化工原理_34精馏过程的节能途径
蒸馏技术的强化与节能
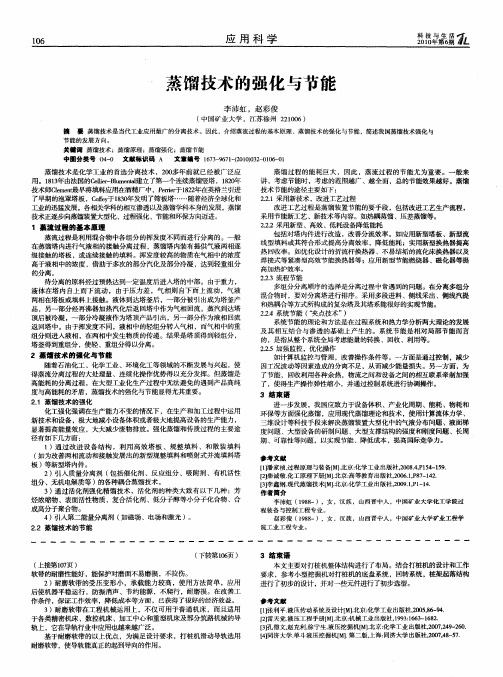
2 蒸 馏技 术 的强化 与 节能
随着石油化工 、化学工业 、环境化工等领域的不断发展与兴起 ,使 得蒸流分离过程的大处理量 、连续化操作优势得以充分发挥 。但蒸馏是 高能耗的分离过程 ,在大型工业化生产过程 中无法避免的遇到产品高纯 度与高能耗的矛盾 ,蒸馏技术 的强化与节能显得尤其重要 。 21 蒸馏技术的强化 . 化工强化强调在生产能力不变的情况下 ,在生产和加工过程 中运用 新技术和设备 ,极大地减小设备体积或者极大地提高设备 的生产能力 , 显著提高能量效应 ,大大减少废物排放。强化蒸馏和传质过程 的主要途 径有如下几方面: 1 通过改 进设备 结构 ,利用高效 塔板 、规整填 料 、和散装填料 ) ( 如为改善两相流动和接触发展出的新型规整填料和喷射式并流填料塔 板) 等新型塔内件 。 2 )引入质量分离剂 ( 包括催化 剂、反应组分 、吸附剂、有机活性 组分、无机电解质等 ) 的各种耦合蒸馏技术。 3 通 过活化 剂强化精馏技 术 ,活化剂的种类 大致有以下几种 : ) 芳
1 蒸流 过 程的 基本原 理
蒸流过程是利用混合物 中各组分的挥发度不 同而进行 分离的。一般 在蒸馏塔内进行气液相的接触分离过程 ,蒸馏塔 内装有提供气液两相逐 级接触的塔板 ,或连续接触 的填料 。挥发度较高 的物质在气相 中的浓度 高于液相中的浓度 ,借助于多次 的部分汽化及部分冷凝 ,达到轻重组分 的分离。 待分离 的原料经过预热达到一定温度后进入塔的中部 。由于重力 , 液体 在塔 内 自上而下流 动,由于压力差 ,气相则 自下而上 流动 ,气液 两相在塔板或填料上接触 。液体到达塔釜后 ,一部分被引出成为塔釜产 品,另一部分经再沸器加热汽化后返回塔中作为气相回流。蒸汽到达塔 顶后被冷凝 , 一部分冷凝液作为塔顶产品引出,另一部分作为液相回流 返 回塔中。由于挥发度不同 , 液相 中的轻组分转入气相 ,而气相 中的重 组分则进入液相 ,在两相 中发生物质的传递 。结果是塔 顶得到轻组分 , 塔釜得到重组分,使轻 、 重组分得以分离。
精馏过程的节能途径及新型的精馏技术
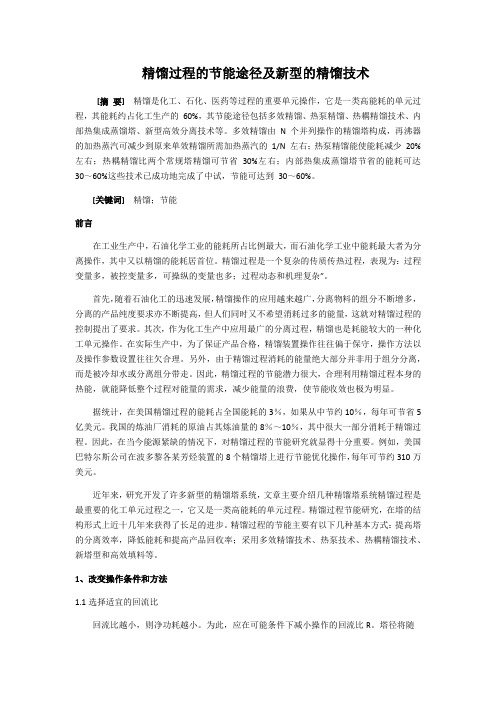
精馏过程的节能途径及新型的精馏技术[摘要]精馏是化工、石化、医药等过程的重要单元操作,它是一类高能耗的单元过程,其能耗约占化工生产的60%,其节能途径包括多效精馏、热泵精馏、热耦精馏技术、内部热集成蒸馏塔、新型高效分离技术等。
多效精馏由N 个并列操作的精馏塔构成,再沸器的加热蒸汽可减少到原来单效精馏所需加热蒸汽的1/N 左右;热泵精馏能使能耗减少20%左右;热耦精馏比两个常规塔精馏可节省30%左右;内部热集成蒸馏塔节省的能耗可达30~60%这些技术已成功地完成了中试,节能可达到30~60%。
[关键词]精馏;节能前言在工业生产中,石油化学工业的能耗所占比例最大,而石油化学工业中能耗最大者为分离操作,其中又以精馏的能耗居首位。
精馏过程是一个复杂的传质传热过程,表现为:过程变量多,被控变量多,可操纵的变量也多;过程动态和机理复杂”。
首先,随着石油化工的迅速发展,精馏操作的应用越来越广,分离物料的组分不断增多,分离的产品纯度要求亦不断提高,但人们同时又不希望消耗过多的能量,这就对精馏过程的控制提出了要求。
