CA6150数控车床主轴箱及传动系统的设计
机械机床毕业设计16CA6150数控车床主轴箱及传动系统系统的设计业设计

机械机床毕业设计16CA6150数控车床主轴箱及传动系统系统的设计业设计一、设计背景目前,数控车床是机械加工行业中常用的一种设备。
其主要作用是通过数控系统控制刀具的运动轨迹,对工件进行加工。
本设计的目标是设计一个适用于16CA6150数控车床的主轴箱及传动系统,以提高车床的加工准确性和效率。
二、设计要求1.主轴箱及传动系统要具备足够的刚性和稳定性,以确保整个车床在工作过程中不发生振动和变形;2.主轴箱传动系统的设计应使得主轴的旋转速度能够达到要求,并且有一定的速度范围可调;3.主轴箱传动系统的设计应保证传动效率高,噪音低,并且易于维护和保养;4.主轴箱和传动系统的设计应满足机械加工的要求,对于各个工件的加工均能保证高精度和高质量。
三、主轴箱设计主轴箱是数控车床中的核心部件,其作用是连接主轴和机床床身,并提供主轴的旋转运动。
为了保证主轴和工件的高精度加工,主轴箱设计应满足以下要求:1.主轴箱整体结构应具备足够的刚性和稳定性;2.主轴箱应具备一定的自冷却和监测功能,以保证主轴的温度和振动处于合理范围内;3.主轴箱应具备一定的调节装置,方便对主轴进行润滑和保养。
四、传动系统设计传动系统是主轴箱的重要组成部分,其作用是将动力传递给主轴,使得主轴能够旋转。
在设计传动系统时,应满足以下要求:1.传动系统应选择合适的传动方式,如齿轮传动、带传动等;2.传动系统的设计应保证传动效率高、噪音低,且易于维护和保养;3.传动系统应满足主轴旋转速度的要求,并具备一定的速度调节范围;4.传动系统应具备自动化控制功能,以便实现数控车床的自动操作。
五、总结本设计对16CA6150数控车床的主轴箱及传动系统进行了设计,并提出了相应的要求。
在设计主轴箱和传动系统时,应注重刚性和稳定性的提升,以及传动效率的提高。
同时,还应考虑主轴箱的自冷却和监测功能,以及传动系统的自动化控制功能。
通过合理设计和选用适当的材料和部件,可以提高数控车床的加工准确性和效率,满足机械加工的要求。
C6150车床主轴箱箱体加工工艺及工装夹具设计

C6150车床主轴箱箱体加工工艺及工装夹具设计1.C6150车床主轴箱箱体加工工艺主轴箱箱体一般由铸铁材料制成,其加工工艺主要包括以下几个步骤:(1)铸造准备:对铸铁材料进行熔炼、净化和浇铸前的处理,确保铸件质量。
(2)铸件浇铸:将熔化的铸铁材料倒入模具中,使其冷却、凝固成型。
(3)铸件脱模:待铸件冷却后,从模具中取出,进行清理和修整。
(4)精密加工:对铸件进行加工,包括切割、铣削、钻孔等工序,以使得箱体尺寸和形状精确到达要求。
(5)表面处理:对箱体表面进行打磨、抛光,以提高外观质量。
(6)检测和装配:对加工好的主轴箱箱体进行检测,确保质量达到要求,然后进行组装。
在主轴箱箱体的加工过程中,合理设计工装夹具可以提高加工效率和加工质量,减少劳动强度。
(1)定位夹具设计:主要用于确定箱体的位置和角度,以保证加工精度。
定位夹具可以根据箱体形状和尺寸设计,一般采用刚性夹具,如V型块。
(2)夹紧夹具设计:用于夹紧箱体,以防止其在加工过程中发生松动或位移。
夹紧夹具可以采用螺栓和垫圈进行固定,或者采用气动或液压夹紧装置。
(3)切削夹具设计:用于加工箱体的切削过程,包括刀具和刀架的选择和安装。
切削夹具要根据加工要求和箱体材料的切削特性来设计,以保证加工质量和效率。
(4)保护夹具设计:用于保护箱体的外表面和内孔。
保护夹具可以采用橡胶垫和保护套等材料进行设计,以确保箱体不被切削工具碰伤。
(5)检测夹具设计:用于检测箱体的尺寸和形状,以确保其符合加工要求。
检测夹具可以采用测量工具和传感器等设备进行设计,以确保检测的准确性和可靠性。
总之,C6150车床主轴箱箱体加工工艺和工装夹具设计是车床加工中的重要环节,可以通过合理的工艺和夹具设计来提高加工效率和加工质量。
C6150主轴箱箱体的加工工艺及其工装设计

xx学院毕业设计(论文)C6150主轴箱箱体的加工工艺及其工装设计所在学院专业班级姓名学号指导老师年月日诚信承诺我谨在此承诺:本人所写的毕业论文《C6150主轴箱箱体的加工工艺及其工装设计》均系本人独立完成,没有抄袭行为,凡涉及其他作者的观点和材料,均作了注释,若有不实,后果由本人承担。
