ASTM E 96 E 96M-2005 材料透湿性能的标准试验方法
防水透湿功能面料测试方法

2
高水压法
mm-H2O
测试面积 100cm ,加压速度为每分钟 600mm - H2O
2
低水压法
ISO 20811 DIN EN 20811
mm-H2O mm-H2O
测试面积 100cm ,9000 以下加压速度为 每分钟 600mm - H2O,9000 以上加压速度 为每分钟 10000mm - H2O
2
9000 分界 0 分界
透湿度测试
测试名称 JIS L 1099 A -1
单位 gm/m /24hrs
2
测试方式 CaCl2 法,温度 40 C ,相对湿度 90%,风速 0.8M /S
0
备注 正杯法
JIS L1099 B-1 ASTM E-96 B ASTM E-96 D ASTM E-96 E ASTM E-96 BW
0 0 0 0
0
0
倒杯法 正杯法 正杯法 正杯法 倒杯法
ASTM E-96 DW
gm/m /24hrs
2
水,温度 32 C ,相对湿度 50%;1995 年 版风速 2.8M /S, 2000 年版风速 0.02~ 0.3M /S
0
倒杯法
BS 7209-1990 ISO 11092-1993
% Pa.m /W 或 m .mber/W
gm/m /24hrs gm/m /24hrs gm/m /24hrs gm/m /24hrs gm/m /24hrs
2 2 2 2
2
醋酸钾法,水温 23 C ,室温 30 C 水,温度 23 C ,相对湿度 50% 水,温度 32 C ,相对湿度 50% CaCl2 法,温度 37.8 C ,相对湿度 90% 水,温度 23 C ,相对湿度 50%;1995 年 版风速 2.8M /S, 2000 年版风速 0.02~ 0.3M /S
吸湿速干型纺织品的概述及其测试方法
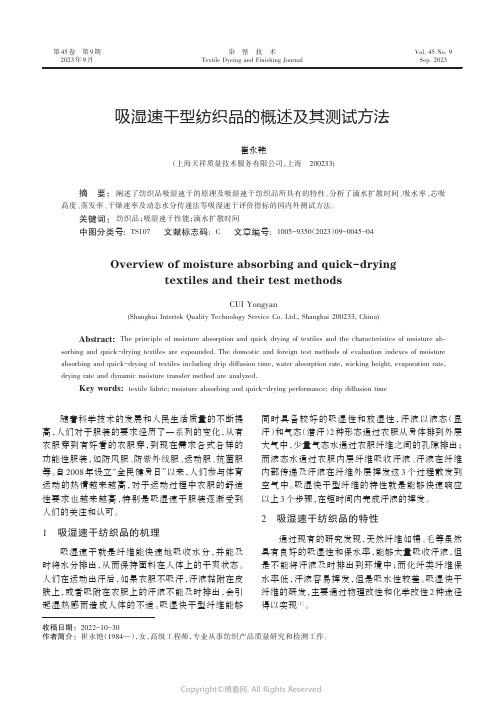
随着科学技术的发展和人民生活质量的不断提高,人们对于服装的要求经历了一系列的变化,从有衣服穿到有好看的衣服穿,到现在需求各式各样的功能性服装,如防风服、防紫外线服、运动服、抗菌服等。
自2008年设立“全民健身日”以来,人们参与体育运动的热情越来越高,对于运动过程中衣服的舒适性要求也越来越高,特别是吸湿速干服装逐渐受到人们的关注和认可。
1吸湿速干纺织品的机理吸湿速干就是纤维能快速地吸收水分,并能及时将水分排出,从而保持面料在人体上的干爽状态。
人们在运动出汗后,如果衣服不吸汗,汗液黏附在皮肤上,或者吸附在衣服上的汗液不能及时排出,会引起湿热感而造成人体的不适。
吸湿快干型纤维能够同时具备较好的吸湿性和放湿性,汗液以液态(显汗)和气态(潜汗)2种形态通过衣服从身体排到外层大气中,少量气态水通过衣服纤维之间的孔隙排出;而液态水通过衣服内层纤维吸收汗液、汗液在纤维内部传递及汗液在纤维外层挥发这3个过程散发到空气中。
吸湿快干型纤维的特性就是能够快速响应以上3个步骤,在短时间内完成汗液的挥发。
2吸湿速干纺织品的特性通过现有的研究发现,天然纤维如棉、毛等虽然具有良好的吸湿性和保水率,能够大量吸收汗液,但是不能将汗液及时排出到环境中;而化纤类纤维保水率低,汗液容易挥发,但是吸水性较差。
吸湿快干纤维的研发,主要通过物理改性和化学改性2种途径得以实现[1]。
吸湿速干型纺织品的概述及其测试方法摘要:阐述了纺织品吸湿速干的原理及吸湿速干纺织品所具有的特性。
分析了滴水扩散时间、吸水率、芯吸高度、蒸发率、干燥速率及动态水分传递法等吸湿速干评价指标的国内外测试方法。
关键词:纺织品;吸湿速干性能;滴水扩散时间中图分类号:TS107文献标志码:C 文章编号:1005-9350(2023)09-0045-04Abstract:The principle of moisture absorption and quick drying of textiles and the characteristics of moisture ab⁃sorbing and quick-drying textiles are expounded.The domestic and foreign test methods of evaluation indexes of moisture absorbing and quick-drying of textiles including drip diffusion time,water absorption rate,wicking height,evaporation rate,drying rate and dynamic moisture transfer method are analyzed.Key words:textile fabric;moisture absorbing and quick-drying performance;drip diffusion timeOverview of moisture absorbing and quick-drying textiles and their test methods收稿日期:2022-10-30作者简介:崔永艳(1984—),女,高级工程师,专业从事纺织产品质量研究和检测工作。
透湿性常识及测试方法

一、防水透湿性面料介绍当你去登山的时候,冷不丁会下雨,总不能撑着雨伞上山吧。
爬山又是一项非常消耗体力的运动,出大量的汗水,而山上的温度一般都很低,总不能把衣服脱掉吧。
那么,怎么样才能一下解决这类问题呢?实际上,人们很早就在研究这个问题了,那就是穿一件既防水又能透湿的衣服。
(平时人们常称它为透气织物,但不是空气中的气体,而是汗水蒸发出来的蒸汽)。
具体来讲,防水透湿织物是指水在一定压力下不浸入织物,而人体散发的汗液却能以水蒸气的形式通过织物传导到外界,从而避免汗液积聚冷凝在体表与织物之间以保持服装的舒适性,它是一种高技术、独具特色的功能性织物。
防水对于普通面料工作者来说并不是什么难题,关键是如何实现透湿。
下面,我们从防水透湿织物的种类来深入了解一下它。
一、通过纤维来实现透湿1、文泰尔织物。
最早的防水透湿织物是著名的文泰尔(Ventile)织物。
它是上世纪40年代由英国的Shirley 研究所设计的,选用埃及长绒棉的高支低捻度纯棉纱高密重平组织织物,最初主要用于第二次世界大战期间的英国空军飞行员的防寒抗浸服。
当织物干燥时,经纬纱线间的间隙较大,大约10微米,能提供高度透湿的结构;当雨或水淋织物时,棉纱膨胀,使得纱线间的间隙减至3~4 微米,这一闭孔机制同特殊的拒水整理相结合,保证织物不被雨水进一步渗透。
目前该类面料早已被其它防水透湿面料所取代。
2、Coolmax类面料。
杜邦、日本东丽等国际大公司研究的通过纤维内部制造出孔道的方式实现将汗水排出体外,也就是市场上的吸湿排汗面料。
该类纤维生产技术集中在这类国际大公司手上,价格相对较高,难以成为市场的主流。
二、通过涂层来实现透湿采用干法直接涂层、转移涂层、泡沫涂层、相位倒置或湿法涂层(凝固涂层)等工艺技术,将各种各样具有防水、透湿功能的涂层剂涂敷在织物的表面上,使织物表面孔隙被涂层剂封闭或减小到一定程度,从而得到防水性。
织物透湿性则通过涂层上经过特殊方法形成的微孔结构或涂层剂中的亲水基团与水分子作用,借助氢键和其它分子间力,在高湿度一侧吸附水分子,后传递到低温度一侧解析的作用来获得。
称重法透湿性测试标准ASTME96概要_上_

称重法透湿性测试标准ASTME96概要_上_技术检测材料中国包装报/2005年/04月/25日/第006版/称重法透湿性测试标准AST M E96概要(上)透湿性指标是包装材料的主要性能指标之一。
随着人们对产品防潮、防水重视程度的增加,阻湿性能更优的包装材料(即包装材料的透湿性更小)已经成为包装材料开发和使用的重点,近几年受到越来越多的关注。
包装商、材料供应商、产品制造商以及各检测机构纷纷引进透湿性检测设备,加强对包装材料透湿性能测试的力度。
现在市场上销售的透湿性测试仪的主要有称重法(Cup M ethod)透湿仪和传感器法透湿仪两大类。
AST M E96是称重法测试标准之一,它不但详细介绍了在其它标准中常见的增重法(Desiccant M ethod),而且还介绍了在透湿性测试领域中与增重法具有同等地位的减重法(Water Method)。
1、称重法概要称重法是一种独立的透湿性测试方法,测试原理简单明了:在规定的温度、相对湿度下,使试样两侧保持一定的水蒸气压差,测量透过试样的水蒸气量,计算透湿性相关参数。
称重法可以分为渗透进入透湿杯的增重法和渗透离开透湿杯的减重法两种方法,它们的测试原理相同。
The purpose of t hese tests is to obtain,by means of simple apparatus,reliable values of w ater vapor transfer through permeable and semipermeable materials,expressed in suitable units.These values are for use in design,manufacture,and market ing.(进行这些试验是为了通过简单的设备获得可信的可渗透材料以及半渗透材料的水蒸气透过值。
这些测试值将用于设计、生产以及商贸。
防水透湿面料的测试方法介绍

1,最常用的方法:ASTME96BW,美国材料试验学会标准,水蒸气倒杯法。
由于美国在这个行业一直处于领先地位,而且该国的市场也非常的大,该方法测试的数据也相对较高,ASTM标准自然而然成为最常用的方法。
现在大部分客户都采用该方法做检测。
测试原理如下:将被测试的织物覆盖在盛有蒸馏水的透湿杯上,固定后倒置,用精度为0.001g的顶加载天平称其重量,并将其安置在风洞排的位置上。
在杯子进入温度为23℃、相对湿度50%、风速2.5m/s的环境室进行称量之前,记录环境的温度和相对湿度。
每个杯子的重量和称量的时间都记录下来。
将3h,6h,9h,13h,23h,26h,30h时的重量记录下来,用WVT=24*△m/(s*t)公式计算水蒸气传递速度。
6个样品的平均值作为测试的结果,平均值乘以24转换为以g/m2*24h为单位的结果。
需要特别指出的是,ASTME96BW法有1995版和2000版,95版的测试条件不成熟,测试的相对数据较高,现在基本上采用的都是2000版。
2,测试结果最高的方法:JISL-1099B1、B2日本工业标准测试原理如下:用醋酸钾作为干燥剂。