其次,作为化工生产中应用最广的分离过程,精馏也是耗能较大的一种化工单元操作。
在实际生产中,为了保证产品合格,精馏装置操作往往偏于保守,操作方法以及操作参数设置往往欠合理。
另外,由于精馏过程消耗的能量绝大部分并非用于组分分离,而是被冷却水或分离组分带走。
因此,精馏过程的节能潜力很大,合理利用精馏过程本身的热能,就能降低整个过程对能量的需求,减少能量的浪费,使节能收效也极为明显。
据统计,在美国精馏过程的能耗占全国能耗的3%,如果从中节约10%,每年可节省5亿美元。
我国的炼油厂消耗的原油占其炼油量的8%~10%,其中很大一部分消耗于精馏过程。
因此,在当今能源紧缺的情况下,对精馏过程的节能研究就显得十分重要。
例如,美国巴特尔斯公司在波多黎各某芳烃装置的8个精馏塔上进行节能优化操作,每年可节约310万美元。
近年来,研究开发了许多新型的精馏塔系统,文章主要介绍几种精馏塔系统精馏过程是最重要的化工单元过程之一,它又是一类高能耗的单元过程。
(化工原理)精馏原理

精馏的原理和过程
原理
基于物质的沸点不同,通过加热和冷凝的方法,将不同沸点的物 质分离出来。
过程
将液体混合物加热至沸腾,产生的蒸汽在冷凝器中冷凝,再通过 回流装置将冷凝液返回精馏塔中,重复进行加热和冷凝的过程, 直至达到分离目的。
操作温度应根据进料组成 和产品要求进行选择,以
实现最佳分离效果。
操作压力应根据进料组成 和产品要求进行选择,以
实现最佳分离效果。
操作条件的优化
实验法
通过实验方法测定不同操作条件下的分离效果,找 出最优的操作条件。
模拟法
利用计算机模拟软件对精馏过程进行模拟,通过优 化算法找出最优的操作条件。
经济分析法
石油化工原料的制备
通过精馏技术可以制备石油化 工原料,如乙烯、丙烯等,这 些原料是生产塑料、合成橡胶 等材料的重要基础。
精馏在其他领域的应用
01
02
03
食品工业
精馏技术可用于食品工业 中,如分离果汁中的果糖 和乙醇饮料中的酒精等。
制药工业
精馏技术可用于药品的生 产和提纯,如分离抗生素、 维生素等。
精馏的分类
02
01
03
根据操作方式的不同,精馏可以分为连续精馏和间歇 精馏。
根据进料位置的不同,精馏可以分为侧线精馏、塔顶 精馏和塔底精馏。
根据操作压力的不同,精馏可以分为常压精馏、加压 精馏和减压精馏。
02
精馏塔的构造和工作原理
精馏塔的结构
塔体
进料板
塔板
溢流管
冷凝器
精馏塔的主要部分,用于 容纳待分离的液体混合物 和进行传热传质过程。
精馏过程节能技术综述

精馏过程节能技术综述现代工业生产过程中,精馏过程是十分常见的一种操作,用于从混合物中分离出不同组分。
然而,传统的精馏过程存在能源浪费的问题,因为它需要大量的能源来进行加热和冷却。
因此,如何降低精馏过程的能源消耗成为了一个重要的研究方向。
在过去的几十年里,研究人员提出了多种节能技术,以下综述了一些常见的节能技术。
首先,改进传统精馏塔的设计是一种简单但有效的节能方法。
例如,使用多级精馏塔可以增加分馏塔的效率,减少需加热和冷却的动力。
此外,增加塔内的换热面积也可以改善能量利用率。
此外,通过使用先进的塔内填料和分布器,可以提高物质的传质效率,从而减少所需的塔高和物料回流比例。
其次,热力耦合是另一种常用的节能技术。
