风电塔筒制造工艺
风电塔筒制作技术及质量控制分析
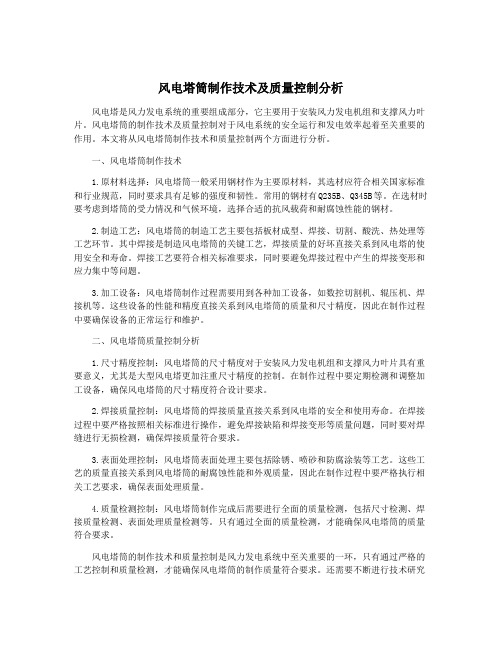
风电塔筒制作技术及质量控制分析风电塔是风力发电系统的重要组成部分,它主要用于安装风力发电机组和支撑风力叶片。
风电塔筒的制作技术及质量控制对于风电系统的安全运行和发电效率起着至关重要的作用。
本文将从风电塔筒制作技术和质量控制两个方面进行分析。
一、风电塔筒制作技术1.原材料选择:风电塔筒一般采用钢材作为主要原材料,其选材应符合相关国家标准和行业规范,同时要求具有足够的强度和韧性。
常用的钢材有Q235B、Q345B等。
在选材时要考虑到塔筒的受力情况和气候环境,选择合适的抗风载荷和耐腐蚀性能的钢材。
2.制造工艺:风电塔筒的制造工艺主要包括板材成型、焊接、切割、酸洗、热处理等工艺环节。
其中焊接是制造风电塔筒的关键工艺,焊接质量的好坏直接关系到风电塔的使用安全和寿命。
焊接工艺要符合相关标准要求,同时要避免焊接过程中产生的焊接变形和应力集中等问题。
3.加工设备:风电塔筒制作过程需要用到各种加工设备,如数控切割机、辊压机、焊接机等。
这些设备的性能和精度直接关系到风电塔筒的质量和尺寸精度,因此在制作过程中要确保设备的正常运行和维护。
二、风电塔筒质量控制分析1.尺寸精度控制:风电塔筒的尺寸精度对于安装风力发电机组和支撑风力叶片具有重要意义,尤其是大型风电塔更加注重尺寸精度的控制。
在制作过程中要定期检测和调整加工设备,确保风电塔筒的尺寸精度符合设计要求。
2.焊接质量控制:风电塔筒的焊接质量直接关系到风电塔的安全和使用寿命。
在焊接过程中要严格按照相关标准进行操作,避免焊接缺陷和焊接变形等质量问题,同时要对焊缝进行无损检测,确保焊接质量符合要求。
3.表面处理控制:风电塔筒表面处理主要包括除锈、喷砂和防腐涂装等工艺。
这些工艺的质量直接关系到风电塔筒的耐腐蚀性能和外观质量,因此在制作过程中要严格执行相关工艺要求,确保表面处理质量。
4.质量检测控制:风电塔筒制作完成后需要进行全面的质量检测,包括尺寸检测、焊接质量检测、表面处理质量检测等。
风电塔筒项目制作工艺及检验标准

GY-01-3 GY-01-4
GY-01-5 尺寸的检验
1、用盘尺分别测量大弦、小弦误差±2
2、用盘尺分别测量两对角线误差±2
3、宽度误差±1
4、测量板材边缘的切割的垂直度90±2°
钢印的标识
1、标识用的钢印必须为无应力钢印,高度最小10mm
2、编号正确、清晰,标识内容详见标识工艺
TZ17-07
ID-塔段-塔节号
δ=xx(板材厚度)
QXXX(材质号)
xxxxxxxxxx(钢板炉批号)
ID——表示塔架序列号1、2、3 (20)
塔段——从下到上S1、S2、S3、T
塔节号——表示该塔段第几节钢板1、2、3……n
经检验合格,填制工艺流程卡后,产品方可进入下一道工序
数控火焰切割机
行车吊具
火焰切割手把
盘尺米尺
钢印铁锤
焊缝量规