将PTFE薄膜用橡皮环箍在塑料杯上制成一个水蒸气通透杯子。
在将薄膜包覆在杯子上之前,将足够的醋酸钾溶液放入到水蒸气通透杯子中,充满杯子容积约2/3。
从每一织物上取出20cm*30cm见方的3块样品。
每一样品放置在测试支撑架上。
所有涂层或层压织物用橡皮环固定在支撑架上,并且涂层或层压面朝外。
样品支撑系统的安装以能够漂浮在23℃水温的水槽中为准。
在薄膜朝上方向测试完测试杯质量(包括试样、干燥剂和薄膜)后,迅速将测试杯倒过来并放入样品支撑架中。
这一装配方式被放置在恒温30℃±2℃装置中。
15min后,将测试杯取出恒温装置,将其倒置过来并测定其重量。
水蒸气通透性按WVT=24*△m/(s*t)公式计算。
在透湿测试中,日本的干燥剂倒杯法似乎更收到生产商的青睐,因为它可以迅速在较小试样上进行测试,不需要对环境中的相对湿度进行控制,而且测试装置和耗材较为便宜。
透湿性常识及测试方法

一、防水透湿性面料介绍当你去登山的时候,冷不丁会下雨,总不能撑着雨伞上山吧。
爬山又是一项非常消耗体力的运动,出大量的汗水,而山上的温度一般都很低,总不能把衣服脱掉吧。
那么,怎么样才能一下解决这类问题呢?实际上,人们很早就在研究这个问题了,那就是穿一件既防水又能透湿的衣服。
(平时人们常称它为透气织物,但不是空气中的气体,而是汗水蒸发出来的蒸汽)。
具体来讲,防水透湿织物是指水在一定压力下不浸入织物,而人体散发的汗液却能以水蒸气的形式通过织物传导到外界,从而避免汗液积聚冷凝在体表与织物之间以保持服装的舒适性,它是一种高技术、独具特色的功能性织物。
防水对于普通面料工作者来说并不是什么难题,关键是如何实现透湿。
下面,我们从防水透湿织物的种类来深入了解一下它。
一、通过纤维来实现透湿1、文泰尔织物。
最早的防水透湿织物是著名的文泰尔(Ventile)织物。
它是上世纪40年代由英国的Shirley 研究所设计的,选用埃及长绒棉的高支低捻度纯棉纱高密重平组织织物,最初主要用于第二次世界大战期间的英国空军飞行员的防寒抗浸服。
当织物干燥时,经纬纱线间的间隙较大,大约10微米,能提供高度透湿的结构;当雨或水淋织物时,棉纱膨胀,使得纱线间的间隙减至3~4 微米,这一闭孔机制同特殊的拒水整理相结合,保证织物不被雨水进一步渗透。
目前该类面料早已被其它防水透湿面料所取代。
2、Coolmax类面料。
杜邦、日本东丽等国际大公司研究的通过纤维内部制造出孔道的方式实现将汗水排出体外,也就是市场上的吸湿排汗面料。
该类纤维生产技术集中在这类国际大公司手上,价格相对较高,难以成为市场的主流。
二、通过涂层来实现透湿采用干法直接涂层、转移涂层、泡沫涂层、相位倒置或湿法涂层(凝固涂层)等工艺技术,将各种各样具有防水、透湿功能的涂层剂涂敷在织物的表面上,使织物表面孔隙被涂层剂封闭或减小到一定程度,从而得到防水性。
织物透湿性则通过涂层上经过特殊方法形成的微孔结构或涂层剂中的亲水基团与水分子作用,借助氢键和其它分子间力,在高湿度一侧吸附水分子,后传递到低温度一侧解析的作用来获得。
功能性整理中有关防水、静水压、透湿、透气等名词的具体含义和测试方法
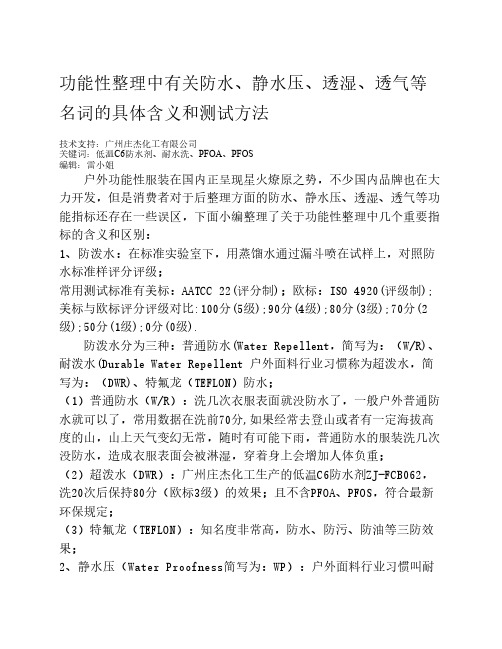
功能性整理中有关防水、静水压、透湿、透气等名词的具体含义和测试方法技术支持:广州庄杰化工有限公司关键词:低温C6防水剂、耐水洗、PFOA、PFOS编辑:雷小姐户外功能性服装在国内正呈现星火燎原之势,不少国内品牌也在大力开发,但是消费者对于后整理方面的防水、静水压、透湿、透气等功能指标还存在一些误区,下面小编整理了关于功能性整理中几个重要指标的含义和区别:1、防泼水:在标准实验室下,用蒸馏水通过漏斗喷在试样上,对照防水标准样评分评级;常用测试标准有美标:AATCC 22(评分制);欧标:ISO 4920(评级制);美标与欧标评分评级对比:100分(5级);90分(4级);80分(3级);70分(2级);50分(1级);0分(0级).防泼水分为三种:普通防水(Water Repellent,简写为:(W/R)、耐泼水(Durable Water Repellent 户外面料行业习惯称为超泼水,简写为:(DWR)、特氟龙(TEFLON)防水;(1)普通防水(W/R):洗几次衣服表面就没防水了,一般户外普通防水就可以了,常用数据在洗前70分,如果经常去登山或者有一定海拔高度的山,山上天气变幻无常,随时有可能下雨,普通防水的服装洗几次没防水,造成衣服表面会被淋湿,穿着身上会增加人体负重;(2)超泼水(DWR):广州庄杰化工生产的低温C6防水剂ZJ-FCB062,洗20次后保持80分(欧标3级)的效果;且不含PFOA、PFOS,符合最新环保规定;(3)特氟龙(TEFLON):知名度非常高,防水、防污、防油等三防效果;2、静水压(Water Proofness简写为:WP):户外面料行业习惯叫耐水压,单位用mmh2O表示,是指单位面积承受水压强力,在标准实验室条件下,织物承受蒸馏水往上喷的压力,并记录水压最大值,如耐水压5000mmh2o,即单位面积最大可承受5m压力而不会发生渗漏。
常用测试标准:美标AATCC 127;日标JIS L 1092B;欧标:IS0 811;耐水压测试分洗前和洗后测试两种方法:(1)洗前测:国产户外品牌一般测试洗前耐水压值,不测洗后值,涂层面料洗几次后耐水压值下降很大的,可能下降1000-3000 mmh2o左右;(2)洗后测:像THE NORTH FACE甚至有采用过水洗5-20次后再测耐水压方法,因多次洗后测试,耐水压值下降非常大,如涂层面料耐水压要求5次水洗后达到5000mmh2o,那么洗前最起码要到7-8000mmh2o以上;当然这种要求会导致成本更高!3、透湿度(Moisture Proofness简写为:MP):透湿用单位g/㎡/24h 表示,指在一定的标准实验室条件下,使试样的两侧形成一特定的湿度差,水蒸汽通过试样进入干燥的一侧,通过测定透湿杯重量随时间的变化量,从而求出试样的水蒸汽透过率等参数。
防水透湿面料测试方法介绍

防水透湿面料测试方法介绍在面料展会上,经常会遇到这样的客户,需要防水透湿达到10000/10000的复合面料。
美国Gore的面料能够达到这个透湿量,一般的TPU高透薄膜做三合一(面布+膜+里布)也只能达到5000的透湿量。
如果用英国的Porelle或荷兰的Sypamtex薄膜透湿量会高一些,但也不能达到10000,而且这些进口膜的价格也不菲。
那怎么解释客户会要求这么高的指标呢?一种可能就是客户不懂这行,看到Gore的衣服上标着10000/10000,就要做这么高的指标;还有一种可能,也就是外行人不懂而被一些常常利用的,那就是测试方法的不同。
现在的测试方法有多少?我列出来的方法希望能帮助大家!1. 水蒸气透过法1.1.1正杯法A,中国国家标准:GB/T12704-91 BB,美国材料实验协会标准:ASTM E96 Produce B and DC,日本工业标准:JIS L-1099 A2D,加拿大标准:(CGSB)-4.2 No.49-99E,英国标准:BS 7209-19901.1.2倒杯法(也叫吸湿法)A,美国材料实验协会标准:ASTM E96 BW(1995版和2000版)1.2 干燥剂法1.2.1正杯法A,中国国家标准:GB/T 12704-91 AB,日本工业标准:JIS L-1099 A1C,美国材料试验学会标准:ASTM E-96 A、C、E1.2.2倒杯法A,日本工业标准:JIS L-1099 B1、B2B,美国材料试验学会标准:ASTM E-96C,比利时UCB公司标准:UCB 法D,英国标准:B.T.T.G法2、出汗热盘法,也称皮肤模型法A,ISO标准:ISO 11092B,消防防护服测试:NFPA 1971C,美国材料试验学会标准:ASTM F 1868-98 BD,德国标准:DIN 54 010 T01-A3、出汗假人法出汗假人法的假人有点像热盘,用来模拟典型人体的形状和尺寸。
- 1、下载文档前请自行甄别文档内容的完整性,平台不提供额外的编辑、内容补充、找答案等附加服务。
- 2、"仅部分预览"的文档,不可在线预览部分如存在完整性等问题,可反馈申请退款(可完整预览的文档不适用该条件!)。
- 3、如文档侵犯您的权益,请联系客服反馈,我们会尽快为您处理(人工客服工作时间:9:00-18:30)。
Designation:E96/E96M–05Standard Test Methods forWater Vapor Transmission of Materials1This standard is issued under thefixed designation E96/E96M;the number immediately following the designation indicates the yearof original adoption or,in the case of revision,the year of last revision.A number in parentheses indicates the year of last reapproval.A superscript epsilon(e)indicates an editorial change since the last revision or reapproval.This standard has been approved for use by agencies of the Department of Defense.1.Scope1.1These test methods cover the determination of watervapor transmission(WVT)of materials through which thepassage of water vapor may be of importance,such as paper,plasticfilms,other sheet materials,fiberboards,gypsum andplaster products,wood products,and plastics.The test methodsare limited to specimens not over11⁄4in.