair-replacement strategies for bridges must be analyzed and resolved from a life-cycle cost perspective. T o achieve this design and management goal, state departments of transportation must begin to collect the data needed to determine bridge life-cycle costs in a systematic manner. The data must include inspection, maintenance, repair, and rehabilitation expenditures and the timing of these expenditures. At present, selected state departments of transportation are considering life-cycle cost methodologies and software with the goal of developing a standard method for assessing the cost-effectiveness of concrete bridges. DECKS Cast-in-place (CIP) deck slabs are the predominant method of deck construction in the United States. Their main advantage is the ability to provide a smooth riding surface by field-adjustment of the roadway profile during concrete placement. In recent years automation of concrete placement and finishing has made this system cost-effective. However, CIP slabs have disadvantages that include excessive differential shrinkage with the supporting beams and slow construction. Recent innovations in bridge decks have focused on improvement to current practice with CIP decks and development of alternative systems that are cost-competitive, fast to construct, and durable. Focus has been on developing mixes and curing methods that produce performance characteristics such as freeze-thaw resistance, high abrasion resistance, low stiffness, and low shrinkage, rather than high strength. Full-depth precast panels have the advantages of significant reduction of shrinkage effects and increased construction speed and have been used in states with high traffic volumes for deck replacement projects. NCHRP Report 407 on rapid replacement of bridge decks has provided a proposed full-depth panel system with panels pretensioned in the transverse direction and posttensioned in the longitudinaldirection.Several states use stay-in-place (SIP) precast prestressed panels combined with CIP topping for new structures as well as for deck replacement. This system is cost-competitive with CIP decks. The SIP panels act as forms for the topping concrete and also as part of the structural depth of the deck. This system can significantly reduce construction time because field forming is only needed for the exterior girder overhangs. The SIP panel system suffers from reflective cracking, which commonly appears over the panel-to-panel joints. A modified SIP precast panel system has recently been developed in NCHRP Project 12-41.SUBSTRUCTURESContinuity has increasingly been used for precast concrete bridges. For bridges with total lengths less than 300 m (1,000 ft), integral bridge abutments and integral diaphragms at piers allow for simplicity in construction and eliminate the need for maintenance-prone expansion joints. Although the majority of bridge substructure components continue to be constructed from reinforced concrete, prestressing has been increasingly used. Prestressed bents allow for longer spans, improving durability and aesthetics and reducing conflicts with streets and utilities in urban areas. Prestressed concrete bents are also being used for structural steel bridges to reduce the overall structure depth and increase vertical clearance under bridges. Precast construction has been increasingly used for concrete bridge substructure components. Segmental hollow box piers and precast pier caps allow for rapid construction and reduced dead loads on the foundations. Precasting also enables the use of more complex forms and textures in substructure components, improving the aesthetics of bridges in urban and rural areas. RETAINING WALLSThe design of earth retaining structures has changed dramatically during the last century. Retaining wall design has evolved from short stone gravity sections to concrete structures integrating new materials such as geosynthetic soil reinforcements and high-strength tie-back soil anchors.The design of retaining structures has evolved into three distinct areas. The first is the traditional gravity design using the mass of the soil and the wall to resist sliding and overturning forces. The second is referred to as mechanically stabilized earth design. This method uses the backfill soil exclusively as the mass to resist the soil forces by engaging the soil using steel orpolymeric soil reinforcements. A third design method is the tie-back soil or rock anchor design, which uses discrete high-strength rods or cables that are drilled deep into the soil behind the wall to provide a dead anchorage to resist the soil forces.A major advancement in the evolution of earth retaining structures has been the proliferation of innovative proprietary retaining walls. Many companies