箱型柱,制作工艺
箱型钢柱制作工艺方案
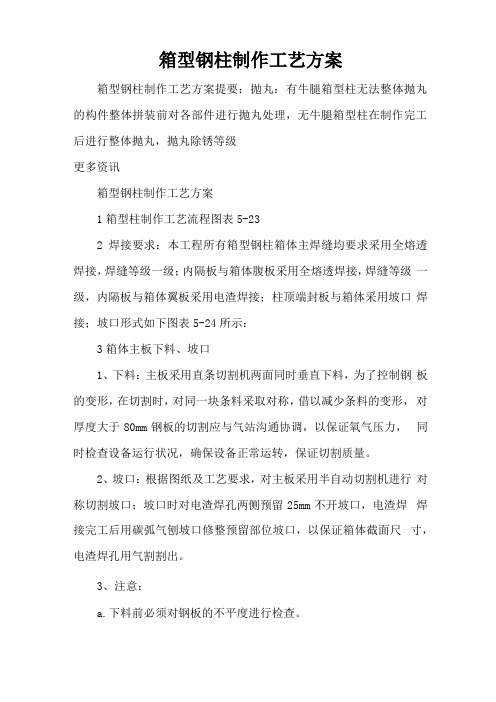
箱型钢柱制作工艺方案箱型钢柱制作工艺方案提要:抛丸:有牛腿箱型柱无法整体抛丸的构件整体拼装前对各部件进行抛丸处理,无牛腿箱型柱在制作完工后进行整体抛丸,抛丸除锈等级更多资讯箱型钢柱制作工艺方案1箱型柱制作工艺流程图表5-232焊接要求:本工程所有箱型钢柱箱体主焊缝均要求采用全熔透焊接,焊缝等级一级;内隔板与箱体腹板采用全熔透焊接,焊缝等级一级,内隔板与箱体翼板采用电渣焊接;柱顶端封板与箱体采用坡口焊接;坡口形式如下图表5-24所示:3箱体主板下料、坡口1、下料:主板采用直条切割机两面同时垂直下料,为了控制钢板的变形,在切割时,对同一块条料采取对称,借以减少条料的变形,对厚度大于80mm钢板的切割应与气站沟通协调,以保证氧气压力,同时检查设备运行状况,确保设备正常运转,保证切割质量。
2、坡口:根据图纸及工艺要求,对主板采用半自动切割机进行对称切割坡口;坡口时对电渣焊孔两侧预留25mm不开坡口,电渣焊焊接完工后用碳弧气刨坡口修整预留部位坡口,以保证箱体截面尺寸,电渣焊孔用气割割出。
3、注意:a.下料前必须对钢板的不平度进行检查。
b.翼板、腹板的平面度允许偏差:在1米长度内不平度在2mm以内。
c.发现不平度超差的禁止使用,平直度合格的钢板才能放样、号料和切割。
d.气割允许偏差:下料时长度方向加放50mm切割加工余量;切割长度、宽度允许偏差:±2;对角线允许偏差:3mm以内;切割表面的缺口深度:割缝深度或以内;局部缺口深度Wlmm, 并打磨平整过渡;切割表面与钢板表面的不垂直度:不得大于钢板厚度的5%,且不得大于;焊接坡口的切割表面的缺口深度:在以内。
下料前,对厚度三40mm厚板母材焊道中心线两侧各2倍板厚加30mm的区域内进行超声波探伤抽查,确保母材中裂纹、夹层等缺陷存在。
下料完成后,应对焊接面仔细检查,并清除割渣。
施工人员必须将下料后的零件加以标记并归类存放。
4装配、焊接箱型柱内隔板的装配焊接为保证电渣焊的焊接质量,对箱型柱的内隔板及夹板在下料时后,对于电渣焊挡板与柱体接触面及其端部进行铳削加工,以保证内隔板在装配焊接后与箱型柱面板之间的装配间隙在以内。
箱型柱制作工艺和各类包括的设备用法

一,施工准备、1、材料(1)钢材的品种、规格、性能应符合设计要求和国家现行有关产品标准的规定;进口钢材产品的质量应符合设计和合同规定的要求;均应具有产品质量合格证明文件。
(2)焊接材料包括焊条、焊丝、焊剂和焊接保护气体等,均必须具有产品质量合格证明文件、生产厂名及产品使用说明书等。
①焊条应符合国家现行标准《碳钢焊条》GB/T5117、《低合金钢焊条》GB/T5118的规定;②焊丝和焊剂:埋弧自动焊和气体保护焊焊丝的各项性能指标,应分别符合《埋弧焊用碳钢焊丝和焊剂》GB/T5293、《埋弧焊用低合金钢焊丝和焊剂》GB/12470、《熔化焊用钢丝》GB/T14957《气体保护焊用焊丝》GB/T8110的各项规定。
被选用的焊丝牌号必须与相应的钢材等级、焊剂和保护气体的成分相匹配。
