箱型柱加工制作工艺技术
箱型钢柱制作工艺方案
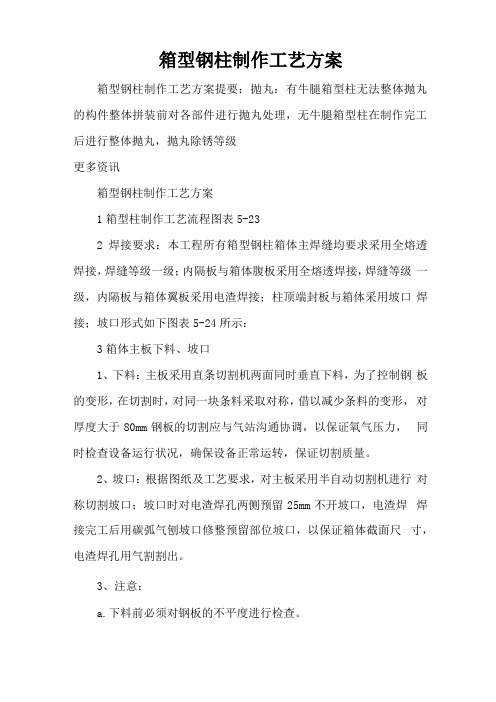
箱型钢柱制作工艺方案箱型钢柱制作工艺方案提要:抛丸:有牛腿箱型柱无法整体抛丸的构件整体拼装前对各部件进行抛丸处理,无牛腿箱型柱在制作完工后进行整体抛丸,抛丸除锈等级更多资讯箱型钢柱制作工艺方案1箱型柱制作工艺流程图表5-232焊接要求:本工程所有箱型钢柱箱体主焊缝均要求采用全熔透焊接,焊缝等级一级;内隔板与箱体腹板采用全熔透焊接,焊缝等级一级,内隔板与箱体翼板采用电渣焊接;柱顶端封板与箱体采用坡口焊接;坡口形式如下图表5-24所示:3箱体主板下料、坡口1、下料:主板采用直条切割机两面同时垂直下料,为了控制钢板的变形,在切割时,对同一块条料采取对称,借以减少条料的变形,对厚度大于80mm钢板的切割应与气站沟通协调,以保证氧气压力,同时检查设备运行状况,确保设备正常运转,保证切割质量。
2、坡口:根据图纸及工艺要求,对主板采用半自动切割机进行对称切割坡口;坡口时对电渣焊孔两侧预留25mm不开坡口,电渣焊焊接完工后用碳弧气刨坡口修整预留部位坡口,以保证箱体截面尺寸,电渣焊孔用气割割出。
3、注意:a.下料前必须对钢板的不平度进行检查。
b.翼板、腹板的平面度允许偏差:在1米长度内不平度在2mm以内。
c.发现不平度超差的禁止使用,平直度合格的钢板才能放样、号料和切割。
d.气割允许偏差:下料时长度方向加放50mm切割加工余量;切割长度、宽度允许偏差:±2;对角线允许偏差:3mm以内;切割表面的缺口深度:割缝深度或以内;局部缺口深度Wlmm, 并打磨平整过渡;切割表面与钢板表面的不垂直度:不得大于钢板厚度的5%,且不得大于;焊接坡口的切割表面的缺口深度:在以内。
下料前,对厚度三40mm厚板母材焊道中心线两侧各2倍板厚加30mm的区域内进行超声波探伤抽查,确保母材中裂纹、夹层等缺陷存在。
下料完成后,应对焊接面仔细检查,并清除割渣。
施工人员必须将下料后的零件加以标记并归类存放。
4装配、焊接箱型柱内隔板的装配焊接为保证电渣焊的焊接质量,对箱型柱的内隔板及夹板在下料时后,对于电渣焊挡板与柱体接触面及其端部进行铳削加工,以保证内隔板在装配焊接后与箱型柱面板之间的装配间隙在以内。
箱型柱制作工艺和各类包括的设备用法

一,施工准备、1、材料(1)钢材的品种、规格、性能应符合设计要求和国家现行有关产品标准的规定;进口钢材产品的质量应符合设计和合同规定的要求;均应具有产品质量合格证明文件。
(2)焊接材料包括焊条、焊丝、焊剂和焊接保护气体等,均必须具有产品质量合格证明文件、生产厂名及产品使用说明书等。
①焊条应符合国家现行标准《碳钢焊条》GB/T5117、《低合金钢焊条》GB/T5118的规定;②焊丝和焊剂:埋弧自动焊和气体保护焊焊丝的各项性能指标,应分别符合《埋弧焊用碳钢焊丝和焊剂》GB/T5293、《埋弧焊用低合金钢焊丝和焊剂》GB/12470、《熔化焊用钢丝》GB/T14957《气体保护焊用焊丝》GB/T8110的各项规定。
被选用的焊丝牌号必须与相应的钢材等级、焊剂和保护气体的成分相匹配。
