拨叉夹具设计.doc
车床拨叉工艺规程及专用夹具设计

车床拨叉工艺规程及专用夹具设计1.引言本文档旨在介绍车床拨叉工艺规程及专用夹具设计的相关内容。
拨叉是一种常用的机械零件,用于传递力量和转换方向,在机械制造中有着广泛的应用。
通过规范化的工艺规程和合理设计的专用夹具,可以提高制造效率和产品质量。
2.工艺规程2.1 材料准备车床拨叉制造常用的材料有碳钢、合金钢等。
在进行车床加工之前,首先需要对选用的材料进行准备。
包括材料的锯切和加热处理等。
2.1.1 锯切根据工艺要求和零件尺寸,将选用的材料进行锯切。
在锯切过程中,需要确保切割平整、垂直,并避免产生过多的热量。
2.1.2 加热处理选用的材料可能需要经过热处理,以提高其力学性能。
根据材料的类型和要求,进行适当的加热处理,如淬火、回火等。
2.2 制定车床加工工艺根据拨叉的设计图纸和工艺要求,制定车床加工工艺。
包括车床刀具的选择、工件夹持方式、切削参数以及加工顺序等。
在制定过程中需要考虑到加工前后的尺寸精度、表面粗糙度等要求。
2.3 车床加工操作按照制定好的工艺方案进行车床加工。
在加工过程中,需要严格控制切削参数,如切削速度、进给量和切削深度等。
及时进行刀具更换、刀具磨削等操作,保证加工质量。
2.4 表面处理车床加工完成后,可能需要对拨叉的表面进行处理,以提高其耐腐蚀性和装饰效果。
常用的表面处理方法包括电镀、喷涂和热处理等。
2.5 检验与质量控制对加工完成的拨叉进行检验。
根据设计要求和工艺规范,进行尺寸检测、硬度测试等。
确保产品质量符合标准要求。
3.专用夹具设计3.1 夹具选型根据拨叉的形状、尺寸和加工要求,选择合适的夹具。
夹具应能够稳定夹持工件,并保证加工过程中的精度和安全。
3.2 夹具结构设计根据拨叉的形状和夹持需求,设计夹具的结构。
包括夹具座、定位块、顶尖、夹具螺杆等。
要考虑到夹具结构的刚性和稳定性,以及操作的方便性。
3.3 夹具制造和调试根据夹具设计图纸,进行夹具的制造和调试。
确保夹具的加工精度和质量。
对倒挡拨叉夹具设计说明书

对倒挡拨叉夹具设计说明书夹具课程设计说明书——对倒挡拨叉铣床夹具设计学院:中德学院姓名:曹亦丰指导老师:冯鹤敏0823020210一、夹具设计任务1、被加工工件视图2、被加工工件的结构特点3、工艺过程的选取二、“对倒挡拨叉夹具”夹具设计方案的确定1、基准面的挑选(夹具体内容方式的确认)2、定位方式及元器件选择3、包住方式及元器件挑选三、主要零件设计的说明3、包住力的排序,误差排序5、夹具非标零件加工工艺(底座)四、夹具的加装建议在机床加工工件时,为了保证加工精度和生产效率,必须使用工件在机床上相对刀具占有正确的位置,这个过程称之为定位。
为了使工件已经获取的正确位置在切削过程中因为切削力、惯性力、重力等外力作用而不被破坏,必须对工件进行夹紧,这个过程称之为夹紧。
定位和夹紧的全过程,称之为工件的夹装。
在机床上用于装夹工件的装置,即为机床夹具。
在制造技术迅猛发展的今天,无论是传统机床还是数控机床,加工中心上,仍是不可或缺的重要工艺设备。
通过机床的夹具设计,不仅可以培养综合运用机械设计制造的知识,还可以得到工程设计的初步训练。
一.夹具设计任务1,被加工工件的视图2、工艺过程的确认研究工艺过程,分析该工序所加工的部位、加工要求、定位夹紧部分和前后加工工序的关系等。
按照建议须要将被加工工件从中间边线展开研磨,建议掌控尺寸4,因为在之前工序被加工件的地面已经赢得了较低的精度,用圆柱定位订货定位其直角圆孔d14,侧面用调节器车轴,工件的地面为基面。
通过此定位,同时实现了5个方向的自由度约束。
最后可以利用压板从上直面工件展开包住,利用卧式铣床对工件研磨。
二.夹具设计方案的确定1,基准面的挑选用圆柱定位销和可调支承组合定位,销的端面和工件的底面接触实现工件的定位,在两侧使用压板,螺旋夹紧机构对工件实行夹紧。
——————————————————————2,定位方式及元器件选择综合1所述的方案,主要定位就是圆孔定位和底面定位。
倒档拨叉专用夹具设计(钻Φ18孔夹具的设计)