(32mm)in thicknessexcept as provided in Section9.Two basic methods,theDesiccant Method and the Water Method,are provided for themeasurement of permeance,and two variations include serviceconditions with one side wetted and service conditions withlow humidity on one side and high humidity on the other.Agreement should not be expected between results obtained bydifferent methods.The method should be selected that more nearly approaches the conditions of use.1.2The values stated in inch-pound units are to be regarded separately as the standard.Within the text,the SI units are shown in parentheses.The values stated in each system are not exact equivalents;therefore each system must be used inde-pendently of the bining values from two systems will result in non-conformance with the standard.However derived results can be converted from one system to other using appropriate conversion factors(see Table1).1.3This standard does not purport to address all of the safety problems,if any,associated with its use.It is the responsibility of the user of this standard to establish appro-priate safety and health practices and determine the applica-bility of regulatory limitations prior to use.2.Referenced Documents2.1ASTM Standards:2C168Terminology Relating to Thermal InsulationD449Specification for Asphalt Used in Dampproofing and WaterproofingD2301Specification for Vinyl Chloride Plastic Pressure-Sensitive Electrical Insulating TapeE691Practice for Conducting an Interlaboratory Study to Determine the Precision of a Test Method3.Terminology3.1Definitions of terms used in this standard will be found in Terminology C168,from which the following is quoted:“water vapor permeability—the time rate of water vapor transmission through unit area offlat material of unit thickness induced by unit vapor pressure difference between two specific surfaces,under specified temperature and humidity conditions.3.1.1Discussion—Permeability is a property of a material, but the permeability of a body that performs like a material may be used.Permeability is the arithmetic product of per-meance and thickness.water vapor permeance—the time rate of water vapor transmission through unit area offlat material or construction induced by unit vapor pressure difference between two specific surfaces,under specified temperature and humidity conditions.3.1.2Discussion—Permeance is a performance evaluation and not a property of a material.3.2water vapor transmission rate—the steady water vapor flow in unit time through unit area of a body,normal to specific parallel surfaces,under specific conditions of temperature and humidity at each surface.”4.Summary of Test Methods4.1In the Desiccant Method the test specimen is sealed to the open mouth of a test dish containing a desiccant,and the1These test methods are under the jurisdiction of ASTM Committee C16on Thermal Insulation and are the direct responsibility of Subcommittee C16.33on Thermal Insulation Finishes and Vapor Transmission.Current edition approved May1,2005.Published June2005.Originally approved st previous edition approved in2000as E96–00e1.2For referenced ASTM standards,visit the ASTM website,,or contact ASTM Customer Service at service@.For Annual Book of ASTM Standards volume information,refer to the standard’s Document Summary page on the ASTM website.TABLE1Metric Units and Conversion Factors A,BMultiply byTo Obtain(for thesame test condition)WVTg/h·m2 1.43grains/h·ft2grains/h·ft20.697g/h·m2Permeanceg/Pa·s·m2 1.7531071Perm(inch-pound)1Perm(inch-pound) 5.72310−8g/Pa·s·m2Permeabilityg/Pa·s·m 6.8831081Perm inch1Perm inch 1.45310−9g/Pa·s·mA These units are used in the construction trade.Other units may be used in other standards.B All conversions of mm Hg to Pa are made at a temperature of0°C.Copyright©ASTM International,100Barr Harbor Drive,PO Box C700,West Conshohocken,PA19428-2959,United States.--`,,`,``-`-`,,`,,`,`,,`---assembly placed in a controlled atmosphere.Periodic weigh-ings determine the rate of water vapor movement through the specimen into the desiccant.4.2In the Water Method,the dish contains distilled water, and the weighings determine the rate of vapor movement through the specimen from the water to the controlled atmo-sphere.The vapor pressure difference is nominally the same in both methods except in the variation,with extremes of humid-ity on opposite sides.5.Significance and Use5.1The purpose of these tests is to obtain,by means of simple apparatus,reliable values of water vapor transfer through permeable and semipermeable materials,expressed in suitable units.These values are for use in design,manufacture, and marketing.A