③ CO2气体应符合《焊接用二氧化碳》HG/T2537的规定。
二,零件下料1 火焰切割(1),切割前应检查工作场地是否符合安全要求,去除钢材表面的污垢、油污、铁锈等杂物,并将工件垫平。
(2)工件下应留有一定的空隙以利于氧化铁渣的吹出,工件下的空间不得密封,避免在切割时引起爆炸。
(3)操作时应先从短边开始切割,防止气割变形。
切割顺序宜先割小件,后割大件,先割复杂工件,后割较简单工件。
(4)对箱形截面的翼板、腹板长度加放50mm余量,宽度不放余量;((6)对于每张钢板的排版,若下四块板时,尽量中间两块为翼板,两侧各一块为腹板,两侧最外边应保证各10mm以上的割去量。
如图所示(7)割缝余量如下表我厂根据经验一般割缝为2mm 和3mm 。
(8)气割时应选择正确的参数,应调节好氧气射流的形状,使其达到并保持轮廓清晰,风线长。
切割时除保证几何尺寸外还要保证切割的垂直度,不应有缺菱和崩坑。
(9) 钢板的拼接1)由于定长进料,原则上箱型柱的翼板、腹板不拼接。
2)但尺度超长或不得已时方可拼接,所有拼接焊缝为一级焊缝,无损探伤合格后,方可下料。
3)拼接时,焊缝应能避开柱节点位置,宜在节点区隔板上下500mm 以外。
箱型柱加工制作工艺..
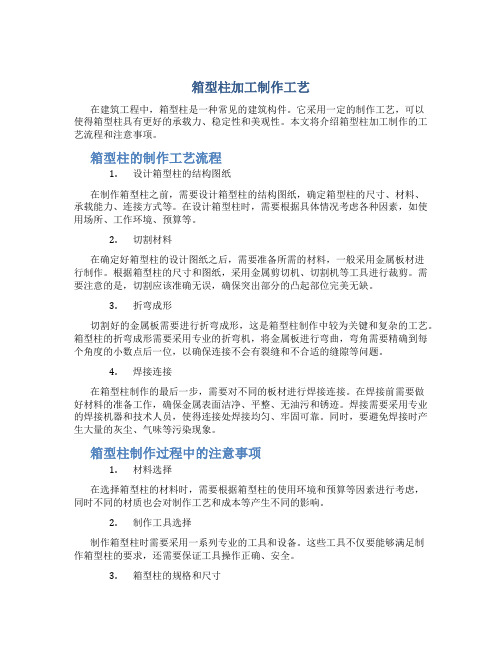
箱型柱加工制作工艺在建筑工程中,箱型柱是一种常见的建筑构件。
它采用一定的制作工艺,可以使得箱型柱具有更好的承载力、稳定性和美观性。
本文将介绍箱型柱加工制作的工艺流程和注意事项。
箱型柱的制作工艺流程1.设计箱型柱的结构图纸在制作箱型柱之前,需要设计箱型柱的结构图纸,确定箱型柱的尺寸、材料、承载能力、连接方式等。
在设计箱型柱时,需要根据具体情况考虑各种因素,如使用场所、工作环境、预算等。
2.切割材料在确定好箱型柱的设计图纸之后,需要准备所需的材料,一般采用金属板材进行制作。
根据箱型柱的尺寸和图纸,采用金属剪切机、切割机等工具进行裁剪。
需要注意的是,切割应该准确无误,确保突出部分的凸起部位完美无缺。
3.折弯成形切割好的金属板需要进行折弯成形,这是箱型柱制作中较为关键和复杂的工艺。
箱型柱的折弯成形需要采用专业的折弯机,将金属板进行弯曲,弯角需要精确到每个角度的小数点后一位,以确保连接不会有裂缝和不合适的缝隙等问题。
4.焊接连接在箱型柱制作的最后一步,需要对不同的板材进行焊接连接。
在焊接前需要做好材料的准备工作,确保金属表面洁净、平整、无油污和锈迹。
焊接需要采用专业的焊接机器和技术人员,使得连接处焊接均匀、牢固可靠。
同时,要避免焊接时产生大量的灰尘、气味等污染现象。
箱型柱制作过程中的注意事项1.材料选择在选择箱型柱的材料时,需要根据箱型柱的使用环境和预算等因素进行考虑,同时不同的材质也会对制作工艺和成本等产生不同的影响。
2.制作工具选择制作箱型柱时需要采用一系列专业的工具和设备。
这些工具不仅要能够满足制作箱型柱的要求,还需要保证工具操作正确、安全。
3.箱型柱的规格和尺寸在制作箱型柱时需要确保规格和尺寸的准确性。