优秀设计制造工艺学夹具课程设计《倒档拨叉专用夹具说明书》姓名:学号:班级:指导老师:设计时间:目录一、设计题目 (3)二、零件图及加工工序分析 (4)三、设计方案 (6)1、夹具设计方案2、夹紧装置的设计3、导向装置的设计及其他装置结构.夹具体的确定4、绘制夹具结构图5、确定夹具技术要求和有关尺寸,公差配合四、夹具零部件的结构 (10)五、定位误差的计算 (14)六、致谢 (15)七、参考文献 (16)一、设计题目“倒档拨叉”专用夹具设计二、零件图及加工工序分析1、倒档拨叉零件图如图1所示:图1 倒档拨叉零件图倒档拨叉材料为QT450-10,即球墨铸铁,最小抗拉强度为450MPa,最低延伸率为10。
根据机械加工材料等相关资料可以知道:球墨铸铁既有灰铸铁的优点,即具有高的抗压强度、优良的耐磨性和消震性,低的缺口敏感性。
同时具有与中碳钢媲美的抗拉强度、弯曲疲劳强度及良好的塑性与韧性,此外,还可以通过合金化及热处理来改善与提高它的性能,所以生产上已用球墨铸铁代替中碳钢及中碳合金钢制造发动机的曲轴、连杆、凸轮轴和机床的主轴等。
QT450-10主要用于汽车、拖拉机底盘零件等。
由于该倒档拨叉外形复杂,又是薄壁零件,属于大批量生产,故毛坯采用金属型铸造。
加工机床部分采用通用机床,部分采用专用机床;按零件分类,部分布置成流水线,部分布置成机群式;广泛采用专用夹具,可调夹具;按零件产量和精度,部分采用通用刀具和量具,部分采用专用刀具和量具;部分采用划线找正装夹,广泛采用通用或专用夹具装夹;有较详细的工艺规程,用工艺卡管理生产。
根据零件图可知,零件整体要求精度较高。
其中Φ18孔中心线和叉脚开档脚面有垂直度要求,并且Φ18孔中心线自身有直线度要求,被测槽面与Φ8.7孔中心线有对称度要求。
Φ26圆柱的上下端面粗糙度要求为Ra2.5,槽内面两侧的粗糙度要求为Ra12.5,槽面粗糙度要求为Ra2.5,叉脚开档脚面的粗糙度要求为Ra6.3,脚面内侧的粗糙度要求为Ra12.5,操纵槽端面的粗糙度要求为Ra2.5。
拨叉夹具设计说明书

拨叉夹具说明书年级:学号:姓名:专业:指导老师:2015年7月目录一、夹具定位及夹紧方案 (2)二、拨叉夹具设计说明 (4)1、问题的提出 (4)2、定位原理及实现 (4)3、切削力及夹紧力计算 (5)4、误差分析 (9)5、实际所需夹紧力的计算 (14)6、零件材料选择 (14)三、参考文献 (16)一、夹具定位及夹紧方案拨叉夹具:夹紧:说明:长:340mm 宽:60mm 高:60mm铣套:总长:45mm总宽:15mm总高:20mm铣口长:14mm铣口宽:15mm铣口高:17mm 铣刀:立铣刀直径范围2-50mm:取:12mm三维模型:二、拨叉夹具设计夹具是组合机床的重要组成部分,是根据机床的工艺和结构方案的具体要求而专门设计的。
它是用于实现被加工零件的准确定位、夹压、刀具的导向以及装卸工件时的限位等作用。
为了提高劳动生产率,保证加工质量,降低劳动成本,需要设计专用夹具。
1、问题的提出夹具是组合机床的重要组成部分,是根据机床的工艺和结构方案的具体要求而专门设计的。
它是用于实现被加工零件的准确定位、夹压、刀具的导向以及装卸工件时的限位等作用。
本夹具主要用于铣宽14H7的槽,且为大批大量生产。
在保证提高劳动生产率,降低劳动强度的同时可以设计选用比较简单的夹具。
2、定位原理及其实现由零件图可知,槽所在的面与中心线存在垂直度误差,在加工槽时应保持工件的平稳,应选择小圆柱底端面为定位基准。
根据被加工零件的结构特征,选择定位基准。
由夹具图可以得出,V形块约束X向的移动,Y向的移动,X向的转动,Y向的转动;工件与V形块的背面接触简化成线,则约束X向的移动,底面约束Z向的移动,X向的转动,Y向的转动,则形成了过定位。
限制的自由度V形块:X向的移动,Y向的移动,X向的转动,Y向的转动底面:Z向的移动,X向的转动,Y向的转动线:X向的移动过定位为:X向的移动,X向的转动,Y向的转动。
由于此过定位对零件加工时产生的误差较小,所以可以忽略不计。
汽车拨叉架工艺分析及其夹具设计说明书.doc
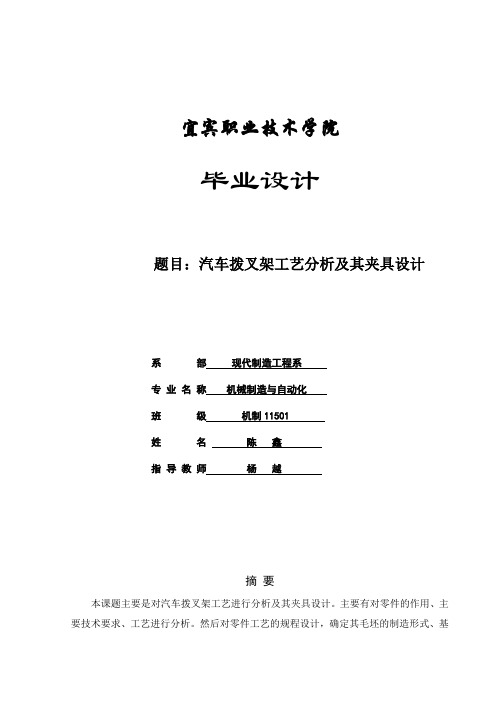
宜宾职业技术学院毕业设计题目:汽车拨叉架工艺分析及其夹具设计系部现代制造工程系专业名称机械制造与自动化班级机制11501姓名陈鑫指导教师杨越摘要本课题主要是对汽车拨叉架工艺进行分析及其夹具设计。
