材料力学性能实验报告
实验报告材料力学性能测试
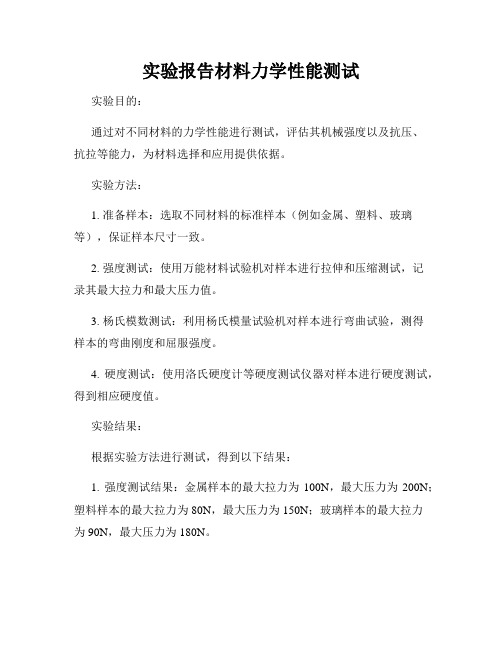
实验报告材料力学性能测试实验目的:通过对不同材料的力学性能进行测试,评估其机械强度以及抗压、抗拉等能力,为材料选择和应用提供依据。
实验方法:1. 准备样本:选取不同材料的标准样本(例如金属、塑料、玻璃等),保证样本尺寸一致。
2. 强度测试:使用万能材料试验机对样本进行拉伸和压缩测试,记录其最大拉力和最大压力值。
3. 杨氏模数测试:利用杨氏模量试验机对样本进行弯曲试验,测得样本的弯曲刚度和屈服强度。
4. 硬度测试:使用洛氏硬度计等硬度测试仪器对样本进行硬度测试,得到相应硬度值。
实验结果:根据实验方法进行测试,得到以下结果:1. 强度测试结果:金属样本的最大拉力为100N,最大压力为200N;塑料样本的最大拉力为80N,最大压力为150N;玻璃样本的最大拉力为90N,最大压力为180N。
2. 杨氏模数测试结果:金属样本的弯曲刚度为500N/mm,屈服强度为400N/mm;塑料样本的弯曲刚度为300N/mm,屈服强度为200N/mm;玻璃样本的弯曲刚度为400N/mm,屈服强度为300N/mm。
3. 硬度测试结果:金属样本的洛氏硬度为80;塑料样本的洛氏硬度为60;玻璃样本的洛氏硬度为70。
实验讨论:从实验结果可以看出,金属样本在强度、刚度和硬度方面表现出较高的数值,具有较好的机械性能。
塑料样本在各项测试指标中表现适中,而玻璃样本在拉伸和硬度方面较弱。
这些结果与我们对材料性质的常识相符。
实验结论:根据实验结果,我们可以得出以下结论:1. 对于需要具备高机械强度和刚度的应用场景,金属材料是一个较好的选择。
2. 对于一些耐腐蚀性、电绝缘性等特殊要求的应用,塑料材料是一个适宜的选择。
3. 玻璃材料在某些特定场景下可以作为透明、坚固的材料选用,但其机械性能相对较弱,需谨慎选择使用。
实验改进:1. 增加样本数量:为了提高实验的可靠性和准确性,可以增加样本数量以扩大样本数据集。
2. 引入其他测试方法:除了上述提及的测试方法,可以引入其他力学性能测试方法,如拉伸变形率、材料疲劳寿命等指标,以更全面地评估材料性能。
材料力学性能实验报告
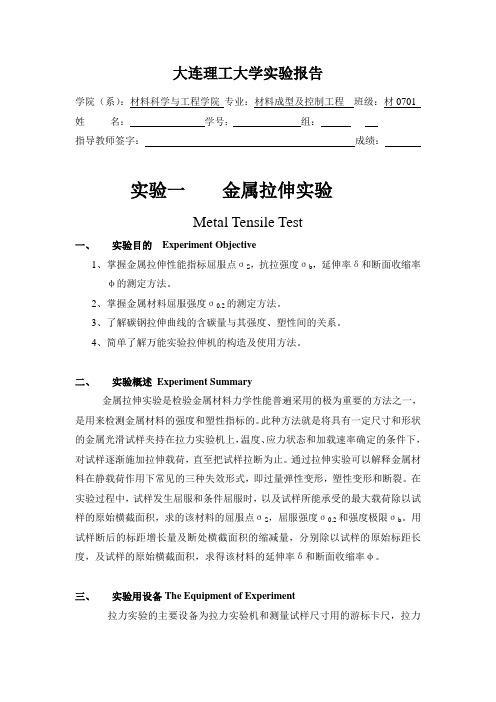
大连理工大学实验报告学院(系):材料科学与工程学院专业:材料成型及控制工程班级:材0701姓名:学号:组:___指导教师签字:成绩:实验一金属拉伸实验Metal Tensile Test一、实验目的Experiment Objective1、掌握金属拉伸性能指标屈服点σS,抗拉强度σb,延伸率δ和断面收缩率φ的测定方法。
2、掌握金属材料屈服强度σ0.2的测定方法。
3、了解碳钢拉伸曲线的含碳量与其强度、塑性间的关系。
4、简单了解万能实验拉伸机的构造及使用方法。