因为任何一个方面偏差都可能导致制作出来的箱型柱无法使用,从而影响建筑工程的整体质量和效果。
4.制作环境制作箱型柱的环境也是需要考虑的因素。
当工作环境噪音,扰动大、灰尘多等环境问题会影响制作工艺的精度和质量。
箱形柱制作工艺
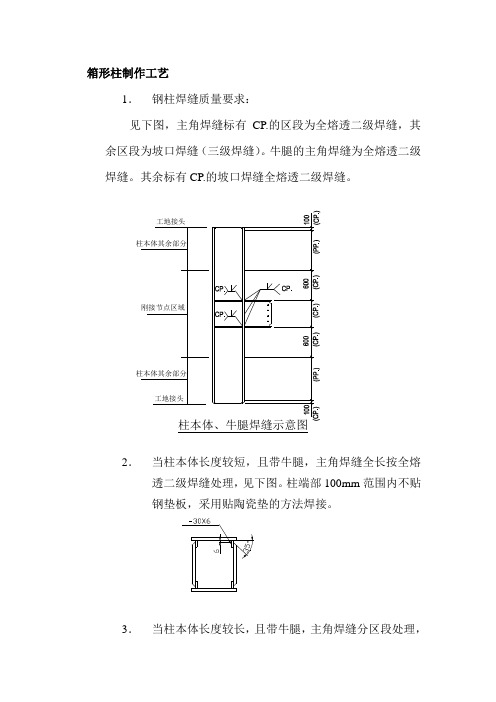
箱形柱制作工艺
1. 钢柱焊缝质量要求:
见下图,主角焊缝标有CP.的区段为全熔透二级焊缝,其余区段为坡口焊缝(三级焊缝)。
牛腿的主角焊缝为全熔透二级焊缝。
其余标有CP.的坡口焊缝全熔透二级焊缝。
柱本体、牛腿焊缝示意图
2. 当柱本体长度较短,且带牛腿,主角焊缝全长按全熔
透二级焊缝处理,见下图。
柱端部100mm 范围内不贴钢垫板,采用贴陶瓷垫的方法焊接。
3. 当柱本体长度较长,且带牛腿,
主角焊缝分区段处理,
腹板坡口按下图加工。
其中全熔透焊缝的坡口按型式
Ⅰ、Ⅱ,型式Ⅱ用于柱端部,局部熔透焊缝的坡口按
型式Ⅲ。
为减少焊接变形,全熔透焊缝的坡口根部采
用CO2气保焊打底填充约1/2的坡口深度、埋弧焊盖
面的焊接方法。
型式Ⅰ型式Ⅱ型式Ⅲ
4.当柱本体不带牛腿,主角焊缝除两端各100mm为全熔透二级焊缝、其余均为局部熔透焊缝,腹板坡口两端
各100mm按上图型式Ⅱ,其余按上图型式Ⅲ加工。
5.箱型柱的隔板焊接,当隔板的四面T型焊缝为全熔透坡口焊缝且位于箱型柱内部时,三面采用气保焊,另
一面采用熔嘴电渣焊,电渣焊部位见以下节点示意图,垫板-60×20与翼板之间须刨平顶紧。
6.箱形牛腿与箱形柱焊接,按下图(当两板之间不垂直时,应考虑自然坡口角度),焊缝等级为一级。
7.装配牛腿,螺栓孔到柱轴线的尺寸应作为装配控制尺寸进行检查,公差:±2 mm。
8.柱公差:柱弯曲、扭曲:≤3mm。
柱高度H:±3mm。
箱型钢柱加工工艺流程
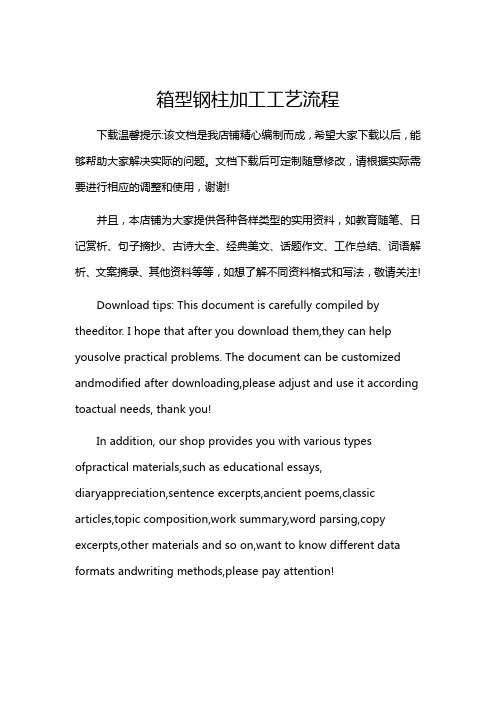
箱型钢柱加工工艺流程下载温馨提示:该文档是我店铺精心编制而成,希望大家下载以后,能够帮助大家解决实际的问题。
文档下载后可定制随意修改,请根据实际需要进行相应的调整和使用,谢谢!并且,本店铺为大家提供各种各样类型的实用资料,如教育随笔、日记赏析、句子摘抄、古诗大全、经典美文、话题作文、工作总结、词语解析、文案摘录、其他资料等等,如想了解不同资料格式和写法,敬请关注!Download tips: This document is carefully compiled by theeditor. I hope that after you download them,they can help yousolve practical problems. The document can be customized andmodified after downloading,please adjust and use it according toactual needs, thank you!In addition, our shop provides you with various