permeance value obtained under one set of test conditions may not indicate the value under a different set of conditions.For this reason,the test conditions should be selected that most closely approach the conditions of use. While any set of conditions may be used and those conditions reported,standard conditions that have been useful are shown in Appendix X1.6.Apparatus6.1Test Dish—The test dish shall be of any noncorroding material,impermeable to water or water vapor.It may be of any shape.Light weight is desirable.A large,shallow dish is preferred,but its size and weight are limited when an analytical balance is chosen to detect small weight changes.The mouth of the dish shall be as large as practical and at least4.65in.2(3000 mm2).The desiccant or water area shall be not less than the mouth area except if a grid is used,as provided in12.1,its effective area shall not exceed10%of the mouth area.An externalflange or ledge around the mouth,to which the specimen may be attached,is useful when shrinking or warping occurs.When the specimen area is larger than the mouth area, this overlay upon the ledge is a source of error,particularly for thick specimens.This overlay material should be masked as described in10.1so that the mouth area defines the test area. The overlay material results in a positive error,indicating excessive water vapor transmission.The magnitude of the error is a complex function of the thickness,ledge width,mouth area,and possibly the permeability.This error is discussed by Joy and Wilson(1)3(see13.4.3).This type of error should be limited to about10to12%.For a thick specimen the ledge should not exceed3⁄4in.(19mm)for a10-in.(254-mm)or larger mouth(square or circular)or1⁄8in.(3mm)for a5-in. (127-mm)mouth(square or circular).For a3-in.(76-mm) mouth(square or circular)the ledge should not exceed0.11in.(2.8mm)wide.An allowable ledge may be interpolated for intermediate sizes or calculated according to Joy and Wil-son.(1)A rim around the ledge(Fig.X2.1)may be useful.If a rim is provided,it shall be not more than1⁄4in.(6mm)higher than the specimen as attached.Different depths may be used for the Desiccant Method and Water Method,but a3⁄4-in. (19-mm)depth(below the mouth)is satisfactory for either method.6.2Test Chamber—The room or cabinet where the as-sembled test dishes are to be placed shall have a controlled temperature(see Note1)and relative humidity.Some standard test conditions that have been useful are given in Appendix X1. The temperature chosen shall be determined according to the desired application of the material to be tested(see Appendix X1).The relative humidity shall be maintained at5062%, except where extremes of humidities are desired,when the conditions shall be10061.8°F(3861°C)and9062% relative humidity.Both temperature and relative humidity shall be measured frequently4or preferably recorded continuously. Air shall be continuously circulated throughout the chamber, with a velocity sufficient to maintain uniform conditions at all test locations.The air velocity over the specimen shall be between0.066and1ft/s(0.02and0.3m·s-1).Suitable racks shall be provided on which to place the test dishes within the test chamber.N OTE1—Simple temperature control by heating alone is usually made possible at90°F(32°C).However,it is very desirable to enter the controlled space,and a comfortable temperature is more satisfactory for that arrangement.Temperatures of73.4°F(23°C)and80°F(26.7°C)are in use and are satisfactory for this purpose.With cyclic control,the average test temperature may be obtained from a sensitive thermometer in a mass of dry sand.The temperature of the chamber walls facing a specimen over water should not be cooler than the water to avoid condensation on the test specimen.6.3Balance and Weights—The balance shall be sensitive toa change smaller than1%of the weight change during the period when a steady state is considered to exist.The weights used shall be accurate to1%of the weight change during the steady-state period(Note2).A light wire sling may be substituted for the usual pan to accommodate a larger and heavier load.6.4Thickness-Measuring Gage—The nominal thickness of the specimen shall be determined using a thickness-measuring gage with an accuracy of61%of the reading or0.0001in.