③ CO2气体应符合《焊接用二氧化碳》HG/T2537的规定。
二,零件下料1 火焰切割(1),切割前应检查工作场地是否符合安全要求,去除钢材表面的污垢、油污、铁锈等杂物,并将工件垫平。
(2)工件下应留有一定的空隙以利于氧化铁渣的吹出,工件下的空间不得密封,避免在切割时引起爆炸。
(3)操作时应先从短边开始切割,防止气割变形。
切割顺序宜先割小件,后割大件,先割复杂工件,后割较简单工件。
(4)对箱形截面的翼板、腹板长度加放50mm余量,宽度不放余量;((6)对于每张钢板的排版,若下四块板时,尽量中间两块为翼板,两侧各一块为腹板,两侧最外边应保证各10mm以上的割去量。
如图所示(7)割缝余量如下表我厂根据经验一般割缝为2mm 和3mm 。
(8)气割时应选择正确的参数,应调节好氧气射流的形状,使其达到并保持轮廓清晰,风线长。
切割时除保证几何尺寸外还要保证切割的垂直度,不应有缺菱和崩坑。
(9) 钢板的拼接1)由于定长进料,原则上箱型柱的翼板、腹板不拼接。
2)但尺度超长或不得已时方可拼接,所有拼接焊缝为一级焊缝,无损探伤合格后,方可下料。
3)拼接时,焊缝应能避开柱节点位置,宜在节点区隔板上下500mm 以外。
箱型柱加工制作工艺..
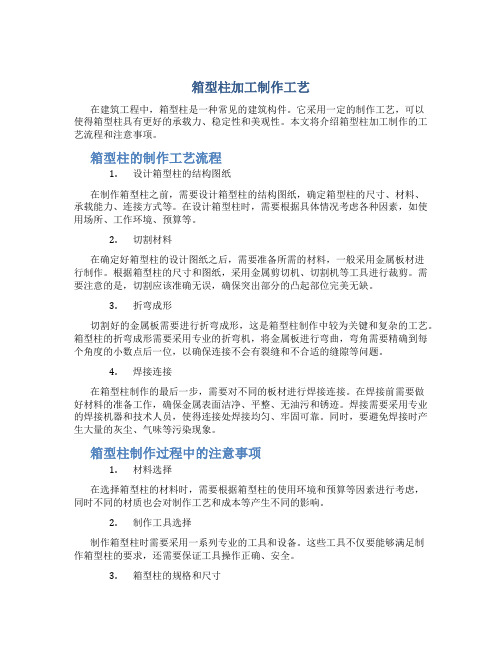
箱型柱加工制作工艺在建筑工程中,箱型柱是一种常见的建筑构件。
它采用一定的制作工艺,可以使得箱型柱具有更好的承载力、稳定性和美观性。
本文将介绍箱型柱加工制作的工艺流程和注意事项。
箱型柱的制作工艺流程1.设计箱型柱的结构图纸在制作箱型柱之前,需要设计箱型柱的结构图纸,确定箱型柱的尺寸、材料、承载能力、连接方式等。
在设计箱型柱时,需要根据具体情况考虑各种因素,如使用场所、工作环境、预算等。
2.切割材料在确定好箱型柱的设计图纸之后,需要准备所需的材料,一般采用金属板材进行制作。
根据箱型柱的尺寸和图纸,采用金属剪切机、切割机等工具进行裁剪。
需要注意的是,切割应该准确无误,确保突出部分的凸起部位完美无缺。
3.折弯成形切割好的金属板需要进行折弯成形,这是箱型柱制作中较为关键和复杂的工艺。
箱型柱的折弯成形需要采用专业的折弯机,将金属板进行弯曲,弯角需要精确到每个角度的小数点后一位,以确保连接不会有裂缝和不合适的缝隙等问题。
4.焊接连接在箱型柱制作的最后一步,需要对不同的板材进行焊接连接。
在焊接前需要做好材料的准备工作,确保金属表面洁净、平整、无油污和锈迹。
焊接需要采用专业的焊接机器和技术人员,使得连接处焊接均匀、牢固可靠。
同时,要避免焊接时产生大量的灰尘、气味等污染现象。
箱型柱制作过程中的注意事项1.材料选择在选择箱型柱的材料时,需要根据箱型柱的使用环境和预算等因素进行考虑,同时不同的材质也会对制作工艺和成本等产生不同的影响。
2.制作工具选择制作箱型柱时需要采用一系列专业的工具和设备。
这些工具不仅要能够满足制作箱型柱的要求,还需要保证工具操作正确、安全。
3.箱型柱的规格和尺寸在制作箱型柱时需要确保规格和尺寸的准确性。