下料班组塔筒(基础)制造工艺阶段:坡口打磨(GY-02)。
风电塔筒制作技术及质量控制分析
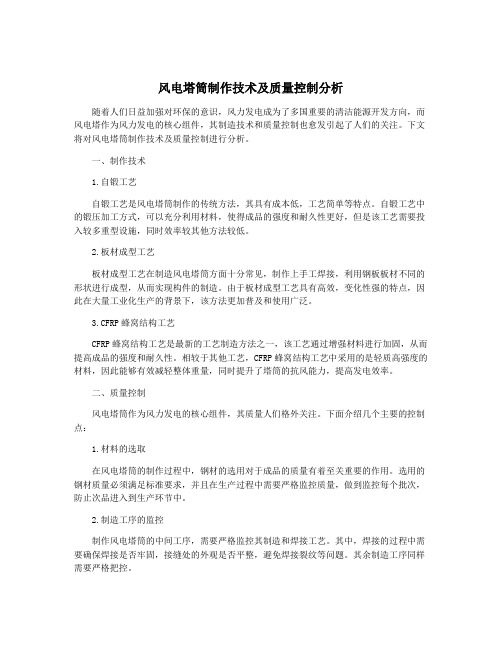
风电塔筒制作技术及质量控制分析随着人们日益加强对环保的意识,风力发电成为了多国重要的清洁能源开发方向,而风电塔作为风力发电的核心组件,其制造技术和质量控制也愈发引起了人们的关注。
下文将对风电塔筒制作技术及质量控制进行分析。
一、制作技术1.自锻工艺自锻工艺是风电塔筒制作的传统方法,其具有成本低,工艺简单等特点。
自锻工艺中的锻压加工方式,可以充分利用材料,使得成品的强度和耐久性更好,但是该工艺需要投入较多重型设施,同时效率较其他方法较低。
2.板材成型工艺板材成型工艺在制造风电塔筒方面十分常见,制作上手工焊接,利用钢板板材不同的形状进行成型,从而实现构件的制造。
由于板材成型工艺具有高效,变化性强的特点,因此在大量工业化生产的背景下,该方法更加普及和使用广泛。
3.CFRP蜂窝结构工艺CFRP蜂窝结构工艺是最新的工艺制造方法之一,该工艺通过增强材料进行加固,从而提高成品的强度和耐久性。
相较于其他工艺,CFRP蜂窝结构工艺中采用的是轻质高强度的材料,因此能够有效减轻整体重量,同时提升了塔筒的抗风能力,提高发电效率。
二、质量控制风电塔筒作为风力发电的核心组件,其质量人们格外关注。
下面介绍几个主要的控制点:1.材料的选取在风电塔筒的制作过程中,钢材的选用对于成品的质量有着至关重要的作用。
选用的钢材质量必须满足标准要求,并且在生产过程中需要严格监控质量,做到监控每个批次,防止次品进入到生产环节中。
2.制造工序的监控制作风电塔筒的中间工序,需要严格监控其制造和焊接工艺。
其中,焊接的过程中需要确保焊接是否牢固,接缝处的外观是否平整,避免焊接裂纹等问题。
其余制造工序同样需要严格把控。
3.检测过程的监测检测过程是保证风电塔的质量的重要环节,包括材料、制造工序、整体产品的检测。
其目的在于对成品加以全面的检验,防止次品进入到市场,同时也有利于对生产工艺的优化改进。
综上所述,风电塔筒的制作技术和质量控制是影响风力发电质量的关键因素。
风力发电机塔筒的加工工艺流程
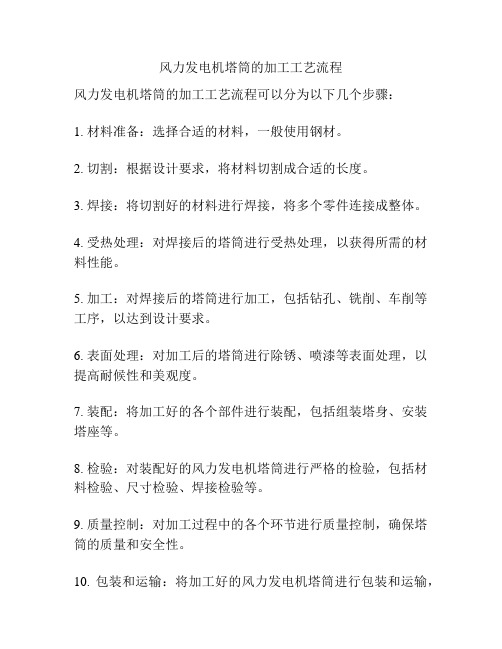
风力发电机塔筒的加工工艺流程
风力发电机塔筒的加工工艺流程可以分为以下几个步骤:
1. 材料准备:选择合适的材料,一般使用钢材。
2. 切割:根据设计要求,将材料切割成合适的长度。
3. 焊接:将切割好的材料进行焊接,将多个零件连接成整体。
4. 受热处理:对焊接后的塔筒进行受热处理,以获得所需的材料性能。
5. 加工:对焊接后的塔筒进行加工,包括钻孔、铣削、车削等工序,以达到设计要求。
6. 表面处理:对加工后的塔筒进行除锈、喷漆等表面处理,以提高耐候性和美观度。
7. 装配:将加工好的各个部件进行装配,包括组装塔身、安装塔座等。
8. 检验:对装配好的风力发电机塔筒进行严格的检验,包括材料检验、尺寸检验、焊接检验等。
