橡胶加工工艺
橡胶加工原理和工艺
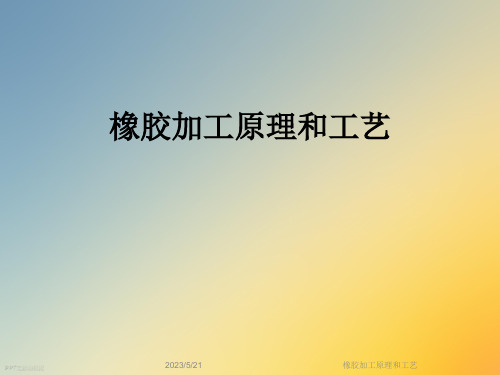
PPT文档演模板
橡胶加工原理和工艺
•五. 填充剂
• 填充剂按用途可分为两大类;即补强填充剂和惰性填充剂。 • 补强填充剂简称补强剂,是能够提高硫化橡胶的强力,撕裂强 度,定伸强度,耐磨性等物理机械性能的配合剂。最常用的补强剂 是炭黑,其次是白炭黑、碳酸镁、活性碳酸钙,活性陶土、古马隆 树脂、松香树脂、苯乙烯树脂、酚醛树脂、木质素等。 • 惰性填充剂又称增容剂,是对橡胶补强效果不大,仅仅是为了 增加胶料的容积以节约生脱从而降低成本或改善工艺性能(特别是压 出、压延性能)的配合剂。增容剂只好是比重小的、这时重量经而体 积大,虽常用的增容剂有硫酸钙,滑石粉、云母粉等。 • 下面着重讨论炭黑的补强机理及影响补强效果的因素。
• 防老剂一般可分为两类,即物理防老剂和化学防老剂。物理防老剂
主要有石蜡、微晶蜡等物质。由于在常温下此种物质在橡胶中的溶解度
较少,因而逐渐迁移到橡胶制品表面,形成一层薄膜,起隔离臭氧、氧
•气与橡胶的接触作用,用量一斑为1—3份。
• 化学防老剂主要有酚类和胺类。酚类一股无污染,但防老性能较差,
主要用于浅色和透明制品,而胺类一般部有污染做主要用于黑色和
PPT文档演模板
橡胶加工原理和工艺
•配方种类有三类,即基础配方、性能配方和生产配方。 • 基础配方是专供研究或鉴定新胶种,新配合剂用的,其配合组分 的比例一般采用传统的使用量,以便对比,并要求尽可能简单。通 用的基础配方其组分和用量如下;
PPT文档演模板
橡胶加工原理和工艺
•配方设计的原则:
•在配方设计之前,首先必须了解制品的使用条件,并考虑制品的质 量,使用寿命及物理机械性能。 •第二 必须了解对使用的生胶和配合剂的性质以及各种配合利的相互 间的关系,尤其是使用新型原材料时,对其质量,等级情况要有分折 和实验的结果。 •第三 原材料的使用必须立足于国内,因地制宜。 •最后, 在制定配方时,还必须考虑到设备的特点和制造工艺上 •的方便,尽量降低成本,降低原材料消耗。
橡胶加工工艺及配方
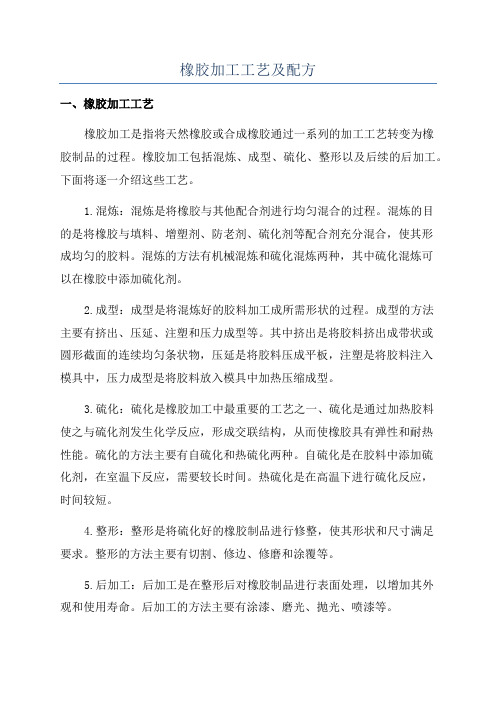
橡胶加工工艺及配方一、橡胶加工工艺橡胶加工是指将天然橡胶或合成橡胶通过一系列的加工工艺转变为橡胶制品的过程。
橡胶加工包括混炼、成型、硫化、整形以及后续的后加工。
下面将逐一介绍这些工艺。
1.混炼:混炼是将橡胶与其他配合剂进行均匀混合的过程。
混炼的目的是将橡胶与填料、增塑剂、防老剂、硫化剂等配合剂充分混合,使其形成均匀的胶料。
混炼的方法有机械混炼和硫化混炼两种,其中硫化混炼可以在橡胶中添加硫化剂。
2.成型:成型是将混炼好的胶料加工成所需形状的过程。
成型的方法主要有挤出、压延、注塑和压力成型等。