二、实验概述Experiment Summary金属拉伸实验是检验金属材料力学性能普遍采用的极为重要的方法之一,是用来检测金属材料的强度和塑性指标的。
此种方法就是将具有一定尺寸和形状的金属光滑试样夹持在拉力实验机上,温度、应力状态和加载速率确定的条件下,对试样逐渐施加拉伸载荷,直至把试样拉断为止。
通过拉伸实验可以解释金属材料在静载荷作用下常见的三种失效形式,即过量弹性变形,塑性变形和断裂。
在实验过程中,试样发生屈服和条件屈服时,以及试样所能承受的最大载荷除以试样的原始横截面积,求的该材料的屈服点σS,屈服强度σ0.2和强度极限σb。
用试样断后的标距增长量及断处横截面积的缩减量,分别除以试样的原始标距长度,及试样的原始横截面积,求得该材料的延伸率δ和断面收缩率φ。
三、实验用设备The Equipment of Experiment拉力实验的主要设备为拉力实验机和测量试样尺寸用的游标卡尺,拉力实验机主要有机械式和液压式两种,该实验所用设备原东德WPM—30T液压式万能材料实验机。
液压式万能实验机是最常用的一种实验机。
它不仅能作拉伸试验,而且可进行压缩、剪切及弯曲实验。
(一)加载部分The Part of Applied load这是对试样施加载荷的机构,它利用一定的动力和传动装置迫使试样产生变形,使试样受到力或能量的作用。
其加载方式是液压式的。
在机座上装有两根立柱,其上端有大横梁和工作油缸。
力学性能实验报告
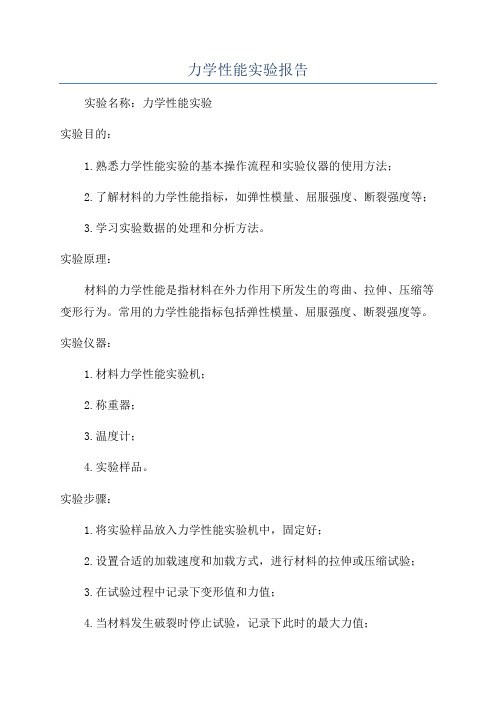
力学性能实验报告实验名称:力学性能实验实验目的:1.熟悉力学性能实验的基本操作流程和实验仪器的使用方法;2.了解材料的力学性能指标,如弹性模量、屈服强度、断裂强度等;3.学习实验数据的处理和分析方法。
实验原理:材料的力学性能是指材料在外力作用下所发生的弯曲、拉伸、压缩等变形行为。
常用的力学性能指标包括弹性模量、屈服强度、断裂强度等。
实验仪器:1.材料力学性能实验机;2.称重器;3.温度计;4.实验样品。
实验步骤:1.将实验样品放入力学性能实验机中,固定好;2.设置合适的加载速度和加载方式,进行材料的拉伸或压缩试验;3.在试验过程中记录下变形值和力值;4.当材料发生破裂时停止试验,记录下此时的最大力值;5.移除实验样品,进行下一组样品的实验。
实验数据处理与分析:1.根据实验数据计算实验样品的应变和应力;2.绘制应力-应变曲线,通过曲线的线性段来计算材料的弹性模量;3.根据应力-应变曲线的非线性段或材料破裂前的最大应力来计算材料的屈服强度;4.根据破裂时的最大力值来计算材料的断裂强度。
实验结果:1.绘制应力-应变曲线,通过斜率计算得出材料的弹性模量;2.通过非线性段或最大应力计算得出材料的屈服强度;3.通过破裂时的最大力值计算得出材料的断裂强度。
实验结论:通过力学性能实验,得出了材料的弹性模量、屈服强度、断裂强度等指标。