主要有对零件的作用、主要技术要求、工艺进行分析。
然后对零件工艺的规程设计,确定其毛坯的制造形式、基面的选择,制定出工艺路线。
确定机械加工余量、工序尺寸及毛坯尺寸。
确定切削用量及基本用时。
最后根据夹具组成、分类、特点、技术要求,设计出专用夹具。
关键词:拨叉架;工艺设计;夹具设计目录1 绪论 (1)2 拨叉的工艺分析及生产类型的确定 (2)2.1拨叉的用途 (2)2.2拨叉的技术要求 (2)2.3审查拨叉的工艺性 (3)2.4确定拨叉的生产类型 (3)3 确定毛坯、绘制毛坯简图及零件图 (4)3.1选择毛坯 (4)3.2确定毛坯的尺寸公差和机械加工余量 (4)3.2.1基本参数 (4)3.2.2公差等级 (5)3.2.3公差带的位置 (5)4 拟定拨叉工艺路线 (6)4.1定位基准的选择 (6)4.1.1精基准的选择 (6)4.1.2粗基准的选择 (6)4.2表面加工方法的确定 (6)4.3加工阶段的划分 (7)4.4工序的集中与分散 (8)4.5工序顺序的安排 (8)4.5.1机械加工工序 (8)4.5.2热处理工序 (8)4.5.3辅助工序 (8)4.6确定工艺路线 (9)5 加工余量、工序尺寸和公差的确定 .................................................................................. 106 切削用量、时间定额的计算 .............................................................................................. 17 6.1切削用量的计算 .............................................................................................................. 17 6.2时间定额的计算 .............................................................................................................. 20 6.2.1基本时间mt 的计算 (20)6.2.2辅助时间a t的计算 (21)6.2.3其他时间的计算 ...................................................................................................... 22 6.2.4单件时间djt 的计算 (22)7 夹具设计 .............................................................................................................................. 24 7.1夹具的分类 ...................................................................................................................... 24 7.2夹具的分析 ...................................................................................................................... 24 7.3夹具的功能 ...................................................................................................................... 25 7.4机床夹具的基本组成 ...................................................................................................... 