其中挤出是将胶料挤出成带状或圆形截面的连续均匀条状物,压延是将胶料压成平板,注塑是将胶料注入模具中,压力成型是将胶料放入模具中加热压缩成型。
3.硫化:硫化是橡胶加工中最重要的工艺之一、硫化是通过加热胶料使之与硫化剂发生化学反应,形成交联结构,从而使橡胶具有弹性和耐热性能。
硫化的方法主要有自硫化和热硫化两种。
自硫化是在胶料中添加硫化剂,在室温下反应,需要较长时间。
热硫化是在高温下进行硫化反应,时间较短。
4.整形:整形是将硫化好的橡胶制品进行修整,使其形状和尺寸满足要求。
整形的方法主要有切割、修边、修磨和涂覆等。
5.后加工:后加工是在整形后对橡胶制品进行表面处理,以增加其外观和使用寿命。
后加工的方法主要有涂漆、磨光、抛光、喷漆等。
二、橡胶配方橡胶配方是指将橡胶与各种配合剂按一定比例混合,形成胶料的配方。
橡胶配方的配料包括橡胶本体、填充剂、增塑剂、硬化剂、防老剂、防护剂、促进剂等。
下面将介绍常用的橡胶配方。
1.橡胶本体:橡胶本体是指原料橡胶,可以是天然橡胶或合成橡胶。
常用的橡胶有天然橡胶、丁苯橡胶、丁腈橡胶、氯丁橡胶、丁基橡胶等。
2.填充剂:填充剂是指填充到橡胶中的无机或有机物质,可以改变橡胶的物理和机械性能。
常用的填充剂有炭黑、白炭黑、沉香末、沥青等。
3.增塑剂:增塑剂是指能增加橡胶柔软性和延展性的物质。
常用的增塑剂有塑化油、脂肪酸酯、酸酐和酯类增塑剂等。
橡胶加工工艺
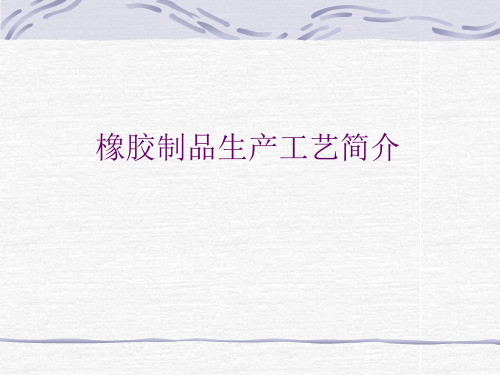
➢ 化学塑解剂:塑解剂的用量,在NR中一般为生胶重量的0.1~0.3%,合 成橡胶则应增大到2~3%。
橡胶制品生产工艺简介-塑炼工艺塑炼工艺
不同胶料开炼机混炼时辊筒温度
胶种
天然胶 丁苯胶 氯丁胶 丁基胶 丁腈胶 顺丁胶 三元乙丙胶 氯磺化聚乙烯 氟橡胶23—27 丙烯酸酯橡胶
橡胶制品生产工艺简介-塑炼工艺塑炼工艺
常用橡胶的塑炼特性
2. SBR ➢ 软SBR的初始门尼粘度一般在54~64之间,不需进行塑炼。 ➢ SBR采用机械塑炼效果不大,比较有效的方法时采用高温
塑炼法,以130~140℃温度最好,温度过高易生成凝胶。 3.BR ➢ BR一般不需要进行塑炼。 4.CR ➢ CR的初始门尼粘度都较低,一般不需要进行塑炼。但在储
➢ 物料在密炼室中主要受到几种作用: 转子间及转子与混炼室内壁间的作用;
转子棱间的搅拌作用;
转子轴向的往复切割作用。
➢ 优点:自动化程度高,生产效率高,节能,劳动强度低
➢ 缺点:温度高,冷却困难,易过炼,出料为无定形状
橡胶制品生产工艺简介-塑炼工艺塑炼工艺
密炼机
橡胶制品生产工艺简介-塑炼工艺塑炼工艺
存过程中其可塑性会下降,因此CR仍需经过塑炼加工,才 能获得所要求的可塑性。 ➢ CR宜采用开炼机进行塑炼,低温薄通塑炼效果最好。
橡胶制品生产工艺简介-塑炼工艺塑炼工艺
常用橡胶的塑炼特性
5.IIR ➢ 门尼粘度在38~75之间的品种一般不需要塑炼。 ➢ IIR采用机械塑炼效果不大,但用密炼机在120℃以上,并