这些指标可以为材料的选用和设计提供参考依据,也可以为相关材料的研究提供实验数据支持。
此外,实验过程中的数据处理和分析方法也是力学性能实验的重要内容,掌握了这些方法可以更准确地评估材料的力学性能。
实验改进意见:1.增加实验样品数量和种类,以提高实验数据的准确性和可靠性;2.注意在实验过程中的温度控制,以减小温度对材料力学性能的影响;3.结合理论知识,对实验结果进行更详细的分析和解释。
以上是力学性能实验的实验报告,总字数为298字。
您可以根据实际情况进行修改和补充。
材料力学性能测试实验报告

材料力学性能测试实验报告为了评估材料的力学性能,本实验使用了拉力试验和硬度试验两种常见的力学性能测试方法。
本实验分为三个部分:拉力试验、硬度试验和数据分析。
通过这些试验和分析,我们可以了解材料的延展性、强度和硬度等性能,对材料的机械性质有一个全面的了解。
实验一:拉力试验拉力试验是常见的力学性能测试方法之一,用来评估材料的延展性和强度。
在拉力试验中,我们使用了一个万能材料试验机,将试样夹紧在两个夹具之间,然后施加拉力,直到试样断裂。
试验过程中我们记录了试验机施加的力和试样的伸长量,并绘制了应力-应变曲线。
实验二:硬度试验硬度试验是另一种常见的力学性能测试方法,用来评估材料的硬度。
我们使用了洛氏硬度试验机进行试验。
在实验中,将一个试验头按压在试样表面,然后测量试验头压入试样的深度,来衡量材料的硬度。
我们测得了三个不同位置的硬度,并计算了平均值。
数据分析:根据拉力试验得到的应力-应变曲线,我们可以得到材料的屈服强度、断裂强度和延伸率等参数。
屈服强度是指材料开始塑性变形的应变值,断裂强度是指材料破裂时的最大应变值,延伸率是指试样在断裂前的伸长程度。
根据硬度试验得到的硬度数值,我们可以了解材料的硬度。
结论:本实验通过拉力试验和硬度试验对材料的力学性能进行了评估。
根据拉力试验得到的应力-应变曲线,我们确定了材料的屈服强度、断裂强度和延伸率等参数。
根据硬度试验的结果,我们了解了材料的硬度。
这些数据可以帮助我们判断材料在不同应力下的性能表现,从而对材料的选用和设计提供依据。
总结:本实验通过拉力试验和硬度试验对材料的力学性能进行了评估,并通过应力-应变曲线和硬度数值来分析材料的性能。
通过这些试验和分析,我们对材料的延展性、强度和硬度等性能有了全面的了解。
这些结果对于材料的选用和设计具有重要意义,可以提高材料的应用性能和可靠性。
材料力学实验报告报告
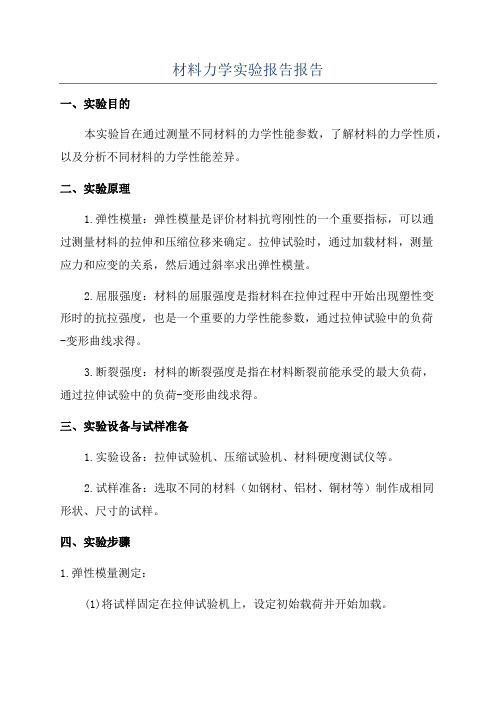
材料力学实验报告报告一、实验目的本实验旨在通过测量不同材料的力学性能参数,了解材料的力学性质,以及分析不同材料的力学性能差异。
二、实验原理1.弹性模量:弹性模量是评价材料抗弯刚性的一个重要指标,可以通过测量材料的拉伸和压缩位移来确定。
拉伸试验时,通过加载材料,测量应力和应变的关系,然后通过斜率求出弹性模量。