types ofpractical materials,such as educational essays, diaryappreciation,sentence excerpts,ancient poems,classic articles,topic composition,work summary,word parsing,copy excerpts,other materials and so on,want to know different data formats andwriting methods,please pay attention!箱型钢柱加工工艺流程箱型钢柱的加工工艺流程包括多个方面,从原材料准备到最终产品形成,每个步骤都有其独特的工艺流程。
箱型柱,制作工艺
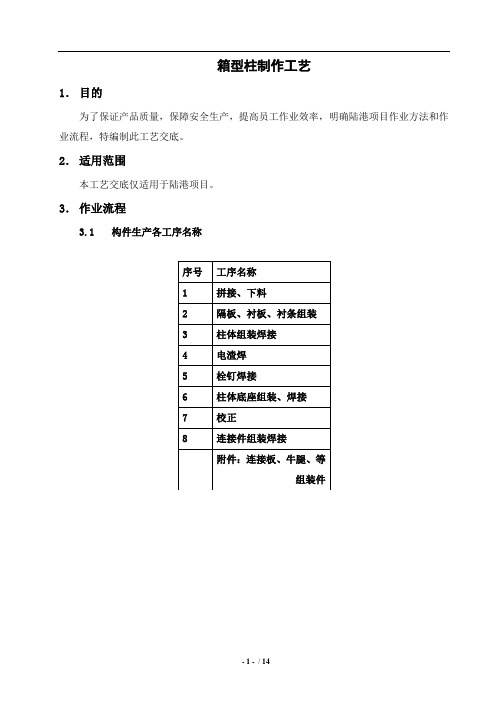
箱型柱制作工艺1.目的为了保证产品质量,保障安全生产,提高员工作业效率,明确陆港项目作业方法和作业流程,特编制此工艺交底。
2.适用范围本工艺交底仅适用于陆港项目。
3.作业流程3.1构件生产各工序名称3.2 工艺流程图3.3作业准备3.3.1工作前穿戴好劳保用品:安全帽、护目镜、口罩、手套、工作服和劳保鞋;气体保护焊机、电渣焊设备、角磨机、钢板尺、铁锤、3.3.2准备好生产工具:CO2卷尺、半自动切割等;3.3.3准备项目生产所需要的技术图纸。
注意:图纸图册不齐全不清晰时,应确认清楚后再使用。
3.4焊接方法及作业标准3.4.1根据图纸对物料进行分配,按照图纸的零件图进行归类,有无不合格产品,如有不符要求部件需对其修整,使其符合技术图纸要求。
3.4.2下料3.4.2.1.具体操作参照《小料零件剪切下料作业指导书》、《小料零件切割下料作业指导书》。
3.4.2.2.切割前的准备工作●在切割胎架上清除有碍于切割的杂物,清理干净;工作场地附近不得有易燃易爆物品。
●检查气源与切割设备的连接胶管有无漏气,气源供应量是否正常。
●割炬是否正常,切割应用通针清理割炬内孔;使割炬风线成笔直而清晰的圆柱体。
检查割炬纵向行走,横向及上下调节机构处于正常状态。
3.4.2.3.切割操作程序●操作人员必须经培训后上岗。
●调整各割炬位置,使割炬处于割缝的正上方,割炬离钢板表面距离宜为 10~15mm。
●按气割工艺参数要求调整切割速度。
●点燃割炬,再开预热氧阀,预热钢板边缘 1~2 分钟;打开切割氧气;调整火焰至中性焰;按钢板厚度调整火焰温度。
当氧化渣随气流一起飞出时,证明已割透。
按下行走按钮;开始试切割。
●当切割10~20mm 后,检查翼腹板的宽度是否符合要求,否则应进行调整。
●切割中应随时观察各个割炬是否正常,切割速度是否合适;并随时作调整。
●切割过程中,因割炬过热,堵塞而发生回火现象;应适时关闭氧气使之排除回火气体。
●切割至终端时,迅速关闭氧气阀,再关闭可燃气体,最后关闭预热氧气阀。
钢结构箱型柱异型柱制作生产工艺