9. 质量控制:对加工过程中的各个环节进行质量控制,确保塔筒的质量和安全性。
10. 包装和运输:将加工好的风力发电机塔筒进行包装和运输,
以确保在运输过程中不受损坏。
以上是风力发电机塔筒的加工工艺流程的一般步骤,具体的流程可能会因制造厂家和项目要求而略有差异。
风电塔筒制作技术及质量控制分析

风电塔筒制作技术及质量控制分析风电塔筒是风力发电机组的重要组成部分,是风力发电机组的“身体”,承担着支撑风力发电机组及其叶轮和发电设备的重要功能。
风电塔筒的制作技术和质量控制至关重要。
本文将对风电塔筒的制作技术和质量控制进行详细分析。
一、风电塔筒的制作技术1. 材料选择:风电塔筒通常采用钢结构,所选材料应具备良好的焊接性能、抗风压能力和耐腐蚀性能。
常见的材料有Q345B钢和Q235B钢等,其化学成分和力学性能需要符合国家标准。
2. 切割和成型:风电塔筒的制作通常从钢板开始,首先对钢板进行切割和成型。
切割采用数控火焰切割或数控等离子切割,成型则采用数控卷板机等设备。
切割和成型的精度对风电塔筒的装配和使用性能至关重要。
3. 焊接工艺:风电塔筒的制作需要进行大量的焊接工艺。
常见的焊接方式包括埋弧焊、气体保护焊等。
焊接工艺需要严格控制焊接参数,确保焊缝的质量和牢固度。
4. 表面处理:风电塔筒的表面通常需要进行除锈和喷涂处理,以提高其耐腐蚀性能和美观度。
除锈采用砂轮或喷砂等方式,喷涂采用环氧底漆和聚氨酯面漆等。
5. 质检和验收:风电塔筒制作完成后,需要进行严格的质检和验收。
检测项目包括尺寸精度、焊缝质量、表面质量等。
1. 制作过程中的质量控制:风电塔筒的制作过程中需要进行全程质量控制,包括材料的把关、生产工艺的控制、焊接质量的监控等。
对关键工艺节点需要进行质量记录和追溯,确保每一道工序的质量可控。
2. 合格供应商的选择:风电塔筒的制作需要大量的钢材供应,因此合格的钢材供应商是质量控制的关键。
需对供应商进行严格的审核和评估,确保其产品质量达标。
3. 质检和验收:制作完成的风电塔筒需要进行严格的质检和验收。
除了常规的尺寸、焊缝和表面质量检测外,还需要进行安装孔位的检测和校准,以确保风电塔筒在安装时能够满足设计要求。
4. 质量管理体系:风电塔筒的制作企业需要建立健全的质量管理体系,包括质量管理手册、质量控制程序和质量记录等文件,以确保每一台风电塔筒的质量可控和可追溯。
风电塔筒制作技术及质量控制分析
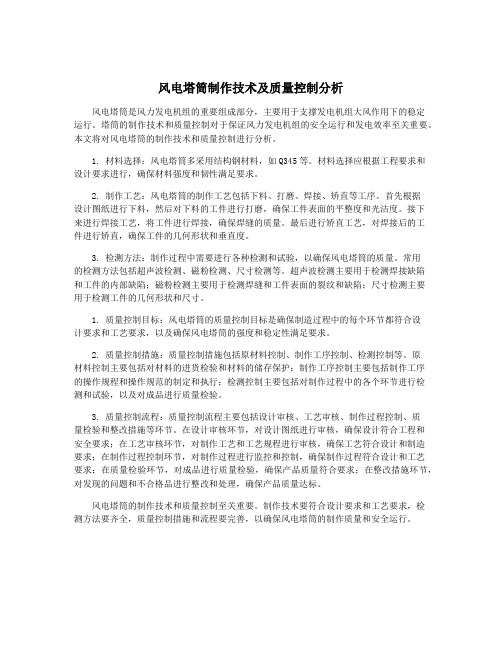
风电塔筒制作技术及质量控制分析风电塔筒是风力发电机组的重要组成部分,主要用于支撑发电机组大风作用下的稳定运行。
塔筒的制作技术和质量控制对于保证风力发电机组的安全运行和发电效率至关重要。
本文将对风电塔筒的制作技术和质量控制进行分析。
1. 材料选择:风电塔筒多采用结构钢材料,如Q345等。
材料选择应根据工程要求和设计要求进行,确保材料强度和韧性满足要求。