2.屈服强度:材料的屈服强度是指材料在拉伸过程中开始出现塑性变形时的抗拉强度,也是一个重要的力学性能参数,通过拉伸试验中的负荷-变形曲线求得。
3.断裂强度:材料的断裂强度是指在材料断裂前能承受的最大负荷,通过拉伸试验中的负荷-变形曲线求得。
三、实验设备与试样准备1.实验设备:拉伸试验机、压缩试验机、材料硬度测试仪等。
2.试样准备:选取不同的材料(如钢材、铝材、铜材等)制作成相同形状、尺寸的试样。
四、实验步骤1.弹性模量测定:(1)将试样固定在拉伸试验机上,设定初始载荷并开始加载。
(2)根据试验机上的位移计和负荷计,测量不同应力水平下的应变,并记录数据。
(3)通过绘制应力-应变曲线,根据直线部分的斜率求得材料的弹性模量。
2.屈服强度测定:(1)将试样固定在拉伸试验机上,设定初始载荷并开始加载。
(2)根据试验机上的压力计和位移计,测量不同载荷下的变形,并记录数据。
(3)通过绘制负荷-变形曲线,找到试样开始出现塑性变形的点,根据载荷计的读数求得材料的屈服强度。
3.断裂强度测定:(1)将试样固定在拉伸试验机上,设定初始载荷并开始加载。
(2)根据试验机上的压力计和位移计,测量试样在拉伸过程中的载荷和位移,并记录数据。
(3)通过绘制负荷-变形曲线,找到试样断裂前的最大负荷,并记录。
五、实验结果与讨论根据实验测量的数据,可以得到不同材料的力学性能参数,如弹性模量、屈服强度和断裂强度。
通过对比不同材料的实验结果,可以得出以下结论:1.钢材的弹性模量较大,机械性能优异。
2.铝材的屈服强度较低,耐腐蚀性能较好。
3.铜材的断裂强度较高,适用于承受较大载荷的工程应用。
国家开放大学《材料科学》金属材料的力学性能实验报告

国家开放大学《材料科学》金属材料的力学性能实验报告实验目的1. 掌握金属材料力学性能的基本测试方法。
2. 了解材料在不同温度和加载速度下的力学性能变化。
3. 分析实验结果,探讨材料力学性能与微观结构的关系。
实验原理金属材料的力学性能主要包括抗拉强度、抗压强度、弹性模量等。
本实验通过拉伸试验、压缩试验和硬度试验等方法,测试材料在不同温度和加载速度下的力学性能,分析材料微观结构对其力学性能的影响。
实验材料与设备1. 实验材料:低碳钢、不锈钢、铜等。
2. 实验设备:万能材料试验机、高温炉、硬度计等。
实验方法与步骤1. 拉伸试验:a. 按照国家标准制备试样。
b. 将试样装入万能材料试验机。
c. 以不同的加载速度和温度进行拉伸试验。
d. 记录应力-应变曲线,计算抗拉强度、弹性模量等参数。
2. 压缩试验:a. 按照国家标准制备试样。
b. 将试样装入万能材料试验机。
c. 以不同的加载速度和温度进行压缩试验。
d. 记录应力-应变曲线,计算抗压强度等参数。
3. 硬度试验:a. 按照国家标准制备试样。
b. 使用硬度计在不同温度下进行硬度测试。
c. 记录硬度值,计算硬度系数。
实验结果与分析1. 拉伸试验结果:- 低碳钢:抗拉强度约为400 MPa,弹性模量约为200 GPa。