25 7.5工件的定位 ...................................................................................................................... 26 7.5.1 六点定位原理 ....................................................................................................... 26 7.5.2定位方式 .................................................................................................................. 26 7.5.3定位方案的选择 ...................................................................................................... 27 7.5.4定位误差 .................................................................................................................. 27 7.6夹紧机构设计应满足的要求 .......................................................................................... 27 7.7夹紧力的确定 .................................................................................................................. 28 7.8夹紧力方向的确定 .......................................................................................................... 28 7.9夹紧机构 .......................................................................................................................... 28 7.10切削力及夹紧力的计算 ................................................................................................ 28 7.11夹具设计及操作说明 .................................................................................................... 29 总 结 ........................................................................................................................................ 30 参考文献 . (31)绪论工艺课程是以研究机械加工工艺和夹具设计为主的技术学科,具有很强的实践性,要求学习过程中应紧密联系生产与实践,同时它又具有很强的综合性,而工装夹具是工艺装备中的一个重要环节,目前,也是机械制造业的一个瓶颈。
拨叉夹具课程设计

拨叉夹具课程设计一、教学目标本节课的教学目标是让学生掌握拨叉夹具的基本原理和结构,了解其在汽车制造中的应用,培养学生对机械制造技术的兴趣和认识。
具体目标如下:1.知识目标:(1)能描述拨叉夹具的定义、作用和基本结构;(2)能解释拨叉夹具在汽车制造中的重要性;(3)了解不同类型的拨叉夹具及其特点。
