压力传感器HM10
美国ZEMIC称重传感器

美国ZEMIC称重传感器美国ZEMIC有限公司在美国成立,是一个基于应变式称重传感器,压力传感器及称重系统,自成立以来,ZEMIC称重传感器的产品远销38个国家,在多个国家设立了分支机构或办事处,生产基地遍布美洲、东欧、东南亚、中国等地;并在中国设立苏州称重传感器事业部,可为用户的实验和生产提供最佳的服务与解决方案。
以下例举部分传感器型号:BM-11-401型产品型号:美国ZEMIC称重传感器BM11型产品品牌:美国ZEMIC称重传感器美国ZEMIC单点式称重传感器:H6E3 20/30/50/75/100/150/200/250/300 KGB6G5 0.1/0.2/0.25/0.3/0.4/0.5/0.6/0.75/1/1.5/2 KGB6E3 20/30/50/75/100/150/200/250/300 KG、L6B 0.3/0.6/1.2/3 KGL6C 3/5/8/20/30/50KGL6D 2.5,3,5,6,8,10,15,20,30,35,40,50 KG、L6E 50,60,80,100,150,200,300 KG、L6E3 50,60,80,100,150,200,300 KG、L6F 50/100/150/200/250/500/750/1000/2000KGL6G 50/100/150/200/250/300/500/600 KGL6H5 4/5/8/10/20 KG、L6J 1/2/3/5/8/10/15/20 KG、L6J1 0.3/0.4/0.5/0.6/1/3 KG、L6L 5/8/10/15/20/30/50/80/100/150/200 KG美国ZEMIC波纹管单点式称重传感器:BM11 20/30/50/100/200/350/500 KG、HM11 20/30/50/100/200/300/350/500 KG美国ZEMIC轮辐式称重传感器:H2A 1/2/3/4/5 MN、H2D 5/10/20 t、H2F 1/2/3/5/10/15/20/30/50 t 美国ZEMIC双平行梁式称重传感器:L16 500 KG、L16A 100 KG美国ZEMIC S型梁式称重传感器:B3G 0.05/0.1/0.25/0.5/1/2.5/5/7.5/10 t、H3 25㎏~30t;100lb~20Klb、H3C 10/20 t、H3E 1/2/3/5/7.5/10/15 t、H3F 0.1/0.25/0.5/0.75/1/1.5/2/2.5/5 t、H3G 0.05/0.1/0.25/0.5/1/2.5/5/7.5/10 t、BM3 0.5/1/2/3/4/5/6/7.5 t、L3V 200、500 KG 美国ZEMIC单剪切梁式称重传感器:B8D 250lb~20Klb;100kg~5t、BM8D 0.5/1/1.5/2/2.5/3/5/7.5/10 t、BM8H 0.25/0.5/1/2/5 t、H8 0.5/1/2/2.5/3/5/10/15/20/25 t、HM8 0.5/1/2/2.5/3/5/10/15/20/25/30 t、H8B 0.5/1/2/2.5/3/4/5/8/10 t、H8C 0. 5/1/1.5/2/2.5/3/5/10 t、HM8C 0. 5/1/1.5/2/3/5/10 t、H8H 0.25/0.5/1/2/5 t苏州赛奥仪器仪表有限公司是众多称重传感器品牌最具权威的一级销售代理渠道,专业提供欧美工业品牌自动化设备、仪器仪表、备品备件的中国区域一级代理供应商,通过我们专业的服务诚信的经营已在国内传感器行业树立了良好的口碑和信誉。
A320飞机空调部件

• 空气循环机压气机温度传感器
– (左)12HH,(右)32HH – (左)191,(右)192 – 空气循环机压气机温度传感器 用于PACK组件温度控制功能 和PACK组件过热探测。它连 接到PACK组件控制器主计算 机。
热交换器
• 初级热交换器
– (左)10HM6,(右)11HM6 – (左)191,(右)192 – 初级热交换器为单通道交叉气 流型——金属板制翅片式热交 换器。它的作用是使用飞机外 部冲压空气,对进入空气循环 机之前的空调引气进行冷却。
• 主(次)级热交换器
– (左)10HM7,(右)11HM7 – (左)191,(右)192 – 初级热交换器为逆流型——金 属板制翅片式热交换器。它安 装在空气循环机的压气机与涡 轮之间,它也使用飞机外部冲 压空气,对空调引气进行冷却。
•
• •
客舱再循环风扇气滤
客舱再循环风扇
地面气源接头
客舱再循环风扇单向活门
增压舱压力调节
客舱压力控制板
• 当水上迫降 (“DITCHING”)按钮 电门选择在“ON”位(压 入)时,CPC使放气关闭。 另外,应急冲压空气入口, 电子设备通风口,PACK 组件流量控制活门都关闭。 • 注意:在人工模式下,放 气活门不能自动关闭。
人工马达
•
电激励器
–
–
•
齿轮箱和反馈组件
– 齿轮箱将工作马达的运动传递到放气活门。有 一个机械止动限制放气活门转动轴的运动。放 气活门位置反馈模块有3个电位计,与齿轮箱 构成一个整体,反馈信号送到座舱压力控制器 (CPC)。 自动模式下,驱动放气活门使用的是两个无刷 式直流马达,每个马达上各有一个电气机械刹 车。人工模式下,驱动活门使用的是一个有刷 式直流马达,它通过一个蠕行齿轮驱动放气活 门。
BD SENSORS GmbH DMP 331 工业压力传感器说明书
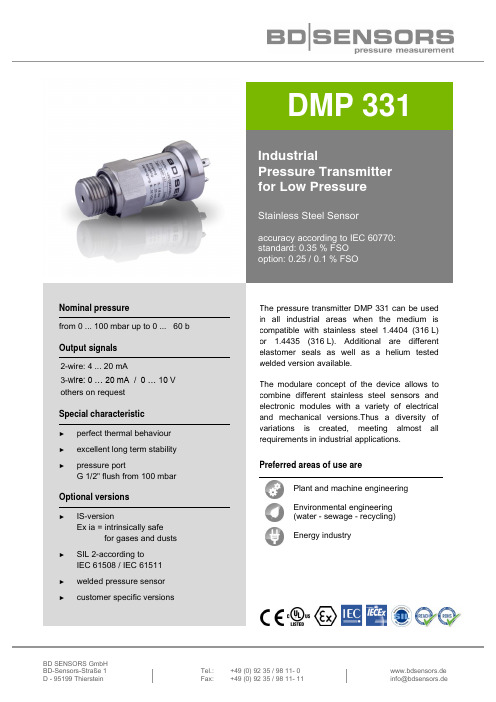
BD SENSORS GmbH BD-Sensors-Straße 1 Tel.: +49 (0) 92 35 / 98 11- 0www.bdsensors.de D - 95199 ThiersteinFax: +49 (0) 92 35 / 98 11- 11*****************DMP 331IndustrialPressure Transmitter for Low PressureStainless Steel Sensoraccuracy according to IEC 60770: standard: 0.35 % FSO option: 0.25 / 0.1 % FSONominal pressurefrom 0 ... 100 mbar up to 0 ... 60 b Output signals 2-wire: 4 ... 20 mA3-wire: 0 … 20 mA / 0 … 10 V others on request Special characteristic►perfect thermal behaviour ►excellent long term stability ►pressure portG 1/2" flush from 100 mbarOptional versions►IS-versionEx ia = intrinsically safefor gases and dusts ►SIL 2-according toIEC 61508 / IEC 61511►welded pressure sensor ►customer specific versionsThe pressure transmitter DMP 331 can be used in all industrial areas when the medium is compatible with stainless steel 1.4404 (316 L) or 1.4435 (316 L). Additional are different elastomer seals as well as a helium tested welded version available.The modulare concept of the device allows to combine different stainless steel sensors and electronic modules with a variety of electrical and mechanical versions.Thus a diversity of variations is created, meeting almost all requirements in industrial applications. Preferred areas of use arePlant and machine engineeringEnvironmental engineering (water - sewage - recycling) Energy industrypressure and levelwww.bdsensors.deExplosion protection (only for 4 … 20 mA / 2-wire)ApprovalsDX19-DMP 331 IBExU 10 ATEX 1068 X / IECEx IBE 12.0027X zone 0: II 1G Ex ia IIC T4 Gazone 20: II 1D Ex ia IIIC T135 °C DaSafety technical maximum values U i = 28 V, I i = 93 mA, P i = 660 mW, C i ≈ 0 nF, L i ≈ 0 μH,the supply connections have an inner capacity of max. 27 nF to the housingPermissible temperatures for environment in zone 0: -20 ... 60 °C with p atm 0.8 bar up to 1.1 bar in zone 1 or higher: -40/-20 ... 70 °CConnecting cables (by factory)cable capacitance: signal line/shield also signal line/signal line: 160 pF/m cable inductance: signal line/shield also signal line/signal line: 1 μH/mMiscellaneousOption SIL2 version 3 according to IEC 61508 / IEC 61511 Current consumption signal output current: max. 25 mAsignal output voltage: max. 7 mAWeight approx. 