基于机器视觉的PCB在线检测设备的图像采集系统
基于机器视觉的PCBA元器件实时检测系统

基于机器视觉的PCBA元器件实时检测系统闫梦涛;苏玮;冉海周【摘要】随着电子用品的普及和需求量的上升,其主要组成部分PCBA的生产量也十分巨大.为了保证产品的功能性完备,对PCBA的检测也是不可或缺的,现在大部分PCBA生产公司中还在使用人工检测.对于每天的生产量而言,人工检测的成本高、效率低,时间性价比不高,针对目前印刷电路板组装件(PCBA)元器件检测存在的问题,从经济、快捷、可靠的角度出发,提出了一款新的基于机器视觉的检测系统.以流水线上实时检测为目标,以LabVIEW14.0作为开发平台,将硬件设备和软件相结合,运用虚拟仪器LABVIEW中的IMAQ Vision模块进行图像处理,对PCBA元器件进行高效、精确地实时检测,实验结果表明,系统能够适应高速流水线上的实时PCBA板元器件的精准快速检测,实现人工智能.【期刊名称】《无线电工程》【年(卷),期】2018(048)004【总页数】6页(P272-277)【关键词】机器视觉;虚拟仪器;PCBA元器件;LABVIEW;实时检测【作者】闫梦涛;苏玮;冉海周【作者单位】浙江理工大学信息学院, 浙江杭州 310018;浙江理工大学信息学院, 浙江杭州 310018;浙江理工大学信息学院, 浙江杭州 310018【正文语种】中文【中图分类】TN911.730 引言近年来,印刷电路在全球电子元件中产值稳定增长,而伴随着整机产品品种结构的调整,印刷电路板(Printed Circuit Board,PCB)的面积已大大减小,其精度、复杂度迅速提高,印刷电路板组装件(Printed Circuit Board Assembly,PCBA)的检测必将朝着自动化、可视化的计算机检测方向发展[1]。
目前,我国检测PCBA板元器件技术设备已经在一些大公司生产线上投入使用,此设备的出现几乎完全替代人工操作,提高了产品质量和生产效率,但是设备成本极高,一套自动光学检测系统价值几十万美元,甚至高达数百万美元[2],如此高额的成本对于大部分中小企业来说是不能接受的,也是不切实际的。
基于图像处理技术的PCB板缺陷检测系统设计
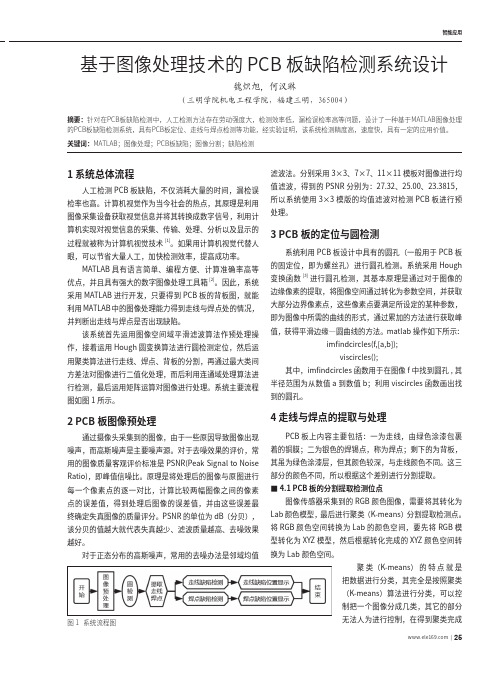
www�ele169�com | 25智能应用1 系统总体流程人工检测PCB 板缺陷,不仅消耗大量的时间,漏检误检率也高。
计算机视觉作为当今社会的热点,其原理是利用图像采集设备获取视觉信息并将其转换成数字信号,利用计算机实现对视觉信息的采集、传输、处理、分析以及显示的过程就被称为计算机视觉技术[1]。
如果用计算机视觉代替人眼,可以节省大量人工,加快检测效率,提高成功率。
MATLAB 具有语言简单、编程方便、计算准确率高等优点,并且具有强大的数字图像处理工具箱 [2]。
因此,系统采用MATLAB 进行开发,只要得到PCB 板的背板图,就能利用MATLAB 中的图像处理能力得到走线与焊点处的情况,并判断出走线与焊点是否出现缺陷。
该系统首先运用图像空间域平滑滤波算法作预处理操作,接着运用Hough 圆变换算法进行圆检测定位,然后运用聚类算法进行走线、焊点、背板的分割,再通过最大类间方差法对图像进行二值化处理,而后利用连通域处理算法进行检测,最后运用矩阵运算对图像进行处理。
系统主要流程图如图1所示。