因为任何一个方面偏差都可能导致制作出来的箱型柱无法使用,从而影响建筑工程的整体质量和效果。
4.制作环境制作箱型柱的环境也是需要考虑的因素。
当工作环境噪音,扰动大、灰尘多等环境问题会影响制作工艺的精度和质量。
箱形柱制作工艺
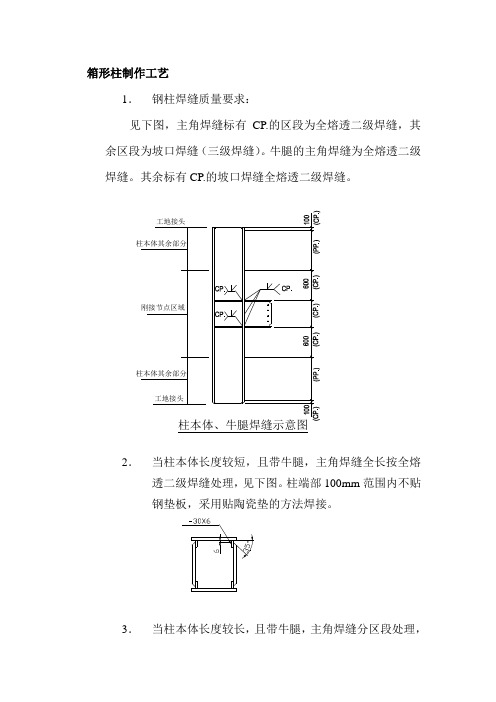
箱形柱制作工艺
1. 钢柱焊缝质量要求:
见下图,主角焊缝标有CP.的区段为全熔透二级焊缝,其余区段为坡口焊缝(三级焊缝)。
牛腿的主角焊缝为全熔透二级焊缝。
其余标有CP.的坡口焊缝全熔透二级焊缝。
柱本体、牛腿焊缝示意图
2. 当柱本体长度较短,且带牛腿,主角焊缝全长按全熔
透二级焊缝处理,见下图。
柱端部100mm 范围内不贴钢垫板,采用贴陶瓷垫的方法焊接。
3. 当柱本体长度较长,且带牛腿,
主角焊缝分区段处理,
腹板坡口按下图加工。
其中全熔透焊缝的坡口按型式
Ⅰ、Ⅱ,型式Ⅱ用于柱端部,局部熔透焊缝的坡口按
型式Ⅲ。
为减少焊接变形,全熔透焊缝的坡口根部采
用CO2气保焊打底填充约1/2的坡口深度、埋弧焊盖
面的焊接方法。
型式Ⅰ型式Ⅱ型式Ⅲ
4.当柱本体不带牛腿,主角焊缝除两端各100mm为全熔透二级焊缝、其余均为局部熔透焊缝,腹板坡口两端
各100mm按上图型式Ⅱ,其余按上图型式Ⅲ加工。
5.箱型柱的隔板焊接,当隔板的四面T型焊缝为全熔透坡口焊缝且位于箱型柱内部时,三面采用气保焊,另
一面采用熔嘴电渣焊,电渣焊部位见以下节点示意图,垫板-60×20与翼板之间须刨平顶紧。
6.箱形牛腿与箱形柱焊接,按下图(当两板之间不垂直时,应考虑自然坡口角度),焊缝等级为一级。
7.装配牛腿,螺栓孔到柱轴线的尺寸应作为装配控制尺寸进行检查,公差:±2 mm。
8.柱公差:柱弯曲、扭曲:≤3mm。
柱高度H:±3mm。
钢结构箱型柱异型柱制作生产工艺

钢结构箱型柱、异型柱制作生产工艺施工组织方案钢结构箱型柱、异型柱制作生产工艺工程名称:广州市正佳广场(西塔楼)建设单位:广州市正佳企业有限公司编制单位:日期:二〇〇八年五月十五日箱型柱、异型柱制作生产工艺一、制作准备1、技术准备(1)图纸会审:进行图纸会审,与甲方,设计人员,监理充分勾通,了解设计意图.(2)熟悉施工图:根据工厂、工地现场的实际起重能力和运输条件,核对施工图中钢结构的分段是否满足要求;工厂和工地的工艺条件是否能满足设计要求.(3)详图设计:根据设计文件进行构件详图设计,以便于加工制作和安装.(4)加工方案及工艺设计1)钢结构的加工工艺方案,由生产车间根据施工图及合同对钢结构质量、工期的要求编制,并经工厂(公司)总工程师审核,经设计单位代表批准后实施.2)根据构件特点和工厂实际情况,为保证产品质量和操作方便,应适当设计制作部分工装夹具.(5)组织必要的工艺实验,如焊接工艺评定等试验,尤其是对新工艺、新材料,做好工艺试验,作为指导生产的依据.(6)编制材料采购计划.2、材料要求(1)钢材制作钢结构的钢材应符合下列规定:1、板厚度、型钢的规格尺寸及允许偏差应符合其产品标准的要求,每一品种、规格抽查5处.2、材的表面外观质量除应符合国家现行有关标准的规定处,尚应符合下列规定:当钢材的表面有锈蚀、麻点可划痕等缺陷时,其深度不得大于该钢材厚度负允许偏差值的1/2;1.