have developed modular wall designs that are highly adaptable to many design scenarios. The innovative designs combined with the modular standard sections and panels have led to a significant decrease in the cost for retaining walls. Much research has been done to verify the structural integrity of these systems, and many states have embraced these technologies. RESEARCHThe primary objectives for concrete bridge research in the 21st century are to develop and test new materials that will enable lighter, longer, more economical, and more durable concrete bridge structures and to transfer this technology into the hands of the bridge designers for application. The HPCs developed toward the end of the 20th century would be enhanced by development of more durable reinforcement. In addition, higher-strength prestressing reinforcement could more effectively utilize the achievable higher concrete strengths. Lower-relaxation steel could benefit anchor zones. Also, posttensioning tendons and cable-stays could be better designed for eventual repair and replacement. As our natural resources diminish, the investigation of the use of recycled materials is as important as the research on new materials.The development of more efficient structural sections to better utilize the performance characteristics of new materials is important. In addition, more research is required in the areas ofdeck replacement panels, continuity regions of spliced girder sections, and safe,durable, cost-effective retaining wall structures.Research in the areas of design and evaluation will continue into the next millennium.The use of HPC will be facilitated by the removal of the implied strength limitation of 70 MPa (10.0 ksi) and other barriers in the LRFD bridge design specifications. As our nation’s infrastructure continues to age and as the vehicle loads continue to increase, it is important to better evaluate the capacity of existing structures and to develop effective retrofitting techniques. Improved quantification of bridge system reliability is expected through the calibration of system factors to assess the member capacities as a function of the level of redundancy. Data regarding inspection, maintenance, repair, and rehabilitation expenditures and their timing must be systematically collected and evaluated to develop better methods of assessing cost-effectiveness of concrete bridges. Performance-based seismic design methods will require a higher level of computing and better analysis tools.In both new and existing structures, it is important to be able to monitor the “health” of these structures through the development of instrumentation (e.g., fiber optics) to determine the state of stresses and corrosion in the members.CONCLUSIONIntroduced into the United States in 1949, prestressed concrete bridges today represent over 50 percent of all bridges built. This increase has resulted from advancements in design and analysis procedures and the development of new bridge systems and improved materials.The year 2000 sets the stage for even greater advancements. An exciting future lies ahead for concrete bridges!混凝土桥梁在美国甚至在世界桥梁上,混凝土是最常用的建设材料。
土木工程专业钢筋混凝土结构设计毕业论文外文文献翻译及原文
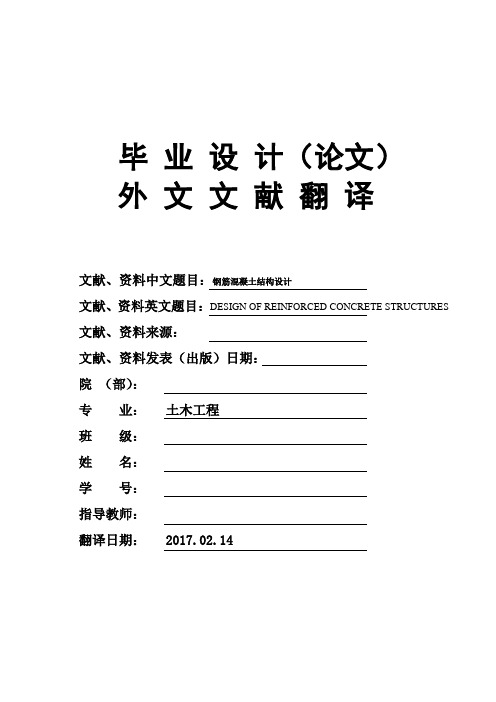
毕业设计(论文)外文文献翻译文献、资料中文题目:钢筋混凝土结构设计文献、资料英文题目:DESIGN OF REINFORCED CONCRETE STRUCTURES 文献、资料来源:文献、资料发表(出版)日期:院(部):专业:土木工程班级:姓名:学号:指导教师:翻译日期: 2017.02.14毕业设计(论文)外文参考资料及译文译文题目:DESIGN OF REINFORCED CONCRETE STRUCTURES原文:DESIGN OF REINFORCED CONCRETESTRUCTURES1. BASIC CONCERPTS AND CHARACERACTERISTICS OF REINFORCED CONCRETEPlain concrete is formed from hardened mixture of cement, water , fine aggregate , coarse aggregate (crushed stone or gravel ) , air and often other admixtures . The plastic mix is placed and consolidated in the formwork, then cured to accelerate of the chemical hydration of hen cement mix and results in a hardened concrete. It is generally known that concrete has high compressive strength and low resistance to tension. Its tensile strength is approximatelyone-tenth of its compressive strength. Consequently, tensile reinforcement in the tension zone has to be provided to supplement the tensile strength of the reinforced concrete section.For example, a plain concrete beam under a uniformly distributed load q is shown in Fig .1.1(a), when the distributed load increases and reaches a value q=1.37KN/m , the tensile region at the mid-span will be cracked and the beam will fail suddenly . A reinforced concrete beam if the same size but has to steel reinforcing bars (2φ16) embedded at the bottom under a uniformly distributed load q is shown in Fig.1.1(b). The reinforcing bars take up the tension there after the concrete is cracked. When the load q is increased, the width of the cracks, the deflection and thestress