(0.0025mm),whichever is greater.N OTE2—For example:1-perm(57ng·Pa-1·s-1·m-2)specimen10in. (254mm)square at80°F(26.7°C)passes8.6grains or0.56g/day.In18 days of steady state,the transfer is10g.For this usage,the balance must have a sensitivity of1%of10g or0.1g and the weights must be accurate to0.1g.If,however,the balance has a sensitivity of0.2g or the weights are no better than0.2g,the requirements of this paragraph can be met by continuing the steady state for36days.An analytical balance that is much more sensitive will permit more rapid results on specimens below1perm (57ng·Pa-1·s-1·m-2)when the assembled dish is not excessively heavy.7.Materials7.1Desiccant and Water:7.1.1For the Desiccant Method,anhydrous calcium chlo-ride in the form of small lumps that will pass a No.8 (2.36-mm)sieve,and free offines that will pass a No.303The boldface numbers in parentheses refer to the list of references at the end of this standard.4The minimum acceptable is to perform this measurement each time the sample isweighed. --`,,`,``-`-`,,`,,`,`,,`---(600-µm)sieve,shall be used(Note3).It shall be dried at 400°F(200°C)before use.N OTE3—If CaCl2will react chemically on the specimen,an adsorbingdesiccant such as silica gel,activated at400°F(200°C),may be used;but the moisture gain by this desiccant during the test must be limited to4%.7.1.2For the Water Method,distilled water shall be used in the test dish.7.2Sealant—The sealant used for attaching the specimen to the dish,in order to be suitable for this purpose,must be highly resistant to the passage of water vapor(and water).It must not lose weight to,or gain weight from,the atmosphere in an amount,over the required period of time,that would affect the test result by more than2%.It must not affect the vapor pressure in a water-filled dish.Molten asphalt or wax is required for permeance tests below4perms(230ng·m-2·s-1·Pa-1).Sealing methods are discussed in Appendix X2. 8.Sampling8.1The material shall be sampled in accordance with standard methods of sampling applicable to the material under test.The sample shall be of uniform thickness.If the material is of nonsymmetrical construction,the two faces shall be designated by distinguishing marks(for example,on a one-side-coated sample,“I”for the coated side and“II”for the uncoated side).9.Test Specimens9.1Test specimens shall be representative of the material tested.When a product is designed for use in only one position, three specimens shall be tested by the same method with the vaporflow in the designated direction.When the sides of a product are indistinguishable,three specimens shall be tested by the same method.When the sides of a product are different and either side may face the vapor source,four specimens shall be tested by the same method,two being tested with the vapor flow in each direction and so reported.9.2A slab,produced and used as a laminate(such as a foamed plastic with natural“skins”)may be tested in the thickness of use.Alternatively,it may be sliced into two or more sheets,each being separately tested and so reported as provided in9.4,provided also,that the“overlay upon the cup ledge”(6.1)of any laminate shall not exceed1⁄8in.(3mm).9.3When the material as used has a pitted or textured surface,the tested thickness shall be that of use.When it is homogeneous,however,a thinner slice of the slab may be tested as provided in9.4.9.4In either case(9.2or9.3),the tested overall thickness,if less than that of use,shall be at leastfive times the sum of the maximum pit depths in both its faces,and its tested permeance shall be not greater than5perms('300ng·m-2·s-1·Pa-1). 9.5For homogeneous(not laminated)materials with thick-ness greater than1⁄2in.,the overall nominal thickness of each specimen shall be measured with an accuracy of61%of the reading at the center of each quadrant and the results averaged.9.6When testing any material with a permeance less than 0.05perms(3ng·m-2·s-1·Pa-1)or when testing a low permeance material that may be expected to lose or gain weight through-out the test(because of evaporation or oxidation),it is strongly recommended that an additional specimen,or“dummy,”be tested exactly like the others,except that no desiccant or water is put in the dish.Failure to use this dummy specimen to establish modified dish weights may significantly increase the time required to complete the test.Because time to reach equilibrium of water permeance increases as the square of thickness,thick,particularly hygroscopic,materials may take as long as60days to reach equilibrium conditions.10.Attachment of Specimen to Test Dish10.1Attach the specimen to the dish by sealing(and clamping if desired)in such a manner that the dish mouth defines the area of