- 不锈钢:抗拉强度约为500 MPa,弹性模量约为180 GPa。
- 铜:抗拉强度约为200 MPa,弹性模量约为110 GPa。
2. 压缩试验结果:- 低碳钢:抗压强度约为500 MPa。
- 不锈钢:抗压强度约为600 MPa。
- 铜:抗压强度约为300 MPa。
3. 硬度试验结果:- 低碳钢:硬度系数约为0.2。
- 不锈钢:硬度系数约为0.15。
- 铜:硬度系数约为0.1。
结论1. 金属材料的力学性能受微观结构影响显著。
2. 随着温度的升高,材料力学性能降低。
3. 加载速度对材料力学性能有一定影响,加载速度越高,材料力学性能越差。
建议1. 进一步研究材料微观结构与力学性能的关系,为材料设计提供理论依据。
材料的力学性能实验报告
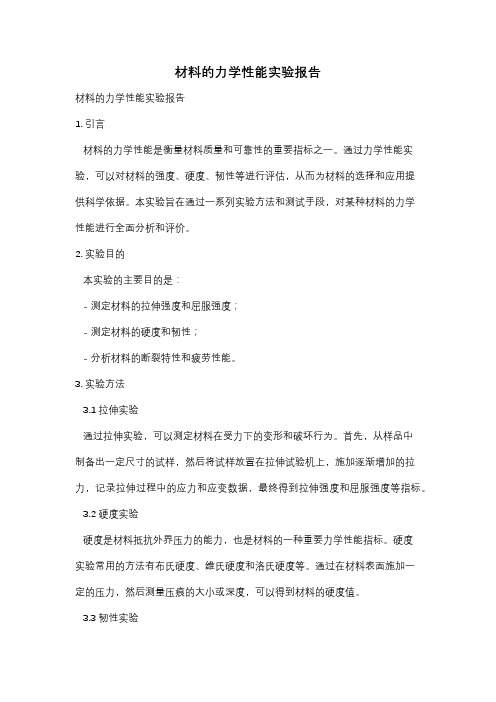
材料的力学性能实验报告材料的力学性能实验报告1. 引言材料的力学性能是衡量材料质量和可靠性的重要指标之一。
通过力学性能实验,可以对材料的强度、硬度、韧性等进行评估,从而为材料的选择和应用提供科学依据。
本实验旨在通过一系列实验方法和测试手段,对某种材料的力学性能进行全面分析和评价。
2. 实验目的本实验的主要目的是:- 测定材料的拉伸强度和屈服强度;- 测定材料的硬度和韧性;- 分析材料的断裂特性和疲劳性能。
3. 实验方法3.1 拉伸实验通过拉伸实验,可以测定材料在受力下的变形和破坏行为。
首先,从样品中制备出一定尺寸的试样,然后将试样放置在拉伸试验机上,施加逐渐增加的拉力,记录拉伸过程中的应力和应变数据,最终得到拉伸强度和屈服强度等指标。
3.2 硬度实验硬度是材料抵抗外界压力的能力,也是材料的一种重要力学性能指标。
硬度实验常用的方法有布氏硬度、维氏硬度和洛氏硬度等。
通过在材料表面施加一定的压力,然后测量压痕的大小或深度,可以得到材料的硬度值。
3.3 韧性实验韧性是材料在受力下发生塑性变形和吸收能量的能力。
韧性实验主要通过冲击试验来评估材料的韧性。
在冲击试验中,将标准试样固定在冲击机上,然后施加冲击力,观察试样的破裂形态和吸能能力,从而得到材料的韧性指标。
3.4 断裂特性分析通过断裂特性分析,可以了解材料在破坏过程中的断裂形态和机制。
常用的断裂特性分析方法有金相显微镜观察、扫描电镜观察和断口形貌分析等。
通过对破坏试样进行断口观察和形貌分析,可以揭示材料的断裂行为和破坏机制。
3.5 疲劳性能测试疲劳性能是材料在交变载荷下的抗疲劳破坏能力。
疲劳性能测试常用的方法有拉伸疲劳试验和弯曲疲劳试验等。
通过施加交变载荷,观察材料在不同循环次数下的变形和破坏情况,可以评估材料的疲劳寿命和抗疲劳性能。
4. 实验结果与分析通过上述实验方法和测试手段,得到了某种材料的力学性能数据。
在拉伸实验中,测得该材料的拉伸强度为XXX,屈服强度为XXX。
材料力学性能实验报告.