钢材表面的锈蚀等级应符合现行国家标准《涂装前钢材表面锈蚀等级和除锈等级》GB8923规定的C级及C级以上;2.钢材端边或断口处不应有分层、夹渣等缺陷.上述要求作全数观察检查.1)钢材应按种类、材质、炉(批)号、规格等分类平整堆放,并作好标记,堆放场地应有排水设施.2)钢材入库和发放应有专人负责,并及时记录验收和发放情况.3)钢结构制作的余料,应按种类、钢号和规格分别堆放,作好标记,记入台帐,妥善保管.(2)焊接材料1)焊条应符合现行国家标准《碳钢焊条》GB/T117、《低合金钢焊条》GB/T5118.2)焊丝应符合现行国家标准《熔化焊用钢丝》GB/T14957、《气体保护电弧焊用碳钢、低合金钢焊丝》GB/T8110及《碳钢药芯焊丝》GB/T10045、《低合金钢药芯焊丝》GB/T17493的规定.3)埋弧焊用焊丝和焊剂应符合现行国家标准《埋弧焊用碳钢焊丝和焊剂》GB/T5293、《低合金钢埋弧焊用焊剂》GB/T12470的规定.4)气体保护焊使用的氩气应符合现行国家标准《氩气》GB/T4842的规定,其纯度不应低于99.95%.气体保护焊使用的二氧化碳气体应符合现行国家标准《焊接用二氧化碳》GB/T2537的规定.大型、重型及特殊钢结构工程中主要构件的重要焊接节点采用的二氧化碳气体质量应符合该标准中优等品的要求,即其二氧化碳含量(V/V)不得低于99.9%,水蒸气与乙醇总含量(m/m)不得高于0.005%,并不得检出液态水。
钢结构箱型柱制作工艺
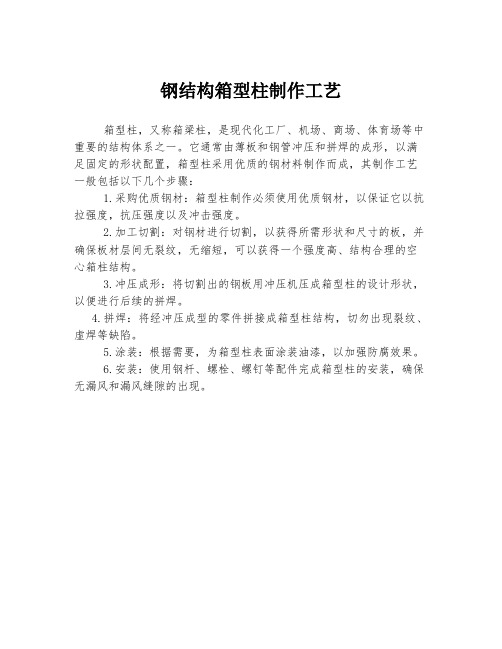
钢结构箱型柱制作工艺
箱型柱,又称箱梁柱,是现代化工厂、机场、商场、体育场等中重要的结构体系之一。
它通常由薄板和钢管冲压和拼焊的成形,以满足固定的形状配置,箱型柱采用优质的钢材料制作而成,其制作工艺一般包括以下几个步骤:
1.采购优质钢材:箱型柱制作必须使用优质钢材,以保证它以抗拉强度,抗压强度以及冲击强度。
2.加工切割:对钢材进行切割,以获得所需形状和尺寸的板,并确保板材层间无裂纹,无缩短,可以获得一个强度高、结构合理的空心箱柱结构。
3.冲压成形:将切割出的钢板用冲压机压成箱型柱的设计形状,以便进行后续的拼焊。
4.拼焊:将经冲压成型的零件拼接成箱型柱结构,切勿出现裂纹、虚焊等缺陷。
5.涂装:根据需要,为箱型柱表面涂装油漆,以加强防腐效果。
6.安装:使用钢杆、螺栓、螺钉等配件完成箱型柱的安装,确保无漏风和漏风缝隙的出现。
箱型柱制作工艺
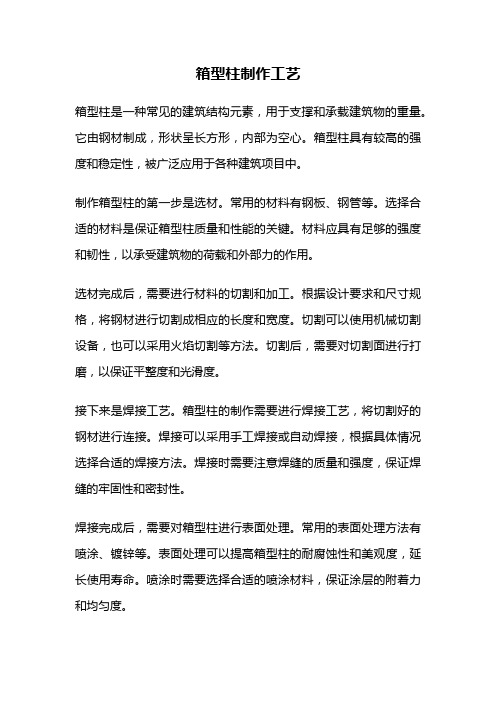
箱型柱制作工艺箱型柱是一种常见的建筑结构元素,用于支撑和承载建筑物的重量。
它由钢材制成,形状呈长方形,内部为空心。
箱型柱具有较高的强度和稳定性,被广泛应用于各种建筑项目中。
制作箱型柱的第一步是选材。
常用的材料有钢板、钢管等。
选择合适的材料是保证箱型柱质量和性能的关键。
