ICAO Annex14
民用机场飞行区技术标准

在国际民nex 14)中,规定了民用机场飞行区的技术标准。这些标准包括飞行区内的地面标志、导航设施、通信设备、能见度要求、照明设备等。
根据ICAO的规定,民用机场的飞行区应具有足够的宽度和长度,以满足不同类型的飞机的起飞和着陆要求。此外,飞行区的地面应平整、稳定,并具有足够的承载能力。飞行区内的导航设施、通信设备和照明设备应符合ICAO的规定,以保证飞行的安全性。
机场滑行引导标记牌培训教程

滑行引导标记牌中国民用航空局机场司马志刚caacma@2008年10月滑行引导标记牌滑行引导标记牌•传达飞机或车辆必须停住等待塔台放行的信息;•传达禁止进入某一地区的信息;•帮助驾驶员识别其所在位置;•帮助驾驶员识别滑行道交叉或分支点前方滑行道的代号;•向驾驶员指明前往目的地的方向;•帮助驾驶员判断其飞机是否已脱离跑道。
滑行引导标记牌包括指令性标记牌左侧的标记牌设在Mandatory Instruction SignsFigure 5-30 ICAO 5.4.2.2 –Mandatory instruction signs shall include runway designation signs, category I, II or III holding position signs,runway-holding position signs, road-holding position signs and NO ENTRY signs.Mandatory Instruction SignsB115R -33L15R -33L33L CAT IIIB2{Runway designation sign on a taxiway Runway designation sign on a runway Category III holding position signRunway-holding position sign on a taxiway NO ENTRY signICAO 5.4.2.12 –A mandatory instruction sign shall consist of an inscription in white on a red background.Comparison of Runway Holding Position SignsB115R -33L15R -33L33L CAT IIIB2Runway designation signon a taxiwayRunway designation signon a runwayILS holding position signs Runway-holding position sign ILS CAT II/III 14 -APCH ICAOFAA B115R -33L Holding position sign on a taxiway 15R -33L Holding position sign on a runway Category III holding position signApproach holding position sign强制标记牌Mandatory instruction signs指令性标记牌(Mandatory instruction Signs)信息标记牌(Information Signs)信息标记牌主要包括:•位置标记牌(Position sign)•方向标记牌(Direction sign)•目的地标记牌(destination sign)•跑道入口标记牌(Runway threshold sign)•脱离跑道标记牌(Runway turn-off sign)•飞机机位号码标记牌(Aircraft stand number sign)•VOR校准点标记牌(VOR check-point sign)信息标记牌(Information Signs)•位置标记牌一般为黑底黄字,•其他信息标记牌一般均为黄底黑字。
航空障碍灯设计标准
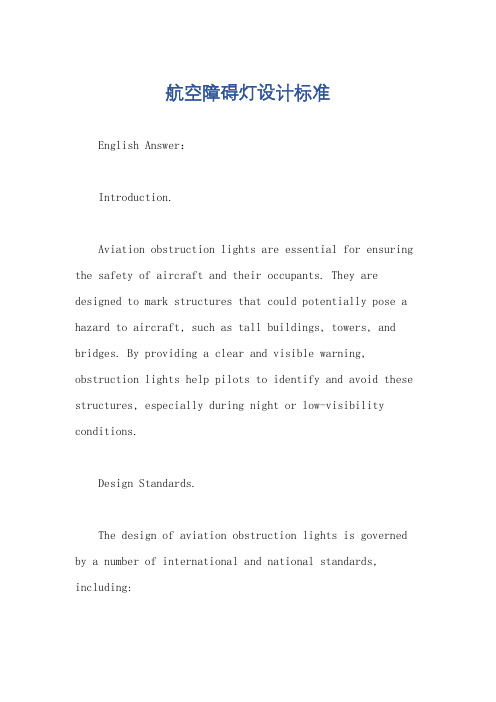
航空障碍灯设计标准English Answer:Introduction.Aviation obstruction lights are essential for ensuring the safety of aircraft and their occupants. They are designed to mark structures that could potentially pose a hazard to aircraft, such as tall buildings, towers, and bridges. By providing a clear and visible warning, obstruction lights help pilots to identify and avoid these structures, especially during night or low-visibility conditions.Design Standards.The design of aviation obstruction lights is governed by a number of international and national standards, including:International Civil Aviation Organization (ICAO) Annex 14, Volume I Aerodromes.Federal Aviation Administration (FAA) AdvisoryCircular AC 150/5345-43F, Approved Model List of Obstruction Marking and Lighting Aids.International Electrotechnical Commission (IEC) 61439 series of standards for aviation obstruction lights.These standards specify the following requirements for aviation obstruction lights:Light intensity: The light intensity must besufficient to ensure that the light is visible from a distance of at least 5 nautical miles (9 kilometers) under clear night sky conditions.Light color: The light must be either red or white, depending on the location and purpose of the structure.Flash rate: The light must flash at a rate of between20 and 60 flashes per minute.Light pattern: The light must be visible from all directions.Light source: The light source must be a high-intensity LED or halogen lamp.Housing: The housing must be weatherproof and durable enough to withstand the elements.Types of Aviation Obstruction Lights.There are several different types of aviation obstruction lights, each designed for a specific purpose:Steady-burning lights: These lights emit a continuous beam of light. They are typically used to mark structures that are less than 150 feet (45 meters) tall.Flashing lights: These lights emit a flashing beam of light. They are typically used to mark structures that arebetween 150 feet (45 meters) and 500 feet (150 meters) tall.High-intensity flashing lights: These lights emit a very bright flashing beam of light. They are typically used to mark structures that are over 500 feet (150 meters) tall.Obstacle lights: These lights are designed to mark obstacles that are located near airports, such as trees, buildings, and wind turbines.Installation and Maintenance.Aviation obstruction lights must be installed and maintained according to the manufacturer's instructions. This includes ensuring that the lights are properly aligned and that the light intensity is within the specified range. Obstruction lights should also be inspected regularly to ensure that they are functioning properly.Conclusion.Aviation obstruction lights play a vital role inensuring the safety of aircraft and their occupants. By providing a clear and visible warning, obstruction lights help pilots to identify and avoid structures that could pose a hazard to their aircraft. The design andinstallation of obstruction lights is governed by a number of international and national standards, which ensure that these lights are effective and reliable.Chinese Answer:航空障碍灯设计标准。
ICAOAnnex14
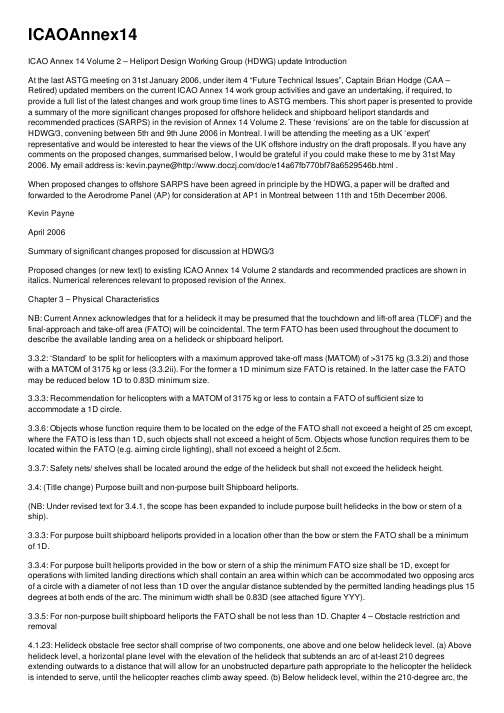