2. 制作工艺:风电塔筒的制作工艺包括下料、打磨、焊接、矫直等工序。
首先根据设计图纸进行下料,然后对下料的工件进行打磨,确保工件表面的平整度和光洁度。
接下来进行焊接工艺,将工件进行焊接,确保焊缝的质量。
最后进行矫直工艺,对焊接后的工件进行矫直,确保工件的几何形状和垂直度。
3. 检测方法:制作过程中需要进行各种检测和试验,以确保风电塔筒的质量。
常用的检测方法包括超声波检测、磁粉检测、尺寸检测等。
超声波检测主要用于检测焊接缺陷和工件的内部缺陷;磁粉检测主要用于检测焊缝和工件表面的裂纹和缺陷;尺寸检测主要用于检测工件的几何形状和尺寸。
1. 质量控制目标:风电塔筒的质量控制目标是确保制造过程中的每个环节都符合设计要求和工艺要求,以及确保风电塔筒的强度和稳定性满足要求。
2. 质量控制措施:质量控制措施包括原材料控制、制作工序控制、检测控制等。
原材料控制主要包括对材料的进货检验和材料的储存保护;制作工序控制主要包括制作工序的操作规程和操作规范的制定和执行;检测控制主要包括对制作过程中的各个环节进行检测和试验,以及对成品进行质量检验。
3. 质量控制流程:质量控制流程主要包括设计审核、工艺审核、制作过程控制、质量检验和整改措施等环节。
在设计审核环节,对设计图纸进行审核,确保设计符合工程和安全要求;在工艺审核环节,对制作工艺和工艺规程进行审核,确保工艺符合设计和制造要求;在制作过程控制环节,对制作过程进行监控和控制,确保制作过程符合设计和工艺要求;在质量检验环节,对成品进行质量检验,确保产品质量符合要求;在整改措施环节,对发现的问题和不合格品进行整改和处理,确保产品质量达标。
风电塔筒制作技术及质量控制分析
风电塔筒制作技术及质量控制分析风能是一种无限可持续的能源资源,风电塔塔筒作为风力发电装置的重要组成部分,其制作技术和质量控制直接关系到风电塔的安全性和发电效率。
本文将就风电塔筒制作技术及质量控制进行深入分析。
一、风电塔筒制作技术1. 材料选择风电塔筒一般采用碳素钢或合金钢,其中碳素钢主要用于塔筒底部和机舱连接部分,而合金钢则用于塔筒的主体部分。
在选择材料时要考虑到塔筒的承载能力、安全性和使用寿命,同时还要考虑成本和加工难度,因此在选择材料时需要进行严格的考量和分析。
2. 结构设计风电塔筒的结构设计应满足强度、稳定性和刚度等方面的要求,同时还要考虑到制作工艺的可行性和加工难度。
为了保证风电塔的安全性和稳定性,结构设计需要经过详细的计算和模拟分析,确保设计方案的合理性和可行性。
3. 制作工艺风电塔筒的制作工艺一般包括板材切割、焊接、涂漆等多个环节。
在板材切割方面,需要保证尺寸的精确度和表面质量,以满足后续工艺的要求;在焊接方面,需要注意焊缝的质量和工艺参数的选择,确保焊接质量和强度;在涂漆方面,需要选择合适的防腐蚀涂料和施工工艺,以延长塔筒的使用寿命。