承诺人(签名):年月日2摘要零件的加工工艺编制,在机械加工中占有非常重要的地位,零件工艺编制得合不合理,这直接关系到零件最终能否达到质量要求;夹具的设计也是不可缺少的一部分,它关系到能否提高其加工效率的问题。
因此这两者在机械加工行业中是至关重要的环节。
这次设计主要经历了两个阶段:第一阶段是机械加工工艺规程设计,第二阶段是专用夹具设计。
通过对C6150 主轴箱体零件图的分析及结构形式的了解,从而对主轴箱体进行工艺分析、工艺说明及加工过程的技术要求和精度分析。
然后再对主轴箱体的底孔、轴承孔的加工进行夹具设计与精度和误差分析,该工艺与夹具设计结果能应用于生产要求。
通过此次设计,使我们基本掌握了零件的加工过程分析、工艺文件的编制、专用夹具设计的方法和步骤等。
学会了查相关手册、选择使用工艺装备等等。
关键词:加工工艺,夹具设计,机床,分析I宁波大红鹰学院毕业设计(论文)AbstractPreparation of parts of the processing technology, processing machinery occupies a very important position, part preparation process was reasonable, which is directly related to the final part quality requirements can be met; fixture design is an indispensable part, it is related to whether can improve its processing efficiency problem. Therefore, both in the machining industry is a very important link.This design mainly experienced two stages: the first stage is the machining process planning, the second stage is the special fixture design.Based on the C6150 spindle box parts diagram analysis and the structural form of understanding, thus the spindle box for process analysis, process explanation and analysis the technical requirement and the precision. Then the spindle box bottom, bearing hole processing fixture design and precision and error analysis, the craft and the jig design results can be applied to production requirements.Through this design, we mastered the basic parts of the process analysis, process documentation, special fixture design methods and steps. Learn to check the relevant manual, choose to use the technology and equipment and so on..Key Words:Processing, fixture design, machine tool, analysisII目录摘要 (I)Abstract (II)目录 (III)第1章绪论 (4)1.1车床发展史 (4)1.2 数控车床的概念 (4)1.3 主轴箱的功用 (5)1.4 本课题的研究对象 (6)第2章C6150主轴箱体加工工艺规程设计 (6)2.1 方案论证 (6)2.2确定方案 (7)2.3 具体方案设计 (9)2.3.1 零件的分析 (9)2.3.2 编写工艺路线 (9)2.3.3机械加工工艺分析 (10)2.3.4 确定切削用量及基本工时(机动时间) (11)第3章专用夹具设计 (22)的夹具设计 (22)3.1加工顶面螺纹孔4-M12-6H底孔103.1.1定位基准的选择 (23)3.1.2切削力的计算与夹紧力分析 (23)3.1.3夹紧元件及动力装置确定 (23)3.1.4钻套、衬套、钻模板及夹具体设计 (23)3.1.5夹具精度分析 (25)3.1.6夹具设计及操作的简要说明 (26)总结 (27)参考文献 (28)致谢 (29)III第1章绪论1.1车床发展史古代的车床是靠手拉或脚踏,通过绳索使工件旋转,并手持刀具而进行切削的。
C6150铣床主轴箱箱体加工工艺及工装夹具设计
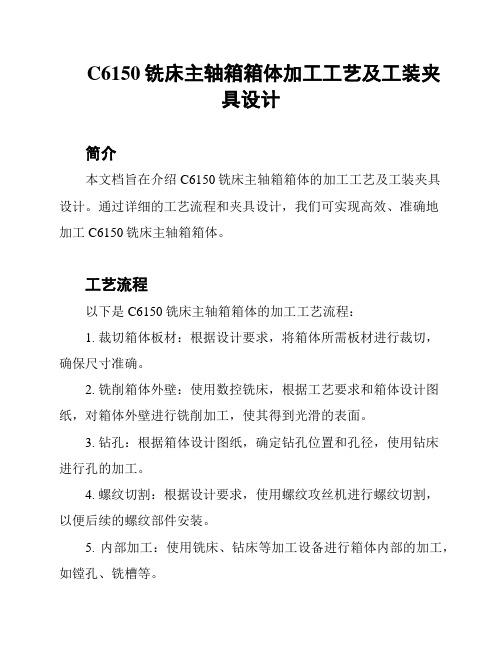
C6150铣床主轴箱箱体加工工艺及工装夹具设计简介本文档旨在介绍C6150铣床主轴箱箱体的加工工艺及工装夹具设计。
通过详细的工艺流程和夹具设计,我们可实现高效、准确地加工C6150铣床主轴箱箱体。
工艺流程以下是C6150铣床主轴箱箱体的加工工艺流程:1. 裁切箱体板材:根据设计要求,将箱体所需板材进行裁切,确保尺寸准确。
2. 铣削箱体外壁:使用数控铣床,根据工艺要求和箱体设计图纸,对箱体外壁进行铣削加工,使其得到光滑的表面。
3. 钻孔:根据箱体设计图纸,确定钻孔位置和孔径,使用钻床进行孔的加工。
4. 螺纹切割:根据设计要求,使用螺纹攻丝机进行螺纹切割,以便后续的螺纹部件安装。
5. 内部加工:使用铣床、钻床等加工设备进行箱体内部的加工,如镗孔、铣槽等。
6. 表面处理:对箱体外表面进行喷漆、砂光等表面处理,提高外观质量和耐腐蚀性能。
7. 总装:将各个部件进行组装,确保箱体完整并达到设计要求。
8. 检验:对加工完成的箱体进行检验,确保尺寸、外观等符合要求。
工装夹具设计为了确保加工过程的稳定性和准确性,需要设计适用的工装夹具。
以下是针对C6150铣床主轴箱箱体加工的工装夹具设计要点:1. 定位夹具:设计合适的定位夹具,确保箱体定位准确且稳定。
2. 固定夹具:设计合适的固定夹具,保持箱体在加工过程中的稳定性,防止移位或震动。
3. 安全夹具:考虑工人安全,设计适用的安全夹具,确保操作过程中人员不受伤。
4. 加工导向夹具:设计适用的加工导向夹具,可以确保箱体在加工过程中的位置准确,避免误差。
以上是C6150铣床主轴箱箱体加工工艺及工装夹具设计的简要介绍。
通过遵循这些工艺流程和合理设计工装夹具,我们能够高效、准确地加工C6150铣床主轴箱箱体。
C6150普通车床主传动系统的数控改造设计
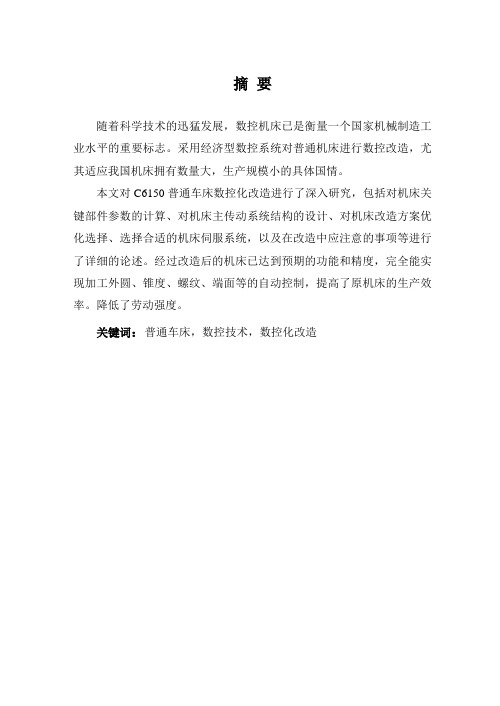
摘要随着科学技术的迅猛发展,数控机床已是衡量一个国家机械制造工业水平的重要标志。
采用经济型数控系统对普通机床进行数控改造,尤其适应我国机床拥有数量大,生产规模小的具体国情。
本文对C6150普通车床数控化改造进行了深入研究,包括对机床关键部件参数的计算、对机床主传动系统结构的设计、对机床改造方案优化选择、选择合适的机床伺服系统,以及在改造中应注意的事项等进行了详细的论述。
经过改造后的机床已达到预期的功能和精度,完全能实现加工外圆、锥度、螺纹、端面等的自动控制,提高了原机床的生产效率。
降低了劳动强度。
关键词:普通车床,数控技术,数控化改造AbstractWith the rapid devlopment of science and technology, CNC is becoming an important symbol to measure a country,s machinery manufaucturing level .Using economic numerical control system to transform General machine tools, adapts to our country which has large number General machine tools and is small scale production.The paper studied