天津大学反应工程PVC装置氯乙烯合成车间工艺设计
年产万吨聚氯乙烯车间工艺设计

一、工艺流程概述1.原料准备:将乙烯气体通过氯化反应和氯化工艺制备成氯乙烯。
2.聚合反应:将制备好的氯乙烯与过氯化钴等催化剂进行聚合反应,生成聚氯乙烯。
3.精炼和提炼:通过卸料和提炼过程,除去聚合反应产生的杂质和残留催化剂。
4.融化加工:将精炼和提炼后的聚氯乙烯经过加热和融化,通过挤出、注塑、吹膜等加工工艺,制成各种产品。
5.产品检验:对融化加工后的产品进行物理性能和质量的检验。
6.包装和出库:将合格的产品进行包装,并出库销售。
二、关键设备的选择和工艺参数的确定1.氯化塔:采用液氯氯化法,选择高效的氯化塔设备,保证氯化反应的高效进行。
2.反应釜:选择适当规格的不锈钢反应釜,对聚合反应进行控制。
3.蒸馏塔:选择具有高效蒸馏性能的蒸馏塔,进行精炼和提炼过程。
4.挤出机、注塑机、吹膜机等加工设备:选择具有高效和稳定性能的加工设备,满足产品加工要求。
5.检测仪器:选择高精度的物理性能和质量检测仪器,确保产品符合标准要求。
三、安全措施和环保要求1.氯气泄漏报警和处理系统:设置氯气泄漏探测器,在发现泄漏情况时及时报警,并启动处理系统进行处理,保证车间人员的安全。
2.废气处理系统:设置废气处理设备,对产生的废气进行处理,减少对环境的污染。
3.废水处理设施:建立废水处理系统,对产生的废水进行处理,达到排放标准。
4.严格操作规程和个人防护措施:制定严格的操作规程,包括操作流程、操作要求等,并提供个人防护装备,提醒员工遵守相关安全规定。
5.废弃物处理:建立废弃物分类处理系统,对废弃物进行分类、包装和处理,减少对环境的影响。
四、能源消耗和优化1.合理规划车间布局和设备布置,减少能源输送、损耗和消耗。
2.对设备进行定期检修和维护,保持设备运行的稳定性和高效性,减少能源的浪费。
3.提高工艺参数的优化,减少生产过程中能源的消耗。
4.引入智能化管理系统,对能源消耗进行实时监控和调整,达到最佳的能效。
总结:年产万吨聚氯乙烯车间的工艺设计需要考虑原料准备、聚合反应、精炼和提炼、融化加工、产品检验以及包装和出库等环节。
年产万吨聚氯乙烯车间工艺设计

年产万吨聚氯乙烯车间工艺设计1. 引言本文档旨在对年产万吨聚氯乙烯(PVC)车间的工艺设计进行详细说明。
PVC是一种重要的合成树脂,广泛应用于建筑材料、电线电缆、塑料制品等领域。
设计一个高效、稳定和可持续发展的车间工艺对于确保产品质量和提高生产效率至关重要。
2. 工艺流程2.1 原料准备PVC的主要原料包括乙烯、氯乙烯和氢氯酸等。
原料准备阶段需要对原料进行储存、提供和混合。
储存区域应具备良好的通风和防火设施,确保原料的安全性和稳定性。
2.2 反应PVC的生产主要通过聚合反应完成。
聚合反应要求严格的温度控制、压力控制和触媒添加。
反应釜设备应具备高效的加热和冷却系统,以确保反应的可控性和高效性。
2.3 分离和磺化在聚合反应完成后,需对产物进行分离和磺化处理。
分离过程主要通过卸料和过滤等方式进行,确保分离效果良好。
磺化处理则需通过控制温度和添加磺化剂等手段,使产物获得所需的性质和品质。
2.4 硫化经过分离和磺化处理后的产物需要进行硫化反应,以提高PVC的机械性能和耐候性。