2 PCB 板图像预处理通过摄像头采集到的图像,由于一些原因导致图像出现噪声,而高斯噪声是主要噪声源。
对于去噪效果的评价,常用的图像质量客观评价标准是PSNR(Peak Signal to Noise Ratio),即峰值信噪比。
原理是将处理后的图像与原图进行每一个像素点的逐一对比,计算比较两幅图像之间的像素点的误差值,得到处理后图像的误差值,并由这些误差最终确定失真图像的质量评分。
PSNR 的单位为dB(分贝),该分贝的值越大就代表失真越少、滤波质量越高、去噪效果越好。
对于正态分布的高斯噪声,常用的去噪办法是邻域均值滤波法。
分别采用3×3、7×7、11×11模板对图像进行均值滤波,得到的PSNR 分别为:27.32、25.00、23.3815,所以系统使用3×3模版的均值滤波对检测PCB 板进行预处理。
基于机器视觉的自动检测系统设计与实现

基于机器视觉的自动检测系统设计与实现一、引言随着工业化生产的普及,自动化驱动生产方式已成为社会发展的趋势。
基于机器视觉的自动检测系统因其高效、可靠、灵敏等优点,逐渐成为自动检测的热门研究方向。
本文旨在介绍一个基于机器视觉的自动检测系统的设计与实现过程。
二、自动检测系统的设计与实现1.系统结构设计本系统采用了传统的客户端/服务器结构。
客户端(PC)用于控制和数据处理,而服务器(嵌入式系统)用于采集和处理实时图像数据。
2.硬件准备使用嵌入式计算平台和相机模块,本系统需要使用USB接口进行连接。
采用嵌入式计算平台是为了提高系统运行效率和稳定性,而相机模块则实现了对物品的高清拍摄。
3.图像采集系统需要采集图像数据,包括颜色、形状、大小等。
采集的图像数据会发送到PC客户端进行后续处理。
4.特征提取系统会根据物品的特征,如颜色、纹理、边缘等进行特征提取。
特征提取是实现自动检测的重要一步,提取特征的正确性影响着后续检测的准确性。
5.物品匹配系统会将特征信息与预设的模型进行匹配。
匹配成功表示物品通过了检测,匹配失败表示物品未通过检测。
6.结果反馈系统会将检测结果反馈给PC客户端。
系统会告知用户是否通过检测,检测时间等信息。
三、实验结果本文设计的自动检测系统的实验结果表明,系统具有很好的稳定性和实用性。
在涉及到大批量物品检测时,系统的速度也非常快,可适应不同尺寸、颜色和形状的物品。
同时,该系统能够自动分辨异常物品,充分实现了自动检测的功能。
四、总结与展望本文介绍了一个基于机器视觉的自动检测系统的设计与实现过程。
通过实验结果表明,本系统具有高效、可靠、灵敏等特点。
但是,由于技术的限制,系统仍有一定的改进空间。
未来,我们将继续不断优化理论模型和算法,不断完善软硬件配置,致力于打造更加智能和高效的自动检测系统。
机器视觉应用于 PCB 缺陷检测技术研究
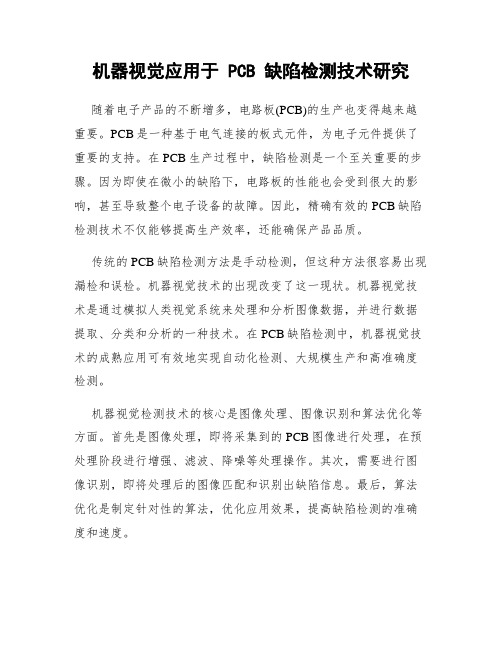
机器视觉应用于 PCB 缺陷检测技术研究随着电子产品的不断增多,电路板(PCB)的生产也变得越来越重要。
PCB是一种基于电气连接的板式元件,为电子元件提供了重要的支持。
在PCB生产过程中,缺陷检测是一个至关重要的步骤。
因为即使在微小的缺陷下,电路板的性能也会受到很大的影响,甚至导致整个电子设备的故障。
因此,精确有效的PCB缺陷检测技术不仅能够提高生产效率,还能确保产品品质。
传统的PCB缺陷检测方法是手动检测,但这种方法很容易出现漏检和误检。