且加入塑解剂进行高温塑炼则可取得较好的塑炼效果。 6.NBR ➢ NBR的塑炼应采用开炼机在低温(40℃以下)、小辊距
橡胶加工工艺—橡胶压出工艺(高分子成型课件)
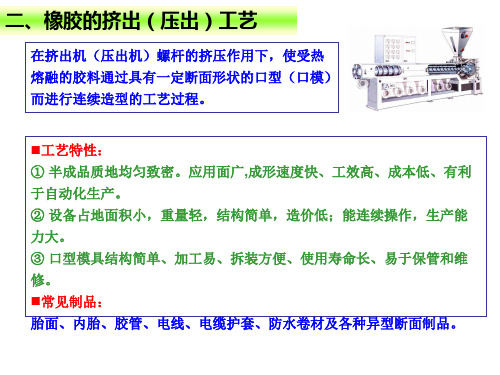
二、橡胶的挤出(压出)工艺
(一)压出机工作原理及胶料的运动状态 3 物料在口型中的流动状体和挤出变形 胶料经机头进入口型后,由于口型形状不同及内表 面对物料流动的阻碍,物料流动速度也存在有与机 头类似的速度分布。中间流速大,越接近口型壁流 速越小 。 一般粘弹性的物料,从口型挤出后就不可避免地存 在松弛现象,即:胶条的长度会沿挤出方向缩短, 厚度沿垂直挤出方向增加(离模膨胀现象或称作挤 出变形现象)。挤出后的变形(收缩和膨胀)可以控制 在一定范围,但不可能完全消除。要求收缩率为 2~5%。 物料可塑性小、含胶率大,填充剂用量小,物料挤 出快,机头和口型温度低,膨胀和收缩率就大。
二、橡胶的挤出(压出)工艺
在挤出机(压出机)螺杆的挤压作用下,使受热 熔融的胶料通过具有一定断面形状的口型(口模) 而进行连续造型的工艺过程。
工艺特性: ① 半成品质地均匀致密。应用面广,成形速度快、工效高、成本低、有利 于自动化生产。 ② 设备占地面积小,重量轻,结构简单,造价低;能连续操作,生产能 力大。 ③ 口型模具结构简单、加工易、拆装方便、使用寿命长、易于保管和维 修。 常见制品: 胎面、内胎、胶管、电线、电缆护套、防水卷材及各种异型断面制品。
二、橡胶的挤出(压出)工艺
(一)压出机工作原理及胶料的运动状态
1 胶料在挤出机中的运动状态
加料段:加入的条状胶料,受到旋转螺杆的推挤作用形成连续的胶 团,并沿着螺槽的空间一边旋转,一边不断前进。 压缩段:加料段输送过来的松散胶团在压缩段被逐渐压实、软化, 并把夹带的空气向加料段排出。同时胶团间间隙缩小,密度增高, 进而粘在一起,再加上受到剪切和搅拌作用,因而胶团逐渐被加热 塑化形成连续的粘流体。 挤出段:在挤出段,压缩段输送过来的物料进一步塑化均匀,并输 送到机头和口模处挤出成型。
橡胶加工工艺流程
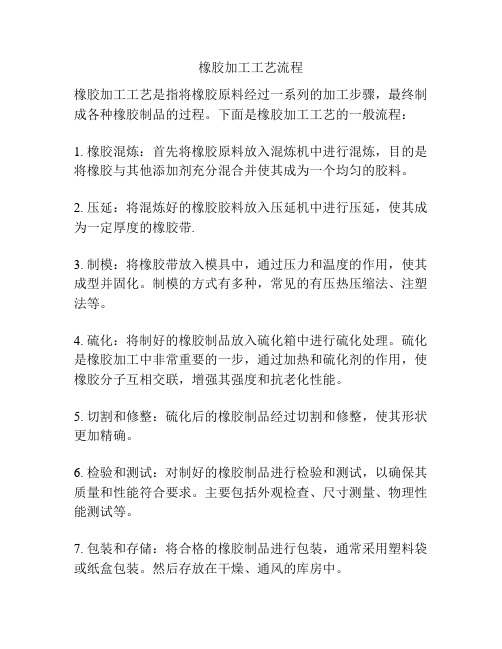
橡胶加工工艺流程
橡胶加工工艺是指将橡胶原料经过一系列的加工步骤,最终制成各种橡胶制品的过程。
下面是橡胶加工工艺的一般流程:
1. 橡胶混炼:首先将橡胶原料放入混炼机中进行混炼,目的是将橡胶与其他添加剂充分混合并使其成为一个均匀的胶料。
2. 压延:将混炼好的橡胶胶料放入压延机中进行压延,使其成为一定厚度的橡胶带.
3. 制模:将橡胶带放入模具中,通过压力和温度的作用,使其成型并固化。
制模的方式有多种,常见的有压热压缩法、注塑法等。
4. 硫化:将制好的橡胶制品放入硫化箱中进行硫化处理。