of steel bars will increase . When the steel approaches the yielding stress ƒy , thedeflection and the cracked width are so large offering some warning that the compression zone . The failure load q=9.31KN/m, is approximately 6.8 times that for the plain concrete beam.Concrete and reinforcement can work together because there is a sufficiently strong bond between the two materials, there are no relative movements of the bars and the surrounding concrete cracking. The thermal expansion coefficients of the two materials are 1.2×10-5K-1 for steel and 1.0×10-5~1.5×10-5K-1 for concrete .Generally speaking, reinforced structure possess following features :Durability .With the reinforcing steel protected by the concrete , reinforced concreteFig.1.1Plain concrete beam and reinforced concrete beamIs perhaps one of the most durable materials for construction .It does not rot rust , and is not vulnerable to efflorescence .(2)Fire resistance .Both concrete an steel are not inflammable materials .They would not be affected by fire below the temperature of 200℃when there is a moderate amount of concrete cover giving sufficient thermal insulation to the embedded reinforcement bars.(3)High stiffness .Most reinforced concrete structures have comparatively large cross sections .As concrete has high modulus of elasticity, reinforced concrete structures are usuallystiffer than structures of other materials, thus they are less prone to large deformations, This property also makes the reinforced concrete less adaptable to situations requiring certainflexibility, such as high-rise buildings under seismic load, and particular provisions have to be made if reinforced concrete is used.(b)Reinfoced concrete beam(4)Locally available resources. It is always possible to make use of the local resources of labour and materials such as fine and coarse aggregates. Only cement and reinforcement need to be brought in from outside provinces.(5)Cost effective. Comparing with steel structures, reinforced concrete structures are cheaper.(6)Large dead mass, The density of reinforced concrete may reach2400~2500kg/pare with structures of other materials, reinforced concrete structures generally have a heavy dead mass. However, this may be not always disadvantageous, particularly for those structures which rely on heavy dead weight to maintain stability, such as gravity dam and other retaining structure. The development and use of light weight aggregate have to a certain extent make concrete structure lighter.(7)Long curing period.. It normally takes a curing period of 28 day under specified conditions for concrete to acquire its full nominal strength. This makes the progress of reinforced concrete structure construction subject to seasonal climate. The development of factory prefabricated members and investment in metal formwork also reduce the consumption of timber formwork materials.(8)Easily cracked. Concrete is weak in tension and is easily cracked in the tension zone. Reinforcing bars are provided not to prevent the concrete from cracking but to take up the tensile force. So most of the reinforced concrete structure in service is behaving in a cracked state. This is an inherent is subjected to a compressive force before working load is applied. Thus the compressed concrete can take up some tension from the load.2. HISTOEICAL DEVELPPMENT OF CONCRETE STRUCTUREAlthough concrete and its cementitious(volcanic) constituents, such as pozzolanic ash, have been used since the days of Greek, the Romans, and possibly earlier ancient civilization, the use of reinforced concrete for construction purpose is a relatively recent event, In 1801, F. Concrete published his statement of principles of construction, recognizing the weakness if concrete in tension, The beginning of reinforced concrete is generally attributed to Frenchman J. L. Lambot, who in 1850 constructed, for the first time, a small boat with concrete for exhibition in the 1855 World’s Fair in Paris. In England, W. B. Wilkinson registered a patent for reinforced concrete l=floor slab in 1854.J.Monier, a French gardener used metal frames as reinforcement to make garden plant containers in 1867. Before 1870, Monier had taken a series of patents to make reinforcedconcrete pipes, slabs, and arches. But Monier had no knowledge of the working principle of this new material, he placed the reinforcement at the mid-depth of his wares. Then little construction was done in reinforced concrete. It is until 1887, when the German engineers Wayss and Bauschinger proposed to place the reinforcement in the tension zone, the use of reinforced concrete as a material of construction began to spread rapidly. In1906, C. A. P. Turner developed the first flat slab without beams.Before the early twenties