材料学性能实院系:材料学院姓名:王丽朦学号:200767027验报力告实验目的:通过拉伸试验掌握测量屈服强度,断裂强度,试样伸长率,界面收缩率的方法;通过缺口拉伸试验来测试缺口对工件性能的相关影响;通过冲击试验来测量材料的冲击韧性;综合各项试验结果,来分析工件的各项性能;通过本实验来验证材料力学性能课程中的相关结论,同时巩固知识点,进一步深刻理解相关知识;实验原理:1)屈服强度金属材料拉伸试验时产生的屈服现象是其开始产生宏观的塑性变形的一种标志。
弹性变形阶段向塑性变形阶段的过渡,表现在试验过程中的现象为,外力不增加即保持恒定试样仍能继续伸长,或外力增加到某一数值是突然下降,随后,在外力不增加或上下波动情况下,试样继续伸长变形,这便是屈服现象。
呈现屈服现象的金属材料拉伸时,试样在外力不增加仍能继续伸长时的应力称为屈服点,记作(T S 屈服现象与三个因素有关:(1)材料变形前可动位错密度很小或虽有大量位错但被钉扎住,如钢中的位错为杂质原子或第二相质点所钉扎;(2)随塑性变形发生,位错快速增殖;(3)位错运动速率与外加应力有强烈的依存关系。
影响屈服强度的因素有很多,大致可分为内因和外因。
内因包括:金属本性及晶格类型的影响;晶界大小和亚结构的影响;还有溶质元素和第二相的影响等等。
通过对内因的分析可表征,金属微量塑性变形抗力的屈服强度是一个对成分、组织极为敏感的力学性能指标,受许多内在因素的影响,改变合金成分或热处理工艺都可使屈服强度产生明显变化。
外因包括:温度、应变速率和应力状态等等。
总之,金属材料的屈服强度即受各种内在因素的影响,又因外在条件不同而变化,因而可以根据人们的要求予以改变,这在机件设计、选材、拟订加工工艺和使用时都必须考虑到。
2)缺口效应由于缺口的存在,在静载荷作用下,缺口截面上的应力状态将发生变化,产生所谓的缺口效应”从而影响金属材料的力学性能。
缺口的第一个效应是引起应力集中,并改变了缺口前方的应力状态,使缺口试样或机件所受的应力由原来的单向应力状态改变为两向或三向应力状态,也就是出现了CX (平面应力状态)或cy与CZ (平面应变状态),这要视板厚或直径而定。
- 1、下载文档前请自行甄别文档内容的完整性,平台不提供额外的编辑、内容补充、找答案等附加服务。
- 2、"仅部分预览"的文档,不可在线预览部分如存在完整性等问题,可反馈申请退款(可完整预览的文档不适用该条件!)。
- 3、如文档侵犯您的权益,请联系客服反馈,我们会尽快为您处理(人工客服工作时间:9:00-18:30)。
大连理工大学实验报告学院(系):材料科学与工程学院专业:材料成型及控制工程班级:材0701姓名:学号:组:___指导教师签字:成绩:实验一金属拉伸实验Metal Tensile Test一、实验目的Experiment Objective1、掌握金属拉伸性能指标屈服点σS,抗拉强度σb,延伸率δ和断面收缩率φ的测定方法。
2、掌握金属材料屈服强度σ0.2的测定方法。
3、了解碳钢拉伸曲线的含碳量与其强度、塑性间的关系。
4、简单了解万能实验拉伸机的构造及使用方法。
二、实验概述Experiment Summary金属拉伸实验是检验金属材料力学性能普遍采用的极为重要的方法之一,是用来检测金属材料的强度和塑性指标的。
此种方法就是将具有一定尺寸和形状的金属光滑试样夹持在拉力实验机上,温度、应力状态和加载速率确定的条件下,对试样逐渐施加拉伸载荷,直至把试样拉断为止。
通过拉伸实验可以解释金属材料在静载荷作用下常见的三种失效形式,即过量弹性变形,塑性变形和断裂。
在实验过程中,试样发生屈服和条件屈服时,以及试样所能承受的最大载荷除以试样的原始横截面积,求的该材料的屈服点σS,屈服强度σ0.2和强度极限σb。
用试样断后的标距增长量及断处横截面积的缩减量,分别除以试样的原始标距长度,及试样的原始横截面积,求得该材料的延伸率δ和断面收缩率φ。
三、实验用设备The Equipment of Experiment拉力实验的主要设备为拉力实验机和测量试样尺寸用的游标卡尺,拉力实验机主要有机械式和液压式两种,该实验所用设备原东德WPM—30T液压式万能材料实验机。
液压式万能实验机是最常用的一种实验机。
它不仅能作拉伸试验,而且可进行压缩、剪切及弯曲实验。
(一)加载部分The Part of Applied load这是对试样施加载荷的机构,它利用一定的动力和传动装置迫使试样产生变形,使试样受到力或能量的作用。