机器视觉技术的出现改变了这一现状。
机器视觉技术是通过模拟人类视觉系统来处理和分析图像数据,并进行数据提取、分类和分析的一种技术。
在PCB缺陷检测中,机器视觉技术的成熟应用可有效地实现自动化检测、大规模生产和高准确度检测。
机器视觉检测技术的核心是图像处理、图像识别和算法优化等方面。
首先是图像处理,即将采集到的PCB图像进行处理,在预处理阶段进行增强、滤波、降噪等处理操作。
其次,需要进行图像识别,即将处理后的图像匹配和识别出缺陷信息。
最后,算法优化是制定针对性的算法,优化应用效果,提高缺陷检测的准确度和速度。
在机器视觉技术的应用下,PCB缺陷检测有了更加准确的方法,如裸露焊盘检测、元件损坏检测、连通性检测、污染检测等。
其中,裸露焊盘检测是检测电子产品上焊盘缺陷的重要步骤之一。
焊盘缺陷包括开口、制造缺陷或破裂。
通过机器视觉技术,我们可以对焊盘进行精确、自动化的检测,缺陷筛选统计和可视化等。
元件损坏检测可以检测元件破裂、扭曲、损坏等缺陷。
通过专有算法可以检测元件表面大面积伪影、弯曲和碎片等问题。
连通性检测检测PCB电路线路及元件的连通性是否正确,包括短路、开路、偏差等方面的问题。
污染检测则涵盖了PCB板面的污染程度,如氧化、腐蚀、化学污染等。
通过机器视觉技术,我们可检测到PCB表面上透明或光滑的区域及不同角度的反射和视角问题,从而实现污染检测。
另外,机器视觉技术还可用于定量分析PCB缺陷数据。
第三章 基于机器视觉的自动检测系统图像采集部分设计

第三章基于机器视觉的自动检测系统图像采集部分设计本系统的设计主要包括 CCD简介,CCD、镜头等光学元件的选择,背景光源的设计以及CCD与图像采集卡的联接等。
3.1 工业CCD以及CCD信息采集技术CCD(Charge-Coupled Devices)即电荷祸合器件,它是一种以电荷包的形式存贮和传递信息的半导体表面器件,是1969年秋由美国贝尔(Bell)实验室的W.S.Boyle和 GE.Smith发明的[ 10 ]。
电荷祸合器件(CCD)是一种新型光电转换器件,它能存储由光产生的信号电荷。
当对它施加特定时序的脉冲时,其存储的信号电荷便可在CCD内作定向传输而实现自扫描。
它主要由光敏单元、输入结构和输出结构等组成。
它具有光电转换、信息存贮和延时等功能,而且集成度高、功耗小,已经在摄像、信号处理和存贮二大领域中得到广泛的应用,尤其是在图像传感器应用方面取得令人瞩目的发展。
3.2 CCD的工作原理CCD的工作原理是由外部信号作用于CCD的感应元件上,从而产生电荷,再经过存储电荷、转移电荷最后的得到所需要的信息。
其图像采集的原理图如图3.1所示[11]:图3.1 CCD图像采集基本原理图3.3 CCD的选择CCD摄像头性能的好坏对采集图像的精度,对以后图像处理的效果、图像处理程序的难易程度和整个系统的最终检测精度有直接的影响,性能优良、图像精度高的CCD摄像头可以使以后的处理更容易,检测精度会更高。
CCD的选择主要是根据被测物体的大小以及测量精度来选择CCD 的尺寸和CCD 的分辨率。
本系统的测量精度要求小于0.1mm,因此要求采集图像的单位像素对应的实际距离至少要小于0.1mm。
根据这个要求可以得出关系式:Kv/β≦0.1mm,Kh/β≦0.1mm其中Kv(Kh)代表CCD 单位像素对应的实际距离;β是光学系统放大倍率。