ICAOAnnex14ICAO Annex 14 Volume 2 – Heliport Design Working Group (HDWG) update IntroductionAt the last ASTG meeting on 31st January 2006, under item 4 “Future Technical Issues”, Captain Brian Hodge (CAA –Retired) updated members on the current ICAO Annex 14 work group activities and gave an undertaking, if required, to provide a full list of the latest changes and work group time lines to ASTG members. This short paper is presented to provide a summary of the more significant changes proposed for offshore helideck and shipboard heliport standards and recommended practices (SARPS) in the revision of Annex 14 Volume 2. These ‘revisions’ are on the table for discussion at HDWG/3, convening between 5th and 9th June 2006 in Montreal. I will be attending the meeting as a UK ‘expert’representative and would be interested to hear the views of the UK offshore industry on the draft proposals. If you have any comments on the proposed changes, summarised below, I would be grateful if you could make these to me by 31st May 2006. My email address is: kevin.payne@/doc/e14a67fb770bf78a6529546b.html .When proposed changes to offshore SARPS have been agreed in principle by the HDWG, a paper will be drafted and forwarded to the Aerodrome Panel (AP) for consideration at AP1 in Montreal between 11th and 15th December 2006. Kevin PayneApril 2006Summary of significant changes proposed for discussion at HDWG/3Proposed changes (or new text) to existing ICAO Annex 14 Volume 2 standards and recommended practices are shown in italics. Numerical references relevant to proposed revision of the Annex.Chapter 3 – Physical CharacteristicsNB: Current Annex acknowledges that for a helideck it may be presumed that the touchdown and lift-off area (TLOF) and the final-approach and take-off area (FATO) will be coincidental. The term FATO has been used throughout the document to describe the available landing area on a helideck or shipboard heliport.3.3.2: ‘Standard’ to be split for helicopters with a maximum approved take-off mass (MATOM) of >3175 kg (3.3.2i) and those with a MATOM of 3175 kg or less (3.3.2ii). For the former a 1D minimum size FATO is retained. In the latter case the FATO may be reduced below 1D to 0.83D minimum size.3.3.3: Recommendation for helicopters with a MATOM of 3175 kg or less to contain a FATO of sufficient size to accommodate a 1D circle.3.3.6: Objects whose function require them to be located on the edge of the FATO shall not exceed a height of 25 cm except, where the FATO is less than 1D, such objects shall not exceed a height of 5cm. Objects whose function requires them to be located within the FATO (e.g. aiming circle lighting), shall not exceed a height of 2.5cm.3.3.7: Safety nets/ shelves shall be located around the edge of the helideck but shall not exceed the helideck height.3.4: (Title change) Purpose built and non-purpose built Shipboard heliports.(NB: Under revised text for 3.4.1, the scope has been expanded to include purpose built helidecks in the bow or stern of a ship).3.3.3: For purpose built shipboard heliports provided in a location other than the bow or stern the FATO shall be a minimum of 1D.3.3.4: For purpose built heliports provided in the bow or stern of a ship the minimum FATO size shall be 1D, except for operations with limited landing directions which shall contain an area within which can be accommodated two opposing arcs of a circle with a diameter of not less than 1D over the angular distance subtended by the permitted landing headings plus 15 degrees at both ends of the arc. The minimum width shall be 0.83D (see attached figure YYY).3.3.5: For non-purpose built shipboard heliports the FATO shall be not less than 1D. Chapter 4 – Obstacle restriction and removal4.1.23: Helideck obstacle free sector shall comprise of two components, one above and one below helideck level. (a) Above helideck level, a horizontal plane level with the elevation of the helideck that subtends an arc of at-least 210 degrees extending outwards to a distance that will allow for an unobstructed departure path appropriate to the helicopter the helideck is intended to serve, until the helicopter reaches climb away speed. (b) Below helideck level, within the 210-degree arc, thesurface shall extend downwards below the elevation of the helideck to water level for an arc of not less than 180 degrees that passes through the centre of the FATO and outwards to a distance that will allow for safe clearance from obstacles below the helideck in the event of an engine failure for the type of helicopter the helideck is intended to serve.Note: For PC1 and PC2 helicopters the horizontal extent of these distances from the helideck will be compatible with the one-engine inoperative capability of the helicopter type to be used.4.1.28 (Characteristics of the limited obstacle sector – LOS): Unchanged (including Figures 4-3 to 4-5) for 1D helidecks. In the case of a FATO less than 1D, the limited obstacle surfaces shall nonetheless reflect the same dimensions and requirements as if the FATO was of diameter 1D.4.2.14: Recommendation (applicable for helidecks excluding heliports on ships), if a permitted obstacle is located within the inner portion of the LOS at a height >5cm but less than 0.05D, a prohibited landing sector (PLS) should be established to provide the helicopter with further protection from obstacles not readily visible to flight crew because the obstacles are positioned behind a landing helicopter.4.2.15: Falling 5:1 gradient may be reduced to a ratio of one unit horizontally to three units vertically within the 180 degree sector for multi-engine helicopters.Shipboard heliports: Obstacle restriction criteria for an amidships location differentiated between landings facing athwart ships and landings facing fore and/or aft. Obstacle criteria from 4.2.24 to 4.2.27 are