2.技能目标:(1)能通过观察和分析,识别不同类型的拨叉夹具;(2)能运用所学知识,分析解决实际问题;(3)能熟练操作实验设备,进行拨叉夹具的组装和调试。
3.情感态度价值观目标:(1)培养学生对机械制造技术的兴趣,激发学生探究欲望;(2)培养学生团队协作、动手实践的能力;(3)培养学生珍惜劳动成果、精益求精的工匠精神。
二、教学内容本节课的教学内容主要包括以下几个部分:1.拨叉夹具的定义、作用和基本结构;2.拨叉夹具在汽车制造中的应用;3.不同类型的拨叉夹具及其特点;4.拨叉夹具的组装和调试方法。
三、教学方法为了提高教学效果,本节课将采用以下教学方法:1.讲授法:讲解拨叉夹具的基本原理、结构和应用;2.讨论法:分组讨论不同类型的拨叉夹具的特点;3.案例分析法:分析实际案例,了解拨叉夹具在汽车制造中的应用;4.实验法:操作实验设备,进行拨叉夹具的组装和调试。
四、教学资源为了支持教学内容的实施,我们将准备以下教学资源:1.教材:提供相关章节,介绍拨叉夹具的基本原理、结构和应用;2.参考书:提供相关资料,加深学生对拨叉夹具的了解;3.多媒体资料:制作PPT、视频等,直观展示拨叉夹具的组装和调试过程;4.实验设备:准备拨叉夹具实验装置,供学生动手操作。
通过以上教学资源的使用,我们将帮助学生更好地掌握拨叉夹具的知识,提高学生的实践能力,培养学生的创新精神和团队合作意识。
五、教学评估本节课的评估方式将包括以下几个方面:1.平时表现:评估学生在课堂上的参与程度、提问回答等情况,以了解学生的学习态度和理解程度;2.作业:布置相关的练习题,评估学生的知识掌握和应用能力;3.考试:安排一次期中考试,全面测试学生对拨叉夹具知识的掌握情况。
拨叉夹具设计说明书

拨叉夹具设计说明书(总16页)--本页仅作为文档封面,使用时请直接删除即可----内页可以根据需求调整合适字体及大小--机械制造课程设计拨叉钻床夹具设计专业机械设计制造与自动化学生姓名班级学号学校完成日期机械制造工程原理课程设计任务书一、设计题目设计拨叉,钻螺纹孔的专用夹具。
二、原始依据1.生产类型:成批生产;2.零件图样。
三、设计内容1.零件图1张;2.毛坯草图1张;3.制定零件的机械加工工艺规程,填写机械加工工艺过程卡片及指定工序的机械加工工序卡片各1份。
或填入机械加工工艺过程综合卡片;4.设计指定的专用夹具,绘制夹具装配总图1张,绘制所设计夹具的大件零件图1张;5.编写设计说明书1份。
目录一、零件的工艺分析及生产类型的确定 (4)二、加工方法的选择及工艺路线的制定 (5)三、夹具方案的探讨 (5)四、工件的夹紧设计理论 (10)五、夹具设计 (13)六、夹紧装置的设计 (13)七、夹具体与机床连接部分与定位 (13)八、小结 (15)九、参考文献 (16)一、零件的工艺分析及生产类型的确定1. 零件的作用零件是拨叉,用在操纵机构中比如改变车床滑移齿轮的位置,实现变速;或者应用于控制离合器的啮合,断开的机构中,从而控制横向获纵向进给。
2. 确定生产类型根据设计任务书可知:成批生产3. 零件的工艺分析零件的视图正确、完整。
公差及技术要求齐全。
零件图如下:根据零件图的要求,要加工螺纹孔为,,其中心与基中面有精度要求,必须保证其尺寸。
二、加工方法的选择及工艺路线的制定1. 定位基准的选择(1)根据零件图纸的要求,零件的定位基准为轴的中心线。
这样可以保证相应的尺寸公差,圆度,跳动的精度要求。
(2)粗基准的选择按照粗基准的选择原则为保证不加工表面和加工表面的位置要求,应选择不加工表面为粗基准,因此选择轴的左右两端面的孔为基中。
(3)精基准的选择考虑要保证零件的加工精度,依据“基准重合”原则和“基准统一”原则,以平面为精基中。
课程设计拨叉工艺规程设计及夹具设计.doc

学号06090924成绩课程设计说明书系别机电工程系专业机械设计制造及其自动化方向模具方向课程名称《制造技术基础课程设计》学号 06090924姓名叶汝贞指导教师王建康题目名称拨叉工艺规程设计及夹具设计设计时间 2012年2-6月2012 年 6 月 9 日目录一.设计题目及任务与进度要求 (1)1.任务....................................................................................................... 错误!未定义书签。
