过程检验程序
过程检验和试验程序

4.2各阶段操作者,应根据质量要求和质量计划进行自检、合格品和不
合格品须及时分隔并予以记录。
4.3在每阶段的检验或试验完成并获得相关人员认可之后,才能执行下
阶段的工作任务。
4.4如在工作中发现不合格现象,应及时提出,相关人员应视情况决定
是否发出更正行动(CAR)。
4.5如在工作中发现不合格品,则按《不合格品的控制程序》处理。
标题:过程检验和试验程序页码
1.0目的:
此文指导工程过程按规定的要求进行检验或试验,确保过程受控。
2.0范围:
此文适用于工程过程中各阶段的工序检验或试验。
3.0职责:
3.1总工程负责重大质量问题的决定。
3.2工程部经理负责技术方案及质量标准的审定、质量问题的处理及决
定。
3.3项目负责人负责质量检验和标准的设定、质量问题的处理及决定。
4.6必要时,可安排业主方面的人员参加检验或试验,并做好记录。
5.0参考文件
5.1《项目质量计划》
5.2《设计控制程序》
5.3《图纸审核程序》
5.4《软件编程控制程序》
5.5《设备成套/安装控制程序》
5.6《现场安装/调试控制程序》
5.7《纠正和预防措施程序》
5.8《静态测试指引》
6.0记录
6.1各质量记录文件
3.4项目工程师负责质量检验工作的执行及记录,质量问题的处理。
3.5工程秘书负责质量记录的统计及归档。
4.0程序:
4.1工程各阶段必须依据项目质量计划的任务分解表和《设计控制程序》
《静态测试指引》、《/调试控制程序》的要求,执行阶
施工过程检验程序

施工过程检验程序一、过程检验1.项目经理部主任工程师组织现场测量人员及公司技术质量部人员参与对建筑物定位、定高部位的检查, 由技术、测量、复测、施测人员签认, 由项目经理部主任工程师安排质量员将检查结果上传至项目综合管理信息系统相应模块。
2.公司技术质量部、建设、勘察、设计、监理单位参加验槽检查, 由项目经理部主任工程师填写《地基验槽记录》, 建设、勘察、设计、监理单位的相关人员签字确认, 并加盖单位公章。
由项目经理部主任工程师安排质量员将检查记录上传至项目综合管理信息系统相应模块。
3.公司技术质量部参加对单位(子单位)工程的主要部位(地基与基础、主体结构), 重点部位隐蔽工程和单位(子单位)工程的验收。
4.隐蔽工程检查由单位工程工长自检合格后, 报项目技术质量组对隐蔽部位进行检查。
工长填写《隐蔽工程检查记录》, 经监理单位检查后, 由监理工程师、施工项目经理部/专业公司技术负责人、质检员、工长签认, 标明此部位属合格状态。
由项目经理部主任工程师安排质量员将检查结果上传至项目综合管理信息系统相应模块。
5.需进行预检的部位由工长自检合格后, 报项目质量组对预检部位进行检查, 工长填写《预检记录》, 质检员、工长签认。
由项目经理部主任工程师安排质量员将检查结果上传至项目综合管理信息系统相应模块。
6.在施工操作过程中或工序完工后, 由所承担该项工程的工长组织班组进行自检、互检、交接检, 班组质检员负责填写《自检、互检记录》、《交接检记录》, 项目经理部质检员负责督促检查。
7、检验批工程完工后, 项目经理部/专业公司应对检验批的主控项目和一般项目的质量检验合格, 具有完整的施工操作依据、质量检查记录, 质量符合要求后由工长填写《检验批质量验收记录》, 由项目经理部/专业公司质量检查员签认后, 交监理工程师组织施工项目经理部/专业公司质检员、工长进行验收并签认。