材料应具有足够的强度和韧性,以承受建筑物的荷载和外部力的作用。
选材完成后,需要进行材料的切割和加工。
根据设计要求和尺寸规格,将钢材进行切割成相应的长度和宽度。
切割可以使用机械切割设备,也可以采用火焰切割等方法。
切割后,需要对切割面进行打磨,以保证平整度和光滑度。
接下来是焊接工艺。
箱型柱的制作需要进行焊接工艺,将切割好的钢材进行连接。
焊接可以采用手工焊接或自动焊接,根据具体情况选择合适的焊接方法。
焊接时需要注意焊缝的质量和强度,保证焊缝的牢固性和密封性。
焊接完成后,需要对箱型柱进行表面处理。
常用的表面处理方法有喷涂、镀锌等。
表面处理可以提高箱型柱的耐腐蚀性和美观度,延长使用寿命。
喷涂时需要选择合适的喷涂材料,保证涂层的附着力和均匀度。
最后是质量检验和包装。
制作完成的箱型柱需要进行质量检验,检查尺寸、焊缝和表面处理等是否符合要求。
检验合格后,进行包装,以便运输和安装。
包装可以采用木箱、塑料薄膜等材料,保护箱型柱不受外界环境和物理损害。
通过以上的工艺流程,箱型柱的制作就完成了。
箱型柱的制作工艺需要严格遵循相关标准和要求,确保制作出的箱型柱具有良好的质量和性能。
箱型柱作为建筑结构的重要组成部分,承担着重要的支撑和承载作用,对于建筑的安全和稳定性至关重要。
因此,制作过程中需要严谨认真,确保每一个环节都符合要求,以保证制作出的箱型柱能够满足工程需要。
以上就是关于箱型柱制作工艺的介绍,希望对大家有所帮助。
箱型钢柱制作工艺方案
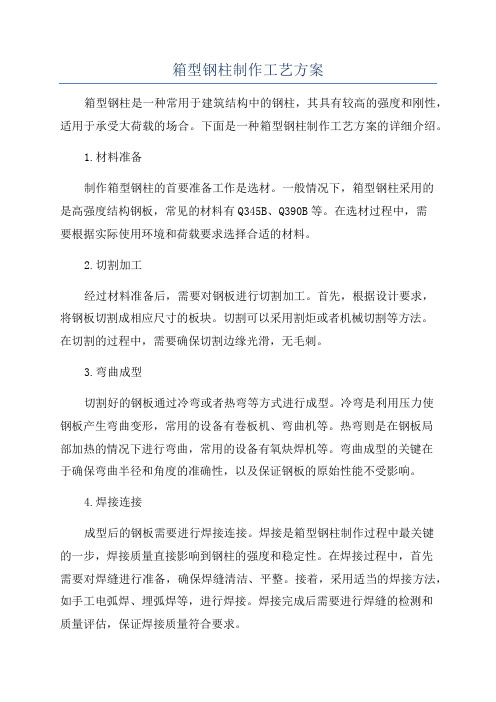
箱型钢柱制作工艺方案箱型钢柱是一种常用于建筑结构中的钢柱,其具有较高的强度和刚性,适用于承受大荷载的场合。
下面是一种箱型钢柱制作工艺方案的详细介绍。
1.材料准备制作箱型钢柱的首要准备工作是选材。
一般情况下,箱型钢柱采用的是高强度结构钢板,常见的材料有Q345B、Q390B等。
在选材过程中,需要根据实际使用环境和荷载要求选择合适的材料。
2.切割加工经过材料准备后,需要对钢板进行切割加工。
首先,根据设计要求,将钢板切割成相应尺寸的板块。
切割可以采用割炬或者机械切割等方法。
在切割的过程中,需要确保切割边缘光滑,无毛刺。
3.弯曲成型切割好的钢板通过冷弯或者热弯等方式进行成型。
冷弯是利用压力使钢板产生弯曲变形,常用的设备有卷板机、弯曲机等。
热弯则是在钢板局部加热的情况下进行弯曲,常用的设备有氧炔焊机等。
弯曲成型的关键在于确保弯曲半径和角度的准确性,以及保证钢板的原始性能不受影响。
4.焊接连接成型后的钢板需要进行焊接连接。
焊接是箱型钢柱制作过程中最关键的一步,焊接质量直接影响到钢柱的强度和稳定性。
在焊接过程中,首先需要对焊缝进行准备,确保焊缝清洁、平整。
接着,采用适当的焊接方法,如手工电弧焊、埋弧焊等,进行焊接。
焊接完成后需要进行焊缝的检测和质量评估,保证焊接质量符合要求。
5.表面处理焊接完成后,钢柱的表面需要进行处理,以防止钢柱受到氧化、腐蚀等影响。
常见的表面处理方法有喷漆、镀锌等。