200 g Installation position any 4 Operational life 100 million load cycles CE-conformity EMC Directive: 2014/30/EU ATEX Directive 2014/34/EU3 only for4 … 20 mA / 2-wire, not in combination with accuracy 0.1 %4Pressure transmitters are calibrated in a vertical position with the pressure connection down. If this position is changed on installation there can be slight deviations in the zero point for pressure ranges p N ≤ 1 bar.Wiring diagrams2-wire-system (current)3-wire-system (current / voltage)Pin configuration Electrical connectionISO 4400Binder 723 (5-pin)M12x1 / metal(4-pin)Bayonet MIL-C-26482(10-6)2-wire3-wire Supply + Supply –Signal + (for 3-wire)1 2 33 4 1 1 2 3 A B -A D BShieldground pin54pressure portElectrical connectioncompact field housingcable colours (IEC 60757)V S+ V S- S+ GNDSupply + Supply –Signal + (for 3-wire)V S + V S - S+ WH (white) BN (brown) GN (green) ShieldGNDGNYE (green-yellow)psupply +supply –V SIsupply +A/Vsignal +V SpI/Usupply –ISO 4400 Binder series 723, 5-pin M12x1, 4-pin(IP 65) (IP 67) (IP 67)cable outlet with PVC cable cable outlet, cable with(IP 67) 5ventilation tube (IP 68) 6compact field housing(IP 67)universal field housing stainless steel 1.4404 (316 L) with cable gland M20x1.5 (ordering code 880) and other versions on request pressure and levelwww.bdsensors.deDimensions (mm / in)standardSIL- and SIL-IS version* with electrical connection Bayonet MIL-C-26482 (10-6) increases the length of devices by 5 mmMechanical connections (dimensions mm / in)G1/2" DIN 3852 G1/2" EN 837 1/2" NPTG1/4" DIN 3852 G1/4" EN 837 1/4" NPTG1/2" open port DIN 3852G1/2" flush DIN 3852(p N ≤ 40 bar) (p N ≤ 40 bar)DMP331_E_310123Tel.: +49 (0) 92 35 / 98 11- 0www.bdsensors.de Fax: +49 (0) 92 35 / 98 11- 11*****************© 2023 B D |S E N S O R S G m b H – T h e s p e c i f i c a t i o n s g i v e n i n t h i s d o c u m e n t r e p r e s e n t t h e s t a t e o f e n g i n e e r i n g a t t h e t i m e o f p u b l i s h i n g . W e r e s e r v e t h e r i g h t t o m a k e m o d i f i c a t i o n s t o t h e s p e c i f i c a t i o n s a n d m a t e r i a l s .metric threads and other versions on request**-------1101110.1010000.1616000.2525000.4040000.6060001.010011.616012.525014.040016.06001101002161602252502404002606002-1 … 0X 1029999consult123E 1S 9consultstandard for p N ≥ 0.4 bar:0.35 % FSO 3standard for p N < 0.4 bar:0.50 % FSO 5option 1 for p N ≥ 0.4 bar:0.25 % FSO 2option 2:0.10 % FSO19consult100200T A 0cable with ventilation tube (IP68)M 10B G 0B G 4stainless steel 1.4301 (304)999consult 10020030040055H 00N 00N 40999consult1329consult000999consult1 absolute pressure possible from 0.4 bar2 not in combination with SIL3 standard: 2 m PVC cable without ventilation tube (permissible temperature: -5 … 70°C), others on request4code TR0 = PVC cable, cable with ventilation tube available in different types and lengths 5only for p N ≤ 40 bar6welded version only with pressure ports according to EN 837 and NPT31.01.2023customer34T R 0111intrinsic safety 4 … 20 mA / 2-wire2gauge 4 … 20 mA / 2-wire SIL2 4 … 20 mA / 2-wire 0 … 10 V / 3-wire0 … 20 mA / 3-wire absolute customer15, 6without (welded version)© 2023 B D |S E N S O R S G m b H - T h e s p e c i f i c a t i o n s g i v e n i n t h i s d o c u m e n t r e p r e s e n t t h e s t a t e o f e n g i n e e r i n g a t t h e t i m e o f p u b l i s h i n g . W e r e s e r v e t h e r i g h t t o m a k e m o d i f i c a t i o n s t o t h e s p e c i f i c a t i o n s a n d m a t e r i a l s .DMP 331standard G1/4" DIN 3852customercustomerEPDM4 … 20 mA / 2-wirecustomercustomerSIL2 with intrinsic safetymale plug M12x1 (4-pin) / metal ES G1/4" EN 837G1/2" DIN 3852male and female plug ISO 4400male plug Binder series 723 (5-pin)cable outlet with PVC cable (IP67)8customercable outlet,1/4" NPT FKM Bayonet MIL-C-26482 (10-6); 2 wire Bayonet MIL-C-26482 (10-6); 3 wire00F G1/2" EN 837G1/2" DIN 3852501/2" NPT compact field housing G1/2" DIN 3852 open pressure portwith flush sensor。
伊顿 康弗洛 GH10 系列压力调节器 说明书 用户手册 使用指南
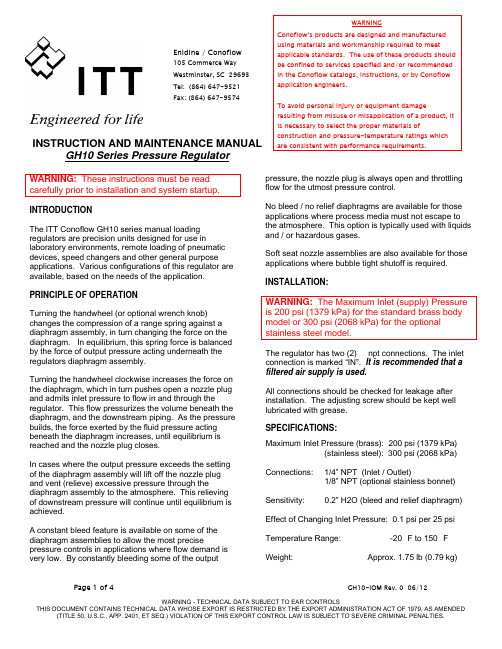
Enidine / Conoflow105 Commerce WayWestminster, SC 29693Tel: (864) 647-9521Fax: (864) 647-9574INSTRUCTION AND MAINTENANCE MANUAL GH10 Series Pressure RegulatorWARNING: These instructions must be read carefully prior to installation and system startup. INTRODUCTIONThe ITT Conoflow GH10 series manual loading regulators are precision units designed for use in laboratory environments, remote loading of pneumatic devices, speed changers and other general purpose applications. Various configurations of this regulator are available, based on the needs of the application.PRINCIPLE OF OPERATIONTurning the handwheel (or optional wrench knob) changes the compression of a range spring against a diaphragm assembly, in turn changing the force on the diaphragm. In equilibrium, this spring force is balanced by the force of output pressure acting underneath the regulators diaphragm assembly.Turning the handwheel clockwise increases the force on the diaphragm, which in turn pushes open a nozzle plug and admits inlet pressure to flow in and through the regulator. This flow pressurizes the volume beneath the diaphragm, and the downstream piping. As the pressure builds, the force exerted by the fluid pressure acting beneath the diaphragm increases, until equilibrium is reached and the nozzle plug closes.In cases where the output pressure exceeds the setting of the diaphragm assembly will lift off the nozzle plug and vent (relieve) excessive pressure through the diaphragm assembly to the atmosphere. This relieving of downstream pressure will continue until equilibrium