硫化过程需要控制温度、压力和硫化剂的添加量,确保硫化反应的完全性和一致性。
2.5 润滑和加工硫化后的PVC需要进行润滑处理,以增强其流动性和加工性。
润滑处理一般通过添加润滑剂,同时需要控制温度和混合速度,以确保润滑剂均匀分布。
之后,PVC可进行成型、挤出、注塑等加工方式,制成最终的产品。
3. 设备需求为了实现年产万吨聚氯乙烯的目标,车间需要配置以下主要设备:•反应釜:高效的反应釜能够提供良好的加热和冷却系统,满足反应过程的要求。
•分离设备:包括卸料和过滤设备,能够实现有效和高效的分离过程。
•磺化设备:具备精确的温度控制和添加磺化剂的能力,以实现良好的磺化效果。
•硫化设备:提供准确的温度和压力控制,确保硫化反应的完全性和一致性。
•润滑设备:包括润滑剂添加设备和混合设备,能够实现均匀的润滑处理。
4. 安全和环境考虑在设计车间工艺时,安全和环境因素是非常重要的考虑因素。
氯乙烯合成工艺设计
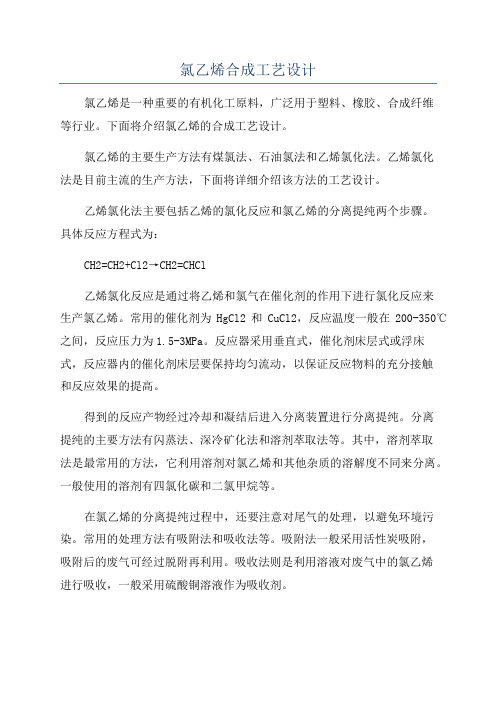
氯乙烯合成工艺设计氯乙烯是一种重要的有机化工原料,广泛用于塑料、橡胶、合成纤维等行业。
下面将介绍氯乙烯的合成工艺设计。
氯乙烯的主要生产方法有煤氯法、石油氯法和乙烯氯化法。
乙烯氯化法是目前主流的生产方法,下面将详细介绍该方法的工艺设计。
乙烯氯化法主要包括乙烯的氯化反应和氯乙烯的分离提纯两个步骤。
具体反应方程式为:CH2=CH2+Cl2→CH2=CHCl乙烯氯化反应是通过将乙烯和氯气在催化剂的作用下进行氯化反应来生产氯乙烯。
常用的催化剂为HgCl2和CuCl2,反应温度一般在200-350℃之间,反应压力为1.5-3MPa。
反应器采用垂直式,催化剂床层式或浮床式,反应器内的催化剂床层要保持均匀流动,以保证反应物料的充分接触和反应效果的提高。
得到的反应产物经过冷却和凝结后进入分离装置进行分离提纯。
分离提纯的主要方法有闪蒸法、深冷矿化法和溶剂萃取法等。
其中,溶剂萃取法是最常用的方法,它利用溶剂对氯乙烯和其他杂质的溶解度不同来分离。
一般使用的溶剂有四氯化碳和二氯甲烷等。
在氯乙烯的分离提纯过程中,还要注意对尾气的处理,以避免环境污染。
常用的处理方法有吸附法和吸收法等。
吸附法一般采用活性炭吸附,吸附后的废气可经过脱附再利用。
吸收法则是利用溶液对废气中的氯乙烯进行吸收,一般采用硫酸铜溶液作为吸收剂。
除了反应和分离提纯步骤外,还要对生产过程中产生的废水、废热等进行处理利用,以达到资源综合利用和环境保护的目的。
总结起来,氯乙烯的合成工艺设计主要包括乙烯氯化反应和氯乙烯的分离提纯两个步骤,其中乙烯氯化反应通过催化剂的作用将乙烯和氯气进行氯化反应,分离提纯则通过溶剂萃取法将氯乙烯和其他杂质进行分离。
在生产过程中还要注意对废气、废水和废热的处理利用。
正确设计和优化各个环节的操作条件和流程,能够提高产量、品质和能源利用率,降低生产成本和环境污染,实现可持续发展。
年产16万吨氯乙烯合成工艺设计

年产16万吨氯乙烯合成工艺设计1. 引言氯乙烯是一种重要的有机化工原料,广泛应用于塑料、合成橡胶、溶剂等行业。
本文旨在设计一种年产16万吨氯乙烯的合成工艺,以满足市场需求并提高生产效率。
2. 工艺概述合成工艺的概述如下:1.原料准备:主要原料包括乙烯、氯气和催化剂。
2.反应装置:采用流动床反应器,具有较高的热传导和负载能力。
