PID 控制器的正作用与反作用
PID参数设置及调节方法

PID参数设置及调节方法方法一:PID参数的设定:是靠经验及工艺的熟悉,参考测量值跟踪与设定值曲线,从而调整P\I\D的大小。
PID控制器参数的工程整定,各种调节系统中P.I.D参数经验数据以下可参照:温度T: P=20~60%,T=180〜600s,D=:3・180s压力P: P=30~70%,T=24~180s,液位L: P=20~80%,T=60~300s,流量L: P二40〜100%,T=6〜60s。
我在手册上查到的,并已实际的测试过,方便且比较准确应用于传统的PIDlo首先将I, D设置为0,即只用纯比例控制,最好是有曲线图,调整P值在控制范围内成临界振荡状态。
记录下临界振荡的同期Ts2o将Kp值二纯比例时的P值3。
如果控制精度=1.05%,则设置Ti=0.49Ts ;Td=0.14Ts ;T=0.014 控制精度=1.2%,则设置Ti=0.47Ts ;Td=0・16Ts ;T=0.043控制精度=1.5%,则设置Ti=0.43Ts ;Td=0.20Ts ;T=0.09朋友,你试一下,应该不错,而且调试时间大大缩短我认为问题是,再加长积分时间,再减小放大倍数。
获得的是lOOOrpm以上的稳定,牺牲的是系统突加给定以后系统调节的快速性,根据兼顾原则,自己掌握调节指标吧。
方法二:1.PID调试一般原则a•在输出不振荡时,增大比例增益P。
b.在输出不振荡时,减小积分时间常数Ti。
c•在输出不振荡时,增大微分时间常数Td。
2.一般步骤a・确定比例增益P确定比例增益P时,首先去掉PID的积分项和微分项,一般是令Ti=O、Td=O (具体见PID的参数设定说明),使PID为纯比例调节。
输入设定为系统允许的最大值的60%〜70%,由0逐渐加大比例增益P,直至系统出现振荡;再反过来, 从此时的比例增益P 逐渐减小,直至系统振荡消失,记录此时的比例增益P,设定PID的比例增益P为当前值的60%~70%。
PID调节

PID调节你要分清用的是什么系统1.在你所用的系统里,P是纯比例,还是比例度,比如ITCC系统,P是比例度,如果P有值而I为0 的话,阀是不会自动动作的,而如果P为比例,那么只要比例有值阀就可以动作了.中文词条名:比例度英文词条名: proportional band又称比例带。
是调节器放大倍数KP的倒数。
是调节器的一个重要参数。
实质上是表示调节阀开度的百分比与被调量偏差变化的百分比的比值。
若比例度古Δ=50%,调节器放大倍数KP为2,即为被调量产生50%的偏差时,调节阀能从全开到全关(或全关到全开)满量程变化。
加大比例度能提高系统稳定性,但静态偏差要增加;反之,能提高系统的精度,但调节过程的振荡程度要增加。
现在的控制系统都选择p为比例度,不是比例系数2.比例是越大作用越强,而比例度是越大作用越弱(百事公司温控器的P都是比例度),一般温控器P都是比例度,所以概念要搞清,3.ITCC系统当防喘振点超过防喘振线时原来的比例度作用会变成纯的比例作用.所以建议你最好把概念和控制理念结合到一起,至于D是克服之后的,温度液位调节阀设定参数时一般需要加微分.PID中的正反作用是针对:“现场值的变化趋势”与“PID控制输出值变化趋势”之间的关系。
例一:用PID调节器控制恒温炉的炉温。
这是一个典型的反作用调节。
如果炉温下降(现场值下降趋势),我们PID控制输出要增加输出量,来增加功率。
是增加的趋势。
两个趋势相反。
所以,是反作用。
例二:用PID调节器来控制冰库的温度,如果冰库的温度在上升,我们PID调节的输出也要增加,增加制冷的功率。
两个趋势是相同的。
这就是正作用。
我的理解:P 实际值和设定值有偏差时,根据偏差的大小调节阀门的开度大小,偏差大调节的大,偏差小调节的小。
这是随动。
当偏差很小时,P控制的输出就很小,系统要么存在一个稳定的小偏差,要么就来回震荡。
I 实际值和设定值的偏差很小时,在一定时间内计算出小偏差的累积量,然后输出,这就是积分。
过程控制系统PID控制器的参数整定意义

积分饱和示例
单回路系统积分饱和现象举例
单回路系统积分饱和仿真结果
单回路系统的防积分饱和原理
ysp(t) e(s)
+
KC +
-
+
d(t)
v
广义
+ +
对象
y(t)
1 TI s 1
讨论:正常情况为标准的PI控制算法; 而当出现超限时,自动切除积分作用。
积分外反馈
积分分离
PID控制器的作用
比例作用P是基本控制作用,输出与输入无 相位差。Kc越大控制作用越强,随着Kc 的 增加(比例度δ减小) ,余差下降,最大偏 差减小,但稳定性变差。
控制器增益 Kc或比例度δ
但稳定增性益下K降c 的;增大(或比例度δ下降),使系统的调节作用增强,
积分时间Ti
但控制积系分统作的用稳的定增性强下(降即;Ti 下降),使系统消除余差的能力加强,
微分时间Td
性得到微加分强作,用但增对强高(频即噪T声d 增起大放)大,作可用使,系主统要的适超合前于作特用性增滞强后,较稳大定的 广义对象,如温度对象等。