is achieved.A constant bleed feature is available on some of the diaphragm assemblies to allow the most precise pressure controls in applications where flow demand is very low. By constantly bleeding some of the output pressure, the nozzle plug is always open and throttling flow for the utmost pressure control.No bleed / no relief diaphragms are available for those applications where process media must not escape to the atmosphere. This option is typically used with liquids and / or hazardous gases.Soft seat nozzle assemblies are also available for those applications where bubble tight shutoff is required. INSTALLATION:WARNING: The Maximum Inlet (supply) Pressure is 200 psi (1379 kPa) for the standard brass body model or 300 psi (2068 kPa) for the optional stainless steel model.The regulator has two (2) ¼ npt connections. The inlet connection is marked “IN”. It is recommended that a filtered air supply is used.All connections should be checked for leakage after installation. The adjusting screw should be kept well lubricated with grease.SPECIFICATIONS:Maximum Inlet Pressure (brass): 200 psi (1379 kPa)(stainless steel): 300 psi (2068 kPa) Connections: 1/4” NPT (Inlet / Outlet)1/8” NPT (optional stainless bonnet) Sensitivity: 0.2” H2O (bleed and relief diaphragm) Effect of Changing Inlet Pressure: 0.1 psi per 25 psi Temperature Range: -20 °F to 150 °F Weight: Approx. 1.75 lb (0.79 kg)WARNINGConoflow’s products are designed and manufacturedusing materials and workmanship required to meetapplicable standards. The use of these products shouldbe confined to services specified and/or recommendedin the Conoflow catalogs, instructions, or by Conoflowapplication engineers.To avoid personal injury or equipment damageresulting from misuse or misapplication of a product, itis necessary to select the proper materials ofconstruction and pressure-temperature ratings whichare consistent with performance requirements.Page 1 of 4GH10-IOM Rev. 0 06/12Catalog Part Number Breakdown (Control Engineering Data or CED Codes) for the GH10 Series RegulatorCharacter Position1-4 Model5 - Operational Feature6 – Bonnet Options7 - Adjustment Selections8 – Diaphragm Selections9 – Seat Selections10 – Material Options11 – Cleaning Options12 – Range Selections Feature by Code CharacterGH10 = RegulatorX = StandardA = Bonnet w/1/8” NPT Tapped VentF = Tapped Bonnet for Flush Back Panel Mounting NOTE: This option is standard on the GH10XF.S = Plain BonnetT = Threaded Bonnet (Standard)C = Tamperproof (Factory output setting CANNOT be field adjusted) ( See Notes 1 and 2)H = Handwheel (Standard)K = Knob (Wrench Style)P = Preset (Factory output setting CAN be field adjusted) (See NoteS 1 and 2)NOTES:1. Customer must specify output setting, supply pressure and flow.2. For list price adder, refer to price list CP-5000. The catalog number(s) listed under each diaphragm option is the standard diaphragm used in that regulator. These options apply to all output ranges of that unit. For non-standard diaphragm price adders, refer to price list CP-5000.A = Teflon (Rubber Backed) Corrosive Service On Process Side (No Bleed, No Relief)B = Silicone on Glass (No Bleed, No Relief)C = Buna “N” (w/Relief and Bleed) (See Note 1)D = Neoprene (w/Relief, No Bleed)E = Buna “N” (w/Relief, No Bleed)F = Viton on Nomex (No Bleed, No Relief)G = Silicone on Glass (w/Relief, No Bleed)H = Teflon (Sandwich Type - w/Relief, No Bleed)J = Viton on Nomex (w/Relief, No Bleed)L = Nordel on Nomex (EPDM) (w/Relief, No Bleed)M = Buna “N” (No Bleed, No Relief)N = Nordel on Nomex (EPDM) (No Bleed, No Relief)P = Neoprene (No Bleed, No Relief)R = Teflon (Sandwich Type - w/Relief and Bleed)NOTE: 1. This option cannot be supplied in 316 Stainless Steel construction.A = Buna “N”B = NeopreneC = VitonX = Standard - Unless option code is specifiedB = Brass Construction (body and bonnet are brass)S = Stainless Steel Construction (Stainless Steel Internals)X = Standard - Unless option code is specified.A = Cleaned for Oxygen ServiceX = Standard - Unless option code is specifiedA = 0-5 PSI (0-35 kPa)B = 0-15 PSI (0-103 kPa)C = 0-25 PSI (0-172 kPa)D = 0-35 PSI (0-241 kPa)E = 0-50 PSI (0-345 kPa)F = 0-60 PSI (0-414 kPa) (For Model “1166” onlyG = 0-125 PSI (0-862 kPa)L = 0-3 PSI (0-21 kPa)Page 2 of 4GH10-IOM Rev. 0 06/12When replacement parts are required, please contact the factory with the full model number and serial number of the regulator.MAINTENANCECAUTION: Remove air supply pressure and thoroughly vent the inlet and outlet pressure prior to performing maintenance.Periodic replacement of the diaphragm assembly and nozzle assembly is recommended for services where the unit is on-stream continuously and where consistent, high accuracy regulation is required. The frequency of replacement is dependent on the nature of the application and can be affected by the cleanliness of the media, the temperature and humidity of the environment, the rate of flow, and other factors.To replace the diaphragm assembly, loosen the wrench knob (or handwheel) and jam nut until compression is relieved from the range spring. Loosen and