表达式如下:Kv=v/n,或 Kh=h/m;β=v/V 或β=h/H式中v:CCD 靶面高度;n:CCD 垂直方向有效像素个数即垂直分辨率;h:CCD 靶面宽度;m :CCD 水平方向有效像素个数即水平分辨率;V:被测零件高度;H:被测零件宽度。
基于图像处理的PCB自动检测系统的设计与研究

基于图像处理的PCB自动检测系统的设计与研究【摘要】研究一种高精度、大场景、快速实时的PCB缺陷自动光学检测系统,分别进行了硬件结构和软件系统的设计。
该系统主要由二维运动平台、电机控制模块、图像采集模块、图像处理模块、结果分析模块组成。
改进的步进电机驱动方式——细分驱动以及改进的图像识别算法保证了系统的准确率,一键式自动检测的设计提高了检测速度。
实验结果证明,该系统能快速并准确的检测出PCB上的缺陷,有一定的实用和开发价值。
【关键词】PCB;细分驱动;自动光学检测(AOI);图像识别电子产品的核心部分——印刷电路板(PCB),是集成各种电子元器件的信息载体,在各个领域得到了广泛的应用,是电子产品中不可缺少的部分。
PCB的质量成了电子产品能否长期、正常、可靠的工作的决定因素[1]。
随着科技的发展,PCB产品的高密度、高复杂度、高性能发展趋势不断挑战PCB板的质量检测问题。
传统PCB缺陷检测方式因接触受限、高成本、低效率等因素,己经逐渐不能满足现代检测需要,因此研究实现一种PCB缺陷的自动检测系统具有很大的学术意义和经济价值[2]。
国内外研究的PCB缺陷检测技术中,AOI (Automatic Optic Inspection自动光学检测)技术越来越受到重视,其中基于图像处理的检测方法也成为自动光学检测的主流。
本文通过图像处理技术研究了一种大视场、高精度、快速实时的PCB缺陷自动检测系统,设计了硬件结构和软件算法流程。
通过改进的电机驱动方式配合一键式自动检测软件的设计,大大提高了系统的检测速度,对结果分析模块的缺陷识别算法的改进提高了检测结果的准确性。
1.系统结构PCB缺陷自动检测系统主要由运动控制模块、图像采集模块、图像处理模块、结果分析模块组成。
系统工作过程如下:上位机控制步进电机运动,步进电机带动二维平台运动,将CCD摄像机传输到待检测PCB上方,对PCB进行大场景图像采集,采集的图像经过图像采集卡送到上位机,上位机软件对采集的图像进行拼接、图像预处理,对处理的图像进行准确定位并校准,通过图像分割、图像形态学处理等,最后进行模板匹配、图像识别,得出缺陷检测结果。
PCB线路自动光学检查AOI原理介绍
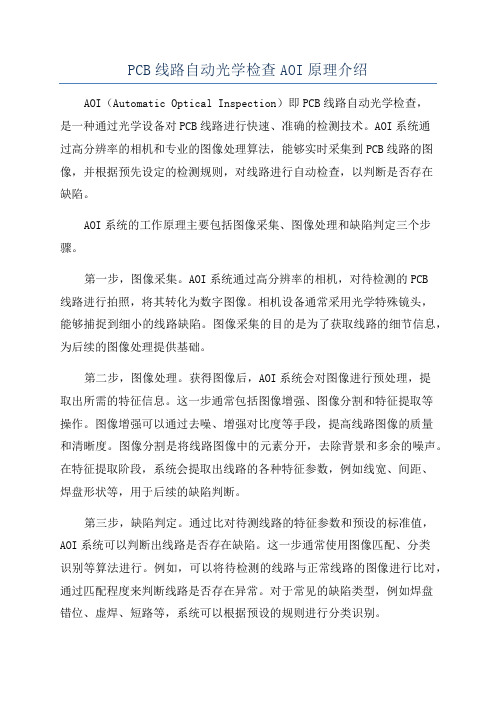
PCB线路自动光学检查AOI原理介绍AOI(Automatic Optical Inspection)即PCB线路自动光学检查,是一种通过光学设备对PCB线路进行快速、准确的检测技术。
AOI系统通过高分辨率的相机和专业的图像处理算法,能够实时采集到PCB线路的图像,并根据预先设定的检测规则,对线路进行自动检查,以判断是否存在缺陷。
AOI系统的工作原理主要包括图像采集、图像处理和缺陷判定三个步骤。
第一步,图像采集。
AOI系统通过高分辨率的相机,对待检测的PCB线路进行拍照,将其转化为数字图像。
相机设备通常采用光学特殊镜头,能够捕捉到细小的线路缺陷。
图像采集的目的是为了获取线路的细节信息,为后续的图像处理提供基础。