假设测量范围为 200 ~ 400 ℃, Kp = 1.75, Tp = 10 min, τ = 7 min. Kc = 0.98, Ti = 14 min, T“积分饱和”问题
ysp(t)
+ -
K
C
ççèæ1
1 TI s
÷÷øö
u
d(t)
v
广义
+ +
对象
y(t)
响应曲线
u(t) u0
0
y(t)
p y0
τT
T0
T1 T2
u1 y1
T3
对象的近似模型:
y(s) Kp es u(s) Tps1
PID控制的正作用反作用
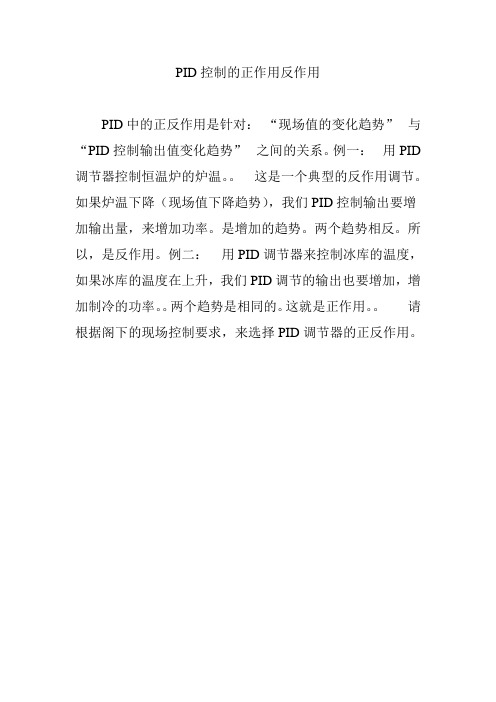
PID控制的正作用反作用
PID中的正反作用是针对:“现场值的变化趋势”与“PID控制输出值变化趋势”之间的关系。
例一:用PID 调节器控制恒温炉的炉温。
这是一个典型的反作用调节。
如果炉温下降(现场值下降趋势),我们PID控制输出要增加输出量,来增加功率。
是增加的趋势。
两个趋势相反。
所以,是反作用。
例二:用PID调节器来控制冰库的温度,如果冰库的温度在上升,我们PID调节的输出也要增加,增加制冷的功率。
两个趋势是相同的。
这就是正作用。
请根据阁下的现场控制要求,来选择PID调节器的正反作用。
PLC的PID功能介绍
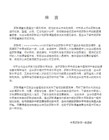
[S3]+ 7
~ [S3]+ 19 — — PID运算占用
[S3]+ 20 输入变化量(增方)警报设定值 0~32767 由用户设定ACT([S3]+ 1)为K2~K7时有效,即ACT的Bit1 和Bit2至少有一个为1时才有效;
1为有输出变化量报警 Bit3 ~ Bit15不用
[S3]+ 2 输入滤波常数(L) 0~99(%) 对反馈量的一阶惯性数字滤波环节
[S3]+ 3 比例增益(K p) 1~32767(%)
[S3]+ 4 积分时间(T I) 0~32767(×100ms) 0与∝作同样处理
[S3]+ 5 微分增益 (K D) 0~100(%)
2)使用PID功能指令。现在很多中小型 PLC都提供PID控制用的功能指令,如FX2N系列PLC的PID指令。它们实际上是用于PID控制的子程序,与A/D、D/A模块一起使用,可以得到类似于使用PID过程控制模块的效果,价格却便宜得多。
3)使用自编程序实现PID闭环控制。有的PLC没有有PID过程控制模块和 PID控制指令,有时虽然有PID控制指令,但用户希望采用变型PID控制算法。在这些情况下,都需要由用户自己编制PID控制程序。
3. FX2N的PID指令
PID指令的编号为FNC88,如图6-36所示源操作数[S1]、[S2]、[S3]和目标操作数[D]均为数据寄存器D,16位指令,占9个程序步。[S1]和[S2]分别用来存放给定值SV和当前测量到的反馈值PV,[S3]~[S3]+6用来存放控制参数的值,运算结果MV存放在[D]中。源操作数[S3]占用从[S3]开始的25个数据寄存器。
3PLC程序的PID参数的设定与调节(精)
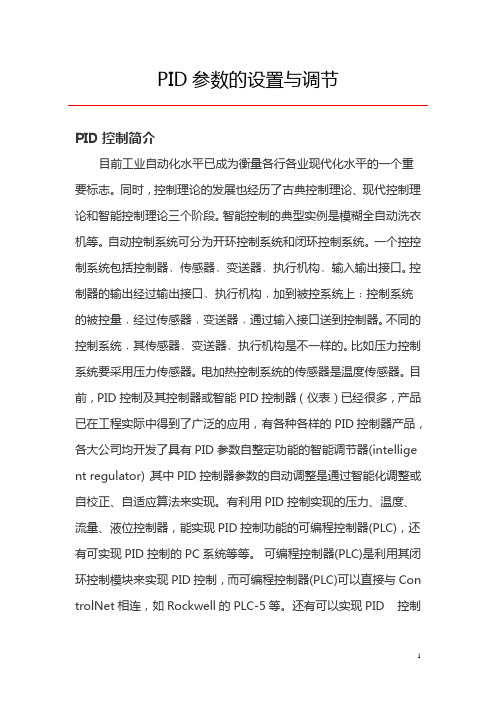
PID参数的设置与调节PID控制简介目前工业自动化水平已成为衡量各行各业现代化水平的一个重要标志。
同时,控制理论的发展也经历了古典控制理论、现代控制理论和智能控制理论三个阶段。
智能控制的典型实例是模糊全自动洗衣机等。
自动控制系统可分为开环控制系统和闭环控制系统。
一个控控制系统包括控制器﹑传感器﹑变送器﹑执行机构﹑输入输出接口。
控制器的输出经过输出接口﹑执行机构﹐加到被控系统上﹔控制系统的被控量﹐经过传感器﹐变送器﹐通过输入接口送到控制器。
不同的控制系统﹐其传感器﹑变送器﹑执行机构是不一样的。
比如压力控制系统要采用压力传感器。
电加热控制系统的传感器是温度传感器。
目前,PID控制及其控制器或智能PID控制器(仪表)已经很多,产品已在工程实际中得到了广泛的应用,有各种各样的PID控制器产品,各大公司均开发了具有PID参数自整定功能的智能调节器(intellig ent regulator),其中PID控制器参数的自动调整是通过智能化调整或自校正、自适应算法来实现。
有利用PID控制实现的压力、温度、流量、液位控制器,能实现PID控制功能的可编程控制器(PLC),还有可实现PID控制的PC系统等等。
可编程控制器(PLC)是利用其闭环控制模块来实现PID控制,而可编程控制器(PLC)可以直接与Cont rolNet相连,如Rockwell的PLC-5等。
还有可以实现PID控制功能的控制器,如Rockwell的Logix产品系列,它可以直接与Contro lNet相连,利用网络来实现其远程控制功能。
1、开环控制系统开环控制系统(open-loop control system)是指被控对象的输出(被控制量)对控制器(controller)的输出没有影响。