applicable to a non-purpose built ships side location.4.2.21: Amidships location with landing facing athwart ships. No objects permitted above helideck level except those essential for the safe operation of the helicopter and then only up to a maximum height of 5 cm. No raised fittings permitted on the deck that might induce dynamic rollover.4.2.23: Amidships location with landings facing fore and/or aft. Obstacles located in the 150- degree sector to the rear of a landing helicopter, shall not exceed a height of 5 cm for a distance from the edge of the FATO of 0.5D. See Figure 4-11.4.2.25-4.2.26: Ships side location: Obstacle criteria in accordance with revised Figure 4-12 (shown below).4.2.27: Ships side location, to provide further protection from obstacles not readily visible to the flight crew obstacles within the 1.5D circle (out-with the 1D portion designated as the FATO) located to the rear of a landing helicopter shall not exceed 5cm for a distance from the edge of the FATO of 0.5D. See Figure 4-12.Chapter 5 – Visual Aids5.2.9.3 Location of the touchdown marking (aiming circle): Note “It is not considered appropriate to offset a touchdown marking on a helideck located on the bow of a vessel or for any helideck where the certificated D value is 16.0m or less.”5.2.9.6 Characteristics of the touchdown marking: Recommendation: “Where a touchdown marking is intended to serve helicopters of significantly different sizes, an additional concentric touchdown marking should also be displayed.”5.2.12 Helideck Surface Marking: New standards introduced requiring the FATO to be painted dark green or dark grey usinga high friction paint coating. On unpainted (light grey) aluminium decks, markings shall be enhanced by a black outline or black background.5.2.13 Helideck Prohibited Landing Sector Marking: New Recommendations introduced to provide PLSM on the touchdown marking to the edge of the FATO where it is necessary to prevent the helicopter from landing within specified arcs. PLSM‘Characteristics’ are the same as CAP 437, chapter 4, Figure6.Arc of minimum value 1D FIGURE YYY(b) landing fore or aftMax height of obstacle within (a) landing athwartships FIGURE 4-11。
机场规划和候机楼设计说明书

November 2018
(RGS WG/5)
12
Airport Master Planning Process Cont.
• Physical Planning
– Airspace and air traffic control provisions. – Airfield configuration (including approach zones). – Terminal complex. – Circulation, utility and communications networks. – Support and service facilities. – Ground access systems. – Over‐all land use patterns.
budgets. – Prepare and evaluation and decision format. – Establish coordination and monitoring procedures. – Establish data management and public
information system.
needs among aerodrome authority, businesses
5
and community.
November 2018
(RGS WG/5)
Changi Airport Master Plan
November 2018
(RGS WG/5)
Eaton Crouse-Hinds系列机场照明设备操作手册说明书
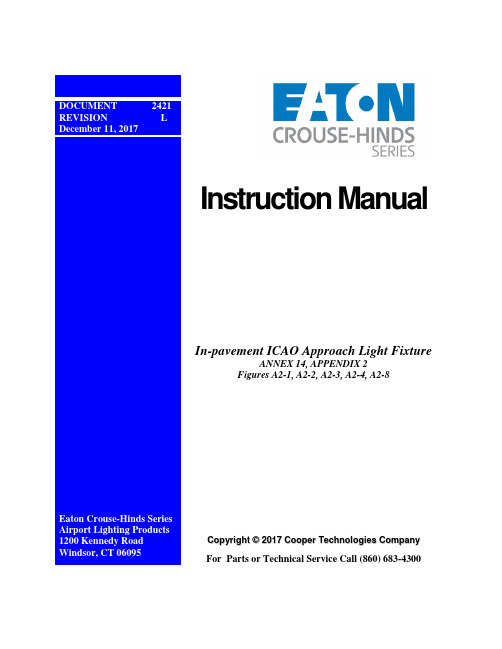
2421Instruction ManualIn-pavement ICAO Approach Light FixtureANNEX 14, APPENDIX 2Figures A2-1, A2-2, A2-3, A2-4, A2-8C o p y r i g h t © 2017 C o o p e r Te c h n o l o g i e s C o m p a n yFor Parts or Technical Service Call (860) 683-4300Instruction ManualICAO Approach Fixture 1.0 RevisionsRevision Issue/ReissueLetter NumberDescription Created/Updated Checked Approved See record copy for revisionhistoryK A215-119 Updated installation bolttorque range and torquemethod; Added section 7.1, 7.2,and 7.3CS KF 4/23/15L A217-185 Revised title page & section 2;Section 8.4, torque 55-60 was30 in-lbs; Updated section 8.8& Figure 5 for grounding lug.EB PG 12/11/17Instruction ManualICAO Approach Fixture2.0 Product WarrantyWarrantyRefer to Eaton’s Crouse-Hinds Airport Lighting Products Terms and Conditions for product specific warranty information.Instruction ManualICAO Approach Fixture3.0 Safety NoticesThis equipment is normally used or connected to circuits that may employ voltages that are dangerous and may be fatal if accidentally contacted by operating or maintenance personnel.Extreme caution should be exercised when working with this equipment. While practicalsafety precautions have been incorporated in this equipment, the following rules must bestrictly observed:3.1 Keep Away from Live CircuitsOperating and maintenance personnel must at all times observe all safety regulations. DONOT PERFORM MAINTENANCE ON INTERNAL COMPONENTS OR RE-LAMP WITH POWER ON.3.2 ResuscitationMaintenance personnel should familiarize themselves with the technique for resuscitationfound in widely published manuals of first aid instructions.IMPORTANTIMPORTANT:See FAA Advisory Circular AC 150/5340-26 for additional information.Instruction ManualICAO Approach Fixture4.0Table Of ContentsTitle Page (1)1. Revisions (2)2. Product Warranty (3)3. Safety Notices (4)4. Table of Contents (5)5. Part Number Explanation (6)6. General Description (7)6.1 ICAO Approach Light (7)7. Installation (8)7.1 Metric Base Installation Bolt Torque and Installation Method (8)7.2 ANSI Base Installation Bolt Torque and Installation Method (9)7.3 Heico-Lock Installation Guidelines (2014) (9)8. Maintenance (10)8.1 Cleaning Lenses (10)8.2 Relamping (10)8.3 O-Ring Replacement (10)8.4 Lens Replacement (11)8.5 Power Lead Feed-Thru Replacement (12)8.6 Pressure Test (12)8.7 Cleanliness and Workmanship (13)8.8 Maintenance Program (13)9. Parts List (14)Figure 1. Exploded View of Fixture (15)Figure 2. Isometric View of