第二步,图像处理。
获得图像后,AOI系统会对图像进行预处理,提取出所需的特征信息。
这一步通常包括图像增强、图像分割和特征提取等操作。
图像增强可以通过去噪、增强对比度等手段,提高线路图像的质量和清晰度。
图像分割是将线路图像中的元素分开,去除背景和多余的噪声。
在特征提取阶段,系统会提取出线路的各种特征参数,例如线宽、间距、焊盘形状等,用于后续的缺陷判断。
第三步,缺陷判定。
通过比对待测线路的特征参数和预设的标准值,AOI系统可以判断出线路是否存在缺陷。
这一步通常使用图像匹配、分类识别等算法进行。
例如,可以将待检测的线路与正常线路的图像进行比对,通过匹配程度来判断线路是否存在异常。
对于常见的缺陷类型,例如焊盘错位、虚焊、短路等,系统可以根据预设的规则进行分类识别。
AOI系统的优点是速度快、准确度高和自动化程度高。
相比传统的人工检查方法,AOI系统可以大大提高检查的效率和准确度。
而且由于其全自动化的特点,可以适用于大批量生产,并能够检测到人眼难以察觉的线路缺陷。
不过,AOI系统也存在一些局限性。
例如,对于非透明的线路或者多层线路的检测,可能会受到光照条件等因素的限制。
此外,AOI系统也无法检测到一些隐蔽的缺陷,例如线路的电性能或者可靠性等方面的问题,需要借助其他测试方法进行检测。
pcb内层aoi的工作流程
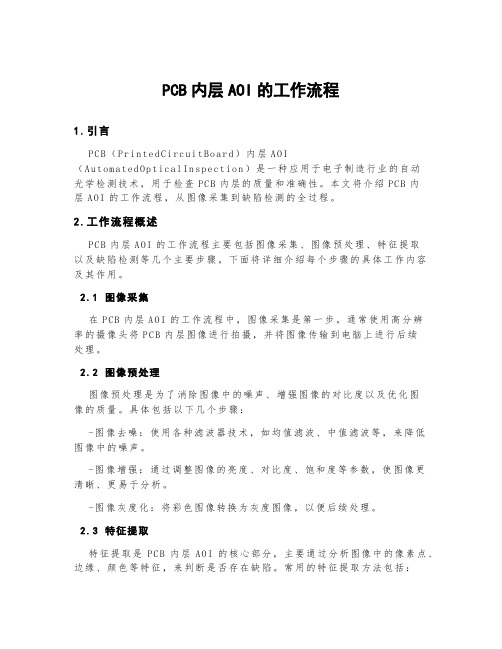
PCB内层AOI的工作流程1.引言P C B(Pr in te dC ir cu i tB oa rd)内层A OI(A ut om at ed Op ti ca l In sp ec ti on)是一种应用于电子制造行业的自动光学检测技术,用于检查PC B内层的质量和准确性。
本文将介绍PC B内层A OI的工作流程,从图像采集到缺陷检测的全过程。
2.工作流程概述P C B内层A OI的工作流程主要包括图像采集、图像预处理、特征提取以及缺陷检测等几个主要步骤。
下面将详细介绍每个步骤的具体工作内容及其作用。
2.1图像采集在P CB内层AO I的工作流程中,图像采集是第一步。
通常使用高分辨率的摄像头将PC B内层图像进行拍摄,并将图像传输到电脑上进行后续处理。
2.2图像预处理图像预处理是为了消除图像中的噪声、增强图像的对比度以及优化图像的质量。
具体包括以下几个步骤:-图像去噪:使用各种滤波器技术,如均值滤波、中值滤波等,来降低图像中的噪声。
-图像增强:通过调整图像的亮度、对比度、饱和度等参数,使图像更清晰、更易于分析。
-图像灰度化:将彩色图像转换为灰度图像,以便后续处理。
2.3特征提取特征提取是P CB内层A OI的核心部分,主要通过分析图像中的像素点、边缘、颜色等特征,来判断是否存在缺陷。
常用的特征提取方法包括:-形状检测:通过检测图像中的圆形、矩形、椭圆等几何形状,来判断是否存在缺陷。
-边缘检测:使用边缘检测算法,如C ann y边缘检测算法等,来提取图像中的边缘信息。
-颜色分析:通过对图像中的颜色进行分析,来判断是否存在颜色不一致或异常。
2.4缺陷检测缺陷检测是P CB内层A OI的最终目标,通过对特征提取后得到的特征进行分析和比对,来判断是否存在缺陷。
常见的缺陷包括焊盘缺失、元件偏移、短路、过孔等。
在缺陷检测中,通常会设置一定的阈值或规则,以判断缺陷是否超过了可接受的范围。