8、分项工程完工后, 由项目经理部/专业公司质量检查员填写《分项工程质量验收记录》, 由主任工程师检查后签认, 交监理工程师签认。
过程检验程序

检验控制程序青海金安建设工程有限公司1.目的在生产过程中,对每道工序加工的零部件、半成品,按产品图样、工艺文件规定的技术要求进行检验,以保证不合格零部件、半成品不流入下道工序。
2.适用范围本程序适用于本公司产品制造中工序检验工作,也适用于外协生产的工序检验工作。
3.职责3.1 研发部制定各工序检验质量标准,编写工艺文件,绘制产品图样。
3.2 品管部负责生产过程产品的检验和试验,并做检验记录。
3.3 生产部指导、督促操作工作好自检工作。
4.工作程序、方法4.1 各工序操作工根据图纸、作业指导书等工艺文件规定的技术要求进行加工。
4.2 自检操作工加工完零件后,应按图纸、工艺文件的技术要求进行自我检验。
车间主任、班组长负责指导、督促操作工作好自检工作。
4.3 首检质检人员对木工加工的由设备的定位装置和模具决定其质量的零部件进行首检试验(电锯工序由操作工自检后,将结果记录与《工序流转单》上),以避免批量返工或不合格。
首检检验合格后,可继续加工;如首检检验不合格,应返工或重新加工首件,只只检验合格后才可加工其余零部件。
首检检验的结果应记录与《首件检验记录表》。
4.4 巡检质检人员应按照施工图及其他相关检验标准进行巡回检查。
巡检合格的可以继续操作。
发现不合格时,质检员应与操作工一起分析原因、制定措施,以便迅速调整,防止不合格品的再次发生。
4.5 终检4.5.1 操作工将完工的零部件整齐码放在机床或工作台旁的指定区域,并及时通知质检员报检。
4.5.2质检员接到报验后,即按照各工序检验质量标准进行终检,在《质量检验日报表》和工序流转单上记录终检结果,并按(检验和试验状态控制程序)的规定对检验后的产品进行标识,合格转入下道工序,不合格品则按《不合格品控制程序》的规定处理。
必要时采取纠正和预防措施。
4.6试装4.6.l当木工车间加工完成后,由装配工序操作工和质检员对经过检验合格的零件进行试装检查。
试装结果记录在《试装记录表》上。
机加工过程检验流程
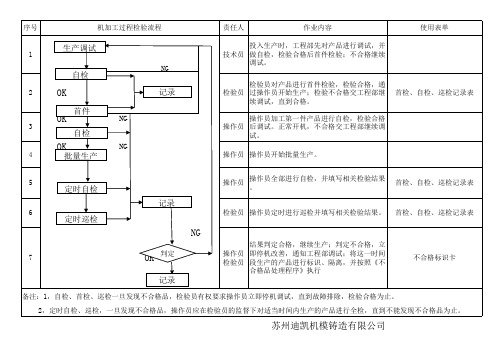
序号
机加工过程检验流程
责任人
作业内容
使用表单
1
生产调试 自检
NG
投入生产时,工程部先对产品进行调试,并 技术员 做自检,检验合格后首件检验;不合格继续 调试。 检验员对产品进行首件检验,检验合格,通 检验员 过操作员开始生产;检验不合格交工程部继 续调试,直到合格。 操作员加工第一件产品进行自检,检验合格 操作员 后调试。正常开机,不合格交工程部继续调 试。 操作员 操作员开始批量生产。 操作员全部进行自检,并填写相关检验结果 。
不合格标识卡
记录
备注:1,自检、首检、巡检一旦发现不合格品,检验员有权要求操作员立即停机调试,直到故障排除,检验合格为止。 2,定时自检、巡检,一旦发现不合格品,操作员应在检验员的监督下对适当时间内生产的产品进行全检,直到不能发现不合格品为止。
苏州迪凯机模铸造有限公司
2
OK OK OK
批量生产
首件
记录 NG NG
首检、自检、巡检记录表
3
自检
4ቤተ መጻሕፍቲ ባይዱ
5
定时自检
记录
操作员
首检、自检、巡检记录表
6
定时巡检
检验员 操作员定时进行巡检并填写相关检验结果。
首检、自检、巡检记录表
NG
7
OK
判定
结果判定合格,继续生产;判定不合格,立 操作员 即停机改善,通知工程部调试;将这一时间 检验员 段生产的产品进行标识、隔离,并按照《不 合格品处理程序》执行