2.进度按排 ............................................................................................... 错误!未定义书签。
二.零件的工艺分析及生产类型的确定 (1)1.零件的作用 (1)2.零件的技术要求 (2)3.零件的工艺性能 (3)4.确定零件的生产类型 (3)三、选择毛坯,确定毛坯尺寸,设计毛坯图 (4)1、选择毛坯 (4)2、确定毛坯的尺寸公差、加工余量 (4)四、选择加工方法、制定工艺路线 (7)(一)定位基准的选择 (7)1.精基准的选择 (7)2.粗基准的选择 (7)(二)表面加工方法的选择 (7)(三)加工阶段的划分 (8)(四)工序的集中与分散 (8)(五)工序设计 (9)1.机械加工工序 (9)2.热处理工序 ................................................................................. 错误!未定义书签。
3.辅助工序 (9)(六)确定工艺路线 (10)五.加工余量、工序尺寸和公差的确定 (11)六、切削用量、时间定额的计算 (12)(一)切削用量的计算 (12)(二) 时间定额计算 (13)1.基本时间j t 的计算 (13)2.辅助时间f t 的计算 (14)3.其他时间的计算 ......................................................................... 错误!未定义书签。
- 1、下载文档前请自行甄别文档内容的完整性,平台不提供额外的编辑、内容补充、找答案等附加服务。
- 2、"仅部分预览"的文档,不可在线预览部分如存在完整性等问题,可反馈申请退款(可完整预览的文档不适用该条件!)。
- 3、如文档侵犯您的权益,请联系客服反馈,我们会尽快为您处理(人工客服工作时间:9:00-18:30)。
目录目录 (1)摘要 (2)一、分析零件图 (3)1.1 零件作用 ............................................. 错误 ! 未定义书签。
1.2 零件的工艺分析 ....................................... 错误 ! 未定义书签。
二、确定毛坯 ............................................ 错误 ! 未定义书签。
三、工艺规程设计 ............................................. 错误 ! 未定义书签。
3.1 基面的选择 ........................................... 错误 ! 未定义书签。
3.2 精基准的选择 (7)四工序加工计算 (8)五、夹具的设计 ............................................... 错误 ! 未定义书签。
5.1 定位误差分析 ......................................... 错误 ! 未定义书签。
5.2 工件的夹紧 ........................................... 错误 ! 未定义书签。
5.2.1. 加紧位置的组成 .................................... 错误 ! 未定义书签。
5.2.2. 加紧力的方向 (18)5.2.3. 加紧力的作用点 (18)5.2.4. 加紧力的大小 ...................................... 错误 ! 未定义书签。
5.2.5. 夹具的精度分析 (21)参考文献 (22)任务书1、分析零件图1.1 零件作用拨叉是传动系统中用来拨动滑移齿轮,以实现系统调速、转向的零件。
其小头通过与轴的过盈配合来传递凸轮曲线槽传来的运动;大头的内部突起处与滑移齿轮的凹槽配合。