该技术通过将不同温度的流体进行热交换,来降低能源消耗。
例如,实施热力耦合可以将进出精馏塔的气体进行热交换,从而降低所需的加热和冷却负荷。
此外,热力耦合还可以用于塔内热交换,例如通过使用塔内回流来预热进入精馏塔的物料。
另外,采用较低的工艺温度和压力也可以有效地减少精馏过程的能耗。
降低工艺温度可以减少所需的加热负荷,而降低工艺压力可以减少所需的冷却负荷。
因此,在设计和操作精馏过程时,应考虑选取较低的工艺温度和压力,以降低能源消耗。
此外,使用较低的辅助能源,如太阳能、余热等,也是一种常用的节能技术。
太阳能可以用于提供所需的加热或冷却能量,从而降低对传统能源的依赖。
余热是指在其他工艺过程中产生的废热,在精馏过程中可以被回收利用,用于提供所需的加热或冷却能源,进一步减少能源消耗。
最后,引入新的分离技术也是提高精馏过程能耗效率的一种途径。
例如,膜分离技术被广泛应用于分离混合物中的气体或液体组分,并且其能耗通常较低。
相比传统的蒸馏过程,膜分离技术不需要额外的加热和冷却能源,因此能够有效地节约能源。
总的来说,精馏过程节能技术的研究和应用对能源的合理利用具有重要意义。
通过改进传统精馏塔的设计、热力耦合、降低工艺温度和压力、使用低辅助能源和引入新的分离技术等方法,可以有效地降低精馏过程的能耗。
精馏过程的节能降耗

精馏过程的节能降耗精馏过程在化工产业中是一项重要的分离技术,但是它也是能耗较高的过程。
为了降低能耗,节能降耗已经成为精馏技术的一个重要研究方向。
本文将介绍几种精馏过程的节能降耗技术。
首先,提高精馏塔的热效率是提高精馏过程的一个关键。
一种常见的做法是引入换热器网络来最大程度地利用出塔冷凝液和进塔蒸汽之间的热量传递。
这种方法可以降低所需的蒸汽量,从而降低了能耗。
此外,还可以使用多效精馏、热泵或采用废热回收技术进一步提高热效率。
其次,提高精馏过程的物质效率也是节能降耗的一个重要途径。
物质效率是指在精馏过程中使用的干燥剂或者吸附剂能够更有效地去除杂质,从而减少能耗。
通过改进精馏塔的操作条件,如温度、压力和液体流速等参数,可以提高物质效率。
同时,使用高效的精馏填料或者塔板也能够提高分离效果,减少杂质的含量。
此外,使用先进的辅助技术可以进一步降低精馏过程的能耗。
例如,在精馏过程中引入膜分离技术可以减少能源消耗。
膜分离技术是一种基于材料表面或孔隙的选择性渗透性原理分离混合物的方法。
与传统的溶剂萃取或者蒸馏技术相比,膜分离技术具有能耗低、操作简单、体积小等优点。
通过将膜分离技术与精馏过程相结合,可以实现更高效的分离效果。
最后,优化精馏过程的操作策略也是节能降耗的一个重要途径。
通过优化参数设定和控制策略,可以使精馏过程更加稳定和高效。
例如,采用先进的控制算法,如模型预测控制或者模糊控制算法,可以实现对精馏过程的快速响应和精确控制,从而降低了能耗和运行成本。
总的来说,精馏过程的节能降耗是一个涉及多个方面的工程问题。
通过提高热效率、物质效率,使用先进的辅助技术和优化操作策略,可以有效地降低精馏过程的能耗。
这些节能降耗技术不仅可以减少环境污染,还可以提高精馏过程的经济效益。
因此,精馏过程的节能降耗在工业应用中具有重要的意义。
精馏过程的节能途径

广
东
化
工
20 0 7年 第 1 期 1
W WW .dc e . m g h m co
第3 4卷 总第 1 5 7 期
精 馏 过 程 的节 能途 径