过程检验作业指导书
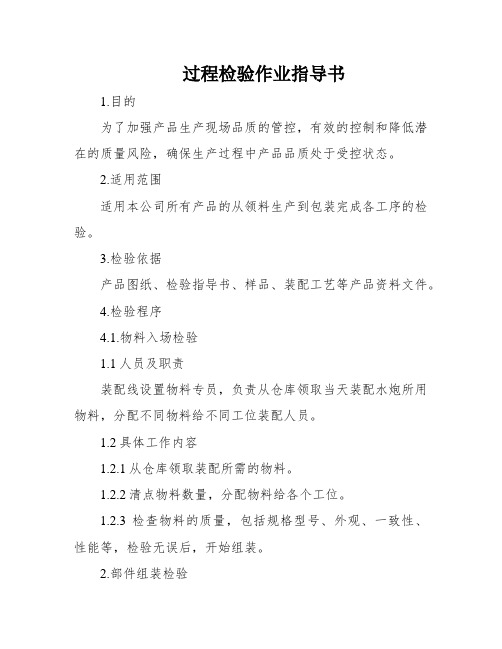
过程检验作业指导书1.目的为了加强产品生产现场品质的管控,有效的控制和降低潜在的质量风险,确保生产过程中产品品质处于受控状态。
2.适用范围适用本公司所有产品的从领料生产到包装完成各工序的检验。
3.检验依据产品图纸、检验指导书、样品、装配工艺等产品资料文件。
4.检验程序4.1.物料入场检验1.1人员及职责装配线设置物料专员,负责从仓库领取当天装配水炮所用物料,分配不同物料给不同工位装配人员。
1.2具体工作内容1.2.1从仓库领取装配所需的物料。
1.2.2清点物料数量,分配物料给各个工位。
1.2.3检查物料的质量,包括规格型号、外观、一致性、性能等,检验无误后,开始组装。
2.部件组装检验2.1自检装配人员每装配完成第一个部件后,进行自检合格后在装配剩余部分,整批装配完成后逐个进行自我检验,全部无误后,才能流到下一工序。
如果组装的部件有一部分部件组成,则装配人员需要对上一工序的部11件举行检验,合格后方能使用。
2.2互检装配人员在一批部件自检完成后,要求相邻工序装配人员或下一工序装配人员给做互检,互检完成后,检验人签字确认。
2.3巡检4巡检是出产过程中,检验员对出产出的产品举行巡回检验,质检员对产品举行抽样家宴,目的是为了避免成批不合格品的发生或工艺发生异常。
检验员对个生产工序产品品质状况进行巡回检查,在巡检过程中需特别注意物料加工的工位、常换人、有新人上岗的工位以及关键工位,如有发现异常及时通知生产管理负责人进行改善。
巡检过程中同时注意操作人员是否按照《作业指导书》进行操作,如发现操纵人未按照作业指导书进行操作,应立即要求作业人员改善。
检验员有权对不符合规定的操作,现场易引发质量问题和生产效率的操作,要求进行整改。
5.不合格的处理方法5.1由自检、互检发现的由装配人员引起的不合格品,由装配人员自行返工维修,返工后的产品需要重新检验。
返工返修仍然不能解决的,可以做报废处理。
5.2巡检发现不合格品,必须标识隔离零丁存放,举行集中同一处理。
过程检验程序(含表格)

过程检验程序(QC080000-2017)1.0目的:确保生产过程中在制品都符合品质要求,防止不良品流至下一工序而影响最终产品的质量。
2.0范围:适用于公司所有制程中的在制品。
3.0定义:3.1 IQC:进料检验3.2 IPQC:制程巡检3.3 PQC:制程抽检3.4 FQC:出货检验3.5 OQC:出货抽检4.0权责:4.1品管部主管:4.1.1详见《职责划分程序》;4.1.2制定品质目标及改善计划;4.1.3建立相关规范流程,使制定品质目标如期完成4.2 IPQC(制程巡检):4.2.1指导IPQC人员按各工序IPQC作业指导书及进行日常巡验工作,指导操作员按《作业指导书》进行生产制造。
4.2.2发现严重异常问题时,应及时按《纠正与预防措施程序》进行质量跟踪改善或按《特采控制程序》进行质量放行。
4.3 PQC(制程抽验):4.3.1按《MIL-STD-105E抽样计划》、《检验标准》及《量产技术规格书》进行品质检验。
4.3.2发现不良异常情况及时通过[异常单]向品管部汇报反馈,并按《不合格品控制程序》进行处理不合格品。
4.4 FQC(出货检验):4.4.1按《MIL-STD-105E抽样计划》、《检验标准》及《量产技术规格书》进行品质检验。