硫化是橡胶加工中非常重要的一步,通过加热和硫化剂的作用,使橡胶分子互相交联,增强其强度和抗老化性能。
5. 切割和修整:硫化后的橡胶制品经过切割和修整,使其形状更加精确。
6. 检验和测试:对制好的橡胶制品进行检验和测试,以确保其质量和性能符合要求。
主要包括外观检查、尺寸测量、物理性能测试等。
7. 包装和存储:将合格的橡胶制品进行包装,通常采用塑料袋或纸盒包装。
然后存放在干燥、通风的库房中。
以上是橡胶加工工艺的一般流程,不同的橡胶制品可能会有一些特殊的工艺步骤。
橡胶加工的过程中,需注意橡胶原料的质量、混炼工艺参数、硫化条件等。
只有严格控制每一个环节,才能制备出质量稳定、性能优越的橡胶制品。
橡胶密封圈加工工艺

橡胶密封圈加工工艺
橡胶密封圈加工工艺一般可以包括以下几个步骤:
1. 材料准备:选择适合的橡胶材料,如丁腈橡胶、氟橡胶等,根据产品要求的耐温、耐油、耐化学品等特性进行选择。
2. 模具设计与制造:根据产品要求绘制3D模型,然后设计和制造相应的模具。
模具一般采用金属材料,如铝合金、工程塑料等。
3. 橡胶成型:将橡胶材料加热到适当温度,然后放入预先设计好的模具中,加压使其充满模具的空腔,并在一定时间内保持压力和温度,使橡胶材料具有相应的形状和硬度。
4. 压痕处理:根据产品要求,对橡胶密封圈进行压痕处理,可以增加密封性能和抗老化能力。
5. 表面处理:橡胶密封圈的表面可以进行喷涂、印刷、涂覆等处理,以提高其耐磨性、耐腐蚀性和防尘性能。
6. 检验和包装:对橡胶密封圈进行外观质量检验、尺寸检验等,合格后进行包装和标识。
需要注意的是,橡胶密封圈加工工艺可能因不同产品和要求而有所差异,以上仅为一般加工工艺的简要介绍。
实际操作应根据具体情况进行调整和优化。
简述橡胶加工工艺

简述橡胶加工工艺一、塑炼橡胶受外力作用产生变形,当外力消除后橡胶仍能保持其形变的能力叫做可塑性。
增加橡胶可塑性工艺过程称为塑炼。
橡胶有可塑性才能在混炼时与各种配合剂均匀混合;在压延加工时易于渗入纺织物中;在压出、注压时具有较好的流动性。
此外,塑炼还能使橡胶的性质均匀,便于控制生产过程。
但是,过渡塑炼会降低硫化胶的强度、弹性、耐磨等性能,因此塑炼操作需严加控制。
橡胶可塑度通常以威廉氏可塑度、门尼粘度和德弗硬度等表示。
1、塑炼机理橡胶经塑炼以增加其可塑性,其实质乃是使橡胶分子链断裂,降低大分子长度。
断裂作用既可发生于大分子主链,又可发生于侧链。
由于橡胶在塑炼时,遭受到氧、电、热、机械力和增塑剂等因素的作用,所以塑炼机理与这些因素密切相关,其中起重要作用的则是氧和机械力,而且两者相辅相成。
通常可将塑炼区分为低温塑炼和高温塑炼,前者以机械降解作用为主,氧起到稳定游离基的作用;后者以自动氧化降解作用为主,机械作用可强化橡胶与氧的接触。
塑炼时,辊筒对生胶的机械作用力很大,并迫使橡胶分子链断裂,这种断裂大多发生在大分子的中间部分。
塑炼时,分子链愈长愈容易切断。