边 习棉 ,朱银惠 ,李辉
(.河 北省 产 品质量 监督检 验 院 ,河 北 石家庄 0 05 ;2 1 50 1 .河 北工 业职 业技术 学 院 ,河 北 石家庄 00 9) 501
Bi nXi a Zh n ui, i a mi n , u Yi h Li Hu
(. h b i rvn e rd c Q a t uv ia c xmie h c utad S iah a g0 0 5 ; 1T e He e Po ic o u t u lyS rel n e a n s eo r r, hj z u n 5 0 P i l E T y i 1 2 He e Istt o o ai . b in tue f c t n&T cn lg , h iz un 5 0 C ia i V o eh oo y S iah a g0 0 9 . hn ) j 1
mu t l — f c r ci c t n e t u e tf ai n l p ee e t e t a i ,h a— mp r c i c t ,h t c u l rc i c t n n e h t i tg a e itl t n t we, n w i h e e t i i f o p i o o o p e e t ai ,i n r o n e r td d si ai o r e h g — f c i f o l o s p r t n tc n l g n O o .M u t l— fe t rc i c t n i cu i g N a all o e a in r c i c to o  ̄,t e h a i g se m f e a ai e h o o y a d S n o l p e e f c e t ai n l d n p r l p r t e t ai n t we i i f o e o i f h e t ta o n r — o lr c n r d c n o / c mp r g t e o i i a sn l —fe t r ci c t n T e e eg o s mp i n c n r d c 0 i e t u e b i a e u e i t 1 e N o a i h rg n l i ge e c e t a i h n r y c n u t a e u e 2 % n h a— mp n i f o o p r ci c t n T eh t o p er c i c t n c n r d c 0 e e g o a i g t h o e t ai . h o u l e t ai a e u e 3 % n r y c mp rn ot e t c mmo we s T e e e g a i g r a h d 3 - 0 i f o c i f o wo nt o r . h n r ys v n c e 0 6 % e i n r o t g ae it lt n t we . i c n l ge r v d t e S C E Si d l s, a i g e e g e c e 0 6 % . ni e t n e r t d d si a i o rTh s e h o o i s o e b U C S mi d et t s v n n r yr a h d 3 - 0 n h i l o t p o n e Ke wo d : e t c t n; e e g o s r ai n y r s r ci a i i f o n r yc n e v t o