remove the fillister head machine screws and lift off bonnet, spring button, range spring, restrictor plate (0-125 psi models) and diaphragm assembly. Place the new diaphragm assembly on the bonnet, with the diaphragm plate and staked side face upward (away from the body). Place the range spring, spring button, restrictor plate (if applicable) and bonnet over the diaphragm assembly then secure the bonnet with the fillister head machine screws tightened to 30 in-lb. Replace wrench knob or handwheel and jam nut if previously removed.To replace the nozzle assembly, disassemble the regulator as previously described, then remove the baffle plate and the nozzle assembly. Use a 5/8” socket wrench to remove and install the nozzle assembly.An all metal nozzle assembly may be cleaned in solvent, however a nozzle assembly that uses any rubber components must be replaced with the equivalent factory part.When replacing the nozzle assembly, the metal to metal seal nozzles are installed with 80 in-lb assembly torque; the rubber bottom nozzle assemblies are installed with 30 in-lb assembly torque. Incorrect torque can create leakage and damage the nozzle assembly.Page 3 of 4GH10-IOM Rev. 0 06/12This page intentionally left blank for user notesPage 4 of 4GH10-IOM Rev. 0 06/12。
HM中文说明书1

目录第一节系统说明1 引言2 电解液3 电解槽4 电解液子系统(1)KOH泵(2)KOH贮罐(3)换热器(4)KOH过滤器(5)流量开关(6)KOH温度传感器(7)KOH液位计5 给水子系统(1)给水(2)给水水质监测器(3)给水泵(4)给水控制6 气体控制和调节子系统(1)压力变送器(2)产气速率(3)预压(4)备用(5)压力释放(6)背压调节器(7)差压调节器(8)安全阀(9)排空阀(10)冷凝器和捕集器(11)纸型隔膜(12)氮气冲洗7 氢气干燥(1)干燥器(2)干燥器阀8 冷却及冷凝器冷却水子系统(1)温度调节阀(2)冷凝器冷却水及其控制9 系统安全(1)氧中氢监测器(2)电流监测器(3)氢检测器(4)停车报警10 电力和工艺控制子系统(1)DC电源(2)可编程控制器(3)工艺控制及程序(4)干燥器程序11 数据显示和工艺监控(1)触摸屏显示(2)发光二极管监控第二节发生器安装1 系统类别2 发生器安装3 设备连接(1)给水(2)冷却水(3)冷凝器冷却水(4)氢、氧排气阀(5)产品气输送(6)电力(7)氮气吹洗4电源的电连接5 外部报警连接第三节发生器运行1 前言2 初次启动3 启动模式4 运行模式5 备用模式6 常规运行7 压力释放8 停车第四节维护和校验规程1 前言2 电解液(1)电解液混和(2)电解液注入(3)电解液检查(4)电解液排放3 电解槽检查(1)外观检查(2)内部检查(3)再紧固规程4 纸型隔板更换5 渗透渗漏检查6 KOH过滤器更换7 给水过滤器更换8 KOH泵检查9 阀门和调节器维修和校验(1)电磁阀(2)差压调节器(3)背压调节器(4)止回阀和安全阀10 氧中氢监测器维修及校验(1)流量控制器(2)过滤器罐(3)温度传感器11 系统试压12 差压变速器13 KOH流量开关检查14 给水泵起动及冲洗15 给水检测器检查16 干燥器维修(1)孔板维修(2)止回阀维修(3)分子筛更换(4)气体过滤器更换17 温度调节阀检查第五节排除故障指南附录A目录系统组件图1 框架组件图号;A-12 电解槽组件图号;A-23 给水和冷却水组件图号;A-34 气体控制组件图号;A-45 控制箱组件图号;A-56 干燥器组件图号;A-6附录B目录系统图1 HM管道图图号;M141562 HM-C1D2发生器接线图图号;ES-M-009第一节系统说明1 引言HM系统的基本设备配置包括两块,即氢气发生器和电源。
压力传感器说明书

MPM582 型两线制电子式压力开关
特点
·全不锈钢结构设计,传感器隔离膜片为不锈钢 316L,介质兼容性强; ·整体结构符合 IP65 防护要求; ·体积小、安装使用方便,可调整开关设置点; ·可提供 NPN 型和 PNP 型两种工作模式。
概述
该产品以两线制电流环的形式向用户提供了一个与压力控制点相应的 电信号,用于驱动后续继电器或向后续电子线路提供开关信号以实现系统 压力控制。适用于石油、化工、冶金、交通、电力等流体压力的控制。
空
继 电 器J
选型指南
MPM582
型两线制电子式压力开关
代号
[0~X1]X2 kPa 或 MPa
X1 系统最大压力 X2 开关设置点压力
代号 工作模式
1
NPN 型
2
PNP 型
代号
C1
C3
C5
P
G
A
控制范围 -0.1…0~0.01…10MPa X2=X1(10%~100%)
附加功能 M20×1.5 外螺纹压力接口,端面密封 G1/2 外螺纹压力接口 M20×1.5 外螺纹压力接口,水线密封 齐平膜片型,G1/2 外螺纹压力接口 表压型 绝压型
工作模式
MPM582 型有以下两种工作模式 NPN 型:被测压力≥设定压力时
输出电流=负载电流 PNቤተ መጻሕፍቲ ባይዱ 型:被测压力≤设定压力时
输出电流=负载电流 其余压力状态时,输出电流=漏电流 工作时必须接负载,在实际应用中负载电阻因在 200Ω~3kΩ之间,功率≥1/2W。配接感性负载时, 应在负载两端并入适当电容。
MPM582
[0~2]1.6MPa
1
C1G
氛压传感器通用流体产品说明书

No.PS※※-OMT0006-BPressure Sensor for General FluidsPSE575/576/577Safety Instructions 2 Model Identification and How to Order 8 Names of Parts of Product and Handling Precautions 9 Mounting and Installation 10 Wiring 10 Troubleshooting 12 Specification 13 Specifications 13 Dimensions 15Safety InstructionsThese safety instructions are intended to prevent hazardous situations and/or equipment damage. These instructions indicate the level of potential hazard with the labels of "Caution", "Warning" or "Danger".They are all important notes for safety and must be followed in addition to International Standards (ISO/IEC)*1), and other safety regulations*2).*1) ISO 4414: Pneumatic fluid power -- General rules relating to systems.ISO 4413: Hydraulic fluid power -- General rules relating to systems.IEC 60204-1: Safety of machinery -- Electrical equipment of machines .(Part 1: General requirements)ISO 10218: Manipulating industrial robots -Safety. etc.*2) High Pressure Gas Safety Law.Caution Caution indicates a hazard with a low level of risk which, if not avoided, couldresult in minor or moderate injury.Warning Warning indicates a hazard with a medium level of risk which, if not avoided,could result in death or serious injury.Danger Danger indicates a hazard with a high level of risk which, if not avoided, willresult in death or serious injury.Warning1. The compatibility of the product is the responsibility of the person who designs theequipment or decides its specifications.Since the product specified here is used under various operating conditions, its compatibility withspecific equipment must be decided by the person who designs the equipment or decides itsspecifications based on necessary analysis and test results.The expected performance and safety assurance of the equipment will be the responsibility of the person who has determined its compatibility with the product.This person should also continuously review all specifications of the product referring to its latestcatalog information, with a view to giving due consideration to any possibility of equipment failure when configuring the