of 20th century, reinforced concrete went through the initial stage of its development, Considerable progress occurred in the field such that by 1910 the German Committee for Reinforced Concrete, the Austrian Concrete Committee, the American Concrete Institute, and the British Concrete Institute were established. Various structural elements, such as beams, slabs, columns, frames, arches, footings, etc. were developed using this material. However, the strength of concrete and that of reinforcing bars were still very low. The common strength of concrete at the beginning of 20th century was about 15MPa in compression, and the tensile strength of steel bars was about 200MPa. The elements were designed along the allowable stresses which was an extension of the principles in strength of materials.By the late twenties, reinforced concrete entered a new stage of development. Many buildings, bridges, liquid containers, thin shells and prefabricated members of reinforced concrete were concrete were constructed by 1920. The era of linear and circular prestressing began.. Reinforced concrete, because of its low cost and easy availability, has become the staple material of construction all over the world. Up to now, the quality of concrete has been greatly improved and the range of its utility has been expanded. The design approach has also been innovative to giving the new role for reinforced concrete is to play in the world of construction.The concrete commonly used today has a compressive strength of 20~40MPa. For concrete used in pre-stressed concrete the compressive strength may be as high as 60~80MPa. The reinforcing bars commonly used today has a tensile strength of 400MPa, and the ultimate tensile strength of prestressing wire may reach 1570~1860Pa. The development of high strength concrete makes it possible for reinforced concrete to be used in high-rise buildings, off-shore structures, pressure vessels, etc. In order to reduce the dead weight of concrete structures, various kinds of light concrete have been developed with a density of 1400~1800kg/m3. With a compressive strength of 50MPa, light weight concrete may be used in load bearing structures. One of the best examples is the gymnasium of the University of Illinois which has a span of 122m and is constructed of concrete with a density of 1700kg/m3. Another example is the two 20-story apartment houses at the Xi-Bian-Men in Beijing. The walls of these two buildings are light weight concrete with a density of 1800kg/m3.The tallest reinforced concrete building in the world today is the 76-story Water Tower Building in Chicago with a height of 262m. The tallest reinforced concrete building in China today is the 63-story International Trade Center in GuangZhou with a height a height of 200m. The tallest reinforced concrete construction in the world is the 549m high International Television Tower in Toronto, Canada. He prestressed concrete T-section simply supported beam bridge over the Yellow River in Luoyang has 67 spans and the standard span length is 50m.In the design of reinforced concrete structures, limit state design concept has replaced the old allowable stresses principle. Reliability analysis based on the probability theory has very recently been introduced putting the limit state design on a sound theoretical foundation. Elastic-plastic analysis of continuous beams is established and is accepted in most of the design codes. Finite element analysis is extensively used in the design of reinforced concrete structures and non-linear behavior of concrete is taken into consideration. Recent earthquake disasters prompted the research in the seismic resistant reinforced of concrete structures. Significant results have been accumulated.3. SPECIAL FEATURES OF THE COURSEReinforced concrete is a widely used material for construction. Hence, graduates of every civil engineering program must have, as a minimum requirement, a basic understanding of the fundamentals of reinforced concrete.The course of Reinforced Concrete Design requires the prerequisite of Engineering Mechanics, Strength of Materials, and some if not all, of Theory of Structures, In all these courses, with the exception of Strength of Materials to some extent, a structure is treated of in the abstract. For instance, in the theory of rigid frame analysis, all members have an abstract EI/l value, regardless of what the act value may be. But the theory of reinforced concrete is different, it deals with specific materials, concrete and steel. The values of most parameters must be determined by experiments and can no more be regarded as some abstract. Additionally, due to the low tensile strength of concrete, the reinforced concrete members usually work with cracks, some of the parameters such as the elastic modulus I of concrete and the inertia I of section are variable with the loads.The theory of reinforced concrete is relatively young. Although great progress has been made, the theory is still empirical in nature in stead of rational. Many formulas can not be derived from a few propositions, and may cause some difficulties for students. Besides, due to the difference in practice in different countries, most countries base their design methods on their own experience and experimental results. Consequently, what one learns in one country may be different in another country. Besides, the theory is still in a stage of rapid。