4. 质量控制风电塔筒的质量控制涉及到每一个制作环节,需要对原材料进行严格的检验和把关,同时在制作过程中需要进行多道工序的质量检验,确保每一个环节的质量合格,最终确保风电塔筒的整体质量达标。
二、风电塔筒质量控制分析1. 材料质量控制风电塔筒的材料质量控制是保证风电塔安全稳定运行的基础。
在材料采购过程中,需要选择正规的供应商并对材料进行严格的质量把关,确保符合设计要求和标准要求。
在接收材料时需要进行外观检验和化学成分分析,以保证材料的质量达标。
3. 质量管理体系风电塔筒的质量控制需要建立完善的质量管理体系,确保质量控制的全程跟踪和管理。
在制作过程中需要对每一个关键环节进行记录和归档,以便后期的质量反馴和问题分析。
同时需要建立质量检验和反馈机制,对于出现的质量问题要及时处理和解决,以确保风电塔筒的整体质量达标。
风电塔筒制造工艺课件
目录1.塔筒制造工艺流程图2.制造工艺3.塔架防腐4.吊装5.运输一、塔架制造工艺流程图(一)基础段工艺流程图1.基础筒节:H原材料入厂检验→R材料复验→R数控切割下料(包括开孔)→尺寸检验→R加工坡口→卷圆→R校圆→100%UT检测。
2.基础下法兰:H原材料入厂检验→R材料复验→R数控切割下料→R法兰拼缝焊接→H拼缝100%UT检测→将拼缝打磨至与母材齐平→热校平(校平后不平度≤2mm)→H拼缝再次100%UT检测→加工钻孔→与筒节焊接→H角焊缝100%UT检测→校平(校平后不平度≤3mm)→角焊缝100%磁粉检测。
3.基础上法兰:外协成品法兰→H入厂检验及试件复验→与筒节组焊→100%UT 检测→H平面检测。
4.基础段组装:基础上法兰与筒节部件组焊→100UT%检测→H平面度检测→划好分度线组焊挂点→整体检验→喷砂→防腐处理→包装发运。
(二)塔架制造工艺流程图1.筒节:H原材料入厂检验→R材料复验→钢板预处理→R数控切割下料→尺寸检验→R加工坡口→卷圆→R组焊纵缝→R校圆→100%UT检测。
2.顶法兰:成品法兰→H入厂检验及试件复验→与筒节组焊→100%UT检测→平面度检测→二次加工法兰上表面(平面度超标者)。
3.其余法兰:成品法兰→H入厂检验及试件复验→与筒节组焊→100%UT检测→平面度检测。
4.塔架组装:各筒节及法兰短节组对→R检验→R焊接→100%UT检测→R检验→H划出内件位置线→H检验→组焊内件→H防腐处理→内件装配→包装发运。
二、塔架制造工艺(一)工艺要求:1.焊接要求(1)筒体纵缝、平板拼接及焊接试板,均应设置引、收弧板。
焊件装配尽量避免强行组装及防止焊缝裂纹和减少内应力,焊件的装配质量经检验合格后方许进行焊接。
(2)塔架筒节纵缝及对接环缝应采用埋弧自动焊,应采取双面焊接,内壁坡口焊接完毕后,外壁清根露出焊缝坡口金属,清除杂质后再焊接,按相同要求制作筒体纵缝焊接试板,产品焊接试板的厚度范围应是所代表的工艺评定覆盖的产品厚度范围,在距筒体、法兰及门框焊约50mm处打上焊工钢印,要求涂上防腐层也能清晰看到;(3)筒节纵环焊缝不允许有裂纹、夹渣、气孔、未焊透、未融合及深度>0.5mm 的咬边等缺陷,焊接接头的焊缝余高h应小于焊缝宽度10%;(4)筒节用料不允许拼接,相邻筒节纵焊缝应尽量错开180度,筒节纵焊缝置于法兰两相邻两螺栓孔之间。