thoroughly the retrofitting technology on C6150 universal lathe ,including thecomutating of parameters of key components, the design of lathe structure ,optimization of the retrofitting scheme,as well as matters needing attention of reform in detail ,etc.The result shows that the machine tools achieveed expected function and precision after retrofitting ,the machine can sufficienfly execute automatic control on outside diameter taper screw ends etc, it important the production rate of the machine and decreases the labor stress from the operator.Key words: Unversal Lathe Numerical Technology Numerical Control Transformation目录1 绪论 (1)1.1概述 (1)1.1.1国内外数控机床的发展状况 (1)1.1.2 国内外数控机床改造的状况 (2)1.1.3机床数控化改造的优点 (3)1.1.4 机床数控化改造的必要性和可能性 (4)1.2本课题的目的和意义 (5)2 CA6150普通车床主传动系统数控化改造 (6)2.1C6150车床简介 (6)2.1.1 原机床功能 (6)2.1.2 原机床精度 (6)2.1.3 原机床的主要技术参数 (7)2.1.4 原机床的传动系统 (8)2.1.5 普通车床的数控化改造 (8)2.2总体方案的确定 (9)2.3数控机床主传动系统 (9)2.3.1 概述 (9)2.3.2 与普通机床比较,数控机床主传动系统具有下列特点: (10)2.3.3 数控机床主传动系统配置方式 (10)2.3.4 主传动系统可按不同的特征来分类 (12)2.4数控改造对机械传动系统的要求 (13)2.5无极变速传动链的设计 (13)2.5.1 主运动参数计算 (13)2.5.2 主轴最大切削功率及电动机的确定 (14)2.5.3 主传动系统的设计 (16)2.5.4 确定各级传动副齿轮的齿数 (18)2.5.5 轴及齿轮计算转矩的确定 (20)2.5.6 各齿轮副模数计算 (21)2.5.7 各轴间中心距的计算 (23)2.5.8 确定各轴最小直径 (23)2.5.9 齿轮参数的计算 (24)3 主轴组件的设计 (26)3.1主轴组件的基本要求 (26)3.2主轴 (28)3.2.1 主轴的构造 (28)3.2.2 主轴的材料和热处理 (28)3.2.3 主轴的技术要求 (29)3.3主轴部件轴承的配置 (30)3.4主轴主要结构参数的确定 (36)3.5主轴组件校核 (37)3.6主轴脉冲编码器的加装 (42)4 刀架及导轨部分的改造设计 (44)4.1刀架改造设计 (44)4.1.1 电动刀架的选择 (44)4.1.2 电动刀架的工作原理及控制 (44)4.1.3 电动刀架的安装 (46)4.2机床尾座的改造设计 (46)4.3机床导轨部分的改造设计 (47)4.3.1 聚四氟乙烯基软带的主要性能 (47)4.3.2聚四氟乙烯基软带的粘接工艺 (48)4.4伺服驱动系统的选择 (49)4.5数控改造的控制方式选择 (50)4.5.1 步进电机拖动的开环方式 (50)4.5.2 交/直流伺服电机拖动,编码器反馈的半闭环数控方式 (51)4.5.3 异步电动机或直流电动机拖动,光栅测量反馈的闭环控制方式 (51)结束语 (53)致谢 (54)参考文献 (55)1 绪论1.1概述1.1.1国内外数控机床的发展状况1946年第一台计算机在美国诞生,1952年世界第一台数控机床也在美国诞生,用于三轴镗铣床的加工,自此,数控机床的发展紧随着微电子技术和计算机技术的发展而发展,近60年来,数控机床经历了两个阶段,六个时代的发展过程。