在这种控制系统中,不依赖将被控量反送回来以形成任何闭环回路。
2、闭环控制系统闭环控制系统(closed-loop control system)的特点是系统被控对象的输出(被控制量)会反送回来影响控制器的输出,形成一个或多个闭环。
PID讲解理论课件
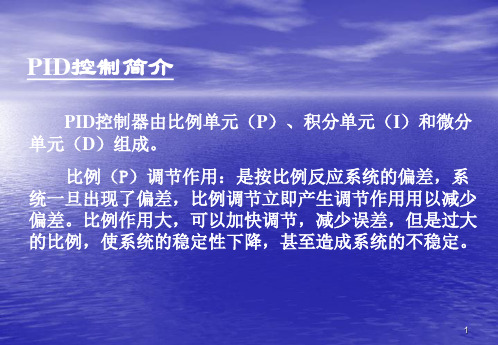
PID参数是根据控制对象的惯量来确定的。大惯量如: 大烘房 的温度控制,一般P可在10以上,I=3-10,D=1左右。小惯量如: 一个小电机带一台水泵进行压力闭环控制,一般只用PI控制。 P=1-10,I=0.1-1,D=0,这些要在现场调试时进行修正的。 6
微分(D)调节作用: 微分作用反映系统偏差信号的 变化率,具有预见性,能预见偏差变化的趋势,因此能产 生超前的控制作用,在偏差还没有形成之前,已被微分调 节作用消除。因此,可以改善系统的动态性能。在微分时 间选择合适情况下,可以减少超调,减少调节时间。此外, 微分反应的是变化率,而当输入没有变化时,微分作用输 出为零。微分作用不能单独使用。
经验法简单可靠, 但需要有一定现场运行经验, 整定时易带有 主观片面性。当采用PID调节器时, 有多个整定参数, 反复试凑的次 数增多, 不易得到最佳整定参数。
5
下面以PID调节器为例,具体说明经验法的整定步骤: A. 让调节器参数积分系数I=0,实际微分系数D=0,控制系统投
入闭环运行,由小到大改变比例系数P,让扰动信号作阶跃变化, 观察控制过程,直到获得满意的控制过程为止。
I是解决动作响应的速度快慢的, 可消除系统稳态误差, I变大时 响应速度变慢, 反之则快;
D是消除静态误差的, 提高系统动态特性, (减少超调量和反应时3
PID控制器参数的工程整定,各种调节系统中P.I.D参数经验数据以 下可参照:
温度TIC: P=20~60%,I=180~600s,D=3-180s; 压力PIC: P=30~70%,I=24~180s; 液位LIC: P=20~80%,I=60~300s; 流量FIC: P=40~100%,I=6~60s。
Honeywell_DCS_控制回路PID参数整定方法

Honeywell PKS系统控制回路PID参数整定方法鉴于目前一联合装置仪表回路自控率比较低,大部分的回路都是手动操作,这样不但增加了操作员的工作量,而且对产品质量也有一定的影响,特编制了此PID参数整定方法。
修改PID参数必须有“SUPV(班长)”及以上权限权限,具体权限设置切换方法如下;一、打开要修改的控制回路细目画面,翻到下图所示的页面(Loop Tune),修改PID控制回路整定的三个参数K,T1,T2;二、PID参数代表的含义Control Action:控制器的作用方式,正作用(DIRECT),反作用(REVERSE);Overal Gain(K):比例增益(放大倍数),范围为0.0~240.0;T1:积分时间,范围为0.0~1440.0,单位为分钟,0.0代表没有积分作用;T2:微分时间,范围为0.0~1440.0,单位为分钟,0.0代表没有微分作用。
三、PID参数的作用(1)比例调节的特点:1、调节作用快,系统一出现偏差,调节器立即将偏差放大K倍输出; 2、系统存在余差。
K越小,过渡过程越平稳,但余差越大;K增大,余差将减小,但是不能完全消除余差,只能起到粗调作用,但是K过大,过渡过程易振荡,K太大时,就可能出现发散振荡。
(2)积分调节的特点:积分调节作用的输出变化与输入偏差的积分成正比,积分作用能消除余差,但降低了系统的稳定性,T1由大变小时,积分作用由弱到强,消除余差的能力由弱到强,只有消除偏差,输出才停止变化。
(3)微分调节的特点:微分调节的输出是与被调量的变化率成正比,在引入微分作用后能全面提高控制质量,但是微分作用太强,会引起控制阀时而全开时而全关,因此不能把T2取的太大,当T2由小到大变化时,微分作用由弱到强,对容量滞后有明显的作用,但是对纯滞后没有效果。
四、控制器的选择方法(1)P控制器的选择:它适用于控制通道滞后较小,负荷变化不大,允许被控量在一定范围内变化的系统;(2)PI控制器的选择:它适用于滞后较小,负荷变化不大,被控量不允许有余差的控制系统;(3)PID控制器的选择:它适用于负荷变化大,容量滞后较大,控制质量要求又很高的控制系统,比如温度控制系统。
- 1、下载文档前请自行甄别文档内容的完整性,平台不提供额外的编辑、内容补充、找答案等附加服务。
- 2、"仅部分预览"的文档,不可在线预览部分如存在完整性等问题,可反馈申请退款(可完整预览的文档不适用该条件!)。
- 3、如文档侵犯您的权益,请联系客服反馈,我们会尽快为您处理(人工客服工作时间:9:00-18:30)。