- 1、下载文档前请自行甄别文档内容的完整性,平台不提供额外的编辑、内容补充、找答案等附加服务。
- 2、"仅部分预览"的文档,不可在线预览部分如存在完整性等问题,可反馈申请退款(可完整预览的文档不适用该条件!)。
- 3、如文档侵犯您的权益,请联系客服反馈,我们会尽快为您处理(人工客服工作时间:9:00-18:30)。
中英文资料对照外文翻译目录1 中文翻译 (1)1.1钢筋混凝土 (1)1.2土方工程 (2)1.3结构的安全度 (3)2 外文翻译 (6)2.1 Reinforced Concrete (6)2.2 Earthwork (7)2.3 Safety of Structures (9)1 中文翻译1.1钢筋混凝土素混凝土是由水泥、水、细骨料、粗骨料(碎石或;卵石)、空气,通常还有其他外加剂等经过凝固硬化而成。
将可塑的混凝土拌合物注入到模板内,并将其捣实,然后进行养护,以加速水泥与水的水化反应,最后获得硬化的混凝土。
其最终制成品具有较高的抗压强度和较低的抗拉强度。
其抗拉强度约为抗压强度的十分之一。
因此,截面的受拉区必须配置抗拉钢筋和抗剪钢筋以增加钢筋混凝土构件中较弱的受拉区的强度。
由于钢筋混凝土截面在均质性上与标准的木材或钢的截面存在着差异,因此,需要对结构设计的基本原理进行修改。
将钢筋混凝土这种非均质截面的两种组成部分按一定比例适当布置,可以最好的利用这两种材料。
这一要求是可以达到的。
因混凝土由配料搅拌成湿拌合物,经过振捣并凝固硬化,可以做成任何一种需要的形状。
如果拌制混凝土的各种材料配合比恰当,则混凝土制成品的强度较高,经久耐用,配置钢筋后,可以作为任何结构体系的主要构件。
浇筑混凝土所需要的技术取决于即将浇筑的构件类型,诸如:柱、梁、墙、板、基础,大体积混凝土水坝或者继续延长已浇筑完毕并且已经凝固的混凝土等。
对于梁、柱、墙等构件,当模板清理干净后应该在其上涂油,钢筋表面的锈及其他有害物质也应该被清除干净。
浇筑基础前,应将坑底土夯实并用水浸湿6英寸,以免土壤从新浇的混凝土中吸收水分。
一般情况下,除使用混凝土泵浇筑外,混凝土都应在水平方向分层浇筑,并使用插入式或表面式高频电动振捣器捣实。
必须记住,过分的振捣将导致骨料离析和混凝土泌浆等现象,因而是有害的。
水泥的水化作用发生在有水分存在,而且气温在50°F以上的条件下。
为了保证水泥的水化作用得以进行,必须具备上述条件。
如果干燥过快则会出现表面裂缝,这将有损与混凝土的强度,同时也会影响到水泥水化作用的充分进行。
设计钢筋混凝土构件时显然需要处理大量的参数,诸如宽度、高度等几何尺寸,配筋的面积,钢筋的应变和混凝土的应变,钢筋的应力等等。
因此,在选择混凝土截面时需要进行试算并作调整,根据施工现场条件、混凝土原材料的供应情况、业主提出的特殊要求、对建筑和净空高度的要求、所用的设计规范以及建筑物周围环境条件等最后确定截面。
钢筋混凝土通常是现场浇注的合成材料,它与在工厂中制造的标准的钢结构梁、柱等不同,因此对于上面所提到的一系列因素必须予以考虑。
对结构体系的各个部位均需选定试算截面并进行验算,以确定该截面的名义强度是否足以承受所作用的计算荷载。
由于经常需要进行多次试算,才能求出所需的截面,因此设计时第一次采用的数值将导致一系列的试算与调整工作。
选择混凝土截面时,采用试算与调整过程可以使复核与设计结合在一起。
因此,当试算截面选定后,每次设计都是对截面进行复核。
手册、图表和微型计算机以及专用程序的使用,使这种设计方法更为简捷有效,而传统的方法则是把钢筋混凝土的复核与单纯的设计分别进行处理。
1.2土方工程由于和土木工程中任何其他工种的施工方法与费用相比较,土方挖运的施工方法与费用的变化都要快得多,因此对于有事业心的人来说,土方工程是一个可以大有作为的领域。
在1935年,目前采用的利用轮胎式机械设备进行土方挖运的方法大多数还没有出现。
那是大部分土方是采用窄轨铁路运输,在这目前来说是很少采用的。
当时主要的开挖方式是使用正铲、反铲、拉铲或抓斗等挖土机,尽管这些机械目前仍然在广泛应用,但是它们只不过是目前所采用的许多方法中的一小部分。
因此,一个工程师为了使自己在土方挖运设备方面的知识跟得上时代的发展,他应当花费一些时间去研究现代的机械。
一般说来,有关挖土机、装载机和运输机械的唯一可靠而又最新的资料可以从制造厂商处获得。
土方工程或土方挖运工程指的是把地表面过高处的土壤挖去(挖方),并把它倾卸到地表面过低的其他地方(填方)。
为了降低土方工程费用,填方量应该等于挖方量,而且挖方地点应该尽可能靠近土方量相等的填方地点,以减少运输量和填方的二次搬运。
土方设计这项工作落到了从事道路设计的工程师的身上,因为土方工程的设计比其他任何工作更能决定工程造价是否低廉。
根据现有的地图和标高,道路工程师应在设计绘图室中的工作也并不是徒劳的。
它将帮助他在最短的时间内获得最好的方案。
费用最低的运土方法是用同一台机械直接挖方取土并且卸土作为填方。
这并不是经常可以做到的,但是如果能够做到则是很理想的,因为这样做既快捷又省钱。
拉铲挖土机。
推土机和正铲挖土机都能做到这点。
拉铲挖土机的工作半径最大。
推土机所推运的图的数量最多,只是运输距离很短。
拉铲挖土机的缺点是只能挖比它本身低的土,不能施加压力挖入压实的土壤内,不能在陡坡上挖土,而且挖。
卸都不准确。
正铲挖土机介于推土机和拉铲挖土机的之间,其作用半径大于推土机,但小于拉铲挖土机。
正铲挖土机能挖取竖直陡峭的工作面,这种方式对推土机司机来说是危险的,而对拉铲挖土机则是不可能的。
每种机械设备应该进行最适合它的性能的作业。
正铲挖土机不能挖比其停机平面低很多的土,而深挖坚实的土壤时,反铲挖土机最适用,但其卸料半径比起装有正铲的同一挖土机的卸料半径则要小很多。
在比较平坦的场地开挖,如果用拉铲或正铲挖土机运输距离太远时,则装有轮胎式的斗式铲运机就是比不可少的。
它能在比较平的地面上挖较深的土(但只能挖机械本身下面的土),需要时可以将土运至几百米远,然后卸土并在卸土的过程中把土大致铲平。
在挖掘硬土时,人们发现在开挖场地经常用一辆助推拖拉机(轮式或履带式),对返回挖土的铲运机进行助推这种施工方法是经济的。
一旦铲运机装满,助推拖拉机就回到开挖的地点去帮助下一台铲运机。
斗式铲运机通常是功率非常大的机械,许多厂家制造的铲运机铲斗容量为8 m ³,满载时可达10 m³。
最大的自行式铲运机铲斗容量为19立方米(满载时为25 m ³),由430马力的牵引发动机驱动。
翻斗机可能是使用最为普遍的轮胎式运输设备,因为它们还可以被用来送混凝土或者其他建筑材料。
翻斗车的车斗位于大橡胶轮胎车轮前轴的上方,尽管铰接式翻斗车的卸料方向有很多种,但大多数车斗是向前翻转的。
最小的翻斗车的容量大约为0.5立方米,而最大的标准型翻斗车的容量大约为4.5m³。
特殊型式的翻斗车包括容量为4 m³的自装式翻斗车,和容量约为0.5 m³的铰接式翻斗车。
必须记住翻斗车与自卸卡车之间的区别。
翻斗车车斗向前倾翻而司机坐在后方卸载,因此有时被称为后卸卡车。
1.3结构的安全度规范的主要目的是提供一般性的设计原理和计算方法,以便验算结构的安全度。
就目前的趋势而言,安全系数与所使用的材料性质及其组织情况无关,通常把它定义为发生破坏的条件与结构可预料的最不利的工作条件之比值。
这个比值还与结构的破坏概率(危险率)成反比。
破坏不仅仅指结构的整体破坏,而且还指结构不能正常的使用,或者,用更为确切的话来说,把破坏看成是结构已经达到不能继续承担其设计荷载的“极限状态”。
通常有两种类型的极限状态,即:(1)强度极限状态,它相当于结构能够达到的最大承载能力。
其例子包括结构的局部屈曲和整体不稳定性;某此界面失效,随后结构转变为机构;疲劳破坏;引起结构几何形状显著变化的弹性变形或塑性变形或徐变;结构对交变荷载、火灾和爆炸的敏感性。
(2)使用极限状态,它对应着结构的使用功能和耐久性。
器例子包括结构失稳之前的过大变形和位移;早期开裂或过大的裂缝;较大的振动和腐蚀。
根据不同的安全度条件,可以把结构验算所采用的计算方法分成:(1)确定性的方法,在这种方法中,把主要参数看作非随机参数。
(2)概率方法,在这种方法中,主要参数被认为是随机参数。
此外,根据安全系数的不同用途,可以把结构的计算方法分为:(1)容许应力法,在这种方法中,把结构承受最大荷载时计算得到的应力与经过按规定的安全系数进行折减后的材料强度作比较。
(2)极限状态法,在这种方法中,结构的工作状态是以其最大强度为依据来衡量的。
由理论分析确定的这一最大强度应不小于结构承受计算荷载所算得的强度(极限状态)。
计算荷载等于分别乘以荷载系数的活载与恒载之和。
把对应于不乘以荷载系数的活载和恒载的工作(使用)条件的应力与规定值(使用极限状态)相比较。
根据前两种方法和后两种方法的四种可能组合,我们可以得到一些实用的计算方法。
通常采用下面两种计算方法:确定性的方法,这种方法采用容许应力。
概率方法,这种方法采用极限状态。
至少在理论上,概率法的主要优点是可以科学的考虑所有随机安全系数,然后将这些随机安全系数组合成确定的安全系数。
概率法取决于:(1)制作和安装过程中材料强度的随机分布(整个结构的力学性能数值的分散性);(2)截面和结构几何尺寸的不确定性(由结构制作和安装造成的误差和缺陷而引起的);对作用在结构上的活载和恒载的预测的不确定性;所采用的近似计算方法有关的不精确性(实际应力与计算应力的偏差)。
此外,概率理论意味着可以基于下面几个因素来确定允许的危险率,例如:建筑物的重要性和建筑物破坏造成的危害性;(2)由于建筑物破坏使生活受到威胁的人数;(3)修复建筑的可能性;(4)建筑物的预期寿命。