C6150车床数控改造主传动系统设计
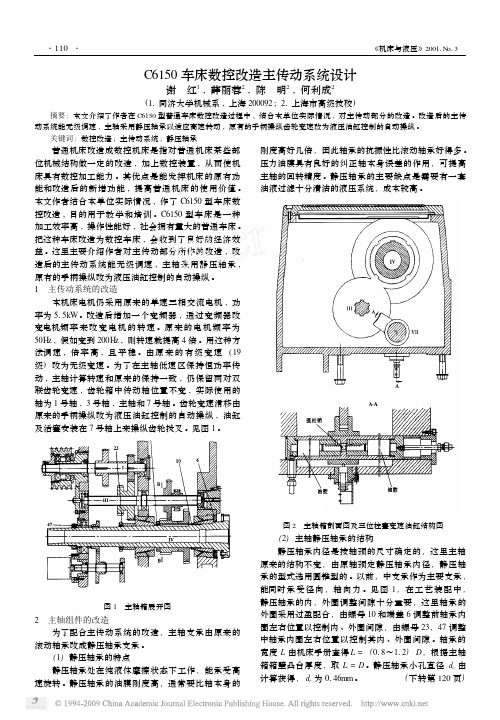
C6150车床数控改造主传动系统设计谢 红1,薛丽蓉2,陈 明2,何利成2(11同济大学机械系,上海200092;21上海市高级技校)摘要:本文介绍了作者在C6150型普通车床数控改造过程中,结合本单位实际情况,对主传动部分的改造。
改造后的主传动系统能无级调速,主轴采用静压轴承以适应高速转动,原有的手柄操纵齿轮变速改为液压油缸控制的自动操纵。
关键词:数控改造;主传动系统;静压轴承 普通机床改造成数控机床是指对普通机床某些部位机械结构做一定的改造,加上数控装置,从而使机床具有数控加工能力。
其优点是能发挥机床的原有功能和改造后的新增功能,提高普通机床的使用价值。
本文作者结合本单位实际情况,作了C6150型车床数控改造,目的用于教学和培训。
C6150型车床是一种加工效率高,操作性能好,社会拥有量大的普通车床。
把这种车床改造为数控车床,会收到了良好的经济效益。
这里主要介绍作者对主传动部分所作的改造,改造后的主传动系统能无级调速,主轴采用静压轴承,原有的手柄操纵改为液压油缸控制的自动操纵。
1 主传动系统的改造本机床电机仍采用原来的单速三相交流电机,功率为515kW 。
改造后增加一个变频器,通过变频器改变电机频率来改变电机的转速。
原来的电机频率为50H z ,假如变到200H z ,则转速就提高4倍。
用这种方法调速,倍率高,且平稳。
由原来的有级变速(19级)改为无级变速。
为了在主轴低速区保持恒功率传动,主轴计算转速和原来的保持一致,仍保留两对双联齿轮变速,齿轮箱中传动轴位置不变,实际使用的轴为1号轴,3号轴,主轴和7号轴。
齿轮变速滑移由原来的手柄操纵改为液压油缸控制的自动操纵,油缸及活塞安装在7号轴上来操纵齿轮拨叉。
见图1。
图1 主轴箱展开图2 主轴组件的改造为了配合主传动系统的改造,主轴支承由原来的滚动轴承改成静压轴承支承。
(1)静压轴承的特点静压轴承处在纯液体摩擦状态下工作,能承受高速旋转。
静压轴承的油膜刚度高,通常要比轴本身的刚度高好几倍,因此轴承的抗振性比滚动轴承好得多。
C6150车床数控改造主传动系统设计
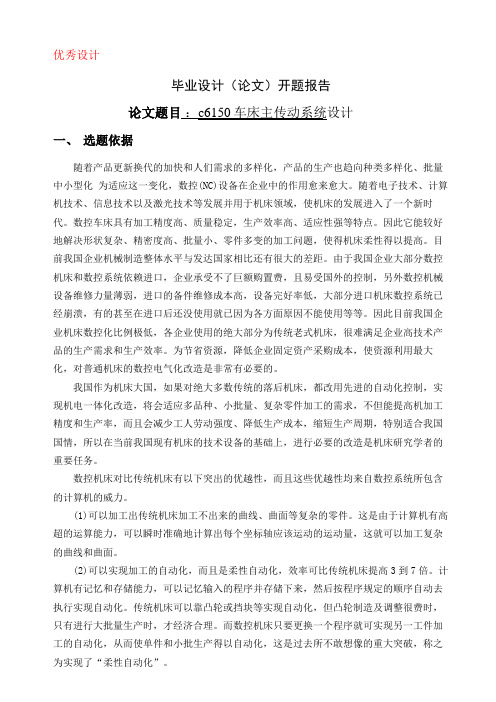
优秀设计毕业设计(论文)开题报告论文题目:c6150车床主传动系统设计一、选题依据随着产品更新换代的加快和人们需求的多样化,产品的生产也趋向种类多样化、批量中小型化为适应这一变化,数控(NC)设备在企业中的作用愈来愈大。
随着电子技术、计算机技术、信息技术以及激光技术等发展并用于机床领域,使机床的发展进入了一个新时代。
数控车床具有加工精度高、质量稳定,生产效率高、适应性强等特点。
因此它能较好地解决形状复杂、精密度高、批量小、零件多变的加工问题,使得机床柔性得以提高。
目前我国企业机械制造整体水平与发达国家相比还有很大的差距。
由于我国企业大部分数控机床和数控系统依赖进口,企业承受不了巨额购置费,且易受国外的控制,另外数控机械设备维修力量薄弱,进口的备件维修成本高,设备完好率低,大部分进口机床数控系统已经崩溃,有的甚至在进口后还没使用就已因为各方面原因不能使用等等。
因此目前我国企业机床数控化比例极低,各企业使用的绝大部分为传统老式机床,很难满足企业高技术产品的生产需求和生产效率。
为节省资源,降低企业固定资产采购成本,使资源利用最大化,对普通机床的数控电气化改造是非常有必要的。
我国作为机床大国,如果对绝大多数传统的落后机床,都改用先进的自动化控制,实现机电一体化改造,将会适应多品种、小批量、复杂零件加工的需求,不但能提高机加工精度和生产率,而且会减少工人劳动强度、降低生产成本,缩短生产周期,特别适合我国国情,所以在当前我国现有机床的技术设备的基础上,进行必要的改造是机床研究学者的重要任务。
数控机床对比传统机床有以下突出的优越性,而且这些优越性均来自数控系统所包含的计算机的威力。
(1)可以加工出传统机床加工不出来的曲线、曲面等复杂的零件。
这是由于计算机有高超的运算能力,可以瞬时准确地计算出每个坐标轴应该运动的运动量,这就可以加工复杂的曲线和曲面。