3.总结P C B内层A OI的工作流程包括图像采集、图像预处理、特征提取和缺陷检测等多个步骤。
- 1、下载文档前请自行甄别文档内容的完整性,平台不提供额外的编辑、内容补充、找答案等附加服务。
- 2、"仅部分预览"的文档,不可在线预览部分如存在完整性等问题,可反馈申请退款(可完整预览的文档不适用该条件!)。
- 3、如文档侵犯您的权益,请联系客服反馈,我们会尽快为您处理(人工客服工作时间:9:00-18:30)。
的运动 , 故采用 两轴 的运动控制卡可以实现 。M C 1 P 0 控制卡是基
于P c机 I S A总线 的步进 电机或数字式 伺服 电机的上位 控制单 元, 它与 P c机构成 主从式控制结构 ,c机 负责人机交互界 面的 P
tl g q i t n S se o — n n p cig De ie o CB a d i a e Ac u s i y tm fOn l e I s e tn vc fP l io i Bo r
LIYi TAN ixn, n ng, L- i LIBi
m tncn o ssm sutr ado r i r c ebsdO eMP O t ot l a dsl o r xone eseic oo otl y e t c en p an p ni ae 1t C 1m o cn o cr a ' m t ,epuddt pc i r t r u e t i p g i 1 h o r r dn e V O o h i f
李 颖 , 立新 , 谭 李 斌
400 ) 120 ( 南信息职业技术学 院, 南望城 湖 湖
摘 要: 介绍 了 P B在线检测原理 , 述 了一种 P B在 线检 测设备 的 系统结构 , C 描 C 在设备 的 P B图像采 集 系统 中, 出了 C 提 采用两轴电机 实现扫描检 测的解决方案 , 介绍 了基 于 M V 运动控制 卡和伺服 电机 的运动控 制 系统 结构和工作原 理 , t ̄I 详
数字式伺服 电机 的上 位控 制单元 , 与 P 它 c机构成 主从 式控制 结构 :c机负责人机交互界 面的管理 和控 制系统的实时监控 等 P 方 面的工作 ( 例如键 盘和 鼠标 的管理 、 系统状态 的显示 、 控制指
到 V o c中去与 c语 言里包 含头文 件类 似 ; 动态链 接库 BP j t re 把
0 引言
采集部分是整个 系统 的重要 组成 部分 。摄像 机 和镜头 在机 器
P B检测 项 目要求 速度快 、 度高 , 于机器 视觉 的智 能 C 精 基 检测设备 , 集光 、 、 计算 机 、 机 电、 图像 处理技 术 于一 体 , 是取 代 人工检测 , 实现高速、 高精度 自动视 觉检测 的最佳选 择 。为此 ,
测设备的结构如图 l 所示 。
处 理的方法判断 P B板是否合格 , 图 2 图 3 C 见 、 。摄像机 在拍摄 P B图像 时 , C 由于要保 证 一定 的检 测精 度 , 以每次 拍摄 的 区 所 域 有限。在检测面积 比较大 的 P B时 , C 摄像 机一次拍摄 很难将 P B的全部 图像 拍摄 下来 。为此 , C 研制 出通过 两轴伺服 电机控
此 , 相关 的函 widn 等 也 没有 包 括在 D L 中, 对 与此 a— e to L库 但