化工精馏节能技术探讨
化工精馏节能技术探讨化工精馏是一种广泛的分离技术,广泛应用于炼油、化工、精细化工、制药等行业。
由于化工精馏的能耗和排放量较高,为了减少对环境的影响以及降低生产成本,探究化工精馏节能技术的应用显得十分重要。
一、精馏原理精馏是一种将混合物中的组分分离为一系列固定沸点组分的方法。
在一个精馏塔中,混合物在塔底蒸发后升往塔顶,通过多级板或者填料进一步蒸馏和分离。
不同沸点的组分会在不同的塔板或填料层凝结、液化分离出来。
经过多次分离,可以得到高纯度的分离产物。
二、节能措施1. 优化工艺参数通过客观分析和实验对化工精馏的工艺参数进行优化,可以达到节能的目的。
优化参数包括塔径、进料温度、进料速率、再沸点的选择等。
优化参数的主要目的是降低热量的损耗,提高再沸进料的回收,提高产品的纯度。
2. 应用热力学分析方法化工精馏通过热量供给来产生馏出性的分级蒸馏过程。
对于具有相同沸点的混合物,应用热力学分析方法来计算馏出程度,优化精馏条件,可达到节约热量、降低气体排放的目的。
3. 利用先进的装置技术采用先进的塔板、塔壳、填料技术,可以优化气液流动、充分利用热量,提高馏分的产量和质量。
例如,采用结构平面装置来提高塔顶的分馏效果,以及选用有效的填料来提高再沸孔的分馏效果等,都是有效的节能措施。
4. 优化回收系统采用高效的回收系统能够有效地提高化工精馏的再利用效益。
例如,实施热回收技术来回收热量和回收常温下的再沸馏分等都能达到节能的目的。
三、总结化工精馏在工业生产和人类生活中有着广泛的应用,同时其高耗能、高排放的特点也给环境带来了不小的影响。
为了减少对环境的影响,降低生产成本,我们需要探究化工精馏的节能降耗技术。
采取以上措施,能够有效地降低化工精馏的能耗和排放,提高生产效益,是企业可持续发展的重要措施。
《化工原理精馏》课件
精馏流程图
• 流程图:精馏流程图展示了精馏 操作的全过程,包括原料的预处 理、加热、蒸发、冷凝、回流等 步骤。通过流程图可以直观地了 解精馏操作的过程和原理,有助 于更好地理解和掌握精馏技术。
02 精馏塔设备
精馏塔类型
板式塔
塔内装有多层塔板,液体在塔板上完成汽化与回流,实现分 离。
填料塔
塔内装有填料,液体沿填料表面流下,与上升气体进行接触 传质。
低温余热利用
利用低温余热驱动精馏过程,减少对新鲜能源的依赖 。
废气处理技术
采用吸附、吸收、催化燃烧等方法处理废气,降低污 染物排放。
新型精馏技术
分子蒸馏
利用高蒸气压下分子间的平均自由程大于蒸馏 器结构尺寸的特点,实现高效分离。
反应精馏
在精馏过程中进行化学反应,实现产物的高效 分离和转化。
膜分离技术
据具体工艺要求进行选择和控制。
苯精馏案例
总结词
苯精馏是石油化工中重要的分离过程,其工 艺流程和操作条件较为复杂。
详细描述
苯精馏的目的是从石油裂解气中分离高纯度 的苯产品。原料经过预处理后进入精馏塔, 在塔内通过多次汽化和冷凝操作,将苯与其 他组分分离。操作过程中需严格控制温度、 压力、进料位置和回流比等参数,以保证苯 产品的质量和收率。
精馏操作优化
04
操作参数优化
01
塔板数优化