Fixture (16)Figure 3. Top View of Fixture (17)Figure 4. Side View of Fixture (17)Figure 5. Bottom View of Fixture (18)Figure 6. Feed-Thru Detail (19)Instruction ManualICAO Approach Fixture5 Part Number Explanation8506 A - XXX - XX FIXTURE TYPE:850 = RUNWAY6 = MODEL 6C-H STYLE:A = ICAO APPROACHICAO FIGURES:CS = FIGURE 2.1; CLEAR, STRAIGHT, UNIDIRECTIONALR2L = FIGURE 2.2, TOE-LEFT; RED UNIDIRECTIONALR2R = FIGURE 2.2, TOE-RIGHT; RED UNIDIRECTIONALG3L = FIGURE 2.3, TOE-LEFT; GREEN UNIDIRECTIONALG3R = FIGURE 2.3, TOE-RIGHT; GREEN UNIDIRECTIONALG2L = FIGURE 2.4, TOE-LEFT; GREEN UNIDIRECTIONALG2R = FIGURE 2.4, TOE-RIGHT; GREEN UNIDIRECTIONALRS = FIGURE 2.8; RED, STRAIGHT, UNIDIRECTIONALGR = G3L / RS; BIDIRECTIONALRG = G3R / RS; BIDIRECTIONALGS = GREEN, STRAIGHT, UNIDIRECTIONALL-823 CONNECTION:P1 = ONE PLUGP2 = TWO PLUGS (GR AND RG UNITS ONLY)Instruction ManualICAO Approach Fixture6General Description6.1ICAO Approach LightThe Crouse-Hinds ICAO Approach Light is a Style II, (≤1/2 inch) fixture that meets thephotometric requirements of ICAO Annex 14 fixtures 2.1, 2.2, 2.3, 2.4, and 2.8 with theappropriate lamp(s) and colored lens/lenses installed. It is designed for installation at therunway threshold or any other location where visual guidance of moving aircraft is desirable.The fixture is designed to fit on a FAA L-868 (do not install on shallow base), steel, size Blight base per FAA AC 150/5345-42 (latest version), and have a total height abovegrade/ground level of < .500 inch. The fixture is uni-directional, projecting the beam of light in one direction or bi-directional when used as a threshold wingbar or siderow light with a red end light. It is weatherproof and will endure roll over loads without damage. The light fixture consists of a 1-piece aluminum optical assembly. The aluminum optical assembly is mounted to a light base with six bolts and six 2-piece lock washers. The aluminum housing has a sand cast bottom cover that is attached using 6 screws. A silicone o-ring is used to provide awatertight seal between the inner cover and the optical housing. The lamp(s) are secured to an installed bracket, which is fastened to the bottom housing using vibration isolators. Electrical connections are made at one or two feed-thru assemblies in the inner cover. The feed-thru has an ITS verified L-823 plug for connecting to FAA L-830/ L-831 Isolation Transformers. The outer lens is held into the aluminum housing with a bracket, gasket, molded elastomeric boot and 2 screws. The light beam color is obtained by coloring the lens to the appropriate colorfor the application. All hardware is type 18-8 stainless steel. The complete light unit is 11.94 inches in diameter, 5.13 inches deep, and weighs 16 lbs.CAUTIONCAUTION:Never handle the light assembly by the leads as this can break thewaterproof seal.Instruction ManualICAO Approach Fixture7 InstallationThe style 2 IAL light units are shipped complete and are ready for installation as received.Installation of a light unit is to be done with primary POWER OFF and SECURED. At each light location, install a steel, Size B, 24 inch deep minimum, L-868 Light Base per FAA AC 150/5340-4 (latest revision). Place the properly sized isolation transformer(s) in the light base and make necessary primary power connection using L-823 connectors. The light unitrequires a 6.6A secondary transformer. Verify that the mounting flange on the light base isclean and the o-ring (optional on deep cans) is coated with Dow Corning FS 1292 grease and is in place on the light base. Connect the plug from the light unit to the secondary of thepreviously installed isolation transformer. Installation tool, Crouse-Hinds P/N 19999, willease in the installation and removal of the light unit. The threaded eyebolts on the lifting tool screw into threaded holes in the light fixture. Lower the light unit straight down onto thebase. The light fixture is subject to optical misalignment or mechanical damage if not seated properly. Secure the light fixture to the base per section 7.1 or 7.2, depending on your basetype.7.1 Metric Base Installation Bolt Torque and Installation Method•Use fully threaded A4-70 M10x1.5 bolts. (P/N 21738 is recommended)•Use Heico-Lock or Nord-Lock stainless steel lock-washers per FAA specification*.•Mounting base holes must be degreased, cleaned, and dried prior to bolt installation.•Base-to-fixture mating surfaces must be degreased, cleaned, and dried prior to installation.•Apply marine grade anti-seize (K=.18) per manufacturer’s instructions to each bolt.•Install the M10 bolts with lock-washers per lock-washer manufacturer’s guidelines.•See section 7.3 for Heico-Lock installation guidelines (2014).•Achieve a full final torque of 26.8 N-m (237 in-lbs) +10%, -0% with a calibrated torque wrench.•Impact wrenches are not recommended as installation tools.•Check torque and re-torque all bolts within 2 weeks of initial installation.•Maintain all bolts by checking torque and re-torqueing per FAA specifications*.•If other lubricants or thread locking compounds are used (not recommended), torque must be recalculated based on K factor provided by lubricant or compound manufacturer.•New bolts and lock-washers shall be used each time a light unit is removed from its base.