equipment.2. Only personnel with appropriate training should operate machinery and equipment.The product specified here may become unsafe if handled incorrectly.The assembly, operation and maintenance of machines or equipment including our products must be performed by an operator who is appropriately trained and experienced.3. Do not service or attempt to remove product and machinery/equipment until safety isconfirmed.1. The inspection and maintenance of machinery/equipment should only be performed after measuresto prevent falling or runaway of the driven objects have been confirmed.2. When the product is to be removed, confirm that the safety measures as mentioned above areimplemented and the power from any appropriate source is cut, and read and understand the specific product precautions of all relevant products carefully.3. Before machinery/equipment is restarted, take measures to prevent unexpected operation and malfunction.4. Contact SMC beforehand and take special consideration of safety measures if theproduct is to be used in any of the following conditions.1. Conditions and environments outside of the given specifications, or use outdoors or in a placeexposed to direct sunlight.2. Installation on equipment in conjunction with atomic energy, railways, air navigation, space, shipping,vehicles, military, medical treatment, combustion and recreation, or equipment in contact with food and beverages, emergency stop circuits, clutch and brake circuits in press applications, safety equipment or other applications unsuitable for the standard specifications described in the product catalog.3. An application which could have negative effects on people, property, or animals requiring specialsafety analysis.4. Use in an interlock circuit, which requires the provision of double interlock for possible failure byusing a mechanical protective function, and periodical checks to confirm proper operation.Safety InstructionsCaution1.The product is provided for use in manufacturing industries.The product herein described is basically provided for peaceful use in manufacturing industries.If considering using the product in other industries, consult SMC beforehand and exchange specifications or a contract if necessary.If anything is unclear, contact your nearest sales branch.Limited warranty and Disclaimer/Compliance Requirements The product used is subject to the following "Limited warranty and Disclaimer" and "Compliance Requirements".Read and accept them before using the product.Limited warranty and Disclaimer1. The warranty period of the product is 1 year in service or 1.5 years after the product isdelivered,whichever is first.*2)Also, the product may have specified durability, running distance or replacement parts.Please consult your nearest sales branch.2. For any failure or damage reported within the warranty period which is clearly ourresponsibility, a replacement product or necessary parts will be provided.This limited warranty applies only to our product independently, and not to any other damage incurred due to the failure of the product.3. Prior to using SMC products, please read and understand the warranty terms anddisclaimers noted in the specified catalog for the particular products.*2) Vacuum pads are excluded from this 1 year warranty.A vacuum pad is a consumable part, so it is warranted for a year after it is delivered.Also, even within the warranty period, the wear of a product due to the use of thevacuum pad or failure due to the deterioration of rubber material are not covered bythe limited warranty.Compliance Requirements1. The use of SMC products with production equipment for the manufacture of weapons ofmass destruction (WMD) or any other weapon is strictly prohibited.2. The exports of SMC products or technology from one country to another are governed bythe relevant security laws and regulation of the countries involved in the transaction. Prior to the shipment of a SMC product to another country, assure that all local rules governing that export are known and followed.CautionSMC products are not intended for use as instruments for legal metrology.Products that SMC manufactures or sells are not measurement instruments that are qualified by pattern approval tests relating to the measurement laws of each country.Therefore, SMC products cannot be used for business or certification ordained by the measurement laws of each country.Caution■After maintenance is complete, perform appropriate functional inspections and leak tests.Stop operation if the equipment does not function properly or there is a leakage of fluid.When leakage occurs from parts other than the piping, the product might be faulty.Disconnect the power supply and stop the fluid supply.Do not apply fluid under leaking conditions.Safety cannot be assured in the case of unexpected malfunction.■Use within the specified operating pressure.Otherwise it can cause damage to the Pressure Sensor or inability to measure correctly.If fluid is supplied at a pressure exceeding the proof pressure, the ceramic diaphragm will be damaged. A significantly damaged diaphragm will result in external leakage. In addition, the power supply is short circuited depending on the applied fluid. Please use a power supply which includes short circuit protection.