钢结构箱型柱、异型柱制作生产工艺施工组织方案钢结构箱型柱、异型柱制作生产工艺工程名称:广州市正佳广场(西塔楼)建设单位:广州市正佳企业有限公司编制单位:日期:二〇〇八年五月十五日箱型柱、异型柱制作生产工艺一、制作准备1、技术准备(1)图纸会审:进行图纸会审,与甲方,设计人员,监理充分勾通,了解设计意图.(2)熟悉施工图:根据工厂、工地现场的实际起重能力和运输条件,核对施工图中钢结构的分段是否满足要求;工厂和工地的工艺条件是否能满足设计要求.(3)详图设计:根据设计文件进行构件详图设计,以便于加工制作和安装.(4)加工方案及工艺设计1)钢结构的加工工艺方案,由生产车间根据施工图及合同对钢结构质量、工期的要求编制,并经工厂(公司)总工程师审核,经设计单位代表批准后实施.2)根据构件特点和工厂实际情况,为保证产品质量和操作方便,应适当设计制作部分工装夹具.(5)组织必要的工艺实验,如焊接工艺评定等试验,尤其是对新工艺、新材料,做好工艺试验,作为指导生产的依据.(6)编制材料采购计划.2、材料要求(1)钢材制作钢结构的钢材应符合下列规定:1、板厚度、型钢的规格尺寸及允许偏差应符合其产品标准的要求,每一品种、规格抽查5处.2、材的表面外观质量除应符合国家现行有关标准的规定处,尚应符合下列规定:当钢材的表面有锈蚀、麻点可划痕等缺陷时,其深度不得大于该钢材厚度负允许偏差值的1/2;1.钢材表面的锈蚀等级应符合现行国家标准《涂装前钢材表面锈蚀等级和除锈等级》GB8923规定的C级及C级以上;2.钢材端边或断口处不应有分层、夹渣等缺陷.上述要求作全数观察检查.1)钢材应按种类、材质、炉(批)号、规格等分类平整堆放,并作好标记,堆放场地应有排水设施.2)钢材入库和发放应有专人负责,并及时记录验收和发放情况.3)钢结构制作的余料,应按种类、钢号和规格分别堆放,作好标记,记入台帐,妥善保管.(2)焊接材料1)焊条应符合现行国家标准《碳钢焊条》GB/T117、《低合金钢焊条》GB/T5118.2)焊丝应符合现行国家标准《熔化焊用钢丝》GB/T14957、《气体保护电弧焊用碳钢、低合金钢焊丝》GB/T8110及《碳钢药芯焊丝》GB/T10045、《低合金钢药芯焊丝》GB/T17493的规定.3)埋弧焊用焊丝和焊剂应符合现行国家标准《埋弧焊用碳钢焊丝和焊剂》GB/T5293、《低合金钢埋弧焊用焊剂》GB/T12470的规定.4)气体保护焊使用的氩气应符合现行国家标准《氩气》GB/T4842的规定,其纯度不应低于99.95%.气体保护焊使用的二氧化碳气体应符合现行国家标准《焊接用二氧化碳》GB/T2537的规定.大型、重型及特殊钢结构工程中主要构件的重要焊接节点采用的二氧化碳气体质量应符合该标准中优等品的要求,即其二氧化碳含量(V/V)不得低于99.9%,水蒸气与乙醇总含量(m/m)不得高于0.005%,并不得检出液态水。
钢结构箱型柱制作工艺
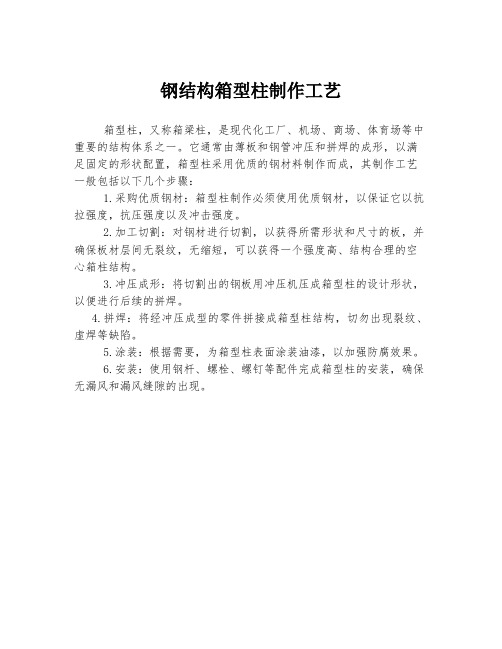
钢结构箱型柱制作工艺
箱型柱,又称箱梁柱,是现代化工厂、机场、商场、体育场等中重要的结构体系之一。
它通常由薄板和钢管冲压和拼焊的成形,以满足固定的形状配置,箱型柱采用优质的钢材料制作而成,其制作工艺一般包括以下几个步骤:
1.采购优质钢材:箱型柱制作必须使用优质钢材,以保证它以抗拉强度,抗压强度以及冲击强度。
2.加工切割:对钢材进行切割,以获得所需形状和尺寸的板,并确保板材层间无裂纹,无缩短,可以获得一个强度高、结构合理的空心箱柱结构。
3.冲压成形:将切割出的钢板用冲压机压成箱型柱的设计形状,以便进行后续的拼焊。
4.拼焊:将经冲压成型的零件拼接成箱型柱结构,切勿出现裂纹、虚焊等缺陷。
5.涂装:根据需要,为箱型柱表面涂装油漆,以加强防腐效果。
6.安装:使用钢杆、螺栓、螺钉等配件完成箱型柱的安装,确保无漏风和漏风缝隙的出现。
- 1、下载文档前请自行甄别文档内容的完整性,平台不提供额外的编辑、内容补充、找答案等附加服务。
- 2、"仅部分预览"的文档,不可在线预览部分如存在完整性等问题,可反馈申请退款(可完整预览的文档不适用该条件!)。
- 3、如文档侵犯您的权益,请联系客服反馈,我们会尽快为您处理(人工客服工作时间:9:00-18:30)。
建筑钢结构箱型柱加工制作工艺技术
小兵中楷剑峰晓斌志伟
(中建三局集团,430064)
摘要:箱型截面柱构件具有结构力学性能好、双向抗弯刚度大、自重轻等特点,目前在工业建筑中应用越来越广泛。
从下料、箱型梁组装、隔板组装、箱型柱焊接以及焊接变形控制等方面介绍了建筑钢结构箱型柱加工制作工艺技术。
关键词:箱型柱;制作工艺;焊接变形控制
1 箱型柱构件的主要特点
一般箱型柱由两块宽板和两块窄板(也可称为两块翼缘板和两块腹板)组成,在箱型柱牛腿上、下翼缘板对应位置设置隔板,且设计要求隔板与翼缘板和腹板全熔透焊接;高层钢结构箱型柱制作和安装通常分为若干节进行施工,下节柱的柱顶四边向50~100 mm围要端铣,端面铣垂直于柱身,以保证箱型柱整体的垂直度;箱型柱必须采用合理的焊接顺序以避免产生扭曲变形,造成上、下节柱对接时出现错口现象;隔板与翼缘板、腹板间须留有足够的间隙并用衬板围成焊道,用电渣焊填充焊道,实现隔板与主板的焊接,从而解决操作人员无法进入箱型柱部,对隔板与四面主板熔透焊缝的焊接问题。
为了达到对称焊接控制变形的目的,一般留置对应的两条焊缝用电渣焊对称施焊。
2 下料工艺
2.1 翼缘板和腹板的下料工艺
箱型柱由翼缘板和腹板组成,下料时应结合下料工艺和焊接工艺考虑切割余量和焊接收缩余量。
4块板下料时,采用门式多头气割机对翼板、腹板两侧同时进行切割,以确保翼缘板和腹板的平直度,翼缘板和腹板下料允许偏差为:宽度±1 mm、垂直度公差1 mm;在板材宽度的端头要用横向割枪切割坡口,单面35°留2 mm钝边,坡口与纵向切割线保证垂直,然后以实际长度进行下料。
主材腹板的坡口采用半自动气体切割机进行加工,腹板的两边坡口应同时切割以防切割后产生一边旁弯。
腹板坡口形式见图1。
图1 箱型柱主焊缝的坡口形式
在部分熔透和全焊透坡口交界位置,用气割将过渡处在部分焊透坡口处割除一个小三角块,再用砂轮打磨以平缓过渡,见图2。
2.2 隔板及衬板的下料工艺
隔板利用数控切割,尺寸规定b1为箱体壁宽度+8 mm(铣削量);b2为箱体壁宽度-50 mm(电渣焊焊孔φ25×2)。