*Refer to the following specifications for FAA installation and maintenance recommendations:•AC150/5340-26 “Maintenance of Airport Visual Aids”•AC150/5345-46 “Specification for Runway and Taxiway Light Fixtures”•FAA Engineering Brief No. 83 “In-pavement Light Fixture Bolts”Instruction ManualICAO Approach Fixture7.2 ANSI Installation Bolt Torque and Installation Method•Use fully threaded, cold-worked 18-8 stainless steel 3/8-16 bolts. (P/N 21715 is recommended.•Use Heico-Lock or Nord-Lock stainless steel lock-washers per FAA specifications*.•Mounting base holes must be degreased, cleaned, and dried prior to bolt installation.•Base-to-fixture mating surfaces must be degreased, cleaned, and dried prior to installation.•Apply marine grade anti-seize (K=.18) per manufacturer’s instructions to each bolt.•Install the 3/8-16 bolts with lock-washers per lock-washer manufacturer’s guidelines.•See section 7.3 for Heico-Lock installation guidelines (2014)•Achieve a full final torque of 225 in-lbs (25.4 N-m) +10%, -0% with a calibrated torque wrench.•Impact wrenches are not recommended as installation tools.•Check torque and re-torque all bolts within 2 weeks of initial installation.•Maintain all bolts by checking and re-torqueing per FAA specifications*.•If any lubricants or thread locking compounds are used (not recommended), torque must be recalculated based on K factor provided by lubricant or compound manufacturer.•New bolts and lock-washers shall be used each time a light unit is removed from its base.*Refer to the following specifications for FAA installation and maintenance recommendations:•AC150/5340-26 “Maintenance of Airport Visual Aids”•AC150/5345-46 “Specification for Runway and Taxiway Light Fixtures”•FAA Engineering Brief No. 83 “In-pavement Light Fixture Bolts”7.3 Heico-Lock Installation Guidelines (2014)Step 1: Hand tighten to ensure that 2-3 threads extend beyond the nut on through-bolt applications.Step 2: Tighten each bolt to one-third of the final required torque following the pattern as shown below.Step 3: Increase the torque to two-thirds following the pattern shown below.Step 4: Increase the torque to full torque following the pattern shown below.Step 5: Perform one final pass on each bolt working clockwise from bolt 1, at the full final torque.Instruction Manual ICAO Approach Fixture8 MaintenanceThe preferred method of maintaining these lights is to periodically and systematically replace the units and return it to the maintenance shop for renovation. As an alternative, the units can be serviced in the field. However, it is recommended that field servicing be limited tocleaning the lens only as described in section 8.1.8.1 Cleaning LensesWith a compressed air blast or suitable brushes, remove all accumulated debris from the lightchannel. Clean the outer lens surface with a detergent solution. If the lens is coated with a substance impervious to the detergent, a suitable solvent should be sparingly applied with a wad of cotton or a patch of cloth on the end of a wood splint. After the solvent has acted the remaining solvent and softened coating should be removed with a clean piece of cotton or cloth. Care should be taken to avoid excessive contact between the solvent and the lens seal. Remove all remaining solvent from lens and seal. A gentle air blast may be used.8.2RelampingRemove and secure power to the fixture. Turn the fixture upside down and remove the six screws holding the inner cover to the light housing. Disconnect the lamp leads. Inspect the feed-thru terminal for signs of corrosion. Replace feed-thru assemblies per paragraph 8.5. Install the new lamps by reversing the procedure above making sure that the Teflon tubingcompletely covers the lamp terminals. Inspect/replace the optical housing’s o-ring perparagraph 8.3. Assemble the inner cover onto the light housing. Tighten the mounting screws to 30 in-lbs. Secure the light fixture to the base per section 7. 8.3 O-Ring ReplacementEvery time the unit is opened, the o-ring must be closely examined and replaced, if necessary. Any o-ring that is stretched, torn, has permanent set, or some other defect, which would prevent it from forming a watertight seal, must be replaced with a new o-ring.NOTICENOTICE:Warranty is void if other than Crouse-Hinds ALP parts are used to relamp or rebuild the fixture.NOTICENOTICE:The lamp is hot when fixture is energized and remains hot for ashort time after fixture is turned off.Instruction Manual ICAO Approach FixtureRemove the old o-ring from the groove in the optical housing. Carefully clean the o-ring groove and flange mating surface on the inner cover. Take care not to damage the mating surface. Clean the new o-ring (P/N 21385) with denatured alcohol. Position the new o-ring in the center of the groove and press it into place. Torque the inner cover screws to 30 in-lbs. Perform a pressure test as described in paragraph 8.6. Secure the light fixture to the base per section 7.8.4Lens ReplacementIf an outer lens is broken, leaks, or is badly pitted or scarred, it must be replaced. It is highly recommended that this task be performed in a clean shop environment. Lens Replacement Kit P/N 21480-X contains all necessary parts to change a lens. Remove and secure power to the fixture. Turn the fixture upside down and remove the six screws holding the inner cover to the light housing. Remove the lens retaining bracket screws from the light housing. Remove the lens-retaining bracket and discard the lens-retaining gasket. Firmly push the lens/boot assembly from the outside of the