■NOTE○Follow the instructions given below when designing, selecting and handling the product.●The instructions on design and selection (installation, wiring, environment, adjustment,operation, maintenance, etc.) described below must also be followed.*Product specifications∙Use the specified voltage.Otherwise failure or malfunction can result.∙Applicable fluid is a fluid that does not corrode C3604 + electroless nickel plated, AI203 (aluminum oxide) and FKM.Do not use a fluid containing chemicals, synthetic oils including organic solvent, salt and corrosive gases.Otherwise, damage to the product and malfunction can result.Check the details of the specifications before using.∙Reserve a space for maintenance.Allow sufficient space for maintenance when designing the system.∙A ceramic diaphragm type pressure sensor is used in this product. The ceramic diaphragm can be damaged by overpressure from hydraulic shock, which can be generated when condensate in the fluid collides with the sensor during pressure fluctuation. This is also known as "water hammer".To mitigate hydraulic shock, it is recommended to insert an orifice between the fluid and the sensor. A gas pocket also needs to be between the orifice and the sensor to cushion the shock pulse. The sensor would then need to be located above the orifice with the orifice mounted vertically so that no fluid gets between the orifice and sensor.Some recommended and NOT recommended examples are shown in the following figure. PartnumbersZS-31-X175 or X188 are applicable orifices (called throttles in product literature).●Product handling*Installation∙Follow the specified tightening torque.Excessive tightening torque can break the Pressure Sensor.Insufficient tightening torque can displace the Pressure Sensor from the original position or loosen the mounting∙When piping, apply a spanner vertically to the piping section for the sensor.Applying the wrench in other position can break the Pressure Sensor∙Be sure to ground terminal FG when using a commercially available switch-mode power supply.∙Do not drop, hit or apply shock to the Pressure Sensor.Otherwise damage to the internal parts can result, causing malfunction.∙Do not pull the lead wire forcefully, not lift the product by pulling the lead wire. (Tensile force 35N or less) Hold the body when handling to avoid the damage of the Pressure Sensor lead to cause the failure andmalfunction.∙For piping of the Pressure Sensor, hold the piping with a spanner on the metal part of the piping(Piping attachment).Holding other part with spanner leads to damage the Pressure Sensor.∙Eliminate any dust left in the piping by air blow before connecting the piping to the product.Otherwise it can cause damage or malfunction.∙Do not insert metal wires or other foreign matter into the pressure measurement port.It can damage the Pressure Sensor causing failure or malfunction.*Wiring∙Do not pull the lead wires.In particular, never lift a Pressure Sensor equipped with fitting and piping by holding the lead wires.∙Avoid repeatedly bending or stretching the lead wire, or placing heavy load on them.Repetitive bending stress or tensile stress can cause the sheath of the wire to peel off, or breakage of the wire.If the lead wire can move, fix it near the body of the product.The recommended bend radius of the lead wire is 6 times the outside diameter of the sheath, or 33 times the outside diameter of the insulation material, whichever is larger.Replace the damaged lead wire with a new one.∙Wire correctly.Incorrect wiring can break the Pressure Sensor.∙Do not perform wiring while the power is on.Otherwise damage to the internal parts can result, causing malfunction.∙Do not route wires and cables together with power or high voltage cables.Otherwise the product can malfunction due to interference of noise and surge voltage from power and highvoltage cables to the signal line. Route the wires (piping) of the product separately from power or high voltage cables.∙Confirm proper insulation of wiring.Poor insulation (interference from another circuit, poor insulation between terminals, etc.) can lead to excess voltage or current being applied to the product, causing damage.∙Keep wiring as short as possible to prevent interference from electromagnetic noise and surge voltage.Do not use a cable longer than 30 m.Wire the DC(-) line(blue) as close as possible to the power supply.∙Ensure that the FG terminal is connected to ground when using a commercially available switch-mode power supply. When a switch-mode power supply is connected to the product, switching noise will be superimposed and the product specification can no longer be met. This can be prevented by insertinga noise filter, such as a line noise filter and ferrite core, between the switch-mode power supply andthe product, or by using a series power supply instead of a switch-mode power supply.