顺丁胶等之所以难以机械断链,重要原因之一就是因为生胶中缺乏较高的分子量级分。
当加入高分子量级分后,低温塑炼时就能获得显著的效果。
氧是塑炼中不可缺少的因素,缺氧时,就无法获得预期的效果。
生胶塑炼过塑炼时,设备与橡胶之间的摩擦显然使得胶温升高。
热对塑炼效果极为重要,而且在不同温度范围内的影响也不同。
由于低温塑炼时,主要依靠机械力使分子链断裂,所以在像章区域内(天然胶低于110℃)随温度升高,生胶粘度下降,塑炼时受到的作用力较小,以致塑炼效果反而下降。
相反,高温塑炼时,主要是氧化裂解反应起主导作用,因而塑炼效果在高温区(天然胶高于110℃)将随温度的升高而增大,所以温度对塑炼起着促进作用。
各种橡胶由于特性不同,对应于最低塑炼效果的温度范围也不一样,但温度对塑炼效果影响的曲线形状是相似的。
橡胶加工工艺—橡胶压延工艺(高分子成型课件)
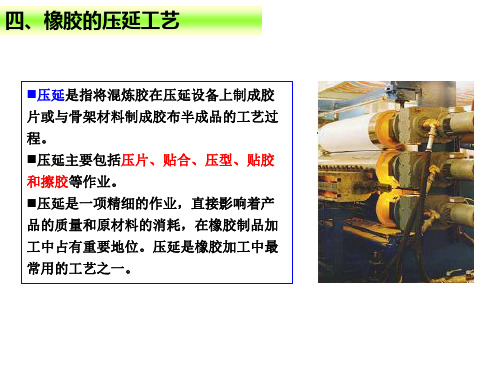
a,b-两辊压型(v1=v2); c-三辊压型(v1v2=v3); d-四辊压型(v2=v3=v4v1)
三、橡胶的压延工艺
(二)压延工艺方法 3 胶片贴合
胶片贴合:通过压延机将两层或多层薄胶片贴合在一起的工艺过程。
通常用于制造较厚、质量要求较高 的胶片和两种不同胶料组成的胶片、 夹布层胶片等。 贴合方法有二辊压延机贴合法、三 辊压延机贴合法、四辊压延机贴合法。 四辊压延机可一次同时完成两个新 鲜胶片的压延与贴合。贴合效率高、 质量好、精度高,但压延效应大。
三、橡胶的压延工艺
(二)压延工艺方法 1 压片
压片:利用压延机等速辊筒将胶料制成具有规定断面厚度和宽度的表面 光滑的胶片。胶片应表面光滑,无绉缩,内部密实,无孔穴、气泡或海绵; 断面厚度均匀,精度,各部分收缩变形一致。 设备:压片压延机一般为三辊或四辊压延机,但多采用三辊压延机
压片工艺分类: ①积胶压延法片材表 面光滑,密实,减少气泡,但会增大压 延效应,适于丁苯橡胶。②普通挤胶法 适于NR。
三、橡胶的压延工艺
(三)压延制品厚度的控制
1 沿辊筒轴线方向上厚度
三高两低现象
(1)辊筒的弹性弯曲变形(横压力) 辊筒弹性弯曲变形(横压力)使压延制品中间厚两边薄 克服方法: a 中高度补偿法 ; b 轴交叉法 ; c 预应力法 (2)辊筒表面温度 轴承润滑油带走部分热量,辊筒温度中间高两边低使压延制品两边 较中间厚。 克服方法: a 中间鼓风冷却; b 两边红外加热
厚擦法:T上>T下>T中; 薄擦法: T上>T中> T下
三、橡胶的压延工艺
(二)压延工艺方法 5 纺织物挂胶的工艺影响因素
(1)胶料的可塑度 为了保证胶料对布孔的充分渗透,胶料要有较高的可塑 度(比压片胶料大)。天然橡胶的贴胶可塑度为0.4-0.5、 擦胶可塑度为0.5-0.6较为合适。 (2)辊温 辊温控制比压片时高,以增大胶料的流动性及胶料与纺织 物间的附着力。但辊温过高易产生焦烧。