(2)可以实现加工的自动化,而且是柔性自动化,效率可比传统机床提高3到7倍。
CA6150数控车床主轴箱及传动开题报告

研究内容
目前要解决如下问题:
电动机功率的确定、滑道角度的确定、气缸型号的选择机器及材料的确定。
现基本以机械设计为主,其它为辅。
拟采取的研究方法、技术路线、实验方案及可行性分析
整个模块化MPS是由上料检测站、搬运站、加工站、安装站、安装搬运站、分类站六个部分组成的。故每一站除了要求能单独完成本站的一个动作过程(功能要求)外,还要考虑能将各站按一定顺序联接在一起,组成一个模块化生产系化,结构简单,模拟性强,操作简便。每一站就是一个模块,各自有一套独立的功能。两模块之间又能相互联系,构成一个的“系统工程”。是一台较理想的理论知识和技能训练相结合的教学设备,非常适合高等职业技术学校进行模块化教学。
(1)设计满足本站功能要求的自动机械装置,包括气动回路;
(2)根据需要选择(或设计)原动机、传动机构、执行元件;
(3)绘制本站全套机械工程图(装配图和零件图)一份;
(4)撰写设计计算说明书一份。
研究计划及预期成果
MPS是模拟生产系统(Model Produce System)的英文缩写,用于模拟一个典型的顺序控制系统。模块化MPS是用于自动化专业高级维修电工进行PLC编程与操作以及PLC联网控制技能训练的教学设备。
院系意见
主管领导签名:
年月日
已具备的条件和尚需解决的问题
在本次MPS上料检测站和搬运站机械设计中,主要解决的问题是材料的选择以及汽缸的选择;其次是对传感器的选择。
由于学校在自动化设计方面的资料比较多,以及在网上找到的资料。故本次设计的资料比较齐全。
指导教师意见
- 1、下载文档前请自行甄别文档内容的完整性,平台不提供额外的编辑、内容补充、找答案等附加服务。
- 2、"仅部分预览"的文档,不可在线预览部分如存在完整性等问题,可反馈申请退款(可完整预览的文档不适用该条件!)。
- 3、如文档侵犯您的权益,请联系客服反馈,我们会尽快为您处理(人工客服工作时间:9:00-18:30)。
毕业设计(论文)任务书指导老师课题名称CA6150车床主轴箱设计学生姓名专业班级数控70201班目录1、概述2、主运动的方案选择与主运动的设计3、确定齿轮齿数4、选择电动机5、皮带轮的设计计算6、传动装置的运动和运动参数的计算7、主轴调速系统的选择计算8、主轴刚度的校核一、概述主传动系统是用来实现机床主运动的传动系统,它应具有一定的转速(速度)和一定的变速范围,以便采用不同材料的刀具,加工不同的材料,不同尺寸,不同要求的工件,并能方便的实现运动的开停,变速,换向和制动等。
数控机床主传动系统主要包括电动机、传动系统和主轴部件,它与普通机床的主传动系统相比在结构上比较简单,这是因为变速功能全部或大部分由主轴电动机的无级调速来承担,剩去了复杂的齿轮变速机构,有些只有二级或三级齿轮变速系统用以扩大电动机无级调速的范围。
1.1数控机床主传动系统的特点与普通机床比较,数控机床主传动系统具有下列特点。
4转速高、功率大。
它能使数控机床进行大功率切削和高速切削,实现高效率加工。
5变速范围宽。
数控机床的主传动系统有较宽的调速范围,一般Ra>100,以保证加工时能选用合理的切削用量,从而获得最佳的生产率、加工精度和表面质量。
6主轴变速迅速可靠,数控机床的变速是按照控制指令自动进行的,因此变速机构必须适应自动操作的要求。
由于直流和交流主轴电动机的调速系统日趋完善,所以不仅能够方便地实现宽范围无级变速,而且减少了中间传递环节,提高了变速控制的可靠性。
7主轴组件的耐磨性高,使传动系统具有良好的精度保持性。
凡有机械摩擦的部位,如轴承、锥孔等都有足够的硬度,轴承处还有良好的润滑。
1.2 主传动系统的设计要求①主轴具有一定的转速和足够的转速范围、转速级数,能够实现运动的开停、变速、换向和制动,以满足机床的运动要求。
②主电机具有足够的功率,全部机构和元件具有足够的强度和刚度,以满足机床的动力要求。
③主传动的有关结构,特别是主轴组件要有足够高的精度、抗震性,热变形和噪声要小,传动效率高,以满足机床的工作性能要求。
④操纵灵活可靠,维修方便,润滑密封良好,以满足机床的使用要求。
⑤结构简单紧凑,工艺性好,成本低,以满足经济性要求。