所有这些因素均与经济和社会条件有关,例如:(1)建筑物的初始建设费;(2)建筑物使用期限内的折旧费;(3)由于建筑物破坏而造成的物质和材料损失费;(4)在社会上造成的不良影响;(5)精神和心理上的考虑。
就给定的安全系数而论,所有这些参数的确定都是以建筑物的最佳成本为依据的。
但是,应该考虑到进行全概率分析的困难。
对于这种分析来说,应该了解活载及其所引起的盈利的分布规律、材料的力学性能的分散性和截面的结构几何尺寸的分散性。
此外,由于强度的分布规律和应力的分布规律之间的相互关系是困难的。
这些实际困难可以采用两种方法来克服。
第一种方法对材料和荷载采用不同的安全系数,而不需要采用概率准则;第二种方法是引入一些而简化假设的近似概率方法(半概率方法)。
2 外文翻译2.1 Reinforced ConcretePlain concrete is formed from a hardened mixture of cement ,water ,fine aggregate, coarse aggregate (crushed stone or gravel),air, and often other admixtures. The plastic mix is placed and consolidated in the formwork, then cured to facilitate the acceleration of the chemical hydration reaction lf the cement/water mix, resulting in hardened concrete. The finished product has high compressive strength, and low resistance to tension, such that its tensile strength is approximately one tenth lf its compressive strength. Consequently, tensile and shear reinforcement in the tensile regions of sections has to be provided to compensate for the weak tension regions in the reinforced concrete element.It is this deviation in the composition of a reinforces concrete section from the homogeneity of standard wood or steel sections that requires a modified approach to the basic principles of structural design. The two components of the heterogeneous reinforced concrete section are to be so arranged and proportioned that optimal use is made of the materials involved. This is possible because concrete can easily be given any desired shape by placing and compacting the wet mixture of the constituent ingredients are properly proportioned, the finished product becomes strong, durable, and, in combination with the reinforcing bars, adaptable for use as main members of any structural system.The techniques necessary for placing concrete depend on the type of member to be cast: that is, whether it is a column, a bean, a wall, a slab, a foundation. a mass columns, or an extension of previously placed and hardened concrete. For beams, columns, and walls, the forms should be well oiled after cleaning them, and the reinforcement should be cleared of rust and other harmful materials. In foundations, the earth should be compacted and thoroughly moistened to about 6 in. in depth to avoid absorption of the moisture present in the wet concrete. Concrete should always be placed in horizontal layers which are compacted by means of high frequency power-driven vibrators of either the immersion or external type, as the case requires, unless it is placed by pumping. It must be kept in mind, however, that over vibration can be harmful since it could cause segregation of the aggregate and bleeding of the concrete.Hydration of the cement takes place in the presence of moisture at temperatures above 50°F. It is necessary to maintain such a condition in order that the chemical hydration reaction can take place. If drying is too rapid, surface cracking takes place. This would result in reduction of concrete strength due to cracking as well as the failure to attain full chemical hydration.It is clear that a large number of parameters have to be dealt with in proportioning a reinforced concrete element, such as geometrical width, depth, area of reinforcement, steel strain, concrete strain, steel stress, and so on. Consequently, trial and adjustment is necessary in the choice of concrete sections, with assumptions based on conditions at site, availability of the constituent materials, particular demands of the owners, architectural and headroom requirements, the applicable codes, and environmental reinforced concrete is often a site-constructed composite, in contrast to the standard mill-fabricated beam and column sections in steel structures.A trial section has to be chosen for each critical location in a structural system. The trial section has to be analyzed to determine if its nominal resisting strength is adequate to carry the applied factored load. Since more than one trial is often necessary to arrive at the required section, the first design input step generates into a series of trial-and-adjustment analyses.The trial-and –adjustment procedures for the choice of a concrete section lead to the convergence of analysis and design. Hence every design is an analysis once a trial section is chosen. The availability of handbooks, charts, and personal computers and programs supports this approach as a more efficient, compact, and speedy instructional method compared with the traditional approach of treating the analysis of reinforced concrete separately from pure design.2.2 EarthworkBecause earthmoving methods and costs change more quickly than those in any other branch of civil engineering, this is a field where there are real opportunities for the enthusiast. In 1935 most of the methods now in use for carrying