其加载方式是液压式的。
在机座上装有两根立柱,其上端有大横梁和工作油缸。
油缸中的工作活塞支持着小横梁。
小横梁和拉杆、工作台组成工作框架,随工作活塞生降。
工作台上方装有承压板和弯曲支架,其下方为钳口座,内装夹持拉伸试样用的上夹头。
下夹头安装在下钳口座中,下钳口座固定在升降丝杆上。
当电动机带动油泵工作时,通过送油阀手轮打开送油阀,油液便从油箱经油管和进入工作油缸,从而推动活塞连同工作框架一起上升。
于是在工作台与大横梁之间就可进行压缩、弯曲等实验,在工作台与下夹头之间就进行拉伸实验。
实验完毕后,关闭送油阀、旋转手轮打开回油阀,则工作油缸中的油液便经油管泄回油箱,工作台下降到原始位置。
(二)测力部分The Part of Measuring Force加载时,油缸中的油液推动工作活塞的力与试样所承受的力随时处于平衡状态。
如果用油管和将工作油缸和测力油缸连同,此油压便推动测力活塞,通过连杆框架使摆锤绕支点转动而抬起。
同时,摆锤上方的推板便推动水平齿杆,使齿轮带动指针旋转。
指针旋转的角度与油压亦即与试样所承受的载荷成正比,因此在测力度盘上便可读出试样受力的量值。
四、试样Sample拉伸试样,通常加工成圆型或矩形截面试样,其平行长度L0等于5d或10d (前者为长试样,后者为短试样),本实验用短试样,即L0=5d。
本实验所用的试样形状尺寸如图1—1所示。
图1-1圆柱形拉伸试样及尺寸五 拉伸性能指标测定方法 The Measuement Method of Tensile Performance Index1、屈服点σS 的测定 The Measuement of Yield Point σS试样在拉伸过程中,载荷不增加或开始降低而试样仍能继续伸长时的恒定最大或最小载荷所对应的应力,分别为屈服点σS ,上屈服点σSU ,下屈服点σSL 。
屈服点可借助于试验机测力度盘的指针或拉伸曲线来确定。
(1)指针法:当测力度盘的指针停止转动的恒定载荷或第一次回转的最小载荷即为所求的屈服载荷P S 。
(2) 图示法:在拉伸曲线上找出屈服平台的恒定负荷或第一次下降的最小载荷,为所求的屈服点载荷P S 。
求出Ps 后,按下式可算出屈服点σS 。
σS =Ps /Fo (MN /m 2或Mpa )图1—2 屈服点负载确定2、屈服强度σ0.2的测定 The Measuement of Yield Strength σ0.2对于拉伸曲线无明显屈服现象的材料,则必须测其屈服强度。
屈服强度为试样在拉伸过程中,规定塑性变形为0.2%时的应力作为条件屈服点,称屈服强度。
(1)图解法:Diagram Method在拉伸曲线上,自弹性直线段与横坐标轴的交点0齐截取一等于残余相对伸长为0.002mm 的距离OA ,再从A 点作平行与弹性直线段的AB 线交于拉伸曲线于B 点。
B 点载荷即为所求的屈服强度载荷P 0.2,其伸长坐标轴放大倍数应不小于50倍(1—4)。
(2)卸力法(引伸计法) The method Unload对试样施加约相当于预期规定残余伸长应力10%的力Px 后,装上引申计,继续施力至2P 。
保持5—10秒,再卸直Po ,记下引申计读数作为条件零点。
从Po 起第一次施力至试样在引申计标距内产生的总伸长为n ×Le ×εr+(1~2)分格。
(Le 为规定残余伸长,即引申计标距与规定残余伸长应为σ0.2所要求的伸长0.2%的积。
εr 为弹性伸长)。
σ0.2=P 0.2/F o3、抗拉强度σb 的测定 The Measuement of Tensile Strength σb实验拉至断裂,从拉伸曲线上确定实验过程的最大力,或从测力度盘上读取最大力。
试样拉伸达到“最大载荷Pb ”以前,伸长在标距范围内均匀分布。
从“最大载荷”开始,试样上产生局部伸长或颈缩现象。
细颈出现后,截面迅速减小。
继续拉伸所需的载荷也变小,直至断裂。
最初对试样加载时,测力指针(主针)即随栽荷的增加而增加。
当载荷达到最大值时,测力指针减少,减少到某一值时,试样断裂,按下式计算。
σb =Pb /Fo4、伸长率δ的测定 The Measuement of Elongation Rate δ伸长率δ为试样拉断后标距长度的增量与原标距长度的百分比δ=(Lk —Lo/Lo )×100%Le :引伸计标距 n :伸长方法倍数 图1—3 屈服强度负载的确定P O伸长A 0.2% n Le长、短试样的断后伸长率分别为δ5,δ10表示。