4.4.2发现不良异常情况及时通过[工艺异常单]向品管部汇报反馈,并按《不合格品控制程序》进行处理不合格品。
4.5 OQC(出货抽检):4.5.1按《成品及出货检验管理办法》、《检验标准》、《量产技术规格书》及《抽样计划》进行抽检;4.5.2发现不良异常情况及时通过[异常单]向品管部汇报反馈,并按《不合格品管理办法》进行处理不合格品。
4.5 统计员:4.5.1负责收集检验数据,并根据《统计分析控制程序》对数据进行汇总分析。
4.5.2对分析后的数据中出现的异常情况,按《纠正与预防措施程序》进行品质改善。
5.0内容: 5.1流程:流程 权责岗位使用表单IPQC 生产部 IPQC生产部检验人员 PQC FQC OQC 统计员 生产部 品管部《首件、过程作业检验记录表》《模块首检日报表》[IPQC 巡检报表][品管检验日报表][出货检验报告][纠正和预防措施处理单]制 造品质改善不良品汇总记录分析首检确认巡检自主检验过程抽检出货抽检入库抽检5.2内容:5.2.1首件确认:生产前必须经过首件确认,首件不合格或未进行首件确认严禁批量生产。
过程检验和试验程序
XXXXX汽车零部件有限公司企业标准
XXX-2020
过程检验和试验程序共5页第1页
1 目的
本标准规定了产品在生产过程中的检验和试验的方法,为了防止不合格品的出现,特制定本标准。
2 适用范围
本标准适用于本公司产品生产过程中的检验和试验。
3 职责
3.1操作者本人负责自检。
3.2检验员负责首件检验、巡回检验。
4 流程图及程序
企业2020-4-1批准2020-4-10实施
XXXXX-2020 第2页
企业2020-4-1批准2020-4-10实施
企业2020-4-1批准2020-4-10实施
企业2020-4-1批准2020-4-10实施
XXXXX-2020 第5页5 相关文件
首件检验单
巡回检验记录单
末件检验单
6 文件分发
本文件发至技术质保部、综合管理部、档案室。
起草人:XXX 校对人:XXX 共印3份。
过程检验程序范文
过程检验程序范文过程检验程序(Process Inspection Procedure)是一种用于评估制造过程中的产品质量和符合性的方法。
它通常由多个步骤和检查程序构成,以确保产品在制造过程中的各个阶段都符合规定的标准和要求。
以下将详细介绍过程检验程序的目的、步骤和实施要点。
一、目的二、步骤1.明确过程标准和要求:首先,制定和明确产品制造的过程标准和要求,包括工艺流程、关键控制点、质量指标、测试方法等。
这些标准和要求应该符合相关的规定和技术要求。
2.确定检验方法和时机:根据制造过程的特点和产品要求,确定适合的检验方法和时机。
可以采用物理测量、化学分析、非损伤测试等方法,以及在线检验、样品检验等时机。
3.建立检验记录和追踪表:建立适当的检验记录和追踪表,记录每个过程步骤的检验结果和相关数据。
这些记录和追踪表可以帮助评估过程的一致性和稳定性,并在需要时进行溯源和追溯。
4.执行过程检验:按照制定的过程标准和要求,执行过程检验并记录结果。
根据结果评估过程的符合性和质量稳定性,并及时发现和处理不符合要求的情况。
5.分析和改进过程:根据过程检验结果和评估情况,分析问题和改进过程。
如果发现问题和缺陷,需要采取适当的纠正措施和预防措施,以提高过程的质量和符合性。
6.监控和验证改进效果:监控改进后的过程,并验证改进效果。
通过比较改进前后的过程检验结果和评估情况,评价改进效果是否达到预期,并根据需要进行进一步优化和改进。