图2 焊接过渡区
按图3进行隔板坡口和铣边加工,在45°过渡位置切完坡口后需进行打磨处理。
若设计要求隔板设置透气孔时,则采用摇臂钻床进行钻孔;若设置中间人孔时,用仿型切割机切割人孔。
隔板衬垫板下料后须端铣。
图3 隔板气割后示意
3 箱型柱的制作主要工艺流程
箱型柱制作工艺流程见图4。
图4 箱型柱制作工艺流程
4 箱型柱组装
箱型柱组装前先检查组装用零件的编号、材质、尺寸、数量和加工精度等是否符合图纸和工艺要求,确认后才能进行装配,构件组装要按照工艺流程进行。
组装平台用水准仪矫平,保证平台平面度误差在±2 mm围,并具有足够的强度和刚度保证在组装过程中不产生过大变形。
4.1 隔板定位
将一块翼缘板上胎架,从下端坡口处(包含预留现场对接的间隙)开始划线,按每个隔板收缩0.5 mm、主焊缝收缩3 mm均匀分摊到每个间距,然后划隔板组
装线的位置,隔板中心线延长到两侧并在两侧的翼板厚度方向中心打上样冲点,见图5。
图5 箱型柱隔板定位线
4.2 隔板装配
为保证箱型柱的截面尺寸在B±2.0 mm围,采取用加劲隔板组件来保证,几何尺寸和正确见图6。
在隔板组件装配前,对4块已铣边的工艺垫板和加工好坡口的隔板在胎架(隔板组立机)上进行装配,并进行焊接,保证其几何尺寸在允许围。
考虑到隔板与箱型柱4大片的焊接均为全熔透的焊接缝,在隔板组装时应考虑2 mm的焊接收缩余量。
隔板长度控制在0~2 mm,宽度控制在0~2 mm,对角线偏差控制在±1.0 mm围。
4.3 隔板固定
将隔板按已划好的定位线装在下翼缘板上,并点焊固定,为了提高柱子的刚性及抗扭能力,在部分焊透的区域每1.5 mm处设置一块工艺隔板,工艺隔板与4大片采用间断焊接,如图7所示。
图6 隔板组装示意
图7 隔板、工艺隔板点焊接示意
4.4 腹板组装
组装两块侧板,在胎架上进行拼装、校正、定位,定位焊的位置应在焊缝的反面。
将腹板与翼缘板下端对齐,并将腹板与翼缘板和隔板顶紧,然后装腹板的熔透焊处衬垫板,下侧的垫板应与下翼缘板顶紧,上侧的垫板上端应与部分焊透处钝边齐平。
垫板的长度可以任意切割,但须保证全焊透位置下面均有衬垫板以防焊接时铁水流到箱体空间,如图8所示。
图8 腹板组装示意
当柱本身较长时,为防止腹板组装发生扭曲,可做些定位夹具,如图9所示,最好在箱型梁组立机上组装。
图9 定位夹具示意
4.5 隔板焊接
对隔板进行焊接,隔板与侧板为单面V形坡口留间隙衬垫焊,采用CO2气体保护焊焊接,由于隔板单独焊接时会引起变形拉弯隔板,须在两隔板中间加撑杆固定住,可防止因焊接热输入引起隔板错动,必要时也可在两腹板之间加撑杆,见图10。
图10 防止隔板焊接变形撑杆示意
对于隔板间距较窄部位,为便于气保焊操作,应在组装时坡口朝外;当隔板又比较密集时,采用先装中间两块隔板,焊好后探伤合格才可从中间向两边依次退着装焊。
须保证隔板与腹板的焊接质量,探伤合格后方可盖板。
4.6 装上翼缘板
组装前清理U形口部的所有杂物,将上翼缘板下端开坡口处对齐,与两腹板压紧,需要注意的是一定要使得上翼缘板与隔板上边靠严(之前应用角尺测平面度以调节隔板上端的工艺垫块在同一水平面上),若留下间隙会使电渣焊接时铁水泄漏从而影响电渣焊质量,最后盖上翼缘板,见图11。