the specimen exposed to the vapor pressure in the dish.If necessary,mask the specimen top surface, exposed to conditioned air so that its exposure duplicates the mouth shape and size and is directly above it.A template is recommended for locating the mask.Thoroughly seal the edges of the specimen to prevent the passage of vapor into,or out of, or around the specimen edges or any portion thereof.The same assurance must apply to any part of the specimen faces outside their defined areas.Suggested methods of attachment are described in Appendix X2.N OTE4—In order to minimize the risk of condensation on the interior surface of the sample when it is placed in the chamber,the temperature of the water prior to preparation of the test specimen should be within62°F (61°C)of the test condition.11.Procedure for Desiccant Method11.1Fill the test dish with desiccant within1⁄4in.(6mm)of the specimen.Leave enough space so that shaking of the dish, which must be done at each weighing,will mix the desiccant.11.2Attach the specimen to the dish(see10.1)and place it in the controlled chamber,specimen up,weighing it at once. (This weight may be helpful to an understanding of the initial moisture in the specimen.)11.3Weigh the dish assembly periodically,often enough to provide eight or ten data points during the test.A data point is the weight at a particular time.The time that the weight is made should be recorded to a precision of approximately1%of the time span between successive weighing.Thus,if weighings are made every hour,record the time to the nearest30s;if recordings are made every day,a time to the nearest15min would be allowed.Atfirst the weight may change rapidly;later a steady state will be reached where the rate of change is substantially constant.Weighings should be accomplished without removal of the test dishes from the controlled atmo-sphere,but if removal is prescribed necessary,the time the specimens are kept at different conditions,temperature or relative humidity,or both,should be kept to a minimum.When results of water vapor transmission are expected to be less than 0.05perm(3ng·m-2·s-1·Pa-1),a dummy specimen is strongly recommended.Such a dummy specimen should be attached to an empty cup in the normal manner.The environmental effects of temperature variation and buoyancy variability due to barometric pressurefluctuation can be arithmetically tared out of the weighing values.This precaution permits earlier and more reliable achievement of equilibrium conditions.Analyze the results as prescribed in13.1.--` , , ` , ` ` -` -` , , ` , , ` , ` , , ` ---11.4Terminate the test or change the desiccant before the water added to the desiccant exceeds10%of its starting weight.This limit cannot be exactly determined and judgement is required.The desiccant gain may be more or less than the dish weight-gain when the moisture content of the specimen has changed.N OTE5—The WVT of some materials(especially wood)may depend on the ambient relative humidity immediately before the test.An apparent hysteresis results in higher WVT if the prior relative humidity was above the test condition and vice versa.It is therefore recommended that specimens of wood and paper products be conditioned to constant weight in a50%relative humidity atmosphere before they are tested.Some specimens may be advantageously preconditioned to minimize the mois-ture that the specimen will give up to the desiccant.This applies when the specimen is likely to have high moisture content or when it is coated on the top(vapor source)side.12.Procedure for Water Method12.1Fill the test dish with distilled water to a level3⁄461⁄4 in.(1966mm)from the specimen.The air space thus allowed has a small vapor resistance,but it is necessary in order to reduce the risk of water touching the specimen when the dish is handled.Such contact invalidates a test on some materials such as paper,wood,or other hygroscopic materials.The water depth shall be not less than1⁄8in.(3mm)to ensure coverage of the dish bottom throughout the test.However,if the dish is of glass,its bottom must be visibly covered at all times but no specific depth is required.Water surges may be reduced by placing a grid of light noncorroding material in the dish to break the water surface.This grid shall be at least1⁄4in.