*Environment∙Do not use the product in area that is exposed to corrosive gases, chemicals, sea water, water or steam.Otherwise failure or malfunction can result.∙Do not use in a place where the product could be splashed by oil or chemicals.If the product is to be used in an environment containing oils or chemicals such as coolant or cleaning solvent, even for a short time, it may be adversely affected (damage, malfunction, or hardening of the lead wires).∙Do not use in an area where electrical surges are generated. (EMI or Electro Magnetic Interference) If there is equipment which generates a large amount of EMI (solenoid type lifter, high frequency induction furnace, motor, etc.) close to the Pressure Sensor, this may cause deterioration or breakage of the internal circuit of the Pressure Sensor. Avoid sources of surge generation and crossed lines.∙The product is CE marked, but not immune to lightning strikes. Take measures against lightning strikes in the system.∙Mount the product in a place that is not exposed to vibration or impact.Otherwise failure or malfunction can result.∙Prevent foreign matter such as remnant of wires from entering the Pressure Sensor.Take proper measures for the remnant not to enter the Pressure Sensor in order to prevent failure or malfunction. ∙Do not use the product in an environment that is exposed to temperature cycle.Heat cycles other than ordinary changes in temperature can adversely affect the inside of the product.∙Do not expose the product to direct sunlight.If using in a location directly exposed to sunlight, shade the product from the sunlight.Otherwise failure or malfunction can result.∙Keep within the specified fluid and ambient temperatures range.The fluid and ambient temperatures should be -10 to 60 °C. Operation under low temperature leads to cause damage or operation failure due to frozen moist in the fluid or air.Protection against freezing is necessary. Air dryer is recommended for elimination of drain and water.Avoid sudden temperature change even within specified temperature.∙Do not operate close to a heat source, or in a location exposed to radiant heat.Otherwise malfunction can result.*Adjustment and Operation∙Do not short-circuit the load.∙If using the product to detect very small pressure rates, warm up the product for 20 to 30 minutes first.There will be a drift on the analogue output of approximate ±1% immediately after the power supply is turned on, within 10 minutes.*Maintenance∙Turn off the power supply, stop the supplied air, exhaust the residual pressure and verify the release of air before performing maintenance.There is a risk of unexpected malfunction.∙Perform regular maintenance and inspections.There is a risk of unexpected malfunction.∙Perform drainage regularly.If condensate enters the secondary side, it can cause operating failure of pneumatic equipment.∙Do not use solvents such as benzene, thinner etc. to clean the Pressure Sensor.They could damage the surface of the body and erase the markings on the body.Use a soft cloth to remove stains. For heavy stains, use a cloth soaked with diluted neutral detergent and fully squeezed, then wipe up the stains again with a dry cloth.○Names of parts of product•Only fluids which are non-corrosive to C3604 + electroless nickel plated, AI203 (aluminum oxide) and FKM should be used.○Handling precautions■Wiring○Connector pin numbersWhen the lead wire and connector (ZS-37-A or ZS-37-B) designated for the PSE570 is used, the wire colours will apply as shown in the diagram.Connector pin numbers (on the lead wire)•ZS-37-A•ZS-37-B*: The unconnected terminals are used in SMC, so please do not connect them.○How to connect the body and the lead wire and connector∙Align the lead wire connector with the connector key groove, and insert vertically.∙Connection is complete when the knurled part is fully tightened. Check that the connection is not loose.○Internal circuit and wiring example∙Output specificationPSE57□-02Voltage output: 1 to 5 VOutput impedance: Approx. 1 kΩPSE57□-02-28Current output: 4 to 20 mAAllowable load impedance:500 Ω or less (at 24 VDC)100 Ω or less (at 12 VDC)*: The unconnected terminals are used in SMC, so please do not connect them.○Analogue outputModel Rated pressure range A BPSE575 0 to 2 MPa 0 2 MPaPSE576 0 to 5 MPa 0 5 MPaPSE577 0 to 10 MPa 0 10 MPa■Dimensions∙Lead wire and M12 connector ZS-37-AZS-37-B∙Adapter with throttleZS-31-X1754-14-1, Sotokanda, Chiyoda-ku, Tokyo 101-0021 JAPANTel: + 81 3 5207 8249 Fax: +81 3 5298 5362URL Note: Specifications are subject to change without prior notice and any obligation on the part of the manufacturer.。
CO 110 CO 氢氧化物传感器说明书