3.反应步骤:氯气与乙烯在催化剂作用下发生氯化反应,生成氯乙烯。
4.分离纯化:通过多级凝馏和萃取等工艺对氯乙烯进行纯化。
5.产品储存和包装:将纯化后的氯乙烯储存于贮罐中,并进行相应的包装以便于运输和销售。
3. 反应装置设计3.1 流动床反应器流动床反应器是当前工业生产中常用的反应器类型之一,由于其具有优良的热传导和负载能力,适用于氯乙烯的合成反应。
流动床反应器的设计要点如下:•反应器材料:选择耐腐蚀性能好、热传导性能高的不锈钢。
•反应器结构:采用垂直式结构,方便气体和液体的流动,并且易于维护和清洗。
•热交换器:在反应器内部设置热交换器,提高反应器的热效率,减少能量损失。
•自动控制系统:采用先进的自动控制系统,实时监测反应器的温度、压力等参数,保证反应的稳定进行。
4. 反应步骤与工艺条件4.1 氯化反应氯化反应是合成氯乙烯的关键步骤,该反应基于氯气与乙烯的化学反应。
反应方程式如下:C2H4 + Cl2 -> C2H3Cl + HCl氯化反应的工艺条件如下:•温度:反应温度为300-500摄氏度。
•压力:反应压力为1-5兆帕。
•催化剂:采用氯化汞作为催化剂,具有较高的活性和选择性。
4.2 分离纯化分离纯化工艺的目的是将氯乙烯从反应产物中分离出来,以提高氯乙烯的纯度和质量。
分离纯化工艺包括多级凝馏和萃取等步骤:•多级凝馏:通过不同的温度和压力条件,将乙烯、氯乙烯和其他杂质分离出来。
•萃取:采用特定的溶剂将残留的杂质进一步去除,提高氯乙烯的纯度。
5. 安全防护措施在氯乙烯合成工艺中,涉及到氯气和高温高压条件,因此必须采取必要的安全防护措施,以防止事故发生,保证生产安全。
反应工程氯乙烯课程设计
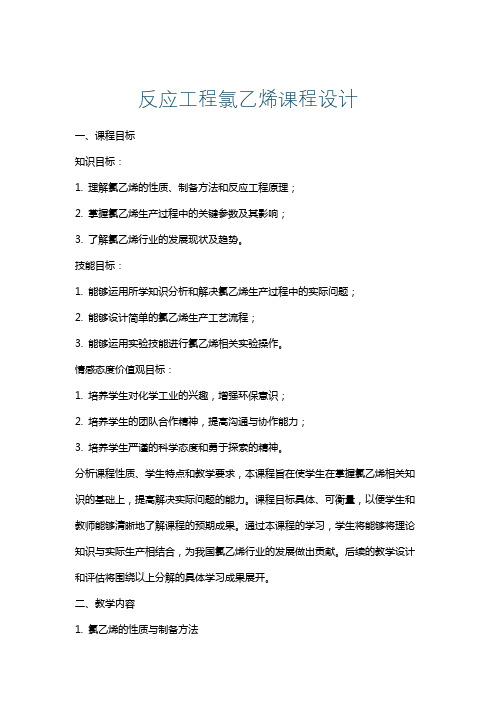
反应工程氯乙烯课程设计一、课程目标知识目标:1. 理解氯乙烯的性质、制备方法和反应工程原理;2. 掌握氯乙烯生产过程中的关键参数及其影响;3. 了解氯乙烯行业的发展现状及趋势。
技能目标:1. 能够运用所学知识分析和解决氯乙烯生产过程中的实际问题;2. 能够设计简单的氯乙烯生产工艺流程;3. 能够运用实验技能进行氯乙烯相关实验操作。
情感态度价值观目标:1. 培养学生对化学工业的兴趣,增强环保意识;2. 培养学生的团队合作精神,提高沟通与协作能力;3. 培养学生严谨的科学态度和勇于探索的精神。
分析课程性质、学生特点和教学要求,本课程旨在使学生在掌握氯乙烯相关知识的基础上,提高解决实际问题的能力。
课程目标具体、可衡量,以便学生和教师能够清晰地了解课程的预期成果。
通过本课程的学习,学生将能够将理论知识与实际生产相结合,为我国氯乙烯行业的发展做出贡献。
后续的教学设计和评估将围绕以上分解的具体学习成果展开。
二、教学内容1. 氯乙烯的性质与制备方法- 氯乙烯的结构、物理性质和化学性质- 氯乙烯的制备方法:乙炔法、乙烯法等- 相关化学反应原理及动力学研究2. 氯乙烯反应工程原理- 氯乙烯合成反应的热力学及动力学- 反应器类型及其在氯乙烯生产中的应用- 影响氯乙烯合成反应的主要因素:温度、压力、催化剂等3. 氯乙烯生产工艺流程及设备- 氯乙烯生产流程:原料处理、反应、分离、精制等- 主要设备及其功能:反应釜、压缩机、冷凝器等- 生产过程中的安全与环保措施4. 氯乙烯行业现状与发展趋势- 国内外氯乙烯行业现状分析- 氯乙烯行业发展趋势及前景- 环保要求对氯乙烯行业的影响5. 实践教学与案例分析- 氯乙烯合成实验操作及注意事项- 案例分析:氯乙烯生产过程中的常见问题及解决方案- 团队合作完成氯乙烯生产工艺流程的设计教学内容根据课程目标进行选择和组织,保证科学性和系统性。