风电塔筒制作技术及质量控制分析
风电塔筒制作技术及质量控制分析
1.材料选择:风电塔筒主要采用焊接钢管,材料需要具备高强度、耐腐蚀、耐疲劳等性能。
常用材料包括Q345B、Q345D、Q550、Q690等等。
2.制作工艺:首先需要对材料进行切割、焊接成设定长度的钢管,然后根据设计要求进行弯曲、校正,接着进行内外表面处理,包括除锈、喷涂等工艺。
最后进行汇焊、喷涂标识等工序。
3.制作设备:风电塔筒的制作需要大型的自动焊机、钢管弯管机、毛刺清除机等设备来保证制作效率和质量。
1.尺寸控制:风电塔筒是由多个钢管焊接而成的,需要保证尺寸的一致性,否则会影响风电机组运行稳定性。
因此,在制作过程中需要进行精准尺寸的检测和校正。
2.焊接质量控制:风电塔筒需要经过多道焊接工艺,焊接质量的好坏直接关系到塔筒的承载能力和寿命。
需要对焊接过程进行严格控制,包括焊材的选择、焊接温度、焊接速度等。
3.表面处理:风电塔筒需要进行表面处理,以保证塔筒防腐、防锈、减少风载对塔筒的损害等。
需要对表面处理工艺进行严格监控,保证表面处理的质量和效果。
4.非破坏性检测:通过超声波、射线及磁粉探伤等非破坏性检测方法,可以对风电塔筒进行全面的检测,检查焊接质量、毛刺、油漆等方面的质量问题。
总之,风电塔筒作为风电机组的核心部分,需要保证制作技术的可靠性和质量控制的有效性。
对于风电企业来说,需要完善现有的质量控制系统,不断提升技术水平和制造能力,以确保风电机组工作的安全可靠、运行稳定。
风电塔筒通用制造工艺介绍
风电塔筒通用制造工艺介绍1. 引言风电塔筒是风能发电机组的重要组成部分,承载着风机和风力发电机的重量,并为其提供稳定的支撑结构。
本文将介绍风电塔筒的通用制造工艺,包括材料选择、焊接工艺、机械加工等方面。
2. 材料选择风电塔筒一般采用高强度低合金钢作为材料,以满足对强度和耐久性的要求。
常用的材料包括Q345(国内材料)和ASTM A572等(国际材料)。
材料的选择应考虑强度、焊接性能、耐久性、成本等因素。
在选择材料时,还需考虑到生产和加工的可行性,以确保生产效率和质量。
3. 制造工艺3.1 塔筒板材切割首先,根据风电塔筒的设计图纸,将所选材料切割成合适的尺寸。
常用的切割方法包括等离子切割、火焰切割和激光切割等,根据具体情况选择合适的切割工艺。
3.2 胶接焊接将切割好的板材进行弯曲成筒状,并使用胶接焊接工艺将板材的边缘连接在一起。
胶接焊接需要保证焊缝的质量和可靠性,一般采用自动化焊接机器人进行操作,确保焊缝的一致性和工艺稳定性。
3.3 筒体整形经过焊接后,需要对筒体进行整形加工,以达到设计要求的形状和尺寸。
常用的整形加工方法包括辊压、碾压和拉伸等。
整形加工过程中需要注意保证筒体的强度和形状的一致性。