根据物料性质和分离要求,合理选择塔板数,以提高分 离效率和产品质量。
02
进料位置优化
通过调整进料位置,改善物料在塔内的分布,提高传热 和传质效率。
03
回流比优化
根据操作条件和分离要求,合理调整回流比,以平衡能 耗和分离效果。
节能减排技术
热集成精馏
精馏的节能技术
图3操作压力对气液 平衡的影响
脱甲烷塔在5~6kg/cm2压力下操作与 30~35kg/cm2压力下操作相比,回流比可下降 1/9~1/10,一个40万吨的乙烯装置,即可节 约压缩功率3600千瓦,而且投资也可减少。 对于减压操作的塔, 纸然进一步降低操 作压力可减少回流比, 但减压下塔板效率降 低,节能效果不一定显著, 必须慎垂对待。
图2进料状态对 精馏塔的影响
2、气液平衡状态的改进
(1)萃取精馏、共沸精馏、加盐精馏
这类精馏技术是由于添加第三组分,使 要分离的两组分的相对挥发度增加,破坏或 利用共沸,来使组分变得更加容易分离。一 般在分离较困难的系统中采用,从节能角度 考虑也可以作为一项很重要的技术而被采用。
(2)选择最优操作压力
1、操作线的改进
⑴选择最优回流比
影响精馏过程能量消耗最主要的因素是回 流比,精馏塔的能耗随回流比几乎成正比增 加。所以应选择完成给定的分离任务所需要 的操作费和设备费的总和为最小值的回流比。 适宜回流比:与最少总费用相对应的回流比 称为适宜回流比或操作回流比。
图1 最宜回流比的确定
回流比倍数经验范围: 大多数文献建议 R=1.1~2.0Rmin。 进入70年代后,由于技 术的进步和能源问题的 产生,对回流比的选择 更加慎重。目前,回流 比的选择选择已经降到 最小回流比的1.3倍以下, 有的甚至推荐 R=(1.1~1.15)Rmin。
一、精馏节能的重要性
我国化学工业能源消耗占全国总额的 11.5%,占工业部总能耗的20.4%,折算标 准煤约8740万吨。 精馏过程是利用组分沸点不同,重复 进行蒸发和冷凝,使组分分离的过程,因 此,热效率很低。 由塔釜加给精馏塔上热能的95%被塔顶 冷却水等介质带走,而真正用于分离的能 量仅为5%。
(完整版)《化工原理》试题库答案(2)
《化工原理》试题库答案一、选择题1.当流体在密闭管路中稳定流动时,通过管路任意两截面不变的物理量是(A)。
A.质量流量B.体积流量C.流速D.静压能2. 孔板流量计是( C )。
A. 变压差流量计,垂直安装。
B. 变截面流量计,垂直安装。
C. 变压差流量计,水平安装。
D. 变截面流量计,水平安装。
3. 下列几种流体输送机械中,宜采用改变出口阀门的开度调节流量的是(C)。
A.齿轮泵 B. 旋涡泵 C. 离心泵 D. 往复泵4.下列操作中,容易使离心泵产生气蚀现象的是(B)。
A.增加离心泵的排液高度。
B. 增加离心泵的吸液高度。
C. 启动前,泵内没有充满被输送的液体。
D. 启动前,没有关闭出口阀门。
5.水在规格为Ф38×2.5mm的圆管中以0.1m/s的流速流动,已知水的粘度为1mPa·s则其流动的型态为(C)。
A.层流B. 湍流C. 可能是层流也可能是湍流D. 既不是层流也不是湍流6.下列流体所具有的能量中,不属于流体流动的机械能的是(D)。
A. 位能B. 动能C. 静压能D. 热能7.在相同进、出口温度条件下,换热器采用(A)操作,其对数平均温度差最大。