喷漆可使用适当的喷漆设备,喷涂耐候性好的油漆,保护钢柱表面。
镀锌是将钢柱浸入熔融的锌液中,形成一层锌膜,保护钢柱免受氧化腐蚀。
6.质量检验完成制作工艺后,需要对箱型钢柱进行质量检验。
主要包括外观检查、尺寸检查、焊缝质量检查等。
外观检查主要是检查钢柱表面有无明显缺陷和瑕疵;尺寸检查主要是对钢柱的尺寸进行测量,检查是否符合设计要求;焊缝质量检查主要是通过无损检测等方法检查焊缝的质量。
以上是一种箱型钢柱制作工艺方案的详细介绍。
在实际制作过程中,还需要根据具体情况进行调整和优化,确保钢柱的质量和性能满足设计要求。
- 1、下载文档前请自行甄别文档内容的完整性,平台不提供额外的编辑、内容补充、找答案等附加服务。
- 2、"仅部分预览"的文档,不可在线预览部分如存在完整性等问题,可反馈申请退款(可完整预览的文档不适用该条件!)。
- 3、如文档侵犯您的权益,请联系客服反馈,我们会尽快为您处理(人工客服工作时间:9:00-18:30)。
箱型柱制作工艺
1.目的
为了保证产品质量,保障安全生产,提高员工作业效率,明确陆港项目作业方法和作业流程,特编制此工艺交底。
2.适用范围
本工艺交底仅适用于陆港项目。
3.作业流程
3.1构件生产各工序名称
3.2 工艺流程图
3.3作业准备
3.3.1工作前穿戴好劳保用品:安全帽、护目镜、口罩、手套、工作服和劳保鞋;
气体保护焊机、电渣焊设备、角磨机、钢板尺、铁锤、
3.3.2准备好生产工具:CO
2
卷尺、半自动切割等;
3.3.3准备项目生产所需要的技术图纸。
注意:图纸图册不齐全不清晰时,应确认清楚后再使用。
3.4焊接方法及作业标准
3.4.1根据图纸对物料进行分配,按照图纸的零件图进行归类,有无不合格产品,如有不符要求部件需对其修整,使其符合技术图纸要求。
3.4.2下料
3.4.2.1.具体操作参照《小料零件剪切下料作业指导书》、《小料零件切割下料作业指导书》。
3.4.2.2.切割前的准备工作
●在切割胎架上清除有碍于切割的杂物,清理干净;工作场地附近不得有易燃易爆物品。
●检查气源与切割设备的连接胶管有无漏气,气源供应量是否正常。
●割炬是否正常,切割应用通针清理割炬内孔;使割炬风线成笔直而清晰的圆柱体。
检查割炬纵向行走,横向及上下调节机构处于正常状态。
3.4.2.3.切割操作程序
●操作人员必须经培训后上岗。
●调整各割炬位置,使割炬处于割缝的正上方,割炬离钢板表面距离宜为 10~15mm。
●按气割工艺参数要求调整切割速度。
●点燃割炬,再开预热氧阀,预热钢板边缘 1~2 分钟;打开切割氧气;调整火焰至中性焰;按钢板厚度调整火焰温度。
当氧化渣随气流一起飞出时,证明已割透。
按下行走按钮;开始试切割。
●当切割10~20mm 后,检查翼腹板的宽度是否符合要求,否则应进行调整。
●切割中应随时观察各个割炬是否正常,切割速度是否合适;并随时作调整。
●切割过程中,因割炬过热,堵塞而发生回火现象;应适时关闭氧气使之排除回火
气体。
●切割至终端时,迅速关闭氧气阀,再关闭可燃气体,最后关闭预热氧气阀。
●切割完成的条板(翼腹板)的切割面熔渣等必须清理干净。