教学大纲明确教学内容安排和进度,结合教材相关章节,使学生在掌握理论知识的基础上,深入了解氯乙烯生产实际,为培养应用型人才奠定基础。
年产2465万吨PVC的氯乙烯合成工段的工艺设计毕业论文设计
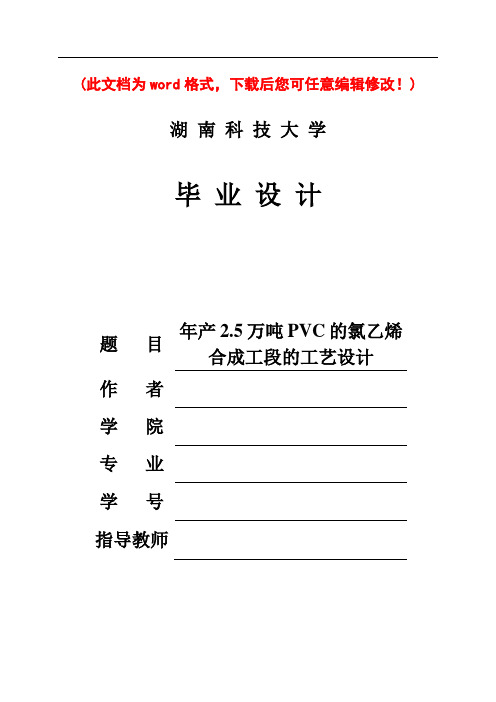
(此文档为word格式,下载后您可任意编辑修改!)湖南科技大学毕业设计题目年产2.5万吨PVC的氯乙烯合成工段的工艺设计作者学院专业学号指导教师湖南科技大学毕业设计任务书化学化工学院应用化学系(教研室)系(教研室)主任:(签名)年月日学生姓名: 学号: 0706020206 专业: 应用化学1 设计(论文)题目及专题:年产2.5万吨PVC的氯乙烯合成工段的工艺设计2 学生设计(论文)时间:自2011 年3 月 8 日开始至 2011 年 6 月 10 日止3 设计(论文)所用资源和参考资料:4 设计(论文)应完成的主要内容:5 提交设计(论文)形式(设计说明与图纸或论文等)及要求:6 发题时间:年月日指导教师:(签名)学生:(签名)湖南科技大学毕业设计指导人评语[主要对学生毕业设计(论文)的工作态度,研究内容与方法,工作量,文献应用,创新性,实用性,科学性,文本(图纸)规范程度,存在的不足等进行综合评价]指导人:(签名)年月日指导人评定成绩:湖南科技大学毕业设计评阅人评语[主要对学生毕业设计(论文)的文本格式、图纸规范程度,工作量,研究内容与方法,实用性与科学性,结论和存在的不足等进行综合评价]评阅人:(签名)年月日评阅人评定成绩:湖南科技大学毕业设计(论文)答辩记录日期:学生:学号:班级:题目:提交毕业设计(论文)答辩委员会下列材料:1 设计(论文)说明书共页2 设计(论文)图纸共页3 指导人、评阅人评语共页毕业设计(论文)答辩委员会评语:[主要对学生毕业设计(论文)的研究思路,设计(论文)质量,文本图纸规范程度和对设计(论文)的介绍,回答问题情况等进行综合评价]答辩委员会主任:(签名)委员:(签名)(签名)(签名)(签名)答辩成绩:总评成绩:摘要本设计是年产2.5万吨PVC的氯乙烯合成工段的初步工艺设计。
采用了设计采用了乙炔气体和氯化氢合成氯乙烯,再聚合而成的聚氯乙烯的生产工艺。
对各工段反应进行了物料衡算、、热量衡算;对各工段的生产原理、流程进行了详细的说明;对工作管道设计,选型进行了理论计算。
聚氯乙烯合成装置工艺设计任务书
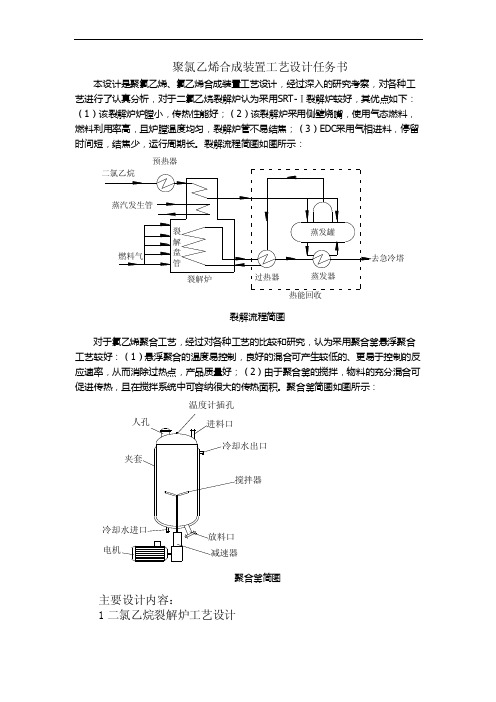
聚氯乙烯合成装置工艺设计任务书
本设计是聚氯乙烯、氯乙烯合成装置工艺设计,经过深入的研究考察,对各种工艺进行了认真分析,对于二氯乙烷裂解炉认为采用SRT-Ⅰ裂解炉较好,其优点如下:
(1)该裂解炉炉膛小,传热性能好;(2)该裂解炉采用侧壁烧嘴,使用气态燃料,燃料利用率高,且炉膛温度均匀,裂解炉管不易结焦;(3)EDC 采用气相进料,停留时间短,结焦少,运行周期长。