A. 逆流B. 并流C. 错流D. 折流8.当离心泵输送液体密度增加时,离心泵的(C)也增大。
A.流量 B.扬程 C.轴功率 D.效率9.下列换热器中,需要热补偿装置的是(A)。
A.固定板式换热器 B.浮头式换热器 C.U型管换热器 D.填料函式换热器10. 流体将热量传递给固体壁面或者由壁面将热量传递给流体的过程称为(D)。
A. 热传导B. 对流C. 热辐射D.对流传热11.流体在管内呈湍流流动时B。
A.Re≥2000B. Re>4000C. 2000<Re<4000D. Re<200012.离心泵最常用的调节方法是(B)A 改变吸入管路中阀门开度B 改变压出管路中阀门的开度C 安置回流支路,改变循环量的大小D 车削离心泵的叶轮13.U型管压差计指示液的密度(A)被测流体的密度。
- 1、下载文档前请自行甄别文档内容的完整性,平台不提供额外的编辑、内容补充、找答案等附加服务。
- 2、"仅部分预览"的文档,不可在线预览部分如存在完整性等问题,可反馈申请退款(可完整预览的文档不适用该条件!)。
- 3、如文档侵犯您的权益,请联系客服反馈,我们会尽快为您处理(人工客服工作时间:9:00-18:30)。
一、恒 R 下间歇精馏的计算
3.物料衡算 恒回流比间歇精馏的物料衡算关系与简单蒸馏 的物料衡算关系类似。
xF dx nF ln xW y x nW
间歇精馏曲线作用
指导试车和生产 对精馏过程进行分析
四、间歇精馏与连续精馏的比较
多组分( n 个组分)混合物分离 比较项目 塔数 塔径 流程 能耗 劳动强度 间歇精馏 1 大 短 高 大 连续精馏 n-1 小 长 低 小
第九章 蒸 馏
9.5 两组分连续精馏的计算 9.6 间歇精馏 9.6.1 间歇精馏概述 9.6.2 间歇精馏计算
二、精馏过程的节能途径
1.精馏塔;2.压缩机 3.再沸器;4.节流阀
热泵精馏技术
二、精馏过程的节能途径
4.多效精馏 将几个精馏塔串联,操作压力依次降低,前一 精馏塔的塔顶蒸汽作为后一精馏塔的再沸器的加热 介质,故除两端精馏塔外,中间的精馏塔不需从外 界引入加热和冷却介质。
二、精馏过程的节能途径
二、恒 xD 下间歇精馏的计算
代入得
( R 1) dn V n F ( x D x F ) dx W 2 (x D x W )
对应釜液组成xW的汽化总量
nV
nV 0
dnV nF ( xD xF )
xF
xWe
( R 1) dx 2 W ( xD xW )
二、恒 xD 下间歇精馏的计算
二、精馏过程的节能途径
原料预热回收精馏过程的热能
二、精馏过程的节能途径
原料预热回收精馏过程的热能
第九章 蒸 馏
9.5 两组分连续精馏的计算 9.5.7 连续精馏装置的热量衡算与节能
9.5.8 精馏过程的操作型计算与调节
精馏过程的操作型计算与调节(自学)
自学提纲 ① 了解影响精馏操作的主要因素。
馏出液的 平均组成
一、恒 R 下间歇精馏的计算
5.每批精馏所需的时间
每批操 作的馏 出量 kmol
每批操作的汽化量
nV ( R 1)nD
每批操作所需的时间
nV qn,V
汽化速率 kmol/h
二、恒 xD 下间歇精馏的计算
1.确定理论塔板层数 计算基准:终态 最小回流比 操作回流比 馏出液组成 xD 釜液组成 xWe
x D yq yq xq ( xq xW e)
Rmin
R (1.1 ~ 2) Rmin
恒 xD 下间歇精馏时理论板层数的确定