light housing; discard the old lens and boot. Thoroughly clean the lens opening with isopropyl alcohol and let dry. Inspect the lens opening for scratches or pits; a damaged lens-opening surface will not seal properly. Place a new lens boot (P/N 21277) over the replacement lens (P/N 21276-X). Apply a thin coat of Dow Corning FS 1292 grease over the entire outside surface of the lens boot. Align the lens/boot assembly in the lens opening and press it into place. Verify that the lens boot is not pinched in the lens opening. Using a new lens-retaining gasket (P/N 21479), fasten the lens-retaining bracket (P/N 21477) to the light housing. Torque the mounting screws to 55-60 in-lbs. Inspect/replace the optical housing’s o-ring per paragraph 8.3. Assemble the inner cover onto the light housing. The screw-hole patterns in the inner cover and light housing are offset to insure proper alignment. Torque the mounting screws to 30 in-lbs. Perform a pressure test per paragraph 8.6. Clean the mounting flange area of the base. Secure the light fixture to the base per section 7.NOTE : Lighting Fixtures built/installed before June 2009 will require the 21276-X Lens Replacement Kit. The 21276-X Kit contains the P/N: 21101 lens-retaining gasket and the P/N: 21100 lens-retaining bracket. Lighting Fixtures built/installed after June 2009 require the 21480-X as listed above.NOTICENOTICE:A bad o-ring seal is the most common cause of inset fixture leaks.A new o-ring must be installed every time theOptical Assembly is openedNOTICENOTICE:The groove is designed to be wider than the o-ring. This provides room for the displacement of the o-ring when compressed between the housing and mating surface.Properly tightened screws are important in obtaining a complete seal.Instruction ManualICAO Approach Fixture8.5Power Lead/ Feedthru ReplacementThe power leads are connected to water tight feedthrus in the inner cover. There is a coating of RTV over the connections, and an epoxy material to encapsulate the entire assembly. The power cord and feedthru components can be replaced, but shipping restrictions prohibitCrouse-Hinds from supplying the epoxy encapsulating material. The complete inner coverassembly, with leads is part number 21286-X. Follow the instructions below to rebuild thepower lead/feedthru assembly.Remove and secure power to the fixture. Turn the fixture upside down and remove the sixscrews holding the inner cover to the light housing. Remove the Teflon leads inside the cover. Cut the power leads off at the encapsulating material. Using a hammer and chisel, separate theencapsulating material from the inner cover. Be careful to not damage the inner cover. Removeand discard the feedthru assemblies. Carefully clean the feed-thru mounting area in the innercover, inspect for any mechanical damage that would prevent a water tight seal. Replace thefeedthru components, refer to Figure 6 for part numbers and orientation. Replace the Teflon leads inside the cover. Replace the optical housing’s o-ring per paragraph 8.3. Assemble the innercover onto the light housing. The screw-hole patterns in the inner cover and light housing areoffset to insure proper alignment. Torque the mounting screws to 30 in-lbs. Perform a pressure test per paragraph 8.6. Secure the light fixture to the base per section 7.8.6 Pressure TestA light fixture should be subjected to a 20-psi air pressure test to verify that it is waterproofwhenever it has been opened or components have been replaced. A tire valve style pressurefitting is located on the bottom of the inner cover. Pressurize the fixture to 20-psi then place it in a tub of water or use a soap solution to locate escaping air bubbles. Carefully inspect theareas around the lens, inner cover seal, and feed-thru adapter for leaks. Relieve the internal air pressure before installing the fixture or attempting to repair a leak.WARNINGWARNING:Do not exceed 20-psi when pressure testing the fixture. Serious injury and/or permanent damage to the fixture may result if a higher air pressure is used. Once the pressure test iscomplete, be sure to relieve the air pressure.Instruction ManualICAO Approach Fixture8.7 Cleanliness and WorkmanshipService life depends upon the entire assembly being waterproof. All surfaces must be clean, dry and free of all foreign matter if the light fixture is to operate for extended periods without requiring maintenance.8.8 Maintenance ProgramIn order to insure maximum light fixture life, the installed units should be subject to amaintenance program in accordance with the following: A daily operation check should bemade of the lighting fixture. The lights should be energized and visually inspected. If anyfixtures are out, the location of the fixture should be recorded and the lamps replaced at a time when the circuit is de-energized. (See Section 8.2)8.8.1 Regular cleaning is necessary in order to insure that inset lighting fixtures operate atmaximum efficiency. The lens should be cleaned periodically with a soft cloth and solvent.The weather and the location of the fixtures will dictate the regularity and type of cleaning. 