- 1、下载文档前请自行甄别文档内容的完整性,平台不提供额外的编辑、内容补充、找答案等附加服务。
- 2、"仅部分预览"的文档,不可在线预览部分如存在完整性等问题,可反馈申请退款(可完整预览的文档不适用该条件!)。
- 3、如文档侵犯您的权益,请联系客服反馈,我们会尽快为您处理(人工客服工作时间:9:00-18:30)。
橡胶的简介
★增塑剂(物理和化学增塑) 目的: 1. 使生胶软化,增加可塑性便于加工,减少动力
消耗; 2. 润湿炭黑等粉状配合剂,提高混炼效果,增加
制品柔软性和耐寒性; 3. 增进胶料的自粘性和粘性。
9
橡胶的简介
★填充剂 补强填充剂提高硫化橡胶的强力,撕裂强度, 定伸强度,耐磨性等物理机械性能。 炭黑、白炭黑、活性陶土、苯乙烯树脂、木质 素等。 惰性填充剂增加胶料体积,节约成本,改善加 工性能。 云母粉、滑石粉、硫酸钡。
3
橡胶的简介
橡胶的作用
橡胶是橡胶工业的重要原料,用以制造轮 胎、胶管、胶带、胶辊等各种橡胶制品。橡胶 还广泛用于电线电缆、纤维和纸加工、石棉以 及塑料改性等方面。世界橡胶耗量中,约80%用 于橡胶工业。在橡胶制品中,轮胎是其典型的 代表性产品,轮胎的用胶量约占全部橡胶耗用 量的50%~70%。
4
橡胶的简介
★硫化剂 硫化剂是一类使橡胶由线形长链分子转变为网状大分子的 物质,这种转变称为硫化。 硫化剂:硫磺、一氯化硫、硒、碲及其氯化物、硝基 化物、有机过氧化物以及某些金属氧化物。
6
橡胶的简介
★硫化促进剂 硫化促进剂可促进橡胶的硫化作用,降低硫化所需温 度,缩短硫化时间,并改善硫化胶的物理机械性能。 硫化促进剂的种类很多。无机类硫化促进剂(如氧化 铅,氧化镁等)硫化效果较差,已被淘汰。目前主要 使用有机类硫化促进剂,
19
橡胶的塑炼和混炼
❖ 混炼示意图
橡胶的塑炼和混炼
❖ 混炼示意图
后辊
前辊
橡胶的塑炼和混炼
❖ 混炼示意图
后辊
前辊
橡胶的塑炼和混炼
后辊
前辊
橡胶的塑炼和混炼
后辊
前辊
橡胶的挤出
❖ 三、挤出
挤出机2
胶料
挤出机头
挤出机1
挤出口型板1 挤出口型板2 挤出口型板3 挤出口型板4 定位头
定位头底座
挤出口模
❖
踏实肯干,努力奋斗。2020年10月 20日 下午6 时4分2 0.10. 2020 .10.2 0
❖
追求至善凭技术开拓市场,凭管理增 创效益 ,凭服 务树立 形象。 2020 年10月 20日 星期二 下午6 时4分4 3秒18 :04:4 320. 10.20
❖
严格把控质量关,让生产更加有保障 。202 0年10 月下午 6时4 分20. 10.20 18:0 4October 20, 2020
橡胶区别于其它工业材料的最主要标志是它在很宽的温度范 围内(-50℃~+150℃)具有优异的弹性。例如其伸长率可达 100%~1000%,为钢的300倍,但其弹性模量仅为2~4MPa, 约为钢材的1/30000.