PID Controller Action: Directing Acting & Reverse ActingAir to open/close valves and direction of control actionControl valves come in two sorts: air to open; and air to close.Air to open valves are normally held closed by the spring and require air pressure (a control signal) to open them – they open progressively as the air pressure increases.Air to close valves are valves which are held open by the valve spring and require air pressure to move them towards the closed position.The reason for the two types of valves is to allow fail safe operation. In the event of a plant instrument air failure it is important that all control valves fail in a safe position (e.g. an exothermic reactor’s feed va lves (or, perhaps, just one of the valves) should fail closed (air to open) and its coolant system valves fail open (air to close)).The type of valve used obviously impacts on what a controller has to do – changing the type of valve would mean that the controller would need to move the manipulation in the opposite direction.To simplify things in this course we shall assume that we are always using air to open valves – an increase in control action will cause the valve to open and the flow through it to increase.The other important thing you need to understand is the direction of control action. Consider the system shown in the diagram.PID Controller ActionConsider Two cases:1) Level Controller LC controlling discharge control valve.In this process I have connected a level controller to the bottom valve. For this configuration the controller needs to increase its signal (and hence the flow) when the level in the tank increases.2) Level Controller LC controlling inlet control valve.In this case the controller needs to reduce the flow when the level in the tank increases.Both configurations are equally capable of controlling the level, but they require the controller to do entirely opposite things. This is what direction of control action involves.A direct acting controller is one whose output tends to increase as the measurement signal increases.A reverse acting controller is one whose output tends to decrease as the measurement signal increases.All control systems are