8.8.2 Snowplow operators should exercise extra care not to strike the light fixtures with snowplowblades (use rubber blades for added protection to the fixture.) After snowplow removaloperations, inspect all light fixtures to locate and replace if necessary, any damaged LightAssemblies. Passes over the light rows should be made with a power broom only if practical.Whenever snowplows must traverse in-pavement light fixtures, they should be traveling atless than 5 mph or have the blades lifted clear of the fixture.8.8.3 The light is designed to exclude both ground and surface water from entering. If the lights arenot properly maintained (i.e., bolts tightened and seals in good condition) water may enter the fixture. To prevent this from occurring, it is recommended that each fixture be inspected for the presence of water at least once a month. More frequent inspection is desirable during and following rainy seasons.8.8.4 ICAO approach fixtures hold-down bolts should be checked for proper torque per section 7.8.8.5 If any fixture contains water, the water should be removed and the entire fixture cleaned anddried. Perform a pressure test per paragraph 8.6 to locate the source of the leak. Replace the o-ring (21385), see Section 8.3.Instruction ManualICAO Approach Fixture9 Parts ListsITEM NO. 8506A-XXX-PX PART NUMBER DESCRIPTION1 SEE TABLE 21287 HOUSING, OPTICAL, ASS'Y, ICAO APPROACH2 1 21385 O-RING, SIZE #2-273, 70 DUROMETER, SILICONE, POST CURED3 SEE TABLE 21286 COVER, BOTTOM, ASS'Y, ICAO APPROACH4 SEE TABLE 21295 BRACKET, BASE, ASS'Y, ICAO APPROACH5 8 20356 GROMMET6 4 19143-2 SPACER7 4 10B08-019D16 PAN HD, #10-32 x .5 LG, SSTL8 6 10000-470 SCREW, 100° FLAT HD/DRI-LOC, #10-32 x 7/16 LG, 18-8 SS9 A/R 21128 105 WATT LAMP10 A/R 10047-417 MALE TERMINAL FOR LEAD ASSEMBLY11 A/R 10048-25 SILICONE GREASE12 1 2421 INSTRUCTION MANUAL13 A/R 21480-X LENS REPLACEMENT KIT G=Green; R=Red; c=ClearNOTE: Lighting Fixtures built/installed before June 2009 will require the 21276-X Lens Replacement Kit. The 21276-X Kit contains the P/N: 21101 lens-retaining gasket and the P/N: 21100 lens-retaining bracket. Lighting Fixtures built/installed after June 2009 require the 21480-X as listed above.P/N ITEM 1 ITEM 3 ITEM 48506A-CS-P1 21287-3C 21286-1 21295-CS8506A-RS-P1 21287-1 21286-1 21295-RS8506A-R2L-P1 21287-3R 21286-1 21295-R2L8506A-R2R-P1 21287-3R 21286-1 21295-R2R8506A-G2L-P1 21287-2 21286-1 21295-G2L8506A-G2R-P1 21287-2 21286-1 21295-G2R8506A-G3L-P1 21287-2 21286-1 21295-G3L8506A-G3R-P1 21287-2 21286-1 21295-G3R8506A-RG-P1 21287-4 21286-1 21295-RG8506A-RG-P2 21287-4 21286-2 21295-RG8506A-GR-P1 21287-4 21286-1 21295-GR8506A-GR- P2 21287-4 21286-2 21295-GR8506A-GS-P1 21287-2 21286-1 21295-GXInstruction ManualICAO Approach FixtureFigure 1: Exploded View of FixtureInstruction ManualICAO Approach FixtureFigure 2: Isometric View of FixtureInstruction ManualICAO Approach FixtureFigure 3: Top View of FixtureFigure 4: Side View of FixtureInstruction ManualICAO Approach FixtureFigure 5: Bottom View of FixtureInstruction ManualICAO Approach FixtureFEEDTHRU REPLACEMENT INSTRUCTIONS1.Torque item 3 to 30 in-lbs2.Coat items 3, 4, 5 and lead terminals, on the outside of thecover only, with item 10. Allow to cure for 8 hours.3.Encapsulate feedthru assembly with Emerson & Cummingscatalyst 9 / resin 2651 or Mavidon catalyst 4195B / resin4195A. Allow to cure per manufacturer’s instructions. Thewire leads exit the bottom of the inner cover, not the sides. Atemporary dam must be placed across the inner cover side tohold the epoxy in place as it cures.NOT SHOWN A/R A/R10048-63RTV 116NOT SHOWN1221038LEAD ASSEMBLY, L-823 82410035-33-010O-RING72410030-100WASHER, SHOULDER,INSULATING62410030-108WASHER, FLAT, INSULATING54810030-57WASHER, FLAT, SS, #1/442420017LEAD LUG32410K04-025D NUT, HEX, SS, #1/4-2022411A12-016D LOCKWASHER, SPLIT, #8, SS12410A06-016D10SCREW, PAN HD, #8-32X5/16, SS ITEM NO.21286-1 QTY21286-2 QTY PART NUMBER DESCRIPTIONFigure 6: Feedthru detail。
机场除冰雪总体要求
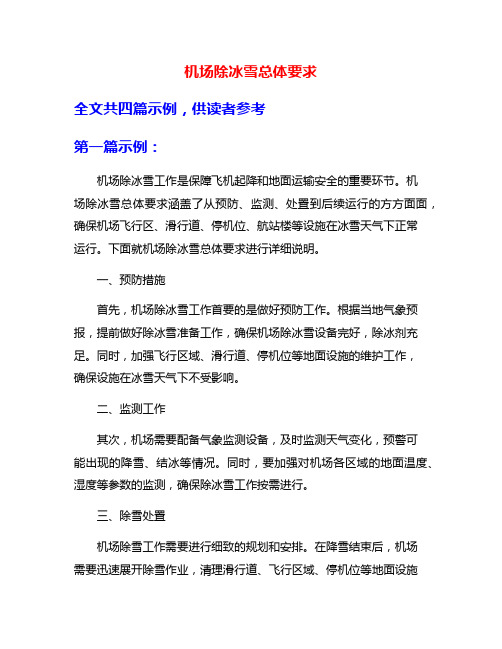
机场除冰雪总体要求全文共四篇示例,供读者参考第一篇示例:机场除冰雪工作是保障飞机起降和地面运输安全的重要环节。
机场除冰雪总体要求涵盖了从预防、监测、处置到后续运行的方方面面,确保机场飞行区、滑行道、停机位、航站楼等设施在冰雪天气下正常运行。
下面就机场除冰雪总体要求进行详细说明。
一、预防措施首先,机场除冰雪工作首要的是做好预防工作。
根据当地气象预报,提前做好除冰雪准备工作,确保机场除冰雪设备完好,除冰剂充足。
同时,加强飞行区域、滑行道、停机位等地面设施的维护工作,确保设施在冰雪天气下不受影响。
二、监测工作其次,机场需要配备气象监测设备,及时监测天气变化,预警可能出现的降雪、结冰等情况。
同时,要加强对机场各区域的地面温度、湿度等参数的监测,确保除冰雪工作按需进行。
三、除雪处置机场除雪工作需要进行细致的规划和安排。
在降雪结束后,机场需要迅速展开除雪作业,清理滑行道、飞行区域、停机位等地面设施上的积雪,确保飞机起降和地面运输的正常进行。
同时,需要根据不同的情况选择合适的除雪设备和除雪方法,确保除雪工作高效、安全。
四、设备要求机场除冰雪工作需要配备适用的除雪设备,包括除冰车、喷雪机等。
这些设备需要定期进行维护和检查,确保在关键时刻能正常使用。
除雪设备的选型要满足机场除雪的实际需要,同时要考虑对环境的影响。
五、除冰剂要求除冰剂是机场除冰雪工作中不可缺少的一部分。
为了确保除冰工作的效果和安全性,机场需要采购质量可靠的除冰剂,并按照规定的比例进行配制和使用。
同时,需要注意除冰剂对环境的影响,尽量选择对环境友好的除冰剂。
六、培训要求除冰雪工作人员需要经过专业的培训,掌握除雪设备的操作技能和除冰剂的使用方法。
机场需要定期组织培训和演练,确保除雪人员具备应对突发情况的能力。
七、后续运行除雪工作结束后,机场需要及时清理除雪作业留下的垃圾、积雪,确保机场地面设施的清洁和安全。
同时,需要及时通知航空公司和相关单位机场除雪工作的情况,确保航班正常运行。
国际民航公约附件14第一章教材
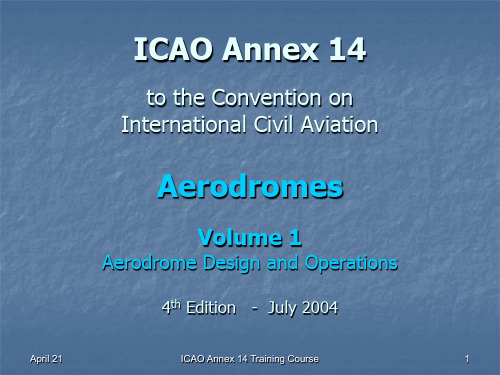
Who are you ? Where do you work? What is your job title? What are your main responsibilities? What do you hope to gain from this course?
April 21
13
ICAO Annex 14 Volume I Aerodrome Design and Operations
PUBLICATIONS
(related to the specifications of this Annex)
Stolport Manual (Doc 9150) World Geodetic System - 1984 (WGS-84) Manual (Doc
Volume II - Design Certification and Continuing Airworthiness
Guidance on the Balanced Approach to Aircraft Noise Management (Doc 9829)
April 21
ICAO Annex 14 Training Course
Standards and Recommended Practices (SARPs) for Aerodromes were first adopted by the Council on 29 May 1951 pursuant to the provisions of Article 37 of the Convention on International Civil Aviation (Chicago 1944) and designated as Annex 14 to the Convention.