橡胶经过硫化可将线型高分子交联成三维网状高分子量聚合 物。这种已硫化交联的橡胶称作硫化橡胶,俗称熟橡胶。未 硫化的橡胶俗称生胶或生橡胶。
橡胶硫化
❖ 硫化后橡胶的性能变化 ❖ 以EPDM为例,随硫化程度的提高:
1)力学性能的变化 弹性 扯断强度 定伸强度 撕裂强度 硬度
伸长率 压缩永久变形 疲劳生热
提高 降低
2)物理性能的变化 透气率、透水率降低 不能溶解,只
能溶胀 耐热性提高 3)化学稳定性的变化
化学稳定性提高。 原因:a. 交联反应使化学活性很高的基 团或原子不复存在,使老化反应难以进 行。
A1
A2
B
C
D
c
d
a
b
A.焦烧阶段; A1.操作焦烧时间 A2.剩余焦烧时间 B.热硫化阶段; C.平坦硫化阶段; D.过硫化阶段
t
橡胶制品的去边
❖五、去边
通过手工或机械的方式,将制品飞边修整干净。
二次硫化
❖ 六、二次硫化
二次硫化也叫后硫化或二段硫化, 是指橡胶制品达到一定硫化程度,除去热源继续进行 加热硫化的工艺。从广义上讲,橡胶制品硫化到一定程 度,即使不加热,它仍可在余热的作用下,或在制品储 存过程中,继续加深硫化程序,或在动态作用下产生继 续交联现象。当然也包括继续加热进行二段硫化的加工 工艺; 二次硫化目的是橡胶制品进一步交联,改善橡胶制品 的力学性能和压缩永久变形性能等; 二次硫化的方法是烘箱热空气硫化或者采用硫化罐热 空气二次硫化。
10
橡胶制品生产工艺流程
工艺流程图
塑炼
混炼
挤出
成型
硫化
检验
二次硫化
去边
橡胶的塑炼和混炼
一、塑炼 1. 塑炼的目的: 橡胶受外力作用产生变形,当外力消除后橡胶仍能保 持其形变的能力称为可塑性。 增加橡胶可塑性的工艺过程称为塑炼。使橡胶具有必要的可塑 性的工艺过程称为塑炼,因为橡胶有恰当的可塑性才能在混炼 时与各种配合剂均匀混合;在压延加工时易于渗入纺织物中; 在压型、注压时具有较好的流动性。此外,塑炼还能使橡胶的 性质均匀,便于控制生产过程。但是,过渡塑炼会降低硫化胶 的强度、弹性、耐磨等性能.因此塑炼操作需严加控制。
硫化前:线形结构,分子间以范德华力相互作用 性能: 可塑性大,伸长率高,具可溶性。
硫化剂(S) 牵线搭桥
硫化时:分子被引发,发生化学交联反应
硫化后:网状结构,分子间主要已以化学键结合 结构:1)化学键;2)交联键的位置;3)交联程 度;4)交联 性能:1)力学性能(定伸强度、硬度、拉伸强度、 伸长率、弹性);2)物理性能;3)化学稳定性
挤出机出料口
挤出设备
挤出设备包括挤出机、挤出机头、挤出口型三大部分。 机头是挤出成型模具的主要部件,它有下述四种作用: 1,使物料由螺旋运动变为直线运动 2,产生必要的成型压力,保证制品密实 3,使物料得以进一步塑化 4,成型制品的断面形状
橡胶硫化
❖ 四、硫化,橡胶制造中最为关键的工艺
❖ 定义:通过一定的温度、压力和时间后,使橡胶大分子发生化学反应 产生交联的过程。
7
橡胶的简介
★防老剂 橡胶的分子结构极易受氧及臭氧的氧化作用,光和热 都能促进氧化作用,使橡胶分子链断裂,支化或进一 步交联,从而使橡胶发粘变硬,物理机械性能变坏, 以至失去使用价值,这种情况叫做老化。凡能抑制 橡胶老化现象的物质就叫做防老剂。
物理防老剂:石蜡、微晶蜡; 化学防老剂:酚类与胺类。
8