三、实施要点1.明确责任和权限:明确过程检验的责任和权限,包括负责人、检验人员和相关部门。
每个人都应了解和承担自己的责任,并有权采取必要的纠正和预防措施。
2.培训和宣传:针对过程检验程序的实施要求和方法,进行培训和宣传。
确保每个人都了解和理解过程检验的重要性和目的,并掌握必要的技能和知识。
3.合理分配资源:合理分配人力、物力和财力资源,以支持过程检验程序的实施。
确保有足够的检验设备、工具和材料,并充分利用现有的质量管理系统和信息技术手段。
过程检验程序
PQC
流程
等级
目标
输入
作业方法描述
输出
信息
时效/反馈
职责
A
9艺卡》
3.《图纸》
4.样板
5.《抽样方法规定》
5.3过程巡检
5.3.1
PQC应在过程控制中,利用《统计技术(SPC)管理程序》对特殊性进行分析,并由车间主任对过程进行分析。
1.X(Bar)~R图
2.X(Bar)—S图
车间
●
PQC
A
98%
1.《过程检验报告》(首检)
——不合格
5.1.2
生产车间应对批准为不合格的首件进行原因分析,进行设备的再次调试,必要时提交《质量异常报告》及首件检验报告作为附页,召集相关部门讨论并分析对策。
1.《质量异常报告》
品质科科长(含副)
●
车间
A
98%
1.《过程检验报告》(首检)
5.1.3
PQC应将《首件检验报告》的不合格次数进行统计,并分析《首检检验一次合格率》
《首检检验一次合格率》
车间
持续发展办
每月5日前
PQC
A
96%
1.《工艺卡》
2.样板
3.图纸
5.2自主检验:
5.2.1
在操作过程中,在有自主检验规定时,操作员应按《工艺卡》及相关文件做产品检验,并做《过程检验报告》(自检)。《过程检验报告》(自检)在操作时间有矛盾时可由PQC协助填写,但操作员必需签名确认。
车间主任
●
FQC
●
●
1.《过程转序检验报告》
5.5.2
《过程转序检验报告》由QE审核。
《过程转序检验报告》
——审核
施工过程质量检验工作程序
施⼯过程质量检验⼯作程序施⼯过程质量检验⼯作程序过程质量检验主要包括班组⾃检、质检员专职检、专业施⼯员间交接检、监理、建设单位参与的隐蔽⼯程检验、公司定期检验,分项、分部评定以及中间验收等程序:班组⾃检施⼯员应依照作业指导书、规范、规程和图纸设计要求等在⼯序开始施⼯前以书⾯形式对班组进⾏操作⼯艺,施⼯⽅法、次序等技术交底,班组应严格按照技术要求进⾏施⼯,在⼯序施⼯过程,专业施⼯员应时刻对班组操作⼯艺,施⼯⽅法进⾏监督检查和指导;在施⼯⼯序完成后,专业施⼯员应组织班组长及操作者按验评规范进⾏⾃检,做好⾃检记录。
质检员专职检专业施⼯员组织的⾃检合格后,由施⼯员整理好相关的质保资料提交质检员检查。
在项⽬技术管理组织下,质检员会同施⼯员,班组长按照验评规范要求进⾏专职检验。
专职检验合格后,才能转⼊下道⼯序施⼯。
同时应做好专职检记录,并将质保资料交技术内业员保管。
交接检在施⼯过程中,开展“三⼯序”活动,即“检查上道⼯序,保证本道⼯序,服务下道⼯序”,实现对⼯序检验的控制。
⼯序转换应在⾃检、专职检合格⼿续基础上,由本道专业施⼯员组织下道⼯序专业施⼯员、班组长及相关专业的施⼯员进⾏交接检验和交底,并办理交接⼿续、填写《⼯序⾃检、专职检、交接检记录》在不同⼯种进⾏交接和转换时,应办理交接会签⼿续,填写会签单。
如砼浇筑前的会签。
隐蔽⼯程检验隐蔽⼯程在隐蔽前,应由质检员先⾏检验。
检验合格后,由施⼯员填写报验单,向监理(业主)申请报验,经监理(业主)代表验证同意后,办理《隐蔽⼯程验收记录》的签证⼿续,⽽后⽅可隐蔽。