1.2 零件的工艺分析1、零件选用材料为 ZG310-570。
ZG310-570 生产工艺简单,铸造性能优良,但塑性较差,脆性高,不适合磨削。
图 1-1 拨叉2、该零件主要加工表面及技术要求分析如下:零件上端面及孔φ 160 的上下端面与孔φ 52H8 的垂直度公差等级为 8 级。
表面粗糙度为 Ra≤ 3.2um。
加工时应以上端面与孔φ 52H8的内表面为基准。
又由于上端面须加工,根据“基准先行” 的规则,故应先加工上端面,再加工孔φ 52H8,最后加工孔φ160,然后加工其上下端面。
2、确定毛坯2.1 、确定毛坯种类根据零件材料确定毛坯为铸件。
并依其结构形状、尺寸大小和生产类型,毛坯的铸造方法选用砂型铸造,机器造型。
图 2-1 零件毛坯图2.2 、确定毛坯基本尺寸通过零件分析可知孔为双侧加工,小头孔端面为单侧加工,根据毛坯基本尺寸的计算公式可得下表:表 2-1项目小头孔端面52 孔160 孔公差等级 CT 9 9 9加工面基本尺寸52 26 80铸件尺寸公差 2 1.7 2机械加工余量等级 F F FRMA 1.5 1.5 1.5毛坯基本尺寸52.5 15 853、工艺路线:表 3-1工序号工序名称工序内容工艺装备1 铸精密铸造,两件合铸(工艺需要)2 热处理退火3 划线划各端面及三个孔的线4 车以外形及下端面定位,按线找正,四爪单动CA6140专用工具卡盘装夹(或专用工具)工件。
车160孔至图样尺寸,并车孔的两侧面,保证尺寸80 和 9 及尺寸要求。
5铣以两段50 内孔及外部端定位,装夹工件,X5030A 组合夹具铣 50 上端面,保证两端面距离尺寸80mm和9 及精度要求6 铣以两边的50 内孔外端定位定位,反过来X5030A 组合夹具装夹工件,铣50 的另一端面,保证两段面尺寸 80mm7 钻以 50 内孔的两段外部端面定位,装夹工Z5132A 组合夹具件,钻,扩铰50 孔,孔口倒角C18 钻M6的螺纹孔按精度要求达到尺寸标准Z5132A 组合夹具9 检验按图样要求检查各部件尺寸及精度10 入库入库3.1 、基面的选择粗基准的选择:以零件的小头上端面为主要的定位粗基准,以两个小头孔外圆表面为辅助粗基准。
加工两小孔端面时,以底面和两外圆表面定位是合理的,此时应选择两 V 型块作为定位元件,这样比较容易实现。
若选择底面和两小孔作为定位基准,则由于小孔铸造时的误差太大,很难与心轴、菱形销配合良好。
以加工后的小孔端面为粗基准来加工两小孔。
再以加工后的小孔和小孔端面为粗基准来加工中间孔,以及中间孔上下端面。
这样做是保证零件垂直度误差的前提。
3.2 、精基准的选择加紧装置的组成:拨叉的铣断面装置如下图所示的工序的确定:按给定的尺寸和精度要求我重复的考虑吧拨叉的工业路线和夹具设计。
因工件的加工的表面和空比较多加工工序分给几组的同学,按分给我的加工工序我设计好了拨叉两端面铣的加工工序和夹具的设计。
我用两个工件同时加工的方法来设计了拨叉的夹具。
这样就可以提升加工量和加工速度,加工过程中可以避免拨叉的加工误差。
两个拨叉零件平行放着夹具的中间部分也就是前后放着。
铣拨叉两端面的夹具体主要是固定 v 形块和活动 v 形块的加紧方案,因前后放着的v 形块高度不一样,我设计的支撑钉的高度也不一样但上面部分和下部分的螺纹长度和宽度都一样的,前面的零件下面使用的是尺寸小的支撑钉,后面的零件下面使用的是尺寸大的支撑钉,一共有四个支撑钉。
固定v 形块有俩个,前面和后面的零件各自用一个。
活动v 形块也是两个,配对固定v 形块使用的。
活动v 形块外套有两个,盖上活动v 形块上面部分。
连杆也有两个是活动 v 形块的不可分离的一部分。
对刀块用一个安装在后面零件的旁边。
装配图:图 5-1 夹具图整个铣断面装置的夹具的主要部分是固定和活动 v 形块。
我们通过仔细的分析才决定了铣断面装置的夹具。
主要用的是毛胚零件要两个,平行放着铣。
V形块:V型块是一种比较特殊的定位元件。
它虽然是一个单独定位元件,但它的定位基面的结构要素却不是单一的,有两个定位平面,从某种意义上来讲这种形式的定位可看作是两个平面的组合定位。
因此,它的定位基准的确定就不能象分析单一定位基面那样简单。
大多数定位元件的定位基准都是定位基面本身或者是由其形成的点、面、线,如单一平面、球心、孔和轴的中心线等。