橡胶的分类
外观形态 来源
固态橡胶(又称为干胶) 乳状橡胶(简称为乳胶) 液体橡胶
其中固态橡胶 的产量约占橡 胶总产量的 85%~90%。
天然橡胶(来自于天然植物)
两种橡胶的消耗 量在橡胶总耗量
中所占的比例,
分别是天然橡胶
合成橡胶(来自于人工合成) 约占1/3,合成
橡胶约占2/3。
5
橡胶的简介
配合剂
12
橡胶的塑炼和混炼
2. 塑炼机理 橡胶经塑炼以增加其可塑性,其实质乃是使橡胶分子 链断裂,降低大分子长度。断裂作用既可发生于大分 子主链,又可发生于侧链。由于橡胶在塑炼时,遭受 到氧、电、热,机械力和增塑剂等因素的作用,所以 塑炼机理与这些因素密切相关,其中起重要作用的则 是氧和机械力,而且两者相辅相成。
❖
牢记安全之责,善谋安全之策,力务 安全之 实。20 20年 10月2 0日星 期二6 时4分4 3秒Tu esday, October 20, 2020
❖
相信相信得力量。20.10.202020 年10 月20日 星期二 6时4 分43秒 20.1 0.20
谢谢大家!
❖
安全象只弓,不拉它就松,要想保安 全,常 把弓弦 绷。20 .10.2 018:04:43 18:0 4Oct- 2020 -Oct- 20
❖
加强交通建设管理,确保工程建设质 量。18 :04:4 318:04:43 18:0 4Tues day, October 20, 2020
❖
安全在于心细,事故出在麻痹。20. 10.20 20.1 0.201 8:04:4318 :04:4 3October 20, 2020
15
橡胶的塑炼和混炼
开放式炼胶机(开炼机)
16
橡胶的塑炼和混炼
密闭式炼胶机(密炼机)
17
Hale Waihona Puke 胶的塑炼和混炼2、 混炼方法 开放式混炼:生胶、小料(促进剂、活性剂、防老剂 等)、液体软化剂、补强剂(填充剂)、硫化剂。 密炼机混炼:生胶、小料(促进剂、活性剂、防老剂 等)、补强剂(填充剂) 、液体软化剂 压片机:硫化剂。
橡胶加工工艺
湖北派克密封件有限公司
1
目录
1
橡胶的简介
2
橡胶的塑炼和混炼
3
橡胶挤出
4
橡胶硫化
5
制品去飞边
6
二次硫化
7
检验
2
橡胶的简介
橡胶是一种高分子弹性化合物,其分子量一般都在10万以上, 有的甚至达到100万以上。组成这种大分子的原子通常排列成 柔性的直链或支链,由于原子的不断旋转和振动,分子链一 般呈卷缩状态。
❖
作业标准记得牢,驾轻就熟除烦恼。 2020 年10月 20日 星期二 6时4分 43秒 18:04 :432 0 October 2020
❖
好的事情马上就会到来,一切都是最 好的安 排。下 午6时4 分43 秒下午 6时4分 18:0 4:432 0.10. 20
❖
一马当先,全员举绩,梅开二度,业 绩保底 。20. 10.20 20.1 0.201 8:04 18:04 :431 8:04:43Oct -20
b. 网状结构阻碍了低分子的扩散, 导致橡胶老化 的
自由基难以扩散。
橡胶硫化
❖ 硫化历程
❖ 在硫化过程中,各种性能均会随硫化的进程而发生变化,这种变化曲 线能够反映胶料的硫化历程,故称为硫化历程图。下图为用硫化仪测 出的硫化历程曲线。该曲线反映胶料在一定硫化温度下,转子的转矩