and excavating earth with rubber-tyred equipment did not exist. Most earth was moved by narrow rail track, now relatively rare, and the main methods of excavation, with face shovel, backacter, or dragline or grab, though they are still widely used are only a few of the many current methods. To keep his knowledge of earthmoving equipment up to date an engineer must therefore spend tine studying modern machines. Generally the only reliable up-to-dateinformation on excavators, loaders and transport is obtainable from the makers.Earthworks or earthmoving means cutting into ground where its surface is too high ( cuts ), and dumping the earth in other places where the surface is too low ( fills). Toreduce earthwork costs, the volume of the fills should be equal to the volume of the cuts and wherever possible the cuts should be placednear to fills of equal volume so as to reduce transport and double handlingof the fill. This work of earthwork design falls on the engineer who lays out the road since it is the layout of the earthwork more than anything else which decides its cheapness. From the available maps ahd levels, the engineering must try to reach as many decisions as possible in the drawing office by drawing cross sections of the earthwork. On the site when further information becomes available he can make changes in jis sections and layout,but the drawing lffice work will not have been lost. It will have helped him to reach the best solution in the shortest time.The cheapest way of moving earth is to take it directly out of the cut and drop it as fill with the same machine. This is not always possible, but when it canbe done it is ideal, being both quick and cheap. Draglines, bulldozers and face shovels an do this. The largest radius is obtained with the dragline,and the largest tonnage of earth is moved by the bulldozer, though only over short distances.The disadvantages of the dragline are that it must dig below itself, it cannot dig with force into compacted material, it cannot dig on steep slopws, and its dumping and digging are not accurate.Face shovels are between bulldozers and draglines, having a larger radius of action than bulldozers but less than draglines. They are anle to dig into a vertical cliff face in a way which would be dangerous tor a bulldozer operator and impossible for a dragline. Each piece of equipment should be level of their tracks and for deep digs in compact material a backacter is most useful, but its dumping radius is considerably less than that of the same escavator fitted with a face shovel.Rubber-tyred bowl scrapers are indispensable for fairly level digging where the distance of transport is too much tor a dragline or face shovel. They can dig the material deeply ( but only below themselves ) to a fairly flat surface, carry it hundreds of meters if need be, then drop it and level it roughly during the dumping. For hard digging it is often found economical to keep a pusher tractor ( wheeled or tracked ) on the digging site, to push each scraper as it returns to dig. As soon as the scraper is full,the pusher tractor returns to the beginning of the dig to heop to help the nest scraper.Bowl scrapers are often extremely powerful machines;many makers build scrapersof 8 cubic meters struck capacity, which carry 10 m ³ heaped. The largest self-propelled scrapers are of 19 m ³ struck capacity ( 25 m ³ heaped )and they are driven by a tractor engine of 430 horse-powers.Dumpers are probably the commonest rubber-tyred transport since they can also conveniently be used for carrying concrete or other building materials. Dumpers have the earth container over the front axle on large rubber-tyred wheels, and the container tips forwards on most types, though in articulated dumpers the direction of tip can be widely varied. The smallest dumpers have a capacity of about 0.5 m ³, and the largest standard types are of about 4.5 m ³. Special types include the self-loading dumper of up to 4 m ³and the articulated type of about 0.5 m ³. The distinction between dumpers and dump trucks must be remembered .dumpers tip forwards and the driver sits behind the load. Dump trucks are heavy, strengthened tipping lorries, the driver travels in front lf the load and the load is dumped behind him, so they are sometimes called rear-dump trucks.2.3 Safety of StructuresThe principal scope of specifications is to provide general principles and computational methods in order to verify safety of structures. The “ safety factor ”, which according to modern trends is independent of the nature and combination of the materials used, can usually be defined as the ratio between the conditions. This ratio is also proportional to the inverse of the probability ( risk ) of failure of the structure.Failure