CO transmitterCO 110KEY POINTSMaterial : ABS V0Protection :- duct model : IP65- ambient model : IP20Display : LCD 10 digits. Size : 50 x 17 mmHeight of digits : Value : 10 mm ; Unit : 5 mmCable gland (only for duct model) : for cables Ø 8 mm maximumWeight : 138 g (ambient model) ; 150 g (duct model)- Range from 0 to 500 ppm- 0-10 V active output, power supply 24 Vac/Vdc (3-4 wires) or 4-20 mA output, passive loop, power supply from 16 to 30 Vdc (2 wires)- ABS V0 housing, IP65 (depending on model), with or without display - “¼ turn” system mounting with wall-mount plate - Housing with simplified mounting systemFEA TURES OF HOUSINGTECHNICAL FEA TURESUnit of measurement ppmMeasuring range From 0 to 500 ppmAccuracy*±3 ppm or 3% of the measured value Type of sensor Electrochemical sensor Response time T63 = 35 s Resolution 0.1 ppm Type of fluid Air and neutral gas Working temperature From 0 to +50 °C Storage temperatureFrom -10 to +70 °CPART NUMBERCO110To order, just add the codes to complete the part number :Power supply / OutputA : Active – 24 Vac/Vdc – 0-10 V P : Passive – 16/30 Vdc – 4-20 mADisplayO : with display N : without displayExample : CO110-POACO transmitter, 4-20 mA passive transmitter, with display and duct probe*All the accuracies indicated in this technical datasheet were stated in laboratory conditions, and can be guaranteed for measurements carried out in the same conditions, or carried out with calibration compensation.90 mm41 mm80150 mm46 mm90 mm109 m mType of probeA : Duct S : ambientDuct modelAmbient modelTECHNICAL SPECIFICA TIONSCONNECTIONSInactive switch Output / Power supply- active 0-10 V (power supply 24 Vac/Vdc ± 10%), 3-4 wires - passive loop 4-20 mA (power supply 16/30 Vdc), 2 wires - maximum load : 500 Ohms (4-20 mA)- minimum load : 1 K Ohms (0-10 V)Consumption2 VA (0-10 V) or max. 22 mA (4-20 mA)Electro-magnetical compatibility EN61326Electrical connection Screw terminal block for cables Ø0.05 to 2.5 mm 2 Communication to PC Kimo USB-mini Din cable EnvironmentAir and neutral gasInside the front housingELECTRICAL CONNECTIONS – as per NFC15-100 standardActive switchThis connection must be made by a qualified technician . To make the connection, the transmitter must not be energized.V-+0-10 V output76L N Power supply 24 Vac class IIN L12+5VCO4GND -7+6-Power supply 24 Vdc-+or4 wiresTo make a 3-wire connection, before powering up the transmitter, please connect the output ground to the input ground. See drawing below.123+54-7+6--Power supply 24 Vdc+-3 wires4 wires3 wires+123+54N 7L 6--Power supply 24 Vac class IIL N3 wires+For CO110-A models with 0-10 V output – active :Regulator display orPLC/BMS passive typeVVRegulator display or PLC/BMS passive type0-10 V outputRegulator display or PLC/BMS passive type0-10 V outputVCOGND Electrochemical sensor3Power supply terminal blockOutput terminal blockLCC-S software connectionFixed back housingRemovable front faceCable glandorFor CO110-P models with 4-20 mA output – passive :2 wiresIP 57+6-Power supply 16-30 VdcVdc A+-IP 57+6-Vdc -2 wires+A 2 wiresSETTINGS AND USE OF THE TRANSMITTER➢ConfigurationTo configure the transmitter, it must not be energized. Then you can make the required settings thanks to the DIP switches as shown on the drawing below. When the transmitter is configured, you can power it up.To configure the transmitter, unscrew the 4 screws of the housing then open it. DIP switches allowing the different settings are accessible.1234............Display/regulator/PLCpassive type To set a measuring range, put the on-off switches 2, 3 and 4 as shown below :➢Measuring range setting1234Combination 11234Combination 2Display/regulator/PLCactive type+-On-off switchSetting ofmeasuring rangeFrom 0 to 500 ppm :1234Combination 3From 0 to 100 ppm :From 0 to 200 ppm :MOUNTINGTo mount the transmitter, mount the ABS plate on the wall (drilling : Ø6 mm, screws and pins are supplied).Insert the transmitter on the fixing plate (see A on the drawing beside). Rotate the housing in clockwise direction until you hear a “click” which confirms that the transmitter is correctly installed.7.584.54050687537.523.7514AAAmbient model has not any fixing plate.4 fixing holes are inside the back housing. Use them to install the transmitter on the required location.16-30 VdcAn easy and friendly configuration with the software !It is possible to configure intermediary ranges.Attention : the minimum difference between the minimum scale and the maximum scale is 20.Example : for a 0-500 ppm transmitter, the minimum delta is 20 ppm. So the transmitter could be configure from 0 to 70 ppm from 0 to 20 ppm.• To access to the configuration via software :- Set the switch as shown beside.- Connect the cable of the LCC-S to the connection of the transmitter.• To configure the transmitter, please refer to the LCC-S user manual.Caution : The configuration of the parameters can be done either by DIP switch, or by software (you cannot combine both solutions).CONFIGURA TION VIA LCC-S SOFTW ARE (optional)1234Switch 1orF T a n g – t r a n s m i t t e r _C O 110 – 08/03/13 – R C S (24) P ér i g u e u x 349 282 095 N o n -c o n t r a c t u a l d o c u m e n t – W e r e s e r v e t h e r i g h t t o m o d i f y t h e c h a r a c t e r i s t i c s o f o u r p r o d u c t s w i t h o u t p r i o r n o t i c e .MAINTENANCEPlease avoid any aggressive solvent. Please protect the transmitter and its probes from any cleaning product containing formol, that may be used for cleaning rooms or ducts.OPTIONS AND ACCESSORIES●KIAL-100A : Power supply class 2 , 230 Vac input, 24 Vac output ●LCC-S :configuration software with USB cable。