3.4.2.1箱柱侧板下料开破口需用半自动如图所示
●坡口加工方法:半自动切割机。
●坡口形式和尺寸:按设计图纸要求,如设计无要求时推荐如下:当翼腹板16≤t≤32 时
制作定位工装辅助切割坡口
当翼腹板 t>32 时
● 在半熔透坡口和全熔透坡口处的过渡部分以 1: 4 圆顺过渡
● 箱型柱两端各100mm 处应为全熔透焊缝,焊接时要引出本体至熄弧板大于1/2长度,应正确安装熄弧板。
● 隔板为双面30~35°坡口,两侧对称施焊 3.4.3 附件焊接及板材拼接原则
➢ 焊接H 型钢、箱形柱因板长不够而需对接拼接,翼缘与腹板的对接焊缝间的相对位置应错开200mm 以上,错开加劲板、连接板、节点不小于200mm ;焊接H 型钢翼缘板拼接长度不应小于2倍板宽、且不小于600mm ,腹板拼接长度不小于600mm 。
3.4.3.1
箱柱组装前箱柱内壁焊接栓钉。
放大图A
图A
3.4.3.2出气孔补强板焊接
3.4.4箱柱组焊
3.4.4.1隔板、垫板组装
➢隔板、垫板组装尺寸按照下图,留有机加工余量,各侧均匀分配,隔板与垫板应贴密间隙≤0.5mm.
➢检查组装尺寸后进行正反面点固焊。
➢脱模后,加焊角焊全长,除净焊渣、毛刺、飞溅等。
➢检查隔板组装件四角是否垂直,合格后方可送机加四周铣削。
➢首件合格后,方可批量生产;中间随时检查组装胎具,以免失真。
3.4.4.2隔板铣削及坡口制备
➢隔板为双面30~35°坡口,两侧对称施焊
➢组装成型后隔板必须四侧铣削,可放置在端面铣床上加工,铣削余量每边≈3.0mm;应保持两侧空间近似相等,不能余量留置单边,影响焊接。
注意(Caution):
➢对边允许公差:L1+ΔL1、L2+ΔL2,0<ΔL<1mm
➢对角线允许公差:L3-L4 <1.5mm
➢L1 与L2 垂直度<1.0mm
3.4.4.3隔板间L1、L2 应预留焊接收缩余量。
隔板组成铣削后去除铣削毛刺,做1x45°倾角。
检验合格后方可组装整体组装、焊接。
L1、L2(mm)焊接收缩余量(mm)
400~600 1~1.2
600~800 1.2~1.5
800~1000 1.5~2.0
3.4.4.4组装胎架和夹具
3.4.4.4.1首先检查上道工序加工的上下翼板、腹板、隔板组件尺寸,坡口是否满足要求,熔渣、毛刺是否清理干净。
3.4.4.4.2组装下翼缘板和内隔板,纵向收缩量Δ≈0.5~0.8mm
3.4.4.4.3在整平的台架上,以下翼板为基准组装,划出内隔板的安装线和腹板安装线;每层隔板间留焊接余量0.5~0.8(以此类推),点焊固定。
3.4.4.4.4组装两侧腹板
➢组装二侧腹板,并保证垂直度,点固焊,形成U 型;打底处根部衬板间隙要保持3~4mm,以保证熔透,可在侧面用千斤顶使腹板和隔板密贴间隙小于0.5mm。
腹板两侧气割电渣焊
焊接孔30*30
对有缝隙处焊
接填充电渣焊
垫板
➢电渣焊垫板点焊固定。
上端可用移动式夹具夹紧,三面围焊。
➢如有端头封板时,四周开45°破口且留2mm间隙。
➢上口与下翼板引出线,在腹板上引线,做UT 用。