has to be considered not only as overall collapse of the structure but also as unserviceability or, according to a more precise. Common definition. As the reaching of a “ limit state ” which causes the construction not to accomplish the task it was designed for. There are two categories of limit state :(1)Ultimate limit sate, which corresponds to the highest value of the load-bearing capacity. Examples include local buckling or global instability of the structure; failure of some sections and subsequent transformation of the structure into a mechanism; failure by fatigue; elastic or plastic deformation or creep that cause a substantial change of the geometry of the structure; and sensitivity of the structure to alternating loads, to fire and to explosions.(2)Service limit states, which are functions of the use and durability of the structure. Examples include excessive deformations and displacements without instability; early or excessive cracks; large vibrations; and corrosion.Computational methods used to verify structures with respect to the different safetyconditions can be separated into:(1)Deterministic methods, in which the main parameters are considered as nonrandom parameters.(2)Probabilistic methods, in which the main parameters are considered as random parameters.Alternatively, with respect to the different use of factors of safety, computational methods can be separated into:(1)Allowable stress method, in which the stresses computed under maximum loads are compared with the strength of the material reduced by given safety factors.(2)Limit states method, in which the structure may be proportioned on the basis of its maximum strength. This strength, as determined by rational analysis, shall not be less than that required to support a factored load equal to the sum of the factored live load and dead load ( ultimate state ).The stresses corresponding to working ( service ) conditions with unfactored live and dead loads are compared with prescribed values ( service limit state ) . From the four possible combinations of the first two and second two methods, we can obtain some useful computational methods. Generally, two combinations prevail:(1)deterministic methods, which make use of allowable stresses.(2)Probabilistic methods, which make use of limit states.The main advantage of probabilistic approaches is that, at least in theory, it is possible to scientifically take into account all random factors of safety, which are then combined to define the safety factor. probabilistic approaches depend upon :(1) Random distribution of strength of materials with respect to the conditions of fabrication and erection ( scatter of the values of mechanical properties through out the structure );(2) Uncertainty of the geometry of the cross-section sand of the structure ( faults and imperfections due to fabrication and erection of the structure );(3) Uncertainty of the predicted live loads and dead loads acting on the structure;(4)Uncertainty related to the approximation of the computational method used ( deviation of the actual stresses from computed stresses ).Furthermore, probabilistic theories mean that the allowable risk can be based on several factors, such as :(1) Importance of the construction and gravity of the damage by its failure;(2)Number of human lives which can be threatened by this failure;(3)Possibility and/or likelihood of repairing the structure;(4) Predicted life of the structure.All these factors are related to economic and social considerations such as:(1) Initial cost of the construction;(2) Amortization funds for the duration of the construction;(3) Cost of physical and material damage due to the failure of the construction;(4) Adverse impact on society;(5) Moral and psychological views.The definition of all these parameters, for a given safety factor, allows construction at the optimum cost. However, the difficulty of carrying out a complete probabilistic analysis has to be taken into account. For such an analysis the laws of the distribution of the live load and its induced stresses, of the scatter of mechanical properties of materials, and of the geometry of the cross-sections and the structure have to be known. Furthermore, it is difficult to interpret the interaction between the law of distribution of strength and that of stresses because both depend upon the nature of the material, on the cross-sections and upon the load acting on the structure. These practical difficulties can be overcome in two ways. The first is to apply different safety factors to the material and to the loads, without necessarily adopting the probabilistic criterion. The second is an approximate probabilistic method which introduces some simplifying assumptions ( semi-probabilistic methods ) .。