图11 盖上翼缘板
4.7 焊接箱型柱自身纵向焊缝
将坡口点焊固定,在组装好的箱体两端加设引熄弧板。
然后焊接箱型柱自身4条纵向焊缝,焊接前须在焊缝围和焊缝外侧面处单边30 mm围清除氧化皮、铁锈、油污等。
先用气体保护焊焊接全焊透坡口处,当焊透部分的焊缝与部分焊透的根部齐平时再纵向埋弧自动焊,主角焊缝同向对称焊接,以减少扭曲变形,焊接顺序见图12。
图12 箱型梁主焊缝焊接顺序
注:焊接顺序1→2→3→4。
5 箱型柱焊接
5.1 箱型柱的埋弧自动焊
若焊接坡口填充量较大,如单面全部焊接完会引起箱体变形时,可采用先焊1、2焊缝,焊缝深度达到填充量的一半时,翻过来焊3、4焊缝,待全部焊满后再翻过来将1、2焊缝焊满。
这样可使构件受热均匀,抵消焊接变形,一旦发生扭曲变形,矫正变形很困难,因此采用合理的焊接顺序对减少焊接变形至关重要。
5.2 电渣焊
按照翼缘板两侧事先打好的样冲点划线,定出钻孔位置,翻身180°同样划线将电渣焊焊接位置钻孔,清理孔无杂物。
然后移至电渣焊设备处进行电渣焊,两侧槽口应用两台焊机同时焊接。
采用丝极电渣焊,根据GB 50661—2011《钢结构焊接规》参数为:焊接电流380~400 A,焊接电压45~48 V。
丝极电渣焊焊接时应注意事项为:
1)电渣焊的夹板隔板组装前必须经过三边刨平处理;
2)为了防止电渣焊气孔发生,一定要在隔板组装前对电渣焊部位以及焊缝两侧各30 mm的围对油、锈和污物进行处理;
3)丝极电渣焊采用电渣弧压反馈自动调节系统,彻底解决了电渣焊接中间断弧问题;
4)焊接工艺参数符合焊接工艺评定要求。
5.3 箱型梁焊接变形的控制
箱型柱隔板的焊接采用热影响区比较小的CO2气体保护焊,按相同的焊接规参数进行焊接,以有效减少焊接变形。
箱型梁生产线同一隔板采用两台电渣焊机同时施焊,两台电渣焊机的工艺参数基本保持一致,通过合理的工艺参数控制,焊接成型后不会产生过大变形。
埋弧自动焊的坡口焊缝焊接收缩比较大,在坡口方向必须加大4 mm,由于埋弧自动焊接采用两台埋弧自动焊同时对称施焊,不会产生过大扭曲变形。
通过评定合格焊接工艺参数和合理的焊接顺序进行控制。
通过合理的焊接顺序控制箱型柱的焊接变形。
主要的焊接顺序和焊接原则为:先焊短焊缝、后焊长焊缝;先焊中间焊缝、后焊周边焊缝,先焊主要受力焊缝、后焊次要受力焊缝。
6 箱型柱的铣端
在箱型柱全部焊接、矫正完毕后,将钢柱放在平台上,用划线检验样杆放线,划线的容包括:4个面的中心线,上、下铣切或切割线和100 mm检验线,划线经过检验合格后送机加工铣头。
7 结束语
通过对箱型柱从下料、组装、焊接到端铣等制作全过程的研究,总结了成熟的箱型柱制作和焊接的全过程,可供生产同类箱型构件制作时参考。
参考文献:
[1]GB 50017—2003 钢结构设计规[S].
[2]GB 50205—2001 钢结构工程施工质量验收规[S].
[3]GB 50661—2011 钢结构焊接规[S].。