Wi o 消息传递 机制 比较熟悉 的开 发者 一般 都能编制出相同 nw ds
功 能的 Wi o s n w 函数 。 d
设置一 台 P c机上使用控制 卡的数量 函数 : t ol_l i s_ a nn t n eb r n d
机, 两个伺 服电机分 别控 制摄 像机 运动 模块 作 、 Y方 向的运
动 C 4。 3 l —
调用 D L中提供 的运动 函数 十分容 易 , L 由于 D 3 0 ks MC0 . s 文件包 含 D L函数 的必要说 明, L 程序 中调用 D L函数 与 c中调 L
用基本一样 。
是 P B检测 系统 的重要环节 , C 也是 检测处理 的基础 。P B检 测 C 系统强调检测 的速度 和精度 , 以需要 图像 采集部 分及 时 、 所 准 确地提供清晰 的图像 【 l 卜2。 2 图像采集 系统 的运动控 制研 究及 实现
P B在检测时运行在专用 的卡槽式传 送带上 , 入检测机 C 进 柜后 就会 触发检测机 柜 内的检测 装置对 P B进行检 测 。此 时 C 的流水线就应停止 运动 , 待检测 完成 后 , 等 流水线 运行将 下一 待检测 P B传送至检测机位 。在完成 P B板检测时 , C C 由于采用
n, ta ) o i s ; n be
如图 4 示 , 动控 制 卡通 过接 线 板 与 电机 的驱 动器 相 所 运
连, 电机 驱 动 器 与 电 机 相 连 。混 合 式 步 进 电 机 选 用 意 大 利 H 2032 ( ., . ・ ) 驱动器选用 I4 ( 大细分为 26 N 0 46 18 28N m , M 8最 5,
的机器视觉的方法 , 即通过 摄像机 拍摄 P B的 图片 , 用 图像 C 采
P B在线 检测 系统结 构复 杂 , C 其传 动控制设 备 、 电气控 制
系统 和摄像 机 必须 在计 算机 的精确 控 制下 , 能协 调处 理 工 才
作, 完成 复杂 的检测 和分拣任务 。基 于机 器视觉 的 P B在线 检 C
针对这一需求 , 图像 采集系统将摄像 机安装在 高精度运动 模块上 , 动模块 有伺 服 电机驱 动 , 服 电机 运动 控制 系统采 运 伺
用基于 P c机 的运动控制 卡控制 , 运动控制卡插在 P c机扩展槽
维普资讯
Isrme t e hiu n e sr ntu n cnq ea dS no T
制摄像 机和光源在一个平面上 的移动采集 P B图像 。 C
圈1 P CB在线检测 系统 结构
圈2 C P B在线检测示意圈
系统主要分为运动控制 、 图像 采集 和图像处理 部分 。图像
收稿 日 : O — 4 2 收修改稿 日 : O — 5 0 期 2 7 0— 0 0 期 2 7 0—8 0
在运动控制 系统中 , 运动控制卡 需要控制模 、 Y两个方 向
绝大多数 D S O 环境下的 函数都包括在 D L L 动态链接库 中 ,
但并非是所有 的函数 , 如 由于 Wi o 环境下 的中断处理 较 例 nw ds 为复杂 和繁琐 , 以与中断相关 的 函数还 没有包括 进来。Wi. 所 n
细 阐述 了系统的硬件 具体 实现 , 用 V 并采 B为工具 , 了具有 良 可靠性 的软件控制平 台。 开发 好