二、恒 xD 下间歇精馏的计算
2.确定xW和 R 的关系 若已知精 馏过程某一时 刻下釜液组成 xW1,对应的 R 可采用试差作 图的方法求得。 恒 xD下间歇精馏时R和xW的关系
二、恒 xD 下间歇精馏的计算
3.物料衡算 设
d 时间内
溶液的汽化量为 d nV kmol 馏出液量为 d nD kmol 瞬间的回流比为 R
则
dnV ( R 1)dnD
二、恒 xD 下间歇精馏的计算
每批操作中任一瞬间前馏出液量
xF xW nD nF xD xW
微分得
( xF xD ) dnD nF dxW 2 ( xD xW )
二、精馏过程的节能途径
2.降低塔釜操作温度 塔压降△P 示例
~ 釜温tW
~
能耗
采用高效塔填料代替原有塔板,降低塔压降
二、精馏过程的节能途径
3.热泵精馏 将塔顶蒸汽绝热压缩升温,作为再沸器的热源, 将再沸器中的液体部分汽化,而压缩气体本身冷凝 成液体,经节流阀后一部分作为塔顶产品采出,另 一部分作为塔顶回流液。
qn , D qn , F qn , F qn , F
p1 > p2 > p3 t1 > t2 > t3
qn,W
qn多效精馏技术
二、精馏过程的节能途径
5.原料预热 将原料预热可回收精馏过程的热能,减少精馏 过程的能耗。原料预热有两种流程:
用塔顶蒸气预热原料 用塔釜采出液预热原料
2.间歇精馏的操作方式
间歇精馏操作方式
馏出液组成恒定
xD恒定
R 恒定
~R ~ xD
回流比恒定
二、间歇精馏的应用场合
间歇精馏适用场合
所分离的原料是分批获得的 分离的原料多变 原料种类多变 原料组成多变 多组分混合物的分离
三、间歇精馏曲线
间歇精馏曲线形式
馏出液组成 ~ 精馏时间 塔顶温度 ~ 精馏时间
xF dxW nF ln xWe x x nWe D W
简单蒸馏过程 物料衡算关系 恒 R 下间歇蒸馏 过程物料衡算关系
一、恒 R 下间歇精馏的计算
4.馏出液平均组成 xDm计算 由
nD nF nW
nD xDm nF xF nW xW
联立得
xDm
nF xF nW xW nF nW
4.每批精馏所需的时间
确定xW和 R 的关系
积分求出 nV 则
nV qn,V
汽化速率 kmol/h
练 习 题 目
第九章 蒸 馏
3.5 两组分连续精馏的计算 3.5.7 连续精馏装置的热量衡算与节能
一、连续精馏装置的热量衡算
二、精馏过程的节能途径
1.减小操作回流比
qn, L、qn,V qn, L、qn,V
R R
示例
~
~
~ 能耗
NT
~ NP一定,需提高ET
采用高性能新型塔板代替原有塔板,提高效率 采用高效塔填料代替原有塔板,提高效率
② 了解操作型计算与设计型计算的区别。
③ 了解精馏过程的控制与调节。
第九章 蒸 馏
9.5 两组分连续精馏的计算 9.6 间歇精馏 9.6.1 间歇精馏概述
一、间歇精馏的特点与操作方式
1.间歇精馏的特点
间歇精馏特点
~ xD
xW tD tW
非稳态操作过程 只有精馏段
操作灵活、适应性强
一、间歇精馏的特点与操作方式
一、恒 R 下间歇精馏的计算
1.确定理论塔板层数 计算基准:初态 馏出液组成 xD1 釜液组成 xW1 (xF)
最小回流比
Rmin
xD1 yq yq xq
( xq xF )
操作回流比
R (1.1 ~ 2) Rmin
恒 R 下间歇精馏时理论板层数的确定
一、恒 R 下间歇精馏的计算