裂解流程简图如图所示:
预热器
裂解炉热能回收
裂解流程简图 对于氯乙烯聚合工艺,经过对各种工艺的比较和研究,认为采用聚合釜悬浮聚合工艺较好:(1)悬浮聚合的温度易控制,良好的混合可产生较低的、更易于控制的反应速率,从而消除过热点,产品质量好;(2)由于聚合釜的搅拌,物料的充分混合可促进传热,且在搅拌系统中可容纳很大的传热面积。
聚合釜简图如图所示: 电机夹套
搅拌器
减速器
冷却水进口
放料口冷却水出口
进料口
温度计插孔
人孔 聚合釜简图
主要设计内容:
1二氯乙烷裂解炉工艺设计
物料衡算;裂解炉能耗计算;裂解炉炉管工艺计算;裂解炉设计
2氯乙烯聚合釜工艺设计
聚合釜釜体和夹套设计;夹套和筒体厚度设计以及材质选择;搅拌器选型及计算;夹套传热面积的计算。
年产5万吨PVC的氯乙烯合成工段的工艺设计

氯乙烯是一种重要的有机化工原料,广泛应用于塑料、橡胶、涂料等行业。
为了满足年产5万吨PVC的生产需求,需要进行氯乙烯的合成工艺设计。
本文将从原料选择、反应条件、催化剂选择、分离工艺、产品纯化和废水处理等方面进行详细讨论。
首先,氯乙烯的合成主要通过乙烯进行氯化反应得到。
乙烯可以采用石油轻烃或乙烷气相氯化的方法进行制备,其中后者是最常用的方法。
乙烯和氯气在加热的条件下进入氯化炉,通过氯化剂进行反应。
在反应条件方面,首先需要控制反应温度和压力。
一般来说,氯乙烯的合成反应需要在高温条件下进行,可以选择在300-400℃之间的温度范围内进行反应。
压力方面,一般选择在1-3 atm之间。
此外,还需要控制乙烯和氯气的摩尔比,通常选择1:1的比例。
催化剂选择是氯乙烯合成的重要环节。
常用的催化剂有氧化铜、氯化铜和氯化铁等。
其中,氧化铜催化剂广泛应用于工业氯乙烯的合成中,因其催化活性高,选择速度快,具有良好的经济效益。
在分离工艺方面,主要是将合成氯乙烯和催化剂进行分离。
可以采用蒸馏或萃取等方法,将氯乙烯从反应混合物中分离出来。
蒸馏是一种常用的分离方法,通过控制温度和压力,将氯乙烯从混合物中分离出来。
此外,也可以采用萃取的方法,选择适当的溶剂将氯乙烯从混合物中提取出来。
在产品纯化方面,需要对分离得到的氯乙烯进行纯化处理,以提高产品质量。
可以采用氧化、脱色、脱酸等方法进行纯化处理。
其中,氧化是一种常用的方法,通过氯气的氧化作用,将杂质气体、不饱和物质和酸性物质等进行氧化,提高产品纯度。
最后,需要对废水进行处理,以满足环保要求。
合成氯乙烯的过程中会产生含有盐酸和氯化物等的废水,需要进行中和处理和固液分离等工艺,以达到排放标准。
综上所述,年产5万吨PVC的氯乙烯合成工段的工艺设计,需要从原料选择、反应条件、催化剂选择、分离工艺、产品纯化和废水处理等方面进行综合考虑。
通过合理的工艺设计和操作控制,可以实现高效、稳定的氯乙烯合成过程,满足PVC生产的需求。
- 1、下载文档前请自行甄别文档内容的完整性,平台不提供额外的编辑、内容补充、找答案等附加服务。
- 2、"仅部分预览"的文档,不可在线预览部分如存在完整性等问题,可反馈申请退款(可完整预览的文档不适用该条件!)。
- 3、如文档侵犯您的权益,请联系客服反馈,我们会尽快为您处理(人工客服工作时间:9:00-18:30)。
氯化汞触媒的规格表 规格 10~13 ≤0.3 >90 500~600 ≤5 ≥85 ≤15 ≤1