(6mm) below the specimen,and it shall not reduce the water surface by more than10%.N OTE6—For the Water Method,baking the empty dish and promptly coating its mouth with sealant before assembly is recommended.The water may be added most conveniently after the specimen is attached, through a small sealable hole in the dish above the water line.12.2Attach the specimen to the dish(see10.1).Some specimens are likely to warp and break the seal during the test. The risk is reduced by preconditioning the specimen,and by clamping it to the dish ledge(if one is provided).12.3Weigh the dish assembly and place it in the controlled chamber on a true horizontal surface.Follow the procedure given in11.3.If the test specimen cannot tolerate condensation on the surface,the dish assembly shall not be exposed to a temperature that differs by more than5°F(3°C)from the control atmosphere to minimize the risk of condensation on the specimen.When results of water vapor transmission are expected to be less than0.05perm(3ng·m-2·s-1·Pa-1),a dummy specimen is strongly recommended.Such a dummy specimen should be attached to an empty cup in the normal manner.The environment effects of temperature variation and buoyancy variability due to barometric pressurefluctuation can be arithmetically tared out of the weighing values.This precaution permits earlier and more reliable achievement of equilibrium conditions.Analyze the results as prescribed in 13.1.12.4Where water is expected to be in contact with the barrier in service,proceed as in11.3except place the dish in an inverted position.The dish must be sufficiently level so that water covers the inner surface of the specimen despite any distortion of the specimen due to the weight of the water.With highly permeable specimens it is especially important to locate the test dish so that air circulates over the exposed surface at the specified velocity.The test dishes may be placed on the balance in the upright position for weighing,but the period during which the wetted surface of the specimen is not covered with water must be kept to a minimum.13.Calculation and Analysis of Results13.1The results of the rate of water vapor transmission may be determined either graphically or numerically.13.1.1Dummy Specimen—If a dummy specimen has been used to compensate for variability in test conditions,due to temperature or barometric pressure,or both,the daily recorded weights can be adjusted by calculating the weight change from initial to time of weighing.This adjustment is made by reversing the direction of the dummy’s weight change,relative to its initial weight,and modifying all the appropriate specimen weight(s)recorded at this time.This permits earlier achieve-ment of equilibrium conditions.An alternate procedure,par-ticular for tests of long duration and more than six weighings, is to subtract the arithmetic mean slope of the rate of weight change of the dummy specimen from the arithmetic mean slope of each similar specimen to get an effective rate of weight change.These procedures are also desirable if the specimen is changing weight due to a curing process while under test. 13.1.2Graphic Analysis—Plot the weight,modified by the dummy specimen when used,against elapsed time,and in-scribe a curve that tends to become straight.Judgment here is required and numerous points are helpful.When a straight line adequatelyfits the plot of at least six properly spaced points (periodic weight changes matching,or exceeding20%of the multiple of100times the scale sensitivity),a nominally steady state is assumed,and the slope of the straight line is the rate of water vapor transmission.13.1.3Numerical Analysis—A mathematical least squares regression analysis of the weight,modified by the dummy specimen when used,as a function of time will give the rate of water vapor transmission.An uncertainty,or standard deviation of this rate,can also be calculated to define the confidence band.For very low permeability materials,this method can be used to determine the results after30to60days when using an analytical balance,with a sensitivity of'1mg,even if the weight change does not meet the100times the sensitivity requirement of6.3.These specimens must be clearly identified in the report.13.2Calculate the water vapor transmission,WVT,and permeance as follows:13.2.1Water Vapor Transmission:WVT5G/tA5~G/t!/A(1) where:In inch-pound units:G=weight change,grains(from the straight line),t=time during which G occurred,h,G/t=slope of the straight line,grains/h,A=test area(cup mouth area),ft2,and --`,,`,``-`-`,,`,,`,`,,`---WVT=rate of water vapor transmission,grains/h·ft2.In metric units:G=weight change(from the straight line),g,t=time,h,G/t=slope of the straight line,g/h,A=test area(cup mouth area),m2,andWVT=rate of water vapor transmission,g/h·m2.13.2.2Permeance:Permeance5WVT/D p5WVT/S~R12R2!