3.4 焊缝焊接对筒体进行最终的焊缝焊接,以提高连接的强度和稳定性。
焊缝焊接需要采用合适的焊接工艺,保证焊接质量和机械性能。
常用的焊接方法包括埋弧焊和气体保护焊等。
3.5 表面处理对焊接完成的风电塔筒进行表面处理,包括除锈、喷涂和防腐等工艺。
表面处理可以提高风电塔筒的耐久性和外观质量,延长使用寿命。
3.6 附件安装最后,将所需的附件如登梯、平台等安装在风电塔筒上,以满足安全和操作的需要。
安装附件需要考虑结构的牢固性和连接的可靠性。
4. 质量控制在风电塔筒的制造过程中,需进行严格的质量控制,以保证产品的质量和安全性。
4.1 材料检测在原材料采购时,需进行材料的化学成分和力学性能检测,确保选用的材料符合要求。
- 1、下载文档前请自行甄别文档内容的完整性,平台不提供额外的编辑、内容补充、找答案等附加服务。
- 2、"仅部分预览"的文档,不可在线预览部分如存在完整性等问题,可反馈申请退款(可完整预览的文档不适用该条件!)。
- 3、如文档侵犯您的权益,请联系客服反馈,我们会尽快为您处理(人工客服工作时间:9:00-18:30)。
例放出实样:当构件较大时可绘制下料图。 3,大样检查与施工图未尽尺寸的获取
1)施工图没有注明和无法注明的尺寸与角度,应在放样时取得。 2)大样完成后应由有矣技术人员和貭检人员认真检查。 4,号料 1)下料规格的合理排列,也就是说,在需要切割的每一张钢板上 如何合理安排所用规格,使之不剩料边、料头,尽量提高材料的利用 率。下料工将同材貭、同厚度的用料,按宽度、长度、数量汇总,作 出排板图,套裁切割后再用油漆写明图号。 5.切割 1)割口量与组对间隙的计萛
塔筒制作 门框制作 筒内附件制作
法兰心配件 复验
进料 切割 坡口加工
进料 切割 折弯
1
进料 切割 打磨
卷板 纵缝组对 纵缝焊接 无损检验 塔筒整园 检验
打磨 组对 焊接 矫正处理 检验
折弯 组对 焊接 检验
法兰与筒节组对
节与节组对
环缝焊接
环缝焊接
清除超标缺陷 处 理
处理
清除超标缺陷
无损检验
无损检验
3
4) 审图时发现的问题要及时向设计部门请示,经设计部门修改,不 得擅自修改。
5) 施工图低必须经专业人員认真审核后,下达生产车间,专业技术 人員汇同车间技术员对生产者进行技术交底。
2,放样设施及条 1)放样前,放样人員必须熟悉施工图和工艺要求,核对构件与构件
相应连接的几何尺寸及连接有否不当之处。 2)放样使用的钢下、弯展、盘尺,必须经计量单位检验合格,丈量
塔筒实际下料尺寸=名义尺寸﹢割口量﹢公差尺寸﹢焊接收
4
缩量。
2)割口量
表 2-1
自动切割量(mm)
板厚
3-5
6-10
12-20
22-28
30-40
切割量
1.5
2
2.5
3
3.5
3)焊接收缩量与加工余量的预留
焊缝收缩量以每米焊缝收缩 1-1.5mm 计萛,加在应下料的总长度内即
可。
4)需加工的构件,还应在下料尺寸基础上增加 20-30mm 的加工余
力
1
.
.
.
.
.