关键 词 :C P B检测 ; 动控 制 ; 运 图像采集 ; 伺服 电机 中图分类号 :P 7 . T 235 文献标识码 : A 文章编号 - 0 —14 (0r c —04 0 1 2 8 l20 )r 03— 3 0 7 7
维普资讯
年
仪 表 技 术 与 传 感 器
I s u n T c n q e a d S n o n t me t e h i u n e s r r
2 O7 0r
No. 7
第 7期
基 于 机器 视 觉 的 P B在 线 检 测设 备 的 图像 采 集 系统 C
针对 P B的特点设计 了 P B在线检测设备 的硬件装 置 , 细讨 C C 详 论 了检测设 备图像采 集系 统 的的硬件 实现 方案 , 并采 用 Vsa i l u Bs 。 ai 实现软件 的研究与 开发 。 c 1 系统的总体结构
视觉 中相 当于人 的眼睛 , 负责拍摄对 象的 图像 。图像 采集部分
读取每块控制卡 的基地址 函数 : e ba —ae i or— i gt or bs(n ba t n — d t d
管理和控制系统 的实时监控等方 面的工作 , 如键盘 和 鼠标 的 例 管理系统状态 的显示控制指令的发送外部信号 的监控等。 在视觉检测平 台系统 中, 要求 执行 电机 的空载响应 时间为
4 6 s而步进 电机 的响应时间(0 s 右) 能满 足该 系 0 0m . 20m 左 不
( i nC lg f tomai 。 agh a 120 a血m) Hma o eeo l r t n W nce g400 , l f o
Ab la t ra r cpe o nie P n p ci a n e ci igo e s s m t c r f h n p c o a t d c d, l t n s e : l p i ii f l CB is e t n w sa d d s r n n yt s u t e o t ei e t n W i r u e a s u o z le n o n o b e r u s i s no o i fr ua o o be moo o t l y tm a r sn e i h CB ilg c Ist n s tm f e fc i e .Me n hl tit d c d te o m l f u l t r nr s d c o s e W p ee td, te P I£ e a ql io y e o a it s s n lI ii s h t l i a w i i nr u e h e o
r ai t n o te h lwa o te s tm n d t l .a d d v lp d a w l rl b e sf r o t lpa om t o . e l a o f h a' l f y e i a s n eo e e ei l t e c n r lt r wi VB a a t 1 zi d  ̄ h s e i e l a o wa o f h s o Ke o d : C n p c o ; t n c nr l i g c Ist n sl O m tr y w r s P B i e t n m i o t ; s i o o o ma ea ql io ; ' o i i eV o
D C0 .L M 30 D L拷入 c 、 no s ye 子 目录; : Wi w 、s t d sm 在应用程 序 中