4
100000 吨/年 PVC 装置氯乙烯合成车间工艺设计
其中,乙炔加成反应的转化率为 99%,主反应的收率为 98.2% 反应方程式为: 主反应:
C2 H2 HCl CH 2CHCl
副反应:
1.1.2 聚氯乙烯 聚氯乙烯(PVC)是 5 大通用塑料之一,目前产量仅次于聚乙烯,位居第 2。 PVC 具有较好的机械性能、耐化学药品性能、耐腐蚀性和难燃性,可广泛应用 于塑料管材、塑料门窗、仿木塑料、板材、薄膜、人造革、电线电缆及包装材料 等,是一种低能耗、低成本、用途广泛的塑料,因此,它在各国仍以较快速度发 展[2]。 PVC 生产技术及产品均在不断研究与开发,尤其在生产技术的创新、生产 规模的大型化、产品的高性能等方面取得较大进展,主要有 3 个方面:(1) 氯乙 烯生产技术方面, 开发出利用不同原料生产氯乙烯的新工艺路线。采用价格便宜 的乙烷作原料, 用直接氧氯化法生产低成本的氯乙烯单体,并正在设计万吨级大 型生产装置。(2) PVC 树脂生产方面,新技术发展集中在进一步解决聚合体系的 稳定和防粘釜问题上, 改进悬浮聚氯乙烯树脂的粒径分布以及开发一些性能更好
1
表 2-1-2 产品技术规格表 序号 名称 VC 1 VCM EDC C 2H 2 规格 99.99% <0.01% <0.001% 化学法 分析方法 国家标准 备注
表 2-1-3 指标名称 HgCl2,% H2O,% 机械强度,% 装填密度,g/l >65 粒度,% 2.75~65 1.0~2.75 <1.0
表 2-3-1 管线 1 进料组成 摩尔流量 kmol/h C2H2 N2 CO2 H2O 总计 234.9184 2.3017 0.0712 1.8577 239.1490 摩尔组成 mol% 质量流量 kg/h 质量组成 w%
98.2310 0.9625 0.0298 0.7768
100.0000
1
100000 吨/年 PVC 装置氯乙烯合成车间工艺设计
的 PVC 专用树脂,如开发透明度更好的抗冲击氯化聚乙烯——丙烯酸酯接枝共 聚物、改进丙烯酸酯改性的 PVC 型材专用树脂的生产方法等;(3)在聚氯乙烯加 工应用方面, 现已研究出用聚丁烯改进 PVC 制品冲击强度和热稳定性的新技术, 研制成功粘结力强、耐风化性好的汽车车体防锈涂料,采用交联 PVC 发泡材料 生产出仪表盘发泡板,开发出水性 PVC 涂料,改进了农用薄膜的防雾性能,生 产出高强度地板夹、热变形温度高的超韧性 PVC 合金等[3]。
C2 H 2 H 2O CH3CHO C2 H 2 2HCl CH 2ClCH 2Cl
氯乙烯单体的聚合率 85.5%,合成反应未反应的 VCM 回收率 20%。 反应流程图如下图所示:
2.2 氯乙烯单体(VCM)流量
由已知年产量 100000 吨聚氯乙烯,年工作小时 8000 小时,设计裕量 5% 得 PVC 产量为 100000 × 由已知 VC 合成收率 95.5% 得聚合所需的氯乙烯单体量为
100000 吨/年 PVC 装置氯乙烯合成车间工艺设计
第一章 文献综述
1.1 氯乙烯和聚氯乙烯的发展状况