1.3 数控机床主传动系统配置方式数控机床的调速是按照控制指令自动执行的,因此变速机构必须适应自动操作的要求。
在主传动系统中,目前多采用交流主轴电动机和直流主轴电动机无级调速系统。
为扩大调速范围,适应低速大转矩的要求,也经常应用齿轮有级调速和电动机无级调速相结合的调速方式。
数控机床主传动系统主要有四种配置方式,如图3-1所示。
⑴带有变速齿轮的主传动大、中型数控机床采用这种变速方式。
如图3-1(a)所示,通过少数几对齿轮降速,扩大输出转矩,一满足主轴低速时对输出转矩特性的要求。
数控机床在交流或直流电动机无级变速的基础上配以齿轮变速,使之成为分段无级变速。
滑移齿轮的移位大都采用液压缸加拨叉,或者直接由液压缸带动齿轮来实现。
⑵通过带传动的主传动如图3-1(b)所示,这种传动主要应用于转速较高、变速范围不大的机床。
电动机本身的调速能够满足要求,不用齿轮变速,可以避免齿轮传动引起的振动与噪声。
它适用于高速、低转矩特性要求的主轴。
常用的是V带和同步齿形带。
⑶用两个电动机分别驱动主轴如图3-1(c)所示,这是上述两种方式的混合传动,具有上述两种性能。
高速时电动机通过带轮直接驱动主轴旋转;低速时,另一个电动机通过两级齿轮传动驱动主轴旋转,齿轮起到降速和扩大变速范围的作用,这样就使恒功率区增大,扩大了变速范围,克服了低速时转矩不够且电动机功率不能充分利用的缺陷。
⑷内装电动机主轴传动结构如图3-1(d)所示,这种主传动方式大大简化了主轴箱体与主轴的结构,有效地提高了主轴部件的刚度,但主轴输出转矩小,电动机发热对主轴影响较大。
1.4 主传动系统结构设计机床主传动系统的结构设计,是将传动方案“结构化”,向生产 提供主传动部件装配图,零件工作图及零件明细表等。
在机床初步设计中,考虑主轴变速箱机床上位置,其他部件的相互关系,只是概略给出形状与尺寸要求,最终还需要根据箱内各元件的实际结构与布置才确定具体方案,在可能的情况下,设计应尽量减小主轴变速箱的轴向和径向尺寸,以便节省材料,减轻质量,满足使用要求。
设计中应注意对于不同情况要区别对待,如某些立式机床和摇臂钻床的主轴 箱;要求较小的轴向尺寸而对径向尺寸要求并不严格;但有的机床,如卧式铣镗床、龙门铣床的主轴箱要沿立柱或横梁导轨移动,为减少其颠覆力矩,要求缩小径向尺寸。
机床主传动部件即主轴变速箱的结构设计主要内容包括:主轴组件设图3-1 数控机床主传动的四种配置方式()两个电动机分别驱动电动机电动机()带传动电动机()变速齿轮电动机()内装电动机主轴传动机构计,操纵机构设计,传动轴组件设计,其他机构(如开停、制动及换向机构等)设计,润滑与密封装置设计,箱体及其他零件设计等。
主轴变速箱部件装配图包括展开图、横向剖视图、外观图及其他必要的局部视图等。
给制展开图和横向剖视图时,要相互照应,交替进行,不应孤立割裂地设计,以免顾此失彼。
给制出部件的主要结构装配草图之后,需要检查各元件是否相碰或干涉,再根据动力计算的结果修改结构,然后细化、完善装配草图,并按制图标准进行加深,最后进行尺寸、配合及零件标注等。
二、主运动的方案选择与主运动设计1、机床的工艺特性1.1 工艺范围精车、半精车外圆、车螺纹、车端面 1.2 刀具材料硬质合金、高速钢 1.3 加工工作材料 钢、铸铁 1.4 尺寸范围 0~500㎜2、确定主轴转速2.1 最高转速 nmax采用硬质合车刀半精车小直径钢材的外圆时,主轴转速最高。
参考切削用量资料:Vmax =150~200 m/s K = 0.5 Rd =0.2~0.25 dmax =K ·D =0.5×400 =200㎜dmin =Rd ·dmax =0.2×200 =40㎜nmax =minmaxπd 1000V =2003.14201000⨯⨯ =1592.362.2最低转速:①用高速钢车刀,粗车铸铁材料的端面时,参考切削用量资料:Vmax =15~20 m/s nmin =maxminπd 1000V =2003.14201000⨯⨯ =31.8②用高速钢车刀,精车合金钢材料的丝杠时,参考资料: 直径500㎜普通车床加工丝杠的最大直径是50㎜, Vmin =1.5 米/分 nmin =maxminπd 1000V =403.141.51000⨯⨯ =11.9转/分因此:取最低转速nmin=11.9转/分 ③转速范围Rn=minmaxn n =11.91592.36=133.8由于高速钢车刀少用低速,且为了避免结构过于复杂,因此取转速范围Rn=1592.36/31.8=50④主运动结构图三、确定齿轮齿数1、根据分度圆直径选齿数: d=mza组: Z a1 = 64Z a2 = 54Z3a= 34b组:Z b1 = 95Z b2 = 302、齿轮的各参数a组:模数m = 4压力角α=20°齿距 P = πm =12.56齿厚 s = πm/2 = 6.28齿槽宽 e =πm/2 = 6.28顶隙 c = c*m =1.2齿顶高 ha = ha*m = 4齿根高 hf = (ha*+ c*)m = 5.2全齿高 h = ha + hf=(2ha*+ c*)m = 9.2中心距 a1 = (d1+d2)/2 = 240 a2 = (d1+d3)/2 = 178 b组: 模数m = 3.5压力角α=20°齿距 P = πm =12.56齿厚 s = πm/2 = 6.28齿槽宽 e =πm/2 = 6.28顶隙 c = c*m =1.2齿顶高 ha = ha*m = 4齿根高 hf = (ha*+ c*)m = 5.2全齿高 h = ha + hf=(2ha*+ c*)m = 9.2中心距 a = (d4+d5)/2 = 240四、选择电动机1、 电动机功率N 电=7.5kw 转速n 电=1450转/分 2、 电机型号J02—51—4 电机轴径=38㎜五、皮带轮的设计计算:设一天运转时间=8~10小时(按小带轮计算) 1、 计算功率P c = K A ·P = 1.2×7.5 = 9kw 2、 选胶带型别为:B 型3、 选小带轮直径d 1=140㎜(实心轮)大带轮直径d 2=280㎜(四孔板轮) 4、 带速:V=100060n πd 11⨯=10006014501403.14⨯⨯⨯=10.6米/秒 (B 型:V max =25米/秒) 5、 实际传动比:i=()12dε1d - 取ε=005 i=()1400.051280⨯-=4<76、 初定中心距α=(1~0.95)d 2=(1~0.95)×280=280~266 取0α=2707、 初定胶带节线长度L op =20α+2π(d 1+d 2)+()02124αd d -=2×270+23.14×(140+280)+()22704140280⨯-=1218取L p =1290 L i =1250 8、 计算中心距α=0α+2LL opp-=270+212181290-=306㎜ 9、 小带轮包角1α≈180°-αd-d 12×60° =180°-306140280-×60°=152.5°>120° 10、 单根胶带传递的功率: P 0=2.03kw11、 单根胶带传递功率的增量:ΔP 0=k b ·n 1·(1-ik 1)=1.99×103-×1450×(1-11) =2.8 12、 胶带根数:由于需要传递的功率N=7kw , 因此需胶带4根 13、 单根胶带初拉力: F 0=18公斤14、 有效圆周力: F t =v 102p c=109102⨯=91.8公斤 15、 作用在轴上的力:F=2F 0·Z ·sin 2α1=2×18×4×sin 2152.5=134公斤 16、 带轮宽:B=(Z-1)e+2f=(4-1)×20+2×12.5=85㎜六、 传动装置的运动和运动参数计算: 1、传动比:i= 1.192、传动装置的运动参数: Ⅰ轴(电动机轴):P 0=Pd=7.5 kwn 0=1450r/min T 0=9550×0n P =9550×14505.7=49.4 N ·mⅡ轴(主轴):P 1= P 0η01=7.5×0.96=7.2 kw n 1=010i n = 19.11450 = 1218 r/minT 1=9550×11n P =9550×12182.7=56.45 N ·mⅢ轴(编码器):P 2= P 1η12=7.2×0.99×0.97=6.9 kw n 2=121i n = 59.11218 = 766 r/minT 2=9550×22n P =9550×7669.6=86.02 N ·m七、 主轴调速系统的选择计算1、 对调速系统的基本考虑:a.由于调速范围广,且要求有较硬的机械特性。