➢检查翼腹板拼缝距离,需≥500mm,腹板拼缝与隔板距离≥150mm。
腹板与下翼板、隔板组成 U 形件,侧翻90°,进行所有隔板 GMAW 坡口焊接,焊完至构件冷却进行UT 检测合格后方可盖上翼板。
3.4.4.4.5隔板焊接
➢每个隔板两侧200~300mm处焊接支撑,以防变形。
腹板两侧,距衬垫距离约
15~20mm,固定斜撑
3.4.4.4.6安装上翼板
3.4.4.4.7箱型构件四条纵缝焊接
➢在电渣焊完,隔板UT 合格后清理好引熄弧物,四条纵向组合焊缝采用GMAW打底填充,埋弧自动焊盖面。
➢焊接时采用在水平位置焊接,焊接时从中间两面向两端对称焊接。
电渣焊接参数
焊接方法 焊丝直径、焊剂 电流A 电压V
ESW
Ø2 HJ431
330~360 25~30
埋弧焊接参数
焊接方法 焊丝、牌号、直径 焊剂或气体 电流 A 电压 V
cm/min 速度
GMAW ER50-6 Ø1.2 CO2 120~130 20~22 14~16
SAW
H08MnA Ø5.0
SJ101
650~700 34~36 30~32
3.4.5 牛腿部位焊接
注意(Caution ):
两端焊时要引出本体至引熄弧板>120mm
在与箱柱装配前
焊接栓钉
坡口角度参照
技术交底
所有牛腿对接处两
侧开坡口焊接
3.4.6底座及构件节点位置焊接
所有框架、桁架等构件节点区域内界面组合焊缝均为全熔透一级焊缝。
此处为一级焊缝
4.抛丸
4.1.所有构件禁止超过宽1.5m高1.7m进入抛丸机
4.2.箱型柱与牛腿分开抛丸后进行组焊
4.3.附件组焊影响抛丸的,应组焊前以零件形式抛丸
5.生产自检
5.1.检查无误后转到下工序。
5.2.打扫卫生,整理现场,并把工具归类。
6.注意事项
6.1.本工序,如涉及到工具、设备的具体操作方法,可参阅其配套的说明书。
6.2.本工序,如涉及到其他工艺守则或作业指导书,可参阅具体文件。
6.3.如发现异常时,应及时向上级报告。
6.4.作业前中后,都应执行6S管理。
6.5.作业后,更应注意整理工作现场,确保物料、工具等摆放整齐,标识清晰。
6.6.该道工序操作完毕后,应距端头1000mm中间位置打钢印。
6.7.当构件总装外形尺寸大于宽1500 mm、高度1500mm要分批次抛丸。
6.8.对30mm 以上厚板焊接、为防止在厚度方向出现层状撕裂,采取措施:对母材焊
道中心线两侧各2倍板厚加30mm的区域内进行超声波探伤检查。
母材中不得有裂纹、夹层及分层等缺陷存在。
6.9.严格控制焊接顺序,尽可能减少板厚方向的约束。
6.10.根据母材的碳当量及焊接裂纹敏感性系数值选择正确的预热措施和后热处理。
6.11.当焊件厚度较大(>36mm)时,宜按接头的约束条件考虑焊接的预热措施,并根据焊接工艺评定试验结果确定焊后是否需要采取保温措施。
6.12.对接接头、T型接头和要求全熔透的角部焊缝,应在焊缝两端配置引弧板和引出板,其材质应与焊件相同。
气体保护焊引板长度不应小于60mm,埋弧自动焊引板长度不应小于120mm,引焊到引板上的焊缝不得小于引板长度的2/3。