技术复核在每⼀个施⼯过程中,均要对轴线和标⾼以及预埋件,预留孔洞等进⾏技术复核。
由施⼯员进⾏放样,质检员随后进⾏复核。
复核的具体情况应记录在《技术复核记录》表中,未经技术复核或检查不合格的不得予以放⾏。
公司定期检验在公司总⼯程师的主持下,公司技术部每⽉组织有关⼈员对本⼯程进⾏⼀次全⾯质量检查,对专职检进⾏核定,对⾃检、交接检、隐蔽⼯程检验、技术复核、技术内业资料等⼯作情况进⾏抽查。
- 1、下载文档前请自行甄别文档内容的完整性,平台不提供额外的编辑、内容补充、找答案等附加服务。
- 2、"仅部分预览"的文档,不可在线预览部分如存在完整性等问题,可反馈申请退款(可完整预览的文档不适用该条件!)。
- 3、如文档侵犯您的权益,请联系客服反馈,我们会尽快为您处理(人工客服工作时间:9:00-18:30)。
⒈目的:
对产品零件加工和成品装配的各工序的质量进行规定的检验和试验,防止不合格产品的流失,保证产品加工过程中符合标准要求。
⒉范围:
适用于指导产品零件加工,和成品装配过程中的工序检验工作。
⒊职责:
3·1检验组是工序检验的归口管理部门,负责工序检验的组织实施工作。
3·2技术部负责工序检验的技术标准等有关文件的编制工作。
4·2·2巡检:
加工中,检验员按照检验规程要求的频次进行巡检,巡检间隔时间不大于二小时,对重点的工序或机床应当适当的增加巡检次数,巡检抽样一般为3——5件,异常时加倍抽样。巡检中发现异常波动,应立即通知操作者进行分析调整;如发现严重质量问题,按程序规定向有关部门及时反馈,等候处理。对巡检情况检验员要在《工序质量检验记录表》中做好记录。
4·2过程检验
4·2·1首检:
操作人员对上班加工的首件或首次产品,以及更换型号、工装、刀具后加工的首件产品,都要进行首检。首检按"作业指导书"的检验要求执行。操作者首检合格后交专职检验员进行确认。确认前,检验员首先核对仪表、标准件,确认无误后方可进行。首检一般查3——5件,有异常时加倍抽样。首检产品质量正常可继续加工,如发现问题则立即通知操作者进行机床、工装调整。出现异常现象时,向有关领导反馈,等候处理,首检记录由操作者负责在《工序质量检查记录表》上填写,检验员在"认可栏"签字确认。
3·3生产部及有关产品加工车间负责工序的首检、自检等检验工作据产品工艺流程图及产品质量特性等技术文件的要求,制定产品的工序检验流程,设立适当的工序检验点、站、网络,合理配置资源,生产部检验组按检验规程实施工序检验,以保证产品的工序加工质量。
4·1·2生产车间要按作业指导书和工序检验要求组织有关人员进行首检、自检、完工检。工段长应确保工序产品质量,防止不合格品流入下工序。
⒍质量记录:
见清单。
4·2·6自检:
各工序操作者要按工艺文件要求进行自检,操作者的自检记录须经检验员认可后方可生产。
⒌相关文件:
5·1QS/TSB21301-2002《不合格品控制程序》
5·2QS/TSB21401-2002 《纠正和预防措施控制程序》
5·3QS/TSB20801-2002 《产品标识和可追溯性控制程序》
4·2·3工序间的下转验收:
工段或车间之间的转序检验,按下转产品的各项质量特性和技术条件由检验员进行抽检,抽检合格后和工段长共同在《工序流转单》中签字后方可后移交到下一道工序。
4·2·4装前检:
为确保成品质量,对加工完毕的零件质量中的容易引起用户投诉的质量特性,在成品装配前实行100%全检。检验标准执行企业的内控标准。