programmable (usually marked DIR/REV) which allows the controller to be switched from direct acting to reverse acting or vice versa.It is important to get the correct direction of control action. If things are set-up correctly a feedback control system will experience negative feedback, which means that the system will act to reduce errors in its output.If you get the direction of control action wrong the system will undergo positive feedback and will act to reinforce output errors – this is very likely to cause the system to go unstable. If you are having problems in setting up a stable controller the first thing to check is that you have set the correct direction of control action!Different Combinations of Control Valves & Controllers action1. Fail Open Control Valve / Direct Acting ControllerIf a fail open control valve is paired with a direct acting controller we get the following process performance: On rising process level the controller output rises which closes the valve.If the process level is below the set point the controller would be wide open.This would behave similar to a direct acting regulator only the valve / controller response is slower.2.Fail Open Control Valve / Reverse Acting ControllerIn this case when the process level rises the controller output decreases which tends to open the valve.If the process level is below the set point the valve is closed.An example of this application is a compressor recycle valve.3.Fail Closed Control Valve / Direct Acting ControllerThis is the same as the fail open valve / reverse acting controller. An increase in process level means an increase in controller output which means the valve is opened.If the process level is below the set point the valve is closed. A typical application is backpressure control. (In this case the valve controller acts similar to that of a PSV.)4.Fail Closed Control Valve / Reverse Acting ControllerA rise in process level means a decrease in controller output which means the valve is closed.If the process level is below the set point the valve is open.This is typically used for pressure control.。