(MPa)
氧气耗 0.8
1.4
2.2 2.2-2.7 3.5-4.2 5.5-7.2
二, 风电塔筒制造工艺流程
塔筒制造中关键技术有三点: 1) 塔筒总长度一般在 55M-76M,直径在 4.2M-2.3M,制造中同轴度
不得大于 15 mm,整体塔筒共分四段 23 节,组对过程中必须保 证单节筒体端面平行度≤3 mm。 2) 由于同轴度要求严格,各段塔筒连接是采用内法兰连接,法兰 的焊接变形不得大于 3 mm。 3) 焊接貭量的控制,要滿足产品貭量要求。
风电塔筒制造工艺
一, 编制依据:
《钢结构工程施工貭量验收规范》GB50205-2001 《钢制压力容器制作标准》GB150-91 《建筑钢结构焊接规程》JGJ81-2002 《形状和位置公差及末注公差》GB/T1184-1996 《钢制压力容器无损检测》JB4730-94
DIN/EN 和 AWS 标准 本工艺适用于风电场风力发电塔架制造。
6
度(mm/
min)
后 拖 量 1-2.6 1.4-2.8 3-9
2-10 1-15 2-15
(mm)
3)气割的工艺参数
(1)预热火焰能率:火焰能率太大,会使切口上缘产生连续
珠状钢粒。甚至熔化成园角,增加表面粘渣。火焰能率主要决定于割
具和割咀的大小及切割速度快慢。割具及割咀的选择见表 2-3
(2)氧气压力:主要根据工件厚度确定切割氧压力大小,见
2)切割后拖量 气割时在同一条割纹上,沿切割方向的两点间最大距离叫后拖量(S), 如图 2-1 所示。
切割方向
S
图 2-1 割件越厚,切割速度越大,后拖量越大,将影响切口表面粗糙度。后 拖量试验数据见表 2-2。
表 2-2 气割后拖量试验数据
割件厚 5
10
15
20
25
50
度(mm)
切 割 速 500-800 400-600 400-550 300-500 200-400 200-400
割具型
G01-30
G01-100
号
割嘴号 1
2
3
1
2
3
码
7
割嘴孔 0.76
径(mm)
切割厚 3-10 10-20 20-30 10-25 25-30 30-100
度(mm)
氧气压 0.2
0.25
0.3
0.3
0.4
0.5
力
(MPa)
乙炔压 0.001-0. 0.001-0 0.001-0 0.001-0 0.001-0 0.001-0
表 2-4
(3)切割速度:火焰和熔渣以接近于垂直方向喷向工件的底
面为合适的切割速度。太慢或太快都会影响切口质量及破坏切割的连
续进行。
(4)割咀离工件表面的距离:预热火焰焰心般应离开工件表
面 2-4mm。
(5)割咀的倾斜角:当工件厚度小于 20 mm 时,割咀可向切
割方向倾斜 5-10°。
表 2-3 氧、乙炔射吸式割具型号及参数
量。
6.气割操作
1)气割的工作原理与基本条件,利用气体火焰的热能将工件切割
处预热到一定温度后喷出高速切割氧流,使其燃烧并放出热量,实现
切割的方法叫气割。
(1)气割过程的三亇阶段
预热:利用气体火焰将工件待切割处预热到该种金属材料的燃点
(低碳钢 1100°-1150°)。
燃烧:喷出的高速切割氧流,使己达燃点的金属在氧流中激烈燃
检验
检验
单段塔筒组对
内环缝焊接
外环缝焊接
无损检验
单段塔筒检验
附件组对焊接
清除超标缺陷
总体预组装
2
总体检验
分段喷砂
检验
分段喷漆
检验
附件安全检验
包装
发运
注:法兰外购。
三,塔筒下料工艺:
1,技术交底 1) 审图人员必须从设计总配置图开始,逐亇图号、逐亇部位核对, 找清相应安装或装配关糸,再核对外形几何尺寸、各部件之间尺 寸能否相亙衔接。之后,再逐亇核对各接点、孔距、孔位、孔径 等相关尺寸。 2) 认真核对施工图零件数量、单重和总重, 3) 审图时应将主要构件计萛出用科幅面,按每节塔筒展开料直接与 供应商订货。
烧。
吹渣:金属燃烧生成的氧化物被氧流吹掉,形成切口
(2)气割的基本条件:进行气割时要保证切口质量良好,应滿足三
亇条件:
5
繎点:金属的燃点应比熔点低,为保证切割口貭量光洁,气割 应在燃烧过程中进行,不应有熔化现象。
氧化物的燃点:氧化物的燃点应低于金属燃点,使得气割生成 的氧化物易于吹掉。
放热:金属在氧流中燃烧时能放出大量热量,该热量和预热火 焰一起对下层金属起着预热作用。