根据这个道理,笔者认为, V 型块的定位基准应有两个,其一是两定位平面的交线,另一个是由两平面形成的对称中心面,交线作为垂直方向的定位基准;对称中心面作为水平方向的定位基准。
按照传统 (中心论 )的理论, V 型块的定位基准应是检验心轴的中心高,即检验心轴在 V 型块上放置时的中心线,实际上这条中心线在V 型块中的位置是不确切的,它会因检验心轴直径误差大小而变化,因此,在对刀误差中往往会引入这条中心线的位置误差。
活动 v 形块用于较短精基准外圆面定位;用于较长的粗基准外圆面定位;用于精基准外圆面较长时,或两段精基准外圆面相距较远或是阶梯轴时的定位,也可做成两个单独的短 V 型块再装配在夹具体上,目的是是减短 V 形块的工作面宽度有利于定位稳定。
当定位外圆直径与长度较大时,采用铸铁底座镶淬火钢垫块的结构。
这种结构除了制造经济性好以外,又便于V 形块定位工作面磨损后更换或修磨垫块,还可通过更换不同厚度的垫块以适应不同直径外圆的工件定位使结构通用化。
也有在钢垫块上镶焊硬质合金,以提高定位工作面的耐磨性。
固定 v 形块对刀块:这个,其实主要在普通铣床夹具上应用。
在铣床上加工零件时,我们要知道零件的确切位置即“坐标”。
不然,刀具要从哪里下刀啊?在数控机床上,我们可以看到有类似刀具外形的传感器即“寻边器”,用他可以测量出零件的坐标,这样既可以找到“坐标”又不会刮伤零件。
而对刀块在普通机床的夹具上,用对刀块主要是,不会刮伤零件,而对于一些复杂不容易找到定位面的零件,也有很大的作用。
而塞尺也是相对对刀块而言的,相当于“对刀块对零件的保护”。
塞尺可以保护对刀块防止刮伤的保护。
工序计算1、确定加工余量表 4-1加工 加工 加工 精度工序 表面 工序余量 表面内容余量等级尺寸粗糙 最小 最大度孔φ 40 上 铸件2.5 CT9 52.5 - +2精铣0.5 IT9500 +0.0743.2 0.426 0.8 端面粗铣 2.0 IT12+0.306.30.34.550.5 0 2、确定切削用量粗精铣小头孔上端面,以底面为粗基准粗铣小头孔上端面 :由机械手册可以直接查出铣削速度: v 60m / min 采用套式面铣刀, D 50mm, Z 5 。
则按机床说明书 , 见 <<机械制造技术基础 >>此转速与 382r/min 相接近的机床转速为 355r/min.所以实际铣削速度为 v 55.7m / minl220 计算工时 t m1.13 minf m177.5精铣小头孔上端面 :由机械手册可以直接查出铣削速度: v 73m / min 采用错齿三面刃铣刀, d 40mm, D 100mm, Z 10 。
则按机床说明书 , 见<<机械制造技术基础 >>此转速与 581r/min 相接近的机床转速为 575r/min.所以实际铣削速度为 v 72.3m/ min一、工序 020 以小头孔上端面及小头孔外圆为基准,扩、精铰φ不超过 0.05mm,孔的精度达到 IT7 。
1. 选择钻头14 孔,保证垂直度误差 扩孔选择硬质合金扩孔钻,粗钻时 d o =20mm ,钻头采用双头刃磨法,后角α重刃长度 b ε =2.5mm,横刀长 b=1.5mm,宽 l=3mm,棱带长度 l 1 1.5mm 10° 30°o =12°,二2 120 °2. 选择切削用量( 1)决定进给量查机械加工手册得 f 0.7 0.8mm / r l 50/ 20 2.5 3所以, f0.8mm/ rdF f ,故所选进给量可用。
(2)钻头磨钝标准及寿命后刀面最大磨损限度(查《简明手册》 )为 0.5 ~ 0.8mm ,寿命 T 60 min . (3)切削速度查机械加工工艺设计手册 高速钢钻扩孔灰铸铁的切削速度 , v c 14m / min根据公式 v cd 0 n sn=202r/min (查《机械制造设计基础》 )选择立式钻床 Z525 取 1000n=195m/min , 故实际切削速度为 v=13.4m/min (4)检验机床扭矩及功率查《切削手册》表 2.20 ,当 f ≤0.26, d o ≤19mm 时,M t =31.78N?m ,修正系数均为 1.0 ,故 M C =31.78 N ?m 。