(2) where:In inch-pound units:D p=vapor pressure difference,in.Hg,S=saturation vapor pressure at test temperature,in.Hg, R1=relative humidity at the source expressed as a fraction (the test chamber for desiccant method;in the dish forwater method),andR2=relative humidity at the vapor sink expressed as a fraction.In metric units:D p=vapor pressure difference,mm Hg(1.3333102Pa), S=saturation vapor pressure at test temperature,mm Hg(1.3333102Pa),R1=relative humidity at the source expressed as a fraction (the test chamber for desiccant method;in the dish forwater method),andR2=relative humidity at the vapor sink expressed as a fraction.13.2.3In the controlled chamber the relative humidity and temperature are the average values actually measured during the test and(unless continuously recorded)these measurements shall be made as frequently as the weight measurements.In the dish the relative humidity is nominally0%for the desiccant and100%for the water.These values are usually within3% relative humidity of the actual relative humidity for specimens below4perms(230ng·Pa-1·s-1·m-2)when the required condi-tions are maintained(no more than10%moisture in CaCl2and no more than1in.(25mm)air space above water).13.3The calculation of permeability is optional and can be done only when the test specimen is homogeneous(not laminated)and not less than1⁄2in.(12.5mm)thick,calculate its average permeability as follows:Average permeability5Permeance3Thickness(3) 13.4Corrections—It is important that all applicable correc-tions be made to all measurements that result in permeance value more than2-perm(114ng·Pa-1·s-1·m-2).Corrections for materials with permeance value below2-perm(114ng·Pa-1·s-1·m-2)are insignificant and need not be done.The procedures for making various corrections,as summarized below,are found in the literature.(2,3,4,5)13.4.1Buoyancy Correction—The duration for one set of measurements can be many days or weeks.The atmospheric pressure may significantly change during such periods.If the test specimen is highly vapor resistant,the changes in mass due to vapor transport may be overshadowed by the apparent gravimetric changes observed.In such cases,all gravimetric data should be corrected to vacuum or any base line pressure. The following equation(2)can be used for buoyancy correc-tion.m2m1511r a~r12r2!r1~r22r a!(4)where:m1=mass recorded by balance,kg,m2=mass after buoyancy correction,kg,r a=density of air,kg m-3,r1=density of material of balance weights,kg m-3,and r2=bulk density of test assembly,kg m-3.13.4.1.1The density of air can be calculated using the ideal gas law for the measured atmospheric pressure and ambient temperature.13.4.1.2The buoyancy correction is important(6)when measured mass changes are in the range of0to100mg. 13.4.2Corrections for Resistance due to Still Air and Specimen Surface—In general,if the material is highly perme-able,these corrections are more significant.With known thickness of the still air layer in the cup,the corresponding vapor resistance can be calculated using the following equation (3)for permeability.d a52.30631025P oR v TPS T273.15D1.81(5)where:d a=permeability of still air,kg·m-1·s-1·Pa-1,T=temperature,K,P=ambient pressure,Pa,P o=standard atmospheric pressure,that is,101325Pa,and R v=ideal gas constant for water,that is,461.5J·K-1·kg-1.13.4.2.1In the absence of any measured data,the surface resistances(that is,inside and outside surfaces of the speci-men)may be approximated using Lewis’relation.(4)For cup methods that follow this standard,the total surface resistance (Hansen and Lund(5))should be'43107Pa·s·m2·kg-1. 13.4.3Edge Mask Correction—The following equation (Joy and Wilson(1))is to be used to correct the excess WVT effect due to edge masking:Percent excess WVT5400tp S1log e S211e2~2p b/t!D(6)where:t=specimen thickness,m,b=width of masked edge,m,andS1=four times the test area divided by the perimeter,m.13.4.3.1If the cup assembly includes any edge masking this correction shall be made.13.5Metric units and conversion factor are given in Table1.13.6Example(in SI unit)—In a desiccant test on a sample of medium density glassfiber insulation the following results were recorded.Thickness of the specimen=25.81mmTest area=0.01642m2Mass of the test specimen=20.44gMass of the desiccant=554.8gInitial mass of the test assembly=1.257810kgThickness of air layer in the cup=15mm。