- 1、下载文档前请自行甄别文档内容的完整性,平台不提供额外的编辑、内容补充、找答案等附加服务。
- 2、"仅部分预览"的文档,不可在线预览部分如存在完整性等问题,可反馈申请退款(可完整预览的文档不适用该条件!)。
- 3、如文档侵犯您的权益,请联系客服反馈,我们会尽快为您处理(人工客服工作时间:9:00-18:30)。
n Associates, Inc
International Federation of Helicopter Associations
IFHA
ICAO ‘Annex 14 Update’ Workshop – HAI HeliExpo 2010
HELIPORT/HELIDECK DESIGN
ICAO ‘ANNEX 14 UPDATE’
(ICAO Annex 14 Volume II –Heliports)
WORKSHOP
Dr John W. Leverton
IFHA Representative to ICAO Aerodrome Panel HAI Heliport Design Focal Point Vice President Infrastructure Development, AHS
*********************** FAA Advisory Circular (AC) 150-5390-2B (2004)
= AC-2B
ICAO ‘Annex 14 Update’ Workshop – HAI HeliExpo 2010
Leverton Associates, Inc
Leverton Associates, Inc
HELIPORT/HELIDECK DESIGN
ICAO ‘ANNEX 14 UPDATE’
(ICAO Annex 14 Volume II –Heliports)
WORKSHOP # 1
Dr John W. Leverton
IFHA Representative to ICAO Aerodrome Panel HAI Heliport Design Focal Point Vice President Infrastructure Development, AHS
ICAO „State Letter‟ ** issued with „Tranche 1 changes‟ August 2007.
** State Letter included also changes to Annex 14 Volume 1 related to Aerodromes
ICAO ‘Annex 14 Update’ Workshop – HAI HeliExpo 2010
Annex 14 Future Work
ICAO agreed –at AP1 (Dec 2006)- for Annex 14 to be reformatted to make it easier to use – the existing and „new‟ text will be grouped in the following Chapters:Chapter 1. General Chapter 2. Surface-level Heliports Chapter 3. Elevated Heliports Chapter 4. Instrument Heliports Chapter 5. Helidecks Chapter 6. Shipboard Heliports and Winching Areas
ICAO ‘Annex 14 Update’ Workshop – HAI HeliExpo 2010
Leverton Associates, Inc
PRESENTATION TERMINLOGY
ICAO ANNEX 14: VOLUME II – HELIPORTS
New ‘Tranche 1’ Annex 14 = THIRD EDITION – JULY 2009 2004 Annex 14 = SECOND EDITION – Amendment 3 – July 2004
•Chapter 6: Heliport Services (Fire Fighting) – being addressed by separate RFFWG
ICAO ‘Annex 14 Update’ Workshop – HAI HeliExpo 2010
Leverton Associates, Inc
•Chapter 5: Visual Aids (Markings & Lighting) - minor changes issued in tranche 1 – changes to ‘markings’ to be issued as part of tranche 2, lighting 40 % complete – still being ‘worked’ – changes to ‘lights’ to be made post-tranche 2.
ICAO ‘Annex 14 Update’ Workshop – HAI HeliExpo 2010
Leverton Associates, Inc
CURRENT STATUS
Updated Annex 14 Volume II – Heliports (Tranche 1)
.......... Issue July 2009:
HDWG/2 – June 2006
First set of changes (Tranche 1) agreed at HDWG/2 (June 2006) – Changes endorsed by the „WG of the Whole‟ at WGoTH/3 meeting (August 2006) Approved by Aerodrome Panel at AP/1 December 2006. Tranche 1 Changes approved by ICAO ANC May 2007
Leverton Associates, Inc
ANNEX 14 Vol II WORKSHOP
Comments based on my involvement as the IFHA Representative to the ICAO Aerodrome Panel (AP), the Heliport Design Working Group (HDWG), the Visual Aids Working Group (VAWG) and associated Sub-groups …. …. and Rapporteur of the HDWG Visual Aids Sub-group (VASG). COMMENTS SHOULD NOT BE TAKEN AS STATEMENT OF ACTUAL ICAO POLICY OR WHAT WILL APPEAR IN THE NEW ‘TRANCHE 2’ ICAO ANNEX 14 VOLUME II - HELIPORT DESIGN TO BE ISSUED IN 2011 (or 2012!!)
Annex 14 UPDATE PROGRESS
HDSG formed late 2003
HDSG/1 Meeting May 2004 [AP formed Dec 2004]
HDWG/1 Meeting June 2005 [Agreed changes should be addressed in 2 parts – tranche 1 and 2]
Leverton Associates, Inc
Annex 14 STATUS
•Chapter 1: General (Definition) - main changes completed in ‘tranche 1’ - addition changes to be made in tranche 2 to cover ‘floating (pontoon) heliports’ etc., and to ensure requirements for VFM (VFR) heliports cover also heliports where an instrument (Point in Space/PinS) approach is used. •Chapter 2: Heliport Data – tranche 2 minor changes. •Chapter 3: Physical Characteristics – main changes completed in ‘tranche 1’: some additional changes and new term ‘FATO/TLOF’ for elevated heliports and helidecks to be made in tranche 2. •Chapter 4: Obstacle Restriction and Removal (Airspace) : Study completed for VFM (VFR) heliports - to be issued as part of tranche 2.
ICAO ‘Annex 14 Update’ Workshop – HAI HeliExpo 2010
Leverton Associates, Inc
ICAO ANNEX 14 Vol II HELIPORTS
(Heliport/Helideck/Shipboard Heliport Design)
................applicability date 19 November 2009!
Note: Some ‘helideck requirements’ have later applicability date of 2012
HDWG now finalizing ‘Tranche 2’ Changes ICAO AP/2 to address ‘tranche 2’ changes, originally planned for 2009, now October 2010. HDWG planning to ‘start work’ on updating the ICAO Heliport Design Manual (Doc 9261) in 3rd Quarter of 2010 ? – this is of major importance since Manual will detail how to apply ‘Annex 14 Volume II’ ICAO ‘Annex 14 Update’ Workshop – HAI HeliExpo 2010