1.1.1 氯乙烯 氯乙烯是制备聚氯乙烯及其共聚物的单体。也常称为氯乙烯单体 (VCM), 在世界上是与乙烯和氢氧化钠等并列的最重要的化工产品之一,98% VCM 都用 来生产 PVC,其余的用于生产聚偏二氯乙烯(PVDC)和氯化溶剂等。氯乙烯单体 的工业生产方法主要有乙烯氧氯化法和电石乙炔法。 在英美等发达国家由于石油 工业的优势,主要以乙烯氧氯化法生产[1]。氯乙烯近年来随着世界石油资源储量 逐渐减少,原油价格不断走高,在世界能源供应持续紧张。与我国国内贫油、少 气、富煤、资源特点的背景之下,近些年来电石乙炔法聚氯乙烯产业在我国取得 了飞速的发展,成为了中国聚氯乙烯行业的主流工艺。 目前,采用乙炔法生产的氯乙烯(占总产量的 76%以上) 具有良好的物理及 机械性能,用于生产建筑材料、包装材料、电子材料和日用消费品,广泛应用于 工业、农业、交通运输、电力电讯和包装等各领域。
1.2 生产工艺
1.2.1 电石法生产 PVC 工艺 PVC 树脂生产工艺目前有两种制备工艺,一种是电石法,其主要生产原料 是电石、煤炭和原盐;再有一种是乙烯法,主要原料是石油。下面我们主要介绍 电石法: 该方法是在氯化汞催化剂存在下 , 由乙炔与氯化氢加成,直接合成氯乙烯 (VCM),然后经聚合制得聚氯乙烯。其生产过程可分为乙炔制备和净化,氯乙烯 合成、产品精制及氯乙烯聚合。这一制法工艺和设备较简单,投资低,收率高; 但能耗大,原料成本高,催化剂汞盐毒性大,故受环境保护等所制约[4]。
6107.878 64.4476 3.1328 33.4386 6208.8970
98.3730 1.0380 0.0505 0.5386
100.0000
氯 化 氢 进 料 温 度 10.5 ℃ , 压 力 164KPa , 40% 盐 酸 上 方 水 的 饱和 蒸 汽 压 为 P=0.1357KPa 则氯化氢气体中含水的百分数为 0.1357 = 0.0008274 164 则氯化氢气体中含水量为 280.8806 × 0.0008274 = 0.2326(������������������������/ℎ) 1 − 0.0008274 氯化氢气体总流量为 280.8806 + 0.2326 = 281.1132(kmol/h) 由此得到氯化氢气体进料即管线 2 组成为:
6
100000 吨/年 PVC 装置氯乙烯合成车间工艺设计
1.274 = 0.007768 164 则乙炔气中含水量为 237.2913 × 0.007768 = 1.8577(������������������������/ℎ) 1 − 0.007768 乙炔气总流量为 1.8577 + 237.2913 = 239.1490(������������������������/ℎ) 由此得到乙炔气进料即管线 1 组成为:
氯化氢(干基)总流量为 258.4102÷ 0.92=280.8806(kmol/h)其中 HCl258.4102(kmol/h) H2280.8806 × 7% = 19.6616(������������������������/ℎ) CO2 280.8806 × 0.8% = 2.2470(������������������������/ℎ) O2 280.8806 × 0.2% = 0.5618(������������������������/ℎ) 乙炔气进料温度 10.5℃,压力 164KPa,由《化学工程手册》该温度下的水的饱 和蒸汽压为 1.274KPa 则乙炔气中含水的百分数为:
205.7504 × 1.11 = 228.3829(������������������������/ℎ)
13.7434 = 0.855 ������ + ������ y = 3.2148
即进入聚合釜的氯乙烯单体量为 12.8594 t / h (即 205.7504 kmol / h ), 合成反
图 1-1 乙炔和氯化氢生产聚氯乙烯工艺流程示意图[5]
1.2.2 生产方法的比较 最初的氯乙烯生Байду номын сангаас全部以乙炔为原料,20 世纪 60 年代后期,随着乙烯装置
2
100000 吨/年 PVC 装置氯乙烯合成车间工艺设计
大型化及乙烯氧氯化技术的成熟,乙烯法 PVC 在经济和环保等方面占有明显的 优势,在世界范围内迅速取代电石法。但是在高油价的地区(例如我国) ,电石 法制聚氯乙烯仍然是较主要的方法。 乙炔法氯乙烯合成工艺流程是:电石与水反应生成乙炔,乙炔与氯化氢在氯 化汞的催化作用下合成氯乙烯; 乙烯法氯乙烯合成工艺流程是:乙烯经氯化或氧 氯化反应合成二氯乙烷,再裂解生成氯乙烯。从目前合成工艺路线可知,乙炔法 氯乙烯工艺流程较短,技术较成熟,但生产能力相对较小。乙烯法氯乙烯工艺流程 较长,但副产物较少,并且设备能耗较乙炔法低,污染较小。 从成本上比较: 电石法成本构成主要由电石费用、 氯化氢费用和水电费构成, 总体来讲, 电石法的成本构成分配比例约为: 电石占 65%~70%, 氯化氢占 15%, 电力占 6%,其他制造费用占 6%电石法的一个显著特点为耗电较高,不但在生 产 PVC 时要耗费电力,由焦炭制备电石也要消耗大量的电,如生产 1 吨电石约 需消耗 3450kw/h 的电 0.6 吨的焦炭和 0.9 吨的石灰石。而在乙烯法 PVC 中,乙 烯价格仅占 PVC 生产成本的 50.6 %,主要影响乙烯法制 PVC 的是石油价格。目 前,乙烯法 PVC 生产成本与乙炔法 PVC 生产成本相比具有较大的优势[6]。国外 公司通常以乙烯法作为生产 PVC 的主要工艺,而在我国,由于国内油气资源不 足,而生产电石的石灰石资源非常丰富,因而电石法 PVC 生产在我国具有更好 的资源优势。特别是在石油价格不断上涨的形势下,电石法 PVC 在我国 PVC 生 产能力中所占的比例持续提高。 有人说,国内发展电石法 PVC 是以牺牲环境来追逐利润的,乙烯法 PVC 与 电石法 PVC 的竞争与其说是产品的竞争,不如说是两种观念的竞争,实质的问 题在于是否应当遵循科学的发展观,坚持走可持续发展的道路, 创建环境友好型 社会[7]。不可否认,电石法 PVC 生产中不可避免地存在一定的污染问题,据统 计,采用电石法生产 1tPVC 要排放电石渣 1.5t、废水 20m3、粉尘 20kg;排出的 污水和废渣中含有大量的汞, 而汞对环境的污染是永久性的。 但同时也应该看到, 随着电石渣制砖、电石渣制水泥的推广和普及,电石渣治理问题已经得到解决。 随着低汞触媒的推广和应用,由汞造成的污染逐渐减轻。今后,随着无汞触媒的 开发和应用,PVC 行业将彻底告别汞时代,真正实现清洁生产。
5
1.05 = 13.1250(������/ℎ) 8000