试样在拉伸前先将标距部分划分10等份,划上标距,测量断后伸长时,分两种情况。
(1)如断口到邻近标距断点的距离大于(1/3)Lo ,可直接测量断后两点的距离为Lk ;(2)如断口到邻近标距端点小于或等于(1/3)Lo ,要用位移法换算。
如图1—5所示。
先在长段上从断口处O 截取一段OC ,其长度等于1/2或稍大于(不大于一格)1/2标距的总格数;再由C 向断口方向截取一段CD ,令CD 的格数等于C 到邻近标距端点A 的格数CA ;断后BC+CD 的长度便是L K 。
这样,就相当于把CD 移到试样标距的另一端,接到B 处,变为断口在中间。
5、断面收缩率φ的测定 The Measuement of Contraction of cross Sectional Area δ断面收缩率φ为试样拉断后颈缩处横截面积的最大缩减量与原横截面积的百分比,即00100%K F F F -Φ=⨯ 拉断后颈缩处截面积F K 的测定,原形试样在颈缩最小处两个互相垂直方向上测其直径,用两者的算术平均值计算。
六 实验步骤 Experiment Procedure1、用游标卡尺测量原始直径d O (在试样上、中、下段互相垂直的两个方向分别测量)取其最小值。
2、在试样上用划线仪,画出原始标距100mm (中间以10mm 为间隔画点,以备用位移法计算δ)3、根据材料估计本实验的载荷使用量程,选好读数盘。
4、将试样安装在上夹头内,再移动下夹头使之达到适当位置,将试样下端加紧,要求试样夹正,并对准中心,以保证试样轴向受力。
5、打开送油阀,缓慢加载,当测力指针不动或第一次往回转时的最小载荷,就是屈服载荷P S 。
过屈服阶段后,可稍快一些加栽,直至试样断裂,记录下指针指示的断裂前的最大栽荷Pb 。
关闭油门停机,取下试样。
6、断裂试样的测量。
将两段试样尽量对紧在一起,用游标卡尺直接测量或用位移法换算后测量的标距长度L K ,并用游标卡尺在断口最小截面处测量断口直径。
七 实验数据记录与计算 The experimental results1、实验结果加载数据:S P =32.5 KN b P =50.5 KN其中:原始直径L 0为三次测量结果10.02mm 、10.12mm 、10.20mm 的最小值 2、实验数据处理(1) 根据的d 0、d k 求F 0、F K :2220081.78)2/02.10(14.3)2/(mm d F =⨯==π222180.39)2/12.7(14.3)2/(mm d F K =⨯==π(2)强度指标:屈服极限:MPa F P s s 15.41281.78105.3230=⨯==σ 强度极限:MPa F P b b 42.64081.78105.5030=⨯==σ (3)塑性指标:断面延伸率: %20.27%100505060.63%100)(00=⨯-=⨯-=L L Lk δ 断面收缩率: %51.49%10081.7880.3981.78%100)(00=⨯-=⨯-=F F F K ψ八 思考题 Questions1、退火的低碳钢,中碳钢和高碳钢的屈服现象,在拉伸图上的区别?为什么?答:低碳钢的拉伸图上分为四个阶段:弹性变形阶段、不均匀塑性变形(即屈服现象)、均匀塑性变形和不均匀集中塑性变形(即颈缩);而中、高碳钢的拉伸图上无明显屈服现象,即由弹性变形阶段、均匀塑性变形和不均匀集中塑性变形(即颈缩)。
原因可能是屈服现象是位错运动和增殖的结果,由于中、高碳钢中第二相的影响较大,阻碍或约束位错的运动,从而使中、高碳钢中屈服现象不明显。
2、碳钢、含碳量与其强度、塑性的关系。
答:碳钢中,在含碳量小于共析成分0.77%时,随含碳量的升高、其强度和硬度增加,塑性下降;而在高于0.77%后,其硬度继续增高,但强度下降,塑性也降低。
大连理工大学实验报告学院(系):材料科学与工程学院专业:材料成型及控制工程班级:材0701姓名:学号:组:___指导教师签字:成绩:实验二缺口拉伸实验The indentation pulls to stretch the experiment一实验目的Experiment the purpose1、了解材料在硬性应力状态和应力集中下的脆化倾向。